II.3. Comportement des polymères vis avis de
l'usinage:
Le point de fusion et la conductibilité thermique des
plastiques, en général, sont des valeurs inférieures
à celles des métaux et il est donc nécessaire de limiter
au minimum la chaleur engendrée en diminuant la friction. Des outils
émoussés ou bien des tranchants qui raclent plutôt qu'ils
ne coupent provoquent un dégagement de chaleur excessif, qui risque de
générer des contraintes internes préjudiciables à
géométrie et à la fiabilité de la pièce
finie. Les arrêtes des outils doivent donc être toujours
parfaitement affûtées et la dépouille doit être
suffisante pour garantir que seul l'arête de coupe soit en contact avec
la pièce usinée. On obtient généralement les
meilleurs résultats en travaillant à très grandes vitesses
avec une faible avance et des outils bien affûtés et lisses. Pour
les pièces de faibles sections, une passe trop profonde est susceptible
de provoquer son fléchissement. L'utilisation d'une lunette est
conseillée pour les pièces assez longues, et pour les plastiques
ayant un point de fusion bas, la lunette sera équipée de galets
car des sabots risqueraient de porter la pièce en fusion. L'emploi d'un
fluide de refroidissement est indispensable pour la réalisation de ces
pièces.
Lors du tournage de pièces de précision, il faut
éviter soigneusement toute surchauffe de la pièce tournée,
faute de quoi on s'expose à réaliser une passe excessive due
à la dilatation thermique de l'ébauche. Les mesures des
pièces doivent toujours être effectuées à
température ambiante, car le coefficient de dilatation dans le cas des
plastiques est parfois jusqu'à 10 fois supérieure à celui
de l'acier [12]. Dans ces cas, on peut également travailler avec
refroidissement par fluide, quoi que, par ailleurs certains plastiques se
travaillent aussi bien sans refroidissement.
Parmi les caractéristiques des polymères qui ont
une influence sur les opérations d'usinage on peut citer [13] :
II.3.1 La dilatation et la conductivité
thermique : Les matières plastique non chargées ont
des coefficients de dilatation thermique généralement compris
entre 50 et 200 m/m.k. ce sont des matériaux isolants, la combinaison de
ces deux caractéristiques, fait que la chaleur engendrée par
l'opération d'usinage reste concentrée sur la zone usinée
et entraîne une déformation thermique importante, voire un risque
de dégradation thermique.
II.3.2 Le module d'élasticité et la
dureté : Les plastiques sont très souples par
rapport aux aciers (modules compris entre 1000 et 2000 Mpa) et beaucoup moins
durs ce qui impose, par exemple, des précautions de serrage
particulières pour ne pas déformer la pièce ni en marquer
la surface.
II.3.3 Les contraintes internes: Les
pièces plastiques contiennent souvent des contraintes internes
après moulage, dues, en particulier, au retrait de la matière
passant de l'état liquide à l'état solide. Il arrive
fréquemment que l'usinage modifie la répartition de ces
contraintes. Dans l'étude [14] il a été prouvé que
le tournage préserve la rigidité mais perd beaucoup sur
óf et óy. Des précautions doivent
par conséquent être prises pour qu'il n y ait pas d'accumulation
de contraintes susceptibles d'entraîner des fissurations. Un des
remèdes peut être de pratiquer un requit des pièces
après moulage. La vitesse de refroidissement est un
élément essentiel pour réduire les contraintes internes.
Plus la température de recuit est élevée, plus la baisse
de température doit être lente. Parfois, l'usinage est
réalisé après dégrossissage d'une ébauche.
Dans ce cas, l'ébauche est généralement sans contraintes
internes car celles-ci sont libérée lors du
dégrossissage.
II.3.4 L'usure des outils: Une grande partie
des plastiques non chargés ont un comportement autolubrifiant et ne
créent pas d'usure importante des outils. Par contre, Ceux qui
comportent des charges minérales (verre) ont tendance à accentuer
l'usure des outils traditionnels d'usinage par enlèvement de copeaux.
II.3.5 L'hygrométrie: Certains
polymères absorbent un taux important d'humidité (polyamide, par
exemple). Les phénomènes d'absorption ne sont pas
instantanés mais se produisent au bout de quelques minutes, voire de
quelques heures. Cela modifie les caractéristiques mécaniques et
dimensionnelles. Cette évolution entre l'instant où on usine le
polymère (échauffement donc séchage) et celui où on
l'utilise (ambiance humide éventuellement donc dimensions
différentes). Il faut donc tenir compte du comportement du
polymère en présence d'humidité, de la présence ou
non d'un liquide de refroidissement, de l'ambiance hygrométrique de
l'atelier, du fait que l'échauffement dû à l'usinage va
sécher le matériau en surface, etc....
II.3.6 L'électrostatique: Certains
plastiques développent des charges électrostatiques
superficielles importantes par frottement, qui attire les copeaux ou la poudre
issus de l'usinage.
II.4. Conditions d'usinage du
polyéthylène de haute densité :
Les matériaux d'outils peuvent être en
acier rapide qui sont les moins chers à l'achat. Ils ont une
durée de vis moins longue, surtout avec les matériaux
renforcés de fibre de verre. Les carbures, qui ont une plus grande
résistance à l'abrasion que les aciers rapides et ils ont un bon
rapport prix/usure. Pendant l'usinage, Parfois le refroidissement n'est pas
nécessaire. C'est le cas de certains usinages de matières
plastique à faible coefficient de frottement, par exemple
polyéthylène. La précaution essentielle consiste à
éviter toute déformation. Il faut penser aussi que l'effort
d'usinage est inférieur à celui nécessaire pour usiner une
pièce similaire en acier ; il n'est donc pas nécessaire de serrer
la pièce avec le même effort. Ce qui nous à pousser
d'utiliser des montages spéciaux ; pour l'alésage en à
pénétrer notre tube dans tube en acier, pour éviter toute
déformation, pendant l'usinage et surtout à faible
épaisseur, par contre pour le chariotage en à utiliser un mandrin
en bois. Les mesures des cotes doivent toujours être effectuées
après retour de la pièce à la température ambiante.
Une tolérance de 0.1 à 0.2% de la cote nominale est accessible
sans précautions spéciales.
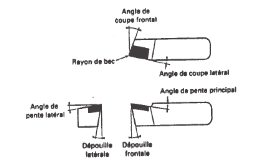
La Figure (9) définit différent angle d'un outil
de tour, les autres paramètres de coupes sont illustrés sur le
Tableau (III).
Figure 9 : Géométrie type d'un
outil de tournage [5].

Tableau III : Tournage du
polyéthylène [15].
II.5. Les efforts de la coupe :
Les efforts de coupe sont à l'origine des
déformations plastiques et donc des élévations de
température qui se produisent au cours de la coupe. Pour toutes autres
conditions de coupe égales, l'augmentation de la vitesse de coupe ne
s'accompagne pas d'une variation notable des efforts de coupe (10% de baisse
environ), alors que l'augmentation de la vitesse d'avance entraîne une
augmentation de la valeur de l'effort tangentiel (relation linéaire:
l'effort double environ quand la vitesse d'avance double).
II.5.1. Définition et intérêt de
leur mesure :
Le tournage longitudinal donne lieu à un effort de
coupe dont la décomposition dans trois directions
privilégiées peut servir de base à la définition
des efforts de coupe pour toutes les opérations d usinage [16].
Ø Fz : composante dans
le sens de la vitesse de coupe, appelée effort tangentiel ou effort
principal de coupe.
Ø Fx: composante dans le sens
de l avance, appelée effort d'avance ou effort axial en tournage, joue
un rôle fondamentale dans le processus de coupe.
Ø Fy : composante dans
le sens perpendiculaire aux deux autres, appelée effort de refoulement
ou effort radial, n'a qu'une importance secondaire est disparaît dans le
cas de coupe orthogonale pure.
Fz
Fy
Fx
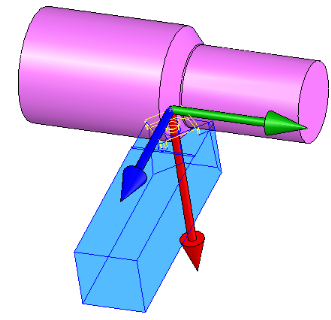
Figure 10 : Les composantes de l'effort de
coupe.
La connaissance des efforts de coupe est à la base de
puissance nécessaire à la coupe. Quand on veut connaître le
rendement mécanique d une machine outil, on a besoin de savoir quelle
est la puissance prise à l outil, et donc d avoir des renseignements sur
les efforts de coupe.
La valeur des efforts de coupe sert aussi à dimensionne
les organes de machine et à prévoir les déformations des
pièces. Elle intervient dans la précision d'usinage, dans les
conditions d'apparition des vibrations, au broutage, et indirectement dans la
formation de l'état de surface.
Enfin, les efforts de coupe, étant en relation avec les
propriétés mécaniques du métal, dans le processus
de formation du copeau.
Les formules empiriques les plus utilisées pour le
calcul pratique sont les suivantes [17]:
Fz = C1 PX
1. ay1. Vn 1. KV
(3)
Fy = C2
PX 2. ay 2 . Vn 2. KP
(4)
Fx = C3 PX
3. ay 3. Vn 3. Ka.
(5)
Avec:
Les coefficients C1, C2,
C3 sont des constantes qui dépendent des
propriétés mécaniques du métal à usiner et
conditions de son usinage.
Les coefficients KV, KP, Ka
se sont les coefficients correctif relatif aux conditions d'usinage
concrète.
Les coefficients X1,2,3 , y1,2,3
, n1,2,3 se sont des exposants qui caractérise le
degré d'influence des paramètres p,a , v sur les forces de coupes
Fz , Fx , Fy.
II.5.2. Influence des différents facteurs sur
les composantes de l'effort de coupe :
- Les propriétés mécaniques du
matériau à usiner :
La valeur de réaction Fz , Fx , Fy est
proportionnelle à la charge rupture à la traction Rt et à
la dureté HB du métal à usiner.
- Influence de la profondeur de passe et l'avance:
Avec l'augmentation des ces deux facteur, la section droit du
copeau s'accroît, de même que le volume du métal
déformé, il en résulte que le métal résiste
plus à la formation du coupeau et la valeur des composantes Fz ,
Fx et Fy nécessaire pour assurer la coupe est plus importante. En
chariotage, la profondeur de passe intervient d'une manière plus
accentuée sur les efforts de coupe que l'avance.
- Influence de la vitesse de
coupe : On peut distinguer 03 zones (Figure 11) ;
Ø Zone A : diminution de F avec
les vitesses bases due à une diminution de frottement copeau - outil.
Ø Zone B : l'apparition de
l'arrête rapportée provoque une augmentation des frottements et
par suite de l'effort tangentiel de coupe.
Ø Zone C : La VC
augmente arête rapportée diminue. L'effort tangentiel de
coupe F diminue et se stabilise vers 200m/min.
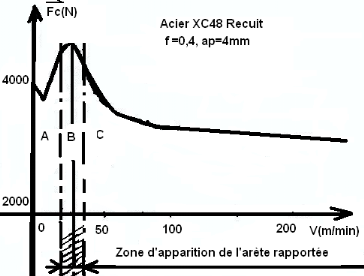
Figure 11 : Influence de la vitesse
de coupe sur l'effort de coupe.
- Influence de l'angle d'attaque (
) :
Lorsque () est négatif l'effort
tangentiel de coupe est important au fur et à mesure que augmente,
l'effort de coupe diminue et prend une valeur stable à partir de
30° (Figure 12) : Petit est grand la résistance
imposée à l'outil attaquant la pièce usiner est
importante.
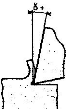
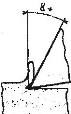
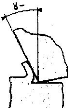
Figure 12 : Influence del'angle
d'attaque.
- Influence de l'angle de direction principale
(÷) :
Avec une avance inchangée, le copeau devient plus fin
au fur et à mesure que l'angle ÷r diminue. Ceci conduit
à une augmentation de l'effort de coupe, la réduction de l'angle
de position est limitée par les dégradations croissantes de la
stabilité (forte augmentation des efforts d'avances et de
pénétration tendance au broutage) figure 13.
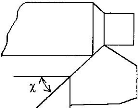
Figure 13 : Influence de l'angle de
direction principale.
Influence de matériau de
coupe :
Les matériaux de coupe revêtus, en particulier
ceux avec des revêtements TiN ou Ti (C,N), accusent un frottement moindre
et des efforts de coupe plus faible que les matériaux de coupe non
revêtus. Les faces d'attaque superfinies (rectifiées,
rodées, polies) et dotées d'une arête de coupe dure et
tranchante, réduisent les efforts de coupe (Figure 14).
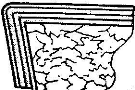
Figure 14 : Matériau de coupe.
III.1. Introduction:
En Algérie, le réseau de distribution de gaz
naturel compte plus de 22000Km construits en polyéthylène. Le
choix de ce dernier (en fait des copolymères d'éthylène
à faible proportion de butène ou d'hexène voir
d'octène) pour la fabrication des tubes de distribution du gaz
découle des nombreux avantages technico-économiques
procurés par ce matériau. Le PE est un matériau
léger, ce qui facilite les opérations de manutention et de mise
en oeuvre sur le terrain. Il possède une bonne résistance
à la corrosion, quelles que soient les conditions au sol, ce qui permet
d'éviter les surcoûts dus à l'application d'une protection
passive ou active. De plus, les systèmes en PE supportent les effets des
mouvements du sol dus aux instabilités et aux grandes variations de
température. Du fait de leur bonne résistance à la
fissuration, les canalisations en PE présentent un degré de
fiabilité élevé dans des conditions d'utilisations
normales. Dans ces conditions leur durée de vie est estimée
à plus de 50 ans sur la base de courbes de régression construites
à partir d'essais accélérés en pression hydraulique
[18].
En service, Ces tubes en polyéthylène subissent
des charges internes et des charges externes qui provoquent des
déformations et altères leurs propriétés
mécaniques.
Afin de mesurer ces propriétés
mécaniques, la préparation d'éprouvettes d'essais
mécaniques, directement extraites à partir du tube pour conserver
l'histoire thermomécanique intrinsèque et ayant un état de
surface comparable a celui des éprouvettes obtenues par moulage ou par
injection, s'impose.
C'est dans ce cadre que s'inscrit cette étude
expérimentale concernant le suivi des efforts de coupe
générés et de la rugosité de la surface
usinée, lors de l'usinage des tubes en HDPE-80, en fonction des
paramètres du régime de coupe.
|