La fabrication d'un cylindre de laminage nécessite, le
plus souvent, des opérations d'usinage complexes et précises, et
le volume de copeaux enlevé par rapport au volume total de la
pièce peut être grand.
La réalisation des cannelures nécessite par
exemple l'emploi de nouvelles technologies. L'usinage par le laser et le
faisceau d'électrons et largement utilisé. La figure
(I.3.5) montre une des procèdes d'usinage d'un cylindre
de laminage.
Le traitement thermique constituant une étape essentielle
pour l'obtention des propriétés d'emploi des cylindres.
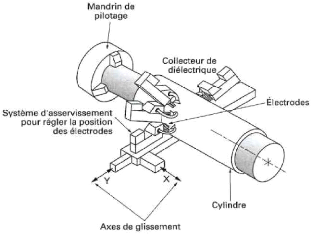
Figure I.3.5 Schéma du dispositif
Spark-Tec pour réaliser des textures par
électroérosion
sur un cylindre de laminoir [16].
En laminage à chaud, les points d'amélioration
du procédé résident dans l'allongement des compagnes de
laminage, la diminution des reprises des cylindres de travail par rectification
et donc dans l'allongement de la durée de vie des cylindres.
La durée de vie d'un cylindre est conditionnée par
la nature et l'amplitude des endommagements qu'il subit.
Ces endommagements sont induits par des sollicitations
d'ordre thermique, chimique et mécanique dépendantes des
caractéristiques de l'emprise et de fait, du laminoir (type de cage,
nuances laminées...). Ils sont globalement repris dans le terme d'usure
qui se quantifie à l'échelle industrielle par la quantité
de matière reprise par rectification à l'issue de chaque
montage.
La position des cylindres dans le train détermine la
prédominance d'une sollicitation par rapport aux autre. Les cylindres en
cage dégrossisseuses sont ainsi plus largement soumis à des chocs
thermiques (usure par fatigue), alors qu'en cages finisseuses, les
sollicitations mécaniques présentent une influence
prépondérante (usure abrasive).
Une voie d'innovation en laminage est alors
l'amélioration des propriétés physicochimiques et
mécaniques des nuances de cylindres de travail à chaud afin
d'optimiser la résistance aux sollicitations thermomécanique et
chimiques subies dans l'emprise.
Ces sollicitations sont :
> Les gradients thermiques supportés par le cylindre
lors du contact avec la bande à laminer et son refroidissement en sortie
d'emprise,
> La réduction appliquée conduisant à
une modification des forces de laminage, > Le cisaillement assurant
l'entraînement de la bande dans l'emprise,
> La température de laminage garantissant la
réduction et les propriétés de la bande, > La
lubrification assurant le refroidissement des cylindres et limitant les efforts
de laminage.
Autant de sollicitations qui vont être à
l'origine de la limitation de la durée de vie des cylindres et donc de
la quantité de rebut de bande laminée selon l'impact des
endommagements des cylindres sur la qualité de la bande.
Ces dégradations peuvent être assemblées en
deux groupes essentiels :
> Dégradations catastrophiques, telles que la rupture
des cols, fissures traversant le corps du cylindre ;
? Détérioration de la surface du cylindre due
à la fatigue thermique/mécanique ou à l'usure.
L'origine de la fatigue thermique est la variation de la
température superficielle dans le cylindre durant chaque rotation. La
fatigue mécanique est due aux tensions causées par la
déformation de la bande et le contact entre les cylindres de travail et
les cylindres d'appui. L'usure se justifie en vertu du glissement existant
entre le cylindre et la bande sous l'effet de la force de laminage, en
présence des particules oxydées dures au niveau du contact.