Année Académique :
2012-2013
1
REPUBLIQUE DEMOCRATIQUE DU CONGO
MINISTERE DE L'ENSEIGNEMENT SUPERIEUR, UNIVERSITAIRE
ET RECHERCHE SCIENTIFIQUE
INSTITUT SUPERIEUR DE TECHNIQUES APPLIQEES
« I.S.T.A »

B.P. 6593 KIN 31 SECTION : MECANIQUE PREMIER
CYCLE KINSHASA
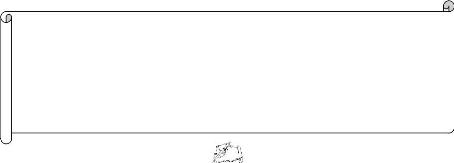
ETUDE FONCTIONNELLE ET IDENTIFICATION DE LA
POLITIQUE DE MAINTENANCE EFFICACE POUR UNE PRODUCTION OPTIMALE DE
LA DEROULEUSE DES GRUMES COLOMBO & CREMONA N2700 DE L'INDUSTRIE DE
TRANSFORMATION DE BOIS « I.T.B/KINSHASA »
NKELANI NKELAME Emery
Directeur :
TSHAONA TSHIMBADI Marcel Chef des
Travaux
|
Travail de fin de cycle présenté et défendu
en vue de l'obtention de Grade académique d'ingénieur technicien
en Mécanique. Orientation : Electromécanique
|
2
EPIGRAPHE
« La différence entre ce que nous faisons et
ce dont nous serions capables, suffirait à résoudre la
majorité des problèmes du monde »
Gandhi
Emery NKELANI NKELAME
3
DEDICACE
Ce travail de patience et persévérance est
dédié
A ma défunte Mère MONENE OYEME Berthe qui a
été la source de ma vie dont, je rends grâce à Dieu
à travers tous les sacrifices, peines, privations,
persévérance, conseils, éducation et surtout le souci de
me faire ce que je suis aujourd'hui, malgré que la nature nous a
séparée sans qu'elle ne jouisse du fruit de son travail
enduré.
A mes frères, soeurs, Oncles, Tantes, Nièces
et Neveux : PONGE Lucien, ETONGA Anne, Bobo, Papy, Ruth, Carine, Horline,
Glody, et Jephté pour leur soutien et attachement.
Aux familles KOKATE et GANU pour leur affection,
encouragement et soutien qu'elles ne cessent de témoigner notre
vie.
A toi la fille de mes rêves : KYUNGU MUKEYNA Gloria,
pour tes belles paroles d'espoir, Trouve ici l'expression indescriptible
d'attachement et d'amour.
A tous ceux qui ont contribué d'une manière
ou d'une autre à ma vie d'étudiant, qu'ils trouvent ici
l'expression de ma gratitude.
Emery NKELANI NKELAME
4
REMERCIEMENT
Quelque soit la durée de la nuit, le soleil
apparaîtra.
Ce soleil représente le résultat d'un
travail dur de longue haleine et essoufflant qui a été abattue
tout au long de notre formation académique.
Nous sommes conscient que sans le précieux concours
de notre Seigneur Jésus-Christ, ce travail n'aurait pas pu avoir le
caractère qu'il a maintenant.
De tout coeur, nous disons merci à Monsieur Marcel
TSHAONA TSHIMBADI, Ingénieur civil des Mines, Maître en Sciences
Appliquées, Chef de travaux à l'Institut Supérieur de
Techniques Appliquées et Chef de section Maintenance, qui, malgré
ses multiples occupations a bien voulu accepter la direction de ce
travail.
Nous témoignons notre gratitude aux responsables de
l'Industrie de Transformation du Bois « I.T.B » en sigle qui ont
accepté et permis d'avoir les données qui constituent ce travail,
le Chef du personnel M'BIEME KOMIPOKO Jean Pierre, les ingénieurs Van,
Alain, Michel, Chef Guy, et Mr Placide et aux autorités
académiques de l'I.S.T.A qui, malgré les difficultés de
l'heure se sont données à notre formation.
Egalement nos remerciements aux : Rév. Basile
MULOKA SANTINI, Rév. PEKOMBE LIKABE, Rév. MBO NGIAYI, Rév.
NDENGO, Pasteur Egide TAMBULA, Diacres et Diaconesses, Fidèles de
l'Eglise C.B.F.C/KINGASANI II et Enfants de l'Ecole du Dimanche ainsi
qu'à mes très chers : Doppy NDAMBU, Jeannot HOMBI, Jeancy ILONDO,
Serge BOLA, Michée BONGONGO, Nadège AOSSA, Sagesse NKEY, Docta
Bienvenu DINGO, Grévy AOSA, Nicha AOSA, Ornella AOSA, Gracia AOSA, Dozy,
Reagan, Ir Rudrich NGANDU, Péguy KONI, Yanick KONI, MATONDO Matty,
Falonne MUBIALA, Huguette, Berlisse, Rachel MBAYA, Charlène NGWEME,
Aimée MAYINDOMBE, Charlène MATOBO pour leur soutien, conseils et
attachement qu'ils ne cessent de témoigner à notre
égard.
5
Ainsi nos sincères remerciements à tous nos
compagnons de lutte : Les ingénieurs OKWES, NGALE, NYEMBWE, NGEKWE,
NZOLANI Charline, NZINGANTOYA, TSHILEU, NGOMA MAMBOUENI, MWILAMBWE, MANISHA et
à tous ceux dont par leurs conseils, contributions financières et
matérielles ont influencé le bon déroulement de ce
travail.
Emery NKELANI NKELAME
6
INTRODUCTION GENERALE
0.1. MOTIVATION
La République Démocratique du Congo a besoin des
industries de bois pour son développement et ces dernières
nécessitent des machines qui requièrent une prise en charge
technique rationnelle et devront être maintenues ou rétablies dans
un Etat en mesure d'assurer un service déterminé pour une bonne
sûreté de fonctionnement.
L'une des tâches des machines est l'usinage des grumes
dont le déroulage exige une certaine force motrice importante.
Il se fait que les paramètres de fonctionnement de ces
machines ne sont pas respectés ; ce qui est à l'origine de
beaucoup des problèmes.
Cet aspect des problèmes a suscité en nous le
désir de l'appréhender et l'analyser.
0.2. PROBLEMATIQUE
Les différents problèmes s'articulent autour des
préoccupations
suivantes :
· La fréquence des pannes liées au circuit
électronique qui se justifie par le claquage des diodes ;
· La lenteur de la production des feuilles, due à
la faible vitesse de rotation qu'imprime le moteur asynchrone triphasée
;
· Les cassures de vis de fixations des mandrins, due
à la mauvaise qualité des matières de fabrication des
mandrins (bronze) ;
· Le disfonctionnement de circuit de blocage des billes,
due au mauvais état des bourrages qui enclave le bon fonctionnement des
vérins hydrauliques qui devrait commander les mandrins.
O.3. OBJECTIF
Nous voulons par cette étude :
· Décrire le fonctionnement systématique
de la machine et interpréter les résultats obtenus après
analyse du fonctionnement ;
· Relever les obstacles majeurs liés à la
production ;
· Proposer une politique de maintenance efficace afin
d'optimiser la production.
7
O.4. METHODOLOGIE DU TRAVAIL
Pour mieux élaborer notre travail, nous avons
utilisé les méthodes descriptives ayant consistées
à décrire le système de fonctionnement de la
dérouleuse de grumes N2700 et d'analyse scientifique qui est
complétée par la technique documentaire laquelle consiste
à consulter des livres, notes des cours et bibliothèques, ainsi,
que les sites internet.
0.5. DELIMITATION DU SUJET
Dans notre étude, nous nous sommes fixés
à décrire le fonctionnement de la dérouleuse des grumes
colombo&Cremona N2700, relever les obstacles qui enclavent son bon
fonctionnement et proposer une politique de maintenance pour sa remise à
l'état de bon fonctionnement.
En abordant ce sujet, nous ne pensons pas avoir mené
une analyse exhaustive sur un sujet aussi vaste et complexe que nous proposons
par contre, ce sujet comporte plusieurs aspects techniques pouvant faire chacun
l'objet d'analyse séparée.
0.6. SUBDIVISION DU TRAVAIL
Hormis l'introduction générale et la conclusion
générale, notre travail comprend trois chapitres :
? Le premier chapitre parle de recension des écrits ;
? Le deuxième chapitre : études
systémiques de la dérouleuse de grumes N2700 ;
? Le troisième chapitre : politique de maintenance
adaptée à la dérouleuse de grumes N2700.
8
CHAPITRE I : RECENSION DES ECRITS
I.1. NOTION DE MAINTENANCE
I.1.1. Historiques1
La maintenance est une des fonctions de l'entreprise,
mais elle n'est pas une fin en soi. A ce titre, elle est peu lisible et parfois
méconnue des décideurs qui sous-estiment son impact.
Le terme « Maintenance », forgé sur
les racines latines Manus et tenere, est apparu dans la langue française
au XIIème siècle. L'étymologiste Wace a
trouvé la forme mainteneor (celui qui soutient).
Dans son acception actuelle, le terme «
Maintenance » est un anglicisme partiel il est donné comme «
Réemprunt intégré » par Jean TOURNIER dans les mots
anglais du français Belin dans la section « Armement, armée
vers 1953 ».
I.1.2. Définitions
· D'après LAROUSSE : c'est l'ensemble de
tout ce qui permet de maintenir ou rétablir un système en
état de fonctionnement ;
· D'après L'AFNOR2 (NFX60-010)
: il parle de l'ensemble des actions permettant de maintenir ou de
rétablir un bien dans un état ou dans des conditions
données de sûreté de fonctionnement, pour accomplir une
fonction requise ;
· Depuis 2001, les Européens on
remplacé AFNOR (NF X60-010) par une nouvelle définition (NF
X60-319) : l'ensemble de toutes les actions techniques, administratives et de
management durant le cycle de vie d'un bien, destinées à le
maintenir ou à le rétablir dans un état dans lequel il
peut accomplir la fonction requise ;
· Maintenir sous entend, prévention pour
un système en fonctionnement ;
· Rétablir sous entend, correction
consécutive à perte de fonction ;
· Etat spécifié ou service
déterminé, implique la prédétermination d'objectifs
à atteindre, avec quantification des niveaux caractéristiques. La
connaissance d'un matériel de ses faiblesses et ses dégradations
complétées jour après jour permet des corrections, des
améliorations économiques des optimisations ayant pour objet de
minimaliser le ratio
s
(ou rapport) :Frais de
maintenance+Co t des arr ts for t uit
service rendu
· Bien maintenir : c'est assurer les
opérations au coût global optimal.
1 INTERNET
2 F. BOUCLY et A. OGUS, le management de la
maintenance, AFNOR, Eyrolles, Paris 1987
9
On peut noter que la maintenance est l'ensemble des
opérations exercées à un matériel défaillant
ou dégradé pour le rétablir ou le maintenir afin d'assurer
une fonction requise.
I.1.3. Les Méthodes de la maintenance1
Le choix entre les méthodes de maintenance s'effectue
dans le cadre de la politique de la maintenance et doit s'opérer en
accord avec la direction de l'entreprise.
Pour choisir, il faut être informé des objectifs
de la direction, des décisions politiques de maintenance, mais il faut
aussi connaître le fonctionnement et les caractéristiques des
matériels ; le comportement du matériel en exploitation ; les
conditions d'application de chaque méthode ; les coûts de
maintenance et les coûts de perte de production.
I.1.3.1.La maintenance corrective
Définition : « Maintenance
effectuée après défaillance. »
La maintenance corrective a pour objet de redonner au
matériel des qualités perdues nécessaires à son
utilisation.
Les défauts, pannes ou avaries diverses exigeant une
maintenance corrective entraînent une indisponibilité
immédiate ou à très brève échéance
des matériels affectés ou / et une dépréciation en
quantité ou / et en qualité des services rendus.
I.1.3.1.1. La maintenance curative
Définition : « Activités
de maintenance corrective ayant pour objet de rétablir un bien dans un
état spécifié ou de lui permettre d'accomplir une fonction
requise. »
Elle comprend des interventions de types réparations
(donc durable) consistant en une remise à l'état initial. Le
résultat des activités réalisées doit
présenter un caractère permanent.ces activités peuvent
être des réparations, des modifications ou aménagement
ayant pour objet de supprimer les défaillances.
1 F. MONCHY, Maintenance, méthodes et
organisations, Dunod, Paris 2003
10
I.1.3.1.2. La maintenance palliative
Définition : « Activités
de maintenance corrective ayant pour destinée à permettre
à un bien d'accomplir provisoirement tout partie d'une fonction requise.
»
Elle s'effectue après défaillance et comprend
des interventions de type dépannage (donc provisoire) de
l'équipement, permettant de remettre provisoirement en fonctionnement
avant la réparation. Elle doit toute fois être suivie d'une action
curative dans le plus bref délai.
I.1.3.2. La maintenance préventive
Maintenance effectuée selon des critères
prédéterminés, dans l'intention de réduire la
probabilité de défaillance d'un bien ou la dégradation
d'un service rendu. »
Elle doit permettre d'éviter des défaillances
des matériels en cours d'utilisation. L'analyse des coûts doit
mettre en évidence un gain par rapport aux défaillances qu'elle
permet d'éviter.
Elle a pour but :
· Augmenter la durée de vie des matériels
;
· Diminuer la probabilité des défaillances en
service ;
· Diminuer le temps d'arrêt en cas de révision
ou de panne ;
· Prévenir et aussi prévoir les
interventions de la maintenance corrective coûteuse ;
· Permettre de décider la maintenance corrective
dans de bonnes conditions ;
· Eviter les consommations anormales d'énergie,
de lubrifiant, etc.;
· Diminuer le budget de la maintenance ;
· Supprimer les causes d'accidents graves.
I.1.3.2.1. La maintenance systématique
Définition : Maintenance
préventive effectuée selon un échéancier
établi selon le temps ou le nombre d'unités d'usages.
Cette méthode nécessite de connaître : le
comportement du matériel, les usines, les modes de dégradations,
le temps de bon fonctionnement entre deux avaries (MTBF).
11
Elle peut être appliquée dans les cas suivant :
? Equipements soumis à la législation en vigueur
;
? Equipements dont la panne risque de provoquer des accidents
graves ;
? Equipements ayant un coût de défaillance
élevé ;
? Equipements dont les dépenses de fonctionnement
deviennent
anormalement élevées ou cours de leur temps de
service.
I.1.3.2.2. La maintenance conditionnelle
Définition : Maintenance
préventive subordonnée à un type d'événement
prédéterminé (auto diagnostique, information d'un capteur,
mesure d'une usure etc....) révélateur de l'état de
dégradation de l'équipement et est caractérisée par
visite, inspections et contrôle avec ou sans appareils audiovisuels.
Elle se caractérise par la mise en évidence des
points faibles. Suivant les cas il est souhaitable de les mettre sous
surveillance et à partir de là, nous pouvons décider d'une
intervention lorsqu'un certain seuil est atteint, mais les contrôles
demeurent systématiques et font partie des moyens de contrôle non
destructifs.
I.1.3.2.3. La maintenance
prévisionnelle
C'est la maintenance préventive subordonnée
à l'analyse de l'évolution surveillée des
paramètres significatifs de la dégradation du matériel
permettant de retarder et de planifier les interventions.
I.1.4. ORGANISATION DE LA MAINTENANCE1
I.1.4.1. Analyse des défauts de
rentabilité du service « Maintenance-Construction »
La maintenance coûte chère de 1,5 à 15% du
prix de revient du produit fabriqué dans le vas extrêmes et de 5
à 10% dans les cas les plus courant.
Quant aux travaux neufs, ils représentent souvent les
investissements considérables.
1F. MONCHY, Maintenance, méthodes et
organisations, Dunod, Paris 2003
12
Toute économie sur le prix de la maintenance ou des
installations nouvelles, permettra donc une réduction du prix de revient
et l'augmentation importante du bénéfice de l'entreprise.
En conséquence, le rôle essentiel de tout chef
d'un service de « maintenance-construction
» consiste à organiser son département, pour
limiter les coûts au strict minimum sans nuire, toutefois à la
qualité du travail fourni. En particulier, il devra dans le domaine de
la maintenance rechercher le plus faible coût de défaillance,
c'est-à-dire minimiser le total : « Frais de
maintenance + Frais de perte de production ». Mais cette
organisation implique nécessairement que le chef de maintenance sache
analyser les principales raisons d'augmentation de ses prix de revient et
puisse y remédier en connaissance de cause.
Or, les causes pouvant provoquer une augmentation des
coûts et une baisse de rentabilité du service «
Maintenance-Construction » sont multiples.
Toutefois, nous n'avons pas la prétention d'en avoir
fait une liste complète, et sans doute, en existent-ils d'autres.
I.1.4.1.1. Les défauts de rentabilité
propres à la maintenance Les principaux défauts propres
à la maintenance sont provoqués par :
a. Défauts dans la conception de la définition des
travaux ;
b. Défauts dans l'étude des méthodes ;
c. Défauts dans l'allocation des temps ;
d. Défauts dans la tenue des délais ;
e. Défauts des méthodes ou de rendement dans
l'exécution ;
f. Défauts de qualité dans l'exécution ;
g. Défauts dans l'organisation de la maintenance
préventive ou maintenance corrective ;
Un document permettant une bonne organisation des inspections
est la fiche de visite (fig.1.1)
Nom :
|
N°
|
Organe
|
N
|
F
|
R
|
Date :
|
1
|
Compresseur
|
X
|
|
|
Heure :
|
2
|
Pompe
|
|
X
|
|
|
3
|
Générateur
|
|
|
X
|
N= rien à signaler : Normal
F= petite réparation exécution de suite R=
réparation
Fig.I.1 : Fiche de visite
13
h. Défauts d'organisation générale ;
i. Manque de moyens ;
j. Défauts dans la politique de la sous-traitance.
I.1.4.1.2. Défauts de rentabilité
intéressant d'autres services que la maintenance
a. Défauts d'approvisionnement ;
b. Défauts dans la gestion des stocks ;
c. Défauts d'organisation comptable ;
d. Défauts de sécurité ;
e. Défauts découlant des fautes propres à
la nature de la production.
I.1.4.2. Les politiques de maintenance
Maintenance
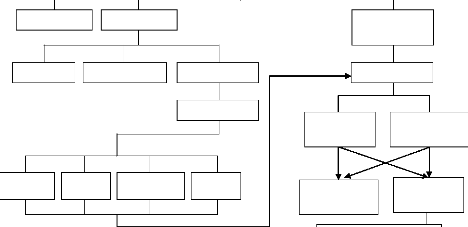
Contrôle
Prédictive
Corrective
Ronde
Tx systmatiques
Préventive
Inspection
Conditionnelle
Etat du bien
Visite
Dépannage ou Mce palliative
Défaillance partielle
Palliative et curative
Défaillance
Défaillance totale (panne)
Réparation
Avec modification Mce
d'amélioration
Sans modification Mce curative
Fig.I.2 : Concepts et différents travaux dans le
cadre de la Maintenance d'un équipement
14
I.1.4.3. Emploi préférentiel des diverses
formes de maintenance Le chef de maintenance qui dispose de plusieurs
méthodes :
? Maintenance corrective ; ? Maintenance préventive :
- Par visites systématiques ou conditionnelle
(prédictive) ; - Par travaux systématiques.
? Maintenance palliative ou curative :
- Dépannage ; - Réparations.
Il doit utiliser de préférence l'une ou l'autre
de ces méthodes, en fonction de l'évolution de l'état du
matériel pour obtenir un coût de maintenance minimum. C'est ainsi
que pendant la phase d'installation et de mise en route d'un matériel,
prédominance sera donnée à la maintenance corrective qui
sera sans doute pratiquée avec intérêt pendant les 2 ou 3
premières années de fonctionnement.
Pendant la vie normale du matériel, on donnera le pas
à la maintenance préventive et celle-ci sera d'autant plus
importante qu'il s'agira d'une machine-clé pour la production.
On commencera par des visites systématiques dès
l'arrivée du matériel dans l'entreprise puis l'on continuera par
des travaux de révisions systématiques intercalées avec
des inspections tant que l'état du matériel conditionnera la
production. Au contraire, pour des machines devenues vétustes, la
maintenance palliative sera sans doute plus rentable et l'on attendra que le
matériel tombe en panne pour procéder à sa
réparation.
C'est grâce à un contrôle comptable que le
chef de maintenance sera à même de déterminer exactement le
moment où un changement de méthode s'impose. Cela
nécessitera une comptabilisation de toutes les interventions
pratiquées sur le matériel de l'entreprise et la
récapitulation annuelle des dépenses par machine et par type de
maintenance.
15
I.1.4.3.1. Organisation de la maintenance
corrective
Dans les processus industriels, que le fonctionnement soit
discontinu ou continu pour le maintien ou la remise en état de l'outil
de production, nous chercherons à améliorer la qualité de
l'intervention qui doit se traduire par une meilleure qualité du produit
fabriqué ou du service rendu et à diminuer le « temps propre
d'indisponibilité» par une organisation appropriée et une
mise en oeuvre de moyens adaptés.
S'effectue à 3 niveaux afin de réduire les
immobilisations des
matériels :
· avant la panne,
· au déclenchement de la panne,
· après la panne.
a) Organisation avant la panne
Il faut pouvoir rassembler tous les moyens nécessaires
à une intervention rapide.
Connaissant l'organisation et la structure du service nous
pouvons récupérer rapidement :
? La documentation relative au
matériel
? Le dossier technique :
il comprend tous les renseignements et documents qui concernent un
même type de machine :
· Eléments d'identification : désignation
du type, constructeur, caractéristiques générales,
listes des machines du même type, fiche technique ;
· Répertoire des documents classés dans le
dossier ;
· Synthèse des modifications effectuées
sur ces machines ;
· Nomenclature de la machine ;
· Instructions de maintenance.
? Le dossier historique : il
comprend tous les renseignements et documents concernant la vie d'une machine
:
· Les modifications, y compris les améliorations de
maintenance ;
· Les commandes extérieures ;
· Les ordres de travaux ;
· Les rapports d'expertise ou d'incident ;
· La fiche historique :
16
Relative à chaque machine, regroupe les informations
concernant les interventions de maintenance effectuées :
· Numéro d'ordre des travaux ;
· Date d'exécution ;
· Nature et désignation du travail ;
· Temps passé ;
· Coût de l'intervention ;
· Durée d'arrêt à l'intervention ;
· Nombre d'unités d'usage ou d'heures de
fonctionnement.
? Documentation relative aux
travaux
? La demande de travail (DT)
: elle émane le plus souvent d'un responsable
production qui la dirige vers le responsable de maintenance qui
l'enregistre.
? L'ordre de travail (OT) : c'est
la fiche d'ordonnancement qui comporte tous les éléments relatifs
à la programmation et au lancement (dates, délais,
matières et outillages, éléments de
sécurité).
? Le bon de travail (HT) : il
constitue l'interface
« méthodes/réalisation ». Tous les
éléments relatifs à la quantification et à la
qualification du travail y figurent, de façon à permettre la
valorisation du bon (estimation du coût de maintenance).
Les trois fiches précédentes ne sont valables
que si le travail à faire ne comporte qu'une seule phase (ensemble
d'opérations confiées à un même ouvrier ou une
même équipe, dont le début et la fin sont bien
définis, et dont le contenu est contrôlable).
Elles sont le plus souvent regroupées sur un carnet
à souche dont le numéro d'OT est pré imprimé.
? L'outillage de première urgence :
pour respect des règlements de sécurité ; de
contrôle ; de mesure ; de diagnostic ; etc.
17
b) Organisation au moment du déclenchement de la
panne A ce niveau nous dégageons 3 phases importantes.
1ère phase : enregistrement de
l'appel
Il peut provenir d'une alarme, d'un coup de
téléphone, d'un télex, d'une communication orale ou par
écrit (demande de travaux de maintenance).
2ème phase : l'analyse du travail
Dans un premier temps, il faut appliquer ou faire appliquer
les consignes pour une intervention immédiate. Elles peuvent être
liées à la sécurité, aux arrêts de
production, au nettoyage préalable des abords.
Il faut ensuite organiser le poste de travail, rassembler les
moyens matériels, constater les anomalies pouvant se présenter et
voir le meilleur moyen d'y remédier.
3ème phase : la discussion au niveau de
l'analyse
Nous pensons qu'à ce stade il faut se poser les
questions de la méthode interrogative : « Quoi ? Qui ? Quand ?
Où ? Comment et combien ? » Afin de ne pas faire une intervention
trop poussée et choisir entre le dépannage (intervention
provisoire) et la réparation (intervention définitive).
Contrairement au dépannage, à chaque fois que
cela est possible, la réparation se fait dans l'atelier central
plutôt que sur le site. Le travail est ainsi réalisé dans
de meilleures conditions.
Une réparation méthodique passe
nécessairement par les étapes suivantes : diagnostiquer les
causes de panne ; expertiser le matériel ; décider si
l'intervention doit se faire sur le site ou dans l'atelier de maintenance ;
préparer le poste de travail ; respecter les consignes de
sécurité ; rassembler les moyens matériels et humains.
18
c) Organisation après la panne
Après l'intervention en dépannage le technicien
a plusieurs tâches à effectuer :
· faire le compte rendu de l'intervention ;
· déclencher éventuellement une remise en
service du matériel pour le personnel utilisateur ;
· mettre à jour le stock de pièces
détachées ;
· exploiter les résultats des dépannages
;
· corriger la gamme-type de démontage ou
d'auscultation ;
· mis à jour de l'historique des pannes.
I.1.4.3.2. ORGANISATION DE LA MAINTENANCE
PRÉVENTIVE
1. Organisation de la maintenance préventive
systématique
Ces opérations étant parfaitement
stabilisées dans le temps, permettent une organisation rationnelle.
Cependant elles doivent être utilisées à bon escient, le
critère « coût » étant un élément
déterminant dans le choix de cette méthode. Les interventions se
faisant à partir d'un échéancier préétabli,
la mise en oeuvre des moyens en personnels et en matériels, des
procédures de sécurité, des procédures
d'intervention (chronologie des opérations, réglages) se fait
avec un minimum d'aléas. Les types de travaux entrant dans le cadre de
cette maintenance autorisent une préparation rigoureuse, précise
et conséquente. La répétitivité de ces tâches
permet de rentabiliser facilement l'aspect méthode. Le compte rendu
d'intervention est très important notamment pour les opérations
de surveillance (inspection et visite) et permettra une exploitation
ultérieure.
2. Organisation de la maintenance préventive
conditionnelle
Le choix du matériel où sera appliquée
cette méthode étant fait (matériel stratégique d'un
processus de production), nous pouvons mettre en évidence les
différentes étapes du suivi du matériel en exploitation.
Cette méthode de maintenance implique la mise en oeuvre de techniques de
contrôle en cours de fonctionnement. A ce titre se posent deux questions
fondamentales :
· quelle(s) technique(s) utilisée(s) ?
· quelles modalités de mise en oeuvre adopter ?
5. Choisir l'accéléromètre sachant que
l'accéléromètre idéal devrait avoir une très
grande sensibilité, une large gamme de fréquence, un très
faible poids.
19
a- Parmi les techniques de contrôle en cours de
fonctionnement nous avons : l'analyse des huiles de lubrification,
l'analyse des vibrations, l'évaluation et le suivi des performances, la
thermographie, etc...
La technique vibratoire est celle qui donnera le plus grand
nombre de renseignements notamment dans le domaine des machines tournantes.
b- Modalités de mise en oeuvre pour une analyse
de vibrations
1. Prendre connaissance des principales causes de vibrations,
exemples : balourds, défauts d'alignements, lubrification insuffisante
ou/et les caractéristiques mal adaptées, défauts de
fixation au sol, perturbations dues à la circulation des fluides,
phénomènes de résonance, mauvaise mise à la terre
des rotors et des stators pour les moteurs, etc.
2. Identifier la ou les causes les plus probables.
3. Avoir une idée sur la nature des vibrations.
Sachant qu'une vibration correspond à un mouvement oscillatoire, ce
mouvement peut être périodique, aléatoire ou
transitoire.
4. Choisir le facteur le mieux adapté permettant
d'interpréter les vibrations. Trois paramètres peuvent
décrire une vibration :
? le déplacement qui est la distance parcourue par le
point de mesure depuis sa position neutre. Il est proportionnel à la
contrainte dans le matériau et se mesure en millimètres (mm) ;
? la vitesse qui est la rapidité à laquelle se
déplace le point de mesure. Elle se mesure en millimètres par
seconde (mm/s) ;
? l'accélération qui est la variation de la
vitesse avec le temps. Elle est proportionnelle à la force
appliquée sur l'objet, et se mesure en mètres par seconde au
carré (m/s2).
Les valeurs de ces trois paramètres sont reliées
entre elles par une fonction de la fréquence f et du temps, ce qui
permet, en détectant l'accélération, de pouvoir convertir
ce signal en termes de vitesse à l'aide d'intégrateurs
électroniques.
Les mesures des déplacements sont effectuées
pour le contrôle de phénomènes vibratoires à basse
fréquence. Les mesures d'accélération sont
utilisées pour les délections de phénomènes
vibratoires à haute fréquence. Cependant la vitesse de vibration
est souvent considérée comme le meilleur paramètre
utilisable sur une large gamme de fréquence.
20
Ces conditions étant incompatibles, il faut trouver un
compromis idéal. Certains accéléromètres ont
été étudiés pour supporter d'extrêmes
conditions d'environnement.
6. Choisir l'emplacement de
l'accéléromètre en fonction de critères
prédéterminés et d'indications proposées par le
fabriquant du matériel de contrôle des vibrations.
7. Définir les précautions à prendre au
montage de l'accéléromètre.
8. Choisir la mesure la mieux appropriée au cas
considéré. Il y a deux façons de rendre utilisables les
signaux de vibrations :
· mesure du niveau global des vibrations à l'aide
d'un simple mesureur de vibrations ;
· analyse en fréquence qui consiste à
découper le signal de vibrations en bandes de fréquences dans
chacune desquelles le niveau est mesuré.
La mesure du niveau donne l'indication de la
sévérité des vibrations, mais quand on veut
connaître les causes d'une vibration excessive, la possibilité
d'en mesurer la fréquence est d'une aide précieuse.
L'enregistrement des mesures et des graphiques des courbes de
tendance se fait :
· soit sur microfilm ;
· soit sur ordinateur avec sortie sur imprimante.
9. Analyser le spectre.
La technique d'analyse la plus puissante est l'analyse spectrale
en fréquence :
· car des variations mineures de certaines composantes
spectrales n'affecteront pas nécessairement le niveau vibratoire global,
mais seront décelables dans le spectre de fréquence, et
indiqueront souvent la naissance d'une panne ;
· car une augmentation du niveau vibratoire global
indique que quelque chose s'est modifié, mais ne donne aucune indication
quant à la source du changement, tandis que ceci est souvent
indiqué par la fréquence à laquelle le changement est
intervenu.
10. Détecter la future défaillance.
L'une des approches du problème de la détection
d'un défaut dans les conditions de fonctionnement est la comparaison des
niveaux vibratoires avec des critères standards.
11. Diagnostiquer les causes de défaillance.
21
La fréquence à laquelle apparaît une
variation dans le spectre donne une information fondamentale sur la source
probable, qui est souvent reliée par exemple à l'une des vitesses
de rotation.
c- Les matériels
Les appareils peuvent être installés de
façon permanente ou être utilisés manuellement en capteur
mobile.
L'utilisation rationnelle par la mesure d'ondes de choc offre
les avantages suivants : elle assure une surveillance objective de
l'état des roulements, elle supprime le risque d'un arrêt
inopiné de la production, elle permet de planifier le travail de
maintenance corrective à effectuer et donne le moyen d'utiliser chaque
roulement au maximum de ses possibilités.
I.1.5.LES OPÉRATIONS DE MAINTENANCE
I.1.5.1 OPERATIONS DE MAINTENANCE CORRECTIVE Ces
opérations peuvent être classées en trois groupes d'actions
:
? Le premier groupe concerne la localisation de la
défaillance ; il
comprend les opérations suivantes : le test, la
détection, le dépistage et le diagnostic.
? Le deuxième groupe concerne les opérations de
la remise en état ; il comprend les opérations suivantes : le
dépannage, la réparation et la modification soit et du
matériel ou du logiciel.
? Le troisième groupe concerne la durabilité ;
il comprend les opérations suivantes : la rénovation, la
reconstitution et la modernisation.
I.1.5.2. LA LOCALISATION DE DEFAILLANCE
C'est l'action qui conduit à rechercher
précisément le (les) élément(s) par le(s) quel(s)
la défaillance se manifeste.
Le test : c'est une opération qui
permet de comparer les réponses d'un système à une
sollicitation appropriée et définie, avec celles d'un
système de référence, ou avec un phénomène
physique significatif d'une marche correcte.
La détection : c'est l'action de
déceler au moyen d'une surveillance accrue, continue ou non,
l'apparition d'une défaillance ou l'existence d'un élément
défaillant.
Le dépistage : c'est une action qui
vise à découvrir les défaillances dès leur
début par un examen systématique sur des équipements
apprenant en état de fonctionnement.
22
Le diagnostic : c'est l'identification de la
cause probable de la (ou les ) défaillance(s) à l'aide d'un
raisonnement logique fondé sur un ensemble d'informations provenant
d'une inspection, d'un contrôle ou d'un test. Le diagnostic permet de
confirmer, de compléter ou de modifier les hypothèses faites sur
l'origine et la cause des défaillances et de préciser les
opérations de maintenance corrective nécessaires.
I.1.5.3. LA REMISE EN ETAT
La remise en état de fonctionnement peut consister
à réaliser l'une des opérations suivantes.
A. LE DÉPANNAGE a) Définition
C'est une action sur un bien en panne, en vue de le remettre
en état de fonctionnement ; compte tenu de l'objectif, une action de
dépannage peut s'accommoder de résultats provisoires et de
conditions de réalisation hors règles de procédures, de
coûts et de qualité, et dans ce cas sera suivie de la
réparation.
h) Conditions d'applications
Le dépannage, opération de maintenance
corrective, n'a pas de conditions d'applications Particulières. La
connaissance du comportement du matériel et des modes de
dégradation n'est pas indispensable même si cette connaissance
permet souvent de gagner du temps.
Souvent les interventions de dépannage sont de courtes
durées mais peuvent être nombreuses. De ce fait les services de
maintenance, soucieux d'abaisser leurs dépenses, tentent d'organiser les
actions de dépannage. D'ailleurs certains indicateurs de maintenance,
pour mesurer son efficacité, prend en compte le problème du
dépannage.
c) Cas d'applications
Ainsi le dépannage peut être appliqué par
exemple sur des équipements fonctionnant en continu dont les
impératifs de production interdisent toute visite ou intervention
à l'arrêt.
23
B. LA RÉPARATION a) Définition
C'est une intervention définitive et limitée de
maintenance corrective après défaillance.
h) Conditions d'applications
L'application de la réparation, opération de
maintenance corrective, peut être décidée, soit
immédiatement à la suite d'un incident, ou d'un d'une
défaillance, soit après dépannage, soit après une
visite de maintenance préventive conditionnelle ou
systématique.
c) Cas d'application
Tous les équipements sont concernés.
C. LA MODIFICATION
C'est une opération à caractère
définitif effectuée sur un bien en vue d'en améliorer le
fonctionnement, ou d'en changer les caractéristiques d'emploi.
I.1.5.4. LA DURABILITÉ
La durabilité est la durée de vie ou
durée de fonctionnement potentielle d'un bien pour la fonction qui lui a
été assignée dans des conditions d'utilisation et de
maintenance données.
Les opérations maintenance qui concernent la
durabilité d'un bien sont les suivantes.
La rénovation : inspection
complète de tous les organes, reprise dimensionnelle complète ou
remplacement des pièces déformées, vérification des
caractéristiques et éventuellement réparation des
pièces et sous-ensembles défaillants, conservation des
pièces bonnes.
La rénovation apparaît donc comme l'une des
suites possibles dune révision générale au sens strict de
sa définition.
La reconstitution : remise en l'état
défini par le cahier des charges initial, qui impose le remplacement de
pièces vitales par des pièces d'origine ou des pièces
neuves équivalentes. La reconstruction peut être assortie d'une
modernisation ou de modifications.
24
Les modifications apportées peuvent concerner, en plus
de la maintenance et de la durabilité, la capacité de production,
l'efficacité, la sécurité, etc.
La modernisation : remplacement
d'équipements, accessoires et appareils ou éventuellement de
logiciel apportant, grâce à des perfectionnements techniques
n'existant pas sur le bien d'origine, une amélioration de l'aptitude
à l'emploi du bien.
Cette opération peut aussi bien être
exécutée dans le cas d'une rénovation, que celui d'une
reconstruction. La rénovation ou la reconstruction d'un bien durable
peut donner lieu, pour certains de ses sous-ensembles, à la pratique
d'un échange standard.
Echange standard : c'est la reprise d'une
pièce, d'un organe ou d'un sous-ensemble usagé, et vente au
même client d'une pièce, d'un organe ou d'un sous-ensemble, neuf
ou remis en état conformément aux spécifications du
constructeur, moyennant le paiement d'une soulte dont le montant est
déterminé d'après le coût de remise en
état.
Soulte : somme d'argent qui, dans un
échange ou dans un partage compense l'inégalité de valeur
des lots ou des biens échangés. Afin d'accélérer
les procédures et de diminuer les coûts, le recouvrement de la
soulte peut être forfaité.
I.1.5.5. OPÉRATIONS DE MAINTENANCE
PRÉVENTIVE Ces opérations peuvent être
classées en quatre groupes d'actions.
? Le premier groupe concerne les travaux systématiques
; il comprend les opérations suivantes : le nettoyage, la
dépollution et le retraitement de surface.
? Le deuxième groupe concerne la surveillance ; il
comprend les opérations suivantes : l'inspection le contrôle et la
visite.
? Le troisième groupe concerne la révision ; il
comprend les opérations suivantes : la révision partielle et la
révision générale.
? Le quatrième groupe concerne la préservation ;
il comprend les opérations suivantes : la mise en conservation, la mise
en survie et la mise en service.
25
I.1.5.5.1. Les Travaux systématiques
Les travaux systématiques comprennent les
opérations courantes et régulières de la maintenance
préventive tels que le nettoyage, la dépollution et le
retraitement de surface qu'ils soient externes ou internes. Par exemple, on
peut signaler pour le nettoyage extérieur l'existence de divers types de
nettoyage en fonction de la structure et de l'état d'un bien, des
produits utilisés et de la méthode employée (les solutions
alcalines aqueuses, les solvants organiques, le soufflage aux abrasifs, etc.).
Il faut aussi préciser que le retraitement de surface inclut les
opérations suivantes de la lubrification et de graissage.
I.1.5.5.2. LA SURVEILLANCE
Les termes définis ci-après sont
représentatifs des opérations nécessaires pour
maîtriser l'évolution de l'état réel du bien,
effectuées de manière continue ou à des intervalles
prédéterminés ou non, calculés sur le temps ou le
nombre d'unités d'usage.
L'inspection : c'est une activité de
surveillance s'exerçant dans le cadre d'une mission définie. Elle
n'est pas obligatoirement limitée à la comparaison avec des
données préétablies. Cette activité peut s'exercer
notamment au moyen de ronde.
Le contrôle : c'est une
vérification de la conformité à des données
préétablies, suivie d'un jugement. Le contrôle peut :
? comporter une activité d'information,
? inclure une décision : acceptation, rejet,
ajournement,
? déboucher sur des actions correctives.
La visite : c'est une opération
consistant en un examen détaillé et
prédéterminé de tout (visite générale) ou
partie (visite limitée) des différents éléments du
bien et pouvant impliquer des opérations de maintenance du 1er
niveau.
I.1.5.5.3 LA RÉVISION
C'est l'ensemble des actions d'examens, de contrôles et
des intervenions effectuées en vue d'assurer le bien contre toute
défaillance majeure ou critique pendant un temps ou pour un nombre
d'unités d'usage donné. Il est d'usage de distinguer suivant
l'étendue de cette opération les révisions partielles des
révisions générales. Dans les deux cas, cette
opération implique la dépose de différents sous-ensembles.
Ainsi le terme de révision ne
26
doit en aucun cas être confondu avec les termes visites,
contrôles, inspections, etc. Les deux types d'opération
définis (révision partielle ou générale)
relèvent du 4ème niveau de la maintenance.
I.1.5.5.4. LA PRÉSERVATION
Elle comprend les opérations suivantes :
La mise en conservation : c'est l'ensemble
des opérations devant être effectuées pour assurer
l'intégrité du bien durant les périodes de
non-utilisation.
La mise en survie : c'est l'ensemble des
opérations devant être effectuées pour assurer
l'intégrité du bien durant les périodes de manifestations
de phénomènes d'agressivité de l'environnement à un
niveau supérieur à celui défini par l'usage de
référence.
La mise en service : c'est l'ensemble des
opérations nécessaires, après l'installation du bien
à sa réception, dont la vérification de la
conformité aux performances contractuelles.
I.1.6. ORGANISATION DES TRAVAUX
NEUFS1
I.1.6.1. Fonctions principales
Un service « travaux neufs » a deux fonctions
principales :
? Etudier, exécuter et mettre en place des
installations nouvelles, dans le but d'augmenter la capacité de
production de l'usine ;
? Etudie et réaliser des modifications aux
installations et matériels existants, pour améliorer, soit le
rendement de ces installations, soit la qualité de leur production.
I.1.6.2. Taches élémentaires
Qu'il s'agisse d'équipement de capacité ou de
productivité, la caractéristique principale des travaux
réside dans la recherche d'un prix de revient minimum,
comptabilité avec la qualité nécessaire.
Il faut donc les organiser et les contrôler de
près, ce qui oblige à exécuter les tâches
élémentaires suivantes pour chaque travail neuf important :
1 R. JABOT, Entretien et travaux neufs, hommes et
techniques, Puteau 1969
27
· Etablir un avant projet sommaire ;
· Chiffrer grossièrement ct avant propos ;
· Vérifier par un enquête l'utilité
et la rentabilité du travail prévu) partir des résultats
de l'avant projet ;
· Dans l'affirmative poursuivre l'étude
détaillée ;
· L'étude terminée, établir un
devis précis, en ébauchant simultanément la
préparation du travail ;
· Demandé l'accord définitif de la
direction sur le projet chiffré ;
· Terminer la préparation détaillée
du travail ;
· Sous-traiter, le cas échéant, les
travaux que l'on ne peut faire à bonnes conditions dans l'entreprises
;
· Réaliser ou surveiller la réalisation
des travaux en contrôlant en cours divers corps d'état, la tenue
des détails ;
· Provoquer à temps la prise de toute mesure
corrective utile pour la tenue des détails et le respect du prix
initialement prévu.
L'organisation des « travaux neufs
» doit donc permettre la réalisation permanente de ces
élémentaires.
I.1.6.3. Justification du rattachement des travaux
neufs à la maintenance
I.1.6.3.1. Cas des petites entreprises
Dans la plupart des petites et moyennes entreprises, le
service des installations nouvelles ne fait qu'un avec le service de
maintenance.
Cette unification est normale :
· Si la totalité des deux services ne groupe
qu'un effectif réduit, car le taux d'emploi de la main-d'oeuvre sera
meilleur dans une seule équipe moyenne que dans deux équipes
minuscules ;
· Dans le cas où les techniciens de la
maintenance sont les seuls à connaitre les différents corps
d'état nécessaires à la construction des bâtiments
ou à la réalisation des installations ;
· Car elle permet aux gens de la maintenance qui vont
etre chargés de réparer un matériel, de prendre contact
avec ce matériel dès son origine et d'assister à sa
conception permanente de l'étude et du travail en cours de
réalisation pour gêner au minimum la fabrication, oblige à
recevoir au service maintenance déjà ridé à une
telle souplesse ;
· Dans le cas où le travail est
sous-traité à des entreprises extérieures, car alors les
sous-traitants doivent trouver en face d'eux, non un directeur, un financier,
ou un fabricant, mais un technicien connaissant parfaitement le travail
à réaliser, capable de jouer le rôle de maitre d'oeuvre
pour l'ensemble des exécutants, et d'assurer les liaisons avec
28
les divers services de l'entreprise. Un cadre de la maintenance
est parfaitement capable de tenir ce rôle.
I.1.6.3.2. Cas des entreprises importantes
Dans les importantes ou les équipes «
travaux neufs » et « maintenance
» sont respectivement très nombreux les deux services sont
en général, séparés.
Nous estimons, toutefois, qu'ils doivent constituer un
département « maintenance-construction »
dirigé par un chef de service unique.
Cette solution permet d'assurer le meilleur taux d'emploi du
personnel par des déplacements d'ouvrier, vers le dépannage en
cas des pannes importantes, ou vers les travaux servir de régulateurs de
charge.
En fin, si les deux services « maintenance
» et « travaux neufs » ont une
direction unique, le bureau d'études des travaux neufs possède
mieux l'optique suffisante pour se défendre contre un usager qui, voyant
son projet coûter plus cher que prévu, tente de faire diminuer la
marge de sécurité, la précision ou la finition
d'exécution pour arriver à l'installation prévue dans les
limites de son crédit, ce qui se traduira invariablement par une
augmentation du coût de maintenance ultérieure.
Dans tous le cas, la réunion des travaux neufs
à la maintenance permet à celui-ci de mieux connaître les
installations qu'il a lui-même mis en place, et aux travaux neufs
d'éviter toute erreur qui augmenterait ensuite les difficultés de
maintenance.
I.1.7. LES NIVEAUX DE MAINTENANCE
En fonction de la politique de maintenance et du potentiel
humain et technique de l'entreprise, les opérations de maintenance sont
décomposées en cinq niveaux d'intervention du simple
réglage (1er niveau) à l'opération lourde de maintenance
confiée à un atelier central ou à une unité
extérieure (5ème niveau). Ces niveaux sont donnés à
titre indicatif et leur utilisation n'est concevable qu'entre des parties qui
sont convenues de leur définition précise selon le type du bien
à entretenir.
Cependant, il est important de noter que la tendance actuelle
est de se ramener à trois niveaux seulement dans une logique de
TPM1. A savoir : I = 1 + 2 : c'est la maintenance
de première ligne transférée progressivement aux
opérateurs de production, assisté si nécessaire par les
techniciens de maintenance.
1 TPM=Total Production Maintenance
29
II = 3 + 4 : domaine d'action privilégié des
équipes polyvalentes de techniciens de maintenance. Diagnostics,
interventions techniquement évoluées, mis en oeuvre
d'amélioration, etc.
III = 5 : travaux spécialisés souvent
sous-traités pour que la maintenance puisse recentrer ses moyens sur son
savoir-faire c'est-à-dire le niveau II.
30
Tableau I.1. Les cinq niveaux de
Maintenance
Niveau
|
Personnel intervenant
|
Nature de l'intervention
|
Moyens requis
|
Interventions et opérations
|
1
|
L'exploitant du bien sur place.
|
Réglages simples,
généralement prévus par le
constructeur, au moyen
d'organes accessibles sans
aucun démontage ou
aucune ouverture de
l'équipement, ou échange
d'éléments consommables en toute
sécurité tels que voyants ou certains fusibles, etc.
|
Sans outillage ou outillage
léger et à l'aide des instructions
d'utilisation et de conduite. Le stock des
pièces consommables nécessaires dans ce cas est
très
faible.
|
- Niveau d'huile moteur ;
- Niveau d'eau ;
- Indicateur de colmatage ;
- Niveau de la réserve de combustible ;
- Niveau de la réserve d'huile ; - Régime du
moteur ;
- Température de l'eau de refroidissement ;
- Température d'échappement ;
- Test des voyants et indicateurs ;
- Purge de circuit d'échappement ;
- Nettoyage des filtres ;
- Contrôle visuel de l'état des organes ;
- Contrôle auditif des bruits de marche.
|
2
|
Un technicien habilité*
de qualification moyenne ou un ouvrier qualifié de
maintenance
(dépanneur) sur place.
Ce dernier suit les
|
Dépannage par échange
standard des éléments
prévus à cet effet, ou
opérations mineurs de maintenance préventive,
par exemple de graissage ou de
|
Outillage standard ou
spécial, les pièces de
rechanges situés à proximité
immédiate sont des types consommables
; filtres, joints, huile,
|
- Remplacement des filtres à
gazole ;
- Remplacement des filtres à huile moteur ;
- Remplacement des filtres à air ;
|
|
31
|
instructions de
maintenance qui
définissent les tâches, la manière et les
outillages spéciaux.
|
contrôle de bon
fonctionnement.
|
liquide de
refroidissement. Suivant
les instructions de maintenance.
|
- Prélèvement d'huile pour
analyse ;
- Vidange de l'huile de moteur ;
- Analyse de liquide de refroidissement ;
- Contrôle des points signalés pour le
1er niveau ;
- Graissage de tous les points en fonction de la
périodicité ; - Contrôle des batteries.
|
3
|
Un technicien spécialisé
ou un ouvrier spécialisé
de maintenance sur
place ou en atelier de maintenance, avec l'aide
d'instructions de
maintenance et d'outils spécifiques.
|
Identification et diagnostic
des pannes, réparation par échange de composants
ou
d'éléments fonctionnels,
réparations mécaniques
mineures, et toutes
opérations courantes de
maintenance préventive
telles que réglage général
ou réalignement des appareils de mesure.
|
Outillage plus appareils de mesure et de réglage ou de
calibrage prévus dans
les instructions de
maintenance, et éventuellement des bancs
d'essais et de contrôle des équipements et en
utilisant l'ensemble de la documentation nécessaire à la
maintenance du bien,
ainsi que les pièces
approvisionnées par le magasin.
|
- Réglage des jeux des
soupapes ;
- Réglages des injecteurs ;
- Contrôle des sécurités du moteur ;
- Contrôle et réglage des protections
électriques ;
- Contrôle des refroidisseurs ; - Contrôle du
démarreur ;
- Remplacement d'un injecteur ;
- Contrôle et réglage de la régulation de
puissance ;
- Contrôle et révision de la pompe ;
- Contrôle des turbocompresseurs ;
- Remplacement d'une
|
|
32
|
|
|
|
résistance de chauffe ;
- Contrôle de l'isolement électrique ;
- Remplacement des sondes et capteurs ;
- Remplacement d'une bobine de commande, remplacement d'un
disjoncteur.
|
4
|
Des techniciens
bénéficiant d'un
encadrement technique
très spécialisé, ou une
équipe comprenant un
encadrement technique très spécialisé,
dans des
ateliers spécialisés (rectification,
réusinage).
|
Tous les travaux importants
de la maintenance
préventive ou corrective à
l'exception de la
reconstruction et de la
rénovation. Ce niveau comprend aussi le
réglage
des appareils de mesure utilisés pour la
maintenance
et, éventuellement, la
vérification des étalons de travail par des
organismes
spécialisés. Plus les opérations de
révision.
|
Outillage général complet
et outillage spécifique (moyens mécaniques, de
câblage et de nettoyage).
Eventuellement, des bancs de mesures et des
étalons de travail
nécessaires, à l'aide de
toutes documentations générales
ou particulières.
|
- Déculassage (révision,
rectification) ;
- Révision de la cylindrée ;
- Contrôle d'alignement du moteur / alternateur ;
- Changement des pôles d'un disjoncteur Haute
Tension.
|
5
|
Une équipe complète
polyvalente en atelier
spécialisé ou par le constructeur lui
même.
|
Travaux de rénovation, de reconstruction ou
exécution des réparations importantes
confiées à un atelier
spécialisé ou une
unité extérieure de maintenance
|
Moyens proches de ceux de fabrication définis par le
constructeur.
|
Il s'agit d'opérations lourdes de rénovation ou de
reconstitution d'un équipement.
|
|
33
I.2. NOTION DE SURETE DE
FONCTIONNEMENT
I.2.1. Définitions
La sûreté de fonctionnement est
l'aptitude d'une entité à satisfaire à une ou plusieurs
fonctions requises dans des conditions données.
Selon Jean-Claude LAPRIE « elle est la
propriété qui permet aux utilisateurs du système de placer
une confiance justifiée dans le service qu'il leur délivre
»
Au sens large, la sûreté de
fonctionnement est considérée comme « La science des
défaillances et des pannes ». Elle consiste en analyse, mesure,
traitement, modélisation, prévention,...
Elle englobe principalement différents
paramètres tels que : la fiabilité, la disponibilité, la
maintenabilité et la sécurité (qui forment le sigle FDMS).
La sûreté de fonctionnement couvre toutes les étapes du
cycle de vie d'un système : conception, fabrication,
exploitation.
I.2.2. Défaillance
C'est l'altération ou la cessation de
l'aptitude d'un bien à remplir une fonction requise.
On distingue deux formes de défaillance : la
défaillance partielle et la défaillance
complète.
· Défaillance partielle :
«Altération de l'aptitude d'un bien à accomplir les
fonctions requises. »
· Défaillance complète :
«Cessation de l'aptitude d'un bien à accomplir la fonction requise.
»
Altération : défaillance partielle ou
dégradation. Cessation : défaillance totale ou panne
0 : état d'arrêt pour panne ou
défaillance totale
1 : état dégradé ou
défaillance partielle
2 : état de bon fonctionnement.
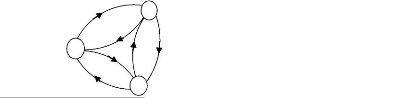
u1
1
u = taux de répartition [rép./h]
X, = taux de défaillance [déf./h]
X,1
O
X,2
u2
X,3
Fig.I.3.Chaine de MARKOV ou graphe de
transition
u3
2
1 C.T TSHAONA T. Marcel, Cours de logistique
industrielle, G3 Mécanique, ISTA, 2012
34
I.2.3. Durée de vie
C'est la durée dans laquelle un bien a accompli la
fonction qui lui a été assignée.
Durée prévisionnelle : déterminée
à la conception Durée opérationnelle exprimée :
? En unité de temps (années, heures, etc...) ?
En d'autres unités d'usages (cycles, etc...)
I.2.4. La fiabilité
Définition : d'après (Norme
AFNORX60-500)
Aptitude d'un équipement à accomplir une
fonction requise dans des conditions données, pendant un intervalle de
temps donné.
On suppose en général que l'entité est en
état d'accomplir la fonction requise au début de l'intervalle de
temps donné. Le concept de fiabilité est traduit souvent dans la
pratique comme l'aptitude d'une entité à avoir une faible
fréquence de défaillance.
R(t) : probabilité que l'entité accomplisse une
fonction requise dans des conditions données, pendant un intervalle de
temps donné (o,t).
I.2.5. La mainténabilité
Définition : d'après (Norme
AFNORX60-500)
? Aptitude d'un équipement a être maintenu ou
rétabli dans un état dans lequel il peut accomplir une fonction
requise, lorsque la maintenance est accomplie dans des conditions
données, avec des procédures et des moyens prescrits.
? M(t) : pour une entité utilisée dans des
conditions données d'utilisation, probabilité pour qu'une
opération donnée de maintenance puisse être
effectuée sur un intervalle de temps donné (O,t), lorsque la
maintenance est assurée dans des conditions données et avec
l'utilisation de procédures et moyens prescrits.
35
I.2.6. La Disponibilité
Définition : d'après (Norme
AFNORX60-500)
? Aptitude d'une entité à être en
état d'accomplir une fonction requise dans des conditions
données, à un instant donné ou pendant un intervalle de
temps donné, en supposant que la fourniture des moyens extérieurs
nécessaires soit assurée.
? D(t) : Probabilité qu'une entité soit en
état de disponibilité dans des conditions données,
à un instant donné en supposant que la fourniture des moyens
extérieurs nécessaires soit assurée.
I.2.7. La Sécurité
La capacité d'un produit à respecter, pendant
toutes les phases de vie, un niveau acceptable de risques d'accident
susceptible d'occasionner une agression du personnel ou une dégradation
majeure du produit ou de son environnement.
I.2.8. Traçabilité
Capacité d'un bien à être identifié
chaque moment dans des conditions données quand le besoin se fait
jour.
I.2.9. Testabilité
Aptitude d'une entité à être
déclarée défaillante dans des limites de temps
spécifiées, selon des procédures prescrites et dans des
conditions données.
I.3. NOTION DU BOIS
I.3.1. Définitions1
La Norme NFB50-003, définit le bois comme un ensemble
des tissus résistants secondaires qui forment les troncs, branches et
les racines de plantes ligneuses.
Le bois est une matière organique. Parmi ces principaux
constituants organiques nous pouvons citer la cellulose environ 50% et la
lignine environ 20%. Le bois est la matière ligneuse et compacte qui
compose les branches, le tronc et les racines d'un arbre. Chimiquement le bois
se
1
http://www.site-en-bois.net/fr/accueil.phtml
36
compose presque toujours de 50% de carbone, 42%
d'oxygène, 6%d'hydrogène, 1%d'azote et 1%
d'éléments divers. Le bois a des qualités et des
défauts dont il faut tenir compte dans le façonnage et surtout
dans l'assemblage, même des plus petits objets.
I.3.2. Structures
Le bois possède une structure complexe et variable en
fonction des essences. Tout d'abord, on observe une différence nette
entre l'écorce et le bois lui-même. Celui-ci est constitué
par l'aubier, partie périphérique du tronc située sous
l'écorce où circule la sève, et le bois de coeur ou
duramen.
I.3.3. Caractéristiques du bois
Le tronc d'un arbre est constitué de bois et
d'écorce. Une coupe transversale du tronc d'un arbre est montrée
sur la Fig. (1.4.). Dans certains cas la partie adjacente à
l'écorce (l'aubier) a une couleur plus claire que la partie interne
(duramen ou bois parfait). Pour de nombreuses essences, cette distinction de
couleur entre l'aubier et le duramen n'existe pas. Dans les arbres, le bois
exerce trois fonctions notamment, la conduction de la sève brute de la
racine vers les branches, le soutien de l'ensemble de l'arbre contre son poids
et les forces extérieures (du vent) et la réserve des substances
nutritives comme l'amidon. Les cellules du bois qui remplissent la fonction de
conduction dans l'aubier sont souvent mortes, tandis que les cellules vivantes
jouent le rôle de l'emmagasinement. Les cellules de conduction et de
soutien meurent entre 15 et 20 jours après leur formation, par contre
les cellules d'emmagasinement restent vivantes pendant plusieurs années.
La mort de ces dernières et la formation du bois parfait sont
accompagnées de la sécrétion des phénols
oxydés qui sont souvent à l'origine de la pigmentation du bois.
Pour des arbres où le bois parfait et le bois aubier ont la même
couleur la mort de ces cellules n'est pas accompagnée d'une
pigmentation. Les matériaux sécrétés sont
nommés les extractifs. Ils sont toxiques et augmentent la
durabilité du bois.
Le bois est généré entre l'aubier et
l'écorce dans l'assise génératrice, tandis que l'aubier
adjacent au bois parfait se convertit en duramen. La proportion d'aubier et de
bois parfait varie selon l'âge et l'essence de l'arbre. Le pourcentage
volumique des cellules vivantes dans l'aubier varie entre 10 et 40 %.
Parmi les résineux indigènes : les pins,
cyprès, épicéas, sapins, mélèzes,
cèdres (classement par ordre de densité croissante).
37
Ecorce
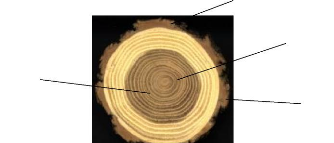
Moelle
Bois parfait
Aubier
Fig. I.4 : Section transversale d'un tronc
I.3.4. Classifications du bois
Outre les éléments de classification botanique,
une classification catégorielle permet de distinguer les
différents bois. Deux grandes catégories de bois sont
distinguées :
Les bois de pays ou indigènes,
Les bois étrangers ou d'importation.
Au sein de chacune de ces catégories, les bois feuillus
et résineux sont différenciés. La densité des bois
intervient aussi dans ce classement.
Ainsi, parmi les essences feuillues indigènes, nous
retrouvons:
Les bois tendres (densité 0,4 à 0,65) : le
peuplier, le saule, le tilleul, l'aulne, le bouleau et le tremble. Les bois
tendres sont ceux qui se laissent rayer facilement ; ils sont légers.
Plus un bois pousse rapidement, plus il est léger et tendre. Les bois
tendres sont abattus entre 30 et 50 ans.
Les bois demi-durs (densité 0,65 à 0,8) : le
charme, le
châtaignier, le chêne, l'érable, le
frêne, le hêtre, le merisier, le noyer, l'orme, le platane, le
poirier,
Les bois durs (densité 0,8 à 0,95) : le buis, le
chêne vert, le cornouiller, le sorbier,... les bois durs sont abattus,
entre 200 et 250 ans.
38
I.3.5. Utilisations du bois
Le bois a différentes utilisations, en partant du plus
valorisant vers le moins rémunérateur pour le propriétaire
forestier :
· Tranchage ou déroulage ;
· Ebénisterie ;
· Bois de fendage (pour faire des tonneaux...) ;
· Menuiserie ;
· Charpente ;
· Menuiserie de second choix ;
· Palettes.
I.3.6. Usinage
Nous distinguons deux opérations d'usinages :
I.3.6.1. Le sciage du bois1
Le bois est scié de différentes façons,
comme le montrent les schémas ci-après.
Ces schémas montrent la grume en coupe transversale,
avec la façon de les scier, en fonction des besoins des utilisateurs.
- Le schéma théorique correspond à
l'utilisation optimale des qualités mécaniques du bois, sans
chercher à tenir compte du rendement matière.
- Le débit sur boule est surtout utilisé pour
les bois en provenance des forêts tropicales, avec des grumes qui ont un
diamètre important, supérieur à celui des bois
européens.
- Le débit sur dosse est le plus courant en Europe : la
vitesse de travail est privilégiée au détriment du
rendement matière.
- Les débits sur maille, sur quartier et sur faux
quartier correspondent à des usages en menuiserie ou en
ébénisterie, où les qualités esthétiques
priment souvent sur celles mécaniques.
- Le débit varié est souvent utilisé dans
des scieries artisanales ou à façon, afin d'optimiser le
rendement d'une grume pour des besoins spécifiques, le plus souvent en
rénovation de charpente.
1
http://uipp.fr/app2.php-
Fig.I.6 : Le déroulage
39
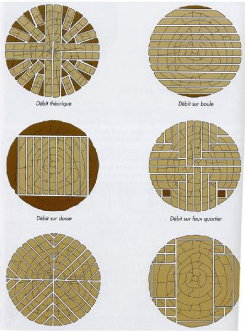
Débit varié
Fig.I.5 : Les modes de débit des troncs d'arbre
(grumes) en scierie vus en coupe
transversale.
I.3.6.2. Le déroulage et le tranchage du
bois
Le déroulage et le tranchage du bois sont des
procédés de découpage du bois nécessitant des
troncs de très bonne qualité
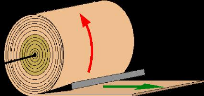
Fig.I.7 : Le tranchage
40
a) Le déroulage
Le peuplier pour les cagettes, les boites à camembert
et les allumettes. Déroulage d'une bille de bois : La bille de bois est
animée d'un mouvement de rotation. Un couteau est appuyé contre
la bille. Une mince feuille de bois en section tangentielle de largeur de la
bille et de longueur indéfinie est formée.
Ils sont utilisés abondamment sur la surface des
panneaux d'agglomérés et dans la fabrication des panneaux de
contreplaqués qui sont eux-mêmes utilisés en menuiserie et
en ébénisterie, dans la construction, la décoration
intérieure et extérieure, la fabrication des allumettes et des
emballages légers. Les modes de fabrication sont
schématisés au début de cette note.
h) Le tranchage
Les billons écorcés sont le plus souvent ouverts
en deux ou en quatre, l'aubier est généralement exclu, le bois
est « ramolli » par étuvage, puis tranché sur quartier,
faux quartier ou dosse.
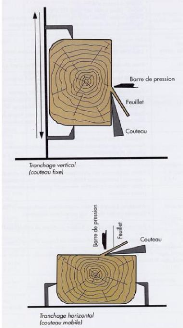
41
Les placages sont donc des feuilles de bois de faible
épaisseur (de quelques dixièmes de millimètre à
quatre ou cinq millimètres environ) obtenues par le tranchage des billes
et billons découpées dans les grumes. Ils sont collés sur
des supports en aggloméré ou sur des contreplaqués.
Ils constituent la meilleure valorisation des produits
forestiers tant feuillus que résineux. Chaque essence a en fait ses
utilisations potentielles.
42
CHAP.II : ETUDE SYSTEMIQUE DE LA DEROULEUSE N2700
II.1. PRESENTATION DE L'INDUSTRIE (I.T.B)
II.1.1. Historique!
L'Industrie de transformation du Bois I.T.B en sigle a vu le
jour au Mois de Juin 1987 Par Monsieur SABBAGH YOUSSEF associé à
Monsieur MUKADI KENG.C'est vers l'année 1988 que l'industrie a
commencé sa production.
En sa création, les associés visaient la
fabrication et la vente des multiplex et contre-plaqués, tant à
l'échelon national qu'international. L'usine comprenait une chaîne
de déroulage et une autre de contreplacage, une chaudière, et un
hangar de stockage de produits finis et matières premières. En
1991 est venu s'ajouter une scierie pour la production des planches, chevrons,
madriers et autres. De ce fait, la société I.T.B
s'approvisionnait en grumes auprès des sociétés telles que
SIFORCO, FORESCOM, SOCOBELAM, SCIBOIS, LOMATA,... et quelques particuliers.
Avec la guerre de libération de 1996 et 1997 ainsi que
la rébellion qui en a suivi en 1998, le ravitaillement de l'usine
était devenu problématique. Les associés avaient alors
pensé acquérir deux petits pousseurs qui pourraient alimenter
l'usine en bois flottants à partir des chantiers forestières.
Suite aux difficultés continuelles d'approvisionnement en grumes, les
associés ont décidé de faire leur propre exploitation
forestière.
Pour ce faire, en 2001, le gouvernement à travers le
ministère de l'environnement, donna à la société
I.T.B l'autorisation de prospecter dans la province de Bandundu, district de
Mai-Ndombe, territoires de Kutu et d'Oshwe, une forêt d'une superficie de
222.000 Ha. Après prospection, la société I.T.B n'a retenu
que la partie de la forêt située dans le territoire d'Oshwe d'une
superficie de 147.000 Ha.
Toutes les formalités d'usage faites, vers fin
décembre 2001, une garantie d'approvisionnement portant le
n°002/CAB/MIN/AFF-ET/01 fut accordée à la
société I.T.B sur cette forêt.
Le début effectif de l'exploitation forestière
n'a commencé qu'au mois d'Août 2002 avec la coupe des essences
flottantes telles que le Tôla, Aiele, Ako, Bomanga, Tiama et Tshitola.
Par insuffisances des moyens d'évacuation, des essences non flottantes
telles que les Wenge, Iroko et Kossipo n'étaient coupé qu'en
petite quantité.
1 ITB, Service du personnelle
43
Dans sa recherche de moyens d'évacuation des grumes non
flottantes qui paient mieux à l'export, la société I.T.B a
contacté la société commerciale et industrielle en
Afrique, en sièges SINCA qui, elle, possédait deux bateaux et
quatre barges pontons.
Pendant les négociations, il s'est avéré
que la société SINCA possédait deux lettres d'intention,
dont l'une à Bikoro/Ingende dans la province de l'Equateur et l'autre
à BASOKO dans la province Orientale et aussi un important
matériel d'exploitation forestière mais n'avait pas encore
commencé l'exploitation.
La société SINCA en plus des ses forêts de
la province Orientale et de l'Equateur, a une flotte importante pour
l'évacuation des essences flottants et non flottantes et la
société I.T.B en plus de sa forêt de Bandundu et ses deux
petits pousseurs, a une importance unité de transformation du bois.
Ainsi, la société SINCA suggéra
l'idée de fusionner les deux sociétés. Ce qui fur en
décembre 2004 ; la société I.T.B absorba la
société SINCA par contrat de fusion absorption.
Sous la forme actuelle, la société I.T.B est
dirigée par un gérant.
II.1.2. Localisation1
Identité :
- N°NRC : 14.449 Kinshasa
- N°Id. Nat : 01-25-K21.481J - N°INSS : 0103000228-01 -
N°INPP : 517300
Forme juridique - SPRL
Siège social
- Sise à Kinshasa, avenue de l'Ouest n° 5501,
quartier
Kingabwa/Madrandele, Commune de Limete.
Objet social
- Industrie du Bois
- Exploitation Forestière - Import et Export.
1 ITB, service du personnelle
44
Activité
- Exploitation et transformation du bois.
II.1.3. Organigramme1
Sous sa forme actuelle, au sommet de l'industrie de
transformation du Bois chapeaute un géant qui coordonne toutes les
activités de la société. Il est assisté pour cette
tache d'un adjoint et de quatre directeurs ainsi que des chefs de services et
les exécutants.
Ci-dessous nous vous présentons un extrait de
l'organigramme de la société I.T.B :
GERANT
Gérant adjoint chargé de
l'Administration et Finances
Assistant de Direction
Secrétaire de Direction
Direction Technique
Direction Production
Direction commerciale et d'Exploitation Forestière
- Serv. Electricité
|
|
- Déroulage
|
|
- Service du
|
|
Service de
|
|
- Sce Navigation
|
- Serv. Mécanique
|
|
- Contreplacage
|
|
personnel
|
|
Comptabilit
|
|
- Export
|
- Tour
|
|
- Scierie
|
|
- S. Médical
|
|
|
|
- Chantiers
|
|
- Trésorerie
- Cpté Fiscale - Vente Locale
|
1 IDEM
45
II.2. MODELE DESCRIPTIF DE LA DEROULEUSE N27001
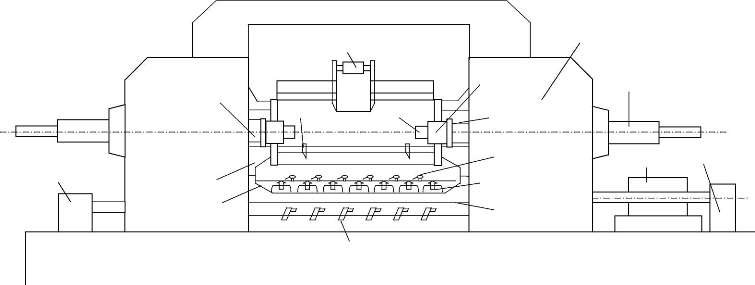
13
6
5
1
4
7
14
3
2
15
17
16
12
8
9
11
10
LEGENDE
|
|
|
|
|
|
|
|
1. Chariot porte couteau
|
5. Vis sans fin
|
9. Vérin hydraulique
|
13. Boite d'épaisseur
|
2. Grand mandrin
|
6. Glissière
|
10. Moteur Electrique
|
14. Déflecteur
|
3. Petit mandrin
|
7. Anti-flambage
|
11. Boite de vitesse
|
15. Couteau
|
4. Fin de course
|
8. Poupée fixe
|
12. Bâti
|
16. Contre-couteau
|
|
|
|
17. Broche
|
|
1 Colombo&Cremona, Notices et
schémas, C.C, Villa santa, 1988
46
II.3. ANALYSE DES STRUCTURES PARTIELLES DE BASES
Cette analyse nous permet d'étudier et de comprendre
les différentes parties et organes essentielles de la machine et leurs
rôles.
La dérouleuse est une machine servant à
dérouler les billes de grumes en bandes de feuilles suivant les
épaisseurs définies par l'opérateur. Elle est munie d'un
moteur principal à courant continu et d'un bloc réducteur pour
réduire la vitesse et pour entrainer les mandrins. Cette machine est
capable de dérouler jusqu'à un diamètre maximum de 1700 mm
de longueur 2700mm et à une vitesse de rotation varie de 0 à 3000
tr/min.
Elle est composée, hormis sa structure, des circuits
auxiliaires permettant son bon fonctionnement, nous citons :
? Circuit électrique ; ? Circuit hydraulique ; ? Circuit
pneumatique ; ? Circuit électronique.
II.3.1. Les circuits auxiliaires de la
dérouleuse
Palan billes
|
Pompe
hydraulique
|
Compresseur
|
Massicot
Parc à grume
|
Dérouleuse
|
Tapis roulant vers Massicot
|
Fig. II.1 : Circuits auxiliaires de la
dérouleuse
II.3.1.1. Le palan bille
Est un appareil de manutention sous forme de chariot suspendu
sur les poteaux permettant de soulever les billes et les faires déplacer
vers les mandrins de la dérouleuse pour centrage et déroulage.
Il comprend : un crochet, un câble métallique, un
galet, une poulie, deux moteurs (marche à impulsion), l'un pour le
déplacement avant et arrière et l'autre pour soulever et
descendre les billes et il se déplace sur un rail métallique.
47
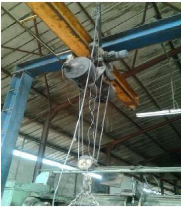
Fig. II.2 : Système de chargement de billon
L1
L2
L3
N
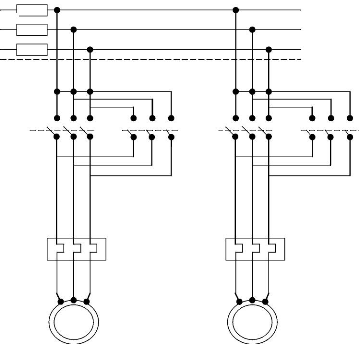
F1
F2
F3
KM
2
1 3
U V
M
3 ?
4
W
6 2 4 6
5
KM
R
1
3 5
KM
U V
2
1 3
M
3 ?
4
W
5 1
6 2 4 6
KM
R
3 5
Fig.II.3 : Schéma de puissance de deux moteurs
à marche à impulsion
48
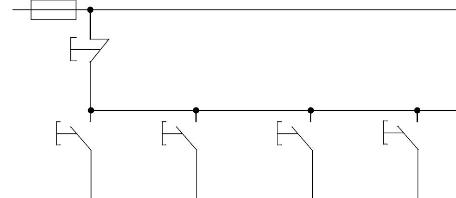
13
S1
S1
13
13
S1
14
14
14
11
14
L1
13
S1
|
|
|
|
|
|
|
|
|
|
|
|
|
|
|
|
|
|
|
|
|
|
|
|
|
|
|
|
|
95
|
RT
|
|
|
|
|
95
|
RT
|
|
|
|
|
|
|
|
|
|
|
|
|
|
|
|
|
|
|
|
|
|
|
|
|
|
|
|
|
|
|
|
|
|
|
|
|
|
|
|
|
|
|
|
|
|
|
|
|
96
|
|
|
|
|
|
96
|
|
|
L2
|
|
|
|
|
|
|
|
|
|
|
|
|
|
|
|
|
|
|
|
|
|
|
|
|
|
|
KM2
|
|
KM1
|
|
KM4
|
|
KM3
|
|
|
|
|
|
|
A
|
|
|
A
|
|
A
|
|
|
A
|
|
KM1
|
|
KM1
|
|
KM1
|
|
KM1
|
|
A
|
|
|
A
|
|
A
|
|
|
A
|
|
Fig.II.4 : Circuit de commande de deux moteurs
Légende :
F1 : Protection fusible
So : Bouton poussoir arrêt émergence
S1 : Bouton poussoir montée
S4 : Bouton poussoir descente
KM1 : Contacteur montée
KM2 : Contacteur descente
KM3 : Contacteur marche avant
KM4 : Contacteur marche arrière
49
RTL1 : Relais thermique montée/descente
KM1 : Verrouillage de contacteur KM1
KM2 : Contacte de verrouillage de KM2
KM4 : contacte de verrouillage de contacteur KM4
RTL2 : Relais thermique marche avant/arrière
II.3.1.2. Circuit Pneumatique
L'air comprimé fournit par le compresseur est
filtré avant d'être soumis à nouveau à une pression
d'exercice comprise entre 6 et 7bar, par le branchement d'un réducteur
de pression, et d'être lubrifié à l'aide d'huile
pulvérisée en vue de l'alimentation du circuit.
Le circuit pneumatique, se distingue par sa simplicité
étant donné que l'air comprimé capté par des
électrovannes spéciales, alimente les cylindres de l'embrayage et
les cylindres des couteaux pneumatiques du dispositif anti-flambage.
Il est composé d'un moteur électrique à
démarrage simple qui entraine un compresseur qui produit de l'air
comprimé.
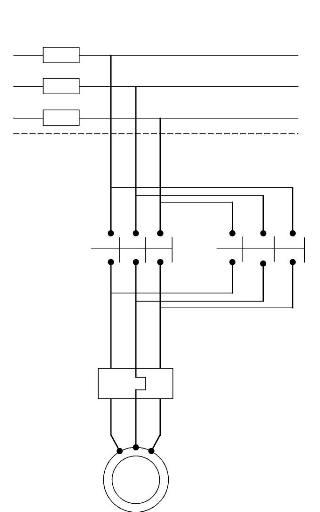
L2
F1
F2
F3
N
L1
L3
M
3?
RT
CL
CL
50
Fig.II.5 : Schéma de puissance du moteur
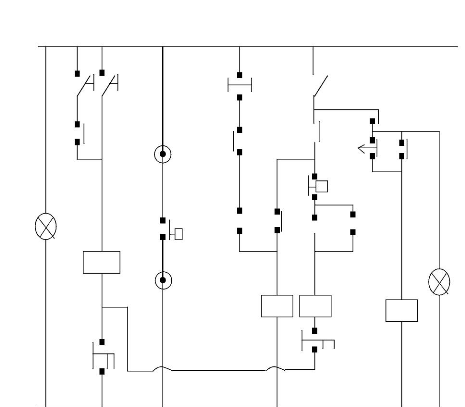
51
K5
L VERT
CL
15
CHUTE
CV
41
Pos2
ISO
K5
42
AIR
41
KB K7
13
28
K7
14
42
24
CL
CL
Pos1
CM
CM
CM
CV
L ROUGE
CL
CV
KB
K7
K8
Fig.II.6 : Circuit de commande du moteur
II.3.1.3. Circuit Hydraulique
Le moteur électrique entraine deux pompes hydrauliques
à une vitesse de 1440 tr/min de qu'on appuie sur le bouton poussoir la
disposition des voies changent et l'huile venant des pompes commande
automatiquement les vérins hydrauliques qui à son tour entraine
les mandrins pour le blocage de la bille. La commande est dite automatique
quant une seul impulsion de départ provoque ou entraine une suite des
interrompus de va et vient.
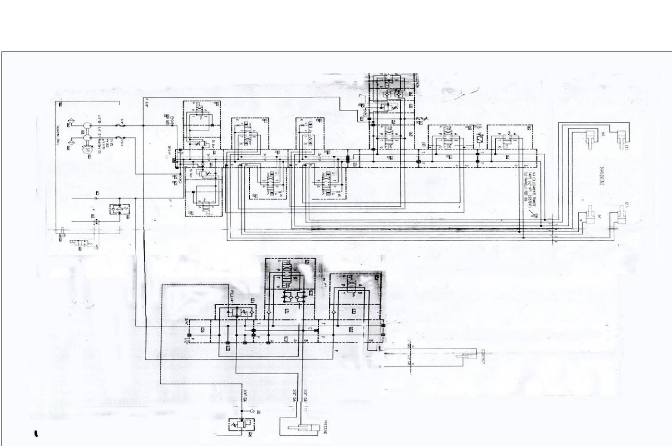
52
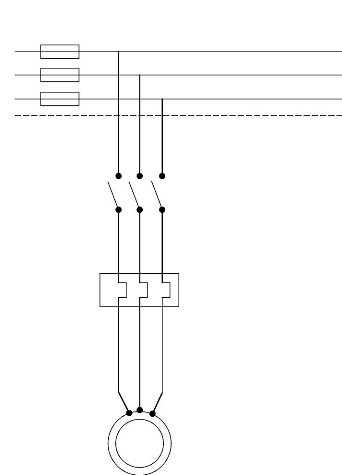
L1
L2
L3
N
Rth
M
3?
53
Fig.II.8 : Circuit de puissance de la pompe

11
12
SO
14
A1

S1
13
F1
L1
54
KM
KM
A2
95
96
L2
Fig.II.9 : Circuit de commande

RTL
Légende
F1 : Protection fusible
SO : Bouton poussoir arrêt S1 : Bouton poussoir marche KM :
Contacteur 380
RTL : Relais thermique
L1 ou L2 : Phase du courant
55
II.3.2. Description des organes principaux de la
dérouleuse
II.3.2.1. Organes support de pièces
a) La poupée fixe
Supporte et assure la rotation et le positionnement de la broche.
b) La broche
C'est une de pièces maîtresse tournante le plus
importante de la dérouleuse, elle est en acier traitée,
rectifiée et montée sur roulement, la broche reçoit
l'accessoire de fixation de billon (mandrin) qui le fait tourner à une
vitesse qui varie de 0 à 3000 tr/min.
II.3.2.2. Organes Support d'outils Le chariot
porte-couteau
C'est une partie aussi importante de la machine sur lequel
sont monté le couteau et le contre couteau qui est réglée
automatiquement selon l'épaisseur de feuille.
Guidé par une glissière et une vis sans fin, son
perpendiculaire à l'axe de la broche.
II.3.2.3. Organes permettant le (changement)
réglage de vitesse
a) Le bâti
Donne les dimensions de la machine (hauteur, longueur,
largeur) et supporte tout le système et organes de la machine.
b) Glissière
C'est un rail permettant le déplacement du chariot
transversalement à l'axe de la broche afin d'éplucher le billon
du bois par le couteau.
c) Réflecteur
Facilite le dégagement des déchets du billon
avant son arrondissement complet et permet le passage des feuilles sur le tapis
pour le massicotage.
D'où nous avons la rotation des broches et des mandrins
ainsi que l'avance du chariot porte couteau.
56
d) Boite de vitesses
Permet la sélection des vitesses de rotation. Elle
permet d'augmenter ou de diminuer progressivement la vitesse en fonction de la
qualité du bois à dérouler.
e) Boite d'épaisseur
Organe permettant la sélection d'épaisseurs
à dérouler, qui varie de 0,8 - 4mm selon la demande.
f) Fin de course
Dispositif de protection permettant d'éviter le
dépassement de l'avance et recul du chariot afin de ne pas se
cogné contre le billon ou sortir hors de la limite de la
glissière.
g) Anti-flambage
Dispositif de sécurité permettant
d'éviter les vibrations de billon de plus en plus que le diamètre
devient petit.
h) Coupe-file
Permet d'éliminer le surdimensionnement et limiter la
longueur exacte de billon selon la demande dont le maximum est de 2,60m.
i) Vérin hydraulique
Est un actionneur permettant de réalisé un
mouvement linéaire.
Il permet la commande des mandrins via la broche pour la
fixation de la bille sur la machine afin de la dérouler.
J) Moteur électrique
Dans la dérouleuse nous avons un moteur
électrique principal à courant continu qui assure le
fonctionnement de toutes les parties mécaniques de la machine à
l'aide de système de transmission par poulie et courroie au
régulateur de vitesse qui entraine la boite de vitesse et la celui
d'épaisseur par le billais d'un arbre moteur.
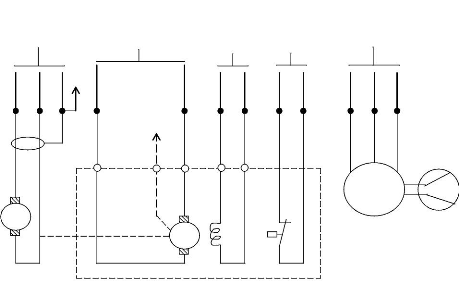
8 9
12
11
10
X1
6
5
7
X1
[EJ3]
[E]
[EC3]
3 4
[EN2] [EA2]
PE
1
X1
PE
H
A J
K
M
3?
DI
BR1 RO444
60V - 1000 Tours
EV1
HP 4
VOLT: 380V INTENSITE: 7A MOTOR FAN
M
6
ST1
THERMO PROBE
57
Fig.II.10 : Système de démarrage de moteur
principal de la dérouleuse DM225S
Caractéristique du moteur
Type : DM225S
Puissance : 100 KW
Facteur de puissance : 0,9
Tension : 400V
N : 2000 tour/min
Inom : 276A
Iex : 08,5 - 3,3A
Vex : 220V
Couplage : ?-?
II.3.3. Régulateur de vitesse
Le régulateur de vitesse est un mécanisme ou
système destinés, dans le fonctionnement de la dérouleuse,
à stabiliser ou à faire varier automatiquement la vitesse de
rotation de la machine en jouant sur le potentiomètre.
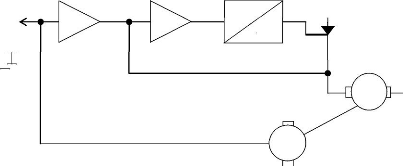
RIFERIMENTO
Ampèremètre Ohmmètre
A
Redressement
Rn RI
?
Potentiomètre
Moteur électrique
58
M
_
TD
Variateur
Fig.II.11 : Système de régulation de vitesse
de la dérouleuse
Potentiomètre
Valeur : 1 K?
Tour : de 0 à 1 K? vaut 10 Tours
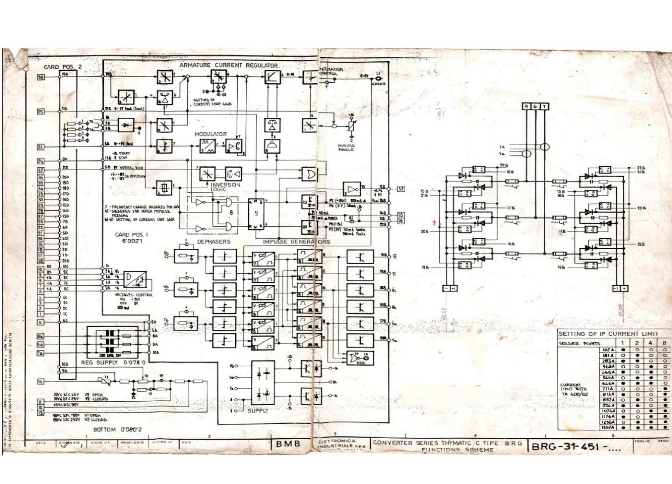
59
Fig.II.12 : Circuit Electronique de régulation de
vitesse
60
II.4. ETUDE FONCTIONNELLE1
Le principe de base consiste à faire tourner le billon
devant un couteau déplaçant transversalement au contact de la
bille en rotation pour avoir des feuilles déroulées.
II.4.1. Fonctionnement
De que le bois arrive, on démarre le moteur primaire du
circuit hydraulique qui entraîne la pompe hydraulique. De qu'on appuie
sur un bouton de commande la disposition des voies changent et l'huile
hydraulique de la pompe commande automatiquement les deux vérins
hydrauliques qui entraînent la sortie des mandrins via les broches
tournantes qui sont fondamentalement constituées par un arbre creux qui
déclenche la sortie des broches prévues afin de bloquer la
bille.
La bille positionnée entre deux mandrins, on
démarre le moteur électrique principal à courant continu
avec boite des vitesses tournant de 0 à 3000 tr/min qui par le biais de
l'embrayage principal monté à l'intérieur de la boite de
vitesse alors qu'une poulie tourne librement autour de l'arbre.une fois
l'embrayage enclenché, celle-ci devient solidaire par rapport à
l'arbre et déclenche la rotation de la bille devant le chariot porte
couteau qui avance automatiquement vers le billon à une vitesse requise
pour dérouler le bois selon la passe voulue.
II.4.1.1. Processus de déroulage2
Le déroulage est une opération d'usinage du
bois. Elle est relativement simple mais nécessitant de la part de
l'opérateur de la machine : une bonne connaissance de la machine, une
bonne connaissance du bois et des produits à obtenir.
Nous notons ici que, tout bois n'est pas déroulable.
Parmi les bois déroulables, il y a n'a d'autres qui ne sont pas frais et
devra subir l'opération d'étuvage (étuver le bois à
une Température #177; 100°C).
1 Colombo&Cremona, Notice et
schémas, C.C, VILLASANTA, 1988
2 Vincent BONIN, Modélisation analytique
de la formation du copeau durant le procédé de déroulage
du bois de hêtre, ENSAM, Paris 2006
61
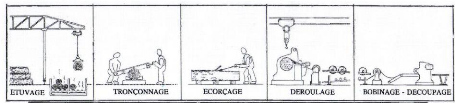
Fig.II.13 : Le processus du déroulage
II.4.1.2. Procédé de déroulage
Le déroulage est la combinaison simultanée d'une
rotation de la bille sur elle-même suivant sa longueur par rapport au
bâti et d'une translation du chariot porte-couteau par rapport au
bâti et perpendiculaire à l'axe de rotation de la bille.
A l'arrivé du bois, il est coupé à une
dimension bien définit de 2,63m ou inférieur à des
diamètres variables selon la demande.
Une fois découper le bois, on le dépose sur la
machine à l'aide d'un palan qui sera fixer aux mandrins et
l'opérateur démarre le moteur électrique pour entrainer
les mandrins et le chariot contenant le couteau qui doit éplucher la
bille jusqu'à ce que le bois devient complètement rond.
Après cette opération, on déclenche le
déroulage proprement dit du bois sur une épaisseur bien
définit de l'ordre de : 8/10, 10/10, 13/10, 20/10 et 30/10 etc...) Une
fois le bois déroulé sur les épaisseurs définies,
est étalé sur un tapis roulant pour le massicotage.
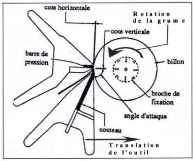
Fig.II.14 : Procéder de déroulage
62
II.4.2. Les grandeurs cinématiques du
procédé de déroulage
L'avance de l'outil et la vitesse de rotation du billon sont les
deux grandeurs cinématiques du procédé de
déroulage.
L'avance de l'outil (couteau) est déduite de la vitesse de
rotation du billon car il faut garder une épaisseur théorique de
feuille constante.
De plus, afin de garder les mêmes conditions de
création de feuille à l'échelle macroscopique, la vitesse
de rotation du billon est déduite d'une vitesse de coupe via rayon de
coupe.
Ainsi la seule grandeur cinématique indépendante
est la vitesse de coupe (vitesse défilement du matériau bois par
rapport à l'arrêté de coupe).
II.4.3. Chaine cinématique de la
dérouleuse
MOTEUR
|
BOITE DE
|
BROCHE
|
BILLE
|
BOITE DES EPAISSEURS
CHARIOT PORTE-COUTE
Fig.II.15 : Chaine cinématique de la dérouleuse
FONCTIONNEMENT
L'énergie motrice est donnée par le moteur
électrique sous forme d'un mouvement de rotation ; par un système
des poulies et courroies, ce mouvement est transmis à la boîte de
vitesse qui le transmet ensuite à la broche sur laquelle est
adaptée la bille une vitesse précise. Par l'entremise d'un arbre
sur lequel est enclenchée une roue solidaire à la broche via la
boîte d'épaisseurs, ce mouvement est transmis à la vis sans
fin qui permet la translation du chariot transversal sur lequel est
adapté l'outil (couteau).
63
CHAPITRE III. POLITIQUE DE MAINTENANCE ADAPTEE A LA
DEROULEUSE N2700
III.1. ANALYSE D'APPARITION DES PANNES1
Notre analyse se fixe sur une période de 3 ans qui part
de 2008 à 2010, sans tenir compte du temps total d'exploitation de la
machine pour de raison de délimitation du travail et nous avons
enregistré quelques pannes qui font l'objet de notre analyse.
III.1.1. CHECK-LIST DES PANNES
Nous avons durant cette période repéré les
pannes suivantes :
· Les mandrins ne bloquent pas la bille, due à la
fermeture de l'électrovanne basse pression de la pompe ;
· Manque de pression pneumatique à la machine ;
due au disfonctionnement du compresseur ;
· Brulure du moteur de la pompe ;
· Brulure du moteur monté et descente du palan,
due à une grosse bille qu'il n'a pas pu soulever ;
· Blocage du contacteur de palan ;
· Automatisme de la montée du palan sans
l'intervention de l'opérateur, due à l'inversion des positions
des fusibles ;
· Le moteur principal ne tourne pas et
déclenchement du disjoncteur C.C, due au manque de l'alimentation +24V
;
· Mauvais état des couteaux ;
· Court-circuit dans la carte électronique (entre
gate et anode ; entre gate et cathode) claquage de 4 thyristors ;
· Claquage de diodes sur la carte 60.021 ;
· Pas de sortie de grands mandrins, due au mauvais
état des joints du piston, ainsi déversement d'huile hydraulique
sur le bâti support des mandrins ;
· Sortie des petits mandrins sans être actionner
panne mécanique ;
· Cassures des vis de fixations des mandrins, due
à la mauvaise qualité de la matière de fabrication des
mandrins ; qualités de la matière de fabrication des nouveaux
mandrins (bronze simple au lieu de bronze gravite) ;
1 ITB, Fiches des rapports journaliers de la
dérouleuse, 2008, 2009, 2010
64
? Perte d'huile hydraulique due au mauvais état des
joints ;
? Grillage du moteur principal de la machine ;
? Pas d'avance du chariot porte couteau ;
? Lenteur de la production des feuilles, due à la faible
vitesse de rotation qu'imprime le nouveau moteur principal et suppression de
circuit électronique de régulation des vitesses.
65
III.1.2. TABLEAU HISTORIQUE DES PANNES (2008 A 2010) DE LA
DEROULEUSE N27001
N°
|
Nomination
|
2008
|
2009
|
2010
|
Total
|
|
F
|
M
|
A
|
M
|
J
|
J
|
A
|
S
|
O
|
N
|
D
|
J
|
F
|
M
|
A
|
M
|
J
|
J
|
A
|
S
|
O
|
N
|
D
|
J
|
F
|
M
|
A
|
M
|
J
|
J
|
A
|
S
|
O
|
N
|
D
|
|
Circuit
hydraulique
|
|
|
|
|
|
2
|
|
|
|
|
|
|
|
|
|
|
|
|
|
|
|
1
|
|
|
|
|
|
|
|
4
|
|
|
3
|
1
|
|
|
11
|
02
|
Moteur Electrique principal
|
|
|
|
|
|
1
|
|
|
|
|
1
|
|
|
|
|
|
|
|
1
|
|
|
|
|
1
|
|
|
|
1
|
|
1
|
|
|
|
1
|
|
1
|
8
|
03
|
Carte
Electronique
|
2
|
1
|
2
|
1
|
|
|
|
|
3
|
|
|
3
|
|
|
2
|
1
|
2
|
|
|
|
1
|
|
|
1
|
|
2
|
|
|
|
|
|
|
|
|
|
|
21
|
04
|
Régulateur
de vitesse
|
1
|
|
|
|
|
|
|
|
1
|
|
|
|
|
|
|
|
|
|
|
|
|
|
|
|
|
|
|
|
|
1
|
|
|
|
|
|
|
3
|
05
|
Boite
d'épaisseur
|
|
|
|
|
|
|
|
|
|
|
|
|
|
|
|
|
|
|
|
|
|
|
|
|
|
|
|
|
|
|
|
|
|
|
|
|
0
|
06
|
Boite de
vitesse
|
|
|
|
|
|
|
|
|
|
|
|
|
|
|
|
|
|
|
|
|
|
|
|
|
|
|
|
|
|
|
|
|
|
|
|
|
0
|
07
|
Mandrins de
blocage des billons
|
|
|
1
|
|
|
|
|
1
|
|
|
|
|
|
|
|
1
|
|
|
|
|
|
|
|
|
|
|
|
1
|
|
|
2
|
|
|
4
|
|
|
10
|
08
|
Palan
|
|
|
|
|
|
|
|
1
|
|
|
|
|
|
|
|
|
|
|
1
|
|
|
|
|
|
|
|
|
|
|
|
|
|
|
|
|
|
2
|
09
|
Circuit
pneumatique
|
|
|
|
|
|
|
1
|
|
|
|
|
|
|
|
|
|
|
|
|
|
|
|
|
1
|
|
|
|
|
|
|
|
|
|
|
|
2
|
4
|
10
|
Chariot porte- couteau
|
|
|
|
|
|
|
|
1
|
|
|
|
|
|
|
|
|
|
|
1
|
|
|
|
|
|
|
|
|
1
|
|
|
1
|
|
|
2
|
|
1
|
7
|
Total
|
3
|
1
|
3
|
1
|
0
|
3
|
1
|
3
|
4
|
0
|
1
|
3
|
0
|
0
|
2
|
2
|
2
|
0
|
3
|
0
|
1
|
1
|
0
|
3
|
0
|
2
|
0
|
3
|
0
|
6
|
3
|
0
|
3
|
8
|
0
|
4
|
|
? Pannes par
classes soit après 1000 heures
|
8
|
12
|
7
|
6
|
6
|
12
|
15
|
66
|
|
1 ITB, Fiches Techniques de la dérouleuse,
2008, 2009, 2010
Soit
66
Par rapport au tableau, nous avons relevé ce
qui suit :
· Nombre de pannes, ni=66
· Nombre de pièces en bon état,
No=100 (ti=0)
· Intervalle de temps d'observation ?t= 3
ans
· Ni= 70
III.1.3. DEPOUILLEMENT DES DONNEES
III.1.3.1. DETERMINATION DE L'INTERVALLE DE TEMPS
D'OBSERVATION
La dérouleuse des grumes N2700, totalise
jusqu'à nos jours 25 ans dans l'industrie de transformation du bois
« I.T.B ».
Nous procédons au calcul de sa
fiabilité en fonction de ces trois dernières années dont,
de 2008-2010. La machine travaille chaque semaine du Lundi au Vendredi de 7h30'
à 15h30' et le Samedi de 7h30' à 12h30', ce qui donne 8 heures du
temps de Lundi au Vendredi et 5 heures du temps le Samedi.
· Par semaine 45 heures ;
· Par mois 45 heures x 4 = 180 heures
· Par an 180 heures x 12 = 2.160
heures.
Ce qui entraine qu'en 3 ans, on aura 2.160 heures x 3
qui donne 6.480 heures. Donc, nos calculs de fiabilité seront
effectués dans cet intervalle de temps ti=6.480 heures.
III.1.3.2. DETERMINATION DES NOMBRES DE CLASSES
Etant donné que la somme de défaillance
est de 66 dans une période de 6.480 heures, la détermination du
nombre de classes doit-être telle que la courbe de vie de la machine ne
soit pas trop déformée, elle dépend du nombre total des
défaillances.
Avec les formules, on calcul comme suite :
v? v (3.1)
( ) (3.2)
Soit r= 7 Classes
67
Tableau III.1 : Les intervalles de temps
d'observation
N°
|
?ti=ti+1-ti
|
ni
|
Ni
|
1
|
0 - 1000
|
8
|
70
|
2
|
1000 -2000
|
12
|
50
|
3
|
2000 - 3000
|
7
|
40
|
4
|
3000 - 4000
|
6
|
35
|
5
|
4000 - 5000
|
6
|
30
|
6
|
5000 - 6000
|
12
|
20
|
7
|
6000-7000
|
15
|
5
|
Avec : Ni= nombre d'éléments en bon état
à l'instant ti ni= nombre d'éléments défaillants
dans la tranche d'âge ?ti N0= nombre d'éléments en bonne
état à l'instant t0
?ti= intervalle de temps observé
III.2. ANALYSE DU RETOUR D'EXPERIENCE1 (REX)
Le retour d'expérience consiste à
l'amélioration de performances de processus industriels de l'industrie
par la réutilisation de l'expérience acquise au cours des
activités antérieures.
III.2.1. ANALYSE DE LA PRODUCTION2
Notre analyse se fonde sur les données de production de
ces trois dernières années (2008 à 2010), que nous
présentons dans le tableau.III.2
III.2.1.1.CHECK-LIST DE LA PRODUCTION
Au cours de ces trois dernières années, la
dérouleuse des grumes Colombo&Cremona N2700 a déroulée
des billes des diamètres variables allant jusqu'environ 1700mm, selon
les longueurs demandées dont nous avons :
? En 2008 : 6088 billes qui varient entre 30m3 -
50m3/j dont 40m3 en moyenne/j
? En 2009 : 5079 billes qui varient entre 25m3 -
35m3/j dont 30m3 en
moyenne/j
? En 2010 : 3407 billes qui varient entre 10m3 -
20m3/j dont 15m3 en
moyenne/j
1 C.T TSHAONA T. Marcel, Cours de logistique
industrielle, G3 Mécanique, ISTA, 2012, inédit.
2 ITB, Fiches des productions journalières,
2008, 2009, 2010
68
Ce qui explique les fiches des productions de la machine.
Tableau III.2 : Historique de la
production1
Mois
|
2008
|
2009
|
2010
|
Janvier
|
432
|
625
|
403
|
Février
|
445
|
632
|
356
|
Mars
|
420
|
546
|
392
|
Avril
|
632
|
523
|
302
|
Mai
|
460
|
615
|
273
|
Juin
|
446
|
462
|
326
|
Juillet
|
542
|
401
|
345
|
Août
|
482
|
262
|
178
|
Septembre
|
454
|
308
|
165
|
Octobre
|
683
|
275
|
141
|
Novembre
|
556
|
225
|
372
|
Décembre
|
536
|
205
|
154
|
Total
|
6088
|
5079
|
3407
|
III.2.1.2.DETERMINATION DES COURBES DE PRODUCTION
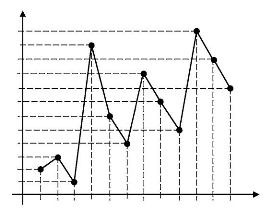
0
Production
683
632
556
542
7
536
7
482
460
454
446
445
432
420
J
Mois
N
D
S
J
F M A M J
O
A
Fig. III.1 : Allure Production 2008
1 ITB, Fiches des productions journalières,
2008, 2009, 2010
69
Production
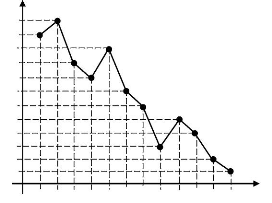
0
632
625
615
546
523
462
401
308
275
262
225
205
J
Mois
D
N
S
J
F M A M J
O
A
Fig.III.2 : Allure production 2009
Production
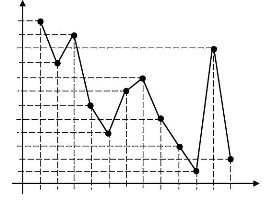
0
403
392
374
356
345
326
302
273
188
165
154
141
J
Mois
D
N
S
J
F M A M J
O
A
Fig.III.3 : Allure de production 2010
70
Production
6088
5079
3407
|
|
|
|
|
2008
|
2009
|
2010
|
Année
|
Figure.III.4 : Allure de production pendant 3 ans
(2008 à 2010)
III.2.1.3. INTERPRETATION DES COURBES DE PRODUCTION
Les données recueillies ci-dessus nous ont
permis d'analyser la production de la machine de 2008 à 2010 et de
tracer les courbes de production selon les années.
En se référent à ces courbes,
nous pouvons dire que la production de la dérouleuse de grumes N2700
varie d'une manière décroissante ce qui se justifie par une
baisse sensible de la production en 2010, à cause des pannes
répétitives. D'où la nécessité
d'optimisation de sa production.
III.2.2. DETERMINATION DU TAUX DE DEFAILLANCE (?(TI))
( )
( )
( )
( )
( )
( )
( )
71
ë(t).10-4déf/h
30

30
6
2,4
2
1,75
1,7
1,1
0
0
Fig.III.5 : Histogramme de la courbe de vie de la
machine
ë(t).10-4déf/h
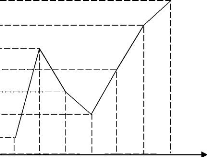
1 2 3 4 5 6 7 ?ti(h)
Fig.III.6 : Allure de la courbe de vie de la machine
72
III.2.3. DETERMINATION DE LA FONCTION DE REPARTITION
(F(TI)%)
On sait que N0=100 pièces
( ) ( ) ( ) ( ) ( ) ( ) ( )
F(t)% 95%
80%
70%
65%
60%
50%
30%
0
1 2 3 4 5 6 7 ?ti(h)
Fig.III.7 : Histogramme de la fonction de
répartition
73
III.2.4. DETERMINATION DE LA FONCTION DE FIABILITE
R(TI)%
( ) ( ) ( ) ( ) ( ) ( ) ( )
R(t)%
70%
50%
40% 35% 30% 20%
5%
|
|
0 1 2 3 4 5 6 7 ?ti(h)
Fig.III.9 : Histogramme de fiabilité
1 P. Lyonnet, La maintenance, mathématiques
et méthodes, technique et documentation, Lavoisier, Paris, 2000
74
Tableau III.3 : Résumé des calculs des
fonctions fiabilité
N°
|
?ti=ti+1-ti
|
ni
|
Ni
|
ë(ti)10-4
|
F(ti)%
|
R(ti)%
|
1
|
0 - 1000
|
8
|
70
|
1,1
|
30
|
70
|
2
|
1000 -2000
|
12
|
50
|
2,4
|
50
|
50
|
3
|
2000 - 3000
|
7
|
40
|
1,75
|
60
|
40
|
4
|
3000 - 4000
|
6
|
35
|
1,7
|
65
|
35
|
5
|
4000 - 5000
|
6
|
30
|
2
|
70
|
30
|
6
|
5000 - 6000
|
12
|
20
|
6
|
80
|
20
|
7
|
6000-7000
|
15
|
5
|
30
|
95
|
5
|
?
|
66
|
|
44,95
|
450
|
250
|
?(t)moy = 6,4.10-4 déf/h F(t)moy =
64,3% R(t)moy = 35,7%
Au regard de ces valeurs, nous nous trouvons en face
d'une insuffisance de la fiabilité de la machine qui se justifie par une
valeur de 35,7% en moyenne due à un taux de défaillance de
6,4.1O-4 déf/h en moyenne et de 64,5% en moyenne de la
fonction de répartition. D'où nous disons que notre machine est
moins fiable.
III.2.5. CALCUL DE LA MOYENNE DE TEMPS DE BON
FONCTIONNEMENT « M.T.B.F »1
C'est un autre indicateur de la fiabilité, Elle
est liée aux lois de fiabilité par le taux de
défaillance.
Elle se calcule par la relation suivante :
1
La MTBF = ? n .t ( heure) N
0
[(niti) + (n2t2) +
(n3t3) + (n4t4) + (nsts) +
(n6t6)]
[( 8 x 1000) + ( 12 x 2000) + ( 7 x 3000) + ( 6 x 4000) + ( 6 x
5000) + ( 12 x 6000) + ( x 7000)]
000x (8+24+21+24+30+72+105)
0 0
MTBF=10 x 284
MTBF= 2840 heures

30
6
2,4
2
1,75
1,7
1,1
0
75
Après calculs, Nous avons eu une MTBF de 2840
heures qui est insuffisante sur les 6480 heures d'intervalle de temps
d'observation de la machine, donc après 2840 heures de fonctionnement en
moyenne, il y a apparition de pannes. On peut alors prendre 2500 heures comme
temps d'alerte.
III.2.6. COURBE DE VIE ET POLITIQUE DE MAINTENANCE
III.2.6.1. REPRESENTATION DE LA COURBE DE VIE DE LA
DEROULEUSE N2700
ë(t).10-4déf/h
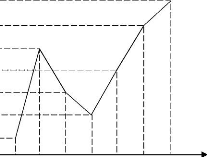
1 2 3 4 5 6 7 ?ti(h)
Fig.III.11 : Représentation de la courbe de
vie pratique de la dérouleuse N2700
La courbe de vie permet la mise en place d'une
politique de maintenance efficace ; puisse qu'elle détermine l'âge
de la machine par la présentation de la variation de taux de
défaillance en fonction du temps.
III.2.6.2. IDENTIFICATION DE LA POLITIQUE DE
MAINTENANCE EFFICACE DE LA DEROULEUSE N2700
Partant de l'allure de la variation du taux de
défaillance ë(t) qui est quasi-constant, par conséquent,
nous nous retrouvons dans la période de maturité.
Dans ce cas, la politique de maintenance
adéquate et efficace qui devra être appliquée à la
machine est la maintenance préventive, caractérisée par la
maintenance par travaux systématiques et préventive
conditionnelle et en cas de défaillance catalectique, on applique le
dépannage ou la réparation.
76
III.3. DISPONIBILITE ET PROGRAMMATION DES TRAVAUX1
III.3.1. ANALYSE DE LA DISPONIBILITE
III.3.1.1. CALCUL DES INDICATEURS DE DISPONIBILITE
a. Calcul de la MTBF
1
b. Calcul de MTTR
Avec : Teff = 6480 heures ; Temps inexpliqué= 10
à 25%
( 6480 x 25)
III.3.1.2. DETERMINATION DE LA DISPONIBILITE
III.3.1.2.A. CALCUL DE LA DISPONIBILITE
OPERATIONNELLE
III.3.1.2.B. CALCUL DE LA DISPONIBILITE PRATIQUE
1 C.T TSHAONA T. Marcel,
Cours de logistique industrielle, G3 Mécanique, ISTA,
2012
77
Avec :
La disponibilité étant un facteur
clé de la détermination de la qualité d'une machine, car
remettre en bon état la dérouleuse des grumes COLOMBO&CREMONA
N2700 découle des tous les moyens et éléments disponibles
permettant d'accomplir une fonction requise.
Après analyse et calcul on a :
· La MTBF : 2840 heures ;
· La MTTR : 2020 heures ;
· Inexpliqué : 1620 heures.
Par la suite, nous réalisons que la
dérouleuse des grumes COLOMBO&CREMONA N2700 est moins disponible,
soit avec une disponibilité opérationnelle de 58,43% contre une
disponibilité pratique de 43,82% ce qui est aussi insuffisant pour une
machine industrielle, d'où la nécessité d'améliorer
le taux de disponibilité.
III.3.2. PROGRAMMATION DES TRAVAUX DE MAINTENANCE
III.3.2.1. AMELIORATION DE TAUX DE DISPONIBILITE DE LA
MACHINE
Augmenter le taux de disponibilité d'une
machine consiste à réduire le nombre de ses arrêts
(fiabilité) et à réduire le temps mis pour les
résoudre (maintenabilité).
· Spécialiste en maintenance : Ima= 2 avec
Pma= 30%
· Spécialiste en électronique :
IEtro= 2 avec PEtro = 60%
· d'autres : Iautre = 2 avec Pautre =
10%
On a : H=E
( Pmaint x'maint) + ( PEtro x 'Etro) +
(Pautre x 'autre)
H=( 2x0,30) +( 2x0,60) +( 2x0,10) =2,0
78
u : taux de réparation (Rép/h) A : taux de
défaillance (Déf/h) IX : disponibilité
amélioré (%) M : paramètre matériel=85%
H : paramètre humain
MTTR : moyenne de temps techniques de réparation (h)
I : nombre des techniciens par spécialité
MTBF : moyenne de temps de bon fonctionnement (h)
Considérant une équipe de 6 personnes, on pourra
avoir un taux de disponibilité amélioré de 43,82% à
99,4% ce qui est excellente.
III.3.2.2. PLANIFICATION 11E TRAVAUX 11E
MAINTENANCE
La méthode ABAC - ABAD La MTBF = 2840 heures
Nous fixons plus notre attention sur les organes ayant connus
les défaillances au cours de ce trois dernières années
d'observation tels que :
? Circuit hydraulique (11 pannes);
? Circuit électronique (21 pannes);
? Chariot porte couteau (7 pannes);
? Mandrins de blocage (10 pannes);
? Moteur électrique (8 pannes).
et ce conformément au tableau historique des pannes.
III.3.2.2.A. CHECK-LIST 11ES TACHES
Tâche A : Inspection et graissage des articulations.
Tâche B : Inspection et réglage du chariot porte
couteau.
Tâche C : Contrôle et remplacement des pièces
dans le circuit électronique. Contrôle et remplacement des
pièces dans le circuit hydraulique et pneumatique.
Tâche D : Révision générale de la
machine et remplacement des organes défaillants.
79
III.3.2.2.B. PROGRAMMATION GEOMETRIQUE
Notre programmation est de base t1=MTBF=2840 heures et de raison
2
Soit MTBF=2500 heures
Les tâches A à t1=2500 heures
Les tâches B à t2= 2t1= 5000 heures
Les tâches C à t3= 1t2=4t1= 10000 heures
Les tâches D à t4= 2t3=8t1=20000 heures
III.3.2.2.C. PLANIFICATION ABAC - ABAD
· Les tâches A s'exécutent toutes les 2500
heures
· Les tâches B + A s'exécutent toutes les 5000
heures
· Les tâches A s'exécutent toutes les 7500
heures
· Les tâches C + B + A s'exécutent toutes les
10000 heures
· Les tâches A s'exécutent toutes les 12500
heures
· Les tâches B + A s'exécutent toutes les
15000 heures
· Les tâches A s'exécutent toutes les 17500
heures
· Les tâches D + C + B + A s'exécutent toutes
les 20000 heures.
80
INTERPRETATION DES RESULTATS OBTENUS
1. TABLEAU RECAPUTILATIF DES RESULTATS
N°
|
DESIGNATION
|
UNITES
|
SYMBOLES
|
RESULTATS
|
OBSERVATION
|
1
|
Nombre de classe
|
-
|
R
|
7
|
|
2
|
Intervalle de temps observé
|
heure
|
?t
|
1000
|
|
3
|
Temps d'observation
|
heure
|
T.Obs
|
6480
|
|
4
|
Taux de défaillance moyen
|
10-4Déf/h
|
ë(t)
|
6,4
|
|
5
|
Fonction de répartition moyenne
|
%
|
F(t)
|
64,3
|
|
6
|
Fonction de fiabilité moyenne
|
%
|
R(t)
|
35,7
|
|
7
|
Moyenne de temps de bon fonctionnement
|
heure
|
MTBF
|
2840
|
Insuffisante
|
8
|
Production moyenne annuelle
|
Billes
|
Pmoy
|
4858
|
Insuffisante
|
9
|
Moyenne de temps technique de répartition
|
heure
|
MTTR
|
2020
|
trop
|
10
|
Le temps inexpliqué
|
heure
|
I
|
1620
|
|
11
|
Disponibilité opérationnelle
|
%
|
D0
|
58,43
|
Insuffisante
|
12
|
Disponibilité pratique
|
%
|
DP
|
43,82
|
Très insuffisante
|
13
|
Paramètre humain
|
-
|
H
|
2,0
|
|
14
|
Paramètre matériel
|
-
|
M
|
0,85
|
|
15
|
Facteur multiplicateur
|
-
|
n
|
1,7
|
|
16
|
Taux de réparation
|
10-4 Rép/h
|
u
|
4,95
|
|
17
|
Taux de défaillance
|
10-4 Déf/h
|
?
|
3,52
|
|
18
|
Programmation de travaux M ou Am taux
disponible
|
%
|
?am
|
99,4
|
Excellent
|
81
2. DISCUSSION ET ANALYSE CRITIQUE DES
RESULTATS
Partant des calculs effectués des différents
paramètres entrant dans l'analyse et étude des résultats
récoltés entre autres le taux de défaillance, la
fiabilité ainsi que la disponibilité qui nous permet de
décider et d'apporter des solutions adéquates afin de promouvoir
une production optimale de la dérouleuse des grumes COLOMBO &
CREMONA N2700.
En se référant aux différentes valeurs
trouvées dans les calculs des taux des défaillances qui nous ont
permis de tracer une courbe de vie pratique de la dérouleuse qui est
quasi-constante avec une valeur moyenne de 6,4.10-4déf/h qui
justifie la baisse sensible de la production de la machine de 6088 billes en
2008 contre 3407 billes en 2010, la machine est dans sa phase de
maturité.
En calculant, nous avons trouvé une valeur insuffisante
de 35,7% en moyenne de la fiabilité et de 43,82% de disponibilité
de la machine qui nous amène à déclarer la machine moins
fiable, car des valeurs trouvées sont moins de 95% pour la
fiabilité et moins de 85% pour la disponibilité qui sont prises
comme une garantie et nous pousse à apporter une solution.
D'où, la nécessité d'améliorer la
disponibilité et la fiabilité. En améliorant la
disponibilité tout en tenant compte des paramètres humain et
matériel ainsi que le multiplicateur en cas de plusieurs
réparateurs, nous sommes parvenus à trouver une
disponibilité excellente de 99,4% contre 43,82%.
A ce stade nous pouvons espérer que notre
dérouleuse sera disponible, en respectant les intervalles
d'interventions définies et en diminuant la MTTR et en augmentant la
MTBF par la mise des dispositifs de prévention de la programmation ABAC
ABAD des travaux.
Ainsi, nous pensons avoir donné la synthèse de nos
résultats.
82
SUGGESTIONS
Etant donné que la maintenance des équipements
de production est un enjeu clé pour la production des industries, aussi
bien que pour la qualité des produits, qui doit être un
défi industriel impliquant la remise en cause des structures
figées actuelles et promotion de méthodes adaptées
à la nature nouvelle des matériels.
En se basant sur la mission de la maintenance qui est : la
surveillance permanente ou périodique, dépannage et
réparation ainsi les actions préventives, nous évoquons
ici, le problème de la technologie du matériel actuel qui
implique une compétence technique polyvalente pour l'équipe qui
en a la responsabilité. Les frontières entre les domaines
mécaniques, hydraulique, électroniques, électriques,
pneumatique, informatiques ne sont pas évidentes sur des machines, car
nul n'est savant en tout, sauf Dieu.
Désormais, il sera important d'éviter les
actions brutales sur la dérouleuse par les techniciens profanes venant
des autres domaines, car chacun est savant que dans son domaine. Ainsi donc, la
maîtrise est indispensable à la prise de décision. Il faut
avoir à l'esprit qu'il n'existe pas une bonne maintenance dans
l'absolue, mais une maintenance économique et efficace à un
moment donné, sur un équipement donné.
Ainsi, le dernier rôle des techniciens est de
déterminer le moment économique de cessation du soin à
apporter à une machine et de participer au choix de son remplacement,
car une machine meurt inexorablement et l'acharnement thérapeutique,
même technique, coûte cher ! Et enfin, si nous appliquons ainsi,
nous garantirons une longue durée de vie à notre machine.
83
CONCLUSION GENERALE
Notre travail se fondait sur l'étude fonctionnelle et
identification de la politique de Maintenance pour une production optimale de
la dérouleuse des grumes COLOMBO&CREMONA N2700 de l'Industrie de
Transformation du Bois « I.T.B/Kinshasa »
En abordant ce sujet, Nous avons développé les
généralités ayant trait à la Maintenance, la
Sûreté de fonctionnement et au Bois suivi de l'Etude
systémique présentant le fonctionnement dédite Machine et
une politique de Maintenance.
Les données enregistrées nous ont permis
d'identifier une politique de Maintenance adéquate pour la
dérouleuse des grumes N2700 et la courbe de vie pratique a permis
d'établir une Maintenance qui garantira la production et la durée
de vie de la machine.
Nous pensons que les divers problèmes techniques de la
machine trouvent déjà solution dans l'application de la
maintenance préventive caractérisée par la maintenance
préventive par travaux systématique et préventive
conditionnelle qui s'accompagnera des actions des visites, les rondes,
dépannages et réparations, suivant la programmation ABAC-ABAD en
raison d'augmentation de la MTBF.
Etant humain et que nul n'a le monopole de la science, nous
restons ouvert aux remarques et suggestions de tous en vue
d'amélioration et réussite de cette oeuvre scientifique.
84
BIBLIOGRAPHIE
I. Livres utilisés
1) F. BOUCLY et A. OGUS, le management de la maintenance,
AFNOR, Eyrolles, Paris 1987.
2) F. MONCHY, Maintenance, méthodes et organisations,
Dunod, Paris 2003.
3) F. MONCHY, la fonction maintenance, formation à la
gestion de la maintenance industrielle, Masson, Paris 1994.
4) R. JABOT, Entretien et travaux neufs, hommes et
techniques, Puteau 1969.
5) P. Lyonnet, La maintenance, mathématiques et
méthodes, technique et documentation, Lavoisier, Paris, 2000.
6) G. BOSSER et Al, Maintenance des systèmes de
production, Foucher, Paris 1990.
7) J.C FRANCASTEL, Ingénieur de la maintenance, de la
conception à l'exploitation d'un bien, Dunod, Paris 2003.
8) J.C FRANCASTEL, Le fond de la baignoire, le tour de la
maintenance en 80 jours, Dunod, Paris 2002.
9) R. FAURE, Précis de recherche
opérationnelle, Dunod, Paris 1979.
II. Cours et documents de la machine
1) C.T TSHAONA T. Marcel, Cours de logistique industrielle, G3
Mécanique, ISTA, 2012 inédit.
2) ITB, service du personnelle
3) Colombo&Cremona, Notice et schémas, C.C,
VILLASANTA, 1988
4) ITB, Fiches des rapports journaliers de la dérouleuse,
2008, 2009, 2010
5) ITB, Fiches Techniques de la dérouleuse, 2008, 2009,
2010
6) ITB, Fiches des productions journalières, 2008, 2009,
2010
III. Mémoire
1) Vincent BONIN, Modélisation analytique de la
formation du copeau durant le procédé de déroulage du bois
de hêtre, ENSAM, Paris 2006
IV. SITE WEB
1) INTERNET
2)
http://www.site-en-bois.net/fr/accueil.phtml
3)
http://uipp.fr/app2.php-
85
TABLE DES MATIERES
Epigraphe i
Dédicace ii
Remerciements iii
INTRODUCTION GENERALE 1
O.1. MOTIVATION 6
O.2. PROBLEMATIQUE 6
O.3. OBJECTIF 6
O.4. METHODOLOGIE DU TRAVAIL 7
0.5. DELIMITATION DU SUJET 7
0.6. SUBDIVISION DU TRAVAIL 7
CHAPITRE I : RECENSION DES ECRITS 8
I.1. NOTION DE MAINTENANCE 8
I.1.1. Historiques 8
I.1.2. Définitions 8
I.1.3. Les Méthodes de la maintenance 9
I.1.4. ORGANISATION DE LA MAINTENANCE 11
I.1.4.2. Les politiques de maintenance 13
I.1.4.3. Emploi préférentiel des diverses
formes de maintenance 14
I.1.5.LES OPÉRATIONS DE MAINTENANCE 21
I.2. NOTION DE SURETE DE FONCTIONNEMENT 33
I.2.1. Définition 33
I.2.2. Défaillance 33
I.2.3. Durée de vie 34
I.2.4. La fiabilité 34
I.2.5. La mainténabilité 34
I.2.6. La Disponibilité 35
I.2.7. La Sécurité 35
I.2.8. Traçabilité 35
I.2.9. Testabilité 35
CHAP.II : ETUDE SYSTEMIQUE DE LA DEROULEUSE N2700 42
II.1. PRESENTATION DE L'INDUSTRIE (I.T.B) 42
II.1.1 Historique 42
II.1.2. Localisation 43
II.1.3. Organigramme 44
II.2. MODELE DESCRIPTIF DE LA DEROULEUSE N2700 45
II.3. ANALYSE DES STRUCTURES PARTIELLES DE BASES 46
II.3.1. Les circuits auxiliaires de la dérouleuse
46
II.3.2. Description des organes principaux de la
dérouleuse 55
II.3.3. Régulateur de vitesse 57
Potentiomètre 58
II.4. ETUDE FONCTIONNELLE 60
86
II.4.1. Fonctionnement 60
II.4.2. Les grandeurs cinématiques du
procédé de déroulage 62
II.4.3. Chaine cinématique de la dérouleuse
62
CHAPITRE III. POLITIQUE DE MAINTENANCE ADAPTEE A LA
DEROULEUSE
N2700 63
III.1. ANALYSE D'APPARITION DES PANNES 63
III.1.1. Check-list des pannes 63
III.1.2. Tableau historique des pannes (2008 à
2010) de la dérouleuse N2700 65
III.1.3. Dépouillement des données
66
III.2. ANALYSE DU RETOUR D'EXPERIENCE (REX) 67
III.2.1. Analyse de la production 67
III.2.2. Détermination du taux de
défaillance (ë(ti)) 70
III.2.3. Détermination de la fonction de
répartition (F(ti)%) 72
III.2.4. Détermination de la fonction de
fiabilité R(ti)% 73
III.2.5. Calcul de la moyenne de temps de bon
fonctionnement « M.T.B.F » 74
III.2.6. Courbe de vie et politique de maintenance
75
III.3. DISPONIBILITE ET PROGRAMMATION DES TRAVAUX 76
III.3.1. Analyse de la disponibilité 76
III.3.2. Programmation des travaux de maintenance
72
1. TABLEAU RECAPUTILATIF DES RESULTATS 75
2. DISCUSSION ET ANALYSE CRITIQUE DES RESULTATS 76
SUGGESTIONS 77
CONCLUSION GENERALE 78
BIBLIOGRAPHIE 79
TABLE DES MATIERES 80
|