1.4. Diagramme Pareto :
Le diagramme de Pareto permet de mettre en évidence les
causes les plus importantes sur le nombre total d'effets et ainsi de prendre
des mesures ciblées pour améliorer une situation. Il nous servira
à classer les causes des gaspillages par ordre de gravité, ceci
imposera des priorités particulières afin de les
résoudre.
Méthode de construction du diagramme Pareto
:
1. Enumérer les différentes causes ou
problèmes
2. Quantifier l'importance de chacun
3. Déterminer le pourcentage de chacun par rapport au
total
4. Classer les pourcentages de chacun par valeurs
décroissantes
5. Déterminer une échelle adaptée pour
tracer le graphique
6. Choisir le « histogramme » comme type de graphique,
le plus grand à gauche
7. Ajouter la courbe de pourcentage cumulé sur le
même graphique
Jawaher ben Ameur
Page 27
Suite aux observations faites durant le premier mois du stage
; nous avons cité les différents problèmes
remarqués puis nous avons opté à la méthode de vote
pour déterminer l'ordre d'importance des causes de gaspillage. Pour le
faire, nous avons demandé au responsable de production de nous donner un
poids entre 1 et 10 à chaque cause, la cause qui fait la plus de
gaspillage aura le poids le plus haut.
|
Tableau 3 : Données collectées sur les
causes de gaspillage
|
|
Nr
|
Causes
|
5M
|
Poids
|
1
|
Pas très efficacement nettoyé
|
Milieu
|
8
|
2
|
Absence de maintenance préventive
|
Méthode
|
8
|
3
|
Recherche d'outillage
|
Main d'oeuvre
|
7
|
4
|
Arrêt machine (coupure du courant)
|
Machine
|
7
|
5
|
Réglage des machines difficile
|
Machine
|
6
|
6
|
5S non appliqué
|
Méthode
|
6
|
7
|
Poste de travail non agronomique
|
Méthode
|
6
|
8
|
Erreur d'inattention
|
Main d'oeuvre
|
6
|
9
|
Beaucoup des mouvements inutiles
|
Main d'oeuvre
|
6
|
10
|
Temps perdu à cause du triage des blocs
|
Matière
|
5
|
11
|
Temps d'attente élevé
|
Méthode
|
5
|
12
|
Stock en cours élevé
|
Matière
|
5
|
13
|
Mauvaise organisation
|
Méthode
|
5
|
14
|
L'absentéisme
|
Main d'oeuvre
|
5
|
TOTAL
|
|
|
86
|
Selon la méthode décrite ci-dessus nous avons
groupé les causes de gaspillage dans des catégories pour
faciliter leur traitement comme dans le tableau suivant
Jawaher ben Ameur
Page 28
Tableau 4: classification des
causes de gaspillage par catégorie
Nr
|
Causes
|
Poids
|
% Poids
|
% cumulé
|
1
|
Pas très efficacement nettoyé+5S non
appliqué
|
15
|
17%
|
17%
|
2
|
Absence de maintenance préventive +Réglage des
machines difficile
|
14
|
16%
|
33%
|
3
|
Recherche d'outillage+ Poste de travail non
équilibrés
|
13
|
15%
|
48%
|
4
|
Beaucoup des mouvements inutiles +Temps d'attente
élevé
|
11
|
13%
|
61%
|
5
|
Arrêt machine (coupure du courant)
|
7
|
8%
|
69%
|
6
|
Erreur d'inattention
|
6
|
7%
|
76%
|
7
|
Temps perdu à cause du triage des
blocs
|
5
|
6%
|
82%
|
8
|
Stock en cours élevé
|
5
|
6%
|
88%
|
9
|
Mauvaise organisation
|
5
|
6%
|
94%
|
10
|
L'absentéisme
|
5
|
6%
|
100%
|
TOTAL
|
86
|
100%
|
|
A partir du tableau précédent, il nous est devenu
possible de représenter le diagramme de Pareto sur Microsoft Excel tel
que le montre la figure suivante :
Jawaher ben Ameur
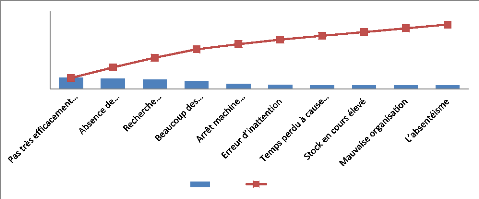
120%
100%
40%
80%
60%
20%
0%
17% 16% 15% 13% 8% 7% 6% 6% 6% 6%
Série1 Série2
Figure 10 : Diagramme de
Pareto
Interprétation :
Selon le principe Pareto seule 20% des causes
représentent 80% du gaspillage, nous devons donc dans notre cas agir en
premier lieu sur les causes majeurs pour garantir une amélioration
rapide et remarquable.
Nous devons déployer en priorité des actions
correctives pour résoudre les 4 causes principales.
|