Chapitre II
Procédés de mise en forme des
métaux
Chapitre II : Procédés de mise en forme
des métaux

18
I. Introduction
L'objectif premier de la mise en forme des métaux est
de conférer à une pièce métallique des dimensions
situées dans une fourchette de tolérance donnée. Les
principaux procédés de mise en forme des métaux sont
apparus progressivement, donnant naissance par la suite à diverses
variantes, parfois très nombreuses. Les formes modernes des divers
procédés sont le plus souvent apparues récemment pour
assurer la production en grande série de pièces à faible
coût. Il existe trois voies principales de mise en forme selon
l'état de départ du matériau métallique (le
moulage, le façonnage et le frittage). La Figure suivante
récapitule les principaux procédés de mise en forme des
métaux utilisés actuellement.
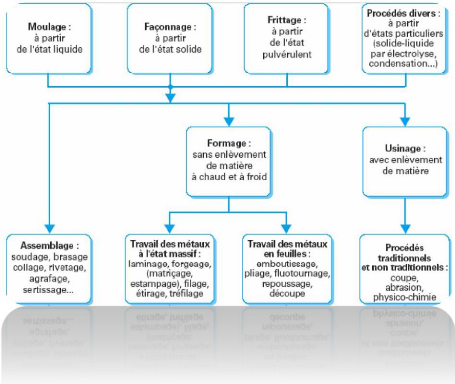
Figure 13:Principaux procédés de mise
en forme des métaux
Chapitre II : Procédés de mise en forme
des métaux
II. Moulage

19
L'opération de moulage consiste à fabriquer un
moule, généralement en matériaux réfractaires, qui
porte l'empreinte en négatif de la pièce, cette empreinte
étant obtenue à partir d'un modèle reproduisant la
pièce à fabriquer.
L'opération de moulage est une des plus importantes du
processus industriel de la fonderie. Elle détermine en effet,
d'après le modèle, les formes de la pièce à couler,
ses dimensions et leur précision, ses états de surface, son
refroidissement, et joue un rôle prépondérant sur de
très nombreux paramètres influant sur sa qualité.
À titre d'exemple, dans des productions de grandes
séries, les opérations de moulage représentent
fréquemment 30 % environ des prix de revient hors matière Il
convient donc que le choix d'un procédé de moulage soit fait avec
le maximum de précaution pour ne pas pénaliser les productions
futures, tant en qualité qu'en prix de revient.[6]
1 Matériaux de moulage
1.1 Matériaux pour moules non permanents :
Pour la fabrication des moules et des noyaux, la fonderie
utilise de nombreux matériaux et produits dont les plus importants sont
cités ci-après.
a) Sables de base et siliceux :
Ils sont composés essentiellement de grains de silice
SiO2 ; c'est le matériau le plus universellement employé pour la
confection des moules et des noyaux. Parmi toutes les variétés on
citera :
? les sables silico-argileux naturels, utilisés à
l'état brut ;
? les sables blancs extra-siliceux de carrière,
très souvent traités par lavage,
classement granulométrique et séchage avant
livraison.
? Les Sables spéciaux (chromite, olivine, zircon,
silico-alumineux)
Tous ces produits doivent présenter des
caractéristiques bien définies, comme par
exemple:
y' la répartition granulométrique ou la forme des
grains ;
y' des propriétés chimiques en accord avec celles
des liants ;
y' des propriétés physiques à froid
(perméabilité) et à chaud (réfractarité,
dilatation, capacité et conductivité thermiques,
mouillage par le métal liquide).
b) Liants
Ce sont les deuxièmes constituants les plus importants
employés pour la fabrication des moules et noyaux en fonderie. Ils
doivent en effet donner :
Chapitre II : Procédés de mise en forme
des métaux

20
y' la plasticité au sable pour épouser les
formes du modèle et acquérir ensuite par durcissement une
résistance mécanique permettant de conserver la forme
jusqu'à la solidification du métal ;
y' le minimum de réactions moule/métal qui sont
des risques de défauts sur pièce de types piqûres ou
soufflures.
On peut classer les liants en deux grandes familles :
? Les liants minéraux comme les argiles, bentonite,
silice colloïdale, silicate soluble, plâtre et ciment ;
? Les liants organiques comme les matières
amylacées (dérivées de l'amidon), les huiles siccatives et
les résines synthétiques durcissables à chaud ou à
froid, avec catalyseurs solide, liquide ou gazeux.
|