
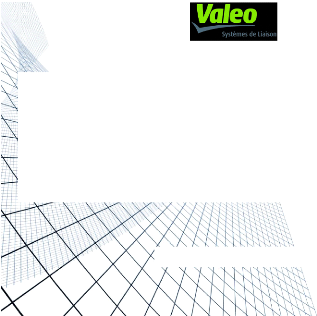
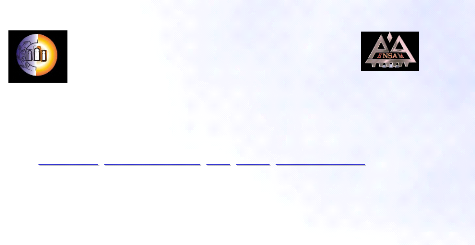
Ecole Nationale
Supérieure d'Arts et
Métiers - Meknès
Projet Industriel de Fin d'Etudes
Présenté
Pour l'obtention du titre :
Université Moulay
Ismaïl
Année Universitaire 2006/2007
Par
Youssef MELLOUKI

litre :
Mise en place d'une méthodologie de management
des proj ets de Modification Série à Valeo.

Jury :
M. Brahim OUHBI Président (ENSAM)
M. Kamal KAYA Encadrant (ENSAM)
M. Taoufik LAAMIRI Parrain du projet (Valeo)
Mme. Imane BOUHADDOU Examinateur (ENSAM)
Mme. Latifa OUZIZI Rapporteur (ENSAM)
PIFE n° :
Aux opératrices et aux opérateurs grâce
à qui, Valeo existe.
REMERCIEMENTS
Mes vifs remerciements à :
Monsieur Taoufik LAAMIRI, Responsable Projet à la
division Equipementier
Modification Série et productivité m'ayant fait
confiance en m'accueillant dans son équipe.
Monsieur Kamal KAYA, Professeur ã l'ENSAM-Meknès
m'ayant encadré dans mon Projet Industriel de Fin d'Etudes.
Messieurs Bruno FLORES, directeur R&D DEP et Aziz
TAHARROUCHTE,
Responsable Qualité projet Montigny, m'ayant fourni les
éléments nécessaires de la
planification des projets sur la plateforme informatique.
Mademoiselle Khadija KOUMIR, formatrice ã l'unité
de production, m'ayant accompagné et formé dans le métier
du câblage dès mon arrivée ã Valeo Connective
Systems.
Monsieur Michel DALIO, ex directeur Qualité DEP, m'ayant
aidé ã formaliser l'amélioration relative à la
génération des codes des étiquettes.
Les membres de l'équipe projets P0 et P1, Amine EZZAOUIA,
Abdelali
SIRAJ EL HAQ, Anas ERRAKKAB, Hicham DAOUD, Khadija AKTEF,
Mohamed BENJELLOUN, Mostafa HARIRI, Saïd ANNI, Madame Sylvie CHARREAU,
Tarik ANZAL, Tarik SANDALI et Zakaria BENABIA, pour leur esprit d'accueil, et
en facilitant mon intégration dans leur équipe, m'ont fait part
d'une attention dont je les remercie vivement.
Mes vifs remerciements aussi aux membres du jury de la
soutenance
ayant accepté d'évaluer ce travail.

Abstract :
Valeo Connective Systems is a matrix management where a plenty
of projects are driven. Among these projects, we find the serial modification
projects which consist on the modification of the product definition already in
production and the corresponding lines. The lack of the management tools for
these projects, the general disorder, the overload of the project team members
and rude research and development cost estimation, are reasons that make these
projects almost never respect the cost, the quality and the time constraints
causing as result losses exceeding 500 K€ per year. To this end, we setup
a project management methodology, made it operational an implant it onto the
project management platform based on PSNext software, eliminating then all the
managerial problems that, none has thought, it can be so fatal for the
company.

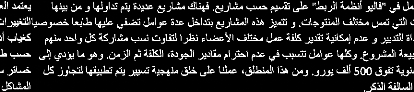
LisTe Des Acronymes, figures eT
Tableaux

Acronymes :
|
AB : Air Bag ;
AC : Actual Cost ;
AMDEC : Analyse des Modes de Défaillance, leurs Effets
et
|
leurs Criticités ;


AQP : Assurance Qualité Projet ;
C/SCSC : Cost/Schedule Control System Criteria;
CD : Critère de Dépendabilité ;
CERN : Conseil Européen pour la Recherche Nucléaire
;
CIP : Constant Innovation Policy ;
CMS : Coût Matière Standard ;
CR : Coût Réel ;
DAD : Direction à Droite ;
DAG : Direction à Gauche ;
DAI : Demande d'Autorisation d'Investissement ;
DAQ : Dossier Assurance Qualité ;
DCP : Division Citroën Peugeot ;
DEP : Division Equipementier ;
DEV : Dossier d'Exigences Valeo ;
DoD : Departement of Defense ;
DoE : Departement of Energy ;
DRN : Division Renault Nissan ;
EI : Echantillons Initiaux ;
EV : Earned Value ;
GCI : Générateur des Codes des Images ;
JPC : Journée Pleine Cadence ;
MEP : Membre de l'EquiÐe Projet ;
NASA : National Aeronautics and Space Administration ;
PDCA : Plan, Do, Check, Act ;
PDP : Plan Directeur de Production ;
PDS : Plan de Surveillance ;
PMI : Project Management Institut ;
PPV : Pretensionneur Pyrotechnique Ventral ;
PQP : Plan Qualité Projet ;
PSA : Peugeot Société Anonyme ;
PV : Programme de Vente ;
R&D : Recherche et Développement ;
SBR : Seat Belt Reminder ;
SIGIP : Système Informatique de Gestion
Intégrée de la
Production ;
TNB : Témoin de Non Bouclage ;
UAP : Unité Autonome de Production ;

VA : Valeur Acquise ;
VC : Valeo Compressors ;
VCC : Valeo Climate Control ;
VCS : Valeo Connective Systems ;
VEC : Valeo Engine Cooling ;
VEMS : Valeo Engine Management Systems ;
VES : Valeo Electrical Systems ;
VLCL : Valeo Low Cost Linear ;
VLS : Valeo Lighting Systems ;
VP : Valeur Prévue ;
VS : Valeo Services ;
VSDS : Valeo Switch Detection Systems ;
VSS : Valeo Security Systems ;
VT : Valeo Transmissions ;
VWS : Valeo Wiper Systems ;
WBS : Work Breakdown Structure.

Figures :

Fig. 01 : Organigramme de la Division Equipementier (p 5) ; Fig.
02 : Les 5 axes de Valeo (p 6) ;
Fig. 03 : Schéma d'une organisation matricielle (p 7) ;
Fig. 04 : Triptyque Qualité, Coût Délai d'un
projet (p 15) ;
Fig. 05 : Diagramme GANTT d'un projet en deux versions de
planning
(p 17) ;
GANTT (p 18) ;
|
|
Fig. 06 : Diagramme Dates-Dates correspondant au diagramme
|

Fig. 07 : Diagramme Dates-Dates à la fin du projet (p 19)
;
Fig. 08 : Tâche exécutée non satisfaisante (p
20) ;
Fig. 09 : Courbe en S d'un projet et écarts
constatés (p 22) ;
Fig. 10 : Tortue de Crosby des projets P0 (p 25) ;
Fig. 11 : Logigramme des projets de Modification Série (p
26 et 27) ; Fig. 12 : Structure générale d'un Projet P0 (p 28)
;
Fig. 13 : Diagramme réseau de la Phase 0 des projets de
Modification Série : Chiff rage (p 33) ;

Fig. 14 : Diagramme réseau de la Phase 1 des projets de
Modification Série : Prépa ration des prototypes ( p 38) ;

Fig. 15 : Diagramme réseau de la Phase 2 des projets de
Modification Série : Prépa ration des moyens (p 41) ;

Fig. 16 : Documents au poste d'une planche de montage (p 42) ;
Fig. 17 : Diagramme réseau de la Phase 3a des projets de
Modification Série : Préparation des Echantillons Initiaux (p 44)
;

Fig. 18 : Diagramme réseau de la Phase 3b des projets de
Modification Série : Modification de tous les moyens série et
lancement de la production (p 46) ;

Fig. 19 : Exemple d'une connexion surmoulée sur un fil
électrique (p

(p 6 et 8) ;
(p 10).
|
|
Tab. 20 : Critères de Dépendabilité d'un
Projet de Modification Série
|
Fig. 20 : Architecture Informatique de PSNext (p 54) ;
Fig. 21 : Schéma organisationnel des projets P0 (p 56)
;
Fig. 22 : Répartition de la charge de travail du projet
B55 VCC par
métier (p 58) ;
Fig. 23 : Aperçu du diagramme GANTT du projet B85 VCC (p
59) ;
Fig. 24 : Aperçu des ressources affectées ã
la tâche de l'élaboration du
planning prévisionnel de la demande du projet B85 VCC (p
59) ;

Fig. 25 : Durée et marge permise d'une tâche (p 59)
; Fig. 26 : Fenêtre de saisie des heures de travail ( p 60) ;
Fig. 27 : Approbation des heures de travail des membres de
l'équipe
de projet (p 60) ;

4) ;

Fig. 28 : Aperçu des courbes en S sur PSNext (p 61) ;
Fig. 29 : WBS Complet d'un Projet de Modification Série (p
1, 2, 3 et
Fig. 30 : Image binaire et code correspondant (p 11) ;
Fig. 31 : Interface de l'application de génération
des codes des
étiquettes (p 12).

Tableaux :

Tab. 01 : Matrice d'antécédence, exemple (p 30)
;
Tab. 02 : Liens entre les tâches, exemple (p 30) ;
Tab. 03 : Liens entre les tâches de la Phase 0 : Chiff rage
(p 32) ; Tab. 04 : Liens entre les tâches de la Phase 1 : Prépa
ration des
prototypes (p 37) ;

Tab. 05 : Liens entre les tâches de la Phase 2 :
Prépa ration des
moyens (p 40) ;

Tab. 06 : Liens entre les tâches de la Phase 3a :
Réalisation des Echantillons Initiaux (p 43) ;

Tab. 07 : Liens entre les tâches de la Phase 3b :
Modification des
moyens (p 45) ;

Tab. 08 : Définition des Critères de
Dépendabilité (p 50) ; Tab. 09 : Exemples de Critères de
Dépendabilité (p 51) ;
Tab. 10 : Exemple de Calcul des Coûts RÈD d'un
projet (p 53) ;
Tab. 11 : Comparaison entre MS Project 2003 et PSNext 8 (p 55)
;
Tab. 12 : Données d'entrée du Cost Driver (p 57)
;
Tab. 13 : Données de sortie du Cost Driver (p 58) ;
Tab. 14 : Matrice d'antécédence de la Phase 0 (p 4)
; Tab. 15 : Matrice d'antécédence de la Phase 1 (p 5) ; Tab. 16 :
Matrice d'antécédence de la Phase 2 (p 5) ; Tab. 17 : Matrice
d'antécédence de la Phase 3a (p 6) ; Tab. 18 : Matrice
d'antécédence de la Phase 3b (p 6) ;
Tab. 19 : Durées de base des tâches d'un Projet de
Modification Série
Table Des matières
Introduction Générale 1
Première partie : de la planification organisationnelle
aux techniques de suivi des projets. 3
Ch. I : Valeo et organisation des projets 4
I-1-Valeo : 4
I-1-1- Historique : 4
I-1-2- Organisation : 4
I-1-3- Organigramme : 5
I-1-4- Les 5 axes : 6
I-1-5- Clients : 6
I-1-6- Chiffres clés : 6
I-2- Organisation des projets chez Valeo : 7
I-2-1- Organisation matricielle : 7
I-2-2- Typologie des projets chez Valeo : 7
I-2-2-1- Projets P3 : 8
I-2-2-2- Projets P2 : 8
I-2-2-3- Projets P1 : 8
I-2-2-4- Projets P0 : 8
Ch. II : Identification et analyse des problèmes de
gestion des projets PO 9
II-1- Gestion actuelle des projets P0 : 9
II-1-1- Introduction : 9
II-1-1-1- Origines des modifications : 9
II-1-1-2- Classes des modifications : 10
II-1-2- Carences managériales de l'organisation des
Ðrojets P0 : 10
II-1-2-1- Vue globale du projet : 10
II-1-2-2- Communication entre les membres de
l'équiÐe Ðrojet : 10
II-1-2-3- Répartition de la charge : 11
II-1-2-4- Passage documentaire entre P1-P0 : 11
II-1-2-5- Coûts des projets : 11
II-2- Pertes constatées : 12
II-2-1- Types des pertes résultantes : 12
II-2-2- Chiffrage des pertes : 12
Ch. III : Techniques de suivi de projets 15
III-1- Management de projet : 15
III-1-1- Projet : 15
III-1-2- Management de projet : 16
III-2- Techniques de suivi des projets : 17
III-2-1- Réunion d'avancement : 17
III-2-2- Diagramme Dates-Dates : 17
III-2-3- Système de gestion de la valeur acquise : 20
III-2-3-1 Coût Réel (Actual Cost) : 21
III-2-3-2 Valeur Acquise (Earned Value) : 21
III-2-3-3 Valeur Prévue (Planned Value) : 21
Conclusion de la première partie : 22
Deuxième partie : Implémentation d'une
démarche de management des projets de
Modification Série 23
Ch. I - Méthodologie de management des projets PO 24
I-1- Tortue de Crosby : 24
I-2- Logigramme/procédure des projets de Modification
Série : 26
I-3- Structure détaillée du projet : 27
I-3-1- Phase 0 : Chiff rage 28
I-3-2- Phase 1 : Préparation des prototypes 34
I-3-3- Phase 2 : Prépa ration des moyens 39
I-3-4- Phase 3a : Réalisation des Echantillons Initiaux
42
I-3-5- Phase 3b : Modification de tous les moyens série
45
I-4- Cost Driver : 47
I-4-1 - Introduction : 47
I-4-2- Critères de Dépendabilité : 49
Ch. II : Plateforme de gestion des projets PO 54
II-1- PSNext : 54
II-1-1- Présentation : 54
II-1-2 - MS Project vs. PSNext : 55
II-2- Plate forme de gestion des projets : 55
II-2-1- Schéma organisationnel : 55
II-2-2 Projet B85 VCC : 56
Conclusion de la deuxième partie : 61
Conclusion Générale 62
Bibliographie/Sitographie 63
Annexes 1
Annexe 1 . WBS com plet du projet 1
Annexe 2 : Matrice d'antécédence de la Phase 0 4
Annexe 3 : Matrice d'antécédence de la Phase 1 4
Annexe 4 : Matrice d'antécédence de la Phase 2 5
Annexe 5 : Matrice d'antécédence de la Phase 3a
6
Annexe 6 : Matrice d'antécédence de la Phase 3b
6
Annexe 7 : Durées de base des tâches d'un Projet de
Modification
Série . 6
Annexe 8 : Critères de DéÐendabilité
d'un Projet de Modification Série .
8
Annexe 9 - GCI (Générateur des Codes des Images) .
10
1- Fonctionnement général . 11
2- Lecture du contenu d'une image . 12
Etiquettes imprimées . 14
INTRoDucTioN GéNéRale
D
|
e nombreuses recherches scientifiques très
poussées sont menées afin de déterminer l'origine de la
création de l'univers. L'époque d'oz il est issu tel que nous le
connaissons, reste mystérieuse
|
jusqu'ã aujourd'hui. En 1950, le physicien anglais Fred
HOYLE a comparé le phénomène de la dilatation et de
l'expansion de l'univers à une explosion gigantesque appelée pour
la première fois Big Bang, lors d'un programme radio de la BBC, the
nature of things.
Le Big Bang désigne l'époque qu'a connu
l'univers il y a environ 13,7 milliards d'années ainsi que l'ensemble
des modèles cosmologiques qui la décrivent. Jusqu'ã
aujourd'hui, il reste établi sous forme de modèles
théoriques. Certains de ces modèles devront être
confortés par l'expérience dans l'objet le plus froid de
l'univers.
En effet, l'objet le plus froid de l'univers se trouve pas
très loin de chez nous, à proximité de la frontière
franco-suisse. Actuellement, il s'agit d'un objet relativement modeste et qui
est le futur grand collisionneur d'hadrons en cours de construction au CERN
(Conseil Européen pour la Recherche Nucléaire) près de
Genève. Ce collisionneur sera le plus grand instrument jamais construit
et devrait nous rapprocher encore un peu plus du Big Bang. Des protons et ions
orbiteront dans un vide presque parfait, à une vitesse proche de celle
de la lumière. Pour qu'il en soit ainsi, le champ magnétique
appliqué à ces particules devra atteindre une intensité
200 000 fois plus importante que le champ magnétique terrestre. Ceci
sera fait en utilisant des bobines à base câbles supraconducteurs
: alliage de niobium et de titane dans une matrice de cuivre qui ne peuvent
présenter une résistance électrique nulle qu'ã de
très basses températures. Pour cela, les électroaimants du
collisionneur devront baigner dans une température de 1,85 kelvin.
Sachant que la température de l'univers intersidéral
s'établit ã quelques 2,7 kelvins, l'instrument sera, pour ce
qu'on en sait, l'objet le plus froid de l'univers...
Mais ã l'heure qu'il est, le chemin ã parcourir
pour que ce projet devienne une réalité est encore très
long et semé de nombreuses difficultés. Si on imagine que
l'instrument pèsera plus du double du poids de la tour Eiffel, sera
d'une sensibilité telle que même les marées seront
perceptibles et que le tout sera enfoui à une centaine de mètres
sous terre, on devine nettement la complexité de la réalisation
de ce projet. Pour en assurer sa réussite, il faut bien
évidemment en maîtriser tous les aspects, aspects techniques mais
aussi programmatiques et financiers, des aspects qui constituent l'essence du
management de projet.
Le management de projet consiste ainsi en l'estimation, la
conception et la planification (structurelle, opérationnelle,
budgétaire, suivi et contrôle) d'un projet afin de respecter les
trois contraintes de Coût, de Qualité et de Délai. A cette
fin, il nous a semblé intéressant de concrétiser ces
différentes phases au niveau de Valeo Connective Systems, objet de notre
sujet de Projet Industriel de Fin d'Etudes. A cet effet, il convient de
souligner que Valeo est structurée en une organisation matricielle par
projets. En outre, plusieurs types
de projets y sont pilotés parmi lesquels, des projets
de Modification Série qui consistent à modifier, pour plusieurs
raisons, la définition d'un produit déjã en production
ainsi que le process correspondant. Au regard du manque de moyens de gestion de
ces projets, de l'estimation « grossière » de leurs
coûts de recherche et développement, d'une désorganisation
quasi-totale, de la surcharge des membres de l'équipe, ces raisons nous
ont incité ã mettre l'accent sur ces projets dans la mesure
où les trois objectifs ne sont que rarement atteint. Dans cette optique,
nous avons focalisé notre mission au niveau de Valeo Connective Systems
sur la mise en place d'une méthodologie de gestion de ces projets de
Modification Série. Par ailleurs, et parallèlement à notre
mission principale, nous avons été
amenés ã développer une application
informatique facilitant l'insertion des logos sur les
étiquettes des faisceaux produits. La méthode
existante étant très complexe, il était parfois difficile
d'insérer un nouveau logo, une exigence souvent demandée par le
client et qui est rarement satisfaite.
Dans cette optique, notre démarche sera articulée
autour de deux
principales parties. La première fera l'objet d'une
étude théorique de l'environnement de
travail et du cadre conceptuel qui sous-entend le management de
projet. Elle comportera
trois chapitres, le premier consistera ã
présenter Valeo et l'organisation des projets, le deuxième
portera sur l'identification et l'analyse des problèmes de gestion des
projets de
Modification Série, puis un troisième qui
présentera les techniques générales de suivi d'un projet.
La deuxième partie quant à elle, se focalisera sur
l'implémentation de la démarche à suivre dans le cadre de
la gestion des projets de Modification Série. Celle-ci comportera deux
chapitres, un premier relatif à la méthodologie et un
deuxième portant sur la plateforme
informatique de gestion des projets concernés pour finir
par détailler l'application de
génération des codes des étiquettes en
annexe.
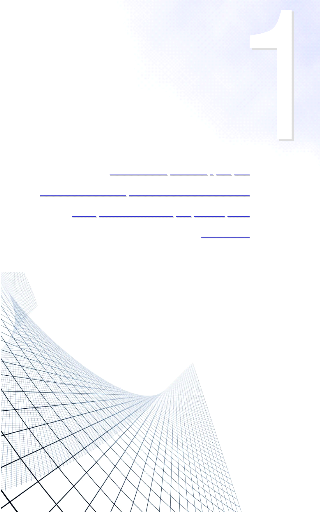
Première partie
PREMièRE pARTiE : DE LA
pLANificATioN
oRgANisATioNNELLE
Aux TEcHNiQuEs DE suivi DEs
pRojETs.

1 Source :
http://fr.wikipedia.org/wiki/valeo,
http://www.valeo.com/automotive-supplier/jahia/lang/fr/pid/12
Ca. I : VAlEo Et oRGANisAtioN DEs
pRojEts
|
Ce premier chapitre du rapport a pour objet de
présenter le contexte du sujet, à savoir
la présentation de Valeo, l'organisation des projets et les
typologies existantes.
|
I- 1-Valeo :
I-1-1- Historique :
Valeo est une grande entreprise multinationale
spécialisée dans les équipements et sous ensembles de
l'industrie automobile. Elle a été créée en 1834
ã Seine-Saint-Denis sous le nom de Société Anonyme
Française du Ferodo pour devenir Valeo par la suite. Elle s'occupait de
la production et la distribution des garnitures de freins et d'embrayages sous
licence de la société anglaise de Ferodo (Ferodo
UK)1.
La société a cherché à se
diversifier à partir des années 1960 où elle a
commencé à produire des systèmes de freinage (1961), des
systèmes thermiques (1962), des composants et systèmes
électroniques (1963), systèmes d'éclairage (1970) et
électriques (1978).
En mai 1980, la société prend le nom de Valeo,
« je vais bien » en Latin, date ã partir de laquelle, elle
atteint la dimension d'un groupe international parmi les plus importants du
secteur des équipements automobiles, en adoptant une stratégie de
redéploiement externe (acquisition) très intense.
Aujourd'hui, le groupe Valeo est composé de 12 branches
pour la plupart issues de rachats d'entreprises étrangères du
secteur.
I-1-2- Organisation :
Valeo est présent dans 26 pays et dispose de 130 centres
de production, 65 centres de Recherche & Développement et 9
plates-formes de distribution.
Le groupe se divise en 3 grands pôles d'activités,
branches industrielles et une branche Valeo Service répartis comme suit
:

Pôle aide à la conduite :
Commutation et Systèmes de Détection (VSDS),
Eclairage Signalisation (VLS), Système d'Essuyage (VWS)
;
Pôle efficacité de la propulsion :
Systèmes de Contrôle Moteur (VEMS),
Système Electrique (VES), Compresseurs (VC),
Thermique Moteur (VEC), Transmissions (VT) ;
Pôle amélioration du confort :
Sécurité Habitacle (VSS), Thermique Habitacle (VCC),
Systèmes de Liaison (VCS).
Et enfin, la branche Valeo Service (VS) dédiée
au marché de la deuxième monte et la commercialisation des
produits Valeo auprès des professionnels (concessionnaires, garagistes,
distributeurs des pièces détachées).
I-1-3- Organigramme :
La branche de Valeo installée au Maroc est Valeo
Connective Systems (Valeo Systèmes de Liaisons). Cette même
branche est formée de plusieurs divisions (DRN : Division Renault
Nissan, DCP : Division Citroën Peugeot...). L'organigramme de la
Division
Equipementier (la Division où j'ai effectué mon
Projet Industriel de Fin d'Etudes) est Ðrésenté
comme suit :
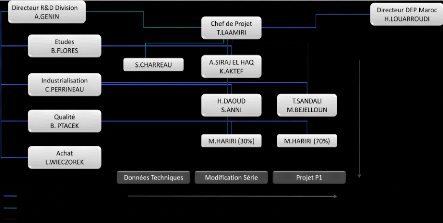
Fig. 1. Organigramme de la Division
Equipementier
Organisation Service Projets Bouskoura.
La Division Equipementier est structurée en une
organisation matricielle par projets (voir organisation matricielle page :
7).
I-1-4- Les 5 axes :
Valeo a conçu et applique la méthode dite des 5
axes2 (Voir Fig. 1),
fondation de la culture d'entreprise du groupe. Elle vise
ã atteindre la satisfaction du client par l'atteinte du zéro
défaut quel que soit le type de produit et le lieu de production.
Les 5 axes sont :

L'implication du personnel ;
Le système de production ;
L'intégration des fournisseurs ; L'innovation constante
;
La qualité totale.
La Qualité Totale
Innovation Constante
|
|
Intégration des Fournisseurs
|

|
2 Source : Valeo - CIP Constant Innovation Policy, Paris,
2004.
|
6
|
Système de Production
Implication du Personnel
Fig. 2. Les 5 axes de Valeo.
I-1-5- Clients :
Valeo équipe les principaux constructeurs automobiles
internationaux, parmi lesquels nous pouvons citer :
BMW, DailmerChrysler, Fiat, Ford, General Motors, Honda, Porsche,
Peugeot Citroën, Renault, Nissan, Toyota, Volkswagen Group.
I-1-6- Chiffres dlés :
70 400 collaborateurs représentant ;
Chiffre d'affaires en 2005 : 9,9 milliards d'euros ;
Répartition du C.A par ligne de produits :
Electronique
|
:
|
63
|
% ;
|
Thermique
|
:
|
30
|
% ;
|

Transmissions : 7 %.

6,6 % du chiffre d'affaire du total des Ðroduits de
l'activité du grouÐe est destiné à la Recherche et le
Développement.
:
I-2- Organisation des projets chez Valeo

I-2-1- Organisation matricielle :
Une organisation matricielle3 est un organigramme
bidimensionnel dans lequel les ressources dépendent de Ðlusieurs
objets d'organisation suÐérieure. Sont associées dans une
organisation matricielle, deux types de structures : une structure horizontale
représentant les liens fonctionnels et une structure verticale
représentant les liens hiérarchiques (voir Fig. 3 ci dessous).
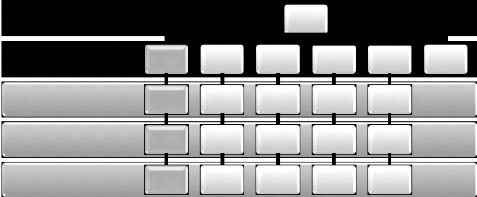
Equipe Projet 1
Equipe Projet 2
Equipe Projet 3
Directeur
Projet
Chef de projet 1
Chef de projet 2
Chef de projet 3
Directeur Marketing
Ressource
1
Ressource
2
Ressource
3
Ressource
1
Ressource
2
Ressource
3
Directeur
Achat
Direction générale
Directeur Production
Ressource
1
Ressource
2
Ressource
3
Ressource
1
Ressource
2
Ressource
3
Directeur Vente
Etc.
Fig. 3 : Schéma d'une organisation
matricielle
Dans une organisation matricielle par projets, chaque
ressource est experte dans son métier, travaille sous les instructions
de son supérieur fonctionnel mais évaluée par son
supérieur hiérarchique qui est un super expert dans la même
fonction.
Les matrices sont les seules organisations qui peuvent
régulièrement créer des produits complexes techniquement
tels que des avions ou des fusées.
I-2-2- Typologie des projets chez Valeo :
La structure organisationnelle chez Valeo est de type
Matricielle par Projets. En effet des équipes de travail
pluridisciplinaire de recherche et développement mènent les
projets qui leur sont affectés. Ces projets sont classés en
quatre types4 :
8

I-2-2-1- Projets P3 :
Les projets P3 ont pour objectif l'investigation et la
viabilité de nouvelles idées pour des technologies,
systèmes, fonctions, modules, composants ou logiciels. Ils permettent
d'obtenir un premier feedback marché.

Pour favoriser la créativité, les projets P3 n'ont
aucune structure prédéterminée ni de phases.
I-2-2-2- Projets P2 :
Les projets P2 se focalisent sur la création de
nouveaux standards génériques validés qui seront
utilisés ultérieurement dans les projets P1.
|
Ces standards portent sur les systèmes, les modules, les
composants et les logiciels.
Les projets P2 sont structurés en 5 phases.
|
I-2-2-3- Projets P1 :
Développent des applications client spécifiques.
Les projets P1 doivent être basés sur des standards
génériques validés (P2) ou des technologies
déjà appliquées dans la production série.
Les projets P1 sont structurés en 6 phases.
I-2-2-4- Projets P0 :
Il s'agit d'une modification majeure sur un produit existant
déjà en production pour la (les) même (s) application (s)
clients développée (s) en P1.
Ces projets n'ont ni méthodologie, ni plateforme de
gestion dans la DEP (Division Equipementier) et c'est ce qui a fait justement
l'objet du Projet de Fin d'Etudes.
En somme, les typologies des projets ainsi définies,
nous nous focaliserons dans le reste du rapport sur les projets de Modification
Série (P0) en commençant tout d'abord par identifier et analyser
les problèmes de gestion de ces projets puis présenter les
techniques générales de suivi d'un projet pour résoudre
finalement les problèmes dégagés dans le diagnostic
à base de ces techniques.
Ca. II : IDENTiFicATioN ET ANALysE DEs probLèmEs
DE gEsTioN DEs

projETs PO
|
Le deuxième Chapitre quant à lui, portera
sur les problèmes managériaux existants dans l'organisation
des projets de Modification Série présentant ainsi un
justificatif du suet du Projet Industriel de Fin d'Etudes.
Nous traiterons, en premier lieu, les origines des projets de
Modification Série, leurs classes et les pertes financières
résultantes.
|

II-1- Gestion actuelle des projets P0 :
II-1-1- Introduction :
Comme vu dans les définitions de la première
partie, les projets P0 concernent une modification majeure sur un produit
existant déjà en production développé en P1.
II-1-1-1- Origines des modifications :
Les projets de Modification Série ont plusieurs
origines classées en trois grandes catégories : demande
interne, demande client ou
événement fournisseur. Les origines des
modifications sont listées comme suit :
Demande explicite du client ou évolution d'une norme
client ;

Evolution d'une réglementation, d'une directive, d'une
norme, d'un standard ou d'une spécification interne ;

Productivité produit/process. L'objectif ici est de
réduire le prix du produit soit en agissant sur le process (exemple : en
réduisant le nombre d'opérations lors du montage du faisceau et
par la suite obtenir un temps de montage inférieur) ou en agissant sur
le produit lui-même (exemple : un composant approvisionné
auprès d'un fournisseur peut être fait chez Valeo et coûtera
moins cher) ;


Non-conformité interne, réclamation client ou
retour garantie ;
Proposition d'amélioration touchant au produit ou au
process ;
Modification d'un composant du produit par le fournisseur.
9

II-1-1-2- Classes des modifications :
Dans le jargon de gestion des projets de Modification
Série, on parle de 3 classes de modification :

Classe A : Introduction d'un nouveau composant hors
connexion ou composant affectant la fonction sécurité ;

Classe B : Modification dimensionnelle ou habillage sans
introduction de nouveaux composants.

Classe C : Toutes modification ne faisant partie ni de la
classe B ni C (suppression d'une branche d'un faisceau par exemple) ;
Les projets de classe A (respectivement C) représentant
une modification majeure (respectivement mineure), cette classification sert
à gérer les priorités lors des conflits entre les projets
ou en cas d'urgence.
II-1-2- Carences managériales de l'organisation des

projets P0 :
Le nombre de projets P0 menés en parallèle peut
atteindre 12 voir 14 projets de modification. L'absence de moyens de gestion de
ces projets, l'estimation grossière des coûts des projets, une
désorganisation quasi-totale, des membres de l'équipe projet en
surcharge? sont des raisons, entre autre, qui font que les projets P0
dépassent de loin à la fois les délais prescrits et les
budgets alloués, et causent par la suite des pertes énormes.
Les failles managériales de l'ancienne gestion des
projets P0 constatées sont les suivantes :
II-1-2-1- Vue globale du projet :
Absence d'une vue globale du projet pour l'ensemble des
intervenants dans le projet. Toute l'équipe travaille suivant les
demandes du client ce qui rend les délais très serrés pour
les satisfaire car aucune préparation préalable n'a lieu.
Exemple : si le client demande des Echantillons Initiaux, il
faut avoir déjà créé leur nomenclature
complète sur le système informatique pour pouvoir les produire.
Si cette tâche n'a pas été faite avant, le délai
sera serré pour pouvoir effectuer, ã la fois cette action (ou, en
général, toutes les actions devant être faites avant la
réalisation des Echantillons Initiaux), et la réalisation des
Echantillons Initiaux.
II-1-2-2- Communication entre les membres de
l'équipe


10

projet :
La communication au sein de l'équipe (connaitre
l'état d'avancement d'une activité donnée ou le
résultat d'une tâche donnée) est difficile d'une part
ã cause de la

délocalisation (certains membres de l'équipe
sont en France et d'autres au Maroc) et d'autre part parce que cette
communication est basée principalement sur des moyens informels et des
informations non centralisées, ce qui induit très souvent
à des informations erronées ou non à jour.
II-1-2-3- Répartition de la charge :
Vu qu'il n'y a aucun plan de charge pour les ressources du
projet, une mal répartition de la charge du travail était
constatée. Certains membres de l'équipe sont souvent en surcharge
alors que d'autres ne travaillent que rarement à plein temps.
II-1-2-4- Passage documentaire entre P1-P0 :
L'un des principaux points bloquants dans l'organisation des
projets P0 est le passage documentaire entre projets P1 et P0. Un mauvais
passage documentaire (Dossier du projet, Dossier Assurance Qualité,
Plans du faisceau...) au lancement du projet fait que le travail des membres de
l'équipe P0 reste dépendant des équipes projets P1 et par
la suite, une simple absence d'un membre des équipes P1 (congé
maladie ou mission) retardera considérablement certaines tâches du
projet P0.
II-1-2-5- Coûts des projets :
Le coût d'un projet de modification, présenté
au client avant son lancement, est décomposé en deux parties :


Coût des investissements : il s'agit du coût des
nouveaux moyens à acheter si nécessaire (outils, planches...)
pour aboutir à la production du nouveau produit. Son calcul est simple
car basé sur des dépenses explicites (ces coûts même
s'ils sont anticipés, les anticipations sont exactes car obtenues
à base de devis fournisseurs).
Coûts des heures R&D (Recherche et
Développement) : constitue le coût des heures de travail des
membres de l'équipe.
Dans l'ancienne organisation des projets P0, il n'y avait
aucun moyen de calculer ou d'anticiper ces heures RÈD, elles
étaient plutôt chiffrées très grossièrement.
Et vue que ces heures de travail dépendent naturellement de la taille de
la modification, le résultat est totalement flou pour un coût
absolument pas négligeable. Il représente, en
général, la moitié du coût total d'un projet de
modification.
II-2- Pertes constatées :



12

II-2-1- Types des pertes résultantes :
Les failles managériales de l'ancienne
méthodologie de gestion des projets P0 généraient des
pertes annuelles énormes. Ces pertes sont toutes liées au temps
et aux retards et sont de trois types.

1er type :
Pertes de temps par les membres de l'équipe dans
l'exécution de leur activités à cause de la
désorganisation quasi totale (Exemple : tâches devront être
faites avant de passer ã de nouvelles en s'en apercevant ã la
dernière minute).
Les membres de l'équipe estiment que les pertes de temps
de ce genre sont de l'ordre de 35% de leur charge horaire (valeur très
optimiste).
2ème type :
Pertes liées aux retards des demandes client. S'il
s'agit par exemple d'envoyer des prototypes au client et un retard a
été fait en interne, les prototypes ne seront pas envoyés
par voie normale (Camions de Valeo à destination des plateformes
logistiques de distribution en Europe) mais plutôt par envoi express
(DHL, FedEx) ou encore par avion. Des envois qui sont beaucoup plus chers
naturellement. 80% de ces retards est du à l'absence d'une planification
efficace et concerne 40% des projets menés.
3ème type :
Pertes liées aux sous estimations des coûts
R&D des projets de modification. Ces erreurs d'estimation sont dues
ã l'absence d'un moyen permettant de calculer ou de chiffrer le total
des heures R&D nécessaires pour mener à bien un projet. Elles
constituent la plus grande partie des pertes globales (plus de la moitié
des pertes).

II-2-2- Chiffrage des pertes :
Les pertes citées se chiffrent comme suit :
(Remarque : Certains chiffres seront présentés sous
forme de moyennes sans préciser aucun détail, ceci pour des
raisons de confidentialité).
1er Type :
Le calcul des pertes du premier type, à savoir les
retards dans l'exécution des tâches des membres de l'équipe
projet, peut se faire en calculant le coût RÈD annuel total pour
lui appliquer les 35% des pertes.

Nombre d'heures de travail par jour = 8 heures
X
Nombre de jours de travail par an = 250 jours
X
Coût hora ire moyen R&D = 27,04 €
X
Nombre des membres de l'équipe projet = 8
Coût total R&D = 432,640 K€/an
X
Pourcentage des pertes = 35%
Pertes du premier type = 151,424 K€/an
2ème type :
Dans la division DEP, 40% des projets de Modification
Série génèrent des retards dans la préparation des
prototypes et des Echantillons Initiaux à une moyenne d'un retard par
projet. Ces statuts logistiques critiques mènent à des envois
express soit par DHL/FedEx ou par avion. 80% de ces retards sont dus à
la mauvaise gestion des projets P0.
Le calcul de ces pertes est le suivant :
Nombre de projets de modification menés par an = 100
X
Pourcentage des projets ayant des retards de livraison = 40%
X
Moyenne des coûts des envois express faits par
l'équipe projet = 2 K€
X
Pourcentage des retards dus à la mauvaise gestion =
80%
Pertes du deuxième type = 64
K€/an
3ème type :
14

Les historiques de l'année 2006 des projets de
Modification Série ont montré un décalage entre ce qui a
été estimé comme coût R&D des projets (et par la
suite facturé au client) et ce qui a été
réalisé réellement. Ce décalage a concerné
62 projets de modification.
Le total des heures de décalage constaté est =
11348 heures
Soit un décalage moyen par projet de = 183.03 heures
Et avec un coût hora ire moyen R&D de 27,04 €,
les pertes des sous-estimations des heures R&D des projets de Modification
Série en 2006, s'élèvent à 306.79
K€.
Pertes du troisième type en 2006 = 306?796
K€
Total des pertes :
Le total des pertes en 2006 dues à la mauvaise gestion des
projets de modification se chiffre ainsi à :

Total des pertes en 2006 = 522.22 K€
A l'issue de ce chapitre, ces chiffres plutôt
énormes représentent les
pertes dues ã l'absence d'un moyen et ã une
désorganisation dans la gestion des projets de
Modification Série. Une désorganisation, à
laquelle à peine on fait attention, personne
n'aurait cru qu'elle pouvait être si fatale pour
l'entreprise.
Ch. III : Techniques de suivi de
projets
|
Après avoir présenté le contexte et la
problématique de l'organisation des projets
de Modification Série dans les deux
premiers Chapitres, ce troisième vient pour mettre en relief les
éléments généraux constituant la
base des techniques de suivi d'un projet.
|
III-1- Management de projet :
III-1-1- Projet :
Définition :
Un projet est une séquence d'activités uniques,
complexes et connectées, avec pour but d'atteindre un
objectif5. Il doit être réalisé ã
l'intérieur d'un cadre temporel, d'un budget et en respectant des
spécifications données. En effet, c'est un ensemble d'actions
pour lequel des ressources humaines, matérielles et financières
sont organisées de manière nouvelle pour entreprendre un ensemble
unique d'activités bien spécifiées ã
l'intérieur de contraintes de coûts et de délais en vue de
réaliser un changement bénéfique
défini par des objectifs quantitatifs et qualitatifs.
C'est un système dynamique à maintenir en équilibre (voir
figure ci-dessous).
Qualité
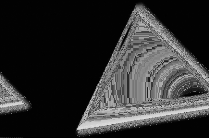
Délai
|
5 Source : Maksay (G.). - Management de projet, 2004.
|
15
|
Coût
Fig. 4 Triptyque Qualité Coût
Délai
d'un projet

L'objectif est d'atteindre la qualité exigée au
moindre coût et livrée le
plutôt possible. Chaque changement
déséquilibre tout le projet.
Exem ples de projet :
|
Développer une nouvelle application informatique ;
Définir et mettre en place une nouvelle organisation du
travail ;
Organisation d'un salon ;
Création d'un nouveau produit ; Construction d'un
chantier.
|
A l'opposé, une procédure ou une activité
permanente d'une entreprise
ne sont pas des projets.
Caractéristiques d'un projet :
Les caractéristiques d'un projet sont les suivantes :


Un projet est une action ponctuelle, unique et non
répétitive ;
Un projet est limité dans le temps : il a une date de
début et une date de fin ;
Un projet apporte une réponse à un besoin bien
identifié : il a un objectif précis matériel ou
intellectuel ;
Un projet est une démarche spécifique visant
à atteindre
l'objectif en métrisant la qualité du produit fini,
les coûts et
les délais grâce à des étapes, des
jalons constituant autant de points de contrôle ;
Un projet mobilise des compétences multiples et
complémentaires (la conduite d'un projet est une affaire
d'équipe).
III-1-2- Management de projet :
Le management de projet consiste à planifier, organiser,
suivre et
maitriser tous les aspects d'un projet, de façon ã
atteindre les objectifs en respectant les Coûts, les Délais et les
spécifications prédéfinies. D'après le PMI (Project
Management
Institut), c'est l'application de connaissances,
compétences, outils, et techniques dans des
activités de projet en vue d'atteindre ou de
dépasser les attentes des parties impliquées dans
le projet.
Dans la pratique, la majorité des projets
échouent et n'atteignent pas leurs objectifs ã cause soit d'un
dépassement dans les délais prévus, les budgets
alloués ou en ne satisfaisant pas toutes les exigences
demandées. La gestion et la motivation des
équipes, l'aptitude ã l'anticipation, la gestion
de l'information et de prise de décision sont
|
6 Source : Vallet (G.). - Techniques de suivi de projets, Dunod,
Paris, 2003.
|
17
|
toutes des difficultés qui font que la gestion des
projets, est à la fois un art et une science suivant des règles
et des lois. Ainsi, le paragraphe suivant présentera les techniques de
suivi assurant une bonne gestion des projets.
III-2- Techniques de suivi des projets :
III-2-1- Réunion d'avancement :
La réunion d'avancement est un point clé dans le
suivi du projet. Elle est menée périodiquement par l'ensemble des
intervenants dans le projet et a pour but de localiser les problèmes
d'avancement pour déclencher par la suite les actions de pilotage
nécessaires avec les seules personnes concernées et non pas les
résoudre pendant la réu n ion.
La réunion d'avancement est une réunion qui se
prépare. Tout intervenant doit savoir oz en est l'avancement de son
activité et quand l'activité sera terminée. La
finalité de cette préparation est de fournir une vue
cohérente de l'ensemble des activités menées pour
déclencher les actions nécessaires en cas de dérive.
III-2-2- Diagramme Dates-Dates :
Le planning d'un projet étant remis à jour lors
de chaque période d'avancement pour tenir compte de la
réalité d'une part, et des décisions de pilotage d'autre
part, le diagramme Dates-Dates6 est un moyen de visualiser de
manière synthétique l'évolution du planning d'un projet.
C'est une représentation de la succession des projections ã
achèvement du projet. En d'autres termes, il permet de visualiser
l'évolution des dérives qui est beaucoup plus significative que
la dérive en elle-même (voir diagramme figure ciaprès).
Ch iffrage
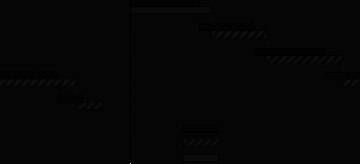
Prototypes
Prépa ration des moyens
Planning de référence du projet
Planning remis à jour
Passé du projet
Echantillons Initiaux
Clôture
Fig. 5 Diagramme GANTT d'un projet en deux
versions
de plannings

Sur le diagramme GANTT, le projet considéré est
en fin de la Phase Chiffrage. Cette phase a eu un retard par rapport à
ce qui était prévu sur le planning de référence. Le
projet dérive. Une nouvelle planification est établie à
base de cette dérivation en fonction des nouvelles durées
estimées de chaque phase. Si dans le même projet, une nouvelle
dérive sur le nouveau planning survienne (un retard ou une avance sur
une tâche donnée), ce sera mal visualisé sur le digramme
GANTT du projet. Le digramme Dates-Dates permet justement de voir
l'évolution de ces dérives indépendamment des
durées des tâches (voir figure ci-après).
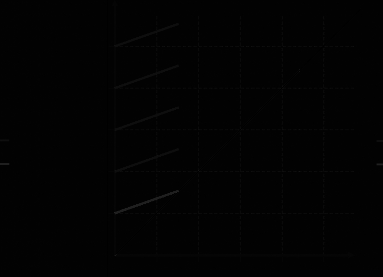
Aven i r
Passé
Phases non achevées Phases term inées à
temps
T0 T1 T2 T3 T4
Clôture
Echantillons initiaux
Prépa ration
des moyens
Prototypes
Chiffrage
Fig. 6 Diagramme Dates-Dates correspondant
au GANTT
précédent
La droite diagonale est dite la droite du présent. Elle
sépare entre la zone avenir en haut et la zone en bas
représentant le passé.
Sur un digramme Dates-Dates, seuls les jalons clé sont
représentés (ici les jalons ont été
considérés comme la date de fin de chaque phase). Chaque ligne
qui coupe la première bissectrice (droite du présent) correspond
à un jalon qui a été atteint. Lorsqu'une ligne coupant la
bissectrice est horizontale, ça veut dire que le jalon a
été terminé à sa date prévue. Lorsque par
contre la pente d'une droite est positive (respectivement négative),
elle coupera la ligne du présent dans un point à droite
(respectivement à gauche) de sa date prévue. Un retard
(respectivement une avance) a été fait(e) sur le jalon comme dans
la figure ci-dessus (le chiffrage a pris du retard et n'a pas pu être
achevé ã terme, c'est-à-dire, à la date T0), un
retard qui affectera par la suite tous les autres jalons.
|
7 Source : Vallet (G.). - Techniques de suivi de projets, Dunod,
Paris, 2003.
|
19
|
Le projet avance, le planning est remis à jour et les
nouvelles dates sont établies. Nous supposons que malgré le
retard fait sur la Phase de Chiffrage, les membres de l'équipe se sont
avérés très performants dans la phase suivante et la
durée de préparation des prototypes a été
réduite de manière à ce que sa date de fin coïncide
avec le planning de référence. La préparation des moyens
s'est terminée elle aussi avant sa date prévue par rapport au
planning de référence, quant à la préparation des
Echantillons Initiaux, elle a pris du retard et a duré un plus que
prévu. Le projet avance et la visibilité est de plus en plus
claire, nous constatons que la phase de clôture du projet pouvait se
faire dans moins de
temps que prévu, et par la suite le retard fait sur la
phase précédente n'affectera pas sa date
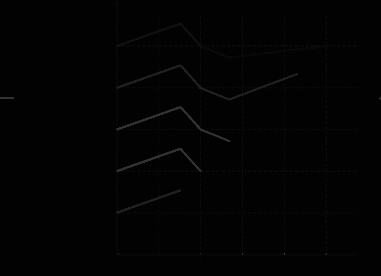
Aven ir
Passé
Phases term inées en retard
T0 T1 T2 T3 T4
de fin prévue. Le diagramme Dates-Dates correspondant
à ces suppositions est le suivant :
Clôtu re
Echantillons Initiaux
Prépa ration
des moyens
Prototypes
Ch iffrage
Fig. 7 Diagramme Dates-Dates à la fin du
projet7
Les projections ã achèvement se font ainsi de
cette manière jusqu'ã la fin
du projet. Le principal indicateur sur le respect du
délai sur la fin du projet est le point
d'intersection de la ligne de la dernière phase avec la
ligne du présent.
Remarque :
Une situation qui peut survenir, dans la pratique, c'est
lorsque la ligne correspondante à une tâche donnée a
coupé la première bissectrice (c'est-à-dire que la
tâche s'est terminée) mais qui revient encore une fois dans la
zone avenir (voir diagramme ciaprès).
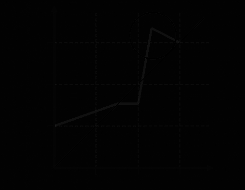
Aven i r
Passé
Chiffrage
T0 T1 T2
|
8 Source : Vallet (G.). - Techniques de suivi de projets, Dunod,
Paris, 2003.
|
20
|
Fig. 8 Tâche exécutée non
satisfaisante
Interprétation :
Dans ce diagramme Dates-Dates, la Phase de Chiffrage a
été achevée mais il y a eu une cause qui a fait que le
résultat de la phase n'a pas été accepté (des
prototypes non validés par le client ã titre d'exemple) donc les
membres de l'équipe devront plutôt refaire des actions
correctives.
III-2-3- Système de gestion de la
valeur acquise :
Un système de gestion de la valeur acquise (EVMS :
Earned Value Management System) est fondé sur un ensemble de
trois indicateurs qui assurent la liaison entre l'avancement de chaque
activité individuelle et l'avancement de l'ensemble du
projet8.
Dans un projet, il arrive que plusieurs activités
soient en cours lors d'un point d'avancement (Réunion d'avancement par
exemple). L'avancement du projet est alors le résultat de la
consolidation des avancements des activités. Or cette consolidation est
parfois difficile ã faire pour obtenir l'avancement global du projet car
les activités du projet n'ont pas forcément les mêmes
unités (exemple : la préparation des moyennes de production
série et la réalisation des prototypes sont deux activités
qui n'ont pas la même unité de mesure de leur avancement). Donc il
va falloir pondérer chaque activité pour pouvoir calculer
l'avancement global du projet. Ces activités peuvent être
pondérées entre elles vis-à-vis de plusieurs
critères : leurs risques, les facteurs de risque qu'elles portent sur
l'ensemble du projet, leur taille, etc.
Devant la multiplicité des métriques
d'avancement, trois grands donneurs d'ordre américains de projets (DoE :
Departement of Energy, DoD : Departement of Defense et la NASA : National
Aeronautics and Space Administration) ont définit un cadre commun de
compte rendu d'avancement de projets fondé sur des indicateurs
d'avancement standard. Ce carde commun a été appelé
Indicateur d'un Système de Suivi de l'Avancement par les Coûts
(C/SCSC : Cost/Schedule Control System Criteria).
|
9 Source : Vallet (G.). - Techniques de suivi de projets, Dunod,
Paris, 2003.
|
21
|
La norme C/SCSC, en tant que document de
référence, décrit en détail les aspects formels
d'un compte rendu d'avancement de projet, mais sur le fond identifie trois
indicateurs qui sont déterminés activité pas
activités sur le projet et qui sont consolidés par sommation pour
fournir la vue globale de l'avancement du projet. Ces indicateurs sont les
suivants :
: Actual Cost, ou CR : Coût Réel ;
: Earned Value, ou VA : Valeur Acquise ;
: Planned Value, ou VP : Valeur Prévue ;
III-2-3-1 Coût Réel (Actual Cost) :
Le coût réel d'une activité mesure les
temps passés par les ressources sur l'activité ou les
dépenses de la période. Il représente le coût
réel des travaux qui ont été effectués pendant la
période (voir figure page suivante).
Le CR d'un ensemble d'activités est, naturellement, la
somme des CR de chacune des activités9.
III-2-3-2 Valeur Acquise (Earne4 Value) :
La valeur acquise d'une activité mesure le budget qui
correspond ã l'avancement technique constaté pendant la
période (Voir courbe ci-après ). La VA est appelée aussi
parfois VBTR (Valeur Budgétée des Travaux
Réalisés).
La VA d'un projet donné est la somme des VA de chacune
des activités du
projet.
III-2-3-3 Valeur Prévue (Planne4 Value) :
La VP d'une activité mesure la part du budget de
référence qui correspond ã l'avancement prévu (dans
le planning de référence) de l'activité pour la
période (voir figure ci-après).
La VP étant une image du planning de
référence, elle n'est donc pas strictement un indicateur
d'avancement, mais plutôt un indicateur de référence pour
l'avancement.
La VP d'un ensemble d'activités est la somme des VP de
chacune des
activités.
figure 9 :
|
Voici un exemple de représentation graphique du CR, VA et
VP sur la
|

Coût
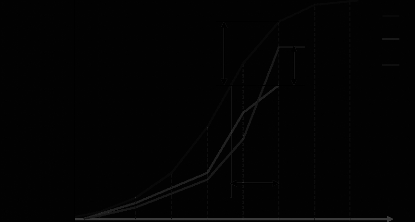
VP (Valeur Prévue)
Ecart en production
CR (Coût Réel)
VA (Valeur Acquise)
Ecart en coût
Ecart en délai
|
10 Source : Vallet (G.). - Techniques de suivi de projets,
Dunod, Paris, 2003.
|
22
|
Temps
Fig. 9 Courbes en S d'un projet et écarts
constatés



Ecart en production : représente la valorisation de
l'ensemble des travaux qui auraient dû être effectués
ã la date du point d'avancement et qui ne l'ont pas
été10.
Ecart en coût : représente la différence
entre le coût des travaux effectués et leur valorisation (sur la
base des budgets de référence).
Ecart en délai : représente la valorisation de
l'ensemble des travaux qui ont été effectués à la
date du dernier point d'avancement.
Conclusion de la première partie :
Dans cette première partie du rapport, nous avons
étudié le contexte de management des projets chez Valeo
Connective Systems, en particulier les projets de Modification Série sur
lesquels nous allons nous focaliser durant tout le reste du rapport. Nous avons
identifié et analysé par la suite les lacunes managériales
relatives à ces projets et les pertes énormes en
résultantes pour présenter à la fin les techniques
générales nécessaires de suivi d'un projet ã
déployer dans leur méthodologie de gestion que nous avons mis en
place. Parmi ces éléments, nous citons le digramme Dates-Dates
représentant l'évolution des dérives dans un projet et le
système de gestion de la valeur acquise permettant la mesure de
l'avancement global du projet.

Deuxième 2 partie
DEuxIEME PAPTIE :
IMPLEMENTATioN D 'uNE
DEMARcHE DE MANAGEMENT DES
PRojETS DE MoDIFIcATioN SEPIE

Ca. I - MéTaODOlOGIE DE
MANAGEMENT DES PrOjETS PO
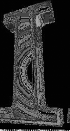
La méthodologie de management des projets
P0 visant
à corriger les lacunes managériales et
éliminer les
pertes qui en résultent sera présentée en
quatre
parties.
Une première partie constituera une analyse
de
l'environnement des projets P0 sous forme d'une Tortue
de Crosby
déterminant les facteurs en relation avec les
projets.
Un logigramme global fera l'objet d'une deuxième
partie
suivie par la structure détaillée du projet
décomposée en 5
phases.
La quatrième partie concernera le « Cost Driver
», l'outil qui résoudra le
problème des estimations
grossières des coûts de Recherche et Développement des
projets
de Modification Série en faisant des calculs basés sur
la taille de chaque projet.

I-1- Tortue de Crosby :
La Tortue de Crosby (Voir Fig. page suivante) décrit un
projet P0 sous forme d'un diagramme spécifiant l'objectif,
l'environnement, les différentes ressources participantes dans le
projet, le comment de la réalisation et les critères de son
évaluation.
Les données d'entrée d'un projet de modification
sont l'origine de la demande, le dossier du projet P1 clôturé et
le Dossier Assurance Qualité. L'exigence de sortie est la modification
dans le couple produit/process en fonction de l'origine de la demande.
Entrées
- Demandes client, évolution, réglementaire,
directive,
norme standard, spécification ou norme client ;
- Non-conformité interne ou réclamation client
;
- Productivité sur produit, process ;
- Modification d'un composant par le fournisseur ;
- Dossier projet P1 clôturé, Dossier Assurance Qua
lité.
|
|

Avec quoi ?
- Outils bureautique, système de gestion SIGIP, ligne de
production et composants approvisionnés, atelier prototypes, outillage,
matière.
|
|
Combien ?
- Indicateur set objectifs : pourcentage mensuel des
Echantillons Initiaux acceptés par le client, nombre des modifications
appliquées sur le nombre des modifications chiffrées,
résultats de l'audit process.
|
Avec qui ?
- Chef de projet et son équipe, cellule Plasturgie,
Méthodiste UAP (Unité Autonome de Production), superviseur,
personnel de ligne formé au métier poste et produit.
|
Comment ?
- Processus formalisé (procédures, documents au
poste?), 5S, PDCA, Instructions de travail, respect du produit, qualité
d'identification, plans d'expérience.
|
|
Sorties
- Planning projet, nouveaux plans à jour, Demande
d'Autorisation
d'I nvestissement, chiffrage, Plan Qualité Projet,
Résultats des essais de validation ;
- Contrats avec les
fournisseurs, Rapports des audits fournisseurs ;
- Prototypes et rapports de contrôle ;
- Rapport d'audit produit, process, JPC (Journée Pleine
Cadence) ;
- AM DEC process finale, documents au poste, nomenclature
vérifiée et signée ;
- JPC et Echantillons Initiaux acceptés, process
qualifié.
|
Projet P0
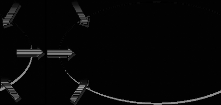
Adapter le produit/process aux
propositions internes,
propositions
client ou aux événements
fournisseur
Exigences
Exigences
25
Fig. 10 Tortue de Crosby des Projets P0

I-2- Logigramme/procédure des projets de
Modification Série :
Le logigramme suivant définit la structure
organisationnelle globale des projets de Modification Série. Il
présente un descriptif bref de ces projets sans rentrer dans le comment
de chaque action, des détails qui seront explicités dans la
structure détaillée du projet.
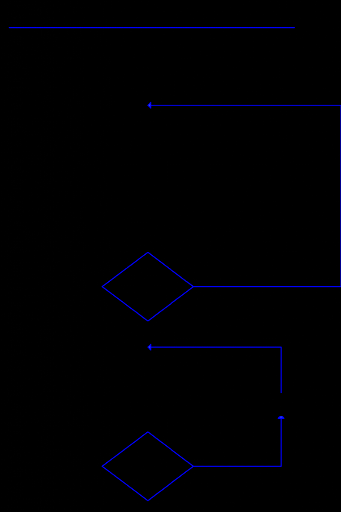
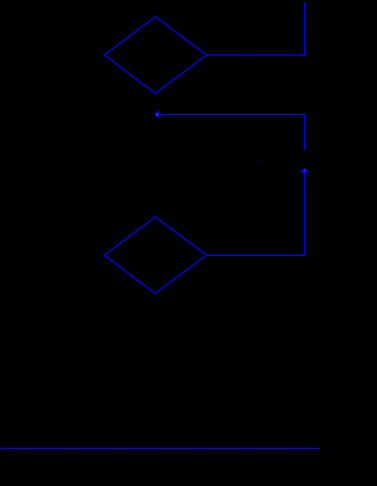

Fig. 11 Logigramme/procédure des projets
de
Modification Série
I-3- Structure détaillée du projet
:
A partir du logigramme précédent, nous
remarquons qu'il y a principalement 5 phases dans un Projet de Modification
Série : Chiffrage, Préparation des prototypes, Préparation
des moyens, Réalisation des Echantillons Initiaux et Duplication de la
modifications (Voir Structure globale ci-après et WBS complet du projet
en annexe page : 1). Cette décomposition est basée sur les
"produits" livrables du projet, que cela soit au client

(Chiffrage du projet, prototypes, Echantillons Initiaux) ou en
interne (Validation des moyens et démarrage de la production
série). C'est-à-dire, qu'ã chaque fois qu'il y a un
produit livrable accepté, ça constituera la fin d'une phase et le
début d'une nouvelle. L'acceptation de ces produits sera le
résultat des points de contrôle (jalons) qui seront définis
à la fin chaque phase et dont la validation conditionne le passage
à la phase suivante.
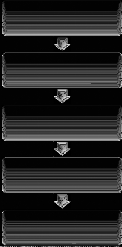
Phase 3b : Modification de tous les moyens série
Phase 3a : Réalisation des Echantillons Initiaux
Phase 1 : Prépa ration
des prototypes
Phase 2 : Prépa ration
des moyens
Phase 0 : Chiffrage
Jalon 1 : Acceptation du chiffrage et validation
de la Phase par le Comité de Modification
Jalon 2 : Validation des prototypes et
faisabilité produit, process
Jalon 3 : Validation des moyens de production
Jalon 4 : Acceptation des EI par le client
Jalon 5 : Validation du Comité de
Modification
Fig. 12 : Structure générale
d'un
Projet P0
I-3-1- Phase 0 : Chiffrage
Cette Phase est la phase de lancement du projet. Elle consiste
à faire un chiffrage détaillé du projet ã
présenter au client et dont l'acceptation conditionne le passage
à la phase suivante.
Remarque :
Les tâches qui seront citées ne
s'exécutent pas forcément l'ordre qui suit. Il s'agit ici
uniquement de détailler les travaux à effectuer dans chaque
phase. Pour comprendre l'ordre ou les liens entre les tâches, se
référer aux diagrammes réseau de chaque phase.
Les tâches constituant la Phase 0 sont comme suit :

A - Transmission de la demande ã
l'équipe P0 : c'est le point de démarrage officiel du projet. Si
la modification n'est pas d'origine interne, le commercial de l'équipe
reçoit de la part du client la demande de modification officielle pour
la transmettre ã l'équipe sous le format standardisé de
Valeo, Sinon la demande de modification est faite en interne ;


B - Analyse de la modification : étude
strictement nécessaire car, il s'agit d'interpréter correctement
le besoin exprimé par le client. Le responsable de cette action est le
MEP Etude (Membre de l'Equipe Projet Etude constituant l'interface technique
avec le client) ;

C - Faisabilité Produit-Process :
juste après l'analyse de la modification, une étude de
faisabilité Produit-Process sera faite afin de vérifier la
faisabilité de la réalisation du produit sur les moyens de
production de Valeo ;

D - La capacité technique est une
étude ayant pour objectif de vérifier si, avec les moyens de
production actuels, le besoin annuel du client pourra être satisfait.
Normalement puisque le produit était déjà en production
dont les lignes ont été dimensionnées à partir du
besoin annuel, les moyens sont capables de livrer le client en volume
demandé. Cependant, une modification dans la définition du
produit (ajout ou suppression d'un composant) peut engendrer un changement dans
la durée de montage des faisceaux électriques et par la suite une
modification du nombre de lignes, afin de répondre au besoin du client
et juste à ce besoin, peut avoir lieu. Et c'est ã base de cette
modification dans la ligne de production que le chiffrage des moyens dans le
calcul du coût global du projet va être fait ;

E - Consultation des fournisseurs pour les
nouveaux moyens ;
F - Elaboration du chiffrage
(Préparation du chiffrage à présenter au client). Le
chiffrage des moyens sera obtenu à partir des devis des fournisseurs
quant au coût des heures de travail des membres de l'équipe
(coût de Recherche et Développement), il sera calculé
à partir du Cost Driver que nous allons définir dans la
troisième partie ;

G - Vérification de la
disponibilité des tous les documents auprès de l'équipe
projet P1. Ceci assurera le bon passage documentaire P1-P0 ;

H - Elaboration du planning prévisionnel
de la demande ;
I - Présentation du chiffrage et planning
prévisionnel au client.
Succession des tâches :
Les liens entre les tâches n'ont toujours pas
été définis. Le but de ce paragraphe est de les
définir, en présentant tout d'abord la méthode
utilisée puis en l'appliquant pour chaque phase du projet.
|
Méthode : la méthode sera
présentée sous forme d'une matrice avec les tâches
inscrites sur la première ligne et la première colonne. Suivant
le sens Vertical ? Horizontal, nous allons noter 1 ã
chaque fois qu'une des tâches disposées verticalement
précède celles disposées horizontalement à la case
correspondante. Nous calculons
|
|
ensuite le total pour chaque colonne, ça constituera
"l'ordre" d'exécution de la tâche dans la phase. Pour chaque
tâche, nous regarderons parmi ces précédentes, la
tâche ayant un
ordre directement inférieur, ça sera l'(es)
antécédent(s)
direct(s) de la tâche.
Exemple :
Soit un projet P contenant 8 tâches
présentées comme suit : Tâche A : N'est
précédée par aucune tâche ;
Tâche B : Précédée par A ;
Tâche C : Précédée par B, A et D ;
Tâche D : Précédée par A ;
Tâche E : Précédée par A et D ;
Tâche F : Précédée par A, B, C et D
;
Tâche G : Précédée par A, B, C et D
;
Tâche H : Précédée par A, D et E.
|


Matrice d'antécédence :
Précède
|
A
|
B
|
C
|
D
|
E
|
F
|
G
|
H
|
A
|
|
1
|
1
|
1
|
1
|
1
|
1
|
1
|
B
|
|
|
1
|
|
|
1
|
1
|
|
C
|
|
|
|
|
|
1
|
1
|
|
D
|
|
|
1
|
|
1
|
1
|
1
|
1
|
E
|
|
|
|
|
|
|
|
1
|
F
|
|
|
|
|
|
|
|
|
G
|
|
|
|
|
|
|
|
|
H
|
|
|
|
|
|
|
|
|
Total
|
0
|
1
|
3
|
1
|
2
|
4
|
4
|
3
|
Tab. 01 : Matrice d'antécédence,
exemple
Ainsi le tableau des antécédents est
établi :
Tâche
|
Antécédent
|
A
|
-
|
B
|
A
|
C
|
B, D
|
D
|
A
|
E
|
D
|
F
|
C
|
G
|
C
|
H
|
E
|
Tab. 02 : Liens entre les tâches,
exemple
Ce tableau sera la base de la génération du
diagramme réseau ou du PERT au cas où toutes les informations
sont disponibles.
Diagramme réseau du projet P
considéré :
A
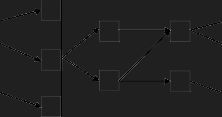
B
D
C
E
G
F
H

|
Remarque : l'application de la méthode
présentée n'est pas nécessaire lorsque le nombre de
tâches est petit, ça peut se faire d'une manière intuitive,
par contre lorsque le nombre de tâches est important, ce qui est le cas
dans les projets de Modification Série, son application est très
recommandée car évite la création de liens en double (Voir
figure ci-dessous) pouvant causer un dysfonctionnement anormal lors de
l'implantation du planning sur la plateforme informatique.
|
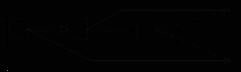
D
A
B
C
E

: Lien en double. Puisque B précède C qui
précède à son tour D, systématiquement B
précède D et par la suite le lien entre B et D est un lien en
double. De même entre A et E. Ces liens en double sont très
difficilement détectés et ne sont pas acceptés lors de
l'implantation des projets sur la plateforme informatique car ils
génèrent des redondances des liens entre les tâches.
|
En appliquant la méthode ci-dessus (Voir les Matrices en
annexe page : 4) nous obtenons le tableau suivant :
|
Tâche
|
Antécédent
|
A
|
-
|
B
|
A
|
C
|
B
|
D
|
B
|
E
|
C
|
F
|
E, D
|
G
|
A
|
H
|
C
|
I
|
H, F
|

Tab. 03 : Liens entre les tâches de la Phase 0 :
Chiffrage
Diagramme réseau de la Phase 0 :
Sera présenté ici un diagramme réseau et
non pas un digramme PERT car aucune information temporelle relative ã
l'ordonnancement ou aux durées des tâches ne peut être
définie. Il s'agit d'un squelette servant ã n'imÐorte quel
Ðrojet de modification et non pas spécifique à un projet
donné. De même pour le chemin critique du projet, il ne peut
être spécifié car il dépend du projet
considéré, de sa planification et de la durée de ses
tâches.
Le diagramme réseau présente les relations entre
les différentes tâches de la phase car, comme le montre le tableau
des liens entre les tâches, plusieurs raisons font que les tâches
ne soient pas exécutées d'une manière successive
(Certaines tâches peuvent se faire en Ðarallèle, d'autres sont
indépendantes les unes des autres, etc.) Ce même réseau
sera la base du suivi des projets sur la plateforme informatique de gestion des
projets.
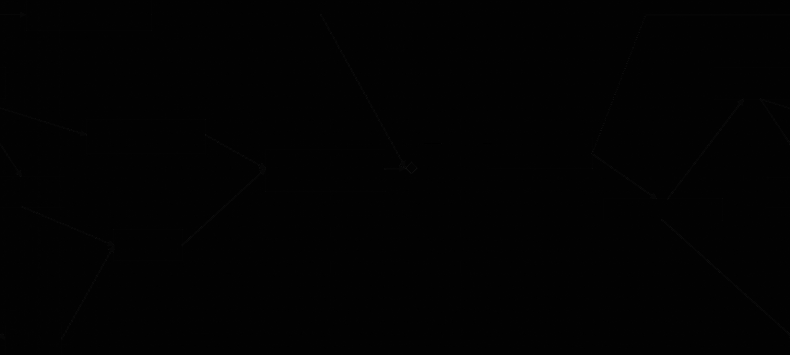
A- Transmission de la
dÐmandÐ ã l'équiÐÐ P0
B- Analyse de la modification
C- Faisabilité
Produit - Process
E- Consultation des
fournisseurs
D- Capacité technique
G- Vérification de la
disponibilité
des documents du projet
H- Elaboration du planning prévisionnel
de la demande
F- Elaboration du chiffrage
I- Présentation du chiffrage et
du
planning prévisionnel au
client
Jalon 1 :
Acceptation du
chiffrage et
validation de la
Phase 0 par le
Comité de
Modification.

Fig. 13 Diagramme réseau de la Phase 0
des
projets de Modification Série : Chiff rage
I-3-2- Phase 1 : Préparation des prototypes

Cette Phase assure que la nouvelle définition du
produit est valide lors du montage du produit dans le système du client
(Exemple : Voir si les faisceaux témoins de non bouclage de la ceinture
sécurité sont montables sur les sièges que produit le
client et vend à Renault) ainsi que de préparer tous les
éléments nécessaires pour la préparation de la
ligne en phase suivante.
Les activités constituant cette phase sont :

A - Réunion de lancement de
modification : Tous les contributeurs de l'équipe projet se
réunissent afin de discuter l'impact de la modification de la
définition du produit sur tout le circuit en relation avec le produit
(la ligne de production, le process, la logistique, l'approvisionnement, etc.)
;

B - Vérification de
l'intégration sur système informatique des CMS (Coûts
Matières Standards) : Ce sont les coûts matières (contre
les coûts de la main d'oeuvre) des faisceaux électriques produits.
L'intégration de ces coûts sert dans les prévisions
budgétaires de la production ;

C - Elaboration et renseignement de l'avis de
modification : Dans les standards Valeo, aucune modification ne pourra
être effectuée, qu'elle soit au niveau de la ligne de production,
dans le circuit logistique ou dans le système de gestion production sans
qu'un avis de modification ne soit communiqué ã l'ensemble des
services en relation avec la ligne de production afin que la modification soit
traitée vis-à-vis de tous les services concernés ;

D - Discuter le sort des obsolètes :
la modification dans la définition d'un produit peut engendrer des
obsolètes en matière de stocks notamment lorsque des composants
du produit ne seront plus utilisés dans sa nouvelle version et le client
demande une livraison assez urgente du nouveau produit. Discuter le sort des
obsolètes, c'est voir parmi les composants du produit ceux qui pourront
être rendus aux fournisseurs, ceux qui ne le peuvent pas à cause
des commandes fermes (des boitiers par exemple) ou ceux qui seront
rebutés tels que des fils déjà coupés en fonction
des dimensions des anciens faisceaux, ainsi que de chiffrer le coût de
ces obsolètes pour le facturer au client ;

E - Choix des solutions process,
industrialisation et logistique : dans cette action le MEP Indus (Membre de
l'Equipe Projet Industrialisation) fait une étude ayant pour objectif le
choix des solutions ã mettre en oeuvre pour pouvoir produire la nouvelle
version du produit et satisfaire le besoin au client. Cette étude
concerne à la fois le process, l'industrialisation et le circuit
logistique ;

F - Revue de faisabilité et
capacité technique : revoir l'étude de faisabilité et
capacitaire faites dans la Phase 0 et vérifier leur compatibilité
avec les solutions process, industrialisation et logistiques retenues ;
G


- Mise à jour du chiffrage : le chiff
rage du coût du projet et du prix série du faisceau sont mis
à jour en fonction des nouvelles solutions retenues (Le prix
série du faisceau est le prix de vente lorsque le nouveau produit sera
lancé en production) ;
H

- Réalisation du PQP (Plan
Qualité du Projet) : le plan qualité projet constitue un document
de référence interne pour Valeo. C'est un document officiel
spécifiant les personnes ayant participé au projet, les objectifs
qualité du projet et le pilote de chaque activité ;

I - Création et validation de la DAI
(Demande d'Autorisation d'Investissement) : la DAI est un document interne lui
aussi fait par les membres de l'équipe devant commander un moyen
auprès des fournisseurs. Elle est faite ã base des devis
fournisseurs des moyens qu'il faudra acheter, validée par le Chef de
Projet, le service financier et la direction pour aboutir ã l'obtention
de la commande à envoyer aux fournisseurs ;

J - Validation du contrat : Dans les projets
de Modification Série, même s'il s'agit d'un faisceau qui
était déjã produit par Valeo, un nouveau engagement
officiel doit être validé entre le client et Valeo. Cet engagement
définit tous les articles relatifs à la Qualité du nouveau
produit (Nombre de PPM autorisées, Retour garantie...), le Coût
(Coût de la modification, prix faisceau série...) et le
Délai (Délais de livraison des prototypes, Echantillons Initiaux,
faisceau série etc.) ;

K - Modification des plans et validation du
client : dans cette activité, le MEP Etude (Membre de l'Equipe Projet
Etude) modifie les plans du produit en fonctions des modifications à
apporter au produit et les envoie au client pour une validation officielle si
la demande de la modification n'est pas d'origine client ;


I - Mise ã jour de l'AMDEC et Plan De
Surveillance (PDS) : l'Analyse des Modes de Défaillance, leurs Effets et
leurs Criticités est mise à jour (car elle était
déjà faite lorsque le projet était en Projet P1). En
fonction des nouveaux moyens, des nouveaux composants ou des modifications qui
ont été apportées au produit/process. Le plan de
surveillance décrit en détail les étapes par lesquelles
doit passer le processus de montage des faisceaux, de la réception des
composants ã l'envoi des produits finis, et définit les
paramètres à surveiller dans chaque étape du processus, la
fréquence de contrôle, le moyen de contrôle, la valeur
nominale et les tolérances acceptées. Exemple :
Dans la machine de coupe des fils, les dimensions des fils
coupés doivent être contrôlées après chaque
5000 coupes, le contrôle sera fait visuellement, la valeur nominale et
l'intervalle de tolérance sont de mm ;

M - Elaboration du Plan de Validation :
à la différence du Plan De Surveillance, le Plan de Validation
définit les caractéristiques critiques à contrôler
sur le produit fini et non pas sur une partie du composant car il se peut que
tous les

composants soient conformes mais le montage final ne l'est pas
(exemple : une agrafe est décalée par rapport ã l'endroit
oz elle devait être montée alors que toutes les dimensions des
fils sont bien dans leurs intervalles de tolérance). Le plan de
validation définit aussi les limites de capabilités
acceptées du process ;
N

- Constitution du cahier de charges,
lancement et validation des nouveaux moyens : Un cahier de charges
établi par le MEP Indus (Membre de l'Equipe Projet Industrialisation)
définit officiellement les besoins de l'équipe projet P0 et sera
la base des devis des fournisseurs ;
m

- Valider le DEV (Dossier d'Exigences Valeo)
s'il y a un nouveau fournisseur : pour qu'un nouveau fournisseur puisse faire
partie du panel des fournisseurs de Valeo, il faut qu'il satisfasse des
exigences formalisées imposées par Valeo vis-à-vis de ses
fournisseurs. Exemples d'exigences : fréquence et conditions de
livraison ;

P - Création sur SIGIP des nouveaux
composants : c'est une action qui consiste en la création des nouveaux
composants jamais utilisés par Valeo sur SIGIP (Système
Informatique de Gestion Intégrée de la Production). Le
responsable de cette action est le gestionnaire des données techniques
;
Q

- Approvisionnement et homologation des
nouveaux composants qui feront partie du nouveau produit. Leur homologation se
fait à la fois par rapport aux standards de Valeo et par rapport aux
standards du client autorisant ainsi son utilisation dans la production ;

R - Réalisation des prototypes
faisceaux : c'est la tâche clé de cette Phase. La
réalisation des prototypes est faite avant de modifier les moyens.
L'objectif principal est de vérifier la montabilité des faisceaux
sur le système du client et faire les essais de validation. Les
prototypes définissent la structure globale du faisceau et vue qu'ils ne
sont pas faits sur les moyens de production série car la modification
des moyens n'a pas encore eu lieu, certaines exigences peuvent ne pas
être respectées en particulier, les exigences dimensionnelles,
celles-ci seront satisfaites dans le processus série ;

S - Préparer le DAQ (Dossier Assurance
Qualité) : le Dossier Assurance Qualité est le dossier
résumant le projet en entier vis-à-vis du client. Il englobe tous
les documents du projet et les précautions qualité mises en
place. Il contient le plan du faisceau, l'Etat d'acceptation des composants,
leurs spécifications techniques, l'AMDEC Processus, le plan de
surveillance, le suivi des Echantillons Initiaux, les capabilités, fiche
de conditionnement (définit la manière avec laquelle le produit
fini sera emballé : exemple : 30 pièces par carton
séparées par des intercalaires (10 + 10 + 10) et dont
l'orientation est inversée). Il est fait en parallèle des autres
actions et étalé sur 3 phases (Phase préparation des
prototypes, Phase modification des moyens, Phase préparation des
Echantillons Initiaux) en fonction de la disponibilité des documents
;


T - Réalisation des essais de
validation : les essais de validation sont faits dans des laboratoires.
Certains clients demandent des comportements spéciaux de leurs produits
vis-à-vis des agressions du milieu où le produit va fonctionner.
Exemple : la résistance au feu, test d'inflammabilité, limite de
la vitesse de combustion, chutes de tension électrique dues aux
vibrations, etc. ;

U - Validation des prototypes et des
résultats des essais de montabilité : c'est le pont de passage
ã la phase suivante. Une fois les prototypes conformes et les tests
validés, on passe à la Phase 2 pour la préparation des
moyens.
Succession des tâches :
Vue la complexité de cette phase, la méthode
présentée précédemment simplifiera grandement
l'étude des liens entre les tâches. Le tableau de succession des
tâches est établi comme suit (voir matrice
d'antériorité en Annexe page : 4) :
Tâche
|
Antécédent
|
A
|
Jalon 1
|
B
|
A
|
C
|
A
|
D
|
A
|
E
|
Jalon 1
|
F
|
E
|
G
|
E
|
H
|
Jalon 1
|
I
|
E
|
J
|
I
|
K
|
Jalon 1
|
L
|
K
|
M
|
K
|
N
|
J
|
O
|
J
|
P
|
N, O
|
Q
|
N, O
|
R
|
P, Q
|
S
|
H, L
|
T
|
R
|
U
|
T
|
Tab. 04 : Liens entre les tâches de la Phase 1 :
Préparation
des prototypes

Diagramme réseau de la Phase 1 :
Les liens entre les actions de la Phase préparation des
prototypes sont présentés dans le diagramme réseau
ci-après.
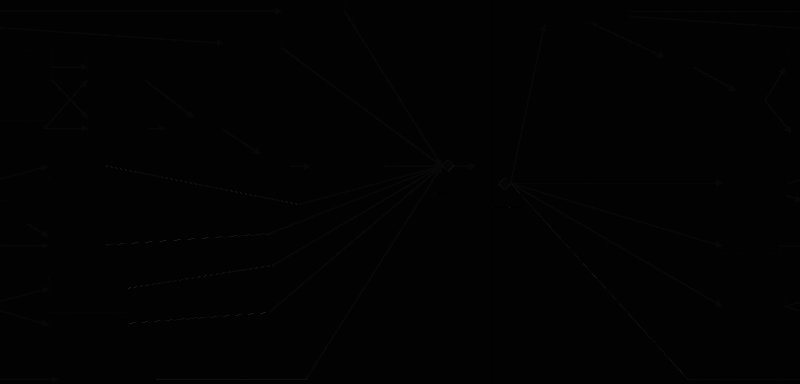
Jalon 1 :
E- Choix des solutions process industrialisation
et logistique
I- Création et validation
de la
DAI
J- Validation du contrat
A- Réunion de lancement
de la modification
K- Modification des plans et validation
client
H- POP
N- Constitution du CdC,
lancement et validation
des
moyens
P- Validation du DEV
L- Mise à jour de
l'AMDEC Ðt PDS
B- Vérification dÐ l'intégration
des CMS sur système
C- Elaboration et renseignement
dÐ l'avis dÐ modification
M- Elaboration du plan de validation
S- DAO
D- Décider le sort des
obsolètes
P- Création SIGIP des nouveaux composants
R- Approvisionnement
et homologation des
nouveaux
moyens
R- Réalisation des prototypes faisceau
G- Mise à jour du
chiffrage
T- Réalisation des essais de
validation
F- Revue de faisabilité et
capacité technique
U- Validation des prototypes et des essais de
montabilité
Jalon 2 :
Validation des
prototypes et de
la faisabilité
produit et
process.

Fig. 14 Diagramme réseau de la Phase 1
des
projets de Modification Série : Préparation des
prototypes
I-3-3- Phase 2 : Préparation des moyens

Cette Phase consiste en la prépa ration des moyens de
production série. La modification est apportée à une seule
ligne de production afin de pourvoir produire les Echantillons Initiaux qui,
une fois validés par le client, toutes les autres lignes seront mod
ifiées.
Les actions de cette Phase ont été
définies comme suit :

A - Mise à jour du tableau de synthèse AQP : le
tableau de synthèse AQP définit le statut d'acceptation de tous
les composants faisant partie du faisceau. Cette acceptation conditionne le
lancement de la production en série. Remarque : Un même composant
peut être accepté auprès d'un client et refusé pour
un autre (chaque client a des standards propres à lui) ;

B - Revue d'avancement entre l'équipe P0, les
équipes de la production et le Comité de Modification : dans
l'ancienne gestion des projets P0, la modification des moyens de production
causait des arrêts dans des moments très critiques pour la
production alors qu'il y avait des moments oz la ligne ne tournait pas et
où tout arrêt n'aurait causé aucune perturbation. Ceci
était dû à l'absence d'une collaboration entre
l'équipe projet, et les équipes de la production. Cette revue
d'avancement vise ainsi à éliminer ce genre de situations en
partageant l'information entre l'équipe projet et les équipes de
la production avec la participation du Comité de Modification
formé des directeurs des différents métiers et du
directeur projets de la division ;

C - Mise à jour des données techniques (exemple
: changer les références ou modifier les nomenclatures sur le
système informatique) ;

D - Intégration du PV (Programme de Vente) et du PDP
(Plan Directeur de Production) : le programme de vente donne les volumes des
produits à livrer au client ainsi que la fréquence de livraison
(exemple : 2000 faisceaux par semaine pour les deux premiers mois, 1500
faisceaux par semaine à partir du 3 mois etc.). Il est
intégré dans le circuit logistique de la société et
le PDP est mis à jour en fonction des composants de la nouvelle version
du produit ;

E - Renseignement du prix série du faisceau par le chef
de projet : après le calcul du prix série du faisceau, il est
communiqué par le chef de projet à tous les acteurs
concernés (la direction, le service financier etc.) à travers le
système informatique interne de Valeo ;

F - Préparation du planning de montée en cadence
et du planning d'extinction des anciennes références : lors du
lancement d'une nouvelle référence sur les lignes, les
opératrices ne sont pas habituées au nouveau produit, ceci induit
à un temps de montage assez grand et par la suite à une cadence
de production faible ou du moins, ne pouvant pas satisfaire
immédiatement le besoin du client. Cette situation est


prise en compte dans le planning de montée en cadence
car ce planning spécifie préalablement l'évolution
croissante que doit suivre la production afin de pouvoir satisfaire le besoin
du client dès la première date de livraison demandée. Le
planning d'extinction des anciennes références décrit
l'évolution décroissante que doit suivre la production de ces
dernières ;
G - DAQ (Dossier Assurance Qualité) suite ;
H - Réalisation des moyens et validation : la
modification est apportée à une ligne de production pour pouvoir
préparer les Echantillons Initiaux en phase suivante qui, validés
par le client, déclenchent la modification de toutes les lignes de
production et par la suite le lancement de la production en série.
Succession des tâches :
De même que pour les deux premières phases, les
liens entre les tâches seront établis à partir du tableau
suivant (Matrice d'antériorité en Annexe page 4) :
Tâche
|
Antécédent
|
A
|
Jalon 2
|
B
|
C
|
C
|
A
|
D
|
Jalon 2
|
E
|
D
|
F
|
Jalon 2
|
G
|
Jalon 2
|
H
|
C
|
Tab. 05 : Liens entre les tâches de la
Phase 2
: Préparation des moyens
Diagramme réseau de la Phase 2 :
De même que pour les Phases 1 et 0, les liens entre les
tâches de cette phase sont présentés sous forme du
diagramme réseau à la page suivante.
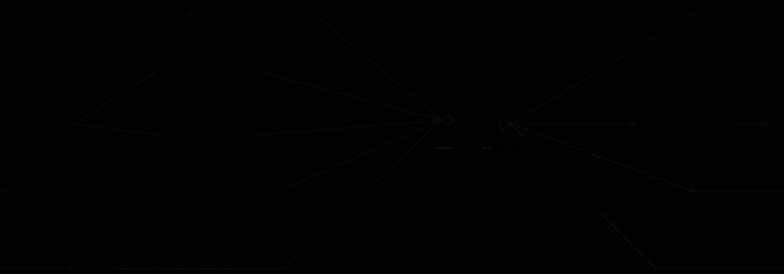
Jalon 2 :
A- Mise à jour du
tableau de
synthèse AQP
D- Intégration du PV et du
PDP
C- Mise à jour des données
techniques
F- Planning de montée en cadence et
extinction des anciennes références
G- DAQ
B- Revue d'avancement entre
l'équiÐe
P0, l'UP et le Comité de Modification
H- Réalisation des moyens et
validation
E- Renseignement du prix série
du
faisceau dans le système
Jalon 3 :
Validation des
moyens de
production.

Fig. 15 Diagramme réseau de la Phase 2
des
projets de Modification Série : Préparation des
moyens

I-3-4- Phase 3a : Réalisation des Echantillons
Initiaux
Le but principal de cette Phase est de préparer les
Echantillons Initiaux. A la différence des prototypes, les Echantillons
Initiaux représentent la version finale du faisceau que Valeo peut
produire. Et vu qu'ils sont montés sur le processus série, les
produits qui seront vendus au client seront exactement les mêmes que ces
derniers.
Remarque : si une exigence n'a pas pu être satisfaite sur
les Echantillons Initiaux, elle ne pourra l'être sur les produits
série.
Les activités de cette Phase se déroulent comme
suit :

A - Mise à jour des documents au poste
: parmi les documents au poste il y a des figurines, des schémas donnant
aux opératrices les indications de montage des faisceaux
électriques et des dossiers de suivi des modifications d'un projet. Ils
doivent être mis à jour en fonction de la nouvelle
définition du produit ;
|
Figurines indiquant les fils à monter dans chaque
connecteur en fonction des références du faisceau.
Le type de
l'enrubannage ã
mettre dans une branche du faisceau est indiqué sur la
planche de montage.
Ici il s'agit d'un
enrubannage à pas découvert.
|
Fig. 16 Documents au poste sur une planche de
montage
|

B - Vérification de l'état du
stock des composants avant de lancer la production de la nouvelle
définition du faisceau ;

C - Audit process : le process est
auditée par un auditeur interne pour vérifier que le processus
respecte les standards des systèmes de production Valeo incluant entre
autre l'ergonomie des postes et les normes de sécurité ;

D - Formation produit process : Avant le
lancement de la production de la nouvelle définition du produit, les
opératrices doivent être formées dans le montage du nouveau
faisceau. Les indications du montage du faisceau sont indiquées par les
MEP Etude et Indus aux formateurs de la ligne qui formeront à leur tour
les opératrices de la production ;

E - Réunion de préparation de
la JPC (Journée Pleine Cadence) : la Journée Pleine Cadence est
une journée où la production est lancée sur la ligne afin
de simuler le processus de production réel. L'objectif principal lors de
la JPC est d'atteindre 80% de la cadence demandée par le client qui une
fois atteinte, le process sera jugé bon. Les 20% restantes seront
atteintes après quelques mois (le temps que les opératrices
s'habituent à la nouvelle définition du produit et gagnent
d'avantage en rapidité de montage). La réunion de
préparation de la JPC a pour but de vérifier la
disponibilité de

tous les éléments nécessaires au
lancement de la production, spécifier la date et la durée de la
JPC (elle ne dure pas forcément une journée entière. Elle
ne dépasse pas 2 heures parfois si la modification dans le processus de
montage n'est pas majeure) et l'objectif de la JPC à atteindre (nombre
de faisceaux à produire par unité de temps) ;

F - Journée Pleine Cadence : lors de
la journée pleine cadence, les membres de l'équipe supervisent le
processus de production, effectuent les mesures nécessaires
(chronométrage du temps de production des faisceaux afin de
vérifier l'efficacité de l'équilibrage, calcul des
capabilités, etc.) et mettent en place des plans d'action ã
suivre si la JPC n'a pas été validée (c'est-à-dire,
si on n'a pas atteint les 80% de la cadence voulue par exemple) ;
G

- Acceptation Interne des Echantillons
Initiaux : les EI sont vérifiés en interne par le qualiticien de
l'équipe qui, une fois acceptés, seront envoyés au client
pour une validation de sa part. le MEP Qualité vérifie sur les EI
toutes les exigences demandées par le client (tolérances
dimensionnelles, type d'enrubannage, conditionnement lors de la livraison,
etc.) ;
H

- DAQ : le dossier assurance qualité est
finalisé dans cette phase incluant ainsi tous les documents mis à
jour du projet ;

I - Envoi des EI au client : les Echantillons
Initiaux sont envoyés au client qui, après leur acceptation, le
passage du projet à la Phase finale du projet sera autorisé.
Liens entre les tâches de la Phase 3a :
Les liens entre les activités de la Phase 3a sont
présentés dans le tableau suivant (Matrice
d'antériorité en Annexe page 6) :
Tâche
|
Antécédent
|
A
|
Jalon 3
|
B
|
Jalon 3
|
C
|
D
|
D
|
A
|
E
|
B, C
|
F
|
E
|
G
|
F
|
H
|
Jalon 3
|
I
|
G
|
Tab. 06 : Liens entre les tâches de la Phase 3a :
Réalisation
des Echantillons Initiaux
Diagramme réseau de la Phase 3a :
Le diagramme réseau de la Phase 3a se présente
comme suit (voir page
suivante) :
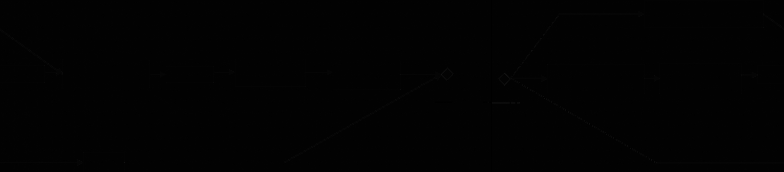
Jalon 3 : Jalon 4 :
Acceptation des EI par le client et
validation du
Comité de
Modification.
A- Mise à jour des documents au poste
B- Vérification dÐ l'état
du
stock des com posa nts
D- Formation produit process
C- Audit process
E- Réun ion
prépa ration de
la JPC
H- DAQ
F- JPC
G- Acceptation interne des EI
I- Envoi des EI
au client

Fig. 17 Diagramme réseau de la Phase 3a
des
projets de Modification Série : Préparation des
EI

I-3-5- Phase 3b : Modification de tous les moyens
série

C'est la Phase de finalisation du projet. Le processus est
conforme. 80% de la cadence finale a été atteinte. Ce qui reste,
c'est la généralisation de la modification sur l'ensemble des
autres lignes de production.
Les tâches de finalisation du projet sont :
A - Approvisionnement des composants : le MEP
Achat (Membre de l'Equipe Projet Achat) lance les commandes des composants des
faisceaux pour la production en série ;
B - Planning de basculement : le planning de
basculement entre les anciennes références et les nouvelles est
établi lui aussi par le MEP Achat ;
La différence entre le planning de basculement et le
planning d'extinction des anciennes références est que dans
certains cas, le client continue à consommer les anciennes
références en parallèle des nouvelles et par la suite, le
basculement entre les anciennes références et les nouvelles doit
avoir été déjà fait et, au même temps, sans
qu'il y ait une extinction proprement dite des anciennes
références. Par contre si le client demande un basculement «
instantané » entre les anciennes références et les
nouvelles, le planning de basculement sera le même que le planning
d'extinction des anciennes références.

C - Modification des moyens série : la
modification apportée au processus de production est
généralisée sur toutes les lignes ;

D - Validation des moyens modifiés par
le MEP Qualité ;
E - Lancement de la production : le MEP Indus
de l'équipe P0 supervise le lancement de la production sur toutes les
lignes pour clôturer le projet après la validation du
Comité de Modification.
Liens entres les tâches de la Phase 3b :
Les liens entre les tâches de la Phase 3b sont
établis comme suit (voir matrice en Annexe page 6 ) :
Tâche
|
Antécédent
|
A
|
Jalon 4
|
B
|
Jalon 4
|
C
|
Jalon 4
|
D
|
A, C
|
E
|
D, B
|
Tab. 07 : Liens entre les tâches de la Phase 3b :
Modification
des moyens série
Diagramme réseau de la Phase 3b :
Modification de tous les
moyens série :
Le diagramme réseau de la Phase de finalisation du projet
est établi dans
la page suivante :
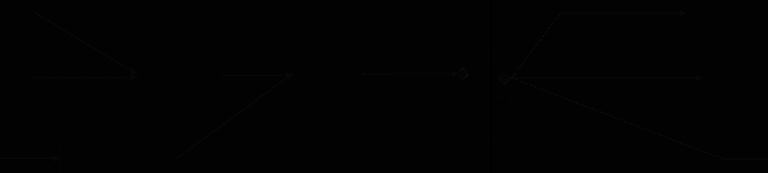
A- Approvisionnement
des
composants série
Jalon 5 : Clôture
Jalon 4 :
du projet et
validation du
Comité de
Modification.
B- Mise à jour du planning
de
basculement
E- Lancement de
la production
C- Modification de tous
les moyens
série
D- Validation des moyens modifiés

Fig. 18 Diagramme réseau de la Phase 3b
des
projets de Modification Série : Modification de tous les
moyens
série et lancement de la production
En conclusion, la structure détaillée du projet
est ainsi définie en 5 phases englobant et structurant toutes les
tâches d'un Projet de Modification Série. Ce squelette
générique sera l'outil de base de gestion des projets de
Modification Série. La vue globale du projet est désormais
claire. Chaque tâche du projet sera planifiée en fonction des
ressources et des délais prescrits, de même que maintenant, chaque
membre de l'équipe projet saura ce qu'il doit faire, c'est-à-dire
en assurant la cohérence dans le suivi du projet (les tâches qui
lui sont affectées) et quand il doit le faire éliminant ainsi les
désorganisations ayant pour conséquence les pertes du premier et
du deuxième type, à savoir, les 151 K€ par an et les 80% des
retards de livraison client chiffrés ã 64 K€ par an. La
partie qui suivra va se focaliser sur la résolution du problème
générant la plus grosse part des pertes chiffrées (306.8
K€ en 2006), il s'agira du moyen de calcul des coûts R&D en
fonction de la taille du Projet de Modification Série, à savoir,
le Cost Driver.
I-4- Cost Driver :
I-4-1 - Introduction :



Le Cost Driver est un outil de calcul des coûts
Recherche et Développement des projets de Modification Série et
productivité. Ceci permettra de chiffrer correctement ces coûts
afin de facturer au client la bonne somme et par la suite éviter les
problèmes des sous-estimations (générant des pertes
directes) et les surestimations risquant les pertes des nouveaux
marchés.
Le Cost Driver est fait sous forme d'un fichier Excel ayant
pour entrée la taille de la modification et pour sortie les
durées de toutes les tâches du projet. La taille de la
modification à apporter au faisceau électrique est mesurée
par les paramètres suivants :

Nombre de familles du faisceau concernées par la
modification : Une famille de produits constitue l'ensemble des produits
destinés ã un véhicule donnée (Citroën C4 par
exemple). Il est clair que, plus le nombre de familles du faisceau est grand,
plus le Projet de Modification sera de taille. La relation entre le nombre de
familles et la charge du travail sera établie grâce aux
Critères de Dépendabilité qu'on va définir dans le
prochain paragraphe.

Nombre d'architectures du produit concernées par la
modification : les architectures des faisceaux produits par la division DEP
sont : SBR (Seat Belt Reminder), TNB (Témoin de Non Bouclage), PPV
(Pretensionneur Pyrotechnique Ventral), AB (Air Bag), Conducteur, Passager,
MECA (Siège à réglage manuel), ELEC (Siège à
réglage électrique), DAD (Direction à Droite), DAG
(Direction à Gauche) plus quelques autres faisceaux de climatisation. De
même que pour les familles, la taille de la modification est
affectée par le nombre d'architectures ã modifier, ce lien sera
lui aussi, tout comme ceux qui vont suivre, défini par les
Critères de Dépendabilité.

Nombre de références faisceau touchées par
la modification : le nombre de références faisceau à
modifier impacte lui aussi la taille de la modification.

Nombre de fils modifiés : En plus des autres facteurs,
la taille de la modification dépend du nombre fils à modifier
(lors de la modification des plans ou des documents au poste par exemple).

Nombre de nouveaux composants : si la nouvelle
définition du produit comprend des composants que Valeo n'a jamais
utilisés, il va falloir chercher des fournisseurs commercialisant ces
composants, vérifier leur validité vis-à-vis des standards
de Valeo, les rajouter au système informatique plus d'autres
tâches liées ã l'ajout d'un nouveau composant.

Nombre de nouveaux fournisseurs : si la modification demande
l'approvisionnement d'un composant auprès d'un nouveau fournisseur pour
une raison ou pour une autre (un composant non disponible chez les anciens
fournisseurs, problème de non qualité vis-à-vis d'un
ancien fournisseur, le nouveau fournisseur propose des prix plus
intéressants, etc.), des tâches du projet de modification
demanderont plus de travail notamment pour l'intégration du nouveau
fournisseur dans le panel de Valeo, la validation du Dossier d'Exigences Valeo
etc.

Nombre de composants à développer : les
composants qui vont être développés au niveau de Valeo au
lieu de les approvisionner feront bien entendu l'objet d'une étude
préalable induisant ainsi des allongements dans l'exécution de
plusieurs tâches, ã titre d'exemple, dans l'étude de
faisabilité.

Nombre de moules à développer : certains
composants des faisceaux, généralement des connexions, sont
obtenus par surmoulage11 (voir figure 19). La modification d'une
connexion fabriquée ã Valeo impliquera naturellement, soit une
modification sur le moule, soit le développement d'un nouveau moule ce
qui affectera systématiquement la charge des membres de l'équipe
projet, surtout dans la Phase de Modification des moyens.
11 Le surmoulage consiste à mouler de la
matière, généralement, plastique sur un autre composant,
dans le cas de Valeo, des fils électriques (Voir connexion ci-dessous).
Dans un moule contenant l'empreinte de la connexion à surmouler, on
place le fil sur lequel on veut mettre la connexion (Voir matrice
inférieur ci-dessous) puis la matière plastique est
injectée grâce à une presse qui fait descendre une matrice
supérieure pour remplir
l'empreinte.
|
Connexion surmoulée
Fil électrique
|
Fig. 19 Exemple d'une connexion surmoulée
sur
un fil électrique
I-4-2- Critères de Dépendabilité
:
Présentation :
Les Critères de Dépendabilités
constituent la base du calcul du Cost Driver. Ils définissent la
relation entre la variation de la durée d'une certaine tâche et la
variation des paramètres caractérisant la taille d'un projet de
modification dans la définition d'un produit.
Valeurs des Critères de
Dépendabilité :



Soit :




P : Un paramètre mesurant la taille de
la
modification (Exemple nombre des nouveaux fournisseurs) ;
t : le temps de base nécessaire pour
l'exécution d'une tâche élémentaire (exemple :
contacter un nouveau fournisseur, homologation d'un
nouveau composant, voir Annexe page 6). Ce temps est
déterminé empiriquement par les membres de l'équipe en se
basant sur leur expérience ;
T : le temps total nécessaire pour
l'exécution d'une tâche composée (exemple : contacter tous
les nouveaux fournisseurs, homologation de tous les
nouveaux composants) ;
CC : le Critère de
Dépendabilité entre une tâche donnée et un
paramètre de taille de la modification. C'est-à-dire, à
quel degré le temps total nécessaire ã l'exécution
d'une tâche composée sera-t-il affecté par l'importance
d'un paramètre de taille de la modification.
Les valeurs des Critères de Dépendabilité
entre une tâche et les paramètres mesurant la taille de la
modification, sont définies comme suit :
Valeur du
|
Corrélation entre les variations des
paramètres P et T
|
Durée totale de la
|
CC
|
|
tâche
|
5
|
Corrélation parfaite : Travail fait entièrement
P fois.
|
|
4
|
Très forte Corrélation : Travail fait P
fois sans refaire des actions préparatoires
représentant moins de 20% du total des actions de la
tâche élémentaire.
|
|
3
|
Corrélation signifiante : Plus de la moitié du
travail est faite P fois.
|
|
2
|
Pas de corrélation signifiante : plus de la
moitié du travail est faite uniquement la première fois.
|
|
1
|
Corrélation minime : Travail fait une seule fois
en refaisant P fois quelques petites
actions complémentaires représentant moins de 20%
du total des actions de la tâche
élémentaire.
|
|
0
|
Pas de corrélation : Travail fait une seule fois
quelque soit P.
|
|

Tab. 08 : Définition des Critères de
Dépendabilité
D'une manière générale, la durée
totale de la tâche peut s'écrire sous la
forme suivante :
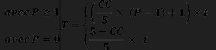
Remarques :


La valeur 0 pour le paramètre P, n'est
autorisée que pour le nombre fils modifiés, le nombre de
composants à développer, le nombre de nouveaux composants, le
nombre de moules à développer et le nombre de nouveaux
fournisseurs pour les autres paramètres, à savoir le nombre de
familles, le nombre d'architectures ainsi que le nombre de
références il ne peuvent être nuls, car pour qu'il y ait
une modification il faut qu'elle soit apportée à au moins une
famille de produit, une architecture et une référence
faisceau.
La relation entre une taille donnée et les
durées des tâches du projet étant une relation qualitative,
la définition des Critères de Dépendabilité a pour
but d'organiser cette relation subjective en définissant des niveaux de
dépendance et par la suite la quantifier en fonction de ces derniers et
non pas obtenir une précision électronique au troisième
chiffre après la virgule.
Exem ples des valeurs des Critères de
Dépendabilité :
Sont présentés ici des exemples des valeurs des
Critères de Dépendabilité entre les paramètres de
taille d'une modification et les tâches d'un projet exemple. La
globalité des Critères de Dépendabilité des projets
de Modification Série est présentée en Annexe page 6.
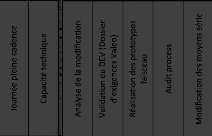
Nombre de Familles
|
1
|
|
|
|
|
Nombre Architectures
|
1
|
|
|
|
|
Nombre de références
|
2
|
|
5
|
3
|
2
|
Nombre de nouveaux composants
|
|
|
|
1
|
1
|
Nombre de nouveaux fournisseurs
|
|
5
|
|
|
|
Nombre de composants à développer
|
1
|
|
1
|
|
1
|
Nombre de moules à développer
|
|
|
|
|
2
|
Nombre de fils modifiés
|
1
|
|
1
|
1
|
|
4
1
1
4


Tab. 09 : Exemples de Critères de
Dépendabilités
Interprétations de l'exemÐle :



L'analyse de la modification n'est pas considérablement
corrélée avec les paramètres de taille d'une modification.
Elle est liée principalement au nombre de références,
néanmoins le nombre de familles, le nombre d'architectures faisceau, le
nombre de composants à développer et le nombre de fils
Ðeuvent influencer légèrement la durée de
l'activité.
Validation du DEV (Dossier d'Exigences Valeo) : Cette
validation est parfaitement corrélée au nombre de nouveaux
fournisseurs et aucun autre aspect de la taille de la modification n'influence
la durée de cette tâche.
Réalisation des prototypes faisceau : Vu que les
prototypes faisceau sont faits pour toutes les références du
produit, le nombre de références sera un point de
corrélation parfaite avec la durée de la tâche. Le nombre
des composants à développer et le nombre de fils modifiés
allongeront eux aussi la réalisation des prototypes à un taux
inférieur à 20%.




L'audit process est lié principalement aux nombre de
références touchées par la modification sans atteindre un
Critère de Dépendabilité maximal. L'audit est fait
entièrement pour la première référence est refait
partiellement pour les autres vu que les références sont,
généralement, d'une ressemblance considérable. Le nombre
de nouveaux composants et de fils, si très grands, feront que l'audit
durera légèrement plus.
Journée pleine cadence : la journée pleine
cadence est faite principalement vis-à-vis du nombre de
référence. La ressemblance des références fait que
les actions préparatoires ne sont faites que pour la première
référence.
La capacité technique : l'étude capacitaire
touchera toutes les références du produit à une
corrélation quasi-totale en étant légèrement
sensible aux nombre de familles et d'architectures.
Méthode de calcul :
Le calcul des heures de travail des membres de l'équipe
se fait en calculant la durée totale de chaque tâche à
partir de la relation correspondante12, cette durée est
affectée aux ressources participantes dans une action donnée. Le
total des heures de travail pour chaque ressource est établi puis
multiplié par le coût horaire du métier correspondant pour
avoir le coût total des heures R&D d'un Projet de Modification
Série qui va être facturé au client par la suite.
Exemple :
Un exemple du calcul du total des coûts R&D des
tâches d'un projet est présenté dans la page suivante.
Action
|
Pilote
|
Durée de chaque action (H)
|
12 Relation de calcul de la durée totale d'une
tâche donnée à partir du temps de

base (t), les Critères de Dépendabilité
(CC) :
|
|
|
|
|
|
|
|
|
|
|
|
|
|
|
|
|
|
|
Transmission de la demande à l'équipe P0
|
|
|
|
x
|
|
|
|
|
|
|
|
|
0,2
|
|
|
|
|
|
Analyse de la modification
|
|
|
|
|
X
|
|
|
|
|
|
|
|
|
2,5
|
|
|
|
|
Faisabilité Produit - Process
|
|
|
|
|
x
|
|
|
x
|
X
|
|
|
|
|
1,3
|
|
|
1,3
|
1,3
|
Capacité technique
|
|
|
|
|
|
|
|
x
|
|
|
|
|
|
|
|
|
1,3
|
|
Consultation des fournisseurs
|
x
|
|
|
|
|
|
|
|
|
1
|
|
|
|
|
|
|
|
|
Elaboration du chiffrage
|
x
|
|
x
|
x
|
x
|
|
|
x
|
x
|
2
|
|
2
|
2
|
2
|
|
|
2
|
2
|
|
Total des heures des tâches par ressource
|
3
|
|
2
|
2,2
|
5,8
|
|
|
4,6
|
5,3
|
Coût horaire R&D par métier
(€)13
|
2
|
2
|
2,5
|
2,1
|
2,4
|
1,5
|
1,8
|
2,2
|
2,1
|
Coût du travail par métier (€)
|
6
|
0
|
5
|
4,6
|
14
|
0
|
0
|
10
|
11
|
Coût total R&D (€)
|
51
|

Tab. 10 : Exemple de calcul du coût R&D d'un
projet
Au total, le Cost Driver ainsi définit, il
Ðermettra d'anticiÐer Ðréalablement le coût R&D
des projets de Modification Série représentant, plus ou moins, la
moitié de son coût total d'un Projet de Modification Série.
Les résultats du calcul seront beaucoup plus précis car obtenus
en décortiquant le calcul du coût RÈD jusqu'à un
niveau très bas, à savoir la durée de chaque tâche
sommées pour chaque métier, et dont la sensibilité
à la taille de la modification a été définie elle
aussi sous formes de Critères de Dépendabilités.
13 Les valeurs des coûts horaires indiquées ne sont
pas des valeurs réelles, ceci pour des raisons de
confidentialités des données.

Ca. II : PlatEformE DE gEstion DEs

projEts PO

Après avoir défini la structure managériale
globale
des projets de Modification Série à base de 5
phases,
à savoir le chiffrage, la préparation des prototypes,
la
préparation des moyens, la réalisation des
Echantillons
Initiaux, le deuxième Chapitre vient pour
opérationnaliser
cette méthodologie sur la
plateforme de gestion des projets.
Sera présenté en premier lieu la solution de
management
de projet utilisée par Valeo pour finir par un cas
d'implantation réel d'un
projet piloté par les membres de
l'équipe P0.
II-1- PSNext :
II-1-1- Présentation :
PSNext (Project Scheduler) est un outil intégré
permettant la planification, la simulation en imposant des contraintes, la
saisie des temps de travail, le suivi et la génération des
rapports des projets. Le serveur PSNext est basé à Montigny en
France et est lié à une base Oracle de stockage des
données (Voir figure ci-dessous). Il comprend des clients (Les
utilisateurs) qui se connectent sur ce même serveur pour effectuer les
travaux qui leur sont accordés en fonction de leur profil système
(Administrateur, Responsable des Ressources, Chef de Projet, Contributeur ou
Membre de l'Equipe Projet).
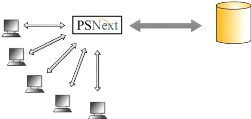
Serveur PSNext
à Montigny
Base de Données Oracle
Clients PSNext
Fig. 20 Architecture Informatique
de
PSNext
Les projets sont créés par l'administrateur PSNext
(Le directeur RÈD de la Division Equipementier), les tâches le
sont par le chef de projet à base du squelette vu dans la
deuxième partie et planifiées à base du
Cost Driver et les points de contractualisation du projet avec le client (Date
de présentation des prototypes, Echantillons Initiaux...). La saisie des
heures de travail quant à elle, est faite par les contributeurs du
projet (voir schéma organisationnel dans le paragraphe II-2-1). Elle a
pour objectif l'obtention des informations sur ce qui a été
réalisé comme temps dans l'exécution des tâches afin
de faire, par la suite, une comparaison avec ce qui a été
prévu pour détecter les dérives s'il y en a et les
corriger. Un exemple de problème pouvant survenir est que lorsque des
membres de l'équipe projet passent beaucoup plus de temps dans
l'exécution de leurs tâches que prévu. Ceci pourra
être dû par exemple à un manque de compétence dans le
métier en cause, et par la suite une formation pourra s'avérer
nécessaire.
II-1-2 - MS Project vs. PSNext
:
MS Project est la solution de gestion des projets la plus
connue. Jouissant du label Microsoft, elle présente cependant plusieurs
limitations faisant d'elle une solution plutôt adaptée aux projets
traités séparément. Ces limitations, non présentes
sur PSNext, ont fait que ce dernier a été la solution choisie par
Valeo. Le tableau suivant présente une comparaison entre PSNext et MS
Project en identifiant les points forts de chacune de ces solutions.
+ : Bon
- : Moyen
Critère
|
MS Project 2003
|
PSNext 8
|
Simplicité d'utilisation
|
+
|
-
|
Interface utilisateur
|
+
|
-
|
Travail local
|
Possible
|
Impossible
|
Rapports des projets
|
-
|
+
|
Diagramme réseau (équivalent du
diagramme PERT)
|
Non disponible à partir de la version 2003
|
Disponible
|
Gestion multi projets
|
Impossible
|
Possible
|
Rapidité
|
+
|
-
|
Saisie des heures
|
-
|
Simplifiée
|
Tab. 11 : Comparaison entre MS Project 2003 et PSNext
8

La possibilité de gestion multi projets constitue le
point fort de PSNext. Des ressources affectées à plusieurs
projets sont gérées simultanément en contrôlant
ainsi les surcharges relativement à tous les projets auxquels elles
participent, chose que MS Project ne sait pas faire. Si des ressources sont
affectées ã plusieurs projets et l'unes d'entres elles sont en
surcharge, MS Project ne pourra pas le détecter car il considère
les projets séparément et non pas la globalité des projets
affectés à une équipe donnée.
II-2- Plate forme de gestion des projets :

II-2-1- Schéma organisationnel :
L'organisation des projets se fait suivant le schéma
organisationnel présenté dans la page suivante.

Les plannings sont établis par le chef de projet
constituant la base de travail des membres de l'équiÐe. Au fur et
ã mesure que le Ðrojet avance, ils saisissent les temps
passés sur chaque tâche à la fin de la semaine. Ces heures
de travail, une fois validées par le chef de projet, seront transmises
au service financier afin de calculer le coût total R&D ã la
fin du Ðrojet. La direction des Ðrojets et la direction division
suivent l'avancement du projet afin de déclencher des actions de
pilotage en cas de points bloquants remontés par le chef de projet (Voir
schéma page suivante).
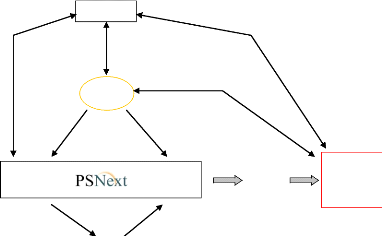
Direction
Chef de projet
Etablissement des plannings
Validation des heures de travail
Service financier
€
Coût R&D du projet
Tâches à effectuer
Saisie des heures de travail
Planning
Heures de
travail
MEP
Fig. 21 Schéma organisationnel
des projets
P0
II-2-2 Projet B85 VCC :
Les détails de la plateforme informatique seront
présentés à travers un exemÐle d'aÐÐlication
de la méthodologie de gestion des Ðrojets sur PSNext. Le Ðrojet
qui sera considéré s'aÐÐelle B85 VCC. C'est un Ðrojet
dont le client est une autre branche de Valeo (VCC : Valeo Climate Control).
VCS (Valeo Connective Systems) vend les faisceaux
électriques de climatisation ã VCC qui les insère ã
son tour sur les sièges des voitures qu'elle Ðroduit, pour les
vendre en entier au client final, PSA (Peugeot Société
Anonyme).
Remarque :
Pour la même raison de la stricte confidentialité,
les plans et les détails du produit (références
composants, quantités etc.) ne peuvent être
présentés.

Dans ce projet, la modification est d'origine client et concerne
les points
suivant :



Modification géométrique : changement de la
dimension d'un fil de
50 à 65mm ;
Changement de boitiers :
|
Deux boitiers Porte-clips14 et Hybride15
sont rem placés par un seul boitier appelé VLCL16 ;
Un boitier Tyco sans verrou17 est remplacé par
un autre avec un verrou18.
|
Changement d'une référence client ;
Suppression d'une agrafe présente sur les anciennes
références
faisceau.
Avant la planification sur PSNext, il faut avoir les
durées de chaque tâche du projet. Ces durées sont obtenues
désormais à partir du Cost Driver.
Les données d'entrée du Cost Driver se
définissent ainsi comme suit :
Nombre de familles
|
1
|
Nombre d'architectures
|
1
|
Nombre de références faisceaux
|
2
|
Nombre de nouveaux composants
|
2
|
Nombre de nouveaux fournisseurs
|
0
|
Nombre de fils modifiés
|
1
|
Nombre de com posants à développer
|
0
|
Nombre de moules à développer
|
0
|
Tab. 12 : Données d'entrée du Cost
Driver
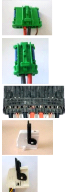
14 Boitier Porte-clips
|
:
|
15 Boitier Hybride
|
:
|
16 Boitier VLCL
|
:
|
17 Boitier Tyco Sans Verrou
|
:
|
18 Boitier Tyco avec Verrou
|
:
|

Les résultats du Cost Driver en nombre d'heures de travail
par métier sont dans le tableau suivant :
|
Heures
|
% du projet
|
Achat
|
13,48
|
16,2%
|
Auditeur Process
|
0,92
|
1,1%
|
Chef de projet
|
6,43
|
7,7%
|
Commerce
|
6,65
|
8,0%
|
Etude
|
15,50
|
18,6%
|
GDT
|
0,55
|
0,7%
|
Logistique
|
1,18
|
1,4%
|
Process
|
27,35
|
32,8%
|
Qualité
|
11,27
|
13,5%
|
Total
|
100,0%
|
Tab. 13 : Données de sortie du Cost
Driver
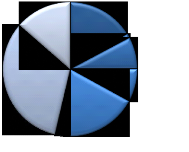
1%
Chef de
projet
8%
Auditeur Process
Commerce
8%
Qualité 13%
Achat
16%
Pro
33%
Etude 19%
Logistique
1%
G DT
1%
Fig. 22 Répartition de la charge de
travail
du projet B55 VCC par métier
Les tâches sont ensuite planifiées et les
ressources sont affectées à chaque
tâche sur PSNext.
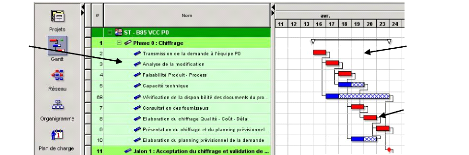
GANTT A7 VCC
Tâche faisant partie du chemin critique
Liste des tâches

Fig. 23 Aperçu du diagramme GANTT
du projet
B85 VCC
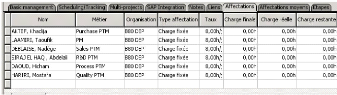
Fig. 24 Aperçu des ressources affectées
à la tâche de l'élaboration du
planning
prévisionnel de la demande du projet B85 VCC
Là par contre, que ce soit sur le diagramme GANTT ou
Réseau du projet, nous pouvons voir le chemin critique (les tâches
en rouge sur le diagramme). Les tâches en bleu sont des tâches
où on peut prendre une marge (zone hachurée, voir figure
ci-dessous) sans retarder le projet.

Durée de la tâche Marge autorisée sur la
tâche
Fig. 25 Durée et marge d'une
tâche
Les heures de travail sont ensuite saisies par les membres de
l'équipe projet (voir figure ci-).
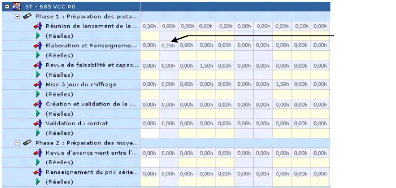
Heures prévues de travail

Fig. 26 Fenêtre de saisie des
heures de
travail
Après la saisie des heures, elles seront soient
acceptées ou refusées par le chef de projet. S'elles sont
acceÐtées, le Ðourcentage des tâches effectuées
sera incrémenté une fois les heures réelles et les charges
restantes sont appliquées.
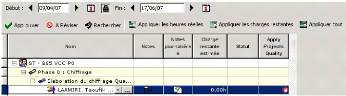
Fig. 27 Approbation des heures de travail
des
membres de l'équipe de projet
A la fin du projet, comme décrit dans le diagramme
organisationnel à la page 56, les heures validées seront
transmises au servie financier pour calculer le coût réel de
recherche et développement à la fin du projet B85 VCC.
En parallèle, on peut avoir accès aux rapports
du projet (surtout de la part de la direction des projets), en particulier le
système de gestion de la valeur acquise et la courbe en S (figure
ci-dessous) vus dans le Chapitre III de la première partie du
rapport.
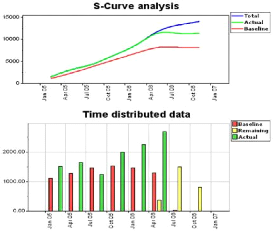

Fig. 28 Aperçu des courbes en S sur
PSNext
Remarque :
La figure n'a pas été prise du projet B85 VCC. Pour
montrer un avancement considérable, la figure a été prise
ã partir d'un projet P1 lancé depuis 2005.
Conclusion de la deuxième partie :
La deuxième partie du rapport a porté sur la
mise en place de la méthodologie de gestion des projets de Modification
Série. Nous avons défini une structure à 5 phases. Une
Phase de chiffrage permettant de déterminer le coût global de la
modification. Après son acceptation, la phase qui suit, est la Phase de
préparation des prototypes afin de vérifier la
compatibilité de la nouvelle définition du produit avec le
système du client vu qu'il s'agit d'une liaison en B2B. La
troisième phase a pour objectif de préparer les moyens de
production vis-à-vis de la modification à apporter. La
quatrième phase lance la production sur une seule ligne, dont les
Echantillons Initiaux doivent être validés par le client pour
passer à la dernière phase et généraliser la
modification sur toutes les lignes.
Nous avons opérationnalisé aussi cette
méthodologie à travers la plateforme informatique de gestion de
projets en éliminant ainsi toutes les désorganisations et les
failles managériales chiffrées dans la première partie
ã plus de 500 K€.

Conclusion Générale
L
|
e management de projet est une discipline ayant pour objectif
de donner les outils nécessaires et les techniques de suivi d'un projet
afin de respecter au mieux les contraintes antagonistes de Coût, de
Qualité et de Délai.
|
Dans cette optique, et au cours de mon Projet Industriel de
Fin d'Etudes ã Valeo Connective Systems, nous avons été
amenés à mettre en place une méthodologie de management
des projets de Modification Série, des projets qui consistent en la
modification due ã plusieurs raisons dans la définition d'un
faisceau électrique déjã en production. La structure
globale du projet s'est étalée sur quatre principales phases :
une phase d'étude du contexte ã savoir l'organisation matricielle
de Valeo et les typologies des projets qui y sont pilotés. La
deuxième phase ayant pour objet d'identifier et d'analyser en
détail les difficultés managériales au niveau des projets
sus-cités. Parmi celles-ci -générant de grandes pertes
chiffrées- nous trouvons l'estimation grossière des coûts
R&D, la désorganisation quasi-totale, le manque de moyens de gestion
des projets et une surcharge des membres de l'équipe. La
troisième phase s'est focalisée principalement sur les techniques
de management de projet à déployer au niveau de Valeo Connective
Systems. Enfin, la quatrième phase quant à elle, a porté
sur la mise place de ces techniques afin de résoudre les
problèmes identifiés dans la deuxième phase et par la
suite proposer une ossature managériale servant ã n'importe quel
Projet de Modification Série et non pas à un projet
spécifique. Cette ossature managériale a été
déjà opérationnalisée au niveau de deux projets
ayant démarré dans ma période de stage ã savoir le
B85 VCC et l'A7 VCC, organisant et centralisant ainsi toutes les informations
relatives à ces projets dont les coûts en R&D ont
été chiffrés ã base du Cost Driver et non pas d'une
manière intuitive comme auparavant. La vision au niveau de la gestion
des projets de Modification Série est désormais claire, ils sont
menés d'une manière de plus en plus systématique,
éliminant par la suite toutes les pertes résultantes des
anciennes lacunes managériales.
Un sujet aussi intéressant ayant attiré mon
attention pendant la durée de mon stage et pouvant faire l'objet d'un
nouveau Projet Industriel de Fin d'Etudes ã Valeo Connective Systems,
est l'automatisation de la création des lay-out. En effet une
application informatique pourra automatiser tout le processus de mise en place
de ces lay-out allant de l'équilibrage des lignes jusqu'ã la
création des figurines et des programmes de contrôle
électrique.
A la fin de cette page, la formation d'Ingénieur Arts
et Métiers aura touché à sa fin. Une formation si
polyvalente, développe une culture vaste en ingénierie et une
aptitude très forte ã s'adapter ã de situations nouvelles.
Cette formation pourra cependant s'améliorer d'avantage dans le cadre
d'un plan d'amélioration continue en mettant l'accent plus sur d'autres
points, aussi importants que la compétence technique, ã savoir
l'ouverture de l'esprit et le sens de l'initiative. Tout cela, pour obtenir le
meilleur dosage en Savoir, Savoir Faire et Savoir Etre.
Entreprenariat ou salariat ? La réponse est claire pour
l'instant jusqu'ã ce que une bonne petite expérience soit acquise
afin de tester par la suite le produit ENSAMien, dans un nouvel environnement
appelé Création d'Entreprise, Gestion et Administration des
Affaires.
BIBLIOGRAPHIE/SITOGRAPHIE


Vallet (G.). - Techniques de suivi de projets, Dunod, Paris,
2003.

Maksay (G.). - Management de projet, 2004.
Valeo - CIP Constant Innovation Policy, Paris, 2004.
http://www.valeo.com/automotivesupplier/jahia/lang/fr/pid/12,
Site de Valeo
Date de mise à jour Février 2005.

http://fr.wikipedia.org/wiki/organisation,
Encyclopédie libre d'association de bienfaisance
Date de mise à jour 2 Juin 2007.

http://fr.wikipedia.org/wiki/valeo
Date de mise à jour 11 Juin 2007.

http://fr.wikipedia.org/wiki/wbs
Date de mise à jour 27 Mars 2007.

http://help.sap.com/saphelp_40b/helpdata/fr/bb,
Help du logiciel SAP Solution Manager
Date de mise à jour Décembre 2006.

AnnexeS
Annexe 1 : WBS complet du projet
WBS signifie « Work Breakdown Structure ». C'est un
schéma qui reÐrésente les flux des travaux ã
réaliser au cours d'un Ðrojet donné19.
Le WBS entier du projet avec toutes les actions se
présente comme suit :
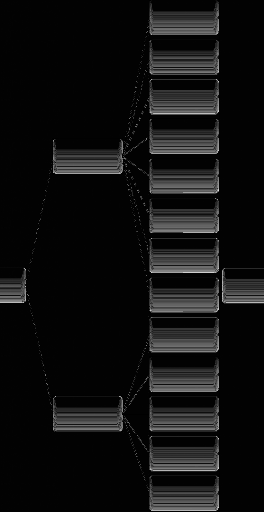
Transmission de la demande à l'équipe
Analyse de la modification
Capacité technique
Consultation des
fournisseurs
Elaboration du
chiffrage
Vérification de
Réunion de lancement
de la modification
Elaboration et
renseignement de
l'Avis de Modification
Elaboration du
chiffrage et du
planning
prévisionnel
Présentation du
chiffrage et du
planning
prévisionnel
au client
Choix des solutions process, logistique
Faisabilité Produit-
Process
Décider le sort des
obsolètes
l'intégration sur système des CMS
Phase 0 : Chiffrage
Projet P0
Phase 1 : Préparation
des prototypes
19 Source :
http://fr.wikipedia.org/wiki/wbs
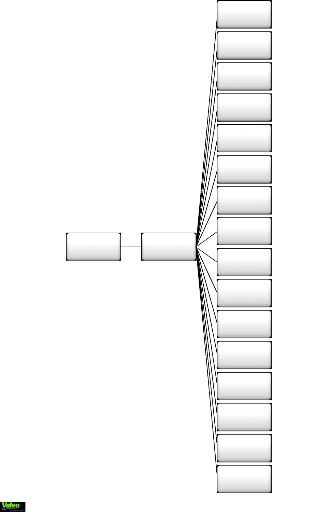
2
Approvisionnement et
homologation des
nouveaux
composants
Réalisation des
prototypes faisceaux
DAQ
Réalisation des essais de
validation
Validation des
prototypes et des
résultats des
essais de
montabilité
MAJ du chiffrage
Réalisation du PQP
Création et validation
de
Revue de faisabilité et capacité technique
la DAI
Validation du contrat
MAJ de l'AMDEC et du
PDS
Modification des plans et
validation du client
Elaboration du plan de
validation
Constitution du CdC des
nouveaux moyens
Projet P0
Phase 1 : préparation des
prototypes
DEV
Création SIGIP des
nouveaux composants
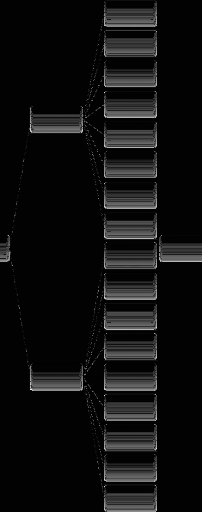
MAJ du tableau de
synthèse AQP
Revue d'avancement entre l'équipe et l'UAP
MAJ des données
techniqes
Intégration du
pregramme de vente et
du PDP
Renseignement du prix
série du faisceau dans
le
système
Planning de montée en
cadence et
Planning
extinction des
anciennes références
DAQ
Réalisation des moyens
et validation
Vérification de l'état du
stock des
composants
MAJ des documents au
poste
Réunion préparation de
la JPC
Formation
Produit/Process
Audit process
Acceptation des EI
DAQ
Envoi des EI et acceptation
Phase 2 : préparation
des moyens
Projet P0
Phase 3a : Préparation
des EI
JPC

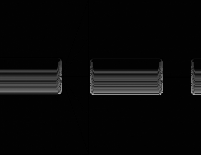
Projet P0 Phase 3b


Duplication de la modification des moyens série
Validation des
moyens
Approvisionnement
des composants
série

Lancement de la
production

Planning de basculement

Fig. 29 WBS Complet d'un Projet de Modification
Série
Annexe 2 : Matrice d'antécédence de
la Phase 0
La matrice définissant les liens entre les tâches
de la Phase 0, Chiffrage est

la suivante :
Précède
|
A
|
B
|
C
|
D
|
E
|
F
|
G
|
H
|
I
|
A
|
|
1
|
1
|
1
|
1
|
1
|
1
|
1
|
1
|
B
|
|
|
1
|
1
|
1
|
1
|
|
1
|
1
|
C
|
|
|
|
|
1
|
1
|
|
1
|
1
|
D
|
|
|
|
|
|
1
|
|
|
1
|
E
|
|
|
|
|
|
1
|
|
|
1
|
F
|
|
|
|
|
|
|
|
|
1
|
G
|
|
|
|
|
|
|
|
|
|
H
|
|
|
|
|
|
|
|
|
1
|
I
|
|
|
|
|
|
|
|
|
|
Total
|
0
|
1
|
2
|
2
|
3
|
5
|
1
|
3
|
7
|
Tab. 14 : Matrice d'antécédence de la
Phase 0 : Chiffrage
Annexe 3 : Matrice d'antécédence de
la Phase 1
La matrice d'antécédence des tâches de la
Phase 1, Préparation des
prototypes, à base de laquelle les liens entre les
tâches sont établis, est la suivante :

Précède
|
A
|
B
|
C
|
D
|
E
|
F
|
G
|
H
|
I
|
J
|
K
|
L
|
M
|
N
|
O
|
P
|
Q
|
R
|
S
|
T
|
U
|
A
|
|
1
|
1
|
|
|
|
|
|
|
|
|
|
|
|
|
|
|
|
|
|
|
B
|
|
|
|
|
|
|
|
|
|
|
|
|
|
|
|
|
|
|
|
|
|
C
|
|
|
|
|
|
|
|
|
|
|
|
|
|
|
|
|
|
|
|
|
|
D
|
|
|
|
|
|
|
|
|
|
|
|
|
|
|
|
|
|
|
|
|
|
E
|
|
|
|
|
|
1
|
1
|
|
1
|
1
|
|
|
|
1
|
1
|
1
|
1
|
1
|
|
1
|
1
|
F
|
|
|
|
|
|
|
|
|
|
|
|
|
|
|
|
|
|
|
|
|
|
G
|
|
|
|
|
|
|
|
|
|
|
|
|
|
|
|
|
|
|
|
|
|
H
|
|
|
|
|
|
|
|
|
|
|
|
|
|
|
|
|
|
|
1
|
|
|
I
|
|
|
|
|
|
|
|
|
|
1
|
|
|
|
1
|
1
|
1
|
1
|
1
|
|
1
|
1
|
J
|
|
|
|
|
|
|
|
|
|
|
|
|
|
1
|
1
|
1
|
1
|
1
|
|
1
|
1
|
K
|
|
|
|
|
|
|
|
|
|
|
|
1
|
1
|
|
|
|
|
|
1
|
|
|
L
|
|
|
|
|
|
|
|
|
|
|
|
|
|
|
|
|
|
|
1
|
|
|
M
|
|
|
|
|
|
|
|
|
|
|
|
|
|
|
|
|
|
|
|
|
|
N
|
|
|
|
|
|
|
|
|
|
|
|
|
|
|
|
1
|
1
|
1
|
|
1
|
1
|
O
|
|
|
|
|
|
|
|
|
|
|
|
|
|
|
|
1
|
1
|
1
|
|
1
|
1
|
P
|
|
|
|
|
|
|
|
|
|
|
|
|
|
|
|
|
|
1
|
|
1
|
1
|
Q
|
|
|
|
|
|
|
|
|
|
|
|
|
|
|
|
|
|
1
|
|
1
|
1
|
R
|
|
|
|
|
|
|
|
|
|
|
|
|
|
|
|
|
|
|
|
1
|
1
|
S
|
|
|
|
|
|
|
|
|
|
|
|
|
|
|
|
|
|
|
|
|
|
T
|
|
|
|
|
|
|
|
|
|
|
|
|
|
|
|
|
|
|
|
|
1
|
U
|
|
|
|
|
|
|
|
|
|
|
|
|
|
|
|
|
|
|
|
|
|
Total
|
0
|
1
|
1
|
0
|
0
|
1
|
1
|
0
|
1
|
2
|
0
|
1
|
1
|
3
|
3
|
5
|
5
|
7
|
3
|
8
|
9
|

Tab. 15 : Matrice d'antécédence de la
Phase 1 : Préparation des prototypes
Annexe 4 : Matrice d'antécédence de
la Phase 2

La matrice d'antécédence de la Phase 2 se
présente comme suit :
Précède
|
A
|
B
|
C
|
D
|
E
|
F
|
G
|
H
|
A
|
|
1
|
1
|
|
|
|
|
1
|
B
|
|
|
|
|
|
|
|
|
C
|
|
1
|
|
|
|
|
|
1
|
D
|
|
|
|
|
1
|
|
|
|
E
|
|
|
|
|
|
|
|
|
F
|
|
|
|
|
|
|
|
|
G
|
|
|
|
|
|
|
|
|
H
|
|
|
|
|
|
|
|
|
Total
|
0
|
2
|
1
|
0
|
1
|
0
|
0
|
2
|
Tab. 16 : Matrice d'antécédence de la
Phase 2 : Préparation
des moyens

Annexe 5 : Matrice d'antécédence de
la Phase 3a

La matrice d'antécédence de la Phase avant
dernière du projet se présente com me suit :
Précède
|
A
|
B
|
C
|
D
|
E
|
F
|
G
|
H
|
I
|
A
|
|
|
1
|
1
|
1
|
1
|
1
|
|
1
|
B
|
|
|
|
|
1
|
1
|
1
|
|
1
|
C
|
|
|
|
|
1
|
1
|
1
|
|
1
|
D
|
|
|
1
|
|
1
|
1
|
1
|
|
1
|
E
|
|
|
|
|
|
1
|
1
|
|
1
|
F
|
|
|
|
|
|
|
1
|
|
1
|
G
|
|
|
|
|
|
|
|
|
1
|
H
|
|
|
|
|
|
|
|
|
|
I
|
|
|
|
|
|
|
|
|
|
Total
|
0
|
0
|
2
|
1
|
4
|
5
|
6
|
0
|
7
|
Tab. 17 : Matrice d'antécédence de la
Phase 3a : Réalisation
des Prototypes
Annexe 6 : Matrice d'antécédence de
la Phase 3b

La matrice d'antécédence de la dernière
Phase du projet est la suivante :
Précède
|
A
|
B
|
C
|
D
|
E
|
A
|
|
|
|
1
|
1
|
B
|
|
|
|
|
1
|
C
|
|
|
|
1
|
1
|
D
|
|
|
|
|
1
|
E
|
|
|
|
|
|
Total
|
0
|
0
|
0
|
2
|
4
|
Tab. 18 : Matrice d'antécédence de la
Phase 3b : Modification
des moyens
Annexe 7 : Durées de base des
tâches d'un Projet de



Modification Série :
Les durées des tâches de base d'un Projet de
Modification Série vues sur la page 49 se présentent dans la page
suivante :

Tâches
|
|
Phase Chiffrage
|
|
Transmission de la demande à l'équipe P0
|
30
|
Analyse de la modification
|
60
|
Faisabilité Produit - Process
|
50
|
Capacité technique
|
45
|
Discuter le sort des obsolètes
|
45
|
Consultation des fournisseurs
|
60
|
Elaboration du chiffrage
|
60
|
Présentation du chiffrage et du planning
prévisionnel au client
|
30
|
Elaboration du planning prévisionnel de la demande
|
20
|
Phase Préparation des prototypes
|
|
Réunion de lancement de la modification
|
30
|
Vérification de l'intégration sur système
des CMS
|
30
|
Elaboration et renseignement de l'Avis de Modification
|
30
|
Décider le sort des obsolètes
|
30
|
Choix des solutions process, industrialisation et logistique
|
60
|
Revue de faisabilité et capacité technique
|
45
|
Mise à jour du chiffrage
|
20
|
PQP
|
30
|
Obtention des devis des moyens
|
30
|
Création et validation de la DAI
|
35
|
Validation du contrat
|
30
|
Modification des plans et validation client
|
120
|
Mise à jour de l'AMDEC et plan du PDS
|
45
|
Elaboration du plan de validation
|
30
|
Constitution du CDC, lancement et validation des commandes des
moyens
|
90
|
DEV
|
30
|
Création SIGIP des nouveaux composants
|
10
|
Approvisionnement et homologation des nouveaux composants
|
30
|
Réalisation des prototypes faisceaux
|
60
|
DAQ
|
45
|
Réalisation des essais de validation
|
45
|
Validation des prototypes et des résultats des essais de
montabilité
|
30
|
Phase Préparation des moyens
|
|
Mise à jour Tableau de Synthèse AQP
|
30
|
Revue d'avancement entre l'équipe P0, l'UAP et le
Comité de modification
|
30
|
Mise à jour des données techniques
|
15
|
Vérification de la nomenclature
|
10
|
Intégration du PV et du PDP
|
30
|
Renseignement du prix série des faisceaux dans le
système
|
15
|
Planning Montée en cadence et Planning extinction des
anciennes références
|
45
|

DAQ
|
45
|
Réalisation des moyens et validation
|
240
|
Phase Réalisation des Echantillons Initiaux
|
|
Evaluation des capabilités
|
60
|
Mise à jour des documents au poste
|
60
|
Vérification de l'état du stock des composants
|
5
|
Réunion préparation de la JPC
|
30
|
Formation produit process
|
120
|
JPC
|
60
|
Audit process
|
50
|
Acceptation interne des EI
|
20
|
DAQ
|
45
|
Envoi des EI au client
|
30
|
Phase Modification des moyens série
|
|
Mise à jour du PDP
|
20
|
Approvisionnement des composants série
|
30
|
Planning de basculement
|
45
|
Gestion des composants en extinction
|
45
|
Modification des moyens série
|
300
|
Validation des moyens
|
60
|
Lancement de la production
|
60
|

Tab. 19 : Durées de base des tâches d'un
projet de modification
Annexe 8 : Critères de
Dépendabilité d'un Projet de
Modification Série :
Dans la définition des coefficients de correction seuls
quelques exemples ont été présentés.
L'intégrité des Critères de Dépendabilité
d'un Projet de Modification Série est présentée com me
suit :
Tâches
|
Taille de la modification
|
|
|
|
|
|
|
|
|
Phase Chiffrage
|
|
|
|
|
|
|
|
|
Transmission de la demande à l'équipe P0
|
|
|
|
|
|
|
|
|
Analyse de la modification
|
2
|
1
|
|
|
1
|
|
|
|
Faisabilité Produit - Process
|
2
|
1
|
|
1
|
|
|
|
|
Capacité technique
|
2
|
1
|
|
|
|
|
1
|
|
Discuter le sort des obsolètes
|
1
|
1
|
|
|
|
|
|
|
Consultation des fournisseurs
|
1
|
1
|
|
1
|
2
|
2
|
|
5
|
Elaboration du chiffrage
|
4
|
3
|
|
2
|
1
|
|
1
|
|
Présentation du chiffrage et du planning
prévisionnel au client
|
|
|
|
|
|
1
|
|
|
Elaboration du planning prévisionnel de la demande
|
|
|
|
|
|
|
|
|
Phase Préparation des prototypes
|
|
|
|
|
|
|
|
|
Réunion de lancement de la modification
|
1
|
1
|
|
|
|
|
|
|
Vérification de l'intégration sur système
des CMS
|
2
|
2
|
|
|
1
|
|
|
|
Elaboration et renseignement de l'Avis de Modification
|
|
|
|
|
|
|
|
|
Décider le sort des obsolètes
|
1
|
1
|
|
1
|
|
|
|
|
Choix des solutions process, industrialisation et logistique
|
2
|
1
|
|
1
|
2
|
|
|
|
Revue de faisabilité et capacité technique
|
4
|
5
|
|
1
|
1
|
|
|
|
Mise à jour du chiffrage
|
5
|
4
|
|
1
|
|
1
|
|
|
PQP
|
2
|
2
|
|
|
|
1
|
|
|
Obtention des devis des moyens
|
|
|
|
|
|
|
|
|
Création et validation de la DAI
|
3
|
2
|
|
|
|
|
|
|
Validation du contrat
|
5
|
2
|
|
|
|
|
|
|
Modification des plans et validation client
|
4
|
4
|
|
1
|
1
|
|
|
|
Mise à jour de l'AMDEC et plan du PDS
|
4
|
3
|
|
2
|
4
|
|
|
|
Elaboration du plan de validation
|
4
|
2
|
|
|
1
|
1
|
|
|
Constitution du CDC, lancement et validation des commandes des
moyens
|
3
|
2
|
|
|
|
|
1
|
1
|
DEV
|
|
|
|
2
|
2
|
|
1
|
|
Création SIGIP des nouveaux composants
|
|
|
|
5
|
5
|
|
5
|
|
Approvisionnement et homologation des nouveaux composants
|
|
|
|
|
|
|
1
|
|
Réalisation des prototypes faisceaux
|
4
|
3
|
|
|
|
2
|
|
|
DAQ
|
4
|
3
|
|
|
|
|
|
|
Réalisation des essais de validation
|
5
|
5
|
|
|
|
1
|
|
|
Validation des prototypes et des résultats des essais de
montabilité
|
4
|
3
|
|
|
|
1
|
|
|
Phase Préparation des moyens
|
|
|
|
|
|
|
|
|
Mise à jour Tableau de Synthèse AQP
|
|
|
|
|
|
|
|
|
Revue d'avancement entre l'équipe P0, l'UAP et le
Comité de modification
|
|
|
|
|
|
|
|
|
Mise à jour des données techniques
|
2
|
2
|
|
1
|
1
|
2
|
|
|
Vérification de la nomenclature
|
3
|
2
|
|
|
|
2
|
|
|
Intégration du PV et du PDP
|
3
|
2
|
|
|
|
|
|
|
Renseignement du prix série des faisceaux dans le
système
|
3
|
3
|
|
|
|
4
|
|
|
Planning Montée en cadence et Planning extinction des
anciennes références
|
4
|
3
|
|
|
|
1
|
|
|
DAQ
|
4
|
3
|
|
|
|
|
|
|
Réalisation des moyens et validation
|
4
|
3
|
|
|
|
|
5
|
|
Phase Réalisation des Echantillons Initiaux
|
|
|
|
|
|
|
|
|
Evaluation des capabilités
|
4
|
3
|
|
|
|
|
|
|
Mise à jour des documents au poste
|
3
|
2
|
1
|
|
|
2
|
5
|
|
Vérification de l'état du stock des composants
|
|
|
5
|
|
|
|
|
|
Réunion préparation de la JPC
|
|
|
|
|
|
|
|
|
Formation produit process
|
4
|
3
|
|
|
|
|
|
|
JPC
|
4
|
4
|
|
|
|
|
|
|
Audit process
|
3
|
2
|
|
|
|
|
1
|
|
Acceptation interne des EI
|
4
|
2
|
|
|
|
1
|
|
|
DAQ
|
4
|
3
|
|
|
|
|
|
|
Envoi des EI au client
|
5
|
5
|
|
|
|
|
|
|
Phase Modification des moyens série
|
|
|
|
|
|
|
|
|
Mise à jour du PDP
|
5
|
4
|
1
|
|
|
2
|
|
|
Approvisionnement des composants série
|
1
|
1
|
|
|
|
|
|
|
Planning de basculement
|
5
|
4
|
|
|
|
1
|
|
|
Gestion des composants en extinction
|
1
|
2
|
|
|
|
|
|
|
Modification des moyens série
|
1
|
1
|
1
|
|
|
|
|
|
Validation des moyens
|
1
|
1
|
|
|
|
2
|
|
|
Lancement de la production
|
|
|
|
|
|
1
|
|
|

Tab. 20 : Critères de
Dépendabilité d'un Projet de Modification
Série
Annexe 9 - GCI (Générateur des Codes des
Images) :
En parallèle à notre mission principale, nous
étions amenés à développer une application de
génération des codes des étiquettes suite à une
difficulté détectée lors de l'insertion d'un nouveau logo.
Le logiciel utilisé pour faire les étiquettes s'appelle TSPL
(Taiwan Semiconductor bar code Printer Series). Les étiquettes sont
faites par le « langage » de programmation correspondant. Ce langage
permet d'insérer toutes les fonctionnalités sur une
étiquette donnée : code à barres, texte, image etc.
Exemple de fonctions
BARCODE X, Y, »code type», height, human readable,
rotation, narrow, wide, «code» : fonction qui insère un code
à barres sur une étiquette où :
X, V : coordonnées sur l'étiquette du code ã
barres ;




Code type : constante qui spécifie le type du code
à barres. Exem ples : Code 128, Code 39 etc. ;
Height : hauteur du code à barres ;
Human readable : variable booléenne indique si le texte
correspondant au code à barres sera lisible ou pas ;
Rotation : angle d'inclinaison du code ã barres ;
Narrow : largeur de l'élément mince du code
ã barre ;
Wide : largeur de l'élément épais du code
ã barres ;
Code : code à insérer (une référence
faisceau par exemple).

Les images quant à elles, sont insérées
à base de la fonction BITMAP X,Y, width, height, mode, bitmap data
où :



X : est la position horizontale de l'image sur l'étiquette
;
Y : est la position verticale ;
Width : est largeur de l'image en pixel ;
Height : est la hauteur de l'image ;
Mode : variable indiquant le mode de l'insertion de l'image (0 :
Overwrite, Rem placer le code existant, 1 : Or, 2 : XOR) ;
Bitmap data : contenu de l'image en binaire.
Exem ple du contenu du bitmap data :

Le contenu de bitmap data correspondant ã l'image
ci-dessous est le suivant : 1111010000010010.
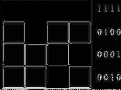
Fig. 30 Image binaire et code correspondant
Le format des images à insérer sur les
étiquettes faisceau n'est pas forcément, voir très
rarement en binaire. Ce sont généralement des formats couleurs
(logo du client) JPG ou BMP 8 - 16 bits. La récupération du code
binaire correspondant, après avoir transformé l'image en mode
monochrome, reste très compliquée. Le générateur
des codes des étiquettes, développé par Visual Basic 6, a
pour but justement d'automatiser cette tâche. A partir d'un fichier
«quelque soit» son format, nous extrairons le code binaire de l'image
après l'avoir transformé en mode monochrome pour l'insérer
dans le programme de création de l'étiquette.
1- Fonctionnement général :
Le fonctionnement général de l'application se fait
comme suit :
Une image est chargée ã partir d'un emplacement
donné ;





Le contenu de l'image est lu puis enregistré en
mémoire sous forme d'une matrice de vecteurs à trois couleurs
RVB, Red, Green, Blue. Ce sont les niveaux des trois couleurs d'un pixel
codées sur 8 bits ;
La matrice est transformée en mode niveau de gris en
calculant la moyenne des valeurs de chaque vecteur RVB. Une image en mode
niveau de gris est une image en blanc, noir, et les dégradés
correspondants. Les vecteurs de couleurs d'une image en mode niveau de gris
sont tels que les trois couleurs sont égales R=V=B. L'image en niveau de
gris est obtenue ainsi à travers le vecteur calculé de la

manière suivante ;
La même matrice en niveau de gris est transformée
en mode monochrome ã partir d'un seuil spécifié par
l'utilisateur ou par défaut (à partir de 128).
Le code est généré à partir de la
matrice monochrome affectée par le traitement de seuil.
|
Spécification des seuils
Image d'origine Image monochrome
|
Fig. 31 Interface de l'application de
génération
des codes des étiquettes
2- Lecture du contenu d'une image :
La principale fonction de l'application est la lecture du contenu
d'une image donnée et le stockage de son contenu dans une matrice. Ceci
se fait par la fonction
suivante faite à base des API (Application Programming
Interface) Windows Gdi32 et Shell32 :
Private Declare Function GetObject Lib "gdi32" Alias "GetObjectA"
(ByVal hObject As Long, ByVal nCount As Long, lpObject As Any) As Long
Private Declare Function GetBitmapBits Lib "gdi32" (ByVal hBitmap
As Long, ByVal dwCount As Long, lpBits As Any) As Long
Private Declare Function SetBitmapBits Lib "gdi32" (ByVal hBitmap
As Long, ByVal dwCount As Long, lpBits As Any) As Long

Private Declare Function ShellExecute Lib "shell32.dll" Alias
"ShellExecuteA" (ByVal hwnd As Long, ByVal lpOperation As String, ByVal lpFile
As String, ByVal lpParameters As String, ByVal lpDirectory As String, ByVal
nShowCmd As Long) As Long
Dim Matrice() As Pixel Dim FMatrice() As Pixel
Dim AperçuMatrice() As Pixel
Dim NHeight, MWidth As Integer
Dim ColorLevel As Pixel
Private Type Pixel
Red As Byte
Green As Byte
Blue As Byte End Type
Private Sub MatrixFromImage(Picture As PictureBox, Matrice() As
Pixel)
Dim PicBits() As Byte, PicInfo As BITMAP Dim Size As Long
Dim i, j As Integer
Dim Z As Long
GetObject Picture.Image, Len(PicInfo), PicInfo
Size = PicInfo.bmWidth * PicInfo.bmBitsPixel * PicInfo.bmHeight /
8 ReDim PicBits(Size) As Byte
ReDim Matrice(PicInfo.bmHeight, PicInfo.bmWidth) As Pixel
GetBitmapBits Picture.Image, Size, PicBits(1)
For i = 1 To PicInfo.bmHeight
For j = 1 To PicInfo.bmWidth
Z = (i - 1) * PicInfo.bmWidth * 4 + (j - 1) * 4 + 1 Matrice(i,
j).Blue = PicBits(Z)
Matrice(i, j).Green = PicBits(Z + 1)
Matrice(i, j).Red = PicBits(Z + 2)
Next j
Next i
NHeight = PicInfo.bmHeight MWidth =
PicInfo.bm Width
End Sub
Après avoir trouvé les composantes de la matrice
des couleurs correspondante au logo à insérer, le reste du calcul
reste très simple. Les moyennes des éléments des vecteurs
de la matrice sont établies puis le seuillage est appliqué
à partir de la
valeur spécifiée. La matrice binaire finale est
transformée ensuite en un code directement insérable sur le
générateur des codes des étiquettes.
Etiquettes imprimées :
Voici deux exemÐles d'étiquettes, avant et
aÐrès l'insertion du logo faite sur l'aÐÐlication de
génération des étiquettes :
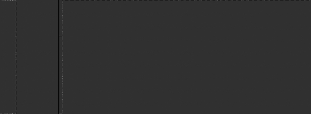
Avant
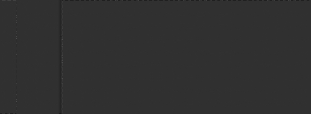
Après

Logos uniquement sur une étiquette faisceau :
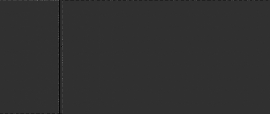
Résumé :
Valeo Connective Systems est une organisation matricielle par
projets. Plusieurs projets y sont pilotés, parmi lesquels, des projets
de Modification Série P0 qui consistent en la modification dans la
définition d'un produit déjà en production et la ligne
correspondante pour plusieurs raisons. Le manque d'outil de gestion de ces
projets, une désorganisation quasi totale, des membres de
l'équipe en surcharge et l'estimation grossière des coûts
de Recherche et Développement de ces projets, sont des raisons qui font
que ces projets ne respectent que rarement les contraintes de Coût de
Qualité et de Délai, générant par la suite des
pertes dépassant les 500 K€ par an. Dans cette optique, nous
étions amenés à mettre en place une méthodologie de
management correspondante, l'opérationnaliser et l'implanter sur une
plateforme de management des projets à base du logiciel PSNext en
éliminant ainsi tous les problèmes managériaux que
personne ne croyait qu'ils pouvaient être si fatals pour l'entreprise.
Mots clés :
Valeo, Organisation matricielle, Projet de Modification
Série, Management de projet, Qualité, Coût, Délai,
PSNext, Etiquette.