SOMMAIRE
REMERCIEMENTS 2
AVANT-PROPOS 3
INTRODUCTION 4
GENERALITES 5
I. GENERALITES SUR LE SECHAGE 5
II. PRINCIPE DU SECHAGE PAR CONDENSATION 6
III. GENERALITES SUR LA CONCEPTION 7
ANALYSE TOPOFONCTIONNELLE 8
I. ANALYSE FONCTIONNELLE 8
II. ANALYSE TOPOLOGIQUE 11
III. PRESENTATION DE LA CONFIGURATION FINALE 14
CHOIX TECHNOLOGIQUES ET DIMENSIONNEMENTS 17
I. DIMENSIONS INITIALES DU COFFRET 17
II. ELABORATION DES MODELES DE CALCUL 19
III. SIMULATION DES EVOLUTIONS D'AIR HUMIDE 24
IV. DIMENSIONNEMENT DES PAROIS ET DES OUVERTURES 28
V. DIMENSIONNEMENT DE LA MACHINE FRIGORIFIQUE 29
VI. DIMENSIONNEMENT DU VENTILATEUR 34
VII. DIMENSIONNEMENT DU CIRCUIT ELECTRIQUE 34
MONTAGE 36
I. MONTAGE DU COFFRET 36
II. MONTAGE DES ECHANGEURS 37
III. MONTAGE DU CIRCUIT FRIGORIFIQUE 37
VI. REALISATION DU CABLAGE ELECTRIQUE 37
DEVIS QUANTITATIF DU SECHOIR 38
PREMIERE MISE EN ROUTE 40
CONCLUSION 41
ANNEXE 1 : ESPACES D'ACCESSIBILITE D'APRES AFNOR 42
ANNEXE 2 : EQUATIONS DE L'AIR HUMIDE 43
ANNEXE 3 : LISTING DU CODE DE SIMULATION 44
ANNEXE 4 : EXEMPLE DE DIAGRAMME DE DETERMINATION DU FACTEUR DE
CORRECTION DE LA PUISSANCE DU CONDENSEUR 51
BIBLIOGRAPHIE 52
REMERCIEMENTS
Nous tenons ici à remercier tous ceux qui de près
ou de loin ont permis la réalisation de ce travail. Ce sont :
Dr KUITCHE Alexis pour la qualité de son encadrement ;
Le Ministère de l'Enseignement Supérieur pour le
financement du projet ;
Sans toute fois oublier tous les techniciens et le personnel de
l'ENSAI de Ngaoundéré, pour toute l'attention qu'ils ont toujours
porté à notre égard.
AVANT-PROPOS
L'Ecole Nationale Supérieure des Sciences
Agro-Industrielles (ENSAI) est l'un des établissements de
l'Université de Ngaoundéré né de la réforme
de janvier 1993. Elle n'était constituée que de la filière
IAA (Industries Agricoles et Alimentaires) jusqu'en 2000, date à
laquelle fut créée la filière MIP (Maintenance
Industrielle et Productique). La formation dure trois ans, et afin de forger au
maximum les ingénieurs qu'elle forme aux contraintes de l'entreprise sur
les plans humains et technologiques, un avant-projet ingénieur est
prévu en dernière année d'étude.
Ce rapport a été effectuer au terme d'un tel
projet, dont le thème était : « Conception et
réalisation d'un séchoir à condensation ».
INTRODUCTION
La conservation des produits agricoles est un problème
épineux dans les pays tropicaux. En effet, les activités
agricoles occupent 80% de la population, et les pertes post-récolte
avoisinent 50% dans certaines régions. Le séchage, moyen de
conservation économique, apparaît donc comme une solution
satisfaisante à ces problèmes de conservation. Aussi, une
nouvelle activité économique est en pleine expansion dans cette
partie du monde : l'exportation vers les pays du nord de fruits tropicaux
séchés, respectant bien sûr des normes de qualité
très contraignantes.
Il apparaît donc tout l'enjeu qu'il y a aujourd'hui dans
nos pays à développer des technologies de séchage de plus
en plus performantes. Ce travail s'inscrit dans cette ligne, et a pour
thème : « Conception et réalisation d'un séchoir
à condensation ». Il s'agira ici de spécifier, de concevoir
et de réaliser un tel séchoir.
Dans un premier temps, des généralités
viendront fixer les idées sur le séchage et le processus de
conception.
Ensuite, une analyse topo-fonctionnelle simplifiée
permettra de spécifier et d'analyser le besoin. Cela nous conduira
directement à la définition d'une configuration pour le
séchoir.
A base de modèles de calcul simplifiés, le
dimensionnement des composants du séchoir suivra.
Puis alors, on présentera les grands points de la phase de
montage et l'essai de première mise en route.
Enfin, un devis quantitatif de matériel sera
établit, résumant ainsi tout le travail
amont.
GENERALITES
I. GENERALITES SUR LE SECHAGE
Un problème généralement posé en
agroalimentaire est celui de la conservation des denrées agricoles. En
effet, placées dans des conditions d'ambiance, celles-ci entrent dans
une phase de putréfaction irréversible, d'autant plus rapide que
l'environnement est malsain. La conservation consiste alors à trouver
des moyens de ralentir autant que possible les transformations internes
à l'origine du pourrissement. Deux méthodes sont
généralement employées :
· Le froid intense : elle consiste à placer les
denrées dans une ambiance saine, d'hygrométrie convenable et
à basse température. Ici, c'est la basse température qui
ralentit la putréfaction ;
· Le séchage : elle consiste à soustraire du
produit une partie de son eau, qui est un grand catalyseur des réactions
de pourrissement.
La grande différence entre ces deux
procédés de conservation se trouve dans l'aspect final du produit
au moment de la conservation. Par congélation (effectué selon les
règles de l'art), on a un produit plus proche de son aspect initial que
par séchage. Par contre, la congélation exige une mobilisation de
machine et d'énergie durant toute la période de conservation, ce
qui n'est pas le cas du séchage, où cette mobilisation est faite
ponctuellement et une fois pour toute.
Il apparaît donc là tout l'intérêt
économique du séchage. Le challenge étant alors de pouvoir
offrir au consommateur un produit séché ayant gardé la
majorité, sinon toutes ses propriétés nutritionnelles et
organoleptiques. C'est dans ce sens que les techniques de séchage
à faible température sont prometteuses.
Le séchage par condensation mis en oeuvre dans ce
travail fait partie de ces techniques de séchage à basse
température. Nous la décrivons un peu plus en détail dans
le paragraphe suivant.
II. PRINCIPE DU SECHAGE PAR CONDENSATION
Comme on là dit plus haut, le séchage consiste
en l'extraction d'une partie de l'eau (environ 85%) d'un produit. Deux
gradients moteurs sont à l'origine de ce transfert de masse : les
gradients de température et d'hygrométrie entre le produit et son
environnement. En gardant une faible température de séchage, on
peut plutôt accentuer le gradient d'hygrométrie. C'est ce qui est
fait dans le séchage par condensation, où l'air circulant sur les
produits sera déshumidifié sur une batterie froide, puis
réchauffée sur une batterie chaude. Le schéma suivant
explicite ce principe.
|
|
|
|
|
Batterie froide de déshumidification
Chambre de séchage des produits
Batterie chaude de chauffage
|
Sens de circulation de l'air de séchage
|
|
|
|
|
|
|
|
|
|
|
|
|
|
|
Figure 0 : Schéma de principe du
séchage par condensation
III. GENERALITES SUR LA CONCEPTION
Dans le fort contexte concurrentiel international actuel, la
nécessité est de plus en plus grande chez les industriels d'avoir
des cycles de conception rapides, économiques et offrants des produits
de qualité aux consommateurs. C'est pourquoi depuis ces dernières
années, de nombreux cercles de réflexion travaillent sur les
possibilités de formalisation de la démarche de conception. C'est
ainsi que des termes tels que l'analyse fonctionnel, l'analyse de la valeur,
l'ingénierie intégré, le soutien logistique
intégré, la gestion de la configuration, ... ont vus le jour. Il
existe même des documents de références en la
matière : norme ISO 9004-7 ou le célèbre concept CALS
(Continuous Acquisition and Life cycle Support) américain.
Dans un projet comme le notre, aucune spécification
normative sur la conduite du projet n'a été faite. Dans de tel
projet, il est alors conseillé de faire une synthèse de la
multitude de principes existants, en fonctions des ressources disponibles, des
délais et de la complexité dudit projet. C'est ce que nous avons
fait dans ce travail.
Ainsi, la démarche de conception a consisté en les
étapes suivantes :
· Analyse fonctionnelle : afin d'expliciter les fonctions
à réaliser ainsi que les tolérances sur leur
réalisation ;
· Analyse topologique : elle se fait en deux étapes
:
o Arborescence produits : ressortant les systèmes
techniques devant
réaliser les fonctions du produits, ainsi que leur
interconnexion ;
o Arborescence topologique : précisant la disposition
spatiale des systèmes
précédents, ce qui permettra d'aboutir à
la configuration finale du séchoir ;
· Dimensionnement et choix technologiques : ici les
systèmes constitutifs du séchoir sont dimensionnés ;
· Montage ;
· Mise en route.
ANALYSE TOPOFONCTIONNELLE
I. ANALYSE FONCTIONNELLE
Cette étude aura pour but de ressortir et bien
délimiter les fonctions à remplir par le séchoir.
1. Recensement des fonctions
Nous allons classer les fonctions en 4 catégories :
· Fonctions principales : ce sont elles qui justifient la
raison d'être du produit ;
· Fonctions de service : elles sont liées à
l'usage du produit. Ce sont ces fonctions qui sont directement visibles
à l'utilisateur, et la qualité du produit en dépend donc
;
· Fonctions techniques : elles sont internes au produit,
et d'elles dépendent le choix et la conception des solutions
technologiques devant satisfaire les fonctions de service ;
· Fonctions contraintes : elles imposent des limites aux
fonctions principales. Elles traduisent surtout les contraintes d'acceptation
du produit en termes de normes, de résistance à l'environnement,
d'esthétique, ... .
Cette classification des fonctions peut être rendue
plus fine, mais compte tenu de la relative faible complexité de la
machine à concevoir, nous nous sommes arrêtés à ces
4 classes.
Les fonctions principales
Ici, nous n'avons qu'une seule fonction principale. Elle peut
s'énoncer en les termes suivants :
Fp : Sécher les produits
agroalimentaires tropicaux les plus courants (fruits et légumes) par
condensation.
Les fonctions de services
Nous les définissons par rapport aux critères
d'acceptabilité du produit par le consommateur camerounais (que nous
connaissons le mieux).
Fs1 : Avoir un encombrement semblable à
celui des appareils ménagers habituels ;
Fs2 : Etre de manipulation aisée ;
Fs3 : Consommer peu d'énergie ;
Fs4 : Sécher une large gamme de produits
;
Fs5 : Etre fiable et facilement maintenable ;
Fs6 : Etre peu coûteux en acquisition
;
Fs7 : Valoriser les matériaux locaux
;
Fs8 : Avoir une grande contenance ;
Fs9 : Sécher rapidement.
Les fonctions techniques
Elles sont définies par rapport aux exigences techniques
d'un séchage domestique par condensation optimal.
Ft1 : Avoir une batterie chaude et une autre
froide ;
Ft2 : Etre à ventilation forcée
;
Ft3 : Avoir un circuit de recyclage d'air ;
Ft4 : Etre de conception monobloc ;
Ft5 : Permettre le contrôle et la
visualisation de la température de séchage ;
Ft6 : Avoir de faibles gradients de
température ;
Ft7 : Etre isolé par rapport aux
transferts de chaleur et de masse d'air ;
Ft8 : Etre connectable à un réseau
électrique domestique.
Les fonctions contraintes
Nous les définissons par rapports aux normes en vigueur
dans le domaine de l'électroménager alimentaire.
Fc1 : Ne pas polluer les produits ;
Fc2 : Avoir un niveau sonore acceptable.
2. Caractérisation des
fonctions
Cette étape a pour but d'énoncer les
critères d'appréciation et les niveaux de flexibilité de
certaines fonctions précédemment définies.
Caractérisation des fonctions de
services
Les spécifications établies ici le sont afin
d'obtenir pour ce nouveau séchoir des performances nettement
supérieures par rapport à celles des autres de même gamme
déjà conçus à l'école.
Fs1 : Les dimensions du séchoir doivent
être semblables à celles d'un réfrigérateur
domestique. De préférence, au tour de :
- Longueur : 60cm
- Largeur : 60cm
- Hauteur : 200cm
Fs2 : Les procédures de mise en
marche, arrêt, réglage de la température de séchage
et suivit du séchage doivent être simples, et exécutable
par toute personne d'un niveau scolaire du primaire ;
Fs3 : La puissance du séchoir doit
être au plus de 2 KW ;
Fs4 : La plage des températures de
séchage doit être de [+30°C ; +50°C] ;
Fs5 : Etre aussi fiable qu'un
réfrigérateur domestique, et ne demander pour sa maintenance
aucune compétence supplémentaire autre que celles requises pour
les appareils électroménager habituels
(réfrigérateur, machines à laver, ...) ;
Fs7 : Utiliser autant que possible du
contre-plaquet pour les parois, et tout autre matériaux local (plaques
d'aluminium, pointes, ... ).
Caractérisation des fonctions
techniques
Ft1 : Utiliser un circuit frigorifique pour
appareils ménagers ;
Ft2 : La vitesse de circulation de l'air doit
être comprise entre [0.5 m/s ; 1.5 m/s] ;
Ft6 : Avoir une baisse de température de
moins de 1°C par claie de séchage ;
Ft7 : L'étanchéité et
l'isolation thermique seront faites de façon à respecter la
contrainte de gradient thermique maximal de la fonction Ft6 ;
Ft8 : Les caractéristiques du
réseau d'alimentation sont 220V-50Hz ;
II. ANALYSE TOPOLOGIQUE
En se basant sur l'analyse fonctionnelle, cette étape
consistera :
· Dans un premier temps à ressortir les
systèmes indispensables pour réaliser les fonctions
précédentes : c'est l'arborescence produit ;
· Ensuite guidés aussi par nos connaissances
scientifiques et technologiques d'une part, et par l'expérience
puisée sur des séchoirs existant d'autre part, nous
élaborerons l'arborescence topologique de notre séchoir
(répartition spatiale des systèmes de l'arborescence produit).
· Dans le même esprit qu'au point
précédent, nous déduirons de l'arborescence topologique un
configuration initiale du séchoir, puis la ferrons évoluer pour
parvenir à la configuration finale, devant être
dimensionnée pour la réalisation ;
1. Arborescence produit
Maintenant que nous connaissons les fonctions à
remplir et leur caractérisation, nous pouvons alors commencer à
penser les différents systèmes qui seront indispensables pour
réaliser ces fonctions. Cette démarche nous a donc conduit
à l'arborescence produit suivante :
Conception et réalisation d'un séchoir
à condensation.
SECHOIR Coffret monobloc Fp
Circuit de recyclage d'air Ft3
Système de réglage et de visualisation de
la température Ft5
Circuit frigorifique
Ft1
Système de ventilation
Ft2
Compresseur
Evaporateur (batterie froide)
Condenseur (batterie chaude)
Autres accessoires du circuit frigorifique
Dispositif d'étanchéité
et d'isolation thermique Ft7

Claies de séchage Fp
Système d'homogénéisation des
températures Ft6
Compartiment de séchage Fp
Alimentation électrique Ft8
Figure 1 : Arborescence produit du
séchoir
3. Arborescence topologique
A partir de cette arborescence produit, on peut commencer
à penser à la disposition spatiale des différents
systèmes. Dans cette démarche nous sommes guidés par
l'expression et la caractérisation des fonctions de services, techniques
et contraintes de l'analyse fonctionnelle, mais aussi par les remarques
suivantes :
· Un écoulement économique d'air chaud doit
être vertical ascendant ;
· L'air doit se réchauffer (au condenseur) avant son
passage dans le compartiment de séchage, et se déshumidifier
(à l'évaporateur ) après ;
· En fonctionnement, le compresseur frigorifique rejette
une chaleur considérable, qu'on pourrait récupérer en
plaçant ce dernier dans le circuit de recyclage d'air.
Après plusieurs séances de réflexion, nous
avons convenu de l'arborescence topologique suivante :
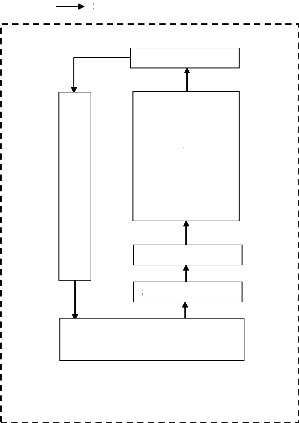
Compartiment de recyclage d'air
Compresseur + accessoires frigorifiques + Alimentation
électrique
: Sens de circulation d'air
Coffret monobloc
Système de réglage et de visualisation de
la température
Système de ventilation
Compartiment de séchage
Evaporateur
Condenseur
+
Figure 2 : Arborescence topologique du
séchoir
III. PRESENTATION DE LA CONFIGURATION FINALE
Arborescence topologique nous a renseigné sur la
disposition spatiale des systèmes. Il reste alors d'en déduire
une configuration initiale, image schématique du futur séchoir.
Nous avons établit cette première configuration, que nous avons
ensuite fait évoluer après plusieurs séances de
concertation. La configuration finale retenue est celle de la figure suivante
:




A -A
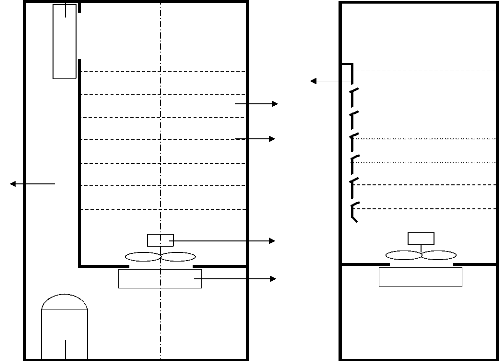
6
8
1
2
3
4
A
5
1. LEGENDE
1- Compartiment de séchage
2- Claies de séchage
3- Système de ventilation
4- Condenseur
5- Compresseur
6- Compartiment de recyclage
7- Evaporateur
8- Système d'homogénéisation des
températures
Figure 3 : Configuration finale du
séchoir
Avant de passer au dimensionnement des différents
systèmes, nous allons d'abord passer à une visualisation en 3
dimensions de cette configuration. Cette visualisation sera très utile
pour apprécier l'influence des diverses décisions de
dimensionnement sur la réalisation (phase de montage), la
maintenabilité (phase d'exploitation) et la présentation finale
du séchoir.
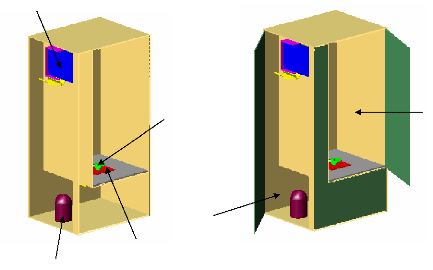
6
4
1
2
3
5
LEGENDE
1- Compresseur
2- Condenseur
3- Ventilateur aspirant
4- Evaporateur
5- Compartiment des visites techniques
6- Compartiment de séchage
Figure 4 : Vue 3D de la configuration
retenue
CHOIX TECHNOLOGIQUES ET DIMENSIONNEMENTS
La configuration finale a déjà été
retenue, et une première visualisation 3D du futur séchoir aussi.
Il reste maintenant à effectuer les meilleurs choix technologiques et
calculer les systèmes constituants le séchoir. Nous serons
guidés en cela par :
· Les spécifications de l'analyse fonctionnelle ;
· Les contraintes de soutien logistique : elles sont
données par les critères de maintenabilité telles que
l'accessibilité, la modularité, l'interchangeabilité, la
démontabilité, ... . L'annexe 1 donne des limites dimensionnelles
pour le critère d'accessibilité, selon les normes
françaises AFNOR;
· Les contraintes d'ingénierie simultanée
: elles nous demandent de toujours vérifier que nos choix seront
disponibles sur notre marché local, et que leur montage sera possible
dans nos ateliers ;
· Les contraintes d'esthétique ;
· La visualisation 3D qui est d'une aide très
précieuse dans cette étape.
I. DIMENSIONS INITIALES DU COFFRET
Des dimensions de départ du coffret sont établies
en se basant sur les spécifications suivantes :
· Son encombrement doit être autour de 600x600x2000
(voir analyse fonctionnelle) ;
· Le compresseur doit être hermétique
à piston, pour rester en conformité avec les appareils de froid
ménager habituels. Sachant que sa puissance absorbée ne peut
excéder 2KW, on peut donc par expérience estimer que son
encombrement sera contenu dans un parallélépipède
rectangle de dimensions 35cm x 20cm x 20cm. C'est sur cette base que seront
fixées les dimensions de l'espace de pose du compresseur.
· Généralement, un espacement acceptable
entre claies est de 10cm.
Les dimensions des ouvertures à prévoir pour
l'évaporateur et le condenseur n'ont pas d'importance à cette
étape.
On est donc conduit aux dimensions des la figures suivantes.
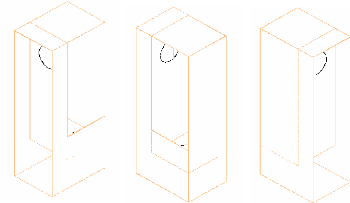
200 500 500
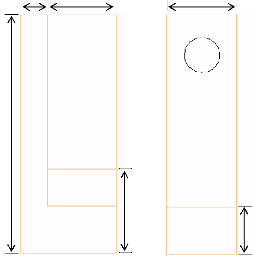
1750
350
620
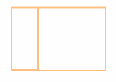
Figure 5 : Principales dimensions du
coffret
II. ELABORATION DES MODELES DE CALCUL
Le dimensionnement des différents systèmes ne
peut se faire que si les principaux paramètres thermiques sont
maîtrisés dans le séchoir. Pour y parvenir, il faut donc
élaborer des modèles de calcul pour prédire
l'évolution de ces paramètres. C'est ce qui est fait dans cette
section. Nous devons donc modéliser les transformations subies par l'air
humide à la traversée de chaque système (voir figures 2 et
3 pour mémoire).
1. Quelques notions fondamentales sur le
séchage
· Eau libre : tout produit à sécher est
poreux. Il existe dans le produit de l'eau sous forme liquide
piégée dans les pores par capillarité, c'est l'eau libre
;
· Eau liée : grâce aux
propriétés hydrophiles du produit à sécher, une
portion d'eau se retrouvera sur et dans les parois des pores (on parle alors
d'adsorption). C'est l'eau liée ;
· Flux-masse : c'est la masse d'eau évaporée
par unité de surface d'échange du produit et par unité de
temps. Elle sera notée par la suite Fm ;
· Teneur en eau base sèche du produit : noté
W, et définie par
W = Masse d'eau dans le produit
Masse de produit sec
|
|
· Porosité d'un amas de produit : notée
å, elle vaut
å = Volume de l'amas - Volume du produit Volume de
l'amas
|
|
· Compacité d'un amas de produit : noté
á, elle vaut
á = Surface d'échanges convectifs
Volume de l'amas
|
|
· Compacité base sèche d'un produit :
elle est définies par
ás = Surface d'échanges convectifs sur le
produit Volume sec du produit
N.B. : Dans la définition des
compacités, il s'agit d'échanges convectifs de chaleur et de
masse.
2. Les différentes phases de
séchage
On distingue 4 principales phases lors du séchage d'un
corps hygroscopique, ce qui est le cas des denrées à
sécher.
· Une période de préchauffage : elle
correspond à la montée en température du produit,
jusqu'à atteindre la température de bulbe humide
caractéristique de l'environnement séchant. Cette période
est généralement très courte au regard du temps de
séchage global. C'est pourquoi nous ne la prendrons pas en compte dans
les dimensionnement ;
· Une période à vitesse constante : ici,
l'eau libre est éliminée à flux-masse constant. Elle est
généralement isenthalpe. L'évaporation s'effectue à
la surface du matériaux, à la température de bulbe humide
de l'environnement séchant. Dans cette phase la température reste
constante, car toute la chaleur apportée est utilisée pour
l'évaporation. Cette phase est la plus exigeante d'un point de vue
énergétique. C'est pourquoi c'est elle qui sera
modélisée pour les dimensionnements.
· Une première période de ralentissement :
elle commence quand le font d'évaporation, qui se trouvait à la
surface du produit, se déplace vers l'intérieur. Là
commence alors une migration d'eau liée, en plus de celle d'eau
libre.
· Une seconde période de ralentissement : le
flux-masse décroît plus rapidement que précédemment.
Ici, l'eau libre est finie et il ne reste plus que l'eau liée qui sera
évacuée très lentement par le phénomène de
diffusion-sorption.
Par OUAMBO. R et DJUIKAM M.F.H.M. ENSAI de
Ngaoundéré, février 2003. 21
3. Equations des bilans dans le compartiment de
séchage
Ces équations décrivent l'évolution des
paramètres d'air humide et du produit à la traversée d'une
claie grillagée, pendant un temps At. Elles sont issues de la
référence [6]. Les hypothèses sont les suivantes :
· Les variations d'humidité absolue et de
température de l'air sont unidirectionnelles et spatiales uniquement
;
· La variation de teneur en eau base sèche des
produits est uniquement temporelle ;
· La vitesse de l'air est constante dans tout le
compartiment de séchage ;
· Les déperditions à travers les parois sont
négligées en première approximation ;
· L'ambiance de séchage est non rayonnante ;
· Les propriétés physiques du produit et de
l'air humide sont supposées constantes ;
· L'influence de la teneur en eau de l'air sur sa chaleur
massique est négligée ;
· Le produit est en phase isenthalpe (sa température
reste constante).
Bilan de masse sur le produit
a Ä
s W = - F m
ñ

á Ä t
s
Bilan de masse sur l'air
Ä W
ñ a 8
U =F
8 m
Ä z
å
1 - å
á
Bilan d'énergie sur le produit
h · ( T 8 - T) = ÄH
v ·Fm

å
1
-
å
ña
á
8
CpaU = · -
h T T (
8 8
Ä
z
ÄT
)
Bilan d'énergie sur l'air
· a
ñs est la masse volumique apparente
du produit sec.
· ña est la masse volumique de
l'air sec. Elle dépend de la température (voir [6]) ;
· U8 est la vitesse de l'air de
séchage ;
· W8 est l'humidité absolue de
l'air humide de séchage ;
· T8 est la température de l'air
humide de séchage ;
· T est la température du produit ;
· h est le coefficient d'échange convectif
à la surface du produit. On là supposé identique
à celui d'une plaque plane traversée par un courant d'air de
vitesse U8
· Cps est la chaleur massique du
produit sec ;
· Cpa est la chaleur massique de l'air
sec, et vaut 1.006 KJ/Kg °C ;
· Pour un produit découpé en lamelles comme
les mangues d'épaisseur e, on a 2
á =
e
4. Modélisation de la traversée de
l'évaporateur (batterie froide)
Ici, l'air humide subira un refroidissement avec condensation.
L'évolution est celle décrite dans la figure suivante.
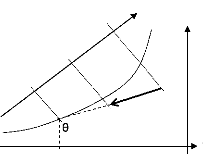
h1
w
h2
hè
1
2
t
èe
h
Figure 6 : Evolution de l'air sur la
batterie froide
èe est la température moyenne de surface de
l'évaporateur. Le problème ici est de trouver w2 et t2 en
fonction de w1 et t1. Pour cela, nous utiliserons les deux équations
suivantes :
· L'efficacité de la batterie (chaleur
échangée sur le maximum échangeable) est
ç =
h h
1 - è
h h
1 - 2 et est de l'ordre de 0.7 ;
· Les points 1, 2 et è sont situés sur la
même droite :
-
w w
-
1 2
wè
w 1
.
t1
-
-
t1
tè
t 2

Ce sont ses deux équations qui ont été
utilisés dans le code de simulation donné dans l'annexe 3.
5. Modélisation du préchauffage sur
le compresseur
Le compresseur n'a pas encore été
sélectionné. Néanmoins, à partir de l'analyse
fonctionnelle, on sait qu'il sera hermétique à piston, et que sa
puissance n'excédera pas 2 KW. Nous ferrons donc nos estimations
préliminaires sur les bases ci-après :
· Compresseur de puissance 1.5 KW et de rendement effectif
0.7 ;
· Toutes les pertes sont transformées en chaleur
;
· Les déperditions à travers les parois sont
négligées dans ce compartiment.
·
m
1
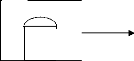
2
·
m
·
m · h - h = - eff
·
( 2 1 ) (1 ç )
Le bilan d'enthalpie donne alors :
6. Modélisation de la traversée du
condenseur (batterie chaude)
A la traversée du condenseur, l'air humide subit un
échauffement simple, décrit dans la figure suivante.
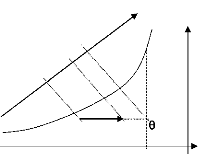
w
hè
h2
h1
1 2
t
èc
h
Figure 7 : Evolution de l'air sur la
batterie chaude
èc est la température moyenne de surface du
condenseur. Les 2 équations à prendre en compte ici sont :
· w2 = w1
· L'efficacité de la batterie (chaleur
échangée sur le maximum échangeable) est h h
-
2 1
ç = et est de l'ordre de 0.7.
h h
-
è 1
Ce sont ses deux équations qui ont été
utilisés dans le code de simulation donné dans l'annexe 3.
III. SIMULATION DES EVOLUTIONS D'AIR HUMIDE
A partir des modèles simplifiés
précédents, on peut alors simuler les évolutions d'air
humide dans le séchoir. Nous avons pour cela écrit un code de
calcul dans le module VBA (Visual Basic pour Applications) d'Excel. Dans
l'éditeur VBA, nous avons
défini des fonctions personnalisées qui ont
ensuite été appelés depuis une feuille de calcul. Ce code
est entièrement listé dans l'annexe 3.
Les données de base de cette simulation sont les
suivantes :
· Produit séché : mangue ;
· Type de tranche de produit : plat 40mm x 40mm ;
épaisseur : 5mm ;
· Longueur caractéristique d'une tranche de produit
pour le calcul du coefficient d'échange thermique : 50mm ;
· Porosité de l'amas de produit dans le
séchoir : 0.9 ;
· Température de séchage : 45°C ;
· Pression atmosphérique : 101300 Pa ;
· Chaleur massique de l'air sec : 1006 J/kg.K ;
· Chaleur latente de vaporisation de l'air à Pat :
2500000 J/Kg ;
· Hauteur d'établissement des échanges sur
une claie : 20mm ;
· Section d'une claie : 0.132m2 ;
· Vitesse de l'air de séchage : 0.5m/s. Cette
vitesse est différente de la vitesse délivrée à la
sortie du ventilateur, à cause des nombreuses pertes de charge ;
· Section de sortie d'une chicane
d'homogénéisation : 0.02m2 (50cm x 40cm) ;
· Section totale de passage après le condenseur :
0.25m2 ;
· Efficacité des échangeurs de chaleur : 0.7
;
· Rendement effectif du compresseur : 0.7 ;
· Puissance présumée du compresseur : 1.5 KW
;
· Température ambiante : 35°C ;
· Humidité relative ambiante : 35% ;
· Coefficient de correction de débit (qui corrige le
fait que le profil de vitesse n'est pas uniforme dans les sections) : 0.6.
La simulation ici se fait pour la phase isenthalpe de
séchage, puisque les modèles sont élaborés pour
cette phase.
Les conditions ambiantes nous permettent de donner une valeur
initiale à l'humidité absolue w, qui est 0.0123 Kg/Kg as. Les
valeurs de régime permanent pour w
et t dans le séchoir ne seront obtenus qu'après
plusieurs itérations en bouclant la circulation d'air.
La température d'attaque sur la première claie
a été fixée à 45°C. Partant de cette claie,
l'objectif de la simulation est d'avoir des températures
d'évaporation et de condensation qui permettront d'avoir à
nouveau ces 45°C à la sortie du condenseur.
Connaissant les températures d'évaporation et
de condensation, la simulation nous fournit en plus les caractéristiques
de l'air humide en tous point du séchoir. C'est donc cela qui nous
permettra de dimensionner les systèmes constitutifs du
séchoir.
Les tableaux suivants, issus de la feuille de calcul Excel
donnent les résultats de la simulation de cette phase de séchage,
en unités SI :

|
|
|
|
Ventilateur
|
|
|
|
Claie 2
|
|
Claie 1
|
|
|
|
|
|
Vitesse sortie 0,5 T entrée
44,948 T entrée 43,855
W entrée 0,0071 W entrée
0,0075
T produits 21,910 T produits
21,900
Flux masse 0,000302 Flux masse
0,000288
T sortie 43,745 T sortie
42,712
W sortie 0,0076 W sortie
0,0080
Claie 3
|
Claie 4
|
Claie 5
|
|
T entrée
|
42,817 T entrée
|
41,831 T entrée
|
40,894
|
W entrée
|
0,0080 W entrée
|
0,0084 W entrée
|
0,0087
|
T produits
|
21,892 T produits
|
21,883 T produits
|
21,876
|
Flux masse
|
0,000274 Flux masse
|
0,000262 Flux masse
|
0,000249
|
T sortie
|
41,732 T sortie
|
40,800 T sortie
|
39,914
|
W sortie
|
0,0084 W sortie
|
0,0088 W sortie
|
0,0091
|
|
Claie 6
|
Claie 7
|
Claie 8
|
|
T entrée
|
40,004 T entrée
|
39,157 T entrée
|
38,352
|
W entrée
|
0,0091 W entrée
|
0,0094 W entrée
|
0,0098
|
T produits
|
21,868 T produits
|
21,861 T produits
|
21,855
|
Flux masse
|
0,000238 Flux masse
|
0,000227 Flux masse
|
0,000216
|
T sortie
|
39,072 T sortie
|
38,271 T sortie
|
37,508
|
W sortie
|
0,0095 W sortie
|
0,0098 W sortie
|
0,0101
|
|
Evaporateur
|
|
Préchauffage
|
Condenseur
|
|
T entrée
|
37,508 T entrée 15,491 T
entrée
|
20,328
|
W entrée
|
0,0101 W entrée 0,0071 W
entrée
|
0,0071
|
T surface
|
6 T sortie 20,328
|
T surface
|
55,5
|
T sortie
|
15,491 W sortie 0,007 T
sortie
|
44,948
|
W sortie
|
0,0071
|
W sortie
|
0,0071
|
T rosée entrée
|
14,156
|
|
|
|
On fait les constats suivants :
· La température d'attaque de la
1ère claie se stabilise à : 44.948°C. C'est
encore celle qu'on a en sortie du condenseur (bouclage réalisé)
;
· L'humidité absolue à l'entrée de la
1ère claie est stabilisée à : 0.0071 kg/kg as,
soit 12% d'humidité relative. Cette valeur est aussi la même
à la sortie du condenseur ;
· Le flux masse diminue fortement entre 2 claie
successive. Pour avoir des temps de séchage uniforme, il faut donc
permuter le positionnement des claies durant le séchage ;
· La température d'attaque diminue d'environ
1°C ent re 2 claies successives ;
· Les chicanes d'homogénéisation font gagner
environ 0.1°C par claie, soit environ 1°C pour l'ensemble du
compartiment de séchage ;
· Un fait étonnant est que la température
du produit (température humide de l'air) reste pratiquement constante
sur toutes les claies pendant cette phase isenthalpe de séchage. Ceci
doit être vérifier par l'expérience.
IV. DIMENSIONNEMENT DES PAROIS ET DES OUVERTURES
Dans la simulation précédente, nous n'avons pas
pris en compte les déperditions par les parois. Maintenant, il faut
dimensionner les parois du séchoir de telle sorte qu'elles n'influence
pas trop les gradients de température.
Le flux perdu à travers les parois est
Ö = Kg S ( T in - T
ex )
avec
Kg 1 e p
+
h i ë p
1
A partir des données suivantes :
· Température extérieure : 35°C ;
· Température intérieure : 45°C ;
· Périmètre de la surface d'échange :
2m (voir Figure 5) ;
· Hauteur de la section d'échange (espace entre 2
claies) : 0.1m ;
· Coefficient de convection intérieur : hi = 16.66 W
/ m2 °C (voir [3]).
On voit que pour une déperdition limitée
à 2W par claie (1000ème de la puissance produite au
condenseur : voir le paragraphe suivant), la résistance de conduction
minimale de la parois est :
ë p
ep m2 °C / W
R min = = 0. 94
Pour une parois en contre-plaquet okoumé, on a ëp =
0.12 (voir [3]). L'épaiseur correspondante est donc ep = 10cm.
Les ouvertures seront aussi en contre-plaquet de 10cm. Un
revêtement intérieur en feuille d'aluminium de 0.3mm permettra de
protéger le contre-plaquet et rendre le séchoir plus sain et
esthétique. Une fine couche d'armaflex d'épaisseur 5mm assurera
l'étanchéité des ouvertures.
V. DIMENSIONNEMENT DE LA MACHINE FRIGORIFIQUE
1. Conditions de base
Ces conditions sont connues à partir de la simulation, et
sont :
2.
Caractéristiques des
échangeurs
|
Evaporateur Condenseur
|
H entrée (KJ/Kg as)
|
63,659
|
38,454
|
H sortie (KJ/Kg as)
|
33,525
|
63,541
|
Puissance (KW)
|
2,507
|
2,087
|
Débit d'eau (Kg/h)
|
0,898
|
|
Caractéristiques du cycle
frigorifique
Pour cette gamme de puissance, le fréon le plus
utilisé est le R134a. C'est donc lui qui sera utilisé pour le
cycle. Nous avons pris un pincement d'environ 3°C par rapport à la
température moyenne de surface, et un rendement isentropique de 0.7 pour
les calculs. La surchauffe totale et le sous-refroidissement ont
été fixés à 5°C (valeur
généralement admise). Les caractéristiques suivantes ont
été calculées dans le logiciel Forane.
Fluide R134a
Paramètres Valeurs Unités
Température d'évaporation 3 °C
Température de condensation 58 °C
Pression d'évaporation 3,256 bar
Pression de condensation 16,037 bar
Taux de compression 4,93
Température à l'aspiration 8 °C
Sous-refroidissement 5 °C
Puissance frigorifique 2,5 kW
Puissance au condenseur 3,44 kW
Débit massique 70,03 kg/h
Rendement isentropique 0,7
COP frigorifique 2,65
Ici, nous avions le choix entre fixer la puissance
frigorifique ou fixer la puissance au condenseur. C'est la première
alternative qui a été retenue. La puissance calculée au
condenseur est alors : 3.44KW, au lieu des 2KW requis dans les conditions de
base. On voit donc qu'un thermostat est indispensable pour ne pas avoir des
montées excessives de température.
3. Sélection du
compresseur
Nous disposons d'un important matériel frigorifique de
récupération. Le challenge ici sera donc d'utiliser au maximum ce
parc. C'est ainsi que à partir de logiciels de constructeurs, nous avons
recherché les matériels pouvant convenir.
Il est ainsi apparut que le compresseur CAJ4492A du
constructeur UH (Unité Hermétique), disponible dans notre parc
pouvait convenir à notre application. Les caractéristiques
étant les suivantes :
Compresseur
Constructeur Unité Hermétique
Modèle CAJ4492A
Fréon R12
Puissance absorbée (KW) 1,011
Intensité absorbée (A) 5,81
Capillaires conseillés 2mm/3,22m
0,070"/1,76m
Le fluide de travail de ce compresseur est le R12. Mais le
R134a sera utilisé sans problème, car il est un fluide de
substitution du R12 valable pour les applications Moyenne/Haute pression.
4. Sélection du
condenseur
Les données de sélection du condenseur sont :
· Température d'entrée de l'air : 20°C
;
· Température de condensation : 58°C ;
· Charge thermique à évacuer : 3.44 kW.
Le constructeur donne généralement une
puissance standard évacuée dans des conditions données.
Pour avoir la puissance correspondante aux conditions du projet, un abaque
(voir Annexe 4) du constructeur permet de trouver le facteur de correction
à appliquer à la puissance standard. On remarque alors que la
puissance évacuée est d'autant plus grande que l'écart At
entre les températures d'entrée de l'air et de condensation est
élevée. Une valeur communément admise pour At est
15°C. C'est cette remarque qui va guider la sélection heuristique
suivante.
Le compresseur dont nous disposons est en fait celui d'un
groupe de condensation. Sachant que ces groupes sont utilisés pour des
applications
Moyenne/Haute Pression comme la notre, alors on sait que pour
un At d'environ 15°C, son condenseur évacuera environ 2.5 kW. On
est donc presque sûr qu'avec notre At de 25°C (voir résultats
de simulation), ce condense ur pourra nous évacuer les 3.4 kW voulus.
Comme le groupe de condensation entier est
récupéré, les seuls composants du système
frigorifique restant à dimensionner sont l'évaporateur, le
détendeur et les tuyauteries.
5. Sélection de l'évaporateur et du
détendeur
Les données de sélection de l'évaporateur
sont :
· Puissance frigorifique : 2.5 kW ;
· Température d'entrée de l'air : 37.5°C
;
· Titre à l'entrée : 0.32.
Pour des raisons économiques, le choix n'a pas
été réalisé dans un catalogue de constructeur. De
par son expérience, notre encadreur nous a recommandé un
matériel de récupération pouvant assurer ces mêmes
conditions.
La sélection du compresseur UH nous a recommandé
des détendeurs à capillaire possibles :
· 2mm/3,22m
· 0,070''/1,76m
Mais des détendeurs thermostatiques à
égalisation interne peuvent aussi être utilisés. Pour cela,
les données de sélection sont :
· Chute de pression : AP = 12.75 bar ;
· Puissance frigorifique : 2.5 kW ;
· Température d'évaporation : 3°C.
6. Sélection des
tuyauteries
Les tuyauteries sont celles données à l'aspiration
et le refoulement du compresseur. Leur caractéristiques sont :
· Tuyauterie Haute Pression : o Diamètre : 5/16
`' ; o Longueur : 3m.
· Tuyauterie Basse Pression : o Diamètre : 3/8 `' ;
o Longueur : 3m.
7. Schéma Fluidique de la machine
frigorifique
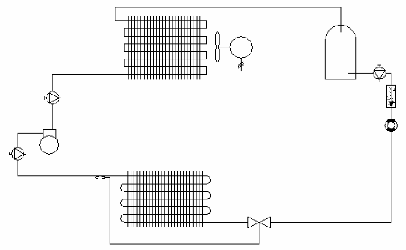
Figure 8 : Schéma fluidique de la
machine frigorifique
VI. DIMENSIONNEMENT DU VENTILATEUR
Le problème ici est d'avoir 0.5m/s comme vitesse de
passage sur les produits, après les nombreuses pertes de charge
rencontrées. Nous ne possédons pas de référence
nous permettant de modéliser ces pertes de charges sur les claies et les
échangeurs. C'est pourquoi nous utiliserons dans un premier temps le
ventilateur fournit avec le groupe de condensation. Des expérimentations
ultérieures permettrons la modélisation de ces pertes de
charge.
Les caractéristiques de ce ventilateur sont les suivantes
:
· Type : aspirant ;
· Alimentation : 208 V - 220 V, 50Hz ;
· Puissance utile : 22 W ;
· Intensité absorbée : 0.54 A ;
· Vitesse de rotation : 1350 tr/min.
VII. DIMENSIONNEMENT DU CIRCUIT ELECTRIQUE
1. Principes de commande et de
régulation
· La régulation sera en tout ou rien, par thermostat
électronique avec afficheur de température ;
· Un voyant vert `Sous-Tension' permettra de
vérifier la présence de tension ;
· Un voyant rouge `Marche Compresseur' permettra d'indiquer
l'état de marche du compresseur, pendant la régulation ou
à l'arrêt ;
· Un commutateur à deux position permettra la mise
en marche ou l'arrêt du séchoir.
2. Emplacement des organes de contrôle et
de signalisation
Ces organes comprennent :
· Le commutateur Marche-Arrêt ;
· Le voyant `Sous-Tension' ;
· Le voyant `Marche Compresseur'
Ils sont disposés comme sur le schéma suivant :
160
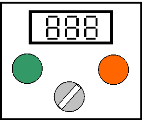
TENSION
A M
140
COMP.


950
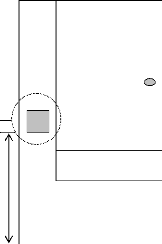
Figure 9 : Emplacement du tableau de
contrôle
3. Schémas
électriques
Le ventilateur n'absorbe que 0.54 A. Il sera donc placé
directement dans le circuit de commande. Le circuit de puissance sera
câblé avec des câbles de 2.5mm2 et le circuit de
commande en 1.5mm2.
MONTAGE
Le montage est une phase délicate, car si des
réalités ont été omises ou négligées
plus en amont, alors un retour en arrière dans le processus de
conception est souvent indispensable.
I. MONTAGE DU COFFRET
On a vu que le coffret est fait en contre-plaquet
d'épaisseur 10 cm, avec un revêtement intérieur en
tôle d'aluminium d'épaisseur 0.3mm.
Le raccordement des plaques est fait par des pointes et de la
colle forte, pour assurer une étanchéité maximale.
La tôle d'aluminium est revêtue sur les faces
intérieures par collage, pour plus d'esthétique. Cette tôle
est aussi utilisée pour le découpage des chicanes
d'homogénéisation.
La portière de face sera maintenue fermée par deux
loketo aimantés, et l'ouverture de visite technique par une targette.
L'armaflex d'étanchéité des ouvertures est aussi
fixé par collage.
La peinture est du type métallisée de couleur
marron, avec un premier revêtement de cintrofer.
Les claies sont grillagées. Les extrémités
des grillages sont prises en sandwich entre des planches de 10 x10.
Le socle est réalisé en cornière de 25.
Avec les remarques ci-dessus et les dimensions de la figure 5,
un cahier des charges a été établi. La réalisation
du coffret a ainsi été confiée à un atelier
spécialisé dans la menuiserie.
II. MONTAGE DES ECHANGEURS
Les deux échangeurs ont été fixés
au bâtit par boulonnage. Un bac de collecte des condensas
étanché par silicone a été fixé sous
l'évaporateur, et un orifice d'évacuation des condensas par tuyau
PVC a été réalisé à l'arrière du
séchoir.
Le ventilateur a aussi été fixé par
boulonnage au dessus du condenseur, après avoir adapté des
supports de fixation convenables.
III. MONTAGE DU CIRCUIT FRIGORIFIQUE
Le montage du circuit frigorifique a été fait en
suivant les étapes suivantes :
· Remplacement de l'huile du compresseur par une huile
compatible avec le R134a ;
· Réalisation des soudures les plus
compliquées à l'extérieur, et remplacement du filtre
déshydrateur ;
· Fixation du compresseur dans son logement ;
· Réalisation du reste des soudures ;
· Fixation du bulbe du détendeur ;
· Mise sous vide des tuyauterie et premier contrôle
des fuites ;
· Charge de l'installation en basse pression,
jusqu'à l'obtention d'environ 10 bars en haute pression. La charge sera
complétée au cours des premiers essais.
VI. REALISATION DU CABLAGE ELECTRIQUE
Le profilé de montage des organes de commande est
placé dans le compartiment de recyclage. Une presse-étoupe
placée sur la face arrière du séchoir assure la fixation
du câble d'alimentation, en 2P+T.
DEVIS QUANTITATIF DU SECHOIR
Nous allons ici lister les éléments
indispensables au montage du séchoir. Les prix ne seront pas
mentionnés, car ils sont variables en fonction des fournisseurs, des
régions et de l'état du matériel (neuf ou seconde main). A
titre indicatif, nous dirons quand même qu'il faut compter environ
750.000FCA pour l'acquisition d'un séchoir à l'état
neuf.
Les caractéristiques de certains éléments
dans le tableau suivant sont données à titre indicatif. Voir le
texte pour des spécifications plus complètes.
Qté Désignation
Caractéristiques
3 Feuille de contre-plaquet 2000x1000; épaisseur 100
4 Tôle d'aluminium 2000x1000; épaisseur 0,3
2 Pot de colle forte 1 litre
1 Paquet de pointes
4 Pommelle Non apparentes, pour bois
1 Poignet
2 Loketo aimanté
2 Armaflex en tube Epaiseur 6; Longueur 2000
1 Profilé Type L, 2500
3 Planche 10x10
30 Vis à bois F/90, 2 - 6
15 Boulons H, M 6 - 20
1 Groupe condenseur Puissance 2 kW, Tc = 58°C
1 Evaporateur Puissance 2,5 kW, Tev = 3°C
1 Détendeur thermostatique AP = 12,75 bar, R134a
1 Tuyauterie 5/16'' - 3m
1 Tuyauterie 3/8'' - 3m
1 Bouteille de fréon R134a; 15 kg
10 Baguette de soudure En cuivre
Matériel de soudure
1 Sectionneur porte fusible 16A, 220V
1 Sectionneur porte fusible 6A, 220V
1 Fusible aM, 10A
1 Fusible gG, 2A
1 Contacteur 10A, bipolaire, 220V
1 Thermostat électronique Sonde PTC, 20 - 80°C
1 Commutateur Marche - Arrêt
1 Voyant 220V, Vert
1 Voyant 220V, Rouge
1 Profilé de câblage électrique Longueur
200
1 Câble Souple 3G2,5, 4m
1 Câble Souple 1G1,5, 10m
1 Presse étoupe Pour câble 3G2,5
10 Bornier 2,5mm2
1 Pot de silicone
1 Tube PVC Diamètre 150, Longueur 500
PREMIERE MISE EN ROUTE
Compte tenu des restrictions économiques, nous avons
utilisé un détendeur thermostatique pour R12. On ne peut donc pas
espérer avoir les conditions complètes de dimensionnement au
cours du premier essai. Les étapes de cet essai sont :
· Vérifier que toutes les vannes 3 voies du circuit
frigorifique sont ouvertes ;
· Fermer tous les sectionneurs du circuit électrique
;
· Brancher la fiche d'alimentation au secteur : le voyant
`Sous-Tension' doit s'allumer ;
· Mettre alors en marche le séchoir : le voyant
`Marche Compresseur' doit s'allumer ;
· On peut alors faire un complément de charge
pour obtenir une condensation suffisante à l'évaporateur. Le
détendeur monté n'a pas permis d'avoir une condensation
satisfaisante. Pour palier à cela, nous avons augmenté la charge.
Dans ce cas, la puissance au condenseur devient si élevée que les
cycles de régulation sont trop courts, empêchant ainsi
l'évaporateur d'atteindre son bon régime. Il faudrait donc
modifier la buse du détendeur, le régler, ou simplement le
remplacer. Il faudrait aussi envisager le montage d'un ventilateur à
l'évaporateur pour augmenter l'efficacité de cet
échangeur. Enfin, on pourrait aussi envisager un renouvellement d'air
CONCLUSION
Dans ce travail, nous avons valorisé la formation
suivie à l'ENSAI de Ngaoundéré depuis 2 ans et demie. Nous
avons émis des spécifications fonctionnelles d'un séchoir
à condensation. Une méthodologie de conception simplifiée,
répondant à nos contraintes de temps à ensuite
été suivie. Cela nous a permis d'aboutir à une
configuration satisfaisante pour le séchoir. Le dimensionnement s'est
fait à partir de modèles habituels d'air humide et de
séchage. Ces modèles ont ensuite été
exploités pour l'écriture d'un code de simulation dans MS Excel.
La phase de montage ne s'est pas faite sans difficultés, car les
restrictions financières nous ont amenés a changer certains choix
fait en dimensionnement. Pour ce fait, bien que la machine fonctionne et que
nous avons même déjà fait des essais de séchage,
elle n'est pas encore au point d'après les dimensionnements
effectués.
Le séchoir conçu est un modèle initial,
et il est évident qu'il doit être continûment
amélioré au fil des ans. Nous espérons que ce travail a
été assez méthodique et explicite pour faciliter les
travaux futurs qui pourraient être réalisés sur ce
séchoir à condensation.
ANNEXE 1 : ESPACES D'ACCESSIBILITE D'APRES AFNOR
ANNEXE 2 : EQUATIONS DE L'AIR HUMIDE
Les équations utilisées sont donc les suivantes
:
· Humidité absolue
(1)
·
(2)
(4)
(5)
Enthalpie du mélange
hs = (1 . 006 +1. 826ù)t
+ 2500ù
· Humidité relative
(3)
?
· Equilibre liquide-vapeur
Log
|
7 . 625 · t
1 0 ( )
Psat = +
241 + t
|
2. 7877
|
|
· Equilibre solide-vapeur
·

Log
2. 7877
9 .7 5 6 · t
1 0 ( )
Psat = +
272 .7 + t
(6)
(7)
Volume spécifique
·
461 (0 . 62
· + ù
' '
=
P
V
) · T
Température humide
2500(wh sat - w)
(1 .006 1 . 826
+
t t
=
h
)
w h
sat
T = t + 273.15
wsat est w au point de saturation correspondant à
une transformation isenthalpe issu du
h
point (t,w).
'# '# '# '# '# '# '# '#
|
ANNEXE 3 : LISTING DU CODE DE SIMULATION
|
'#######################################################
#
MODULE DE SIMULATION DU SECHOIR A CONDENSATION #
#
Les fonctions définies dans ce module ont pour #
but de simuler les évolutions d'air humide #
dans un séchoir par condensation. #
Leur compréhension peut être rendue aisée par
#
la lecture du rapport qui a suivit la conception #
|
'#
|
d'un tel séchoir à l'ENSAI de
Ngaoundéré
|
#
|
'#
|
l'année académique 2002-2003 par
|
#
|
'#
|
OUAMBO T. Raoul et
|
#
|
'#
|
DJUIKAM M. F. H. Marlyse.
|
#
|
'#
|
|
#
|
'#
|
|
#
|
'#
|
Seules les fonctions n'étant pas définies comme
|
#
|
'#
|
Private sont visibles dans le classeur Excel,
|
#
|
'#
|
et sont utiles à la simulation. Les fonctions
|
#
|
'#
|
Private ne sont visibles que dans ce module,
|
#
|
'#
|
et servent pour des calculs intermédiaires.
|
#
|
'#
|
|
#
|
'#######################################################
'
'Section des déclarations du module Option Explicit
'Pression atmosphérique (Pa) Const Pat As Single =
101300
'Longueur caractéristique d'une tranche de produit (m)
Const Lp As Single = 0.05
'Chaleur massique de l'air sec (J/kg.K) Const Cpa As Single =
1006
'Chaleur latente de vaporisation de l'air à Pat (J/Kg)
Const DHv As Single = 2500000
'Hauteur d'établissement des échanges sur une claie
(m) Const Dz As Single = 0.02
'Porosité de l'amas de produit sur les claies Const Poro
As Single = 0.9
'Epaisseur équivalente d'une tranche de produit (m) Const
Epais As Single = 0.005
'Section d'une claie (m2) Const Sc As Single = 0.132
'Section de passage à travers une chicane
d'homogénéisation (m2) Const So As Single = 0.02
'Efficacité des échangeurs de chaleur Const Eff As
Single = 0.7
'Rendement effectif du compresseur Const Neff As Single = 0.7
'Puissance présumée du compresseur (KW) Const Pcomp
As Single = 1.5
'Section totale de passage après le condenseur (m2) Const
Stot As Single = 0.25
'Coefficient de débit dans la section Stot Const Km =
0.6
Private Function Psat(T As Single) As Single
'Pression de saturation de l'air humide If T > 0 Then
'Equilibre liquide-vapeur
Psat = 7.625 * T / (241 + T)
Else
'Equilibre solide-vapeur
Psat = 9.756 * T / (272.7 + T) End If
Psat = Psat + 2.7877
Psat = 10 ^ Psat
End Function
Function Enthal(W As Single, T As Single) As Single
'Enthalpie spécifique de l'air humide (KJ/Kg) Enthal =
(1.006 + 1.826 * W) * T + 2500 * W
End Function
Private Function Wab(HR As Single, T As Single) As Single
'Humidité absolue de l'air humide (Kg/Kg as) Dim Pv As
Single
Pv = HR * Psat(T)
Wab = 0.62 * Pv / (Pat - Pv)
End Function
Private Function Inter(W As Single, T As Single, th As Single) As
Single 'Fonction intermédiaire utilisée dans le calcul
'de la température humide
Dim Wsat As Single
Wsat = Wab(1, th)
Inter = T - 2500 * (Wsat - W) / (1.006 + 1.826 * Wsat)
End Function
Private Function Thum(W As Single, T As Single) As Single
'Température humide
Dim min As Single, max As Single, temp1 As Single, temp2 As
Single
min = -50
max = 100
temp1 = min - Inter(W, T, min) temp2 = max - Inter(W, T, max)
If temp1 * temp2 > 0 Then
MsgBox ("Dichotomie impossible dans le calcul de T humide")
Exit Function
End If
'Boucle de dichotomie, précision 0.001
While (max - min) > 0.001 Thum = (min + max) / 2
temp1 = Thum - Inter(W, T, Thum) temp2 = max - Inter(W, T, max)
If temp1 * temp2 < 0 Then
min = Thum
Else
max = Thum
End If
Wend
End Function
Private Function Cond_th(W As Single, T As Single) As Single
'Conductivité thermique de l'air humide
(W/(m.°C))
Dim A As Single, B As Single, C As Single, D As Single, E As
Single
A = 0.0000000803 * W ^ 4 - 0.000000186 * W ^ 3 + 0.000000151 * W
^ 2 - 0.0000000527 * W + 0.00000000356
B = -0.0000434 * W ^ 4 + 0.000000101 * W ^ 3 - 0.0000818 * W ^ 2
+ 0.0000275 * W - 0.00000146
C = 0.00814 * W ^ 4 - 0.0142 * W ^ 3 + 0.0124 * W ^ 2 - 0.00341 *
W - 0.000677
D = -0.0234 * W ^ 4 - 0.231 * W ^ 3 + 0.112 * W ^ 2 + 0.0231 *
W + 1.9
E = -90.99 * W ^ 4 + 296.75 * W ^ 3 - 497.32 * W ^ 2 + 93.45 * W
+ 572.28 Cond_th = A * T ^ 4 + B * T ^ 3 + C * T ^ 2 + D * T + E
End Function
Function Rho_h(Wa As Single, Ta As Single) As Single
'Masse volumique de l'air humide (Kg/m3)
Rho_h = (461.5 * Wa + 287.1) * (Ta + 273.15) / Pat Rho_h = (1 +
Wa) / Rho_h
End Function
Private Function Visc_cin(W As Single, T As Single) As Single
'Viscosité cinématique de l'air humide (m2/s)
Dim A As Single, B As Single, C As Single, D As Single, E As
Single
A = 0.0000000395 * W ^ 4 + 0.0000000643 * W ^ 3 - 0.0000000154 *
W ^ 2 - 0.0000000969 * W + 0.000000000542
B = 0.0000106 * W ^ 4 - 0.0000151 * W ^ 3 - 0.00000371 * W ^ 2 +
0.00000367 * W - 0.0000000401
C = -0.00277 * W ^ 4 + 0.00437 * W ^ 3 + 0.00124 * W ^ 2 +
0.00153 * W - 0.0043
D = 0.57 * W ^ 4 - 1.71 * W ^ 3 + 1.08 * W ^ 2 - 1.3 * W +
4.97
E = -46.32 * W ^ 4 + 310.73 * W ^ 3 - 1036.13 * W ^ 2 - 60.24 * W
+ 1716.88
Visc_cin = A * T ^ 4 + B * T ^ 3 + C * T ^ 2 + D * T + E
Visc_cin = Visc_cin / Rho_h(W, T)
End Function
Function Débit_m(Wa As Single, Ta As Single, Ua As Single)
As Single
'Débit massique d'air humide dans le séchoir
Débit_m = Km * Rho_h(Wa, Ta) * Stot * Ua
End Function
Private Function H_conv(Ua As Single, Wa As Single, Ta As Single)
As Single
'Coefficient d'échange par convection
Dim Re As Single, Nu As Single
Re = Lp * Ua / Visc_cin(Wa, Ta)
If Re > 100000# Then
'Régime turbulent
Nu = 0.032 * Re ^ 0.8
Else
'Régime laminaire
Nu = 0.66 * Re ^ 0.5 End If
H_conv = Cond_th(Wa, Ta) * Nu / Lp
End Function
Function T_rosée(W As Single) As Single
'Température de rosée
T_rosée = 1013.25 * W / (W + 0.622)
T_rosée = Log(T_rosée)
T_rosée = 5204.9 / (20.9 - T_rosée) - 273.15
End Function
Function T_produit(Wa As Single, Ta As Single) As Single
'Température du produit sur une claie
'Wa => humidité absolue à l'entrée de la
claie 'Ta => température à l'entrée de la claie
T_produit = Thum(Wa, Ta)
End Function
Function Flux_masse(Wa As Single, Ta As Single, Ua As Single) As
Single
'Flux masse sur une claie
'Wa => humidité absolue à l'entrée de la
claie
'Ta => température à l'entrée de la
claie
'Ua => vitese d'ataque de la claie
Flux_masse = H_conv(Ua, Wa, Ta) * (Ta - Thum(Wa, Ta)) / DHv
End Function
Function T_claie(Wa As Single, Ta As Single, Ua As Single) As
Single
'Température de sortie d'une claie
'Wa => humidité absolue à l'entrée de la
claie
'Ta => température à l'entrée de la claie
'Ua => vitese d'ataque de la claie
Dim compa As Single
compa = 2 / Epais
T_claie = H_conv(Ua, Wa, Ta) * (Ta - Thum(Wa, Ta))
T_claie = Ta - T_claie * Dz * compa * (1 - Poro) / (Poro *
Rho_h(0, Ta) * Cpa * Ua)
End Function
Function W_claie(Wa As Single, Ta As Single, Ua As Single) As
Single
'Humidité absolue de sortie d'une claie
'Wa => humidité absolue à l'entrée de la
claie
'Ta => température à l'entrée de la
claie
'Ua => vitese d'ataque de la claie
Dim Tp As Single, Fm As Single, compa As Single
compa = 2 / Epais
Tp = Thum(Wa, Ta)
Fm = Flux_masse(Wa, Ta, Ua)
W_claie = Wa + Fm * Dz * compa * (1 - Poro) / (Poro * Rho_h(0,
Ta) * Ua)
End Function
Function W_entrée(Wa As Single, Ta As Single, Wo As
Single) As Single
'Humidité absolue à l'entrée d'une claie
'Wa => humidité absolue à la sortie de la claie
précédente 'Ta => température à la sortie de la
claie précédente
'Wo => humidité absolue à l'entrée des
chicanes d'homogénéisation Dim S As Single
S = So / (1.5 * Sc)
W_entrée = (Wa + S * Wo) / (1 + S)
End Function
Function T_entrée(Wa As Single, Ta As Single, Wo As
Single, T As Single) As Single
'Température à l'entrée d'une claie
'Wa => humidité absolue à la sortie de la claie
précédente 'Ta => température à la sortie de la
claie précédente
'Wo => humidité absolue à l'entrée des
chicanes d'homogénéisation 'T => Température à
l'entrée des chicanes d'homogénéisation
Dim W2 As Single
W2 = W_entrée(Wa, Ta, Wo)
T_entrée = T - (Wo - W2) * (T - Ta) / (Wo - Wa)
End Function
Function W_evap(Wa As Single, Ta As Single, Tev As Single) As
Single
'Humidité absolue à la sortie de
l'évaporateur
'Wa => humidité absolue à l'entrée de
l'évaporateur 'Ta => température à l'entrée de
l'évaporateur
'Tev => température d'évaporation
Dim K1 As Single, K2 As Single, H2 As Single, Wt As Single
Dim A As Single, B As Single, C As Single, D As Single Wt =
Wab(1, Tev)
H2 = Enthal(Wa, Ta)
H2 = H2 - Eff * (H2 - Enthal(Wt, Tev))
K1 = (Ta - Tev) / (Wa - Wt)
K2 = Ta - K1 * Wa
A = 1.826 * K1
B = 1.006 * K1 + 1.826 * K2 + 2500
C = 1.006 * K2 - H2
D = B ^ 2 - 4 * A * C
D = Sqr(D)
W_evap = (-B + D) / (2 * A)
If W_evap < 0 Then W_evap = (-B - D) / (2 * A)
End Function
Function T_evap(Wa As Single, Ta As Single, Tev As Single) As
Single
'Température à la sortie de l'évaporateur
'Wa => humidité absolue à l'entrée de
l'évaporateur 'Ta => température à l'entrée de
l'évaporateur
'Tev => température d'évaporation
Dim H2 As Single, W2 As Single, Wt As Single Wt = Wab(1, Tev)
H2 = Enthal(Wa, Ta)
H2 = H2 - Eff * (H2 - Enthal(Wt, Tev))
W2 = W_evap(Wa, Ta, Tev)
T_evap = (H2 - 2500 * W2) / (1.006 + 1.826 * W2)
End Function
Function W_prech(Wa As Single) As Single
'Humidité absolue après préchauffage sur le
compresseur
'Wa => humidité absolue à l'entrée du
compartiment de préchauffage W_prech = Wa
End Function
Function T_prech(Wa As Single, Ta As Single, Ua As Single) As
Single
'Température après préchauffage sur le
compresseur
'Wa => humidité absolue à l'entrée du
compartiment de préchauffage 'Ta => Température à
l'entrée du compartiment de préchauffage
'Ua => vitese d'ataque des claies
Dim H2 As Single, Dm As Single
Dm = Débit_m(Wa, Ta, Ua)
H2 = Enthal(Wa, Ta)
H2 = H2 + (1 - Neff) * Pcomp / Dm
T_prech = (H2 - 2500 * Wa) / (1.006 + 1.826 * Wa)
End Function
Function W_cond(Wa As Single) As Single
'Humidité absolue à la sortie du condenseur
'Wa => humidité absolue à l'entrée du
condenseur W_cond = Wa
End Function
Function T_cond(Wa As Single, Ta As Single, Tc As Single) As
Single
'Température à la sortie du condenseur
'Wa => humidité absolue à l'entrée du
condenseur 'Ta => température à l'entrée du
condenseur
'Tc => température de condensation
Dim H2 As Single
H2 = Enthal(Wa, Ta)
H2 = H2 + Eff * (Enthal(Wa, Tc) - H2)
T_cond = (H2 - 2500 * Wa) / (1.006 + 1.826 * Wa)
End Function
ANNEXE 4 : EXEMPLE DE DIAGRAMME DE DETERMINATION
DU FACTEUR DE CORRECTION DE LA PUISSANCE DU CONDENSEUR
BIBLIOGRAPHIE
[1] A. KUITCHE ; Cours de CAO ; ENSAI de Ngaoundéré
; 2003.
|2] E. SAATDJIAN ; Phénomènes de Transferts et
leurs Résolutions Numériques ; Polytechnica ; 1998.
[3] H.J. BREIDERT ; Calcul des chambres froides ; PYC Livres ;
1998.
[4] C. KAPSEU ; Mise au point d'un séchoir pour
oléagineux ; Rapport d'activité à l'issue de de la bourse
d'excellence AUPELF-UREF ; 1997.
[5] AFNOR ; Maintenance Industrielle, Tome 1 : Méthodes
et Outils ; AFNOR ; 1996.
[6] J-P. NADEAU, J-R. PUIGALI; Séchage: des Processus
Physiques aux Procédés Industriels; Lavoisier Tech. et Doc.;
1995.
[7] A. GAC , W. GAUTHERIN ; Le Froid dans les magasins de vente
des Denrées périssables ; PYC Editions ; 1987.
[8] J-F. SACADURA ; Initiation aux Transferts Thermiques ;
Lavoisier Tech. et Doc. ; 1977.
|