Conclusion
L'objectif de cette enquête était d'apporter une
validation empirique aux hypothèses soulevées lors de la revue de
l'Etat de l'art. Grâce aux résultats obtenus, nous avons pu en
premier lieu comprendre que le Lean est bien intégré au quotidien
dans les industries pharmaceutiques, et cela au quotidien.
L'intérêt réglementaire du Lean est
perçu, car cette méthodologie est bien intégrée
dans les BPF Les deux méthodologies ne sont pas contradictoires, et le
Lean permet même de faciliter l'application du référentiel.
Malgré cela, les BPF n'encouragent pas l'application du Lean. Cela est
expliqué par l'obligation de résultats et non de moyens du
référentiel. La comparaison des deux populations
interrogées a montré un résultat plutôt
homogène concernant les questions posées.
L'intérêt économique de l'application
d'une stratégie Lean est bien perçue par les répondants.
Deux principes sont peu appliqués en industrie pharmaceutique,
concernant l'adoption d'une philosophie à long terme et la production
constante et lissée. Cela confirme les difficultés
soulevées dans l'état de l'art.

50
Enfin, l'intérêt humain est bien perçu par
les répondants, concernant la productivité, la
sécurité ou le partage avec les autres. De plus, les effets
négatifs possibles ne sont pas rencontrés pour la majorité
des répondants.
Nous pouvons donc conclure que les hypothèses
soulevées sont bien vérifiées en entreprise. Nous allons
maintenant examiner les opportunités et limites soulevées par
l'adoption d'une méthodologie Lean, dans le cadre de missions
d'amélioration, menées durant cette année d'alternance
dans l'entreprise Novo Nordisk.
IV. Observations
Durant cette année de formation, plusieurs missions
m'ont été confiées. La première consistait à
suivre et améliorer le processus de supervision des APS (Aseptic
Process Simulation, ou Simulation de Procédé Aseptique). La
deuxième mission consistait à mettre en place une démarche
Nécessaire et Suffisant, pour les activités du service Assurance
Qualité.
Après avoir décrit le procédé de
simulation aseptique, nous allons analyser ces missions d'amélioration,
qui ont été menées en suivant une méthodologie
Lean. Nous tenterons de déterminer l'intérêt d'une telle
démarche pour ces cas pratiques, et en examinerons les avantages et les
limites.
Le processus de simulation de procédé aseptique
Comme nous l'avons vu auparavant, les médicaments
contenant de l'insuline doivent être produits de façon aseptique,
de leur filtration stérilisante à la fin du remplissage.
Les Bonnes Pratiques de Fabrication imposent des exigences
particulières aux industries pharmaceutiques produisant des
médicaments stériles, qui ne peuvent pas être
stérilisés à la fin du processus. Selon cette
réglementation, « la validation des procédés de
fabrication aseptique doit comprendre la simulation du procédé
à l'aide d'un milieu de culture », c'est-à-dire qu'on
exécute le processus de production aseptique en utilisant un milieu de
culture favorable à la croissance des micro-organismes. Cela permet
d'identifier d'éventuelles contaminations.

51
Chez Novo Nordisk, cette validation des procédés
de fabrication est évaluée par les APS, via un rapport de
validation. Le respect des critères de validation et la
non-contamination du média permettent d'approuver le rapport, et de
valider les procédés de fabrication de l'entreprise.
Ce processus est supervisé par l'Assurance
Qualité, qui assiste en direct ou en visionnant des enregistrements
à l'ensemble des activités du processus. Le rôle d'un
superviseur est de vérifier le bon comportement aseptique des
opérateurs de production et techniciens de maintenance, ainsi que de
s'assurer du respect des procédures applicables.
Production Contrôle qualité Assurance
Qualité

Lavage et Approbation
Formulation Remplissage Incubation Inspection
Stérilisation de l'APS
Figure 18 : Processus simplifié de la
réalisation d'un APS
En cas d'observation, un retour doit être
effectué à la personne concernée, sous forme d'une
remarque, ou d'une reformation. Ces retours, s'ils sont critiques, doivent
être faits avant l'approbation du rapport de validation.
Nous pouvons représenter ce processus ainsi :
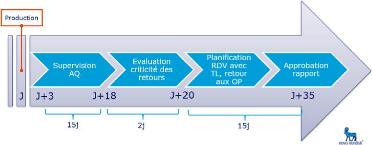
Figure 19 : Processus simplifié de la supervision
des APS par l'Assurance Qualité Etat des lieux
préalable
Ma mission a débuté avec une formation à
la supervision des APS, pour le processus de remplissage. Cette formation m'a
permis d'être habilitée à réaliser cette
activité. Cette

52
supervision s'effectue en zone de production, ou bien à
l'aide d'enregistrements vidéo. Cela m'a permis d'avoir un regard
interne sur ce processus, et d'en comprendre les dysfonctionnements.
La supervision des APS par l'Assurance Qualité est
suivie et pilotée grâce à un board de performance
hebdomadaire. Plusieurs indicateurs de performance y sont
évalués, concernant notamment l'état de la supervision en
cours, les délais de retours aux opérateurs ou bien l'approbation
de l'APS.
Nous avons pu nous rendre compte qu'un indicateur de
performance était souvent peu respecté. Cela concernait le temps
nécessaire pour réaliser les retours aux opérateurs, qui
dépassait parfois 60 jours après la réalisation des
activités, entrainant la perte des enregistrements vidéo
associés. Cela avait pour conséquence de ne pas avoir de support
pour effectuer les retours aux opérateurs. De plus, les
procédures du groupe exigent que les retours aux opérateurs
soient effectués le plus rapidement possible après
l'observation.
Il a donc été décidé de
réaliser un document A3, qui est un outil de résolution
systématique des problèmes, aussi appelée 8D pour 8
disciplines. Il est disponible en annexe (Annexe 3).
Amélioration du flux de retours APS
Résolution du problème
La clarification du problème montre que les retours
sont effectués trop longtemps après les activités. La
recherche du point d'origine pointe les étapes de gestion des retours
par l'Assurance Qualité, et de retour aux opérateurs, qui
s'effectuent en zone de production.
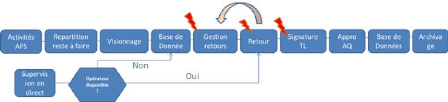
Figure 20 : Processus détaillé de la
supervision des APS par l'Assurance Qualité, avec recherche du point
d'origine des problèmes.

53
Après l'étape de clarification, nous nous sommes
aperçus qu'il y avait deux problèmes distincts à
résoudre, qui ont fait l'objet de deux recherches de causes :
- La gestion des retours commence trop tard après la
supervision,
- Il y a des difficultés pour faire les retours une fois
les observations faites.
Nous avons recherché toutes les causes possibles, en
utilisant un diagramme d'Ishikawa. En analysant ces retours d'un point de vue
Lean, nous pouvons identifier un grand nombre de gaspillages :
- Transport : Les retours aux opérateurs sont
effectués en zone à atmosphère contrôlée,
difficile d'accès. Des retours fréquents posent un
problème de sécurité, car il faut limiter l'accès
à ces zones pour éviter les contaminations par exemple. De plus,
cela allonge le temps de déplacement.
- Stock : A cause de ces déplacements
difficiles, les retours sont effectués seulement après
réception de tous les créneaux de supervision, et pas dès
la réception de chaque créneau. Cela crée un stock
d'informations.
- Retards : Ces stocks d'information créent des
retards pour les retours, qui ne sont pas effectués dès que cela
est possible.
- Sur-qualité : Les retours non-critiques sont
traités de la même manière que les retards critiques.
Après avoir effectué un diagramme d'Ishikawa
pour rechercher les causes possibles, nous avons mené des investigations
pour vérifier si ces causes avaient une réelle influence sur
notre problème ou non. La cause la plus probable est nommée cause
directe. Elle permet, en utilisant l'outil « 5 Pourquoi », de trouver
la cause racine.
Dans notre cas, nous avons abouti à deux causes directes
:
- Les rôles et responsabilités, définies
dans la procédure décrivant l'exécution de la supervision
des APS par l'Assurance Qualité, ne sont pas respectés : le suivi
des observations est effectué par les équipes d'Assurance
Qualité et non de la production.

54
- Des retards dans le flux de traitement des retours
entrainent un retard dans la prise en charge de ces retours.
L'équipe de l'Assurance Qualité doit donc
effectuer une activité qui ne lui est pas dédiée. Cela
entraine une charge supplémentaire, qui cause du retard dans le flux de
traitement des retours, principalement car cette activité n'est pas
prioritaire par rapport aux autres activités du service.
La première cause racine, concernant le non-respect des
rôles, pointe l'absence de formation pour le rôle de superviseur de
production, qui, de plus, n'est pas clairement défini. La supervision
n'est pas effectuée par la production, qui recense seulement les
activités effectuées en production. C'est donc l'Assurance
Qualité qui prend en charge cette activité.
L'investigation menée pour trouver la cause racine du
deuxième problème, concernant les retards dans le flux de
traitement des retours, met en cause les retards dans la supervision des APS
par l'Assurance Qualité. Ce problème sera détaillé
ultérieurement.
Afin de limiter les retards, plusieurs actions ont
été prises. Le board de performance, dédié
à l'APS, a été muté sous Trello, qui est un outil
de gestion de projet en ligne. L'utilisation d'un tel outil a permis une
meilleure visualisation des retours restant à faire, tout en regroupant
les informations nécessaires à la prise de rendez-vous avec
l'opérateur (équipe de rotation, date limite, date de retour
possible, commentaire associé, responsable du retour, ...)
De plus, afin de faciliter le suivi à plus long terme,
un graphique regroupant les délais de retour et de supervision a
été produit (Annexe 4). Il permet de visualiser le
délai de supervision, cumulé au délai de retour, pour
chaque opérateur à qui un retour a été fait depuis
le début de l'année 2019.
De plus, pour simplifier le flux de traitement des feuilles
d'observation, il a été décidé de séparer
physiquement les feuilles, selon leur stade de traitement :
- Les feuilles non traitées sont déposées
dans une pochette spécifique, avec le document de
traçabilité.

55
- Les feuilles traitées, c'est-à-dire pour
lesquelles les commentaires ont été entrés dans la base,
sont conservées dans un dossier identifié. Il est ajouté
un post-it sur la feuille, lorsqu'on identifie un retour nécessaire. De
plus, un suivi est assuré via Trello.
- Une fois les retours effectués, les feuilles pouvant
être archivées sont approuvées et rangées dans le
dossier identifié.
Enfin, pour permettre le respect des rôles et
responsabilités de chacun, deux propositions ont été
suggérées. La première consiste à mettre en place
un statut de superviseur de production, en construisant une formation
adaptée. Il faudra auparavant organiser un atelier de travail avec les
process de production, afin de définir le minimum attendu pour la
supervision.
Le processus de production des APS sera ainsi supervisé
d'une part par les équipes de production, et d'autre part par
l'Assurance Qualité. Les observations générées
pendant ces supervisions seront mises en commun, et feront l'objet de retours
aux opérateurs de production, effectués par les superviseurs de
production. Cela permettra un suivi plus efficace des actions sur le long
terme, et facilitera les retours aux opérateurs car ils seront
réalisés plus rapidement. De plus, une montée en
compétence des superviseurs de production sera réalisée.
Enfin, pour garantir un niveau de qualité suffisant, l'Assurance
Qualité réalisera les retours critiques, résultant de
gestes pouvant avoir une incidence sur le produit par exemple.
Concernant la mise en place d'un rôle de superviseur de
production, le gain de temps potentiel concernant l'équipe de
l'Assurance Qualité est conséquent. Sur l'année 2018, 16
APS ont été menés, aboutissant à 753 observations.
Cela a entrainé un retour à 35 équipes différentes
sur trois lignes de production. En arrondissant le temps moyen d'un retour
à 10 minutes, et en prenant en compte du temps d'accès à
la zone de production de 10 minutes en moyenne, cela aboutit à un total
de 251 heures de retours, pour l'année 2018. Après la mise en
place de l'amélioration proposée, la très grande
majorité de ces retours pourraient être effectués par le
superviseur de production, en collaboration avec l'Assurance Qualité.
Résultat obtenu

56
Les actions correctives menées, bien que provisoires et
non pérennes, ainsi qu'une vigilance accrue sur les délais, et
des rappels réguliers ont permis de diminuer sensiblement le temps
alloué à l'organisation des retours.
Le tableau suivant nous renseigne sur les délais moyens
de supervision et de remplissage, ainsi que les délais maximum et
minimum, pour tous les lots APS remplis depuis le début de
l'année 2019 :
|
Numéro de lot APS
|
JT6L180
|
JT6L294
|
JT6L572
|
JT96M005
|
JT6M189
|
JT6M287
|
JT6N304
|
JT6P157
|
Supervision
|
Moy
|
28
|
24
|
29
|
8
|
14
|
10
|
13
|
10
|
Max
|
34
|
41
|
35
|
31
|
18
|
27
|
24
|
24
|
Min
|
12
|
13
|
21
|
-
|
8
|
1
|
-
|
3
|
<18j
|
9%
|
36%
|
0%
|
89%
|
93%
|
88%
|
63%
|
77%
|
Retour
|
Moy
|
57
|
56
|
53
|
32
|
39
|
36
|
23
|
25
|
Max
|
94
|
77
|
80
|
84
|
78
|
64
|
43
|
36
|
Min
|
37
|
41
|
36
|
- 61
|
11
|
-
|
-
|
15
|
<60j
|
73%
|
73%
|
75%
|
92%
|
87%
|
94%
|
100%
|
100%
|
Tableau 8 : Tableau de statistiques sur les indicateurs
de délais et supervision des APS
Le délai de supervision est la différence entre
la date de l'activité et la validation de la supervision. Le
délai de retour est la différence entre la date de
l'activité, et la date du retour à l'opérateur.
Sur les derniers APS organisés, tous les rendez-vous
pour les retours ont été organisés avant l'approbation du
rapport, soit moins de 36 jours après les activités. Concernant
le premier APS réalisé en 2019, le délai moyen de
supervision était de 28 jours, pour un délai de retour global de
57 jours. Seulement 9% de la supervision était réalisée
dans les temps, et 73% des retours étaient effectués avant 60
jours. La différence est marquante avec le dernier APS organisé,
avec un délai moyen de supervision de 10 jours, avec 77% de la
supervision réalisée dans les temps.

57
Les retours ont été effectués en moyenne
après 25 jours, et 100% ont respecté les délais de 60
jours.
Nous pouvons visualiser l'évolution de la
conformité des délais de retour sur le graphique suivant :
JT6L180 JT6L294 JT6L572 JT96M005 JT6M189 JT6M287 JT6N304 JT6P157
Numéro de lot APS
Supervision conforme (%) Retours conformes (%)
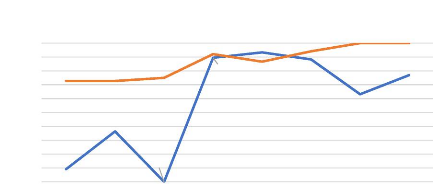
Taux de conformité (en %)
100%
40%
90%
80%
70%
60%
50%
30%
20%
10%
0%
94%
93%
92%
Evolution de la conformité des délais de
retour et de
supervision (en % de conformité)
100% 100%
75%
73% 73%
89%
87%
88%
63%
36%
9%
0%
77%
Figure 21 : Graphique montrant l'évolution de la
conformité des indicateurs aux KPIs
Nous pouvons noter l'influence de la conformité des
délais de supervision, sur les délais de retour. Lorsque la
supervision est réalisée en retard, il est plus difficile de
compenser lorsqu'il faut effectuer les retours. Il est donc important de
maintenir les efforts déployés à travers les actions
correctives mises en place, aussi bien pour respecter les délais de
supervision que de retours, et cela jusqu'à la mise en place d'une
solution durable et pérenne.
Analyse
Cette amélioration a permis de mettre en lumière
un manque de formation du personnel de production pour effectuer certaines
activités. Ces activités étaient réalisées
par d'autres personnes qui étaient formées, mais cela entrainait
une surcharge de travail. En conséquence, ces activités
étaient gérées après les autres activités de
routine, ce qui occasionnait des retards.

58
De plus, l'utilisation d'un outil Lean tel que l'outil de
résolution de problèmes A3 a permis de mettre en avant d'autres
sources de gaspillages, qui n'avaient pas été identifiées
au départ, et s'ajoutent à celles déjà
identifiées plus tôt :
- Un manque de formation du service de production
- Une surcharge de travail du service Assurance Qualité -
Des zones de stockage de l'information
- Des zones d'attente
Chez Novo Nordisk, le respect des BPF est primordial, et au
centre des activités de chacun. Les améliorations mises en place
respectent toujours ce référentiel. L'adoption d'une
démarche d'amélioration Lean, à travers une
résolution systématique des problèmes, a permis de se
rendre compte des sources de gaspillages cachées. Cela a pour effet
d'augmenter les compétences du personnel, d'optimiser la gestion du
temps du service d'Assurance Qualité, et de favoriser l'implication du
service de production dans les retours aux opérateurs.
Nous allons maintenant étudier la résolution du
deuxième problème, concernant l'organisation de la supervision
des APS par l'Assurance Qualité.
Optimisation de l'organisation pour l'observation AQ
Résolution du problème
La clarification du problème, concernant les
délais pour les retours aux opérateurs de productions, a mis un
deuxième problème à jour : la supervision de la production
par l'Assurance Qualité ne respecte pas les délais fixés.
Nous avons réalisé un deuxième A3 traitant de ce
problème.
La phase de clarification, effectuée sur trois APS
début 2019, permet de mettre en avant plusieurs problèmes :
- Les documents nécessaires à la supervision ne
sont pas toujours transmis rapidement à l'Assurance Qualité.
- La répartition des créneaux de supervision au
sein de l'équipe s'effectue trop tardivement après la
réception de ces documents

59
- Les dates limites pour la supervision des APS par
l'assurance Qualité ne sont pas toujours respectées. Tout cela
repousse les retours aux opérateurs, qui sont faits sur la base des
commentaires effectués pendant ces supervisions.
Cela a pour effet de retarder l'approbation des rapports
Mediafill, et donc de retarder la libération sur le marché des
lots insuliniques produit. A terme, des retards de livraisons peuvent avoir des
effets sur la santé des patients.
Des actions provisoires, pour apporter des solutions au plus
vite et éviter que la situation s'aggrave, ont été mises
en place. Le premier problème, concernant la transmission des documents,
contribue aux retards de supervision mais n'en est pas la cause principale. Il
a été résolu provisoirement en demandant les documents aux
processus supports dès que les activités étaient
réalisées, et non après l'écoulement du
délai imparti pour la transmission. De plus, la vigilance sur le
délai de répartition des vidéos a été
accrue, et les créneaux de supervision sont répartis dès
réception. Enfin, les délais fixés pour le visionnage des
activités est rappelé plus régulièrement.
L'utilisation du diagramme d'Ishikawa et l'investigation
menée a permis d'identifier la cause directe des retards : cette
activité n'est pas perçue comme une priorité. Les dates
limites sont alors oubliées ou ignorées, et les informations
nécessaires à la supervision ne sont pas cherchées.
L'emploi de l'outil « 5 Pourquoi » a permis de
comprendre qu'un sentiment de non expertise est à l'origine du
problème : toute l'équipe ne s'implique donc pas, par crainte de
ne pas avoir les capacités suffisantes. Seuls quelques membres de
l'équipe se sentent concernés. En conséquence, il n'y a
pas de communication sur l'importance de cette activité, et donc cela
n'est pas perçu comme urgent et prioritaire.
Il a été décidé de réaliser
un suivi poussé de cette activité. Dans un premier temps, ce
suivi s'est effectué en temps réel, via l'outil Trello. Une carte
été ajoutée au tableau de l'équipe, ce qui
permettait d'aborder de façon journalière cette
thématique, avec l'équipe entière. De plus, la mise en
place d'indicateurs, suivi à l'aide d'un graphique (Annexe 4),
a donné un point de vue macroscopique de l'évolution des
délais.

60
Le plan de formation de l'Assurance Qualité à la
supervision des APS a été revu et amélioré. L'enjeu
est d'augmenter l'efficacité de cette formation, afin d'une part de
gagner du temps et d'autre part de lutter contre le sentiment de non-expertise.
Pour cela, la première tâche a été d'identifier les
redondances entre les différents modules. Ensuite, les activités
sans valeur ajoutée ont été supprimées. La pratique
a été renforcée, avec la visualisation de vidéos
test pour évaluer les capacités des personnes à cette
activité. Enfin, les différentes sections de la formation ont
été pensées de façon à fonctionner
séparément les unes des autres, ce qui permet une meilleure
flexibilité pour la planification.
Résultat obtenu
Sur la dernière activité d'organisation des APS,
nous avons pu observer une réelle amélioration. Malgré une
période d'activité intense et une charge accrue à cause
des vacances d'été, tous les créneaux ont
été supervisés dans les temps. Le délai moyen entre
les activités de production et la fin de la supervision était de
28 jours avant les améliorations, et de 10 jours pour le dernier APS
supervisé. Les actions mises en place sont donc efficaces.
Il est cependant important de préciser que ces actions
ont pour but de contenir le problème, les résultats ne sont donc
pas permanents. Il est nécessaire de mettre en place des solutions
pérennes, qui assureront des effets à long terme.
Pour pérenniser les bonnes tendances, une communication
a été réalisée aux équipes en charge de la
supervision, pour rappeler l'importance d'une telle activité, qui est
une exigence réglementaire et qui conditionne la validation des
processus de production, au regard des réglementations. (Annexe
5)
L'activité de supervision des Mediafill est aujourd'hui
considérée comme une activité non prioritaire, car elle ne
concerne pas toute l'équipe, qui ne s'investit pas de la même
façon. Cette image nuit au respect des objectifs, car d'autres
activités sont considérées comme plus urgentes et plus
critiques. Ce manque d'investissement peut être dû à un
sentiment de non-expertise sur le sujet.
Pour diminuer ce ressenti, deux axes d'actions peuvent
être explorés, selon si le manque d'expertise est réel, ou
seulement ressenti. Dans le premier cas, il est important de garantir que

61
le personnel est suffisamment formé pour effectuer
cette activité. Dans le deuxième cas, un accompagnement sera
nécessaire, afin de permettre aux membres de l'équipe de prendre
confiance en leurs capacités.
Analyse
Encore une fois, l'adoption d'une démarche de
résolution de problème systématique a été
bénéfique. Cela a permis de prendre conscience de l'impact des
délais de supervision dans la gestion des retours aux
opérateurs.
Nous avons pu identifier plusieurs sources de gaspillages :
- Un manque de formation, réel ou ressenti, qui est la
cause racine du problème rencontré. - Des moments d'attente,
lorsqu'il faut attendre des documents non transmis.
- Des stocks d'information, lorsque les créneaux de
supervision ne sont pas répartis dès que cela est possible, ou
bien quand une personne ne transmet pas ses commentaires concernant la
supervision dans les temps.
- Une surcharge de travail, car cette activité n'est
pas régulière et cause des pics d'activité importants.
Nécessaire et Suffisant, communiquer et partager
La démarche Nécessaire et Suffisant a pour but
de faire réfléchir sur le niveau d'exigence attendu sur certaines
tâches, ce qui est nécessaire, pour la conformité avec les
réglementations par exemple, et ce qui est suffisant d'un point de vue
qualité. Elle est animée pendant la réunion
d'équipe quotidienne au board de performance. Le but est de
partager un questionnement rencontré pendant les activités
quotidiennes, et d'obtenir une réponse à la fois satisfaisante
d'un point de vue réglementaire, et qui n'engendre pas de
sur-qualité.
Cette réflexion permet donc de fixer une limite haute et
basse au niveau d'exigence requis :


Sur-qualité
Suffisant
Nécessaire et suffisant
Nécessaire
Sous-qualité

Niveau d'exigence
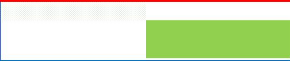
Figure 22 : Représentation schématique du
principe Nécessaire et Suffisant
62
Ma mission a consisté tout d'abord à mettre
cette pratique en commun avec plusieurs autres équipes de l'Assurance
Qualité.
Nous avons ensuite réalisé plusieurs
séances de travail avec un stagiaire d'une autre équipe, afin de
croiser les données obtenues par les deux équipes et les
réponses apportées aux différentes questions. Le but
était de garantir une homogénéité des
réponses apportées, et d'éviter de possibles
dérives, dans le temps mais aussi entre les différentes
équipes de l'Assurance Qualité.
Nous avons ensuite choisi de valider les réponses,
apportées pendant la discussion de l'équipe, auprès
d'experts, en fonction du sujet évoqué. Enfin, la parution
régulière d'une communication (Annexe 6),
diffusée à l'ensemble du service d'Assurance Qualité,
permet de transmettre l'avis des experts, et l'échange entre les
différentes équipes.
Cette activité permet d'éviter de nombreux
gaspillages. Les plus notables sont la sur-qualité et les
défauts, car il faut apporter une réponse qui soit
réellement nécessaire, d'un point de vue réglementaire,
mais aussi suffisante. Cela permet d'éviter une correction superflue par
exemple, ce qui aurait engendré de l'attente et des transports
d'information sans valeur ajoutée.
|