II.2.2 Etude bidimensionnelle
II.2.2.1 Introduction
Pour notre tubulure, des simulations numériques
bidimensionnelles seront effectuées, afin d'apprécier l'erreur
engendrée par ce type de modélisation, en considération du
gain de temps qu'elle apporte. Les données des matériaux pour ce
type de simulation seront les plus précises dont nous disposons tout en
les introduisant en fonction de la température.
II.2.2.2 Géométrie
On considère une simulation bidimensionnelle sur une
coupe méridienne de la tubulure dans une option de calcul
axisymétrique. Dans ce cas, il existe différents moyens de
représenter l'apport de chaleur imposé. Dans une telle approche,
à chaque passe de soudage, le métal est déposé sur
toute une circonférence en une seule fois. De façon à
reproduire les conditions de bridage exercées par la partie de la
sourdure solidifiée sur le métal en fusion, la
Chapitre II Modélisation du procédé de
soudage d'un tube
44
structure est bloquée axialement pendant la phase de
chauffage simulant le dépôt du métal et
relâchée ensuite pendant la phase de refroidissement
[15].
Pour notre cas, c'est le soudage d'une tubulure de
diamètre extérieur D = 432mm, d'épaisseur e = 23 mm et de
longueur totale L=1000 mm (longueur considérée l = 500mm). Un
chanfrein, situé au milieu de la tubulure, est rempli par le
métal d'apport par un procédé MAG (figure
II.1). La tubulure (métal de base et métal
d'apport) est constituée d'un acier à haut grade X100. Cet acier
ne présente pas de transformation métallurgique. Les distorsions
et les contraintes résiduelles sont déterminées
après chaque passe de soudage.
La figure II.1, montre le modèle
géométrique du métal de base (avant l'opération de
soudage). Pour des raisons de symétrie du cylindre dans le plan (Oyz),
alors il sera souhaitable d'analyser que sa moitié. Ce qui diminue le
nombre d'éléments et de noeuds et par conséquent minimise
le temps de calcul (voir maillage "figure II.5")
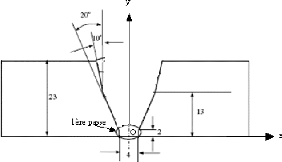
Figure II.1 : Géométrie de la
tubulure (dimensions en mm).
La figure II.2 montre la géométrie de la
tubulure considérée avec 13 passes de soudage. Les surfaces
1,2,...,13 indiquent les 13 passes de soudage.
La figure II.3 représente la moitie de la tubulure, en
fait c'est la partie simulée de la tubulure. La distance d (longueur)
simulée est égale à 0.5m. Pour le cas de soudage
monopasse, toutes
Chapitre II Modélisation du procédé de
soudage d'un tube
les passes de 1 à 13 sont regroupées pour donner
naissance à une seule passe. Le cas de soudage à trois passes
sera réalisé par trois groupes de passes:
? Le premier groupe est formé des passes 1, 2, 3 et 4,
ce qui engendre la création de la première passe.
? Le second groupe est constitué de l'ensemble des
passes 5, 6, 7, 8, 9 et 10, ce qui conduit à la formation de la
deuxième passe.
? Le dernier groupe contient les passes 11,12 et 13, ce qui
mène à la réalisation de la troisième passe.

45
Figure II.2 : Géométrie de la
tubulure avec 13 passes de soudage.
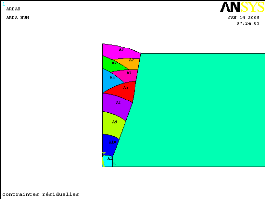
Chapitre II Modélisation du procédé de
soudage d'un tube
46
Chapitre II Modélisation du procédé de
soudage d'un tube
Figure II.3 : Géométrie de la
partie simulée de la tubulure (cas de soudage à 13 passes).
|