Partie 1 : Réalisation du capteur de gaz et
process

II.1 Introduction . 58
II.2 Généralité sur les méthodes de
dépôt de couches minces 58
II.2.1 les méthodes de dépôts physiques
58
II.2.1.1 Dépôt par évaporation 59
II.2.1.2 Evaporation par effet Joule 59
II.2.1.3 Evaporation par bombardement électronique 59
II.2.1.4 Evaporation par un faisceau Laser 60
II.2.1.5 Dépôt par pulvérisation cathodique
.. 61
II.2.1.5.1 Pulvérisation DC (direct curent) 61
II.2.1.5.2 Pulvérisation RF (radio
fréquence) 62
II.2.1.5.3 Pulvérisation à magnétron 62
II.2.2 les méthodes de dépôt chimique 63
II.2.2.1 Dépôt en phase vapeur chimique (CVD) ..
63
II.3 Aspect physique de l'oxydation thermique du silicium ..
65
II.4 Procédure expérimentale . 69
II.4.1 Préparation des plaquettes de silicium
polycristallin . 69
II.4.1.1 Nettoyage .. 70
II.4.1.2 oxydation thermique des plaquettes de Si
(polycristallin) 70
II.4.1.3 découpage des plaquettes de Si (polycristallin)
71
II.4.2 Réalisation du capteur de gaz 71
II.4.2.1 Description du montage expérimentale 71
II.4.2.2 Conception du four intégré 72
II.4.2.2.1 Dépôt de couche mince de Nickel .. 72
II.4.2.2.2 Dépôt de couche mince de Tungstène
73
II.4.2.2.3 Dépôt de couche mince diélectrique
73
II.4.2.3 Réalisation de couches minces d'oxyde de zinc non
dopée et dopée 74
II.4.2.3.1 Dépôt de ZnO non dopé et
dopé 74

Partie 2 : caractérisation du capteur de gaz

II.5 Introduction .. 77
II.6 caractérisation structurelle et morphologique ..
77
II.6.1 Diffraction des rayons X 77
II.6.2 Caractérisation morphologique des
échantillons par microscope électronique à
balayage (MEB) . 78
II.7 caractérisation électrique . 79
II.7.1 Méthode de la pointe chaude pour la
détermination du type de conductivité dans
un semiconducteur .. 79
II.7.2 Mesure de l'épaisseur des couches minces
métalliques par la méthode des quatre pointes . 81 II.8 Banc
d'essai et de mesure de la réponse du capteur au gaz
d'éthanol 84
II.8.1 Gaz utilisé .. 84
II.8.2 Concentration du gaz débité dans le
dispositif de détection 84
II.8.3 Banc de caractérisation électrique du
capteur de gaz 86

Chapitre III Résultats expérimentaux et
discussion

89
89
89
III.1 Introduction
III.2 Dimension du capteur de gaz obtenu
III.2.1 Mesures d'épaisseur et de résistance des
couches minces métalliques III.2.2 mesure d'épaisseur des
couches minces d'oxyde de silicium formé par
90
90 92 94 97
oxydation thermique
III.2.3 Mesure d'épaisseur des couches minces d'oxyde de
zinc non dopé et dopé
III.3 Mesure thermique effectué sur le mini four du
capteur .
III.3.1 Relation résistance épaisseur de couches
.
III.4 Type de conductivité dans l'oxyde zinc non
dopé et dopé .
97
III.5 Résultat des caractérisations structurelles
et morphologiques des oxydes de zinc (ZnO) et oxyde de silicium (SiO2)
. III.5.1 Diagramme de diffraction de rayon X des couches minces de ZnO non
dopé et
97 99
99
100 103 103 103 103 118
dopé
III.5.1.1 Taille des grains
III.5.2 Morphologie des surfaces obtenues sur le SiO2
III.5.3 Morphologie de surfaces obtenues sur le ZnO non
dopé et dopé
III.6 Etude de la réponse du capteur envers le gaz
d'éthanol .
III.6.1 système de barbotage
III.6.2 Etape de la détection .
III.6.3 Protocole de la manipulation
III.6.3.1 Mesure de sensibilité des capteurs CG1, CG2, CG3
et CG4 ..

127 131

Annexe
Références bibliographiques

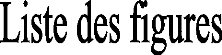
Figure I.1. Dispositif Direct .. 20
Figure I.2. Dispositif complexe 20
Figure I.3. Schéma d'un capteur de gaz de
type GASFET ... 21
Figure I.4. Capteur Electrochimique à
électrode .. 22
Figure I.5. Structure d'un capteur à
ondes acoustiques de surface 23
Figure I.6. Capteur de gaz à fibre
optique 24
Figure I.7. Structure d'un microcapteur MOX
développé par la société Microsens. ..
26 Figure I.8. Diagramme d'énergie d'un
semiconducteur type n et d'un adsorbat
avant la chimisorption 29
Figure I.9. Schéma du champ
électrique à l'intérieur de la Z.C.E 30
Figure I.10. Schéma de l'énergie
potentiel à l'intérieur de la Z.C.E 32
Figure I.11. Diagramme de bande
énergétique pour la chimisorption d'un
semiconducteur type (n) . 32
Figure I.12. Schéma du champ
électrique à l'intérieur de la Z.C.E .. 34
Figure I.13. Schéma de l'énergie
potentiel à l'intérieur de la Z.C.E 35 Figure I.14.
Diagramme de bande énergétique pour la chimisorption
d'un
semiconducteur type (p) . 35
Figure I.15. Représentation d'une
schématique de joint de grain 38
Figure I.16. Différentes structures de
l'oxyde de zinc .. 42 Figure I.17. Structure de bande de
ZnO en utilisant la méthode du pseudo
potentiel .. 43
Figure I.18. Phénomène de la non
stoechiométrie de ZnO 45
Figure I.19. Structure cristalline du nickel et
tungstène 48
Figure I.20. La sphere de Fermi qui englobe les
états occupés dans l'espace k dans l'état
fondamentale du gaz électronique 50 Figure I.21.
L'influence d'une force constante F agissant pendant
l'intervalle de
temps t 50
Figure I.22. Simulation de l'évolution du
temps de chauffage du micro four conçue
en cuivre par rapport à des puissances d'alimentations
différentes . 52 Figure I.23. Diffusion du flux de
chaleur à travers le substrat de silicium et les
différentes couches de SiO2 55 Figure I.24.
Représentation d'une simulation de la diffusion de la chaleur
du micro
four vers les deux régions isolatrice en SiO2 55
Figure II.1. Méthodes
générales de dépôt de couches minces sous vide ..
58
Figure II.2. Schéma de principe d'un
système de chauffage par un faisceau
d'électrons 60
Figure II.3. Schéma conventionnelle de
l'ablation Laser 60
Figure II.4. Schéma de principe de la
pulvérisation cathodique 61
Figure II.5. Système de
pulvérisation DC 62
Figure II.6. Schéma de principe de
dépôt en phase vapeur chimique (CVD) dans un
réacteur à parois chaudes 64
Figure II.7. Représentation de
l'épaisseur de SiO2 et de Si consommé .. 65
Figure II.8. Représentation de
l'oxydation thermique du Si 67
Figure II.9. Schéma de principe du four
servant à l'oxydation de Si . 70
Figure II.10. Les dimensions des substrats de Si
utilisé . 71
Figure II.11. Représentation de la
configuration finale du four . 74
Figure II.12. Configuration finale de notre
capteur de gaz, intégrant à la fois les
éléments chauffants et sensibles aux gaz . 75
Figure II.13. Géométrie de
diffraction (èhkl -2èhkl) et la loi de Bragg . 77
Figure II.14. Pouvoir thermoélectrique en
fonction de la température dans le
silicium n et p 80
Figure II.15. Schéma de principe de
technique de la pointe chaude 81
Figure II.16. Configuration des quatre pointes
alignées 82
Figure II.17. Schéma de principe du
barbotage suivi au LMESM pour contrôlé la variation du
Débit d'éthanol .. 85
Figure II.18. Schéma de principe du
dispositif pour le test du capteur 87 Figure III.1.
Géométrie du capteur de gaz réalisé en
technologie des couches
minces .. 89 Figure III.2. Image MEB de
l'épaisseur de la couche de SiO2 coté face du substrat
de Si, im x 300 .. 90
Figure III.3. Image MEB de l'épaisseur de
la couche de ZnO avec grossissement
de 10k 91 Figure III.4. Image MEB de
l'épaisseur de la couche de ZnO : 3% Al avec
grossissement de 10k 91 Figure III.5. Image
MEB de l'épaisseur de la couche de ZnO : 1% Al avec
grossissement de 10k 91 Figure III.6. Image
MEB de l'épaisseur de la couche de ZnO : 1% Cu avec
grossissement de 10k 91 Figure III.7.
Évolution de la température d'équilibre Tf de la
plaque chauffante en
fonction de la puissance fournie 92 Figure III.8.
Représente la variation de la résistance des couches
minces métallique
en fonction du temps de dépôt . 95 Figure
III.9. Représente le caractère ohmique des plaques
chauffantes des séries S1
et S2 .. 96 Figure III.10. Spectres de
diffraction de rayon X des couches minces de ZnO non
dopé et dopé . 98 Figure III.11.
Image MEB d'une couche de SiO2 formé par pulvérisation
rf, avec
un grossissement de 4k . 100 Figure III.12.
Image MEB d'une couche de SiO2 formé par oxydation thermique
de
Si polycristallin, avec un grossissement de 10k
100 Figure III.13. Image MEB d'une couche de ZnO
dopé Al 1%, avec un
grossissement de 10k 101 Figure III.14.
Image MEB d'une couche de ZnO dopé Al 3%, avec un
grossissement de 10k 101 Figure III.15.
Image MEB d'une couche de ZnO dopé Cu 1%, avec un
grossissement de : 4k (a) et 10k (b) . 101 Figure
III.16. Image MEB d'une couche de ZnO non dopé, avec un
grossissement
de : 4k (a) et 10k (b) . 101
Figure III.17. Ensemble ZnO non dopé SiO2
et Si IM x 340 102 Figure III.18. Représente la
variation de la résistance de trois capteurs (CG1) en
fonction de la température pour une concentration C1= 337
ppm 104 Figure III.19. Représente la variation de
la résistance de capteurs CG1 en fonction
de la température (pour une concentration C1 = 337 ppm) :
(a) échantillons soumis
à un recuit à 500 °C avant exposition au gaz
d'éthanol, (b) échantillon testé directement après
dépôt de la couche sensible . 105 Figure III.20.
Représente la variation de la résistance de capteurs CG1
en fonction
de la température (pour une concentration d'éthanol
C1 = 337 ppm) . 106 Figure III.21. Représente la
variation de la résistance de capteurs CG1 en fonction
de la température (pour une concentration d'éthanol
= 194 ppm) . 107 Figure III.22. Représente la
variation de la résistance de capteurs CG2 en fonction
de la température (pour une concentration d'éthanol
C1 = 337 ppm) . 109 Figure III.23. Représente la
variation de la résistance de capteurs CG2 en fonction
de la température (pour une concentration d'éthanol
= 194 ppm) . 110 Figure III.24. Représente la
variation de la résistance de capteurs CG3 en fonction
de la température (pour une concentration d'éthanol
C1 = 337 ppm) . 112 Figure III.25. Représente la
variation de la résistance de capteurs CG3 en fonction
de la température (pour une concentration d'éthanol
= 194 ppm) . 113 Figure III.26. Représente la
variation de la résistance de capteurs CG4 en fonction
de la température (pour une concentration d'éthanol
C1 = 337 ppm) . 115 Figure III.27. Représente la
variation de la résistance de capteurs CG4 en fonction
de la température (pour une concentration d'éthanol
= 194 ppm) . 116 Figure III.28. Evolution de la
Sensibilité de deux capteurs CG1 : (a) élément sensible
(ZnO non dopé) soumis à un recuit à 500 °C avant
exposition au gaz d'éthanol, (b) élément sensible (ZnO non
dopé) testé directement après dépôt de la
couche sensible, pour une concentration d'éthanol : C1 =
337 ppm 118 Figure III.29. Evolution de la
Sensibilité d'un capteur CG1 durant trois tests, pour
une concentration d'éthanol : (a) C1 = 337 ppm, (b) = 194
ppm 119 Figure III.30. Evolution de la Sensibilité
d'un capteur CG2 durant trois tests, pour
une concentration d'éthanol : (a) C1 = 337 ppm, (b) = 194
ppm 120 Figure III.31. Evolution de la Sensibilité
d'un capteur CG3 durant trois tests, pour
une concentration d'éthanol : (a) C1 = 337 ppm, (b) = 194
ppm 121 Figure III.32. Evolution de la Sensibilité
d'un capteur CG4 durant trois tests, pour
une concentration d'éthanol : (a) C1 = 337 ppm, (b) = 194
ppm 122
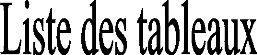
Tableau I.1. Classification des capteurs de gaz
selon leur principe de détection 20
Tableau I.2. Propriétés
générales de l'oxyde de zinc en couche mince .. 44
Tableau I.3. Propriétés
générales du Nickel et Tungstène .. 47
Tableau II.1. Propriété
générales des plaquettes de Si utilisés 69
Tableau II.2. Présentation de principales
caractéristiques et performances du
pulvérisateur cathodique radiofréquence RFS 200 ..
72
Tableau II.3. Paramètre de
dépôt de nickel 73
Tableau II.4. Paramètre de
dépôt de Tungstène . 73
Tableau II.5. Paramètre de
dépôt de SiO2 .. 74
Tableau II.6. Paramètre de
dépôt de ZnO pur et dopé 75
Tableau III.1. Mesure des épaisseurs des
couches minces métallique 89
Tableau III.2. Mesure des épaisseurs de
l'oxyde de silicium . 90
Tableau III.3. Mesure des épaisseurs de
l'oxyde de zinc 91
Tableau III.4. Les valeurs des puissances et
des températures de fonctionnement, sous tension et courant continu
concernant les mesures effectuées sur les
échantillons S1 et S2 93
Tableau III.5. Résultat des mesures de
conductivité .. 97
Tableau III.6. Représente la taille des
grains des films d'oxyde de zinc non dopé et dopé obtenus .
99 Tableau III.7. Représente la taille moyenne des
colonnes des films d'oxyde de zinc
non dopé et dopé obtenus . 102
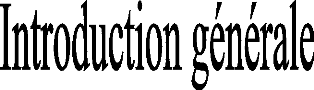
Le monde dans lequel nous vivons est en transformation
permanente et rapide, dominé par une biodiversité aux
phénomènes physiques prépondérants quant à
la qualité de notre environnement.
Ainsi, les avancées technologiques s'identifient par
des améliorations, des corrections et des ajouts de
procédés et moyens à l'effet de contrôler,
réguler et répondre au mieux à nos besoins quotidiens.
A l'heure actuelle ces transformations sont marquées
principalement par l'élaboration de capteurs qui ne cessent de se
développer, formant une interface entre le monde réel dans lequel
nous vivons et celui des systèmes modernes industriels et
environnementaux [1]. A telle enseigne qu'il nous est
dorénavant possible d'obtenir des informations en temps réel sur
des aspects physiques et chimiques de substance nocives ou
bénéfiques pour notre survie [2].
L'objectif fixer par nos travaux au sein du laboratoire de
microscopie électronique et sciences des matériaux est de
présenter l'état d'avancement de nos recherches dans le domaine
des dispositifs [3, 4, 5].
Pour cela nous avons focalisé notre travail sur le
développement d'une nouvelle méthodologie d'apports
énergétiques, pour la réalisation d'un capteur de gaz
à base de couches minces d'oxyde de zinc (ZnO) dopées (Al «
1% et 3% » et Cu « 1% ») et non dopées, avec un mini four
intégré (conçu avec une double couche de nickel plus
tungstène) sur un wafer de Si poly cristallin, afin de contrôler
et de réguler à plus au moins un demi degré Celsius
(0.5°C) de précision.
Notre mémoire s'articulera autour de trois chapitres. A
ce titre le chapitre un sera scindé en deux volets :
- le premier constituera en un rappel des capteurs de gaz,
ainsi que leurs principes de détections, dont ceux à base d'oxyde
métallique présentement il concernera l'oxyde de zinc (ZnO).
- Le second consacrera le principe de chauffage par effet joule
dans les couches minces métalliques, ainsi que les
phénomènes de transfert de chaleur dans les corps solides.
Le chapitre deux présentera les démarches
expérimentales entreprises pour la réalisation de notre capteur
de gaz, ainsi que les différentes méthodes de le
caractériser (électriquement, structurellement et
morphologiquement).
Enfin, dans le chapitre trois, nous exposerons l'ensemble des
résultats et performances obtenus, pour le mini four d'une part, et
d'autre part les analyses conséquentes à l'élément
sensible.
Références bibliographiques :
[1] J. FRADEN, Handbook of Modern Sensors
Physics, Designs, and Applications, 3rd Edition Springer, 2004.
[2] Pavel Ripka et Alois Tipek, Modern Sensors
Handbook, 1st edition ISTE, 2007.
[3] M. K Bendimerad, Réalisation d'un
capteur de gaz à base de couches mince d'oxyde de zinc avec un micro
four intégré, Mémoire d'ingéniorat,
Université d'U.S.T.O.M.B, 2007.
[4] Y. BAKHA, Adsorption des gaz sur des
couches d'oxyde de zinc préparées par la technique pyrolyse
spray, Mémoire de magister, Université d'U.S.T.O.M.B, 2007.
[5] D. Cherrad, Élaboration et Etude
technologique des couches minces T.C.O de type « n »et « p
» par micro pipetage et procédé rf, Application : à
la détection des polluants, radiations ultraviolettes, jonction «
pn >>, Mémoire de magister, Université d'U.S.T.O.M.B,
2008.
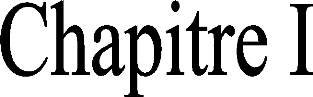

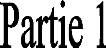
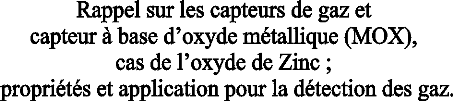
I.1 Introduction
Au titre de cette partie du chapitre (I), nous nous
étalerons sur un bref rappel des capteurs de gaz, déterminerons
les définitions et performances, pour entamer par la suite leur principe
de détection dans ceux à base d'oxyde métallique et dans
notre cas l'oxyde de zinc (ZnO).
|