1.1.1. 4ème Révolution industrielle :
On peut considérer que des économistes tels que
Adam Smith (1723-1790), David Ricardo (17721823) et Jean-Baptiste Say
(1767-1832) sont à l'origine de la gestion moderne des organisations et
de la théorie des organisations. En effet, bien avant Taylor, dès
le XIXe, ils ont proposé les premiers concepts de division du travail ou
de spécialisation des tâches. Ces théoriciens en
préconisant l'introduction d'une logique de rationalité dans
l'accomplissement de toute démarche gestionnaire ont manifestement
influencé le courant rationnel de la théorie des organisations
[5]. Mais les travaux fondateurs réalisés par
Frédéric W Taylor et la publication en 1911 d'un ouvrage qui fera
date : « The Principles of Scientific Management » font de celui-ci
le promoteur le plus connu de l'organisation scientifique du travail (OST) et
du management scientifique. En étudiant les conditions
nécessaires à l'amélioration de la productivité des
ouvriers, il conclut qu'une approche méthodique s'impose, qu'il
décrit comme étant l'organisation scientifique du travail. Le
principe de la démarche réside dans une double division du
travail, verticale (séparation des tâches de conception et
d'exécution) et horizontale (spécialisation en une seule et
même tâche).
Il a ainsi posé les bases du management scientifique
basé sur des concepts de rationalité, et de ce qu'on a
appelé par la suite le Taylorisme et qui constitue l'une des
premières grandes transformations organisationnelles. De la
théorie à la pratique, il fût le premier théoricien
à avoir mis en place une méthode opérationnelle visant
à accroître le niveau de production des organisations.
Aujourd'hui on identifie très aisément certaines
des limites de son modèle dans le fait que sa conception de l'homme au
travail repose sur une vision très appauvrie du potentiel humain. En un
certain sens, Ford qui est le véritable concepteur du travail à
la chaîne, est un successeur de Taylor. Il mettra en application les
principes de rationalisation du taylorisme tout en les adaptant dans ses usines
de production automobile. C'est la naissance du « fordisme », dont
les notions principales sont le travail à la chaîne, la
standardisation et le principe du « five dollars a Day ». C'est sur
ce mode de production nécessitant encore de nouvelles transformations
organisationnelles que le modèle industriel du XXe s'est
développé partout dans le monde en contribuant largement à
la croissance mondiale (production de masse - baisse des prix de vente - hausse
des salaires - consommation de masse - élévation des profits).
Mais le modèle fordiste a lui aussi montré ses limites et son
incapacité à s'adapter lors des crises économiques
révélées par les deux chocs pétroliers de 1973 et
de 1979. La prise de conscience des limites du modèle est totale dans
les
15
années 80, face à la prospérité de
la nouvelle concurrence japonaise fondée sur d'autres principes
organisationnels. Ce nouveau modèle industriel japonais dont Toyota est
le fer de lance, a su répondre aux évolutions de la demande et
résoudre le problème d'une production de masse mais sur des biens
différenciés (à l'opposé de la standardisation
imposée par la production fordiste), tout en répondant à
des obligations de qualité, de compétitivité en terme de
coûts constamment décroissants. Le succès de ce
modèle, montrant qu'il était possible de produire en
séries courtes, sans stocks intermédiaires, à des niveaux
de productivité élevés, des produits de qualités, a
obligé l'industrie occidentale à se transformer à nouveau,
à évoluer (intégration des fonctions R&D, production
et marketing).
Le tableau1 propose un comparatif des trois modèles
[6].
Tableau I : Comparatif des principes fondateurs de l'industrie
du XXe siècle
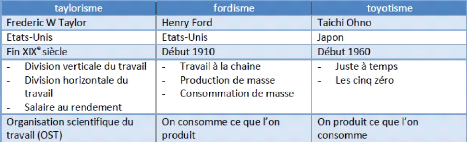
L'industrie 4.0 est un concept qui fait
référence à une quatrième révolution
industrielle et donc, à l'image des 3 dernières (machine à
vapeur et mécanisation au 19ème siècle, production de
masse et convoyeur au 20ème siècle, automatisation depuis les
années 70), à une nouvelle méthode de production. Plus
concrètement, l'usine 4.0 est un système interconnecté qui
relie machines, méthodes de gestion (telles que les Enterprise Resource
Planning, ERP) et les produits.
Il s'agit d'un «nouvel atelier» qui peut prendre les
formes suivantes :
· Une usine innovante
· Une usine totalement digitalisée
· Une usine flexible
· Une usine tournée vers ses acteurs externes
· Une usine responsable sur le plan sociétal
· Une usine économe et responsable sur le plan
environnemental
16
Avec la chute des barrières internationales et
l'arrivée des technologies numériques dans l'environnement
manufacturier et commercial, les entreprises de toutes tailles doivent faire
preuve d'ingéniosité pour demeurer concurrentielles sur le
marché. Pour se distinguer, les entreprises doivent miser sur la valeur
ajoutée pour le client. Les technologies numériques et
l'utilisation des données ont amené aux entreprises une nouvelle
manière de générer de la valeur.
En 2011, à la foire annuelle d'Hanovre, l'Institut des
Fraunhofer dévoilait une nouvelle politique gouvernementale allemande
pour améliorer les pratiques industrielles à la grandeur du pays
:
L'Industrie 4.0 est définie par « Blanchet »
comme une politique industrielle développée par le gouvernement
allemand ayant pour objectif de gagner et maintenir un avantage
compétitif mondial au niveau des entreprises manufacturières. De
par l'investissement dans les nouvelles technologies (automatisation,
systèmes cyber-physiques, etc.), l'Industrie 4.0 se voit une solution
d'avenir pour les industries manufacturières [7]. Ces dernières
doivent en effet répondre à un changement des consommateurs qui
les force à aller vers la production de masse personnalisée.
Elles doivent donc changer leurs paradigmes et leurs pratiques d'affaires. Pour
ces raisons, l'Industrie 4.0 est de plus en plus utilisée dans les
grandes industries allemandes. D'autres pays comme la France et les
États-Unis mettent des efforts importants dans la numérisation de
leur industrie dans l'objectif de gagner un avantage compétitif
mondial.
Une exploration de la littérature a été
effectuée afin de faire le point sur l'état des connaissances
actuelles concernant l'Industrie 4.0 et les principaux outils numériques
et leurs impacts sur les petites et moyennes structures manufacturières.
Les moteurs de recherche Xerfi, ScienceDirect, et Google Scholar ont permis de
cibler différents documents tels que des livres, articles scientifiques,
rapports de recherche, sites internet, conférences et vidéos
portant sur l'Industrie 4.0, la numérisation, l'agilité,
l'économie, l'automatisation, le management et le leadership pour
couvrir le sujet dans sa globalité. Des ouvrages datant des
années 1970 jusqu'à 2018 ont permis d'observer la chronologie et
l'évolution de l'économie globale et des industries dans le
temps. La structure de la recherche présentée à la Figure
2 a permis de guider et d'organiser les idées principales issues de la
revue de la littérature. L'Industrie 4.0 n'est pas une mode ou une
tendance à proprement parler. Cette révolution industrielle
provient d'une chaîne d'événements qui ont amené
à chercher de nouvelles solutions pour demeurer compétitif,
répondre à l'environnement inconstant, incertain, complexe et
ambigüe et pallier au manque de main d'oeuvre vécu dans la plupart
des entreprises manufacturières [7].
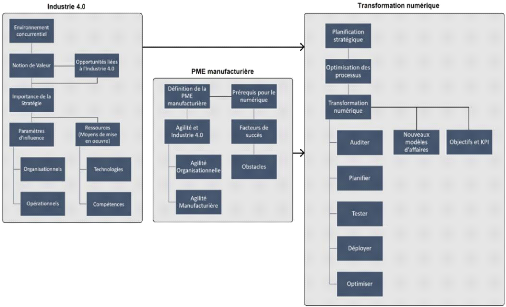
17
Figure 2 : Structure de la recherche
Le potentiel de l'Industrie 4.0
Hermann et al. (2015) ont mené une revue de 51
publications et ont fait ressortir les termes et concepts les plus
fréquemment associés à l'Industrie 4.0. Les auteurs
confirment que les principes clés reliés à l'Industrie
4.0, ou à la numérisation des industries, sont
l'interopérabilité, la virtualisation, la
décentralisation, la capabilité en temps réel,
l'orientation service et la modularité, possibles grâce à
l'implantation de ces différentes technologies [8].
Porter et Heppelmann (2014) démontrent que les
nouvelles technologies numériques, intelligentes et connectées,
sont la clé pour avancer vers un environnement 4.0. Les auteurs
définissent l'intelligence des produits par leur capacité
à collecter et analyser des données. La connectivité est,
quant à elle, la capacité à transférer les
données d'un objet à un autre pour faciliter le transfert
d'information, la prise de décision, et l'analyse plus avancée
des données collectées. Les auteurs présentent la forte
relation entre les besoins de gestion d'une entreprise et le niveau de
numérisation requis. Les différents niveaux de
numérisation sont, selon les auteurs : La
18
surveillance (monitoring) ; le contrôle ; l'optimisation
; et l'automatisation. En fonction de ce qui est recherché par une
solution numérique, il est possible que seul un niveau de surveillance
ne soit requis [9]. Dans une autre application, une solution numérique
pourra complètement automatiser une tâche.
|