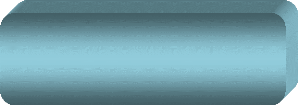
~~~~~~~~
4
~ 4 4
XO'L 4LM 4N'DRXE
REMERC~EMENTS
Ce mémoire aussi riche qu'il soit ne saurait être
la réalisation d'un seul individu, c'est pourquoi je ne saurais
commencer sa rédaction sans remercier vivement tous ceux qui de
près ou de loin ont contribué à son élaboration.
Je pense ainsi à:
· L'éternel tout puissant pour toutes les
grâces qu'il ne cesse de me combler ;
· Toute l'équipe dirigeante de l'IUT FOTSO
VICTOR de Bandjoun et en particulier Le directeur Pr. FOGUE
MEDARD et tout le corps enseignant de l'IUT, pour leur
imprégnation totale dans une formation toujours à la hauteur des
attentes ;
· Au chef du département Génie
Mécanique et productique, Dr.SOH FOTSING BERTIN, pour
les précieuses connaissances qu'il nous a transmises durant notre
formation ;
· Au responsable de niveau de la filière
maintenance, Dr BLAISE MTOPI FOTSO, pour ses conseils et ses
enseignements ;
· Tout le corps enseignant de l'IUT de
Bandjoun ;
· Au Directeur Général de BUETEC-Broderie
Sarl, Mme. GUEMTO BETTINA pour m'avoir accordé une
place dans sa structure ;
· Au responsable de maintenance, M. TALLER TIERRY
KOUOGCHOU, pour la mise au point de mon sujet et son encadrement tout
au long de mon stage;
· Tout le personnel de BUETEC
particulièrement ceux de BASSA avec qui j'ai
passé tous ce temps. Notamment :
Mme NYAWA, Papa Thomas, Eloa, Célestin, Thierry,
Hervé, Rodrigue, Salomon, Russel, André.
· Á toute ma famille
· Á tout mes amis de l'IUT- FV de Bandjoun
· A tout mes amis loin de l'IUT et partout dans le monde
· Á tout ceux qui n'ont pas été
cités
· Un salut particulier à Monsieur Dany
KACHER de l'université de Strasbourg en France pour sa
brillante mission effectuée au sein de notre département et qui
nous a apporté un pourcentage inestimable en valeur pour notre
formation.
Que Dieu vous bénisse
AVANT-PROPOS
L'Institut Universitaire de Technologie Fotso Victor de
Bandjoun (IUT-FV) situé dans la région Ouest du Cameroun a
été construit en 1987 par le fondateur donateur monsieur Fotso
Victor. Initialement collège privé laïque polyvalent Fotso
Victor, ce collège fut cédé au gouvernement camerounais le
12 Août 1993. Suite à la reforme universitaire de janvier 1991,
elle devient Institut Universitaire de Technologie Fotso Victor de Bandjoun.
Elle fait partie aujourd'hui des établissements de l'Université
de Dschang et représente environ 15% de son effectif, soit environ 2000
étudiants.
Cet institut offre aux étudiants camerounais et
étrangers titulaires d'un Baccalauréat, plusieurs cycles de
formation à savoir:
- DUT (Diplôme Universitaire de Technologie),
- BTS (Brevet de Technicien Supérieur),
- Licence Technologique,
- Licence professionnelle,
- Académie Cisco.
S'agissant du cycle DUT, l'admission se fait sur concours et
requiert les diplômes de fin d'étude secondaire (Bac C, D, E, F,
etc.), pour une formation de 2 ans au terme de la quelle les étudiants
obtiennent le Diplôme Universitaire de Technologie (DUT) dans l'une des
filières suivantes :
- Electrotechnique (EL),
- Electronique (EN),
- Informatique de gestion (IG),
- Génie en télécommunication et
réseaux (GTR),
- Génie civil (GC),
- Maintenance industrielle et productive (MIP).
Concernant le cycle BTS, l'admission se fait sur étude
de dossier et entretien avec un jury à l'IUT- FV de Bandjoun et requiert
les diplômes de fin d'étude secondaire (BAC A, B, C, D, E, F, G
etc.). Pour une formation de 2 ans au terme de la quelle les étudiants
admis à l'examen national obtiennent le Brevet de Technicien
Supérieur dans l'une des filières suivantes :
- Comptabilité et gestion des entreprises (CGE),
- Action commerciale (AC),
- Secrétariat de direction (SD),
- Electronique (EN),
- Electrotechnique (EL),
- Génie civil (GC),
- Banque et finance (BF).
Concernant le cycle licence de technologie, l'admission se
fait sur étude de dossier et requiert un (BAC+2), et la formation
s'étend sur une année et est censurée par l'obtention
d'une Licence Technologique dans les filières suivantes :
- Génie électrique (GE) ;
- Informatique et réseaux (IR) ;
- Génie civil (GC) ;
- Ingénierie des réseaux et
télécommunications ;
- Maintenance industrielle et productique (MIP).
En ce qui concerne la licence professionnelle, l'admission se
fait sur étude de dossier et requiert un (BACC+2) ; La formation
s'étant sur une année et est marquée par l'obtention d'une
licence professionnelle dans les filières suivantes :
- Action commerciale (AC)
- Comptabilité et gestion des entreprises (CGE)
En somme, l'IUT-FV avec son administration entreprenante, des
enseignants dotés d'une conscience professionnelle et ses
étudiants bénéficiant de son lotissement prodigieux, a un
avenir vivant et prometteur. Pour compléter la formation, les
étudiants sont appelés à faire un stage académique
avec un temps définit en fonction de leur cycle de formation, permettant
ainsi de toucher du doigt les réalités du monde de l'emploi et de
pratiquer ce qui est pour la plupart du temps théorique. C'est dans
cette optique que j'ai effectué un stage dans la société
BUETEC-Broderie industrielle du Cameroun pour la période allant du 08
novembre au 23 Décembre 2011.
Sommaire
REMERCIEMENTS 2
AVANT-PROPOS 3
LISTE DES FIGURES 7
LISTE DES TABLEAUX 8
LISTE DES CHECK-LISTS 8
INTRODUCTION GENERALE 9
PARTIE I : PRESENTATION DE L'ENTREPRISE ET DU PROCESSUS DE
PRODUCTION 10
CHAPITRE I : PRESENTATION GENERALE DE L'ENTREPRISE 10
I-HISTORIQUE 10
II- IDENTIFICATION DE L'ENTREPRISE 11
III- ORGANIGRAMME DE L'ENTREPRISE 11
CHAPITRE II : DESCRIPTION DE LA CHAINE DE PRODUCTION 13
I- IVENTAIRE DES EQUIPEMENTS DE PRODUCTION 13
II- PROCESSUS DE PRODUCTION 14
PARTIE II : ETUDE DU CAHIER DE CHARGE 15
CHAPITRE I ETUDE SUR L'EXISTANT 15
I- ANALYSE DE L'EXISTANT 15
II- RESULTAT DE L'ANALYSE 16
CHAPITRE II: RECOMMANDATIONS 17
I- MAINTENANCE BASEE SUR LA FIABILITE 17
II- APPLICATION AUX EQUIPEMENTS DE PRODUCTION 18
1- ANALYSE DESCENDANTE STRUCTURELLE DES EQUIPEMENTS (ADS) 18
2- MISE SUR PIED D'UN OUTIL DE PRISE DE DECISION ET D'AIDE AU
DIAGNOSTIQUE 23
2-1) METHODOLOGIE DE L'AMDEC 23
2-2) PRINCIPE DE BASE 23
2- 3) COTATION DES RISQUES DE DEFAILLANCE SUR LES EQUIPEMENTS
24
2-4) APPLICATION DE L'AMDEC AUX EQUIPEMENTS 26
3- PLANIFICATION DES TACHES DE MAINTENANCE ET AMELIORATION DE LA
QUALITE
DES INTERVENTIONS 31
3-1) LES NIVEAUX DE MAINTENANCE 31
-2) PLANNING DE MAINTENANCE RECOMMANDE AUX EQUIPEMENTS 32
PARTIE III : SUGGESTIONS ET REMARQUES 47
CHAPITRE I : SUGGESTIONS 47
I- LES PROGICIELS DE GMAO : ANALYSE DES DIFF"RENTS
MODULES FONCTIONNELS 47
CHAPITRE II : REMARQUES 53
I- POSITIVES 53
II- NEGATIVES 53
CONCLUSION 54
BIBLIOGRAPHIE 55
ANNEXES 56
LISTE DES FIGURES
Figure 1 : Organigramme de l'entreprise 12
Figure 2 : Schéma du processus de production ..14
Figure 3 : Schéma du flux d'énergie ..14
Figure 4 : Etapes de la démarche MBF ..18
Figure 5 : ADS ECO ..19
Figure 6 : ADS ESSOREUSE 20
Figure 7 : ADS SECHOIR .21
Figure 8 : ADS COMPACTEUR 22
LISTE DES TABLEAUX
Tableau 1 : Inventaire des équipements de production
|
13
|
Tableau 2 : Actions à engager en fonction de la
criticité d'un défaut
|
..26
|
Tableau 3 : AMDEC ECO
|
27
|
Tableau 4 : AMDEC ESSOREUSE
|
28
|
Tableau 5 : AMDEC SECHOIR
|
29
|
Tableau 6 : AMDEC COMPACTEUR
|
30
|
Tableau 7 : Planning mensuel de maintenance ECO
|
33
|
Tableau 8 : Planning annuel de maintenance ECO
|
..34
|
Tableau 9 : Planning mensuel de maintenance SECHOIR
|
..35
|
Tableau 10 : Planning annuel de maintenance SECHOIR
|
36
|
Tableau 11 : Planning mensuel de maintenance COMPACTEUR
|
..37
|
Tableau 12 : Planning annuel de maintenance COMPACTEUR
|
38
|
Tableau 13 : Planning mensuel de maintenance ESSOREUSE
|
39
|
Tableau 14 : Planning annuel de maintenance ESSOREUSE
|
.40
|
Tableau 15 : Planning hebdomadaire de maintenance CHAUDIERE ET
COMPRESSEUR .41
LISTE DES CHECK-LISTS
Check-list01 : ECO-6-2T/ECO-38-1T
|
42
|
Check-list02: ESSOREUSE
|
43
|
Check-list03: SECHOIR
|
44
|
Check-list04: COMPACTEUR .
|
.45
|
Check-list05 : CHAUDIERE ET COMPRESSEUR
|
46
|
Rédigé et présenté par :
Roméo KAMWA KAMTO Elève ingénieur MIP
|
Page 8
|
INTRODU~TION 6IENIERALIE
Les entreprises sont de plus en plus sensibilisées
à l'importance des pertes par les défaillances accidentelles des
systèmes de production. Nous somme de plus en plus conscients qu'elle
peut contribuer d'une manière significative à la performance
globale de l'entreprise. La complexité des mécanismes de
dégradation des équipements a fait en sorte que la durée
de vie de ces derniers soit toujours traitée comme une variable
aléatoire. De plus, on a constaté que l'absence de donnés
fiables et d'outils efficaces de traitement de ces données a
réduit la fonction maintenance à des taches de maintenance
corrective, et par le fait même, à une fonction dont les
coûts ne cessent d'augmenter et dont la contribution à la
performance de l'entreprise n'est pas évidente. L'entreprise
BUETEC-Broderie se voit donc dans l'obligation d'assurer sa mise à
niveau par l'optimisation de ses moyens humains, techniques et
matériels, en vue d'assurer sa compétitivité dans un
contexte ou seuls les plus performants seront viables. Cette
compétitivité ne se repose pas en terme de production seulement,
mais aussi en terme de qualité de gestion de son service de maintenance.
Aujourd'hui, BUETEC est très conscient de ce problème, pour cela,
ses dirigeants nous ont confié cette mission
« l'amélioration de la politique de
maintenance sur les équipements de production », dans le
but d'apporter des améliorations au niveau de l'analyse des
défaillances, des diagnostique, de qualité des interventions,
mais aussi au niveau des méthodologies de travail.
Ce mémoire sera à cet effet structuré en
trois parties : la première pour la présentation de l'entreprise
d'accueil et son processus de production, la deuxième pour l'analyse de
l'existant et les recommandations à suivre, et la dernière partie
pour les suggestions et les remarques.
PARTIE I : PRESENTATION DE L~ENTREPRISE ET DU PROCESSUS
DE PRODUCTION
C11APITRE I : PRESENTATION GENERALE DE L~ENTREPRISE
I-11ISTORIQUE
Fondé en 1998, BUETEC, s'est imposé comme leader
dans le domaine de broderie industrielle au Cameroun et en Afrique centrale.
L'équipe de BUETEC dispose aujourd'hui d'une expertise dans le domaine
textile ;
Le polo et le tee-shirt étant devenus des outils de
communication de premier plan, de véritable signe d'expression pour les
entreprises, des vecteurs d'identité , BUETEC fabrique des polos et
tee-shirts à travers un complexe industriel, repartis sur deux sites,
représentant plus de 5000m2 implanté à Douala
(Logpom et bassa-zones industrielle), dans la pure tradition du design textile,
selon des normes environnementales strictes. Pour BUETEC l'avenir passe par
-une exigence du confort et du produit parfaitement adapté à la
demande et aux exigences des entreprises locale et de la sous région,
comme à l'international. -Une démarche qualité fruit de 10
ans d'expérience dans le secteur textile et d'un savoir faire hors du
commun en Afrique centrale. -Une volonté d'innover tant en revendiquant
le droit à la différence. Une différence d'excellente
technique, technologique et créative. Capacité :2500 broderies
par jour 10 000 marquages par jour 6000 polos et tee-shirts par jour.
La production est répartie sur 02 sites, comprenant une
unité de tricotage, une usine de teinture, un atelier de confection, des
unités de sérigraphie, une unité de coupe et de la
broderie industrielle. BUETEC met à la disponibilité de ses
clients une collection de polos et de tee-shirts parfaitement adaptée
à la communication d'entreprise et à l'évènementiel
.Pour compléter son service aux clients, l'entreprise fournit
également d'autres supports publicitaires, tels que les casquettes, les
serviettes, les stylos....
En dix ans de travail sur la qualité et la satisfaction
de la clientèle, BUETEC s'est taillé une réputation
enviable sur le marché et offre des services permettant de
répondre aux besoins de sa clientèle actuelle et future.
11- IDENTIFICATION D1 L' 1
BUETEC est une entreprise dont la direction commerciale est
située à AKWA et elle possède 02 sites d'usines : l'une
à Logpom et l'autre à Bassa.
Raison sociale : BUETEC
Date de création : 1998
Forme juridique : SARL (société à
responsabilité limité)

Logo:
Siege social: BP 1919 DOUALA Akwa Cameroun
TEL :(237)33 43 3936
FAX (237)33 43 70 19
Capital social : 130 000 0000 Fcfa
III- ORGANIGEAMME DE L'ENTREPELSE

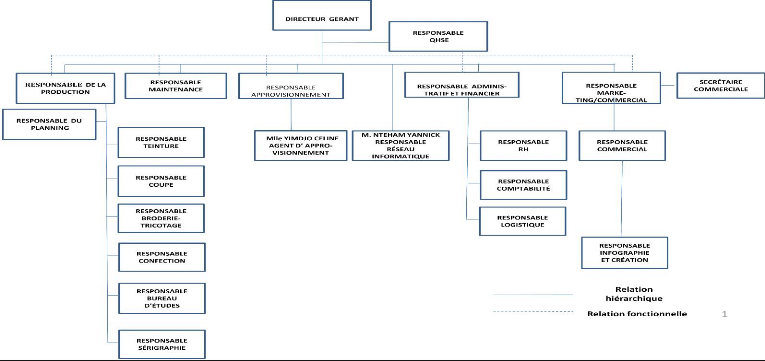

CHAPITRE II : DESCRIPTION DE LA CHAINE DE
PRODUCTION
I- IVENTAIRE DES EQUIPEMENTS DE PRODUCTION
1- Définition
L'inventaire des biens d'un site est une
nomenclature codifiée et quantifiée de tous les
équipements liés à la production.
La codification quant-a-elle permet de :
- Identifier un équipement donné
au sein de l'usine, sa famille, sa position
- Le regroupement de tous les équipements
de même famille et de secteur différent.
- L'identification des lignes de maintenance
formées des équipements de même durée de
fonctionnement.
- L'intervention à l'équipement de
toute nature des actions de maintenance s'y rapprochant.
2- Inventaire
MACHINES
|
CODES
|
FONCTIONS
|
Chaudière
|
C-01
|
Alimenter les machines en vapeur d'eau
|
Compresseur
|
C-02
|
Produire de l'air sous pression
|
Visiteuse
|
M-01
|
Contrôler les défauts de qualité sur le
tissu à l'entrée et a la sorti de l'usine
|
ECO-38-1T
|
M-02
|
Teinter le tissu
|
ECO-6-2T
|
M-03
|
Teinter le tissu
|
ESSOREUSE
|
M-04
|
Essorer le tissu
|
SECHOIR
|
M-05
|
Sécher et rétrécir le tissu
|
COMPACTEUR
|
M-06
|
Repasser le tissu
|
Tableau 1 : inventaire des
équipements
II PROCESSUS DE PRODUCTION
1- Description
La production à l'usine BASSA suit une chaine purement
linéaire : Les ballots de tissus arrivent dans le site comme
matière première, passe à la visiteuse
pour un contrôle de la qualité du tissu a l'arrivé, passe
ensuite dans la machine ECO-38/ECO-6 en fonction de la masse,
pour le processus de teinture, passe après la teinture à
l'ESSOREUSE pour débarrasser le tissu mouillé de
l'eau ; le tissu restant mouillé, est conduit au
SECHOIR pour le rendre sec et le rétrécir ;
Enfin, le tissu sorti du séchoir sera repassé par
l'intermédiaire de la machine COMPACTEUR ; le tissu
sorti de cette machine sera emballé et considéré comme
produit fini de l'usine.
2- Schéma du processus
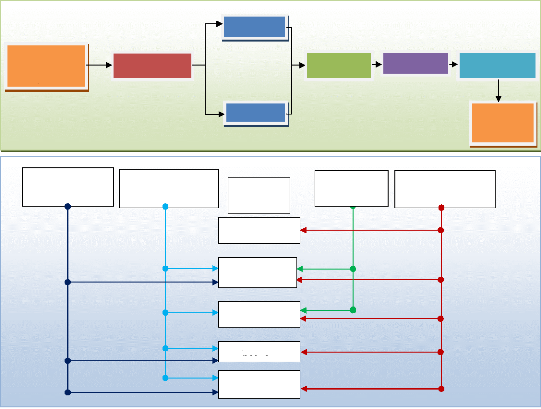
ECO-38-
COMPACTEU
VISITEUSE
ECO-6-2T
Arrivé et pesé des
ESSOREUS SECHOIR
Pesé et SORTIE
Machines
Visiteuse
ECO-x-xT
Essoreuse
Séchoir
Compacteur
Alimentation en vapeur
Alimentation en Air comprimé
Alimentation en Eau
Alimentation en énergie électrique
Figure3 : Schéma du flux
d'énergie
PARTIE II : ETUDE DU CAHIER DE CHARGE CHAPITRE I ETUDE
SUR L'EXISTANT
I- ANALYSE DE L'EXISTANT
La réussite d'un tel projet repose en premier temps sur la
définition des objectifs, la clarté et la compréhension du
sujet. Pour cela, l'analyse de l'état des lieux s'avère
très importante pour la définition réelle du travail
à faire. C'est dans cette rubrique que nous allons cerner les points
malveillants de la politique mise sur pied.
Cet état des lieux concernera essentiellement les 04
domaines suivants :
- La politique de maintenance existant : Dans
cette rubrique nous allons évaluer l'efficacité de la
politique de maintenance mise sur pied et de son effectivité.
· Quelle est la politique de maintenance mise sur pied ?
· Existe il des outils d'aides au diagnostique ?
- Le plan de maintenance existant : il sera
question ici pour nous de suivre l'exécution du plan de maintenance
existant.
· Est-il effective ?
· Y a-t-il un suivit ?
- La planification des travaux de maintenance :
cette rubrique couvre l'évolution et l'organisation des travaux
de maintenance suivant un échéancier.
· Les périodicités des actions de maintenance
préventive sont-elles définies ?
· Y'a-t-il une planification calendaire de ces actions ?
- La gestion des interventions. Il s'agit
là du traitement des informations en ce qui concerne les
équipements (fiches technique, modification d'équipement)
· Existe-t-il un système de gestion des
interventions sur l'équipement ?
· Les interventions se préparent-elles à
l'avance ?
Ces interrogations et bien d'autres faits auprès des
conducteurs de machine nous ont permis d'analyser l'état des lieux. Cet
analyse nous permettra donc de définir les points censives de notre
travail et de mieux répartir nos efforts sur les taches
concernées.
II- RESULTAT DE L'ANALYSE
Au terme de notre analyse, il ressort que l'entreprise a un
plan de maintenance mise sur pied mais a comme politique de maintenance «
la maintenance basé sur la curatif ». Le plan de maintenance mise
sur pied n'est pas effectif et bien que la maintenance soit basée sur le
curatif, elle n'est pas suivit.
A cet effet, la charge de notre travail sera de :
> Mettre sur pied des méthodes pour l'application
d'une politique de maintenance basé sur la fiabilité
(MBF)
> La planification des actions de maintenance
préventive
> La constitution des fiches de suivit technique des
équipements et de gestion des interventions.
CHAPITRE II: RECOMMANDATIONS
I- MAINTENANCE BASEE SUR LA FIABILITE
Nous présenterons ici la méthodologie
employée afin de mettre en place notre politique de maintenance
préventive.
1. Justification du choix
Compte tenu du fait que nos équipements se trouvent
dans leur phase de vie utile, nous avons opté pour une politique de
maintenance préventive systématique. Pour élaborer le
planning de maintenance préventive, nous avons opté pour la
méthode MBF (Maintenance Basée sur la Fiabilité).
C'est une méthode reposant essentiellement sur la
connaissance précise du comportement fonctionnel et du dysfonctionnement
des systèmes.
2. Principes de la MBF
L'ambition de la MBF est de guider la démarche
industrielle dans une voie d'augmentation des moyens organisationnels,
techniques et d'informations. Ici, la maintenance est construite par rapport
à des critères fixés par l'entreprise. C'est un outil
permettant d'optimiser les actions de maintenance programmées. Les
critères pris en compte sont généralement la
sécurité, la disponibilité (tenant compte d'un consensus
fiabilitémaintenabilité) et le coût de maintenance.
Lorsqu'il s'agit de produits fabriqués, la notion de qualité est,
elle aussi, prise en compte.
3. Objectifs de la MBF
Les objectifs de la MBF sont :
n Améliorer la disponibilité des
équipements sélectionnés comme critiques par leur
influence sur la sécurité, la qualité et leur impact sur
le flux de production ;
n maîtriser les coûts par l'optimisation du plan de
maintenance préventive ;
n changer la politique de maintenance pour des actions de
maintenance préventive contrôlées.
4. Etapes de la démarche MBF Les
étapes de la démarche MBF sont :

1. Sélection des sites et des équipements
critiques
Liste des équipements sélectionnés

2. Analyse descendante structurelle des équipements
sélectionné
Décomposer l'équipement en sous ensemble
maintenable de façon hiérachique

5. analyse du retour d'expérience

3. Analyse des défaillances fonctionnelles
|
|
Liste des défaillances (AMDEC) Liste des causes de
défaillances

4. Sélection des actions de maintenance
préventive
|
Liste des actions préventives
Mise en oeuvre du plan de maintenance
Figure 4 : Etapes de la démarche
MBF
II- APPLICATION AUX EQUIPEMENTS DE PRODUCTION
Cette méthode reposant essentiellement, sur la
connaissance du matériel, nous avons établi l'analyse descendant
structurelle (ADS) des équipements de l'usine. Cette partie ressort le
principe de fonctionnement du système concerné et l'ensemble des
éléments maintenable du système de façon
hiérarchique.
1- ANALYSE DESCENDANTE STRUCTURELLE DES EQUIPEMENTS
(ADS)
ADS ECO
ECO
Système de commande
Bac de service
Système de circulation
Chambre de stockage
Panneau de contrôle pneumatique
Pompe d'alimentation de la matière colorante
Poulie
Moteur- réducteur
Filtre
Valve de solénoïde pilote
Potentio mètre
Valve de réduction
Séparateur
Figure5: ADS ECO
Courroie
Bielle
Manivelle
L'axe de la manivelle
Limiteur de couple
Roulements
Balais
Collecteur
Echangeur de chaleur
Sonde de température
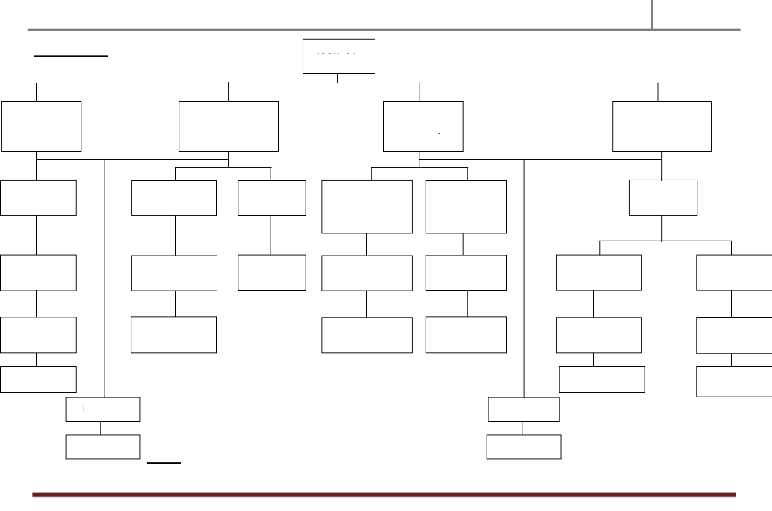
Rédigé et présenté par :
Roméo KAMWA KAMTO Elève ingénieur MIP Page 20
ESSOREUSE
ADS ESSOREUSE
Rouleaux
Rouleaux
Roulements
Roulements
Figure6: ADS ESSOREUSE
Amélioration de la politique de maintenance
appliquée au,équipements de production
2011
Dispositif d'essorage
Dispositif d'entrainement du tissu à la sortie
Moteur ASS
|
|
|
Moteur ASS
|
|
Boite de commande
|
|
Moteur d'entrainement des rouleaux
|
|
Système de commande des rouleaux
|
|
|
Moteur ASS
|
|
|
|
|
|
|
|
|
|
|
|
|
Capteurs
|
|
|
|
|
|
|
|
|
|
|
|
|
|
|
|
Cuvette de
|
Bobines
|
Roue dentée
|
Distributeur
|
Système poulie
|
Système
|
déroulement
|
|
d'entrainement
|
|
|
|
|
|
pneumatique
|
|
|
courroie
|
|
d'engrenage
|
|
|
|
|
|
|
|
|
|
|
|
|
|
|
|
|
|
|
|
|
Poulie
|
Ressorts
|
Chaine
|
Vérin pneumatique
|
Poulie
|
Roues dentées
|
|
|
|
|
|
|
|
|
|
|
|
|
|
|
|
|
|
Courroie
|
Courroie
|
|
Chaines
|
Dispositif de déroulement du tissu
Dispositif d'entrainement du tissu à l'essorage
ADS du séchoir
SECHOIR
Système de chauffage
Système d'entrainement/tressage
Système de commande
Coffret de commande
Variateur de fréquence
Moteur asynchrone
Pignons
Roulements
Engrenages
Aspirateur
Filtre
|
|
|
|
|
|
|
|
Chaine
|
Pignons
|
Echangeur thermique
|
|
|
|
|
|
|
|
|
Chaine
|
Ventilateur de
|
Figure7 : ADS
|
SECHOIR
|
|
|
circulation
|
Table de réception
|
|
Moteur ASS
|
ADS COMPACTEUR
Compacteur
Système d'engagement
Système d'entrainement e et de tressage
Système de chauffage
Moteur ASS
Rouleau d'entrainement
Box à vapeur
Tapis roulants
Distributeur pneumatique
Echangeur thermique
Rouleaux d'entrainement
|
Vérin
|
|
Vérin
|
Poulies
|
|
|
|
|
Moteur
|
|
Système
|
|
Système
|
Pignons
|
|
|
|
|
pneumatique
|
|
pneumatique
|
|
|
|
|
ASS
|
|
poulie
|
|
d'engrainage
|
|
|
|
|
|
|
Courroies
|
|
|
|
|
|
|
|
|
|
|
|
|
|
Roulements
|
Capteur
|
Chaines
|
Vis sans frein
|
Poulie Pignons
|
Capteurs
|
Figure 8 : ADS Compacteur
|
Roulements
|
|
Roulements
|
|
Capteur
|
|
Courroie
|
|
Chaine
|
|
|
|
|
|
|
|
2- MISE SUR PIED D'UN OUTIL DE PRISE DE DECISION ET D'AIDE
AU DIAGNOSTIQUE
2- 1) METHODOLOGIE DE L'AMDEC
L'AMDEC étymologiquement est l'analyse des modes de
défaillances, de leurs effets et de leurs criticités. C'est une
méthode d'analyse de la fiabilité qui permet de recenser les
défaillances dont les conséquences affectent le fonctionnement
d'un système.
Il existe plusieurs types d'AMDEC à savoir : -
L'AMDEC produit ;
- L'AMDEC processus ;
- L'AMDEC machine : qui analyse de la
conception et / ou l'exploitation d'un moyen ou d'un équipement de
production pour améliorer la sûreté de
fonctionnement (sécurité, disponibilité
fiabilité, et maintenabilité) de celui-ci.
2-2) PRINCIPE DE BASE
Il s'agit d'une analyse critique consistant à
identifier de façon inductive et systématique les risques de
dysfonctionnement des machines puis à en rechercher les origines et
leurs conséquences. Elle permet de mettre en évidence les points
critiques et de proposer des actions correctives adaptées. Ces actions
peuvent concerner aussi bien la conception des machines étudiées
que leur fabrication, leur utilisation ou leur maintenance. C'est
essentiellement une méthode préventive.
L'AMDEC est une méthode participative. Fondée
sur la mise en commun des expériences diverses et des connaissances de
chaque participant, elle trouve toute son efficacité dans sa pratique en
groupe de travail pluridisciplinaire. La composition du groupe de travail entre
d'ailleurs pour une large part dans le succès d'une étude AMDEC.
Cette réflexion en commun est source de créativité. Elle
favorise les échanges techniques entre les différentes
équipes d'une entreprise, voire entre clients et fournisseurs. Elle
permet l'évolution des connaissances et contribue même à la
formation technique des participants.
L'AMDEC machine est essentiellement destinée à
l'analyse des modes de défaillance d'éléments
matériels (mécaniques, hydrauliques, pneumatiques,
électriques; électroniques...). Elle peut aussi s'appliquer aux
fonctions de la machine, au stade préliminaire de sa conception par
exemple.
Cependant, l'AMDEC n'est pas un outil universel. Ainsi, la
méthode ne permet pas de prendre en compte les combinaisons de plusieurs
défaillances. D'autres méthodes peuvent alors être
utilisées en complément (arbres de défaillance,
méthode de combinaison de pannes...). De plus, les conséquences
des erreurs humaines sont mal prises en compte. Mais l'une des missions propre
de la méthode AMDEC est de pouvoir également quantifier
l'importance du risque lié à chaque effet. Pour ce fait,
trois critères sont ainsi définis.
2- 3) COTATION DES RISQUES DE DE~AILLANCE SUR LES
EQUIPEMENTS
L'analyse des modes de défaillance et leur
évaluation seront menées sur la base de trois critères
:
· Fréquence (F)
· Gravité (G)
· Non détection (D)
1. La fréquence
La fréquence est le reflet de l'exposition de
l'équipement au danger et donc de la probabilité des
défaillances. Elle dépend de la fréquence de
l'activité et des circonstances de l'activité.
L'appréciation de la fréquence tient compte :
· de la fréquence de l'exposition des machines au
danger du (l'une peut s'avérer plus dangereuse que l'autre, donc sa note
sera plus sévère)
· des mesures de prévention déjà
existantes.
Ainsi, quatre niveaux de fréquence sont
retenus :
1 : rare : < 25% du temps d'exposition
2 : peu fréquent : 25% < Temps
exposition < 50%
3 : fréquent : 50% < Temps exposition
< 75%
4 : très fréquent : > 75% du
temps d'exposition
2. La gravité
La gravité reflète l'importance des
conséquences de la défaillance si celui-ci se produit.
Quatre niveaux de gravité sont retenus
:
1 : bénin = défaillance sans
influence sur la production
2 : sérieux = défaillance avec
influence sur la production, mais négligeable
3 : grave = défaillance avec une
portée grande sur la production
4 : très grave = avec arrêt total
de la production
L'évaluation de la gravité doit être
modulée par les mesures de prévention déjà
existantes.
3. La non détection
C'est la probabilité que la cause ou le mode de
défaillance supposés apparus provoquent l'effet le plus grave,
sans que la défaillance ne soit détectée au
préalable.
Quatre niveaux de non détection sont retenus
1 : A coup sur détection facile de la
défaillance
2 : Possible = panne facilement décelable, mais moyennant
action première de l'opérateur
3 : Difficile= signes avant coureur difficilement
décelable
4 : Très difficile = défaillance quasi
indétectable, aucun signe avant coureur
La criticité est donc C=F*G*D
De par sa démarche, une analyse AMDEC doit commencer par
une analyse fonctionnelle du système, afin d'identifier
les fonctions des différents sous-systèmes et du système
proprement dit.
NIVEAU DE CRITICITE
|
ACTIONS CORRECTIVES A ENGAGER
|
|
1 < C < 10
Criticité négligeable
|
Aucune modification de conception Maintenance corrective
|
|
10 = C < 20
Criticité moyenne
|
Amélioration des performances de l'élément
Maintenance préventive systématique
|
|
20 = C < 40 Criticité
élevée
|
Révision de la conception du sous-ensemble et du choix des
éléments
Surveillance particulière, maintenance préventive
conditionnelle
prévisionnelle
|
/
|
40 = C < 64 Criticité
interdite
|
Remise en cause complète de la conception
|
|
Tableau2 : Actions corrective à
engager en fonction de la criticité de l'équipement
2-4) APPLICATION DE L'AMDEC AUX EQUIPEMENTS
L'AMDEC est parfaitement justifiée lorsqu'aucun
historique concernant l'installation n'est disponible (en particulier pour les
machines neuves ou de conception récente). Il faut alors pouvoir
prédire les pannes susceptibles d'affecter le fonctionnement de la
machine
AMDEC ECO
AMDEC : Analyse des Modes de Défaillance de leur
Effets et de leur Criticités
|
Système : ECO
|
Eléments
|
Fonction
|
Modes de défaillance
|
Effets
|
Cause probable
|
Détection
|
Criticité
|
Actions correctives
|
F
|
G
|
D
|
C
|
Pompe d'alimentation
|
Assurer l'alimentation en matière colorante
|
Pas d'alimentation ou
débit d'alimentation faible
|
Alimentation anormale
|
Vieillissement
|
Visuel
|
1
|
4
|
2
|
8
|
Remplacer
|
Mort subite
|
Visuel
|
1
|
4
|
3
|
12
|
Remplacer
|
Moteur asynchrone
|
Assure la transformation de l'énergie
|
Le moteur ne tourne pas ou il est bloqué
|
N'assure pas la transmission du mouvement aux systèmes
concernés
|
Pas d'alimentation
|
Visuel
|
1
|
4
|
3
|
12
|
Alimenter en énergie
|
Rotor bloqué
|
Tachymètre
|
1
|
4
|
3
|
12
|
Lubrifier les roulements du moteur
|
Balais défectueux
|
|
1
|
4
|
3
|
12
|
Changer les balais
|
Surintensité
|
Multimètre
|
1
|
4
|
3
|
12
|
Le rebobiner
|
Système poulie courroie
|
Entrainer le tissu dans le bac de service
|
Courroie coupée
|
Pas d'entrainement du tissu
|
Vieillissement de la courroie
|
Visuel
|
1
|
4
|
1
|
4
|
Remplacer la courroie
|
Poulie rongée
|
Visuel
|
1
|
4
|
2
|
8
|
Changer la poulie
|
Filtre
|
Eliminer les impuretés solides ou liquides
avant la circulation dans le bac de service
|
Bouché ou colmaté
|
Laisse passer les impuretés
|
Mauvais entretient
|
Visuel
|
1
|
3
|
2
|
6
|
Nettoyer ou remplacer
|
Echangeur de chaleur
|
Permet la dissipation de la chaleur des vapeurs.
|
Ne chauffe pas assez
|
Temps de chauffage lent
|
Manque d'entretient
|
Visuel
|
1
|
3
|
3
|
9
|
Dépiécer et nettoyer
|
Sonde de température
|
Détermine le degré de température
dans l'échangeur
|
Affiche de données erronées
|
Conduit aux mauvais résultats
|
Vieillissement
|
visuel
|
1
|
3
|
3
|
9
|
Remplacer
|
Tableau3 : AMDEC ECO
AMDEC ESSOREUSE
AMDEC : Analyse des Modes de Défaillance de leur
Effets et de leur Criticités
|
Système : ESSOREUSE
|
Eléments
|
Fonction
|
Modes de défaillance
|
Effets
|
Cause probable
|
Détection
|
Criticité
|
Actions correctives
|
F
|
G
|
D
|
C
|
Moteur asynchrone
|
Assure la transmission du mouvement de rotation
aux systèmes mobiles
|
Ne tourne pas ou grillé
|
N'assure pas la transmission du mouvement aux systèmes
concernés
|
Pas d'alimentation
|
Visuel
|
1
|
4
|
3
|
12
|
Alimenter en énergie
|
Rotor bloqué
|
tachymètre
|
1
|
4
|
3
|
12
|
Graisser les roulements du moteur
|
Balais défectueux
|
multimètre
|
1
|
4
|
3
|
12
|
Changer les balais
|
Surintensité
|
multimètre
|
1
|
4
|
3
|
12
|
Rebobiner le moteur
|
Cuvette de déroulement
du tissu
|
Déroule le tissu et l'envoi vers les bobines
d'entrainement
|
Système bloqué
|
Pas de déroulement du tissu
|
Moteur défectueux
|
Visuel/ multimètre
|
1
|
4
|
3
|
12
|
Intervenir sur moteur
|
Courroie coupé
|
Visuel
|
1
|
3
|
3
|
9
|
Remplacer la courroie
|
Partie rotative grippé
|
visuel
|
1
|
3
|
2
|
6
|
Lubrifier
|
Bobines d'entrainement
|
Entraine le tissu vers le système d'essorage
|
Ne tourne pas
|
Pas d'essorage
|
Moteur d'entrainement défectueux
|
Visuel
|
1
|
4
|
3
|
12
|
Intervenir sur le moteur
|
Ressorts
|
Assure l'ouverture et la fermeture des
bobines d'entrainement
|
Ne se comprime plus ou cassé
|
Pas d'entrainement du tissu
|
Vieillissement
|
Visuel
|
1
|
4
|
3
|
12
|
Changer
|
Capteurs
|
|
|
|
|
|
1
|
4
|
3
|
12
|
Remplacer
|
Distributeurs pneumatique
|
Distribue l'air dans les canalisations qui conduisent aux
chambres du vérin
|
Ne fonctionne pas
|
Pas d'alimentation des circuits pneumatique
|
Vieillissement
|
|
1
|
4
|
2
|
8
|
Remplacer
|
Vérins
|
Assure l'ouverture et la fermeture des
rouleaux d'essorage
|
Ne réagit pas à la commande
|
Pas d'essorage
|
Pas d'alimentation en air
|
Visuel
|
1
|
2
|
2
|
4
|
Vérifier l'alimentation en air
|
Vérin défectueux
|
Visuel
|
1
|
4
|
3
|
12
|
Remplacer
|
Tableau4 : AMDEC ESSOREUSE
AMDEC SECHOIR
AMDEC : Analyse des Modes de Défaillance de leur
Effets et de leur Criticités
|
Système : SECHOIR
|
Eléments
|
Fonction
|
Modes de défaillance
|
Effets
|
Cause probable
|
Détection
|
Criticité
|
Actions correctives
|
F
|
G
|
D
|
C
|
Moteur asynchrone
|
Assure la transformation de l'énergie
|
Ne tourne pas ou grillé
|
N'assure pas la transmission du mouvement aux systèmes
concernés
|
Pas d'alimentation
|
Visuel
|
1
|
4
|
3
|
12
|
Alimenter en énergie
|
Rotor bloqué
|
tachymètre
|
1
|
4
|
3
|
12
|
Graisser les roulements du moteur
|
Balais défectueux
|
multimètre
|
1
|
4
|
3
|
12
|
Changer les balais
|
Surintensité
|
multimètre
|
1
|
4
|
3
|
12
|
Rebobiner le moteur
|
Système d'engrenage
|
Entrainer le tissu dans la chambre de chauffage et vers
la sortie
|
Système bloqué
|
Pas d'entrainement du tissu
|
Chaine défectueuse
|
Visuel
|
1
|
4
|
3
|
12
|
Remplacer la chaine
|
Pignons grippés
|
Visuel
|
1
|
3
|
3
|
9
|
Lubrifier le système
|
Filtre
|
Eliminer les impuretés solides ou liquides
dans l'air aspiré
|
Bouché ou colmaté
|
Augmentation du temps de séchage
|
Mauvais entretient
|
Visuel
|
1
|
3
|
2
|
6
|
Le nettoyer
|
Echangeur de chaleur
|
Permet la dissipation de la chaleur des vapeurs.
|
|
N'assure pas le chauffage en temps réel
|
Manque d'entretient
|
Visuel
|
1
|
4
|
3
|
12
|
Le nettoyer
|
Sonde de température
|
Détermine le degré de température
dans l'échangeur
|
Affiche de données erronées
|
Conduit aux mauvais résultats
|
Vieillissement
|
visuel
|
1
|
4
|
3
|
12
|
Le remplacer
|
Tableau5 : AMDEC SECHOIR
AMDEC COMPACTEUR
AMDEC : Analyse des Modes de Défaillance de leur
Effets et de leur Criticités Système : COMPACTEUR
|
Eléments
|
Fonction
|
Modes de défaillance
|
Effets
|
Cause probable
|
Détection
|
Criticité
|
Actions correctives
|
F
|
G
|
D
|
C
|
Moteur asynchrone
|
Assure la transmission du mouvement de rotation
aux systèmes mobiles
|
Ne tourne pas ou grillé
|
N'assure pas la transmission du mouvement aux systèmes
concernés
|
Pas d'alimentation
|
Visuel
|
1
|
4
|
3
|
12
|
Alimenter en énergie
|
Rotor bloqué
|
tachymètre
|
1
|
4
|
3
|
12
|
Graisser les roulements du moteur
|
Balais défectueux
|
multimètre
|
1
|
4
|
3
|
12
|
Changer les balais
|
Surintensité
|
multimètre
|
1
|
4
|
3
|
12
|
Rebobiner le moteur
|
Distributeur pneumatique
|
Distribue de l'air dans les chambres de vérin et
|
N'assure plus sa fonction requise
|
Pas de chauffage, le vérin ne travail pas
|
Vieillissement
|
Visuel
|
1
|
4
|
3
|
12
|
Changer
|
Vérin pneumatique
|
Assure la mise en position haute ou basse de la plaque ;
assure la tension du tapi de tissu
|
Ne se déplace pas à la commande
|
La plaque ne se mouvemente pas à la commande ;le
tapis
|
Pas d'alimentation en air
|
visuel
|
1
|
2
|
3
|
6
|
Alimenter en air
|
Vérin défectueux
|
Visuel
|
1
|
4
|
3
|
12
|
Remplacer
|
Echangeur de chaleur
|
Assure la conduction de chaleur des vapeurs au tissu
|
Ne chauffe pas le tissu
|
Le repassage peu effectif
|
Absence de vapeur
|
Visuel
|
1
|
4
|
3
|
12
|
Voir l'alimentation en vapeur
|
Rouleaux
|
Entraine le tissu
|
Ne tourne pas
|
Pas de repassage
|
Défaut du système poulie courroie
|
visuel
|
1
|
4
|
3
|
12
|
Intervenir sur le système
|
Défaut du système d'engrainage
|
Visuel
|
1
|
4
|
3
|
12
|
Intervenir sur le système
|
Vis sans fin
|
Assure la descente et la monté de la table de
réception
|
bloqué
|
Pas de mouvement de la table
|
Manque d'entretien
|
Visuel
|
1
|
4
|
3
|
12
|
Graisser
|
Système poulie courroie
|
Transmet le mouvement de rotation aux rouleaux
|
Ne fonctionne pas
|
Pas de mouvement des rouleaux
|
Courroie coupée
|
Visuel
|
1
|
4
|
3
|
12
|
Remplacer
|
Système d'engrainage
|
Transmet par engrainage le mouvement aux rouleaux
|
bloqué
|
Pas de mouvement des rouleaux
|
Chaine coupé
|
Visuel
|
1
|
4
|
3
|
12
|
remplacer
|
Capteurs
|
Détecte les défauts, la position du tapis, la
présence du tissu et la position de la table.
|
Ne détecte pas le signal
|
Mauvais repassage ou destruction de la vis
|
Mauvais câblage
|
Multimètre
|
1
|
4
|
3
|
12
|
Retoucher le câblage
|
Capteur défectueux
|
Visuel
|
1
|
4
|
3
|
12
|
Changer
|
Tableau6 : AMDEC COMPACTEUR
- PLANIFICATION DES TACHES DE MAINTENANCE ET AMELIORATION DE LA
QUALITE DES INTERVENTIONS
Dans cette partie, il serrait question pour nous de d'organiser
le travail de maintenance et la préparation des ordonnancements. C'est
une répartition annuelle des tâches de maintenance
préventives à exercer sur les équipements concernés
au moment opportun pour assurer sa bonne disponibilité. Pour ce fait, il
sera intéressant pour nous de connaitre quelque notion en ce qui
concerne les niveaux de maintenance.
-1) LES NIVEAUX DE MAINTENANCE
Pour mettre en oeuvre une organisation efficace de la maintenance
et prendre des décisions comme gestionnaire dans des domaines tel que la
soutrétance le recrutement de personnel approprié..., Les niveaux
de maintenance sont définis en fonction de la complexité des
travaux. L'AFNOR identifie 5 niveaux de maintenance dont en précise le
service:
- NIVEAU 1:
Réglage simple prévu par le constructeur ou le
service de maintenance, au moyen d'élément accessible sans aucun
démontage pour ouverture de l'équipement. Ces interventions
peuvent être réalisées par l'utilisateur sans outillage
particulier à partir des instructions d'utilisation ou des instructions
reçues du responsable de maintenance.
- NIVEAU 2:
Dépannage par échange standard des
éléments prévus à cet effet et d'opération
mineure de maintenance préventive, ces interventions peuvent être
réalisées par un technicien habilité ou l'utilisateur de
l'équipement dont la mesure ou ils ont reçu une formation
particulière.
- NIVEAU 3:
Identification et diagnostique de panne suivit
éventuellement d'échange de constituant, de réglage et
d'étalonnage général. Ces interventions peuvent être
réalisées par un technicien qualifié ou
spécialisé sur place ou dans un local de maintenance à
l'aide de l'outillage prévu dans des instructions de maintenance de
l'entreprise.
- NIVEAU 4:
Travaux importants de maintenance corrective ou préventive
à l'exception de la rénovation et de la reconstruction. Ces
interventions peuvent être réalisées par une
équipe disposant d'un encadrement technique très
spécialisé et des moyens importants adaptés à la
nature de l'intervention.
- NIVEAU 5:
Travaux de rénovation, de reconstruction ou de
réparation importante confiée à un atelier central de
maintenance ou une entreprise extérieure prestataire de service.
-2) PLANNING DE MAINTENANCE RECOMMANDt AUX tQUIPEMENTS
Ce planning a été établi en fonction de
l'inventaire des interventions du plan de maintenance existant et se veux
être modifié au fur et à mesure que nécessité
s'impose. Pour le suivit de ce planning, l'ordre d'intervention peut être
donné par le service maintenance au moment opportun ou tout simplement
en fonction du temps de maintenance, des check-lists qui suivent ces planning
seront remplies et permettra ainsi au service de maintenance de suivre
l'évolution du planning.
Pour ce qui est de l'amélioration de la qualité
des interventions et du suivit technique des équipements, des fiches
techniques que vous retrouverez en annexe sont établies dans le souci de
satisfaire à ces besoin ; Notamment :
- une fiche de demande d'intervention qui sera
mise à la disposition des conducteurs machine pour faire appel au
service de maintenance pour un disfonctionnement constaté ou tous autres
constats.
- une fiche d'analyse de la défaillance
qui sera remplie par un technicien ou un responsable de maintenance pour un
diagnostique et détermination de l'élément
défaillant.
- Une fiche d'ordre d'intervention qui sera
remplie par le responsable maintenance ordonnant un agent à intervenir
sur un système défaillant (notez que la fiche d'ordre
d'intervention suit la fiche d'analyse de la défaillance.).
- Une fiche d'intervention qui sera remplie par
l'intervenant à la fin de son intervention.
Toutes ces informations permettra au service maintenance de
suivre l'évolution technique des équipements afin de mieux
prendre des décision et faire des amélioration dans les
méthodes de travail.
|
SITE :
|
BUETEC-Broderie SARL
|
Equipement : ECO-xx
|
CHECK-LIST 01
|
Page : 1/2
|
PLAN DE MAINTENANCE
|
Planning mensuel
|
SEMAINE - JOURS
|
Semaine 1
|
Semaine 2
|
Semaine 3
|
Semaine 4
|
Semaine 5
|
L
|
M
|
M
|
J
|
V
|
S
|
D
|
L
|
M
|
M
|
J
|
V
|
S
|
D
|
L
|
M
|
M
|
J
|
V
|
S
|
D
|
L
|
M
|
M
|
J
|
V
|
S
|
D
|
L
|
M
|
M
|
J
|
V
|
S
|
D
|
Interventions
|
|
|
|
|
|
|
|
|
|
|
|
|
|
|
|
|
|
|
|
|
|
|
|
|
|
|
|
|
|
|
|
|
|
|
|
Nettoyer le filtre après chaque teinture
|
|
|
|
|
|
|
|
|
|
|
|
|
|
|
|
|
|
|
|
|
|
|
|
|
|
|
|
|
|
|
|
|
|
|
|
Vider l'eau dans le filtre (séparateur air- eau)
|
|
|
|
|
|
|
|
|
|
|
|
|
|
|
|
|
|
|
|
|
|
|
|
|
|
|
|
|
|
|
|
|
|
|
|
Nettoyer la surface interne et externe de l'inox
métallique avec un nettoyant chimique approprié tel que la soude,
le Borax, ou le perborate de sodium
|
|
|
|
|
|
|
|
|
|
|
|
|
|
|
|
|
|
|
|
|
|
|
|
|
|
|
|
|
|
|
|
|
|
|
|
Vérifier l'état de dégradation des joints
d'étanchéité ou d'obstruction
|
|
|
|
|
|
|
|
|
|
|
|
|
|
|
|
|
|
|
|
|
|
|
|
|
|
|
|
|
|
|
|
|
|
|
|
|
|
|
|
|
|
|
|
|
|
|
|
|
|
|
|
|
|
|
|
|
|
|
|
|
|
|
|
|
|
|
|
|
|
|
|
|
|
|
|
|
|
|
|
|
|
|
|
|
|
|
|
|
|
|
|
|
|
|
|
|
|
|
|
|
|
|
|
|
|
|
|
Tableau7 : planning de maintenance
mensuel ECO
Check-list 01
|
PLAN DE MAINTENANCE
|
Page 2/2
|
Planning annuel
|
MOIS - SEMAINE
|
J
|
F
|
M
|
A
|
M
|
J
|
J
|
A
|
S
|
O
|
N
|
D
|
S1
|
S2
|
S3
|
S4
|
S1
|
S2
|
S3
|
S4
|
S1
|
S2
|
S3
|
S4
|
S1
|
S2
|
S3
|
S4
|
S1
|
S2
|
S3
|
S4
|
S1
|
S2
|
S3
|
S4
|
S1
|
S2
|
S3
|
S4
|
S1
|
S2
|
S3
|
S4
|
S1
|
S2
|
S3
|
S4
|
|
|
|
|
|
|
|
|
|
|
|
|
Interventions
|
|
|
|
|
|
|
|
|
|
|
|
|
|
|
|
|
|
|
|
|
|
|
|
|
|
|
|
|
|
|
|
|
|
|
|
|
|
|
|
|
|
|
|
|
|
|
|
|
Vérifier et si nécessaire serrer les supports de la
machine
|
|
|
|
|
|
|
|
|
|
|
|
|
|
|
|
|
|
|
|
|
|
|
|
|
|
|
|
|
|
|
|
|
|
|
|
|
|
|
|
|
|
|
|
|
|
|
|
|
Vérifier que la courroie est bien tendue et son
état de
dégradation
|
|
|
|
|
|
|
|
|
|
|
|
|
|
|
|
|
|
|
|
|
|
|
|
|
|
|
|
|
|
|
|
|
|
|
|
|
|
|
|
|
|
|
|
|
|
|
|
|
Nettoyer les composants de l'armoire de contrôle à
l'aide d'un aspirateur
|
|
|
|
|
|
|
|
|
|
|
|
|
|
|
|
|
|
|
|
|
|
|
|
|
|
|
|
|
|
|
|
|
|
|
|
|
|
|
|
|
|
|
|
|
|
|
|
|
Lubrifier à l'aide de la graisse au Lithium le
dispositif anti friction du réducteur de vitesse
|
|
|
|
|
|
|
|
|
|
|
|
|
|
|
|
|
|
|
|
|
|
|
|
|
|
|
|
|
|
|
|
|
|
|
|
|
|
|
|
|
|
|
|
|
|
|
|
|
Lubrifier à l'aide de la graisse au Lithium le
dispositif anti friction du réducteur de vitesse
|
|
|
|
|
|
|
|
|
|
|
|
|
|
|
|
|
|
|
|
|
|
|
|
|
|
|
|
|
|
|
|
|
|
|
|
|
|
|
|
|
|
|
|
|
|
|
|
|
Vérifier pour la compression d'air des orifices du
piston
|
|
|
|
|
|
|
|
|
|
|
|
|
|
|
|
|
|
|
|
|
|
|
|
|
|
|
|
|
|
|
|
|
|
|
|
|
|
|
|
|
|
|
|
|
|
|
Vérifier l'étanchéité des orifices de
la vanne
|
|
|
|
|
|
|
|
|
|
|
|
|
|
|
|
|
|
|
|
|
|
|
|
|
|
|
|
|
|
|
|
|
|
|
|
|
|
|
|
|
|
|
|
|
|
|
Tableau8 : planning de maintenance
annuel ECO
|
SITE :
|
BUETEC-Broderie SARL
|
Equipement : SECHOIR
|
CHECK-LIST 02
|
Page : 1/2
|
PLAN DE MAINTENANCE
|
Planning mensuel
|
SEMAINE - JOURS
|
Semaine 1
|
Semaine 2
|
Semaine 3
|
Semaine 4
|
Semaine 5
|
L
|
M
|
M
|
J
|
V
|
S
|
D
|
L
|
M
|
M
|
J
|
V
|
S
|
D
|
L
|
M
|
M
|
J
|
V
|
S
|
D
|
L
|
M
|
M
|
J
|
V
|
S
|
D
|
L
|
M
|
M
|
J
|
V
|
S
|
D
|
Interventions
|
|
|
|
|
|
|
|
|
|
|
|
|
|
|
|
|
|
|
|
|
|
|
|
|
|
|
|
|
|
|
|
|
|
|
|
Démonter et nettoyer les filtres
|
|
|
|
|
|
|
|
|
|
|
|
|
|
|
|
|
|
|
|
|
|
|
|
|
|
|
|
|
|
|
|
|
|
|
|
Nettoyer l'armoire principale
|
|
|
|
|
|
|
|
|
|
|
|
|
|
|
|
|
|
|
|
|
|
|
|
|
|
|
|
|
|
|
|
|
|
|
|
Nettoyer la tuyère et les conduits d'air
|
|
|
|
|
|
|
|
|
|
|
|
|
|
|
|
|
|
|
|
|
|
|
|
|
|
|
|
|
|
|
|
|
|
|
|
|
|
|
|
|
|
|
|
|
|
|
|
|
|
|
|
|
|
|
|
|
|
|
|
|
|
|
|
|
|
|
|
|
|
|
|
|
|
|
|
|
|
|
|
|
|
|
|
|
|
|
|
|
|
|
|
|
|
|
|
|
|
|
|
|
|
|
|
|
|
|
|
|
|
|
|
|
|
|
|
|
|
|
|
|
|
|
|
|
|
|
|
|
|
|
|
|
|
|
|
|
|
|
|
|
|
|
|
Tableau9 : planning de maintenance
mensuel SECHOIR
Check-list 02
|
PLAN DE MAINTENANCE
|
Page 2/2
|
Planning annuel
|
MOIS - SEMAINES
|
J
|
F
|
M
|
A
|
M
|
J
|
J
|
A
|
S
|
O
|
N
|
D
|
S1
|
S2
|
S3
|
S4
|
S1
|
S2
|
S3
|
S4
|
S1
|
S2
|
S3
|
S4
|
S1
|
S2
|
S3
|
S4
|
S1
|
S2
|
S3
|
S4
|
S1
|
S2
|
S3
|
S4
|
S1
|
S2
|
S3
|
S4
|
S1
|
S2
|
S3
|
S4
|
S1
|
S2
|
S3
|
S4
|
|
|
|
|
|
|
|
|
|
|
|
|
Interventions
|
|
|
|
|
|
|
|
|
|
|
|
|
|
|
|
|
|
|
|
|
|
|
|
|
|
|
|
|
|
|
|
|
|
|
|
|
|
|
|
|
|
|
|
|
|
|
|
|
Effectuer le calibrage du PT100
|
|
|
|
|
|
|
|
|
|
|
|
|
|
|
|
|
|
|
|
|
|
|
|
|
|
|
|
|
|
|
|
|
|
|
|
|
|
|
|
|
|
|
|
|
|
|
|
|
Nettoyer l'armoire principale de commande
|
|
|
|
|
|
|
|
|
|
|
|
|
|
|
|
|
|
|
|
|
|
|
|
|
|
|
|
|
|
|
|
|
|
|
|
|
|
|
|
|
|
|
|
|
|
|
|
|
Faire un test de pression hydrostatique
|
|
|
|
|
|
|
|
|
|
|
|
|
|
|
|
|
|
|
|
|
|
|
|
|
|
|
|
|
|
|
|
|
|
|
|
|
|
|
|
|
|
|
|
|
|
|
|
|
Changer le lubrifiant de la boite de vitesse
|
|
|
|
|
|
|
|
|
|
|
|
|
|
|
|
|
|
|
|
|
|
|
|
|
|
|
|
|
|
|
|
|
|
|
|
|
|
|
|
|
|
|
|
|
|
|
|
|
Effectuer le calibrage du contrôle d'humidité*
|
|
|
|
|
|
|
|
|
|
|
|
|
|
|
|
|
|
|
|
|
|
|
|
|
|
|
|
|
|
|
|
|
|
|
|
|
|
|
|
|
|
|
|
|
|
|
|
|
Effectuer le calibrage des appareils de mesure
|
|
|
|
|
|
|
|
|
|
|
|
|
|
|
|
|
|
|
|
|
|
|
|
|
|
|
|
|
|
|
|
|
|
|
|
|
|
|
|
|
|
|
|
|
|
|
|
|
Vérifier l'état de la chaine et le remplacer
|
|
|
|
|
|
|
|
|
|
|
|
|
|
|
|
|
|
|
|
|
|
|
|
|
|
|
|
|
|
|
|
|
|
|
|
|
|
|
|
|
|
|
|
|
|
|
|
|
Vérifier les bordures de la bande transporteuse et la
remplacer si usée
|
|
|
|
|
|
|
|
|
|
|
|
|
|
|
|
|
|
|
|
|
|
|
|
|
|
|
|
|
|
|
|
|
|
|
|
|
|
|
|
|
Tableau10: planning de maintenance annuel
SECHOIR
2011
Amélioration de la politique de maintenance
appliquée au,équipements de production
|
|
SITE :
|
BUETEC-Broderie SARL
|
Equipement : COMPACTEUR
|
CHECK-LIST 03
|
Page : 1/2
|
PLAN DE MAINTENANCE
Planning mensuel
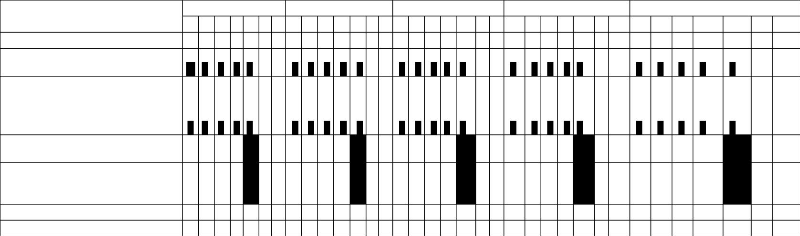
J
S D
S D
S D
S D
J
J
D
V
S
V
M
M
L
L
V
M
M
M
M
M
L
V
M
L
M
V
J
M
J
L
SEMAINE - JOURS
Semaine 1
Semaine 2
Semaine 3
Semaine 4
Semaine 5
Interventions
Nettoyer la poulie, chaines, pignons et toutes autres parties
rotatives
retirer l'eau accumulée dans le filtre / lubrificateur par
action sur la vis de fond, vérifier aussi l'huile de lubrification dans
le lubrificateur
Nettoyer le pot d'échappement de la vanne pneumatique
Vérifier et serrer si nécessaire les boulons de
tous les supports et du réducteur
Tableau11: planning de maintenance
mensuel COMPACTEUR
Check-list 03 PLAN DE MAINTENANCE Page 2/2
|
Planning annuel
|
MOIS - SEMAINE
|
J
|
F
|
M
|
A
|
M
|
J
|
J
|
A
|
S
|
O
|
N
|
D
|
S1
|
S2
|
S3
|
S4
|
S1
|
S2
|
S3
|
S4
|
S1
|
S2
|
S3
|
S4
|
S1
|
S2
|
S3
|
S4
|
S1
|
S2
|
S3
|
S4
|
S1
|
S2
|
S3
|
S4
|
S1
|
S2
|
S3
|
S4
|
S1
|
S2
|
S3
|
S4
|
S1
|
S2
|
S3
|
S4
|
|
|
|
|
|
|
|
|
|
|
|
|
Interventions
|
|
|
|
|
|
|
|
|
|
|
|
|
|
|
|
|
|
|
|
|
|
|
|
|
|
|
|
|
|
|
|
|
|
|
|
|
|
|
|
|
|
|
|
|
|
|
|
|
Vérifier et si nécessaire serrer les boulons de la
machine
|
|
|
|
|
|
|
|
|
|
|
|
|
|
|
|
|
|
|
|
|
|
|
|
|
|
|
|
|
|
|
|
|
|
|
|
|
|
|
|
|
|
|
|
|
|
|
|
|
Vérifier et serrer en cas de fuite d'air/d'eau du
système pneumatique (jonction, etc.)
|
|
|
|
|
|
|
|
|
|
|
|
|
|
|
|
|
|
|
|
|
|
|
|
|
|
|
|
|
|
|
|
|
|
|
|
|
|
|
|
|
|
|
|
|
|
|
|
|
Vérifier les moteurs électriques et utiliser l'air
comprimé pour enlever la poussière
|
|
|
|
|
|
|
|
|
|
|
|
|
|
|
|
|
|
|
|
|
|
|
|
|
|
|
|
|
|
|
|
|
|
|
|
|
|
|
|
|
|
|
|
|
|
|
|
|
Vérifier la tension et l'usure de la courroie en forme de
V
|
|
|
|
|
|
|
|
|
|
|
|
|
|
|
|
|
|
|
|
|
|
|
|
|
|
|
|
|
|
|
|
|
|
|
|
|
|
|
|
|
|
|
|
|
|
|
|
|
Vérifier le graissage du pivot rond sur les colonnes du
support panier de dessus
|
|
|
|
|
|
|
|
|
|
|
|
|
|
|
|
|
|
|
|
|
|
|
|
|
|
|
|
|
|
|
|
|
|
|
|
|
|
|
|
|
|
|
|
|
|
|
|
|
Vérifier la lubrification des supports
|
|
|
|
|
|
|
|
|
|
|
|
|
|
|
|
|
|
|
|
|
|
|
|
|
|
|
|
|
|
|
|
|
|
|
|
|
|
|
|
|
|
|
|
|
|
|
|
Vérifier et si nécessaire serrer les supports des
cylindres des capteurs pneumatique et hydraulique,
|
|
|
|
|
|
|
|
|
|
|
|
|
|
|
|
|
|
|
|
|
|
|
|
|
|
|
|
|
|
|
|
|
|
|
|
|
|
|
|
|
|
|
|
|
|
|
|
vérifier la graisse sur la machine principale et le moteur
au dessous s'il le faut.
|
|
|
|
|
|
|
|
|
|
|
|
|
|
|
|
|
|
|
|
|
|
|
|
|
|
|
|
|
|
|
|
|
|
|
|
|
|
|
|
|
|
|
|
|
|
|
|
|
|
|
|
|
|
|
|
|
|
|
|
|
|
|
|
|
|
|
|
|
|
|
|
|
|
|
|
|
|
|
|
|
|
|
|
|
|
|
|
|
|
|
|
|
|
|
|
|
|
Tableau12: planning de maintenance annuel
COMPACTEUR
|
SITE :
|
BUETEC-Broderie SARL
|
Equipement : ESSOREUSE
|
CHECK-LIST 04
|
Page : 1/2
|
PLAN DE MAINTENANCE
|
Planning mensuel
|
SEMAINE - JOURS
|
Semaine 1
|
Semaine 2
|
Semaine 3
|
Semaine 4
|
Semaine 5
|
L
|
M
|
M
|
J
|
V
|
S
|
D
|
L
|
M
|
M
|
J
|
V
|
S
|
D
|
L
|
M
|
M
|
J
|
V
|
S
|
D
|
L
|
M
|
M
|
J
|
V
|
S
|
D
|
L
|
M
|
M
|
J
|
V
|
S
|
D
|
Interventions
|
|
|
|
|
|
|
|
|
|
|
|
|
|
|
|
|
|
|
|
|
|
|
|
|
|
|
|
|
|
|
|
|
|
|
|
Nettoyer les pignons, chaines et toutes les parties rotatives
|
|
|
|
|
|
|
|
|
|
|
|
|
|
|
|
|
|
|
|
|
|
|
|
|
|
|
|
|
|
|
|
|
|
|
|
Nettoyer l'armoire principale
|
|
|
|
|
|
|
|
|
|
|
|
|
|
|
|
|
|
|
|
|
|
|
|
|
|
|
|
|
|
|
|
|
|
|
|
Vérifier le filtre et le nettoyer par action sur la vis de
fond
|
|
|
|
|
|
|
|
|
|
|
|
|
|
|
|
|
|
|
|
|
|
|
|
|
|
|
|
|
|
|
|
|
|
|
|
Nettoyer les poulies et toutes les parties mobiles
|
|
|
|
|
|
|
|
|
|
|
|
|
|
|
|
|
|
|
|
|
|
|
|
|
|
|
|
|
|
|
|
|
|
|
|
|
|
|
|
|
|
|
|
|
|
|
|
|
|
|
|
|
|
|
|
|
|
|
|
|
|
|
|
|
|
|
|
|
|
|
|
|
|
|
|
|
|
|
|
|
|
|
|
|
|
|
|
|
|
|
|
|
|
|
|
|
|
|
|
|
|
|
|
|
|
|
|
|
|
|
|
|
|
|
|
|
|
|
|
|
|
|
|
|
|
|
|
|
|
|
|
|
|
|
|
|
|
|
|
|
|
|
|
|
|
|
|
|
|
|
|
|
|
|
|
|
|
|
|
|
|
|
|
|
|
|
|
|
|
|
|
|
|
|
|
|
|
|
|
|
|
|
|
|
|
|
|
|
|
|
|
|
|
|
|
|
|
|
|
|
|
|
|
|
|
|
|
|
|
|
|
|
|
|
|
Tableau13: planning de maintenance
mensuel ESSOREUSE
Check-list 04
|
PLAN DE MAINTENANCE
|
Page 2/2
|
Planning annuel
|
MOIS - SEMAINE
|
J
|
F
|
M
|
A
|
M
|
J
|
J
|
A
|
S
|
O
|
N
|
D
|
S1
|
S2
|
S3
|
S4
|
S1
|
S2
|
S3
|
S4
|
S1
|
S2
|
S3
|
S4
|
S1
|
S2
|
S3
|
S4
|
S1
|
S2
|
S3
|
S4
|
S1
|
S2
|
S3
|
S4
|
S1
|
S2
|
S3
|
S4
|
S1
|
S2
|
S3
|
S4
|
S1
|
S2
|
S3
|
S4
|
|
|
|
|
|
|
|
|
|
|
|
|
Interventions
|
|
|
|
|
|
|
|
|
|
|
|
|
|
|
|
|
|
|
|
|
|
|
|
|
|
|
|
|
|
|
|
|
|
|
|
|
|
|
|
|
|
|
|
|
|
|
|
|
Vérifier et si nécessaire serrer les boulons de la
machine
|
|
|
|
|
|
|
|
|
|
|
|
|
|
|
|
|
|
|
|
|
|
|
|
|
|
|
|
|
|
|
|
|
|
|
|
|
|
|
|
|
|
|
|
|
|
|
|
|
Vérifier et serrer en cas de fuite d'air/d'eau du
système pneumatique (jonction, etc.)
|
|
|
|
|
|
|
|
|
|
|
|
|
|
|
|
|
|
|
|
|
|
|
|
|
|
|
|
|
|
|
|
|
|
|
|
|
|
|
|
|
|
|
|
|
|
|
|
|
Vérifier les moteurs électriques et utiliser l'air
comprimé pour enlever la poussière
|
|
|
|
|
|
|
|
|
|
|
|
|
|
|
|
|
|
|
|
|
|
|
|
|
|
|
|
|
|
|
|
|
|
|
|
|
|
|
|
|
|
|
|
|
|
|
|
|
Vérifier la tension et l'usure de la courroie en forme de
V
|
|
|
|
|
|
|
|
|
|
|
|
|
|
|
|
|
|
|
|
|
|
|
|
|
|
|
|
|
|
|
|
|
|
|
|
|
|
|
|
|
Vérifier le graissage de l'ensemble de tous les
roulements (rouleaux, système de détorsion)
|
|
|
|
|
|
|
|
|
|
|
|
|
|
|
|
|
|
|
|
|
|
|
|
|
|
|
|
|
|
|
|
|
|
|
|
|
|
|
|
vérifier toutes les fuites d'air ou pertes d'huile du
système pneumatique, des tuyaux, les jonctions et joints
d'étanchéité.
|
|
|
|
|
|
|
|
|
|
|
|
|
|
|
|
|
|
|
|
|
|
|
|
|
|
|
|
|
|
|
|
|
|
|
|
|
|
|
|
Tableau14 : planning de maintenance
annuel ESSOREUSE
BUETEC-Broderie SARL
|
SITE :
|
PLAN DE MAINTENANCE
|
PLANNING HEBDOMADAIRE
|
SERVICE : MAINTENANCE
|
Page 1/
|
EQUIPEMENT :
CHAUDIERE/COMPRESSEUR
|
Code :
|
|
|
Opérations
|
Périodicité
|
CHAUDIERE
|
L
|
M
|
M
|
J
|
V
|
S
|
D
|
Vérifier l'état du gicleur
|
|
|
|
|
|
|
|
Vérifier et nettoyer l'état des filtres
|
|
|
|
|
|
|
|
Vérifier s'il ya lieu de faire une vidange
|
|
|
|
|
|
|
|
Vérifier l'état de dégradation des
électrovannes
|
|
|
|
|
|
|
|
Vérifier l'état fonctionnel de la pompe
d'alimentation d'eau douce
|
|
|
|
|
|
|
|
Vérifier l'état fonctionnel de la pompe doseuse
|
|
|
|
|
|
|
|
Vérifier l'état fonctionnel de la pompe de fuel
|
|
|
|
|
|
|
|
COMPRESSEUR
|
Vérifier le niveau d'huile
|
|
|
|
|
|
|
|
Contrôler l'état des courroies
|
|
|
|
|
|
|
|
Vérifier et nettoyage le filtre à air
|
|
|
|
|
|
|
|
Vidanger le réservoir
|
|
|
|
|
|
|
|
Contrôler la pression effective d'air (6 bars environ)
|
N
|
|
|
|
|
|
|
|
|
Rédacteur
|
Vérificateur
|
Approbateur
|
Date
|
|
|
|
Nom
|
|
|
|
Signature
|
|
|
|
Tableau15 : planning de maintenance
hebdomadaire sur la chaudière et le compresseur
BUETEC-Broderie SARL
|
SITE :
|
|
PLAN DE MAINTENANCE -cheik list01
|
SERVICE : MAINTENANCE
|
Page 1/1
|
EQUIPEMENT : ECO-6-2T/ECO-38-1T
|
Code :
|
|
|
Niveau de maintenance
1 2 3 4 5
|
Technique
|
réglages électrique mécanique automatique
hydraulique pneumatique
|
|
|
Opérations
|
B
|
M
|
Action Fait
|
Action à Faire
|
Remarques
|
Vérifier l'état de serrage des supports de la
machine
|
|
|
|
|
|
Vérifier que la courroie de transmission est bien
tendue
|
|
|
|
|
|
Vérifier pour la compression d'air les orifices du piston
pneumatique
|
|
|
|
|
|
Vérifier l'état de dégradation des joints
d'étanchéité ou d'obstruction
|
|
|
|
|
|
Vérifier l'étanchéité des orifices de
la vanne pneumatique
|
|
|
|
|
|
|
|
|
|
|
|
|
|
|
|
|
|
|
|
|
|
|
|
|
|
|
|
|
|
|
|
|
|
|
|
|
|
|
|
|
|
|
|
|
|
|
|
|
|
|
|
|
|
|
Rédacteur
|
Vérificateur
|
Approbateur
|
Date
|
|
|
|
Nom
|
|
|
|
Signature
|
|
|
|
Légende : B=bon ; M=mauvais
BUETEC-Broderie SARL
|
SITE :
|
PLAN DE MAINTENANCE -cheik list02
|
SERVICE : MAINTENANCE
|
Page 1/1
|
EQUIPEMENT : ESSOREUSE
|
Code :
|
|
|
Niveau de maintenance
1 2 3 4 5
|
Technique
|
réglages électrique mécanique automatique
hydraulique pneumatique
|
|
Opérations
|
B
|
M
|
Action Fait
|
Action à Faire
|
Remarques
|
Vérifier l'huile de lubrification dans le lubrificateur
|
|
|
|
|
|
Vérifier que les vis ou boulons de tous les supports,
réducteur principaux sont parfaitement serrés
|
|
|
|
|
|
Vérifier et si nécessaire serrer les boulons de la
machine
|
|
|
|
|
|
Vérifier et si nécessaire serrer en cas de fuite
d'air/oil du système pneumatique (tuyaux, joint
d'étanchéité, jonctions),
|
|
|
|
|
|
Vérifier les moteurs électriques et utiliser l'air
comprimé pour enlever la poussière dans les moteurs
|
|
|
|
|
|
Vérifier la tension et l'usure de la courroie en forme de
V
|
|
|
|
|
|
Vérifier le graissage de l'ensemble de tous les roulements
(rouleaux, système de détorsion)
|
|
|
|
|
|
Vérifier et si nécessaire serrer les supports des
capteurs de position
|
|
|
|
|
|
vérifier toutes les fuites d'air ou pertes d'huile du
système pneumatique, des tuyaux, les jonctions et joints
d'étanchéité. Vérifier aussi et
serrer les fermetures d'écrous de l'arbre du cylindre,
|
|
|
|
|
|
|
|
|
|
|
|
|
|
Rédacteur
|
Vérificateur
|
Approbateur
|
Date
|
|
|
|
Nom
|
|
|
|
Signature
|
|
|
|
Légende : B=bon ; M=mauvais
BUETEC-Broderie SARL
|
SITE :
|
PLAN DE MAINTENANCE -cheik list03
|
SERVICE : MAINTENANCE
|
Page 1/1
|
EQUIPEMENT : SECHOIR
|
Code :
|
|
|
Niveau de maintenance
1 2 3 4 5
|
Technique
|
réglages électrique mécanique automatique
hydraulique pneumatique
|
|
Opérations
|
B
|
M
|
Action Fait
|
Action à Faire
|
Remarques
|
Vérifier l'état de la pression hydrostatique au
niveau des échangeurs de chaleur
|
|
|
|
|
|
Contrôler l'état du lubrifiant dans la boite de
vitesse
|
|
|
|
|
|
Contrôler l'état d'usure de la chaîne
|
|
|
|
|
|
Vérifier l'état de la bande transporteuse
|
|
|
|
|
|
Vérifier l'état de dégradation des
filtres
|
|
|
|
|
|
Vérifier l'état du contrôleur
d'humidité
|
|
|
|
|
|
|
|
|
|
|
|
|
|
|
|
|
|
|
|
|
|
|
|
|
|
|
|
|
|
|
|
|
|
|
|
|
|
|
|
|
|
|
|
|
|
|
|
|
|
Rédacteur
|
Vérificateur
|
Approbateur
|
Date
|
|
|
|
Nom
|
|
|
|
Signature
|
|
|
|
Légende : B=bon ; M=mauvais
BUETEC-Broderie SARL
|
SITE :
|
PLAN DE MAINTENANCE -cheik list04
|
SERVICE : MAINTENANCE
|
Page 1/1
|
EQUIPEMENT : COMPACTEUR
|
Code :
|
|
|
Niveau de maintenance
1 2 3 4 5
|
Technique
|
réglages électrique mécanique automatique
hydraulique pneumatique
|
|
Opérations
|
B
|
M
|
Action Fait
|
Action à Faire
|
Remarques
|
Vérifier l'état de serrage des boulons de la
machine.
|
|
|
|
|
|
Vérifier l'existence des fuites d'air/eau du
système
pneumatique/hydraulique,(tuyaux, joint
d'étanchéité, jonctions).
|
|
|
|
|
|
Vérifier et si nécessaire serrer les supports des
cylindres des capteurs pneumatique et hydraulique.
|
|
|
|
|
|
Vérifier la tension et l'usure de la courroie en forme de
v.
|
|
|
|
|
|
Vérifier le graissage du pivot rond sur les colonnes du
support du panier de dessus.
|
|
|
|
|
|
Vérifier les moteurs électriques et utiliser l'air
comprimé pour enlever la poussière des moteurs
|
|
|
|
|
|
Vérifier la nécessité de la lubrification
des supports
|
|
|
|
|
|
vérifier que l'intérieur du panier est toujours
propre.
|
|
|
|
|
|
vérifier l'état de la graisse sur la machine
principale et le moteur en dessous.
|
|
|
|
|
|
Vérifier le graissage du pivot rond sur les colonnes du
support panier de dessus.
|
|
|
|
|
|
vérifier toutes les fuites d'air ou pertes d'huile du
système pneumatique, des tuyaux, les jonctions et joints
d'étanchéité.
|
|
|
|
|
|
Vérifier et serrer les fermetures d'écrous de
l'arbre du cylindre
|
|
|
|
|
|
|
Rédacteur
|
Vérificateur
|
Approbateur
|
Date
|
|
|
|
Nom
|
|
|
|
Signature
|
|
|
|
Légende : B=bon ; M=mauvais
BUETEC-Broderie SARL
|
SITE :
|
PLAN DE MAINTENANCE -cheik list05
|
SERVICE : MAINTENANCE
|
Page 1/1
|
EQUIPEMENT :
CHAUDIERE/COMPRESSEUR
|
Code :
|
|
|
Niveau de maintenance
1 2 3 4 5
|
Technique
|
réglages électrique mécanique automatique
hydraulique pneumatique
|
|
Opérations
|
B
|
M
|
Action Fait
|
Action à Faire
|
Remarques
|
CHAUDIERE
|
Vérifier l'état du gicleur
|
|
|
|
|
|
Vérifier l'état des filtres
|
|
|
|
|
|
Vérifier s'il ya lieu de faire une vidange
|
|
|
|
|
|
Vérifier l'état des électrovannes
|
|
|
|
|
|
Vérifier l'état fonctionnel de la pompe
d'alimentation d'eau douce
|
|
|
|
|
|
Vérifier l'état fonctionnel de la pompe doseuse
|
|
|
|
|
|
Vérifier l'état fonctionnel de la pompe de fuel
|
|
|
|
|
|
COMPRESSEUR
|
Vérifier le niveau d'huile
|
|
|
|
|
|
Contrôler l'état des courroies
|
|
|
|
|
|
Vérifier et nettoyage le filtre à air
|
|
|
|
|
|
Vidanger le réservoir
|
|
|
|
|
|
Contrôler la pression d'air (6 bars environ)
|
|
|
|
|
|
|
|
|
|
|
|
|
Rédacteur
|
Vérificateur
|
Approbateur
|
Date
|
|
|
|
Nom
|
|
|
|
Signature
|
|
|
|
Légende : B=bon ; M=mauvais
PARTIE III : PERSPECTIVE/SUGGESTIONS
ET REMARQUES
CHAPITRE I : PERSPECTIVE /SUGGESTIONS
Nous proposons à l'entreprise la mise sur pied d'un outil
de gestion de la maintenance assisté par ordinateur (GMAO) ; Compte tenu
de la longévité de l'entreprise et de ces équipements,
l'outil de GMAO sera indispensable pour une gestion plus efficace de la
maintenance au sein de cette entreprise.
I- LES PROGICIELS DE GMAO : ANALYSE DES
DIFFÉRENTS MODULES
FONCTIONNELS
Les progiciels de GMAO ont des structures modulaires proposant
diverses fonctions. Mais, selon les logiciels, les fonctions remplies sont
diversement dénommées, diversement réparties et
diversement organisées. Nous trouverons beaucoup d'intérêt
à mettre sur pied cet outil de part l'intérêt des dix
fonctions que nous analyserons.
Les détails proposés pour chaque fonction n'a pas
l'ambition d'être exhaustif (pourra être modifié par le
service de maintenance en place), mais nous attirons ainsi leur 'attention sur
certains points souvent négligés. Les fonctions analysées
sont les suivantes :
1. gestion des équipements ;
2. gestion du suivi opérationnel des équipements
;
3. gestion des interventions en interne et en externe ;
4. gestion du préventif ;
5. gestion des stocks ;
6. gestion des approvisionnements et des achats ;
7. analyses des défaillances ;
8. gestion du budget et suivi des dépenses ;
9. gestion des ressources humaines ;
10. tableaux de bord et statistiques ;
11. autres modules et interfaçages possibles.
1- GESTION DES EQUIPEMENTS
Il s'agit de décrire et de coder l'arborescence du
découpage allant de l'ensemble du parc à maintenir aux
équipements identifiés et caractérisés par leur DTE
(dossier technique équipement) et leur historique, puis à leur
propre découpage fonctionnel. A partir du code propre à
l'équipement, le module doit permettre de :
- pouvoir localiser et identifier un sous-ensemble dans
l'arborescence ;
- connaître l'indice de criticité fonctionnelle de
l'équipement, sa durée d'usage relevé par compteur ;
- accéder rapidement au « plan de maintenance »
de l'équipement ;
- pouvoir trouver ses caractéristiques techniques,
historiques et commerciales à partir du DTE ;
- pouvoir localiser un ensemble mobile, trouver son DTE et son
historique (gestion multisite)
- connaître ses consommations en énergie, en
lubrifiants, etc. ;
- connaître la liste des rechanges consommés ;
- connaître le code des responsables exploitation et
maintenance de l'équipement ;
- accéder aux dessins et schémas relatifs à
l'équipement contenus dans un logiciel de gestion documentaire (hors
DTE).
2- GESTION DU SUIVI OPÉRATIONNEL DES
ÉQUIPEMENTS
A travers le module de suivi des performances d'un
équipement, il s'agit de retrouver les indicateurs de fiabilité,
de maintenabilité, de disponibilité et le taux de rendement
synthétique TRS si la TPM est envisagée ou effective. Le choix
des indicateurs prédétermine la nature des saisies
nécessaires. Celles-ci doivent pouvoir se faire « au pied de la
machine » et en temps réel, aussi bien en ce qui concerne les
demandes que les comptes rendus.
· Dans le cadre d'un suivi technique par
l'indicateur Disponibilité
Le module doit être capable d'assurer la gestion en
affichant :
- les graphes d'évolution des Di par périodes de
suivi ;
- les graphes de Pareto se rattachant aux équipements par
nature des arrêts ;
- le rappel des valeurs des indicateurs MTA (moyenne des temps
d'arrêt) ou MTTR
(mean time to repair ; en français TTR : temps
technique de réparation) pour les
dernières périodes.
· Dans le cadre d'un suivi par le TRS
Le module doit être capable, à partir des
données opérationnelles liées aux pertes ; de
performances, aux pertes de qualité et aux pertes de
disponibilité, de calculer les trois taux et leur produit (le TRS) par
période, de montrer leur évolution, de présenter
l'affichage analytique des valeurs après sélection, pour
diagnostic. De façon plus générale, l'agent des
méthodes doit être capable de trouver à travers ce module
tous les éléments quantitatifs lui permettant d'approfondir une
analyse de logistique, de fiabilité, de maintenabilité ou de
disponibilité.
3- GESTION DES INTERVENTIONS
Nous avons vu en ordonnancement l'existence de plusieurs
procédures adaptées à la nature des travaux. Pour les
nombreux petits travaux, pas de demande DI (demande d'intervention) ni
d'attribution de numéro, mais un enregistrement rapide a posteriori de
leur durée, de leur localisation et de leur nature. Il est
nécessaire de créer une bibliothèque des différents
codes utiles afférents aux clients, aux intervenants, aux
différents statuts de l'intervention. D'autre part, à chaque
équipement doit correspondre une bibliothèque de codes standards,
relatifs au découpage de l'équipement, à l'effet
déclenchant (souvent appelé par erreur « cause »
d'arrêt) et à la cause identifiée.
· Pour les DI, demandes d'intervention
Le module doit permettre :
- la création d'un numéro DI, OI, qui servira de
référence pour toutes les opérations liées,
procédures de sécurité spécifique,
préparation et DA (demande d'approvisionnement) ou BSM (bon de sortie
magasin) par exemple ;
- l'horodatage de la demande, avec identification du demandeur
et du secteur (code client) et l'urgence ou le délai attribué
;
- le suivi possible du statut de la demande par le demandeur
(code des différents statuts).
· Au niveau de la préparation de
l'OT
Le module doit permettre :
- l'insertion de gammes de maintenance préétablies
;
- les réservations d'outillages, de moyens
spéciaux, de pièces de rechanges, etc. ; - l'affectation des
ressources ;
- le regroupement de la gamme de maintenance avec des plans, des
pictogrammes et des schémas extraits d'un logiciel de gestion
documentaire ;
- l'insertion automatique de procédures de
sécurité liées à certains secteurs ou à
certains équipements ;
- l'intégration d'un groupe de travaux à un
gestionnaire de projet, avec graphismes Gantt et PERT.
· Pour les comptes rendus
d'intervention
Le module doit permettre :
- la saisie « facile et rapide » (critère
très important) des paramètres et de la caractérisation de
l'intervention, même et surtout s'il s'agit d'une correction de
microdéfaillance ;
- l'utilisation par les dépanneurs d'une borne en libre
service, située à proximité immédiate du site
d'intervention, réduisant ainsi les distances et les temps de saisie
d'intervention ;
- de caractériser l'intervention par les codes de la
bibliothèque de l'équipement (localisation, cause, etc.) ;
- l'imputation des travaux à des comptes analytiques ;
- de distinguer les durées d'intervention des
durées d'indisponibilité ;
- d'enrichir chronologiquement l'historique de
l'équipement dès la clôture de l'OI;
- de connaître les consommations de pièces
utilisées, éventuellement leurs valeurs ; - la rédaction
d'un texte libre contenant les remarques et les suggestions de
l'intervenant.
Par contre, il ne doit pas donner l'impression d'une «
inquisition », mais d'un besoin de savoir pour mieux comprendre et
améliorer avec l'aide du technicien d'intervention.
· Pour la gestion des travaux
externalisés
Le module doit permettre une gestion semblable aux
procédures de préparation et d'ordonnancement internes :
- émission de DIE (demande de travaux externalisés)
pour les prestations ponctuelles ;
- création de contrats-type (clauses techniques,
économiques et techniques, plan de sécurité) qu'il suffit
d'adapter à chaque commande.
4- GESTION DU PRÉVENTIF
Le module permettra de gérer la maintenance
systématique à travers un planning calendaire par
équipement, les dates étant prédéterminées
ou déterminées à partir d'un relevé de compteur (ou
d'une mesure dans le cas de la maintenance conditionnelle). Le
déclenchement sera automatique, par listing hebdomadaire des
opérations prévues dans la semaine. Chaque opération sera
définie par sa gamme préventive. Le module devra aussi permettre
un déclenchement « manuel d'opportunité », par exemple
par anticipation d'une opération préventive à la suite
d'un arrêt fortuit.
5- GESTION DES STOCKS
Le système repose sur le « fichier des articles
» en magasin comprenant les « lots de maintenance » par
équipement et sur les mouvements entrées/sorties du magasin. Une
fiche article doit comprendre :
- le code article défini par l'organisation interne, son
libellé et sa désignation technique; - le code article du ou des
fournisseurs et le code fournisseur (et fabricant éventuellement) ;
- le code du gisement en magasin ;
- les codes des articles de substitution, en cas de rupture ;
- le rattachement aux équipements possédant cet
article ;
- le prix unitaire et le prix moyen pondéré
automatiquement calculé ; - les quantités en stock,
commandées en attente ;
- la méthode de réapprovisionnement et ses
paramètres (stock de sécurité, stock maxi. etc.) ;
- les dates des derniers mouvements ;
- l'historique des consommations.
Les outils d'analyse du stock en nature et en valeurs sont :
- le classement des articles en magasin par valeurs et par taux
de rotation ; - la valeur des stocks par nature et par périodes (mois
par mois) ;
- la liste des articles « dormants » ;
- la liste des cas de ruptures de stock (demandes non
satisfaites).
Il importe de vérifier certaines potentialités du
module :
- la possibilité ou non d'actualisation automatique des
paramètres en fonction des consommations ;
- la possibilité d'avoir le profil des consommations et le
tracé de la courbe ABC en valeurs ;
- les possibilités relatives aux transactions du magasin :
réceptions provisoires ou définitives, retours au fournisseur en
cas de non-conformité, etc. ;
- l'édition de pièces réservées sur
une préparation (numéro d'OT pour l'imputation) ; - la
présence d'un écran d'inventaire comprenant les différents
critères d'article ;
- la possibilité d'effectuer des recherches et des
analyses multicritères.
6- GESTION DES APPROVISIONNEMENTS ET DES ACHATS
Caractéristiques de la fonction en maintenance : beaucoup
de références et de fournisseurs pour des quantités
faibles et des délais courts. Ce module doit permettre, en interface
avec le logiciel du service « achat » de maîtriser et de
gérer avec aisance :
- le fichier des fournisseurs et des fabricants avec leurs tarifs
liés aux quantités ; - le lancement d'appels d'offre aux
fournisseurs ;
- l'édition de bons de commandes standard ou
personnalisés, et le suivi des autorisations de dépenses ;
- le contrôle des factures ;
- l'édition automatique des codifications internes et
fournisseurs (transcodage) ; - le suivi des états de la commande ;
- le suivi des réceptions totales, partielles et des refus
;
- l'estimation de la qualité des fournisseurs par les
contrôles de réception et le suivi des délais ;
- l'édition automatique de lettres de relance pour les
retards.
7-ANALYSE DES DÉFAILLANCES
La base de ce module est constituée des historiques
automatiquement alimentés par chaque saisie de BPT (bon de petits
travaux) et d'OI (ordre d'intervention) mis en famille par ses codes
d'imputation. A partir d'un équipement donné, il doit permettre
:
- l'établissement des analyses quantitatives par graphes
de Pareto, avec plusieurs critères (MTTR, TA ; durée
d'arrêt) et plusieurs mises en familles (par cause, par localisation, par
nature de défaillance, etc) et sur plusieurs périodes d'analyse
(hier, la semaine écoulée, les trois derniers mois,
l'année, etc.) ;
- puis l'analyse qualitative des défaillances
sélectionnées comme prioritaires, éventuellement mise sous
forme AMDEC.
La productivité de l'analyse de défaillance comme
outil de progrès rend cette fonction de GMAO stratégique : il est
indispensable de savoir par qui, quand, comment vont être
organisées ces analyses pour tester l'adéquation du logiciel au
cahier des charges du module. Ce module est la base de la MBF (maintenance
basée sur la fiabilité).
8- BUDGET ET LE SUIVI DES DÉPENSES
La gestion analytique ne permet que des « macro-analyses
» des comptes. Un découpage plus fin de la fonction maintenance
doit donc pouvoir permettre des analyses détaillées grâce
à la GMAO, l'objectif étant le suivi de l'évolution des
dépenses par activité dans un budget donné. Quelques
éléments du cahier des charges à préciser,
c'est-à-dire le module permet-il :
- la création d'un nouveau budget en modifiant des
chapitres de l'ancien ?
- la comparaison entre plusieurs exercices ?
- la prise en compte des frais généraux du service
?
- l'éclatement en coûts directs et indirects (pertes
de qualité, de production, etc.) ? - la ventilation des coûts par
équipement, par «client», par type d'activité de
maintenance, par origine de défaillance, par sous-ensemble
«fragile» communs à
plusieurs équipements, etc. ?
- la comparaison entre la prévision et la
réalisation ?
- la gestion en plusieurs devises : francs, euros, dollars, etc.
?
- la possibilité d'exporter les résultats
comptables sur un logiciel de comptabilité ? - la décomposition
structurelle du budget en sous-budgets consolidables ?
- le suivi des coûts pour établir le LCC (life cycle
cost ; coût du cycle de vie) d'un
équipement ?
9- GESTION DES RESSOURCES HUMAINES
Spécifiquement adapté au service maintenance, ce
module sera principalement une aide à l'ordonnancement. Il sera
construit autour d'un « fichier-technicien » pouvant comprendre, pour
chacun :
- la qualification, les habilitations, les diplômes,
l'ancienneté dans son échelon actuel, les différentes
affectations, l'affectation actuelle, etc. ;
- les formations suivies, demandées et le bilan de
compétence ;
- les congés pris, demandés et les
récupérations (données nécessaires à la
programmation des travaux) ;
- les temps de présence et d'absence (historique des
arrêts de travail) ;
- les coûts horaires pour chaque qualification (pour
imputation des coûts d'intervention).
Remarquons l'intérêt, pour chaque technicien, de
pouvoir accéder par la GMAO, à partir du terminal atelier,
à ses propres informations relatives aux reliquats des congés
à prendre ou à des informations générales de
l'entreprise. C'est un facteur d'acceptation du système informatique.
10- TABLEAUX DE BORD ET STATISTIQUES
Les tableaux de bord concernent la mise en forme de tous les
indicateurs techniques, économiques et sociaux
sélectionnés pour assurer la gestion et le management du service
maintenance. Certains sont livrés en « standard » avec le
logiciel. Il faut vérifier s'ils peuvent être personnalisés
rapidement (courbes, graphiques et autres visuels), ou développés
avec un générateur d'état extérieur au logiciel.
Vérifier également que l'extraction de données se fait
simplement.
En cas de projet TPM, il faut vérifier la
possibilité de former l'indicateur TRS et de visualiser ses variations
par périodes.
11- MODULE COMPLÉMENTAIRES OU INTERFAÇAGES
UTILES La revue des besoins internes et externes du service peut
amener à rechercher des extensions par interfaçage, par
acquisition de modules complémentaires ou par développement de
logiciels applicatifs spécifiques. Interfaçage requis ou non avec
:
- le logiciel de comptabilité et de paie,
- le logiciel de gestion des ressources humaines,
- le logiciel de gestion des achats et approvisionnements,
- la GPAO, la GTC, les réseaux techniques,
- le logiciel de gestion documentaire (GED),
- les outils multimédias,
- la supervision : saisie automatique de données «
machines » par collecteur portable, par code barres, par automates ou par
capteurs.
Autres fonctionnalités possibles :
- liaison avec le logiciel de gestion de projet,
- lecteur de badges,
- saisie des images : scanner, hypertexte, etc.,
- analyses de pannes, génération d'AMDEC, etc.
Toutes ces potentialités étant très
évolutives, il importe de ne pas prendre de retard au départ d'un
projet GMAO, qui doit déboucher sur une durée d'exploitation
significative pour se justifier économiquement, sans pour cela aller au
superflu.
CHAPITRE II : REMARQUES
I- POSITIVES
Nous avons pendant notre passage dans cette entreprise
constaté des points biens appréciables dans une entreprise
industrielle ; notamment :
La sécurité au travail nous avons constaté
un système de gestion de sécurité à priori efficace
de part la mise à la disposition des travailleurs des consignes de
sécurité, l'affichage des panneaux de signalisation d'obligation
et de d'interdiction.
La mise à la disposition des employés des
séminaires de formation particulièrement es
sécurité pendant notre passage ;
La mise à la disposition des employés un
système de communication interne.
II- IkItGATIVES
- Pas de magasin de pièce de rechange suffisamment
équipé ;
- Pas de gestion des couts de maintenance corrective ;
- Pas d'évaluation des couts de non production par
défaut d'indisponibilité des équipements de production
;
- Pas d'évaluation des couts de non qualité par
défaut d'une mauvaise maintenance ; - Pas de suivit périodique
des couts de maintenance en fonction de la production ;
- Perte de temps de production suite à des coupures de
courant électrique ; - Peu d'équipements de protection
individuelle (EPI).
CONCLUSION
Au terme de ce travail ou il était question pour nous
d'améliorer la politique de maintenance appliquée à
l'usine de production, nous avons en fonction de l'état des lieux fait
des recommandations à prendre en compte pour une maintenance plus
efficiente. Pour y arriver, nous avons mis sur pied l'analyse descendante
structurelle (ADS) des équipements de production, qui est un outil
efficace pour la connaissance de l'équipement. Nous avons par la suite
mis sur pied un outil d'aide au diagnostique et de prise de décision
pour chaque équipement de production (AMDEC). Pour les travaux de
maintenance préventive, nous avons sur la base de l'inventaire des
interventions du plan de maintenance de l'entreprise, mis sur pied une
organisation calendaire des taches de maintenance préventive. Enfin,
nous avons mise sur pied des fiches pour la suivie technique des
équipements et l'amélioration de la qualité des
interventions. Nous sommes à coup sur que l'effectivité de ce
travail ferra la bonne disponibilité des équipements de
production et donc une bonne participation du service maintenance à la
compétitivité de l'entreprise. Les perspectives de ce travail
fait le point sur la mise sur pied d'un outil de Gestion de la Maintenance
Assistée par Ordinateur (GMAO). Au bout donc de ce travail intense, nous
en sommes sortis victorieux avec beaucoup d'expériences. Nous avons par
ces expériences joint la théorie à la pratique et avons
à cet effet une vision globale du monde de l'entreprise.
BLBLLOGRAPIIL~
- Pratique de la maintenance préventive Dunod [396
pages]
- Mémotech Maintenance Industrielle F CASTELLAZZI
[331pages]
Documents non publiés :
- Cours d'exécution de la maintenance industrielle Ing
NGOUCHE - Cours de maintenance et fiabilité Ing DOMPIE
Liens internet :
-
www.hubertfaigner.com
-
www.buetec-broderie.com
ANN~X~S
Annexe 1 : Fiche de demande d'intervention Annexe 2 : Fiche
d'analyse de la défaillance Annexe 3 : Fiche d'ordre d'intervention
Annexe 4 : Fiche d'intervention
|