|
République Tunisienne
Ministère de l'Enseignement
Supérieur
Et de la Recherche Scientifique Université de
Sousse
|
|
******
Institut Supérieur du Transport et de la
Logistique de Sousse
*****
PROJET DE FIN D'ETUDES
Présenté en vue de l'obtention de la
Licence Appliquée en Technologie de Transport et du la
Logistique
Spécialité :
Système Logistique et Transport
Sujet :
ELIMINATION DES GASPILLAGES AU
SEIN DE LA SECTION BLOC MOTEUR
Réalisé par : Ben Ameur Jawaher
Encadré par :
Encadrant académique : Mme .Ben Elhadj
Abir Encadrant professionnel : Mr. Laarif Wissem
Le projet a été préparé au sein de la
société «VEGE MOTEUR »
Année universitaire : 2017/2018
Dédicace
Du plus profond de mon coeur et avec tout le respect
que je vous dois, je dédie sincèrement ce
rapport de stage :
Ames chers parents Mohamed et
Dalila
Pour votre amour, votre
générosité et votre patience, Que
DIEU vous préserve longtemps et vous
accorde joie, bonheur et santé.
Ames chers frères et soeurs
Par ce que votre amour, vos tendresses et
vos encouragements m'ont toujours assuré un
grand soutien moral, je vous aime.
Atous les membres de ma famille pour leurs
amabilités à mon égard. Atous mes chers amis
et surtout Sghayer
Pour leurs sacrifices et leurs
encouragements illimités.
Atous ce qui m'aiment et à tous ceux
que j'aime et à tous ceux qui auront l'occasion
de lire ce travail.
Remerciements
Au terme du stage effectué à
VEGE MOTEUR, je vais adresser mes remerciements vifs aux tous ceux
qui ont contribué, aussi bien par leur patience morale ou
pratique, à l'élaboration et au déroulement
de ce stage dans les meilleures conditions.
Je tiens, en particulier, à remercier
et à exprimer ma profonde gratitude
à Mme. Ben Elhadj Abir en tant qu'encadreur qui,
de sa
part, n
|
'a pas cessée de me guider et
qui a contribué à la réalisation
finale
|
de ce rapport en m'apportant le soutien morale et
matériel nécessaire.
Ainsi, j'aime bien adresser mes remerciements les plus
chaleureux et les plus distingués à mon
encadreur professionnel Mr.Laarif Wissem Responsable
développement qui m'a fourni de l'aide durant
toute la période de projet et aux
personnels de service logistique,
production et qualité sans exception
qui m'ont rendu le stage aussi agréable
qu'il l'a été.
Finalement, je vais adresser des remerciements
chaleureux aux membres du jury pour leurs attentions, leurs conseils
et leurs différents
critiques
Sommaire
Introduction générale 1
Chapitre I : Présentation de VEGE MOTEURS
2
I. Présentation de VEGE MOTEURS 3
II. Processus de production 9
Chapitre II : La logistique de production
15
I. La logistique de production 16
II. Définition de gaspillage et leurs types 17
III. Lean : Historique et définition
18 Chapitre III : L'étude de l'existant et la mise en place
de la méthode « 5S » au sein de la
section Bloc Moteur 22
I. Étude de l'existant 23
II. Calcul du temps réels : 29
III. Les solutions adéquates 37
Conclusion générale 49
Webographies 50
ANNEXE 51
Liste des tableaux
TABLEAU1 : LES PRODUITS DE VEGE 7
TABLEAU 2 : LES NOMBRES DES POSTES ET DES EFFECTIFS 25
TABLEAU 3 : DONNEES COLLECTEES SUR LES CAUSES DE GASPILLAGE
27
TABLEAU 4: CLASSIFICATION DES CAUSES DE GASPILLAGE PAR
CATEGORIE 28 TABLEAU 5 : LA QUANTITE DEMANDEE DE DIFFERENTES REFERENCES
PRODUIT 29 TABLEAU 6 : COMPARAISON ENTRE LE TEMPS REEL ET
LE TEMPS STANDARD
POUR LE BLOC1 31 TABLEAU 7: COMPARAISON ENTRE LE TEMPS REEL
ET LE TEMPS STANDARD
POUR LE BLO 32 TABLEAU 8: LA COMPARAISON ENTRE LE TEMPS
REEL ET LE TEMPS
STANDARD POUR LE BLOC3 33 TABLEAU 9 : COMPARAISON ENTRE LE
TEMPS REEL ET LE TEMPS STANDARD
POUR LE BLOC1 34 TABLEAU 10 : COMPARAISON ENTRE LE TEMPS
REEL ET LE TEMPS STANDARD
POUR LE BLO 35 TABLEAU 11 : COMPARAISON ENTRE LE TEMPS REEL
ET LE TEMPS STANDARD
POUR LE BLOC3 36
Listes des figures
FIGURE1 : LA PHOTO REELLE DE VEGE MOTEUR EN 1978 4
FIGURE2 : LES CLIENTS DE VEGE 4
FIGURE3 : LA FICHE SIGNALETIQUE DE VEGE MOTEUR 5
FIGURE4 : L'ORGANIGRAMME DE VEGE MOTEUR 7
FIGURE5 : LES CERTIFICATS DE VEGE 8
FIGURE 6 : LA CARTOGRAPHIE DU PROCESSUS 9
FIGURE 7 : LE CYCLE DE PRODUCTION DE VEGE 14
FIGURE 8: LA MODELISATION DE LA SECTION BLOC MOTEUR 24
FIGURE 9 : DIAGRAMME D'ISHIKAWA 26
FIGURE 10 : DIAGRAMME DE PARETO 29
FIGURE 11: PARETO DE TYPES DE BLOC LES PLUS DEMANDEES 31
FIGURE 12: L'ECART ENTRE LE TEMPS REEL ET LE TEMPS STANDARD
POUR LE BLOC1 32
FIGURE 13: L'ECART ENTRE LE TEMPS REEL ET LE TEMPS STANDARD
POUR LE BLO 33
FIGURE 14: L'ECART ENTRE LE TEMPS REEL ET LE TEMPS STANDARD
POUR LE BLOC 3 34
FIGURE15: L'ECART ENTRE LE TEMPS REEL ET LE TEMPS STANDARD
POUR LE BLOC 1 35
FIGURE 16: L'ECART ENTRE LE TEMPS REEL ET LE TEMPS STANDARD
POUR LE BLOC 2 36
FIGURE 17: LA COMPARAISON ENTRE LE TEMPS REEL ET LE TEMPS
STANDARD POUR LE BLOC 3 37
FIGURE 18 : LES « 5S » 38
FIGURE 19: DEBARRASSER 38
FIGURE 20: RANGER 39
FIGURE21: NETTOYER 40
FIGURE 22: STANDARDISER 40
FIGURE23 : MAINTENIR 41
FIGURE 24 : LE GRAPHE DE L'ORGANISATION REELLE DE LA SECTION
42
FIGURE25: L'ORGANISATION REELLE DE LA SECTION 45
FIGURE 26 : LE GRAPHE DE L'ORGANISATION PROPOSEE DE LA SECTION
45
FIGURE 27: LA PROPOSITION DE LA NOUVELLE ORGANISATION DE LA
SECTION 48
Page 1
Introduction générale
La fonction production est la pierre angulaire de l'entreprise.
Qu'il s'agisse d'une société de Services ou d'une compagnie
manufacturière, le succès d'une entreprise est directement
lié à sa capacité de maintenir de façon constante
une production de qualité supérieure à moindre coût.
Toute déficience dans la dynamique de fabrication ou de livraison du
produit peut entraîner des rejets coûteux, des coûts
supplémentaires ou des plaintes qui font un tort considérable
à l'entreprise.
De plus, une nouvelle logique voit le jour sous l'effet
conjugué des exigences accrues des clients et d'une concurrence de plus
en plus féroce. Il ne s'agit plus de proposer un produit mais de
concevoir une offre complète sur mesure, sans défauts et dans les
plus brefs délais. Pour ce faire, l'entreprise doit se focaliser sur la
valeur ajoutée du produit, et donc produire au plus juste, avec
l'élimination de tous les gaspillages, et de toutes les
opérations sans valeur ajoutée.
Parmi les méthodes qui augmentent la
performance de telle entreprise, on peut citer la philosophie de « LEAN
MANUFACTURING » qui est certainement souhaitable en raison de ces nombreux
avantages (gain de temps, éliminer le gaspillage de temps, meilleur
ciblage, diffusion plus large de l'information, diminution de stock, etc.).
Dans le cadre de collaboration entre la
société VEGE MOTEURS (industrie de
rénovation des moteurs) représentée par le bureau de
développement et l'institut de Transport et logistique de
Sousse, représentée par le département de
système de transport et de logistique, Ce projet s'intitule
« et la mise en place de la méthode 5S au niveau de la section bloc
moteur ». L'objectif de ce travail est d'éliminer le gaspillage de
temps dans la section et l'organisation du poste de travail.
Ce travail portera trois chapitres principaux, nous
commençons par le premier chapitre qui trait la description de
l'entreprise, ainsi que ses sections. Dans le deuxième chapitre une
étude théorique sur la logistique de production, le concept
« Lean Manufacturing » .Ainsi que nous nous intéresserons sur
la méthode 5S. En ce qui concerne le troisième chapitre nous
avons trois grandes parties : La première portera sur le diagnostic de
l'existant et l'étude du temps perdus de la section bloc, la
deuxième partie est consacrée à l'application de la
méthode « 5S » .Pour terminer avec notre proposition d'une
nouvelle organisation dans la section.
Jawaher ben Ameur
Page 2
Chapitre I
Présentation de VEGE
MOTEURS
Jawaher ben Ameur
Page 3
Introduction
Dans ce chapitre, nous allons commencer par la
présentation de la société VEGE MOTEUR, son domaine de
travail, ses activités, ses clients et ses objectifs.
I. Présentation de VEGE MOTEURS
VEGE Moteurs est le leader du segment de son activité,
le premier dans le marché Européen, spécialisé dans
le secteur rénovation et la vente de moteurs, culasses, pompes
injections, frein et pièces moteurs pour l'industrie automobile, le
développement techniques de réparation et modification des
moteurs, pièces et composants.
Aujourd'hui,l'entreprise dispose d'un programme de fabrication
diversifié comprenant les marques européennes, américaines
et japonaises les plus connus :VOLVO, RENAULT, PEUGEOT, FIAT, CITROEN,
TOYOTA...
La seule unité de production est installée en
Tunisie à kalaa kebira-sousse et elle posséde un large
réseau de distribution au marché européen dont 7 points de
vente :
· France
· Angleterre
· Suéde
· Espagne
· Italie
· Allemagne
· Holland
1. Historique
En 1981 : Début de la première production de
moteurs Citroën 2CV air refroidi.
En 1985 : Début de la production de moteurs a essence de
Renault « Types A, B, C ».
En 1989 : Début de la production de moteurs a essence de
Peugeot « Types XV, XW ».
En 1990 : Début de la production des premières
moteurs Diesel« Peugeot, Renault et
Citroën ».
En 2001 : Début de la production des combustibles pompes
Delphi.
En 2004 : Début de la production des combustibles pompes
électroniques.
En 2005 : VEGE fusionne avec Continental Engins Groupes Ltd
(CEL).
En 2007 : Contrat avec GM (General Motors) pour la remise a neuf
des moteurs.
Jawaher ben Ameur
En2009 : Contrat avec PSA (Constructeur automobile
français Peugeot, Citroën) pour la
fabrication des composants diesel (carburants pompes Bosch et
Siemens).
En 2010 : Mise en production de turbocompresseurs.
En 2014 : Mise en production des boites vitesses
En 2017 : Mise en production des étriers des freins.
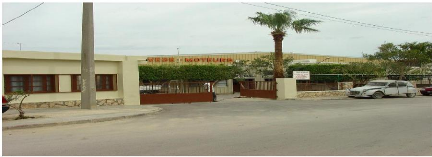
Figure1 : la photo réelle de
VEGE MOTEUR en 1978
2. Clientèle de VEGE :
Notons par ailleurs, que la société dispose d'un
nombre important de partenaires et clients étrangers. VEGE est
également le premier fabricant des moteurs pour le compte des
principales marques européennes.
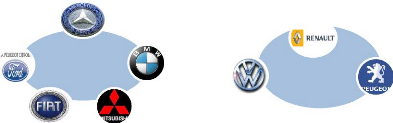
les clients
les clients divers
principaux
Page 4
Figure2 : les clients de
VEGE
Jawaher ben Ameur
3. Fiche signalétique :
La figure présente des informations
générales sur la société VEGE MOTEUR.
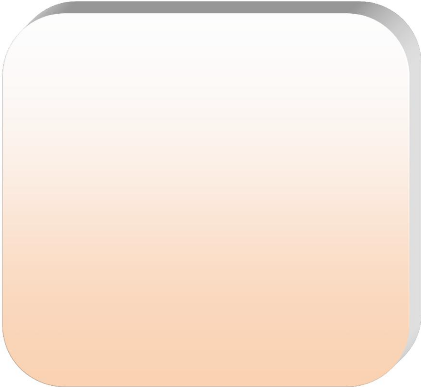
La raison social : VEGE MOTEURS
Nationalité : Néerlandaise
Date d'entrée en production :
15/08/1975
L'adresse de siège sociale : Rue 9 avril
1938 kalaa kébira-Sousse 4060
Statut juridique : société
anonyme
Nom de dirigeant : Fred Helder
Secteur d'activité : industrie
automobile
Capital sociale : 1 500 000 DT
Chiffre d'affaires : 15 000 000 DT
Marché : totalement exportatrice
Code TVA : 4774Kam000
Numéro de téléphone :
73253068
Figure3 : la fiche signalétique de VEGE
MOTEUR
Page 5
Jawaher ben Ameur
4. L'organigramme de VEGE MOTEUR

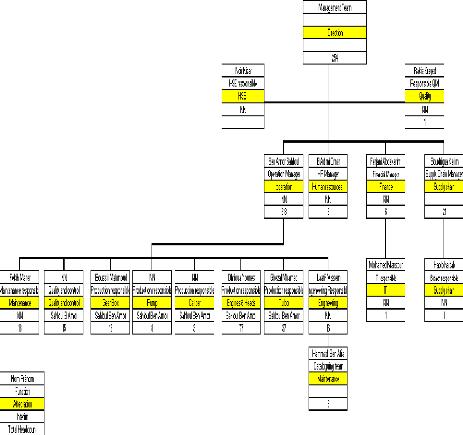
Page 6
Jawaher ben Ameur
Page 7
Figure4 : L'organigramme de VEGE MOTEUR
5. Les Produits de VEGE :
Ce tableau présente les différents produits de VEGE
et les quantités vendus en 2017 :
Tableau1 : les produits de VEGE
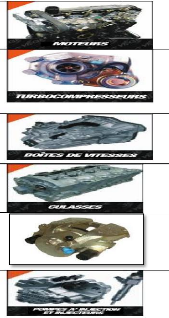
Produits
Moteur
Aperçu
Quantités vendues annuelles
5760
Turbocompresseur
Boites de vitesse
Culasse
Etrier de frein
Pompe à injection
2944
25
2420
100 000
6363
6. La qualité comme facteur clefs de succès
de VEGE :
« Toujours plus de qualité, de productivité,
de formation et de motivation ! » : est la stratégie axiale de
VEGE. La société est certifiée ISO 9000 : 2008 et ISO TS
16942 et a été désignée meilleur site de
l'année 2009 au sein du groupe. Son Management, aujourd'hui totalement
tunisien, met en oeuvre les techniques les plus récentes de gestion de
la production, de système qualité et de responsabilisation du
personnel.
Jawaher ben Ameur
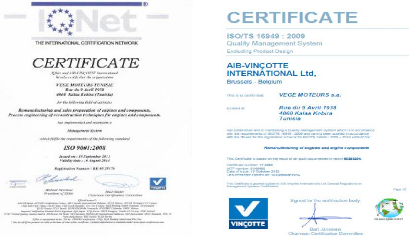
Page 8
Figure5 : les certificats de VEGE
7. Le7. s objectifs de VEGE MOTEURS Les
objectifs principaux de VEGE sont :
Satisfaire ses clients et ses employés.
Avoir des produits de bonne qualité, à juste
à temps et à moindre coût en se basant sur
la créative et l'esprit d'équipe.
Améliorer les conditions de travail en appliquant la
discipline des 5S.
Améliorer la communication et la motivation.
Cerner et résoudre les problèmes à
l'origine.
Encourager les décisions créatives axées sur
l'amélioration continue.
Mettre en place une organisation apprenante, et créer un
esprit de compétition.
Garantir un respect de l'homme, en responsabilisant mutuellement
l'ensemble du
personnel.
Jawaher ben Ameur
Page 9
8. La cartographie du processus :
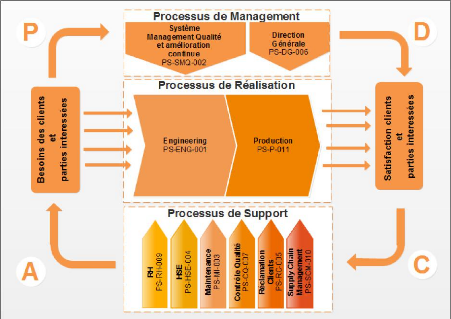
Figure 6 : la cartographie du processus
II. Processus de production
La production de VEGE est basée principalement sur les
vieux moteurs et turbos parvenus de la maison mère à Hollande
après leur collecte en Europe. Les vielles matières feront
l'objet principal des travaux de transformation actuelles (pour commande en
cours) ou future (juste stockée pour le besoin des commandes futures). A
sa réception, la matière première va être
classée selon le programme de production (placée au magasin ou
introduite directement au cycle de transformation). Le circuit passe par les
étapes suivantes :
Jawaher ben Ameur
Page 10
1. Section Démontage moteur:
Dès leur arrivée, les moteurs reçoivent un
code VEGE, une sorte d'identifiant au sein de la société, puis
suivant le besoin de production nous faisons passe les moteurs pour les
démonter. Ainsi, nous séparons les différentes parties du
moteur et leurs pièces.
1. Démontage couvre soupape
2. Démontage distribution :
V' Démontage pignon arbre à came
V' Démontage de tendeur, courroie, pompe
à eau
3. Démontage culasse
4. Démontage carté d'huile
5. Démontage type de jauge
6. Démontage pompe à huile
7. Démontage les chapeaux de ligne vilebrequin
8. Démontage vilebrequin
9. Démontage bille et piston
2. Section Nettoyage :
Arrivées après le démontage, les
différentes parties des moteurs doivent être nettoyées
avant de subir les procédés requis.
En effet, pour se débarrasser des huiles, graisse,
poussière, traces de gaz d'échappement... nous utilisons le savon
SD15 + eau dans un grand bain pour nettoyer les pièces en acier et en
fonte, et le savon neural + eau pour les pièces aluminiums.
3. Section culasse :
La culasse est la partie supérieure, la plus souvent
démontable, d'un moteur à pistons alternatifs. Elle ferme le haut
des cylindres. Sur certains moteurs, les soupapes d'admission et
d'échappement y sont logées.
Après le démontage du moteur et le lavage de
différentes pièces, les culasses viennent dans leur section pour
subir la procédure de rénovation. La première étape
dans la section culasse
Jawaher ben Ameur
Page 11
est le brossage, il consiste à débarrasser la
culasse des résidus de nettoyage, après vient l'étape
d'identification dont le but est de contrôler trois choses :
· L'état général de la culasse,
fissures, endommagements.
· La planéité de la surface du plan de
joint.
· La hauteur de la culasse.
C'est à ce niveau que nous identifions les culasses
fissurées et les culasses non fissurées, une culasse
fissurée doit être soudée, le soudage déclenche une
suite d'opérations outre que celles réalisées sur une
culasse non fissurée car le soudage nécessite des travaux de
préparations appelées travaux avant soudure.
4. Section de rectification :
Les éléments qui subissent une rectification sont
:
· Vilebrequins
· Arbre à cames,
· Soupapes,
· Bielles
5. Section bloc moteur :
Le bloc cylindre, aussi appelé bloc-moteur, constitue
le bâti du moteur à piston dont la partie intérieure est
usinée pour former les cylindres ou les logements de chemises s'il
s'agit d'un moteur à chemises rapportées. Les opérations
de la section sont :
· préparation bloc moteur
· honage ligne
· Alésage cylindre
· Honage cylindre
· Montage bague
· Dressage bloc
· Lavage tripentine
· Lavage final
Jawaher ben Ameur
Page 12
6. Section montage moteur :
Le montage se fait sur des tables avec des supports qui sont
accrochés aux elles. Nous commençons le montage par la fixation
des moteurs sur le support puis nous faisons le montage par ordre de toutes les
autres pièces :
· Montage des gicleurs d'huiles
· Montage coussinet vilebrequin
· Montage vilebrequin
· Vérification jeu fonctionnel de vilebrequin
· Montage des bielles sur le piston
· Contrôle du dépècement du piston
· Montage des plaques portes joint spi coté
distributeur et volant
· Montage des bouchons canal d'huile sur le bloc
· Montage de pompe à huile (chaine galet tendeur)
· Montage pignon de vilebrequin
· Montage de carte d'huile
· Montage joint de culasse
· Montage culasse
· Montage pignon arbre à came coté
distribution
· Montage pompe à eau, galet tendeur, roue
tendeur
· Montage des gougeons sur culasse
· Montage tube d'eau sur culasse
· Montage couvre soupape
7. Section banc d'essai :
A cette section on teste les moteurs nus pour voir les
défauts du lors du montage ou les défauts de réparation.
Après l'essai du moteur on doit vider l'huile pour contrôler s'il
y a un mélange d'eau et d'huile
· Contrôle au banc d'essai.
· Contrôle bruit
· Contrôle endommagement
· Contrôle fuite d'huile
Jawaher ben Ameur
·
Page 13
Contrôle fuite compression
· Contrôle fuite d'eau
· Contrôle fuite carburant
· Contrôle canaux d'admission
· Contrôle canaux d'échappement
· Contrôle pompe d'injection
· Contrôle de la pression d'huile
8. Section de contrôle :
· Contrôle de piston :
· Contrôle état générale puis
la référence
· Contrôle l'épaisseur du segment
· Contrôle du diamètre extérieur du
piston
· Contrôle la hauteur de piston
· Contrôle culasse :
· Contrôle type
· Contrôle plaque et numéro série
· Contrôle lavage et peinture
· Contrôle plan de joint
· Contrôle coté collecteur
· Contrôle trous taraudés
· Contrôle trou de bougie et injecteur
· Contrôle du goujon
· Contrôle montage bouchon de canal d'huile
· Contrôle bague d'arrêt soupape
· Contrôle arbre à came
· Contrôle soudure
Jawaher ben Ameur
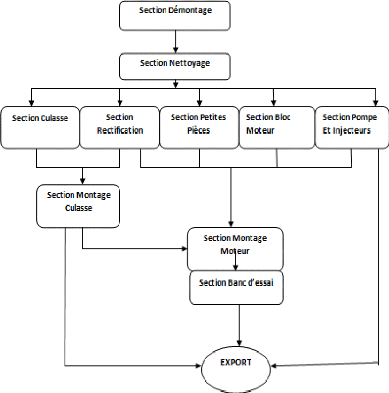
Page 14
Figure 7 : le cycle de production de VEGE
Conclusion
Dans ce chapitre, nous avons présenté la
société dans laquelle nous avons effectué ce stage. Pour
bien étudier notre problématique dans l'entreprise on peut
utiliser des outils de la philosophie Lean Manufacturing. Dans notre projet
nous avons intéressé à la méthode « 5S »,
et pour identifier les causes de notre problématique nous avons
utilisé le diagramme d'ISHIKAWA.
Jawaher ben Ameur
Chapitre II
La logistique de production
Page 15
Jawaher ben Ameur
Page 16
Introduction
Dans ce chapitre nous allons définir la logistique de
production, les différents types de gaspillages, quelques
méthodes de la gestion de production puis nous nous
s'intéresserons sur la méthode 5S qui occupe une place
particulière par compromis idéal qu'il offre du fait de la
simplicité de son concept et de son efficacité.
I. La logistique de production
En observant la logistique de production comme une partie de
la chaine logistique, la définition que l'on obtient est la suivante
:
« la logistique de production repose sur la logistique
d'entreprise, la totalité des actions et des mesures en découlant
pour assurer un flux optimal d'information, de matériel et de valeurs
dans le processus de transformation de la production »[1].
La logistique de production exerce une fonction de
coordination axée sur le flux dans le cadre de l'économie de
production. Elle doit ainsi contribuer à l'atteint
d'amélioration, de simplification et d'économies dans le secteur
de la production.
En détail, la logistique de production concerne les
éléments suivants :
- Amélioration de la production « proche » du
client
- Augmentation de la flexibilité
- Réduction des temps de passage
- Réduction des stocks
- Gestion optimale des voies de transport de la production
- Réduction de la largeur de la gamme, du nombre de
versions et de la diversité des pièces
- Amélioration de la taille des lots
- Diminution des couts de fabrication
La logistique de production a pour but principal l'orientation
de la production selon les besoins du marché et les objectifs de
l'entreprise. Pour atteindre ce but, des stratégies de production sont
développées. Elles doivent contribuer à l'organisation
optimale des procédés de planification et de contrôle de la
production ainsi qu'à la création de conditions cadres
avantageuses à cet effet [1].
Jawaher ben Ameur
Page 17
? Pour atteindre le but de la logistique de production on va
définie la cause du dysfonctionnement d'un chaine de production dans une
entreprise qu'est le gaspillage et sont sept sources.
II. Définition de gaspillage et leurs types
1. Définition
Appelé « Muda »en japonais ou la non-valeur
ajoutée (NVA) « non added value » en anglais, comprend les
opérations qui engagent les ressources sans créer de valeur
ajoutée. Ces opérations situées dans l'entreprise et dans
la chaine logistique sont jugées inutiles par le client qui n'a pas
envie de les payer [2].
2. Les différents types de gaspillage
1. La surproduction : est la production trop
élevée ou effectuée trop tôt par rapport aux besoins
qui entraine la nécessité de stocker.
2. Le temps d'attente : les files d'attente d'en
cours, l'emploi inefficient du personnel, le manque d'équilibrage des
charges des machines, le temps d'attente de l'opérateur jusqu'à
la fin du travail de a machine.
3. Le transport inutile : le déplacement
inutile des objets, des personnes se des informations, le transport
supplémentaire pour la reprise des produits, les transports des produits
dans des endroits éloignés.
4. Les tâches inutiles : le dépassement
des spécifications du client qui provoque une augmentation des couts et
le ralentissement de la fabrication, l'emploi d'outils ou de procédures
inappropriés.
5. Les stocks excessifs : le niveau
élevée des stocks sans raison valable, les retards des flux
physiques et d'informations, le maintien et le contrôle des stocks.
6. les mouvements inutiles : la mauvaise organisation
des postes du travail qui manquent d'ergonomie, la nécessité de
chercher des pièces difficiles d'accès, les déplacements
excessifs entre les opérations, le déballage.
Jawaher ben Ameur
Page 18
7. la fabrication des produits
défectueux : les erreurs lors de la production, du travail
bureautique, de la distribution, les retouches, la transmission d'un
élément défectueux au poste en aval ou au client externe
[2].
> On comprendra donc que ces sept sources de
gaspillage peuvent engendrer d'énormes couts pour l'entreprise, sans
ajouter de valeur au produit.
III. Lean : Historique et définition
1. Historique :
Au lendemain de la seconde guerre mondiale, les industries
japonaises ont dû affronter la
Récession en repensant l'entreprise autrement. Face
à cette situation économique, Taiichi Ohno,
ingénieur industriel japonais et dirigeant de Toyota, a
inventé un concept pour réduire
Les coûts de production : le Toyota Production System
(TPS). Ce concept repose sur un
Système de production « au plus juste »
suffisamment flexible pour s'adapter aux fluctuations
Des commandes des clients, il consiste à :
V' Réduire les coûts
V' Eviter les gaspillages
V' Maintenir une qualité optimale
V' Produire en flux tendu
V' Prendre en compte les idées provenant du
terrain
V' S'améliorer continuellement
2. Définition
D'après l'ouvrage « système Lean, penser
l'entreprise au plus juste », le Lean est défini Comme « une
discipline industrielle qui ne s'acquiert que par la pratique et la
persistance. Il Ne s'agit pas simplement de « techniques » mais d'une
méthode globale de management qui Permet de maintenir l'entreprise sous
tension créative pour générer toujours plus de valeur
en
Éliminant les gaspillages [...] c'est autant une attitude
qu'un savoir-faire » (1).
Les gaspillages, mudas en japonais, ont été
identifiés par Taiichi Ohno qui en dénombre
Sept :
? Excès de production
? Circulation des machines et des hommes
? Opérations inutiles
? Mouvements inutiles
Jawaher ben Ameur
Page 19
? Accumulation de stocks et d'encours
? Non-conformités
? Inoccupation des machines ou des personnes
3. Les objectifs de Lean Manufacturing :
Un système ou une entreprise qui fonctionne en
Lean Manufacturing (appelée aussi Lean Production)
reçoit ses matières premières uniquement lorsqu'une
commande ferme est donnée par un client, fabrique ses produits finis ou
sous-ensembles juste à temps pour être vendus ou assemblés
en produits finis et finalement, livre au client uniquement lorsque ce dernier
en fait la demande.
La philosophie du Lean Manufacturing repose
sur la fabrication de plusieurs produits en petites quantités afin de
mieux répondre aux besoins des clients. Cette méthode s'appuie
sur l'amélioration continue de la qualité et de la
productivité dans toutes les activités de l'entreprise et est
soutenue par deux grands principes, l'élimination du gaspillage, partout
dans l'entreprise, et le respect de la personne.
4. Principes de base du Lean Manufacturing : Le Lean
Manufacturing est fondé sur 14 principes :
1. Fondez vos décisions sur une philosophie à
long terme, même au détriment des objectifs financiers à
court terme.
2. Organisez les processus en flux pièce à
pièce pour mettre autour les problèmes.
3. Utilisez des systèmes tirés pour
éviter la surproduction.
4. Lissez la charge de travail (Heijunka)
5. inculquez une culture de résolution
immédiate des problèmes, d'obtention de la qualité au
premier coup.
6. La standardisation des tâches est la base de
l'amélioration continuée et de la responsabilisation des
employés.
7. Utilisez des contrôles visuels pour qu'aucun
problème ne reste pas caché.
8. Utilisez uniquement des technologies fiables, longuement
éprouvées, qui servent vos collaborateurs et vos processus.
9. Former des responsables qui maîtrisent parfaitement
le travail, sans imprégnés de la philosophie et l'enseignent aux
autres
10. Formez des individus et des équipes exceptionnels,
qui appliquent la philosophie de votre entreprise.
Jawaher ben Ameur
11.
Page 20
respectez votre réseau de partenaires et de
fournisseurs en les encourageant et en les aidant à progresser.
12. Allez sur le terrain pour bien comprendre la situation
13. Décidez en prenant le temps nécessaire, par
consensus, en examinant en détail toutes les options. Appliquez
rapidement les décisions.
14. Devenez une entreprise apprenante grâce à la
réflexion systématique (Hansei) et à
l'amélioration continue (kaizen). [2]
5. Les méthodes de Lean :
Dans cette partie, nous avons présenté quelques
outils de Lean Mangement Qu'ont va les utiliser pour réduire le
gaspillage dans l'entreprise.
5.1. Diagramme d'ISHIKAWA
Le diagramme d'ISHIKAWA, dit aussi 5M, fournit une vision
globale des causes aboutissant à un effet, Il permet, en
conséquence, d'agir sur les causes à travers des solutions
correctives. Donc cet outil se présente donc sous la forme
d'arêtes de poisson. Il répertorie les causes inventoriées
selon la loi des 5M :
Matière : fournitures, matière première,
...
Milieu : localisation, aménagement, environnement
physique, ...
Méthode : instruction, mode opératoire, ...
Matériel : équipements, machines, outillage, ...
Main d'oeuvre : directe, indirecte, compétence,
qualification,... [3].
5.2. Les 5S :
Les premières lettres de 5 termes japonais (Seiri :
trier, Seiton : ranger, Seiso : nettoyer, Seiketsu : standardiser, Shitsuke :
respecter) qui ont pour objectif de ranger et nettoyer, et d'éliminer
ainsi les causes de nombreux petits problèmes sources de perte
d'efficacité. C'est une des premières méthodes à
mettre en oeuvre dans une démarche de Lean Manufacturing. Elle vise
aussi à changer la mentalité des opérateurs et de
l'encadrement [2].
La méthode des 5S va permettre:
Jawaher ben Ameur
- Construire un environnement de travail agréable, par
des règles simples, précises et efficaces.
- Réduire le gaspillage (des postes de travail bien
organisés réduisent les déplacements, les manutentions,
les gestes inutiles et donc les pertes de temps).
- Améliorer la sécurité des personnes, des
équipements.
- Développer l'esprit d'équipe.
Le déploiement du 5S doit être
intégré dans la politique de l'entreprise, ce n'est pas une
méthodologie à appliquer dans une période limitée,
c'est un travail continu, elle doit être soutenue par l'ensemble de la
direction.
Conclusion :
Dans ce chapitre, nous avons défini la logistique de
production, le gaspillage et ses sept sources. Aussi que la philosophie «
Lean Manufacturing », ses objectifs et leur principe. Puis nous avons
démontré les différentes méthodes de lean. Par
ailleurs nous étudierons la méthode qui on va utiliser au niveau
de la solution.
Comme la plupart des industries automobiles, VEGE MOTEUR
rencontre toujours des défaillances au niveau de sa maîtrise de
flux. Par conséquent nous essayerons par la suite de diagnostiquer
l'existant en adoptant les outils de lean Manufacturing puis nous allons
appliquer la méthode 5S.
Page 21
Jawaher ben Ameur
Page 22
Chapitre III :
L'étude de l'existant et la
mise en place de la
méthode « 5S » au sein de
la section Bloc Moteur
Jawaher ben Ameur
Page 23
Introduction
Dans ce chapitre, nous allons nous intéresser à
bien étudier la section bloc moteur. Nous allons commencer tout d'abord
par l'application des outils de diagnostic sur l'état existant pour
identifier la problématique et ses causes effets. Ensuite, nous allons
appliquer la méthode « 5S » pour améliorer la chaine de
production au sein de la section.
I. Étude de l'existant
Dès le départ de ce projet, nous avons
passé la plupart de temps de travail dans la section bloc moteur et cela
pour collecter les informations qui va nous permettre de compléter ce
travail. Ainsi, nous avons suivi les différentes étapes de
production afin de comprendre le processus de fonctionnement de la chaine. Nous
avons accompagné les responsables de méthodes et de production,
et nous avons supervisé le travail des opérateurs afin de
comprendre les tâches qu'ils effectuent et connaitre les contraintes
qu'ils rencontrent.
1. Diagnostic de la section bloc moteur :
Avant de procéder à une analyse des changements
d'envergure dans une société, une phase de diagnostic
s'avère indispensable. Cette phase consiste à analyser la
situation actuelle de l'entreprise. Elle nous mènera à une
identification des problèmes.
1.1. Les étapes de diagnostique
Pour réaliser l'analyse de la situation actuelle de
l'entreprise, nous avons suivi les étapes suivantes :
V' Recueil des informations
Durant cette étape nous avons essayé de suivre
une démarche basée sur l'observation et l'analyse des documents
et des historiques.
V' L'observation
Pendant cette période, nous avons passé les
premières semaines à observer le travail, les mouvements des
opérateurs et des ouvriers, nous avons essayé d'avoir une vision
de loin sur la section et nous avons commencé à s'approcher petit
à petit pour ne pas être dépassé par les
événements. Après avoir compris le fonctionnement
général de la section, nous avons
Jawaher ben Ameur
Page 24
commencé à visiter les postes, l'un après
l'autre en essayant de distinguer les taches réservées pour
chaque poste et les causes de ces affectations.
En fait, nous avons constaté que le nombre des
tâches est impressionnant et il faudra de temps pour mieux comprendre au
mieux les choses et déterminer les défaillances de l'existant.
En effet, nous avons commencé à communiquer avec
les cadres du bureau méthode et les ouvriers dans la section bloc pour
détecter les sources de gaspillage. On a fait l'étude poste par
poste pour bien préciser ces problèmes.
? L'analyse des documents et des
historiques
Là il s'agit de collecter les informations à
partir tous types de documents (plans, chiffres, notes, schémas,
procédures...).
Dans cette période, nous avons pris la liste des postes
réalisées de la section bloc et leurs durée et le nombre
des ouvriers dans chaque poste.
1.2. La modélisation de la section bloc Moteur
:
Dans cette partie, nous sommes appuyé sur un outil de
modélisation c'est le «Microsoft Office Word», Ce dernier vous
aidera à avoir une image approximative sur l'implantation des postes
dans la chaine, comprenant la modélisation de la section bloc avec les
différentes opérations.
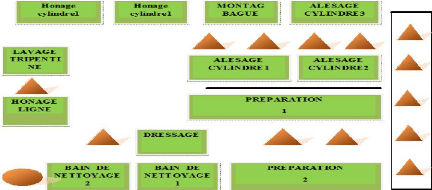
Figure 8: la modélisation de la section bloc
Moteur
Jawaher ben Ameur
Page 25
Tableau 2 : les nombres des postes et des
effectifs
Postes
|
Effectifs
|
Nombre de poste
|
Préparation
|
1
|
2
|
Honage ligne
|
1
|
1
|
Alésage cylindre
|
1
|
3
|
Montage pour bague
|
0
|
1
|
Dressage cylindre
|
1
|
1
|
Honage cylindre
|
1
|
2
|
Lavage tripentine
|
1
|
1
|
Lavage final
|
1
|
2
|
1.3. Diagramme de causes à effet « ISHIKAWA
»
Nous avons procédé dans ce qui suit à
chercher et analyser les problèmes qui constituent et
génèrent le gaspillage tout au long de la chaine de production
grâce au diagramme Ishikawa.
? Les facteurs influés sur la production
Le temps de production associé à un poste
donné correspond à la somme de toutes les
élémentaires qui lui sont affectées. Toutefois, ce temps
n'est pas fixe et peut être influencé par plusieurs facteurs. Ces
derniers dépendent de :
? Main d'oeuvre : dans la section, nous
trouvons des ouvriers de différente génération. Ils
existent ceux qui ont une expérience de vingt à trente ans et
ceux qui sont des nouveaux recrutés. Les ouvriers âgés ont
du métier et maitrisent beaucoup leurs tâches mais leurs
rendements sont en décroissance. Certains sont très proches
à la retraite, s'ennuient rapidement et n'acceptent ni
d'accélérer leur rythme ni de changer leurs modes de travail. Par
conséquent ils peuvent retarder la production.
? Machine : Réglage difficile pour
certaines machines peu prendre jusqu'à trente minutes pour fonctionner.
À cause de la défaillance d'un outillage (brosse spiral,
taraud,...), l'ouvrier passe son temps à trainer dans la section sous
prétexte de manque d'outillage.
Jawaher ben Ameur
Page 26
y' Matière : Il y'a des cas où
l'ouvrier se trouve en cas de rupture de stocks d'une matière
donnée et il doit attendre l'arrivée du stock du magasin. Aussi,
nous avons des défauts des stockages de matières premières
et des stocks encours élevés.
y' Milieu : Il y'a beaucoup des bruits et mal
nettoyé
y' Méthode : Mauvaise implantation de
l'usine, postes de travail non équilibrées et l'absence de
maintenance préventive
Pour bien identifier la cause nous avons
schématisé le diagramme ISHIKAWA.
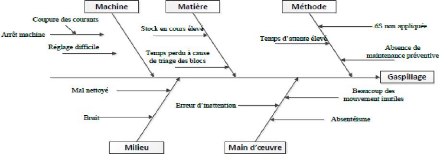
Figure 9 : Diagramme
d'ISHIKAWA
1.4. Diagramme Pareto :
Le diagramme de Pareto permet de mettre en évidence les
causes les plus importantes sur le nombre total d'effets et ainsi de prendre
des mesures ciblées pour améliorer une situation. Il nous servira
à classer les causes des gaspillages par ordre de gravité, ceci
imposera des priorités particulières afin de les
résoudre.
Méthode de construction du diagramme Pareto
:
1. Enumérer les différentes causes ou
problèmes
2. Quantifier l'importance de chacun
3. Déterminer le pourcentage de chacun par rapport au
total
4. Classer les pourcentages de chacun par valeurs
décroissantes
5. Déterminer une échelle adaptée pour
tracer le graphique
6. Choisir le « histogramme » comme type de graphique,
le plus grand à gauche
7. Ajouter la courbe de pourcentage cumulé sur le
même graphique
Jawaher ben Ameur
Page 27
Suite aux observations faites durant le premier mois du stage
; nous avons cité les différents problèmes
remarqués puis nous avons opté à la méthode de vote
pour déterminer l'ordre d'importance des causes de gaspillage. Pour le
faire, nous avons demandé au responsable de production de nous donner un
poids entre 1 et 10 à chaque cause, la cause qui fait la plus de
gaspillage aura le poids le plus haut.
|
Tableau 3 : Données collectées sur les
causes de gaspillage
|
|
Nr
|
Causes
|
5M
|
Poids
|
1
|
Pas très efficacement nettoyé
|
Milieu
|
8
|
2
|
Absence de maintenance préventive
|
Méthode
|
8
|
3
|
Recherche d'outillage
|
Main d'oeuvre
|
7
|
4
|
Arrêt machine (coupure du courant)
|
Machine
|
7
|
5
|
Réglage des machines difficile
|
Machine
|
6
|
6
|
5S non appliqué
|
Méthode
|
6
|
7
|
Poste de travail non agronomique
|
Méthode
|
6
|
8
|
Erreur d'inattention
|
Main d'oeuvre
|
6
|
9
|
Beaucoup des mouvements inutiles
|
Main d'oeuvre
|
6
|
10
|
Temps perdu à cause du triage des blocs
|
Matière
|
5
|
11
|
Temps d'attente élevé
|
Méthode
|
5
|
12
|
Stock en cours élevé
|
Matière
|
5
|
13
|
Mauvaise organisation
|
Méthode
|
5
|
14
|
L'absentéisme
|
Main d'oeuvre
|
5
|
TOTAL
|
|
|
86
|
Selon la méthode décrite ci-dessus nous avons
groupé les causes de gaspillage dans des catégories pour
faciliter leur traitement comme dans le tableau suivant
Jawaher ben Ameur
Page 28
Tableau 4: classification des
causes de gaspillage par catégorie
Nr
|
Causes
|
Poids
|
% Poids
|
% cumulé
|
1
|
Pas très efficacement nettoyé+5S non
appliqué
|
15
|
17%
|
17%
|
2
|
Absence de maintenance préventive +Réglage des
machines difficile
|
14
|
16%
|
33%
|
3
|
Recherche d'outillage+ Poste de travail non
équilibrés
|
13
|
15%
|
48%
|
4
|
Beaucoup des mouvements inutiles +Temps d'attente
élevé
|
11
|
13%
|
61%
|
5
|
Arrêt machine (coupure du courant)
|
7
|
8%
|
69%
|
6
|
Erreur d'inattention
|
6
|
7%
|
76%
|
7
|
Temps perdu à cause du triage des
blocs
|
5
|
6%
|
82%
|
8
|
Stock en cours élevé
|
5
|
6%
|
88%
|
9
|
Mauvaise organisation
|
5
|
6%
|
94%
|
10
|
L'absentéisme
|
5
|
6%
|
100%
|
TOTAL
|
86
|
100%
|
|
A partir du tableau précédent, il nous est devenu
possible de représenter le diagramme de Pareto sur Microsoft Excel tel
que le montre la figure suivante :
Jawaher ben Ameur
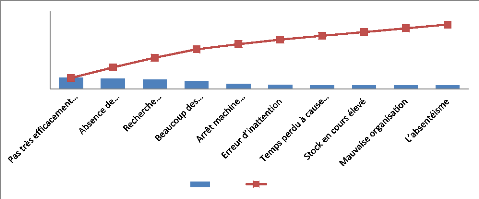
120%
100%
40%
80%
60%
20%
0%
17% 16% 15% 13% 8% 7% 6% 6% 6% 6%
Série1 Série2
Figure 10 : Diagramme de
Pareto
Interprétation :
Selon le principe Pareto seule 20% des causes
représentent 80% du gaspillage, nous devons donc dans notre cas agir en
premier lieu sur les causes majeurs pour garantir une amélioration
rapide et remarquable.
Nous devons déployer en priorité des actions
correctives pour résoudre les 4 causes principales.
II. Calcul du temps réels :
L'idée de cette méthode consiste à
décomposer, au début, l'ensemble des tâches
effectuées dans la réalisation d'un produit en tâches
élémentaires qui se répètent chaque fois.
Après pour chacune des tâches, nous avons
chronométré le temps d'exécution. Nous avons essayé
de prendre plusieurs mesures, qui sont trois blocs pour chaque type de
famille.
1. Identification de la référence à
étudier :
Le problème rencontré lors du
chronométrage c'est que nous avons a une diversité dans les
produits qui se fabriquent dans la section bloc, c'est que nous a met devant
l'outil « PARETO » pour l'exploiter afin de sortir
avec l'élément ou bien la référence sur laquelle le
chronométrage sera établis. La demande c'était le
critère de notre « PARETO », cette demande
est représentée sous forme d'un tableau appelée la suivie
de production.
Le tableau suivant représente chaque type de moteur en
fonction de la quantité Demandée :
Tableau 5 : la quantité
demandée de différentes références
produit
Jawaher ben Ameur
Page 29
les familles
|
Quantité
|
|
|
|
|
|
|
|
|
|
classe
|
|
|
|
|
|
|
|
|
|
|
|
|
|
|
|
|
|
|
|
|
peugeot\citroen_DV6 (4 cylindre)
|
50
|
Quantité cumuleé
50
|
%
14,33%
|
%cumuleé
14%
62%
|
peugeot\citroen_P22 (4 cylindre)
|
46
|
96
|
13,18%
|
28%
|
Opel_1.2 (4 cylindre)
|
39
|
135
|
11,17%
|
39%
|
Renault _ M9R (4
cylindre)
|
30
|
165
|
8,60%
|
47%
|
Renault _ G9U (4
cylindre)
|
27
|
192
|
7,74%
|
55%
|
|
|
|
|
|
A
|
VW\AUDIT_1.9 (4 cylindre)
|
24
|
216
|
6,88%
|
|
Ford_2.4 (4 cylindre)
|
23
|
239
|
6,59%
|
68%
|
Opel_1.4 (4 cylindre)
|
17
|
256
|
4,87%
|
73%
|
Renault_8140.43 (4 cylindre)
VW\AUDIT_ 2.5 (5 cylindre)
|
13
|
269
|
3,72%
|
77%
90%
|
|
10
|
279
|
2,87%
|
80%
|
Ford_1.8 (4 cylindre)
|
10
|
289
|
2,87%
|
83%
|
Renault_K9K (4 cylindre)
|
8
|
297
|
2,29%
|
85%
|
Mercedes _646.986 (4 cylindre)
Opel_1.0 (4 cylindre)
|
7
|
304
|
2,01%
|
87%
|
|
5
|
309
|
1,43%
|
89%
|
VW\AUDIT_2.0 (4 cylindre)
|
4
|
313
|
1,15%
|
|
B
|
Fiat\Opel_1.3 (4 cylindre)
|
4
|
317
|
1,15%
|
91%
|
Ford_1.0 (4 cylindre)
|
4
|
321
|
1,15%
|
92%
|
Nissan_YD25DDTI (4 cylindre)
|
3
|
324
|
0,86%
|
93%
|
Opel_1.7 (4 cylindre)
|
3
|
327
|
0,86%
|
94%
|
VW\AUDIT_1.2 ( 3
cylindre)
VW\AUDIT_1.6 (4 cylindre)
|
3
3
|
330
333
|
0,86%
0,86%
|
95%
95%
98%
|
Renault_F9Q (4 cylindre)
|
2
|
335
|
0,57%
|
96%
|
peugeot\citroen_DW10 (4 cylindre)
|
2
|
337
|
0,57%
|
|
VW\AUDIT_1.8 (4 cylindre)
|
2
|
339
|
0,57%
|
|
VW\AUDIT_1.4 (4 cylindre)
|
2
|
341
|
0,57%
|
|
|
|
|
|
|
peugeot\citroen_Dj5 (4 cylindre)
|
2
|
343
|
0,57%
|
|
BMW _ M47N (4
cylindre)
|
1
|
344
|
0,29%
|
|
|
peugeot\citroen_DW12 (4 cylindre)
peugeot\citroen_DV4 (4 cylindre)
Total
Jawaher ben Ameur
C 97%
97% 98% 99% 99% 99%
99% 100% 100% Page 30
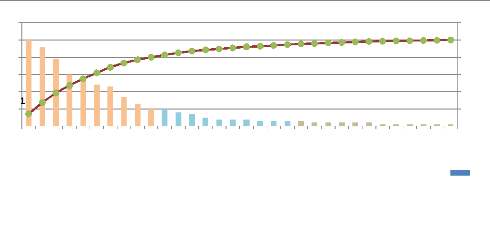
40
60
50
30
20
10
0
peugeot\citroen_DV6... peugeot\citroen_P22 (4... Opel_1.2 (4
cylindre) Renault _ M9R (4... Renault _ G9U (4... VW\AUDIT_1.9 (4... Ford_2.4
(4 cylindre) Opel_1.4 (4 cylindre) Renault_8140.43 (4... VW\AUDIT_ 2.5 (5...
Ford_1.8 (4 cylindre) Renault_K9K (4 cylindre) Mercedes _646.986 (4... Opel_1.0
(4 cylindre) VW\AUDIT_2.0 (4... Fiat\Opel_1.3 (4 cylindre) Ford_1.0 (4
cylindre) Nissan_YD25DDTI (4... Opel_1.7 (4 cylindre) VW\AUDIT_1.2 ( 3...
VW\AUDIT_1.6 (4... Renault_F9Q (4 cylindre)
peugeot\citroen_DW10... VW\AUDIT_1.8 (4... VW\AUDIT_1.4 (4...
peugeot\citroen_Dj5 (4... BMW _ M47N (4... Mercedes _OM612 (4...
Mercedes_ 646.982 (4... Ford_1.6 (4 cylindre)
peugeot\citroen_DW12... peugeot\citroen_DV4...
4%
28%
39%
47%5
5%62%68%7
3%77%80%83%85%87%89%90%91%92%93%94%95%95%96%97%97%98%98%99%99%99%99%100%100%
80%
40%
0%
60%
20%
120%
100%
fré...
Figure 11: Pareto de types de bloc les
plus demandées
La classe A comporte 10 familles de produit mais à cause
de la grande taille des familles nous avons choisir de travailler sur les deux
premières qui sont les plus importantes.
2. Chronométrage :
Apres l'identification de la référence critique,
maintenant nous passons au terrain pour le chronométrage, nous
définissons définis le nombre 3 comme le nombre
d'échantillon et nous commençons le chronométrage par la
première famille :
? Peugeot DV6 :
Tableau 6 : comparaison entre le temps
réel et le temps standard pour le bloc1
Opérations
|
Le temps réel du bloc1- DV6/4585
|
Temps standards
|
Le temps perdu
|
Préparation bloc
|
41:57,0
|
31:48,0
|
10:09,0
|
Honage ligne
|
15:53,0
|
11:23,0
|
04:30,0
|
Alésage cylindre
|
26:47,0
|
26:41,0
|
00:06,0
|
Dressage
|
23:15,0
|
10:34,0
|
12:41,0
|
Honage cylindre
|
33:46,0
|
16:39,0
|
17:07,0
|
Lavage tripentine
|
09:19,0
|
10:38,0
|
|
Lavage final
|
19:01,0
|
18:43,0
|
00:18,0
|
Jawaher ben Ameur
Page 31
Totale
|
02:49:58
|
02:06:26
|
43:32,0
|
|
|
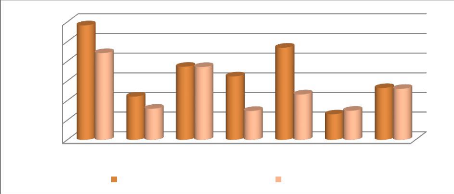
43:12,0
07:12,0
00:00,0
36:00,0
28:48,0
21:36,0
14:24,0
1 2 3 4 5 6 7
Le temps réel du bloc1- DV6/4585 Temps standars
Figure 12: l'écart entre le
temps réel et le temps standard pour le bloc1
Remarque : Dans la majorité des
opérations, nous trouvons que le temps réel dépasse le
temps standard or le temps perdu total des opérations est [44(min)] pour
seulement un bloc.
Tableau 7: comparaison entre le temps
réel et le temps standard pour le bloc2
Opérations
|
Le temps réel du bloc2- DV6/4585
|
Temps standard
|
Le temps perdu
|
Préparation bloc
|
41:26,0
|
31:48,0
|
09:38,0
|
Honage ligne
|
15:49,0
|
11:23,0
|
04:26,0
|
Alésage cylindre
|
18:56,0
|
26:41,0
|
|
Dressage
|
13:25,0
|
10:34,0
|
02:51,0
|
Honage cylindre
|
18:26,0
|
16:39,0
|
01:47,0
|
Lavage tripentine
|
08:32,0
|
10:38,0
|
|
Lavage final
|
17:04,0
|
18:43,0
|
|
Totale
|
02:13:38
|
02:06:26
|
07:12,0
|
Jawaher ben Ameur
Page 32
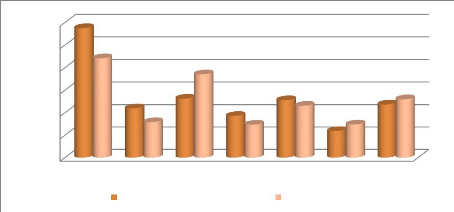
43:12,0
07:12,0
00:00,0
36:00,0
28:48,0
21:36,0
14:24,0
1 2 3 4 5 6 7
Le temps réel du bloc2- DV6/4585 Temps standars
Figure 13: l'écart entre le
temps réel et le temps standard pour le bloc2
Remarque : le temps réel est
supérieur au temps standard or le temps perdu total des
opérations est [7(min)] pour seulement un bloc.
Tableau 8: la comparaison entre le temps
réel et le temps standard pour le bloc3
Opérations
|
Le temps réel du bloc3- DV6/4585
|
Temps standard
|
Le temps perdu
|
Préparation bloc
|
42:02,0
|
31:48,0
|
10:14,0
|
Honage ligne
|
11:37,0
|
11:23,0
|
00:14,0
|
Alésage cylindre
|
22:50,0
|
26:41,0
|
|
Dressage
|
17:00,0
|
10:34,0
|
06:26,0
|
Honage cylindre
|
19:03,0
|
16:39,0
|
02:24,0
|
Lavage tripentine
|
09:29,0
|
10:38,0
|
|
Lavage final
|
17:18,0
|
18:43,0
|
|
Totale
|
02:19:19
|
02:06:26
|
12:53,0
|
Jawaher ben Ameur
Page 33
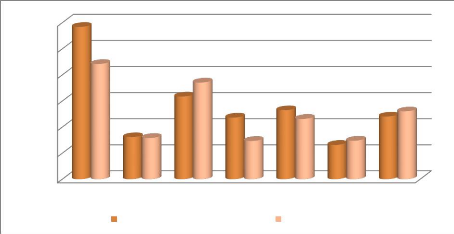
43:12,0
07:12,0
00:00,0
36:00,0
28:48,0
21:36,0
14:24,0
1 2 3 4 5 6 7
Le temps réel du bloc3- DV6/4585 Temps standars
Page 34
Figure 14: l'écart entre le
temps réel et le temps standard pour le bloc 3
Remarque : dans la majorité des
opérations , nous trouvons que le temps réel est supérieur
au temps standard or le temps perdu total des opérations est [13(min)].
Cette perte est due à la mauvaise implantation du poste et à la
recherche des outillages.
? La famille Peugeot P22 :
Tableau 9 : comparaison entre le temps
réel et le temps standard pour le bloc1
Opérations
|
Le temps réel du bloc1- P22/4073
|
Temps standard
|
Le temps perdu
|
Préparation bloc
|
39:43,0
|
24:16,0
|
15:27,0
|
Honage ligne
|
15:50,0
|
11:06,0
|
04:44,0
|
Alésage cylindre
|
26:21,0
|
22:40,0
|
03:41,0
|
Dressage
|
15:28,0
|
12:22,0
|
03:06,0
|
Honage cylindre
|
26:58,0
|
15:58,0
|
11:00,0
|
Lavage tripentine
|
11:46,0
|
11:51,0
|
|
Lavage final
|
14:11,0
|
16:27,0
|
|
Totale
|
02:30:17
|
01:54:40
|
35:37,0
|
Jawaher ben Ameur
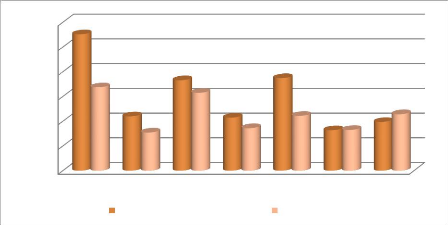
43:12,0
07:12,0
00:00,0
36:00,0
28:48,0
21:36,0
14:24,0
1 2 3 4 5 6 7
Le temps réel du bloc1- P22/4073 Temps standars
Page 35
Figure15: l'écart entre le temps
réel et le temps standard pour le bloc 1
Remarque : Dans la majorité des
opérations , nous trouvons que le temps réel est supérieur
au temps standard or le temps perdu total des opérations est
[36(min)]pour seulement un bloc. C'est une valeur élevée, et cela
est due à le réglage difficile des machines, le temps de
changement d'outillage et à la recherche des outillages.
Tableau 10 : comparaison entre le temps
réel et le temps standard pour le bloc2
Opérations
|
Le temps réel du bloc2- P22/4073
|
Temps standard
|
Le temps perdu
|
Préparation bloc
|
43:17,0
|
24:16,0
|
19:01,0
|
Honage ligne
|
12:34,0
|
11:06,0
|
01:28,0
|
Alésage cylindre
|
22:40,0
|
22:40,0
|
00:00,0
|
Dressage
|
12:59,0
|
12:22,0
|
00:37,0
|
Honage cylindre
|
18:23,0
|
15:58,0
|
02:25,0
|
Lavage tripentine
|
11:49,0
|
11:51,0
|
|
Lavage final
|
13:36,0
|
16:27,0
|
|
Totale
|
02:15:18
|
01:54:40
|
00:20:38
|
Jawaher ben Ameur
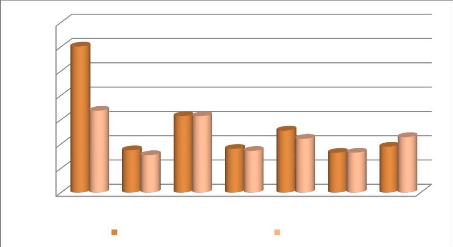
43:12,0
07:12,0
00:00,0
50:24,0
36:00,0
28:48,0
21:36,0
14:24,0
1 2 3 4 5 6 7
Le temps réel du bloc2- P22/4073 Temps standars
Page 36
Figure 16: l'écart entre le
temps réel et le temps standard pour le bloc 2
Remarque : Dans la majorité des
opérations , nous trouvons que le temps réel est supérieur
au temps standard or le temps perdu total des opérations est
[20(min)]pour seulement un bloc. Cette perte est due à la mauvaise
implantation du poste et à la recherche des outillages.
Tableau 11 : comparaison entre le temps
réel et le temps standard pour le bloc3
Opérations
|
Le temps réel du bloc3- P22/4073
|
Temps standard
|
Le temps perdu
|
Préparation bloc
|
35:44,0
|
24:16,0
|
11:28,0
|
Honage ligne
|
12:09,0
|
11:06,0
|
01:03,0
|
Alésage cylindre
|
22:05,0
|
22:40,0
|
|
Dressage
|
12:47,0
|
12:22,0
|
00:25,0
|
Honage cylindre
|
18:36,0
|
15:58,0
|
02:38,0
|
Lavage tripentine
|
12:13,0
|
11:51,0
|
|
Lavage final
|
14:28,0
|
16:27,0
|
|
Totale
|
02:08:02
|
01:54:40
|
13:22,0
|
Jawaher ben Ameur
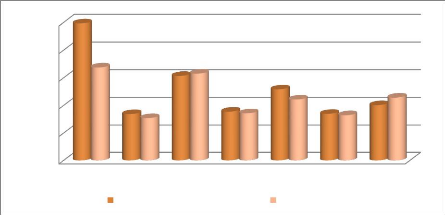
07:12,0
00:00,0
36:00,0
28:48,0
21:36,0
14:24,0
1 2 3 4 5 6 7
Le temps réel du bloc3- P22/4073 Temps standars
Page 37
Figure 17: la comparaison entre le temps
réel et le temps standard pour le bloc 3
Remarque : On peut conclure que le temps
réel est supérieur au temps standard pour la majorité des
opérations. En fait, la perte de temps totale est appropriés
égale à [14(min)] pour seulement un bloc. C'est
une valeur élevée, et cela est dû à des causes
diversifiées telles que la mauvaise implantation de la section,
l'absence des méthodes d'organisation dans la section et la
déséquilibre des postes de travail.
Après avoir un diagnostic et une analyse de la
problématique dans la section, pour résoudre le problème
du gaspillage de temps dans la section, nous avons appliqué la
méthode « 5S » dans la deuxième partie de ce chapitre
et nous avons proposé une nouvelle organisation de la section.
III. Les solutions adéquates
1. La méthode « 5S »
1.1. Objectifs de la « 5S » au sein de la
société « VEGE MOTEUR »
Parmi les objectifs de la méthode « 5S
» on peut citer :
V' Amélioration de la sécurité.
V' Élimination du temps perdu à chercher ses
outils, ses habits...
V' Amélioration de l'efficacité.
V' Diminution et prévenir les pannes.
V' Libération de l'espace inutilement utilisé.
V' Avoir une meilleure qualité de vie.
Jawaher ben Ameur
Page 38
1.2.. L'application de la méthode « 5S
»
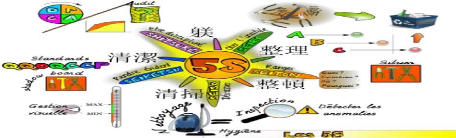
Figure 18 : Les « 5S »
a. Débarrasser et supprimer l'inutile
(Seiri)
Trier, c'est "l'art de savoir jeter", garder le strict
nécessaire sur le poste et se débarrasser
le reste, car une poste de travail encombrée ne
favorise pas la performance. Le résultat de l'opération doit
être visible.
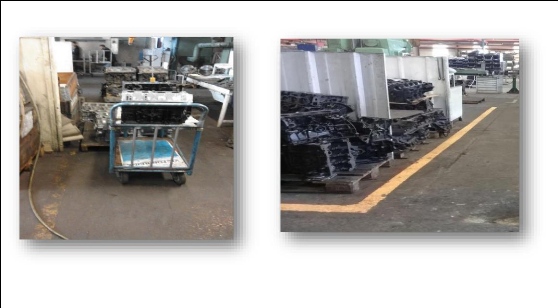
Avant
Après
Figure 19:
Débarrasser
Jawaher ben Ameur
b. Ranger et bien situer les choses (Seiton)
Il s'agit de ranger et situer les choses utiles, celles
indispensables au travail, de manière fonctionnelle et s'astreindre
à remettre en place les objets, donner un nom et une place bien
définie aux outils, réaliser des accessoires et supports
permettant de trouver les outils rapidement et plus largement, définir
les règles de rangement : cela se concrétise par la mise en place
d'un arrangement pour visualiser et/ou situer facilement ces objets.
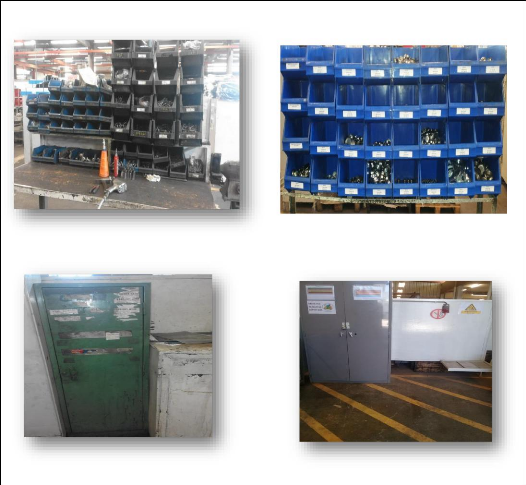
Avant
Après
Figure 20: Ranger
Jawaher ben Ameur
Page 39
c. Page 40
Nettoyer et scintiller (Seiso)
Une fois chaque chose à sa place, il faut veiller
à la propreté des lieux. Il s'agit d'éliminer les
déchets, les saletés, les corps étrangers afin que le
poste de travail et son environnement soient propres. Après le premier
grand nettoyage, étape obligée de l'introduction des 5S, il faut
en assurer la continuité.
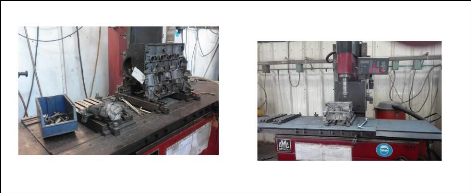
Avant
Après
Figure21: Nettoyer
d. Standardiser (Seiketsu)
Les 3 premiers S sont des actions à mener. Elles sont
les plus souvent exécutées sous la contrainte
hiérarchique. Afin que le maintien de la propreté et
l'élimination des causes de désordre deviennent normaux,
naturels. Il est indispensable de les inscrire comme des règles
ordinaires, des standards. Le Seiketsu permet de simplifier la
compréhension du poste et de son environnement si l'on privilégie
les aides visuelles
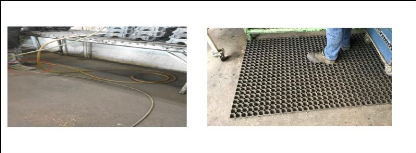
Avant
Après
Figure 22: Standardiser
Jawaher ben Ameur
Page 41
e. Maintenir et faire évoluer
(Shitsuke)
Pour faire vivre les 4 premiers S, il faut surveiller
régulièrement l'application des règles, les remettre en
mémoire, en corriger les dérives. En instituant un système
de suivi avec affichage d'indicateurs, les désormais 5S sont
assurés de continuer à vivre, mais aussi de graduellement
repousser leurs limites initiales, dans une démarche
d'amélioration continue.
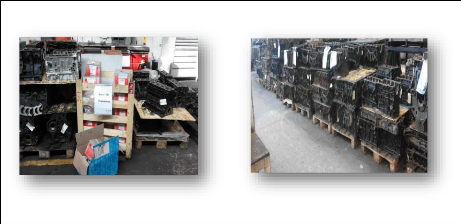
Avant
Après
Figure23 : Maintenir
Les activités développées dans le cadre
des « 5S » sont des actions concrètes qui nous avons permis de
nous rendre compte que les résultats dans une entreprise sont
proportionnels à l'effort fourni. Cependant, il est difficile de
quantifier les 5S. En fait, nous avons remarqué que le scepticisme de
certains pouvait s'expliquer par le fait que l'application d'une telle
méthode ne pouvait se justifier que par l'expérience. C'est pour
cette raison qu'il est nécessaire d'engager moralement et physiquement
les opérateurs à la réalisation de tels changements sur
leur poste.
Nous pensons qu'il n'en reste pas moins que les 5S sont
essentiel pour toute l'entreprise et qu'ils ont toujours des effets
positifs.
Jawaher ben Ameur
Page 42
2. Les flux de la chaine de production
Dans cette étude nous allons présenter les flux de
la chaine de production au sein de la
section bloc moteur et nous allons appliquer la programmation
dynamique pour déterminer le chemin le plus court pour réaliser
un bloc.
2.1.L'organisation réelle de la section bloc
moteur :
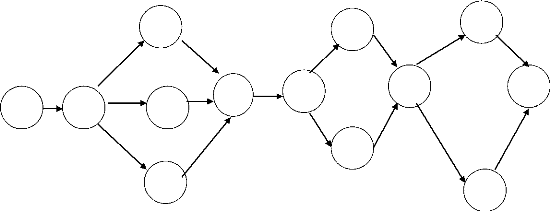
C
13met 20cm 4m et 60cm
H
K
6m et 70 cm 2m et 55cm 9m 2m
3m 11et 70cm 8m F 15m
G
J
Mf
A0 B
D
2met50cm
I
14m et 40 cm 4met 20cm 12m 10m et 40cm
2met 50cm
E
L
Figure 24 : le graphe de l'organisation
réelle de la section
A0 : Préparation H : Honage cylindre2
B : Honage ligne I : Honage cylindre 1
C : Alésage cylindre 1 J : Lavage tripentine
D : Alésage cylindre 2 k : Lavage final 1
E : Alésage cylindre 3 L : Lavage final 2
F : montage bague Mf : produit finis
G: Dressage
C (B) =3 p (B) =A0
Jawaher ben Ameur
Page 43
C(C) = c (B) +c (B, C) = 3+6.70 =9.70 P(C) =B
C (D) = c (B) +c (B, D) =3+11.70= 14.70 p (D) =B
C (E) = c (B) +c (B, E) =3+14.40=17.40 P (E) =B
C(F)= C(C)+C(C,F)=9.70+2.55=12.25 (MIN)
C (D) +C (D, F) =14.7+8=22.7 P (F) =C C (E) +C (E, F)
=17.40+4.20=21.60
C (G) = c (F) +c (F, G) =12, 25+15=27.25 P(G)=F
C (H) = c (G) +c (G, H) =27.25+12=39.25 P (H) =G
C (I) = c (G) +c (G, I) =27.25+12=39.25 p (I) =G
C (J) = C (IT) +c (IT, J) =40.45+4.50=44.95 P (J) =I C (I) +c
(I, J) = 39.25+3=42.25 (MIN)
C (k) = C (J) +C (J, K) =42.25+9=51.25 P (K) =J
C (L) = C (J) +C (J, L) =42.25+10.40=52.65 p (L)=J
C (Mf) = C (K) +C (K, Mf) =51.25+2=53.25(MIN) P (Mf) =k C (L)
+C (L, Mf)= 52.65+2.50= 55.15
Le chemin le plus court est:
P(Mf)=k P(K)=J P(J)=I P(I)=G P(G)=F p(F) =C P(C)=B
P(B)=A0
A0-B-C-F-G-I-J-K-Mf
LA distance minimale de l'organisation réelle est : 53m et
25cm
Jawaher ben Ameur
HONAGE
|
HONAGE
|
|
MONTAGE
|
|
ALESAGE
|
CYLINDRE2
|
CYLINDRE1
|
|
BAGUE
|
|
CYLINDRE3
|
H
|
I
|
|
F
|
|
E
|
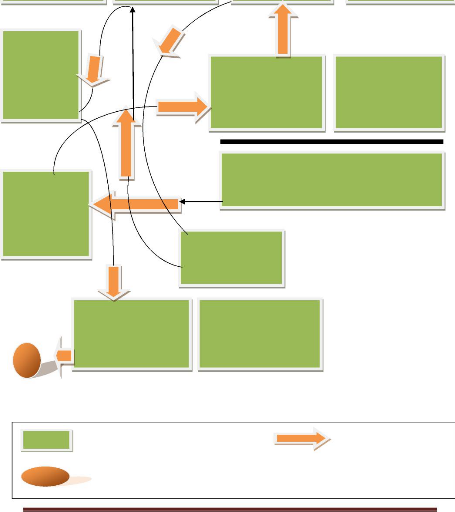
J
C
D
A0
B
DRESSAGE
G
K
L
LAVAGE TRIPENTIN
E
HONAGE LIGNE
BAIN DE NETTOYAGE1
BAIN DE NETTOYAGE2
ALESAGE CYLINDRE1
PREPARATION1
ALESAGE CYLINDRE2
: Opération à valeur ajouté :
Transfert de flux
: Produit fini
Jawaher ben Ameur
Page 44
Page 45
Figure25: l'organisation réelle de la
section
2.2. Proposition d'une nouvelle organisation :
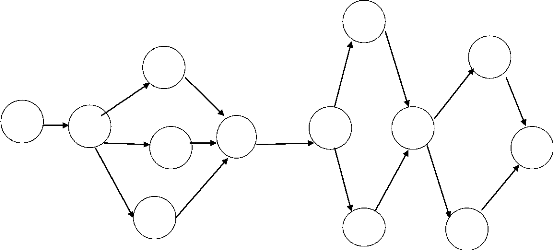
I
K
C
4met 60cm 2m et 20cm
4m et 70 cm 2m et 55cm 3m et 40
A0 2m 7B
G
J
F
D
Mf
1m 9et 70cm 8m 3m et 50cm
3met 70cm
12m et 70cm E 4met 20cm 6met 90 4 t 20cm
H
L
3met 50cm
Figure 26 : le graphe de l'organisation
proposée de la section
A0 : Préparation H : Honage cylindre2
B : Honage ligne I : Honage cylindre 1
C : Alésage cylindre 1 J : Lavage tripentine
D : Alésage cylindre 2 k : Lavage final 1
E : Alésage cylindre 3 L : Lavage final 2
F : montage bague Mf : produit finis
G: Dressage
Jawaher ben Ameur
Page 46
C (B) =1 p (B) =A0
C(C) = c (B) +c (B, C) = 1+4.70 =5.70 p(C) =B
C (D) = c (B) +c (B, D) =1+9.70= 10.70 p (D) =B
C (E) = c (B) +c (B, E) =1+12.70=13.70 P (E) =B C (F) = C(C)
+C(C, F) =5.70+2.55=8.25 (MIN)
C (D) + C (D, F) =10.70+8=18.70 P(F)=C C (E) +C (E, F)
=13.70+4.20=17.90
C (G) = c (F) +c (F, G) =8.25+3.50=11.75 P (G) =F
C (H) = c (G) +c (G, H) =11.75+6.90=18.95 P (H) =G
C (I) = c (G) +c (G,I )=11.75+4.60=16.35 P(I) =G
C (J) = C (H) +c (H, J) =18.95+3.70=22.65 P(J)=I
C (I) +c (I, J) = 16.35+2.20=18.55 (MIN)
C (k) = C (J) +C (J, K) =18.55+3.40=21.95 P (K) =J
C (L) = C (J) +C (J, L) =18.55+4.20=22.75 p(L)=J
C (Mf) = C (K) +C (K, Mf) =21.95+2.70=24.65 (MIN) P (Mf)=k C
(L) +C (L, Mf)= 22.75+3.50= 26.25
Le chemin le plus court est:
P(Mf)=k P(K)=J P(J)=I P(I)=G P(G)=F p(F) =C P(C)B
P(B)=A0
A0-B-C-F-G-I-J-K-Mf
LA distance minimale parcourue de la nouvelle organisation est :
24m et 65cm
Jawaher ben Ameur
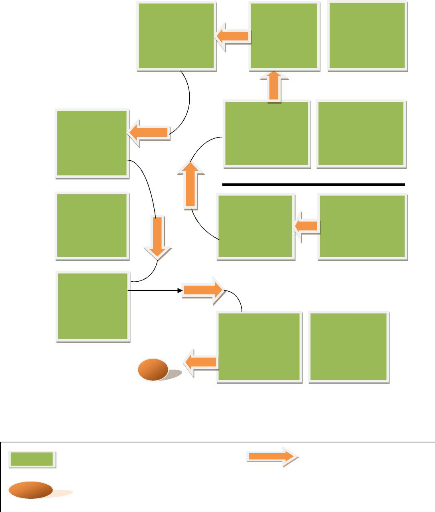
: Produit fini
Montage bague
F
Alésage cylindre3
E
Dressage
G
Alésage cylindre1
C
Honage cylindre 1
I
Préparation A0
Honage ligne
B
Honage cylindre 2
H
Lavage tripentine
J
Bain de nettoyage 1
K
Bain de nettoyage 2
L
Alésage cylindre
2
D
: Opération à valeur ajouté :
Transfert de flux
Page 48
Figure 27: la proposition de la nouvelle organisation de
la section
D'après la nouvelle organisation qui est fondée
sur l'élimination des mouvements inutiles et la diminution de temps
perdu. En effet, l'entreprise aura gagné beaucoup des avantages tels que
; l'amélioration de sa productivité, la diminution des temps
perdu.
3. Le gain de l'application de la méthode « 5S
» et la proposition d'une nouvelle organisation :
Nous avons appliqué la méthode durant les
derniers 15 jours de stage au sein de la section bloc moteur et elle donne les
résultats suivants :
-Avant la mise en place de la méthode
nous avons un gaspillage de temps dans la majorité des postes, les poste
ne sont pas organisées, les outils de travail ne sont pas
cordonnés.
- Après La mise en place, la
méthode « 5s » donne des meilleurs résultat sur
plusieurs niveaux, on peut citer la diminution de temps de gaspillage dans les
postes, amélioration de la productivité et la flexibilité
de la chaine, meilleure organisation des outils de travail et la diminution du
temps perdu à chercher ses outils, ses habits, libération de
l'espace inutilement utilisé.
Conclusion
Dans ce chapitre, nous avons mis en oeuvre Les méthodes
de la philosophie de la Lean management (ISHIKAWA, Pareto, « 5S »),
qui a pour but d'identifier les causes de ce problème dans la section
bloc moteur, Et qui permit aussi de réduire la plupart de ses causes.
Jawaher ben Ameur
Conclusion générale
Page 49
La philosophie du Lean mangement 5S est un état
d'esprit visant à un fort accroissement de compétitivité
au moyen de la maximisation de l'efficacité, de la souplesse, de la
productivité, de la qualité, de la réduction des couts de
production et l'enrichissement du travail individuel.
A travers ce projet, des perfectionnements du fonctionnement
d'une section de production ont été réalisée.
L'idée de ce projet était, de réduire le temps de
gaspillage dans la section bloc moteur et l'organisation du poste de travail.
Autrement dit, nous avons essaye d'avoir une production plus rapide et plus
efficaces à travers l'élimination de gaspillage de temps et la
réduction des disfonctionnement des postes.
Dans la première partie du projet on a
présenté la société, les processus de production.
Dans la partie suivante on a mené une étude théorique de
la gestion de production, l'étude de la philosophie Lean. Ensuite nous
avons mené une analyse de l'existant qui permet de bien comprendre la
problématique ses causes principales et l'application de la
méthode « 5S » au niveau de la section.
Enfin, l'étude de cette méthode m'a permis de
prendre des responsabilités et d'éveilleur en moi un esprit
créatif et exploratoire. C'était surtout une occasion d'enrichir
mes connaissances et de les confronter avec la vie professionnelle.
En fait, sur le plan des fonctionnalités, ce projet
reste ouvert à des évolutions sous forme de modules
intégrable de manière indépendante.
Jawaher ben Ameur
Webographies
[1]:
http://www.cat.logistique.com/production.htm
[2]:
http://www.bpmconsulting.ca/fr/course/lean-fundamentals/
[3]:www.qualiteonline.be
Page 50
Jawaher ben Ameur
Page 51
ANNEXES
Annexe1 : Listes des taches de chaque poste
les noms des postes
|
Opérations
|
Préparation bloc
|
Réception des blocs et les mettre sur la table
|
contrôle visuel (nettoyage , endommagement...)
|
Identification
|
Marquage de bloc et "ses chapeaux ou partie inférieur"
|
Démontage de la partie inférieur de bloc
|
Démontage des chapeaux
|
Brossage
|
Révision des trous
|
Contrôle Fissure
|
Codification
|
Mettre les blocs sur la palette
|
Honage ligne
|
Mettre Le Bloc Sur La Machine d'honage
|
Fixation Bloc Sur La Machine
|
Monter Les Chapeaux + Faire Le Couple de serrage
|
Honage Ligne
|
Contrôle Dimensionnel
|
Démontage Chapeaux et Contrôle Visuel
|
Remettre Le Bloc Sur La Palette
|
Réglage Comparateur
|
Réglage Machine
|
Alésage cylindre
|
Mettre Le Bloc Sur La Machine d'alésage
|
Fixation Bloc
|
Réglage Machine
|
Réglage Outil
|
Réglage Comparateur
|
Alésage 1er Cylindre
|
Alésage 2eme Cylindre
|
Jawaher ben Ameur
Page 52
|
Alésage 3 eme Cylindre
|
Alésage 4 eme Cylindre
|
Contrôle Visuel
|
Desserrage Bloc De La Machine
|
Remettre Sur La Palette
|
Honage cylindre
|
Mettre Le Bloc Sur La Machine d'honage cylindre
|
Positionnement de bloc
|
Fixation Bloc
|
Chanfreinage
|
Réglage Machine
|
Réglage Outil ( Changement des Meules )
|
Réglage Comparateur
|
Honage Cylindre
|
Contrôle Visuel
|
Desserrage Bloc De La Machine
|
Remettre Le Bloc Sur La table
|
Marquage Bloc ( Date / Semaine / Ø / Fournisseur de
Pistons )
|
Remettre Le Bloc Sur La Palette
|
Dressage
|
Mettre Le Bloc Sur La Machine de dressage
|
Fixation Bloc
|
Parallélisme de bloc
|
Dressage Surface Plan De Joint
|
Contrôle visuel
|
Contrôle Dimensionnel
|
Réglage Machine
|
Réglage Comparateur
|
Ecrire L'hauteur Sur La Label
|
Contrôle Rugosité
|
Remettre Sur La Palette
|
lavage tripentine
|
Mettre Le Bloc Dans Le Bain n:°1
|
Monter Et Descente De Bloc Dans Le Bain
|
Jawaher ben Ameur
|
Brossage Bloc
|
Monter Et Descente De Bloc Dans Le Bain
|
Remettre Sur La Palette
|
lavage final
|
Mettre Le Bloc Dans Le Bain n:° 1
|
Monter et Descente De Bloc
|
Brossage Canal D'huile
|
Monter et Descente De Bloc
|
Mettre Le Bloc Dans Le Bain n:° 2
|
Monter et Descente De Bloc
|
Nettoyer Le Bloc Avec L'air Comprimé
|
Mettre Le Bloc Sur La Table
|
Montage Opercule
|
Contrôle Visuel
|
Retouche manuelle
|
Monter La partie inférieur
|
Lubrification De Bloc
|
Mettre Le Bloc Sur La Palette
|
Annexe 2 : Audit 5S avant la mise en place de la
méthode
Audit -6S
|
Auditeurs : Mr Fathi Mani et Jawaher Ben Ameur
Le:16/04/2018
|
|
|
|
|
Site : VEGE 1
Section : BLOC MOTEUR
|
|
|
|
|
Les critères de
jugement
|
Note exigé
|
Note Reçu
|
Observations
|
|
|
|
1
|
Débarrassage --> Séparer ce qui est
utile de l'inutile
|
|
1,1
|
Est ce qu'il y a des équipements inutilisés,
inexploités? Ex: Outils, ressource, équipement de mesure,
Tôle, Papier, classeur, etc.
|
5
|
1
|
|
1,2
|
Est ce qu'il ya des équipements ou des moyens de
production endommagés? Ex: Moyens de transport
|
5
|
2
|
une lampe brulée
|
Jawaher ben Ameur
Page 53
Page 54
|
(Chariots, Chariots élévateurs), Dispositifs de
nettoyage, outils, éclairage ...
|
|
|
|
1,3
|
Est ce qu'il ya des matériaux ou des conteneurs
inutiles? Ex: Matériaux d'emballage, récipients
|
|
|
Deux récipients inutile dans la zone
|
|
(cuves vides, boites, seaux,...), Matières
premières, matières de production, moyens de nettoyage
|
5
|
1
|
des rebuts
|
|
(Chiffons, Brosses, Dissolvants....)
|
|
|
|
1,4
|
Est ce qu'il ya des dispositifs inutiles? Ex: Armoires,
étagères, bancs, chaises, tables, matériels de nettoyage,
supports de boissons, matériels d'emballage, existence des affaires
personnelles dans la place de travail...
|
5
|
2
|
il ya des chaises devant les postes de travail sauf
que l'opération ne dépend pas des chaises
|
1,5
|
Est ce qu'il ya des informations inutiles ou non-
|
|
|
|
|
actuelles? Ex: Affiches, directives, consignes de travail,
description d'objectifs, indicateurs de travail,...(Inclus dépôts,
dossiers etc.)
|
5
|
3
|
|
Total
|
25
|
9
|
|
Résultat (%)
|
|
36%
|
|
2
|
Rangement systématique --> Rendre l'ordre
visible : Marquage &
|
|
|
Identification
|
|
2,1
|
Est ce que les outils, outils de mesures, équipements,
Machines, armoires, étagères, etc.
|
|
|
les armoires et les étagères ne sont pas
|
|
sont identifiés. Est ce qu'on peut identifie0r si il
manque une chose à la place de travail et ou est ce que chaque chose
doit être remise?
|
5
|
1
|
identifiés
|
2,2
|
Est ce que les couloires et les places de stationnement ou de
dépôt pour les palettes, matériaux, moyens d'emballage,
etc. sont identifiés. Est ce qu'on peut reconnaitre ou est ce que chaque
dispositif doit être rangé?
|
5
|
1
|
l'emplacement encadré en jaune non respecté
(les pièces et
les stocks encours
dans les couloires),
|
2,3
|
Est ce que les données des machines, d'appareils et des
voyants sont identifiés? Est ce qu'on peut reconnaitre le type de la
machine et a quoi ca sert?
|
5
|
2
|
les appareils de travail(poste préparation) ne
sont pas identifiés
|
2,4
|
Est ce que le stockage et les réserves sont
identifiés
|
|
|
|
|
(Données de transport ou d'Export, identification
|
|
|
|
|
des quantités...), est ce que les consignes de stockage
sont respectées: (Les palettes, les BOX et les Jit sont-ils
conformes)?
|
5
|
2
|
|
Total
|
20
|
6
|
|
Résultat (%):
|
|
30%
|
|
3
|
Le meilleur menage c'est de ne pas avoir besoin de
nettoyer
|
|
3,1
|
Est ce que les machines, autres objets ou places de travail sont
minutieusement nettoyés et libres de toutes saletés? par exemple
par de l'huile, graisse, papier, matières premières,
déchets...
|
5
|
1
|
les machines et les postes de travail sont très
sales (sur les machines il ya des
|
Jawaher ben Ameur
Page 55
|
|
|
|
chiffons, des gants, des papiers)
|
3,2
|
Est ce que l'environnement de la place de travail Ex: sol, murs,
fenêtres, porte est libre de toutes saletés? par exemple par de
l'huile, graisse, papier, matières premières,
déchets...
|
5
|
1
|
l'huile et les papiers sont sur le sol
|
3,3
|
Est ce que les outils de travail sont propres? (outils et moyens
de mesure) Par Ex: par des poussières, de l'huile, des écritures,
peinture... (Inclus tout dispositif qui n'est pas directement utilisé
dans la place de travail mais rangé dans les armoires ou les tiroirs)
|
5
|
2
|
|
3,4
|
Est ce qu'il ya une définition de règles ou de
processus pour le nettoyage? (Les plans de nettoyage doivent contenir les
activités nécessaires ainsi que la fixation des délais et
des méthodes à utiliser)
|
5
|
2
|
|
3,5
|
Est ce que les moyens de nettoyage (Par exemple: Balai, Chiffons,
nettoyant ou détergeant) définis dans la "Check liste" sont
disponibles?
|
5
|
2
|
l
|
Total
|
25
|
8
|
|
Résultat (%):
|
|
32%
|
|
4
|
Standardiser -> Faire des règles
|
|
4,1
|
Est ce que les identifications désignent vraiment le
contenu (Surfaces, armoires, tiroirs)?
|
5
|
2
|
|
4,2
|
Est ce que les solutions sont identiques et uniformément
utilisées?
Par Ex: Le principe de FIFO est respecté (consommation du
matériel...etc.), Les tabliers sont identifiés selon les
fonctions/ les badges sont mis, Emplacement de dispositifs encadré en
jaune, classeurs uniformément identifiés, uniformité des
tableaux d'affichage, identification uniforme...
|
5
|
2
|
il existe des blocs moteurs situés hors
de l'emplacement encadré en jaune
|
4,4
|
Est ce qu'il y a des "Check-lists" ou des modes d'usage
visualisés pour les machines? Est ce qu'ils contiennent des indications
sur les dangers ou sur le comportement requis en situations
imprévisibles?
|
5
|
2
|
|
4,5
|
Est ce qu'il ya des standards, des formulaires, des rapports, ou
des notes de services...est ce qu'ils sont conformément
utilisés?
|
5
|
1
|
les standards de temps ne sont pas respectés
|
Total
|
25
|
8
|
|
Résultat (%):
|
|
32%
|
|
5
|
Auto-discipline et amélioration continue ->
Gardez tous les points et améliorez constamment
|
|
Jawaher ben Ameur
5,1
|
Est ce que les standards décrits au point 5 sont
conformément respectés et généralisés?
|
5
|
3
|
|
5,2
|
Est ce que les standards décrits au point 5 sont
vécus, améliorés, optimisés?
|
5
|
3
|
|
5,3
|
Est ce que les mesures de sécurité sont connues et
respectées (Chaussures de sécurité, Vêtements,
extincteurs, produits dangereux...)?
|
5
|
2
|
les bidons de produit chimique(savon neutral)
situés devant les postes de travail(machines)
|
Total
|
15
|
8
|
|
Résultat (%):
|
|
53%
|
|
Grand Total
|
125
|
39
|
|
% Total
|
31%
|
|
Règle d'acceptation
Si un des S est refusé l'audit est
refusé
Si tous les S sont accepttés : moins de
70 pts audit refusé .
De 70 a 84 pts ;audit accepté mais
améliorations nécessaires
De 85 a 100 pts ;audit accepté .
|
|
Actuel
|
Cible
|
S1-Débarrassage
|
36%
|
70%
|
S2-Rangement systématique
|
30%
|
70%
|
S3-Nettoyage
|
32%
|
70%
|
S4-Standardiser
|
32%
|
70%
|
S5-Maintien
|
53%
|
70%
|
Jawaher ben Ameur
Page 56
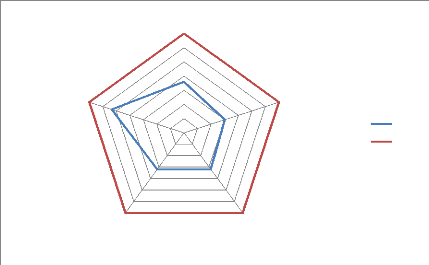
S5-Maintien
S4-Standardiser S3-Nettoyage
S1-Débarrassage
40%
70%
60%
50%
30%
20%
10%
0%
S2-Rangement systématique
Actuel Cible
Jawaher ben Ameur
Page 57
Page 58
Table des matières
Introduction générale 1
Chapitre I : Présentation de VEGE MOTEURS
2
Introduction 3
I. Présentation de VEGE MOTEURS 3
1. Historique 3
2. Clientèle de VEGE : 4
3. Fiche signalétique : 5
4. L'organigramme de VEGE MOTEUR 6
5. Les Produits de VEGE : 7
6. La qualité comme facteur clefs de succès de
VEGE : 7
7. Les objectifs de VEGE MOTEURS 8
8. La cartographie du processus : 9
II. Processus de production 9
1. Section Démontage moteur: 10
2. Section Nettoyage : 10
3. Section culasse : 10
4. Section de rectification : 11
5. Section bloc moteur : 11
6. Section montage moteur : 12
7. Section banc d'essai : 12
8. Section de contrôle : 13
Conclusion 14
Chapitre II : La logistique de production
15
Introduction 16
I. La logistique de production 16
Jawaher ben Ameur
Page 59
II. Définition de gaspillage et leurs types 17
1. Définition 17
2. Les différents types de gaspillage 17
III. Lean : Historique et définition 18
1. Historique : 18
2. Définition 18
3. Les objectifs de Lean Manufacturing : 19
4. Principes de base du Lean Manufacturing : 19
5. Les méthodes de Lean : 20
5.1. Diagramme d'ISHIKAWA 20
5.2. Les 5S : 20
Conclusion : 21
Chapitre III : L'étude de l'existant et la mise
en place de la méthode « 5S » au sein de la
section Bloc Moteur 22
Introduction 23
I. Étude de l'existant 23
1. Diagnostic de la section bloc moteur : 23
1.1. Les étapes de diagnostique 23
1.2. La modélisation de la section bloc Moteur : 24
1.3. Diagramme de causes à effet « ISHIKAWA »
25
1.4. Diagramme Pareto : 26
II. Calcul du temps réels : 29
1. Identification de la référence à
étudier : 29
2. Chronométrage : 31
III. Les solutions adéquates 37
1. La méthode « 5S » 37
1.1. Objectifs de la « 5S » au sein de la
société « VEGE MOTEUR » 37
Jawaher ben Ameur
1.2. . L'application de la méthode « 5S »
38
a. Débarrasser et supprimer l'inutile (Seiri) 38
b. Ranger et bien situer les choses (Seiton) 39
c. Nettoyer et scintiller (Seiso) 40
d. Standardiser (Seiketsu) 40
e. Maintenir et faire évoluer (Shitsuke) 41
2. Les flux de la chaine de production 42
2.1. L'organisation réelle de la section bloc moteur :
42
2.2. Proposition d'une nouvelle organisation : 45
3. Le gain de l'application de la méthode « 5S
» et la proposition d'une nouvelle
organisation : 48
Conclusion 48
Conclusion générale 49
Webographies 50
ANNEXE 51
Page 60
Jawaher ben Ameur
|