3.4 Réalisation
L'édification d'un aérocondenseur intègre
les éléments suivants :
· les éléments échangeurs de
chaleur : condenseurs
· les tuyauteries de liaisons (liaisons vapeur et
circuit de récupération des condensats) ;
· le dispositif de circulation d'air :
moto-ventilateur ;
· la charpente ;
· les auxiliaires (ballon condensats, pompes de
circulation) ;
· dispositif de mise sous vide, régulation et
contrôle, etc.
Le schéma de circulation des fluides est donné par
le P&ID dans l'annexe A pour l'aérocondenseur de vapeur d'eau.
3.4.1 Condenseurs principaux [2]
L'admission se fait en partie haute des tubes ailetés
et la vapeur circule dans le même sens que le condensat (de haut en bas),
ce dernier étant récupéré en partie basse des
éléments. Des faisceaux alignés contenants des tubes
à ailettes sont employés.
Les faisceaux tubulaires sont toujours inclinés,
disposition nécessaire pour assurer, à la fois,
l'écoulement des condensats et une bonne circulation de l'air à
travers les ailettes des tubes.
Les tubes à ailettes (figure 6) présents dans
les faisceaux d'échange ont pour fonction de favoriser le transfert de
chaleur par convection entre vapeur d'eau et air ; leurs principaux avantages
par rapport aux tubes nus sont leur importante surface d'échange et le
grand coefficient de conductivité des ailettes.
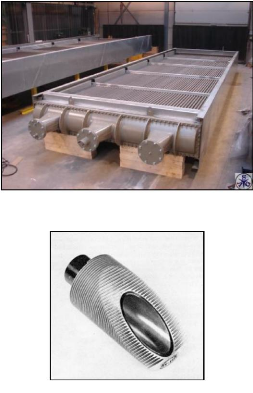
Figure 5 : Faisceaux d'échange
Figure 6 : Coupe du tube à ailette
3.4.2 Tuyauteries de liaisons [2]
· Liaison vapeur : Les performances de
l'aérocondenseur sont généralement garanties à la
liaison « générateur de vapeur » (bride
d'échappement de la turbine pour une centrale thermique, par exemple).
Le dessin de la liaison entre la bride d'échappement de la turbine et
l'entrée de l'aérocondenseur doit être étudié
avec beaucoup de soin afin de minimiser les pertes de charges : la distance
à l'aérocondenseur doit être la plus courte possible
(aérocondenseur placé sur le toit ou le long du bâtiment
turbine) ; la liaison doit comporter un minimum d'accidents (tels que coudes),
créant des pertes de charge singulières importantes ; les coudes
sont normalement équipés d'ailettes internes de guidage. Les
culottes de raccordement entre la canalisation principale et les lignes de
distribution de vapeur sur les éléments d'échange sont
exécutées avec un soin particulier.
Les canalisations vapeur sont réalisées en
tôles d'acier roulées et soudées. Elles sont
généralement soumises au vide et, de ce fait,
équipées de frettes pour éviter le flambage. Elles
sont, en outre, soumises à des efforts importants
d'origine thermique (dilatations) et mécanique (efforts sur les fonds) :
il y a lieu de minimiser les contraintes aux raccordements, notamment aux
brides d'échappement de la turbine. Le raccordement des liaisons vapeur
est généralement fait par soudure sur le site.
? Canalisation de condensât : Les canalisations de
condensats ne posent aucun problème particulier. Il y a lieu, cependant,
de respecter des conditions de vitesses d'écoulement faibles et
d'assurer des pentes permettant d'éviter l'engorgement de l'appareil.
Généralement, la structure de l'aérocondenseur n'est pas
prévue pour supporter l'installation pleine d'eau.
Le ballon est en principe réalisé à
partir de tôles roulées et soudées avec fonds
bombés. Le niveau d'eau est régulé en fonction du
débit de condensats, ce qui permet d'assurer un débit constant
sur les pompes d'extraction. De plus, tout danger de remplissage excessif ou de
vidange est évité par l'utilisation d'alarmes haute et basse
ramenées en salle de commande, permettant une intervention rapide.
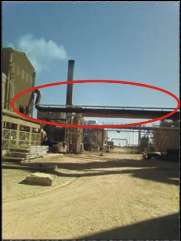
Figure 7 : Partie des canalisations de vapeur et de
condensât sur site 3.4.3 Circulation de l'air [2]
La circulation de l'air peut être assurée soit par
tirage naturel, soit par tirage mécanique. On note que la
quasi-totalité des aérocondenseurs construits à ce jour
sont à tirage mécanique, solution justifiée par le moindre
coût du dispositif. On utilise des ventilateurs axiaux, le plus souvent
à grands débits-volumes (hélices).
On peut noter les tendances suivantes :
Tirage forcé (figure 9a) :
· Avantages relatifs sur le tirage induit :
appareils plus compacts, simplicité de structure (réduction
de coût), accessibilité et mise en place/dépose des
ventilateurs plus facile ;
· Inconvénients relatifs : plus de
risques de recirculation d'air chaud, alimentation en air des faisceaux moins
régulière, et plus de risques d'avarie des faisceaux par
agressions verticales (par exemple, grêle) : protections souvent
nécessaires mais parfois aléatoires.
Tirage induit (figure 9b) :
· Avantages relatifs sur le tirage forcé :
très bonne répartition d'air sur les échangeurs,
influence de l'ensoleillement sur les échangeurs négligeable,
protection antigrêle inutile, et gain sur la puissance de ventilation
possible en ajoutant des diffuseurs (dont la mise en place est pratiquement
impossible en tirage forcé) ;
· Inconvénients relatifs : encombrement
plus important et structure du support plus lourde et plus chère.
La solution adoptée dans notre cas est le tirage
forcé.
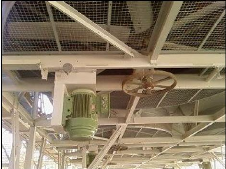
Figure 8 : Partie moto-ventilateur sur site
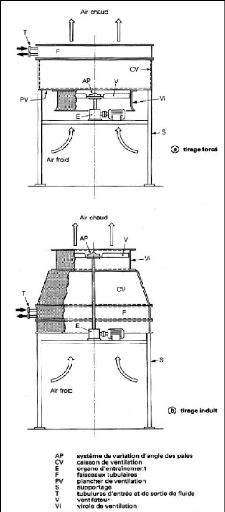
Figure 9 : Eléments composants d'un
aéroréfrigérant avec échangeurs en position
horizontale et ventilateurs dans deux positions : tirage forcé ou
induit [2]
|