2-Les différents ateliers de la ligne :
La ligne de la production du float glass comporte les ateliers
suivants :
2-1- Atelier de composition :
Cet atelier renferme les hangars de stockage des
matières premières, l'acheminement de ces dernières se
fait par des chargeurs et des transporteurs à godets vers les silos qui
assurent l'alimentation en continu des doseurs. Le mélange ainsi
dosé est envoyé vers le malaxeur ou ce fait la première
homogénéisation en présence d'eau .Le mélange
homogénéisé est transporté vers le four à
l'aide d'un transporteur à bondes.
Afin d'éliminer les éléments
minéraux non désirables, nuisibles pour la composition, la
matière première subit après le malaxage un contrôle
magnétique pour séparer les matériaux ferreux et à
l'aide d'un dispositif spécial pour les éléments non
ferreux.
La figure suivant représente le schéma
simplifié de l'atelier de composition :

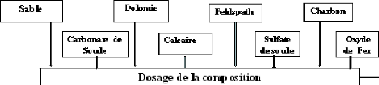
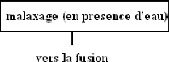
Figure 114.schématisation de l'atelier d'alimentation
Le mélange de matières premières est
pesé électroniquement avec une précision de 0,1%, puis
mélangé et humidifié. Il forme un mélange
vitrifiable auquel on ajoute du calcin avant de le charger directement dans le
four de fusion. L'ajout de calcin permet d'abaisser la température de
fusion du mélange.
La consommation journalière en tonne par jour des
matières premières au niveau de MFG est comme suite :
Tableau 3. Consommation journalière en matières
premières à MFG
MP
|
sable
|
Carbonates de soude
|
dolomie
|
calcaire
|
feldspath
|
Sulfates de soude
|
charbon
|
Oxyde de fer
|
calcin
|
Tonne/j
|
310
|
120
|
80
|
30
|
25
|
6
|
0.4
|
0.25
|
150
|
2-2- Atelier de fusion :
Comporte un four à 6 brûleurs transversaux
à chambre de régénération, long de 62.8 m et large
de 30m avec une quantité de verre en fusion de 2050 tonnes, la
température du four est de l'ordre de 1550°c .la consommation
énergétique est de 120000 m3 /j de gaz naturel.
L'alimentation des fours en mélange vitrifiable est
assurée par4 enfourneuses qui sont programmées de façon
à ce que le niveau du verre fondu soit toujours stable.
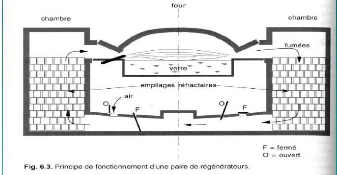
Figure15.Coupe latérale d'un four à
régénérateurs
Le four est constitué de 3 zones essentielles qui sont les
suivantes :
· l'élaboration :
Le mélange doit être transformé en un
liquide dépourvu d'inclusions cristallines. Au alentour de 1000°C,
les premières réactions de fusion et de décomposition
commencent à se produire mais il faut monter entre 1200 et 1500°C
pour s'assurer que les matières moins fusibles puissent réagir
avec les matières en fusion et être digérées par la
phase liquide.
· l'affinage :
Dans le mélange vitrifiable en fusion, il est
nécessaire d'expulser les bulles de gaz provenant des différentes
réactions chimiques mais également de l'air situé entre
les matières premières et de l'évaporation de l'eau.
Cette étape nécessite la présence
d'affinants dans le mélange de départ (voir page 2), une
élévation de la température (pour diminuer la
viscosité du verre fondu) et parfois une agitation mécanique ou
l'insufflation d'air.
· le conditionnement :
Après la fusion et l'affinage, le verre doit
être homogénéisé chimiquement et thermiquement. Les
variations de composition causent des défauts permanents lors de la
production tandis que les variations de températures occasionnent des
problèmes lors de l'étape de formage du verre.
Il existe plusieurs catégories de fours et il se peut
qu'une verrerie regroupe quelques-uns de ces systèmes de fusion
affectés à la production de différents produits
verriers.
Pour obtenir des températures suffisamment
élevées dans les fours, il est impératif de
préchauffer l'air de combustion. Pour réaliser des
économies d'énergie, les gaz chauds issus des fours passent par
des systèmes de régénération ou de
récupération thermique.
· Système de
régénération :
Les gaz brûlés passent dans une chambre
(régénérateur) dotée d'un garnissage
réfractaire absorbant la chaleur. Il y a deux
régénérateurs par four. Le chauffage des chambres n'a lieu
que d'un seul côté à la fois. Toutes les 20 minutes, la
combustion est inversée et l'air (comburant) est passé à
travers la chambre précédemment chauffée par les gaz
brûlés. Ce système permet d'obtenir des températures
de préchauffage de 1400°C.
· Système de récupération
:
Des échangeurs thermiques
(récupérateurs) assurent le préchauffage continu de l'air
(comburant) par la circulation des gaz brûlés. Les
températures de préchauffage atteintes sont limitées aux
alentours de 800°C. Ce système est principalement utilisé
lorsque la taille de l'exploitation est trop faible pour pouvoir rendre un
système de régénération économiquement
rentable. Les consommations énergétiques dépendent de la
capacité de production des fours et de la qualité du verre
à produire.
L'énergie nécessaire pour la fusion d'un
kilogramme de verre varie entre 3700 et 6000 kJ (pour des températures
de fusion qui varient entre 1200°C et 1500°C).
|