Section 2 : Production et technologie
2.1 Le processus
En résumé, il y a un local de stockage des
matières, puis un atelier de préparation des barbotines et des
émaux qui alimentent deux ateliers de coulage, séchage,
émaillage, cuisson autonomes :
a) les pièces en vitréous
b) les pièces en grès fin.
Le laboratoire et l'atelier de réalisation et
séchage des moules est commun.
Stockage matières
Préparation barbotines
Préparation
Émaux
Broyage
Turbo délitage
Stockage tampon
Atelier vitréous
Coulage traditionnel
Coulage sur banc semi auto
Séchage
Emaillage
Cuisson
Contrôle final
Emballage, stockage et enlèvement ou
expédition
Atelier grès fin
Atelier fabrication moules et séchage
Coulage basse pression
Coulage moyenne pression
Séchage
Emaillage
Cuisson
Contrôle final
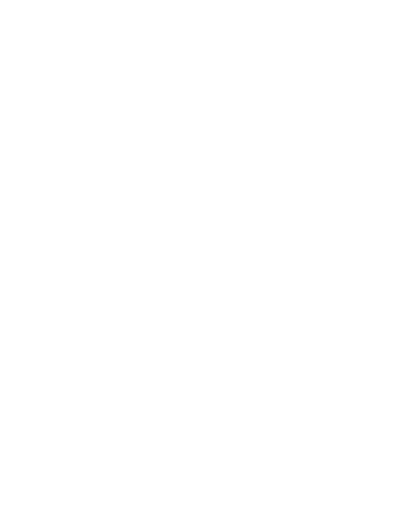
2.2 La technologie
Traditionnellement le coulage des pièces est
réalisé manuellement dans des moules en plâtre. Le
procédé de fabrication autorise une seule coulée par jour
et nécessite un une main d'oeuvre importante.
La technologie de fabrication des articles sanitaires en
céramique a connu une évolution qui consiste en une
mécanisation et un coulage en batterie permettant deux coulées
par jour et un besoin en main d'oeuvre moindre et l'apparition du coulage
moyenne pression.
CERAMIT s'est modernisée en intégrant dans ses
lignes de production ces types d'installation
· 1 machine de coulage moyenne pression des receveurs de
douche et vasque utilisant des moules en résine.
· 2 batteries de coulage bas pression des
éviers.
· Bancs de coulage traditionnels.
Ces deux installations de coulage sont
complétées par l'installation de 2 séchoirs à
chambres, de 4 cabines d'émaillage et de 2 fours intermittents.
Les nouvelles installations de coulage permettent la
fabrication des grosses pièces, receveurs de douche et éviers en
grès fin et augmentent la capacité de l'usine.
2.3 Le fonctionnement des installations
2.3.1 Préparation
barbotine
§ Stockage des matières premières
Les matières premières livrées en vrac
(argiles, kaolins, sable, rognures ou déchets crus) sont chargés
dans deux box de réception ; ensuite elles sont reprises à
l'aide d'un pont roulant à benne et stockées dans des box de
grande capacité.
Les autres matières premières
conditionnées dans des big bag et sacs (feldspath, kaolins et
chamottes) ou en fûts (silicate de sodium) sont stockés au niveau
de l'atelier de préparation barbotine.
L'opérateur du pont roulant prélève les
matières premières des box et les décharge soit dans le
caisson alimentateur pour les argiles, kaolins et rognures, soit dans la
trémie de la ligne quartz pour le sable.
Ces matières sont acheminées par
élévateurs à godets vers les silos de stockage des
matières premières.
§ Pesage des matières premières.
Les composants pour barbotine pour produits en vitréous
ou en grès fin sont prélevés au moyen d'extracteurs des
silos et pesés dans trois trémies balances ; après
pesage, les matières premières sont déchargées sur
un tapis roulant et envoyées soit aux moulins broyeurs pour les
matières dures, soit aux turbo dérayeurs pour les matières
plastiques.
La préparation des barbotines de coulage est ensuite
réalisée en trois phases :
§ Phase 1
La première phase consiste à faire le broyage
humide du sable et du kaolin dans un moulin d'une capacité de 14 tonnes
de matières sèches pendant 18 heures ; après broyage,
le jus de sable obtenu est tamisé à l'aide d'un tamis vibrant
avec une ouverture de mailles de 120 microns puis stocké dans deux cuves
d'une capacité chacune de 50 m3.
§ Phase 2
Cette deuxième phase consiste à délayer
l'argile dans un turbo dérayeur d'une capacité de 10 m3 pendant
1 heure 30 minutes ; le jus d'argile obtenu est tamisé (125
microns) et stocké dans deux cuves, une première cuve de
capacité de 15 m3 pour la préparation barbotine grès fin,
la deuxième d'une capacité de 45 m3 pour la préparation
barbotine pour vitréous.
§ Phase 3
Cette dernière phase consiste à mélanger
dans un turbo pendant une heure un volume de jus de sable et d'argile
délayée avec addition de kaolins et feldspath pour la barbotine
vitréous et kaolins plus chamotte pour la barbotine grès fin.
Les barbotines de deux produits sont préparées
séparément.
La barbotine vitréous dont les paramètres
rhéologiques sont contrôlés par le laboratoire est
tamisée dans un tamis vibrant avec une ouverture de maille de 247
microns et envoyée à l'aide de pompes à pistons vers les
cuves de stockage vitréous pour utilisation par les ateliers de coulage
manuel et semi automatique après contrôle et correction par le
laboratoire.
La barbotine pour grés fin tamisée à
l'aide d'un tamis vibrant est transférée à l'aide d'une
pompe pneumatique à membrane vers les cuves de stockage barbotine
grès fin pour utilisation par les ateliers de coulage basse et moyenne
pression après contrôle et correction par le laboratoire.
2.3.2 Ligne de fabrication
vitréous
§ Coulage manuel
Le recyclage de la barbotine se fait dans la tuyauterie sous
la responsabilité du pompiste, elle est réceptionnée
chaque matin au niveau du poste de travail.
Les moules en plâtre positionnés sur des bancs de
coulage subissent un poudrage au talc sur les parties profondes et sur le
contre moule.
L'opération assemblage et fermeture des moules consiste
à fermer les moules avec des serre- joints et à placer
soigneusement les entonnoirs et les tiges afin d'éviter les pertes de
barbotine pendant l'opération de coulage.
A la veille de l'opération coulage, le responsable du
service coulage est destinataire de la fiche de contrôle des
caractéristiques rhéologiques de la barbotine par le laboratoire.
Le coulage manuel consiste à déverser de la
barbotine dans le moule en plâtre à travers l'entonnoir
placé sur l'orifice d'alimentation.
Après le temps de formation de l'épaisseur de la
couche de tesson par type de produit communiqué par les chefs
d'équipe, les ouvriers commencent le vidage de la barbotine restante
à l'intérieur des moules ; elle est
récupérée dans des conteneurs pour son recyclage au niveau
des cuves de stockage.
Après un temps de repos des produits dans les moules
pour consolidation et durcissement (30 à 90min), le démoulage
commence par l'ouverture des différentes parties du moule et
l'extraction du produit sur plateau suivi des opérations de
perçage des orifices, découpage des bavures et finition en vert
des produits, nettoyage et préparation des moules pour la prochaine
coulée.
Après un séchage primaire de 24 heures au niveau
de la salle de coulage, les pièces font l'objet d'une finition à
sec. Les produits conformes sont chargés sur la chaîne de
transport aérien (chaîne TKT) pour un séchage secondaire
pendant 48 heures au dessus des fours tunnel.
§ Coulage semi automatique (système Shanks)
L'opération consiste à faire le remplissage de
la barbotine sur un ensemble de moules en plâtre reliés les uns
aux autres. On parle de batterie ou de bancs de coulage.
Les moules en plâtre sont placés au dessus des
bancs métalliques de coulage.
Le remplissage de la barbotine dans les moules se fait par
gravité pendant environ 20 minutes.
Après un temps de formation de l'épaisseur
(couche de tesson) sur les parois des moules, l'opération vidage
commence par l'envoi de l'air à l'intérieur des moules.
Avant démoulage, les pièces doivent
séjourner à l'intérieur des moules pendant 2 à 3
heures.
L'opération de démoulage consiste au desserrage
des moules suivi des opérations de finition des pièces.
Ensuite, les pièces extraites manuellement des moules
sont entreposées sur des bancs en bois suivi des opérations de
perçage des orifices, découpage des bavures et finition en vert
des pièces.
Les pièces en cru vert non conformes sont
rebutées et transférées à l'atelier
préparation barbotine pour recyclage.
Après un séchage primaire de 24 heures et une
finition à sec, les pièces sont chargées sur la
chaîne de transport aérien pour un séchage secondaire
pendant 48 heures au dessus des fours tunnels.
§ Séchage des pièces
Le séchage des pièces chargées sur
balancelles est effectué en trois phases :
- Phase 1
Séchage primaire des produits et moules dans la salle
de coulage pendant 24 heures avec une température maximale de 45
°c.
- Phase 2
Séchage secondaire des pièces au dessus des
fours tunnels pendant 24 heures à une température maximale de
100° c.
- Phase 3
Séchage final des pièces au dessus des fours
tunnels pendant 24 heures.
A la fin de l'opération de séchage,
l'opérateur de la chaîne TKT met en marche les balancelles pour
les diriger vers l'atelier contrôle - émaillage.
§ Contrôle - Emaillage
Les pièces séchées arrivent dans
l'atelier de contrôle sur des balancelles de la chaîne TKT de
transport aérien ; sur la fiche VS 01 (retour d'information au
coulage) sont enregistrés les rebuts.
La pièce sèche est prélevée des
balancelles et déposée sur la tourelle de la cabine pour subir le
premier contrôle qui consiste à déceler les défauts
de fabrication, les fissures ainsi que les déformations.
Le deuxième contrôle de précision consiste
à déceler d'éventuelles micro fissures et autres
défauts.
Le contrôleur procède au
dépoussiérage et à la finition des pièces conformes
suivi de l'essuyage avec une éponge humide.
Après l'opération contrôle et finition,
les pièces sont chargées sur les chariots qui seront
dirigés vers les cabines d'émaillage.
L'émaillage des pièces après
contrôle est réalisées dans six cabines
d'émaillage ; les pièces sont prélevées des
chariots et déposées sur le carrousel de la cabine
d'émaillage qui effectue un mouvement de rotation.
Le premier émailleur procède au
dépoussiérage et à l'application de la première
couche d'émail ; ensuite le deuxième applique la
deuxième couche d'émail.
Les pièces ainsi émaillées sont
déposées sur les chariots de stockage.
§ Cuisson
Les pièces émaillées sont reprises des
chariots de stockage et chargées sur les wagons du four tunnel en
respectant le mode et la densité de chargement.
Après contrôle de l'état des wagons, la
conformité du chargement et le dépoussiérage des
pièces émaillées, les wagons sont acheminés
à l'aide d'un transbordeur vers l'entrée des deux fours
tunnels.
La cuisson des produits est assurée par deux fours
tunnel de 116 mètres de long ; la température de cuisson est
de 1230-1240°C avec un cycle de cuisson de 24 - 30 heures.
Le cycle de cuisson dépend de la cadence d'enfournement
qui varie en fonction de la disponibilité des produits à
cuire.
2.3.3 Ligne de fabrication
grès fin
§ Coulage basse pression
L'atelier de coulage bas pression est constitué de deux
batteries à deux bancs et un séchoir moule pour chacun ; la
capacité de cette installation est de 400 pièces/éviers
par jour en deux postes.
La barbotine de coulage est transférée au moyen
d'une pompe à piston de la cuve de stockage barbotine grès fin
vers les deux cuves en acier inoxydable se trouvant à coté des
deux batteries.
Avant l'opération coulage, les moules éviers
installés sur les deux batteries sont poudrés au talc.
Le serrage des moules s`effectue manuellement avec une
pression maximale de 50 bars à l'aide d'une manivelle.
Après contrôle de la barbotine, l'ordre est
donné à l'opérateur de coulage pour placer les tuyaux
d'air ainsi que ceux du remplissage pour alimenter les moules en barbotine, il
ouvre les vannes d'alimentation et le chef d'atelier procède au coulage
automatique à basse pression (1,5 bars) pendant environ 17 minutes.
Après un temps de formation de l'épaisseur sur
les parois des moules, l'ordre est donné pour le vidage des moules
en procédant à l'envoi d'air à 0,16 bars à
l'intérieur des moules suivi de l'ouverture de la vanne de vidage de la
barbotine. L'opération vidage prend environ 20 minutes.
L'opération extraction des pièces ou
démoulage est effectuée 30 à 90 minutes après
consolidation des pièces à l'intérieur des moules. Les
pièces démoulées sont chargées manuellement sur les
chariots.
A l'issue de cette première coulée,
l'opérateur procède au séchage des moules à
52°c pendant 2 heures, pour ce faire, il met en marche les ventilateurs de
brassage et le générateur d'air chaud.
§ Coulage moyenne pression
La machine de coulage moyenne pression est constituée
de 13 moules en résine ; elle est dédiée
principalement au coulage des receveurs de douche de différentes formes
et dimensions.
La capacité est de 400 receveurs de douches /jour en 3
postes en continu.
Les moules liés par un système de suspension
mobile, sont déplacés manuellement jusqu'à leur position
de fermeture, ils sont maintenus en position fermée par
l'intermédiaire d'un vérin hydraulique avec une pression de
serrage de 120 tonnes.
La barbotine de coulage alimente automatiquement un
réservoir en acier inoxydable doté d'une résistance
électrique qui doit maintenir la température de la barbotine
à 50°c maximum.
Le remplissage des moules se fait à basse pression (3
bars) au moyen d'une pompe, le cycle commence par une purge des tuyauteries
vers l'extérieur par la circulation de la barbotine.
Le coulage s'effectue à une pression de 10 bars
maintenue pendant toute la durée du coulage.
A la fin du temps de coulage, la pompe haute pression est mise
à l'arrêt, la barbotine est retirée des moules par
l'introduction d'air comprimé.
Avant démoulage, les pièces doivent
séjourner à l'intérieur des moules pour consolidation.
La fin du cycle de coulage est indiqué par un signal
sur le tableau de commande, à ce moment précis la pression
hydraulique est annulée et le vérin est relâché pour
permettre l'ouverture manuelle des moules.
Les pièces démoulées sont posées
sur les plateaux métalliques, l'opérateur procède à
la finition à l'aide d'une éponge humide ; ensuite les
plateaux sont chargés manuellement sur les chariots pour stockage et
séchage.
§ Séchage des pièces
Deux séchoirs intermittents à deux chambres
assurent le séchage des produits en grès fin ; les chariots
portes pièces sont acheminés manuellement à
l'intérieur du séchoir.
Une fois l'opération chargement des chariots
terminée, les paramètres de séchage sont programmés
selon les conditions :
- Cycle de séchage : 13 - 17 heures
- Température de séchage : 90°c
Après séchage, les pièces sèches
sont déchargées sur des supports.
§ Contrôle - Emaillage
Avant émaillage, les produits secs subissent un
contrôle/finition ; l'atelier contrôle de la ligne grès
fin est constitué de quatre cabines individuelles jumelées.
L'émaillage au pistolet des produits après
contrôle et finition, est assuré par quatre cabines individuelles
jumelées.
Après émaillage et finition, les produits sont
posés soigneusement sur des chariots mobiles.
§ Cuisson
La cuisson des produits émaillés est
assurée par deux fours intermittents ; la température de
cuisson est de 1240 °c avec un cycle de 18-19 heures.
Une fois le cycle de cuisson terminé, le conducteur
éteint les brûleurs et arrête les ventilateurs ;
lorsque la température atteint la valeur de consigne, il procède
à l'ouverture de la porte des fours et à la sortie des wagons qui
seront acheminés par transbordeur vers les lignes de stockage.
2.3.4 Triage -
emballage
A la sortie des fours, les wagons sont dirigés vers la
ligne de déchargement du produit fini.
Le produit fini, déchargé sur un banc de
contrôle, est trié suivant cinq critères de
classification : 1er choix, 2ème choix, 3ème choix, produit
rebuté, re-cuisson.
Les produits triés (à commercialiser) sont
rangés manuellement sur des palettes en bois ; les produits
destinés à l'exportation sont d'abord emballés dans des
boites en carton et ensuite palettisés.
2.3.5 Laboratoire de contrôle
Le laboratoire de contrôle des produits
en cours et en fin de production est équipé
d'appareils de mesure permettant le suivi de la qualité des
matières premières, des produits semi finis et
finis ; des enregistrements sont effectués
à différents stades de transformation des produits. CERAMIT est
certifiée ISO 9001 version 2000 - Système de management de la
qualité, depuis avril 2004.
Le contrôle de conformité du produit fini est
régit par des Normes NA (Algériennes), NF et EN.
Parallèlement au contrôle de laboratoire, des
enregistrements sur fiches sont effectués par les opérateurs
à chaque stade de transformation des produits.
2.3.6 Atelier de
fabrication des moules en plâtre
Les moules en plâtre nécessaires au coulage des
pièces de différentes typologie, sont fabriqués à
partir d'un plâtre d'importation ; les moules ont une durée
de vie supérieure que ceux fabriqués à partir de
plâtres locaux.
De plus, l'utilisation du plâtre d'importation
réduit les rebuts au coulage.
2.4 La productivité
des installations
Ateliers
|
Prévisions 1er semestre
2005
|
Réalisation 1er semestre
2005
|
Taux
|
Préparation barbotine
|
6 153 Tonnes
|
6 194 Tonnes.
|
101%
|
Préparation émaux
|
423 Tonnes
|
357 Tonnes
|
84%
|
Fabrication moules
|
3 221 pièces
|
3 466 pièces
|
108%
|
Produits vitréous
|
213 336 pièces
|
198 040 pièces
|
93%
|
Produits grès fin
|
76 105 pièces
|
59 816 pièces
|
78%
|
Total produit fini
|
289 441 pièces
|
257 856 pièces
|
89%
|
Globalement le taux de réalisation des objectifs est de
89%.
Le taux global de rebut sur la période est de 20% en
vitréous, 27% en grès fin. Toute la matière étant
recyclée, le préjudice se ressent surtout en termes de
capacité et de productivité.
2.5 La productivité du personnel
Avec une production moyenne de 1 983 pièces / jour
travaillé et un effectif total de 557 personnes, la
productivité moyenne est de :
3,6 pièces / jour / personne.
En raisonnant sur le personnel directement lié à
la production (évalué à 287 personnes), ce ratio
devient :
6,9 pièces /jour / personne
2.6 Coût de production (bases 1er
semestre 2005)
Pour procéder à une évaluation dans ses
grandes lignes de la compétitivité de l'entreprise, nous
prendrons le schéma simple du coût de revient du produit,
composé par :
· Coût des matières premières
· Coûts des consommables et pièce de
rechange
· Coût de l'énergie
· Coût du travail.
Les autres composantes du coût de revient sont des frais
de structure tels que les amortissements, frais financiers, services,
impôts et taxes, non mentionnés dans ce chapitre.
2.6.1 Coût des matières
premières
Pour le premier semestre 2005, la production de 257 856
pièces a nécessité un besoin en matières
premières d'un montant de 117 701 KDA (33,1% du prix de revient).
Le coût des matières premières à la
pièce produite est de : 456 DA / pièce,
Soit : 4,96 Euro / pièces.
2.6.2 Coût de l'énergie (gaz et
électricité)
Les consommations sont d'un montant de 7 387 KDA (2,1% du prix
de revient).
Le coût de l'énergie à la pièce
produite est de : 29 DA / pièce,
Soit : 0,31 Euro /
pièces.
2.6.3 Coût des
consommables et pièces de rechange
Les consommations sont d'un montant de 24 377 KDA (6,9% du
prix de revient).
Le coût de l'énergie à la pièce
produite est de : 95 DA / pièce,
Soit : 1,03 Euro /
pièces.
2.6.4 Coût du
travail
Le coût total des frais d'emploi correspondant à
la main d'oeuvre sur la période est de 120 986 KDA (34% du prix de
revient).
Le coût du travail à la pièce produite est
de : 469 DA / pièce,
Soit : 5,10 Euro / pièces.
|