As the aerospace industry operates in a global market and
relies on a complex supply chain, quality management requirements are crucial.
As a consequence, the manufacturers, the suppliers and service organisations
succeeding in this highly competitive market are those who consider management
as a key business driver.
The aerospace supply chain can be described as a pyramid with
a few major Vehicle, Airframe and Propulsion Manufacturers (Tier 1) at the top
supported by Integrators, Major Assemblers, Component Designers, Specialty
Electronics and Software Designers at the 2nd and 3rd
Tiers; and Make-to-print Machine Shops and Fabricators at Tier 4. Lower in the
pyramid are Distributors and Detail Hardware providers and Raw Material
manufacturers. Across all six tiers are organizations that provide Special
Processes.
The Aerospace products, which are huge and complex must be
highly reliable, perform over a long period of time, comply with Public safety
requirements, and use complex platform. They also take years and billions of
dollars of investments. That is the reason why new products are being developed
more and more by teams which creates a virtual product enterprise. This ability
to collaborate has become the key success of an enterprise. That is the reason
why standards are critical to support these product partnerships.

ISO 9000 changed the way the world looked at managing quality.
But to implement ISO 9000, the aerospace industry required a new strategy for
developing an international quality system and for implementing the standards
required to successfully drive those changes down through one of the largest
and most complex supply chains of any industry. The Boeing Company for example,
has over 15 000 suppliers in over 80 countries.
If we consider the past ten years, we can say that the
aerospace industry has significantly improved its quality philosophy and
processes deployment. The aerospace OEMs began to add company-specific
requirements to customer and regulatory requirements such as MIL-Q-9858,
AQAP-1, and NASA and FAA FARs. Suppliers were supposed to adapt to each
company-specific requirements in order to meet the customer's needs. Then, each
OEM was performing audits against its own requirements. With regard to the
implementation and interpretation of the aerospace quality standards, it is
obvious that the performed audits were resources consuming for both the OEM and
the supplier. In addition, the slight differences between the company-specific
requirements obliged the suppliers to be constantly audited to different
criteria for basically the same top-level standard.
In 1995, several major aerospace manufacturers recognized the
need for uniform supplier requirements. That is how they formed the American
Society for Quality (ASQ) and then create the American Aerospace Quality Group
(AAQG). At first, the AAQG considered the use of the ISO 9001 as a stand-alone
document but they rapidly figured out that the aerospace required too much
supplementation. They tried to create an industry quality system called ARD900
published by the Society of Automotive Engineers in 1996. Then, split from the
ASQ, the AAQG formed the SAE Aerospace Council subcommittee. The main objective
of the SAE was the creation of standardized quality requirements for the
aerospace industry. Finally, in 1997, the SAE released a new standard called
AS9000.
In December 1998, the aerospace industry established the
International Aerospace Quality Group (IAQG), with representation from around
the world, with the stated objective of establishing and maintaining

"a dynamic co-operation based on trust between
international aerospace companies on initiatives to make significant
improvements in quality and reductions in cost throughout the value
stream".
According to the problem of duplicate and contradictory
requirements, the aerospace industry learned the hard lesson that product and
service quality in determining customer selection is as important as price or
delivery.
We must also consider the structure of the aerospace industry
itself. As Design and development's high costs favour joint partnerships, most
of the aerospace players are both suppliers and customers to each others and
their supplier network. That is the very reason why a level playing field was
necessary when quality matters are concerned. Consequently, the IAQG
stated that: "Where quality is concerned, there's no competitive
advantage."
2.1 The AS9000 standard
The main interest of the AS9000 is its focus on areas of
importance to the aerospace industry. The recognition of the
relationships and requirements of regulatory agencies is one key
feature of AS9000. Furthermore, the supplier community is considered as an
extension of the processes and procedures of the customer. Therefore, the
supplier must be tightly controlled in order to reduce variation. AS9000 put
the stress on the processes following which can have extreme consequences on
the product's safety, reliability and performance.
AS9000 also adds industry-specific requirements such as
foreign object damage control, which is one of the most prevalent and deadly
problems of the aerospace. The standard highlights the importance of quality
along the entire supply chain. Process planning and control is also
important--not just for a process itself but also for the tooling, equipment,
software and people involved. Finally, AS9000 increases requirements for
documenting results because many times the only evidence that processes have
been correctly performed is the documentation created while the work was
underway
Although AS9000 satisfied these immediate needs, the AAQG
recognized that OEMs operate globally. In 1998, ISO Technical Committee 20,
which is involved in aerospace standards, agreed to sponsor Working Group 11,
which created an ISO technical paper for quality system requirements. It used
as a template AS9000 and a corresponding European document called prEN 9000-1.
However, if ISO TC 20 published the document, the standard would've taken
additional time to implement and would've lost its ISO 9000 identity, as did a
similar standard developed by the automotive industry. About this time, the
IAQG was formed to help facilitate standardization and cooperation among major
aerospace OEMs.
2.2 AS9100: the first international quality systems
aerospace standard
There are a variety of motivators influencing the
introduction of the AS EN SJAC 9100 standard; among these motivators, the data
provided by the various aviation regulatory agencies revealed that the original
equipment manufacturers (OEMs) were exercising insufficient control of the
supplier base.
The industry co-operated in producing AS EN SJAC
9100, the first international quality systems standard specifically developed
by and for the aerospace industry. It is the first single standard
available for use across the global aerospace community. It includes
requirements necessary to address both civil and military aviation and
aerospace needs. The industry-developed common quality management



system requirements within the standard ensures a consistency of
approach throughout the supply chain, both nationally and internationally.
The AS9100, was developed by a conjunction of parties
including the International Organization for Standardization (ISO) This was
accomplished with the support of the International Aerospace Quality Group
(IAQG), which is comprised of members of the aerospace industry from the United
States, Europe, Japan, Brazil and Mexico. The Society of Automotive Engineers
(SAE) published the standard in late 1999. The motive behind the AS9100 was to
create a truly international standard for the worldwide aerospace industry. As
such, the standard complements ISO 9000 requirements by adding provisions that
address both civil and military aerospace specifications.
The new standardized document, called 9100, is still
based on ISO 9001:1994(E), although it was published separately by
each country's aerospace association or standards body. In the United States,
it was an SAE document called AS9100. In Europe it's known as AECMA EN9100, and
in Japan it's JIS Q 9100. It's also published in Brazil and expected to be
published soon in Korea, China and several more cou ntries.
The process of standardization added almost 55 more
amplifications and requirements to ISO 9001:1994. When ISO revised the ISO 9001
quality management system standard in 2000, the aerospace industry kept on top
of the changes and published a revised standard within six months; this revised
document was "technically equivalent" as far as aerospace supplementation was
concerned.
In addition, the new standard harmonises the
requirements of former individual standards like the American AS9000,
the European EN9000-1, prEN9100, and SJAC9100. AS/EN9100 clarifies the specific
aerospace requirements, and is a compliment to national laws and regulations.
It addresses both "design" and "non-design" responsible companies.
The AS9100 retains the ISO 9001's aerospace sector-specific
additions that are essential to maintain the safety, reliability and quality of
aerospace products. It was created with the continuous improvement of
supply chain processes in mind. The ultimate goal of the AS9100 is to
ensure consistently high-quality aerospace products and maintain customer
satisfaction while keeping manufacturing costs at a minimum. To accomplish this
it standardizes to the maximum extent possible, the quality system requirements
of the aerospace industry.
The main goal of the standard is to deliver costs savings, or
at least reducing, individual requirements for each and every aerospace
customer, supplier or vendor, the standard will deliver cost savings to all
parties. The Federal Aviation Association (FAA) was considered in setting the
provisions of the new standard, particularly in regards to their concern that a
greater emphasis be placed on supplier control.
The 28 pages of the document (50% more than AS9000) contain
many new requirements, and numerous points of emphasis, clarification and
interpretation specific to the Aerospace industry. Similar standards are
specifically developed for aerospace suppliers involved in repair and overhaul,
namely AS/EN 9110, and for aerospace distributors AS9120. Only a few minor
enhancements were made and some technical corrections submitted. When it was
published in the United States in 2001, it was released as AS9100 A. The number
of supplementations was significantly reduced in this document. However, it
included both the new version of the standard, based on ISO
9001:2000, and the original version based on ISO 9001:1994.
AS9100 requires that "key characteristics" are managed when
identified. Keys characteristics are features of a material, process or part in
which the variation has a significant influence on product fit, performance,
service life or manufacturability.
The standard also requires that an organization establish and
document a configuration management process. AS9100 includes extensive
supplementation in the design and development processes. Additional notes are
included for both design and development verification and validation, and
highlight traditional areas of emphasis.
Emphasis is placed on managing suppliers throughout the
aerospace supply chain. In particular, AS9100 includes a number of additional
expectations for identifying and maintaining suppliers. The standard lists
seven specific areas to consider when communicating requirements. They range
from clarifying engineering requirements to managing test specimens and right
of access to suppliers' facilities. Procedures for determining the method of
supplier control are required, as are the processes used when employing these
methods.
Controlling production processes is highlighted. This is
especially important when conducting special processes that don't lend
themselves to after-the-fact inspection techniques. Tooling and other
production equipment, including computer-controlled machines to fabricate and
assemble products, are subject to an additional level of scrutiny.
Servicing requirements are an important part of an aerospace
quality management system. These include maintenance and repair manuals as well
as the actual service work. Documenting the work performed, equipment used and
the people involved is crucial. For facilities that engage only in maintenance,
repair and overhaul, the recently released AS9110 is preferred.
The AS9100 standard imposes traceability requirements for
some or all components as dictated by the customer or regulatory authority. The
standard provides the essentials of an effective traceability program and some
additional expectations regarding internal quality audits. Another requirement,
firstarticle inspections, demonstrates product conformance to engineering
requirements. The standard suggests that aerospace standard AS/EN/SJAC 9102,
which was developed by the IAQG and outlines a methodology for performing and
documenting first-article inspections, be consulted for further guidance.
2.3 Industry-managed processes: demonstration of the
supplier compliance
More than 70 percent of global IAQG members have implemented
AS9100 internally and are requiring it of their supply chains. Increasingly,
the aerospace industry is using industry-managed processes as a means of
demonstrating a supplier's compliance to 9100 and other standards. In the
United States, the AAQG, in conjunction with the Registrar Accreditation Board,
have established both requirements and processes for auditors and registration
bodies. Within the Americas, the Registrar Management Committee oversees this
function for aerospace OEMs and their suppliers. The process is defined in the
SAE's Aerospace Information Report 5359. This document details the operation
and responsibilities of all parties involved in the approval process.
The AAQG published AIR 5493 as well, which describes the
requirements for revised AS9100 standards training. The report will be released
soon and will provide for course accreditation by the RAB. These
industry-managed processes are being replicated in the other IAQG sectors of
Asia and Europe, and results will be made available via a common
database managed by SAE. The database and industrymanaged processes will be
overseen by the IAQG so that the concept of "one approval accepted everywhere"
will truly become a reality in aerospace.
The global aerospace authorities are also working together to
review the activities of major OEMs with respect to supplier oversight. The FAA
has concluded that AS9100 is "a comprehensive quality standard containing the
basic quality control/assurance elements required by the current Code of
Federal Regulations, Title 14, Part 21." The Department of Defense has adopted
AS9100 and made it available for use on contracts. Likewise, NASA issued a
similar notice that it had reviewed the standard and approved its use for
contractual requirements. Civil aviation authorities are evaluating and
commenting on the industrymanaged plans. For the most part, these processes
effectively use scarce resources and increase oversight while minimizing
confusion and intrusion into a supplier's and OEM's operations.
Considering that compliance with a new standard implies the
reshaping of old operations, Boeing has given two years to reach compliance to
3,000 of its suppliers. In order to make the transition as smooth as possible
between ISO9001 and AS9100, Boeing provides its suppliers with generous leeway.
In addition, Boeing has asked its suppliers to adopt the Boeing Quality
Management System instead of outmoded legacy quality systems (e.g: D1-9000,
MIL-Q-9858A, MIL-1-45298).
Boeing's suppliers are not the only ones who are put upon to
comply with the AS9100. It is a standard to be met by suppliers across the
aerospace industry. As the SAE puts it, "If your company produces parts and/or
processes for the aerospace industry, AS9100 is an essential industry
document." The IAQG has set November 2003 as the compliance date. Until then
the AS9000 remains available for use. Boeing's Gary Baker, chair of the IAQG,
explains, "We hope that by rapidly aligning the 9100 standard with ISO 9001
:2000, while at the same time retaining the existing version of 9100 for
concurrent use [until November, 2003] that we can minimize the impact of this
revision upon the using organizations."
2.4 The Quality System Audits: the aerospace industry
control other-party process
An adequate audit program is required to provide management
with visibility regarding the effectiveness and efficiency of the quality
management system. ISO Technical Committee (TC) 176 has developed a set of
audit requirements and published them as ISO 19011. These should be reviewed
when establishing the organization's internal audit process.
A number of approaches exist to demonstrate the compliance of
the quality management system to the appropriate standard. These are most
typically referred to as:
- 1st party: an organization conducts their own
evaluation and declares compliance
- 2nd party: a customer reviews their suppliers
quality management system and determines compliance
- 3rd party : an independent organization, typically an
accredited registrar, audits the organizations quality management system and
certifies compliance
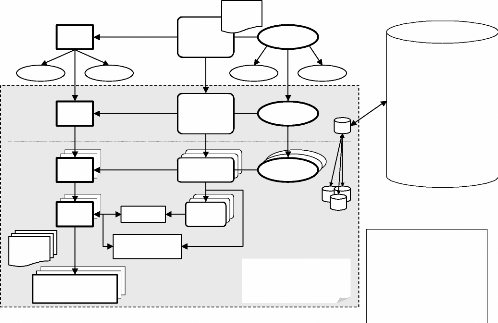
World Level
European Level
National Level
EN 9100...
Certificate
Asia/Pacific Americas
Supplier or
Subcontractor
CRB
NAB
IAF
EA
Local Procedure
Training
Organisations
Auditors
IAQG
Oversight
Team
EU OPS
Team
CBMC
AAB
Document
104
Asia/Pacific Americas
European Aerospace Supplier Quality System Certification
Scheme
AECMA/QC/24281
AECMA QC
IAQG
NAIA
IAF - International
Accreditation Forum
EA - European co-operation for
Accreditation
NAB - National Accreditation Body CRB - Certification Body
NAIA - National Aerospace Industry
Association
CBMC - Certification Body Management Committee AAB - Auditor
Authentication Board
- Mandated Accreditation Bodies
- Accredited Certification Bodies
- Authenticated Aerospace Auditors
- Authenticated Training organizations
- Aerospace QMS Standards Certificated compan ies
DATA BASE

The European Management system for OPS
The aerospace industry has developed a process for the
oversight of the 3rd party process when performing audits to the
9100, 9110 and 9120 standards. This is typically referred to as the
IndustryControlled Other-Party (ICOP) process. Under this process the industry
conducts independent reviews of those accrediting the registrars and conduct
witness audits of these registrars as they perform quality management system
audits. The result is a list of Registrars authorized to perform aerospace QMS
audits. The details regarding this methodology are contained in the IAQG
procedure 9104.
The aerospace industry developed an International Aerospace
Sector Certification Scheme. To that purpose, the IAQG developed and compatible
system acceptable to all. This system allows sharing of audit results and
approvals resulting in the elimination of multiple assessments and process
improvement. Consequently, suppliers receive one aerospace quality system
approval that is acceptable to all aerospace OEMs (and their suppliers)
throughout the world. Obviously, confidence is key to the International
Aerospace Sector Certification Scheme.
The aerospace industry identified eleven requirements of a
global QMS evaluation system. - Single global standard
- Harmonized system of application

- Inter-National accreditation control
- Approved certified bodies and registrars - Approved aerospace
auditors
- Global acceptance by supplier base
- Data easily available to all participants
- Active industry participation
- One audit accepted by primes
- Oversight /control by IAQG and Sectors
- Inter-National Aviation Authority endorsement
The ICOP process includes requirements for the Accreditation
Boards and CRBs, the auditors and the associated training. The system includes
requirements for the minimum audit time and reporting the results of the
audits. The industry is responsible to provide oversight for the process, to
report problems with the registrars and their auditors and to track the
performance of the suppliers and their associated registrars.
An On-line Aerospace Supplier Information System (OASIS) went
operational in July 2003. Since then over 2000 registration have been reported.
All assessments are entered by the registrars and consist of two sets of data.
The first is the public information contained on the Certificate of
Registration. The private information includes the detailed audit findings.
Access to this private data is controlled by the certified organization. This
data is also summarized periodically to allow visibility to the industry's
performance to the standard. The OASIS database is an essential element of this
robust system.
The International Aerospace Sector Certification Scheme results
in the elimination of redundant quality management system assessments and a
clearer communication of industry expectations.
2.5 the OASIS database: a new aerospace procurement
tool?
In May 2003, the International Aerospace Quality Group (IAQG)
issued a letter detailing the roll out of the Online Aerospace Supplier
Information System (OASIS). The Requirements for Certification/Registration of
Aerospace Quality Systems (AIR5359) used for conducting aerospace audits to
Aerospace Quality Management Systems requires Certification/Registration Bodies
(CRBs) to submit the results of the assessment performed. Effective July 1,
2003, CRBs have been required to enter audit information into the OASIS
database.
The database, which is a requirement of AIR5359, is essential
to provide independent verification of the status of the certification. It
enables the acceptance of a single assessment globally and prevents from
multiple visits and audits by multiple customers. Without the OASIS database,
OEM's would have to independently verify each auditor, CRB and assessment
results.
Oasis benefits to all the aerospace industry players as it
keeps customers, OEMs, and suppliers up-to-date. It provides complete
information on Aerospace QMS approvals, with data on Who, How, When and What is
Approved, including results. It also provides ABs, CRBs and Auditors current
information on Who is Approved and for What by the Aerospace Industry. In
addition, Oasis should be part of the OEM/Supplier's process of supplier
management as it should allow a supplier to be added to an ASL without
requiring additional evidence of QMS registration/approval.

The OASIS database has two sections, including one available
to suppliers and anyone else. The other section is limited to member companies
of IAQG. The supplier section identifies contact information , certification
dates and scope of registration. It also identifies all IAQG member companies,
accreditations bodes (Abs), certification/registration bodies (CRBs and
auditors).
The limited access section (IAQG members only) includes
detailed information on every assessment. The assessment dates, auditor names,
an assessment summary and the score from the assessment are available.
IAQG developed OASIS after members expressed a desire to
reduce the amount of audits performed on suppliers in the supply chain. A
consistent set of standards (AS9100, AS91 10 and AS9120) help to solve one part
of the problem. However, the IAQG members still need a mechanism to quickly
access accurate and regularly updated certification and registration
information about suppliers. As a matter of fact, many IAQG member companies
have regulatory requirements to monitor their supply chain. For a member
company to meet the regulatory requirement, they either have to go out and
audit that company or show they can monitor the certification/registration
activity for those suppliers. The IAQG OASIS database provides that place.
Upon registration, the CRB will enter supplier information into
the database. Once established in the database, initial assessment details may
be entered.
Cost for entry into the IAQG OASIS database is 500 U.S
dollars for a three-year registration cycle. The fee covers the cost of design,
development and anticipated maintenance for three years. OASIS database
benefits to both IAQG member companies and suppliers. As a matter of fact,
listing in the IAQG OASIS database, an organization will be recognized as being
certified to the highest level of Quality Management System standards in the
world for aerospace companies.
As the database grows with certification and registration
information, it becomes a procurement tool for companies to select new
suppliers. Once registered to one of the international aerospace QMS standards
and listed in the IAQG OASIS database, an organization gains competitive
advantage.