3.2 Les erreurs statique et dynamique
3.2.1 Les erreurs de positionnement d'un manipulateur [55, 65]
:
Le positionnement réel d'un manipulateur, que ce soit
en statique ou en dynamique (poursuit des trajectoires) s'écarte
inévitablement et pour différentes causes, de sa position
désirée. De même, un manipulateur ne se positionne jamais
au même endroit lorsque la même trajectoire est
répétée plusieurs fois ».
Ces erreurs de positionnement sont d'origines diverses, peuvent
être classées en quatre catégories principales :
- Erreurs de quantification et de calcul.
- Erreurs cinématique de type aléatoire
dominant.
- Erreurs d'étalonnage et d'identification.
- Erreurs cinématique de type systématique
dominant.
Les erreurs de quantification et de calcul :
sont liées à :
- L'arrondi dans les calculs effectués par le
calculateur.
- La quantification des codeurs incrémentaux ou absolus
utilisés pour la détermination des coordonnées
articulaires.
- La performance du calcul numérique et des algorithmes
employés.
- La troncature des valeurs numériques dans les calculs
trigonométriques
Les erreurs cinématique de type aléatoire
dominant:
Chacune des articulations d'un manipulateur à
motorisation électrique peut être déplacée à
l'intérieur d'une petite zone, sans entraîner de signale d'erreur
à l'intérieur du système d'asservissement. Cette zone
morte est due aux défauts géométriques non
systématiques des organes mécaniques (les jeux mécaniques)
à la résolution des capteurs et aux performances des
asservissements (non linéarités dues aux frottements
mécaniques par exemple) [10, 65].
Les erreurs cinématiques de types systématique
dominante sont liées à :
- La déformation des segments sous l'effet des charges
statiques et dynamiques.
- La déformation des articulations sous l'effet des
charges statiques et dynamique. - La dilatation des pièces
mécaniques de la structure sous l'effet de la température.
3.2.2 Identification des paramètres d'un
manipulation :
L'identification consiste à déterminer, suite
à une série de mesures et à l'aide des méthodes de
masse du manipulateur [55,66].
Les erreurs de positionnement statique d'un manipulateur sont de
deux natures : Géométrique et non géométrique.
Les erreurs géométriques : Elles regroupent les
imprécisions de fabrication dons les corps et les liaisons et les
erreurs d'initialisations des offsets codeurs (les valeurs des offsets codeurs
correspondants à la configuration initiale géométrique
dans laquelle les variables articulaires sont nulles).
Les erreurs non géométriques : Elles regroupent
les déformations, les jeux dans les chaînes cinématiques,
les erreurs liées à la résolution des capteurs et aux
performances des asservissements. Elles ne sont pas accessibles à la
calibration géométrique.
La procédure d'identification géométrique
distingue trois niveaux de complexité :
Niveaux 1 : Ou « calibration des
articulations », l'objectif est d'établir la relation la plus
exacte entre le signal produit par les capteurs de position et les
déplacements articulaires. Ceci, implique généralement la
calibration de la cinématique des organes d'entraînement
(réducteurs, courroies, .etc.), les mécanismes des valeurs des
offsets codeurs.
Niveaux 2 : Ou « calibration
géométrique globale » dans ce niveau on doit identifier tous
les paramètres géométriques de description du
manipulateur. L'objectif de ce niveau est de déterminer le modèle
géométrique de base, qui lie les coordonnées
opérationnelles aux coordonnées articulaires (ou valeurs de
commande des actionneurs).
Niveaux 3 : Ou « calibration non
géométrique », il porte sur les possibilités de
compenser les erreurs d'ordre non géométriques à savoir
les déformations des articulations et des segments et des
frottements.
Pour utiliser le modèle dynamique, il faut
connaître les valeurs numériques des paramètres de masse
(masse, centre de masse, et matrice d'inertie) relatifs aux différents
corps et qui interviennent dans le modèle dynamique. Plusieurs
techniques peuvent être envisagées pour estimer ces
paramètres : Soit par calcul au moment de la conception, surtout si on
utilise un logiciel de C.A.O. performant, soit par mesure corps par corps avant
le montage ou par identification.
La technique d'identification des paramètres, consiste
à exploiter le caractère linéaire des actions dynamiques
relativement à ces paramètres pour les identifier, en utilisant
la méthode d'optimisation des moindres carrée[56] .
La précision d'un manipulateur est
généralement définie en terme de précision statique
(les caractéristiques de pose) et de précision dynamique (les
caractéristiques de trajectoire), ces deux caractéristiques,
quantifient la différence entre la situation désirée et
celle réellement atteinte [10, 65, 67].
Pour les manipulateurs utilisés dans les tâches
d'assemblages, d'insertion de composants, de soudage par point..., les
caractéristiques de composantes sont les caractéristiques de
pose. Ces caractéristiques sont définies par trois termes:
- Exactitude statique.
- Répétitivité statique.
- Temps de stabilité et dépassement statique.
Selon la définition ISO, l'exactitude statique est
représentée par l'écart entre une pose commandée
(Pc) et la moyenne des poses réellement atteintes (figures
3.1) , lorsqu'on demande au manipulateur de se positionner plusieurs fois en
Pc en suivant toujours la même trajectoire (exactitude
statique unidirectionnelle) soit Pc le point de la position
commandée de coordonnées Xc , Yc ,
Zc dans le référentiel de bas {Ro}; Pi une
des positions réellement atteintes (i= 1, k) , Pc = [
Xc , Yc , Zj
et Pi = [Xi , Yi , Zi]T
Pi
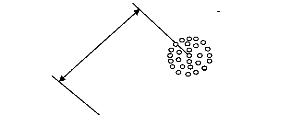
Les positions atteintes
Pc
La position programmées
Figure 3.1: L'exactitude de positionnement statique d'un
manipulateur [55].
L'exactitude locale de position Es est la distance
entre le point Pc et le point Pg barycentre de tous les
points atteints Pi donc:
E s ( x
=
g xc)2 ( y g y c )
2 ( z g z c )2
- + - + -

(3.19)
? yi
=1 ; i = = 1
i =
Y g = 1 ; k
Z g
k k
avec: Xg i
? xi
? zi
i k
Pour les rotations, on peut définir de la même
manière la variation entre la moyenne des positions angulaires atteintes
et la valeur commandée.
Par définition la répétitivité
statique unidirectionnelle est la distance maximale entre le point moyen
Pg et les points réellement atteints Pi , i= 1 .k (Figure
3.2)
Pg
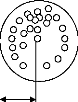
Pi
Les positions atteintes. Rs
Figure 3.2: La répétitivité de
positionnent statique d'un manipulateur [55].

R Max 1 x x y y z z
= = - + - + -
( ) 2 ( ) 2 ( )2 .. (3.20)
s i k k i k i k i
La norme (NF-E 61-103) définit également une
répétitivité statique à partir de la moyenne de
distances entre Pg et les points atteints Pi.
Si les trajectoires pour atteindre la position
désirée Pc sont différentes (on partira de
différentes positions vers la même destination). L'exactitude et
la répétitivité vont avoir des valeurs différentes
appelées exactitudes et répétitivité
multidirectionnelles.
Dans le cas où la position commandée serait
définie par apprentissage, la répétitivité est la
même, par contre l'exactitude est très différente, pour les
manipulateurs très précis la répétitivité
peut être de l'ordre du centième de mm, alors que l'exactitude de
position programmée peut être de plusieurs mm.
Remarque: Au terme répétitivité on
associe souvent la notion de réversibilité qui caractérise
la précision statique quant le point est atteint selon plusieurs
directions ; elle est plus mauvaise que la
répétitivité.
Il est bien intéressant de connaître le
comportement du robot lorsqu'il approche une pose commandée. Suivant le
réglage des asservissements des actionneurs et le niveau de
déformations des segments, le manipulateur peut osciller,
dépasser la situation commandée ou au contraire s'en approcher
sans oscillation, ce comportement se traduit par deux caractéristiques :
Dépassement et temps de stabilisation ces caractéristiques
peuvent être utiles pour régler une temporisation du manipulateur
avant d'effectuer une tâche ; la
connaissance du dépassement permet de s'assurer que
l'espace dégagé autour du point d'arrêt est suffisant pour
éviter les collisions de l'outil avec l'environnement [65].
En robotique, de nombreuses tâches sont
réalisées en utilisant un mode de commande de type interpolation
linéaire ou circulaire afin de quantifier les défauts et les
écarts entre la trajectoire réellement parcourue et la
trajectoire commandée, les caractéristiques essentielles pour ces
applications sont définies par les notions d'exactitudes et de
répétitivité de trajectoire.
Elle caractérise l'aptitude d'un manipulateur à
faire suivre à l'interface mécanique (l'effecteur) une
trajectoire désirée le fois dans la même direction et le
fois dans la direction opposée [10].
L'exactitude de trajectoire est définie par la distance
maximale entre la ligne moyenne des trajectoires réellement atteintes et
la ligne programmée (Figure 3.3), mesurée dans un plan orthogonal
à la trajectoire.
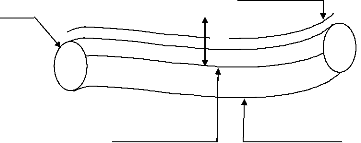
Et
R+
La ligne moyenne des trajectoires effectuées
Enveloppe des trajectoires effectuées
Trajectoire programmée
Figure 3.3: Exactitude de trajectoire [55]
L'exactitude pour des positions ou des trajectoires
programmées dépend surtout ds erreurs
d'étalonnage et des erreurs dues aux déformations de la
structures mécanique du manipulateur [10, 65, 70].
La répétitivité de trajectoire (ou
dynamique) est la distance moyenne (ligne des barycentres des trajectoires
effectuées) et une trajectoire effectuée; sera donc le rayon du
tore qui contiendrait toutes les trajectoires effectuées (Figure
3.3).
Les erreurs de répétitivité sont dues aux
défauts géométriques non systématiques des organes
mécaniques, à la résolution des codeurs de positions et
aux performances des asservissements (non linéarités dues aux
frottements mécaniques par exemple)
[10, 65] avec le développement de
l'électronique, de l'informatique et des moyens de fabrication (machine
à commande numérique, CFAO) la précision
géométrique en terme de répétitivité tend
à devenir largement suffisant pour la majorité des applications
industrielles.
Les applications industrielles de la robotique font appel
à des modes d'emploi principaux des manipulateurs:
De point d'arrêt acquis par apprentissage d'une suite
discrète de configuration articulaires.
- De trajectoires acquises par l'enregistrement
échantillonné d'une suite continue de configurations articulaires
correspondants aux mouvements que doit reproduire le manipulateur.
Les points d'arrêt sont seuls fonctionnels (travail en
cours mouvement).
Dans ces quatre types d'emploi, le problème de
précision prend des dimensions tout à fait différentes:
- Il peut dépendre de la répétitivité
de la réversibilité, de l'exactitude statique ou dynamique
(§ 3.3) ou de l'un de ces critères seulement.
Les déformations de la structure mécanique
peuvent être tout à fait transparentes à l'utilisateur
comme elles peuvent s'imposer comme un aspect du comportement dont la
modélisation et la prise en charge est vital pour l'application.
|