REPUBLIQUE ALGERIENNE DEMOCRATIQUE ET
POPULAIRE
MINISTERE DE L'ENSEIGNEMENT SUPERIEUR ET DE LA RECHERCHE
SCIENTIFIQUE UNIVERSITE MENTOURI-CONSTANTINE
FACULTE DES SCIENCES EXACTES
DEPARTEMENT DE PHYSIQUE
N° d'ordre: Série :
MEMOIRE Présenté pour obtenir le diplôme
de Magister en Physique Spécialité : Sciences des
Matériaux Option: Semi Conducteurs
THEME
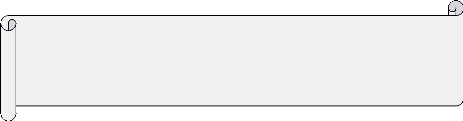
Étude du Dopage des Couches Minces de
ZnO
Élaborées par Spray
Ultrasonique
Par:
HAFDALLAH Abdelkader
Soutenu le : / / 2007
Devant le jury:
Président :
|
M. S. AIDA
|
Prof.
|
Université Mentouri-Constantine
|
Rapporteur :
|
N. ATTAF
|
M. C.
|
Université Mentouri-Constantine
|
|
Examinateurs :
|
R. HALIMI
|
Prof.
|
Université Mentouri-Constantine
|
|
M. L. BENKHEDIR
|
M. C.
|
Centre Universitaire de Tebessa
|
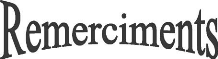
Le présent mémoire a été
réalisé au niveau du laboratoire des couches minces et interfaces
de la faculté des Sciences Exactes de l'Université
Mentouri-Constantine.
Cette étude a été effectuée
sous la direction de monsieur NADHIR ATTAF, Maître de
conférence au Département de Physique de la Faculté des
Sciences Exactes de l'Université Mentouri-Constantine, directeur de
thèse, qui m'a soutenu dans cette épreuve, il m'a surtout
encouragé à travers ses orientations, ses conseils et son
assistance dans l'élaboration du travail et l'appréciation des
résultats.
J'exprime ma profonde gratitude à Monsieur
M.S. AIDA, Professeur au Département de Physique de la
Faculté des Sciences Exactes de l'Université
Mentouri-Constantine, qui a dirigé ce travail efficacement. Ces quelques
lignes sont insuffisantes à exprimer ma reconnaissance pour la confiance
qu'il m'a témoigné, pour l'attention jamais relâchée
qu'il a porté mon travail et pour l'honneur qu'il me fait en acceptant
la présidence de ce jury.
Mes vifs remerciements à :
Monsieur R. HALIMI Professeur au
Département de Physique de l'Université Mentouri Constantine,
directeur de laboratoire des couches minces et interfaces, qui a bien voulu
accepter de faire partie du jury et d'examiner mon travail.
Monsieur M.L. BENKHEDIR Maître de
conférence au Département de Physique de Centre Universitaire de
Tebessa, qui a bien voulu accepter de faire partie du jury et d'examiner mon
travail.
Mes remerciements également à toute personne
ayant contribué de près ou de loin à la réalisation
de ce travail au niveau du laboratoire des Couches Minces et Interfaces
notamment : D. DERGHAM, M. KHECHBA, H. LEKIKET, W. DARANFED et
A. TOUIL.
Enfin, je tiens à exprimer ma gratitude à
toute l'équipe du Laboratoire des Couches Minces et Interfaces et
à mes amis des autres laboratoires, plus particulièrement :
F. HANINI et D. GUITOUM.
Dédicace
Je dédie le présent mémoire
:
?A ma mère et mon père pour
leurs
affections et amours,
?A mes soeurs et frères pour leurs
encouragements et leurs soutiens, ?A
Toute ma famille,
?A tous mes amis,
A tous ceux et celles que j'aime de
près
comme de loin.
Chapitre I
Couches minces d'oxyde de zinc
et Techniques de dépôts
|
Dans ce chapitre nous donnerons une description des diverses
méthodes de dépôt des couches minces et qui sera suivie
d'une étude bibliographique sur les oxydes transparents conducteurs
(TCO), dont l'oxyde de zinc (ZnO) fait partie.
I.1. Définition d'une couche mince:
Par principe, une couche mince d'un matériau
donné est un élément de ce matériau dont l'une des
dimensions qu'on appelle l'épaisseur a été fortement
réduite de telle sorte qu'elle s'exprime en Angstrom et que cette faible
distance entre les deux surfaces limites (cette quasi bidimensionnelle)
entraîne une perturbation de la majorité des
propriétés physiques [7]. La différence essentielle entre
le matériau à l'état massif et celui en couches minces est
liée au fait que dans l'état massif on néglige
généralement avec raison le rôle des limites dans les
propriétés, tandis que dans une couche mince ce sont au contraire
les effets liés aux surfaces limites qui sont
prépondérants. Il est assez évident que plus
l'épaisseur sera faible et plus cet effet de bidimensionnelle sera
important, et qu'inversement lorsque l'épaisseur d'une couche mince
dépassera un certain seuil l'effet d'épaisseur deviendra minime
et le matériau retrouvera les propriétés bien connues du
matériau massif.
L'intérêt des couches minces provient
essentiellement de l'utilisation économique des matériaux en
rapport avec les propriétés physiques et de la simplicité
des technologies mise en oeuvre pour leur réalisation. Une grande
variété de matériaux est utilisée pour produire ces
couches minces. Citons les métaux, alliages, composés
réfractaires (oxydes, nitrures, carbures), les composés
intermétalliques et les polymères.
La seconde caractéristique essentielle d'une couche
mince est que, quelle que soit la procédure employée pour sa
fabrication, une couche mince est toujours solidaire d'un support sur lequel
elle est construite (même s'il arrive parfois que l'on sépare le
film mince dudit support). En conséquence, il sera impératif de
tenir compte de ce fait majeur dans la conception, à savoir que le
support influence très fortement les propriétés
structurales de la couche qui y est déposée. Ainsi, une couche
mince d'un même matériau, de même épaisseur, pourra
avoir des propriétés physiques sensiblement différentes
selon qu'elle sera déposée sur un substrat isolant amorphe tel le
verre, ou un substrat monocristallin de silicium par exemple.
Il résulte de ces deux caractéristiques
essentielles d'une couche mince la conséquence suivante :
une couche mince est anisotrope par construction.
En pratique, on peut distinguer deux grandes familles de
méthodes d'élaboration de couches minces, celles qui font
appel à un gaz porteur pour déplacer le matériau à
déposer d'un récipient au substrat et qui s'apparentent aux
techniques de diffusion utilisées dans la fabrication des
composants actifs, et celles qui impliquent un environnement
à pression très réduite et dans lesquelles le
matériau à déposer sera véhiculé grâce
à une impulsion initiale de nature thermique ou mécanique.
I.2. Mécanisme de formation d'une couche
mince:
La formation d'une couche mince s'effectue par une combinaison de
processus de nucléation et de croissance. Les séquences de
croissance se décomposent comme suit [8]:
- Les espèces, au moment de l'impact
sur le substrat, perdent leur composante de vitesse de déplacement et
sont absorbées physiquement sur la surface du substrat.
- Initialement, les espèces absorbées ne sont
pas en équilibre thermodynamique avec le substrat, et se
déplacent donc sur sa surface. Pendant ces déplacements, et
lorsqu'elles arrivent dans des sites favorable elles; créant des amas
(clusters) qui iront en se développant.
- Ces amas, que l'on appelle Ilots ou noyaux, sont
thermo-dynamiquement instables et tendent naturellement à
désorber. Toutefois, si les paramètres de dépôt sont
tels que les Ilots entrent en collision les uns avec les autres, ils se
développent. Lorsqu'ils atteignent une certaine taille, les Ilots
deviennent thermo-dynamiquement stables. On dit que le seuil de
nucléation a été franchi. Cette étape, de formation
d'Ilots stables, chimisorbés, et d'une dimension suffisante, s'appelle
la nucléation.
- Les Ilots continuent à croItre en nombre et en
dimension jusqu'à ce qu'ilsatteignent une densité de
nucléation dite la saturation. Cette densité de nucléation
et la dimension moyenne des Ilots dépendent de plusieurs
paramètres tels que l'énergie des espèces incidentes, leur
quantité par unité de temps et de surface, les énergies
d'activation, d'absorption, de désorption, la diffusion thermique, la
température, la topologie et la nature chimique du substrat. Un Ilot
peut croItre parallèlement à la surface du substrat par diffusion
superficielle des espèces absorbées ou perpendiculaire par impact
direct des espèces incidentes sur l'Ilot. En général, la
vitesse de croissance latérale est bien plus grande que la vitesse de
croissance perpendiculaire.
- L'étape suivante dans le processus de formation de la
couche mince s'appelle la coalescence. Les Ilots commencent à
s'agglomérer les uns aux autres en réduisant la surface du
substrat non recouverte. La coalescence peut être
accélérée en augmentant la mobilité de surface des
espèces adsorbées, par exemple en augmentant la
température du substrat. On peut, pendent cette étape, observer
la formation de nouveaux Ilots sur des surfaces libérées par le
rapprochement d'Ilot plus anciens.
- Les Ilots deviennent des Iles qui continuent à
croItre, ne laissant que des trous ou des canaux de faibles dimensions entre
elles. Dans cette étape, la structure de la couche passe du type
discontinu au type poreux. Peu à peu, une couche continue
se forme lorsque les trous et les canaux se remplissent.
- On peut donc résumer le processus de croissance d'une
couche mince en disant que c'est une suite statistique de nucléation,
puis une croissance par diffusion de surface et formation d'Ilots, puis une
formation d'Iles de plus grandes dimensions, et enfin la formation d'une couche
continue par remplissage de espèces entre ces Iles. Selon les
paramètres thermodynamiques du dépôts et de la surface du
substrat, les étapes de nucléation et de croissance d'Ilots
peuvent être décrites comme étant :
· Du type Iles (appelé Volmer-Weber).
· Du type couche (appelé Frank-van der Merwe).
· Du type mixte (appelé Stranski-Krastanov).
La figure I.1, présente les trois types de formation
d'une couche mince. En fait, dans la quasi-totalité des cas pratiques,
la croissance de la couche se fait par formation d'Ilots, puis d'Iles, puis
d'une surface continue. Sauf dans les cas de conditions spéciales de
dépôts (température du substrat, nature et énergie
des espèces incidentes, nature chimique du substrat,
caractéristiques du gaz ambiant,...), les orientations
cristallographiques et les détails topographiques des îlots sont
distribués d'une façon aléatoire. Ceci signifie que,
lorsque ces Ilots vont se rencontrer au cours du processus de croissance, des
joints de grains et des défauts et dislocations diverses vont être
inclus dans la couche à la suite des désaccords de configuration
géométrique et d'orientation cristallographique [9].
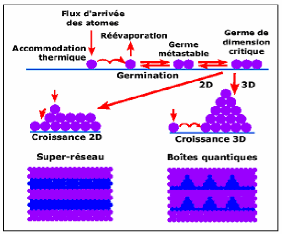
FigureI.1 : les trois modes de
croissance d'une couche mince [10].
Si les grains sont orientés d'une manière
aléatoire, les couches seront dites polycristallines. Toutefois, si la
dimension des grains est très faible (de l'ordre de 20°A), les
couches auront des structures amorphes (non cristallines). Il est à
noter que, même si l'orientation des différents îlots est la
même sur l'ensemble de la surface du substrat et que ce dernier soit un
monocristal, on n'obtiendra pas une couche monocristalline. Dans ce cas, la
couche sera formée de grains monocristallins orientés
parallèlement les uns par rapport aux autres et reliés par des
joints de grains à faible angle. Ces couches sont appelées
épitaxiales/ monocristallines.
D'autres causes pouvant engendrer des défauts dans les
couches minces telles que [11]
v' Une grande différence entre les paramètres de
maille de la couche et ceux du substrat. v' La présence de contraintes
importantes dans la couche.
v' La prolongation dans la couche de dislocations
présentes à la surface du substrat.
Après qu'une couche continue se soit formée, la
croissance anisotropique s'effectue perpendiculairement à la surface du
substrat sous forme de colonnes cylindriques. Le diamètre de ces
colonnes est principalement déterminé par la densité
initiale de nucléation. Toutefois, s'il se produit des
recristallisations pendant la phase de coalescence, la quantité moyenne
de grains par unité de surface de la couche sera inférieure
à la densité initiale de nucléation. Pour des couches
d'épaisseur inférieure à un micron, la dimension
perpendiculaire à la surface des grains sera pratiquement égale
à l'épaisseur de la couche. Pour des couches plus
épaisses, une nucléation se produit à la surface des
grains et chaque colonne verticale va croître d'une manière
multigranulaire, avec des déviations possibles de la croissance
perpendiculaire.
I.3. Procédure de dépôt des couches
minces:
Tous les procédés de déposition de
couches minces contiennent quatre (parfois cinq) étapes successives,
comme le montre la Figure I.2. La source qui constitue le
matériau de base du film mince à élaborer peut être
un solide, un liquide, une vapeur ou un gaz. Lorsque le matériau est
solide son transport vers le substrat s'effectue par vaporisation. Ce qui peut
être réalisé par évaporation thermique, canon
à électrons, ablation laser ou par des ions positifs
"pulvérisation". L'ensemble de ces méthodes est classé
sous le nom de dépôt physique en phase vapeur PVD " physical vapor
deposition". La source solide est occasionnellement transformée en
vapeur par voie chimique. Dans d'autre cas, le matériau de base est sous
forme d'un gaz ou d'un liquide ayant une pression de vapeur suffisante pour
qu'il soit transporté à des températures
modérées. Les procédés qui utilisent, comme
matériau de base, les gaz, les liquides évaporés ou
solides évaporés par voie chimique sont connues sous le nom de
dépôts chimiques en phase vapeur, i.e. CVD " Chemical vapor
déposition "[11].
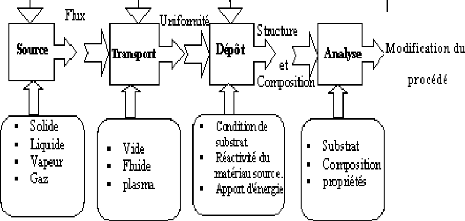
Figure I.2 : Diagramme des
étapes du procédé de fabrication de couches minces
[12].
Dans l'étape de transport,
l'uniformité du flux des espèces qui arrivent sur la surface du
substrat est un élément important, plusieurs facteurs peuvent
affecter cette uniformité et dépendent du milieu dans lequel
s'effectue le transport, un vide poussé ou un fluide "principalement des
gaz ". Dans le cas d'un vide poussé, les molécules, provenant de
la source et allant vers le substrat, traversent le milieu selon des lignes
droites, tandis que dans un milieu fluide elles subissent plusieurs collisions
au cours de leurs transports. En conséquence, dans le vide,
l'uniformité du flux qui arrive sur le substrat est
déterminée par la géométrie, tandis que dans un
fluide il est déterminé par le débit du gaz et par la
diffusion des molécules de la source dans les autres gaz
présents. Souvent, les procédés qui utilisent un vide
poussé sont équivalents aux procédés PVD alors que
ceux qui utilisent un débit fluide sont des procédés CVD.
Cette définition n'est pas toujours confirmée. Il existe
plusieurs procédés de dépôt physique en phase vapeur
qui opèrent dans un vide poussé, d'autres, comme l'ablation laser
et la pulvérisation opèrent souvent à des grandes
pressions caractéristiques du fluide. De la même manière on
trouve que la majorité des procédés de dépôts
par CVD opèrent à des pressions modérées,
l'épitaxie à transmission chimique " chemical beam epitaxy",
quant elle, opère dans un vide.
Dans cette phase, plusieurs procédés de
dépôt de couches minces utilisent un milieu plasma. En effet, la
grande quantité d'énergie contenue dans ce milieu permet,
à faible température,
l'activation de la formation des couches. La pression de
travail d'un plasma peut être celle d'un fluide ou celle d'un vide
poussé.
La troisième étape dans les
procédés d'élaboration des films minces est le
dépôt du film sur la surface du substrat. Cette phase
passe par les étapes de nucléation et de coalescence comme il est
décrit dans le paragraphe précédent (c.f paragrapheI.1).
Le comportement de déposition est déterminé par les
facteurs source, transport et aussi par les trois principales conditions de la
surface du substrat. Ces dernières sont l'état de surface
"Rugosité, niveau de contamination, potentiel chimique avec le
matériau qui arrive", la réactivité du
matériau arrivant sur cette surface " Coefficient de collage" et
l'énergie déposée sur la surface " Température de
substrat, Photons, Ions positifs".
La dernière étape dans le processus de
fabrication est la nécessité de l'analyse du film
obtenu. Le premier niveau de contrôle du matériau consiste
à effectuer des mesures directes de ses propriétés
importantes. Si les résultats de l'analyse sont insuffisants, il est
indispensable de recourir à des expériences particulières
qui permettent de lever les éventuelles ambiguïtés d'un
processus donné.
I.4. Quelques méthodes de dépôt de
couches minces de ZnO :
Les couches minces d'oxyde de zinc sont
réalisées en utilisant une grande variété de
techniques. Elles peuvent être obtenues en opérant en phase
liquide ou en phase vapeur, et par des procédés physiques ou
chimiques.
Par voie liquide, les techniques les plus fréquentes
sont : le dépôt chimique en solution [13],
l'électro-dépôt par synthèse électrochimique
[14], la voie sol-gel [15]. Par voie vapeur, on distingue les méthodes
physiques « PVD » et les méthodes chimiques « CVD
».
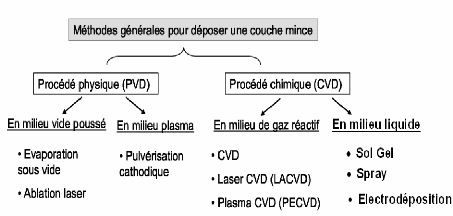
Figure I.3: Présentation des
principaux procédés de dépôt de couches minces
[16].
Dans le cadre de ce mémoire, nous présenterons
d'abord quelquestechniques utilisant la voie vapeur tout en réservant un
développement plus approfondi à la méthode par spray
pyrolytique, technique qui a été choisie pour ce travail.
I.4.1. Dépôts chimiques en phase vapeur
:
Les méthodes par CVD permettent de réaliser des
dépôts à partir de précurseurs gazeux qui
réagissent chimiquement pour former un film solide déposé
sur un substrat. Les méthodes de synthèse les plus
utilisées sont :
- Le dépôt par décomposition de
composés organométalliques (MOCVD) soit à pression
atmosphérique [17] ou à basse pression [18] ;
- Le dépôt par pyrolyse d'aérosol,
appelée aussi <<spray pyrolysis » à partir de
solutions aqueuses ou alcooliques d'un sel de zinc; cette technique est
très employée surtout pour les oxydes car les dépôts
sont élaborés sous atmosphère normale [19,20] ;
- Le dépôt par couche atomique (ALD) [21] ou
epitaxiée (ALE) [22] et la photo-ALE [23] ;
- Le dépôt chimique en phase vapeur
assisté par plasma (PECVD) [24], la photo-CVD [25], et récemment
le dépôt électrophorèse pour les films <<
nanofils » de ZnO [26].
Les principaux avantages de ces techniques sont de permettre
la cristallisation de films sans avoir recours à un recuit, de pouvoir
contrôler la composition durant le dépôt, de réaliser
un dépôt d'épaisseur et de composition uniformes
possédant en plus une excellente adhérence.
Cependant ces techniques ont l'inconvénient de donner
des films contaminés par les résidus des précurseurs et
d'avoir une température de réaction souvent
élevée.
I.4.2. Dépôts physiques en phase vapeur
:
Les procédés par PVD regroupent principalement
l'évaporation, l'ablation laser et la pulvérisation sous toutes
ses formes. Dans la réalisation d'une couche on peut distinguer les
trois étapes suivantes :
- La création de la ou des espèces à
déposer, sous forme d'atomes, de molécules ou de clusters
(groupes d'atomes ou de molécules),
- Le transport de ces espèces en phase vapeur de la
source vers le substrat,
- Le dépôt sur le substrat et la croissance de
la couche.
I.4.2.1.La pulvérisation cathodique :
Dans cette méthode, le substrat est mis dans une
enceinte contenant un gaz (en général de l'Argon) à basse
pression, dans lequel on provoque une décharge électrique. Cette
décharge a pour rôle d'ioniser les atomes de gaz. Les ions ainsi
obtenus sont accélérés par une différence de
potentiel et viennent bombarder une cathode constituée du
matériau à déposer (cible) [27,28]. Sous l'impact des ions
accélérés, des atomes sont arrachés à la
cathode et sont déposés sur le substrat. Dans certains cas, on
introduit dans l'enceinte en plus de l'argon un gaz qui va réagir
chimiquement avec les atomes pulvérisés pour former le
matériau que l'on désire obtenir. Alors, on a une
pulvérisation cathodique réactive. Cette méthode permet
d'avoir des dépôts de faible résistivité et des
couches de bonne stoechiométrie ayant une transmission moyenne dans le
visible [29].
L'avantage de la méthode de pulvérisation
cathodique est de pouvoir réaliser des dépôts sous
atmosphères contrôlées. Cependant, le coût trop
élevé de l'installation, associé à un faible taux
de production fait de la pulvérisation cathodique une technique
réservée à des applications spécifiques
réduites.
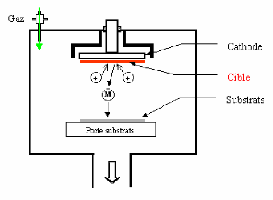
Figure.I.4: Schéma
conventionnel d'un pulvérisateur cathodique [30].
|