1. CONTROLE DE LA DISPERSION CHROMATIQUE DANS LES FIBRES A
CRISTAUX PHOTONIQUES
1.1 Définition et historique de la fibre à
cristal photonique [3-1]
Les Fibres à cristaux photoniques (FCP) sont une classe
de fibres optiques constituées d'un arrangement de trous d'air
parallèles à l'axe de propagation dans d'une matrice de silice,
dont les toutes premières ont été proposées par
Kaiser et al. aux Bell Labs en 1974. L'objectif était à
l'époque d'obtenir un fort guidage dans un coeur de silice
entouré d'une gaine optique à très forte proportion d'air.
Mais ces fibres, très multimodes, n'ont pas provoqué
d'intérêt particulier dans la communauté scientifique car
elles n'apportaient pas de progrès sensible en terme de propagation.
Les travaux sur les FCP ont été relancés
dans les années 90, en vue de réaliser des structures à
bande interdite photonique (BIP). Ils ont très rapidement conduit
à mettre en lumière des propriétés inattendues dans
les FCP, même en l'absence d'effet BIP. C'est l'étude de ces
propriétés et leur exploitation qui est à l'origine de
l'extraordinaire enthousiasme dont les FCP font l'objet depuis une dizaine
d'années.
Ces FCP sont divisé en deux genres différents de
fibres :
> Le premier, FCP à guidage par l'indice, guide la
lumière par une réflexion interne totale entre le coeur plein
et la gaine avec des trous d'air multiples.
> Le second emploie une structure parfaitement
périodique montrant un effet de bande interdite photonique (BIP)
à la longueur d'onde de travail pour guider la lumière dans un
coeur à faible indice.
La figure 13 représente la section transverse d'une fibre
à cristal photonique.
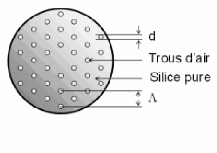
Figure 13 : Section transverse d'une FCP à arrangement
triangulaire
La FCP à guidage par l'indice, également
appelé fibres à trous ou fibres optique microstructurée,
possèdent une propriété particulièrement attrayante
de la grande contrôlabilité de la dispersion chromatique en
variant le diamètre de trous et leurs espacement.
1.2 Fabrication du FCP [3-1]
La fibre à cristal photonique a été
fabriquée dans les laboratoires de l'Université de Bath en 1996,
avec la technique de l'assemblage étirage qui consiste à
étirer à haute température un arrangement de capillaires
et de barreaux de silice.
Le processus de fabrication des FCP se fait en plusieurs
étapes :
La première consiste à réaliser un
arrangement de tubes capillaires à l'intérieur d'un tube de
maintien, comme le montre la figure 14. Ces capillaires sont
sélectionnés en fonction de leurs diamètres
intérieur et extérieur. Ils proviennent soit du commerce soit
d'étirages effectués au laboratoire à partir de tubes de
grande section. Un ou plusieurs capillaires au centre sont remplacés par
des barreaux de silice afin de former le coeur. On s'attend à ce que le
nombre de trous et leur disposition dans cet arrangement soient
conservés dans la fibre étirée. Cependant les conditions
d'étirage (température, pressions interne et externe) peuvent
modifier la taille et la forme de ces trous.
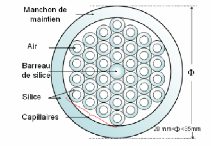
Figure 14 : arrangement de la préforme primaire
Bien que la régularité de l'arrangement ne soit
pas indispensable à l'obtention d'un guidage RTI, elle est
recherchée pour deux raisons. La première est que dans une
distribution aléatoire de trous apparaissent des zones de silice plus
larges susceptibles de se comporter comme autant de "coeurs" dans lesquels la
lumière peut se coupler. D'autre part, il est hautement improbable
qu'une fibre comportant un arrangement de trous quelconque présente des
caractéristiques de propagation pouvant répondre à un
cahier des charges initialement fixé. Autrement dit, la fibre doit
ressembler le plus fidèlement possible aux structures
régulières sur lesquelles sont basées les simulations
numériques qui permettent, connaissant les caractéristiques de
propagation visées, de définir les paramètres
géométriques à atteindre. Les trous interstitiels entre
les capillaires présents dans l'arrangement initial devront être
rebouchés lors de l'étirage. Pour cela, on chauffe une
extrémité de cet arrangement afin de rendre solidaires les
capillaires mais aussi de les reboucher. On réalise ensuite une
opération de verrerie qui consiste à enfermer une
extrémité du manchon de maintien dans une ampoule de silice afin
de pouvoir contrôler ultérieurement la pression
différentielle entre l'intérieur des capillaires et les
interstices lors du fibrage. L'ensemble constitue la préforme primaire
à partir de laquelle vont être étirées des cannes
microstructurées aux dimensions extérieures millimétriques
(figure 15 (a)). Cette première réduction d'échelle
homothétique est effectuée grâce à une tour de
fibrage équipée d'un
système d'entraînement par galets et d'un
dispositif de coupe de capillaires. Le contrôle des dimensions
(diamètre extérieur des cannes, pas et diamètre des trous
de la structure interne) repose sur la maîtrise de la rhéologie de
la silice pendant l'étirage. Les vitesses de descente de la
préforme et de fibrage, la température du four et les
différences de pression dans la préforme sont autant de
paramètres qui doivent être maîtrisés avec
précision pour obtenir une canne microstructurée de
qualité requise.
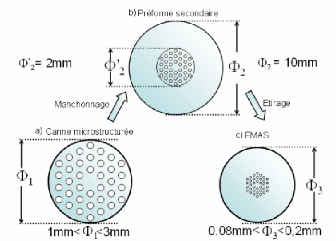
Figure 15: Canne microstructurée, préforme
secondaire et FCP
L'étape suivante consiste à manchonner la canne
microstructurée dans un tube à bord épais pour constituer
la "préforme secondaire" d'environ dix millimètres de
diamètre (figure 15 (b)). Finalement celle-ci est étirée
sur une seconde tour de fibrage qui dispose d'un tambour d'enroulement et d'un
système d'enduction qui permet de protéger la fibre par une gaine
polymère. La fibre obtenue mesure typiquement 125 um de diamètre
extérieur (figure 15 (c)).
Ce fibrage en deux étapes est indispensable pour obtenir
un rapport d'échelle important entre les motifs de la préforme
primaire et ceux de la fibre.
Aux longueurs d'onde de transparence de la silice, la taille
des trous dans la gaine doit être de l'ordre du micron, voire
submicronique, pour obtenir les caractéristiques de propagation voulues.
Cela signifie que le rapport d'échelle entre les trous des capillaires
de la préforme primaire et ceux de la fibre doit être très
grand (supérieur à 1000). C'est pourquoi le fibrage en deux
étapes avec remanchonnage de la canne microstructurée
intermédiaire est une opération indispensable.

Au cours de la seconde étape de fibrage, la
température apparaît comme un paramètre très
critique, qui doit être parfaitement maîtrisé . En effet,
à température trop basse, la trop forte viscosité de la
silice peut conduire à la rupture de la fibre. A mesure que la
température augmente, la viscosité de la silice diminue et la
pression des canaux d'air augmente, ce qui a une forte influence sur la
dimension des trous dans la fibre finale.
La figure 16 représente la section transverse d'une des
fibres réalisée. Ses paramètres géométriques
sont d=2 um et Ë=3,25 um. Le diamètre extérieur de la fibre
est de 125 um. Elle comporte 4 couronnes de trous dans la gaine.
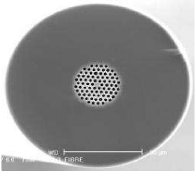
Figure 16 : exemple d'image de la section transverse d'une fibre
réalisée
La réalisation des FCP demande donc la maîtrise
de paramètres physiques (température, pression) qui sont
interdépendants. Le processus de fabrication décrit dans ce
paragraphe s'applique aussi bien aux FCP BIP qu'aux FCP RTI.
|