10 CHAPITRE2 : Rentabilité
du projet
L'activité « zéro panne » que nous avons
menée permettra de réduire les tempsd'arrêts
occasionnés par les défaillances des équipements. Cette
réduction des temps d'arrêts aura unimpact positif sur le volume
de production.
Considérons l'une des emballeuses de la ligne la ACMA 1.La
cadence nominale de cetteemballeuses : 70 savons / minute.
Les temps d'arrêt de l'emballeuse dû aux pannes est
de 551.3 heures or la production de savon de cette ligne s'élève
à 2.78tonnes/h
D'où la mise en place de cette activité
zéro, pourrais faire gagner à la production plus de 1534.614
tonnes en considérant uniquement cette seule emballeuse.
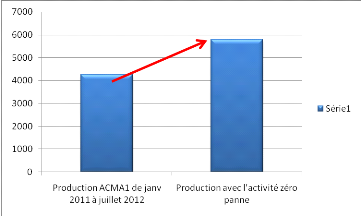
Figure 17: Gain de production
Cette activité est donc bénéfique pour
l'entreprise
11 CONCLUSION
Notre thème consistait à réduire les temps
d'arrêt sur la ligne MAZZONI1 en réduisant au maximum les temps
d'arrêts dus aux équipements les plus pénalisants.
D'abord nous avons, consulté l'historique des
équipements de la savonnerie. L'analyse de ces données nous a
permis de savoir que la ligne MAZZONI 1 enregistrait le nombre de temps
d'arrêt le plus élevé. Et sur cette ligne, les
équipements ayant à leur compte les temps d'arrêt les plus
grands sont les emballeuses ACMA 381 LS et les mouleuses SAS.
Ensuite nous avons étudié les causes de
défaillances des équipements par la méthodeAMDEC. Cette
Méthode nous apermis de faire ressortir les éléments
critiques des équipements ainsi que l'évènement
redouté associé. A l'aide d'un arbre de défaillance nous
avons montré les causes qui pourraient entrainer
cetévènement redouté.
En fin à partir de la méthode 5 M
réalisé en étude de l'existant et l'étude AMDEC
nous avons terminé nos travaux par la proposition d'un plan
préventif adapté aux conditions d'exploitations actuelles.
Pour notre part les contraintes critiques qui peuvent
empêcher l'implémentation de notre projet est principalement le
manque de motivation du personnel. Le service maintenance gagnerait à
favoriser la mise en place d'un management motivationnel.
Au terme de notre étude, nous avons la conviction d'avoir
appris énormément dans la mesure où nous avons
amélioré nos connaissances en maintenance, nos connaissances
de l'entreprise et aussi nos connaissances en matière de
relationshumaines.
12 Bibliographie
[1] JEAN Bufferne, 2006. Le guide de la TPM
Total Productive Maintenance, EYROLLES Editions d'organisation.
[2] JEAN Héng, 2002.Pratique de la
maintenance préventive, DUNOD Edition
[3] AKPO Bessekon Paul, Organisation et Gestion
de la maintenance, Ingénierie pédagogique, 4eme édition
Septembre 2000.
 
|