II-3-Le Broyage
Le minerai repris par les roues-pelles arrive à une
grande trémie principale à deux compartiments d'une
capacité totale de 2000 tonnes et ensuite par 2 extracteurs;
l'extracteur verse le produit sur le convoyeur à bande dont le
débit normal est de 900 t/h pour le TS1 et 650 t/h pour le TS2 et 1300
t/h pour le TH.
Le broyage autogène ou semi-autogène
assuré par deux broyeurs à boulets, type Aerofall (photo2) ligne
A et B, chacun permettant de broyer les concassés jusqu'à une
granulométrie de 0 à 12,5mm.
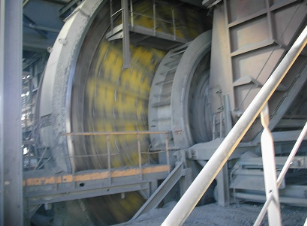
Photo N°2 : Broyage Aerofall
à l'usine du Guelb
Pour aboutir à un débit optimum de ces broyeurs;
il a été recommandé de les faire tourner dans les
conditions suivantes:
- Broyeur Aerofall: (34,5"x 8,5")
- Diamètre: 10,24 m
- Longueur: 4 m
- Vitesse de rotation: 11tr/mn;
- Charge en boulets de 66 tonnes;
- Taux de remplissage de 33%;
- Une ouverture de ventelles de 75% permettant de balayer
toutes les particules broyées;
- Puissance consommée: 4000 à 4500kw;
- Puissance installée: 5220kw.
Le débit du broyeur dépend de :
· La régulation (puissance, ouverture vantelle,
dépression sortie.......);
· La recharge de boulets;
· Usure blindage (il existe a l'intérieure du
broyeur des blindages de viroles, des flasques, et des tourillons);
· Qualité minerai;
· Mode de fonctionnement du broyeur;
· Intervention de l'opérateur.
La décharge du broyeur est répartie entre le
classificateur vertical et l'alimentation du criblage.
Au niveau du classificateur se déroule une
séparation gravimétrique. La sous-verse se dirige vers le
criblage; tandis que la sur-verse (0-500um) non retenus par le
classificateur verticale sont entraînés par le courant
d'air vers une batterie de 6 cyclones de
chaque ligne pour qu'elle fasse l'objet d'une deuxième
séparation gravimétrique. La sous-verse (100 à 500um) est
envoyée par le convoyeur vers la séparation magnétique;
par contre la sur verse (0-100um) des cyclones prend le chemin des
filtres électrostatiques. Après filtration la
sous verse (exhaure) est acheminée vers le stérile, en attendant
le projet de séparation magnétique humide, et la sur verse est
rejetée dans l'air par la cheminée du ventilateur.
II-4-Le Criblage
Après le broyage (0-12,5mm), le crible est
alimenté par les sorties de broyeurs Aerofall (A, B) et la sortie
de presses à rouleaux.
Le minerai est envoyé vers le criblage pour subir un
classement dimensionnel selon la maille du crible (1,6 mm). Les grains d'une
dimension inférieure à la maille du crible constituent le
passant, tandis que ceux qui ont une dimension supérieure
représentant le refus.
Pour être compatible avec le broyage, le criblage
comporte deux lignes: A et B. chaque ligne est constituée de 24 cribles
vibrants; type DERRICK et l'agencement de ces cribles est
représenté par 12 sections, chacune formée de 2
cribles.
Le crible est constitué de haut en bas des
éléments suivants :
- Un chariot verseur : transitant sur un
accumulateur pour le remplir de minerai à cribler, qui sera
divisé entre les cribles. Dans le cas de remplissage de l'accumulateur,
le vérin hydraulique s'avance pour ouvrir la goulotte du chariot pour
qu'il puisse se déplacer vers les deux cribles de by pass (23 et 24)
utilisés souvent dans le cas d'indisponibilité de l'accumulateur.
- L'accumulateur : c'est la caisse qui
assure l'alimentation des cribles en stockant les produits à
cribler,
- L'alimentateur : alimente directement
les cribles,
- Caisson hydraulique : assure
l'énergie,
- Registre denté : il permet le
réglage de l'ouverture d'alimentation du crible qui joue un rôle
déterminant dans l'efficacité de criblage ; cette ouverture
est graduée de 0 a 100 %.
- Crible : chaque crible comprend :
un moteur vibrant et trois toiles, chacune de 1,6 mm
- La goulotte : permet
l'évacuation des passants du criblage.
A l'usine des Guelb, l'efficacité du criblage varie
entre 75% et 90% et pour la fraction critique. Cette efficacité exprime
la qualité de l'épuration du produit passant, autrement dit, le
pourcentage des grains de dimension supérieure à la maille de
crible contenus dans le passant, dans notre cas le pourcentage de refus dans le
passant est de l'ordre de 10 à 15%.
L'efficacité du criblage dépend
de :
- Débit d'alimentation de crible,
- L'état des toiles du crible qui doivent être en
bon état et ne présentent pas des défauts tels que :
usure, tension et colmatage,
- L'inclinaison du crible, elle doit être constante,
- Sens de marche des moteurs du crible.
Le débit moyen d'un crible est de 105 tonnes par heure,
les facteurs suivants affectent la
capacité du crible dépend:
- pourcentage passant,
- % de la fraction critique,
- % en eau,
- Et la forme de grains,
Après le criblage; le passant est envoyé
directement vers la séparation magnétique; tandis que le refus
prend l'itinéraire des presses a rouleaux pour être
rebroyé.
|