1.3 - Structure d'un verre à couches
Pour assurer de bonnes propriétés et une bonne
durabilité, il est souvent indispensable de déposer :
- une sous-couche assurant l'adhérence sur le verre.
- une couche (mais plus généralement plusieurs
couches) pour donner au verre les caractéristiques fonctionnelles
recherchées.
- optionnellement, une couche de protection chimique et
mécanique (dans le cas de verres à faible
émissivité, cette dernière couche peut être du
nitrure de silicium) [9].
1.4 - Nature de couches, procédées de
dépôt
Diverses techniques existent pour apporter de la
matière sur une surface. Nous décrirons les principales
utilisées. On peut les classer de différentes manières
(e.g.physiques ou chimiques), mais nous préférons les classer
selon la phase par laquelle le matériau transite lors du
dépôt : soit par un gaz ionisé (plasma), soit en phase
vapeur, soit en phase liquide. Le choix d'un procédé
dépend de plusieurs facteurs : le matériau à
déposer, la nature du substrat, l'application désiré.
1.4.1- Pulvérisation cathodique
Ce procédé tend à se substituer
progressivement à l'évaporation dès lors que l'on souhaite
des dépôts de grande surface. En effet pour des raisons
strictement géométriques il est évident qu'une source
d'évaporation quasi ponctuelle peut être considérée
comme un centre de symétrie vis a vis des atomes évapores. En
d'autres termes le nombre d'atomes reçus à une distance
donnée de la source sera sensiblement inversement proportionnel à
la carre de la distance. II en résulte que le dépôt
présentera une épaisseur homogène s'il est effectue sur
une surface sphérique dont le centre est constitue par la source
d'évaporation. Comme en pratique les substrats sont
généralement plans, on ne pourra les assimiler qu'au plan tangent
a la sphère et de toute évidence l'épaisseur du
dépôt ne sera pas identique en tout point. On est donne contraint
à limiter fortement la surface utile du substrat, ou a le placer
très loin de la source ce qui entraine alors d'autres difficultés
(nécessite d'enceinte plus grande donne système de pompage
beaucoup plus cher, temps opératoire plus long...) [8].
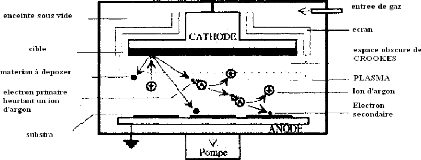
Figure 20. Principe de dépôt par
pulvérisation cathodique.
1.4.1.1- Mécanisme de la pulvérisation
On dispose a faible distance de deux plans parallèles,
1'un support de la source de matériau (cible), 1'autre du
réceptacle du dépôt. On procède au bombardement de
la source par des ions connus (argon le plus souvent) accélères
sous 1kV environ, ces ions vont arracher mécaniquement des atomes de la
source et ceux-ci vont être projetés vers le porte substrat
refroidi et s'y déposer. La source plane pouvant être de
très grande surface on peut théoriquement effectuer des
dépôts relativement homogènes sur une grande surface
[8].
Les dépôts métalliques sont aisés
à produire par pulvérisation cathodique, dans le cas de
matériaux diélectriques, et donc non conducteurs, il y a une
difficulté car les ions ne peuvent se décharger sur la cathode,
ce qui entraine la constitution d'une charge d'espace qui très vite
bloque la progression des ions vers la cathode et interrompt, de facto, le
processus de pulvérisation. On trouve une parade en interposant une
grille soumise a un potentiel module a haute fréquence (27 MHz) ce qui
augmente sensiblement la complexité et le cout du dispositif. La diode
plane représentée cidessus possède une cathode de
diamètre variant entre 10 et 30 cm tandis que la distance cathode anode
se situe entre 5 et 10 cm [8].
|