REPUBLIQUE ALGERIENNE DEMOCRATIQUE ET
POPULAIRE
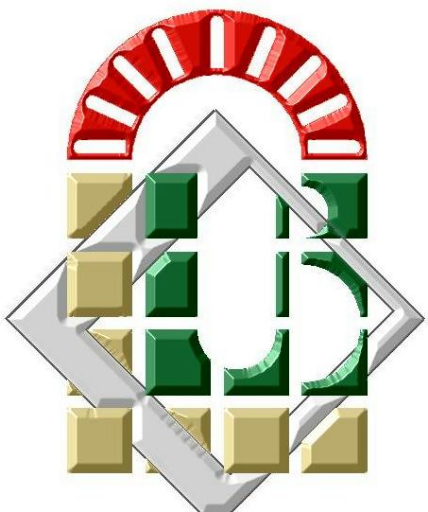


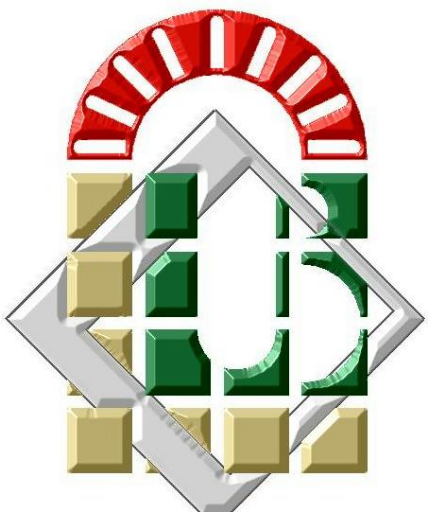


MINISTERE DE L'ENSEIGNEMENT SUPERIEUR
ET DE LA RECHERCHE SCIENTIFIQUE
UNIVERSITE MOHAMED KHIDER -BISKRA
FACULTE DES SCIENCES ET DE LA TECHNOLOGIE
DEPARTEMENT DE GENIE MECANIQUE
PROJET DE FIN D'ETUDE
Pour l'obtention du diplôme
D'Ingénieur d'Etat en Génie
Mécanique
Option:
Construction mécanique
THEME
![]()
Etudiants :
Encadreur :
BAHA Bouziane Mr.
BENMACHICHE Messaoud
NACERI Mohamed
Promotion: Juin 2010REPUBLIQUE ALGERIENNE DEMOCRATIQUE
ET POPULAIRE
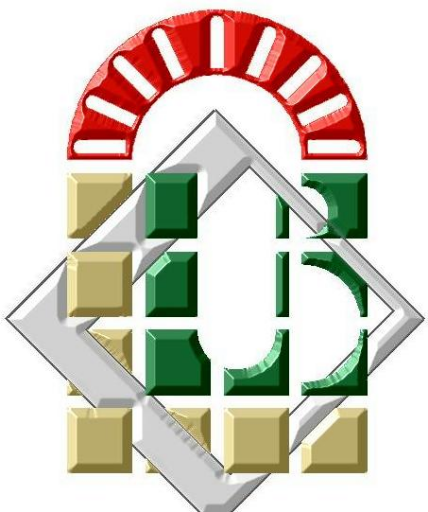


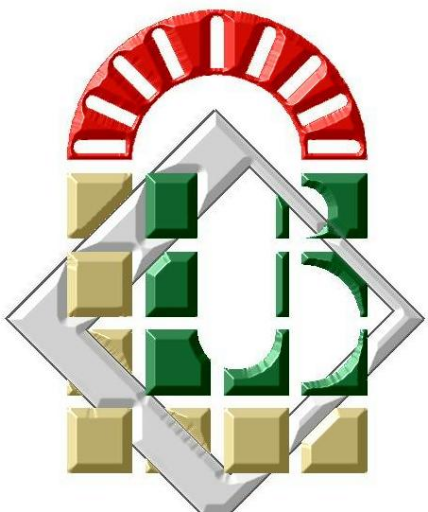


MINISTERE DE L'ENSEIGNEMENT SUPERIEUR
ET DE LA RECHERCHE SCIENTIFIQUE
UNIVERSITE MOHAMED KHIDER -BISKRA
FACULTE DES SCIENCES ET DE LA TECHNOLOGIE
DEPARTEMENT DE GENIE MECANIQUE
PROJET DE FIN D'ETUDE
Pour l'obtention du diplôme
D'Ingénieur d'Etat en Génie
Mécanique
Option:
Construction mécanique
THEME
![]()
Etudiants :
Encadreur :
BAHA Bouziane Mr.
BENMACHICHE Messaoud
NACERI Mohamed
Promotion: Juin 2010
ÓõæÑóÉõ
ÓóÈóó :
ÇáÂíóÇÊ
C'est à :
mes chers parents,
ma fiancée L.Y,
ma belle-mère,
tous mes frères et soeurs,
mes neveux et en particulier Yasmine,
mes amis LEGOUIRA Ridha & TELLI Khaled,
mes collègues de promotion de génie
mécanique,
tout le personnel de département,
à mes amis de G59 sans exception,
tous les Administrateurs, Modérateurs, et Membres
du forum de l'Étudiant,
Que je dédie ce modeste travail
NACERI Mohamed
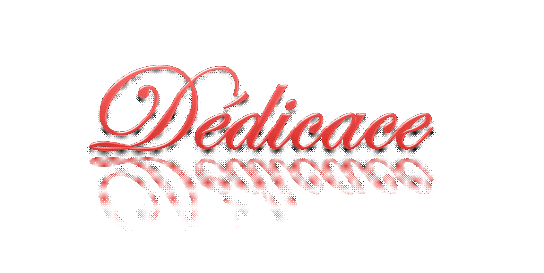
À ceux qui méritent le plus, ceux qui n'ont
ménagé aucun effort pour que je puisse arriver à mes
buts, ceux qui ont veillé tout au long de ces années pour me
voir réussir, ceux grâce à qui je suis là
aujourd'hui
A mes très chers parents,
Que je dédie ce modeste travail
Je le dédie également
A mes soeurs, mon frère et toute ma
famille.
À mes amies : Hassan, Tahar, Mohamed, Samir,
Amin, Yacine, Bilal, Nabil, Abd Essamed,
À ma très chère fidèle intime,
youma « yakoub », et sa famille,
A mon ami Mohamed Naceri.
BAHA Bouziane.
REMERCIEMENTS
C'est un plaisir de remercier notre encadreur Mr. BENMACHICHE
Messaoud pour le choix de ce sujet, pour ses précieux conseils et pour
toute l'aide qu'il nous a apportée tout au long de ce travail.
Nos remerciements anticipés :
Aux membres du jury qui ont acceptés de bien vouloir
juger ce travail.
Toute notre sympathie pour Pr. A.CHALA pour ses
encouragements et ses conseils.
Notre gratitude va à tous les enseignants du
département de génie mécanique de Biskra et en
particulier :
Mr Dj. Mohamedi, Mr M. Hecini, Mr A.H Moummi., Mr M. Hadid,
Mr N.Moummi, Mr N. Deries, Mr K. Meftah, Mr Belahcene, Mr C.
Derfouf.
Nous remercions également tout le personnel du
département de génie mécanique.
Que tous ceux qui ont participé, de près ou de
loin, à l'élaboration de ce travail, trouvent ici l'expression de
nos vifs remerciements.
NACERI & BAHA
TABLE DES MATIERES
Introduction
|
01
|
GENERALITES SUR LES BETONNIERES DE CHANTIER
|
I. Généralités
|
03
|
I.1. Bétonnière portée sur camion (camion
malaxeur)
|
03
|
I.2. Bétonnières à action continue
|
04
|
I.3. Bétonnières à tambour basculant
|
05
|
I.3.1. Principe de fonctionnement
|
06
|
I.3.2. Vue de la bétonnière
étudiée
|
07
|
CALCUL D'UNE BETONNIERE A TAMBOUR BASCULANT
|
Partie 1 : Calcul de la chaîne
|
II.1.1. Choix de la chaîne
|
08
|
II.1.2. Détermination du Nombre de dents du pignon et
de la roue
|
09
|
II.1.3. Calcul de la puissance nette
|
09
|
II.1.4. Calcul de la longueur de la chaîne
|
10
|
II.1.5. Détermination de l'entraxe
|
11
|
II.1.6 Vérification de l'angle d'enroulement
|
11
|
II.1.7 efforts appliques sur une chaîne
|
12
|
Partie 2 : Calcul et dimensionnement des éléments
du réducteur
|
II.2.1 Calcul de denture
|
14
|
II.2.2 Calcul des rapports de transmission i
|
14
|
II.2.3 Calcul des éléments du réducteur
à engrenage conique
|
14
|
II.2.4 Tableau des valeurs calculées
|
15
|
II.2.5. Vérification des engrenages, d'après la
méthode de G. Henriot
|
16
|
1°/ calcul à la rupture des engrenages
|
16
|
2°/ calcul à la pression superficielle
|
21
|
Partie 3 : Calcul et dimensionnement de l'arbre
|
II.3.1. Au plan vertical
|
25
|
1°/ Calcul des réactions
|
26
|
2°/ Calcul des moments
|
26
|
3°/ Diagramme des moments
|
27
|
II.3.2. Au plan horizontal
|
28
|
1°/ Calcul des réactions
|
28
|
2°/ Calcul des moments
|
28
|
3°/ Diagramme des moments
|
30
|
II.3.3. Calcul du moment de flexion max
|
31
|
II.3.4. Calcul du moment de torsion
|
31
|
II.3.5. Calcul du moment idéal
|
31
|
II.3.6. Choix du diamètre de l'arbre
|
32
|
II.3.7. Choix et calcul de vérification des
clavettes
|
32
|
Partie 4 : Calcul des roulements
|
II.4.1. Cas isostatique
|
34
|
II.4.2. Palier A
|
35
|
II.4.3. Palier B
|
35
|
Partie 5 : Calcul du diamètre de l'arbre encastré
et les roulements
|
II.5.1. Calcul du diamètre de l'arbre encastré
|
36
|
II.5.2. Détermination des roulements de grand
diamètre
|
37
|
II.5.3. vérification de l'arbre encastré
|
38
|
Partie 6 : Calcul et dimensionnement des éléments
du réducteur
|
II.6.1. Schéma cinématique du réducteur de
vitesse
|
40
|
II.6.2. Calcul de denture
|
40
|
II.6.3. Calcul des rapports de transmission i
|
40
|
II.6.4. Recherche et calcul des paramètres du premier
étage
|
41
|
II.6.5. Recherche et calcul des paramètres du
deuxième étage
|
43
|
CAO DES ELEMENTS DE LA BETONNIERE
|
III.1. La conception assistée par ordinateur
(CAO)
|
45
|
III.2. Aperçu sur SolidWorks
|
45
|
III.2.1. CosmosWorks
|
45
|
III.2.2. CosmosMotion
|
46
|
III.2.3. CosmosFloworks
|
46
|
III.2.4. CamWorks
|
46
|
III.3. CAO des éléments de la
bétonnière
|
47
|
III.3.1. Réalisation d'engrenage
|
47
|
III.3.2. Conception de Réducteur manuel
|
48
|
III.3.3. Conception du châssis
|
48
|
III.3.4. Conception de La cuve
|
49
|
III.3.5. Le moteur de la bétonnière
|
50
|
III.4. Utilisation de CosmosWorks
|
51
|
III.5. Affichage des résultats de l'analyse
|
52
|
III.6. Diagrammes de tracés de résultats
sondés
|
55
|
FAO DE L'ARBRE DU REDUCTEUR
|
IV.1. La fabrication assisté par ordinateur ( FAO )
|
57
|
IV.2. Etape mise en oeuvre du logiciel
|
57
|
IV.2.1. Choisir le mode de travail
|
57
|
IV.2.2. Définir la machine et directeur de CN
|
58
|
IV.2.3. Définir le brut
|
59
|
IV.2.4. Définir les origines
|
60
|
IV.2.5. Définir les formes usinables « entités
d'usinage »
|
61
|
IV.2.6. Définir, générer les
opérations.
|
62
|
IV.2.7. Choix des outils et des paramètres de coupe
|
63
|
IV.2.8. Générer le parcours d'outil «
Simulation »
|
65
|
IV.2.9. Générer le programme ISO
|
66
|
Conclusion générale
|
68
|
Annexes
|
|
Références bibliographiques
|
|
NOMENCLATURE
: Entraxe en mm.
: Entraxe en nombre de maillons.
: Largeur de
denture ( en mm )
: Coefficient de résistance de la dent
: Facteur de rapport
: Diamètre primitif du pignon, en mm.
: Diamètre primitif du roue, en mm.
: Module d'élasticité longitudinal
:
Action de contact sur la denture
: Tension utile due a la transmission de la puissance.
: Tension due à la force centrifuge.
: Effort normal unitaire
: Facteur de sécurité.
: La charge minimale de rupture déterminer pour chaque
chaîne.
: Facteur tenant compte du nombre de rangée de la
chaîne.
:
Coefficient de largeur de denture.
: Facteur de
service.
: Facteur de
durée.
: Facteur de durée
: Facteur de
portée.
: Facteur de
vitesse.
: Facteur de service.
: Longueur de la chaîne, en mm.
: Longueur de la chaîne, en nombre de maillons.
:
Facteur de conicité
: module
: Nombre de tours du pignon, en tr/min.
: Nombre d e tours du roue, en tr/min.
: Pas primitif de la chaîne, du pignon et de la roue, en mm.
: Puissance de moteur.
: Puissance effective.
: Puissance nette.
: Puissance nominale.
: Vitesse de la chaîne, en m/s.
: Facteur de
forme.
: Facteur
d'inclinaison.
: Facteur de
conduite.
: Nombre de dents du pignon.
: Nombre de dents de la roue.
: Facteur géométrique
: Facteur matériau
: Facteur de longueur de contact
: Angle de pression.
: Valeur limite de base de la pression de Hertz.
: contrainte
limite à la rupture ( sur le pignon, ou sur la roue )
: Facteur de capacité.
: Angle d'enroulement
et : les rayons de courbure en mm des flancs du profil
: Masse linéique, en kg/m.
: Rapport de conduite
: Rapport de recouvrement
INTRODUCTION
L'utilisation de l'ordinateur dans les procédés
de fabrication, de conception, de simulation et d'analyse en mécanique,
ne cesse de se développer et de se généraliser
d'année en année.
La fabrication d'engins de chantier telles que malaxeurs de
béton, grue, pompe à béton... dans les unités
nationales a été à l'origine du choix de notre
sujet : conception d'une bétonnière
L'intérêt de notre travail et non seulement une
étude technique d'une machine, souvent considéré comme une
construction grossière mais aussi l'introduction, pour la
première fois au niveau du département de génie
mécanique de Biskra, de la conception, l'analyse et la fabrication
assistée par ordinateur d'un mécanisme.
Le logiciel utilisé pour la conception
est SOLIDWorks. Ce logiciel de CAO, qui a fait ses preuves dans le domaine, a
été utilisé dans de précédents projets. Nous
ne donnerons pas de détails quant à son principe et ses
fonctions.
L'analyse de la construction est
réalisé par COSMOSWorks : un module complémentaire de
la famille SOLIDWorks. C'est un logiciel puissant et simple à
utiliser.
En effet, il permet non seulement l'analyse statique
(utilisée dans ce mémoire) mais aussi d'autres fonctions telles
que : étude thermique, étude fréquentielle,...etc.
La fabrication est exécutée sur
CAMWorks : c'est un complément qui permet la réalisation et
la transmission des programmes de fabrication aux machines à commande
numérique (MOCN).
Notre mémoire est organisé comme suit :
- - Le premier chapitre contient des
généralités sur les bétonnières de
chantier.
- - Le deuxième chapitre est consacré au calcul,
par la méthode classique, des éléments de la
bétonnière.
- - Les résultats des calculs (dimensions des
pièces) seront exploités au troisième chapitre pour la
conception et le dessin des pièces mécaniques et de l'assemblage.
On a limité l'analyse par COSMOSWorks à l'arbre du
réducteur à denture conique pour lequel nous avons
déterminé les contraintes, les déformations et les
déplacements en toute section de cette pièce.
- - L'application de CAMWorks fait l'objet de chapitre IV,
dans lequel nous avons déterminé le programme ISO pour l'usinage
sur machine à commande numérique (MOCN) de l'arbre
d'entrée du réducteur « manuel ».
![]()
![]()
GENERALITES SUR LES BETONNIERES DE CHANTIER
I. Généralités
Les bétonnières sont des appareils qui assurent
le mélange des constituants par simple rotation de la cuve suivant un
axe qui peut être horizontal ou légèrement incliné.
Des palettes solidaires de la cuve assurent l'entraînement des
matériaux qui retombent par gravité. Ce mouvement de brassage
assure le mélange des constituants.
I.1. Bétonnière portée sur camion
(camion malaxeur)
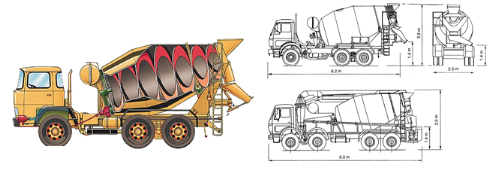
Fig.I.1
Ces appareils assurent une homogénéité du
mélange supérieure à celle obtenue avec les
bétonnières, grâce au déplacement relatif des
composants à l'intérieur du mélange. Ce déplacement
est provoqué par des trains de palettes ou de planétaires dont
l'axe est excentré par rapport à celui de la cuve, qui est
elle-même fixe ou tournante.
La plupart des malaxeurs sont à axes verticaux. Le
béton subit un puissant effet de brassage à la fois dans le sens
vertical et dans le sens horizontal. Ce type de matériel est le mieux
adapté à l'obtention de bétons homogènes.
I.2. Bétonnières à action continue
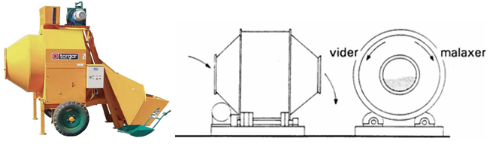
Fig.I.2
Le malaxage s'effectue dans une cuve cylindrique
installée horizontalement, où les palettes tournent sur un arbre
horizontal. Le remplissage est continu à une extrémité du
cylindre et le mélange sort de l'autre côté.
La masse de béton est de composition constante
réglée au préalable. Le rendement est important car il n'y
a pas de pertes de temps.
I.3. Bétonnières à tambour
basculant
Tambour (cuve)
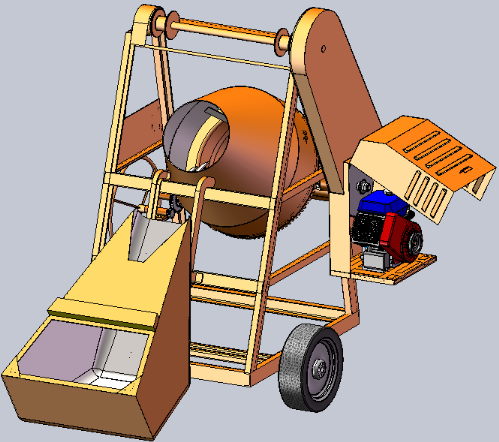 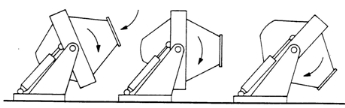
Fig.I.3
Le tambour rotatif mélangeur est muni de palettes pour
le malaxage. Si ces palettes sont fixées à la paroi du tambour
(axe oblique ou horizontal) la masse du béton est entraînée
vers le haut et se mélange en retombant en chute libre. Si les palettes
ou bras agitateurs tournent en sens contraire du tambour (axe oblique ou
vertical) la masse est, pour ainsi dire, malaxée et est alors encore
mieux mélangée.
L'entraînement se fait au moyen d'un moteur à
combustion interne ou d'un moteur électrique.
I.3.1. Principe de fonctionnement
La machine constituée d'une cuve rotative et d'un
moteur qui sert à malaxer les différentes composantes du mortier:
ciment, eau, sable. La bétonnière peut être de petite
taille et facilement transportable. Elle sera munie de roues et servira
à fabriquer du mortier pour des petites surfaces.
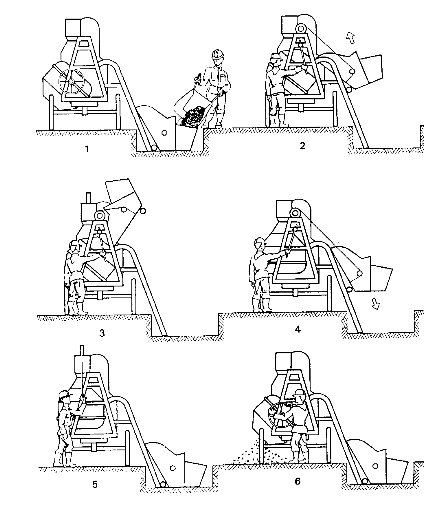
Fig.I.4
1. Opération de charge des composant du béton
(ciment, gravier)
2. Action de la transmission pour la levée de godet.
3. Déchargement dans la cuve.
4. Retour de godet, position vertical de la cuve.
5. Addition de l'eau (arrosage)
6. Décharge du béton mélangé et
prêt à l'emploi
I.3.2. Vue de la bétonnière
étudiée
Réducteur manuel
Moteur
Réducteur
par chaîne
Réducteur
a denture conique
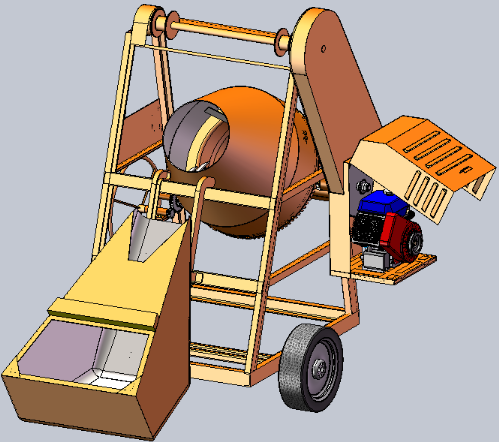
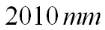
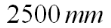




Fig.I.5
![]()
![]()
CALCUL DES ELEMENTS D'UNE BETONNIERE
Partie 1 : Calcul de la chaîne
Données :
Puissance de moteur: 7,5 KW;
Nombre de tours 1500 tr/min ;
Rapport de transmission (chaîne) ;
L'entraxe (Plateau) a = 350 mm;
II.1.1. Choix de la chaîne
Moteur
Chaîne
Arbre (A)
Roue N2
Pignon N1
Chaîne
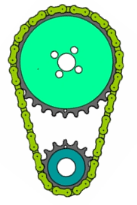
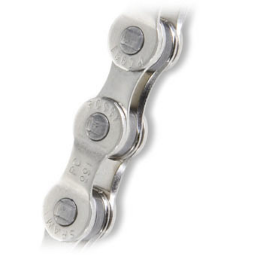
Fig.II.1
Calculons d'abord la puissance effective d'une transmission
par chaîne. [ 1 ]
On sait que :

: Puissance de moteur.
: Puissance effective.
: Facteur de service.
On prend : (voir Tab.1
Annexe)
On obtient :

En consultant l'abaque ( Fig.1 Annexe) on constat qu'on a le
choix entre :
- Une chaîne simple 50-1 (Tab.2 Annexe) pas = 0,625 po
pas =
15,875mm
- Une chaîne double 40-2 ( Tab.3 Annexe) pas = 0,5 po
pas =
12,7mm
- Une chaîne triple 40-3 pas = 0,5 po pas = 12,7
mm
)
II.1.2. Détermination du Nombre de dents du pignon
et de la roue
Calculons d'abord le nombre de tours du la roue N2
Soit :


Puisque ce rapport
est satisfait pour prend Z1 = 21 et Z2 = 105 dents
II.1.3. Calcul de la puissance nette
On sait que :

: Puissance nette.
: Facteur tenant compte du nombre de rangée de la
chaîne.
: Puissance nominale.
Pour Z1 = 21 dents, on obtient les valeur de
présentées au tableau ci-dessous:
Type de chaîne
|
K2(Tab.4 Annexe)
|
Pr(CV)
|
Pr'(CV)
|
Pr'(KW)
|
Chaîne 40-3
|
2,5
|
9.90
|
24,75
|
18,456
|
Chaîne 40-2
|
1,7
|
9,90
|
16,83
|
12,550
|
Chaîne 50-1
|
1
|
17,85
|
17,85
|
13,310
|
On constate que les deux chaînes 40-2 et 50-1 satisfont
à la condition
La chaîne 40-2 sera mieux exploitée ( la valeur
de
étant plus proche de la valeur désire de ), c'est
elle qu'il faudra choisir (même si, fort probablement une étude
économique détaillée ferait opter pour la chaîne
50-1)
II.1.4. Calcul de la longueur de la chaîne
La longueur de la chaîne en nombre de maillons est
donnée par l'équation:
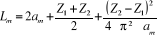
: Longueur
de la chaîne, en nombre de maillons.
: Entraxe en nombre de maillons.
Et on a:
=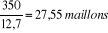
: Entraxe.
: Pas primitif de la chaîne, du pignon et de la roue.
Donc:

On prend:
et la longueur de la chaîne est

: Pas primitif de la chaîne.

II.1.5. Détermination de l'entraxe
A l'aide de l'équation suivant on calcule la valeur
modifiée de soit :



On prend :

II.1.6 Vérification de l'angle d'enroulement
Les équations suivantes permettent de calculer les
diamètres primitifs de la roue et du pignon

Donc: 

On sait que :
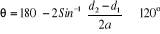

II.1.7 efforts appliques sur une chaîne
Toute fois il faut examiner la possibilité de bris de
la chaîne choisie.
On a :

: Facteur de sécurité.
: La charge minimale de rupture déterminer pour chaque
chaîne.
: Tension utile due a la transmission de la puissance.
: Tension due à la force centrifuge.
Et que :

Pour les
chaîne a rouleaux.
: Pas primitif de la chaîne.
et :
: Vitesse de la chaîne, en m/s.
Ou : 

Donc: 
Et : 

(Voir
Tab.5 Annexe)
: Masse
linéique.
Donc : 
Finalement pour éviter la rupture de la chaîne,
il faut vérifier que l'inégalité suivant est satisfaite
:

Il est donc clair que la chaîne est
sécurisée.
Partie 2 : Calcul des éléments du
réducteur conique
Données
La puissance de moteur : 
La vitesse d'entrée : 
La vitesse de sortie : 

La durée de fonctionnement : 
Chocs modérés travaillant : 
Couronne en fonte grise E = 90000 N/mm2
Pignon en acier E = 200000 N/mm2
II.2.1 Calcul de denture
La denture choisie pour la conception du réducteur et
sur laquelle va se faire tout le calcul est la denture droite.
II.2.2 Calcul des rapports de transmission 
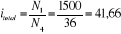
On a

Pour la chaîne 
Pour les engrenages conique 
II.2.3 Calcul des éléments du
réducteur à engrenage conique
Ø Rapport de transmission
 
Ø Angle de pression :

Ø Le module m [2]

: Coefficient de résistance de la dent

(Voir Tab.6 Annexe)
( proposé )
II.2.4 Tableau des valeurs calculées
|
|
Fig.II.2
|
Désignation
|
Symbole
|
Formule
|
Pignon
|
Roue
|
Module
|
m
|
détermine par RDM
|
10
|
Nombre de dents (dent)
|
Z
|
Rapport de vitesse
|
12 dents
|
100
|
Angle primitif ( ° )
|
ä
|
|
6,84°
|
83,16°
|
Diamètre primitif (mm)
|
d
|
|
120
|
1000
|
Largeur de denture (mm)
|
b
|
|
80
|
Diamètre de tête (mm)
|
da
|
|
139,85
|
1002,38
|
Diamètre de pied (mm)
|
df
|
|
95,17
|
997,02
|
Saillie (mm)
|
ha
|
|
10
|
Creux (mm)
|
hf
|
|
12,5
|
Hauteur de la dent
|
h
|
|
22,5
|
Angle de tête
|
äa
|
|
7,97°
|
84,29°
|
Angle de pied
|
äf
|
|
5,42°
|
81,74°
|
Angle de saille
|
èa
|
|
1,13°
|
Angle de creux
|
èf
|
|
1,42°
|
Longueur
|
L
|
|
503,58
|
II.2.5. Vérification des engrenages, d'après
la méthode de G. Henriot [3]
1°/ calcul à la rupture des
engrenages
- Calcul du pignon
Effort tangentiel admissible au
primitif de fonctionnement sur le pignon, ou sur la roue (en N) :

:
contrainte limite à la rupture ( sur le pignon, ou sur la roue )
: Largeur
de denture (en mm)
: module
: Facteur
de vitesse.
: Facteur
de durée.
: Facteur
de portée.
: Facteur
de service.
: Facteur
de conduite.
: Facteur
de forme.
: Facteur
d'inclinaison.
:
Facteur de conicité
Ø Calcul à la pression superficielle
La limite de la pression superficielle
est donnée par la formule de Hertz,

* 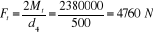
* 
F : action de contact sur la denture
* 
et : les
rayons de courbure en mm des flancs du profil


Donc :

*


Ø Calcul du facteur de vitesse

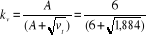

A = 6 (voir Tab.7 Annexe)
Ø Facteur de durée

* 
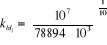

Ø Facteur de portée
A partir le (Tab.8 Annexe) de facteur de portée on
à prendre
Ø Facteur de service
A partir le (Tab.9 Annexe) de facteur de service on
prend
Ø Facteur de conduite 
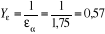
[Pour
] (voir Fig.2 Annexe)
Ø Facteur de forme 
[Pour ; ] par
extrapolation (voir Fig.3 Annexe)

Ø Facteur d'inclinaison
Engrenage conique 


Ø Facteur de conicité
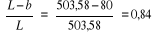
Résumé
|
|
|
|
|
|
|
|
|
276,5
|
0,81
|
0,81
|
0,9
|
0,57
|
0,57
|
3,5
|
1
|
0,84
|


- Calcul de la couronne
Effort tangentiel admissible au
primitif de fonctionnement sur le pignon, ou sur la roue (en N) :

Ø Facteur de durée

Ø Facteur de forme
[Pour ; ] (voir
Fig.3 Annexe)

Pour les autres facteurs, ils sont identiques aux valeurs
calculées précédemment pour le pignon.
Résumé
|
|
|
|
|
|
|
|
|
276,5
|
0,81
|
1
|
0,9
|
0,57
|
0,57
|
2,2
|
1
|
0,84
|


2°/ calcul à la pression
superficielle
- Calcul du pignon
Effort tangentiel admissible au
primitif de fonctionnement sur le pignon, ou sur la roue (en N) :

: Valeur
limite de base de la pression de Hertz.
: Diamètre du pignon.
: Facteur de rapport.
: Facteur de durée
: Facteur matériau.
: Facteur de longueur de
contact.
: Facteur
géométrique.
: Facteur de capacité de charge.
Ø Valeur limite de base de la pression de
Hertz
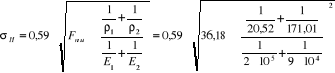

* 
: Effort normal unitaire
Ø Facteur de rapport 
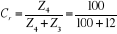

Ø Facteur de durée
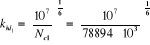

Ø Facteur matériau 


Ø Facteur de longueur de
contact 
Pour la denture droite
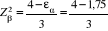

Ø Facteur
géométrique 


Ø Facteur de capacité de charge

 
Résumé
|
|
|
|
|
|
|
|
|
|
|
206,55
|
0,89
|
0,81
|
0,7
|
0,9
|
0,57
|
65,915
|
0,86
|
1,76
|
1
|
0,84
|


- Calcul de la couronne
Effort tangentiel admissible au
primitif de fonctionnement sur la roue (en N) :

Ø Facteur de durée 
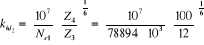

Pour les autres facteurs, ils sont identiques aux valeurs
calculées précédemment pour le pignon.
Résumé
|
|
|
|
|
|
|
|
|
|
|
206,55
|
0,89
|
0,81
|
1
|
0,9
|
0,57
|
65,915
|
0,86
|
1,76
|
1
|
0,84
|


Partie 3 : Calcul et dimensionnement de l'arbre (A)
A
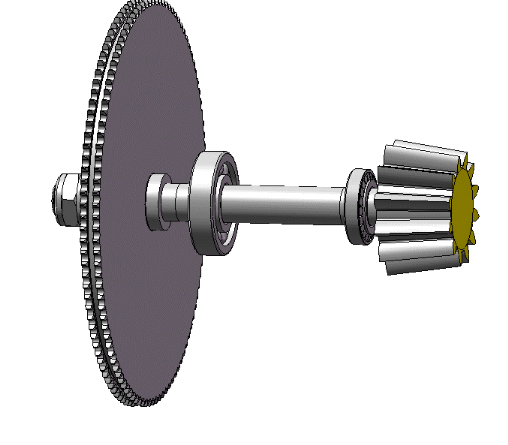
Fig.II.3
T2V T1V
FR
RAv
RBv
a b c
d
On a :
;
;
; 
;
;
II.3.1. Au plan vertical
; ; 
T2V T1V
FR
RAv
RBv
a b c
d
1°/ Calcul des réactions






2°/ Calcul des moments
Pour : 0 = x = 0,05
T2v
x

Pour : 0,05 = x = 0,1
T2v T1v
x
a

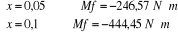
Pour : 0,1 = x = 0,4
T2v T1v
RAV
x
a b

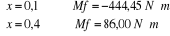
Pour : 0,4 = x = 0,45

T2v T1v
RAV RBV
x
a b c
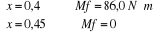

3°/ Diagramme des moments [4]
T2V T1V
FR
RAV
RBV
a b c
d
_
+
86
246,57
444,45
0
II.3.2. Au plan horizontal
T2H T1H
Ft
RAH
RBH
a b c
d
; ; 
1°/ Calcul des réactions








2°/ Calcul des moments
Pour : 0 = x = 0,05

T2H
x
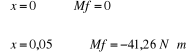
Pour : 0,05 = x = 0,1
T2H T1H
x
a

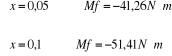
Pour : 0,1 = x = 0,4
T2H T1H
RAH
x
a b

Pour : 0,4 = x = 0,45

T2H T1H
RAH RBH
x
a b c
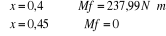
3°/ Diagramme des moments [4]
T2H T1H
Ft
RAH
RBH
a b c
d
+
_
237,99
41,261
54,41
0
II.3.3. Calcul du moment de flexion max [5]


II.3.4. Calcul du moment de torsion [5]
Pour : 0 = x = 0,05

Pour : 0,05 = x = 0,1


II.3.5. Calcul du moment idéal [5]



II.3.6. Choix du diamètre de l'arbre
Nous choisissons comme matériau de
l'arbre:l'acier CC45 (voir Tab.10 Annexe)
Donc :
et on prend comme coefficient de sécurité s = 2
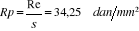
On a : 
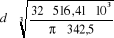
On prend d = 40 mm

II.3.7. Choix et calcul de vérification des
Clavettes [6]
Pour l'assemblage des arbres avec les moyeux des roues
dentées des poulies,...etc, on utilise généralement des
clavettes.
Les dimension principales des clavetage son
normalisées.
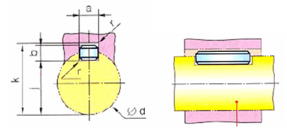
Fig.II.4
1°/ Vérification de la
clavette 1
D'après le Tab.11 on choisit :
; ; 

Ø Vérification a la
compression


Ø Vérification au
cisaillement


La clavette vérifie les deux conditions.
2°/ Vérification de la 2eme
clavette
; ; 

Ø Vérification a la
compression


Ø Vérification au
cisaillement


La clavette vérifie les deux conditions
Partie 4 : Calcul des roulements [7]
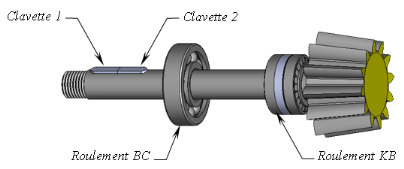
Fig.II.5
II.4.1. Cas isostatique
Ø Calcul des réactions


Ø Durée de fonctionnement en
heures

On sait que la capacité est donnée par :
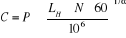
Pour les
roulements a billes.
Pour les
roulement a rouleaux.
Pour un roulement soumis à une charge quelconque P est
donnée par la relation suivante :

Pour
bague intérieur tournante par rapport à la bague
extérieur.
II.4.2. Palier A
Pour un force axiale seul :
D'après [7] et 
Donc :
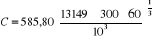

II.4.3. Palier B
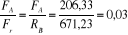
Cette valeur étant inférieur à , la charge
axiale peut être négligé.
D'après [7] et 
Donc : 
Et 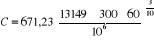

II.4.4. Choix des roulements
D'après les abaques donnant les caractéristiques
des roulements a moyen diamètre on choisit : roulement a bille pour
le palier A (BC), et roulement a rouleaux (KB) pour le palier B
LH
|
Palier
|
C°
daN
|
C
daN
|
Dimensions
|
Désignation
|
N max
Tr/min
|
D
|
B
|
r
|
13149 heures
|
A
|
3650
|
4900
|
110
|
27
|
3
|
40 BC 04
|
6000
|
B
|
11600
|
14300
|
80
|
19 ,75
|
2
|
40 KB 02
|
4000
|
Partie 5 : Calcul du diamètre de l'arbre
encastré et les roulements
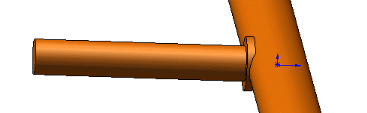
Fig.II.6
Données
La longueur de l'arbre encastré est 390 mm
La flèche déterminée est de 2 mm /
mètre de longueur
La flèche déterminée est
II.6.1. Calcul du diamètre de l'arbre
encastré
Avec

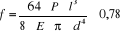
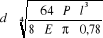
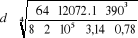

On prend:
II.6.2. Détermination des roulements de grand
diamètre
Les manuels disponibles ne permettent pas de choisir un
roulement à grande dimension.
Mais dans SolidWorks, un module de calcul de roulement permet
de dimensionner tout type de roulement quelque soit ses dimensions.
Nous utiliserons alors cette solution pour dimensionner nos
roulements.
On a choisi la qualité (la marque) SKF et le
modèle du roulement (Butée) à diamètre
intérieur
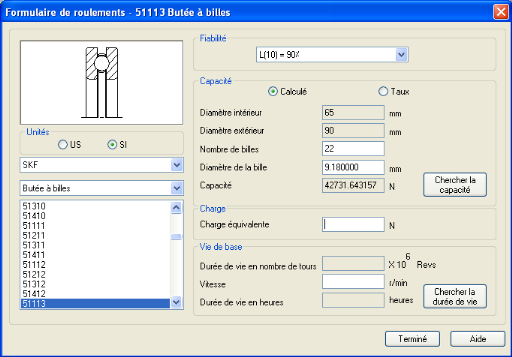
Fig.a
Remplir les données (la charge équivalente et la
vitesse de rotation) dans les cases vides.
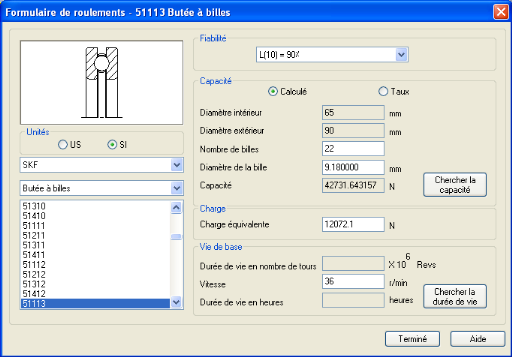
Fig.b
Cliquer sur le bouton Chercher la durée de vie...
pour calculer la durée de vie en nombre de tours ou en heures
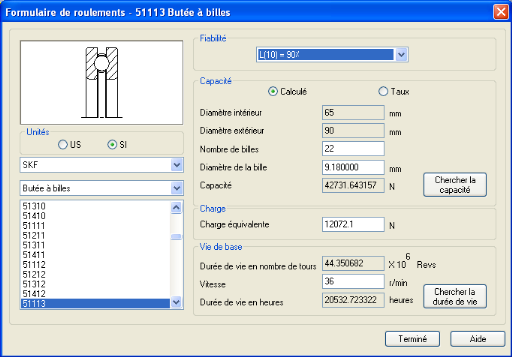
Fig.c
Résultat
Durée de vie en nombre de tours = 
Durée de vie en heures = 
II.6.3. vérification de l'arbre encastré
Dans la barre de menu sélectionner Toolbox puis
cliquer sur Formulaire de flexion... 
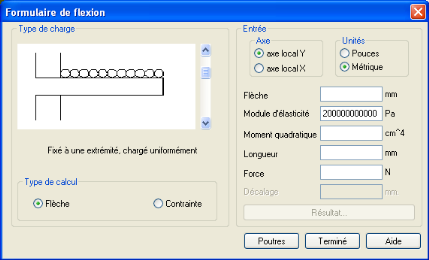
Fig.d
Remplir les données dans les cases vides.
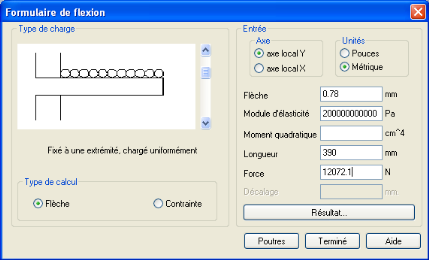
Fig.e
Cliquer sur le bouton Résultat... pour calculer
le moment quadratique
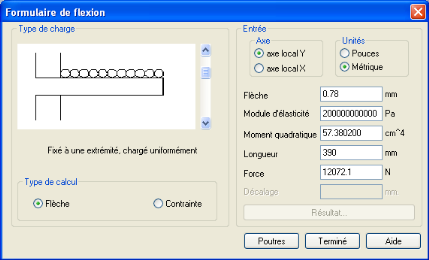
Fig.f
- Calcul du diamètre

On prend 
Partie 6 : Calcul et dimensionnement des
éléments du réducteur manuel
Données
D'habitude on donne les paramètres de départ
suivant:
La vitesse d'entrée (Volant) : 
La vitesse de sortie (Cuve) : par
nécessité de fonctionnement

II.7.1. Schéma cinématique du
réducteur de vitesse
Fig.II.7 Schéma
cinématique.
E
S
II.7.2. Calcul de denture
La denture choisie pour la conception de réducteur est
sur laquelle va se faire la suite des calculs est la denture droite.
II.7.3. Calcul des rapports de transmission i
Le rapport Total i :

Donc:

On a

Pour le premier étage 
Pour le deuxième étage 
II.7.4. Recherche et calcul des paramètres du
premier étage
Ø Rapport de transmission 

Ø Angle de pression 

Ø Le module 
Le premier étage 
Ø Le pas :


Ø Nombre de dent de Roue 
On a 

Nombre de dent de la roue 
Ø Le diametre primitif 




Ø Le diamètre de tête 





Ø Le diamètre de pied 





Ø La saillie 
 
Ø Le creux 
 
Ø Hauteur de la dent 
 
Ø Entraxe 
 
II.7.5. Recherche et calcul des paramètres du
deuxième étage
Ø Rapport de transmission 

Ø Angle de pression 

Ø Le module 
Le premier étage 
Ø Le pas 


Ø Nombre de dent de Roue 
On a 

Nombre de dent de la roue 
Ø Le diametre primitif 





Ø Le diamètre de tête 



Ø Le diamètre de pied 




Ø La saillie 

Ø Le creux 

Ø Hauteur de la dent 

Ø Entraxe 

![]()
![]()
CAO DES ELEMENTS DE LA BETONNIERE [8]
III.1. La conception assistée par ordinateur
(CAO)
Le début des années 90 a été
marqué par une évolution du processus de développement de
produit, l'approche prototype -essai a laissé la place a un nouveau
modèle de développement de produit basé sur la technologie
de conception assistée par ordinateur, afin d'éviter les pertes
de temps et d'argent liées à la construction et a l'essai
prototype.
Les logiciels de CAO regroupent des outils et des programmes
informatiques, qui permettent d'assister l'ingénieur dans la conception
d'un produit, et parmi les logiciels de CAO, on trouve : Inventor, Catia,
SolidWorks, SolidConcept ...etc
III.2. Aperçu sur SolidWorks
SolidWorks est un logiciel de conception mécanique 3D,
il offre des fonctionnalistes très avancées dans le domaine de la
modélisation des pièces, la définition des forme
complexes, la création et la gestion des gros assemblage et la mise en
plan.
Grâce à des modules complémentaires, ce
logiciel peut nous permettre, d'effectuer des calculs d'analyse, ou d'usinage
très avancés et difficiles à réaliser
manuellement.
Parmi ces outils on peut citer :
III.2.1. CosmosWorks
CosmosWorks est un logiciel de calcul de structures
intégré à SolidWorks. Il permet différents
types d'analyse tels que de l'analyse statique (déplacements,
déformations et contraintes), modale (fréquences propres et
déformées modales), thermique (températures, gradients de
température et flux de chaleur), du flambage (charges critiques de
flambage) ou de l'optimisation dimensionnelle.
III.2.2. CosmosMotion
CosmosMotion simule les opérations
mécaniques des assemblages motorisés et les force physiques
générées par ces derniers. Il permet de connaître
des facteurs tels que la consommation d'énergie et les
interférences entre les pièces en mouvement.
III.2.3. CosmosFloworks
CosmosFloworks est un outil original de simulation
d'écoulement fluide développé exclusivement pour les
utilisateurs de SolidWorks. Il fournit des informations sur les conceptions
concernant l'écoulement des fluides, les transferts de chaleur et les
forces appliquées sur les composants immergés.
III.2.4. CamWorks
CAMWORKS est un complément qui s'intègre
complètement à Solidworks.
Il permet la réalisation et la transmission des
programmes de fabrication en Commande Numérique.
Il fonctionne par « RECONNAISSANCE DE
FORMES » grâce à une banque de donnée qu'il est
facile de compléter.
Une banque de donnée « OUTILS » et
« MACHINES », elles aussi personnalisables permettent la
préparation complète de la fabrication.
Un didacticiel permet d'appréhender :
La mise en oeuvre de l'arbre des formes :


La mise en oeuvre de l'arbre d'opérations :


III.3. CAO des éléments de la
bétonnière
Comme il a été mentionné au début
de ce mémoire, nous avons utilisé le logiciel de CAO SolidWorks
pour la conception de tous les éléments de la
bétonnière, calculés au chapitre précédent,
ainsi que leur assemblage et la mise en plan.
III.3.1. Réalisation d'engrenage
On peut facilement réaliser une roue dentée par
CAO.
En utilisant les valeurs calculées d'une roue, on peut
faire sa conception en utilisant des fonction de génération de
volume tells que : « base/bossage
extrudé » ou bien « enlèvement de
matière ».
Cependant les éléments mécaniques d'usage
fréquents tells que clavettes, roulements, roues dentées ....
sont intégrés au logiciel sous forme de bibliothèque des
pièces.
Il suffit de choisir le type et les dimensions d'une roue
dentée et de l'insérer dans l'assemblage.
Dans ce mémoire, nous avons utilisé la
méthode d'insertion d'éléments de la bibliothèque,
qui correspondant aux valeurs que nous avons déterminées par le
calcul.
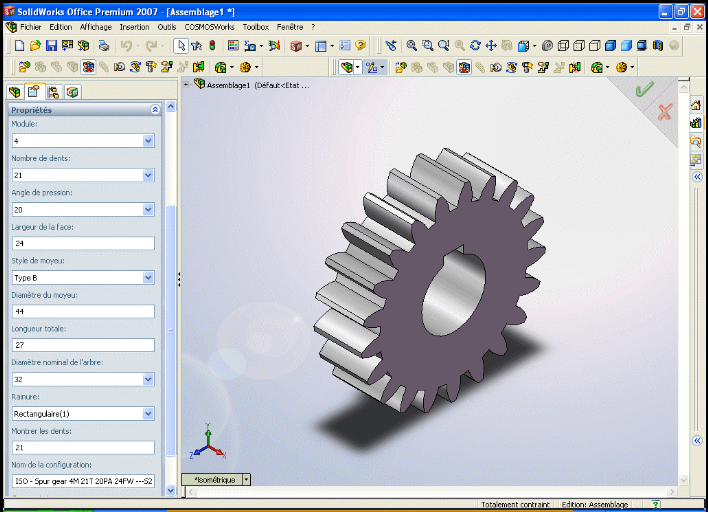
Fig.III.1
III.3.2. Conception du Réducteur manuel
Dans l'ensemble, la bétonnière contient trois
réducteurs.
Le réducteur manuel permet à l'ouvrier de
manipuler la cuve pour le déchargement de son contenu (le béton
mélangé).
C'est un réducteur à deux étages
à denture droit.
Ce réducteur ne nécessite pas une grande
précision de conception ou de fonctionnement :
E
S
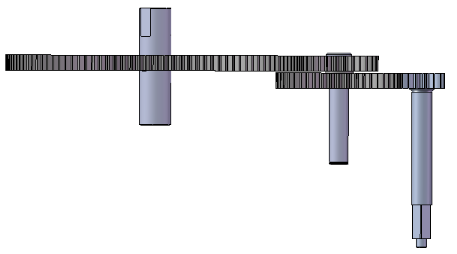
Fig.III.2. Schéma
cinématique.
Les arbre du réducteur ont été
conçus par les fonctions habituelles (bossage, révolution,.....),
les roues ont été choisies dans la bibliothèque.
III.3.3. Conception du châssis
Le châssis est obtenu par assemblage soudé de
plusieurs poutres en U
Le logiciel dispose d'une bibliothèque, de
profilés qu'on peut choisir et dimensionner.
|
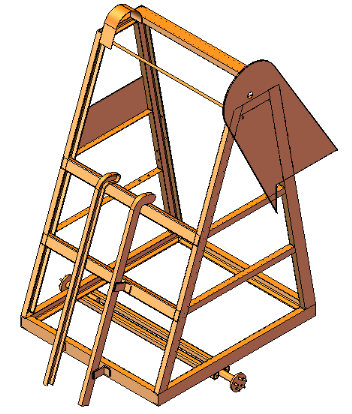
Fig.III.3
|
Methode :
1. Ouvrir la Bibliothèque de conception .
2. Développer Toolbox, ISO, pièces de
structure.
3. faire glisser la poutre en U dans la zone graphique de
l'assemblage
4. définir les paramètres du composant
sélectionné.
III.3.4. Conception de La cuve
La cuve est conçue comme suit:
Les parties (1) et (2) sont en tôle de 5mm
d'épaisseur, assemblées par soudage.
La couronne (3) est fixée par vis sur la partie
cylindrique (2).
La base de la cuve (4) est réalisée par moulage
au sable.
Fig.III.4
CAO : les éléments (1) (2) et (4) sont
obtenu par la fonction révolution
1- Base de la cuve 2- Cylindre
4- Cône
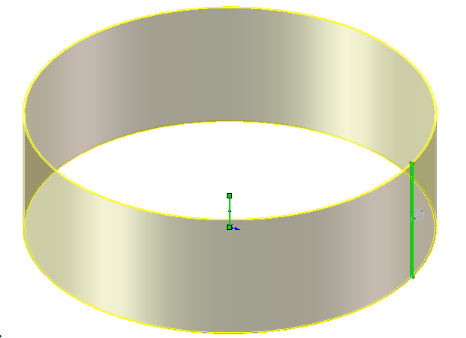
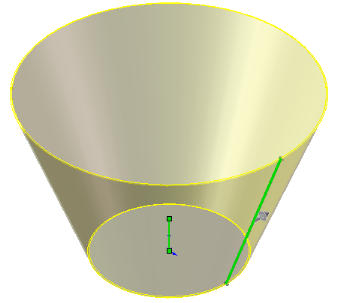
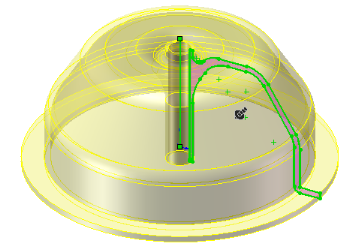
III.3.5. Le moteur de la
bétonnière
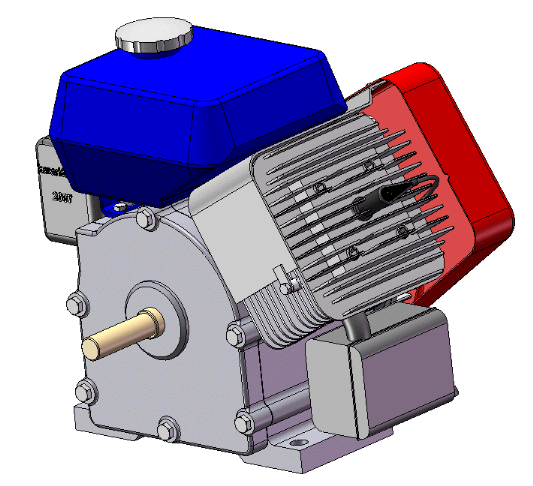
Fig.III.5
Le moteur utilisé est un moteur a combustion interne
à un seul piston, il développe une puissance de 7,5Kw, et un
nombre de tour 1500tr/min.
Sur le plan de la CAO, nous avons découvert qu'un
travail de conception d'un tel moteur à été
effectué en 2007 par des étudiants de notre département
(mémoire de fin d'étude). [10]
Nous avons monté ce moteur sur notre
bétonnière
III.4. Utilisation de COSMOSWorks [9]
Dans ce chapitre nous allons utiliser COSMOSWorks
(§ III.2.1.) pour analyser l'arbre conique.
COSMOSWorks visualise clairement le comportement de la
conception dans des conditions réelles, COSMOSWorks utilisé
pour :
Ø identifier les zone de conceptions susceptibles de
présenter des défauts.
Ø apprécier la réduction des coûts
et des masses engendrés par la suppression des matières
inutiles.
Ø Comparer les différents scénarios en
appliquant des chargements et déplacements imposés : forces
et pressions, couple, chargements des palier et déplacements
imposées fixes ou directionnels.
COSMOSWorks inclut également d'autre fonctions, telles
que l'optimisation des conceptions, la simulation des tests de chute, et des
études thermiques, fréquentielles, de flambage et de fatigue.
Dans ce mémoire nous avons utilisé la
méthode d'étude statique qui calcule les déplacements, les
forces de réaction, les déformations, les contraintes et la
distribution des coefficients de sécurité
III.5. Affichage des résultats de
l'analyse
Ø Les contraintes
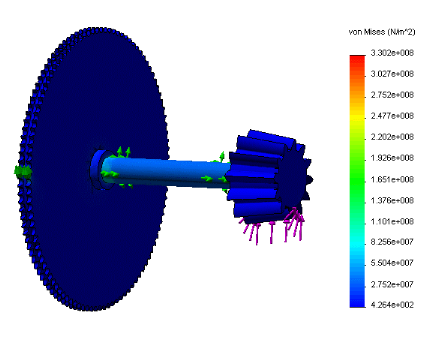
Fig.III.6. les contraints
Nom
|
Type
|
Min
|
Max
|
Contraintes 1
|
VON : contrainte de vonMises
|
426.42N/m^2
Noeud : 57978
|
3.30245e+008N/m^2
Noeud : 95215
|
Ø Déplacements
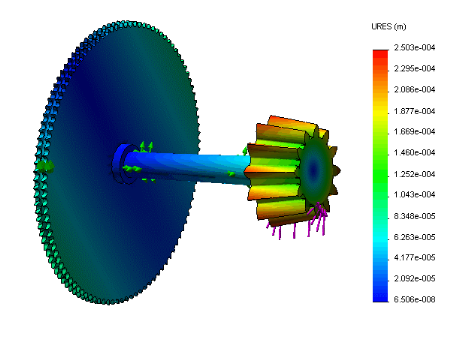
Fig.III.7. les déplacements
Nom
|
Type
|
Min
|
Max
|
Déplacements1
|
URSES: Déplacement résultant
|
426.42 N/m^2
Noeud: 57978
|
0.000250305 m
Noeud: 2660
|
Ø Les déformations
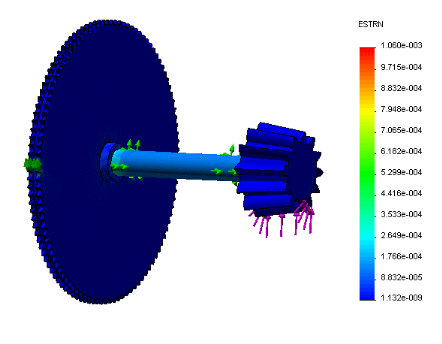
Fig.III.8. les déformations
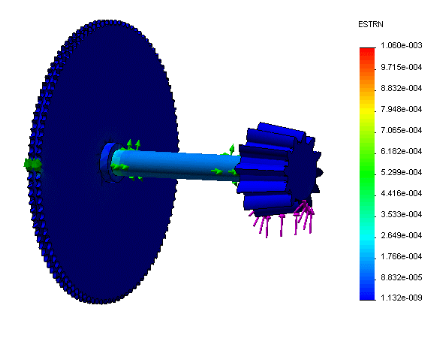
Nom
|
Type
|
Min
|
Max
|
Déformations1
|
ESTRN: Déformation équivalente
|
1.13247e-009
Elément: 48075
|
0.00105979 m
Elément: 58377
|
III.6. Diagrammes de tracés de résultats
sondés
Ø Diagramme de
déplacement
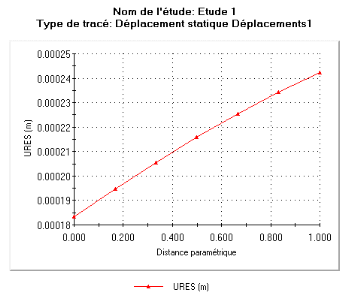
Fig.III.9
La Figure (III.9) présente la variation des noeuds de la
dent.
En se déplaçant du pied vers la tête, on
enregistre une dégradation du déplacement.
Ø Diagramme de contrainte
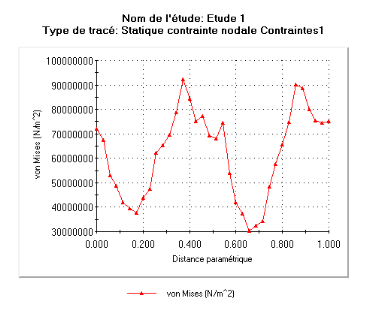
Fig.III.10
La figure (III.10) représente la variation de contrainte
au niveau du palier.
Ø Les déformations dans l'ensemble du
réducteur (ESTRN)
La figure III.8. montre que les déformations se
situent au niveau des paliers.
![]()
![]()
FAO DE L'ARBRE DU REDUCTEUR [8]
IV.1. La fabrication assistée par ordinateur
(FAO)
La fabrication assistée par ordinateur (FAO) s'impose
de plus en plus dans le milieu industriel. Le principe est la
génération d'un code par un logiciel, utilisé par une
machine à commande numérique (MOCN) pour exécuter les
opérations de fabrication.
Nous consacrons ce chapitre à CAMWorks. C'est un
complément de SolidWorks qui nous permet de générer un
programme ISO, à l'aide d'un post-processeur .
Il nous permet aussi de simuler la fabrication sur MOCN d'une
pièce conçu par SolidWorks au préalable.
C'est la première fois que ce logiciel est
utilisé au niveau de notre département.
Nous utiliserons CAMWorks pour la simulation de l'usinage de
l'arbre d'entrée du réducteur manuel.
Nous avons choisi cette pièce parce qu'elle contient
plusieurs formes intéressantes sur le plan de FAO : engrenage,
forme cylindrique, forme carrée
IV.2. Étape mise en oeuvre du logiciel
Une pièce est un solide qui a été
créé avec SolidWorks ou importée dans SolidWorks depuis
un autre système CAO via un fichier IGES, Parasolid, SAT, etc.
IV.2.1. Choisir le mode de travail
CAMWorks est un complément qui s'intègre dans
SolidWorks et travaille dans son l'environnement.
L'utilisation de CAMWorks se fait en mode pièce
(élément modélisé : pièce) et en mode
assemblage (éléments modélisés : pièce,
élément de mise en position, élément de maintien en
position).
IV.2.2. Définir la machine et directeur de CN
La définition de la machine spécifie le type
d'usinage qui doit être réalisé pour le modèle (par
ex. fraisage ou tournage) et le contrôleur associé de la
machine-outil (post-processeur) pour la création appropriée du
programme CN
Cliquer avec le bouton droit de la souris sur Mill machine
- mm dans l'arbre des formes CAMWorks et sélectionner Edit
Definition... dans le menu contextuel.
|
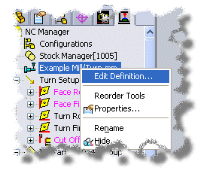
Fig.IV.1
|
L'onglet Machine de la boîte de dialogue
Machine permet de sélectionner la machine-outil à utiliser pour
usiner une pièce. La liste qui apparaît dépend des machines
qui ont été établies dans TechDB ( banque de donnée
).
Cliquer sur l'onglet Post-Processor. L'onglet
Contrôleur vous permet de sélectionner le post-processeur dans une
liste de contrôleurs disponibles. La liste qui s'affiche dépend
des post-processeurs installés dans votre système.
|
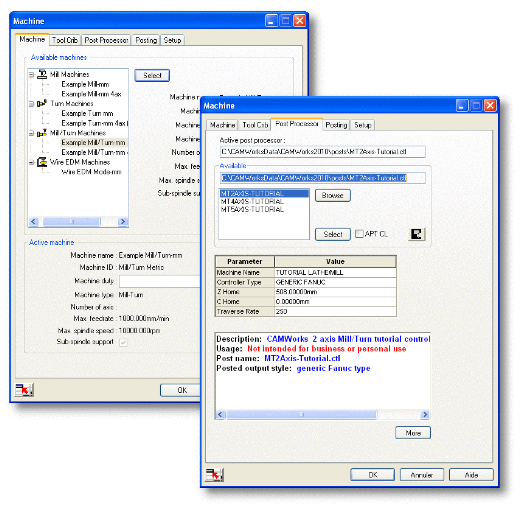
Fig.IV.2
|
IV.2.3. Définir le brut
Le brut est défini par deux attributs:
· Dimension et forme
Le brut par défaut est le plus petit rectangle
(boîte englobante) dans lequel la pièce peut s'encastrer. En
règle générale, on n'utilise pas la dimension du stock et
on doit changer la définition du brut en décalant la boîte
englobante ou en étirant une esquisse.
· Type de matière
Des modifications peuvent être apportées au brut
à n'importe quel moment ; cependant, pour définir un brut
différent après avoir défini les formes usinables, on doit
sélectionner Reconstruire pour que CAMWorks actualise ces
informations pour faire référence aux formes du brut.
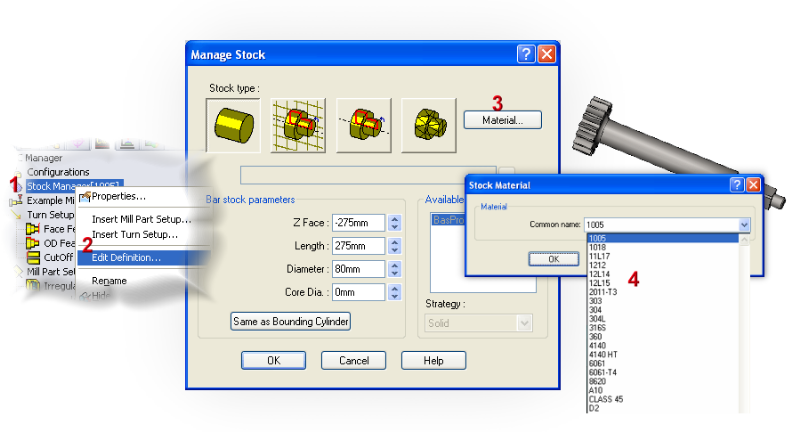
Fig.IV.3
1. Cliquer avec le bouton droit de la souris sur Stock
Manager.
2. Sélectionner Edit Definition ... dans le
menu contextuel.
3. Cliquer sur le bouton Material...
. La boîte de dialogue s'affiche.
4. Sélectionner un type de matière
dans la liste déroulant.
IV.2.4. Définir les origines
La boîte de dialogue Operation Setup
Paramètres s'affiche lorsque on clique avec le
bouton droit de la souris sur Turn Setup dans l'arbre
d'opération et on sélectionne Edit Definition... dans le
menu contextuel.
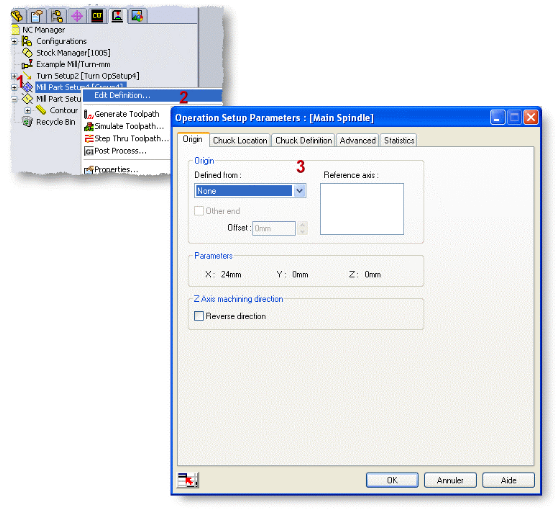
Fig.IV.4
- Système de coordonnées de
fixation
En mode Assemblage, cette option permet de définir le
système de coordonnées de fixation. Ceci concerne la position de
l'origine programme. Bien que la sortie de code G puisse être
basée sur ce point, elle est censée être utilisée
comme point de référence. La définition de la position va
au-delà de la définition de l'emplacement. Elle permet
également de définir les directions X, Y et Z positives à
utiliser pour tous les mouvements de la machine.
Le système de coordonnées de fixation est
défini à partir d'une entité de système de
coordonnées SolidWorks.
IV.2.5. Définir les formes usinables «
entités d'usinage »
L'usinage ne peut être effectué que pour des
formes usinables. CAMWorks fournit trois méthodes pour définir
des formes usinables pour le fraisage 2D et 3D.
1. Reconnaissance Automatique de Formes (RAF)
reconnaissance automatique de formes analyse la
forme de la pièce et essaie de définir les formes usinables les
plus communes telles que les poches, les trous, les centrages/chanfreins et les
bossages. La commande Extraire formes usinables lance la RAF. Selon la
complexité de la pièce, la RAF peut permettre d'économiser
beaucoup de temps dans la définition des formes prismatiques 2D.
|
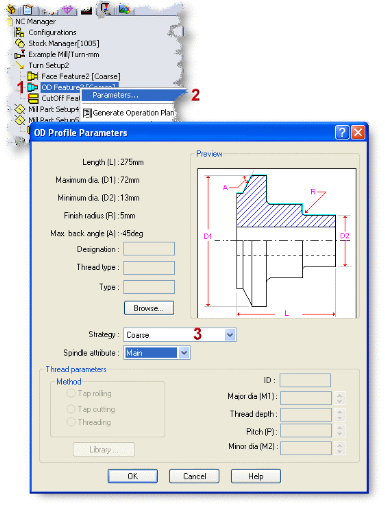
Fig.IV.5
|
2. Formes 2D et 2,5D créées interactivement
La RAF ne peut reconnaître chaque forme sur des
pièces complexes et ne reconnaît pas certains types de formes.
Pour usiner ces zones, vous devez définir des formes de façon
interactive en utilisant la commande Insérer forme 2,5D.
3. Formes 3D créées interactivement
Si vous avez CAMWorks pour fraisage 3D, vous définissez
des formes 3D de façon interactive selon les faces spécifiques
à usiner et les faces à éviter
IV.2.6. Définir, générer les
opérations.
Une opération est définie comme un type de cycle
d'usinage tel que l'ébauche. Après avoir créé les
formes d'usinage, les opérations peuvent être
générées pour usiner les formes de la pièce.
Comprendre les opérations
La Base de données technologique (TechDB)
définit quelles opérations sont nécessaires pour chaque
forme d'usinage et les paramètres pour chaque opération.
Dès que l'opération est définie, les parcours d'outil
peuvent être générés pour usiner la forme. Les
méthodes pour éliminer le matériel s'appellent cycles de
coupe. Lorsque ces cycles de coupe sont lancés, l'opération
contient l'information d'usinage nécessaire pour générer
les parcours d'outil pour couper la pièce.
Commande Generate Operation plan
Pour augmenter la productivité, CAMWorks fournit une
méthode automatique pour générer des opérations
ainsi qu'une méthode manuelle pour insérer des opérations.
La commande Générer plan d'opération est utilisée
pour générer automatiquement un plan d'opération pour
usiner chaque forme usinable.
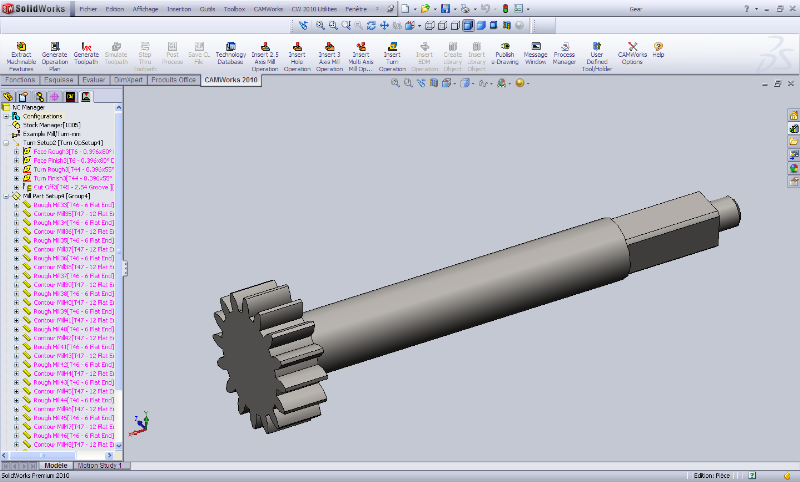
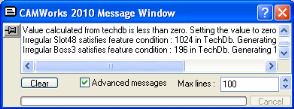
Fig.IV.6
IV.2.7. Choix des outils et des paramètres de
coupe
Les opérations générées par la
commande Generate Operation plan sont basées sur des
informations enregistrées dans la Base de données technologique.
Les paramètres pour chaque opération affectent la création
du parcours d'outil et la sortie du code CN. Ces paramètres incluent le
contrôle pour le diamètre de l'outil, les directions de coupe, les
valeurs avance/vitesse, etc. Comme avec la plupart des fonctions CAMWorks, les
paramètres sont établis automatiquement. Toutefois, ces
paramètres sont prévus comme point de départ et ces
configurations peuvent être modifiées.
Pour éditer les paramètres d'opération
avant la création du parcours d'outil, utiliser la commande Edit
Definition... dans le menu contextuel Opération.
Pour changer les paramètres d'usinage pour une
opération 2D ou 3D :
1. Cliquer sur une opération dans l'arbre
d'opération.
2. Sélectionner Edit Definition...
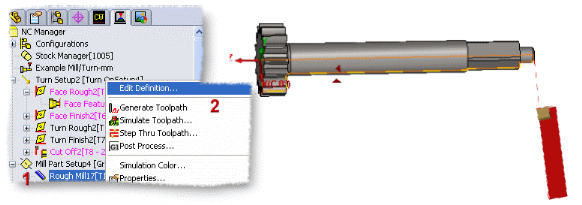
Fig.IV.7
La boîte de dialogue Operation
Paramètres contient les zones qui regroupent les paramètres
pouvant être changés avant de générer les parcours
d'outil et d'exécuter le processus
3. Changer les paramètres
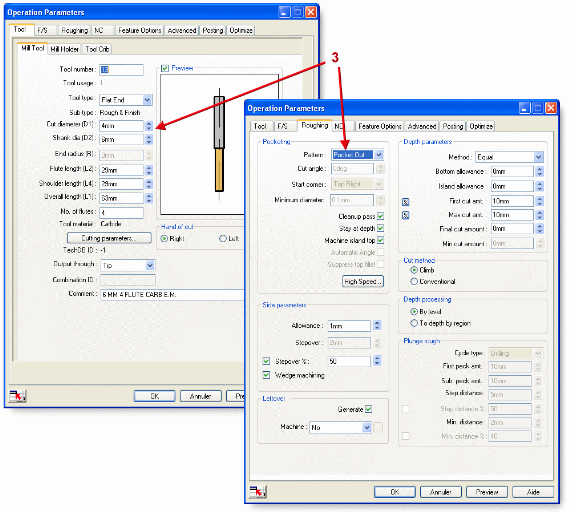
Fig.IV.8
L'onglet Roughing de la boîte
de dialogue Operation Paramètres contient les paramètres
qui influencent le mode de finition de la pièce
L'onglet Tool de la boîte de dialogue
Operation Paramètres contient plusieurs pages d'informations
sur l'usinage :
Outil de calibrage, Outil de centrage, Outil de
rayonnée concave, Outil de centrage/chanfreinage, Outil de queue
d'aronde, Outil de perçage, Outil rainure en T, Outil de fraisage, Outil
de fraisage défini par l'utilisateur Alésoir, Taraud, Outil de
filetage par fraisage Porte-fraise, Tourelle
IV.2.8. Générer le parcours d'outil «
Simulation »
La commande Toolpath Simulation
fournit une représentation graphique de la matière
éliminée pour les opérations de vérification
d'usinage. En démarrant ces aides de simulation, la confirmation des
parcours d'outil créés est faite.
4. Cliquer sur l'icône Simulate
Toolpath 
La boite de dialogue apparaît
5. Cliquer sur l'icône Run
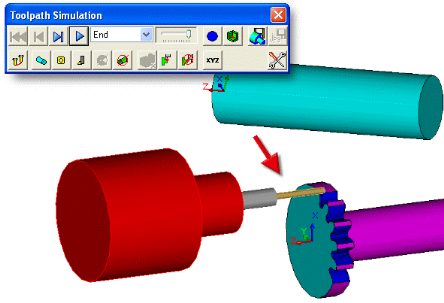
Fig.IV.9
IV.2.9. Générer le programme ISO
Le post-traitement est la démarche finale pour
générer le fichier de programme CN. Cette démarche
convertit des parcours d'outil généralisés et les
informations relatives aux opérations en code ISO de machine pour un
directeur de commande spécifique de machine-outil. Le système
crée un code ISO pour chaque parcours d'outil dans la pièce pour
que l'opération du parcours d'outil apparaisse dans l'arbre
d'opération CAMWorks.
1. Cliquer sur l'icône Post Process Output
2. La boite de dialogue apparaît
3. Cliquer sur l'icône Run
4. Le programme ISO apparaît
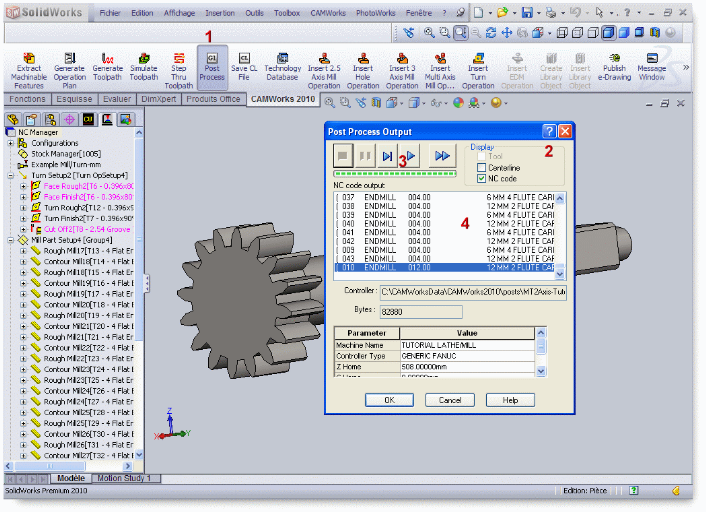
Fig.IV.10
Le CD joint à ce mémoire contient le programme
ISO qui correspond à l'usinage de l'arbre avec pignon. (voir fichier :
programme ISO.txt).
L'utilisation de CAMWorks pour cette pièce a
été à titre de démonstration.
Notre objectif à été d'explique
l'utilisation de ce logiciel pour générer le code ISO sur une
pièce assez compliquée
CONCLUSION GENERALE
Le développement économique de notre pays est
à l'origine de la naissance de nouvelles usines d'engins de chantiers.
On signale le besoin de ces unités de production en matière de
savoir-faire national dans le domaine de la conception mécanique.
Notre sujet a été proposé dans le but de
réaliser une étude d'une bétonnière qui pourrait
être produite au niveau local.
Notre travail a été de faire (sur PC) la
conception, l'analyse et la fabrication de quelques éléments de
cet engin.
Le calcul des pièces a été fait par la
méthode classique. Les résultats ont été introduits
dans le logiciel de CAO (solidworks).
L'analyse et la vérification des contraintes dans les
pièces ont donné des valeurs très proches de celles
calculés par la méthode manuelle classique.
La fabrication assistée par ordinateur (FAO),
introduite pour la première fois au niveau de notre département,
a été utilisée, beaucoup plus, à titre de
présentation.
L'étude complète d'une telle machine
dépasse le cadre d'un mémoire de fin d'études. Nous
espérons que d'autres étudiants continueront dans ce domaine pour
arriver à généraliser l'utilisation de ces nouveaux outils
dans le domaine de la construction mécanique.
ANNEXES
Tableau 1
Facteur de service [1]
Type de machine
entraînée
|
Type de moteur
|
Moteur à combustion interne avec transmission
hydraulique
|
Moteur électrique ou turbine
|
Moteur à combustion interne avec transmission
mécanique
|
Agitateur (produit liquide)
|
1,0
|
1,0
|
1,2
|
|
|
|
|
Broyeurs et concasseurs
|
1,4
|
1,5
|
1,7
|
|
|
|
|
Compresseurs
|
|
|
|
- Centrifuges
|
1,2
|
1,3
|
1,4
|
- à pistons
|
|
|
|
3 cylindres et plus
|
1,2
|
1,3
|
1,4
|
1 ou 2 cylindres
|
1,4
|
1,5
|
1,7
|
|
|
|
|
Convoyeurs et élévateurs
|
|
|
|
- Charge ou alimentation uniforme
|
1,0
|
1,0
|
1,2
|
- Charge ou alimentation non uniforme
|
1,2
|
1,3
|
1,4
|
|
|
|
|
Cribles
|
1,2
|
1,3
|
1,4
|
|
|
|
|
Génératrices
|
1,0
|
1,0
|
1,2
|
|
|
|
|
Grues
|
1,2
|
1,3
|
1,4
|
|
|
|
|
Machinerie générale
|
|
|
|
- Charge uniforme
|
1,0
|
1,0
|
1,2
|
- Charge modérée ou avec chocs
modérées
|
1,2
|
1,3
|
1,4
|
- Chocs sévères, renversement de la charge,
conditions difficiles
|
1,4
|
1,5
|
1,4
|
|
|
|
|
Pompes
|
|
|
|
- Centrifuges
|
1,0
|
1,0
|
1,2
|
- à pistons 3 cylindres ou plus
|
1,2
|
1,3
|
1,4
|
|
|
|
|
Ventilateurs
|
1,0
|
1,0
|
1,2
|
Tableau 2
Chaînes n° 50 (pas = 0,625 po, pas = 25,7 mm) [1]
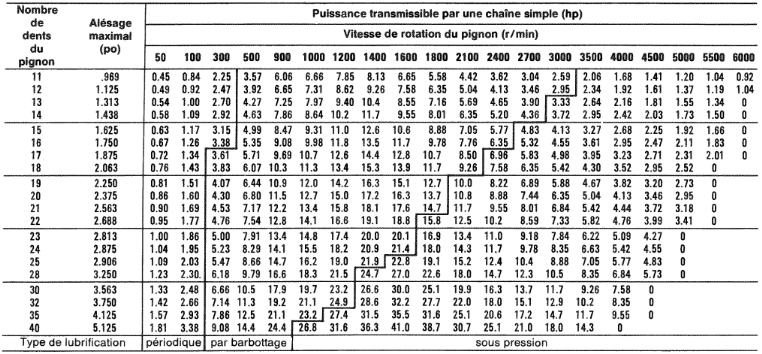
Tableau3
Chaînes n° 40 (pas = 1,500 po = 25,7 mm) [1]
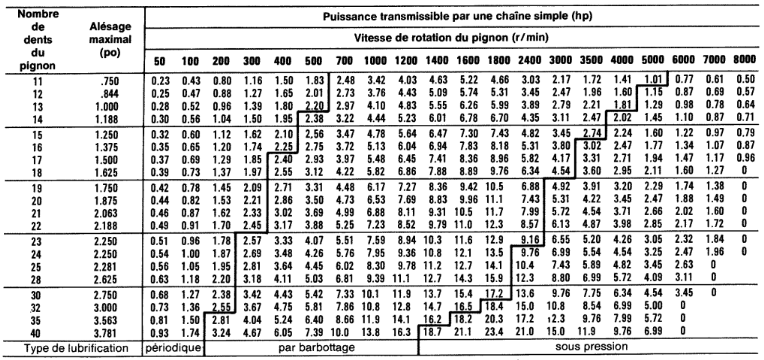
Tableau 4
Facteur de nombre de rangs de maillage K2 [1]
Nombre de range
|
K2
|
1
2
3
4
5
6
= 7
|
1
1,7
2,5
3,3
4,1
5
Consulter le fabricant
|
Tableau5
Caractéristiques des chaînes à rouleaux
[1]
Identification
|
Pas
|
Surface nominale de contact*
Ar(mm2)
|
Masse linéique

|
40
50
60
80
100
120
140
160
200
|
12,70
15,875
19,05
25,40
31,75
38,10
44,45
50,80
63,50
|
44
69
105
178
260
392
470
643
1086
|
0,60
1,00
1,50
2,56
3,84
5,56
7,44
10,44
16,70
|
* Pour les chaînes à maillage double, multiplier
ces valeurs par deux; pour les chaînes à maillage triple
multiplier ces valeurs par trois etc.
Tableau 6
Coefficient de résistance de la dent [2]
Matériaux
|
Valeurs admissibles en daN/mm2
|
óf1
|
c
|
Fonte grise FT 20
|
3 à 4,5
|
0,2 à 0,35
|
Acier moulé Ac clé 50
|
6 à 9
|
0,4 à 0,7
|
Acier Ac 50
|
9 à 12
|
0,7 à 0,9
|
Bronze
|
4 à 8
|
0,3 à 0,9
|
Bois dur
|
1 à 2
|
0,1 à 0,15
|
|
|
|
Polyamide ( Nylon 6,6 )
|
|
Vitesse circonf. en m/s :
|
0,5
|
1
|
2
|
4
|
6
|
8
|
10
|
12
|
Coefficient c daN/mm2 :
|
0,2
|
0,16
|
0,13
|
0,10
|
0,09
|
0,08
|
0,078
|
0,075
|
Tableau 7
Facteur de vitesse (kV) [11]
Qualité ISO
|
1
|
2
|
3
|
4
|
5
|
6
|
7
|
8
|
9
|
10
|
11
|
12
|
A
|
|
12
|
6
|
3
|
kv
|
1
|
|
Tableau 8
Facteur de portée (km) [3]
Application
|
Aucun organe en porte-à-faux
|
Un organe en porte-à-faux
|
Les deux organes en porte-à-faux
|
Mécanique générale
|
0,9 à 1
|
0,8 à 0,9
|
0,7 à 0,8
|
Automobile
|
0,9 à 1
|
0,8 à 0,9
|
-
|
Aviation
|
0,8 à 1
|
0,7 à 0,9
|
0,65 à 0,8
|
Tableau 9
Facteur de service ( kA ) [11]
Organe
moteur
|
Organe récepteur
|
Fonctionnement pratiquement
sans chocs
|
Fonctionnement avec chocs modérés
|
Fonctionnement avec chocs importants
|
12 h/jour
|
24 h/jour
|
12 h/jour
|
24 h/jour
|
12 h/jour
|
24 h/jour
|
Moteurs électriques et turbines
|
1
|
0,95
|
0,8
|
0,7
|
0,67
|
0,57
|
Moteurs à combustion interne à un seul piston
|
0,67
|
0,57
|
0,57
|
0,45
|
0,45
|
0,35
|
Moteurs à combustion interne à pistons multiples
|
0,8
|
0,7
|
0,67
|
0,57
|
0,57
|
0,45
|
Tableau 10
Aciers Fins, non allies, de classe CC et XC
Nuance
|
Etat
|
R
daN/mm2
|
Re
|
A%
|
KCU
|
Propriétés
|
Emplois
|
CC 10
|
R: 900-925
|
34 - 44
|
21,5
|
30
|
-
|
Acier extra doux de cémentation; très
malléable, soudable; magnétique
|
Tôles, tubes, rivets, pièces forgées,
matricées, pliées, embouties
|
TE: 900°
Ru: 200°
|
54 - 103
|
34,5
|
11
|
10
|
CC 20
|
R: 880-910
|
41 - 53
|
27,5
|
26
|
-
|
Acier doux de cémentation; malléable; soudable.
|
Pièces forgées et matricées: arbres,
boulons, clavettes, etc.
|
TE: 880
Ru: 550
|
54 - 78
|
35,5
|
17
|
7
|
CC 35
|
R:850-880
|
55 - 67
|
31,5
|
20
|
-
|
Acier de traitement dans la masse; trempe à l'eau
|
Pièces traitées: cames, engrenages, axes, arbres,
etc. bielles, vilebrequins, organes d'embrayage, et d'accouplement, boulons,
clavettes, etc.
|
TE:850
Ru:550
|
74 - 96
|
56
|
12
|
4
|
CC 45
|
R:840-870
|
62 - 74
|
34,5
|
17
|
-
|
Acier de traitement dans la masse; trempe à l'eau et
à l'huile pour faible section
|
TE:830
Ru:550
|
86 - 106
|
68,5
|
9
|
2
|
XC 10
|
R:900-925
|
34 - 42
|
21,5
|
31
|
-
|
Aciers extra-doux de cémentation; très
malléables, soudables, magnétiques
|
Pièces de petite et moyenne section, à faible
contrainte, résistantes à l'usure: axes, cames, pignons, etc.
|
TE:900
Ru:200
|
54 - 83
|
34,5
|
16
|
12
|
XC 12
|
R:900-925
|
37 - 45
|
23,5
|
29
|
-
|
TE:900
Ru:200
|
73 - 113
|
49,5
|
11
|
6
|
XC 18
|
R:875-900
|
41 - 49
|
25,5
|
28
|
-
|
Acier doux de cémentation; variété XC18S
soudable; malléable
|
Pièces cémentées, travaillant sans chocs:
arbres à cames, pignons, axes, boulons, clavettes, etc.
|
TE:880
Ru:200
|
88 - 127
|
63,5
|
8
|
4
|
XC 25
|
R:860-885
|
47 - 56
|
28,5
|
26
|
-
|
Trempe à l'eau à faible pénétration
et trempe superficielle. Recuit, apte au travail à froid.
|
Pièces traitées de petite et moyenne dimensions
avec contrainte moyenne: arbres, leviers, bielles, crémaillère,
boulons, etc.
|
TE:850
Ru:550
|
61 - 78
|
44
|
17
|
8
|
XC 32
|
R:850-875
|
55 - 64
|
31,5
|
23
|
-
|
TE:850
Ru:550
|
74 - 89
|
56
|
14
|
7
|
XC 38
|
R:850-875
|
58 - 67
|
33,5
|
21
|
-
|
TE:850
Ru:550
|
80 - 95
|
61,5
|
12
|
5
|
XC 42
|
R:840-870
|
63 -71
|
35,5
|
19
|
-
|
Acier pour trempe à l'eau, et trempe à l'huile
à faible section; trempe superficielle
|
Mêmes emplois que XC32 et XC38 avec caractéristiques
plus élevées
|
TE:830
Ru:550
|
86 - 101
|
68,5
|
11
|
4
|
XC 48
|
R:840-870
|
67 - 76
|
37
|
17
|
-
|
Trempe à l'huile en faibles section; trempe
superficielle.
|
Pièces d'usure pouvant subir des chocs
modérés: ressorts peu chargés, cames, engrenages,
pivots...
|
TE:830
Ru:550
|
83 - 98
|
66,5
|
10
|
3
|
XC 55
|
R:830-855
|
73 - 88
|
43
|
15
|
-
|
Trempe à l'huile en faibles et moyennes sections
|
TH:830
Ru:550
|
93 - 113
|
70,5
|
8
|
-
|
XC 65
XC 70
XC 80
|
Caractéristiques mécaniques non
imposées
|
Acier pour trempe à l'huile avec faible
pénétration de trempe. Grande résistance et grande
dureté.
|
Corde à piano pour ressorts, câbles, pivots,
engrenages, matrices, poinçons, lames de cisailles, outils de forge,
scies à bois, etc.
|
( R: recuit - Ru: revenu - TE: trempe à l'eau -
TH: trempe à l'huile)
Tableau 11
Dimensions et tolérances de clavettes [6]
d
arbre
|
Section clavette
|
a
|
J
nom tol.
|
K
nom tol
|
K1
nom tol
|
de 6
Jusqu'à8
|
2×2
|
2
|
d - 1,2
|
0
-100
|
d + 1
|
+100
0
|
d + 0,5
|
+100
0
|
Au-delà 8
Jusqu'à10
|
3×3
|
3
|
d - 1,2
|
0
-100
|
d + 1,4
|
0
+100
|
d + 0,9
|
+100
0
|
Au-delà 10
Jusqu'à12
|
4×4
|
4
|
d - 1,8
|
0
-100
|
d + 1,8
|
+100
0
|
d + 1,2
|
+100
0
|
Au-delà 12
Jusqu'à17
|
5×5
|
5
|
d - 2,5
|
0
-100
|
d + 2,3
|
+100
0
|
d + 1,7
|
+100
0
|
Au-delà 17
Jusqu'à22
|
6×6
|
6
|
d - 3
|
0
-100
|
d + 2,8
|
+100
0
|
d + 2,2
|
+100
0
|
Au-delà 22
Jusqu'à30
|
8×7
|
8
|
d - 4
|
0
-200
|
d + 3,3
|
+200
0
|
d + 2,4
|
+200
0
|
Au-delà 30
Jusqu'à38
|
10 × 8
|
10
|
d - 5
|
0
-200
|
d + 3,3
|
+200
0
|
d + 2,4
|
+200
0
|
Au-delà 38
Jusqu'à 44
|
12 × 8
|
12
|
d - 5
|
0
-200
|
d + 3,3
|
+200
0
|
d + 2,4
|
+200
0
|
Au-delà 44
Jusqu'à 50
|
14 × 9
|
14
|
d - 5,5
|
0
-200
|
d + 3,8
|
+200
0
|
d + 2,9
|
+200
0
|
Au-delà 50
Jusqu'à 58
|
16 × 10
|
16
|
d - 6
|
0
-200
|
d + 4,3
|
+200
0
|
d + 3,4
|
+200
0
|
Au-delà 58
Jusqu'à 65
|
18 × 11
|
18
|
d - 7
|
0
-200
|
d + 4,4
|
+200
0
|
d + 3,4
|
+200
0
|
Au-delà 65
Jusqu'à 75
|
20 × 12
|
20
|
d - 7,5
|
0
-200
|
d + 4,9
|
+200
0
|
d + 3,9
|
+200
0
|
Au-delà 75
Jusqu'à 85
|
22 × 14
|
22
|
d - 9
|
0
-200
|
d + 5,4
|
+200
0
|
d + 4,4
|
+200
0
|
Au-delà 85
Jusqu'à 95
|
25 × 14
|
25
|
d - 9
|
0
-200
|
d + 5,4
|
+200
0
|
d + 4,4
|
+200
0
|
Au-delà 95
Jusqu'à110
|
28 × 16
|
28
|
d - 10
|
0
-200
|
d + 6,4
|
+200
0
|
d + 5,4
|
+200
0
|
Au-delà110
Jusqu'à130
|
32 × 18
|
32
|
d - 11
|
0
-200
|
d + 7,4
|
+200
0
|
d + 6,4
|
+200
0
|
Au-delà130
Jusqu'à150
|
36 × 20
|
36
|
d - 12
|
0
-300
|
d + 8,4
|
+300
0
|
d + 7,1
|
+300
0
|
Au-delà150
Jusqu'à170
|
40 × 22
|
40
|
d - 13
|
0
-300
|
d + 9,4
|
+300
0
|
d + 8,1
|
+300
0
|
Au-delà170
Jusqu'à200
|
45 × 25
|
45
|
d - 15
|
0
-300
|
d + 10,4
|
+300
0
|
d + 9,1
|
+300
0
|
Tableau 12
Dimensionnement des chaînes à rouleaux [6]
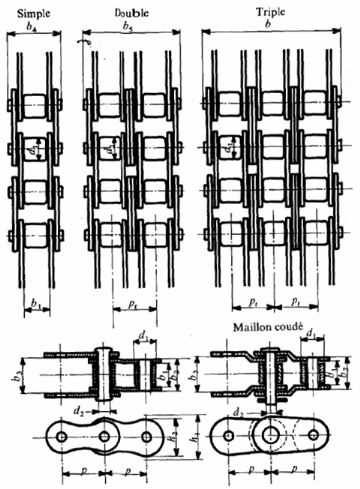
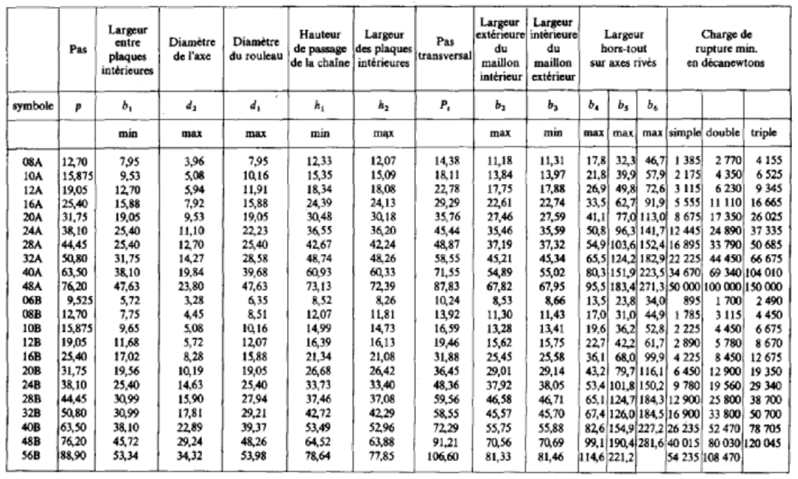
Tableau 13
Dimensionnement des roues dentées pour les chaînes
[6]
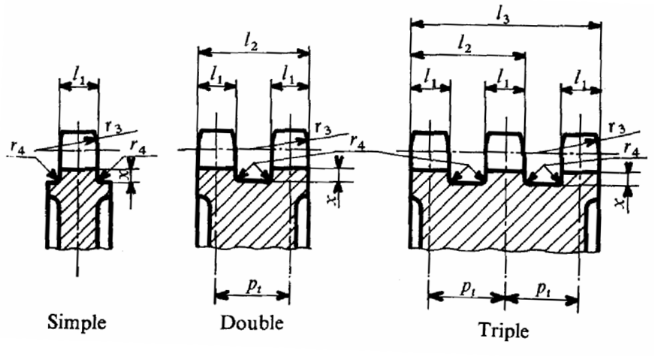
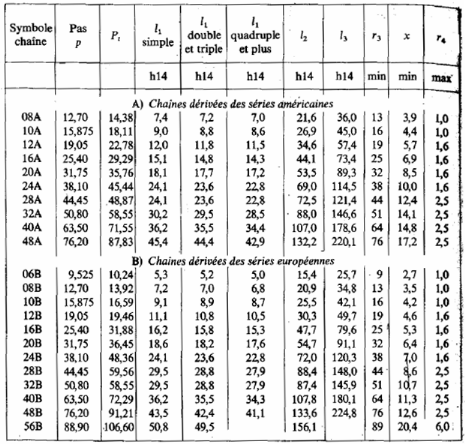
Figure 1
Abaque utilisé pour choisir les chaînes à
rouleaux [1]
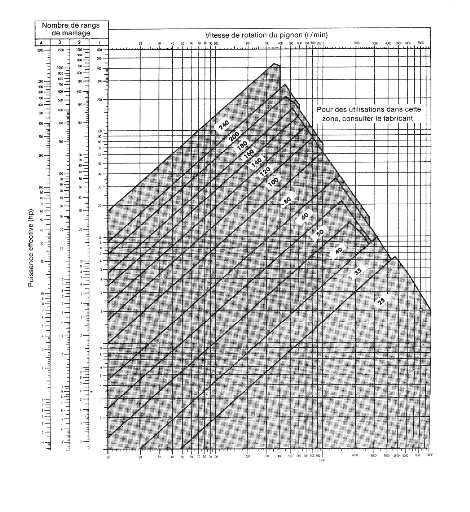
Figure 2
Rapport de conduite [3]
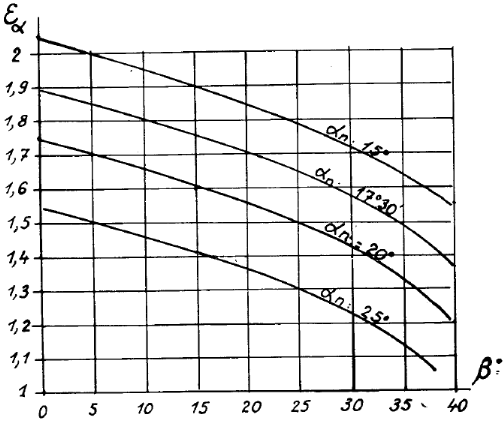
Figure 3
Facteur de forme [3]
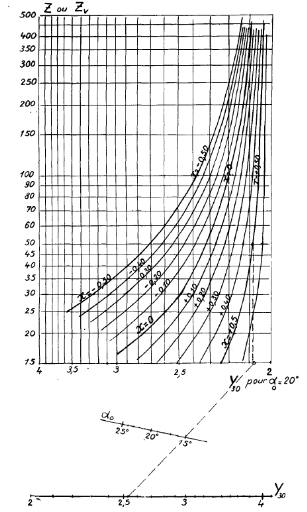
REFERENCES BIBLIOGRAPHIQUES
[1] : G. DROUIN & M. GOU
Eléments de machines. Ed : ECOLE
POLYTECHNIQUE DE MONTREAL.
[2] : G. NICOLET & E. TROTTET
Eléments de machines. Ed : SPES LAUSANNE
1971
[3] : G. HENRIOT
Traité théorique et pratique des engrenages Tome 1.
Ed : DUNDO 1968
[4] : Logiciel RDM6.
[5] : H. MIROLOBOVE
Résistance des matériaux. Ed : MIR
1977.
[6] : Christian ELOY
Conception en construction mécanique. Ed : Dunod
1981
[7] : A. CHEVALIER
Guide de dessinateur industriel. Ed : Hachette,
1980
[8] : L'aide de SolidWorks 2010.
[9] : M. HACINI & K. MAANSER
PFE : Calcul et CAO d'un réducteur de vitesse
à deux étages. Promotion 2008
[10] : F. KARARI & A. LEHLALI
PFE : Etude descriptive et conception par CAO d'un
moteur monocylindre à deux temps. Promotion 2007
[11] : Christian ELOY
Calculs en construction mécanique. Ed : Dunod
1981
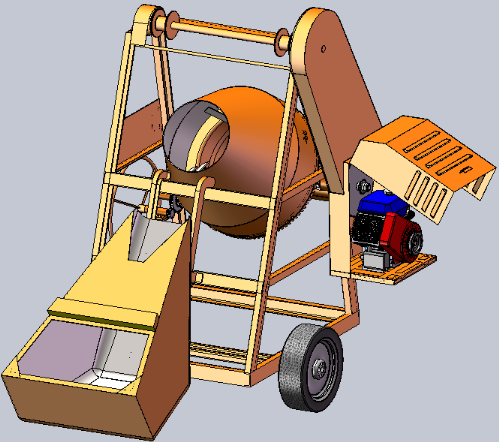
Résumé
Notre sujet a été proposé dans le but de
réaliser une étude d'une bétonnière qui pourrait
être produite au niveau local. Notre travail a été de faire
(sur PC) la conception, l'analyse et la fabrication de quelques
éléments de cet engin. Le calcul des pièces a
été fait par la méthode classique. Les résultats
ont été introduits dans le logiciel de CAO (solidworks).
L'analyse et la vérification des contraintes dans les pièces ont
donné des valeurs très proches de celles calculés par la
méthode manuelle classique. La fabrication assistée par
ordinateur (FAO), introduite pour la première fois au niveau de notre
département, a été utilisée, beaucoup plus,
à titre de présentation.
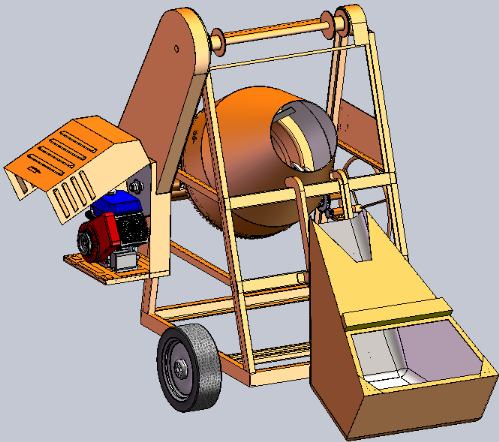
ãáÎÕ
Êã ÇÞÊÑÇÍ
åÐÇ ÇáãæÖæÚ
ãä Ìá ÅÌÑÇÁ
ÏÑÇÓÉ áÎáÇØ
ÇáÓãäÊ ÇáÐí
íãßä ÅäÊÇÌå
ãÍáíÇ. æÞÏ
ÞãäÇ ÈÅäÌÇÒ
åÐå ÇáÏÑÇÓÉ
ÈÇÓÊÚãÇá
(ÇáßãÈíæÊÑ)
í ÊÕãíã æ
ÊÍáíá æ
ÊÕäíÚ ÈÚÖ
ãßæäÇÊ åÐÇ
ÇáÌåÇÒ. æÞÏ
Êã ÍÓÇÈ
ÇáÞØÚ
ÈÇáØÑíÞÉ
ÇáÊÞáíÏíÉ.
æÇÓÊÎÏÇã
ÇáÈÚÇÏ
ÇáãÍÓæÈÉ í
ÈÑäÇãÌ ( SOLIDWorks )
áÊÕãíã
ÇáÌåÇÒ. ßãÇ
áÇÍÙäÇ ä
ÇáäÊÇÆÌ
ÇáãÍÕá
ÚáíåÇ í
ÇáÊÍáíá
ÞÑíÈÉ ÌÏÇ ãä
ÇáäÊÇÆÌ
ÇáãÍÓæÈÉ
ÈÇáØÑíÞÉ
ÇáÊÞáíÏíÉ. ??I E?
C?EIIC? ? ???? ??E ?? ??? C???I?E C????C????E E??C?? C?E???? E??C?IE C??C??E
CamWorks E?I? C?E???? E?.
|