B. En parallèle
La fiabilité d'un système peut être
augmentée en plaçant les composants en parallèle. Un
dispositif constitué de n composants en parallèle ne peut tomber
en panne que si les n composants tombent en panne au même moment.
Si Fi est la probabilité de
panne d'un composant, la fiabilité associée Ri
est son complémentaire :
F??= 1 - R?? (2.2)
32
APPROCHE THÉORIQUE SUR LA MAINTENANCE ET LA
FMD
Fi représentant la
fiabilité associée.
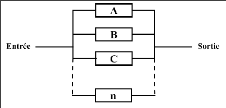
Figure 2-7: Composants en parallèle.
Soit les n composants de la figure ci-dessous montés en
parallèle. Si la probabilité de panne pour chaque composant
repéré (i) est notée Fi alors :
R?? = 1 - (1 - R)?? (2.23)
Le cas particulier de deux dispositifs en parallèle si
ë est constant RS est obtenu par :
R?? = 1 - (1 - R??). (1 - R??) = R?? + R?? - R??. R?? =
??-?????? + ??-?????? - ??-(????+????)?? (2.24)
2.2.2.2. La maintenabilité 2.2.2.2.1.
Définition
Dans des conditions données, la maintenabilité
est l'aptitude d'un bien à être maintenu ou rétabli dans un
état où il peut accomplir une fonction requise.
Maintenabilité = être rapidement
dépanné
C'est aussi la probabilité de rétablir un
système dans des conditions de fonctionnement spécifiées,
en des limites de temps désirées, lorsque la maintenance est
accomplie dans des conditions données, en utilisant des
procédures et des moyens prescrits. A partir de ces définitions,
on distingue :
? La maintenabilité intrinsèque : elle est
« construite » dès la phase de conception à partir d'un
cahier des charges prenant en compte les critères de
maintenabilité (modularité, accessibilité, etc.).
? La maintenabilité prévisionnelle : elle est
également « construite », mais à partir de l'objectif
de disponibilité.
? La maintenabilité opérationnelle : elle sera
mesurée à partir des historiques d'interventions. L'analyse de
maintenabilité permettra d'estimer la MTTR ainsi que les lois
probabilistes de maintenabilité (sur les mêmes modèles que
la fiabilité).
La maintenabilité caractérise la facilité
à remettre ou de maintenir un bien en bon état de fonctionnement.
Cette notion ne peut s'appliquer qu'a du matériel maintenable, donc
réparable.
La maintenabilité d'un équipement dépend
de nombreux facteurs (tableau2-2) [10] :
APPROCHE THÉORIQUE SUR LA MAINTENANCE ET LA
FMD
Tableau 2-2: Facteurs de la maintenabilité
d'un équipement
Facteurs liés
à l'EQUIPEMENT
|
Facteurs liés au CONSTRUCTEUR
|
Facteurs liés à
la MAINTENANCE
|
- Documentation
- Aptitude au démontage
- Facilité d'utilisation
|
- Conception
- Qualité du service après- vente
- Facilité d'obtention des pièces de rechange
- Coût des pièces de rechange
|
- Préparation et formation des personnels
- Moyens adéquats
- Etudes d'améliorations
(maintenance amélioratives)
|
On peut améliorer la maintenabilité en :
? Développant les documents d'aide à
l'intervention.
? Améliorant l'aptitude de la machine au démontage
(modifications risquant de coûter cher).
? Améliorant l'interchangeabilité des
pièces et sous ensemble.
2.2.2.2.2. Maintenabilité et
maintenance
Pour un technicien de maintenance, la maintenabilité
est la capacité d'un équipement à être
rétabli lorsqu'un besoin de maintenance apparaît. L'idée de
« facilité de maintenir » se matérialise par des
mesures réalisées à partir des durées
d'intervention. Il est évident que la maintenabilité
intrinsèque est le facteur primordial pour que la maintenance soit
performante sur le terrain. En effet, une amélioration ultérieure
de la maintenabilité initiale n'est jamais chose facile. Il est donc
indispensable que la maintenance sache définir ses besoins et les
intégrer au cahier des charges d'un équipement nouveau afin que
celui-ci puisse être facilement maintenable. [10]
2.2.2.2.3. Approche mathématique de la
maintenabilité M(t)
La maintenabilité peut se caractériser par sa
MTTR (Mean Time To Repair) ou encore Moyenne des Temps Techniques de
Réparation.
E Temps d'interventionpour n pannes
MTTR = (2.25) Nombre de pannes
La figure 2-8 schématise les états successifs que
peut prendre un système réparable :
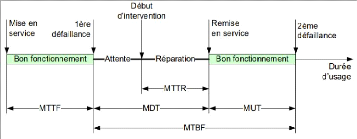
Figure 2-8: Schéma des états successifs que
peut prendre un système réparable. [10]
33
34
APPROCHE THÉORIQUE SUR LA MAINTENANCE ET LA
FMD
Les N valeurs de l'échantillon des durées
d'intervention seront relevées à partir des bons de travaux
complétés, puis portés sur l'historique d'un
équipement, que ce soit sous une forme « papier » ou «
écran ». L'analyse de maintenabilité peut porter sur
l'ensemble de l'équipement (afin de déterminer sa
disponibilité opérationnelle le plus souvent), ou sur l'un
quelconque de ses modules. C'est ainsi que sont élaborés par
exemple les barèmes de temps de réparation automobile. Il existe
une analogie forte entre les notions de fiabilité et de
maintenabilité. Les démarches d'analyse sont donc semblables :
? La VA : c'est la durée d'intervention corrective ou
préventive de maintenance. Elle se note t = TTR (Time To Repair ou Temps
Technique de Réparation), de moyenne MTTR.
? La densité de probabilité est notée
f(t). La distribution des durées d'intervention est cependant
dissymétrique. Les lois de probabilité ajustables à cette
dissymétrie sont la loi « log normale », la loi « gamma
» et la loi « LVE » des valeurs extrêmes appelée
aussi loi de Gumbel.
? La fonction de répartition est notée M(t).
Elle exprime la probabilité qu'une intervention ait une durée TTR
< t, ou que le système en panne à t = 0 soit rétabli
à t .
??(??) = 1 - e-???? (2.26)
? De façon analogue au taux de défaillance, on
définit un taux de réparation ì(t) tel que
??(??) = ????????= ??=
|
1
(2.27)
??
|
|
Les calculs prévisionnels de maintenabilité
reposent sur l'hypothèse exponentielle, signifiant ici que le taux de
réparation est supposé constant. La répartition des TTR
est alors exponentielle.
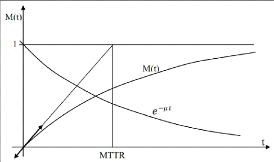
Figure 2-9: Courbe de la maintenabilité.
[10]
35
APPROCHE THÉORIQUE SUR LA MAINTENANCE ET LA
FMD
2.2.2.3. La disponibilité 2.2.2.3.1.
Introduction
La politique de maintenance d'une entreprise est
fondamentalement basée sur la disponibilité du matériel
impliqué dans le système de production. Pour qu'un
équipement présente une bonne disponibilité, il doit :
? Avoir le moins possible d'arrêts de production.
? Etre rapidement remis en bon état s'il tombe en
panne.
La disponibilité d'un équipement dépend de
nombreux facteurs :
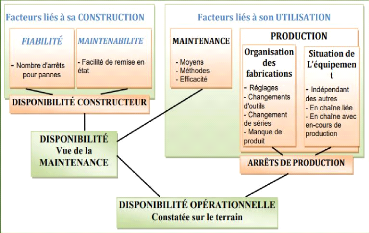
Figure 2-10: Facteurs de la disponibilité.
[10]
La disponibilité allie donc les notions de
fiabilité et de maintenabilité. Augmenter la disponibilité
passe par :
? L'allongement de la MTBF (action sur la fiabilité)
? La notion de le MTTR (action sur la maintenance)
2.2.2.3.2. Les types de disponibilité A.
Disponibilité intrinsèque :
Elle exprime le point de vue du concepteur. Ce dernier a
conçu et fabriqué le produit en lui donnant un certain nombre de
caractéristiques intrinsèques, c'est à dire des
caractéristiques qui prennent en compte les conditions d'installation,
d'utilisation, de maintenance et d'environnement, supposées
idéales.
MTBF
Di = (2.28) MTBF + MTTR + MTTE
36
APPROCHE THÉORIQUE SUR LA MAINTENANCE ET LA
FMD
Où :
· TBF : Temps de bon fonctionnement.
· TTR : Temps techniques de réparation.
· TTE : Temps techniques d'exploitation.
B. Disponibilité opérationnelle
:
Il s'agit de prendre en compte les conditions réelles
d'exploitation et de maintenance. C'est la disponibilité du point de vue
de l'utilisateur.
Le calcul de disponibilité opérationnelle fait
appel aux mêmes paramètres TBF, TTR et TTE sauf que ces 3
paramètres ne sont plus basés sur les conditions idéales
de fonctionnement.
C. Disponibilité moyenne :
La disponibilité moyenne sur intervalle de temps
donné peut être évaluée par le rapport Suivant :
temp de disponibilité ( )
D° =
2.29
temps de disponibilité + temps
d'indisponibilité
TCBF
D° =(2.30) TCBF + TCI
Où :
· TCBF = Temps cumulé de bon fonctionnement.
· TCI = Temps cumulé d'immobilisation.
2.2.2.3.3. Amélioration de la
disponibilité
· L'allongement de la MTBF (action sur la
fiabilité).
· La réduction de la MTTR (action sur la
maintenabilité).
· Fiabilité.
· Maintenabilité.
· Logistique.
2.2.2.3.4. Quantification de la disponibilité
La disponibilité peut se mesurer :
· Sur un intervalle de temps donné
(disponibilité moyenne),
· A un instant donné (disponibilité
instantanée),
· A la limite, si elle existe, de la disponibilité
instantanée lorsque t?8 (disponibilité asymptotique).
37
APPROCHE THÉORIQUE SUR LA MAINTENANCE ET LA
FMD
2.2.2.4. La relation entre MUT, MTBF, et MTTR
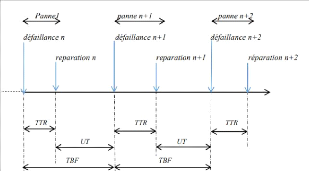
Figure 2-11: La relation entre MUT, MTBF, et MTTR.
[10]
2.2.3. Techniques utilisées en maintenance
2.2.3.1. Méthode ABC (Diagramme Pareto)
Parmi la multitude de préoccupations qui se posent
à un responsable de maintenance, il lui faut décider quelles
défaillances doivent être étudiées et/ou
améliorées en premier. Pour cela, il faut déceler celles
qui sont les plus importantes et dont la résolution ou
l'amélioration serait le plus rentable, en particulier en termes de
coûts d'indisponibilité.
La difficulté réside dans le fait que ce qui
« est important » et que ce qu'il « l'est moins » ne se
distinguent pas toujours de façon claire. La méthode ABC apporte
une réponse. Elle permet l'investigation qui met en évidence les
éléments les plus importants d'un problème afin de
faciliter les choix et les priorités.
On classe les événements (pannes par exemple)
par ordre décroissant de coûts (temps d'arrêts, coût
financier, nombre, etc..), chaque événement se rapportant
à une entité. On établit ensuite un graphique faisant
correspondre les pourcentages de coûts cumulés aux pourcentages de
types de pannes ou de défaillances cumulés. Sur le schéma,
on observe trois zones :
1. Zone A : 20% des pannes occasionnent 80% des coûts ;
2. Zone B : les 30% de pannes supplémentaires ne
coûtent que 15% supplémentaires ;
3. Zone C : les 50% de pannes restantes ne concernent que 5% du
coût global.
Conclusion : il est évident que la préparation
des travaux de maintenance doit porter sur les pannes de la zone A. [14]
38
APPROCHE THÉORIQUE SUR LA MAINTENANCE ET LA
FMD
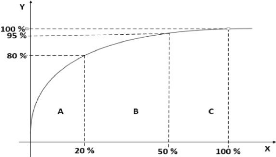
Figure 2-12: Diagramme de Pareto [4].
2.2.3.2. Diagramme des causes à effet 2.2.3.2.1.
Définition
Outil qui permet d'identifier les causes possibles d'un effet
constaté et donc de déterminer les moyens pour y remédier.
[14].
2.2.3.2.2. Représentation
Cet outil se présente graphiquement sous la forme
d'arêtes de poisson classant les catégories de causes
inventoriées selon la loi des 5 M (matière, main d'oeuvre,
milieu, matériels, méthodes)
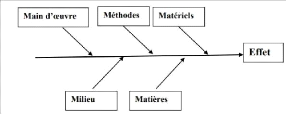
Figure 2-13: Diagramme cause et effet. [14]
? Il est très important de parvenir au consensus sur la
définition et les caractéristiques de la question traitée.
Il faut définir clairement l'effet sur lequel on souhaite directement
agir.
? Lister à l'aide de la méthode de «
brainstorming » par exemple, toutes les causes susceptibles de concerner
le problème considéré
Classer par famille toutes les causes d'un problème
donnée si nombre de causes par famille est trop important
2.2.3.2.3. Construction du diagramme
? Placer une flèche horizontalement pointée vers le
problème identifié ou le but recherché. ? Regrouper les
causes potentielles en familles, appelées les cinq M :
39
APPROCHE THÉORIQUE SUR LA MAINTENANCE ET LA
FMD
- Matière : Recense les causes ayant pour
origine les supports techniques et les produits utilisés.
- Main d'oeuvre : Problème de
compétence, d'organisation, de management.
- Matériel : Causes relatives aux
machines, aux équipements et moyens concernés. -
Méthode : Procédures ou modes opératoires
utilisés.
- Milieu : Environnement physique :
lumière, bruit, poussière, localisation, signalétique.
? Tracer les flèches secondaires correspondant au nombre
de familles de causes potentielles identifiées, et les raccorder
à la flèche principale
? Rechercher parmi les causes potentielles exposées, les
causes réelles du problème identifié.
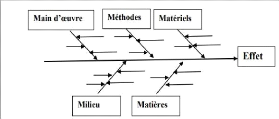
Figure 2-14: Schématique du diagramme cause et
effet. [14].
Ce sera notamment la cause la plus probable qu'il restera
à vérifier dans la réalité et à corriger. Le
diagramme Causes-Effet est donc l'image des causes identifiées d'un
dysfonctionnement potentiel pouvant survenir sur un système. Il se veut
le plus exhaustif possible en représentant toutes les causes qui peuvent
avoir une influence sur la sûreté de fonctionnement. Les 5 grandes
familles ou 5 facteurs primaires sont renseignés par des facteurs
secondaires et parfois tertiaires ; Les différents facteurs doivent
être hiérarchisés L'intérêt de ce diagramme
est son caractère exhaustif. [14]
2.2.3.3. Analyse de modes de défaillance, de leurs
effets et de leur criticité (AMDEC)
Le but d'une AMDEC est d'identifier les effets des modes de
bris d'équipement, de système ou d'usine. Cette analyse produit
généralement des recommandations qui conduisent à une
amélioration de la fiabilité de l'équipement.
L'AMDEC joue un rôle essentiel dans un programme
d'assurance fiabilité. Cette méthode peut s'appliquer à un
large éventail de problèmes survenant dans les systèmes
techniques. Elle peut être plus ou moins approfondies ou modifiées
en fonction du but à atteindre.
L'AMDEC est une méthode inductive qui permet de
réaliser une analyse qualitative de la fiabilité d'un
système depuis un niveau bas jusqu'à un niveau
élevé. [14]
40
APPROCHE THÉORIQUE SUR LA MAINTENANCE ET LA
FMD
2.2.3.4. Gestion de Maintenance Assistée par
Ordinateur (GMAO) 2.2.3.4.1. Définition
G.M.A.O. signifie Gestion de Maintenance Assistée par
Ordinateur. Il s'agit d'un logiciel spécialisé pour
réaliser la gestion d'un service technique. La Gestion de la Maintenance
Assistée par Ordinateur est constituée d'une base de
données (historique) qui est alimentée par le personnel de
maintenance via un formulaire. Chaque GMAO est personnalisée selon les
besoins spécifique d'exploitation de l'historique ou le fonctionnement
d'un site. [14]
2.2.3.4.2. Caractéristiques
générales
Un logiciel de GMAO permet de construire une base de
données dans laquelle on retrouvera :
· Les articles du magasin,
· Les fournisseurs,
· La gestion des entrées et sorties des articles,
· La gestion des achats,
· La gestion des actifs (équipements et
sous-ensembles),
· La gestion des interventions correctives,
· La gestion des interventions préventives,
· La gestion des demandes d'interventions,
· Les analyses financières et le suivi des
indicateurs de maintenance,
· La gestion des contacts clients et la facturation
2.3. Optimisation de la maintenance préventive
[11]
Il sera commode, de considérer ici qu'une machine (ou
un système) qui comporte un organe défaillant d'étudier
quelles sont les conséquences des décisions que l'on peut prendre
au sujet du remplacement de cet organe.
2.3.1. Remplacement systématique au bout du
temps Tr
La maintenance préventive de type systématique
consiste à faire des remplacements périodiques. Ces remplacements
sont effectués à des intervalles de temps fixes et
prédéterminés, si entre les périodes de
remplacement une défaillance se produit, on procède alors
à une maintenance corrective. Cette politique de maintenance
présente des défauts dans son principe puisqu'elle permet un
gaspillage de pièces de rechange. Ainsi, on pourra changer une
pièce ou un organe qui vient d'être remplacé dans
l'intervention d'une opération curative.
2.3.2. Détermination de la
périodicité optimale pour le remplacement préventif
[11]
Dans le cas du remplacement préventif, le
système ou appareil est remplacé par un nouveau avant qu'il ne
tombe en panne. Alors que, dans le cas d'un remplacement correctif c'est
l'unité ou la pièce défaillante qui est
remplacée.
La détermination de la périodicité
optimale pour le remplacement de pièces mécaniques, de
composants, de modules ou de sous-ensembles pose toujours un problème
économique et de
41
APPROCHE THÉORIQUE SUR LA MAINTENANCE ET LA
FMD
rentabilité, surtout lorsque les installations sont
similaires ou les machines sont identiques. Ce problème
économique peut être résolu par la connaissance de la
fiabilité opérationnelle et la détermination du moment le
plus avantageux pour effectuer cette opération de remplacement
préventif.
La périodicité optimale pour le remplacement
préventif peut être obtenue selon deux modèles
mathématiques : le modèle de remplacement par bloc et le
modèle de remplacement basée sur l'âge. Chaque
modèle peut donner lieu à plusieurs variantes.
2.3.2.1. Modèles de remplacements par
block
Toutes les pièces sont changées avec la
même périodicité T0 quel que soit l'âge de la
pièce et une pièce défaillante est remplacée
instantanément au moment de la défaillance (Figure 215).

Figure 2-15: Remplacement à période fixe
T0.
Avec
· S1 : Système 1
· R : Remplacement
· d : Défaillance
· T0 : Périodicité de
remplacement
2.3.2.2. Modèles de remplacements basés
sur l'âge
L'âge de chaque pièce est connu et on change la
pièce dès que son âge atteint la valeur T0 (Figure
2-16).

Figure 2-16: Remplacement lorsque l'âge de la
pièce T0 est atteint.
Avec :
· S1 : Système 1
· R : Remplacement
· d : Défaillance
· T0 : Age de la pièce
Cette étude consiste à faire un remplacement
préventif lorsque l'équipement a atteint l'âge T0 soit la
période de remplacement préventif choisie. La durée de la
période T0 a été déterminée de façon
à effectuer un remplacement préventif un peu avant le moment
où on estime que
APPROCHE THÉORIQUE SUR LA MAINTENANCE ET LA
FMD
l'équipement risque de tomber en panne. Cela permet de
minimiser les coûts. Si toutefois une panne survient, l'équipement
défaillant est remplacé par du neuf.
2.3.2.3. Choix entre réparation et remplacement
avant terme
Pour tout système complexe, il existe une date limite
appelée date L de réforme du système. Cette date L
résulte des phénomènes de fatigue agissant sur l'ensemble
du système. Elle est déterminée par des essais au banc de
fatigue et à partir de statistiques effectuées en temps
réel sur un échantillon.
Il intervient également dans la détermination de
L des facteurs de sécurité et des considérations
économiques. Les défaillances relevées au cours
d'utilisation du système conduiront à la réfection du
système ou à sa réforme avant terme.
La réfection (remise en état ou
réparation) se présente sous les deux aspects suivants :
? Les réparations mineures : ce sont des retouches ou
remplacements d'éléments simples.
? Les réparations majeures : elles conduisent à
reconstruire complètement les éléments autour de
l'élément pour lequel la durée de vie est fixée
L.
La réforme se présente sous les aspects suivants
:
? Dans le cas du matériel surchargé
au-delà des tolérances permises ou accidenté et reconnue
irréparable après expertise.
? Dans le cas où la milite L est arrivée.
? Dans le cas d'un système qui pourrait être
réparé mais dont le temps restant à utiliser est trop
faible pour qu'économiquement l'opération soit rentable. Le
problème est alors de déterminer t1 et t2, c'est-à-dire
l'âge auquel il convient de ne plus effectuer de réparation
majeure et mineure pour que le prix de revient majeur par système et par
unité de temps soit mineur (Fig 217).
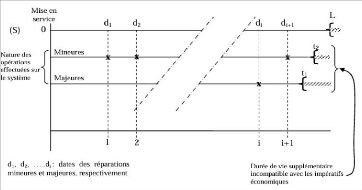
Figure 2-17: Schéma représentatif d'un
remplacement avant terme pour un système (S).
42
APPROCHE THÉORIQUE SUR LA MAINTENANCE ET LA
FMD
2.4. Conclusion partielle
En conclusion, nous avons exploré les dimensions
essentielles de la FMD qui sont intrinsèquement liées à
l'efficacité de la maintenance préventive. La fiabilité
assure une production continue sans défaillance imprévues, tandis
que la maintenabilité garantit que les interventions nécessaires
sont rapides et efficaces, minimisant ainsi le temps d'arrêt. La
disponibilité, résultant de la combinaison de la fiabilité
et de la maintenabilité, est le pilier final qui soutient la
disponibilité opérationnelle optimale de l'équipement.
L'optimisation de la maintenance préventive,
guidée par le principe de la FMD, permet non seulement d'anticiper et de
prévenir les pannes, mais aussi d'aligner les pratiques de maintenance
avec les objectifs stratégiques de l'entreprise. Cela conduit à
une amélioration de la sécurité, une réduction des
coûts et une augmentation de la productivité. En fin de compte,
une approche bien conçue de la maintenance préventive,
éclairé par la FMD, est un investissement stratégique pour
l'avenir, assurant la durabilité et la compétitivité dans
un marché de plus en plus exigeant.
43
44
ANALYSE FMD ET OPTIMISATION DE LA MAINTENANCE PREVENTIVE
DE LA POMPE CENTRIFUGE SULZER 086
Chapitre 3: ANALYSE FMD ET OPTIMISATION DE LA MAINTENANCE
PREVENTIVE DE LA POMPE CENTRIFUGE SULZER 086
3.1. Analyse FMD de la pompe centrifuge Sulzer 086
3.1.1. Cas étudié et préparation des
données
L'examen des fiches techniques de la pompe centrifuge Sulzer
086 a permis de collecter les données brutes relatives aux dates des
interventions ainsi que les temps de réparations correspondants.
Pour pouvoir exploiter ces données brutes, on
procède par :
? Le calcul des heures techniques de réparation (TTR)
(Tableau 3-1) ;
? Le calcul des heures de bon fonctionnement (TBF), qui
résultent des différences entre deux pannes successives. (Tableau
3-2).
3.1.2. Dossier historique de la pompe centrifuge
Sulzer 086
Les pannes enregistrées dans le tableau 3-1 ont
été recueillies à partir du 26 JUIN de l'année 2023
jusqu'au 06 FÉVRIER 2024.
Tableau 3-1: Dossier historique de la pompe.
Centrifuge Sulzer 086
N
|
Date de panne
|
Début d'arrêt
|
Heure de démarrage
|
TTR
|
Interventions
|
1.
|
27/06/2023
|
08h15
|
09h00
|
0.75
|
Installer la tuyauterie d'aspiration
|
2.
|
28/07/2023
|
18h20
|
20h20
|
2
|
Installer la cage pour la pompe submersible
|
3.
|
30/07/2023
|
08h10
|
10h10
|
2
|
Effectuer toutes les taches électriques
|
4.
|
06/08/2023
|
15h25
|
16h25
|
1
|
Remplacement de l'arbre
|
5.
|
10/09/2023
|
10h00
|
10h15
|
0.25
|
Remplacement du manomètre
|
6.
|
21/09/2023
|
15h10
|
16h00
|
0.8
|
Rénovation de la pompe
|
7.
|
28/10/2023
|
20h10
|
21h20
|
1.1
|
Réparer la fuite de la ligne de presse-étoupe
|
8.
|
10/11/2023
|
10h40
|
10h50
|
0.1
|
Vidange de l'huile de la pompe
|
9.
|
25/11/2023
|
16h20
|
17h10
|
0.8
|
Remplacement des roulements
|
10.
|
30/11/2023
|
11h45
|
12h00
|
0.25
|
Panne électrique
|
11.
|
02/12/2024
|
11h00
|
12h00
|
1
|
Remplacement du joint mécanique
|
12.
|
07/12/2024
|
15h50
|
16h20
|
0.5
|
Réalignement du système d'entrainement
|
13.
|
11/12/2024
|
14h20
|
15h00
|
0.6
|
Remplacement du joint mécanique
|
|
45
ANALYSE FMD ET OPTIMISATION DE LA MAINTENANCE PREVENTIVE
DE LA POMPE CENTRIFUGE SULZER 086
14.
|
19/01/2024
|
10h15
|
10h35
|
0.3
|
Serrage des boulons d'encrage
|
15.
|
21/01/2024
|
10h20
|
10h40
|
0.3
|
Réglage du jeu de la roue
|
16.
|
24/01/2024
|
14h10
|
15h00
|
0.8
|
Remplacement de l'arbre
|
17.
|
06/02/2024
|
19h30
|
20h20
|
0.8
|
Remplacement du joint mécanique
|
|
3.1.3. Calcul du temps de bon
fonctionnement
Après l'exploitation du dossier historique des pannes
de la pompe centrifuge Sulzer 086, On peut calculer les temps de bon
fonctionnement (TBF) en le regroupant dans le tableau 3-2 :
TBF : Temps de fonctionnement entre
défaillance ou Temps de Bon Fonctionnement
Tableau 3-2: Calcul du TBF
N
|
Date de panne
|
Début d'arrêt
|
Heure de démarrage
|
TBF
|
1.
|
27/06/2023
|
08h15
|
09h00
|
754
|
2.
|
28/07/2023
|
18h20
|
20h20
|
38
|
3.
|
30/07/2023
|
08h10
|
10h10
|
175
|
4.
|
06/08/2023
|
15h25
|
16h25
|
835
|
5.
|
10/09/2023
|
10h00
|
10h15
|
269
|
6.
|
21/09/2023
|
15h10
|
16h00
|
893
|
7.
|
28/10/2023
|
20h10
|
21h20
|
303
|
8.
|
10/11/2023
|
10h40
|
10h50
|
366
|
9.
|
25/11/2023
|
16h20
|
17h10
|
115
|
10.
|
30/11/2023
|
11h45
|
12h00
|
47
|
11.
|
02/12/2024
|
11h00
|
12h00
|
123
|
12.
|
07/12/2024
|
15h50
|
16h20
|
95
|
13.
|
11/12/2024
|
14h20
|
15h00
|
932
|
14.
|
19/01/2024
|
10h15
|
10h35
|
48
|
15.
|
21/01/2024
|
10h20
|
10h40
|
76
|
16.
|
24/01/2024
|
14h10
|
15h00
|
317
|
17.
|
06/02/2024
|
19h30
|
20h20
|
217
|
Parmi les lois utilisées pour la mesure de la
fiabilité ont choisi la loi de Wei bull, c'est un modèle
mathématique particulièrement bien adapté à
l'étude statistique des défaillances, il couvre le cas où
le taux de défaillance et variable.
3.1.4. Calcul des paramètres de Wei
bull
Le tableau 3-3 comporte les TBF classés par ordre
croissant, et les F(i) calculés par la méthode des rangs
médians F(i)=?(??-0.3) /(??+0.4), (dans notre cas N =17 = 20) et on
trace la courbe de Wei bull (Figure 3.1) pour déduire les
paramètres â, ç et y :
46
ANALYSE FMD ET OPTIMISATION DE LA MAINTENANCE PREVENTIVE
DE LA POMPE CENTRIFUGE SULZER 086
Tableau 3-3: Classement des TBF et calcul des
F(i)
N°
|
TBF
|
F(i)
|
F(i)%
|
R(i)
|
1
|
38
|
0,04022989
|
4,02298851
|
0,95977011
|
2
|
47
|
0,09770115
|
9,77011494
|
0,90229885
|
3
|
48
|
0,15517241
|
15,5172414
|
0,84482759
|
4
|
76
|
0,21264368
|
21,2643678
|
0,78735632
|
5
|
95
|
0,27011494
|
27,0114943
|
0,72988506
|
6
|
115
|
0,32758621
|
32,7586207
|
0,67241379
|
7
|
125
|
0,38505747
|
38,5057471
|
0,61494253
|
8
|
175
|
0,44252874
|
44,2528736
|
0,55747126
|
9
|
217
|
0,5
|
50
|
0,5
|
10
|
269
|
0,55747126
|
55,7471264
|
0,44252874
|
11
|
303
|
0,61494253
|
61,4942529
|
0,38505747
|
12
|
317
|
0,67241379
|
67,2413793
|
0,32758621
|
13
|
366
|
0,72988506
|
72,9885057
|
0,27011494
|
14
|
754
|
0,78735632
|
78,7356322
|
0,21264368
|
15
|
835
|
0,84482759
|
84,4827586
|
0,15517241
|
16
|
893
|
0,90229885
|
90,2298851
|
0,09770115
|
17
|
932
|
0,95977011
|
95,9770115
|
0,04022989
|
3.1.5. Estimation des paramètres de la loi Wei
bull (ç, fi, y)
On utilise la méthode graphique en utilisant le
logiciel Excel pour voir l'allure de la courbe F(i)-TBF.
F(i)% - TBF
120 100 80 60 40 20
0
|
|
0 200 400 600 800 1000
|
Figure 3-1:Courbe F(i) - TBF.
On remarque que les points de notre courbe ne sont pas
alignés, on procède par un changement de variable.
? Premier changement des variables
On ordonne la gauche : on place les valeurs de F(t)
en pourcentage en échelle ln (- ln (1 - F (t))) et on ordonne aussi
sur l'axe X = -1 ; ce sont les valeurs ln (- ln (1 - F (t))).
Donc ??(t) = ln t et ??(t) = ln t(- ln(1 - ??(t)))
47
ANALYSE FMD ET OPTIMISATION DE LA MAINTENANCE PREVENTIVE
DE LA POMPE CENTRIFUGE SULZER 086
Tableau 3-4: Calcul de x(t) et
y(t)
N°
|
TBF
|
F(i)
|
F(i)%
|
R(i)
|
x(t)
|
ytt)
|
1
|
38
|
0,04022989
|
4,02298851
|
0,95977011
|
3,63758616
|
-3,19268466
|
2
|
47
|
0,09770115
|
9,77011494
|
0,90229885
|
3,8501476
|
-2,27487758
|
3
|
48
|
0,15517241
|
15,5172414
|
0,84482759
|
3,87120101
|
-1,78009153
|
4
|
76
|
0,21264368
|
21,2643678
|
0,78735632
|
4,33073334
|
-1,43098059
|
5
|
95
|
0,27011494
|
27,0114943
|
0,72988506
|
4,55387689
|
-1,1556011
|
6
|
115
|
0,32758621
|
32,7586207
|
0,67241379
|
4,74493213
|
-0,92411787
|
7
|
125
|
0,38505747
|
38,5057471
|
0,61494253
|
4,82831374
|
-0,72108079
|
8
|
175
|
0,44252874
|
44,2528736
|
0,55747126
|
5,16478597
|
-0,53726488
|
9
|
217
|
0,5
|
50
|
0,5
|
5,37989735
|
-0,36651292
|
10
|
269
|
0,55747126
|
55,7471264
|
0,44252874
|
5,59471138
|
-0,20426061
|
11
|
303
|
0,61494253
|
61,4942529
|
0,38505747
|
5,71373281
|
-0,04671151
|
12
|
317
|
0,67241379
|
67,2413793
|
0,32758621
|
5,75890177
|
0,10975448
|
13
|
366
|
0,72988506
|
72,9885057
|
0,27011494
|
5,90263333
|
0,26919297
|
14
|
754
|
0,78735632
|
78,7356322
|
0,21264368
|
6,62539237
|
0,43705252
|
15
|
835
|
0,84482759
|
84,4827586
|
0,15517241
|
6,72743172
|
0,62230533
|
16
|
893
|
0,90229885
|
90,2298851
|
0,09770115
|
6,79458658
|
0,8440821
|
17
|
932
|
0,95977011
|
95,9770115
|
0,04022989
|
6,83733281
|
1,16725026
|
On trace ensuite notre deuxième courbe en fonction de x(t)
- y(t)
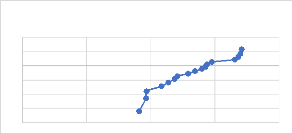
X(t)-Y(t)
2
1
0
- 1
- 2
- 3
- 4
0 2 4 6 8
Figure 3-2: Courbe x(t) - y(t).
On remarque que nos points ne sont toujours pas alignés
sur cette deuxième courbe, on change à nouveau la variable.
On calcul ã à partir de la formule 2.2, et
on trouve :
Tableau 3-5: Recherche de ã
Y1
|
-3,19268466
|
|
X1
|
3,63758616
|
T1
|
38
|
Y3
|
1,16725026
|
X3
|
6,83733281
|
T2
|
106,890662
|
Y2
|
-1,0127172
|
X2
|
4,67180646
|
T3
|
932
|
ã
|
31,724139
|
|
48
ANALYSE FMD ET OPTIMISATION DE LA MAINTENANCE PREVENTIVE
DE LA POMPE CENTRIFUGE SULZER 086
Deuxième changement de variable
x2' 4,31703564 t2'
74,9660718
t1' 6,275861
t3' 900,275861
Tableau 3-6: Deuxième changement de
variable
N°
|
TBF
|
F(i)
|
F(i)%
|
R(i)
|
ã
|
t'
|
x'
|
y
|
1
|
38
|
0,04022989
|
4,02298851
|
0,95977011
|
31,724139
|
6,275861
|
1,83671069
|
-3,1926846
|
2
|
47
|
0,09770115
|
9,77011494
|
0,90229885
|
31,724139
|
15,275861
|
2,72627387
|
-2,2748775
|
3
|
48
|
0,15517241
|
15,5172414
|
0,84482759
|
31,724139
|
16,275861
|
2,78968309
|
-1,7800915
|
4
|
76
|
0,21264368
|
21,2643678
|
0,78735632
|
31,724139
|
44,275861
|
3,79043963
|
-1,4309805
|
5
|
95
|
0,27011494
|
27,0114943
|
0,72988506
|
31,724139
|
63,275861
|
4,14750391
|
-1,1556011
|
6
|
115
|
0,32758621
|
32,7586207
|
0,67241379
|
31,724139
|
83,275861
|
4,42215872
|
-0,9241178
|
7
|
125
|
0,38505747
|
38,5057471
|
0,61494253
|
31,724139
|
93,275861
|
4,53556135
|
-0,7210807
|
8
|
175
|
0,44252874
|
44,2528736
|
0,55747126
|
31,724139
|
143,275861
|
4,96477187
|
-0,5372648
|
9
|
217
|
0,5
|
50
|
0,5
|
31,724139
|
185,275861
|
5,22184585
|
-0,3665129
|
10
|
269
|
0,55747126
|
55,7471264
|
0,44252874
|
31,724139
|
237,275861
|
5,46922343
|
-0,2042606
|
11
|
303
|
0,61494253
|
61,4942529
|
0,38505747
|
31,724139
|
271,275861
|
5,60313624
|
-0,0467115
|
12
|
317
|
0,67241379
|
67,2413793
|
0,32758621
|
31,724139
|
285,275861
|
5,65345665
|
0,10975448
|
13
|
366
|
0,72988506
|
72,9885057
|
0,27011494
|
31,724139
|
334,275861
|
5,81196658
|
0,26919297
|
14
|
754
|
0,78735632
|
78,7356322
|
0,21264368
|
31,724139
|
722,275861
|
6,58240714
|
0,43705252
|
15
|
835
|
0,84482759
|
84,4827586
|
0,15517241
|
31,724139
|
803,275861
|
6,68869819
|
0,62230533
|
16
|
893
|
0,90229885
|
90,2298851
|
0,09770115
|
31,724139
|
861,275861
|
6,75841485
|
0,8440821
|
17
|
932
|
0,95977011
|
95,9770115
|
0,04022989
|
31,724139
|
900,275861
|
6,80270123
|
1,16725026
|
On trace enfin la courbe x' - y
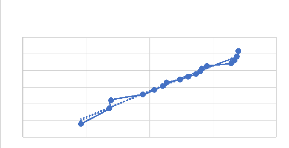
XI -Y
2
1
y = 0,7633x - 4,3029
0
-1
-2
-3
-4
0 2 4 6 8
Figure 3-3: courbe x' - y.
49
ANALYSE FMD ET OPTIMISATION DE LA MAINTENANCE PREVENTIVE
DE LA POMPE CENTRIFUGE SULZER 086
On remarque que notre deuxième courbe a une tendance
droite, on calcule ensuite nos paramètres :
fi
|
=
|
0,7633
|
ç
|
=
|
280,685006
|
ã
|
=
|
31,7639136
|
3.1.5.1. Test de KOLMOGOROV SMIRNOV
Le test de Kolmogorov Smirnov est un test hypothèse qui
permet de voir, pour un échantillon de durées observées,
si l'on peut accepter l'hypothèse d'une loi de distribution a un certain
risque de se tromper exprimer en pourcentage.
Afin de valider la loi de fiabilité, nous avons
calculé les écarts absolus entre le modèle
théorique et le modèle réel (Tableau 3-7) et le
comparé au valeurs seuils D?? ?? (voir Annexe 1)
Tableau 3-7: Le test de Kolmogorov
Smirnov
N°
|
TBF
|
F(i)
|
F(t)
|
F(i) - F(t)
|
1
|
38
|
0,04022989
|
0,19533699
|
0,1551071
|
2
|
47
|
0,09770115
|
0,22556004
|
0,12785889
|
3
|
48
|
0,15517241
|
0,22876031
|
0,0735879
|
4
|
76
|
0,21264368
|
0,30849994
|
0,09585626
|
5
|
95
|
0,27011494
|
0,35428165
|
0,08416671
|
6
|
115
|
0,32758621
|
0,39713586
|
0,06954965
|
7
|
125
|
0,38505747
|
0,41685474
|
0,03179727
|
8
|
175
|
0,44252874
|
0,50204456
|
0,05951583
|
9
|
217
|
0,5
|
0,56030039
|
0,06030039
|
10
|
269
|
0,55747126
|
0,62018245
|
0,06271118
|
11
|
303
|
0,61494253
|
0,65358949
|
0,03864696
|
12
|
317
|
0,67241379
|
0,66623522
|
0,00617858
|
13
|
366
|
0,72988506
|
0,70611245
|
0,02377261
|
14
|
754
|
0,78735632
|
0,88069141
|
0,09333508
|
15
|
835
|
0,84482759
|
0,8995657
|
0,05473812
|
16
|
893
|
0,90229885
|
0,91100098
|
0,00870213
|
17
|
932
|
0,95977011
|
0,91786275
|
0,04190737
|
D'après le tableau de K-S :
D?? ?????? = |??(i) - ??(t)| = 0.1551071 t??ndis??ue D?? ?
= D8,0.20 = 0.358 0.1551071 < 0.358 donc l'h??pothese du
??odele de Weibull est ??ccept??ble
50
ANALYSE FMD ET OPTIMISATION DE LA MAINTENANCE PREVENTIVE
DE LA POMPE CENTRIFUGE SULZER 086
3.1.5.2. Exploitation des paramètres de Wei bull
3.1.5.2.1. Calcul la fiabilité de la pompe
Le tableau en annexe 2 nous permet d'identifier les
paramètres : A=1.1380 et B= 1.4282 pour â= 0,8
Avec la formule ???????? = ??ç + y
???????? = 1.1380.280,685006 + 31,7639136 ???????? =
351,183451 heures
MTBF : Correspond à la durée
moyenne de la défaillance de bon fonctionnement après
réparation du système.
fi = 0,7633 A (â= 0,8) 1,138
ç = 280,685006 MTBF 351,183451
heures
ã = 31,7639136 en jours
14,6326438 jours
3.1.5.2.2. Calcul de R(t), F(t), ë(t) : « t =
MTBF =351 »
A partir de la formule 2-1, on calcul la fiabilité de
notre pompe :
??(??) = ??-(351.1-31.76
280.68 )0.76
??(??) = ??.???????????????????? = ????.??%
Nous avons 33 % de chance pour que la pompe centrifuge survive
au-delà de 351.1 h.
La fonction de réparation est calculée à
partir de la formule 2-2 :
??(??) = ?? - ??.???????????????????? =
??.????????????????????= 66.8%
Nous avons 66,8% de chance pour que la pompe centrifuge tombe en
panne entre 0 et
351h.
Le taux de défaillance est calculé par la formule
2-5 :
0.7633 351.1 - 31.76
??(??) = 280.685 (280.68 )0.76-1
??(??) =0.00263746785
La densité de probabilité de défaillance est
calculée par la formule 2-8 :
??-1
280.68 (351.1 - 31.76
0.76 . ??-(351.1-31.76
280.68 )0.76
??(??) = ??(??) * ??(??) = 280.68 )
??(??) =0.0008749465207
Nous avons 0,08749% de chance pour que la pompe centrifuge tombe
en panne juste à t = 351.1
h.
51
ANALYSE FMD ET OPTIMISATION DE LA MAINTENANCE PREVENTIVE
DE LA POMPE CENTRIFUGE SULZER 086
Tableau 3-8: Les paramètres de
fiabilité en fonction du MTBF
f(t=MTBF)
|
F (t=MTBF)
|
R(t=MTBF)
|
?(t=MTBF)
|
0.08749%
|
66.8 %
|
33.1 %
|
0.00263746785
|
3.1.5.2.3. Calcul du temps souhaitable pour une
intervention systématique L'efficacité que nous a
donné le constructeur de la pompe est de 79.5%
R(t) = 79.5% == t= ?
??-????
??(??) = ??( ??) (2.1)
1
t = ã - ç[lnR(t)]
â
?? = ???? h??u????s
Pour garder la fiabilité de la pompe à 79.5%, il
faut intervenir chaque temps systématique 73h. 3.1.5.3.
Étude du modèle de Wei bull
Les valeurs de la fonction de fiabilité, de
défaillance, de la fonction de probabilité et du taux de
défaillance pour la pompe sont calculées dans le tableau 4-9 :
Tableau 3-9: Les valeurs de R (t), F(t), f(t) et
ë(t)
N°
|
TBF
|
TTR
|
F(i)
|
R(t)
|
F(t)
|
?
|
1
|
38
|
0.75
|
0,04022989
|
0,94676396
|
0,19533699
|
0,00669539
|
2
|
47
|
2
|
0,09770115
|
0,89746278
|
0,22556004
|
0,00541933
|
3
|
48
|
2
|
0,15517241
|
0,89264846
|
0,22876031
|
0,00533839
|
4
|
76
|
1
|
0,21264368
|
0,78344106
|
0,30849994
|
0,00421091
|
5
|
95
|
0.25
|
0,27011494
|
0,72572027
|
0,35428165
|
0,00386939
|
6
|
115
|
0.8
|
0,32758621
|
0,67340357
|
0,39713586
|
0,00362572
|
7
|
125
|
1.1
|
0,38505747
|
0,64974249
|
0,41685474
|
0,00352964
|
8
|
175
|
0.1
|
0,44252874
|
0,54969231
|
0,50204456
|
0,00318855
|
9
|
217
|
0.8
|
0,5
|
0,48279457
|
0,56030039
|
0,00300027
|
10
|
269
|
0.25
|
0,55747126
|
0,41497868
|
0,62018245
|
0,00282961
|
11
|
303
|
1
|
0,61494253
|
0,377494
|
0,65358949
|
0,00274131
|
12
|
317
|
0.5
|
0,67241379
|
0,36336309
|
0,66623522
|
0,00270885
|
13
|
366
|
0.6
|
0,72988506
|
0,31899699
|
0,70611245
|
0,00260908
|
14
|
754
|
0.3
|
0,78735632
|
0,12779464
|
0,88069141
|
0,00217411
|
15
|
835
|
0.3
|
0,84482759
|
0,10739804
|
0,8995657
|
0,00212009
|
16
|
893
|
0.8
|
0,90229885
|
0,09506744
|
0,91100098
|
0,00208539
|
17
|
932
|
0.8
|
0,95977011
|
0,08767853
|
0,91786275
|
0,00206365
|
En fonction de ces différentes valeurs, nous trouvons
ensuite ces différentes courbes :
52
ANALYSE FMD ET OPTIMISATION DE LA MAINTENANCE PREVENTIVE
DE LA POMPE CENTRIFUGE SULZER 086
R(t)-TBF
1 0,8 0,6 0,4 0,2 0
|
|
0 200 400 600 800 1000
|
Figure 3-4: La courbe de fonction de
fiabilité.
F(t)-TBF
1 0,8 0,6 0,4 0,2 0
|
|
0 200 400 600 800 1000
|
Figure 3-5: La courbe de fonction de
répartition.
ë(t)-TBF
0,008 0,006 0,004 0,002
0
|
|
0 200 400 600 800 1000
|
Figure 3-6: La courbe taux de défaillance.
? Analyses des courbes :
Pour les courbes relatives à la fiabilité,
à la fonction de défaillance et au taux de défaillance on
peut tirer les constats suivants :
- Pour la fonction de fiabilité (Figure 3-4), la
fiabilité diminue d'une façon exponentielle avec le temps. Cette
décroissance est due à travers divers facteurs, parmi lesquels on
peut citer :
a. Le vieillissement des composants : Avec le temps, les
composants du système peuvent subir une usure naturelle qui entraine une
diminution de leur fiabilité.
53
ANALYSE FMD ET OPTIMISATION DE LA MAINTENANCE PREVENTIVE
DE LA POMPE CENTRIFUGE SULZER 086
b. Les conditions environnementales : Les conditions
environnementales telles que la température, l'humidité, la
poussière, etc., peuvent affecter la fiabilité des composants et
du système dans son ensemble.
c. La mauvaise maintenance : Une maintenance
inadéquate ou insuffisante peut entraîner une dégradation
de la fiabilité du système au fil du temps.
d. La conception du système : Une conception
inadéquate ou des choix de composants inappropriés peuvent
également contribuer à la diminution de la fiabilité du
système.
Il est important d'identifier les causes spécifiques de
la décroissance de la fiabilité afin de mettre en place des
actions préventives efficaces pour améliorer la fiabilité
du système.
- Pour la fonction de défaillance (Figure 3-5)
contrairement à la fonction de fiabilité
elle augmente avec le temps, cela peut indiquer plusieurs causes
possibles :
a. Le vieillissement accéléré : Certains
composants du système peuvent subir un vieillissement
accéléré en raison de conditions environnementales
défavorables, d'une surcharge de travail ou d'une utilisation intensive,
ce qui entraîne une augmentation de la probabilité de
défaillance.
b. Les défauts cachés : Il est possible que des
défauts ou des problèmes de fabrication non
détectés initialement commencent à se manifester avec le
temps, ce qui se traduit par une augmentation de la fonction de
défaillance.
c. Dégradation des composants : Les composants du
système peuvent subir une dégradation progressive due à
l'usure, à la corrosion, aux contraintes mécaniques, etc., ce qui
peut entraîner une augmentation de la probabilité de
défaillance.
d. Erreurs de conception : Une conception inadéquate
du système, des choix de matériaux inappropriés ou des
conditions de fonctionnement mal évaluées peuvent conduire
à une augmentation de la fonction de défaillance au fil du
temps.
Il est important d'identifier les causes spécifiques de
l'augmentation de la fonction de défaillance afin de prendre les mesures
nécessaires pour prévenir les défaillances et
améliorer la fiabilité du système.
- Pour le taux de défaillance (Figure 3-6), il a une
allure décroissante avec le temps, caractérisant ainsi la
période de jeunesse de la courbe en baignoire (Figure 2-2), cela peut
être dû à plusieurs facteurs :
a. Période de rodage : Au début de la vie du
système, les défaillances dues à des défauts de
fabrication initiaux ou à des conditions de fonctionnement
extrêmes peuvent se produire et être rapidement
détectées et corrigées, ce qui entraîne une
diminution du taux de défaillance.
54
ANALYSE FMD ET OPTIMISATION DE LA MAINTENANCE PREVENTIVE
DE LA POMPE CENTRIFUGE SULZER 086
b. Effet d'apprentissage : Les opérateurs et les
utilisateurs acquièrent de l'expérience dans l'entretien et
l'utilisation du système au fil du temps, ce qui peut réduire les
erreurs humaines et les défaillances liées à une mauvaise
manipulation.
c. Effet de l'environnement initial : Pendant la
période de jeunesse, les conditions environnementales peuvent être
plus favorables, ce qui contribue à réduire le taux de
défaillance.
Il est important de noter que cette décroissance du
taux de défaillance pendant la période de jeunesse n'est
généralement pas durable et peut-être suivie d'une
augmentation du taux de défaillance à mesure que le
système entre en phase de maturité et de vieillissement. Il est
essentiel de surveiller attentivement l'évolution de la courbe de
défaillance pour anticiper les éventuelles dégradations
futures et mettre en place des actions préventives appropriés.
3.1.5.3.1. Calcul de la maintenabilité de la pompe
centrifuge Sulzer 086 D'après l'historique des pannes de la
pompe :
MTTR = ?TR/N.
TR : Temps de réparation. N : Nombre de pannes.
MTTR = 13,25/17 = 0,77 h.
M (t) =1-??-ìt
Avec ? = 1/MTTR =1/0,77= 1,29
interventions/heure. M(MTTR) =1-??-0.77.1.29
M(MTTR) = 0,62964= 63%
Tableau 3-10: La
maintenabilité
TTR
|
M(t)
|
0,1
|
0,12453491
|
0,25
|
0,28287133
|
0,25
|
0,28287133
|
0,3
|
0,3290093
|
0,3
|
0,3290093
|
0,5
|
0,48572647
|
0,6
|
0,54977148
|
0,75
|
0,63119971
|
0,8
|
0,65492724
|
0,8
|
0,65492724
|
0,8
|
0,65492724
|
0,8
|
0,65492724
|
1
|
0,73552274
|
55
ANALYSE FMD ET OPTIMISATION DE LA MAINTENANCE PREVENTIVE
DE LA POMPE CENTRIFUGE SULZER 086
1
|
0,73552274
|
1,1
|
0,76845939
|
2
|
0,93005178
|
2
|
0,93005178
|
M(t)-TTR
1 0,8 0,6 0,4 0,2 0
|
|
|
0 0,5 1 1,5 2 2,5
|
Figure 3-7: La Courbe de maintenabilité de la
pompe.
D'après la courbe de maintenabilité (Figure
3-7), on constate que sa valeur croit avec le temps, cela signifie
généralement que le système devient plus facile à
maintenir et à réparer au fil du temps. Cette augmentation de la
maintenabilité peut être due à plusieurs facteurs :
a. Améliorations techniques : Les technologies
évoluent et les composants du système deviennent plus fiables,
plus faciles à remplacer et à réparer. Cela peut
contribuer à une maintenabilité du système.
b. Retour d'expérience : Les opérateurs et les
techniciens acquièrent de l'expérience dans la maintenance du
système, ce qui leur permet d'identifier plus rapidement les
problèmes et mettre en place des solutions efficaces. Ce retour
d'expérience peut améliorer la maintenabilité du
système au fil du temps.
c. Formation du personnel : Une formation continue du
personnel de maintenance peut également jouer un rôle important
dans l'amélioration de la maintenabilité du système, en
leur permettant de mieux comprendre son fonctionnement et d'effectuer des
interventions plus efficaces.
Il est important de noter que la croissance de la
maintenabilité soit généralement positive, il est
essentiel de surveiller régulièrement l'évolution de cette
courbe pour s'assurer que les améliorations se maintiennent dans le
temps et pour identifier tout potentiel déclin qui pourrait
nécessiter des actions correctives.
ANALYSE FMD ET OPTIMISATION DE LA MAINTENANCE PREVENTIVE
DE LA POMPE CENTRIFUGE SULZER 086
3.1.5.3.2. Calcul la disponibilité de la pompe
centrifuge Sulzer 086 ? Disponibilité intrinsèque de la
pompe :
Di=
|
????????
|
351,18
|
= ??.???? %
|
???????? + ???????? =
|
|
351,18 + 0.77
|
56
? Disponibilité instantanée :
D(??) = IL
A + IL + A
A + IL e-(??+??)??
1 1
A= ???????? = 351.18 = 0.00284h
IL =
|
1
???????? =
|
1
0.77
|
= 1.298 (
|
i????e????e????????
) ??e????e
|
A+ IL= 1.00065
D(??) =
|
1.298
1.00065 +
|
0.00284 1.00065 e
|
-(1.00065)??
|
Tableau 3-11: Disponibilité
instantané
t
|
D(t)
|
0
|
0,99610619
|
1
|
0,99349384
|
2
|
0,99128879
|
3
|
0,98942754
|
4
|
0,98785648
|
5
|
0,98653036
|
6
|
0,98541101
|
D(t)-t
0,998 0,996 0,994 0,992
0,99 0,988 0,986 0,984
|
|
0 1 2 3 4 5 6 7
|
Figure 3-8: Courbe de disponibilité
instantanée.
ANALYSE FMD ET OPTIMISATION DE LA MAINTENANCE PREVENTIVE
DE LA POMPE CENTRIFUGE SULZER 086
D'après la courbe de disponibilité (Figure 3-8),
on constate que sa valeur décroit avec le temps
Lorsque la courbe de la disponibilité
décroît avec le temps, cela signifie généralement
que la performance du système se dégrade au fil du temps. Voici
quelques explications possibles pour cette décroissance de la
disponibilité :
a. Usure et vieillissement : Avec le temps, les composants du
système peuvent subir de l'usure et du vieillissement, ce qui peut
entraîner des pannes plus fréquentes et une baisse de la
disponibilité.
b. Maintenance inadéquate : Si la maintenance
préventive n'est pas effectuée de manière
régulière ou adéquate, cela peut conduire à une
détérioration de la performance du système et à une
diminution de sa disponibilité.
c. Obsolescence : Les technologies et les équipements
peuvent devenir obsolètes avec le temps, ce qui peut rendre plus
difficile la maintenance et la réparation du système,
entraînant ainsi une baisse de disponibilité.
d. Facteurs externes : Des facteurs externes tels que les
conditions environnementales, les changements dans l'utilisation du
système ou les contraintes budgétaires peuvent également
influencer la disponibilité du système au fil du temps.
Lorsqu'on analyse une courbe de disponibilité
décroissante, il est important d'identifier les causes possibles de
cette tendance afin de mettre en place des actions correctives
appropriées. Cela peut inclure des stratégies de maintenance
préventive plus efficaces, des mises à niveau technologiques ou
des ajustements dans les pratiques opérationnelles pour améliorer
la disponibilité du système.
57
58
ANALYSE FMD ET OPTIMISATION DE LA MAINTENANCE PREVENTIVE
DE LA POMPE CENTRIFUGE SULZER 086
3.1.5.3.3. Interprétation des
résultats
Tableau 3-12: Interprétation des
résultats
I
|
Paramètres
|
Valeurs
|
Désignation
|
Interprétation
|
1
|
y
|
31.763
|
Paramètre de de position :
|
Lorsque le paramètre gamma est supérieur
à 1, cela indique une tendance à l'usure du système. Dans
notre cas, avec un paramètre
y de 31.7, cela suggère que la pompe n'a connu
aucune défaillance possible entre t = 0 heure et
t = 31.763 heure
|
C'est le paramètre de position ; il indique le temps de
début d'apparition des défaillances sur l'équipement
|
2
|
fi
|
0.763
|
Paramètre de forme :
|
Lorsque le paramètre bêta est inférieur
à 1, cela indique que la courbe de défaillance est
décroissante, ce qui signifie que la probabilité de
défaillance diminue avec le temps. Dans notre cas, avec un
paramètre bêta étant de 0,763, cela suggère que la
pompe centrifuge a une tendance à une diminution de la
probabilité de défaillance au fil du temps.
|
C'est le paramètre de forme qui indique l'allure de
dégradation du matériel ou l'allure du taux de
défaillance
|
3
|
ë(t)
|
0.00284
|
Taux de défaillance :
|
Le taux de défaillance de 0,00284 qu'on a trouvé
dans le calcul de la fiabilité est une mesure importante qui indique la
probabilité que la pompe centrifuge tombe en panne par unité de
temps spécifique.
Un taux de défaillance de 0,00284 signifie qu'en
moyenne, la pompe centrifuge a une probabilité de 0,00284 h de tomber en
panne.
|
C'est aussi la probabilité de l'apparition d'une
défaillance à un instant t.
|
4
|
ì(t)
|
2.833
|
Taux de réparation :
|
Le taux de réparation de 2,833 qu'on a trouvé
dans le calcul de la fiabilité des paramètres de Wei bull est une
mesure importante qui indique la fréquence à laquelle la pompe
centrifuge peut être réparée en moyenne sur une
période donnée.
|
C'est un indicateur de l'aptitude d'un bien à être
dépanné et/ou réparé. C'est aussi un indicateur de
l'efficacité de la maintenance dans la phase d'une intervention.
|
59
ANALYSE FMD ET OPTIMISATION DE LA MAINTENANCE PREVENTIVE
DE LA POMPE CENTRIFUGE SULZER 086
|
|
|
|
Un taux de réparation de 2,833 signifie qu'en moyenne,
la pompe centrifuge pourrait nécessiter environ 2,833 réparations
par heure
|
5
|
MTBF
|
351h
|
Moyenne de temps de bon fonctionnement
:
|
Dans notre cas, une MTBF de 351 heures signifie que, en
moyenne, notre pompe centrifuge peut fonctionner pendant 351 heures avant de
rencontrer une panne. En résumé, notre pompe centrifuge a une
durée de fonctionnement moyenne de 351 heures avant qu'une panne ne
survienne.
|
La MTBF représente le temps moyen pendant lequel un
système ou un composant fonctionne avant de tomber en panne. Plus les
pannes sont espacées dans le temps, plus le système est
fiable.
|
6
|
MTTR
|
0.352941176 h
|
Moyenne des temps techniques de réparation
:
|
Il est important de noter que le MTTR correspond à un
temps de réparation typique et non à une garantie. Un fournisseur
qui
affiche un MTTR de 24 heures indique le temps qu'il lui faut
généralement pour effectuer une
réparation, mais certains incidents peuvent prendre plus ou moins de
temps. Dans notre cas, un MTTR de 0,3529 heure signifie que, en moyenne, la
réparation de la pompe centrifuge prend environ 21 minutes.
|
Le MTTR représente le temps moyen nécessaire pour
réparer et rétablir la fonctionnalité d'un
système. Il englobe le temps de diagnostic, de correction
et de test, ainsi que toutes les autres activités permettant de remettre
le service à disposition des utilisateurs finaux.
|
7
|
R(t)
|
0,33
|
Fiabilité :
|
Ayant une valeur de 33 %, valeur inférieure à la
moyenne; ceci traduit que la pompe n'est donc pas fiable
|
C'est la caractéristique indiquant une
probabilité ou une proportion de succès.
Autrement dit est considéré fiable, un
système dont la probabilité de connaitre une défaillance
est faible
|
60
ANALYSE FMD ET OPTIMISATION DE LA MAINTENANCE PREVENTIVE
DE LA POMPE CENTRIFUGE SULZER 086
8
|
M
|
0 ,63
|
Maintenabilité :
|
Dans notre cas, une valeur de 0,63 pour la
maintenabilité indique que la pompe centrifuge est relativement facile
à entretenir et à réparer. Plus la valeur de
maintenabilité est élevée, plus il est aisé de
restaurer la pompe en cas de panne. Cela peut avoir un impact significatif sur
la disponibilité opérationnelle de la pompe, car des temps de
réparation plus courts permettent de minimiser les interruptions de
service.
|
La maintenabilité est l'aptitude d'une entité
à être
maintenue ou rétablie, sur un intervalle de temps
donné, dans un état dans lequel elle peut accomplir une fonction
requise, lorsque la maintenance est accomplie dans des conditions
données, avec des
procédures et des moyens prescrits1. En d'autres
termes, la maintenabilité mesure à quel point un
système ou un composant est facilement réparable.
|
9
|
D
|
0,99
|
Disponibilité :
|
Une disponibilité de 0,99 indique que la pompe est
opérationnelle à 99 % du temps. Cela indique que
la pompe centrifuge est prête à fonctionner la plupart du
temps.
|
La disponibilité d'une pompe centrifuge est un
indicateur essentiel qui mesure sa capacité à
fonctionner lorsque nécessaire.
|
61
ANALYSE FMD ET OPTIMISATION DE LA MAINTENANCE PREVENTIVE DE LA
POMPE CENTRIFUGE SULZER 086
3.2. Analyse par la méthode de Pareto
(ABC)
Cette méthode est basée sur la classification
des pannes selon la période où elles ont provoqué
l'arrêt de la machine sur une année complète, et cela nous
révélera les classifications des cellules A, B et C, où
nous commencerons la classification de la période la plus longue au plus
petit compte tenu du nombre de répétition (fréquence).
Tableau 3-13: Fréquences cumulées et
temps d'arrêt cumulés
Cause d'arrêt
|
Fr
|
Fr.c
|
Fr.c %
|
T.a
|
T.a.c
|
T.a.c %
|
Zone
|
Remplacement du joint mécanique
|
3
|
3
|
13,63636364
|
2
|
2
|
10,0452034
|
A
|
Remplacement de l'arbre
|
2
|
5
|
22,72727273
|
2
|
4
|
20,0904068
|
A
|
Remplacement de l'arbre
|
2
|
7
|
31,81818182
|
2
|
6
|
30,1356102
|
A
|
Panne électrique
|
2
|
9
|
40,90909091
|
2
|
8
|
40,1808137
|
A
|
Installer la cage pour le pompe submersible
|
1
|
10
|
45,45454545
|
2
|
10
|
50,2260171
|
A
|
Remplacement du joint mécanique
|
3
|
13
|
59,09090909
|
1,75
|
11,75
|
59,0155701
|
A
|
Rénovation de la pompe
|
1
|
14
|
63,63636364
|
1,5
|
13,25
|
66,5494726
|
A
|
Réparer la fuite de la ligne de presse-étoupe
|
1
|
15
|
68,18181818
|
1
|
14,25
|
71,5720743
|
A
|
Serrage des boulons d'encrage
|
1
|
16
|
72,72727273
|
1
|
15,25
|
76,594676
|
A
|
Réalignement du système d'entrainement
|
1
|
17
|
77,27272727
|
1
|
16,25
|
81,6172777
|
B
|
Installer le tuyau d'aspiration
|
1
|
18
|
81,81818182
|
1
|
17,25
|
86,6398795
|
B
|
Réglage du jeu de la roue
|
1
|
19
|
86,36363636
|
1
|
18,25
|
91,6624812
|
B
|
Effectuer toutes les taches électrique
|
1
|
20
|
90,90909091
|
0,83
|
19,08
|
95,8312406
|
B
|
Remplacement du manomètre
|
1
|
21
|
95,45454545
|
0,5
|
19,58
|
98,3425414
|
C
|
Vidange de l'huile de la pompe
|
1
|
22
|
100
|
0,33
|
19,91
|
100
|
C
|
62
ANALYSE FMD ET OPTIMISATION DE LA MAINTENANCE PREVENTIVE DE LA
POMPE CENTRIFUGE SULZER 086
Courbe de diagramme de Pareto :
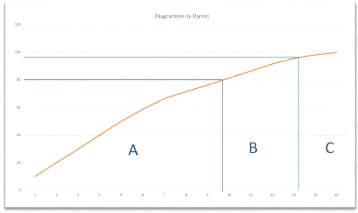
Figure 3-9: Présentation de diagramme de
Pareto.
? Zone A : On note que 9 types de
causes de pannes ont provoqué l'arrêt de la machine pendant 15,25
heures. Ce qui représente 80 % des heures d'arrêt.
? Zone B : on note que 4 types de
causes de pannes ont provoqué l'arrêt de la machine pendant 3,16
heures, ce qui représente 17% des heures d'arrêt.
? Zone C : On note que, 2types de
causes de pannes ont provoqué l'arrêt de la machine pendant 0.83
heures, ce qui représente 2% des heures d'arrêt.
3.3. Optimisation de la maintenance
préventive
3.3.1. Etude amélioratives de la sureté
de fonctionnement de la pompe centrifuge Sulzer 086
3.3.1.1. Présentation
Il est vrai que la pompe centrifuge Sulzer est une machine
capitale dans le processus de production de cuivre des usines MMG ; Cette
machine rencontre des pannes éventuelles qui impactent le fonctionnement
de l'outil tout en réduisant le rendement global de
l'équipement.
Les sources des arrêts de la machine sont les pannes,
celles-ci sont des éléments qui occasionnent le disfonctionnement
partiel ou global de la machine et ne permettent pas le fonctionnement de
l'équipement dans les bonnes conditions possibles.
Bien que les pannes soient imprévisibles pour
l'équipement en production, il est demandé de faire une
étude méthodologique pour l'amélioration du rendement
globale en termes de fiabilité, disponibilité et
maintenabilité de l'équipement d'où l'application de la
maintenance préventive systématique.
63
ANALYSE FMD ET OPTIMISATION DE LA MAINTENANCE PREVENTIVE DE LA
POMPE CENTRIFUGE SULZER 086
La maintenance préventive systématique est
l'ensemble des activités réalisées selon les
critères prédéterminés dans l'intention de
réduire la probabilité des défaillances d'un bien ou la
dégradation de l'équipement, elle consiste en une
opération de maintenance réalisée par un technicien de
manière régulière selon un certain cycle de temps.
3.3.1.2. Arbres des défaillances
Nous présentons les arbres de défaillances de
quelques organes de la pompe puis proposer quelques pistes des solutions
pouvant remédier aux problèmes que rencontre la pompe
centrifuge.
Nous allons présenter les arbres de défaillances
des organes/ éléments suivants :
? Les boulons de serrage
? L'arbre
? La fuite de la pompe
? Les roulements
? Le joint mécanique
3.3.1.2.1. L'arbre de défaillance des
boulons
Le diagramme ci-dessous nous permettra donc de trouver las
pannes primaires que peut connaitre les boulons avant défaillance.
NON ATTEINT
|
|
MANQUE D'OUTILLAGE
APPROPRIES
|
DESSERRAGE DES
BOULONS
COUPLE DE SERRAGE
DE FREIN D'ECROU
MANQUE DE SYSTÈME
VIBRATION
|
Figure 3-10:L'arbre de défaillance des boulons
64
ANALYSE FMD ET OPTIMISATION DE LA MAINTENANCE PREVENTIVE DE LA
POMPE CENTRIFUGE SULZER 086
Le tableau 3-14 nous montre la fiche de visite des boulons de
serrage
Tableau 3-14: Fiche de visite en maintenance
préventive systématique des boulons
CAUSES PRINCIPALES
|
CAUSES SECONDAIRES
|
MODE DE DEFAILLANCE
|
CONSEQUENCES
|
MESURE PREVENTIVE
|
Fatigue
|
Vibrations excessives
|
Rupture par fatigue
|
Fuite de liquide
|
Surveillance des vibrations
|
Surcharge de la pompe
|
Rupture par fatigue
|
Défaillance de la pompe
|
Protection contre la surcharge
|
Mauvais alignement des composants
|
Rupture par fatigue
|
Dommages aux composants
|
Alignement correct des composants
|
Corrosion
|
Humidité
|
Corrosion et perte de résistance
|
Rupture du boulon
|
Protection contre la corrosion
|
Produits chimiques
|
Corrosion et perte de résistance
|
Rupture du boulon
|
Utilisation de matériaux résistants aux produits
chimiques
|
Température élevée
|
Corrosion et perte de résistance
|
Rupture du boulon
|
Refroidissement de la pompe
|
Défaut de fabrication
|
Matériau défectueux
|
Rupture fragile
|
Fuite de liquide
|
Contrôle de la qualité des boulons
|
Usinage incorrect
|
Rupture fragile
|
Défaillance de la pompe
|
Contrôle de la qualité des boulons
|
Traitement thermique insuffisant
|
Rupture fragile
|
Dommages aux composants
|
Contrôle de la qualité des boulons
|
Mauvais serrage
|
Couple de serrage insuffisant
|
Défaut de serrage
|
Fuite de liquide
|
Procédure de serrage adéquate
|
Boulons desserrés
|
Défaut de serrage
|
Défaillance de la pompe
|
Contrôle du serrage des boulons
|
Outils de serrage inadaptés
|
Endommagement du boulon
|
Rupture du boulon
|
Utilisation d'outils de serrage adaptés
|
ANALYSE FMD ET OPTIMISATION DE LA MAINTENANCE PREVENTIVE DE LA
POMPE CENTRIFUGE SULZER 086
3.3.1.2.2. Arbre de défaillance des
roulements
Le diagramme ci-dessous nous permettra de trouver les pannes
primaires que peut connaitre les roulements avant défaillance
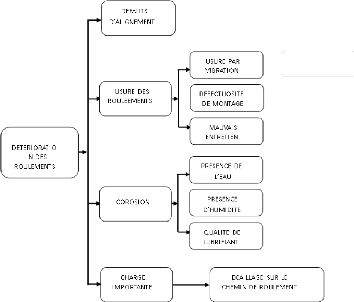
Figure 3-11: L'arbre de défaillance des
roulements
65
66
ANALYSE FMD ET OPTIMISATION DE LA MAINTENANCE PREVENTIVE DE LA
POMPE CENTRIFUGE SULZER 086
Le tableau 3-15 nous montre la fiche de visite des roulements
Tableau 3-15: Fiche de visite en maintenance
préventive systématique des roulements
CAUSE PRINCIPALE
|
CAUSE SECONDAIRE
|
MODE DE DEFAILLANCE
|
CONSEQUENCE
|
MESURE PREVENTIVE
|
Fatigue
|
Surcharge de la pompe
|
Usure excessive
|
Arrêt de la pompe
|
Protection contre la surcharge
|
Mauvais alignement des composants
|
Usure excessive
|
Dommages aux composants
|
Alignement correct des composants
|
Vibrations excessives
|
Usure excessive
|
Fuite de liquide
|
Surveillance des vibrations
|
Contamination du lubrifiant
|
Usure excessive
|
Défaillance du roulement
|
Protection contre la contamination
|
Usure
|
Charge excessive
|
Usure progressive
|
Arrêt de la pompe
|
Diminution de la charge
|
Lubrification insuffisante
|
Usure progressive
|
Dommages aux composants
|
Lubrification adéquate
|
Abrasion
|
Usure progressive
|
Fuite de liquide
|
Filtration du lubrifiant
|
Corrosion
|
Usure progressive
|
Défaillance du roulement
|
Protection contre la corrosion
|
Défaut de fabrication
|
Matériau défectueux
|
Rupture
|
Arrêt de la pompe
|
Contrôle de la qualité des roulements
|
Usinage incorrect
|
Rupture
|
Dommages aux composants
|
Contrôle de la qualité des roulements
|
Défauts de traitement thermique
|
Rupture
|
Fuite de liquide
|
Contrôle de la qualité des roulements
|
ANALYSE FMD ET OPTIMISATION DE LA MAINTENANCE PREVENTIVE DE LA
POMPE CENTRIFUGE SULZER 086
3.3.1.2.3. Arbre de défaillance de
l'arbre
Le diagramme ci-dessous nous permettra de trouver les pannes
primaires que peut connaitre l'arbre avant défaillance
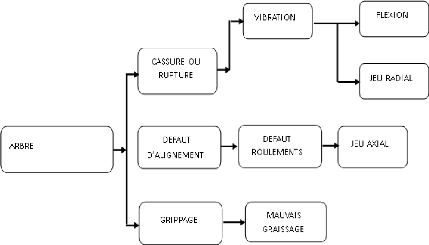
Figure 3-12: L'arbre de défaillance de
l'arbre
67
68
ANALYSE FMD ET OPTIMISATION DE LA MAINTENANCE PREVENTIVE DE LA
POMPE CENTRIFUGE SULZER 086
Le tableau 3-16 nous montre la fiche de visite de l'arbre
Tableau 3-16: Fiche de visite en maintenance
préventive systématique de l'arbre
CAUSE PRINCIPALE
|
CAUSE SECONDAIRE
|
MODE DE DEFAILLANCE
|
CONSEQUENCE
|
MESURE PREVENTIVE
|
Fatigue
|
Vibrations excessives
|
Rupture par fatigue
|
Fuite de liquide
|
Surveillance des vibrations
|
Surcharge de la pompe
|
Rupture par fatigue
|
Défaillance de la pompe
|
Protection contre la surcharge
|
Mauvais alignement des composants
|
Rupture par fatigue
|
Dommages aux composants
|
Alignement correct des composants
|
Corrosion
|
Humidité
|
Corrosion et perte de résistance
|
Rupture de l'arbre
|
Protection contre la corrosion
|
Produits chimiques
|
Corrosion et perte de résistance
|
Rupture de l'arbre
|
Utilisation de matériaux résistants aux produits
chimiques
|
Température élevée
|
Corrosion et perte de résistance
|
Rupture de l'arbre
|
Refroidissement de la pompe
|
Défaut de fabrication
|
Matériau défectueux
|
Rupture fragile
|
Fuite de liquide
|
Contrôle de la qualité de l'arbre
|
Usinage incorrect
|
Rupture fragile
|
Défaillance de la pompe
|
Contrôle de la qualité de l'arbre
|
Traitement thermique insuffisant
|
Rupture fragile
|
Dommages aux composants
|
Contrôle de la qualité de l'arbre
|
Surcharge
|
Débit excessif
|
Déformation et rupture
|
Fuite de liquide
|
Limitation du débit
|
Pression excessive
|
Déformation et rupture
|
Défaillance de la pompe
|
Limitation de la pression
|
69
ANALYSE FMD ET OPTIMISATION DE LA MAINTENANCE PREVENTIVE DE LA
POMPE CENTRIFUGE SULZER 086
3.3.1.2.4. Arbre de défaillance des joints
mécaniques
Le tableau 3-17 nous montre la fiche de visite des joints
mécaniques
Tableau 3-17: Fiche de visite en maintenance
préventive systématique des joints
mécaniques
CAUSE PRINCIPALE
|
CAUSE SECONDAIRE
|
MODE DE DEFAILLANCE
|
CONSEQUENCE
|
MESURE PREVENTIVE
|
Usure
|
Abrasion
|
Dégradation des surfaces
|
Fuite de liquide
|
Sélection du joint adéquat
|
Corrosion
|
Dégradation des matériaux
|
Contamination du produit pompé
|
Installation correcte
|
Erosion
|
Dégradation des surfaces
|
Défaillance de la pompe
|
Surveillance des conditions de fonctionnement
|
Frottement excessif
|
Dégradation des surfaces
|
Dommages aux composants
|
Maintenance préventive
|
Défaut de fabrication
|
Matériau défectueux
|
Rupture du joint
|
Fuite de liquide
|
Sélection du joint adéquat
|
Usinage incorrect
|
Fuite du joint
|
Contamination du produit pompé
|
Installation correcte
|
Assemblage incorrect
|
Fuite du joint
|
Défaillance de la pompe
|
Contrôle qualité des composants
|
Mauvais montage
|
Alignement incorrect
|
Usure excessive
|
Fuite de liquide |
|
Installation correcte
|
Couple de serrage insuffisant
|
Fuite du joint
|
Défaillance de la pompe
|
Maintenance préventive
|
Dommages aux composants
|
Fuite du joint
|
Dommages aux composants
|
Contrôle qualité des composants
|
Conditions de
fonctionnement défavorables
|
Température excessive
|
Dégradation des matériaux
|
Fuite de liquide
|
Sélection du joint adéquat
|
Pression excessive
|
Déformation du joint
|
Défaillance de la pompe
|
Surveillance des conditions de fonctionnement
|
Vibration excessive
|
Usure excessive
|
Dommages aux composants
|
Contrôle des vibrations
|
ANALYSE FMD ET OPTIMISATION DE LA MAINTENANCE PREVENTIVE DE LA
POMPE CENTRIFUGE SULZER 086
3.3.1.2.5. Arbre de défaillance des fuites sur la
pompe
Le diagramme ci-dessous nous permettra de trouver les pannes
primaires que peut connaitre les fuites
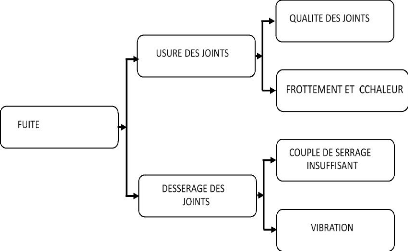
Figure 3-13 : L'arbre de défaillance des
fuites
70
71
ANALYSE FMD ET OPTIMISATION DE LA MAINTENANCE PREVENTIVE DE LA
POMPE CENTRIFUGE SULZER 086
Le tableau 3-16 nous montre la fiche de visites des fuites
Tableau 3-18: Fiche de visite en maintenance
préventive systématique des fuites
CAUSE PRINCIPALE
|
CAUSE SECONDAIRE
|
MODE DE DEFAILLANCE
|
CONSEQUENCE
|
MESURE PREVENTIVE
|
Défaillance des joints
d'étanchéité
|
Usure
|
Perte d'étanchéité
|
Fuite de liquide
|
Surveillance et remplacement des joints
|
Corrosion
|
Dégradation du joint
|
Fuite de liquide
|
Protection contre la corrosion
|
Déformation
|
Perte d'étanchéité
|
Fuite de liquide
|
Utilisation de joints de qualité
|
Mauvais montage
|
Défaut d'étanchéité
|
Fuite de liquide
|
Procédure de montage adéquate
|
Défaillance des garnitures mécaniques
|
Usure
|
Perte d'étanchéité
|
Fuite de liquide
|
Surveillance et remplacement des garnitures
|
Corrosion
|
Dégradation de la garniture
|
Fuite de liquide
|
Protection contre la corrosion
|
Fissuration
|
Perte d'étanchéité
|
Fuite de liquide
|
Utilisation de garnitures de qualité
|
Mauvais montage
|
Défaut d'étanchéité
|
Fuite de liquide
|
Procédure de montage adéquate
|
Fissures dans le corps de pompe
|
Corrosion
|
Affaiblissement du corps de pompe
|
Fuite de liquide
|
Protection contre la corrosion
|
Fatigue
|
Propagation de la fissure
|
Fuite de liquide
|
|Surveillance des vibrations et des charges
|
Défaut de fabrication
|
Défaut du matériau
|
Fuite de liquide
|
Contrôle de la qualité du corps de pompe
|
Surcharge
|
Dépassement de la capacité du corps de pompe
|
Fuite de liquide
|
Protection contre la surcharge
|
Défaillance des boulons de serrage
|
Fatigue
|
Rupture du boulon
|
Fuite de liquide
|
Surveillance et remplacement des boulons
|
Corrosion
|
Affaiblissement du boulon
|
Rupture du boulon
|
Protection contre la corrosion
|
Défaut de fabrication
|
Défaut du matériau
|
Rupture du boulon
|
Contrôle de la qualité des boulons
|
Mauvais serrage
|
Défaut d'étanchéité
|
Fuite de liquide
|
Procédure de serrage adéquate
|
72
ANALYSE FMD ET OPTIMISATION DE LA MAINTENANCE PREVENTIVE DE LA
POMPE CENTRIFUGE SULZER 086
3.3.2. Proposition d'amélioration de la
maintenance
1. Fiabilité : 33%
- Objectif : Augmenter la fiabilité en réduisant le
taux de défaillances. - Actions possibles :
· Améliorer la qualité des composants :
Utiliser des composants de meilleure qualité et plus durables.
· Renforcer les inspections et les tests : Effectuer des
inspections et des tests plus fréquents pour identifier et corriger les
problèmes potentiels avant qu'ils ne causent des défaillances.
· Mettre en place une maintenance conditionnelle :
Surveiller l'état de la pompe et effectuer des interventions de
maintenance uniquement lorsque cela est nécessaire.
· Analyser les modes de défaillance critiques et
identifier les composants les plus susceptibles de tomber en panne.
· Mettre en place une maintenance préventive
basée sur les recommandations du constructeur et l'analyse des
défaillances.
· Utiliser des composants de meilleure qualité et
plus fiables.
· Surveiller les paramètres clés de la
pompe (température, vibrations, pression, etc.) pour détecter les
signes avant-coureurs de défaillance
2. Maintenabilité : 63%
- Objectif : Augmenter la maintenabilité en
réduisant le temps et les ressources nécessaires pour
réparer la pompe.
- Actions possibles :
· Utiliser des outils et des procédures de
maintenance standardisés : Faciliter la tâche des techniciens de
maintenance.
· Former les techniciens de maintenance : Assurer que
les techniciens disposent des compétences et des connaissances
nécessaires pour réparer la pompe de manière efficace.
· Améliorer l'accessibilité des composants
pour faciliter les interventions de maintenance.
· Simplifier les procédures de maintenance et
utiliser des outils adaptés.
· Utiliser des pièces de rechange d'origine et de
qualité.
3. Disponibilité : 99%
- Objectif : Maintenir la pompe en fonctionnement le plus
longtemps possible. - Actions possibles :
· Mettre en place un plan de maintenance
préventive rigoureux : Effectuer des interventions de maintenance
régulières pour prévenir les défaillances.
· Mettre en place un système de redondance :
Installer une pompe de secours en cas de panne de la pompe principale.
· Prévoir des stocks de pièces de rechange
critiques
73
ANALYSE FMD ET OPTIMISATION DE LA MAINTENANCE PREVENTIVE DE LA
POMPE CENTRIFUGE SULZER 086
? Optimiser les interventions de maintenance pour minimiser les
temps d'arrêt.
? Consulter le manuel du constructeur pour obtenir des
recommandations spécifiques de la pompe.
? Utiliser des outils de gestion de la maintenance pour suivre
les interventions et les stocks de pièces détachées.
? Suivre et analyser les données de maintenance :
Identifier les points faibles de la pompe et adapter le plan de maintenance en
conséquence.
En conclusion, l'optimisation de la maintenance
préventive d'une pompe centrifuge nécessite une approche globale
prenant en compte la fiabilité, la maintenabilité, la
disponibilité et l'efficacité de la pompe.
3.4. Conclusion partielle
Au sein de ce chapitre, une analyse FMD concernant la pompe
centrifuge Sulzer 086 a été réalisé. L'historique
des défaillances, exposé en préambule, a facilité
la détermination des paramètres de fidélité, de
maintenabilité et de disponibilité du dudit équipement.
Ces paramètres ont, par la suite, permis le calcul du temps optimal pour
les interventions systématiques de maintenance. Afin d'identifier les
défaillances majeures engendrant des arrêts prolongés, le
diagramme de Pareto a été élaboré. Les
données issues de ce diagramme, conjointement aux paramètres FMD,
ont fondé la base de propositions visant à améliorer les
pratiques de maintenance préventive de la pompe Sulzer 086.
74
|
|