Introduction
2
Introduction
Introduction
The thin layer technology has developed with extreme rapidity
in the last two decades whether in terms of implementation technology or
industrial applications.
In mechanical industry, the objectives of thin films are
mainly to improve the corrosion or wear resistance, to reduce the coefficient
of friction, to modify the surfaces microstructure to improve their ability to
retain lubricants and to optimize the lubrication of the rubbing surfaces and
the improvement of the aesthetic qualities of the products.
In internal combustion engines, the current trend is to save
energy, that is to say, the reduction of fuel consumption for equal or higher
power levels. To do so it is necessary to reduce friction losses between
surfaces in contact and increase their durability.
Several studies have shown that friction losses represent the
major part of the energy consumption developed in an internal combustion engine
(15 to 20%). Piston skirt friction, segmentation and bearings constitute 66% of
total friction losses; Distribution (up to 20-25% at low rpm), crankshaft,
transmission and gearbox contributing to the rest. Beyond the aspects of
reducing friction and wear, reducing oil consumption and exhaust emissions
represent ambitious challenges.
In this work, we propose to apply a thin layer of Ti-W-N on
the piston skirt and the piston crown in order to increase the surface hardness
and its corrosion resistance and to reduce the coefficient of friction.
The present dissertation contains six chapters;
The first chapter gives a brief illustration of the role of
pistons technology, and the main degradations and problems observed in pistons.
In the second chapter we present the mechanical properties of aluminum alloys,
the alloys with which the pistons are generally manufactured. In the third
chapter we describe the different thin film deposition techniques, the
tribological properties of the Ti, W and N layers, and the main deposition
characterization techniques.
In chapter four we give the different experimental procedures
executed in CDTA center, starting with the research of the probable piston
grade used as substrates in our study, passing by the preparation of the
surfaces of the samples and the deposit installations, and arriving at the
characterization of the tribological properties of our Layer (by XRD, SEM,
Raman, nanoindentation, tribometer and corrosion tests).
3
Introduction
In chapter five, we give the experimental results obtained with
their interpretation.
The chapter six dedicated to a medialization of the thin layer,
using Solidworks software, and we make mechanical test on it, in order to a
better characterization of the layer.
4
Literature review
Literature review
Hardness of titanium base thin films
Hard coatings based on nitrides (TiN, CrN, AlTiN, etc.) or
carbonitrides (TiCN) for mechanical applications came on the market in the
mid-1980s. They are characterized by a high hardness (often higher than 20 GPa)
and by great chemical inertia.
The deposited TiN/ZrN coatings have a very high hardness (>
30 GPa), much higher than the individual hardnesses of TiN and ZrN. It is noted
that the hardness increases with the Zr content in the layers, which seems
logical because the hardness of the ZrN is higher than the hardness of the TiN
with the deposition installation and the conditions used. Another interesting
result is the increase in hardness with the decrease in the individual
thickness of the alternating layers.
TiAl(N,C,O) coatings exhibit a wear behavior considerably
superior to the traditional DLC coating.
Corrosion resistance
It is well known that PVD layers generally have a columnar
structure with numerous growth defects (porosities, grain boundaries,
structural defects, etc.); thus, they do not provide adequate protection of the
corrosion-sensitive substrates.
At present, the poor corrosion resistance offered by PVD
coatings requires, on sensitive substrates, the deposition of a relatively
thick electrochemically produced undercoat. The most commonly used solution is
chromium or galvanic nickel with thicknesses of the order of 5-20
ìm.
To further improve the corrosion resistance, a Pd-Ni deposit
is applied to the nickel before the final PVD deposition. This multi-layer
process provides much better corrosion resistance, in particular, since the
galvanic undercoat is much denser and does not have a columnar structure.
However, today, and due to environmental considerations in some countries,
there is an abandonment of galvanic coatings such as nickel, zinc, cadmium,
chromium, gold and many other metals and alloys, unfortunately impossible to
replace.
Other works describe the use of an ionic etching of Nb ions
carried out by cathodic arc on ferrous substrate before PVD deposition [CHA 04;
HOV 02, 05; REI07];
The TiAl(C,O) coatings represent an interesting improvement
compared to the traditional Ti(C,O), especially since there nanohardness is
close to 13 GPa. A SEM photograph shows a dense non-columnar and amorphous
microstructure of this type of coating. This amorphous microstructure is
particularly advantageous since it generally confers a higher resistance to
corrosion of the substrate by preventing the electrolytes from passing through
the coating by the intercolonial porosities.
5
Literature review
Thin films with oblique incidence and GLAD
technical
The properties of thin layers depend primarily on their
microstructure or their nanostructure. From the first experimental studies due
to MOVCHAN and DEMICHISHIN [MOV69] and also to THORNTON [THO 74], to the recent
structural models developed by simulation [ABE 97; MAL 96; TRO 03; WEI00], the
majority of this work was mainly focused on the operating conditions
influencing the morphology and structure of films deposited under normal
incidence. Very few have been dedicated to thin films prepared under oblique
incidence [DON 96; DIT 91; HOD 98; MBI 95; TAI 92].
All this work on the layers prepared under oblique incidence
converges towards the same observation: an enlargement of the spectrum of the
physicochemical properties of the deposited materials including their stress
state, their density, their optical, electrical and magnetic anisotropy,
etc.
The work of the teams of Brett and Robbie for the production
of thin films under oblique incidence and on fixed or mobile substrate, allows
the birth of a new technic: the GLAD technical: GLancing
Angle Deposition.
The property of the GLAD technique in generating columnar
architectures of various shapes at nanometric scales leads inevitably to
questioning the mechanical behavior of these nanostructured films. Indeed, the
structural shapes of some of these architectures (example: zigzags, spirals,
etc.) give extended mechanical characteristics with respect to a conventional
columnar structure.
Using the nanoindentation tests, the authors SETO et al [SET
01] clearly show that the helically-structured films have an elastic
deformability of a higher order of magnitude compared with conventional
columnar films.
Other studies on the elastic properties of GLAD films have
also been carried out by LINTYMER and al [LIN 03a, 04, 05] on inclined and
zigzag chrome layers. In particular, it has been demonstrated that the Young's
modulus of zigzag films can be changed from single to double playing only on
the number and size of the zigzags.
Economic considerations
It is customary to say that nanomaterials are expensive, but
it must be shown that nanomaterials are additives to be used in small
quantities, the cost per function can become minimal. For example, on a square
meter, a 10 ìm coating will weigh about ten grams, adding 1%
nanomaterial will lead to 100 mg of material, even with expensive material
(1000 € / Kg for example), the cost of the coating is 1 € / Kg, which
is negligible compared to the technical, technological and functional
contribution of the layers thus realized.
Then it can be deduced that the use of nanomaterials in
surface coatings is a technological reality, which is transforming itself more
and more into economic reality.
Chapter 1
Overview on engine's piston
7
Chapter 1: Overview on engine's piston
1.1. Piston types
1.1.1. Pistons for four-stroke gasoline engines:
Modern gasoline engines employ lightweight designs with
symmetrical or asymmetrical skirt profiles and potentially different wall
thicknesses for the thrust and antithrust sides. These piston types are
characterized by low weight and particular flexibility in the central and lower
skirt areas.
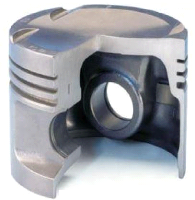
Fig.1.1: Autotermique piston
|