|
|
REPUBLIQUE ALGERIENNE
Ministère de l'Enseignement
Université Mouloud
Faculté
Mémoire
En vue de l'obtention du
diplôme
Option : Fabrication
|
Département
d'études
Supérieur et MAMMERI
de Génie de la Construction
Mécanique
Mécanique
|
DEMOCRATIQUE
de Génie
de Master professionnel
ET POPULAIRE
de la Recherche Scientifique de Tizi-Ouzou
de fin
en Génie Mécanique et
productique
|
|
M Melle
M Co
M
|
Etude et Conception d'un moule
d'injection
d'alliage d'aluminium pour un
flasque-bride
d'un moteur électrique
B5-A106/107-2
|
Proposé
Promoteur
par :
r : IGUER .B
: HAMROUNI .F
:
r : ZIANI.H
promoteur :
r : MENOUER.A
|
Réalisé M r :
M r :
|
par :
AMMOUR Redouane IKERROUIENE Djaffar
|
|
|
|
Promotion 2016-2017
|
|
|
|
Remerciement
Après avoir rendu grâce à Dieu le tout
Puissant et le Miséricordieux qui nous a donné la force et la
patience d'accomplir ce Modeste travail. Nous tenons à remercier
vivement tous ceux qui de près ou de loin ont participé à
la rédaction de ce document.
D'abord, on tient à remercier nos familles pour leurs
inconditionnel, indéfectible soutien durant toutes ces années,
nous voudrions vous associer à cette réussite car c'est avant
tout la vôtre.
Ensuite, nous voudrions présenter nos remerciements
à nous encadreurs Mr ZIANI.H et Mr MENOUER.A. On les
témoigner notre gratitude pour leur patience et leur soutien qui nous a
été précieux afin de mener notre travail à bon
port.
Aussi, on tient à remercier le personnel de
l'ELECTRO-INDUSTRIE qui nous ont chaleureusement accueilli dans leur groupe et
pour leurs précieux conseils et leurs coordinations tout au long de la
réalisation de ce travail et le développement de ce projet de
façon relativement autonome.
Enfin, nos vifs remerciements vont également aux
membres du jury pour l'intérêt qu'ils ont porté à
notre recherche en acceptant d'examiner notre travail et de l'enrichir par
leurs propositions.
DEDICACES
Ce travail est dédié à nos chers
parents
A nos chers frères et soeurs et toute la
famille
A nos chers amis et camarades
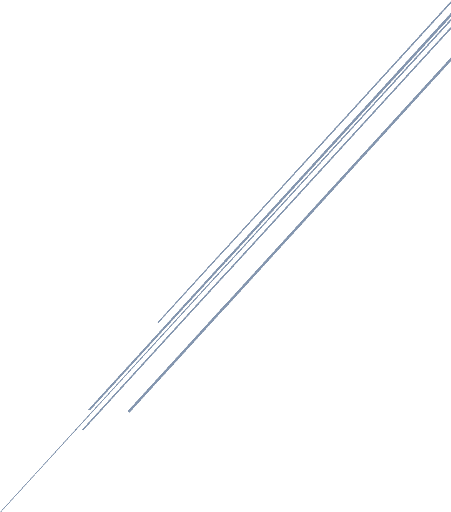
Sommaire
SOMMAIRE
INTRODUCTION GENERALE
PRESENTATION DE L'ENTREPRISE
CHAPITRE I : GENERALITES SUR LES MOTEURS ELECTRIQUES
I. INTRODUCTION 1
II. HISTORIQUE 1
III. COMPOSITION DE MOTEUR ELECTRIQUE 2
1 SCHEMA ET TERMINOLOGIE POUR UN MOTEUR ELECTRIQUE
2
2 LES PRINCIPAUX ELEMENTS DANS UN MOTEUR ELECTRIQUE
3
2.1 LA CARCASSE 3
2.2 L'ARBRE 4
2.3 LE STATOR 4
2.4 L'ENROULEMENT 5
2.5 LE ROTOR 6
IV. SCHEMA FONCTIONNEL 7
V. LE PRINCIPE DE FONCTIONNEMENT 8
VI. PROCESSUS DE FABRICATION DE MOTEUR ELECTRIQUE
10
1 LA GAMME DE FABRICATION 10
2 LA MATIERE PREMIERE 10
3 DESCRIPTION ET ORGANISATION DES ATELIERS PAR
FONCTION PRINCIPALE 11
3.1 ATELIER DE DECOUPAGE, ENCOCHAGE, EMBOUTISSAGE
11
3.2 ATELIER EMPAQUETAGE 12
3.3 ATELIER DE MOULAGE SOUS PRESSION 12
3.4 ATELIER D'USINAGE 13
3.5 ATELIER DE BOBINAGE 14
3.6 ATELIER MONTAGE 17
CHAPITRE II : PROCEDES DE MISE EN FORME DES METAUX
I. INTRODUCTION 18
II. MOULAGE 19
1 MATERIAUX DE MOULAGE 19
1.1 MATERIAUX POUR MOULES NON PERMANENTS
19
1.2 MATERIAUX POUR MOULES PERMANENTS 20
1.3 PRODUITS SPECIAUX 20
2 OUTILLAGES 20
3 MOULAGE EN MOULE NON-PERMANENT 21
3.1 MOULAGE AU SABLE SILICO-ARGILEUX 21
3.2 MOULAGE EN CARAPACE OU PRECEDE CRONING
21
3.3 MOULAGE V-PROCESS 22
1.1 SCHEMA ET TERMINOLOGIE 38
SOMMAIRE
3.4 LOST-FOAM OU MOULAGE A MODELE GAZEIFIABLE
22
3.5 MOULAGE A LA CIRE PERDUE 22
4 MOULAGE EN MOULE PERMANENT 22
5 CHOIX D'UN PROCEDE DE MOULAGE 23
III. MOULAGE EN MOULES METALLIQUES 24
1 GENERALITES 24
2 CARACTERISTIQUES GENERALES 24
3 ALLIAGES COULES 25
4 FORME ET DESSIN DES PIECES 25
5 OUTILLAGES 25
IV. MOULAGE SOUS PRESSION 26
1 GENERALITE 26
2 DESCRIPTION DU PROCEDE 27
3 CARACTERISTIQUES DES PIECES COULEES SOUS PRESSION
27
3.1 GRANDE PRECISION DIMENSIONNELLE 27
3.2 OBTENTION DE PIECES LEGERES 28
3.3 MISE AU MILLE TRES FAIBLE 28
3.4 BONNES CARACTERISTIQUES MECANIQUES 28
4 SYSTEMES D'INJECTION 28
4.1 SYSTEME A CHAMBRE CHAUDE 28
4.2 SYSTEME A CHAMBRE FROIDE 29
5 LES MACHINES UTILISEE 30
5.1 MACHINE A CHAMBRE CHAUDE 30
5.2 MACHINES A CHAMBRE FROIDE 31
6 LES CYCLES DE COULEE 33
6.1 MACHINES A CHAMBRE FROIDE HORIZONTALE
33
6.2 MACHINES ANCIENNES A TROIS PHASES
33
6.3 MACHINES MODERNES A BOUCLE FERMEE
34
7 MOYENS DE REMPLISSAGE DU CONTENEUR EN COULEE SOUS
PRESSION 35
CHAPITRE III : CHOIX DU MOULE ET PROCEDE
V. CONCLUSION 36
I. INTRODUCTION 37
II. CONCEPTION D'UN MOULE A INJECTION SOUS PRESSION
D'ALUMINIUM 37
1 ARCHITECTEURS DE MOULE 37
SOMMAIRE
1.2 ELEMENTS STANDARDS 39
2 LE NOMBRE ET DISPOSITION D'EMPREINTES
39
2.1 NOMBRE D'EMPREINTES 39
2.2 DISPOSITION DES EMPREINTES 40
3 LE SYSTEME D'ALIMENTATION DU MOULE 41
3.1 GENERALITES 41
3.2 TECHNIQUE D'ALIMENTATION 41
3.3 POINT D'INJECTION 42
3.4 REMPLISSAGE DES EMPREINTES 43
3.5 LES CANAUX ET LES ATTAQUES 44
4 LA MATIERE A INJECTER 48
5 L'EJECTION DES PIECES (GRAPPE) 48
5.1 LES EJECTEURS 49
5.1.1 FORME 49
5.1.2 FIXATION 49
5.1.3 POSITION SUR LA PIECE
50
5.2 COMMANDE DE L'EJECTION 50
6 LA MACHINE 51
7 DEGAZAGE DU MOULE 51
8 FIXATION DU MOULE 52
8.1 FIXATION PAR VIS 52
8.2 BRIDAGE 52
9 CIRCUITS DE REFROIDISSEMENT 53
10 CHOIX DES MATERIAUX 53
III. CONCLUSION 53
CHAPITRE IV : CONCEPTION ET CALCUL
I. INTRODUCTION 54
II. INTRODUCTION A LA CONCEPTION ASSISTEE PAR ORDINATEUR
(CAO) 54
III. LE CHOIX DE LA MACHINE 56
IV. CHOIX DE DIAMETRE DE PISTON D'INJECTION
59
V. DIMENSIONNEMENT DE SYSTEME D'ALIMENTATION
60
VI. DIMENSIONNEMENT DE CONDUIT DE REFROIDISSEMENT
63
VII. CALCUL DE TEMPS DE REFROIDISSEMENT 64
VIII. CALCUL DE TEMPS DE CYCLE 64
IX. DIMENSIONNEMENT DES TALONS DE LAVAGE ET DES TIRAGES
D'AIR 65
SOMMAIRE
X. CALCUL DE RESISTANCE 66
1 LES POIDS DES PIECES CONSTITUANTES LE MOULE
66
2 RESISTANCE DES ELEMENTS CONSTITUANTS LE MOULE AU
MATAGE 66
2.1 PLAQUE DE SERRAGE FIXE 67
2.2 CENTRE FIXE 68
2.3 PORTE EMPREINTE FIXE 68
2.4 PLAQUE DE SERRAGE MOBILE 69
2.5 BAGUETTE SUPPORT 69
2.6 CENTRE MOBILE 69
2.7 PORTE EMPREINTE MOBILE 70
3 RESISTANCE DES VIS CHC ET LES COLONNES DE GUIDAGE AU
CISAILLEMENT 70
3.1 RESISTANCE DES 4 COLONNES DE GUIDAGE DE Ø
50 MM 70
3.2 RESISTANCE DES 8 VIS CHC AU CISAILLEMENT DU AU
POIDS DE LA PARTIE MOBILE 71
3.3 RESISTANCE DES 7 VIS CHC AU CISAILLEMENT DU AU
POIDS DE L'EMPREINTE FIXE ET DE PORTE
EMPREINT FIXE 72
XI. CONCLUSION 72
CONCLUSION GENERALE
Liste des figures
Figure 1 : Schéma d'un moteur
électrique 2
Figure 2:carcasse d'un moteur électrique
(métal coulé) 3
Figure 3:Arbre d'un moteur électrique
4
Figure 4:Stator d'un moteur électrique
5
Figure 5:bobinage en un étage
5
Figure 6:bobinage en deux étages
6
Figure 7:Rotor court-circuité par
coulée d'aluminium 7
Figure 8:Schéma fonctionnel d'un moteur
électrique 7
Figure 9:Création d'un champ
magnétique 8
Figure 10: Variation de champ magnétique
8
Figure 11: Résultante des champs
magnétique 9
Figure 12: Champs magnétique
déphasés 9
Figure 13:Principaux procédés de
mise en forme des métaux 18
Figure 14:Differant procédés de
moulage 22
Figure 15:Évolution des coûts de
fabrication en fonction du nombre de pièces fabriquées
23
Figure 16:Système à chambre chaude
29
Figure 17:Système à chambre froide
30
Figure 18:Machine à chambre chaude
30
Figure 19:Les machines horizontales
31
Figure 20:Les machines verticales
32
Figure 21:Machines anciennes à trois phases
34
Figure 22:Machines modernes à boucle
fermée 34
Figure 23:Louches automatique 35
Figure 24:Fours doseurs 35
Figure 25:Remplissage du conteneur par mise en
dépression du moule 36
Figure 26:Moule pour moulage en chambre froide
38
Figure 27: Moule pour moulage en chambre chaude
38
Figure 28:Nombre d'empreintes en fonction de
critères techniques. 40
Figure 29:Composition d'un système
d'alimentation. 41
Figure 30:Injection dans le plan de joint.
41
Figure 31: Injection perpendiculaire au plan de
joint. 42
Figure 32:Équilibrage des efforts
42
Figure 33: Remplissage par jet
43
Figure 34: Remplissage par accumulation
43
Figure 35 : Proportions dimensionnelle de canal
44
Figure 36: Epaisseur et section des attaques par
rapport au canal. 44
Figure 37:Attaques directes 45
Figure 38:Attaques en retour 45
Figure 39:Attaques en queue de poisson
46
Figure 40:Attaque autour du noyau
46
Figure 41:Attaques pour moule a plusieurs
empreintes 47
Figure 42:Attaques centrale 48
Figure 43:Éjection de la grappe
48
Figure 44:Fixation d'un éjecteur
50
Figure 45:Répartition des éjecteurs
sur la pièce 50
Figure 46:Event 52
Figure 47:Procédé de Bridage
52
Figure 48:Schémas d'un plateau d'une presse
58
Liste des tableaux
Tableau 1: terminologie de moteur
électrique 3
Tableau 2 : Contrôle de la matière
Première 10
Tableau 3:Classification des
procédés de moulage 21
Tableau 4:Les différents modes de la
disposition des empreintes 40
Tableau 5 :les différents matériaux
constitutifs du moule 53
Tableau 6: Capacité d'injection
56
Tableau 7:Incidence pondérale en
pourcentage du dispositif de coulée 56
Tableau 8:Caractéristiques techniques de la
machine 59
Tableau 9:Temps de remplissage en fonction de
l'épaisseur de la pièce 62
Tableau 10:Epaisseur de l'attaque de coulée
en fonction de l'alliage utilisé 62
Tableau 11:Les poids des pièces
constituantes le moule 66
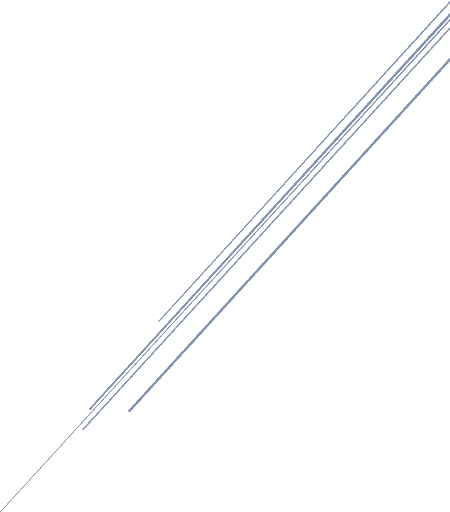
Introduction générale
Introduction générale
Parmi Les procédés de mise en forme ou autrement
appelés procédés de façonnage comprennent les
procédés de formage, ou mise en forme sans enlèvement de
matière, les procédés d'assemblage, ou mise en forme par
juxtaposition de matériaux et les procédés de mise en
forme par enlèvement de matière ou autrement appelés
procédés d'usinage ou techniques d'usinage. L'ingénieur
est confronté avec le problème du choix du meilleur
procédé à sa disposition. Entre les procédés
d'usinage et les procédés de formage, en particulier. Les
procédés de formage possèdent des avantages
indéniables comme l'économie de matière, la consolidation
du métal travaillé et une productivité
élevée, mais, en contrepartie, ils exigent l'emploi de machine
outils et d'outillage coûteux, ils sont de caractère très
spécialisé et ils exigent du matériau à transformer
des qualités métallurgiques de premier ordre. Le choix de la
technique de moulage à utiliser pour la fabrication d'une pièce
est soumis à de nombreux facteurs qui constituent une partie du cahier
des charges de cette pièce. Ce sont les caractéristiques
mécaniques minimales, l'alliage métallique composant la
pièce, la précision dimensionnelle générale et
particulière, l'état de surface et l'importance de la
série à fabriquer. Ces facteurs sont à prendre en compte
dès la conception de la pièce. Ils sont évalués
conjointement par le bureau d'études et de méthodes fonderie.
Parallèlement, il faut aussi évaluer les facteurs
spécifiques à la fabrication d'une pièce moulée :
Moyens de production, dimensions de la pièce et complexité des
formes, coût de l'outillage, coût d'entretien de l'outillage,
dépenses d'énergie, importance relative de l'ébarbage et
l'importance relative de la main-d'oeuvre à utiliser.
L'entreprise ELECTRO-INDUSTRIE a pris l'initiative de
fabriquer certaines pièces dans le but d'éviter leur importation
et améliorer sa gamme de produits. L'unité moteur prestation
technique a confié la conception d'un moule à injection
d'aluminium pour un flasque-bride d'un moteur électrique B5-A106/107
dans le cadre de l'exécution de notre projet de fin d'études.
Ce projet s'articule en quatre chapitres de la manière
suivante :
y' Le premier chapitre présente des
généralités sur le moteur électrique et sont
processus de fabrication.
y' Le deuxième chapitre est consacré aux
différant procédés de mise en forme des métaux ;
y' Le troisième chapitre montre les
méthodologies et les procédés de choix de moule ;
y' Ensuite vient le quatrième chapitre qui est le noyau
central de notre travail ce dernier est dédié à la
conception et dimensionnements de moule et les calculs de
vérification.
Enfin, nous terminerons par les dessins de définitions
et le dessin d'ensemble qui seront présentés après
conclusion générale.
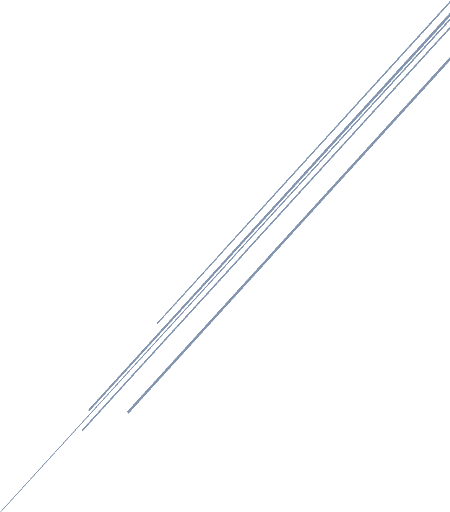
Présentation de l'entreprise
Le complexe occupe une surface totale de 40 hectares, dans
lequel on trouve un effectif de 824 travailleurs dont 16% de cadres, 33% de
maitrise et 50% d'exécution.
Présentation de l'entreprise
I. Introduction
L'ELECTRO-INDUSTRIES (E.I) a été
réalisée dans le cadre d'un contact produit en main avec des
partenaires allemands, en l'occurrence, SIEMENS pour le produit et FRITZ WERNER
pour l'engineering et la construction, l'infrastructure est
réalisée par les entreprises algériennes ECOTEC, COSIDER
et BATIMETAL.
Son activité de production est dans les domaines de
fabrication de Moteurs Electriques, Alternateurs, transformateurs de
distribution.
Le complexe occupe une surface totale de 40 hectares, dans
lequel on trouve un effectif de 824 travailleurs dont 16% de cadres, 33% de
maitrise et 50% d'exécution.
Sa capacité de production de transformateur couvre les
besoins du marché à 70% environ et ses ventes en moteurs
représentent 30% de sa capacité de production.
y' S'agissant du système documentaire, ils utilisent
252 normes internes en plus des normes DIN/VDE et CEI.
y' Il est à signaler que l'ELECTRO-INDUSTRIES est le
seul fabricant de ces produits en Algérie.
II. Historique
L'entreprise électro-industries, a été
créée sous sa forme actuelle en janvier 1999, après la
scission de l'entreprise mère ENEL (entreprise nationale des industries
Electrotechniques).
Son activité de production remonte à 1986, dans
les domaines de fabrication de Moteurs Electriques, Alternateurs et
transformateurs de distribution.
III. Composition
L'ELECTRO-INDUSTRIES est composée de deux (02)
unités; toutes situées sur un même site :
y' unité de fabrication de transformateurs de distribution
MT/BT ;
y' unité de fabrication des moteurs électrique,
alternateurs et prestation techniques.
En matière de qualité ELECTRO-INDUSTRIES dispose
de laboratoires d'essai et mesure, de ses produits ainsi pour le contrôle
des principaux matériaux utilisés dans sa fabrication.
Présentation de l'entreprise
IV. Localisation de l'entreprise et ses
coordonnées
Le siège social de l'entreprise est : Route nationale
N°12 à AZAZGA à 35 Km à l'est du chef-lieu de la
wilaya de TIZI-OUZOU et à 150 Km de la capitale Alger. L'entreprise
dispose de deux unités de production situées sur le même
site à AZAZGA.
Adresse : BP 17 15300 Azazga Algérie.
Téléphone : (00213) 26.34.16.86 (Standard).
Fax : (00213) 26.34.14.24.
? Les coordonnées de l'unité
moteurs & prestations (U.M.P) :
Téléphone : (00213) 26.34.51.31
Tél/Fax : (00213) 26.34.51.29
Le site web de l'entreprise est :
www.electro-industries.com
V. Organigramme de l'entreprise
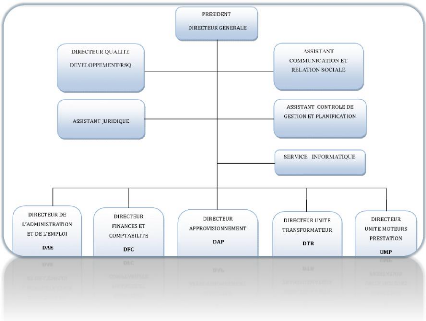
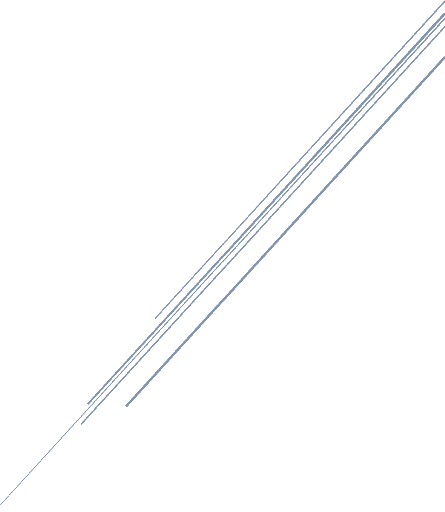
Chapitre I
Généralités sur les moteurs
électriques
Chapitre I Généralités sur les
moteurs électriques

1
I. Introduction
Les moteurs électriques sont aujourd'hui
présents dans toutes les branches de l'industrie et des transports. Ces
moteurs consomment environ la moitié de l'énergie
électrique générée dans le monde. Leur puissance
peut aller de quelques fractions de Watts à quelques centaines de
mégawatts. Les très petites puissances correspondent à des
machines où la transmission d'information prime sur la conversion
d'énergie. Les petites puissances se rencontrent principalement dans les
applications domestiques. Les conversions d'énergie dans ces moteurs
sont effectuées avec de faibles pertes : le rendement des grosses
unités atteint 99 %. Le réseau électrique est partout
disponible dans les pays développés et l'énergie
électrique est ainsi facilement distribuée. Le réglage est
commode grâce à l'électronique de puissance. Enfin, les
moteurs électriques ne sont pas polluants, ce qui ne doit toutefois pas
faire oublier qu'il n'en est pas toujours de même pour la production
d'électricité.
II. Historique
Les historiens des sciences et techniques ont quelques
incertitudes sur les premières réalisations et la
paternité des inventions des machines électriques. Nous
essaierons néanmoins de citer quelques noms et quelques dates de cette
aventure industrielle. Michael Faraday réalise un premier moteur
électromagnétique en 1821. Il est suivi de peu par Peter Barlow
qui invente en 1822 un dispositif qui porte aujourd'hui son nom, la roue de
Barlow. Le physicien et chimiste Moritz Hermann von Jacobi réalise un
moteur à inducteur bobiné à commutateur mécanique
en 1834. Il fait circuler un canot à hélice équipé
de son moteur sur la Neva à Saint-Pétersbourg. L'industriel
allemand Werner von Siemens construit vers 1856 une magnéto. L'Italien
Antonio Pacinotti introduit en 1859 une machine munie d'un rotor en forme
d'anneau. Cinq ans plus tard, il publie la description d'une machine pouvant
être utilisée en moteur ou en générateur. Ses
travaux passent alors inaperçus. L'inventeur belge, installé en
France, Zénobe Gramme construit en 1868 sa célèbre dynamo
et fonde en 1871 la Société des machines
magnéto-électriques Gramme. La réversibilité de la
dynamo est découverte en 1873. En 1872, Werner von Siemens prend un
brevet pour son induit en tambour. Nikola Tesla, alors étudiant, propose
déjà d'utiliser une machine sans commutateur. Devenu
employé de la Continental Edison Company en France, il construit le
premier moteur asynchrone en 1883 alors qu'il séjourne à
Strasbourg et dépose un brevet en 1884. Les moteurs classiques
utilisés aujourd'hui sont donc déjà tous connus en cette
fin de XIX° siècle. À la même époque, l'Italien
Galileo Ferraris établit la théorie du champ tournant.
[1]
Chapitre I Généralités sur les
moteurs électriques

2
III. Composition de moteur électrique
Sur le plan mécanique, un moteur est constitué
d'une partie fixe, le stator et d'une partie mobile, le rotor, entre lesquelles
se trouve un petit intervalle d'air, l'entrefer. Dans pratiquement tous les
moteurs, le rotor est à l'intérieur du stator, bien que la
configuration inverse existe pour des applications particulières.
Sur le plan électromagnétique, un moteur
comporte un circuit magnétique, constitue d'un matériau
ferromagnétique à forte perméabilité,
d'enroulements et éventuellement d'aimants permanents. Le
matériau ferromagnétique est nécessaire pour que le flux
produit soit assez élevé et pour que soit canalise afin de
pouvoir utiliser correctement ses effets. Les parties ferromagnétiques
soumises à un flux constant ou lentement variable peuvent être
massives, alors que les parties soumises à un flux à variation
rapide sont obligatoirement feuilletées pour limiter les pertes par
courants de Foucault.
1 Schéma et terminologie pour un moteur
électrique [3]
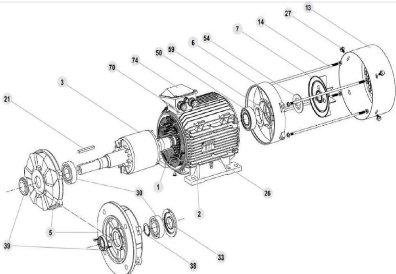
Figure 1 : Schéma d'un moteur
électrique
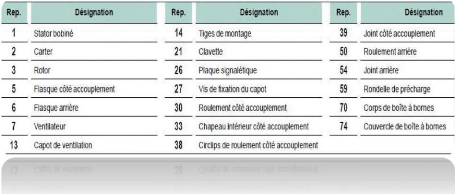
Chapitre I Généralités sur les
moteurs électriques

3
Tableau 1: terminologie de moteur
électrique
2 Les principaux éléments dans un moteur
électrique
2.1 La carcasse
La carcasse sert de support, joue le rôle d'enveloppe,
assure la protection contre les agents extérieurs et guide l'air de
ventilation ; elle agit aussi parfois comme échangeur thermique ; c'est
le cas des carcasses coulées des moteurs à ailettes ou des
moteurs fermés à tubes.
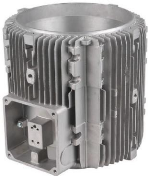
Figure 2:carcasse d'un moteur électrique
(métal coulé)
Chapitre I Généralités sur les
moteurs électriques

4
Les carcasses peuvent être réalisées en
métal coulé (fonte, acier ou aluminium) ; c'est le cas des
petites machines, par exemple le moteur asynchrone à ailettes de
refroidissement. Pour des puissances plus importantes, supérieures
à quelques centaines de kilowatts, la construction
mécano-soudée s'impose ; elle est réalisée en
tôles d'acier découpées, cintrées et
soudées.
2.2 L'Arbre
L'arbre de la machine électrique est un organe de
transmission du mouvement de rotation. Il comprend :
Une partie centrale qui sert de support au corps du rotor, au
circuit magnétique et aux enroulements tournants.
Dans les paliers flasques, le corps de palier est
généralement fixé sur la carcasse. Le rotor est alors
centré dans le stator au moment de la construction de la machine.
L'arbre est lui-même supporté par un ou plusieurs paliers suivant
la configuration de l'ensemble de la ligne d'arbre.

Figure 3:Arbre d'un moteur
électrique
Dans certains cas, l'arbre sert de soutien au collecteur, aux
ventilateurs, aux bagues, au rotor de la machine d'excitation, ainsi
qu'à des accessoires variés.
2.3 Le stator
C'est lui qui comporte les enroulements du moteur, il est
constitué d'un empilement de tôles magnétiques
isolées (d'une mince couche de vernis ou de silicate de soude) ; c'est
le circuit magnétique du stator.
Dans ces tôles, ont été
aménagées des encoches destinées à recevoir
l'enroulement statorique. Cette disposition du circuit magnétique
statorique est rendue nécessaire
Chapitre I Généralités sur les
moteurs électriques

5
pour éviter les courants de Foucault. L'enroulement,
composé de bobines mises en série ou en parallèle est
ensuite relié à la source d'alimentation,
généralement une source de tension.
Chaque bobine comporte deux parties distinctes. Le conducteur
situé dans l'encoche représente la partie active du bobinage. Les
têtes de bobines à l'extérieur du circuit
magnétique, assurent les liaisons entre les différents
conducteurs actifs. L'art du concepteur consiste à rendre maximale la
partie active de l'enroulement et à minimiser l'encombrement des
têtes de bobines qui sont à l'origine de pertes par effet Joule et
de fuites magnétiques.
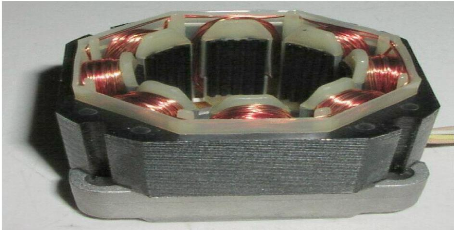
Figure 4:Stator d'un moteur
électrique
2.4 L'enroulement
Les enroulements servent à véhiculer les
courants électriques à l'intérieur de la machine. On
distingue principalement les enroulements inducteurs et les enroulements
d'induits.
Les enroulements d'induit sont constitués de
conducteurs répartis dans des encoches à la
périphérie du stator (machines synchrones et asynchrones) ou
à la périphérie du rotor (machines à courant
continu et machines asynchrones).
Chapitre I Généralités sur les
moteurs électriques
Enroulements parcourus par du courant alternatif :
Ces enroulements sont, dans le cas général, du type
polyphasé. Chaque encoche ménagée dans la tôlerie
magnétique débouche sur l'entrefer et contient un certain nombre
de conducteurs (qui peut varier dans de grandes proportions : de 2 à
20). On réalise :
1. Des bobinages en un étage :
où tous les conducteurs d'une encoche appartiennent à une
même phase et qui sont utilisés pour les machines de faible
puissance.
2. Des bobinages en deux étages :
où tous les conducteurs d'un étage situés dans une encoche
appartiennent à une même phase et sont reliés
électriquement en série ; suivant la valeur du pas de bobinage,
il peut arriver que deux phases cohabitent dans la même encoche ; ces
bobinages sont du type imbriqué ou ondulé (suivant le type de la
machine et le constructeur) et ils sont couramment utilisés dans les
machines de moyenne et de forte puissance.
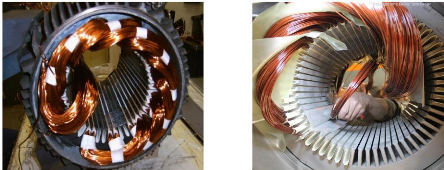

6
Figure 5:bobinage en un étage Figure 6:bobinage en
deux étages
2.5 Le rotor
On distingue deux types de rotor, celui des moteurs synchrones
et celui des moteurs asynchrones.
Le premier comporte des pôles créés par
des moyens électromagnétiques : Des aimants, des encoches vides
ou des enroulements parcourus par un courant continu. Le nombre de pôles
est alors fixé par construction. Ces rotors se rencontrent dans les
différents types de machines synchrones. Le second type de rotor
comporte un enroulement polyphasé en court-circuit. On distingue les
rotors bobinés, dont les enroulements sont accessibles de
l'extérieur à travers des contacts mobiles du type bagues balais
et les rotors à cage d'écureuil. En ce qui concerne les rotos
bobinés, le nombre de pôles du rotor est fixé par
construction. Quant aux rotors à cage, le nombre

7
Chapitre I Généralités sur les
moteurs électriques
de pôles dépend du stator qui induit dans les
barres de la cage des courants dont le déphasage fixe le nombre de
pôles égal à celui du stator.
Les rotors, comme les stators, comportent un circuit
magnétique, feuilleté généralement, mais
quelquefois massif comme celui des turboalternateurs. Dans ces circuits
magnétiques sont aménagées des encoches dans lesquelles
sont placés les conducteurs rotoriques. Le mode de réalisation
des enroulements rotoriques est spécifique à chaque type de
machine. Les enroulements sont constitués de barres
court-circuitées par un anneau placé à chaque
extrémité du rotor. Les conducteurs sont
généralement réalisés par coulage d'un alliage
d'aluminium, ou par des barres massives de cuivre ou, à l'occasion, en
laiton frettés dans les tôles du rotor. Il n'y a
généralement pas, ou très peu, d'isolation entre les
barres rotorique et les tôles magnétiques.

Figure 7:Rotor court-circuité par coulée
d'aluminium
IV. Schéma fonctionnel
Les moteurs électriques assure la fonction convertir de
la chaine d'énergie. Ils convertissent d'énergie
électrique en énergie mécanique, à ce titre, un
moteur électrique doit être aborde selon deux points de vue
énergétiques:
? L'énergie mécanique fournie.
? L'énergie électrique consommée.
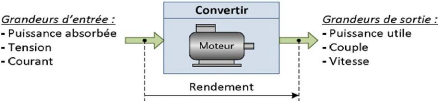
Figure 8:Schéma fonctionnel d'un moteur
électrique
Chapitre I Généralités sur les
moteurs électriques

8
V. Le principe de fonctionnement [1]
Le principe des moteurs à courants alternatifs
réside dans l'utilisation d'un champ
magnétique tournant produit par des tensions
alternatives La circulation d'un courant dans une bobine crée un
champ magnétique (B). Ce champ est dans l'axe de la bobine, sa direction
et son intensité sont fonction du courant (I). C'est une grandeur
vectorielle.
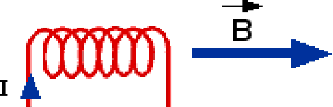
Figure 9:Création d'un champ
magnétique
Si le courant est alternatif, le champ magnétique varie en
sens et en direction à la même fréquence que le courant.
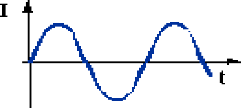
Figure 10: Variation de champ
magnétique
Si deux bobines sont placées à proximité
l'une de l'autre, le champ magnétique résultant est la somme
vectorielle des deux autres. Dans le cas du moteur triphasé, les trois
bobines sont disposées dans le stator à 120° les unes des
autres, trois champs magnétiques sont ainsi créés
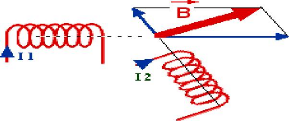
Chapitre I Généralités sur les
moteurs électriques
Figure 11: Résultante des champs
magnétique
Compte-tenu de la nature du courant sur le réseau
triphasé, les trois champs sont déphasés (chacun à
son tour passe par un maximum). Le champ magnétique résultant
tourne à la même fréquence que le courant soit 50 tr/s =
3000 tr/mn.
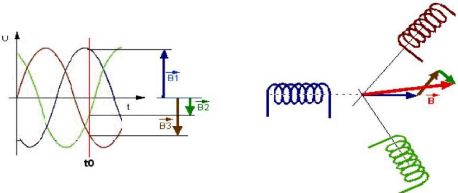

9
Figure 12: Champs magnétique
déphasés
Les 3 enroulements statoriques créent donc un champ
magnétique tournant, sa fréquence de rotation est nommée
fréquence de synchronisme. Si on place une boussole au centre, elle va
tourner à cette vitesse de synchronisme.
Chapitre I Généralités sur les
moteurs électriques
VI. Processus de fabrication de moteur
électrique
Dans ce qui suit on va présenter les étapes de
fabrication de chaque constituant de moteur électrique
présenté ci-dessus au sein de L'entreprise ELECTRO-INDUSTRIES.
1 La gamme de fabrication
Les moteurs électriques, basses tensions,
fabriqués par l'entreprise ELECTRO-INDUSRIES, sont de type asynchrones
triphasés à une ou deux vitesses, et monophasés à
condensateurs permanents.
Ils sont d'une construction fermée, à carasse
ventilée, en alliage d'aluminium et en fonte. Les rotors sont en
court-circuit, à cage d'écureuil, en aluminium pur (petits et
moyens moteurs) et en barre de cuivre (grands moteurs).
2 La matière première
La matière première arrive sous forme de :
y' Lingots d'aluminium pur à 99,5 %
y' Ronds d'acier de diamètres différents
y' Carcasses, flasques, pattes, ventilateurs : en fonte pour les
grands moteurs
y' Ventilateurs en plastique pour les petits moteurs
y' Roulements à billes et à rouleaux
cylindriques
y' Fils électriques de connexion
y' Rouleaux de fil de bobinage
y' Matériaux d'isolation de bobinage
y' Anneaux élastiques, visserie, rondelles, rondelles
ondulées
y' Peinture
y' Bobines de tôle magnétique
Des échantillons de matière première sont
fait contrôler dans deux laboratoires physique et chimique toute on
mesure :
LABO DE PHYSIQUE LABO DE CHIMIE
La résistance (?)
La résistance à la rupture
L'allongement
La tension de claquage la viscosité la
densité
|
classe de risque
|

10
Tableau 2 : Contrôle de la matière
Première
Chapitre I Généralités sur les
moteurs électriques

11
Caractéristiques à
contrôler
· Dimensions des filetages
· Nombre de défauts de vernis d'un fil de bobinage
par mètre
· Dimensions des roulements, et charge radiale
· Raideur des ressorts
· Dimensions de la matière en fonte
· Contrôle de la tôle magnétique
3 Description et organisation des ateliers par fonction
principale
- Atelier de découpage, encochage, emboutissage ;
- Atelier empaquetage ;
- Atelier de moulage sous pression ;
- Atelier d'usinage ;
- Atelier de bobinage ;
- Atelier de montage.
3.1 Atelier de découpage, encochage,
emboutissage
Dans cet atelier, sont découpés et encocher les
deux types de tôles utilisées pour la conception de deux
catégories de moteur de hauteur d'axe : 71 à 160 mm et 180
à 400mm. Le découpage s'effectue sur presse rapide
mécanique pour aboutir aux forme voulues après plusieurs
opération successives ; La tôle avance et arrive entre l'outil et
la matrice de la machine, c'est ainsi que le découpage commence.
L'emboutissage des capots de ventilation et aussi effectue dans
cette atelier.
? contrôle
Une fois le découpage des tôles statorique et
rotorique et fini, un échantillon subi un contrôle des cotes
fonctionnelles :
· le diamètre intérieur ;
· le diamètre extérieur ;
· la coaxialités ;
· le contrôle circularité ;
· le contrôle des bavures ;
· le contrôle de l'épaisseur de la
tôle.
Chapitre I Généralités sur les
moteurs électriques

12
3.2 Atelier empaquetage
La réalisation des paquets statorique et rotorique,
s'effectue sur une presse à empaqueter, en plusieurs étapes :
a) Empaquetage du paquet statoriques :
Après l'emplacement des tôles en nombres
définis, dans un outil monté sur une presse à empaqueter,
on place les agrafes dans les rainures.
b) Contrôle du paquet :
Après sa réalisation le paquet statorique passe au
contrôle visuel et dimensionnel
· Visuel : on contrôle le décalage des
tôles, les bavures, ...
· Dimensionnel : les cotes fonctionnelles,
cylindricité, diamètres intérieurs et
extérieurs.
c) Empaquetage du paquet rotorique :
Ici on empile les tôles sur un calibre triage, pour
obtenir la hauteur du paquet rotorique qui est contrôlé à
l'aide d'un pied à coulisse.
L'arbre est placé sur la partie supérieure de
la presse via un piston, il est emmanché de force dans le paquet
rotorique.
3.3 Atelier de moulage sous pression :
Dans cet atelier sont fabriquées toutes les
pièces constitutives des moteurs
en version aluminium, à savoir :
· Réalisation des pièces en alliage
d'aluminium (Silicium, Manganèse, Cuivre) comme : carcasse, flasque
(AS, BS), boite à bornes, couvercle de boite à bornes
· Injection du rotor en aluminium pur à
99,5%. ? Contrôle :
On achemine cinq (05) échantillons du paquet rotorique
vers le service contrôle pour subir les vérifications suivantes
:
· La conductivité de l'aluminium.
· La longueur du paquet.
· Visuel.
Chapitre I Généralités sur les
moteurs électriques

13
3.4 Atelier d'usinage
Dans cet atelier s'exécute la fabrication des arbres du
rotor et aussi l'usinage des pièces comme : flasque, carcasse, etc.
Les principaux types d'usinages :
a) Fabrication de l'arbre :
L'atelier reçoit les ronds d'acier qui subissent le
contrôle de diamètre, concentricité,... ? Une fois l'acier
contrôlé les arbres sont découpés à l'aide
d'une scie mécanique. ? L'arbre est ensuite acheminé au centre
d'usinage pour être centré.
Cette opération consiste à percer deux trous qui
servent de référence pour pouvoir tourner le rotor dans un axe
bien défini.
b) Usinage du rotor :
On effectue les opérations suivantes sur le rotor :
V' Tournage du paquet :
C'est à l'aide d'un tour parallèle (dressage,
chariotage, gorge,...). V' Rectification :
A l'aide d'une rectifieuse on modifie l'état de surface
où les roulements seront monté et les sorties d'arbre.
V' Fraisage :
A l'aide d'une fraiseuse on réalise les rainures de
clavette.
c) Usinage des différentes pièces
(carcasse, flasque, boite à bornes) : V' Carcasse
:
Alésage des carcasses à l'aide des tours verticaux
;
Perçage et taraudage des trous de fixation ou seront
fixés les flasques et la boite à bornes.
V' Flasque (As et Bs) :
Tournage des bords de centrage et cage des roulements.
V' Boite à bornes :
Perçage et taraudage des trous de fixation recevant le
couvercle.
Chapitre I Généralités sur les
moteurs électriques

14
d) Lavage des pièces :
Les pièces usinées sont lavées afin
d'éliminer les encrassements.
Rq : les techniciens qui travails dans cet atelier doivent suivre
ce qu'on appelle la gamme d'usinage.
Exemple : gamme de fabrication de l'arbre
1. Scier la longueur ;
2. Centrer à la longueur ;
3. Tournage complet ;
4. Rectification ;
5. Fraisage des rainures ;
6. Huiler ;
7. Stockage au magasin.
3.5 Atelier de bobinage
L'atelier de bobinage est divisé en trois sections
principales qui travaillent en parallèle : section de préparation
des bobines, section de préparation des éléments
d'isolation des bobines, et la section de bobinage.
? Section de préparation des bobines
L'ouvrier chargé de préparer les bobines suit
une feuille de calcul sur laquelle les caractéristiques suivantes sont
notées :
? Type de moteur à bobiner (choix de gabarit) ? Nombre des
bobines
? Diamètre de fil
Les bobine sont réalisées à l'aide d'une
bobineuse équipée d'un gabarit, et réglable pour un nombre
de spires définit.
Une fois le fil est bobiné, le paquet est
attaché pour garder sa forme jusqu'à l'étape de bobinage
dans le stator.
Chapitre I Généralités sur les
moteurs électriques

15
? Section de préparation des
éléments d'isolation
A l'aide des opérations de découpage et pliage les
éléments suivants sont
fabriqués :
· Caniveaux d'encoches
· Cales de fermeture
· Gaines isolantes
· Séparateurs de phases
· Lames intermédiaires
· Câbles de raccordement
? Section de bobinage
Dans cette section se déroule le processus final dans
la fabrication de stator allant de l'insertion des caniveaux d'encoches
jusqu'à l'imprégnation.
1. Insertion des caniveaux d'encoches : Cette
opération se fait grâce à une machine qui découpe le
papier isolant et le pénètre automatiquement dans les encoches du
stator.
2. Insertion des bobines dans le stator :
Le bobineur suit une feuille de calcul qui lui est fourni avec
chaque série de stators à bobine, cette feuille comporte :
- Type de moteur
- Diamètre de file
- Nombre de pôles
- nombre de spires par encoche de stator
- Schéma de bobinage
- Type de connexions
- Nombre de bobines en série par phase
- Nombre de bobines en parallèle par phase
- Type d'enroulement
- Nombre de conducteurs par encoche
- Câbles de raccordement (nombre, section)
- Caractéristiques mécaniques du stator : nombre
d'encoches, longueur du paquet
- Angle d'inclinaison de paquet rotorique.
Chapitre I Généralités sur les
moteurs électriques
L'insertion se fait soit :

16
Automatiquement pour les moteurs d'hauteur d'axe70 mm ? 130
mm; Manuellement pour les moteurs d'hauteur d'axe 132 mm ? 400 mm.
Remarque :
C'est pendant cette opération que l'on intègre
aussi les lames intermédiaires pour le bobinage à double couche
ainsi que les cales de fermeture.
Une fois les bobines introduites, on place les
séparateurs de phases pour éviter le court-circuit entre
phase.
4. Connexion :
Connexion entre les bobines et isolation :
Les bobines de chaque phase sont liées entre elles de
façon précise en conformité avec le schéma de
bobinage afin d'obtenir 03 grande bobines ayant chacune d'elles une
entré et une sortie.
Les points de connexion sont basés et isolés
avec des gaines isolantes déjà placées.
Connexion des bobines et câbles de raccordement
:
Les entrées et les sorties de chaque phase sont
connectées et soudées à des câbles de raccordement
qui assurent la liaison électrique avec la boite à borne.
L'entrée et la sortie de chaque phase sont distinguées des autres
avec des couleurs.
5. Imprégnation :
Cette opération consiste à mettre de la
résine au bobinage du stator pour le
rendre plus compact et solide, deux méthodes sont
utilisées :
? Imprégnation goute à goute ;
? Imprégnation dans un bain de résine.
Le stator est maintenant prêt à être
monté, avant cela, il passe au magasin
intermédiaire de stockage.
Chapitre I Généralités sur les
moteurs électriques

17
3.6 Atelier montage
On recense trois (03) secteurs essentiels dans cet
atelier :
1. Secteur équilibrage :
Cette opération se fait essentiellement avec l'ajout
ou l'enlèvement de matière sur le rotor pour assurer son
homogénéité et se termine par une couche de peinture
(antirouille) puis le rotor est envoyé au magasin
intermédiaire.
2. Secteur prés montage : Les
opérations réalisées dans ce secteur sont :
? Huiler l'intérieur de la carcasse pour faciliter
l'insertion du paquet statorique
dans celle-ci ;
? Emmanchement du paquet avec une presse ;
? Mise en longueur et tournage des bords de centrage de la
carcasse coté AS et
BS ;
? Fraisage des pattes pour retrouver la hauteur d'axe exacte
;
? Peinture du diamètre intérieur du stator avec un
antirouille.
3. Secteur montage final :
Dans ce secteur sont effectuées les opérations
suivantes :
> Mise en place du couvercle du palier intérieur
côte BS pour assurer une bonne étanchéité
du moteur ;
> Emmanchent des roulements déjà
graissés côte AS et BS avec une presse verticale
et emplacement de clavette coté AS ;
> Visser le couvercle de palier sur le flasque, cela permet
de cerner le roulement entre ces deux pièces ;
> Emplacement de la clavette coté BS et
emmanchement du ventilateur avec la même presse puis insertion de la
bague d'arrêt (serre clips) pour ventilateur ;
> Intégration du rotor complet dans le stator
bobiné et fixation du flasque coté BS avec des avis ;
> Emplacement des rondelles (rondelle de compensation et
rondelles élastiques) sur le flasque coté AS pour
éviter le jeu axiale du rotor ;
> Fixation du flasque sur la carcasse ainsi que le montage
du capot du ventilateur ; > Préparation de la boite à bornes
et fixation des câbles de raccordement sur la
plaque à bornes ;
> Le moteur sera remis à la plate-forme d'essais.
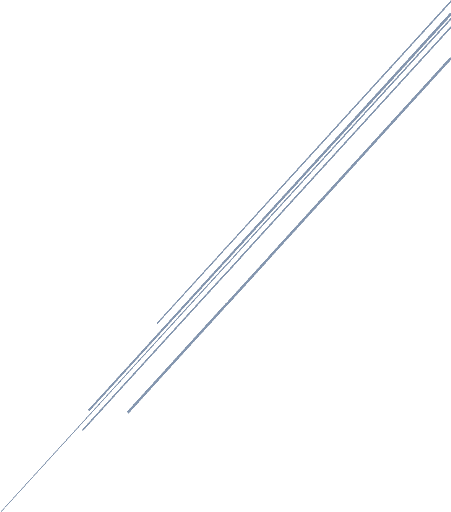
Chapitre II
Procédés de mise en forme des
métaux
Chapitre II : Procédés de mise en forme
des métaux

18
I. Introduction
L'objectif premier de la mise en forme des métaux est
de conférer à une pièce métallique des dimensions
situées dans une fourchette de tolérance donnée. Les
principaux procédés de mise en forme des métaux sont
apparus progressivement, donnant naissance par la suite à diverses
variantes, parfois très nombreuses. Les formes modernes des divers
procédés sont le plus souvent apparues récemment pour
assurer la production en grande série de pièces à faible
coût. Il existe trois voies principales de mise en forme selon
l'état de départ du matériau métallique (le
moulage, le façonnage et le frittage). La Figure suivante
récapitule les principaux procédés de mise en forme des
métaux utilisés actuellement.
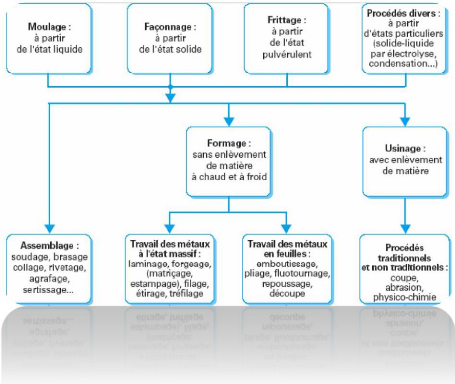
Figure 13:Principaux procédés de mise
en forme des métaux
Chapitre II : Procédés de mise en forme
des métaux
II. Moulage

19
L'opération de moulage consiste à fabriquer un
moule, généralement en matériaux réfractaires, qui
porte l'empreinte en négatif de la pièce, cette empreinte
étant obtenue à partir d'un modèle reproduisant la
pièce à fabriquer.
L'opération de moulage est une des plus importantes du
processus industriel de la fonderie. Elle détermine en effet,
d'après le modèle, les formes de la pièce à couler,
ses dimensions et leur précision, ses états de surface, son
refroidissement, et joue un rôle prépondérant sur de
très nombreux paramètres influant sur sa qualité.
À titre d'exemple, dans des productions de grandes
séries, les opérations de moulage représentent
fréquemment 30 % environ des prix de revient hors matière Il
convient donc que le choix d'un procédé de moulage soit fait avec
le maximum de précaution pour ne pas pénaliser les productions
futures, tant en qualité qu'en prix de revient.[6]
1 Matériaux de moulage
1.1 Matériaux pour moules non permanents :
Pour la fabrication des moules et des noyaux, la fonderie
utilise de nombreux matériaux et produits dont les plus importants sont
cités ci-après.
a) Sables de base et siliceux :
Ils sont composés essentiellement de grains de silice
SiO2 ; c'est le matériau le plus universellement employé pour la
confection des moules et des noyaux. Parmi toutes les variétés on
citera :
? les sables silico-argileux naturels, utilisés à
l'état brut ;
? les sables blancs extra-siliceux de carrière,
très souvent traités par lavage,
classement granulométrique et séchage avant
livraison.
? Les Sables spéciaux (chromite, olivine, zircon,
silico-alumineux)
Tous ces produits doivent présenter des
caractéristiques bien définies, comme par
exemple:
y' la répartition granulométrique ou la forme des
grains ;
y' des propriétés chimiques en accord avec celles
des liants ;
y' des propriétés physiques à froid
(perméabilité) et à chaud (réfractarité,
dilatation, capacité et conductivité thermiques,
mouillage par le métal liquide).
b) Liants
Ce sont les deuxièmes constituants les plus importants
employés pour la fabrication des moules et noyaux en fonderie. Ils
doivent en effet donner :
Chapitre II : Procédés de mise en forme
des métaux

20
y' la plasticité au sable pour épouser les
formes du modèle et acquérir ensuite par durcissement une
résistance mécanique permettant de conserver la forme
jusqu'à la solidification du métal ;
y' le minimum de réactions moule/métal qui sont
des risques de défauts sur pièce de types piqûres ou
soufflures.
On peut classer les liants en deux grandes familles :
? Les liants minéraux comme les argiles, bentonite,
silice colloïdale, silicate soluble, plâtre et ciment ;
? Les liants organiques comme les matières
amylacées (dérivées de l'amidon), les huiles siccatives et
les résines synthétiques durcissables à chaud ou à
froid, avec catalyseurs solide, liquide ou gazeux.
1.2 Matériaux pour moules permanents :
Certains procédés de moulage nécessitent
l'exécution de moules permanents pour lesquels on utilise des
matériaux métalliques comme les fontes, fonte GS, aciers, aciers
spéciaux revêtus d'enduits réfractaires (graphite, lait de
silice) destinés à protéger leur surface de
l'érosion du métal liquide et des chocs thermiques trop brutaux.
C'est le cas principalement :
-- en fonderie de fonte, de la centrifugation et de la
coulée en coquille ;
-- et en fonderie de métaux non ferreux (aluminium,
Zamac) des coulées en coquille par gravité, basse pression et
sous-pression.
1.3 Produits spéciaux :
Beaucoup de procédés de moulage particuliers
font appel à des produits spéciaux, comme par exemple la fonderie
de précision (dite aussi en cire perdue ) qui utilise des modèles
injectés en cire, puis éliminés par chauffage après
dépôt et durcissement des couches réfractaires sur les
modèles. [4]
2 Outillages
L'Empreinte ou moule: souvent
réalisée en matériau réfractaire, parfois
destructible ou permanente. Elle est généralement en deux parties
(parfois plus) et agrémenté de noyaux (formes
intérieures).
La Coulée: C'est le remplissage de
l'empreinte avec le matériau de la pièce, elle s'effectue par
gravite ou sous pression.
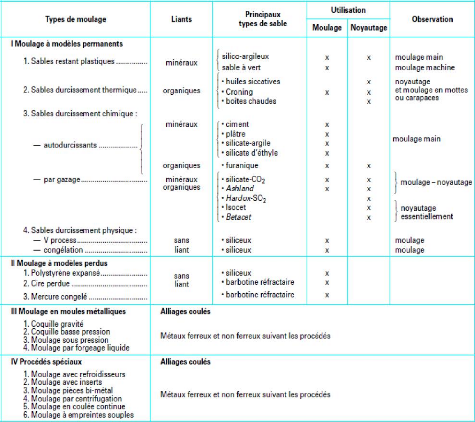
Chapitre II : Procédés de mise en forme
des métaux
Tableau 3:Classification des procédés
de moulage [6]

21
3 Moulage en moule non-permanent
3.1 Moulage au sable silico-argileux
A la main: l`empreinte est obtenue à l'aide d'un
modèle en plusieurs parties ou par taillage du sable.
Particulièrement adapté pour des pièces
unitaires ou de petite série,
Machine: La forme est issue d'une plaque modèle ce
précédé est adapté pour une production en petite et
grande série.
3.2 Moulage en carapace ou Précédé
Croning
Avec modèle d'épaisseur réduite, en sable et
résine thermo durcie : production de pièces précises.
Chapitre II : Procédés de mise en forme
des métaux
3.3 Moulage V-process
Le moule en sable à sec et sans liant est durci sous
vide: production de pièces précises (forme, dimensions,
état de surface).
3.4 Lost-Foam ou moulage a modèle
gazéifiable
Modèle généralement en polystyrène
expansé, détruit lors de la coulée: destiné pour
une production unitaire (prototypage rapide).
3.5 Moulage a la cire perdue
Avec modèle perdu (généralement en cire) qui
est détruit, tout comme le
moule: production de pièces complexes, précise
et de petites dimensions (prototypage rapide).
4 Moulage en moule permanent
i. Moulage en coquille, par gravite
:
Le moule est rempli par la pesanteur. Ce
procédé est adapté à la production en
série.
ii. Moulage par centrifugation:
Injection de l'alliage dans une empreinte en rotation. Adapte
pour la production de pièces de révolution et possibilité
de réaliser des pièces bi ou multi métaux, Souvent utilise
pour des pièces de grande dimension. (Ex: canalisations)
iii. Moulage sous pression :
La matière est injectée sous pression à
l'intérieur de moule. Destiné aux travaux de grande série
avec outillage entièrement automatisé (ex: blocs moteurs en fonte
ou d'aluminium et pièce plastiques).
Coulée
Moule
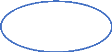
Non permanant
Gravité
Gravité
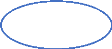
Permanant


22
Modèle permanant
· Moulage au sable silico-argileux
· Moulage en carapace (Croning)
· V-process
Modèle non permanant
· 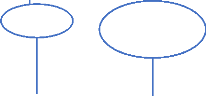
Sous pression
· Coquille
· Coulée continue
· Coquille
· Centrifugation
Lost Foam
(Sable non agglomère)
· Cire perdue (Céramique)
Figure 14:Différant procédés de
moulage
Chapitre II : Procédés de mise en forme
des métaux

23
5 Choix d'un procédé de moulage
Pour la fabrication d'une série de pièces
données, on choisira le procédé de moulage en fonction des
caractéristiques recherchées pour les pièces et des
possibilités techniques des procédés envisagés.
Cette étude devra être appuyée sur une
étude économique, pour calculer, en fonction des investissements
de départ (outillages, installations spécifiques et diverses...)
et des coûts de fabrication (main-d'oeuvre, énergie,
matière, entretien et renouvellement des outillages...), le seuil de
rentabilité d'un procédé par rapport à un autre.
Le graphique de la figure 15 permet de comparer les
coûts du moulage au sable et du moulage en coquille et de
déterminer la quantité de pièces à partir de
laquelle le moulage en coquille deviendra le plus économique (point
Q).
Le choix d'un procédé de moulage devra
également intégrer les gains à l'usinage, très
sensibles lorsque l'on compare des pièces coulées en sable
à des pièces coulées en coquille ou sous pression.
[4]
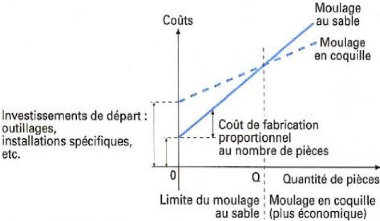
Figure 15:Évolution des coûts de
fabrication en fonction du nombre de pièces
fabriquées
Chapitre II : Procédés de mise en forme
des métaux

24
III. Moulage en moules métalliques
1 Généralités
Dans les procédés de moulage au sable, les
moules et les noyaux doivent être refaits après chaque
coulée, ce qui pose de nombreux problèmes et nécessite des
installations importantes pour la production des moules neufs et de nombreuses
manutentions. On peut estimer que la production d'une tonne de pièces
bonnes nécessite, en moyenne, la manutention de 20 tonnes, voire 50 et
même plus pour des pièces minces Cette production de moules
entraîne de grosses consommations de sable neuf avec des problèmes
d'évacuation et de mise en décharge des sables usés
lorsque les procédés de récupération des vieux
sables ne permettent pas un recyclage à 100 %. Aussi s'est-on
efforcé, de tout temps, de réaliser des moules ou des
éléments de moules capables de supporter plusieurs coulées
successives (moules en pierre taillée, en bois, en fonte, etc.).
Cette idée est très ancienne mais le
procédé ne s'est développé industriellement,
qu'à partir du 20e siècle, avec la mise au point d'alliages dont
la température de fusion est inférieure à 1000 °C
(l'aluminium, le magnésium et leurs alliages, les alliages de cuivre, de
zinc, de plomb et d'étain). Les empreintes furent taillées dans
des blocs métalliques pour obtenir des moules durables, solides et
constants en dimensions, appelés moules permanents ou coquilles. .
[7]
2 Caractéristiques générales
Grâce à l'emploi de moules métalliques,
le moulage en coquille présente les caractéristiques suivantes
pour les moules :
· Rigidité de l'empreinte ;
· Grande précision dimensionnelle ;
· Excellent état de surface des
éléments moulants ;
· Conductivité thermique élevée des
empreintes qui donnent aux pièces moulées un meilleur état
de surface ;
· Des caractéristiques mécaniques plus
élevées de l'alliage coulé, conséquence d'une
vitesse de refroidissement et de solidification plus élevée,
donnant un grain plus fin et une matière plus compacte ; mais des
contraintes résiduelles à l'état brut peuvent
nécessiter un traitement thermique de détente des pièces
surtout pour les métaux ferreux ;
· Une plus grande précision des dimensions des
pièces avec la possibilité de faire venir, bruts de fonderie, des
trous de fixation et de permettre une réduction appréciable des
surépaisseurs d'usinage.
Chapitre II : Procédés de mise en forme
des métaux

25
Chapitre II : Procédés de mise en forme
des métaux

26
3 Alliages coulés
Ce sont généralement des alliages non ferreux
(aluminium, laiton, bronze, etc.) qui sont utilisés dans ce genre de
fabrication. Les métaux ferreux, à cause des températures
plus élevées de coulée, sont rarement employés,
sauf pour des fabrications très spécifiques comme, par exemple,
les tuyaux en fonte, les pièces de grandes séries pour
l'automobile (collecteurs, cylindres de freins...). L'usure rapide des
outillages dans ce cas pénalise lourdement les prix de revient ; ils ne
peuvent donc s'amortir que pour de très grandes séries.
4 Forme et dessin des pièces
Les pièces doivent être de formes assez simples,
surtout intérieurement, afin de pouvoir être obtenues par des
noyaux métalliques dans toute la mesure du possible. L'emploi des noyaux
en sable devra être réservé aux pièces
compliquées dont le dessin ne peut être simplifié (culasses
par exemple). L'emploi de ces noyaux complique la fabrication et entraîne
des difficultés au décochage, la faible température de
coulée des pièces en aluminium ne permettant pas de bien calciner
le noyau qui s'évacuera assez difficilement au débourrage.
Les formes extérieures qui viennent par les parties
moulantes des outillages peuvent être plus compliquées, à
condition toutefois de bien respecter les sens de démoulage choisis. On
peut ainsi faire venir sur les parois extérieures toutes les nervures
nécessaires pour la résistance mécanique des pièces
(carters-cylindres, carters de boîtes de vitesses en aluminium
coulé sous pression, etc.) En cherchant à simplifier à
l'extrême les formes intérieures.
5 Outillages
Leur définition commence par celle des formes de la
pièce qui permettra de préciser les sens de moulage, la venue des
parties creuses (noyaux métalliques, noyaux en sable, broches, etc.),
les dépouilles (généralement de 1 à 3 %), les
retraits, les systèmes de refroidissement du moule, la position des
éjecteurs, les systèmes de remplissage, de coulée et les
masselottes.
Les moules sont constitués d'au moins deux parties
métalliques dont l'assemblage reproduit les formes extérieures de
la pièce et le système de coulée. Des dégagements
d'air du moule et des gaz provenant des noyaux sont à prévoir
pour faciliter la coulée et la bonne venue de la pièce. Les
outillages de moulage en coquille doivent présenter un certain nombre de
qualités permanence des formes à chaud (250 à 400 o C pour
les pièces en aluminium), bonne résistance aux contraintes
thermiques, bonne précision dimensionnelle, démoulage facile sans
arrachement, etc. qui font choisir pour réaliser ces moules des
matériaux métalliques comme les fontes lamellaires, les fontes GS
faciles à couler et à usiner. Les parties les plus soumises
à usure, comme les talus, les broches et les noyaux, sont souvent
réalisées en acier usiné, trempé, revenu pour
améliorer leur résistance à l'usure. Ces moules doivent
avoir un
certain nombre de parties mobiles dont l'effacement permettra
le dégagement de la pièce, l'extraction des noyaux et le
démoulage de la pièce. Toutes les parties moulantes sont en
général usinées sur des fraiseuses à reproduire ou
sur des machines d'électroérosion ; plus rarement, elles sont
obtenues brutes de fonderie. Elles sont fixées sur les
éléments coulissants de la coquille pour pouvoir être
facilement démontées et remplacées.
IV. Moulage sous pression
1 Généralité
La philosophie de remplissage en fonderie sous pression est
radicalement différente de procédés ci-dessus
évoqués. On cherche à remplir un moule complètement
avant même que le liquide ait commencé à se solidifier.
L'objectif est d'atteindre de quelques dizaines de
millisecondes à 0,1 s et des vitesses de remplissage de l'ordre de 20
à 80 m/s à l'entrée de l'empreinte. À ces niveaux
de vitesse-là, le métal liquide est propulsé dans
l'empreinte sous
forme pulvérisée, Pour atteindre ces vitesses de
remplissage vertigineuses, il faut avoir recours à une technologie
hydraulique combinée à la compression de l'azote. Les pressions
appliquées pendant le remplissage atteignent 50 à 150 bars en
fonction de la vitesse recherchée. Les fondeurs sous pression ont
l'habitude de recourir à un diagramme (p, Q) pour déterminer la
pression P nécessaire pour assurer un débit matière Q
voulu. Le remplissage étant complètement turbulent, beaucoup
d'air se trouve entraîné avec le métal dans l'empreinte.
Une pression d'intensification très élevée (de 500
à 1 200 bar) est donc appliquée pour comprimer les pores et
autres bulles et agir contre le retrait de la pièce. Les avantages de ce
saut technologique sont:
y' Des temps de cycles extrêmement courts, de 30
secondes à quelques minutes (pour des pièces de 10 kg);
y' La possibilité de remplir des épaisseurs
très fines; jusqu'à 0,8 mm localement et plusieurs
millimètres sur des longueurs importantes;
y' Une précision dimensionnelle élevée
car l'application d'une forte
pression pendant toute la solidification permet de combler
partiellement
le retrait à la solidification au fur et à
mesure qu'il se forme. Il est même possible de réaliser des
filetages directement;
y' Une température de coulée très proche
de la température de liquidus de l'alliage et des moules beaucoup plus
froids qu'en fonderie gravité et basse pression.
Une machine de fonderie sous pression se compose toujours :

27
Chapitre II : Procédés de mise en forme
des métaux
? D'une unité de fermeture avec usuellement un dispositif
en genouillère.
La capacité (de 5 à 5 000t) conditionne la surface
projetée maximale de pièce
à couler et les pressions maximales applicables;
? D'une unité d'injection. Deux technologies se partagent
le marché, les
chambres chaudes et les chambres froides. Leur différence
tient
essentiellement à la position de l'unité
d'injection du métal. [6]
2 Description du procédé
Dans ce procédé, l'alliage liquide est
injecté sous forte pression dans l'empreinte d'un moule
métallique.
L'alliage, poussé par un piston dans un conteneur en
acier spécial au chrome-molybdène, est introduit dans le moule
par une buse d'injection. En phase finale, la pression peut atteindre 70
à 80 MPa, voire 100 MPa ou plus. L'injection se fait en un temps
très court, 0,1 s en moyenne.
Les moules sont montés sur les plateaux d'une presse
hydraulique horizontale, de grande puissance (jusqu'à 30 MN et plus de
force de fermeture) pour éviter au moment de l'injection toute ouverture
intempestive de l'outillage et toute fuite au plan
de joint. Les pressions et les systèmes d'injection,
les forces de fermeture des machines, dépendent de nombreux facteurs,
notamment du genre d'alliage coulé, de la forme et du volume de la
pièce. Les pièces produites sont précises,
légères, et les cadences de production très rapides. Par
contre, les outillages et les machines représentent des investissements
très coûteux qui font réserver ce procédé
à des fabrications de moyennes ou grandes séries.
3 Caractéristiques des pièces coulées
sous pression
3.1 Grande précision dimensionnelle
Grâce aux moules très rigides, très
précis, et aux conditions de remplissage, les tolérances des
cotes sont très serrées. D'autre part, il n'y a pas de poteyage
permanent sur les parties moulantes comme en coulée en coquille et la
pièce est la réplique exacte de l'empreinte, au retrait
linéaire près.
Très bon état de surface Il est variable selon
le degré de finition du moule, mais il faut noter qu'après un
grand nombre d'injections, les surfaces des empreintes sont
légèrement craquelées et les micro criques superficielles
du moule se retrouvent en relief sur la pièce. Cela n'affecte en rien sa
résistance, mais l'état de surface est moins bon avec des
empreintes un peu usagées. Suppression de certains usinages Il est
possible d'obtenir directement la forme souhaitée dans les
tolérances fonctionnelles requises, en particulier les trous de passage
d'éléments de fixation (vis, etc.).
Chapitre II : Procédés de mise en forme
des métaux

28
Et les avant-trous qui seront ensuite taraudés
directement à l'usinage. On peut aussi insérer au moulage des
filetages tout prêts (helicoils ).
3.2 Obtention de pièces
légères
La pièce doit être dessinée en
évitant les masses inutiles qui risquent d'être retassées.
Les épaisseurs des parois peuvent être minimales en fonction des
caractéristiques mécaniques nécessaires.
3.3 Mise au mille très faible
Elle est de l'ordre de 1,3 au maximum, grâce à
l'absence de masselottes. Seuls quelques dégorgeoirs sont
nécessaires pour rassembler, à l'opposé des attaques
d'injection, le premier métal ayant traversé toute l'empreinte et
risquant d'être un peu oxydé.
3.4 Bonnes caractéristiques
mécaniques
Il faut toutefois noter que la texture d'une pièce
coulée sous pression est très particulière. En effet, le
métal injecté à haute pression dans l'empreinte se
pulvérise littéralement avant d'être comprimé et
solidifié le long des parois et ensuite dans l'épaisseur des
toiles.
L'air du moule est emprisonné dans le métal et
celui-ci présente des microporosités dans la masse des parois,
alors que l'extérieur de celles-ci présente une structure plus
fine et plus compacte favorable à la tenue en fatigue.
4 Systèmes d'injection
Il existe deux systèmes d'injection du métal
liquide dans l'empreinte, le système à
chambre chaude et le système à chambre
froide.
4.1 Système à chambre chaude
Ces dispositif, appelé aussi col de cygne (gooseneck),
comprend un four à creuset, de maintien ou de fusion du métal
liquide, dans lequel est immergé le système d'injection. Celui-ci
est constitué d'un cylindre d'injection en col de cygne (en acier
réfractaire) qui vient s'appliquer contre le trou d'injection du moule.
C'est le système le plus simple, presque idéal. Il réalise
la coulée automatique, le métal est toujours à bonne
température avec beaucoup moins de risque de présence d'oxydes
dans le métal coulé. Malheureusement les alliages d'aluminium,
qui dissolvent le fer à haute température, ne peuvent être
injectés par ce dispositif. Par contre, les alliages de zinc
(température de coulée 420°C) et de magnésium
(température de coulée 650°C) sans action sur les alliages
de fer sont injectés sur ce type de machines.
Les pressions d'injection sont comprises entre 5 et 30 MPa.
Grâce à la simplicité de ce système, les cadences
peuvent être très élevées.
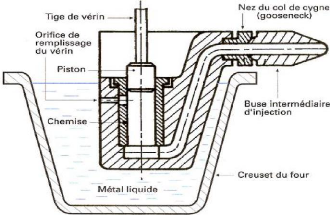
Chapitre II : Procédés de mise en forme
des métaux

29
Figure 16:Système à chambre
chaude
4.2 Système à chambre froide
Dans ce système, l'injection dans le moule se fait
à l'aide d'un vérin horizontal, muni d'un piston en acier au
chrome-molybdène coulissant dans un cylindre appelé conteneur et
qui s'applique sur l'orifice d'injection du moule. Le conteneur possède
un orifice de remplissage par lequel on verse le métal liquide,
manuellement à la louche ou, plus fréquemment, à l'aide
d'un système de coulée mécanisée et automatique
(petite poche verseuse, poche à quenouille, etc.).
Il existe également des machines à axe vertical
mais elles sont très peu utilisées. Le système d'injection
est plus complexe, et elles ont tendance à disparaître. Les
pressions d'injection utilisées dans les dispositifs à chambre
froide peuvent atteindre des valeurs élevées, de 25 à 200
MPa, pouvant dans certains cas atteindre 350 MPa. La manutention et la
coulée du métal sont plus difficiles et le système impose
de le doser soigneusement avant coulée dans le conteneur.
Différents systèmes de programmation existent
pour régler la vitesse de déplacement du piston, vitesse rapide
d'abord, puis vitesse lente et enfin effort maximal de compactage du
métal liquide.
Il existe également des systèmes comprenant un
petit piston au centre du piston principal, qui vient parachever l'effort de
compactage final. Tous ces systèmes visent à améliorer le
remplissage du moule et la pression finale sur le métal liquide pour
améliorer les qualités de la pièce.
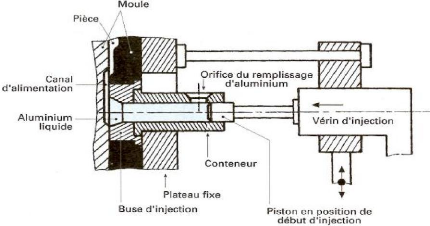
Chapitre II : Procédés de mise en forme
des métaux

30
Figure 17:Système à chambre
froide
5 Les machines utilisée
5.1 Machine à chambre chaude
Elles sont équipées du système
d'injection décrit précédemment, utilisable seulement pour
des alliages d'étain, de plomb ou de zinc (Zamaks). Le système
d'injection à chambre chaude permet des cadences élevées,
50 à 720 injections/h généralement, mais certaines
machines spéciales peuvent atteindre des cadences beaucoup plus
élevées, 2 000 à 5 000 injections/h pour certaines petites
pièces. Pour ces dernières fabrications, les machines restent de
taille moyenne et leurs cycles sont, le plus souvent, entièrement
automatisés.
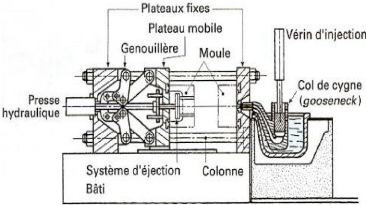
Figure 18:Machine à chambre
chaude
Chapitre II : Procédés de mise en forme
des métaux

31
5.2 Machines à chambre froide
Elles sont équipées d'un système
d'injection comprenant un conteneur dans lequel circule le piston injectant
l'alliage liquide dans le moule. Le four de maintien est installé
à côté de la machine.
Il existe deux types de machines à chambre froide :
-- les machines horizontales ;
-- les machines verticales.
Les machines horizontales sont
universellement répandues dans toutes les fonderies, leurs forces de
fermeture s'échelonnent de 0,5 à 30 MN et plus afin de pouvoir
répondre à la demande du marché de pièces en
aluminium coulées sous pression de plus en plus importante, comme par
exemple des carters-cylindres pour moteurs d'automobile,
4 cylindres (12 kg) ou V 6 (16 kg). Pour cette dernière
pièce par exemple, les moules pèsent plus de 25 t, la machine
à une force de fermeture de 30 MN ( 3 000 Tf), une cadence 8 à 10
pièces/h. Ces énormes machines ont des plateaux de 3 m × 3
m, une longueur de plus de
10 m et représentent un investissement important ne
pouvant s'amortir que sur des grandes séries. Les cadences de production
vont de (10 à 20) pièces/h à 50 pièces/h en moyenne
et jusqu'à 200 pièces/h environ pour les machines les plus
petites.
Pour faciliter les manutentions, diminuer la
pénibilité et améliorer la productivité, les
machines moyennes et surtout les plus importantes ont été
entièrement automatisées.
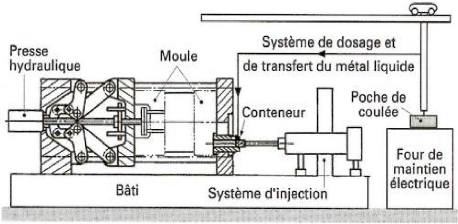
Figure 19:Les machines horizontales
Chapitre II : Procédés de mise en forme
des métaux

32
Les cadences sont exprimées en cadences
instantanées, rendement mécanique machine-moule non compris.
Ces machines ont été équipées d'un
ou plusieurs robots qui forment avec leur four de maintien de véritables
ensembles autonomes entièrement automatiques, depuis la coulée du
métal jusqu'aux opérations d'extraction de la pièce,
poteyage des empreintes, refroidissement de la pièce dans un bac
à eau et pré ébavurage (culot d'injection, grosses
bavures). L'opérateur surveille le fonctionnement de l'ensemble de
l'installation et contrôle la qualité des pièces à
la sortie, avant livraison à l'atelier de parachèvement. Ces
ensembles complètement automatisés ont permis d'améliorer
très sensiblement les conditions de travail, la productivité et
également la qualité des pièces.
Les machines verticales utilisent pour
l'injection un conteneur disposé verticalement, alimenté en
métal liquide à la louche de coulée, ou par
dépression et aspiration par un tube dans le four de maintien. Il est
nécessaire que l'injection se fasse au centre du moule, ce qui limite
leurs applications. Par ailleurs, l'ensemble d'injection n'est pas très
accessible et ce type de machine ne s'est pas développé à
cause des inconvénients liés à son principe.
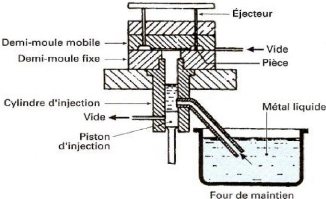
Figure 20:Les machines verticales
Chapitre II : Procédés de mise en forme
des métaux

33
6 Les cycles de coulée
6.1 Machines à chambre froide horizontale
Les phases du procédé sont les suivantes :
- verse du métal dans un cylindre horizontal appelé
conteneur ;
- 1re phase : le piston d'injection pousse assez
lentement le métal jusqu'à l'entrée de l'empreinte,
appelé attaque ;
- 2eme phase : remplissage du moule, la vitesse du
piston et du métal est élevée et peut varier de 20 m/s
à 50 m/s à l'attaque et fortement, notamment avec l'emploi des
machines à boucle fermée ;
- 3eme phase : une application rapide d'une
surpression sur le métal en cours de solidification permet d'augmenter
la compacité de la pièce.
Les pressions exercées sur le métal peuvent varier
entre 50 et 100 MPa.
Compte tenu de la grande vitesse d'écoulement du
métal lors du remplissage, une partie de l'air contenu dans le conteneur
et dans l'empreinte se retrouve dans les pièces sous forme de petites
bulles ou soufflures.
On peut remédier en grande partie à cet
inconvénient en concevant correctement le système de remplissage
et en utilisant des technologies d'assistance par le vide qui consistent
à aspirer l'air et les gaz pendant la phase de remplissage. La pression
résiduelle varie selon les systèmes entre 60 et 100 MPa.
Les machines sont caractérisées par la force de
fermeture des plateaux fixe et mobile sur lesquels est fixé le moule. La
gamme des puissances s'échelonne entre 2 500 et 45 000 kN, plus
couramment exprimée en tonnes, 250 à 4 500 t.
La technologie des machines a fait de gros progrès au
niveau du groupe d'injection. On distingue deux principales catégories
de machines.
6.2 Machines anciennes à trois phases
(Plus vendues aujourd'hui mais encore nombreuses dans le parc
industriel) :
- 1re phase : le mouvement du piston a lieu
à vitesse lente constante (0,30 à 1 m/s) ou
accélérée.
- 2eme phase : elle correspond au remplissage de
l'empreinte et la vitesse du piston peut varier entre 1,5 et 8 m/s. Les
mouvements du piston d'injection sont pilotés du coté primaire du
piston moteur. Le freinage du piston en fin de phase évite le coup de
bélier et permet, pour des pièces fines injectées avec des
vitesses de piston élevées, de ne pas provoquer de bavures au
plan de joint.
- 3eme phase : c'est la phase de compaction
réalisée par un multiplicateur de pression (majoritairement la
pression est régulée par une vanne pointeau). Le
déclenchement de la monté e en pression peut, si
nécessaire, être retardé. En règle
générale, on cherche à appliquer une surpression sur la
pastille de coulée, le plus vite possible.
Chapitre II : Procédés de mise en forme
des métaux
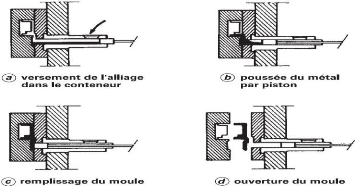

34
Figure 21:Machines anciennes à trois
phases
6.3 Machines modernes à boucle fermée
Elles ne présentent plus que deux phases cadres :
- remplissage qui comporte, si nécessaire, de nombreux
changements de vitesse du piston pour conserver en chaque point la vitesse de
front de métal voulue, malgré les changements de section de
l'empreinte ;
- compaction, pendant laquelle le pilotage du piston ne se
fait plus en vitesse mais en pression. Tous les mouvements du piston
d'injection sont pilotés au moyen d'une vanne de haute précision,
disposée en avant du piston moteur coté injection.
Ce système permet non seulement d'obtenir des vitesses
constantes ou variables, mais aussi de ralentir le mouvement du piston pendant
sa course et de le freiner très rapidement en fin de remplissage, ce qui
élimine le coup de bélier rencontré sur les machines
à trois phases non munies de dispositifs spéciaux.
Ces machines sont bien adaptées à la
coulée de métal semi-solide (à viscosité
élevée et intrinsèquement variable) et également au
squeeze casting horizontal. On peut faire varier la vitesse et la pression en
plusieurs points du cycle de ces machines (jusqu'à 16 points sur
certaines d'entre elles). Il est possible d'appliquer des retards entre chaque
commutation et de programmer les rampes de montée en pression.
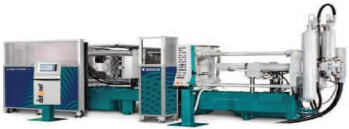
Figure 22:Machines modernes à boucle
fermée
Chapitre II : Procédés de mise en forme
des métaux

35
7 Moyens de remplissage du conteneur en coulée sous
pression
La coulée manuelle n'est pratiquement plus
utilisée sauf pour la coulée de petites pièces. A ce mode,
on a substitue divers dispositifs de transfert automatiques de l'alliage qui
prélèvent et dosent le métal liquide.
Louche automatique
Il existe de nombreux types de louches, l'objectif
étant de prélever le métal au-dessous du niveau du bain
pour éviter d'introduire des peaux d'oxydes et de transférer le
métal rapidement vers le conteneur. La cinématique de ces
dispositifs est programmable selon les besoins et peut être
indexée de manière optimale dans le cycle de la machine.
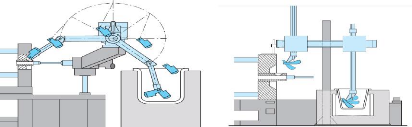
Figure 23:Louches automatique
Fours doseurs
Le transport du métal liquide est réalisé
selon le principe de la coulée basse pression. L'alliage est contenu
dans un four étanche dans lequel on applique une pression d'air
comprimé, de manière à remplir à chaque injection
le conteneur de la quantité de métal voulue
généralement via une goulotte.
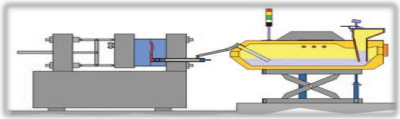
Figure 24:Fours doseurs
Chapitre II : Procédés de mise en forme
des métaux

36
Remplissage du conteneur par mise en dépression du
moule
Le principe est décrit à la figure 25, avec une
machine sous pression équipée du procédé Vacural
développé par Muller Weingarten. Il consiste à aspirer le
métal liquide en créant une dépression dans l'ensemble
empreinte/conteneur. Le conteneur est raccordé au four de maintien par
un tube plongeur.
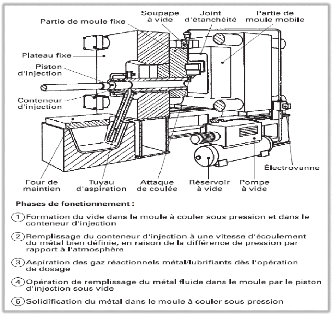
Figure 25:Remplissage du conteneur par mise en
dépression du moule
V. Conclusion
Les procédés de mise en forme des métaux
cités précédemment, nous permettent l'obtention des
produits finis ou semis finis avec une cadence journalière
importante.
De plus, pour changer la forme d'un produit, il suffit de
changer le moule, ce qui permet aux utilisateurs de cette matière
d'obtenir de nouveaux produits avec de nouvelles formes.
Le procédé de moulage sous pression est souvent
utilisé dans l'industrie des alliages non ferreux car il permet de
réaliser en une opération, à des cadences
élevées, des pièces complexes très précises
et parfaitement finies.
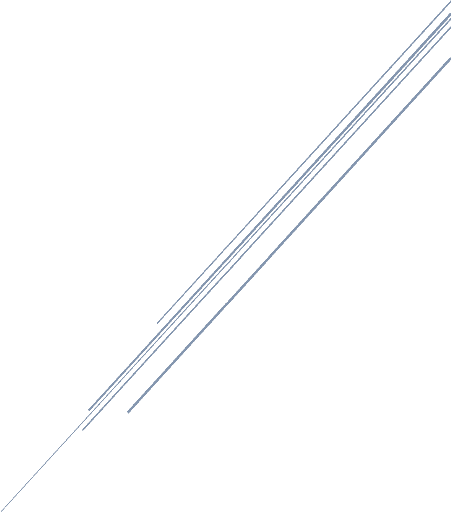
Chapitre III
Choix du moule et procédé
Chapitre III : Choix du moule et procédé

37
I. Introduction
Un moule en termes de moulage sous pression, est un outil
mécanique de très grande précision qui permet de rejouer
un produit sans fin, considéré comme des limites de fabrication,
parmi le processus de consolidation du même métal fondu.
Le moule est alors le premier acteur dans le domaine de la
coulée sous pression.
Sa conception fait appel à des méthodes
complexes et bien spécifiques, que nous allons aborder dans ce
chapitre.
III. Conception d'un moule à injection sous
pression d'aluminium Un moule peut être défini par
les paramètres suivants :
Son architecture ;
Le nombre et disposition d'empreintes ;
Le système d'alimentation ;
La matière à injecter ;
L'éjection des pièces ;
La machine ;
Dégazage du moule ;
Fixation de moule ;
Système de refroidissement ;
La durée de vie (le choix des matériaux...).
1 Architecteurs de moule
Dans l'impossibilité de décrire tous les types
de moules dont la complexité peut être extrême, il a paru
plus utile de montrer sur les figures suivantes les plans schématiques
de deux moules théoriques, l'un pour moulage en chambre chaude, l'autre
pour moulage en chambre froide, comportant la plupart des
éléments constitutifs des moules de fonderie sous pression.
Ces plans établissent la terminologie des divers
organes dont la description et le fonctionnement sont détaillés
ultérieurement dans ce même chapitre.
Chapitre III : Choix du moule et procédé
1.1 Schéma et terminologie
|
1. Bloc fixe
2. Bloc mobile
3. Goujons
4. Partie rapportée
5. Noyau fixe
6. Rallonge
7. Lardon de positionnement
8. Tiroirs
9. Cale de sécurité
10. Crémaillère
11. Pignons
12. Broche
13. Broche de verrouillage
14. Noyau détachable
15. Buse d'injection refroidie
16. Economiseur refroidi
17. Galette 17. Jet
19. Attaque de coulée
20. Pièce
21. Sommier
22. Entretoise
24. Guide d'éjection à
crémaillère
25. Repos d'éjection
26. Plaque d'éjection
27. Contre-plaque d'éjection
28. Ejecteurs
|

38
Figure 26:Moule pour moulage en chambre
froide
|
1. Bloc fixe
2. Bloc mobile
3. Goujons
4. Tiroir
5. Arrêt de positionnement du
tiroir
6. Doigt de démoulage
7. Cale de sécurité
8. Noyau éclipsable
9. Noyau fixe
10. Noyau porte Insert
11. Broche fixe
12. Buse refroidie
13. diffuseurs refroidis
14. carotte
15. attaques
16. pièce
17. pièce
18. insertion
19. sommier
20. entretoise
21. repos d'éjection
22. guide ou vérin
d'éjection
23. butées d'éjection
24 Plaque de fixation
25 Plaque d'éjection
26 contre-plaque d'éjection
27 éjecteurs
28 Ejecteur tubulaire
29 Rappels d'éjection
|
Figure 27: Moule pour moulage en chambre
chaude
Chapitre III : Choix du moule et procédé

39
1.2 Eléments standards
Bloc fixe et bloc mobile (portes
empreintes):les blocs fixes et les blocs mobiles constituent avec entretoise et
sommier, l'ossature du moule .ils supportant les efforts à la fermeture
de la machine et l'injection de l'alliage.
Colonnes de guidage (goujons) : Permet de
guider la partie mobile sur la partie fixe pour aligner parfaitement
l'empreinte.
La buse d'injection: permet le passage de la
matière du fourreau vers l'empreinte. Bague de guidage:
Permet le guidage des colonnes de guidages. Ejecteurs :
Permet d'éjecter la pièce quand le moule est ouvert.
Entretoises (baguettes supports ou bien Tasseaux
d'éjection) : Permet d'obtenir une course optimum de la
batterie d'éjection.
Batterie d'éjection: Permet la
translation des éjecteurs. Est composé de la plaque porte
éjecteurs et de la contre plaque d'éjection.
Vis de fixations: Permet la fixation des
différentes parties de moule.
Repos d'éjection : limite le recul de la
plaque d'éjection lorsque le moule est fermé.
Guide d'éjection : permet le mouvement
de la batterie d'éjection à l'aide d'un système à
crémaillère ou vérins.
2 Le nombre et disposition d'empreintes
2.1 Nombre d'empreintes
La dimension de l'empreinte doit tenir compte de retrait
volumique de la matière à mouler.
Le nombre d'empreinte dépend du volume de la
pièce. Si la pièce est volumineuse, on se limite à une
seule empreinte et si elle est petite, on réalise plusieurs empreintes,
selon les possibilités pour produire des grandes quantités de
pièces dans un temps réduit :
Il faut aussi prendre en considération les critères
suivants :
Critères économiques :
y' Délais de livraison ;
y' Le coût.
Critère techniques (la machine et la quantité
exigée) :
y' Machine à disposition (ex : distance entre colonne ;
y' Quantité exigée du produit ; y' Le volume de la
pièce ; y' La forme de la pièce.
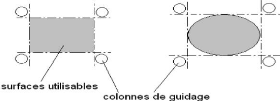
Chapitre III : Choix du moule et procédé

40
Figure 28:Nombre d'empreintes en fonction de
critères techniques. On peut calculer le nombre
d'empreintes par la forme suivante :
2.2 Disposition des empreintes
Répartition en étoiles
|
Avantage :
-Même longueur d'écoulement vers les empreintes.
-Disposition favorable pour démoulage Inconvénients : -Le nombre
d'empreinte à placer est limité.
|
|
Répartition
|
en ligne
|
|
Avantage :
-Placement d'un nombre élevé d'empreintes par
rapport à la répartition en étoile.
Les inconvénients :
-Déférentes longueur d'écoulement
jusqu'aux empreintes.
|
|
|
|
|
Répartition
|
|
symétrique
|
|
|
Avantage :
-Même longueur d'écoulement jusqu'aux empreintes.
Les inconvénients :
-canal trop long, beaucoup de pertes de matière,
refroidissement trop rapide de la pièce.
|
|
|
|
|
|
|
|
|
|
|
|
|
|
Tableau 4:Les différents modes de la
disposition des empreintes
Chapitre III : Choix du moule et procédé

41
3 Le système d'alimentation du moule
3.1 Généralités
Les trois fonctions principales d'un système
d'alimentation sont les suivent :
y' Amener le métal liquide dans l'empreinte ;
y' Faciliter l'évacuation aussi complète que
possible de l'air et des gaz contenus
dans cette empreinte à fin d'en assurer le remplissage
; y' Assurer la transmission des pressions nécessaire pour l'obtention
d'une bonne
compacité.
Le système d'alimentation comprend :
- La pastille (chambre froide) ou la carotte (chambre chaude)
(suivent le type de la machine) ;
- Les canaux d'alimentation conduisant le métal jusqu'
a l'empreinte dont ils sont séparés par l'attaque ;
- L'attaque qui assure le débit de remplissage ;
- Le talon de lavage (trop plain) destinés à
drainer le métal le plus souillé en dehors de la pièce
;
- Le tirage d'air sert à évacue l'air et les gaz
en dehors de l'empreinte.
-
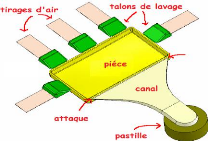
Figure 29:Composition d'un système
d'alimentation.
3.2 Technique d'alimentation
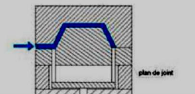
L'alimentation du moule en matière à l'état
visqueux est assurée de deux façons :
a) Injection dans le plan de joint :
Le plus utilisé dans la machine a chambre froid.
[9]
Avantage :
Canaux d'alimentation courte ;
Diminution de perte d'énergie ;
Permet d'avoir des temps de remplissage très court ;
Figure 30:Injection dans le plan de
joint.
Chapitre III : Choix du moule et procédé
Inconvénients :
La pression d'injection entraine des déformations sur
les colonnes de la presse. La fermeture du moule est parfois
incomplète.
b) Injection perpendiculaire au plan de joint
:
Mode peu très utilisé.
Inconvénients :
Canaux d'alimentation assez longs.
Prévoir une extraction de la pastille.
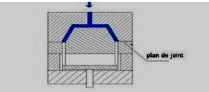

42
Figure 31: Injection perpendiculaire au plan de
joint.
3.3 Point d'injection
La bonne réalisation d'une pièce est
conditionnée par un bon écoulement de la matière, ainsi
que la bonne fermeture de l'outillage.
L'équilibre des forces dans un outil doit être
réalisé avec un soin et l'injection de la matière doit
être placée au point d'équilibre. L'idéal est le
centre de gravité l'empreinte.
Dans le cas d'un moule dont le point d'injection ne peut pas
être placé au centre de gravité, un équilibrage des
efforts doit être réalisé.
Pour faire, un effort complémentaire est
réalisé à l'aide de cales ou tasseaux. La
résultante des deux efforts passe par l'axe du plateau.
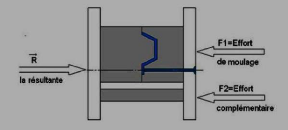
Figure 32:Équilibrage des efforts
Chapitre III : Choix du moule et procédé

43
3.4 Remplissage des empreintes
Les théories concernant le mode de remplissage de
l'empreinte du moule ont été énoncées par Brant et
Frommer, ces deux chercheurs on fait des études et formulé des
théories on réalisant des modèles expérimentaux de
support à la théorie. [8]
? Remplissage par jet
Le remplissage se fait sous l'action d'un jet de métal
liquide qui on partant de l'attaque de coulée, traverserait toutes
l'empreinte et s'accumulait dans la partie opposée en remplissant
progressivement celle-ci, la dernière partie à être remplie
serait celle proche de l'attaque de coulée.
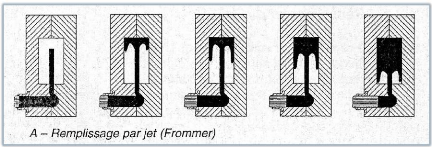
Figure 33: Remplissage par jet
? Remplissage par accumulation
Le remplissage se produirait par accumulation, sous l'action
du métal liquide qui en entrant par l'attaque de coulée
pousserait le métal, jusqu'à rejoindre l'extrémité
opposée de celle-ci. La dernière partie à être
remplie est la plus éloignée de l'attaque de coulée.
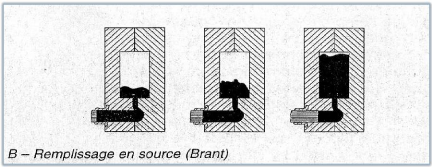
Figure 34: Remplissage par accumulation
Chapitre III : Choix du moule et procédé

44
3.5 Les canaux et les attaques
i. Le canal :
Le canal d'alimentation est considéré comme une
conduite hydraulique et un échangeur de chaleur.
Donc la section circulaire qui répond mieux à
ces deux conditions, sa réalisation est difficile car il
nécessite une gravure dans les deux partie de moule et ne
présente pas de dépouille ou plan de joint.
On lui préfère donc la section
trapézoïdale, elle ne doit pas être trop aplatie pour
n'offrir qu'une surface minimale a l'échange de chaleur et avoir une
dépouille latérale suffisante pour ne causer aucune
difficulté ou démoulage, les proportions indiquer sur la figure
sont satisfaisantes.[9]
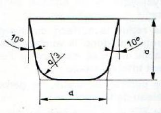
Figure 35 : Proportions dimensionnelle de
canal
Cette section doit être maintenue jusqu'aux abords de la
pièce ; on doit éviter particulièrement tout croissement
de section entrainant une détente dans l'écoulement.
Pour obtenir la longueur et l'épaisseur
nécessaire à l'attaque on doit élargit progressivement le
canal en réduisant son épaisseur (fig.36 a).
Dans le cas où le canal est scindé en plusieurs
canaux secondaires, leurs sections seront telles qu'elles ne produisent pas de
détente (fig.36 c, b). [9]
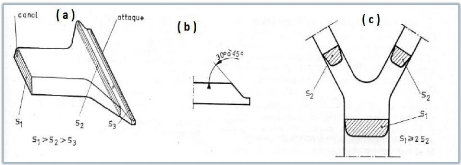
Figure 36: Epaisseur et section des attaques par rapport
au canal.

45
Chapitre III : Choix du moule et
procédé
ii. Les attaques de coulée :
a. Attaques directes
C'est le tracé le plus simple, souvent le meilleur en
fonderie d'aluminium. De l'axe d'injection, le canal d'alimentation suit un
tracer sensiblement rectiligne vers la pièce. Dans ce cas la perte
d'énergie est réduite au minimum.
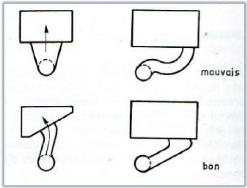
Figure 37:Attaques directes
b. Attaque en retour
Dans cette attaque le canal d'alimentation principal se
termine en cul de sac sur une profondeur suffisante pour que le front du
métal injecté s'y rassemble et y demeure, et le canal secondaire
forme avec lui un angle sensiblement inférieur à
900.
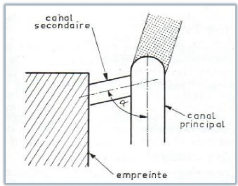
Figure 38:Attaques en retour
Ce système est fréquemment utilisé dans
les moules à empreintes multiples, en vue de favoriser le remplissage
simultané de toutes les empreintes.
Chapitre III : Choix du moule et procédé

46
c. Attaques autour d'un noyau
L'alimentation des pièces cylindriques par une attaque
située sur la surface latérale est difficile. Presque
inévitablement, il y a érosion de a broche ou du noyau central.
On a parfois recours à des attaques en queue de poisson ».
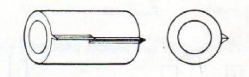
Figure 39:Attaques en queue de poisson
La solution la plus classique et la plus satisfaisante est
l'attaque autour du noyau. Cette disposition épargne la broche dans sa
partie moulante et assure un remplissage bien dirigé à condition
de prévoir une partie conique (5° minimum), au niveau du canal
torique, cette disposition n'entraîne pas un supplément excessif
de frettage» du moulage sur la broche.
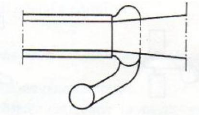
Figure 40:Attaque autour du noyau
d. Attaques multiples
Les inconvénients de ce type d'attaque pour la
coulée des alliages oxydables ont été
évoqués.
Lorsqu'il est utilisé, il est bon de veiller à
ce que toutes les attaques aient la même section, afin que toutes les
zones intéressées par chacune d'elles bénéficient
simultanément de la pression finale. Pourtant dans le cas de
pièces compliquées, on spécule parfois sur la
différence de section des attaques pour équilibrer le remplissage
des différentes parties à nourrir.
e. Attaques pour moule a plusieurs empreintes
:
Des nécessités de matériel (machines
surpuissantes) ou économiques (prix d'outillages) peuvent conduire les
fondeurs à mettre plusieurs empreintes dans le même moule,
l'emploi des attaques précédentes est toujours valable, mais
chacune est l'aboutissement d'un canal secondaire.
Chapitre III : Choix du moule et procédé

47
La répartition des canaux est fonction du type de machine
employé.
En chambre chaude, la position de la pièce par rapport
à l'axe d'injection est indifférente et, à partir de la
carotte, il est possible de prévoir des canaux d'alimentation dans
toutes les directions.
On veille dans tous les cas à assurer la symétrie
d'alimentation pour toutes les pièces Les mêmes dispositions
restent valables en chambre froide verticale.
En chambre froide horizontale, par contre, il est obligatoire que
les canaux issus de la pastille «partent vers le haut, afin que le
métal ne s'écoule pas dans les empreintes avant le
déclenchement de l'injection.
Il est néanmoins possible de placer des empreintes plus
bas que l'axe d'injection ou bien utiliser des moules a trois plaques dans ce
cas les bras de coulée sont alimentés par une carotte centrale
comme le cas des machine a chambre chaude.
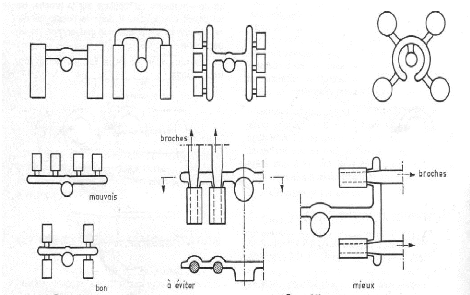
Figure 41:Attaques pour moule a plusieurs
empreintes
f. Attaques centrales
Ce type d'attaque mérite une mention particulière,
car son utilisation conduit dans certains cas à des dispositions
spéciales affectant la machine.
Il concerne particulièrement les pièces qui
présentent un évidement permettant de loger l'attaque ; le
métal dans ces conditions se propage vers la périphérie de
la pièce.
Les avantages d'une attaque centrale sont les suivants:
Chapitre III : Choix du moule et procédé

48
Elle réduit la surface du système d'alimentation,
donc la surface totale de la grappe au plan de joint et l'encombrement total du
moule ;
y' elle centre, au mieux, ce dernier sur le plateau de la machine
;
y' elle réduit le parcours du métal dans la
pièce;
y' elle assure le plus souvent une répartition
satisfaisante du métal dans
y' elle assure, enfin, une évacuation correcte de l'air
à la périphérie de la pièce. de
moteur, poulie à gorge, etc.).
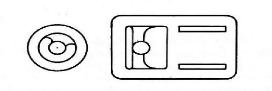
Figure 42:Attaques centrale
4 La matière à injecter
Dans ce point le choix est guidé principalement par les
propriétés de la matière dont :
y' Température de transformation.
y' Coefficient de retrait
y' Temps de refroidissement qui impose le temps de cycle donc
la cadence du moulage.
5 L'éjection des pièces (grappe)
La pièce étant moulée, le moule est
ouvert, la grappe doit être entraînée par le bloc mobile
d'où elle est éjectée.
Dans le cas de moulage en chambre froide, le piston
d'injection accompagne la grappe dans la première partie du mouvement
d'ouverture.
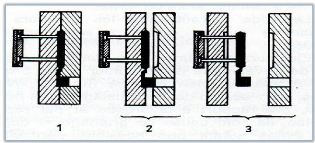
Figure 43:Éjection de la
grappe
Chapitre III : Choix du moule et procédé

49
5.1 Les éjecteurs
5.1.1 Forme
En fonction de la forme de nombre de pièces, des
spécifications du cahier des charges, on choisira un type
d'éjection différent :
· Ejecteur cylindrique ou tubulaire ;
· Ejecteurs à lames ;
· Plaque dévêtisseuse ;
· Soupape d'éjection ;
· Ejection combiné (associé 2 ou 3 formes)
;
· Ejecteur annulaire.
a. Ejecteurs cylindriques
Les tiges d'éjecteurs cylindriques sont les
éléments les plus utilisés pour le démoulage. Ces
éjecteurs doivent être situés judicieusement sur la
pièce et en nombre suffisant, de façon à éjecter la
pièce sans dommage ni déformation.
b. Ejecteurs tubulaires :
Pour certaines pièces à noyau central
cylindrique, l'éjection peut se faire avantageusement à l'aide
d'un éjecteur tubulaire ou annulaire. Il s'agit d'un tube qui coulisse
sur la broche (qui sert de noyau fixe) et vient pousser la pièce sur une
surface plane et circulaire.
c. Ejecteur plaque :
Les pièces à parois minces, déformables
peuvent être éjectées par une plaque de
dévêtissage
d. Ejecteur latéral :
Dans le cas d'une éjection latérale, les
dimensions des éjecteurs doivent être déterminées en
fonction de l'épaisseur de la paroi et de la résistance de la
matière.
e. Ejecteur à lame :
Les lames usinées ou rapportées permettent
d'éjecter des pièces peu épaisses. Les éjecteurs
à lames doivent être guidés pour éviter les risques
de flexion ou de flambage.
5.1.2 Fixation
Les éjecteurs ont une tête ; celle-ci est prise
entre deux plaques appelées plaque et contre plaque
d'éjection.
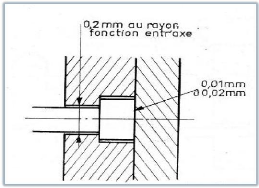
Chapitre III : Choix du moule et procédé

50
Figure 44:Fixation d'un
éjecteur
Le montage est prévu avec un jeu minimal suivant l'axe
de l'éjecteur; par contre, un jeu important est prévu
latéralement, le guidage de l'éjecteur ne devant être
assuré que dans le bloc, à proximité de l'empreinte, en
raison des dilatations différentes de la plaque d'éjection et du
moule.
5.1.3 Position sur la pièce
Les éjecteurs doivent assurer une éjection
équilibrée» de la pièce. Ils doivent être bien
répartis, placés près des zones de fortes retenues (par
exemple autour des broches).
Ils sont prévus pour éjecter la totalité
de la grappe avec la pièce et son système d'alimentation, Ils
sont en particulier souvent nécessaires sur les talons de lavage
faiblement rattachés à la pièce et sur les jets de
coulée.
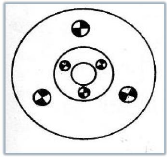
Figure 45:Répartition des éjecteurs
sur la pièce
5.2 Commande de l'éjection
Les plaques d'éjection peuvent être
actionnées manuellement par l'opérateur de la machine, ou par
l'intermédiaire de systèmes mécaniques ou hydrauliques.
a - Crémaillère
Chapitre III : Choix du moule et procédé

51
Le système à crémaillère,
commandé à la main, a l'avantage d'assurer une éjection
dosée» en force et déclenchée au moment voulu par
l'opérateur. On le réserve à des pièces
délicates. Par contre, il nécessite un effort humain à
répéter fréquemment et entraîne un ralentissement de
cadence.
b - Butée
A l'ouverture de la machine, des tiges de butée
arrêtent la plaque d'éjection, le bloc mobile continuant à
se déplacer. Le mouvement relatif entraîne l'éjection. Le
retrait des éjecteurs est obtenu, à la fermeture du moule.
Ce système, simple, est assez brutal, peu favorable
à la planitude du joint et se dérègle dans le temps.
c - Vérin d'éjection
Un vérin, placé au centre du plateau mobile,
assure l'avance et le retrait des plaques d'éjection. Ces mouvements
peuvent être déclenchés au moment désiré par
réglage du programme de cycle.
6 La machine
Lors de la conception d'un moule on doit choisir la machine en
fonction :
? Du volume et de la forme de la pièce.
? Du nombre d'empreintes. ? Du calcul de rentabilité.
? De la précision de la pièce.
7 Dégazage du moule
L'alimentation n'est possible que si l'air de l'empreinte peut
être évacué. Une partie de l'air contenu dans l'empreinte
est évacuée par les jeux autour des éjecteurs ; ces jeux
sont faibles, mais le mouvement des éjecteurs les maintient toujours
libres, leur évitant d'être obturés par le poteyage et les
infiltrations de métal. L'air peut également sortir par les jeux
autour des broches et noyaux mobiles.
Les noyaux fixes laissent également, sur leur pourtour,
des tirages d'air moins efficaces que les précédents, mais
souvent bien utiles.
Des tirages d'air sont réalisés dans le plan de
joint du moule. Leur emplacement exact est souvent défini par les
premières coulées.
On en place également en bout des culs-de-sac des
canaux d'alimentation (attaque en retour) et sur les talons de lavage les
débouchent à l'extérieur. Si ce n'est pas possible, on
peut les relier à l'extérieur par un trou traversant le moule.
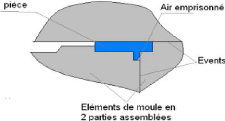
Chapitre III : Choix du moule et procédé

52
Figure 46:Event
8 Fixation du moule
Le maintien en position du moule sur les plaques fixe et
mobile est assuré par vis ou brides.
8.1 Fixation par vis Avantage :
Fixation très simple et fiable, il n'y a pas de besoin
de cales (la plaque du moule faisant office de cales. Bonne
accessibilité pour le serrage.
Inconvénients :
Les trous taraudés doivent avoir des entraxes
identiques sur tous les plateaux de presses pour permettre
l'interchangeabilité des moules.
8.2 Bridage
C'est aussi le procède qui demande le plus de soin et
d'attention lors du montage. En effet, il faut que la cale qui sert d'appui
pour la bride soit de hauteur équivalente à la plaque du moule ou
très légèrement supérieure. Sinon le bridage n'est
pas solide et les vis risquent de se tordre. Il faut que la vis qui sert
à bloquer la bride soit le plus près possible de l'objet à
brider.
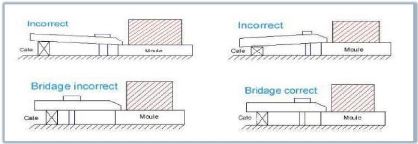
Figure 47:Procédé de Bridage (bride
plate à serrage)
Chapitre III : Choix du moule et
procédé
9 Circuits de refroidissement
L'échange thermique entre l'aluminium injecté et
le moule est un facteur décisif dans les performances économiques
d'un moule d'injection. La chaleur doit être extraite du matériau
jusqu'à ce qu'il ait atteint l'état stable recherché pour
pouvoir être démoulé. Le temps total de refroidissement
intègre la séquence de maintien en pression, même si
celle-ci est décomptée séparément, puisque le
matériau injecté échange de l'énergie avec le moule
dès qu'il est en contact avec la surface moulante. L'énergie
calorifique qu'il faut extraire dépend :
y' Du l'alliage (température, masse, chaleur
spécifique). y' De la température de démoulage.
10 Choix des matériaux
Le tableau suivant regroupe les différents
matériaux constitutifs du moule
MATERIAUX
|
OBSERVATION
|
EMPLOIS
|
X37CrMoV5-1
|
|
|
Acier de travail à chaud haute résistance à
la chaleur et une bonne ténacité
|
40CrMnMoS8-6
|
|
|
Acier traité pour travail à froid et le
moulage.
|
C45U
|
|
|
Acier a outils non allié
|
X40CrMoV5-1
|
|
|
Acier de travail à chaud haute résistance à
la chaleur
|
Empreintes fixe et mobile. Colonne de
guidage.
Insert.
Plaque pour attaque de coulée mobile et
fixe.
Porte empreinte mobile et fixe
Plaque et contre plaque éjectrice.
Goupille et éjecteurs

53
Tableau 5 : différents matériaux
constitutifs du moule
III. Conclusion
Pour une bonne conception d'un moule d'injection aluminium, on
doit suivre toutes les étapes nécessaires car le meilleur choix
des paramètres de conception nous garantit un produit fini et de
qualité.
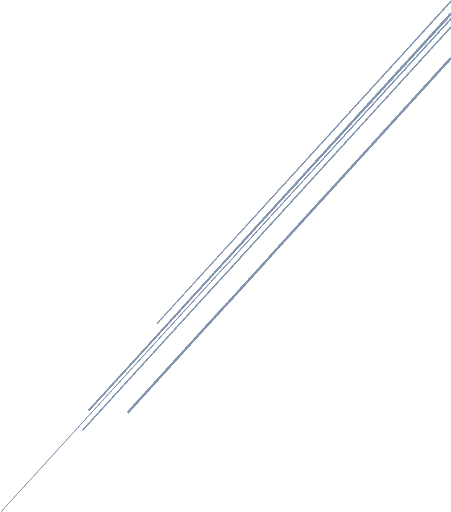
Chapitre IV
Conception et calcul
Présentation du sujet
? Cahier de charges :
L'entreprise Electro-industrie se voit dans l'obligation de
fabriquer certain produits au sien de ses ateliers afin d'éviter leur
importation et pour améliorer son produit, ainsi garder sa place sur le
marché.
Parmi ces pièces prises, dans l'initiative de la
fabrication dans les ateliers de l'entreprise, un flasque-bride d'un moteur
électrique B5-A106/107-2.
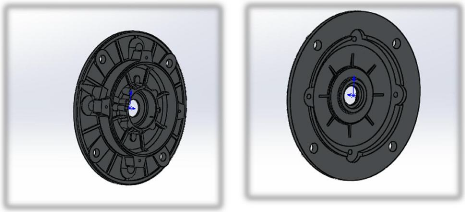
? Travail demandé :
Le travail consiste en étude et conception d'un moule
à injection d'aluminium pour un flasque-bride d'un moteur
électrique B5-A106/107-2
1. Conception du moule sur logiciel SolidWorks :
Consiste à concevoir les empreintes de la pièce
et toutes les autres pièces constituant le moule.
2. Calcul et vérification dimensionnel :
Ce sont des calculs qui nous permettent de choisir la machine
adéquate et de vérifier la résistance des
éléments constituants le moule aux différents efforts.
? Dessin de définition : planche 1/1
Chapitre IV : Conception et calcul

55
I. Introduction
L'objet de ce présent chapitre est la conception de la
pièce, déduire les deux empreintes (fixe et mobile), et les
éléments du moule, par la suite, la détermination des
différents facteurs du choix de la machine, le calcul de
résistance des différents composants du moule au matage dû
à la force de fermeture de la machine et aussi la vérification
des colonnes de guidage et les vis CHC au cisaillement.
III. Introduction à la conception
assistée par ordinateur (CAO) L'introduction de l'outil
informatique dans les différentes branches de l'industrie est d'une aide
très précieuse. En effet, la conception assistée par
ordinateur (CAO) permet, grâce à des logiciels
spécialisés, la conception des pièces qui ont des formes
très complexes. Dans le domaine de moulage, par exemple, l'utilisation
de cette technique facilite la conception des empreintes des moules et leurs
mise en plan.
La technique utilisée permet à l'homme et
à la machine d'être liés pour résoudre un
problème en utilisant au mieux les compétences de chacun.
L'historique de la CAO nous permet d'affirmer que ses débuts remontent
aux années 70. Il a été, dès lors, possible de
mettre en place des logiciels spécifiques destinés à
résoudre le problème des surfaces complexes pour l'industrie
aéronautique et automobile.
2-1. Définition de la CAO:
La conception assistée par ordinateur (CAO) comprend
l'ensemble des logiciels et des techniques de modélisation
géométrique permettant de concevoir, et de tester virtuellement
des produits.
Lorsqu'un système est affecté d'un nombre trop
grand de paramètres, il devient difficile de tout contrôler. La
CAO permet de concevoir des systèmes dont la complexité
dépasse la capacité de l'être humain, et d'apprécier
globalement le comportement de l'objet créé avant même que
celui-ci n'existe. En CAO, on ne dessine pas, on construit virtuellement un
objet capable de réagir dans son espace réel selon des lois
régies par le logiciel. Le résultat, appelé maquette
numérique qui constitue alors un véritable prototype
évolutif.
Durant notre conception nous avons utilisé le logiciel
de conception appelé «SolidWorks».
2-2. Domaines de la CAO :
Le développement rapide de la CAO a permis à
presque tous les domaines de l'industrie d'en profiter des avantages que
présente cette technique, parmi ces domaines on cite:
Fabrication mécanique : conception des moules.
Chapitre IV : Conception et calcul

56
Domaine de la mécanique classique : simulation et
calcul des matériaux, résistance des matériaux, vibration
et acoustique.
Aéronautique : conception des coques d'avions, calculs
d'écoulement et aérodynamique.
Electronique et micro-électronique : assemblage des
composants (résistances, capacités, éléments de
logique...) et leur simulation.
Génie civil : calcul des structures. Automobiles et
transports divers.
La biomécanique : conception d'organes artificiels,
prothèses...
2-3. Avantages de la CAO :
La CAO possède un nombre important d'avantages qui
contribuent énormément à l'amélioration de
l'industrie en général, de ce fait, elle est devenue un
élément essentiel. Parmi ces avantages on note :
Gain de temps et productivité pour les équipes
de conception avec l'utilisation de la modélisation solide.
Amélioration considérable de la qualité
des produits du fait que la CAO permet de contrôler leurs qualités
avant même leurs productions.
Diversification de la production, par la possibilité de
conception des formes complexes.
Importance des échanges entre concepteurs et
réalisateurs, du fait d'une définition beaucoup plus
complète en CAO.
2-4. Application :
Durant la conception des pièces, nous avons
utilisé les commandes du logiciel SolidWorks tel que : Esquisses,
fonctions et surfaces.
Premièrement, nous avons conçu la pièce
(flasque-bride), puis en utilisant la commande «surface cousue » on a
déduit les empreintes (fixe et mobile).
Deuxièmement, nous avons conçu le reste des
pièces constituant le moule en trois dimensions (3D) de manière
à assurer les fonctions objectives et les normes de construction.
Ensuite, l'utilisation de la commande assemblages nous a
permis d'effectuer le montage de toutes les pièces en formant un moule
complet et la détection des interférences qui peuvent exister
entre les pièces assemblées.
Finalement, la commande « Solidworksanimator » nous
a permis d'élaboré une animation 3D qui rend notre conception
très claire malgré sa complexité, et donne aussi une
idée sur le fonctionnement et le montage du moule.
Chapitre IV : Conception et calcul

57
III. Le choix de la machine
Le choix de la machine dépend essentiellement des facteurs
suivants:
1. La capacité d'injection
2. La force de fermeture
3. La distance entre colonnes
4. Epaisseur minimale du moule La capacité
d'injection:
Chaque machine a une capacité d'injection (voir tableau
suivant) ; donc on choisit la machine en fonction du poids de la grappe
(pièce et dispositif de coulé).
La machine Capacité d'injection
(g)
|
Pression moyenne d'injection (tonnes /cm2)
|
380T
|
5054
|
0.15
|
700T
|
17013
|
0.28
|
900T
|
17092
|
0.33
|
Tableau 6: Capacité d'injection La masse
de la moulée (grappe) (m) :
La masse de la pièce=1600 g (La masse de la pièce
est déterminé par le logiciel solidworks)
Calcul de poids du dispositif de coulée:
Poids de la pièce (Kg) Incidence pondérale
en pourcentage du
dispositif de coulée(%)
0.05 à 0.3
|
70 à 100
|
0.5 à 1.99
|
50 à 70
|
2 à 5
|
30 à 50
|
Tableau 7:Incidence pondérale en pourcentage
du dispositif de coulée [9]
Chapitre IV : Conception et calcul

58
(Poids de dispositif de coulée =64% de poids de la
pièce) Poids de dispositif du coulée=1024g
La machine doit pouvoir injecter une quantité suffisante
(m). m= (1600 +1024) g = 2624g
Du tableau (1) on constate que les machines qui peuvent injecter
cette quantité de matières sont : 900 t ; 700 t ; 380 t
La force de fermeture de la machine
:[8]
L'injection de matière à l'intérieur du
moule provoque de grandes pressions engendrant des forces qui ont tendance
à ouvrir le moule (force de verrouillage), et pour faire face à
ces efforts la presse doit appliquer une force de fermeture
supérieure.
Force de fermeture:
F = Fv × K
F : Force de fermeture du moule (T) K
: Coefficient de sécurité (1,5 à 2) FV
: force de verrouillage (T)
Dont :
Fi, = P × St
P: la pression moyenne d'injection ; P= 0.15
(tonnes /cm2) (tableau 6). St : surface projeté de la
+dispositif de coulée.
(La surface projeter de la pièce est
déterminé par le logiciel solidworks)=600 cm2
La surface projeté de dispositif de coulée=10% de
la surface projeté de la pièce. [10]
AN :
St = 600 + 60 = 660 cm 2 Fi, = 0.15 ×
660 = 99T
F = 99 × 2 = 198T
On a besoin de 2624 g de l'aluminium et une force de
fermeture de 198 tonne, il en résulte que la presse devant être de
380 T.
Chapitre IV :
Conception et calcul

59
La distance entre colonnes :
La presse possède quatre colonnes de guidages des
plateaux sur lesquels le moule sera fixé.
Pour ce faire, l'une des dimensions transversales du
moule doit être inférieure à la distance entre
colonnes.
Les dimensions de notre moule sont :
Largeur 395 mm Hauteur 450 mm
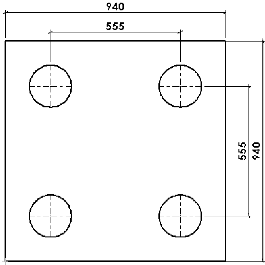
Figure 48:Schémas d'un plateau d'une
presse
Epaisseur minimale du moule :
Les caractéristiques dimensionnelles de la presse
380 T sont :
· La distance entre plateaux 1000mm
· La course maximale du piston 800mm
A partir de là, on voit que l'épaisseur
minimale du moule doit être supérieure à 200mm (notre moule
a une épaisseur de 311mm). (Annexes)
Chapitre IV : Conception et calcul
Pression d'injection
|
2298 Kg/cm2
|
Quantité d'injection
|
5054 g
|
Force de serrage
|
380 Tonnes
|
Force d'ouverture
|
75 Tonnes
|
Exécution
|
a chambre froide
|
Position
|
Horizontal
|
Puissance d'injection
|
14.1 Mpa
|
Puissance d'injection avec multiplicateur
|
14.1 à 45.1 Mpa
|
Épaisseur mini du moule
|
240 mm
|
Commande
|
Oléodynamique
|
Diamètre de piston
|
50 à 90 mm
|
Volume remplissage de conteneurs
|
1907 cm3
|
Moteur destiné à la pompe (puissance)
|
30 KW
|
Moteur destiné à la pompe (Tours)
|
960 tr/min
|
Tableau 8:Caractéristiques techniques de la
machine
IV. Choix de diamètre de piston d'injection
m
V = ñ
V : volume nécessaire pour 2.624 kg
d'aluminium

60
m : Poids de la grappe (poids de la pièce
+ poids de dispositif de coulée).
Chapitre IV : Conception et calcul
ñ : La masse volumique de
l'alliage.(2650kg /m3)
AN :
V =
|
2.624
|
= 0.00099m 3
|
2650
|
|
V=990 cm3 On a
V = ð x
d : rayon de piston d'injection
h : course de piston d'injection (h=400) Donc
|
d
4
|
2
x h
|
4 x V
d2 =
Tc x h
AN :
990 x 4
d2 =
125.6
= 31.53 cm

61
d=5.62 cm =56 mm
Les diamètres disponibles sur la presse 380 t sont
: 55 65 75 85 95 mm Donc on prend d=65 mm.
V. Dimensionnement de système d'alimentation
Calcul de la vitesse à l'attaque de
coulée
[10]
pm x cd2 x 2g
(Va)2 = ñ
Chapitre IV : Conception et calcul

62
Va : vitesse à l'attaque
Cd : coefficient de décharge
(0.45-0.50)
ñ: La masse volumique de l'alliage
(2650kg/m3).
Pm : pression sur le métal
Pm=750×103 kg/m2 (Annexes)
AN:
750 X 10 X 0.2 X 20
(Va)2 = = 1132.07 m/s 2650
Va=33. 64m /s
Calcul de débit à l'attaque:
|
Q =
|
V T
|
Q: débit
V:volume de la grappe
T : Temps de remplissage de l'empreinte de
moule
Epaisseur (mm)
|
Temps de remplissage(s)
|
1.5
|
0.01-0.03
|
1.8
|
0.02-0.04
|
2.0
|
0.02-0.06
|
2.3
|
0.03-0.07
|
2.5
|
0.04-0.09
|
3.0
|
0.05-0.10
|
3.8
|
0.05-0.12
|
5.0
|
0.06-0.20
|
6.4
|
0.08-0.30
|
Chapitre IV : Conception et calcul
Tableau 9:Temps de remplissage en fonction de
l'épaisseur de la pièce (9] Ep : épaisseur minimal de
la pièce =2.5 mm (donner par le logiciel solidworks) Donc t=0.07
s
AN :
Q =
|
1
|
= 14.28 dm 3/s
|
0.07
|
Q=14.28dm 3/s
Calcul de la surface de l'attaque
(9]
Q
Aa =
Va
Aa : surface de l'attaque
AN :
Aa =
Aa=420mm2
Calcul de longueur de l'attaque:
|
14.28 X 10?
|
= 420 mm 2
|
34000
|
A
La = Ea
Alliages Epaisseur de l'attaque
Al Si
Al Si Cu Zn Al4 Zn Al4 Mg Al2
1-1.4 1.2-2.5 0.35-0.8 0.5-1.2 0.6-2

63
Tableau 10:Epaisseur de l'attaque de coulée en
fonction de l'alliage utilisé
Chapitre IV : Conception et calcul
Notre alliage c'est Al Si Cu selon l'entreprise (voirl'annexe)
Donc
Ea : épaisseur de l'attaque = 2mm
AN :
420

64
La=210mm
VI. Dimensionnement de conduit de
refroidissement Le refroidissement s'effectue à l'huile
thermique (selon l'entreprise EI)
Scon = Sp × 2[9] Scon =
n × D × L
Sp: surface projeté de la pièce
(60000 mm2donnée par solidworks)
Scon: surface de conduit de
refroidissement
D : diamètre de conduit de
refroidissement
L : longueur de conduit de refroidissement
Le choix de diamètre deconduit de refroidissement
dépend de 3 factures :
Le raccordement avec le système de refroidissement
central.
Le fluide refroidissement utilisé est de l'huile
thermique.
Le volume et le poids de moule considéré comme
important.
Le diamètre 15 mm est le plus
adapter
Chapitre IV : Conception et calcul
AN :
120 × 103
L=2547.77 mm
Une longueur de 127 3. 88 mm pour chaque partie (fixe et
mobile)
VII. Calcul de temps de refroidissement
tr =
|
e2
n-2 × D
Ln[
|
8
n-2 (
|
Ti- Tm Te-
Tm )
|
e: épaisseur moyenne de la pièce; e = 3
mm
D: la diffusivité thermique de l'aluminium D =
0.02 m2/s
Ti: température d'injection;
Ti=680°C
Te: température d'éjection;
Te=300°C
Tm: température du moule;
Tm=120°C
AN :
tr =
|
32
n-2 × 0.02
Ln[
|
8 '680 -
120'
=
n-2 `300 - 120)
0.4 s
|

65
tr=0.4s
VIII. Calcul de temps de cycle
Le temps de cycle est la somme de tous les temps du
procédé de l'injection.
tc= tf + ti+ tm +
tr+ te+ té
Chapitre IV : Conception et calcul

66
tc : temps de cycle
tf : temps de fermeture 7 s
ti : temps d'injection (temps de remplissage) 0. 07
s
tm : temps de maintien 4s
tr: temps de refroidissement 0.4s
te : temps d'ouverture 7s
té : temps d'éjection 5s
AN :
??= 7 + 0.07 + 4 + 0.4 + 7 + 5 = 23.47
?
tc=23.47 s
IX. Dimensionnement des talons de lavage et des
tirages d'air
Le dimensionnement et la position destalons de lavage
et des tirages d'air s'effectuent après quelques injections.
[8]
Chapitre IV : Conception et calcul

67
X. Calcul de résistance
L'objet de cette partie concerne l'étude de la
résistance des pièces sollicitées mécaniquement.
1 Les poids des pièces constituantes le moule
Le poids est déterminé par la relation suivante
? = ä × V
P : poids de la pièce ä: masse
volumique V :volume (dm3)
Les pièces
|
LES matières
|
Volume (dm3)
|
A (dan/dm3)
|
Les poids
(daN)
|
Plaque de serrage fixe
|
40CrMnMoS8-6
|
16.74
|
7,85
|
131.40
|
Porte empreinte
fixe
|
40CrMnMoS8-6
|
17. 61
|
7.85
|
138.24
|
Empreinte fixe
|
X37CrMoV5-1
|
5.95
|
7,70
|
47.81
|
Centre fixe
|
X37CrMoV5-1
|
12.70
|
7,70
|
97.80
|
Plaque de serrage mobile
|
40CrMnMoS8-6
|
17.89
|
7.85
|
140.44
|
Baguette support
|
40CrMnMoS8-6
|
3.97
|
7,85
|
31.16
|
Porte empreinte
mobile
|
40CrMnMoS8-6
|
17.79
|
7,85
|
139.65
|
Centre mobile
|
X37CrMoV5-1
|
13.38
|
7,70
|
103.03
|
Empreinte mobile
|
X37CRMOV5-1
|
6.55
|
7,70
|
50.43
|
Tableau 11:Les poids des pièces
constituantes le moule
2 Résistance des éléments
constituants le moule au matage dû à la force de fermeture du
moule
La force de fermeture d'une presse 380 tonnes égales:
380 000 Kg = 380 0000 N
Chapitre IV : Conception et calcul
Condition de résistance au matage
F
cr = S = Rpe
Et
Re
Rpe =
Résistance du plan de joint On a :
Re =1100 N/mm2 (pour les porte
empreinte). S' = 2 (coefficient de sécurité).
AN :
|
S
|
Rpe=
|
750
|
= 375N/mm 2
|
2
|
Rp=550N/mm2
|
Spj =
|
F
|
Spj : surface du plan de joint; AN
:
|
0.2 X Re
|
Spj =
|
3800000
|
= 25333.33mm2
|
0.2 X 750
|
La surface de contact entre les deux portes empreintes est de
84553.33mm2 largement supérieure;
Le plan de joint résiste.
Partie fixe:
2.1 Plaque de serrage fixe (
Rpe=375N/mm2)
F
cr = S = Rpe
S = eX l
S : surface matée

68
e : épaisseur de l'élément
l: langueur de l'élément
Chapitre IV : Conception et calcul
AN :
S = 56 X 650 = 36400
3800000
La plaque de serrage résiste ou
matage.
2.2 Centre fixe
( Rpe= 385N/mm2)
e = 146 mm l=220 mm S=32120mm2
3800000
Le centre fixe résiste ou matage
2.3 Porte empreinte fixe (
Rpe=375N/mm2)
e = 66 mm l=450 mm S=29700mm2
3800000
Le Porte empreinte fixerésiste ou
matage

69
Partie mobile
Chapitre IV : Conception et calcul
2.4 Plaque de serrage mobile (
Rpe=375N/mm2)
e = 46 mm l=700 mm S=32200mm2
3800000
La plaque de serrage mobile résiste ou
matage.
2.5 Baguette support (
Rpe=375N/mm2)
e = 46 mm l=600 mm S=27600mm2
3800000
Les baguettes support résistent ou
matage
2.6 Centre mobile ( Rpe= 385N/mm2)
e = 146 mm l=220 mm S=32120mm2
3800000

70
Le centre mobile résiste ou matage
Chapitre IV : Conception et calcul
2.7 Porte empreinte mobile (
Rpe=375N/mm2)
e = 66 mm l=450 mm S=29700mm2
3800000
Le Porte empreinte mobilerésiste ou
matage.
Apres calcul, on remarque que tous les éléments
constituants le moule résistent au matage dû à la force de
fermeture du moule.
3 Résistance des vis CHC et les colonnes de guidage
au cisaillement Partie fixe
3.1 Résistance des 4 colonnes de guidage de
ø 50 mm (Poids de la partie mobile lors de la manutention
seulement)
Le poids de la partie mobile est de : Baguettes
supports=62.32KG=623.2N
Porte empreinte =139.65 KG =1396.5 N
Empreinte = 50.43 KG =504.3 N Centre =103.03 KG =1030.3 N
Condition de résistance s'écrit :
ô =
F
< [T]cis
N × n× S
-
6e
[T]cis= S,×
0.8
ð × D2

71
[ô]cis :
résistance pratique ou cisaillement N =Nombre de
sections cisaillées (N=1).
Chapitre IV : Conception et calcul
S : sections cisaillées
n : Nombre de colonne (n=4).
óe : résistance
élastique
S' : coefficient de sécurité
D : diamètre de la colonne
AN :
[T]cis=
2 x 0.8 = 440 N/mm 2
1100
S=
|
ð x 502
|
= 1962.5 mm 2
|
4
|
ô =
3554.3
= [T]cis 4 x 1962.5
La condition est vérifiée
3.2 Résistance des 8 vis CHC au cisaillement
dû au poids de la partie mobile Dans notre conception, les vis
utilisées sont des vis CHC M 16 en XC35 de résistance à la
traction
Re=335 N /mm2
Condition de résistance :
335
[T]cis= 2 x 0.8 = 134N/mm 2
S=
|
ð x 162
|
= 200.96 mm 2
|
4
|
ô =
|
3554.3
|
= 2.21 N/mm 2 = [T]cis
|
8 x 200.96
|

72
La condition est vérifiée
Chapitre IV : Conception et calcul
3.3 Résistance des 7 vis CHC au cisaillement
dû au poids de l'empreinte fixe et de porte empreint fixe
Le poids de la partie fixe est de :
Porte empreinte =138.24 KG =1382.4 N Empreinte = 47.81 KG =478.1
N
Centre =97.80 KG =978.0 N
Condition de résistance
[?]???=
|
335
2 × 0.8 = 134?/?? ?
|
?=
|
ð × 16?
|
= 200.96 ?? ?
|
4
|
ô =
|
2838.5
|
= 1.76 ?/?? ? = [?]???
|
7 × 200.96
|

73
La condition est vérifiée
XI. Conclusion
Nous avons pu choisir dans ce chapitre la presse qui convient
et le calcul dimensionnel du moule et de système d'alimentation de
l'empreinte et du circuit de refroidissement. Comme on a aussi
vérifié la résistance des différents
éléments, ce qui va nous assurer une bonne réalisation.
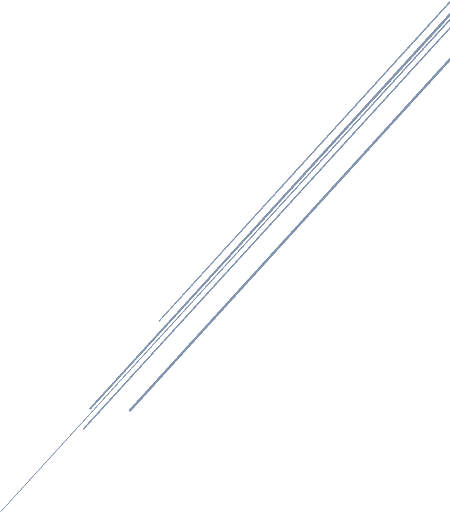
Conclusion générale
Conclusion générale
Le procédé de fabrication des pièces en
fenderie dans l'industrie est connu depuis longtemps et qui ne cesse de
s'agrandir au fil des dernières années ; Il permet d'obtenir un
produit en grande série et à des prix de revient abordables.
La présente étude effectuée dans ce projet
nous a donné l'opportunité d'élargir et d'acquérir
des connaissances dans le domaine de la fonderie, Et nous a aussi permis de
nous initier aux logiciels de CAO tel que SolidWorks.
L'élaboration de ce projet nous a donné une
perspective sur le monde du travail dans les grandes entreprises tel que
l'ELECTRO-INDUSTRIE. Le stage que nous avons effectué au sien de cette
entreprise nous a été d'une grande importance.
Nous avons ainsi, répondu au cahier des charges
exigés par cette entreprise, par la conception d'un moule à
injection d'aluminium, destiné à la fabrication de la
pièce flasque-bride ; Cette conception est réalisée par le
logiciel SolidWorks.
Le calcul de résistance des éléments
constituants le moule a été effectué et le résultat
trouvé est concluant.
Nous souhaitons que ce modeste travail serve comme un guide aux
étudiants(es) de notre département et servira aussi à
d'autres travaux.
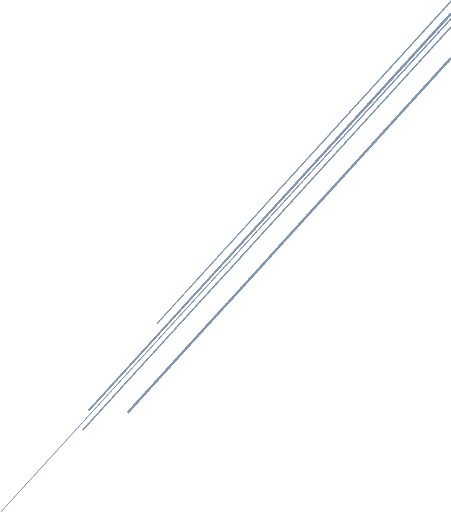
ANNEXES
Caractéristiques dimensionnelles de la machine OL
380 T
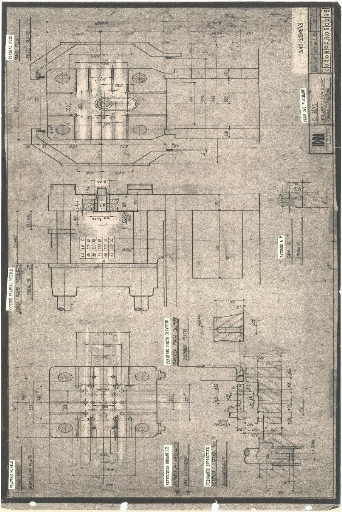
Composants standard pour moule(RABOURDIN)
RABOURDIN INDUSTRIE PIKE
ElffMAel 44,
EvOu Gux tenberg
ANCE. BUSBY SAINT OEOROES
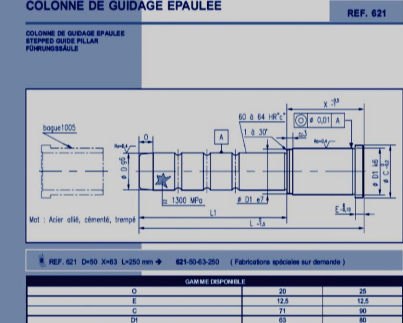
REF. 621
COLONNE DE GUIDAGE EPAULEE
A
0 0,01
60 6 64 Mee
~.1
X
·
OAMMF [71SPONI,M F
COLONNI DE OUR)A06 UPAULUS STEPPED OU10E PILLAR
FUMUNO>NAUL/
Id30'
I
re
Mal kier olli8, cément6, Irempé
c 1300 MPa } D1 e!
LI
REF. 621 0-50 X-03 L250 mm i 621.50433-250 (Febrlee,bne
oplclalls cur demands
25
12,6
90
E
C
20
12.6
11
03
|
L1
|
|
%
|
|
°
|
60 Is
|
|
117
|
|
03
|
|
160
|
|
|
100
|
|
10
|
|
|
|
137
|
|
63
|
|
200
|
|
|
120
|
|
S0
|
|
|
100
|
|
160
|
|
|
167
|
|
62
|
|
260
|
|
|
170
|
|
SO
|
|
|
100
|
|
100
|
|
|
262
|
|
N
|
|
310
|
|
|
236
|
|
66
|
r
|
|
216
|
|
100
|
|
|
190
|
|
1II
|
|
|
337
|
|
43
|
|
400
|
|
|
320
|
|
50
|
|
|
300
|
|
100
|
|
|
276
|
|
_ 126
|
|
|
367
|
|
62
|
|
460
|
|
370
|
|
60
|
|
|
360
|
|
100
|
|
|
326
|
|
120
|
|
|
420
|
|
SO
|
|
000
|
|
|
400
|
|
100
|
|
|
|
|
|
|
|
606
606
|
|
aE
|
|
~
|
|
I:
|
|
|
|
,4 41
|
Caractéristiques de l'alliage
utilisé
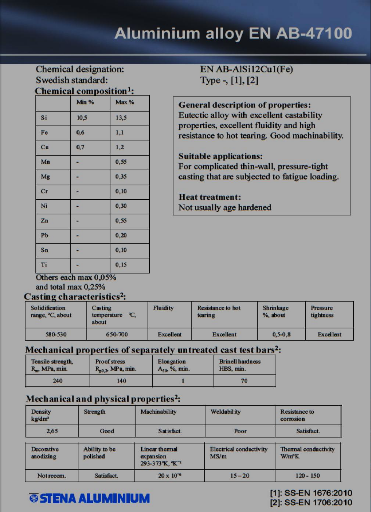
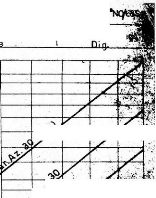
Pression spécifique sur l'alliage
TAB. N.
OL/380 S ML
IDRA 5, N. C.
Coatruzlonl Idromecuplcha
Bre.=4n.
KR/
cm. cm. 200-1
Nomogramma variaziôni dell.'ini.zione Nomogramm der
Presstei1werte Nomogramme variations de I'iniection N


~ç
t\L)
=mm am immi ï----m
--®s--
mummumummmmomm
1500
mmimmmimmommm
mmumrAimmimm ummu//mNim1 ·
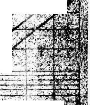
1000
900
800
700
0
--50b
400
300-
100 50
oz
AIWAINIKEr4
ANN MrAii!
\ ./ AliWAIIIMEMP'1
V-461EPrairMilor '410
ars ..
AR21.5110:rrAtarrAtiffeW
WWWMP
IIIIEW' Y n ,'.
·
. sec. x 10+1
.o
400.
500
600- 70OE
800
900-
1000
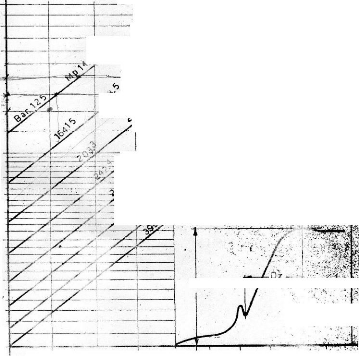

w200
Û ~
a
N
150-
w R Ga
-
rr,E
0
· 6
iii

1500-
2000-
250
U
Q:
O
a
tl
Pk
C. , ?.set.
..K

11,
t
I
'.PRESSION SPECIFIQUE
CO 70 80
L)J CO, . < ,AIRS - der Presskammer
--5
PC:.I DE LA
2.3 313 41
DOE_. ieiLgeW'rcht ( kg. -Atiurrr.)
Donnés logiciel solidWorks
Masse de la piéce
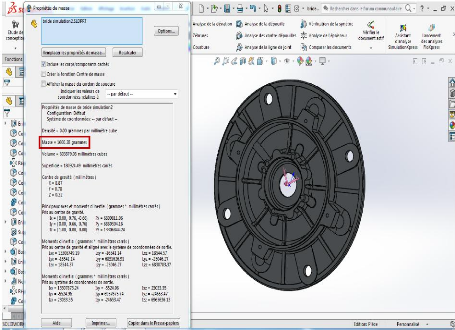
Surface projetée de la pièce
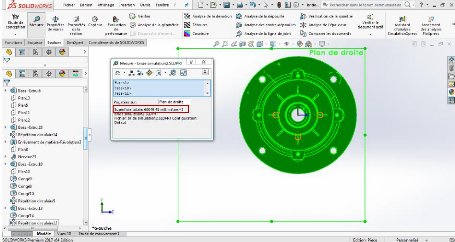
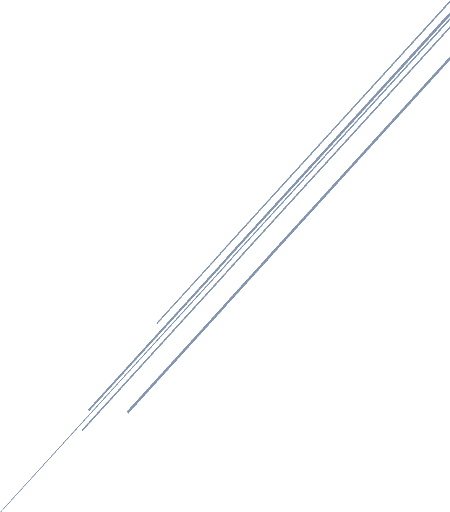
Bibliographie
BIBLIOGRAPHIE
[1] Pierre Mayé Moteurs électriques
industrielles, Edition DUNOD 2005.
[2] Robert PERRET, Albert FOGGIA, Elisabeth
RULLIERE, Pascal TIXADOR, «Entrainements électriques 2 : machines
électriques industrielles », Edition. LOVOISIER, 2007
;
[3] Archive de l'entreprise ;
[4] Éric FELDER, Procédés de
mise en forme, TECHNIQUE DE L'INGENIEUR ;
[6] Pierre CUENIN, Moulage - Noyautage, TECHNIQUE
DE L'INGENIEUR ;
[7] Gilles Dour, Aide-mémoire - Fonderie -
2e édition, Edition DUNOD,
2016.
[8] J.BOUCHET, Technologie de la fonderie en
moules métalliques, « Fonderie sous pression », 2
édition ETIF 1977.
[9] Luigi Andreoni, Mario Casé, Giorgio
Pomesano, le moulage sous pression des alliages d'aluminium, (1 à 7),
édition ETIF, 1993.
[10] Rd, M: Gating Manual, NADCA, USA Wa,
2006.
[11] B. Vijaya Ramnatha*, C.Elanchezhiana, Vishal
Chandrasekharb, A. Arun Kumarb, S.Mohamed Asifb, G. Riyaz Mohamedb, D. Vinodh
Rajb ,C .Suresh Kumarc, Analysis and Optimization of Gating System for
Commutator End Bracket, Procedia Materials Science, 2014.
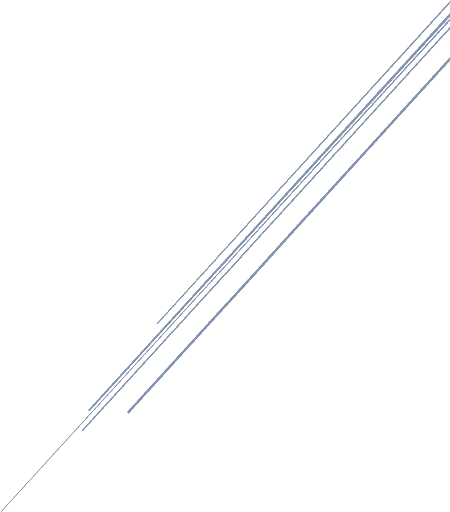
Dessins de conception
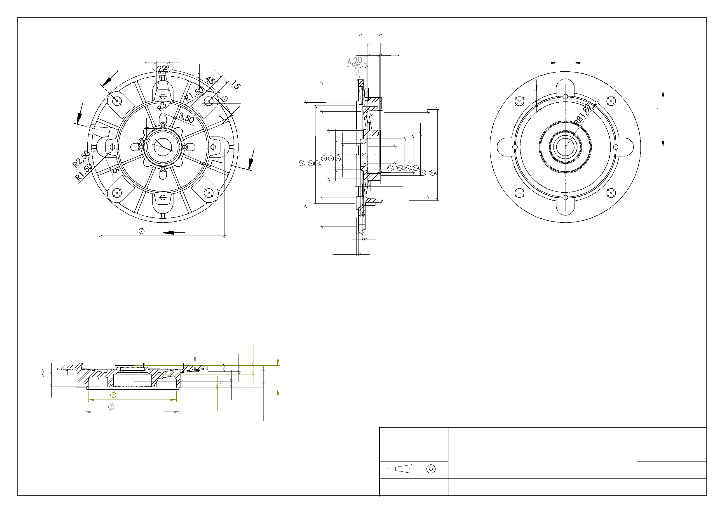
COUPE C-C
22
30
34
22,50
21
9
C
7
15
17,52
98
B
4
1
181
5,50
52
39
170
2 150
84
B
29,20
1
158
56
62,40
72
147
2,50
4,50
215
5,80
3,50
C
3,50
COUPE B-B
3,68
15,20
41,20
8
21,50
8
11
153
165,90
10
3,70
39,38
Echelle : 1:3
IKERROUIENE-DJ AMMOUR-R
flasque-bride B5-A106/107-2
Planche N° :1/1
A 3
FGC - GM - UMMTO
M2 FMP
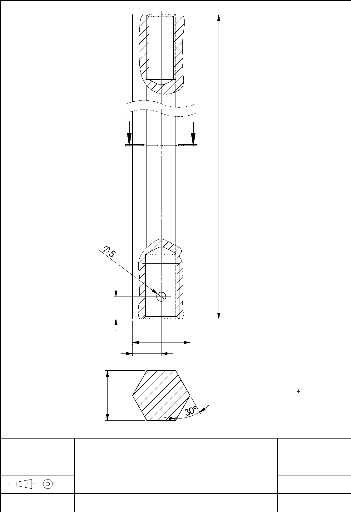
N N
405,5
12
31
15,5
SECTION N-N
27
Ra=1.6
IT= 0.2
sauf indication
Echelle:1:1
IKERROUIENE-Dj AMMOUR-R
barre d'ejection
Planche N°
:1/30
A4
FGC - GM - UMMTO
M2 FMP
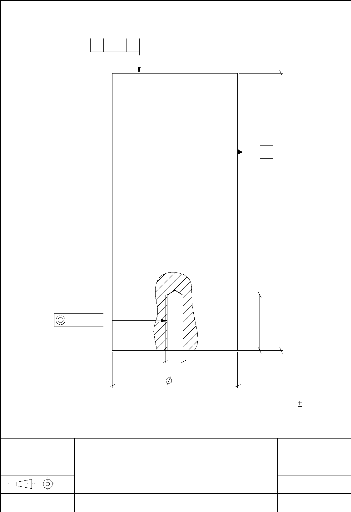
A
0.02
A
150
A
0.02
30
M10
68 g6
Ra=1.6
IT= 0.2
sauf indication
Echelle:1:1
IKERROUIENE-Dj AMMOUR-R
boulon support
Planche N° :2/30
A4
FGC - GM - UMMTO
M2 FMP
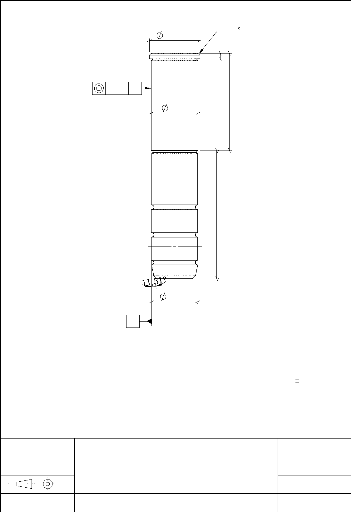
0
55 -
2x45
0,20
0
0,10
6 -
A
0.01
0,50 1
51 k6
-
-
105
0
1,50
138 -
50 g6
A
Ra=1.6
IT= 0.2
sauf indication
Echelle:1:2
IKERROUIENE-Dj AMMOUR-R
colone de guidage D50
Planche N° :
3/30
A4
FGC - GM - UMMTO
M2 FMP
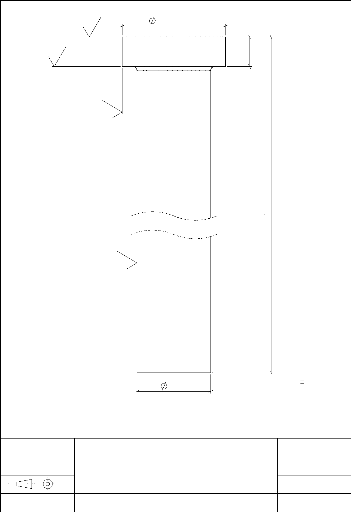
0
28 -
0,20
Ra=1.6
Ra=0.4
0
0 ,0 5
8 -
Ra=3.2
+2
0
25 7 , 50
Ra=0.4
20 g6
Ra=1.6
IT= 0.2
sauf indication
Echelle:2:1
IKERROUIENE-Dj AMMOUR-R
colone guidage D20
Planche N° :
4/30
A4
FGC - GM - UMMTO
M2 FMP
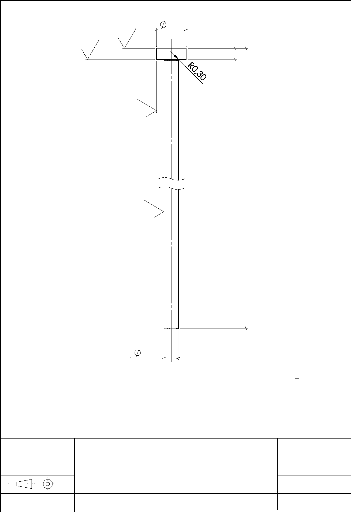
0
8 -
0,20
Ra=1.6
Ra=0.4
0
0,05
3-
Ra=3.2
+2
0
206
Ra=0.4
4 g6
Ra=1.6
IT= 0.2
sauf indication
Echelle:2:1
IKERROUIENE-Dj AMMOUR-R
Ejecteur D4
Planche N° : 5/30
A4
FGC - GM - UMMTO
M2 FMP
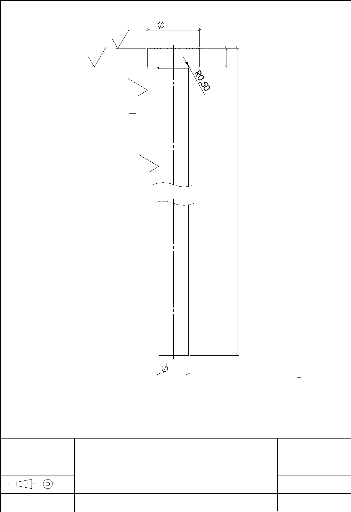
0
14 -
0,20
Ra=1.6 Ra=0.4
0
0,05
5-
Ra=3.2
Ra=0.4
+2
0
234
8 g6
Ra=1.6
IT= 0.2
sauf indication
Echelle:2:1
IKERROUIENE-Dj AMMOUR-R
ejecteur D8
Planche N° :
6/30
A4
FGC - GM - UMMTO
M2 FMP
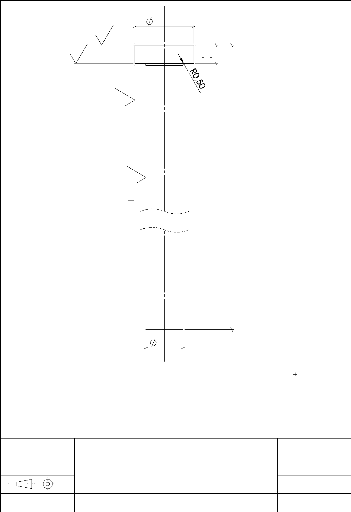
0
16 -
0,20
Ra=1.6 Ra=0.4
0
0,05
5-
Ra=3.2
+2
0
Ra=0.4
227
10 g6
Ra=1.6
IT= 0.2
sauf indication
Echelle:2:1
IKERROUIENE-Dj AMMOUR-R
Ejecteur D10
Planche N°
:7/30
A4
FGC - GM - UMMTO
M2 FMP
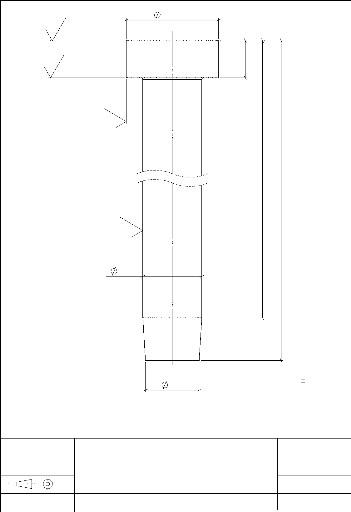
25 -
0
0,20
Ra=1.6
Ra=0.4
0
0 ,05
10 -
+2
0
9 1 , 50
Ra=3.2
+2
0
80
Ra=0À
16
14,5
Ra=1.6
IT= 0.2
sauf indication
Echelle:2:1
insert D15
IKERROUIENE-Dj AMMOUR-R
Planche N° :
8/30
A4
FGC - GM - UMMTO
M2 FMP
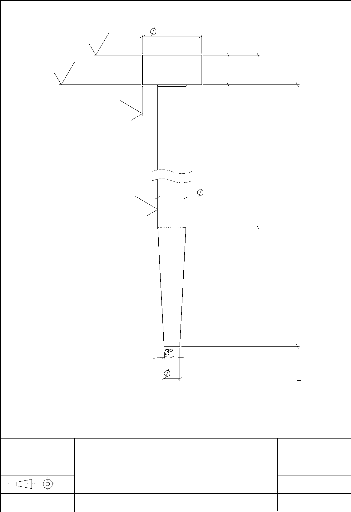
16 -
Ra=1.6
Ra=0.4
0
0,20
0
0 ,0 5
8 -
Ra=3.2
87
+2
0
1 1 1
8 g6
Ra=0À
4
Ra=1.6
IT= 0.2
sauf indication
Echelle:2:1
IKERROUIENE-Dj AMMOUR-R
Insert D7
Planche N°
:9/30
A4
FGC - GM - UMMTO
M2 FMP
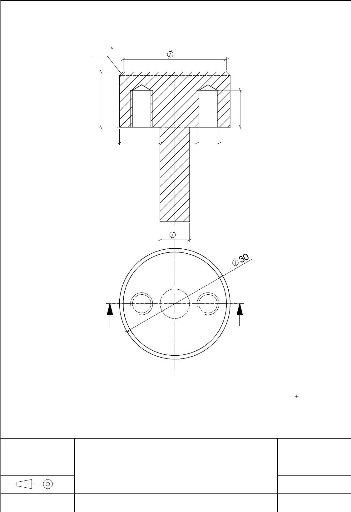
COUPE B-B
1x45
28
15
10
11
M6
8
B B
Ra=1.6
IT= 0.2
sauf indication
Echelle:2:1
IKERROUIENE-Dj AMMOUR-R
pièce d'arrêt
Planche N° :10/30
A4
FGC - GM - UMMTO
M2 FMP
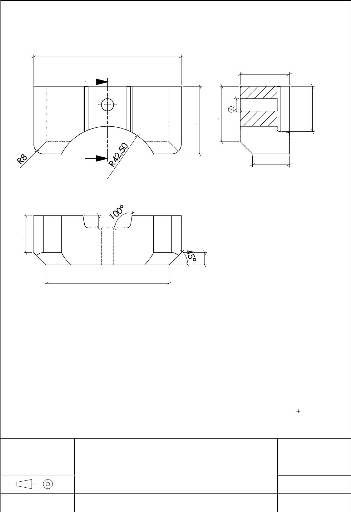
COUPE A-A
120 f7
A
40
10
37
55
45
30
A
10
30
10
100
Ra=1.6
IT= 0.2
sauf indication
Echelle:1:1.5
IKERROUIENE-Dj AMMOUR-R
plaque d'entrée
Planche N°
:11/30
A4
FGC - GM - UMMTO
M2 FMP
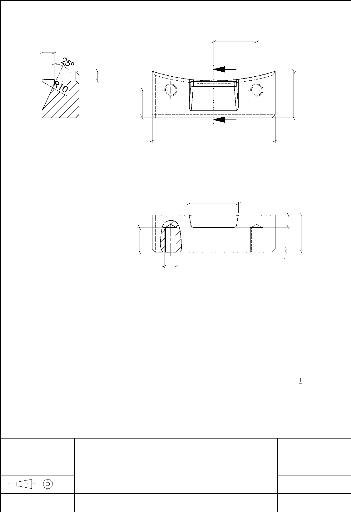
COUPE A-A
35
10
A
8
22,50
38
100
A
40
20
30
2,50 10
M10
Ra=1.6
IT= 0.2
sauf indication
Echelle:1:1.5
IKERROUIENE-Dj AMMOUR-R
plaque pour attaque de coulée fixe
Planche N° :12/30
A4
FGC - GM - UMMTO
M2 FMP
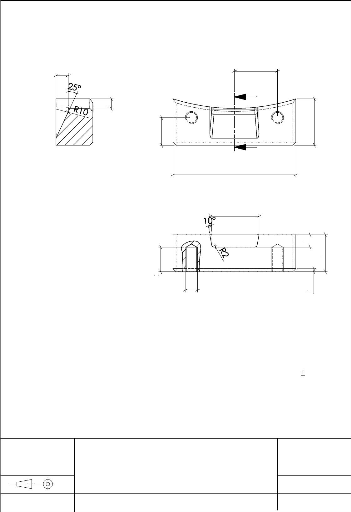
COUPE A-A
10
35
A
8
22,50
38
A
100
40
10
30
20
M10
2,50
Ra=1.6
IT= 0.2
sauf indication
Echelle:1:1.5
IKERROUIENE-Dj AMMOUR-R
plaque pour attaque de coulée mobile
Planche N° :13/30
A4
FGC - GM - UMMTO
M2 FMP
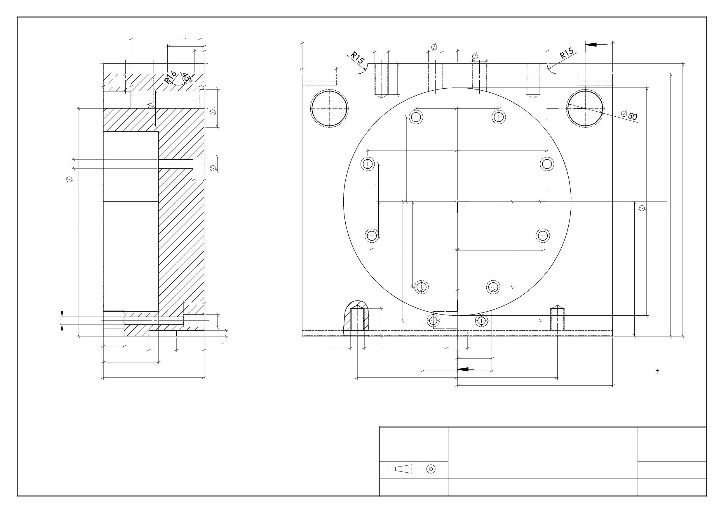
COUPE M-M
100
M
450
53
14
M20
130
20
20
50
6
45
55
60 60
122,50
130
130
13,50
20
51
40
51
16
54,50
330
395
380
330
49,50
124
124
124
195
52 52
124
30
172,50
11
18
172,50
8
30
M20
40
50
100
145 M 145
Ra=1.6
IT= 0.2
sauf indication
225
Echelle : 1:2.5
IKERROUIENE-DJ AMMOUR-R
plaque de moule fixe
Planche N°
:14/30
A 3
FGC - GM - UMMTO
M2 FMP
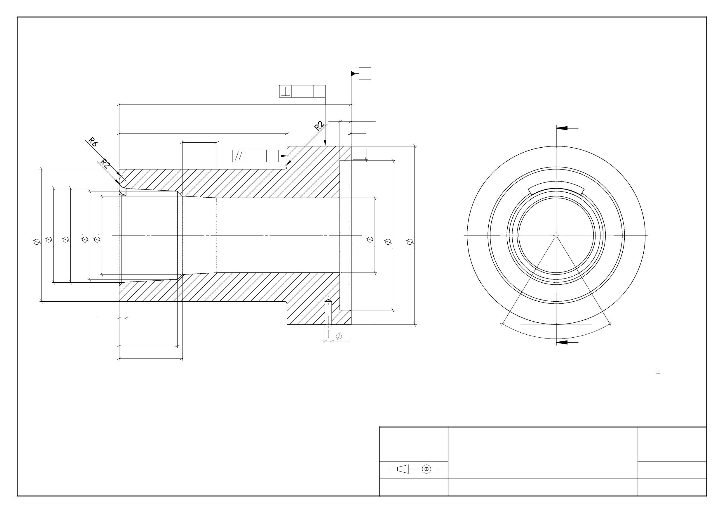
COUPE T-T
A
0.02
A
202
10
T
146
1
30
0.02
1
A
68
77
82
82
115
155
65
130
6
62,61°
51
6
55
T
Ra=1.6
IT= 0.2
sauf indication
Echelle : 1:1.5
IKERROUIENE-DJ AMMOUR-R
douille de coulée
Planche N°
:15/30
A 3
M2 FMP
FGC - GM - UMMTO
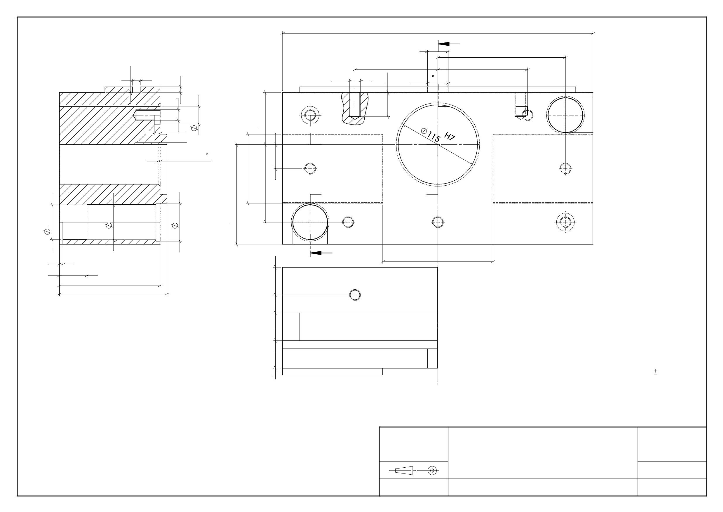
450
O
30
COUPE O-O
185
120
130
0,50
12
M16
35
1x45
8,50
M16
26
3x45
75,50
35
3x45
35
100
H7
50
55
51
144,50
112,50 #177;0,01
5
40
160
O
146
40
156
40
40 #177;0,05
Ra=1.6
IT= 0.2
sauf indication
Echelle : 1:2.5
IKERROUIENE-DJ AMMOUR-R
piéce du centre fixe
Planche N°
:16/30
A 3
M2 FMP
FGC - GM - UMMTO
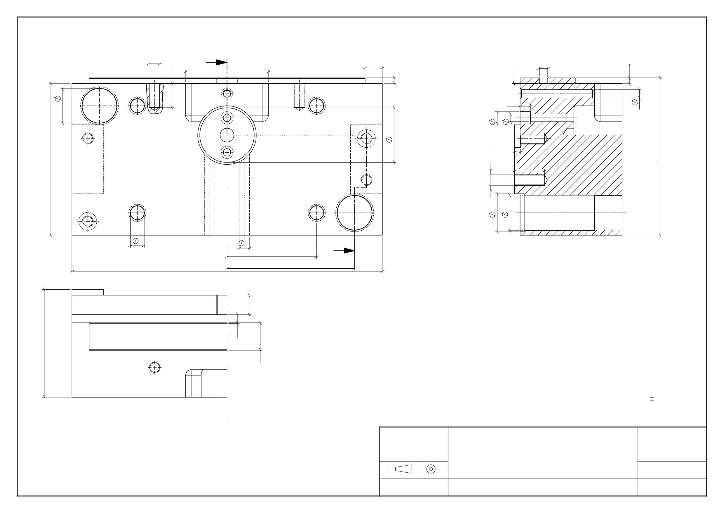
COUPE A-A
A
M16 25
120
12
5
35
8
8,50
50
0,50
12
81
18
220
79
15
8,50
11
228
M16
43,50
55
51
20
15
130
450
185
A
28
13
156
40
Ra=1.6
IT= 0.2
sauf indication
Echelle : 1:2.5
IKERROUIENE-DJ AMMOUR-R
plaque d'entrée
Planche N°
:17/30
A 3
FGC - GM - UMMTO
M2 FMP
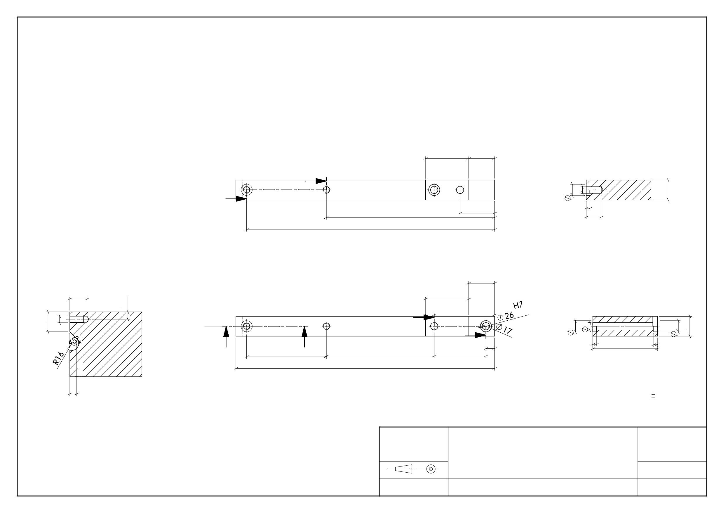
COUPE H-H
100 60
H
26
46
M16
H
8,50
80
35
390
575
COUPE G-G
60
40
COUPE A-A
100
17
A
140
46
17
M16
26
H7
26
46
G
8,50 150 8,50
20 #177;0,01
G
A
120
250
185
600
16
Ra=1.6
IT= 0.2
sauf indication
Echelle : 1:4
IKERROUIENE-DJ AMMOUR-R
baguette support
Planche N°
:18/30
A 3
FGC - GM - UMMTO
M2 FMP
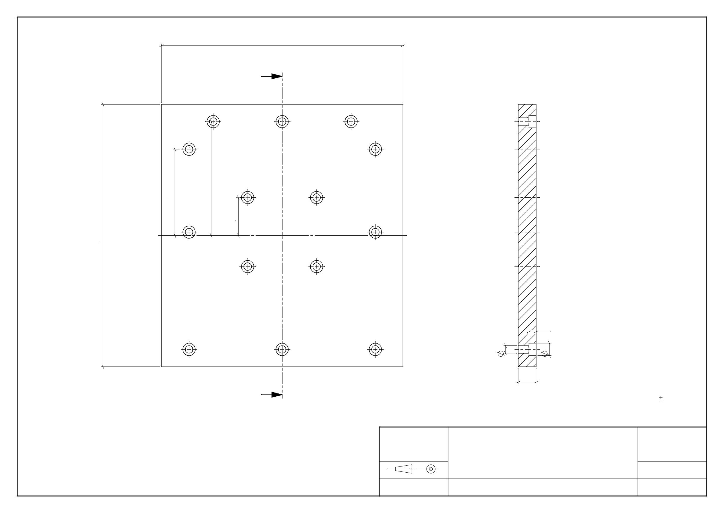
350
A
COUPE A-A
125
1 65
55
380
11
1 1
1 8
26
A
Ra=1.6
IT= 0.2
sauf indication
Echelle : 1:2.5
IKERROUIENE-DJ AMMOUR-R
contre plaque d'ejection
Planche N°
:19/30
A 3
FGC - GM - UMMTO
M2 FMP
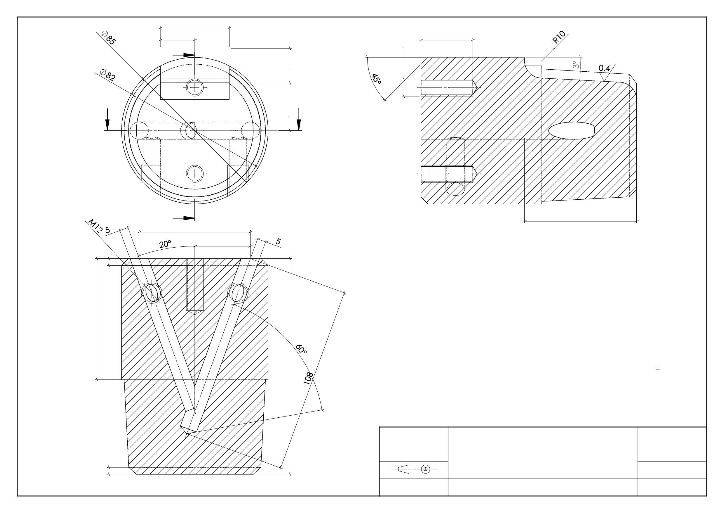
40
20
30 COUPE V-V
V
M 1 0
2 0
2 7 , 5 0
27
W W
65
V
64,50
32
COUPE W-W
4
7 0
1 2 5
Ra=1.6
IT= 0.2
sauf indication
Echelle : 1:1
IKERROUIENE-Dj AMMOUR-R
enclume
4
Planche N°
:20/30
A 3
M2 FMP
FGC - GM - UMMTO
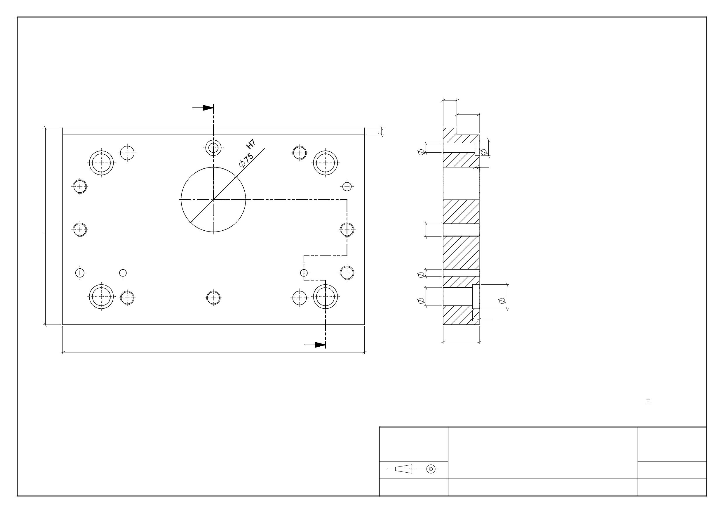
COUPE A-A
16 #177;0,03
26 #177;0,03
8
1 8
5
228
21 8 M16 1 1
28
A
350
8
42
A
Ra=1.6
IT= 0.2
sauf indication
Echelle : 1:2
IKERROUIENE-DJ AMMOUR-R
plaque de couverture
Planche N° :21/30
A 3
FGC - GM - UMMTO
M2 FMP
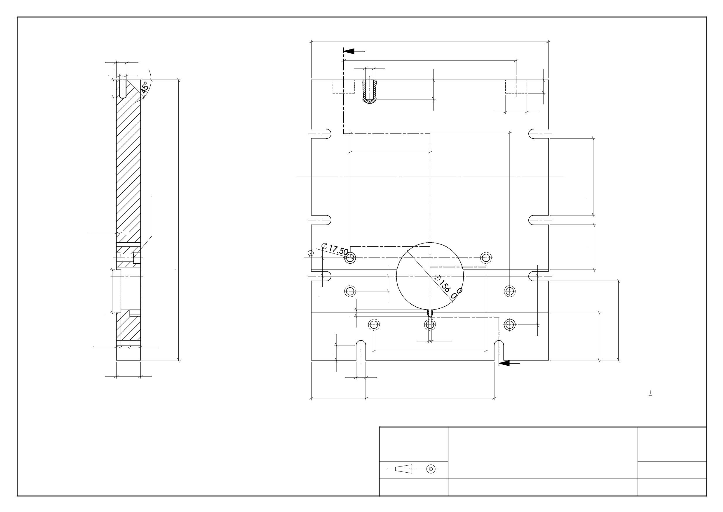
550
K
COUPE K-K
25
400
M20
M16
40
31
45
50
370
185 #177;0,01
178
8,50
M16 DIN912
104
650
26
1
0 ,0 1
4 2,50 #177;
3 5
10 0
1 5
112,50 #177;0,0 1
110
10,50
6,50
25
260
35
184
56
22
K
126
298
Ra=1.6
IT= 0.2
sauf indication
Echelle : 1:4
IKERROUIENE-DJ AMMOUR-R
plaque de serrage fixe
Planche N°
:22/30
A 3
FGC - GM - UMMTO
M2 FMP
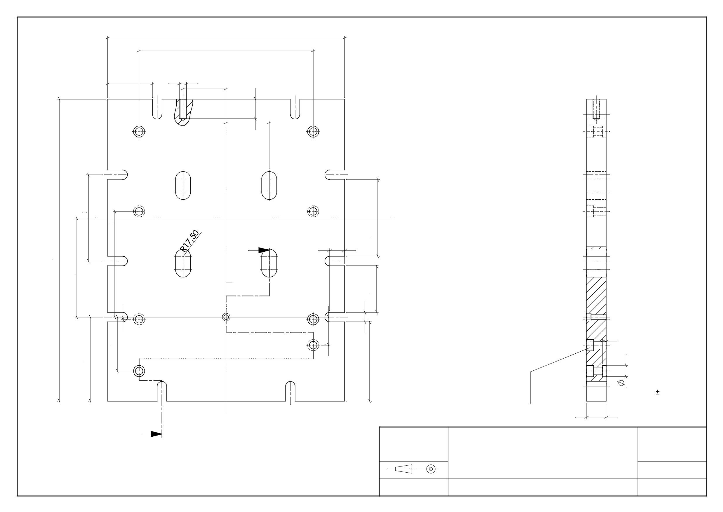
550
404
COUPE J-J
M16
104
100
45
100
200
245
J
178
35
700
230
108
5
22
125
8,50
65
195
184
M16DIN912
H7
26
Ra=1.6
IT= 0.2
sauf indication
46
J
IKERROUIENE-DJ AMMOUR-R
Echelle : 1:4
plaque de fixation mobile
Planche N°
:23/30
A 3
FGC - GM - UMMTO
M2 FMP
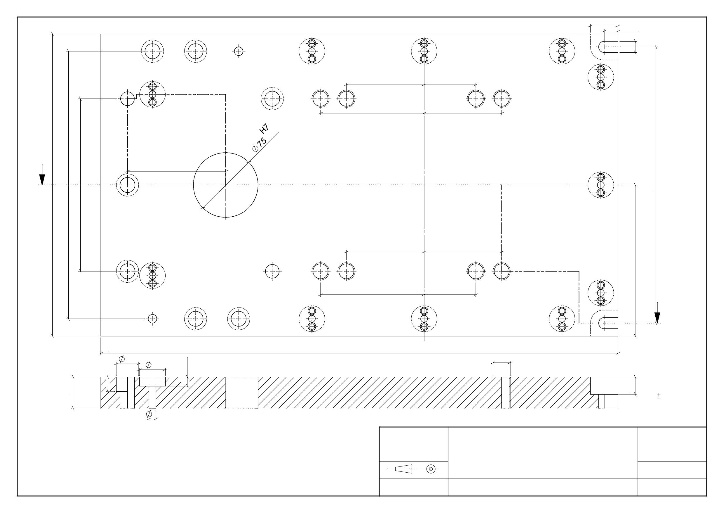
32 16
13
60
90
120 90
114
A
350
310
200
320
90 90
175
120 60
A
600
16,60
M20
26
30
10,50
COUPE A-A
36
20
Ra=1.6
IT= 0.2
sauf indication
8
Echelle : 1:2
IKERROUIENE-DJ AMMOUR-R
plaque d'ejecteur superieur
Planche N°
:24/30
A 3
FGC - GM - UMMTO
M2 FMP
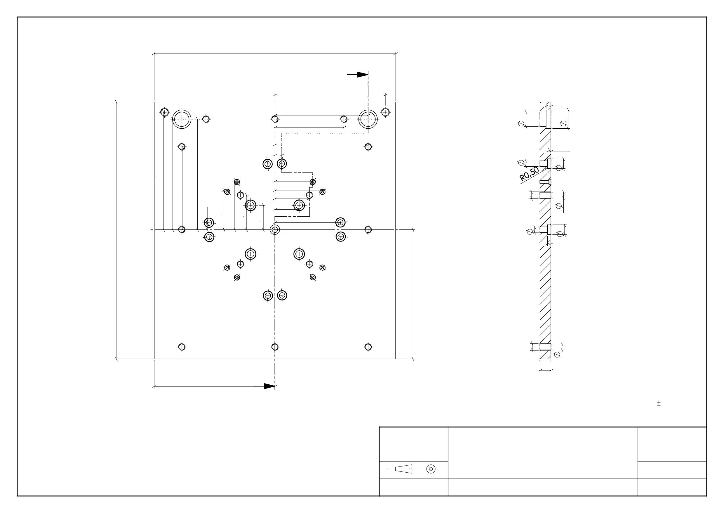
350
A
COUPE A-A
160
7
135
2 7
2 1
100
135
10
4,50
1 4
1 7 0
1 60
120
1 6 0
55
69 50
35
8 , 5 0
8
M 1 0
10
55
69
50
35
1 4
372
8
95
135
5
187
M 1 0
8 , 5 0
16
175
A
Ra=1.6
IT= 0.2
sauf indication
Echelle : 1:2.5
IKERROUIENE-DJ AMMOUR-R
plaque d'ejecteur
Planche N°
:25/30
A 3
FGC - GM - UMMTO
M2 FMP
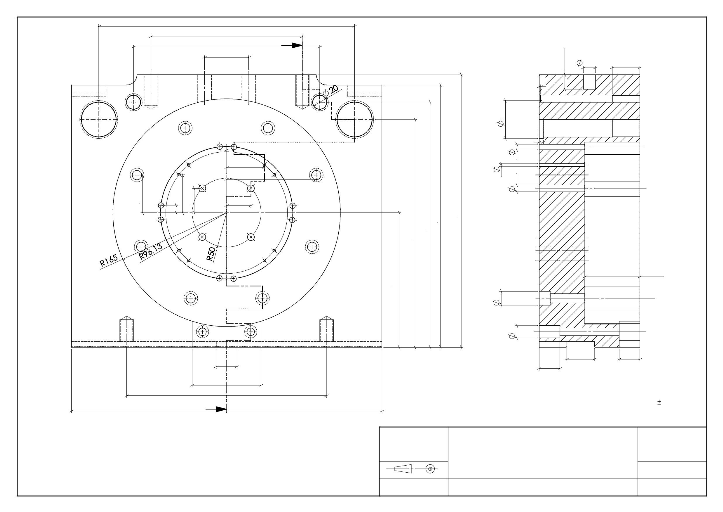
371
219,50
270
A
COUPE A-A
64
2 1, 1 8
40
17,50
2
5 5
6
10,50
8
55
4
130
1 0
5 4 , 5 0
35
10,50
55
35
395
330
355
380
195
80
2 0
1 8
40 30
30
30
100
290
450
Ra=1.6
IT= 0.2
sauf indication
A
Echelle : 1:2.5
IKERROUIENE-DJ AMMOUR-R
porte empreinte mobile
Planche N° :
26/30
A 3
FGC - GM - UMMTO
M2 FMP
|