I.3.3 PROCEDES DE FABRICATION DES CYLINDRES DE TRAVAIL
Parmi les éléments constituant le train de
laminage à bandes, les cylindres de travail sont les plus importants
puisque ce sont eux qui contrôlent la réduction et la forme du
produit laminé. Ils diffèrent par leurs compositions chimiques,
par leurs processus de fabrication et le type de laminage ou ils sont
utilisés.
Les cylindres de travail sont généralement obtenus
à partir d'un processus de moulage:
> Un moulage statique, dans le cas d'un seul matériau.
> Moulage par centrifugation, avec deux coulées.
Les cylindres de travail à haute teneur en chrome et
les aciers rapides se substituent de plus en plus aux fontes nodulaires ou aux
fontes blanches pour des raisons se productivité. Ces cylindres sont
bimétallique avec une âme en acier (ou éventuellement,
quoique de moins en moins, pour des problèmes de rigidité, en
fonte nodulaire) et une périphérie en acier à outils. Ils
sont aussi fabriqués à une échelle commerciale en
recourant à de nouvelles méthodes, telles que les techniques CPC
(Continuos Pouring process for Cladding), ESR (Electroslag Remelting) et HIP
(Hot Isostatic Pressing).
|
coulée par centrifugation
|
|
Permet d'obtenir une bonne liaison sans mélange entre
les deux nuances des cylindres composites, ainsi qu'une structure de
solidification exempte de dendrites et de porosités dans le
matériau de l'enveloppe en acier à outils. Dans ce
procédé, les deux constituants du bimétal sont
élaborés successivement par centrifugation. Les épaisseurs
d'acier à outils sont voisines de 100mm.
C'est un processus utilisé habituellement en Europe et
en Amérique du nord pour la fabrication des cylindres en acier rapide,
alors qu'au Japon entre 30 o/o et 40
o/o des cylindres rapides sont réalisés par
cette méthode [6].
La figure (I.3.1) montre une esquisse du processus de la
coulée par centrifugation horizontale, bien qu'elle puisse aussi
être effectués en position vertical. De cette manière, il a
été obtenu des cylindres composés, constitués par
un noyau et des cols en fonte nodulaire et une couche extérieur,
appelée aussi table de travail du cylindre, en acier rapide, de telle
sorte que sa dureté et sa résistance à l'usure soient
élevées alors que le noyau et les cols sont relativement plus
ductiles et moins résistants. De toute manière, il s'agit d'un
processus de fabrication assez complexe, qui exige un contrôle strict de
ses paramètres.
La machine de coulée par centrifugation a une haute
productivité et peut atteindre la coulée d'un cylindre toute les
deux heures [7].
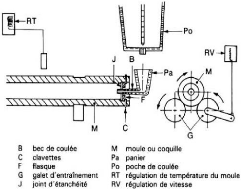
Figure I.3.1 Banc de centrifugation
horizontale.
Il s'agit d'un processus développé au Japon
pour la fabrication des cylindres en acier rapide, ou entre 60 et 70
o/o de ces cylindres sont actuellement fabriqués
par cette technique. Un axe en acier dur, a été
préchauffé au moyen d'une bobine à induction et en suite
le bouillon d'acier rapide est versé, il occupe l'espace existant entre
le moule extérieur en cuivre (voir figure I.3.2) [8].
Une seconde bobine à induction agite le métal
et permet l'union, suite à quoi la région superficielle de l'axe
devrait fondre. Dans ce cas, l'obtention d'une bonne union entre le noyau et la
couche extérieure, nécessite de bien contrôler ce processus
[7] [9].
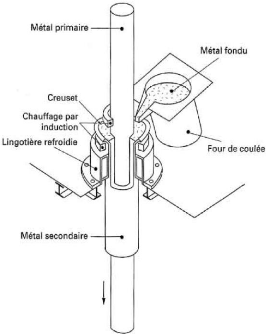
Figure I.3.2 Représentation
schématique du processus CPC [16].
Ce processus est utilisé pour fabriquer de petits
cylindres monoblocs. Un axe en acier résistant a été
utilisé ; il est introduit dans le moule, et rempli ensuite avec de
l'acier rapide en poudre (normalement une poussière
pulvérisée contre un gaz inerte ou l'eau) pour former la couche
extérieur. Celle-ci est consolidée en appliquant
simultanément une haute
pression (au-dessus de 100MPa) et une température
(1000oC) [9] (figure I.3.3). Ainsi, on obtient un cylindre avec une
bonne intégrité et une granulométrie (10-20um).
Le principal problème est la limitation dans la taille
maximale du cylindre obtenu par ce processus. Il n'existe actuellement dans le
monde aucune installation HIP qui pourrait avoir une capacité suffisante
pour produire des cylindres pour train à bandes laminées
à
chaud [8].
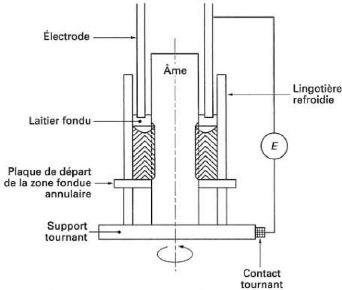
Figure I.3.3 Processus HIP [16].
Ce processus est semblable au CPC, mais le chauffage par
induction est remplacé par un processus ESR. L'électro-scorie
fondue préchauffe et nettoie l'axe solide. Le système agite le
métal ajouté qui se situe sous la scorie, en aidant à
effectuer l'union. La figure (I.3.4) montre la conception
générale du système de revêtement ESR.
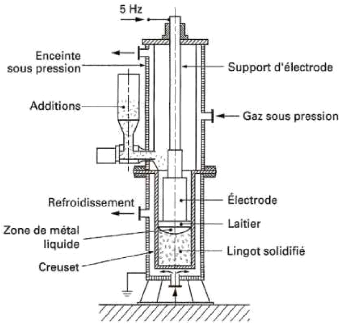
Figure I.3.4 Schéma du
procédé de refusions sous laitier et sous
pression (Système ESR)[16].
|