II. FABRICATION
La fabrication du verre comporte 3 principales
étapes :
2.1 La fusion
Autrefois, la fusion, ou fonte, des matières
premières était réalisée dans des pots en terre et
des creusets (fabrication discontinue) qui ne sont plus employés
aujourd'hui qu'en artisanat et pour la fabrication de petites quantités
de verre, comme en optique. Dans les verreries modernes, la plus grande partie
du verre est fondue dans de grands fours à bassin (fabrication
continue), qui peuvent contenir plus de 1 000 t de verre et permettre
une production journalière dépassant 500 t. Ces fours sont
chauffés au gaz, au mazout ou à l'électricité. Les
matières premières en mélange adéquat sont
portées à l'état de fusion, entre 1 300 et
1 500 °C. Toutes les matières premières
(mélange vitrifiable) sont concassées de manière à
obtenir une granulosité fine, comprise entre 0,1 et 0,6 mm. On
ajoute généralement au mélange des déchets de
verre, appelés calcin ou groisil, afin d'accélérer le
processus de fusion. La cuve de fusion est constituée d'un
réservoir rectangulaire de plusieurs centaines de mètres
carrés de surface en matériau réfractaire
(matériaux à point de fusion élevé). Le
mélange vitrifiable est introduit en continu par un orifice situé
à une extrémité de la cuve, puis il progresse dans
celle-ci en traversant les différentes zones de fusion, d'affinage et de
repos.
2.2 L'affinage
De nombreuses réactions chimiques se
produisent au cours du chauffage. Des gaz se libèrent dans le verre
fondu et, comme la viscosité de celui-ci est très
élevée, il se forme des bulles qui n'atteignent pas la surface du
bain de verre. Les gaz, provenant de l'air ambiant, et produits lors des
réactions chimiques ne sont donc pas éliminés du verre, ce
qui affecte sa qualité et ses propriétés
physico-chimiques. Afin de remédier à ce problème, la
température du verre est augmentée vers le milieu de la cuve de
fusion afin de diminuer sa viscosité. On introduit dans ce bain
« surchauffé » des agents d'affinage
-- essentiellement des nitrates, des sulfates et des oxydes --, qui
se décomposent à haute température en libérant des
gaz. Ces derniers forment des bulles plus grosses, qui atteignent plus
facilement la surface du bain en entraînant avec elles les bulles plus
petites.
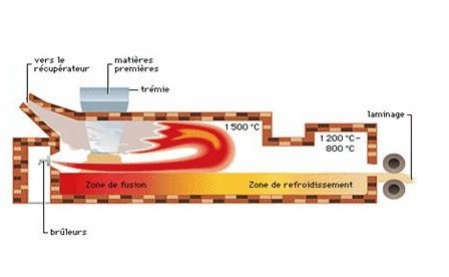
Photo 2 : La fusion
2.3 Le façonnage
Après la fusion et l'affinage, le
verre est refroidi à une extrémité de la cuve. On ajuste
ainsi la viscosité du matériau, qui peut alors être mis en
forme (généralement entre 800 et 1 200 °C). Il
existe différents modes de façonnage : le soufflé, le
pressé-soufflé, l'étirage ou encore le laminage. Tous ces
procédés, utilisés depuis des siècles, ont
été améliorés pour produire du verre à usage
industriel. Ainsi, on peut utiliser des machines de soufflage
entièrement automatisées. Le verre peut être peint ou
verni, être rendu opaque ou être poli en projetant des abrasifs (du
sable par exemple) ou en utilisant une meule ou des acides. Il est possible de
déposer sur le verre un revêtement superficiel comme un traitement
antireflet ou semi-réfléchissant. Les techniques industrielles
utilisées pour la fabrication de produits en verre sont variées
et dépendent généralement du type de produit ainsi que du
type de verre.
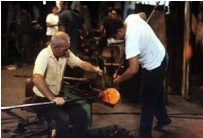
Photo 3 : Le soufflage traditionnel
|