3.1.2 Le processus de fabrication (voir figure 3.1.1)
Aujourd'hui, la majorité des verres sont issus de la
méthode dite du << verre flotté >> ou << float
>> (en anglais). L'ensemble des composants du verre, quelques adjuvants
et les débris de verre sont dosés, mélangés et
amenés dans un four où le tout est chauffé à la
température de fusion de 1500°C. La silice seule a une
température de fusion plus importante (environ 1700°C) mais
grâce à l'ajout de fondant, essentiellement de la soude et des
débris de verre on peut donc diminuer la température de fusion.
La soude entre en fusion à une température de 1200°C et
crée donc un bain dans lequel trempe la silice. Les atomes de silices
sont donc chauffés sur toute leur surface, ce qui diminue le besoin de
chaleur. A la sortie du four la température n'est plus que de
1100°C, le liquide visqueux est versé sur de l'étain en
fusion plus dense que le verre. Cette particularité permet au verre de
flotter sur l'étain et d'avoir une surface parfaitement plane et aussi
une épaisseur constante. Le bain d'étain est placé sous
une atmosphère d'azote et d'hydrogène afin d'éviter tout
risque d'oxygénation. Le verre est entraîné par rouleaux
qui fixent par leur vitesse,
l'épaisseur du vitrage. Le vitrage passe par un four de
recuisson, c'est lors de cette étape que l'on découpe le verre
aux dimensions choisies. On obtient à la fin de ce processus ce qu'on
appelle le verre recuit. D'autres traitements de finitions sont possibles afin
d'améliorer l'une ou l'autre propriété du verre. Quelques
unes des possibilités seront développées
ultérieurement. Ce procédé de fabrication en continu fait
que les industries produisent du verre 24 heures par jour et ce, tous les jours
de l'année.
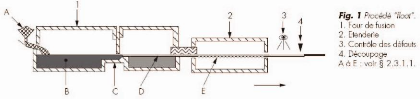
Figure 3.1.1 Processus de fabrication du verre flotté
[53]
Le verre qui sort de la chaîne de fabrication peut avoir
une épaisseur variant de 2mm à 25mm. Les dimensions maximales
d'une feuille de verre standard sont de 6000mm x 3210mm (dimension maximale
chez AGC flat glass) en verre recuit avec une tolérance de 5mm. Il est
possible au niveau technique de fabriquer des feuilles avec des dimensions plus
grandes mais cela pose des problèmes au niveau du transport, l'ensemble
des chevalets a été conçu pour des feuilles de maximum 6m.
Comme pour tous les matériaux fabriqués en usine, il y a une
certaine tolérance permise sur ces mesures. De plus, il y a
également une vérification à faire vis-à-vis de
l'équerrage : il faut vérifier que les angles soient
suffisamment proche de 90°.
Epaisseur nominale `e' (mm)
|
Tolérance sur l'épaisseur Verre float
(mm)
|
3
|
#177; 0.2
|
4
|
#177; 0.2
|
5
|
#177; 0.2
|
6
|
#177; 0.2
|
8
|
#177; 0.3
|
10
|
#177; 0.3
|
12
|
#177; 0.3
|
15
|
#177; 0.5
|
19
|
#177; 1
|
25
|
#177; 1
|
Tableau 3.1 1 : Tolérance sur l'épaisseur nominale
du verre float valeurs [53]
|