Introduction générale
La laverie de KAMATANDA alimente actuellement le circuit de
lixiviation en tas des usines hydrométallurgiques de SHITURU pour la
production d'un lixiviat principalement de cuivre. Les minerais alimentant la
laverie de KAMATANDA subissent successivement une fragmentation, un lavage et
une classification granulométrique. De cette classification
granulométrique, trois fractions en résultent à savoir :
les -30 mm +1mm destinées à la lixiviation en tas ; les -1 mm
+0,8 mm et les -0,8 stockées comme rejets.
La capacité de traitement de la laverie de KAMATANDA
est estimée à 3000 tonnes sèches par jour et se subdivise
en fonction des différentes fractions granulométriques en 1500
tonnes sèches par jour pour la fraction des -30 mm à +1 mm, 780
tonnes sèches par jour pour la fraction des -1 mm à +0,8 mm et
720 tonnes sèches par jour pour la fraction des -0,8 mm.
La forte demande du cuivre sur le marché international
et le besoin d'avoir une alimentation continue des usines
hydrométallurgiques de SHITURU, a poussé la Gécamines
à penser aux diverses sources d'alimentation, notamment la valorisation
des rejets de la laverie de KAMATANDA. En effet, c'est depuis 2018 que la
laverie de KAMATANDA lave les minerais cupro-cobaltifères oxydés
de la mine à ciel ouvert de KAMATANDA.
Plusieurs études ont été initiées
sur la valorisation de ces rejets dont la nôtre qui a pour but de
valoriser uniquement la fraction inférieure à 0,8 mm titrant
généralement 1,44 % pour le cuivre et 0,12% pour le cobalt par la
concentration gravimétrique sur spirale et magnétique. Pour cette
étude, la plage granulométrique alimentée dans le circuit
est comprise entre - 0,8 mm et +53
?m.
Ces deux méthodes de concentration présentent
des coûts opératoires relativement faibles étant
donné qu'elles n'exigent aucun réactif particulier. Pour la
concentration sur spirale, les paramètres qui seront
étudiés sont l'ouverture de la cuillère (collecteur du
concentré), le débit d'alimentation de la pulpe et le pourcentage
solide de la pulpe. Le rejet spirale sera valorisé par séparation
magnétique. Au terme de la réalisation de ces essais, un bilan
métallurgique sera fait pour comparer les résultats obtenus aux
critères d'alimentation des usines hydrométallurgiques de
SHITURU.
Pour bien aborder ce sujet et répondre ainsi aux
attentes de l'entreprise, ce travail a été réalisé
au laboratoire et à l'usine pilote de la division minéralurgique
du département d'études
2 | P a g e
métallurgiques de la Gécamines et comprendra
deux parties essentielles reprises dans les lignes qui suivent outre
l'introduction et la conclusion :
? La première, essentiellement bibliographique ;
comprendra une présentation de la mine et de laverie de Kamatanda, des
notions générales sur les techniques de concentration des
minerais et particulièrement les techniques gravimétrique sur
spirale et magnétique;
? La seconde partie, reprendra les matériels et
méthodes utilisés ainsi que la présentation et l'analyse
des résultats.
3 | P a g e
Présentation de la mine et de la
laverie
de kamatanda
I.1. Mine à ciel ouvert de kamatanda I.1.1.
Historique
La dénomination « KAMATANDA » est tirée
du nom d'un petit cours d'eau situé à l'ouest de ce qui sera la
mine à ciel ouvert de KAMATANDA. Les grandes dates de cette mine sont
les suivantes (Mbwisha. 2021) :
· 1901 : indice d'exploitation artisanale dans la
contrée de KAMATANDA par les habitants de cette contrée ;
· De 1923 à 1925 : prospection minière
dans la contrée de KAMATANDA ;
· 1950 : découverture et début de
l'exploitation minière de la mine à ciel ouvert de KAMATANDA ;
· 1963 : Suspension de l'exploitation de la mine ;
· 2006 : début de l'exploitation artisanale de la
mine dans le cadre d'un partenariat entre la Gécamines et C.D.M ;
· 2015 : exploitation minière de la mine par la
Gécamines dans le cadre du projet « heap leaching » ayant pour
but l'alimentation des usines de SHITURU.
I.1.2. Localisation géographique
La mine à ciel ouvert de KAMATANDA est une
propriété de la GECAMINES SA exploitant un gisement d'une
superficie de 40,8 km2.
Elle est localisée au Nord-est de la ville de Likasi,
à 6,8 km des usines hydrométallurgiques de SHITURU, aux
coordonnées géographiques suivantes : 10°57'8,9» de
latitude Sud et 26°46'19,47» de longitude Est.
I.1.3. Cadre géologique et
minéralogique
La région du gisement est très
vallonnée, les terrains rencontrés dans la zone du gisement sont
de type Kundelungu et Roan moyen. Sur la route d'accès on descend
graduellement dans l'échelle stratigraphique jusqu'au Kundelungu
inferieur près de la mine. Elle se situe dans le flanc sud de
l'anticlinal de Kapolowe dans une roche du Roan extrusif. Les pendages sont
vers le Nord. L'aspect minéralogique de la mine nous montre que la
malachite et la chrysocolle sont
4 | P a g e
les formes minéralogiques principales du cuivre et le
cobalt s'y trouve sous forme d'Hétérogénite (Kabanda.
2020).
I.2. La laverie de kamatanda
D'une manière générale la laverie de
KAMATANDA est alimentée par des minerais de granulométrie allant
jusqu'à 400 mm et fournit trois fractions granulométriques :
? -30 mm à +1 mm : Fraction grossière (50% de la
production) ? -1 mm à +0,8 mm : Fraction fine (26% de la production) ?
-0,8 mm : Fraction fine (24 % de la production)
La fraction grossière est envoyée aux usines
hydrométallurgiques de SHITURU par camions alors que la fraction de -1
mm à +0,8 mm et la fraction inférieure à 0,8 mm sont
entreposées sur une aire de stockage en attendant une revalorisation
future (Mbwisha. 2021).
La figure I.1 présente le flow sheet de la laverie de
KAMATANDA.
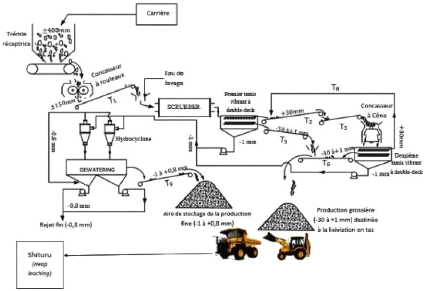
Figure I.1.Flow sheet de la laverie de
Kamatanda (Mbwisha. 2021)
En effet, les minerais tout venant d'environs 400 mm sont
alimentés dans la trémie réceptrice ; puis grâce
à un déverseur, ces minerais sont envoyés dans le
concasseur à rouleaux où ils seront
5 | P a g e
concassés jusqu'à une granulométrie
d'environ 150 mm. A la sortie du concasseur, grâce à la bande
transporteuse T1, ces minerais sont envoyés au laveur (SCRUBBER). Le
lavage permet de débarrasser les minerais des particules de -1 mm
à envoyer par pompage au « dewatering » pour la production
fine et l'obtention des rejets usine. Ainsi, après passage des minerais
lavés dans le premier tamis vibrant à double-deck, les produits
suivants sont obtenus (Mbwisha. 2021) :
· Les minerais de granulométrie comprise entre
-30 mm et +1 mm qui constitue la production grossière de l'usine ;
· Les minerais de granulométrie +30 mm qui sont
envoyés à un deuxième concassage (concasseur à
cône). Après concassage, ces minerais passent par un
deuxième tamis vibrant à double deck, qui fournit à son
tour les produits de -1 mm à envoyer au dewatering, les produits de +30
mm à recirculer, c'est-à-dire à mélanger avec les
produits de sortie lavage. Et enfin les produits de granulométrie
comprise entre -30 et +1 mm qui constituent la production grossière
et
· Les produits de -1 mm sont traités au
dewatering pour obtenir la fraction fine (+0,8 mm) et le rejet de la laverie
(-0,8 mm).
I.3. Estimation de la quantité des rejets de la
laverie
La capacité de traitement de la laverie de KAMATANDA
est estimée à 3000 tonnes sèches par jour. Tenant compte
des données sur les proportions produites après classification
granulométrique et l'année de début de la production de la
laverie, la quantité des rejets ayant une granulométrie
inférieure à 0,8 mm pourrait être estimée à
maximum 1 296 000 tonnes sèches stockées sur une période
de 5 ans. Ce qui représente environ 18 662,4 tonnes sèches de
cuivre.
Les critères à observer pour l'alimentation de
l'unité de lixiviation en tank agité aux US sont :
· Un concentré ou un minerai ayant une teneur en
cuivre d'environ 3% ;
· Un d80 de 75 tm.
6 | P a g e
Synthèse bibliographique sur la
concentration des minerais
II.1. Généralités sur la
concentration
II.1.1. Introduction
A la sortie de la mine, le minerai se présente
généralement sous forme des gros blocs pouvant aller
jusqu'à 1 m de diamètre et présentant des teneurs
diverses. Une telle matière subit en premier lieu une opération
de fragmentation visant à libérer les éléments
valorisables contenus dans la matière hétérogène et
à réduire la taille de la matière à une
granulométrie dictée par les utilisateurs. En second lieu, une
opération de concentration ou d'enrichissement est
généralement nécessaire. Elle consiste en une
séparation des constituants d'une matière suivant l'espèce
en se basant sur la différence des propriétés physiques de
masse ou physico-chimiques de surface : couleur, réflectivité,
forme, transparence, réfraction, radioactivité,
perméabilité magnétique, conductivité
électrique, poids spécifique, dimension, forme,
mouillabilité superficielle (Kalenga. 2016).
II.1.2. Méthodes de concentration
L'existence des plusieurs propriétés
exploitables dans la concentration conduit à un grand nombre de
méthodes de concentration connues de nos jours. Les méthodes de
concentration peuvent être classées selon plusieurs
critères, la classification suivante est faite selon les
propriétés intervenant dans le mécanisme de concentration
(Kalenga. 2016) :
? Concentration par triage manuel et
mécanique
Le triage manuel et mécanique est basé sur la
différence de couleur, de réflectivité et de forme des
minéraux en présence.
? Concentration
gravimétrique
La concentration gravimétrique regroupe l'ensemble des
méthodes de concentration dont la propriété
exploitée pour la séparation est le poids spécifique des
minéraux qui entre en compétition avec la dimension et la forme
des particules. Les forces qui interviennent sont la pesanteur, la
résistance hydraulique et la force centrifuge. Quatre méthodes
ont été mises au
7 | P a g e
point industriellement, il s'agit de la méthode de la
nappe pelliculaire fluente, de l'accélération
différentielle, des milieux denses et des procédés
utilisant la centrifugation.
? Concentration magnétique
La concentration magnétique est une méthode de
séparation des constituants magnétiques des non
magnétiques. Mais seules quelques substances, dont le prototype est le
fer doux, sont naturellement magnétiques. Cependant lorsqu'ils sont
soumis à l'action d'un champ magnétique tous les minéraux,
à des degrés divers sont perméables au champ.
? Concentration
électrostatique
La méthode de concentration électrostatique
consiste en une séparation des constituants conducteurs de non
conducteurs. Son application nécessite la présence conjointe de
deux phénomènes qui sont l'existence d'un champ électrique
d'intensité suffisante pour pouvoir dévier une particule
chargée électriquement et l'existence d'une polarité de la
particule.
? Concentration par flottation
La flottation est une méthode de concentration
exploitant la susceptibilité qu'ont certains minéraux de mouiller
leur surface. Le mécanisme de flottation consiste en la formation, avec
certains minéraux, d'un complexe plus léger que l'ensemble
restant, sur lequel ce complexe peut flotter et dont il peut être
séparé. Ce procédé est très différent
d'une simple séparation par différence de densité entre
solides.
Dans ce travail, nous nous attarderons beaucoup plus sur la
concentration sur spirale, qui est l'une des méthodes de concentration
gravimétriques, et sur la concentration magnétique qui sont les
méthodes de concentration utilisées pour cette étude.
II.2. Concentration sur spirale
II.2.1. Introduction
En tant que technologie de séparation par
gravité la plus simple, et sans doute la plus efficace, les
concentrateurs à spirale jouent depuis longtemps un rôle important
dans le traitement des minéraux. Le concentrateur à spirale est
l'un des dispositifs les plus efficaces et les moins coûteux pour la
concentration gravimétrique des minerais. Les spirales
nécessitent un minimum de maintenance et d'entretien et offrent un
fonctionnement unitaire relativement simple qui se traduit par des faibles
coûts d'investissement et d'exploitation. Ceci, couplé à un
traitement sans réactif, fournit un procédé souhaitable du
point de vue environnemental et économique.
8 | P a g e
Elle est utilisée principalement pour concentrer les
minerais de fer, pour lesquels elle produit un premier concentré de
nettoyage, mais de teneur généralement insuffisante pour des
étapes d'extraction ultérieure. Son utilisation n'est cependant
pas limitée aux minerais de fer. On s'en sert aussi pour les minerais
d'ilménite, pour le traitement du charbon et pour la concentration du
mica et du graphite (Bouchard. 2001).
II.2.2. Description et principe de fonctionnement d'une
spirale Humphreys
? Description
Humphreys introduit la méthode de concentration sur
spirale en 1947 (Apodaca. 1990). Le premier model est fait en métal,
parfois en ciment pourvu d'un trou et utilisé dans le traitement de
minerais de fer, de chromite et aussi dans d'autres applications
(Lalafandeferana. 2009).
Une spirale est un appareil de séparation
gravimétrique par nappe pelliculaire fluente. Elle est constituée
:
y' D'une boite d'alimentation : servant à alimenter
l'appareil ;
y' D'une coquille (hélice) : constituée d'un ou
plusieurs pas ;
y' Et d'une boite de sortie : servant à séparer le
minerai traité et à son évacuation.
L'une des spécificités de la spirale est
qu'elle ne comprend pas d'organe en mouvement, ce qui explique en partie sa
faible consommation d'énergie (EK C. 1973).
Une illustration d'une boite d'alimentation et d'une spirale
Humphreys est faite à la figure II.1 et II.2.
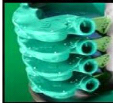
Figure II.1.Boite d'alimentation d'une spirale
Humphreys (Lalafandeferana. 2009)
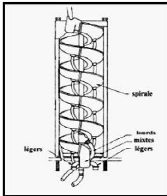
9 | P a g e
Figure II.2.Une spirale Humphreys (Lalafandeferana.
2009)
Les principaux phénomènes responsables de la
séparation des particules sur une spirale sont (Lalafandeferana. 2009)
:
V' La sédimentation V' La
centrifugation
La séparation sur spirale est basée sur la
différence de gravité spécifique présente dans une
suite minérale d'alimentation. Lorsqu'ils sont alimentés avec un
mélange de pulpe diluée de minéraux de densités
spécifiques différentes, les minéraux plus légers
sont plus facilement mis en suspension par l'eau et atteignent des vitesses
tangentielles relativement élevées de sorte qu'ils grimpent vers
le bord extérieur de l'auge en spirale. Dans le même temps, les
grains non suspendus plus lourds migrent par saltation le long de la partie la
plus basse de la section transversale de la spirale. La saltation est
définie comme un mouvement non linéaire qui est une combinaison
de roulement et de rebond. Dans certains modèles, la boue est
sélectivement dirigée avec des séparateurs de produit
réglables dans les orifices de sortie de décharge du produit le
long de l'hélice. D'autres modèles utilisent des
protubérances pour agiter la boue qui coule et aider à
libérer les minéraux piégés pour une meilleure
récupération. Enfin, certains modèles utilisent l'ajout
d'eau de lavage à divers points de la colonne pour un lavage plus
efficace du concentré. Le modèle spécifique requis pour
une séparation précise dépend des besoins d'une
application spécifique.
Comme la plupart des dispositifs de concentration qui
utilisent des principes de séparation physiques, la spirale fonctionne
mieux avec une alimentation de taille raisonnablement
10 | P age
proche mais, dans certains cas, l'unité a une certaine
tolérance pour de larges gammes de tailles. En général,
une limite de taille grossière serait d'environ 20 mesh (Tyler
Standard), soit 1 mm, et une limite fine d'environ 325 mesh (45 microns). Pour
de meilleures performances, l'alimentation doit être relativement exempte
de boues, car une teneur élevée en boue peut agir comme un
"milieu lourd" et diminuer les différences effectives de gravité
spécifique entre les minéraux à séparer. En
règle générale, une boue de -325 mesh (-45 microns)
dépassant 5% en poids de l'alimentation en spirale peut réduire
l'efficacité ; et le déschlammage, en tant qu'étape de
pré-concentration, doit être évalué. Si la
quantité de boue dépasse 10 % en poids, le déschlammage
avant la concentration en spirale entraînera presque certainement une
amélioration des performances de la spirale. Une différence de
gravité spécifique d'au moins 1 est nécessaire entre les
particules légères et lourdes pour réussir une
séparation par gravité (IMSC group. 2018).
La concentration sur spirale nécessite plusieurs
forces dont la plupart d'entre elles n'est pas mesurable, cinq forces
principales peuvent être citées, étant donné que le
vecteur résultant de ces cinq forces détermine la particule dans
la gouttière de la spirale (De Souza. 2009) :
y' La force de pesanteur Fg : agi sur le diamètre d et
la densité ó de la particule submergée dans le
fluide (eau) de densité ?? en donnant :
???? = ?? 6 ???? 3(??-?)g II.1
y' La force centrifuge Fc : cette force provoque le mouvement
radial dirigeant des particules légères vers la paroi de la
gouttière de rayon r à une vitesse vp.
???? =
II.2
??3
?? ??(ó-?)???? 2
6 ??
y' La trainée hydrodynamique Fd ou T : cette force est
exercée sur la particule dans la nappe pelliculaire suite au contact de
celle-ci avec le fluide (eau) en donnant :
????= ????????? 2h sin ? II.3
4
y' La force de Bagnold FBg : incite les particules
les plus grosses (>100um) à se mouvoir vers le dessus du lit,
là où les contraintes de cisaillement sont minimales et les plus
petites vers le haut où les contraintes de cisaillement sont maximales
à la façon inverse d'un classificateur.
???? ??(??????) =
0,04??(ødp)2(????
????)2 II.4
11 | P a g e
? La force de friction Ff : causée par la
surface de la gouttière qui s'oppose au mouvement des particules.
???? = ???? tan ? II.5 Avec FN la force normale (Kalongo.
2016).
Une illustration de la répartition des particules
minérales sur une spirale en fonction de leurs densités est faite
sur la figure II.3.
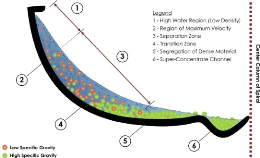
Figure II.3.Répartition des minéraux sur une
spirale (IMSC group. 2018)
II.2.3. Catégories des séparateurs en
spirale
Il existe plusieurs manières de classer les spirales,
elles peuvent être groupées selon la fabrication (en tenant compte
des caractéristiques physiques de la conception), selon les
caractéristiques de l'alimentation (teneur en élément
utile, la granulométrie, ...), etc
Cependant les spirales peuvent être classées en
deux grands types(Lalafandeferana. 2009) : ? Les spirales
Washwaterless
Ce type de spirale est utilisé dans la plupart des
applications, en particulier pour concentrer les minerais à faible
teneur. La seule eau nécessaire est ajoutée avec les solides
avant d'introduire l'alimentation dans la spirale. Les concentrés sont
retirés soit par le bas directement dans la boîte de produit, soit
à plusieurs points de prélèvement intermédiaires le
long de la spirale. Ce type de spirale est utilisé à l'usine
pilote de minéralurgie à la GCM/EMT. Une illustration de cette
catégorie de spirale est faite à la figure II.4.
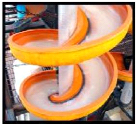
12 | P a g e
Figure II.4.Spirale Washwaterless (IMSC group.
2018)
? Les spirales Wash Water
Les spirales Wash Water nécessitent l'ajout d'eau
à divers points le long de la spirale et fournissent donc un «
lavage » du concentré, c'est-à-dire qu'elles évacuent
la gangue légère de la bande de concentré. La conception
de ce type de spirales, et en particulier le système d'eau de lavage, a
été développé pour répondre aux besoins des
producteurs modernes. La coupelle d'eau de lavage ouverte minimise la
possibilité de colmatage tout en offrant un débit variable et un
contrôle ponctuel au niveau de l'auge en spirale. La quantité
d'eau de lavage et sa distribution dans la cuve en spirale peuvent être
ajustées pour répondre aux exigences de fonctionnement. Le
contrôle ponctuel minimise les besoins totaux en eau en dirigeant
efficacement l'eau dans la pâte qui s'écoule à l'angle le
plus efficace.
Une illustration de ce type de spirale est faite à la
figure II.5.
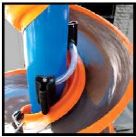
Figure II.5. Spirale Wash water (IMSC group.
2018)
13 | P a g e
II.2.4. Paramètres opératoires
Les procédés gravimétriques sont simples
et ne comportent que peu de variables opératoires, les principales
variables opératoires sur la spirale Humphreys sont la
granulométrie, le débit d'alimentation de la pulpe, le
pourcentage solide de l'alimentation, le débit d'eau de lavage et la
position des cuillères (collecteur de concentré) (Kalongo.
2016).
? La granulométrie
Les spirales ont une limitation dans la plage
granulométrique qui peut être traitée efficacement, cela
est dû à la géométrie générale et
à la conception. La gamme de taille la plus efficace se situe entre 45
et 500 tm dans les applications de sables minéraux lourds (Bornman.
2020).
La teneur en boue dans l'alimentation est aussi un facteur
influant sur les performances de la spirale. Les boues sont définies
comme des particules présentes dans l'alimentation et ayant une
granulométrie inférieure à 45 t (Bornman. 2020). Pour de
meilleures performances, l'alimentation doit être relativement exempte de
boues (-45 t), car une teneur élevée en boue peut agir comme un
"milieu lourd" et diminuer les différences effectives de gravité
spécifique entre les minéraux à séparer. En
règle générale, une boue dépassant 5% en poids de
l'alimentation en spirale peut réduire l'efficacité, et le
déschlammage, en tant qu'étape de pré-concentration, doit
être évalué. Si la quantité de boue dépasse
10 % en poids, le déschlammage avant la concentration sur spirale
entraînera presque certainement une amélioration des performances
de la spirale(Bornman. 2020).
? Le débit de la pulpe
Un accroissement du débit de pulpe fait augmenter la
vitesse de descente de la pulpe dans le couloir, de sorte que la vitesse
tangentielle des solides augmente, de même que la force centrifuge qui
s'y applique, dans ces conditions, plus de solides sont refoulés vers
l'extérieur. La conséquence de ce phénomène est que
plus de particules mixtes se dirigent au rejet, de sorte que le rendement
métal décroit au concentré, sa teneur augmente par le fait
même. Une baisse de débit a l'effet contraire (Kalongo. 2016). Les
fluctuations du débit d'alimentation affecteront la qualité du
concentré puisque la largeur de la bande de concentré changera
(IMSC group. 2018).
14 | P age
? Le débit de l'eau de lavage
L'eau de lavage, lorsqu'elle est utilisée, arrive
presque perpendiculairement à la direction d'écoulement du flot
de pulpe. C'est-à-dire que, si son débit croît, la strate
de particules de plus petite masse volumique, souvent des particules mixtes,
qui continue à subsister sur le dessus de la strate de particules de
haute densité est décapée et entrainée vers
l'extérieur du couloir de façon plus rapide et efficace. Il en
résulte un refoulement dans cette zone des particules mixtes, donc une
baisse de rendement métal au concentré, mais une augmentation de
sa teneur. Evidemment, un débit moindre a l'effet contraire (Kalongo.
2016).
? Le positionnement du collecteur de
concentré
Une concentration efficace dépend de la
sélection appropriée des orifices de prélèvement et
des ouvertures du séparateur utilisé (IMSC group. 2018).
L'ajustement des ouvertures de récupération du
concentré est la seule variable opératoire modifiée
systématiquement et au besoin dans l'usine. Son effet est simple
à déduire ; un degré d'ouverture plus grand permet une
récupération plus complète des particules denses, de sorte
que les solides résiduels ayant échappé aux ouvertures ont
une teneur moindre. Il en résulte un concentré final plus pauvre
et un rendement métal plus élevé. Une ouverture plus
petite a l'effet contraire (Bouchard. 2001).
? Le pourcentage solide de
l'alimentation
Enfin, La concentration de la pulpe de l'alimentation peut
varier selon les cas de 15 à 40 % en solides (généralement
25 à 30 %) (Kalongo. 2016).
Au cours des essais, les différents paramètres
peuvent être modifiés pour obtenir les résultats de
séparation souhaités, en gardant à l'esprit qu'une spirale
atteindra normalement un rapport de valorisation de 3/1 (rapport entre la
qualité du concentré et la qualité d'alimentation en
minéraux lourds). Par conséquent, comme avec la plupart des
concentrateurs gravitaires, un schéma de traitement à plusieurs
passages est souvent nécessaire pour obtenir la qualité et la
récupération souhaitées des minéraux lourds (IMSC
group. 2018).
II.3. Concentration magnétique
II.3.1. Introduction
Les phénomènes magnétiques sont connus
et exploités depuis de nombreux siècles. Les premières
expériences avec le magnétisme impliquaient la magnétite,
le seul matériau qui se
15 | P a g e
produit naturellement à l'état
magnétique. L'importance pratique de l'attraction magnétique en
tant que forme précurseur de la séparation magnétique a
été reconnue en 1792, lorsque W. Fullarton a obtenu un brevet
anglais pour la séparation du minerai de fer par attraction
magnétique. Depuis lors, la science et l'ingénierie du
magnétisme et de la séparation magnétique ont
progressé rapidement et un grand nombre de brevets ont été
délivrés. Alors que la séparation des constituants
intrinsèquement magnétiques était une des premières
applications naturelles du magnétisme, le séparateur de
Wetherill, conçu en 1895, était une innovation importante. Elle a
démontré qu'il était possible de séparer deux
composants, tous deux généralement considérés comme
non magnétiques. Dans la période qui a suivi, divers types de
séparateurs magnétiques secs à disque, à tambour et
à rouleau ont été développés, bien que le
spectre des minéraux pouvant être traités par ces machines
se soit limité à des matériaux plutôt grossiers et
modérément magnétiques. Depuis la fin du
XIXème siècle, il y a eu une expansion constante
à la fois de l'équipement disponible et de la gamme de minerais
auxquels la séparation magnétique est applicable. Le
développement des matériaux magnétiques permanents et
l'amélioration de leurs propriétés magnétiques ont
été les principaux moteurs de l'innovation dans la
séparation magnétique (Svoboda. 2004).
II.3.2. Aperçu général sur la
séparation magnétique ? Principes
Un champ magnétique est une région de l'espace
où une force magnétique fait sentir son influence. Par exemple,
le champ magnétique terrestre permet de s'orienter en affectant
l'aiguille de la boussole. Celle-ci va alors suivre les lignes du champ
magnétique terrestre pour s'aligner vers le pôle positif, ce qui
permet de s'orienter. Sous l'effet d'un champ magnétique, les corps vont
réagir de différentes façons. S'ils sont
Diamagnétiques, la matière répond par un champ
magnétique opposé à celui qui lui est appliqué, ce
qui annule son effet ; Paramagnétiques, la matière
répond par une aimantation dirigée vers le même sens que
celui du champ imposé, ce qui l'attire vers les pôles ;
Ferromagnétiques, s'aimantent fortement sous l'effet d'un champ
magnétique et ceci même après la disparition de ce dernier
(Will. 1998).
La séparation magnétique est utilisée
pour la concentration des matériaux magnétiques et pour
l'élimination des particules magnétisables des flux de fluides.
La séparation est réalisée en faisant passer les
suspensions ou les mélanges de particules dans un champ
magnétique non homogène. Ce processus conduit à une
rétention ou déviation préférentielle des
particules magnétisables. Le même objectif est souvent atteint de
manière très différente, les caractéristiques
communes étant une compétition entre un large spectre de forces
de diverses
16 | P age
amplitudes et portées. Dans la séparation
magnétique, la force externe de séparation est la force
magnétique. La séparation d'un matériau d'un autre ou
l'élimination des particules magnétisables des flux
dépendent de leur mouvement en réponse à la force
magnétique et à d'autres forces externes concurrentes, à
savoir les forces gravitationnelles, inertielles, hydrodynamiques et
centrifuges. Les forces inter particulaires d'origine
électromagnétique et électrostatique contribuent au
scénario global(Svoboda. 2004).
? Propriétés magnétiques des
matériaux
Le magnétisme représente un ensemble de
phénomènes physiques dans lesquels les objets exercent des forces
attractives ou répulsives sur d'autres matériaux. Les courants
électriques et les moments magnétiques des particules
élémentaires fondamentales sont à l'origine du champ
magnétique qui engendre ces forces. Tous les matériaux sont
influencés, de manière plus ou moins complexe, par la
présence d'un champ magnétique, et l'état
magnétique d'un matériau dépend de sa température
(et d'autres variables telles que la pression et le champ magnétique
extérieur) de sorte qu'un matériau peut présenter
différentes formes de magnétisme selon sa température. Les
propriétés magnétiques des matériaux proviennent
des courants électriques existant à l'échelle
microscopique en leur sein. Il existe donc (Vuninga. 2020) :
V' Le mouvement orbital : c'est le mouvement des
électrons autour de noyau ; V' Le mouvement de spin : c'est le
mouvement de rotation de l'électron ;
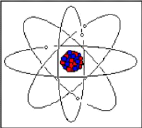
Figure II.6.mouvement des
électrons (Vuninga. 2020)
V' L'électron (blanc) : particule portant une
charge négative et tournant autour du noyau ;
V' Le proton (rouge) : particule portant une charge
positive et située dans le noyau, pesant environ 1850 fois la masse de
l'électron ;
V' Le neutron (bleu) : particule sans charge,
située dans le noyau, pesant la même masse que le proton.
Les aimants permanents possèdent des moments
magnétiques permanents à l'origine du ferromagnétisme.
Cependant, la plupart des matériaux ne possèdent pas de moments
permanents. Parmi ces derniers, certains sont attirés par la
présence d'un champ magnétique (paramagnétisme); d'autres
sont au contraire repoussés par celui-ci (diamagnétisme) ;
d'autres encore ont une relation beaucoup plus complexe avec un champ
magnétique appliqué (antiferromagnétisme) (Vuninga.
2020).
? Définitions des grandeurs fondamentales du
magnétisme ? Champ magnétique et
magnétisation
Lorsque l'on décrit un champ magnétique, deux
entités distinctes sont employées : l'intensité
? ? ? ?
de champ magnétique ??
|
et la densité de flux magnétique (ou induction
magnétique) ??
|
. ??
|
et ??
|
|
sont deux grandeurs vectorielles pourvues d'une direction et
d'une norme, s'exprimant respectivement dans le S.I (système
international d'unités) en Ampère par mètre (A/m) et en
Tesla (1T= 10000 Gauss). Dans le vide, ces deux grandeurs ne sont pas
indépendantes et sont reliées par la relation (Yoann R., 2020)
:
Où 1u0 est la
perméabilité magnétique du vide et est égale
à 4ð.10-7 Henry par mètre (H/m). La
perméabilité magnétique de l'air est de 37.10-6
% et supérieure à celle du vide (Cullity et al.,2008).
Cette relation n'est plus valable à l'intérieur
d'une matière aimantée de magnétisation
???
|
. La
|
|
densité de flux magnétique totale devient alors
:
= 1u0(??
? ) II.7
?
??
? +??
17 | P a g e
La magnétisation ??? , de
même dimension que ??? , est définie par le rapport du
moment magnétique total 1u?? des dipôles et du
volume V, tel que :
??? = 1u?? II.8
??
Dans la convention de Kennelly, particulièrement
privilégiée par les ingénieurs électriciens, la
densité de flux magnétique ??? est donnée par la relation
(Svoboda. 2004) :
??? = 1u0??? + ?? II.9
?
Où ?? est la polarisation magnétique qui est
reliée à ??
|
par la relation :
|
|
?
?? = P0?? II.10
La polarisation magnétique ?? s'exprime en Tesla. La
densité de flux magnétique inclut la
?
contribution de l'aimantation ??
|
, qui est définie comme le moment dipolaire
magnétique d'un
|
|
corps par unité de volume ou polarisation ??
définie par l'équation ci-dessus. ? Susceptibilité et
perméabilité magnétique
Généralement, l'aimantation
(magnétisation) d'un matériau dépend du champ
magnétique agissant sur lui. Pour de nombreux matériaux,
l'aimantation ??? est proportionnelle à
l'intensité
? ?
du champ magnétique ?? (du moins quand ?? n'est pas
trop élevée), ainsi leur relation est telle que (Svoboda. 2004)
:
?
= k?? II.11
?
??
Où k, la susceptibilité
magnétique volumique, est une propriété physique du
matériau représentant sa faculté à s'aimanter sous
l'action d'une excitation magnétique (Coey. 2010).
ont alors la même dimension et k est une
variable sans dimension. La susceptibilité
? ?
?? et ??
??? = P0(1+k)???
|
?
= P0P????
|
?
=P??
|
II.14
|
|
magnétique peut être reliée à la
perméabilité magnétique relative Pr du
matériau, telle que :
P?? = 1 + k II.12
La perméabilité relative P?t
est définie à partir de la perméabilité
magnétique P. La perméabilité magnétique
est une grandeur caractérisant la capacité d'un matériau
à modifier la densité de
?
flux magnétique ?? , c'est-à-dire à
modifier les lignes de flux magnétique. La perméabilité
magnétique et la perméabilité relative sont reliées
par la relation suivante :
P = PrP0 II.13
Où P s'exprime en Henry par mètre (H/m)
et Pr est sans dimension.
En combinant, les équations II.11 et II.7, la
densité de flux magnétique ??? devient :
18 | P a g e
? ?
Cette relation est valable lorsque le matériau est
isotrope et linéaire, M
|
et H
|
ont la même
|
|
19 | P a g e
direction. Cependant, la relation n'est pas
complétement valable dans le cas de matériau
ferromagnétiques.
La susceptibilité ou la perméabilité
peut être utilisée pour caractériser un matériau. La
susceptibilité magnétique volumique prend des valeurs proches de
0, positives et négatives, jusqu'à des valeurs supérieures
à 1 pour différents matériaux.
? Classification magnétique des
matériaux
La classification des matériaux est attribuable
à l'alignement des moments magnétiques des atomes lorsqu'ils sont
exposés à un champ magnétique indépendamment de
l'agitation thermique. Tous les matériaux présentent des
propriétés magnétiques, quels que soient leur état
et leur composition (Svoboda,2004). La plus grande différence se situe
par rapport aux comportements qu'ils affichent en présence d'un champ
magnétique. Ces comportements représentent les
propriétés magnétiques du matériau en
présence. Selon leurs propriétés magnétiques, les
matériaux peuvent être classés en cinq groupes de
base(Yoann. 2020) :
Les diamagnétiques, les paramagnétiques, les
ferromagnétiques, les antiferromagnétiques et les
ferrimagnétiques.
Les trois derniers groupes ont généralement de
très hautes valeurs de susceptibilités magnétiques et sont
fréquemment appelés « ferromagnétiques » au sens
large du terme.
? Les matériaux diamagnétiques
Ce type de matériaux est caractérisé par
une susceptibilité relative négative de faible amplitude et de
l'ordre de 10-9(SI). Le phénomène de
diamagnétisme se caractérise par la modification du mouvement
orbital des électrons autour du noyau atomique par l'application d'un
champ magnétique externe. Le courant induit par ce champ
magnétique donne lieu à un moment magnétique
supplémentaire, autrement dit une faible aimantation est
créée. Cependant, cette aimantation crée un champ
magnétique opposé au champ magnétique externe. Ainsi,
à l'approche d'un champ magnétique, un matériau
diamagnétique est repoussé (Yoann. 2020).
La susceptibilité magnétique pour ce type de
matériaux est totalement indépendante de la température.
Un grand nombre de matériaux inorganiques et quasiment toutes les
molécules organiques sont diamagnétiques. Dans beaucoup de
matériaux, le diamagnétisme est prédominé par les
effets de paramagnétisme et de ferromagnétisme (Svoboda.
2004).
20 | P a g e
? Les matériaux paramagnétiques
Dans les matériaux paramagnétiques, chaque
molécule possède un moment magnétique. En l'absence de
champ magnétique, les orientations des moments magnétiques des
particules sont aléatoires et en moyenne nulle. Par contre si l'on
applique un champ magnétique externe, ces derniers s'alignent avec le
champ, une aimantation apparait et est dirigée dans le sens du champ
appliqué. La susceptibilité magnétique est très
petite mais positive de l'ordre de 10-5 à
10-6(SI). Elle varie en raison inverse de la température en
obéissant à la loi de Curie suivante (Brissonneau. 1997) :
Xr = II.15
T
Avec T : la température absolue en Kelvin (K) C : la
constante de Curie telle que :
Où : c est une constante, n est le nombre de
dipôles magnétiques, ?M est le moment
magnétique et k est la constante de Boltzmann.
Une présentation des moments magnétiques dans
un corps paramagnétique en présence et en absence d'un champ
magnétique est faite à la figure II.7.
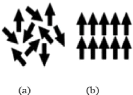
Figure II.7.Présentation des moments
magnétiques dans un corps paramagnétique (a) en absence et (b)
en présence d'un champ magnétique externe
(Mbwisha. 2021)
? Les matériaux ferromagnétiques
Le phénomène de ferromagnétisme est le
phénomène à l'origine des champs magnétiques les
plus importants et est responsable du phénomène bien connu du
magnétisme. Un matériau
21 | P a g e
ferromagnétique est attiré par un champ
magnétique. La susceptibilité magnétique d'un
matériau ferromagnétique est supérieure à
1(Svoboda. 2004).
Les matériaux ferromagnétiques ont une
propriété de s'aimanter même en l'absence d'un champ
magnétique. Lorsque le matériau est excité par un champ
d'excitation, ses moments magnétiques atomiques sont orientés
dans le même sens sur des petits domaines (interaction de proche en
proche entre les atomes). Donc, la valeur de leur aimantation est très
grande. Même après la suppression progressive de ce champ, le
matériau conserve une aimantation. Ces matériaux ont aussi une
température de curie, au-dessus de laquelle ils deviennent
paramagnétiques donc il est caractérisé par la loi de
curie comme suit(Brissonneau. 1997):
??
Xr = II.17
T-Tc
Une présentation des moments magnétiques dans
un corps ferromagnétique est faite à la figure II.8.

Figure II.8.Présentation des moments
magnétiques dans un corps ferromagnétique (Brissonneau.
1997)
La susceptibilité magnétique d'un
matériau ferromagnétique est dépendante de la
température, diminuant d'un maximum à la température T = 0
K, jusqu'à un point critique à la température de Curie Tc.
Au-delà de Tc, un matériau ferromagnétique se comporte
comme un matériau paramagnétique. La susceptibilité
magnétique ne suit pas la relation de Curie mais la relation de
Curie-Weiss telle que décrite ci-haut (Yoann. 2020).
? Les matériaux antiferromagnétiques
Les matériaux antiferromagnétiques
étaient à l'origine considérés comme une classe de
paramagnétiques anormaux, car ils ont de petites susceptibilités
positives d'amplitude similaire à de nombreux matériaux de cette
dernière classe. Cependant, leur susceptibilité magnétique
n'augmente pas régulièrement lorsque la température
diminue jusqu'au zéro absolu(Svoboda. 2004).
Dans les matériaux antiferromagnétiques, les
interactions d'échange entre atomes voisins conduisent à un
alignement antiparallèle des moments magnétiques. Ainsi,
l'aimantation totale
22 | P a g e
d'un matériau antiferromagnétique est nulle. La
susceptibilité magnétique dépend aussi de la
température du milieu, cependant elle n'augmente pas lorsque la
température diminue. À très haute température, la
susceptibilité magnétique suit la relation suivante :
Avec Tn : température de Néel
(température au-delà de laquelle un matériau
antiferromagnétique se comporte comme un paramagnétique).
Ainsi, lorsqu'un champ magnétique est appliqué
à un matériau antiferromagnétique, il présente un
comportement spécial dépendant de la température. Aux
très basses températures, le solide ne présente aucune
réponse au champ extérieur, car l'ordre antiparallèle des
aimants atomiques est maintenu de manière rigide. À des
températures plus élevées, certains moments
magnétiques se libèrent de l'arrangement ordonné et
s'alignent avec le champ externe. Cet alignement et le faible magnétisme
qu'il produit dans le solide atteignent leur pic à la température
de Néel. Au-dessus de cette température, l'agitation thermique
empêche progressivement l'alignement des atomes avec le champ
magnétique, de sorte que le faible magnétisme produit dans le
solide par l'alignement de ses atomes diminue continuellement à mesure
que la température augmente, on retrouve un comportement
paramagnétique (Yoann. 2020).Une illustration des moments
magnétiques dans un corps antiferromagnétique est faite à
la figure II.9.
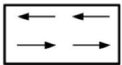
Figure II.9.Représentation des moments
magnétiques dans un matériau antiferromagnétique
(Svoboda. 2004)
? Les matériaux ferrimagnétiques
Dans les matériaux ferrimagnétiques, la
structure cristalline présente des sous-réseaux de moments
magnétiques ordonnés dans une orientation antiparallèle.
La somme des moments magnétiques pointant dans une direction est
supérieure à celle des moments pointant dans la direction
opposée. En l'absence d'un champ magnétique, un matériau
ferrimagnétique se comporte comme un antiferromagnétique
où les moments magnétiques sont alignés
antiparallèlement. Les matériaux ferrimagnétiques ont des
propriétés magnétiques similaires
aux matériaux ferromagnétiques. Lorsqu'un champ
magnétique est appliqué, les moments magnétiques
s'alignent dans la direction du champ magnétique.
À une température inférieure à la
température de Curie, un matériau ferrimagnétique se
comporte comme un ferromagnétique, au-delà de la
température de Curie, il adopte un comportement similaire à un
paramagnétique.
Le ferrimagnétisme apparaît en majorité dans
les ferrites, qui sont des céramiques à base d'oxydes de fer
mélangés avec d'autres éléments, et dans deux
oxydes de fer que sont la magnétite Fe3O4 et la maghémite
ã-Fe2O3(Yoann. 2020).
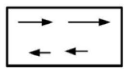
Figure II.10.Représentation des moments
magnétiques dans un matériau ferrimagnétique
(Svoboda. 2004)
II.3.3. Classification des appareils de
séparation magnétique
Dans la séparation magnétique, de nombreux
appareils sont disponibles et leur description ne peut se faire sans une
classification. Plusieurs critères de classement peuvent être
utilisés, l'intensité du champ magnétique, le milieu de
séparation (eau ou air), le mode de fonctionnement (extraction ou
déviation), le générateur de champ magnétique,
etc.
On distingue trois grandes familles des séparateurs
magnétiques(Bousmina. 2015): séparateurs à basse
intensité, séparateurs à haute intensité et les
séparateurs à haut gradient et/ou haut champ. La classification
présentée dans le tableau II.1 est faite en fonction du
générateur de
champ et de l'expression
?0??
(??)2du séparateur magnétique(Bousmina.
2015). Tableau II.1.Classification des séparateurs
magnétiques
Type de séparateur Générateur de
champ ?????
(??)??N/m3
Basse intensité Aimant permanent 2.104
à 106
Haute intensité Aimant permanent ou
électroaimant
|
2.107 à 109
|
|
Haut gradient et/ou haut champ
|
Solénoïde 6.1010 à
1012
|
|
23 | P a g e
24 | P a g e
? Séparateurs à basse
intensité (SMBI)
Les séparateurs magnétiques à basse
intensité fonctionnent normalement à champ ouvert,
c'est-à-dire que les lignes de forces magnétiques se referment
dans un milieu magnétique peu perméable, air ou eau. Ce sont en
général des séparateurs à construction simple, peu
onéreux et des dépenses énergétiques faibles. Ils
s'utilisent principalement pour les matériaux ferromagnétiques et
ferrimagnétiques (Bousmina. 2015).
Les SMBI sont généralement constitués
d'aimants permanents. Ces matériaux sont caractérisés par
une induction magnétique rémanente Br, leur permettant
de créer un champ magnétique sans dépense
énergétique. Les aimants permanent sont constitués
d'alliages de céramique de type Co5RE (où le RE désigne un
élément de terres rares) ou de fer-néodyme-bore (Fe-Nd-B)
pouvant créer un champ magnétique d'intensité atteignant
les 1,5 T (Gillet. 2003).
? Séparateurs magnétiques à
haute intensité (SMHI)
Ces séparateurs à circuits conventionnels sont
à champ magnétique fermé et développent des champs
magnétiques allant de 400 kA/m à 1 600 kA/m pour une consommation
énergétique comprise entre 0,5 et 2,5 kWh par tonne
traitée. Les débits solides varient quant à eux suivant le
mode de séparation et l'opération de traitement (concentration,
épuration) entre 6 et 180t/h (Bousmina, 2015). Pour le traitement en
voie sèche, des séparateurs à tambours à
électroaimant sont utilisés. Le principe de séparation des
particules paramagnétiques et diamagnétiques est illustré
dans la figure II.11.
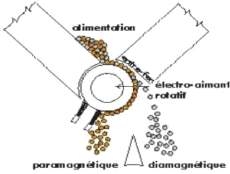
Figure II.11.Illustration du principe de fonctionnement
d'un séparateur magnétique
(Vuninga. 2020)
25 | P a g e
Les particules diamagnétiques sont
évacuées sous l'effet de la force centrifuge et de
répulsion tandis que les paramagnétiques restent collées
au rotor et en sont détachées à l'aide de ballais. Pour la
séparation des particules non ferreuses préalablement
débarrassés de ses composants ferreux, des séparateurs
à tambours à aimants permanents fonctionnant sur la base des
courants de Foucault sont utilisés.
En voie humide, les séparateurs SMHI sont
utilisés pour séparer les particules diamagnétiques et
paramagnétiques contenues dans des pulpes. Le premier des
séparateurs utilisés en voie humide est le type Jones à
carrousel construit par Humboldt (Nava. 1996). Actuellement,
des séparateurs en voie humide sont mis en exploitation par plusieurs
fabricants (ex. Eriez, Raoul lenoir, etc).
Ce séparateur est constitué de 2 pôles
(N-S) créant un champ magnétique intense dans la cellule de
séparation contenant des billes ferromagnétiques. L'utilisation
de billes de diamètres variables mène à l'obtention d'un
gradient de champ magnétique d'autant plus important que les billes sont
petites. Ce gradient de champ magnétique constitue le potentiel de
séparation. La pulpe est alimentée dans la cellule de
séparation. Les particules paramagnétiques sont retenues sur les
billes de fer tandis que les particules diamagnétiques sont
emportées par le flux d'eau puis récoltées. Les particules
paramagnétiques sont ensuite récoltées grâce
à un lavage à l'eau après disparition du champ
magnétique. Ce principe énoncé ci-haut est en application
à notre machine (séparateur magnétique) d'étude. La
figure II.12 illustre le principe de fonctionnement du SMHI en voie humide.
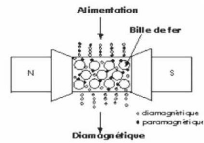
Figure II.12.Principe de séparation SMHI en voie
humide en utilisant des billes Ferro
magnétiques
(Vuninga. 2020)
La figure II.13 montre l'image du séparateur
magnétique utilisé dans le cadre de ce projet au laboratoire de
minéralurgie de la GCM/EMT.
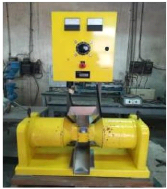
26 | P age
Figure II.13.Séparateur magnétique à
haute intensité en voie humide du type WHIMS 3*4L pesant environ 320
kg
? Séparateurs magnétique à
haut gradient de champ (SMHG) et/ou à haut champ
Ces séparateurs traitent les matériaux à
très petite granulométrie et les matériaux
paramagnétiques faibles. Le champ est généré par
solénoïde en cuivre résistif ou en alliage supraconducteur
qui permet d`atteindre une densité de force magnétique de
6.1010 à 1012N/m 3 (Ouili. 2013).
Le séparateur magnétique haut gradient (SMHG)
à bobinage de cuivre fonctionne à température ambiante et
nécessite un système de réfrigération par eau
déionisée. Le séparateur à bobinage supraconducteur
utilise quant à lui, un système cryostatique pour le
refroidissement de la bobine à la température de l'hélium
liquide. Quelle que soit la configuration de champ retenue, la
séparation supraconductrice nécessite toujours un
réservoir cryostatique rempli d'hélium liquide, destiné
à refroidir le bobinage en alliage supraconducteur (Mehasni. 2007).
II.3.4. Paramètres opératoires de la
séparation magnétique
Une particule de susceptibilité magnétique
Xm et de volume V, plongée dans un champ
magnétique non uniforme d'intensité H, est soumise
à une force dont l'expression simplifiée est donnée par
:
-
F = C XmV H? H II.19
Le gradient du champ magnétique étant
dirigé selon la ligne d'action de la force (C'est une Constante).
27 | P a g e
On constate donc que la force à laquelle est soumise la
particule dépend de sa nature, de son volume, de l'intensité du
champ magnétique et du gradient de celui-ci. Nous allons voir
ci-après l'importance de chaque paramètre dans l'utilisation de
cette force pour la séparation magnétique(Svoboda. 2004).
· Gradient du champ
magnétique
Le gradient du champ magnétique caractérise le
taux de changement spatial des lignes du ,champ magnétique (convergence
ou divergence). L'existence d'un tel gradient est la condition sine qua non
pour qu'une particule plongée dans un champ magnétique soit
soumise à une force.
· Nature des particules
La réaction d'un matériau à l'application
d'un champ magnétique extérieur H? ?
|
est caractérisée
|
par l'induction magnétique B
, laquelle représente l'intensité du champ
magnétique à l'intérieur du matériau, les moments
magnétiques des atomes s'alignant sur le champ extérieur.
?
L'induction magnétique B est
ainsi égale à la somme du champ extérieur (champ
inducteur) et du moment magnétique induit et on peut écrire :
? ? ?
B=
B0 + ?0??
II.20
Nous pouvons avoir les matériaux
paramagnétiques, diamagnétiques, ferromagnétiques et
ferrimagnétiques.
· Granulométrie
Comme le montre la relation de la force agissant sur les
particules, la force agissant sur les particules est proportionnelle à
leur volume qu'on pourra assimiler à la granulométrie. Or, les
opérations de séparation sont réalisées dans le
champ de la pesanteur terrestre et le poids des particules est proportionnel
à leur volume. La séparation entre particules se fait soit par
extraction, soit par déviation des particules magnétiques.
Dès lors, pour que la force magnétique soit suffisante pour
surpasser la force de pesanteur, il est nécessaire de travailler sur des
particules de faible dimension. Par ailleurs, deux particules de
susceptibilités magnétiques et de dimensions différentes
mais dont le produit ???? V est identique
sont soumises à une force de même intensité. La
séparation des grosses particules denses requiert un champ
magnétique plus intense que la séparation des petites particules
légères. Il est essentiel de souligner que
28 | P a g e
l'efficacité du procédé dépend du
degré de libération ou de la pureté des matériaux
à séparer (Gillet. 2003).
· Intensité du champ magnétique
H
L'intensité du champ magnétique traduit le
nombre de lignes de champ qui traverse une surface unitaire. Un champ
magnétique peut être obtenu soit au moyen d'un aimant permanent
soit au moyen d'un électroaimant. Antérieurement, on utilisait
des aimants permanents (fer doux, alliages au cobalt) pour traiter des minerais
contenant des minéraux ferromagnétiques (typiquement la
magnétite) pour lesquels l'intensité du champ
développé, assez faible, était suffisante et des
électroaimants, capables de développer des champs
magnétiques plus importants, pour la séparation des
minéraux paramagnétiques (Vuninga. 2020).
· Les forces compétitrices dans un
séparateur magnétique
Dans un séparateur magnétique, la force
magnétique est en compétition avec de multiples forces externes
comme les forces de gravité et d'inertie, la force centrifuge ou encore
la force de traînée hydrodynamique. L'importance de la
contribution de chacune de ces forces dépend du séparateur et des
conditions d'opérations (Yoann. 2020).
Les différentes forces citées
précédemment présentent des dépendances au rayon de
la particule, pouvant être exprimées telles que (Yoann. 2020):
???? ?????2,
???? ?????3 et ????
????? II.21
Ainsi, d'après l'équation II.21, la force de
gravité et la force centrifuge sont dépendantes du rayon de la
particule respectivement au carré et au cube, et leurs influences
deviennent significatives pour de grosses particules. Dans le cas contraire, la
force de traînée hydrodynamique, dans le régime
d'écoulement de Stokes, devient plus importante pour des particules
fines. Pour obtenir un taux de récupération élevé
de composés magnétiques, la force magnétique de
séparation doit être plus grande que la somme des forces
compétitrices, tel que(Yoann. 2020):
???????????????????? II.22
A ces paramètres nous pouvons ajouter :
· La concentration solide de la pulpe, qui est important
quand nous travaillons en séparation par voie humide ;
29 | P a g e
? La température de la pulpe qui est un
paramètre influant sur les propriétés magnétiques
des phases minérales constituant la pulpe ;
? Le débit volumique de la pulpe qui est le
paramètre de l'appareil employé ;
? La nature et la dose du réactif employé selon le
cas ; etc.
II.3.5. Application de la séparation
magnétique en minéralurgie
L'industrie des minerais est confrontée à des
problèmes de teneurs décroissantes des métaux valorisables
dans les minerais, à des proportions croissantes d'impuretés
nocives et à la nécessité de réduire la taille des
particules afin de libérer les composants précieux. Les nouvelles
technologies capables de relever ces défis doivent être
conçues pour des raisons environnementales et de durabilité.
La séparation magnétique, contrairement
à de nombreuses autres technologies de traitement des minéraux,
peut répondre avec succès aux attentes. En utilisant une
conception d'aimant sophistiquée ou des matériaux d'aimants
permanents avancés, la consommation d'énergie peut être
réduite de manière significative. Contrairement à la
flottation, la séparation magnétique ne nécessite pas de
produits chimiques responsables d'une augmentation constante des coûts
d'exploitation et des préoccupations environnementales. De même,
l'utilisation de liquides lourds, généralement toxiques et
coûteux à acquérir et à éliminer, dans la
séparation par densité et la préparation du charbon,
peuvent être éliminés en utilisant des techniques
basées sur le magnétisme (Svoboda. 2004).
Matériels et méthodes
|