Conclusion
L'étude thermodynamique nous a permis de créer un
modèle relationnel pouvant régir le fonctionnement de
l'aérocondenseur.
Dans la suite du projet, nous allons nous baser sur ce
modèle pour préparer les diagrammes et séquences de
fonctionnement de l'équipement et élaborer le système
d'automatisme.
Chapitre III
SYSTEME DE CONTROLE,
COMMANDE ET SUPERVISION
Introduction
Après la description du fonctionnement de
l'équipement, nous allons procéder à son automatisation,
le système que nous allons installer démarrera avec la mise en
service de l'unité.
Dans ce chapitre, nous allons présenter l'architecture du
système que nous avons choisi pour le contrôle, la commande et la
supervision de l'unité d'aérocondenseur.
Par la suite, nous allons définir les documents utiles
à cette étape et nous allons réaliser des diagrammes
logiques de fonctionnements des différentes parties de
l'équipement.
1 Système de contrôle, commande et
supervision SCADA
Nous allons utiliser le système SCADA pour le
contrôle, la commande et la supervision de l'unité
aérocondenseur ;
L'architecture du système est la suivante :
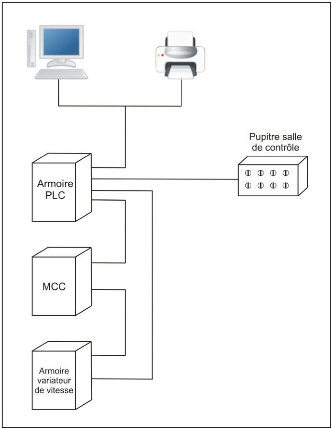
Figure 34 : Architecture du système de commande,
contrôle et supervision
Armoire PLC : elle regroupe deux automates A et B, les
cartes des entrées/sorties analogiques et numériques, les cartes
de communication ainsi que les borniers de connexion.
MCC (Motor Control Center) : regroupe les
départs moteurs, les protections contre les surcharges et
défauts, les RMF (Relais Multi Fonction), les CPI (Contrôleur
Permanant d'Isolement) et les relais auxiliaires.
Armoire variateur de vitesse : contient les variateurs
de vitesse des moteurs électriques. Pupitre : contient les
sélecteurs AUTO/MANU et le bouton AU et se trouve dans la salle de
commande.
2 Présentation de l'automate
2.1 Architecture des automates programmables
De forme compacte ou modulaire, les automates sont
organisés suivant l'architecture suivante :
· Un module d'unité centrale ou CPU, qui assure
le traitement de l'information et la gestion de l'ensemble des unités.
Ce module comporte un microprocesseur, des circuits périphériques
de gestion des entrées/sorties, des mémoires RAM et EEPROM
nécessaires pour stocker les programmes, les données, et les
paramètres de configuration du système.
· Un module d'alimentation qui, à partir d'une
tension 220V/50Hz ou dans certains cas de 24V fournit les tensions continues +
/- 5V, +/-12V ou +/-15V.
· Un ou plusieurs modules d'entrées `Tout Ou Rien'
(TOR) ou analogiques pour l'acquisition des informations provenant de la partie
opérative (procédé à conduire).
· Un ou plusieurs modules de sorties `Tout Ou Rien'
(TOR) ou analogiques pour transmettre à la partie opérative les
signaux de commande. Il y a des modules qui intègrent en même
temps des entrées et des sorties. [10]
· Un ou plusieurs modules de communication comprenant
:
-Interfaces série utilisant dans la plupart des cas comme
support de communication, les liaisons RS-232 ou RS422/RS485 ;
-Interfaces pour assurer l'accès à un bus de
terrain ;
-Interface d'accès à un réseau Ethernet.
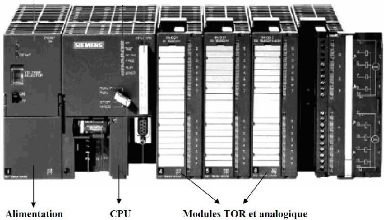
Figure 35 : Automate Programmable Industriel SIEMENS
[11]
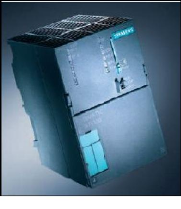
Figure 36 : API S7300 [11]
L'automate utilisé dans notre projet appartient
à la gamme SIMATIC S7 de SIEMENS ; le S7300
est un mini-automate modulaire pour les applications d'entrée et de
milieu de gamme, avec possibilité d'extensions jusqu'à 32
modules, et une mise en réseau par l'interface multipoint (MPI),
PROFIBUS et Industrial Ethernet.
|