CHAPTER 3: AN OVERVIEW OF ERP SYSTEMS
3.1 Introduction
Expanding the discussion of the value chain theories in the
previous chapter, this chapter focuses on ERP systems and their relation to the
value chain concept. The purpose of this chapter specifically is to define and
analyse the concept of an ERP system, its background as well as its benefits,
characteristics, advantages and disadvantages. This is followed by a discussion
of the integrating role ERP plays in IT, its modules, global configuration and
architecture. The factors of strategic evaluation of ERP software, including a
brief overview of the selection and key factors associated with the success and
failure affecting the system during and after implementation, are also
investigated. The evaluation of the system will provide the technical
background theory, allowing the researcher to compare Axapta Microsoft software
under the magnifying glass (in chapter 4) with the theories assessed on value
chain architecture and configuration related to ERP systems in chapter 6, to
develop the overall qualitative part of this study.
3.2 The background of ERP systems
During the 1960s the focus on manufacturing systems was on
traditional inventory control concepts. Most of the software was limited
generally to inventory based on traditional inventory processes, owing to the
need for manufacturing operations. Since then manufacturing systems have moved
to material requirement planning systems, which translated the master planning
schedule to build for the end items into time-phased net requirements for the
sub-assemblies, components and raw materials planning and procurement. In 1975,
MRP grew from a simple tool to become MRPII.
However, according to Chung, Snyder and Gumaer (in Chin,
Hsiung & Ming, 2004:235) the shortcoming of MRPII in managing a production
facility's orders, production plans and inventories, and the need to integrate
these new techniques led to the development of a rather more integrated
solution called an ERP system. The ERP system vanquishes the old stand-alone
computer systems in finance, human resources, manufacturing and the warehouse,
replacing them with a single unified software program divided into software
modules that roughly approximate the old stand-alone systems. Therefore, Baki
and Cakar (2005:75) position an ERP system as an integrated enterprise-wide
system, which automates core corporate activities such as manufacturing, human
resources,
48
finance and supply chain management. With these benefits, an
organisation achieves many improvements such as easier access to reliable
information, elimination of redundant data and operations, reduction of cycle
times and increased efficiency, hence reducing costs.
3.3 Defining the concept of an ERP system
ERP system software links divisions or departments together
through the supply chain, enabling anyone to look into the warehouse, for
example, to see if an order has been shipped. What is important to note is that
most vendors of ERP software are flexible enough that some modules can be
installed without buying the whole package. Therefore many organisations
implementing an ERP system for the first time install the ERP software modules
of finance or human resources, leaving the rest of the functions for later
(Baatz, Koch & Slater: available online). An ERP system works essentially
at integrating the whole business information function, allowing organisations
to effectively manage their resources of people, materials and finance. The
system combines both business processes and IT into one integrated solution in
the organisation, which MRP and MRPII were unable to provide. Thus, asserts
Aladwani (2001:266), the ERP system is an integrated set of programmes that
provides support for core organisational activities. Blasis and Gunson
(2002:16-7) state that an ERP system is a tool that grafts a solution for human
resources, finance, logistics etc., and eventually to SCM and CRM. This
provides a closer relation to partners with the expansion of the customer base
from large organisations to small and medium, and from a wide industry offer by
encompassing service as well as manufacturing industries due to the Web-enabled
technologies as shown in figure 3.1 below.
Figure 3.1: Integrated modules in ERP
solutions
Enhanced ERP Web ERP
ERP basic modules
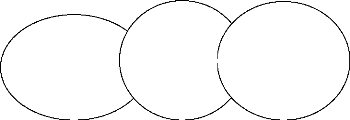
· Finance
· Logistics
· Manufacturing
· Human resources
· etc.
· SCM
· CRM
+
Web-enabled technologies
+
49
Source: Adapted from Blasis & Gunson (2002:17).
For many users, an ERP system is a «do it all» that
performs everything from sales orders to customer service. Others view it as a
data bus with data storage and retrieval capability. In addition, Gardiner,
Hanna and LaTour (in Shehab, Sharp, Supramaniam & Spedding, 2004:8) point
out that an ERP system can be used as a tool to help improve the performance
level of a supply chain network by helping to reduce cycle times. Boykin (in
Shehab et al., 2004:8) argues that an ERP system is the price of entry for
running a business and for being connected to other organisations in a network
economy to create B2B and electronic commerce. ERP brought about the myriad of
interconnections, which ensure that any other unit or department within the
organisation can obtain information in one part of the business. This makes it
simpler to see how the business as a whole is doing. ERP systems help people
eliminate redundant actions, analyse data and make better decisions (Sweat in
Gupta, 2000:115).
An ERP system is the information pipeline system within an
organisation which allows the organisation to move internal information
efficiently so that it may be used for decision support inside the organisation
and communicated via e-business technology to business partners throughout the
value chain (Balls et al., 2000:186). In addition, Siriginidi (2000:378)
defines ERP as an integrated suite of application software modules, providing
operational, managerial and strategic information for organisations to improve
productivity, quality and competitiveness.
From the above definitions, it can be concluded that an ERP
system can be regarded as an integrated organisation-wide software package that
uses a modular structure to support a broad spectrum of key operational areas
of the organisation. It provides a transactional backbone to the organisation
that allows the capture of basic cost and revenue related movements of
inventory. In so doing, ERP affords better access to management information
concerning business activity, showing actual sales and cost of sales in a
real-time fashion (Adam & Carton, 2003:22). The full installation of ERP
software across an entire organisation connects the components of the
organisation through a logical transmission and sharing of commonalties.
Therefore, in this interface the data such as sales becomes available at any
point in the business, and it courses its way through the software, which
automatically calculates the effects of the transaction on areas such as
manufacturing, inventory, procurement, invoicing and bookkeeping (Balls et al.,
2000:12). Clemons and Simons
50
(2001:207) state that ERP is a term used to describe business
software that is multifunctional in scope, integrated in nature and modular in
structure. Indeed, ERP systems are designed for multisite, multinational
companies, which require the ability to integrate business information, manage
resources and accommodate diverse business practices and processes across the
entire organisation. In support of the above view, Wood and Caldas (in Adam
& Carton, 2003:22) found in their survey of 40 organisations that had
implemented ERP that the main reason for doing so was the need to "integrate
the organisation's processes and information".
3.4 The general model of an ERP system compared to a
value chain system
According to McAdam and McCormack (2001:116), the concept of
integration within the functions of an organisation can be represented by
Porter's value chain model as depicted in figure 2.1. Porter looked at the
organisation as a collection of key functional activities that could be
separated and identified as primary activities (inbound logistics, operations,
outbound logistics, marketing and sales, and service) or support activities
(infrastructure, human resource management, technology development and
procurement). Porter arranged these activities in a value chain. Maximising the
linkages between the activities increases the efficiency of the organisation
and the marginal availability for increasing competitive advantage or for
adding shareholder value. Integration occurs between the primary activities in
each value chain, and is enabled by the support activities. It can also take
place between activities in different organisations, and in some cases, the
support activities also share resources. Thus, ERP systems aid the integration
of these various functional processes within the organisation's value chain.
Figure 3.2 below represents the general model of ERP systems and execution,
integrated functionality and the global nature of present-day organisations in
the different functional activities format of Porter's value chain model in
figure 2.1.
In figure 3.2, the circle at the centre represents the
entities (organisation, payroll/employees, cost accounting, general ledger,
job/project management, budgeting, logistics and materials, etc.) that
constitute the central database shared by all functions of the organisation.
The border represents the cross-enterprise functionality (multiplatform,
multimode manufacturing, electronic data interchange, workflow automation,
database creation, imaging, multilingual, etc.) that must be shared by all
systems. The cross-organisation borders would be multifaceted, act as
multifacilities and represent the capability required by the organisation to
compete and succeed globally. It is important for the system's total solution
to support multiple divisions or organisations under a
51
corporate banner and seamlessly integrate operating platforms
as the corporate database that results in integrated management information
(Siriginidi, 2000:379-80). The co-ordination performed by information system
integration (ERP system) within the organisation's value chain enables more
views to be shared, employee awareness to be broadened and customer
expectations to be tracked and met (Bhatt, 2000:1331)
Figure 3.2: The general model of an ERP
system
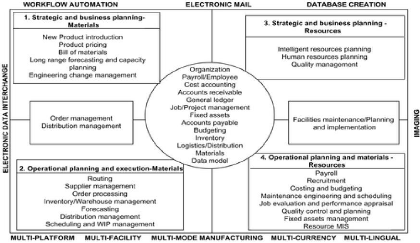
Source: Adapted from Siriginidi (2000:380).
The emphasis is further placed on the fact that the heart of
any ERP exercise materialises in the creation of an integrated data model.
Approaching it holistically, the ERP and execution model and its flexible set
of integrated applications keep operations flowing efficiently. It should be
looked upon as the acquisition of an asset, not as expenditure. An ERP system
as a business tool seamlessly integrates the strategic initiatives and policies
of the organisation with the operations, thus providing an effective means of
translating strategic business goals to real-time planning and control. In
order to achieve the integration of all the basic units of the business
transaction, ERP systems rely on large central relational databases. This
architecture represents a return to the
52
centralised control model of the 1960s and 1970s (Stirling,
Petty & Travis, 2002:430), where access to computing resources and data was
very much controlled by centralised IT departments. Therefore, ERP
implementations are an inherent part of a general phenomenon of centralisation
of control in large businesses back to a central corporate focal point (Clemons
& Simons, 2001:207).
3.5 The role and benefits of an ERP system
According to Ming, Fyun, Shihti & Chiu (2004:689-90), ERP
systems have developed beyond their originally design intended to provide
organisations with integrated, consistent and concurrent information that is
available across the organisation. Integrated with electronic data interchange,
it is used to streamline business processes in vertical markets, giving
organisations the control and management of their resources. Furthermore, ERP
systems provide a platform for integrating applications such as executive
information system data mining, SCM, CRM and e-commerce systems. The real
benefits of ERP systems currently are associated with the arrival of Web
applications, which facilitate ERP systems to extend to electronic markets
integrated with supply chains through B2B e-hubs. It further also extends to
partners to integrate their own operations with other functions and to manage,
monitor and execute all transactions in real time. An ERP system is considered
to be the price of entry into B2B, e-market and other organisations in a
network economy.
Davenport (in Adam & Carton, 2003:24) shows the
paradoxical impact of an ERP system on organisation and culture. ERP systems
provide universal, real-time access to operating and financial data, and allow
the organisations to streamline their management structures, creating flatter,
more flexible and more democratic organisations. ERP systems also involve the
centralisation of control over information and the standardisation of
processes, which are qualities more consistent with hierarchical, command and
control organisations with uniform cultures. Indeed, ERP systems help
organisations in cross-organisation application integration, where the
organisations can link their ERP systems directly to the disparate applications
of their suppliers and customers. Therefore, such integration benefits the
organisation in the following ways, which have been emphasised by Gupta
(2000:115-6):
· Web-based procurement application;
53
· The incorporation of the Internet in its applications;
and
· The outsourcing of ERP applications where the major
vendors of ERP are offering outsourcing programs to small and medium
organisations that are unable to implement the system themselves
Furthermore, an ERP system links processes, people, suppliers
and customers together, and it helps a business to globalise its operations,
expand its supply chain and customer relations base while simultaneously
integrating it with e-commerce. Adam and Carton (2003:22) highlight some of the
benefits achieved by the organisations looking to harness the tight global
co-ordination afforded by ERP systems, which are:
· Streamlining global financial and administrative
processes;
· Global lean production models with rapid shifting of
sourcing, manufacturing and distribution functions worldwide in response to
changing patterns in supply and demand; and
· Minimising excess manufacturing capacity, while reducing
component and finished goods inventory.
Thus, Spathis and Constaninides (in Ming et al., 2004:690)
position an ERP system as a tool which can be used to integrate manufacturing
and marketing functions to determine the competitiveness and profitability of
organisations and the production of real-time data, which is shared across the
organisation, resulting in the integration and the automation of business
processes, and the real benefit of integration and its ability to share
information with customers and suppliers within the organisation. The core
competency of ERP systems within an organisation can be expanded to vertical
networks. Sharing information is what transforms ERP systems into the backbone
of a supply chain, and not just the backbone for internal networks. The
benefits are magnified from the same internal advantages with better
co-ordination and optimisation by eliminating external uncertainties (Ming et
al., 2004:690).
3.5.1 The advantage and disadvantage of an ERP
system
According to Gupta (2000:115-16), the advantages and
disadvantages of ERP systems are as follows:
54
Advantages
· Y2K compliance;
· Ease of use;
· Integration of all functions;
· Online communication with suppliers and customers;
· Customisation;
· Improvement of decision-making due to the availability of
timely and appropriate information;
· Improved process time;
· Feasibility of administering pro facto control
on the operations;
· Internet interface; and
· Reduction of planning inaccuracies.
Disadvantages
· Organisational resistance to change, which may be
high;
· Changeover, which may take a long time causing cost
overruns;
· Data errors, which can be carried throughout the system;
and
· Maintenance is costly and time-consuming.
3.5.2 The characteristics of an ERP system
According to Hyung, Nam-Kyu & Sang (2003:197-200), the
major characteristics of an ERP system are an enterprise-wide system that
covers all the business functions and information resources, integrated
database, built-in best industry practice, packaged software and open
architecture. In addition, ERP enables reduction of system development time,
flexibility, standardisation of workflow and effective business planning
capability. Therefore, ERP is characterised by the aspects of classification of
information exchange, sharing and information service as shown in table 3.1
below.
55
Table 3.1: Characteristics of an ERP system
Classification Characteristics of ERP system
Information interchange EDI connection
Open system and globalisation
Information sharing One fact, one place
(integrated task system)
Standard business process model, GroupWare connection and
executive information system function
Information service End-user computing and
integrated database
Source: Adapted from Hyung et al., (2003:200).
It must further possess some key characteristics and features to
qualify as a true business process integration solution. These features are:
· Flexible. An ERP system should be flexible in order to
respond to the changing needs of an organisation. Client/server technology
enables ERP systems to run across various database servers through open
database connectivity.
· Comprehensive. An ERP system is able to support a variety
of organisational functions and is suitable for a wide range of business
organisations.
· Modular and open. An ERP system should have open
system architecture, meaning that any module can be interfaced or disconnected
whenever required without affecting the other modules. It should also support
multiple hardware platforms for organisations having a diverse collection of
systems.
· Beyond the organisation. A good ERP system is not
confined to the organisational boundaries, but can support online connections
to other business entities outside the organisation.
· Simulation of reality. An ERP system can simulate real
business processes on the computer.
· Multiple environments required. For ERP, most
businesses must maintain multiple environments in order to achieve uptime
requirements: development/test, promote-toproduction, highly available
production, and disaster recovery.
56
3.6 ERP system: The hub of an MNE
Davenport (in Adam & Carton, 2003:22) states that
organisations collect, generate and store vast quantities of data which is
«spread across dozens or even hundreds of separate computer systems, each
housed in an individual function, business unit, region, factory or
office». Therefore, ERP systems have a huge impact on business
productivity due to the workload of reeking, reformatting, updating, debugging,
etc. When management is relying on information from incompatible systems to
make decisions, instinct becomes more important than sound business rationale.
Thus, ERP systems are positioned as a tool designed for multisite,
multinational organisations, which require the ability to integrate business
information, manage resources and accommodate diverse business practices and
processes across the entire organisation. In addition, Balls et al.,
(2000:30-1) note that an ERP system provides consistency of information across
a global organisation and integrates the following:
· Resource planning, which includes forecasting and
planning purchasing and material management, warehouse and distribution
management, product distribution, accounting and finance. By providing timely,
accurate and complete data about these areas, ERP software helps a company to
assess, report on and deploy its resources quickly, while also focusing on
organisational priorities. For example, a company can assess its total cash
position globally for a large supplier who may also be a customer. All too
often, bills are paid to suppliers who are also customers and who are owing
more than they are owed.
· Supply chain management, which includes understanding
demand and capacity, and the scheduling of capacity to meet demand. By linking
disparate parts of an organisation with ERP, more efficient schedules can be
established that optimally satisfies the organisation's needs. This reduces
cycle time and inventory levels, and improves a company's cash position.
· Demand chain management, which includes handling
product configuration (quotes, pricing and contracts, promotions and
commissions). By consolidating information with ERP, contracts can be better
negotiated, pricing can be established to consider the total organisation-wide
position, and sales offices can be better assessed, rewarded and managed.
· Knowledge management, which includes creating a data
warehouse, a central repository for the organisation's data, performing
business analysis on this data, providing decision support for organisation
leadership and creating future customer-based strategies. These activities
comprise
57
a management information system, which facilitates the making
of appropriate business decisions. In this capacity, ERP evolves from a
transaction-processing engine into a true distiller of information. Data
warehousing can become a powerful tool for corporate executives and managers
only if it is fed with data that is consistent, reliable and timely.
3.6.1 The modules of an ERP system
ERP systems generally include some of the most popular
functions within each module, but the names and numbers of modules in an ERP
system provided by various software vendors may differ. A typical system
integrates all these functions by allowing its modules to share and transfer
information freely, centralising information in a single database accessible by
all modules. The model of an ERP system, according to Siriginidi (2000:380) and
shown in figure 3.2 above, includes areas as such as:
· Finance (financial accounting, treasury management,
organisation control and asset management);
· Logistics (production planning, materials management,
plant maintenance, quality management, project systems, sales and
distribution);
· Human resources (personnel management, training and
development and skills inventory); and
· Workflow (integrates the entire organisation with
flexible assignment of tasks and responsibilities to locations, positions,
jobs, groups or individuals).
In addition, other functionality requirements stipulated by
Sarkis and Sundarraj (2000:201) include:
· Business planning and material requirement planning;
· Marketing and sales (sales and distribution, inventory
and purchases);
· Resource flow management (production scheduling, finance
and human resources management);
· Works documentation (work order, shop order release,
material issue release and route cards for parts and assemblies), shopfloor
control and management and costing;
· Manufacturing and maintenance; and
· Engineering data control (bill of materials, process plan
and work centre data).
58
In a fully integrated ERP system, these activities are
accomplished by utilising the five tightly integrated modules of finance,
manufacturing, logistics, sales and marketing, and human resources, as briefly
discussed next (Balls et al., 2000:31).
· Finance
ERP software significantly reduces the cost of financial
record keeping. The consistency of ERP system data provides improved
information for analysis and a seamless reconciliation from the general ledger
sub-ledgers. The data is updated in real time throughout the month, and a basis
is created for linking operational results and the financial effects of those
results. With ERP, a physical transaction cannot be booked without the
resulting financial effect being shown. This visibility of activities across
finance and operations allows operational managers to better understand the
effects of their decisions. The company's financial department is better
equipped to provide decision support to corporate leadership, create strategic
performance measures and engage in strategic cost management.
· Manufacturing
With ERP software's ability to explicitly link the
operational and financial systems, organisations can easily determine how
operational causes equal financial effects. The software provides a consistent
set of product names in a central product registry, a consistent way of looking
at customers and vendors, integration of sales and production information, and
a way to calculate availability of products for sales, distribution and
materials management. An integrated ERP system also enables better order to
production planning by linking sales and distribution to materials management
production planning, and financials in real time, real-time visibility of
customer orders and customer demand, and modelling of anticipated orders. With
ERP, sales opportunities turn into orders based on past performance
information, stock can be adjusted nearly instantly and detailed manufacturing
resource planning can be performed daily.
· Logistics
ERP integrates distribution more tightly with manufacturing,
sales and financial reporting, thereby enhancing reporting of future
performance indicators as well as past performance measures. The software
provides an integrated basis for managing the signals that support the
distribution
59
environment necessary to meet twenty-first century customer
desires and demands. ERP technology supports strategic purchasing and
"materials only" costing rather than standard costing and aligned performance
indicators, rather than traditional indicators that measure functional silos
and support customer-driven, low-cost operations. ERP also supports
cross-functional, process-driven, customer-focused logistics and
distribution.
· Sales and marketing
ERP software enhances an organisation's sales efforts in a
number of ways. Performing profitability analyses requires real-time data for
costs, revenue and sales volumes. With an ERP system, the company can perform
profitability analysis, showing profits and contribution margins by market
segment. With ERP software, it is also possible to design sophisticated pricing
procedures that include numerous prices, discounts, rebates and taxes
considerations. The sales organisations can use ERP to project much more
accurate delivery dates for orders. In an e-business environment, customers
will be able to receive much more accurate delivery date information over the
Web, and, when the ERP system is properly linked to an e-business front-end,
look into the company's finished-goods and work-in-process inventories, as well
as materials availability to determine how quickly an order can be filled.
· Human resources
An ERP system supports an organisation in its human resource
planning, development and remuneration areas. It provides an integrated
database of personnel (employed or contracted), maintains salary and benefits
structures, supports planning and recruiting, and keeps track of reimbursable
travel and living expenses. ERP does payroll accounting for a wide variety of
individual national requirements and allows a company to centralise or
decentralise the payroll function by country or by legal entity. ERP records
individual qualifications and requirements used for resource planning, enhances
career and succession planning, and co-ordination of training programmes, and
maximises time management, from planning to recording and controlling time,
including shift planning, time exception reporting and time reporting for cost
allocation where staff charge their time to specific cost objects such as
projects or service orders.
60
3.6.2 ERP system package
According to Shehab et al., (2004:361), although an ERP
system is a pure software package, it embodies ways of doing business. In
addition, an ERP system is not just a pure software package to be tailored to
an organisation, but rather an organisational infrastructure that affects how
people work. It "imposes its own logic on an organisation' s strategy, and
culture" (Davenport, Lee & Lee in Shehab et al., 2004:361). ERP has
packaged best business practices in the form of a business blueprint. This
blueprint could guide organisations from the beginning phase of product
engineering, including evaluation and analysis, to the final stages of product
implementation.
In total there are about a hundred ERP providers worldwide,
e.g. SAP-AG, Oracle, JD Edwards, PeopleSoft and Baan, SSA, BPCS, Inertia Mover,
QAD, MFG and PRD. The systems have a few common properties and they are all
based on a central, relational database, built on client/server architecture
and consist of various functional modules as indicated above. Among the most
important attributes of an ERP system, according to Shehab et al., (2004:60-5),
is its ability to:
· Automate and integrate business processes across
organisational functions and locations;
· Enable implementation of all variations of best business
practices with a view towards enhancing productivity;
· Share common data and practices across the entire
organisation in order to reduce errors; and
· Produce and access information in a real-time environment
to facilitate rapid and better decisions and cost reduction.
All ERP system packages need to be customised and
parameterised to suit the needs of individual organisations. However, the
system packages touch many aspects of a company's internal and external
operations. Consequently, successful deployment and use of ERP systems are
critical to organisational performance and survival.
3.7 Global ERP system configuration
Davenport (in Adam and Carton, 2003:24) estimates how much
uniformity should exist in the way ERP does business in different regions or
countries. The differences in regional markets remain so profound for most
organisations that strict process uniformity may actually be
counter-productive.
61
A configuration table enables a company to tailor a
particular aspect of the system to the way it chooses to do business.
Organisations can select, for example, the functional currency for a particular
operating unit, or whether they want to recognise product revenue by
geographical unit, product line or distribution channel (Adam and Carton,
2003:24). Therefore, Davenport (in Madapusi & D'souza, 2005:8) warns that
organisations must remain flexible and allow regional units to tailor their
operations to local customer requirements and regulatory structures. In
practical terms, in Europe, ERP projects are more complex than in North America
because of diverse national cultures, which influence organisational culture
and make successful implementation of MNEs' ERP solutions difficult.
However, in the study of Adam and Carton (2003:23-4),
Krumbholz states that failure to adapt ERP packages to fit the national culture
leads to projects which are expensive. Therefore, MNEs face a choice between
using their ERP as a standardisation tool or preserving (or rather tolerating)
some degree of local independence in software terms. The resulting
standardisation in business processes allows companies to treat supply and
demand from a global perspective to consolidate corporate information resources
under one roof, shorten execution time, lower costs in supply chains, reduce
stock levels, improve on-time delivery and improve visibility and product
assortment with respect to customer demand. Thus, Davenport (1998:126)
recommends a type of federalist system, where different versions of the same
system are rolled out to each regional unit. This raises its own problems for
the company, i.e. deciding on what aspects of the system need to be uniform and
what aspects can be allowed to vary (Horwitt, 1998:1).
3.7.1 Alignment between ERP system configuration and
international strategy
Madapusi and D'souza (2005:8) suggest that successful ERP
systems tend to be those that are closely aligned with the types of
international strategies that the organisation has chosen to adopt. Therefore,
it is important that management understand the interrelationship between ERP
system configuration and the international strategy of the organisation.
Madapusi and D'souza use the two constructs to develop a framework explaining
how management at an MNE can use it to align ERP configuration with the
international strategy of the organisation. According to Markus, Tanis and Van
Fenema (2000:42), the prevailing wisdom on ERP system configuration is that
management has to address three issues, namely:
62
· ERP software configuration;
· ERP information architecture; and
· ERP system rollout.
ERP software configuration
The findings of Koch (2001:68) indicate that an ERP system
should be configured hierarchically at four levels in an organisation:
· Organisation level. There are four types of
organisation-level ERP configurations that international organisations can
adopt, namely single-financial/single-operation,
singlefinancial/multi-operations, multi-financials/single-operation, and
multi-financials/multi- operations.
· The system level. At this level, business activities such
as logistics, financials and operations are implemented as modules.
· Business process level. At this level, the focus is on
the customisation of user profiles, parameters and business processes.
· Customisation level. This involves custom-designed
modifications and extensions to ERP application.
ERP information architecture
According to Clemons and Simons, and Zrimsek and Prior (in
Madapusi and D'souza, 2005:10), there are three commonly accepted ways to
configure ERP information architecture:
· Centralised architecture. This refers to an organisation
that has achieved high levels of standardisation of data and commonality of
business processes.
· Distributed architecture. This refers to the organisation
that has a strong history of autonomous business units.
· Hybrid architecture. This refers to the organisations
that want to leverage their global supply chains and at the same time localise
their products and services, and prefer hybrid architectures that are less than
completely centralised or distributed.
63
ERP system rollout
Parr and Shanks (2000:7) comment that when configuring ERP
systems, organisation's management must deal with the challenges of ERP system
rollout. Parr and Shanks' (2000:8) research findings suggest that system
features such as the number of sites and users, the level of complexity of the
business processes, the level of customisation, the mix of ERP modules chosen
and the existence of legacy system could be critical in determining the success
of an organisation's rollout strategy. These factors can lead to varied
approaches to ERP system rollout.
However, there is good support for two general approaches to
ERP system rollout that were popularised in the mid-1990s by Mabert, Soni and
Venkataraman (2003:237) and Markus et al., (2000:45), namely the "big bang"
approach and the phased implementation approach. The organisations that prefer
a "big bang" approach to ERP implementation roll out a set of ERP application
modules across their worldwide operations simultaneously. A well-planned big
bang rollout enables the organisation to rapidly implement and derive benefits
from a core set of integrative application modules and processes. By contrast,
the phased implementation of application modules takes place at national level,
with integration primarily through financial reporting modules. Although phased
implementation is time-consuming, it involves less risk compared to the big
bang approach, and tends to involve less re-engineering efforts. The phased
implementation component of the rollout allows the organisation to learn, adapt
and explore alternate courses of action (Scott and Vessey in Madapusi &
D'souza, 2005:14).
3.7.2 Types of international strategies
Businesses typically adopt one of three types of international
strategies, namely multinational, global, or transnational as briefly discussed
next (Madapusi and D'souza, 2005:11).
· Multinational strategy
One of the primary objectives of a multinational strategy is
to build sensitivity and responsiveness to differing national environments.
Organisations that pursue this strategy offer differentiated products and
services to satisfy the local needs of their national units. These
organisations derive most of their value from downstream value chain
activities, such as marketing, sales and service, and often clone their value
chains in multiple national markets.
64
· Global strategy
The constant search for global efficiencies and cost
considerations drives the actions of organisations that choose a global
strategy. These organisations leverage economies gained through product
standardisation and global sourcing. Control and co-ordination of activities
are typically concentrated at the organisation's headquarters.
· Transnational strategy
Organisations that adopt a transnational strategy focus on
local responsiveness and global efficiency - a "best of both worlds" approach.
Organisations that pursue this strategy recognise that their competitive
advantage accrues from location advantages and economic efficiencies. The
theoretical underpinnings of ERP systems discussed above relate to the
configuration and international strategy viewed in ERP configuration,
architecture and rollout, with international strategy alignment for
organisations that use a multinational strategy only, together with global and
transnational strategies.
3.7.3 ERP systems for organisations that use an MNE
strategy
Organisations that adopt an MNE strategy are often structured
as decentralised federations that grant strategic and operational latitude to
national units. Because headquarters focuses primarily on the bottom line, it
treats each national unit as a profit centre and prefers governance mechanisms
that favour standardised outputs. Mutual adjustment is encouraged through
informal headquarter-national unit relationships. Not surprisingly,
organisations that have strongly independent national units also have
independently run IT operations, as stipulated by Bartlett and Ghoshal,
Jarvenpaa and Ives, Karimi and Konsynski (in Madapusi & D'souza,
2005:12).
· ERP software configuration and MNE
strategy
At organisation level, organisations that implement an MNE
strategy tend to select a multifinancials/multi-operations logical structure
for their ERP. At system level, an organisation tends to have a system
independent of but linked to headquarters through financial reporting modules.
At business process level, the system is based on detailed levels. At
customisation configuration level, the system is based on high levels.
65
· ERP information architecture and MNE
strategy
Organisations using an MNE strategy typically opt for
distributed information architectures with stand-alone local databases and
application, the configuration of local hardware requirements, the involvement
of maximum use of a local area network (LAN) and minimal use of a wide area
network (WAN). In this ERP architecture, each local unit is autonomous.
Headquarter linkage occurs primarily through financial reporting structures
(Clemons & Simons, 2001:207-10). The national units are allowed
considerable latitude in determining their own hardware requirements. Network
bandwidth requirements are restricted to managing and co-ordinating local
operations. WAN bandwidth requirements are minimal because of limited
headquarter-national unit interactions.
· ERP system rollout and MNE strategy
The preferred rollout option would be a phased implementation
of application modules at national level, with integration primarily through
financial reporting. Organisations that adopt a multinational strategy face
unique challenges. The near absence of centralised control and standardisation
often results in multiple and varied ERP configurations across national units.
Application functionality can also vary across multiple platforms, making it
difficult to obtain an integrated/holistic view of crucial business data.
Industry best practices, which are embedded in typical ERP vendor packages,
have been found to enhance control and integration over worldwide operations.
However, because an ERP system is independently developed, organisations must
invest in customised integration code to facilitate data alignment (Madapusi
& D'souza, 2005:12).
3.8 Strategic factors for the evaluation and selection
of an ERP system
For an ERP system to meet the requirement of the
organisation's value chain system, it needs to be evaluated in terms of its
modules and functionality relating to the organisation objectives. ERP
encompasses all the traditional functional areas of a business, in addition to
the manufacturing focus of MRPII systems. A typical set of business functions
supported by an ERP system is summarised below based on Dykstra and Cornelison,
and Olinger (in Sarkis & Sundarraj, 2000:206).
· Business planning includes the vision and the mission of
the organisation, and the strategies needed to accomplish them.
66
· Organisation performance measurement systems help
the organisation to determine how well they are doing, to continuously improve
and manage the organisational processes. These systems include performance
information on the internal and external supply chain.
· Decision support helps in the management of the internal
and external supply chain, which may include optimisation, simulation,
heuristic, quantitative and qualitative modelling approaches.
· Marketing and sales include sales analysis and forecast
of the demand for products in the business plan, sales order management,
customer maintenance and billing information system.
· Manufacturing includes the functions of a traditional
MRPII system (capacity planning, material resource planning, inventory
management, bills of material).
· Finance and accounting include payroll, product costing,
accounts payable and receivable, general ledger and asset management
information systems.
· Engineering includes changes made by the engineering
department with respect to routings, bills of material, quality control,
machining programs, product designs, maintenance information, etc.
· Human resources include a listing of employees, their
status within the organisation and benefits owed to them by the company.
· Purchasing includes supplier, performance,
product sourcing, in-bound logistics tracking and materials management
information systems. These systems can provide direct linkage to the upstream
external supply chain.
· Logistics help the outbound logistics management of
the organisation with control and linkage to external customers or other
divisions of the same organisation such as warehouses. These systems provide
significant linkage to the downstream external supply chain.
· After-sales service is meant to aid the customers
after the sale of a product. Information concerning service parts inventory,
such as locations and sources, product reliability, and other performance
measures would be needed in this system. Its inclusion is important because it
is one of the more forgotten factors.
· Information systems are a function central to the
management of ERP. Data accuracy, maintenance, user and performance information
is all-important to this function. They ensure that the value chain operates
efficiently and effectively with respect to information sharing, acquisition
and delivery.
67
Sarkis and Sundarraj (2000:205) integrate the evaluation
factors mentioned above into one conceptual model as shown in figure 3.3 below.
The control factors (business planning, decision support and organisation
performance measurement system) of the internal supply chain are placed over
the various internal supply chain factors. The various internal supply chain
factors are composed of the remaining processes and functions as described
above (factors, especially the engineering and purchasing, are close to the
suppliers, although they are not the only ones with linkages to suppliers). In
a similar vein, customers are linked to marketing, logistics and after-sales
service. In the middle of figure 3.3, linking all these internal supply chain
factors is the IS factor (ERP). It is clear that there is a two-way
relationship with IS to show that it is meant to integrate all the various
factors to each other, and that they are allowed and able to communicate with
one another.
Figure 3.3: The conceptual model of ERP system linkages
with supply chain factors
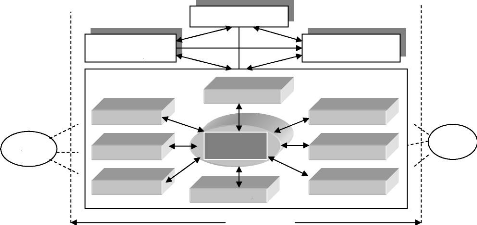
Business Planning
Enterprise Performance Measurement
System
Decision Support
MRP II
Engineering
Marketing
Suppliers
Purchasing
Information System
DRP/ Logistics
Human Resources
After - Sales Service
Finance and Accounting
Internal Supply Chain
Customers
Source: Adapted from Sarkis and Sundarraj (2000:207).
68
3.8.1 Selection of an ERP system
For a global ERP rollout, the MNEs that want to implement the
system need to know if the ERP software selected is designed to work in
different countries. A good selection will allow a global organisation to be
able to control and co-ordinate its various remote-operating units with
accurate and real-time information provided by ERP software, since some of the
system software has the ability to integrate the more remote subsidiaries into
corporate practice and allows the sharing of information in standard format
across departments, currencies, languages and national borders. ERP software
product purchasing is a high cost and risky process. It is therefore critical
to make this project successful for an organisation. To be successful, the
right solution should be selected and the selected software package must be
used effectively (Baki & Cakar, 2005:76). Tanner (in Neves, Fenn &
Sulcas, 2004:45) argues that correct ERP selection is vital to minimise
financial risk and uncertainties about the software and its compatibility with
the organisation's business structure.
If a poor choice of software system is made, it can adversely
affect the organisation as a whole, even jeopardising its very existence. This
highlights the need for performing adequate levels of research into making the
correct choice of software and preparing the organisation for its introduction
(Neves et al., 2004:45). Bingi, Sharma and Godla, as well as Horwitt (in Adam
& Carton, 2003:22) note that ERP systems could be used to provide a
«common language» between units. In addition, Baki and Cakar
(2005:76) assert that a selected ERP solution should be able to support
decision-making. Mabert et al., (in Baki & Cakar, 2005:76) argue that if
the right ERP solution is selected, it can be an excellent decision support
tool that will provide a competitive advantage. In addition, Somers and Nelson
(2001:2939) stress that the choice of package involves important decisions
related to budgets, time frames, goals and deliverables that will shape the
entire project. Choosing the right ERP solution that best matches the
organisational information needs and processes is critical to ensure minimal
modification and successful implementation and use. The wrong software will not
fit the organisation's strategic goal or business.
This necessitates the involvement of a proper selection
mechanism, evaluation and strategic technical planning model tool such as the
value chain approach discussed in chapter 2 and the methodical approach
formulated in chapter 7 of this study. In fact, software and hardware
characteristics are critical for ERP implementation success, and conducting a
requirement analysis
69
in the early stage of project implementation and thoroughly
reviewing a number of hardware/software solutions that might result in the
system that better fits the users' requirements are essential (Petroni,
2002:333). Baki and Cakar (2005:77-81) recommend the importance and usage of a
benchmark selection criteria checklist when selecting the package. Elements
such as functionality, technical aspect, cost, service and support, vision,
system reliability, compatibility with other systems, and ease of customisation
must be taken into account. Other factors to be considered are:
· Market position of the vendor, better fit with
organisational structure, domain knowledge of the supplier, references of the
vendors and fit with parent/allied organisation systems; and
· Cross-module integration, implementation time,
methodology of the software and consultation.
3.8.2 Methodology of an ERP system
According to Stirling, Petty and Travis (2002:430-5), the
methodology has seven decisions points, each relating to a different outcome.
The methodology is supported by a series of questions to assist users in making
appropriate decisions. The goal of the methodology in the analysis of ERP has
to provide a structured approach to the problem of meeting systems requirements
within a specific department or overall within the organisation. Therefore,
once an ERP system database is based on a proprietary package selection, and in
new business requirement identification, this is then subject to a series of
tests in decision point framework questionnaires to assist users in tailoring
their system.
The methodology framework below in figure 3.4 guides the user
through a structured decision-making process, and the decisions at each point
require judgement and experience. As a result, a series of questions were
devised to be applied at each decision point, once the methodology has been
developed. Stirling et al., (2002:431) state that it is crucial to undertake
some forms of validation. This can be achieved through a series of structured
interviews with systems development professionals.
70
The methodology proposed by ERP vendors should be effective
and should not include unnecessary activities for the organisation. In every
stage of the methodology, it should be determined what activities will be
carried out how, when and with which resources.
Figure 3.4: Outline of the methodology
No
No
No
Change core
system
Yes
Change business process
Purchase
appropriate module

Yes
Use
spare field

Yes

Yes

Business requirement

Does the business requirement represent a radical
change?

Should the process be change?

Can an available module be used?

Can spare fields in the core systems be
utilised?

No
Yes
No
Yes
Use subsidiary system
Modify core system
Can a subsidiary system be used?
Must the core be modified?
|
No
|
Yes
|
Requirement for data transfer
|
|
Linked system
|
|
|
|
|
|
|
|
|
|
|
|
|
Use an independent system
|
|
|
|
|
|
|
|
|
|
|
|
|
|
No requirement for data transfer
Source: Adapted from Stirling et al., (2002:436).
3.9 The implementation of an ERP system
The acquisition and implementation of ERP systems are very
effort-intensive processes. An empirical analysis of the implementation
process in European organisations revealed mean
71
implementation costs of 1.5 million Euros and a mean
implementation time of 13.5 months (Buxmann & Konig in Bernroider &
Tang, 2003:7). In addition, high risks are also involved in every ERP project.
The far-reaching structural changes following ERP software implementation can
be disastrous. Many ERP implementations fail to achieve their corporate goals
(Buckhout, Frey & Nemec, 1999:118). It can be assumed that the failure of
the system project implementation can often be attributed to the major mistakes
made in the early stages of the ERP life cycle prior to the implementation
process.
According to Esteves and Pastor (in Bernroider & Tang,
2003:5), a typical life cycle of an ERP system covers six different stages,
namely adoption decision, acquisition, implementation, use and maintenance,
evolution and retirement. Conducting a requirement analysis in the early stage
of the project implementation and thoroughly reviewing a number of
hardware/software solutions might result in a system that better fits the
users' requirements. MNEs that implement a global ERP solution frequently find
themselves in a position where the changes are imposed rather than designed.
Blasis and Gunson (2002:6) assert that IT software projects often fail and ERP
implementation projects do not escape this tendency. However, ERP solutions do
not fail primarily for technical reasons. Further analysis of the factors of
success or failure of ERP implementation projects indicates that it is
primarily the implementation effect of an organisation, the workplace and the
individuals at work, which yields a positive or negative result.
The main implementation risks associated with ERP projects
are related to change management and business re-engineering those results from
switching to ERP software. To overcome users' resistance to change, Aladwani
(2001:273) recommends that top management study the structure and needs of the
users and the causes of potential resistance among them, and deal with the
situation by using the appropriate strategies and techniques in order to
introduce ERP successfully and evaluate the status of change management
efforts. In addition, for many organisations, the real challenge of ERP
implementation is not the introduction of new systems, but the fact that they
imply "instilling discipline into undisciplined organisations." Because of its
modularly, ERP software allows some degree of customisation (i.e. selection of
modules best suited to the business's activities). However, the system's
complexity makes major modifications impracticable. The very integration
afforded by the interdependencies of data within the different modules of the
system means that changes in configuration could have huge knock-on affects
throughout the system.
72
From a management perspective, the nature of ERP
implementation problems includes strategic, organisational and technical
dimensions. ERP implementation involves a mix of business process change and
software configuration to align the software with the business processes.
Ho, Wu and Tai (2004:235) state that numerous scholars and
experts have proposed explanations for the failure of the implementations.
These include inadequate resources, a lack of support from upper management, a
lack of promotion, poor integration of business strategies, inappropriate
choice of tactics and failure to establish the necessary IT infrastructure
within organisations. Together with problems of existing system complexity,
system integration and organisational process transparency, business process
re-engineering, exterior consultation, the role of suppliers, user training and
system customisation all complicate matters.
3.9.1 Factors affecting the implementation
process
The factors specific to ERP implementation success include
re-engineering business processes, understanding corporate cultural change and
using business analysts on the project team. Bancroft, Seip and Sprengel
(Shehab et al., 2004:367) provide the following critical success factors for
ERP implementation:
· Support from top management;
· The presence of a champion;
· Good communication with stakeholders; and
· Effective project management.
Nah, Lau and Kuang (Shehab et al., 2004:369) researched the
critical factors for initial and ongoing ERP implementation success and
identified 11 factors:
· ERP teamwork and composition;
· Change management programmes and culture;
· Support from top management;
· Business plan and vision;
· Business process re-engineering with minimum
customisation;
73
· Project management;
· Monitoring and evaluation of performance;
· Effective communication;
· Software development, testing and troubleshooting; and
· Project champions, and appropriate business and IT legacy
systems.
In a study focusing on the complexity of multisite ERP
implementation, Markus et al., (2000:43) claim that implementing ERP systems
could be quite straightforward when organisations are simply structured and
operate in one or a few locations. However, when organisations are structurally
complex and geographically dispersed, implementing ERP involves difficult,
possibly unique, technical and managerial choices and challenges.
3.9.2 A strategic approach to ERP
implementation
The are two different strategic approaches to ERP
implementation, according to Baatz, Slater and Koch (available online). In the
first approach, an organisation has to re-engineer the business process to
accommodate the functionality of the ERP system, which means changes in
long-established ways of doing business and reviewing important people's roles
and responsibilities. This approach takes advantage of future ERP releases,
benefits from the improved processes and avoids costly irreparable errors. The
other approach is the customisation of the software to fit the existing
process, which slows down the project, introduces dangerous bugs into the
system and makes upgrading the software to the ERP vendor's next release
excruciatingly difficult, because the customisations will need to be developed
and rewritten to fit with the new version. Since each alternative has
drawbacks, the solution can be a compromise between complete process redesign
and massive software modification. However, many companies tend to take the
advice of their ERP software vendor and focus more on process changes (Shehab
et al., 2004:8).
3.9.3 Cost of ERP implementation
ERP implementation involves two kinds of costs: quantifiable
costs that lend themselves to a discounted cash flow analysis, and human factor
costs that are unquantifiable but very real. Quantifiable costs fall into five
categories: hardware, software, training and change management, data
conversions, and re-engineering. Other costs to the organisation involve
non-quantifiable costs
74
to the governance structure. An ERP installation affects both
the power structures within the organisation and the company's usual
decision-making process (Balls et al., 2000:53). The benefits of ERP system
implementation are both quantifiable and qualitative. The quantifiable benefits
are increased process efficiency, reduced transaction costs due to the
availability and accuracy of data and the ability to turn that data into
meaningful information, reduced information organisation costs in hardware,
software and staff necessary to maintain legacy systems, and reduced staff
training costs over time as people become more «change ready». The
qualitative benefits include a more flexible governance and organisational
structure, and a workforce ready to change and focus more on high-value-added
tasks and easy capitalisation on opportunities as they present themselves
(Balls et al., 2000:54).
3.10 Conclusion
There is different ERP software in the market, consisting of
many modules. Since every organisation is unique, before implementing an ERP
system, the organisation must choose the most suitable solution to meet its
needs and thus enable it to gain a competitive advantage. It was argued in this
chapter that this could be achieved by viewing ERP as a strategic IT tool, and
conducting a proper analysis before the adoption and implementation process.
Verville and Halingten (2002:207) highlight the importance of the acquisition
process of an ERP system as it allows examination of all the dimensions and
implications (benefits, risks, challenges, costs, etc.) prior to the commitment
of formidable amounts of money, time and resources.
The literature study of the ERP concept in this chapter has
revealed that ERP software itself is a value chain system related to the value
chain approach. Therefore, the theory of the ERP system discussed in this study
is becoming an evaluative tool relating to the value chain theory that can be
used to analyse and evaluate ERP software (Axapta Microsoft solution software)
components and attributes, modules and functionalities.
75
|