Chapitre I
Diagnostic des défauts dans la
machine
asynchrone
I.1 Introduction
Les machines électriques tournantes occupent une place
prépondérante dans tous les secteurs industriels. Les machines
asynchrones triphasées à cage d'écureuil sont les plus
fréquemment utilisées grâce à leur robustesse, leur
simplicité de construction et leur bas coût. Néanmoins,
celles-ci subissent au cours de leur durée de vie un certain nombre de
sollicitations externes ou internes qui peuvent les rendre défaillantes.
Les contraintes industrielles en fiabilité, maintenabilité,
disponibilité et sécurité des équipements sont par
ailleurs très fortes. C'est pourquoi le monde industriel est fortement
intéressé par un ensemble de techniques permettant de
déterminer l'état de santé de ces machines.
Plus généralement, la surveillance et le
diagnostic en génie électrique remettent en cause les concepts et
les outils traditionnels utilisés en conception et commande des machines
électriques tournantes. La modélisation des machines asynchrones
triphasées à cage d'écureuil en vue de la surveillance et
du diagnostic s'insère dans ce contexte.
I.2 Définitions
a. Terminologie propre au diagnostic de défaut
[10]
La terminologie suivante sera adoptée :
a) Système physique (Physical System)
Un système physique est un ensemble
d'éléments (composants, constituants) interconnectés ou en
interaction organisés pour réaliser une fonction.
b) Composant (Component)
Un composant est une partie du système, choisi selon des
critères liés à la modélisation. En
tout premier lieu, le comportement de référence
de ce composant est bien adapté dans le sens où il peut
être défaillant ou servir de support à la propagation de
pannes dans le système. Un composant doit être simple à
modéliser dans le sens où cela doit être naturel : il peut
s'agir d'un composant (physique ou logique) complet du système ou d'une
partie parfaitement délimitée de ce composant, d'un groupe de
composants.
c) Modèle (Model)
Un modèle d'un système physique est une description
de sa structure et une représentation comportementale ou fonctionnelle
de chacun de ses composants . Une représentation comportementale est
constituée de relations entre diverses variables du système,
appelées classiquement relations de causes à effets. Une
représentation fonctionnelle est plus abstraite puisqu'elle ne s'adresse
qu'aux objectifs présumés que le système physique doit
remplir.
d) Défaut (Fault )
- Tout écart entre la caractéristique
observée sur le dispositif et la caractéristique de
référence, lorsque celui-ci est en dehors des
spécifications [AFNOR, 1994].
- C'est n'importe quel état indésirable d'un
composant ou d'un système. Un défaut n'implique pas
nécessairement une défaillance [IEEE, 1988].
- Déviation non permise d'au moins une
propriété ou un paramètre caractéristique du
système des conditions acceptables ou (et) standards.
- Un défaut est une anomalie de comportement au sein d'un
système physique localisée au niveau d'un composant.
La définition de l'AFNOR rattache la notion de
défaut à celle de déviance d'une
caractéristique d'un phénomène,
subordonnant ainsi cette notion à l'existence d'une
référence absolue.
e) Défaillance (Failure)
Une défaillance définit une anomalie fonctionnelle
au sein d'un système physique , c'est-à-dire caractérise
son incapacité à accomplir certaines fonctions qui lui sont
assignées.
Les défauts incluent les défaillances mais la
réciproque n'est pas vraie. Un système peut
remplir sa fonction tout en présentant une anomalie de
comportement. Par exemple, une machine électrotechnique peut produire un
bruit anormal tout en entraînant correctement une charge, en supposant
que telle est sa fonction. Le bruit anormal est un défaut qui peut
permettre de présager d'une défaillance à venir. La
recherche de défauts est donc fondamentale en diagnostic.
f) Panne (Break-down)
La panne est l'inaptitude d'un dispositif à accomplir la
fonction vitale. Il est clair que dès l'apparition d'une
défaillance, caractérisée par la cessation du dispositif
à accomplir sa fonction, on déclarera le dispositif en panne. Par
conséquent, une panne résulte toujours d'une
défaillance.
g) Signatures
La signature théorique d'un défaut peut
être envisagée comme la trace attendue du défaut sur les
différents RRA qui modélisent le système. Autrement dit la
signature théorique d'un défaut peut être envisagée
comme les résultats de détection lorsque tous les tests sensibles
au défaut réagissent.
h) Symptôme (Symptom)
Caractère distinctif d'un état fonctionnel
anormal.
i) Résidu (Residual)
Souvent, lorsque le modèle comportemental de
référence est analytique, les signaux porteurs
de signes ou de symptômes sont appelés
résidus parce qu'ils résultent d'une comparaison entre un
comportement réel et un comportement de référence.
j) Diagnostic (Diagnosis)
Un diagnostic est un état expliqué d'un
système physique compatible avec les informations disponibles sur le
comportement réel du système et avec le modèle de
comportement de référence disponible. Habituellement, le
diagnostic est exprimé par les états des composants ou les
états des relations de description du comportement .
k) Perturbation
Entrée du système physique qui n'est pas une
commande. Autrement dit, c'est une entrée non contrôlée.
b) la maintenance
La maintenance est définie comme étant «
toutes les activités destinées à maintenir ou à
rétablir un bien dans un état ou dans des conditions
données de sûreté de fonctionnement, pour accomplir une
fonction requise. Ces activités sont une combinaison d'activités
techniques, administratives et de management. ».
Maintenir, c'est donc effectuer des opérations
(dépannage, graissage, visite, réparation,
amélioration...etc.) qui permettent de conserver le potentiel du
matériel, pour assurer la continuité et la qualité de la
production. Bien maintenir, c'est assurer ces opérations pour que le
coût global soit optimum. La figure représente le diagramme des
différents concepts de maintenance et les évènements
associés.
Maintenance

Non Oui
Défaillance
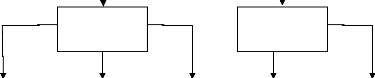
Maintenance préventive
Maintenance Corrective
Maintenance
|
|
Maintenance
|
Maintenance
|
|
Maintenance
|
Maintenance
|
systématique
|
|
conditionnel- le
|
Prévisionnel- le(prédictive)
|
|
palliative
|
curative
|
<< Ensemble des activités
réalisées après la défaillance du bien, ou la
dégradation de sa fonction pour lui permettre d'accomplir une fonction
requise, au moins provisoirement : ces activités comportent notamment la
localisation de la défaillance et son diagnostic, la remise en
état avec ou sans modification, le contrôle du bon fonctionnement.
>>
· Maintenance préventive
<< Maintenance ayant pour objet de réduire la
probabilité de défaillance ou de dégradation d'un bien ou
d'un service rendu. Les activités correspondantes sont
déclenchées selon un échéancier établi
à partir d'un nombre prédéterminé d'usage
(maintenance systématique), et/ou des critères
prédéterminés significatifs de l'état de
dégradation du bien ou du service (maintenance conditionnelle).
>>
1. Maintenance préventive
systématique
<< Ce type de maintenance comprend l'ensemble des
actions destinées à restaurer, en totalité ou
partiellement, la marge de résistance des matériels non
défaillants. Ces tâches sont décidées en fonction du
temps ou de la production, sans considération de l'état des
matériels à cet instant. >>
2. Maintenance préventive
conditionnelle
<< Ce type de maintenance comprend toutes les
tâches de restauration de matériels ou de composants non
défaillants, entreprises en application d'une évaluation
d'état et de la comparaison avec un critère
d'acceptation préétabli (défaillance
potentielle). >>
3. Maintenance prévisionnelle
(prédictive)
« C'est maintenance préventive
subordonnée à l'analyse de l'évolution surveillée
de paramètres significatifs de la dégradation du bien. Elle
permet de planifier les interventions.>>
Mon travail consiste à effectuer une maintenance
prédictive ` à la demande ' plutôt que d'effectuer une
maintenance systématique (méthode traditionnelle). Cela
évite de faire des changements de pièces qui dans 90 % des cas se
font de manière prématurée. Cela permet aussi de
prévoir une intervention lors d'un arrêt de production
programmé ou, si le cas le nécessite, lors d'un arrêt
d'urgence toujours moins pénalisant qu'un arrêt forcé. De
plus, les réparations avant incident sont plus faciles à
exécuter et moins coûteuses (en temps d'intervention et en
matériel). Il est aussi important de savoir qu'un
défaut non traité peut entraîner des dégradations
encore plus importantes.
Le concept hautement stratégique de maintenance
prédictive qui a poussé des chercheurs
à y contribuer diversement, nécessite la
connaissance des grandeurs significatives à mesurer pour avoir une image
aussi proche que possible de l'état de la machine. Le système de
suivi de la machine devrait pouvoir :
· interférer le moins possible avec le
système (les grandeurs peuvent-elles être mesurées " en
ligne ? ", problème de sécurité,....)
· être capable de suivre plusieurs grandeurs,
· être évolutif,
· être pilotable à distance,
· pouvoir stocker les données pour permettre une
analyse tendancielle.
Quant à la stratégie adoptée, elle consiste
à :
· recenser les défauts et les pannes pouvant se
produire,
· trouver les grandeurs mesurables liées à
ces défauts,
· choisir la méthode la plus proche des
critères définis ci-dessus,
· définir les seuils "d'alarme " à partir
desquels il faudra intervenir.
|