Mémoire de Fin d'Etudes
Pour l'Obtention du Diplôme
d'Ingénieur d'Etat
en Informatique
Présenté par :
BOUDAOUD LAKHDAR EL AMINE
Option : Système d'information avancée
I
Session Juin 2009 THÈME
Proposition d'un système de planification de
la
maintenance dans une raffinerie
pétrolière
Encadré par : Mr B. BELDJILALI
Co-encadré par : Mme N. AISSANI
Jury
Président : Mr ADLA
Examinateur : Mme MOKHTARI Examinateur :
Mr LARABI
Code PFE : 479
1
2
Université d'Oran Faculté
des Sciences
Département d'Informatique
Proposition d'un système de
planification
de la maintenance dans une Raffinerie
pétrolière
Projet de Fin d'Etudes pour l'obtention du
Diplôme d'Ingénieur d'Etat en
Informatique
BOUDAOUD Lakhdar El Amine
Encadrés par Mr. BELDJILALI
bouzienne & Mm AISSANI Nassima
Présenté le XX Juin 2009 devant le jury
:
Mr ADLA
Mme MOKHTARI Mr LARABI
Dédicaces
Je dédie ce modeste travail à :
Mes très chers parents, mes soeurs et mes
frères
.
BOUDAOUD BENAMAR
Qui n'a jamais cessé de me soutenir
matériellement et moralement pour que je puisse
finir mes études et avoir une bonne formation et surtout être
le meilleur Merci encore mille fois.
Toute personne qui de prés ou de loin, a
participé à ma formation. Tous ceux qui ont apporté
leur aide ou contribution afin de mener à bien ce modeste
travail.
3
Lakhdar El Amine
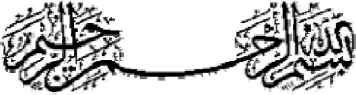
4
Remerciement
Avant toute chose je tiens à remercier le grand
"DIEU" de m'avoir donné le courage et la
volonté qui m'ont permis de réaliser ce travail.
Je tiens à remercier mon encadreurs, Mr BELDJILALI
BOUZIENNE et mon
Co-encadreur Mme AISSANI NASSIMA de proposer ce sujet,
et d'accepter de m'encadrer, et de m'avoir guidé au cours de la
réalisation du projet.
Mes sincères remerciements à Mr ADLA
d'avoir accepté de présider le jury. Je tiens
aussi à remercier les examinateurs de ce travail,
Mme MOKHTARI, Mr LARABI
Merci également à l'ensemble des
enseignants du département d'Informatique à
l'Université d'Oran.
5
Sommaire
6
7
8
Contenu
Mémoire de Fin d'Etudes 1
Introduction générale 14
CHAPITRE I 16
Problème d'ordonnancement 16
I.1 Introduction 17
I.2 Définition générale de
l'ordonnancement 17
I.3 Eléments fondamentaux 17
I.3.? Définition du problème
d'ordonnancement 17
I.3.2 Typologie des problèmes d'ordonnancement
18
I.3.3 Les tâches 20
I.3.4 Les ressources 21
I.3.5 Les contraintes 21
I.3.6 les objectifs 23
I.? Méthodes de résolutions de
problème d'ordonnancement : 23
II.4.1 Méthodes exactes 24
II.4.2 Méthodes Approchées 24
I.? caractéristiques générales
d'ordonnancement : 27
I.5.1 ordonnancement admissible (acceptable) : 27
I.5.2 Ordonnancement semi actif 27
I.5.3 Ordonnancement actif 28
I.5.4 Ordonnancement sans retards 28
I.6 représentation des solutions 29
I.7.1 machine unique 37
I.7.2 machine parallèle 37
I.7.3 flow shop 38
I.7.4 job shop 39
I.8 Conclusion 41
CHAPITRE II 42
Description générale de la raffinerie
d'ARZEW, l'unité 3000 et du département maintenance
42
II.1 Introduction 43
II.2 description générale du complexe 43
II.2.1Historique 43
II.2.2 capacité de production 44
II.2.3 Description des différentes zones de la production
45
II.2.4 organisation du personnel de la raffinerie 49
II.2.5 Organisation du complexe 51
II.3 description de département de maintenance de la
raffinerie 52
II.3.1 Objectif du département maintenance : 52
II.3.2 Organigramme de structure de la maintenance 53
II.3.3 différents services de la maintenance 54
II.3.4 Système de gestion de la maintenance
«Système G » 56
II.4 Conclusion 60
CHAPITRE III 62
La maintenance dans les systèmes de production 62
III.1 Introduction 63
III.2 La maintenance -
Généralités 63
III.2.1 Evolution de la maintenance 64
III.3 Les politiques de maintenance 66
III.3.1 La Maintenance Corrective 67
III.3.2 La Maintenance Préventive 68
III.4 Le système de maintenance 70
III.4.1 Les actions de maintenance 70
III.4.2 Les fonctions et les tâches associées
à la maintenance 71
III.4.3 Les niveaux de maintenance 72
III.5 La Gestion de la Maintenance Assistée par Ordinateur
73
III.6 Les nouvelles approches de maintenance 75
III.6.1 La télémaintenance 75
III.6.2 La maintenance productive totale 76
III.6.3 La maintenance basée sur la fiabilité
77
III.7 Conclusion 77
CHAPITRE IV 79
Les algorithmes génétiques 79
IV. Introduction 80
IV.2 Enoncé de l'exemple 80
IV.3 Algorithmes génétiques 80
IV.4 Principe de base d'un AG standard 81
IV.? processus d'un algorithme génétique
84
IV.5.1 Création de la population initiale : 84
IV.5.2 L'évaluation des individus 85
IV.5.3 La création de nouveaux individus 85
IV.5.4 L'insertion des nouveaux individus dans la population
91
IV.? Paramètres d'un AG 91
IV.? Processus d'évolution des
générations : générationnel, stationnaire et
élitiste 92
IV.6.1 AG en îlots (ou avec demes) 93
IV.7 Conclusion 96
CHAPITRE V 97
Conception 97
V.1 Introduction 98
V.2 conception UML 98
V.2.1 Le diagramme de cas utilisation 98
V.2.2 diagramme de classe 100
V.2.3 diagramme de séquence 102
V.3 Stratégie utilisé dans le problème
de l'ordonnancement des activités de production et de
maintenance 103
V.3.? l'ordonnancement séparé
104
V.3.2 l'ordonnancement séquentiel 104
V.3.3 l'ordonnancement intégré
105
V.4 algorithme génétique mis en place dans
l'application 105
V.4.1 codage de solution 108
CHAPITRE VI Réalisation & Expérimentation
109
VI.1 Introduction 110
VI.2 présentation de l'application 110
VI.2.1 première étape page d'accueil
110
VI.2.2 deuxième étape saisie des données
111
VI.2.3 troisième étapes affichage des
résultats et analyse 114
9
VI.3 conclusion 118
Conclusion générale 119
Références Bibliographiques 121
10
11
Listes des Figures
Figure 1 : Caractéristique d'une tache
i
Figure 2 : ordonnancement admissible
Figure 3 : Ordonnancement semi actif
Figure 4 : Ordonnancement actif
Figure 5 : relation d'inclusion entre les
différents types d'ordonnancement
Figure 6 : Diagramme de Gantt
Figure 7 : Diagramme représentant La
Méthode des potentiels métra
Figure 8 : Diagramme qui représente la
Méthode P.E.R.T
Figure 9 : atelier de production de type machine
unique
Figure 10 : atelier de production de type machine
parallèle
Figure 11 : atelier de production de type flow
shop
Figure 12 : atelier de production de type job
shop
Figure 13 : L'organigramme de la raffinerie
d'Arzew
Figure 14 : organigramme du complexe
Figure 15 : organigramme de structure de la
maintenance
Figure 16 : le contenu de la fonction
maintenance.
Figure 17 : évolution de la
maintenance
Figure 18 : Typologie de la maintenance
Figure 19 : état de taux de panne avec ou sans
MP
Figure 20 : fonction et taches de la
maintenance
Figure 21 : Schéma général d'un
algorithme génétique
Figure 22 : Organigramme d'un AG standard Figure 23 :
Schéma d'une roulette
Figure 24 : exemple de croisement mono point.
Figure 25 : croisement multi-point
Figure 26 : Représentation d'une mutation de bits
dans une chaîne
Figure 27 : Représentation d'un AG en
îlots
Figure 28 : Processus d'évolution dans un
modèle d'AG en îlots, générationnel
Figure 29 : diagramme de cas utilisation
Figure 30 : diagramme de classe
Figure 31 : diagramme de séquence
Figure 32 : ordonnancement séquentiel
Figure 33 : ordonnancement
intégré
Figure 34 : Organigramme générale de
l'algorithme génétique implémenté
Figure 35 : représentations d'un
chromosome
Figure 36 : page d'accueil de notre logiciel
Figure 37 : saisie et chargement des données du
plan de production
Figure 38 : fichier texte qui se charge dans la matrice
du plan de production
Figure 39 : saisie et chargement des données du
plan de maintenance
Figure 40 : fichier texte qui se charge dans la matrice
du plan de maintenance
Figure 41 : insertion des taches de maintenance dans le
plan de production
Figure 42 : population initiale de l'algorithme
génétique
Figure 43 : structure d'un chromosome
Figure 44 : plan final des taches de production en
présence de la maintenance
12
Liste des Tableaux
Tableau 1 : tableau indiquant l'ordonnancement des
taches
Tableau 2 : les marges totales de chaque
tache
Tableau 3 : les marges libres de chaque
tache
Tableau 4 : différent services de la
maintenance
Tableau 5 : planifications des mission pour chaque
zones
13
Introduction
générale
14
Introduction générale
Le Domaine de l'informatique est vaste et complexe en
raison, en particulier, des multiples liens qui le lient à tous les
autres domaines qui sont toujours, par rapport a lui, dans une posture
d'écoute et même d'attente. C'est pour cette raison que
l'informatique a cessé d'être l'affaire des informaticiens seuls
et qu'elle est devenue partie intégrante de la culture et du
savoir-faire de « l'honnête homme » contemporain. Le domaine de
l'informatique est aussi un monde en perpétuelle et rapide mutation. Des
découvertes encensées hier sont devenues aujourd'hui
obsolètes ; Que d'avancées perçues, présentement,
comme révolutionnaire sont appelées a céder le pas
à d'autres qui seront encore plus révolutionnaire. Ce mouvement
continuel de dépassement est, bien sûr, propre a toute science
mais, de toutes les sciences, c'est l'informatique qui enregistre les rythmes
de croissances les plus élevés. Dans ce vaste domaine, nous avons
choisi de centrer notre attention sur la question de la planification et de la
maintenance industrielle en raison de l'importance inouïe qu'elle a prise
dans nos sociétés modernes et en particulier dans les
sociétés avancées appelées, à juste titre,
sociétés du savoir. Pour souligner la part que prend la
maintenance dans le fonctionnement d'une entreprise, la profession utilise
communément la dénomination de « fonction maintenance
». Il s'agit même d'une fonction vitale puisque, sans maintenance,
tout processus industriel cesse, généralement à
brève échéance, de produire les biens ou les services pour
lesquels il a été conçu. On peut ainsi ajouter que, si
elle est consommatrice de ressources, la maintenance est avant tout
créatrice de valeur. La maintenance a donc logiquement sa place dans la
conception d'une installation, dans son exploitation, et dans ce qui constitue
l'organisation de l'entreprise. Il faut optimiser. En permanence, car l'optimum
varie et n'est autre qu'un compromis entre différents critères et
contraintes, elles-mêmes évolutives, et de ce fait il reste
empreint d'une certaine subjectivité. Le poursuivre oblige à une
recherche continue d'améliorations : toujours plus d'efficacité
et de performances et toujours moins de dysfonctionnements. Pour cela, les
différentes fonctions de l'entreprise sont sollicitées et la
fonction maintenance tout spécialement. On lui assigne volontiers le
rôle de limiter au mieux les effets de « l'entropie »
(vieillissement, usure, fatigue, et autres altérations
physico-chimiques). Mais cette vision est un peu réductrice ; Plus
centrée sur la recherche des moyens d'éviter des
dégradations (le comment) que sur les raisons de le faire (le pourquoi).
Ainsi, elle semble parfois s'intéresser plus à trouver la
façon d'améliorer la fiabilité des biens, qu'à
identifier ce qu'il faut améliorer. Or maintenir ne veut plus dire
entretenir en bon état, mais atteindre des objectifs. Plus
15
largement, on peut dire qu'avec les autres fonctions,
le rôle de la maintenance consiste, pas exclusivement mais
principalement, à maximiser le profit que l'on peut tirer d'un
investissement. Le recours à des équipements dont la technologie
est de plus en plus complexe oblige l'entreprise à porter une attention
particulière à la fonction maintenance. Autrefois
considérée comme un mal nécessaire, la maintenance n'est
plus seulement curative mais préventive. La maintenance a longtemps
joué un rôle curatif dont l'unique objectif était de
réduire la durée d'immobilisation des machines. Cette maintenance
curative était axée sur le court terme et ne résolvait en
rien les problèmes liés aux dégradations
inévitables. Désormais, la maintenance devient préventive
en contribuant à améliorer la fiabilité des
équipements et la qualité des produits. L'entreprise ne doit pas
uniquement subir les événements, elle doit les prévoir et
analyser leurs effets sur le long terme. Le principal objectif de la
maintenance est d'assurer la pérennité des équipements, de
diminuer les pannes et les imprévus, de réduire les coûts
de révision et de remise en état. Mais la maintenance c'est aussi
programmer le remplacement des machines, veiller à réduire le
coût des matières premières et des personnels d'entretien.
On voit ici la pluralité des domaines concernés par la
maintenance. Cette dernière n'est plus le parent pauvre de l'entreprise
et est devenue une fonction incontournable dans la chaîne de production.
Notre objectif dans ce travail concernant la raffinerie d'Arzew est d'optimiser
la fonction maintenance de cette dernière en appliquant la
méthode des algorithmes génétiques.
16
CHAPITRE I
Problème
d'ordonnancement
17
I.1 Introduction
La théorie de l'ordonnancement est une branche de
la recherche opérationnelle qui s'intéresse
au calcul de dates d'exécution optimales de
tâches [web 1]. Pour cela, il est très souvent nécessaire
d'affecter en même temps les ressources nécessaires à
l'exécution de ces tâches. Un problème d'ordonnancement
peut être considéré comme un sous-problème de
planification dans lequel il s'agit de décider de l'exécution
opérationnelle des tâches planifiées.
I.2 Définition générale de
l'ordonnancement
L'ordonnancement consiste à organiser dans le
temps l'exécution d'un ensemble de tâches au moyen d'un ensemble
de ressources. Ce problème se trouve au coeur de nombreuses
problématiques industrielles. En gestion de projet, ordonnancer, c'est
déterminer les dates d'exécution des activités constituant
le projet.
En informatique, ordonnancer revient à
décider de l'ordre d'exécution des processus et de leur
attribution à des processeurs parallèles. En gestion de
production, l'ordonnancement consiste à déterminer les
séquences d'opérations à réaliser sur les
différentes machines de l'atelier. Chacun de ces contextes pratiques
définit ainsi les caractéristiques propres des tâches et
des ressources, le type des décisions à prendre, les
modalités d'exécution des tâches par les ressources qui
déterminent des contraintes sur les décisions et aussi les
différents critères qui mesurent la qualité d'une
solution. Un contexte particulier définit en fait un problème
d'optimisation combinatoire en termes de variables de décision, de
contraintes et de fonction objectif. Nous appelons ainsi problème
d'ordonnancement un problème d'optimisation combinatoire dont la
solution donne des indications sur les dates de début d'un ensemble de
tâches à ordonnancer ou sur des relations d'ordre total ou partiel
à respecter dans l'exécution de ces tâches afin de
respecter un ensemble de contraintes et/ou d'optimiser une fonction
objectif.
I.3 Eléments fondamentaux
I.3.1 Définition du problème
d'ordonnancement
Le problème de l'ordonnancement est un
problème de séquencement particulier dans lequel, en plus de
choisir et d'ordonner un ensemble d'opérations ou tâches tout en
satisfaisant un ensemble de contraintes, on doit allouer les opérations
aux ressources et leur fixer des dates de début, en d'autre termes le
problème d'ordonnancement englobe les deux problèmes de
séquencement et d'affectation. Du point de vue complexité il a
été démontré que ces deux problèmes
sont
18
fortement combinatoires et ils appartiennent à
la classe des problèmes NP-difficiles. Plusieurs définitions du
problème d'ordonnancement ont été
données.
Eric Pinson [Pinson 88] le définit comme
étant « l'organisation dans le temps de l'exécution d'un
projet » pour Norman Sadeh [Sade, 91], c'est « l'allocation dans le
temps de ressource permettant l'exécution d'un ensemble de tâches
». Pour Gotha [Goth, 93], c'est « programmer l'exécution des
tâches en leur allouant les ressources requises et en fixant leur date de
début».
Ordonnancer c'est programmer l'exécution d'une
réalisation en attribuant des ressources aux tâches et en fixant
leurs dates d'exécution [web 4].
Un ordonnancement fourni l'ordre de traitement des
différents produits au cours du temps. Les problèmes
d'ordonnancement apparaissent dans tout les domaines de l'économie,
l'informatique
(taches=jobs, produit, pièces .et
ressource=processeurs, mémoire, machine, .), la construction (suivi
de projet), l'industrie (problème d'atelier , gestion de production),
l'administration (emploie du temps) les tâches sont le
dénominateur commun des problèmes d'ordonnancement , leur
définition n'est ni toujours immédiate, ni toujours triviale,
enfin il faut programmer les tâches de façon a optimiser un
certain objectif qui sera, suivant le cas la minimisation de la durée
totale (c'est le critère le plus fréquemment employé) ou
le respect de date de commande ou le lissage de courbe de main d'oeuvres ou
encore la minimisation d'un coût, d'une manière
générale, trois types d'objectifs sont essentiels dans la
résolution des problème d'ordonnancement : l'utilisation
efficaces des ressources, un délais d'exécution des tâches
aussi faible que possible, le respect de dates d'achèvement prescrites a
l'avance. Bien entendue il sera souvent plus réaliste, dans la pratique,
de considérer plusieurs critères.
I.3.2 Typologie des problèmes d'ordonnancement
Le premier point de choix, en vue d'établir une
classification des problèmes d'ordonnancement peut se poser au niveau de
la nature des tâches, on distingue ainsi les problèmes
préemptifs [Slow 82], qui se séparent en deux classes selon que
l'interruption des tâches s'effectue avec ou sans mémorisation du
travail partiellement accompli, et les problèmes
non-préemptifs.
Dans le cadre des problèmes non
préemptifs, B.Roy[Roy , 71] propose une classification selon la nature
des inconnues. Une tâche est décrite par trois sortes de
caractéristiques (T, D, W) qui représentent respectivement la
date de début des taches, leur durée, les ressources
utilisées
19
(nature et quantité). Il dégage ainsi
cinq type de problèmes en fonction de la famille de
caractéristiques inconnues : les problèmes de type T, W, (T, D),
(T, W) et (T, D, W), les problèmes de types W où les
caractéristiques concernant les ressources sont inconnues, constituant
les problèmes d'affectation, dans le cas où la durée ne
dépend que de la ressource utilisée, les problèmes de
types (T, D, W) peuvent être rangés dans le type
(T,W).
Les problèmes de type T ou seules les dates de
début des tâches sont inconnues constituent ce que l'on peut
appeler les problèmes d'ordonnancements purs.
Ce type de classification, bien qu'étant assez
général, ne fait pas apparaître tout les problèmes
qu'inspire la liste des contraintes évoquées au paragraphe
précèdent.
Ainsi lors de lotissements, les temps de
préparation peuvent être vu comme des tâches dont leur
durée dépend à la fois des tâches antérieures
et des tâches suivantes, il s'agit là d'une catégorie de
problèmes ne rentrant pas dans le cadre de la classification (T, D,
W).
Au sein des problèmes de type T, on peut
établir une classification plus fine. On distingue :
Le cas où l'on ne prend pas en compte les
ressources, appelé problème central de l'ordonnancement
;
Le cas général où les ressources
sont prises en compte ;
Dans le cas général, deux
classifications parallèles sont alors possibles suivant le type de
ressources utilisées dans le problème. On a d'une part
:
y' les problèmes à ressources renouvelables
; y' les problèmes à ressource consommable ; Et
d'autre part :
y' Les problèmes à ressource disjonctives
ou problème disjonctifs ; y' Les problèmes
à ressources cumulatives ou problème cumulatifs ;
Les problèmes à ressources renouvelables
et disjonctifs sont souvent appelés problème d'atelier. Dans ce
cas particulier on parle indifféremment de tâches ou
d'opérations, de ressources ou de
20
machines. Une opération nécessite une
machine pour sa réalisation. Les opérations relatives à la
fabrication d'un produit doivent généralement être
réalisées en séquence et constituent un travail ou «
«job ».
I.3.3 Les tâches
Une tâche est un travail mobilisant des
ressources et réalisant un progrès significatif dans
l'état d'avancement du projet compte tenu du niveau de détail
retenu dans l'analyse du problème [Gia, 88].
D'une façons plus schématique : une
tâche qu'on note i est une entité
élémentaire de travail localisée dans le temps par une
date de début ti ou de fin
ci, dont la réalisation nécessite une
durée pi telle que :
pi=ci-ti, et qui utilise des ressources k avec une
intensité ai k [ Lop & Esq, 99].
Généralement trois paramètre
caractérisent une tache [T'ki & BVil , 06] :
1. La durée opératoire
pi (processing time) : c'est la durée
d'exécution de la tache.
2. La date de disponibilité
ri (release time) : c'est la date de début au
plus tôt.
3. La date d'échéance di
(due date) : date de fin au plus tard.
ti : Début
d'exécution ci : fin
d'exécution
ri : date de disponibilité
di : date d'échéance
Figure 1 : Caractéristique d'une tache
i
Selon les problèmes, une tâche peut
être exécutée par morceau ou sans interruption. Chaque
tache est constituée d'un ensemble d'opération liée entre
elle par des contraintes technologique [Keb, 08]. Effectivement, en production
manufacturière, on distingue souvent plusieurs phase dans
l'exécution d'une tache : la préparation, la phase principale, la
finition, le transport, etc.
21
I.3.4 Les ressources
Une ressource est un moyen destiné a être
utiliser pour la réalisation d'une tâche, et disponible en
quantités limités [ Lop & Esq , 99].
Dans le contexte industriel, les ressources peuvent
être des machines, des ouvriers, des équipements, des locaux ou
encore de l'énergie, des budgets, etc..
La disponibilité d'une ressource peut varier
dans le temps suivants une fonction ak(t). cette
disponibilité qui s'appelle la capacité ak
de la ressource k , est une caractéristique qui
détermine la quantité de la ressource [Kebe , 08] .
Plusieurs classifications des ressources peuvent
être distinguées : I.3.4.1 Ressource renouvelables et ressource
consommables
Une ressource est dite renouvelable, si après
avoir été utilisée par une ou plusieurs tâches, elle
est à nouveau disponible en même quantité comme : les
hommes, les machines, l'espace, etc.
Par contre, une ressource est consommable, lorsque
elle devient non disponible après avoir été utilisé
; comme la matière première, l'énergie , etc. .. [Kebe ,
08]
I.3.4.2 ressource disjonctives et ressources
cumulatives
Une ressource est dite disjonctive (ou non
partageable), si elle ne peut être affecter qu'à une seule
tâche à la fois. Ce type concerne surtout les ressources
renouvelables.
Par contre une ressource cumulative (partageable) peut
être utilisée par plusieurs tâches simultanément
(équipe d'ouvriers, poste de travail, ..) [ Lop & Esq ,
99].
I.3.5 Les contraintes
Les contraintes expriment des restrictions sur les
valeurs que peuvent prendre conjointement une ou plusieurs variables de
décision [Lop &Esq 99] donc les contraintes représentent les
limites imposées par l'environnement, tandis que l'objectif est le
critère d'optimisation.
22
Plusieurs types de ces contraintes doivent être
respecter .on distingue notamment [Bap , 98] [ Lop & Esq , 99][T'kit &
Bil, 06] :
I.3.5 .1 Les contraintes de localisations temporelles
Sont issu de l'impératif de gestion, et relative
aux dates limites des tâches ou du projet entier. On
a surtout [Keb, 08]:
y' La date de disponibilité (avant laquelle la
tache ne peut pas commencer). y' La date
d'échéance (avant laquelle la tache doit être
achevée)
I.?.?.? Les contraintes d'enchainement
Nous qualifions de contraintes d'enchainement ou de
succession, une contrainte qui lie le début
ou la fin de deux activités par une relation
linéaire [Bapt, 98]. Ce sont des contraintes imposées
généralement par la cohérence technologique (les gammes
opératoires dans le cas d'atelier) qui décrivent des
positionnements relatives devant être respecté entre les
taches.
D'autre contraintes plus spécifiques entre deux
taches ou plus, telles que : la synchronisation, la simultanéité,
le recouvrement ..... Sont également imposées dans certains
systèmes [Lop & Esq ,99].
I.3.5.3 Les contraintes de ressources
Une contrainte de ressource représente le fais que
les activités utilise une certaine quantité de
ressource, tout au long de leur exécution [Bap
,99], ces contraintes sont essentiellement soit
[Lop & Esq ,99] :
y' Des contraintes d'utilisations des ressources qui
expriment la nature, la quantité et les caractéristiques
d'utilisation de ces ressources.
y' Des contraintes de disponibilité des
ressources qui déterminent les quantités des ressources
disponible au cours de temps [Kebe , 08].
On peut distinguer les contraintes suivant qu'elles
sont strictes ou non. Les contraintes strictes sont des obligations à
respecter. Alors que les contraintes dites « relachables »
(appelées aussi préférences) peuvent éventuellement
n'être pas satisfaites [Leto, 01] .
23
I.3.6 les objectifs
Tout ordonnancement est guidé par un ou
plusieurs objectifs qu'il doit chercher leur optimisation.les objectifs qui
doit satisfaire un ordonnancement sont variés. D'une manière
générale on distingue plusieurs classes d'objectifs concernant un
ordonnancement donnée [Lop & Esq 99] ,[Keb , 08]:
Les objectifs liés au temps : on trouve par
exemple, la minimisation du temps totale d'exécution, du temps moyen
d'achèvement, des durées totales de réglage ou des retards
par rapport au date de livraison.
Les objectifs liés aux ressources : par
exemple, maximiser la charge d'une ressource ou
minimiser le nombre de ressources nécessaire pour
réaliser un ensemble de tâches.
Les objectifs liés au cout : c'est objectifs
sont généralement de minimiser les couts de lancement, de
production, de stockage, de transport, etc.
Les objectifs liés a l'énergie ou au
débits .
I.? Méthodes de résolutions de
problème d'ordonnancement :
Historiquement, c'est la Recherche Opérationnel
qui a commencé à élaborer des modèles
d'optimisation programmables. Depuis, d'autre techniques,
développées dans le cadre de la résolution de
problèmes en I.A sont venues s'y joindre. Le choix d'une méthode
de résolution répond toujours à une certaines
problématique que l'on peut tenter de caractériser à
travers quatre questions-clés [ESQU 99] :
? L'existence d'un modèle
d'optimisation.
? L'exactitude des solutions.
? Le mode résolution
(automatique/interactif).
? Le coût de la méthode.
Présenter la totalité des
méthodes et de leurs variantes apparaît difficile au vu du nombre
de travaux existants. Aussi nous présentons uniquement les grandes
orientations de ces méthodes. Les méthodes de résolution
se répartissent en deux catégories principales : les
méthodes exactes et les méthodes approchées ou Les
métas heuristiques.
24
II.4.1 Méthodes exactes
Les termes « méthodes exactes »
recouvrent un ensemble de méthodes d'ordonnancement issues de la
Recherche Opérationnelle. Ces méthodes sont
dénommées exactes du fait qu'elles sont prouvées
théoriquement convergentes vers une solution optimale à un
problème donné. Elles se basent pour cela sur des calculs
mathématiques complexes et coûteux rendant difficiles leur mise en
oeuvre et leur utilisation en dehors de cas très spécifiques en
nécessitant des ressources calculatoires (i.e. machines informatiques)
importantes [GOTH 93]. De par leur recherche d'optimum, ces méthodes
sont confrontées au problème de l'optimum local. Ce risque, bien
que présent également dans les méthodes approchées
(mais avec une importance moindre), est omniprésent dans toutes les
méthodes exactes.
La méthode dite de « Branch
and Bound » est un exemple caractéristique des
méthodes exactes et illustre ce propos. Elle fonctionne selon un
principe de recherche générale de solution dans une perspective
d'optimisation combinatoire [BLAZ1 96].
Remarquons que les méthodes exactes ne
permettent pas de représenter d'une part toutes les contraintes pouvant
exister sur les jobs dans un contexte d'atelier de production, ni d'autre part
de prendre en compte les préférences contextuelles (i.e. fonction
objectif multi variables) du responsable d'atelier.
II.4.2 Méthodes Approchées
Les méthodes d'ordonnancement dites
approchées, s'attachent davantage au moyen d'obtenir une solution
satisfaisante plutôt qu'optimale. La solution recherchée doit
vérifier un certain nombre de caractéristiques avec un coût
calculatoire raisonnable. Une classification en cinq catégories de ces
méthodes a été proposée [GOTH 93] :
? Les méthodes par construction
progressive.
? Les méthodes par voisinage.
? Les méthodes par
décomposition.
? Les méthodes par relaxation des
contraintes.
? Les méthodes liées à
l'intelligence Artificielle.
Nous décrivons plus précisément
dans les paragraphes suivants chacune de ces méthodes.
25
II.4.2.1 Méthodes par construction progressive
Cette catégorie de méthodes procède
à la construction d'une solution globale à partir
d'une
solution partielle complétée au fur et
à mesure de la résolution. A l'aide de règles de
placement, on ajoute à chaque itération un certain nombre de
tâches au plan de charge. La recherche est terminée quand toutes
les tâches ont été traitées. Ce placement peut
être réalisé aléatoirement, tout en respectant les
contraintes du problème, mais est plus généralement
effectué à l'aide de règles relativement simples ( ex :
placer toutes les tâches d'un job avant de passer à un autre
job).
II.4.2.2 Méthodes par voisinage
Ces méthodes consistent à explorer l'espace
des solutions d'ordonnancement en partant d'une
solution initiale complète de laquelle on
extrait une solution voisine. Cette nouvelle solution est alors
évaluée puis, si cette évaluation révèle que
la nouvelle solution est meilleure, elle devient la nouvelle solution de
référence. Le déplacement dans l'espace des solutions
s'effectue à l'aide d'une fonction de voisinage qui, à partir
d'une solution existante, génère une nouvelle solution qui est
alors réalisée par une fonction d'évaluation
f (monocritère ou multicritères). Le
calcul continue jusqu'à ce qu'une solution satisfaisant au(x)
critères(s) de recherche soit obtenue (i.e. l'évaluation par
f dépasse un seuil minimal).
Notons que ces méthodes de résolution
peuvent être assimilées à des méthodes
d'optimisation de solution (puisqu'elles supposent l'existence d'une solution
complète). Dès lors, le risque potentiel, lié à
toute méthode d'optimisation, de se retrouver bloqué dans des
optima locaux ne peut être écarté. Ce risque est
minimisé en intégrant dans la fonction de voisinage une variable
aléatoire. La méthode dite du recuit simulé
et la méthode Tabou sont
basées sur ce principe.
II.4.2.3 Méthodes par décomposition
Les méthodes par décomposition, comme leur
nom l'indique, procèdent à la décomposition du
problème d'ordonnancement afin de faciliter sa
résolution. Cette approche permet de simplifier les calculs en
restreignant à chaque décomposition l'étendue de l'espace
des solutions. Du fait du nombre et surtout de la variété de ces
méthodes nous ne présentons ici qu'une liste brièvement
décrite de ces méthodes :
? Décomposition hiérarchique :
décomposition du problème en niveaux
d'abstraction différents et
décroissants. On restreint de niveau en niveau l'espace des
solutions.
26
.. Décomposition structurelle : le principe
consiste à ne considérer le problème que du point de vue
temporel, en ignorant les contraintes de ressources. Une fois une solution
obtenue, on optimise l'utilisation des moyens, puis on rétablit les
contraintes sur les ressources et on adapte la solution à ces «
nouvelles » contraintes.
.. Décomposition de l'ensemble des solutions du
problème : l'espace des solutions est décomposé en
catégories, chacune étant évaluées
séparément des autres.
.. Décomposition temporelle : spécifique
aux problèmes d'ordonnancement dynamique, elle consiste à
décomposer le problème en intervalles de temps. Les solutions
sont calculées d'abord indépendamment pour être ensuite
adaptées aux contraintes de l'intervalle suivant.
.. Décomposition spatiale : on décompose
le problème d'atelier en regroupant les machines en îlots de
production (en essayant de les rendre les plus indépendants
possibles).
II.4.2.4 Méthodes par relaxation des contraintes
Afin de favoriser l'obtention d'une solution, il est
fait recours dans ces méthodes à une relaxation de certaines
contraintes du problème. La solution de ce dernier aboutira
naturellement à une solution idéale (en ce sens qu'elle ne peut
être atteinte) qui servira de repère lors de la résolution
du problème initial. Ainsi, la solution obtenue sera proche de la
solution idéale, moins optimale mais réalisable.
II.4.2.? Méthodes liées à
l'Intelligence Artificielle
Cette catégorie regroupe des méthodes
dont la principale caractéristique commune se limite à leur
origine I.A. Aussi cette catégorie de méthodes est-elle vaste et
diverse. Il ressort de [GHOT 93] la distinction des sous-classes de
méthodes suivantes :
> Les systèmes à Base de Connaissances
(SBC) dotés de capacité d'apprentissage
> Les règles de priorité
> La propagation des contraintes
> Les algorithmes génétiques
Toutes ces méthodes sont relativement
récentes et en pleine expansion (notamment celles mettant
en oeuvre les algorithmes
génétiques).
27
Dans le chapitre IV on va faire une étude
générale sur les algorithmes génétiques
I.? caractéristiques générales
d'ordonnancement :
Des sous-ensembles d'ordonnancement particuliers sont ici
présentés dont certains présentent des
priorités de dominance vis-à-vis de tout
critère régulier [ESQU 99].
I.5.1 ordonnancement admissible (acceptable) :
Un ordonnancement est dit admissible s'il
respecte toutes les contraintes du problème (dates
limites, précédences, limitation des
ressources,...)
? Exemple : considérons cinq
tâches 1, 2, 3, 4, 5 telles que l'on doive respecter les
contraintes de précédence 1<2<5 et
3<4. Un ordonnancement admissible est représenté à la
Figure 2.
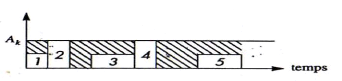
Figure 2 Ordonnancement admissible.
? On parle de glissement à gauche local
lorsqu'on avance le début d'une tâche sans remettre en cause
l'ordre relatif entre les tâches. Sur l'exemple ci-dessus, bien
qu'admissible, la solution pourrait être amélioré du point
de vue du temps total d'exécution, en faisant un glissement local de
certaines tâches vers la gauche (3 et 4 d'une unité, puis 5 de
trois unités).
? On parle de glissement à gauche global
lorsqu'on avance le début d'une tâche en modifiant l'ordre relatif
entre au moins deux tâches. Sur l'exemple précédent, le
repositionnement de la tâche 5 juste au-dessus de la tâche 3 est
admissible mais change la relation 4<5 en 5<4 (Figure 2).
I.5.2 Ordonnancement semi actif
? Dans un ordonnancement semi actif, aucun
glissement à gauche local n'est possible : on ne peut avancer une
tâche sans modifier la séquence sur la ressource. Sur
l'ordonnancement admissible précédent, un glissement à
gauche local permet par exemple d'obtenir l'ordonnancement semi actif de la
Figure 3.
28
On peut montrer que l'ensemble des ordonnancements
semi actifs est dominant pour tout critère régulier.
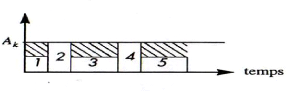
Figure 3 Ordonnancement semi actif.
I.5.3 Ordonnancement actif
Dans un ordonnancement actif, aucun glissement
à gauche local ou global n'est possible. Aucune
tâche ne peut commencer plus tôt sans
reporter le début d'une autre. Comme illustré sur la Figure
4.
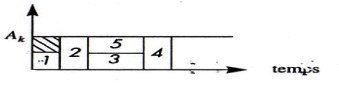
Figure 4 Ordonnancement actif I.5.4 Ordonnancement sans
retards
Un ordonnancement est dit sans retard ou sans
délais, si et seulement si aucune opération n'est mise en attente
alors qu'une machine est disponible pour l'exécuter.
La Figure 5 représente les relations
d'inclusion des classes d'ordonnancement vue précédemment ce
schéma fait apparaître que les ordonnancements sans retards sont
inclus dans le sous ensemble des ordonnancements actifs, qui sont eux
même inclus dans le sous ensemble des ordonnancements semi-actifs. Les
ordonnancements admissibles comprennent tous ceux qui vérifient les
contraintes du problème.
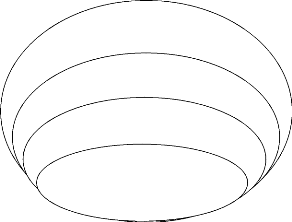
Ordonnancement admissible
Ordonnancement semi-actif
Ordonnancement actif
Ordonnancement sans délais
29
Figure 5 relations d'inclusion entre les
différents types d'ordonnancement
I.6 représentation des solutions
La réalisation d'un projet d'informatique de
gestion nécessite souvent une succession de tâches auxquelles
s'attachent certaines contraintes :
V' De temps : délais à respecter pour
l'exécution des tâches ;
V' D'antériorité : certaines tâches
doivent s'exécuter avant d'autres ;
V' De production : temps d'occupation du matériel
ou des hommes qui l'utilisent. [web 5]. Les techniques d'ordonnancement dans le
cadre de la gestion d'un projet ont pour objectif de répondre au mieux
aux besoins exprimés par un client, au meilleur coût et dans les
meilleurs délais, en tenant compte des différentes
contraintes.
L'ordonnancement se déroule en trois étapes
:
V' La planification : qui vise à
déterminer les différentes opérations à
réaliser, les dates correspondantes, et les moyens matériels et
humains à y affecter [web 5].
V' L'exécution : qui consiste à la mise
en oeuvre des différentes opérations définies dans la
phase de planification [web 5].
30
? Le contrôle : qui consiste à effectuer une
comparaison entre planification et exécution, soit au niveau des
coûts, soit au niveau des dates de réalisation [web
5].
Il existe trois méthodes d'ordonnancement : le
diagramme de Gantt, la méthode MPM(Méthode des potentiels
Métra), le PERT (Program Evaluation Research Technic).
I.6.1 .1 Le Diagramme de Gantt
1. Principe.
Ce type de diagramme a été mis au point
par un américain Henry Gantt.
On représente au sein d'un tableau, en ligne les
différentes tâches et en colonne les unités de temps(
exprimées en mois, semaines, jours, heures...)
La durée d'exécution d'une tâche est
matérialisée par un trait au sein du diagramme [G
BAVIER].
2. Réalisation.
Les différentes étapes de
réalisation d'un diagramme de Gantt son les suivantes :
Première étape : On détermine les
différentes tâches (ou opérations) à réaliser
et leur durée. Deuxième étape : on définit les
relations d'antériorité entre tâches.
Troisième étape : on représente
d'abord les tâches n' ayant aucune antériorité, puis les
tâches dont les tâches antérieures ont déjà
été représentées, et ainsi de suite...
Quatrième étape : on représente par
un trait parallèle en pointillé à la tâche
planifiée la progression réelle du travail [G BAVI].
31
Exemple :
Temps Tâche
|
1
|
2
|
3
|
4
|
5
|
6
|
7
|
8
|
9
|
10
|
11
|
12
|
13
|
A
|
|
|
|
|
|
|
|
|
|
|
|
|
|
|
|
|
B
|
|
|
|
|
|
|
|
|
|
|
|
|
|
|
|
|
|
|
|
|
|
C
|
|
|
|
|
|
|
|
|
|
|
|
|
|
|
|
|
|
|
D
|
|
|
|
|
|
|
|
|
|
|
|
|
|
E
|
|
|
|
|
|
|
|
|
|
|
|
|
|
Figure 6 diagramme de Gantt
+ Remarques :
Chaque colonne représente une unité de
temps.
Les durées d'exécution prévues des
tâches sont représentées par un trait
épais.
(4 unités de temps pour C).
Les contraintes de succession se lisent
immédiatement.
V' Les tâches B et C succèdent à la
tâche A.
V' D succède à B.
Le déroulement d'exécution des tâches
figure en pointillé, au fur et à mesure des
contrôles. On est à la fin de la 6
ème unité de temps, B est en avance d'une
unité
et, C est en retard d'une unité.
On peut alors déterminer le chemin critique : qui
est formé d'une succession de
tâches, sur le chemin le plus long en terme de
durées. Il est appelé chemin critique
car tout retard pris sur l'une des tâches de ce
chemin, entraîne du retard dans
l'achèvement du projet. ( Chemin critique :A, B,
D, E) [G BAVI].
+ Avantage :
V' Permet de déterminer la date de
réalisation d'un projet.
V' Permet d'identifier les marges existantes sur
certaines tâches ( avec une date de
début au plus tôt et une date au plus
tard).
32
y' La date au plus tard de début d'une
tâche, la date à ne pas dépasser sans retarder l'ensemble
du projet.
+ Inconvénient :
y' Ne résoud pas tous les problèmes, en
particulier si l'on doit planifier des fabrications qui viennent en concurrence
pour l'utilisation de certaines ressources. [G BAVI].
I.6.1 .2 La Méthode des potentiels métra
(MPM)
Cette méthode a été
développée par une équipe de chercheurs
français.
1. Principe.
y' Les tâches sont représentées par
des sommets et les contraintes de succession par des arcs.
y' Chaque tâche est renseignée par la date
à laquelle elle peut commencer
(date au plus tôt) et celle à laquelle, elle
doit se terminer (date au plus tard).
y' A chaque arc est associé une valeur
numérique, qui représente soit une durée
d'opération, soit un délai. [G BAVI]
Exemple :
Tâche
|
Durée
|
Tâches antérieures
|
A
|
2
|
|
|
B
|
4
|
|
|
C
|
4
|
A
|
D
|
5
|
A, B
|
E
|
6
|
C,D
|
Tableau 1 tableau indiquant l'ordonnancement des
taches
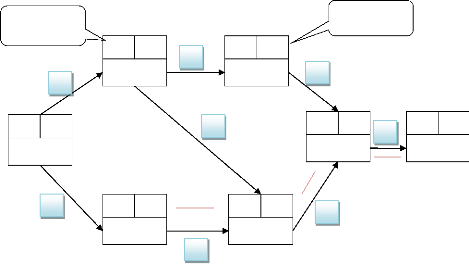
Date au plus tôt
0
DEBUT
0
0
0
0
0
A
B
0
2
2
4
2
2
4
C
D
5
4
9
4
5
E
Date au plus tard
9
6
15
FIN
15
33
Figure 7 : Diagramme représentant La
Méthode des potentiels métra Remarques :
? La date de début au plus tôt d'une
tâche est obtenue en cumulant la durée des tâches qui
précèdent sur la séquence la plus longue.
On initialise le sommet DEBUT avec une date au plus
Tôt = 0.
Date au plus tôt de la tâche j = Max( date
au plus tôt de i + Durée Ti,j) pour tous les
prédécesseurs i de j.
? Les dates au plus tard : dates à laquelle
doivent être exécutées les tâches sans remettre en
cause la durée optimale de fin du projet.
On initialise à l'étape terminale, le
dernier sommet par la date au plus tard = date au plus tôt.
Date au plus tard i = Min (Date au plus tard de j -
durée Ti,j) pour tous les successeurs j de i.
34
y' On peut alors déterminer le chemin critique :
succession de tâches sur le chemin le plus long au sens des
durées. Pour toutes les tâches du chemin critique, les dates au
plus tôt et au plus tard coïncident. Chemin critique : B, D, E. [G
BAVI]
2. La marge totale
La marge totale sur une tâche est le retard que
l'on peut prendre dans la réalisation de cette tâche sans retarder
l'ensemble du projet.
Elle est obtenue , en faisant pour chaque tâche, la
différence entre la date au plus tard de début d'une tâche
et la date au plus tôt.
Marge totale sur A = (2-0)=2.
I.6.1 .3 Méthode P.E.R.T (Program Evaluation and
Research Task)
1. Principe.
Dans un graphe PERT :
y' Chaque tâche est représentée
par un arc, auquel on associe un chiffre entre parenthèses qui
représente la durée de la tâche.
y' Entre les arcs figurent des cercles
appelées « sommets » ou « événement »
qui marquent l'aboutissement d'une ou plusieurs tâches. Ces cercles sont
numérotés afin de suivre l'ordre de succession des divers
évènements. [G BAVI].
2. réalisation
Pour construire un graphe PERT, on utilise la
méthode des niveaux.
y' On détermine les tâches sans
antécédents, qui constituent le niveau 1.
y' On identifie ensuite les tâches dont les
antécédents sont exclusivement du niveau 1. Ces tâches
constituent le niveau 2, et ainsi de suite...[G BAVI]
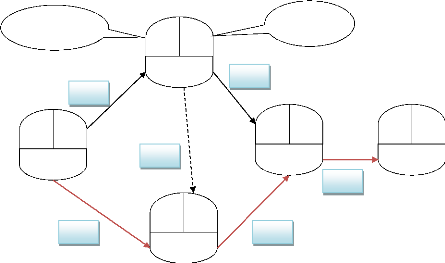
Date au plus tôt
0
1
0
B(4)
A(2)
X(0)
2 4
4 4
2
3
C(4)
D(5)
9 9
4
Date au plus tard
E(6)
15 15
5
35
Figure 8 Diagramme qui représente la
Méthode P.E.R.T Remarques :
V' Il a été nécessaire
d'introduire une tâche fictive de durée égale à 0,
pour représenter la relation d'antériorité entre A et
D.
V' Le cumul des tâches composant la
séquence la plus longue (B, D, E) permet de déterminer la date au
plus tôt de réalisation du projet. Cette succession de
tâches constituent le chemin critique. [G BAVI].
3. Dates et marges en représentation
PERT.
V' Date au plus tôt.
On initialise la date au plus tôt du premier sommet
à 0 :
T 1 = 0 Désigne la date au plus tôt du
sommet 1.
T i = Max (T j + Durée T i,j) pour tous les
prédécesseurs j de i V' Date au plus
tard.
36
On initialise la date au plus tard du dernier sommet avec
sa date au plus tôt.
T* n = T n ( T* n : désigne la date au plus tard
du sommet n)
( T n : désigne la date au plus tôt du
sommet n).
T* i = Min ( T* j - Durée T i,j) pour tous les
successeurs j de i. [G BAVI]
? Marge totale
Marge totale i, j =T* j - T i - Durée T
i,j
T* j : est la date au plus tard du sommet j.
T i : date au plus tôt du sommet i.
T i,j : durée de la tâche entre les sommets
i et j.
Tache
|
A
|
B
|
C
|
D
|
E
|
Marges totales
|
4-0-2=2
|
4-0-4=0
|
9-4-4=1
|
9-4-5=0
|
15-9-6=0
|
Tableau 2 les marges totales de chaque
tache
Remarque : sur le chemin critique, les marges totales des
différentes tâches sont nulles.
Tache
|
A
|
B
|
C
|
D
|
E
|
Marges libres
|
2-0-2=0
|
4-0-4=0
|
9-2-4=3
|
9-4-5=0
|
15-9-6=0
|
Tableau 3 les marges libres de chaque tache
I.7 ordonnancement dans les différents types
d'atelier manufacturier
Une classification très répandue des
ateliers, du point de vue ordonnancement, est basée sur les
différentes configurations des machines. Les modèles les plus
connus sont ceux d'une machine
37
unique, de machines parallèles, d'un atelier
à cheminement unique ou d'un atelier à cheminement multiple [web
3].
? Machines parallèles
? Ateliers à cheminement unique (Flow
Shop)
? Ateliers à cheminements multiples (Job Shop) ?
Autres configurations
I.7.1 machine unique
Dans ce cas, l'ensemble des tâches à
réaliser est fait par une seule machine. Les tâches alors sont
composées d'une seule opération qui nécessite la
même machine. L'une des situations intéressantes où on peut
rencontrer ce genre de configurations est le cas où on est devant un
système de production comprenant une machine goulot qui influence
l'ensemble du processus. L'étude peut alors être restreinte
à l'étude de cette machine [web 3].
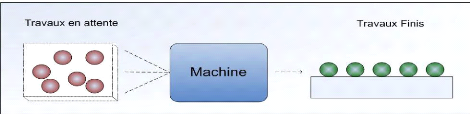
Figure 9 atelier de production de type machine
unique
I.7.2 machine parallèle
Dans ce cas, on dispose d'un ensemble de machines
identiques pour réaliser les travaux. Les travaux se composent d'une
seule opération et un travail exige une seule machine. L'ordonnancement
s'effectue en deux phases : la première phase consiste à affecter
les travaux aux machines et la deuxième phase consiste à
établir la séquence de réalisation sur chaque machine [web
3].
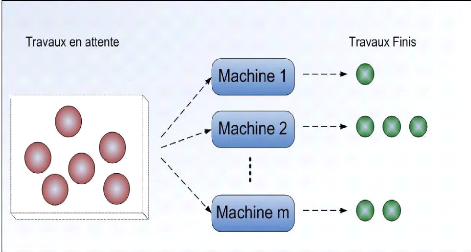
38
Figure 10 atelier de production de type machine
parallèle
I.7.3 flow shop
Un atelier à cheminement unique est un atelier
où le processus d'élaboration de produits est dit «
linéaire », c'est-à-dire lorsque les étapes de
transformation sont identiques pour tous les produits fabriqués. Selon
les types de produits élaborés, on distingue la production
continue et la production discrète. La production continue est
caractérisée par la fluidité de son processus et
l'élimination du stockage. C'est le cas notamment dans les raffineries,
les cimenteries, les papeteries... La production discrète de masse
s'applique principalement aux produits de grande consommation fabriqués
à la chaîne [B &C , 07]
Dans les deux cas, les machines peuvent être
dédiées à une opération précise, et sont
implantées en fonction de leur séquence d'intervention dans la
gamme de production.
L'un des objectifs principaux dans le cas d'atelier
à cheminement unique est de trouver une séquence des tâches
en main qui respecte un ensemble de contraintes et qui minimise le temps total
de production. Parmi les caractéristiques d'un problème de cette
catégorie :
? il existe au minimum n! différentes solutions
où n est le nombre de travaux à réaliser. Notons que n! =
n*(n-1)*(n-2)....K1 ;
39
? le problème est NP-difficile à
l'exception des versions avec deux machines et certains cas particuliers avec
trois machines ;
? une grande productivité mais une faible
flexibilité [web 3].
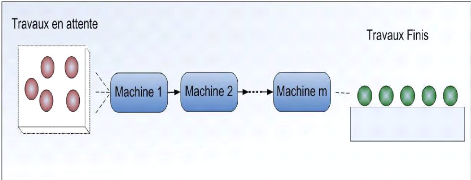
Figure 11 atelier de production de type flow
shop
I.7.4 job shop
Les ateliers à cheminements multiples (ACM)
sont des unités manufacturières traitant une
variété de produits individuels dont la production requiert
divers types de machines dans des séquences variées. L'une des
caractéristiques d'un atelier à cheminement multiple est que la
demande pour un produit particulier est généralement d'un volume
petit ou moyen. Une autre caractéristique est la variabilité dans
les opérations et un mix produit constamment changeant. Ainsi, il est
nécessaire que le système soit de nature flexible. Dans un sens
général, la flexibilité est la capacité d'un
système de répondre aux variations dans l'environnement [web
3].
L'objectif le plus considéré dans le cas
d'un atelier à cheminements multiples est le même que celui
considéré pour un atelier à cheminement unique, à
savoir trouver une séquence de tâches sur les machines qui
minimise le temps total de production [Boul &Cher , 07].
La figure suivante montre un exemple d'un atelier
à cheminements multiples avec quatre travaux et six
machines.
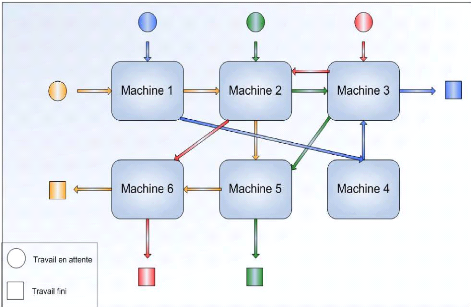
40
Figure 12 atelier de production de type job
shop
Parmi les caractéristiques d'un problème
d'ordonnancement dans un atelier à cheminements multiples [web
3].:
? le nombre de solutions possibles est de l'ordre de
(n!)m, où n est le nombre de tâches à effectuer et m le
nombre de machines. Notons qu'une tâche veut dire la même chose
qu'un travail.
? le problème est NP-difficile et est
considéré parmi les problèmes les plus difficiles à
traiter .
I.7.5 Autre configuration
Les principales catégories, que sont les
ateliers production linéaire (Flow Shop)et les ateliers cheminement
multiple (Job Shop)ne sont pas les seuls modèles dans l 'industrie.
Plusieurs autres Catégories intermédiaires existent, dont les
plus connues sont :
41
les ateliers de type flow shop hybride : il s'agit
d'ateliers flow shop dans lesquels un « étage » Donne de la
fabrication peut être assure par plusieurs machines en parallèle.
Dans ce genre d'ateliers, tout travail passe par chaque étage et l'ordre
de passage sur les étages est le même pour chaque travail. Ce type
d'ateliers est également appelé « atelier cheminement unique
avec machines en exemplaires multiples »;
les ateliers cheminement libre (open shop):chaque
produit traité doit subir un ensemble d'opérations sur un
ensemble de machines, mais dans un ordre totalement libre ;
les ateliers flexibles : ces ateliers sont
caractérisés par un niveau d'automatisation élève,
cherchant par un compromis entre flexibilité et productivité. Ils
sont la base des ateliers cheminements multiples ou les principales taches
(stockage, traitement de pièces, manutention...) sont
automatisées [web 3].
I.8 Conclusion
Dans ce premier chapitre nous avons tout d'abord
présenté le contexte actuel des problèmes
d'ordonnancement, vu que le domaine est en constante évolution dû
au progrès des technologies dans les ateliers de nos jours, et les
besoins d'optimalité dans le domaine industriel ainsi garantir un
minimum de perte et un maximum de bénéfices (financiers dans la
plupart des cas).
Nous avons commencé par des
généralités sur l'ordonnancement ensuite on a
abordé les différents méthodes de résolution de
problèmes d'ordonnancement et nous avons passé a la
représentation de l'ordonnancement ainsi dans les différents
types d'ateliers et dressé l'état de l'art des contributions et
des solutions existantes en détail. En fin on a montré les
inconvénients de certaines solutions en raison de la relation de chaque
problème à son propre cas.
Mais un autre problème se pose qui est celui de
la « maintenance » devenu aujourd'hui une fonction vitale de
l'entreprise que nous détaillerons dans le chapitre suivant.
42
CHAPITRE II
Description générale
de la raffinerie
d'ARZEW, l'unité
3000 et du
département
maintenance
43
II.1 Introduction
La principale conséquence du
développement industriel est la complexité croissante des
machines et des équipements de production. Ainsi, pour satisfaire une
demande de produits avec une meilleure qualité et à des prix
compétitifs tout en respectant les délais de livraison, le
développement des ateliers manufacturiers doit intégrer à
la fois automatisation et flexibilité. D'où l'augmentation du
risque d'occurrence des pannes qui se traduit par un temps croissant de
détection et de réparation des machines. Cela aurait, dans ce
cas, pour effet la diminution de la disponibilité du système
global. Mais comment assurer le fonctionnement des machines, maîtriser
les délais de livraison et améliorer la disponibilité et
la rentabilité des ateliers manufacturiers [Benm,05] ?
Actuellement, la maintenance s'impose comme la
meilleure solution permettant d'accroître les performances et
d'améliorer le niveau de sûreté de fonctionnement, de tout
système industriel. Elle permet d'assurer la pérennité des
équipements et de veiller à ce que le système ne tombe pas
en panne et donc de maintenir le fonctionnement de l'appareil de production au
plus au niveau d'efficacité et garder ainsi le seuil de
productivité à un niveau stable. [Benm,05]
Les entreprises sont de plus en plus
sensibilisées à l'importance des coûts induits par les
défaillances accidentelles des systèmes de production
manufacturiers. La maintenance, jusqu'à très récemment,
était considérée comme un centre de coûts.
Actuellement, les gestionnaires et décideurs, dans l'entreprise, sont de
plus en plus conscients qu'elle peut contribuer d'une manière
significative à la performance globale de l'entreprise. La
complexité des mécanismes de dégradation des
équipements a fait en sorte que la durée de vie de ces derniers a
toujours été traitée comme une variable aléatoire.
Cet état de fait a incité plusieurs entreprises à adopter
des approches plutôt réactives, n'étant pas en mesure de
justifier économiquement les avantages que peut procurer la mise en
place d'une maintenance préventive. [Benm,05]
II.2 description générale du complexe
II.2.1Historique
C'est la société japonaise J.G.C (japon
Gazoline Corporation) qui a pris en charge la construction de la raffinerie
d'ARZEW dans le cadre du premier plan quinquennal 1970-1973 la
réalisation des travaux de la raffinerie a commencé le : 19 juin
1970, pour être achevée deux ans plus tard, en juillet 1972 [Benm,
06] .
Le démarrage des unités d'utilité
a été lancé juste après et ce n'est qu'en mars 1973
que l'ensemble des autres unités de la raffinerie a été
mis en service.
44
L'état décida en 1978 de réaliser
l'extension des installations de production des huiles, le démarrage de
ces unités a été lancé en 1983 [Benm, 06]
.
II.2.2 capacité de production
La raffinerie occupe une surface de 170 hectares, traite
environ 2.5 million de tonnes/an de pétrole brut saharien
acheminé par pipeline de la région de Hassi Messaoud et 295.000
tonnes de brut réduit importé.
Le taux de production diffère selon la demande en
produits :
1. Les carburants
2. Les huiles de base et finis
3. Les bitumes routiers et oxydés
4. Les gaz butane et propane, et les
graisses.
5. La paraffine.
La raffinerie d'Arzew a traité au cours de
l'année 2003, 3.072 millions de tonnes de pétrole brut et environ
188026 tonnes de brut réduit importé.
Sa production en produits finis et semi-finis avoisine
les quantités suivantes ;
Propane
|
30000 T
|
Butane
|
70000 T
|
Essence normale
|
430000 T
|
Essence super
|
220000 T
|
Naphta
|
420000 T
|
Gasoil
|
980000 T
|
Fuel HTS
|
70000 T
|
Fuel BTS
|
550000 T
|
Kérosène
|
150000 T
|
45
Bitumes routiers 120000 T
Bitumes oxydés 20000 T
Lubrifiants 52000 T ( P1 ) 160000 t (P2 : extension
réalisée en 1978).
Graisses 7000 T
Paraffines 7000 T
II.2.3 Description des différentes zones de la
production
Elle comprend plusieurs zones qui sont [Benm, 06]
:
II.2.3.1 Les utilités : Zone 3 et Zone 19.
Elles produisent pour le besoin : l'eau distillée,
l'eau de refroidissement, la vapeur d'eau,
l'électricité, et assure leur
distribution.
II.2.3.2 les carburants : Zone 4 Elle est constituée
de trois unités :
V' Unité 11 : traitant le pétrole
brut par une distillation atmosphérique.
V' Unité 12 : Unité de
traitement du naphta lourd par reforming catalytique.
V' Unité 13 : Unité de
récupération des GPL et de séparation des gaz en butane et
Propane.
II.2.3.3 Huiles de base : Zone 5 et 7 Ces deux zones
disposent de 5 unités :
V' Unité 100 et 21 : Unités de
distillation sous vide pour obtenir des distillats d'huiles.
V' Unité 200 et 22 : Unités de
dés asphaltage au propane du résidu sous vide
V' Unité 300 et 23 : Unités
d'extraction au furfural pour élimination des aromatiques
V' Unité 400 et 24 : Unités
déparaffinage des huiles.
V' Unité 500 et 25 : Unités de
traitement des huiles à l'aide d'hydrogène.
II.2.3.4 les bitumes : Zone 10
Cette zone produit les bitumes routiers et
oxydés
46
II.2.3.5 Mélange et conditionnement : Zone 6 et
unité 3000
Chargées de la fabrication et du conditionnement
des lubrifiants finis (huile, graisses, paraffines)
à partir des huiles de base de zone 5 et 7. [Benm,
06]
II.2.3.6 stockage
Cette zone englobe les différents types de bacs de
stockage suivant la nature des produits stockés
et de leur tension de vapeur. [Benm, 06]
II.2.3.7 Laboratoire de contrôle
Tous les produits des différentes unités
(intermédiaires ou finies) doivent être contrôlés au
niveau
du laboratoire.
Pour les produits finis, un certificat de qualité
doit être établi et signé par le responsable du
laboratoire.
Au niveau du Laboratoire, on procède aussi au
contrôle de la qualité des eaux, et des rejets des unités
vers la mer. [Benm, 06]
II.2.3.8 description détaillée de
l'unité ??00
Elle comporte les unités suivantes ;
? Unité 3100 production des huiles finis ;
a) but ; elle est destinée à fabriquer des
huiles finis à partir des huiles de base fabriquées dans les
unités 100 à 500 et des additifs importés.(Production de
132000 t/an pour une quantité de 10% d'additifs).
b) Grades d'huiles fabriquées ;1) huiles moteurs
81% de la production (essence, diesel, huiles pour transmission). 2) huiles
industrielles[ hydraulique (tiska), turbines (torba), engrenage (fodda),
compresseur (torrada), et huiles divers].
L'unité utilise 2 méthodes de
préparation : 1) mélange en continu (mélangeuse en
ligne).
2) mélange en discontinu (batch).
c) Mélange en continu ; composé de 3
mélangeuses associées à 3 groupes de bacs de stockages des
huiles finis, qui par la suite seront conditionnées en fus, ou
expédiés en vrac. Les 3 mélangeuses fabriquent les 3
catégories d'huiles moteurs avec 3 additifs (livrés en vrac,
ou
47
conditionnés en fus et stockés dans 9
bacs). Une pré dilution des additifs destinés aux
mélangeuses en ligne dans le ballon de pré mélange, en cas
de forte viscosité des additifs, stockage avant utilisation, additifs en
faible proportion pour être dosés directement.
Centrifugeuse ; l'huile finie présentant
parfois des traces d'eau (mauvais pour la commercialisation) doit être
déshydratée dans un ensemble composé de 3 centrifugeuses
disposées à la sortie de la mélangeuse en
ligne.
d) Mélange en discontinu (batch) ;
conçus pour la fabrication des huiles industrielles (2300
t/an).
on utilise pour ce mélange, 12 ballons
divisés en 4 groupes, selon le grade d'huile finie à produire
(évite problème de contamination).le remplissage d'huile est
contrôlé par le 31FQI 101, qui commande la fer/ouv de la vanne
auto, en amont du séparateur et la pompe P3105( la consigne de
prédétermination égale la valeur indiquée). L'ajout
des additifs est comptabilisé par le 31FQI 010. le remplissage des
additifs en fus se fait par le trous d'homme.
e) Events et soupapes de sécurité des bacs
;
? système d'inertage ; utilise des dispositifs
d'inertage à l'air sec relié à l'atmosphère par des
évents, afin de palier les problèmes de dépression
(entée d'air), et de surpression (sortie d'air). Les instruments
utilisés ;1)une vanne 31 PCV D.2) un détendeur 31PCV O
contrôlant la pression dans les bacs (0 à 5 mbar).3)une vanne
à aiguille 31PCV B permet la détente de 52 à 44
mbar.
? trop plein ; ils doivent être remplis de gaz
ou d'huiles, afin d'assurer un joint hydraulique entre l'atmosphère du
bac et l'extérieur.
f) protection des lignes ; les lignes d'huile sont
protégée par des soupapes d'expansion thermique (TSV). Afin
d'éviter les émanations des vapeurs d'huiles et d'additifs. Une
soufflante B3101 assure la ventilation des bâtiments.
? Unité 3200 fabrication des graisses ;
elle utilise 3 étapes.
a) saponification ; un produit gras (glycéride)
en contact avec un alcali, forment un savon. Le linci est utilisé pour
épaissir l'huile (SAE30+Bride stocke), et donne au produit la
consistance de la graisse.
b)
48
déshydratation ;on soutire l'eau du mélange
savon huile sous vide.
c) finissage ; on mélange dans le savon
déshydraté des additifs et du reste d'huile
minérale.
y' Unité 3300 ; elle est conçus
pour le démoulage de la paraffine provenant de l'U600. la paraffine est
introduite dans le skid (par P 2601/2) depuis TK2601/2 à 80°c, puis
pénètre dans la section de réfrigération à
temp° (-15 °c)au propane. Ensuite elle est démoulée en
pain de 5 kg, et conditionnés ensuite dans des cartons de 25
kg
Equipement ; - skid de maintient de temp° à
80°c
- chaîne pour véhiculer la
paraffine
- réfrigération afin de baisser la
temp° de la paraffine à 20 - 25 °c
y' Unité 3400/3500/3600 ; assure le
conditionnement des huiles finis
y' Unité 3700 ; structure implantée
à l'ISP, son rôle consiste :
- Au déchargement des additifs importés des
navires.
- Au suivis des bacs de stockage (contrôle de
temp°, niveau, pression, etc.)
- Au transfert des additifs vers RA1z par camions
citerne.
- Au chargement d'huiles de base dans les
navires.
y' Unité (3900) : réalisée en
1997 elle assure le conditionnement et remplissage des huiles finis en
jerrycans de (2L/5L) et de la graisse dans des pots de 1 Kg Elle comporte
;
a) les utilités ; incluant un ensemble de
transfos d'électricité, 2 compresseurs d'air
(atlas- copco), d'un système de refroidissement, et
de silos de stockage de matière première (PEHD).
b) Les machines ; les machines à soufflage,
à injection, de remplissage, de capsulage, d'étiquetage, de la
mise en ballots, et de palettisation(palettiseuse + filmeuse).ainsi que
l'ensemble des éléments nécessaires à la conversion
d'une ligne de 2 l en 5 l, et les bacs de stockage intermédiaires de
bidons.
Fonctionnement ; le chargement des silos en PEHD
s'effectue à partir de la station de crève sacs ( par un
système de pompes de vide). La matière 1ere est
aspirée vers les machines de soufflage pour la fabrication de bidon
d'huiles et boite de graisse, et vers les machines d'injection pour
la
49
fabrication des bouchons et sous bouchons. Les
carottes et rebuts sont entièrement récupérable
grâce aux broyeurs.
Les bidons passent après le soufflage, par le
système intégré pour le control
d'étanchéité , après être remplis , ils sont
capsulés, étiquetés, mis en ballots, palettisés, et
enfin stockés.
L'ensemble des machines et équipements
étant complètement automatisé, a permis
d'amélioré la qualité de l'emballage (bonne
étanchéité, et un résistance permettant le gerbage
des ballots sur des palettes), et permis aussi d'arriver à un taux de
production jamais égalé par les unités
précédentes.
II.2.4 organisation du personnel de la raffinerie
L'organigramme de la raffinerie est comme suit
:
Direction
Secrétariat
S \direction exploitation
S\direction réhabilitation
Dpt.P1 Dpt.P2
Ser
Comptabilité
|
|
|
Ser
|
Budget et
|
Investissement
|
Ser trésorier
|
Ser
|
Comptabilité
|
Analytique
|
Dpt. F Finance
Dpt. T Technique
Laboratoire
|
Etude
|
Inspection
|
Suivies des d'huiles
|
|
|
Dpt. ADM
|
Dpt. A
|
Dpt. R
|
Administration
|
Approvisionnement
|
Organisation
|
|
|
|
|
|
Gestion adm
|
Ser
|
Informatique
|
des dossiers
|
|
Achat
|
|
Banque de données
|
|
|
OEuvre sociales
|
|
Ser gestion magasin
|
|
|
Organisation procédure
|
|
|
|
|
Documentation
|
|
|
Plan
|
Dpt. H
Gestion de carrière et formation
|
Recrutement Mutation
Formation induction Stagiaire Apprentissage
Dpt. COM
Commercial
Ser vente
Dpt. G
Maintenance
GP planning GE
Electricité
GS Suivi
G C
GI
Instrumentation
Chaudronnerie
50
Figure 13 L'organigramme de la raffinerie d'Arzew II.2.5
Organisation du complexe [Benm, 06]

Directeur
|
|
|
|
|
|
|
Attache direction
|
|
Secrétaire Assistante
|
|
|
|
|
|
Chef Dpt. commercial
|
|
|
Secrétaire principale
|
|
Chef Dpt. Organisation
|
|
|
|
|
Directeur
adj. De réhabilitation
|
|
|
Directeur adj. Exploitation
|
|
|
|
|
|
|
|
|
|
|
|
|
|
|
|
Chef Dpt. Production 1
|
Chef Dpt. Production 2
|
Chef Dpt. Maintenance
|
Chef Dpt. Technique
|
|
|
|
|
|
|
|
|
|
|
|
|
|
|
Chef Dpt.
Approvisionnement
|
Chef Dpt. Sécurité
|
Chef Dpt. Finance
|
Chef Dpt. Ressource humaine
|
|
|
Chef Dpt. SPM
Chef Dpt. administration
Chef Dpt.
Moyens généraux
51
Figure 14 organigramme du complexe
II.3 description de département de maintenance de la
raffinerie
Le but principal poursuivi par l'organisation d'un
département maintenance est de la doter d'une structure susceptible
d'accroître sa contribution à l'efficience générale
du complexe.
Le département maintenance a pour objectif de
servir et de soutenir le département production. Il en résulte
que les problèmes de l'entretien ne peuvent être résolus et
les coûts ne peuvent être réduits en améliorant
seulement l'organisation, les systèmes et les contrôles du
département, car ces derniers ne contrôlent pas entièrement
ses coûts et sa performance.
Les fonctions production, approvisionnement,
sécurité .... Etc., ont une influence directe sur
l'efficacité du département maintenance.
L'organisation de ce département doit donc
permettre une étroite collaboration avec les autres fonctions de
façon à assurer une contribution maximum à la performance
des différentes unités du complexe.
II.3.1 Objectif du département maintenance :
Les objectifs visés en organisation du
département maintenance d'un complexe sont les suivant :
1/ Assurer une étroite supervision du personnel
d'exécution et des travaux exécutés.
2/ Etablir des lignes précises et claires
d'autorité et de responsabilité de l'organisation dans son
ensemble. 3/ Définir la responsabilité et l'autorité
propre à chaque niveau de commandement
4/ doter la supervision directe de l'autorité
maximal, pour l'exécution des travaux de routine, l'autorité
associée à la responsabilité de la qualité, de
l'efficience et de la sécurité du travail
5/ Grouper les activités et les compétences
en ensembles homogènes en vue de fournir le meilleur service à la
production.
6/ fournir la liaison et le conseil à la
production permettant de déterminer un niveau de maintenance
adéquat au moindre coût.
7/ Disposer des éléments Staff
nécessaire à la planification et à la programmation du
personnel, des matériaux et du matériel interne ou
externe.
52
8/ Avoir une structure utilisant au mieux le personnel
d'exécution et de staff disponible.
II.3.2 Organigramme de structure de la maintenance [Benm,
06]
Département maintenance « G
»
|
|
|
|
|
Secrétariat
|
|
|
|
|
|
|
|
Service méthode et
|
|
Service suivi et control
|
|
|
planning
|
|
|
|
« GS »
|
« GP »
|
|
|
|
|
|
|
|
|
|
|
|
|
|
|
|
|
Section
|
Section
|
Section
|
|
|
préparation
|
planning
|
|
statistique
|
|
|
« GPP »
|
« GPL »
|
|
« GPS »
|
|
|
|
Service
|
Service
|
Service
|
Service
|
Service
|
Service
|
mécanique
|
instrumentation
|
|
chaudronnerie
|
Electrique
|
logistique
|
garage
|
« GM »
|
« GI »
|
|
« GC »
|
« GE »
|
« GL »
|
« GG3»
|
53
Figure 15 organigramme de structure de la
maintenance
II.3.3 différents services de la maintenance :
[Benm, 06]
La maintenance symbolisée par « G » est
regroupée de plusieurs services qui sont :
ITEM
|
DESIGNATIONS
|
SYMBOLE
|
1
|
SERVICE PLANNING & METHODES
|
G.P
|
2
|
SERVICE MECANIQUE
|
G.M.T
|
3
|
SERVICE CHAUDRONNERIE
|
G.C
|
4
|
SERVICE INSTRUMENTATION
|
G.I
|
5
|
SERVICE ELECTRICITE
|
G.E
|
6
|
SERVICE LOGISTIQUE
|
G.L
|
7
|
SERVICE SUIVI & CONTROLE
|
G.S
|
8
|
SERVICE GARRAGE
|
G.G
|
Tableau 4 différent services de la
maintenance
? Le service mécanique à une section
usinage symbolisée par : G.M.?
? Le service logistique à une section
maçonnerie, entretien, peinture, menuiserie, vitrier et une section
manutention.
? En plus de ces services, il existe le service
planning & méthodes qui est en quelque sorte l'acteur principal dans
la gestion et l'organisation du système maintenance «G
».
II.3.3.1 Le Service Planning & Méthodes
:(à trois sections qui sont) : [Benm, 06]
1. Section planning : (Dans la programmation des
travaux)
Sa mission générale est
d'affectée d'une façon équilibrée les ressources
disponibles humaines et matérielles pour répondre aux besoins
nécessaires à l'entretien des différents
équipements de la raffinerie.
54
? Il y a un planificateur pour chaque zone de
production.
55
ZONES
|
PLANIFICATEURS
|
MISSIONS
|
Z - 3 / 19
|
1
|
· Le planificateur maintient une liaison sure
et
constante avec les responsables de zone
pour
apporter assistance et conseil nécessaire
à l'entretien des équipements pour assurer la
production.
· Chaque planificateur est
généralement issu de la zone concernée et c'est lui qui
sera l'interlocuteur de
la zone envers les responsables de services de
la maintenance.
|
Z - 4
|
1
|
|
1
|
|
1
|
|
1
|
|
1
|
|
1
|
|
PROCUREMENT
|
· Le planificateur Procurement est issu
du
département approvisionnement pour assurer
la liaison permanente entre celui-ci et la maintenance
|
G.P
|
MAGASIN OUTILLAGE G.P
|
· Responsable de l'outillage & matériels
de G.P
|
|
Tableau5 planifications des mission pour chaque
zones
? Fabrication articles [Benm, 06]
Examine si la fabrication est nécessaire et
évalue l'ampleur du travail sinon, il doit établir une demande
d'achat.
2. Section préparation & Archive [Benm,
06]
· La mission essentielle de cette section est de
déterminer les paramètres nécessaires de chaque travail de
manière à faciliter l'exécution des travaux selon un
planning bien déterminé et étude.
· Chaque corps de métier est
représenté par un préparateur généralement
issu du CRAFT ou il a exercé comme chef d'équipe.
56
? Archive :
La mission essentielle des documentalistes est de
tenir à jour le fichier historique des équipements de la
raffinerie et surtout la conservation des documents et plans des installations.
Chaque équipement dispose d'un fichier historique où sont
reportées toutes les informations nécessaires tel
que.
y' Date d'intervention
y' Nature d'intervention
y' Rapport d'inspection
y' Documents et plans nécessaires
3. Section statistique : (système
information de gestion) [Benm, 06]
? La mission essentielle de cette section est de
collecter, traiter et distribuer l'information relative à la gestion du
département maintenance (en matière d'homme heures, coûts
etc..).Elle assure également la liaison avec le département
finances.
II.3.4 Système de gestion de la maintenance
«Système G » II.3.4.1 Définition [Benm, 06]
Le système « G » est un ensemble de
procédures de travail qui régissent les différents
services de la maintenance en collaboration avec le demandeur et principalement
la production ; ces procédures doivent être appliquées par
les différentes structures.
La raison d'être du département
maintenance est le service qu'il doit fournir aux installations de production
pour qu'elles soient capables de produire dans les meilleures conditions. La
responsabilité du département production est d'exploiter les
différentes unités de production selon les normes en vigueur.
Donc pour préserver cet appareil de production, il faut maintenir tous
les équipements et instruments de contrôle en état
opérationnel.
y' Réduire le temps d'arrêt des
équipements
y' Réduire les coûts
d'intervention
y' Assurer et planifier des entretiens préventifs
et prédictifs.
Pour cela, il faut savoir gérer, organiser et
décider comment et quand intervenir selon les procédures
en
vigueur.
Il est nécessaire de bien distinguer entre les
différents GENRES et les PRIORITES des travaux à
réaliser.
57
II.3.4.2 Code : genre des travaux [Benm, 06]
? La section planning doit attribuer à chaque
demande de travail un CODE GENRE selon les informations suivantes :
y' Genre « 1 » : accidentel : (N° du D.T
Débute à partir de 1000..... )
Ce genre couvre toutes les réparations et tous
les remplacements exécutés suite aux défaillances des
équipements quelque soient les causes.
Ex : Fuite G.M, Bruit pompe, Fuite L.G, Fuite vapeur
etc....
y' Genre « 2 » : préventif/ (N° du
D.T Débute à partir de 2000.....)
Ce genre couvre toutes les interventions
résultant d'un programme d'entretien préventif. Sont
également inclus les travaux relatifs aux inspections imposées
par la loi en vigue. Ex : Equipements réglementaires, Epreuve
décennale, Ballon, Four, Echangeurs
(Pression de service, Pression d'épreuve par les
services des mines, Visite officielle ENACT). y' Genre «
3 » : modification / (N° du D.T Débute à partir de
3000.....)
Ce genre concerne toutes les modifications et tous les
déplacements des équipements ou des installations quelque soient
la valeur investie.
Ex : Prolongement d'une purge.
y' Genre « 4 » : DT Permanente/
Ce genre couvre les demandes de travail permanentes
établies et approuvées par chaque zone (demandeur) et par chaque
CRAFT. Les demandes de travail permanent (D.T.P) concernent les travaux
mineurs, répétitifs routiniers (réglage) exigeant un
travail moins d'une heure. L'exécution de ces travaux peut être
obtenue sur un simple appel téléphonique. Ces travaux sont
définis en commun accord entre les responsables du département
production et le responsable du département maintenance.
Ex : Lubrification, changement goupilles,
éclairage, climatisation, Ph-mètres, conductimètres
etc.... II.3.4.3 Code : priorité des travaux : [Benm, 06]
Le département maintenance ne peut s'acquitter
de sa mission de façon efficace que s'il dispose du temps suffisant pour
la préparation, la programmation et l'exécution des travaux. Pour
cela un code des priorités est employé pour indiquer sur la
demande de travail quand le travail devrait commencer. La
priorité
58
choisie détermine le temps dont disposera le
département maintenance pour préparer et programmer le travail.
Le demandeur doit utiliser le code suivant pour indiquer le degré
d'urgence de ce travail.
w' Priorité « 1 » : (Travail
immédiat)
Cette priorité est attribuée à
toutes les situations, c'est à dire toutes anomalies mettant en danger
la sécurité des installations et des gens (personnels) et peut
causer l'arrêt de l'unité ou une perte important de
produit.
EX : Fuite Garniture mécanique RDC unité
22
· Il faut commencer les travaux
immédiatement après notification du danger constater par un appel
téléphonique au responsable du CRAFT.
· Il faut commencer les travaux sans études
des coûts
· Il faut interrompe d'autres travaux en cours si
nécessaire
· Il faut travailler sans arrêt en faisant
éventuellement des heures supplémentaires jusqu'à fin de
travaux et élimination du danger.
w' Priorité « 2 » : (travail
urgent)
Cette priorité est attribuée à
toutes les situations, c'est à dire toutes anomalies qui pourraient
être préjudiciable aux équipements critiques ou qui
pourraient endommager un équipement d'importance secondaire.
EX : Bruit sur un compresseur (EX : 24-G1 AB) ou
Vibrations importantes sur une pompe.
· Cette priorité dit qu'il faut commencer
les travaux par un jour ouvrable en fonction de la notification de la demande
de travail .
· Il faut interrompe ou retarder d'autres travaux
en priorité 3 si nécessaire (suivant les besoins).
· Il ne faut pas préparer ou préparer
partiellement le travail.
w' Priorité « 3 » : (Travail
impératif ou nécessaire)
Cette priorité est attribuée aux travaux
d'entretien préventif et amélioration des conditions normales de
sécurité.
Elle est également attribuée pour
exécuter les travaux de réparation ou de remplacement dans les
délais raisonnables.
59
? Il existe deux types de priorité 3
? Priorité « 3A » : (travail
impératif)
Cette priorité est attribuée pour
exécuter un travail de réparation ou de remplacement dans les
délais raisonnables.
EX : Réparation d'une pompe de dépotage de
furfural
Cette priorité est attribuée pour
maintenir ou améliorer les conditions normales de
sécurité.
· Les travaux de cette priorité sont soit
à commencer ou à achever à une date qui convient au
demandeur.
· Le demandeur Il doit indiquer sur la demande
de travail la priorité 3A avec la date du début ou la fin des
travaux estimée.
· Le département maintenance doit
disposer d'un temps suffisant pour la préparation et la programmation du
travail à effectuer.
? Priorité « 3B » : (travail
nécessaire)
Cette priorité est attribuée pour
exécuter un travail pour lequel le choix du moment n'est pas essentiel.
EX : Peinture, Réparation voies, aménagement vestiaires ou
bureaux
· Le demandeur doit indiquer sur la demande de
travail la priorité 3B et laisse le choix de la date du début des
travaux à l'appréciation du département
maintenance.
· La préparation de ce travail se fait
d'une manière rigoureuse et la programmation à réaliser
suivant la disponibilité des moyens humaines, matériaux et
matériels.
? Priorité « 4 » : (attente
arrêt) :
Cette priorité indique que le travail ne
pourra se faire que pendant un arrêt programmé de l'unité
ou un arrêt accidentel.
? Priorité « 5 » :
Cette priorité est interne à la
maintenance. Elle indique que le travail ne pourra être exécuter
comme souhaité par le demandeur à cause d'un empêchement
majeur comme :
· Manque matériaux
· Manque matériel (Ex : Grue, Camion
etc....)
· Attente spécialiste
60
La maintenance (le planificateur) informera le demandeur
dès que la demande de travail (D.T) est classée en attente
équipement (priorité 5)
II.3.4.4 Classification des équipements : [Benm,
06]
? Lors de la mise en oeuvre de la G.M.A.O il a
été décider de classifier les équipements en trois
(03) catégories suivantes :
V' Les équipements stratégiques V'
Les équipements importants
V' Les équipements secondaires Définition
[Benm, 06]
? Stratégique : Un équipement est
considéré stratégique lorsque son immobilisation
entraîne l'arrêt de
la production où mettent en danger les
installations.
? Important : Un équipement est
considéré important lorsque son immobilisation remet en cause
le
plan de production en qualité et en
quantité des produits finis.
? Secondaires : Un équipement est
considéré secondaire lorsque son immobilisation ou
indisponibilité
ne présente aucune incidence sur la qualité
des produits ou les installations.
> Symboles :
V' S = Stratégique
V' I = Important
V' C = Secondaire
II.4 Conclusion
La maintenance industrielle joue actuellement un
rôle déterminant dans la conduite de la production. En effet, la
recherche de l'accroissement des performances des ateliers de production, de
plus en plus variés et complexes, conduit à transférer sur
la fonction maintenance la responsabilité de garantir la
disponibilité de ces systèmes. L'objectif de la maintenance
devient alors l'identification réactive de l'élément
défaillant (maintenance corrective) mais aussi la prévision des
pannes afin de réduire la durée moyenne d'indisponibilité
du système (maintenance préventive).
Dans ce chapitre, nous avons présenté
une description générale du personnel de la raffinerie, qui
concerne les systèmes de production manufacturiers et leur maintenance.
Elle constitue une phase de réflexion et d'étude bibliographique.
Dans la première partie, nous avons exposé le contexte
général de la raffinerie et de la gestion de production, La
maintenance étant une fonction complexe, nous avons
présenté dans la
61
seconde partie le département de maintenance.
L'objectif de ce chapitre et de chapitre suivant est la mise en place des deux
concepts de base de cette thèse : la production et la
maintenance.
Les études actuelles tendent à
développer ces deux aspects de manière séparée, du
fait de leurs objectifs antagonistes. En effet, une productivité accrue
implique un système de production qui tourne à plein
régime. Par contre, assurer la sûreté de fonctionnement du
même système impliquerait des arrêts systématiques
pour maintenir les machines, et ainsi pallier à d'éventuels
arrêts. Il serait intéressant de faire converger les objectifs de
productivité et de sûreté de fonctionnement des
gestionnaires. Ce sont ces aspects que nous présenterons dans le
chapitre suivant. De manière plus explicite, nous présenterons la
problématique de La maintenance dans les système de production
liée aux activités de maintenance et de production de
manière séparée, puis nous justifions la
nécessité de mettre en place des relations de coopération,
à ce niveau, par une résolution conjointe du problème de
l'ordonnancement des activités de maintenance et de production, pour
pallier aux conflits production/maintenance.
62
CHAPITRE III
La maintenance dans
les systèmes de
production
63
III.1 Introduction
Les entreprises sont de plus en plus
sensibilisées à l'importance des coûts induits par les
défaillances accidentelles des systèmes de production. Alors que
la maintenance, jusqu'à très récemment, était
considérée comme un centre de coûts, nous sommes de plus en
plus conscients qu'elle peut contribuer d'une manière significative
à la performance globale de l'entreprise. La complexité des
mécanismes de dégradation des équipements a fait en sorte
que la durée de vie de ces derniers a toujours été
traitée comme une variable aléatoire. Cet état de fait a
incité plusieurs entreprises à adopter des approches plutôt
réactives, n'étant pas en mesure de justifier
économiquement les avantages que peut procurer la mise en place d'une
maintenance préventive.
L'absence de données fiables et d'outils
efficaces de traitement de ces données a réduit la fonction
maintenance à des tâches de dépannage, et par le fait
même, à une fonction dont les coûts ne cessent d'augmenter
et dont la contribution à la performance de l'entreprise n'est pas
évidente. Les responsables des services de maintenance dans les
entreprises ne sont pas toujours en mesure de défendre rigoureusement
leur budget d'opération et encore moins leur contribution à
l'efficacité de l'entreprise. En plus de ces lacunes, les petites et
moyennes entreprises manquent souvent de ressources pour mettre en place des
systèmes efficaces de gestion de la maintenance.
Dans ce chapitre, nous rappellerons certains concepts
de maintenance et on identifie la politique utilisée dans un
système de production et en suite on abordera le système de
maintenance et finalement on entame les nouvelles approches de
maintenance.
III.2 La maintenance - Généralités
La Norme AFNOR X 60-010 [web 7] définit la
maintenance comme étant «l'ensemble des
actions permettant de maintenir ou de rétablir un bien dans un
état spécifié ou en mesure d'assurer un service
déterminé ».
RICHET [RICH, 96] définit la maintenance comme
étant « l'ensemble des activités destinées
à maintenir ou rétablir un bien dans un
état ou dans des conditions données de sûreté de
fonctionnement, pour accomplir une fonction requise. Ces
activités sont une combinaison d'activités techniques,
administratives et de management »
64
Maintenir c'est donc effectuer des opérations
(dépannage, graissage, visite, réparation, amélioration,
etc.) qui permettent de conserver le potentiel du matériel pour assurer
la continuité et la qualité de la production. Bien maintenir,
c'est assurer ces opérations au coût global optimum.
Retour & al [RETO , 90] présentent la
fonction maintenance comme un ensemble d'activités regroupées en
deux sous-ensembles : les activités à dominante technique et les
activités à dominante gestion comme le montre la Figure
16.
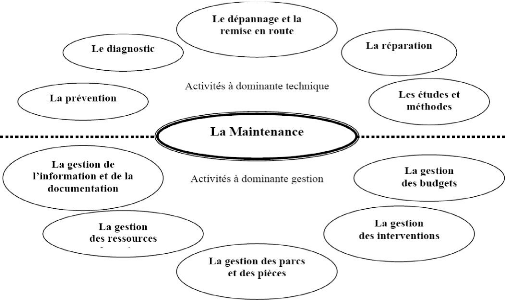
Figure 16 le contenu de la fonction
maintenance.
III.2.1 Evolution de la maintenance
Les premières approches scientifiques de la
gestion de maintenance datent des années cinquante et soixante [MCA , 65
& PIE ,76]. A cette époque, la maintenance a été
préconisée comme un moyen permettant de réduire les
défaillances et les accidents imprévus. Dans plusieurs
entreprises, de très gros programmes de maintenance basés sur le
temps (préventive) ont été développés. Les
premiers modèles de recherche opérationnelle pour la maintenance
sont apparus dans les années soixante pour essayer d'optimiser ces
programmes [VER ,88]. Dans les années soixante-dix, grâce aux
contrôles des ateliers et à la surveillance, l'utilisation de
l'information sur l'état actuel de l'équipement a permis de se
concentrer sur des techniques
pouvant prédire des défaillances. Cela
semblait être plus efficace que les gros programmes de maintenance
préventive. Des études détaillées de la part des
fabricants, des défaillances de leurs produits ont abouti à de
meilleures conceptions, avec moins de défaillances. Dans les
années quatre-vingt, l'ordinateur apporte de l'aide à la fonction
maintenance. Initialement, il a été utilisé pour faciliter
les tâches administratives, ensuite pour la gestion de l'information
disponible et, de nos jours, pour l'aide à la décision [BOU
,88].
Les progrès technologiques des
équipements de production, fruits de la révolution industrielle,
ont orchestré cette évolution de la fonction maintenance qui a
connu trois phases (Figure 17) :
1. Dans la première phase dite d'entretien, la
priorité est accordée à la réalisation (dimension
technique de l'activité). La fonction maintenance était purement
technique.
Elle était réduite aux
dépannages et aux réparations, elle correspondait donc à
ce qu'on appelle actuellement la maintenance corrective.
2. Dans la deuxième phase de maintenance
proprement dite, l'importance est donnée à la dimension
économique. La gestion du travail de maintenance et la gestion des
coûts de maintenance sont le résultat de l'articulation des
dimensions technique et économique, par l'analyse de la valeur
(AV). [Benm ,,05]
3. Dans la troisième dite térotechnique
(de térotechnologie ), où on s'intéresse à la
dimension sociale impliquant les utilisateurs des équipements de
production, qui a conduit à un mode d'organisation intégré
(MOI) des fonctions maintenance et production
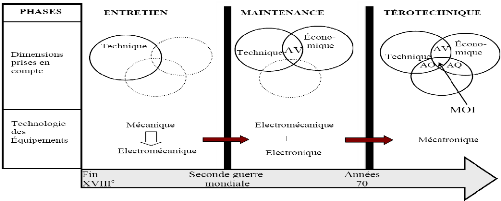
65
Figure 17 évolution de la maintenance
III.3 Les politiques de maintenance
Dans la définition de la maintenance, nous
trouvons deux mots-clés : maintenir et rétablir. Le premier fait
référence à une action préventive, soit avant la
survenue de la panne. Le but de la maintenance préventive est
d'exécuter des tâches (selon un programme établi)
permettant d'anticiper et donc d'éviter une panne. Le deuxième
fait référence à l'aspect correctif. Ce dernier permet de
réagir (par des dépannages ou des réparations) juste
après l'occurrence d'une panne (Figur 18). Il en découle donc
deux principales catégories [BAR60, VAL89]: la Maintenance
Préventive (MP) et la Maintenance Corrective (MC). Nous
présentons dans les paragraphes qui suivent les définitions de
chacune.
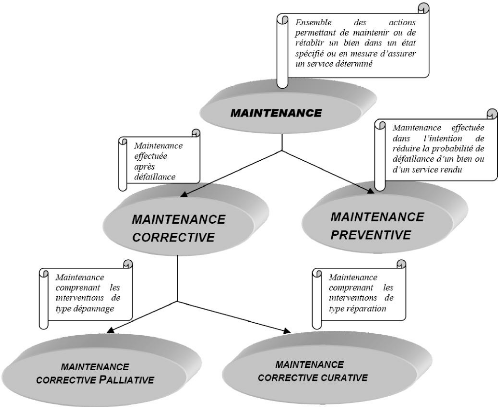
66
Figure 18 Typologie de la maintenance
67
III.3.1 La Maintenance Corrective
La Maintenance Corrective (MC) est
«l'ensemble des activités réalisées
après la défaillance du bien ou la dégradation de
sa fonction pour lui permettre d'accomplir une fonction requise, au moins
provisoirement. Ces activités comportent notamment la
localisation de la défaillance partielle ou complète et son
diagnostic, la remise en état avec ou sans modification, et enfin le
contrôle du bon fonctionnement» [NFX60-010]. Elle
intervient après la panne et devra s'appliquer automatiquement aux
défaillances complètes et soudaines (défaillances
catalectiques). Ce type de maintenance est réservé au
matériel peu coûteux, non stratégique pour la production et
dont la panne aurait peu d'influence sur la sécurité.
Trois politiques de maintenance corrective sont
distinguées (maintenance corrective directe, différée et
globale) et en tout, cinq types sont proposés :
III.3.1.1 Maintenance corrective palliative
Elle regroupe les activités de maintenance
corrective destinées à permettre à un équipement
d'accomplir provisoirement une fonction requise. Appelée couramment
dépannage, cette maintenance palliative est principalement
constituée d'actions à caractère provisoire qui devront
être suivies d'actions curatives.
III.3.1.2 Maintenance corrective curative
Elle regroupe les actions de maintenance corrective ayant
pour objet de rétablir un équipement dans un
état spécifié ou de lui permettre
d'accomplir une fonction requise. Le résultat des activités
réalisées doit présenter un caractère permanent.
Ces activités peuvent être des réparations, des
modifications ou des aménagements ayant pour objet de supprimer la ou
les défaillance(s).
III.3.1.3 Maintenance corrective directe
C'est une opération de maintenance
effectuée juste après la détection (localisation) de la
défaillance,
destinée à remettre la machine dans un
état de fonctionnement normal. Elle peut avoir un caractère
provisoire (palliative) ou définitif (curative).
III.3.1.4 Maintenance corrective différée
C'est une opération de maintenance corrective
(palliative ou curative) qui n'est pas déclenchée
immédiatement après une détection de défaillance
mais est retardée conformément à certaines règles
définies préalablement. Par exemple, attendre que r
équipements parmi m soient défaillants.
III.3.1.5 Maintenance corrective globale
Elle est effectuée lorsque tout le
système (toutes les machines) tombent en panne et sa remise en marche
(provisoirement ou définitivement) ne peut être
réalisée qu'après une intervention de durée
importante.
III.3.2 La Maintenance Préventive
La Maintenance Préventive (MP) est
définie comme une «maintenance ayant pour objet de
réduire la probabilité de défaillance ou de
dégradation d'un bien ou d'un service rendu.»
[NFX60-010].
Elle permet d'éviter les défaillances
des équipements en cours d'exploitation. Elle ne consiste pas à
réparer les pannes mais à les anticiper. Elle est
caractérisée par les actions suivantes :
? L'inspection qui consiste en une activité de
surveillance s'exerçant dans le cadre d'une mission définie et
qui n'est pas obligatoirement limitée à la comparaison avec des
données préétablies. Cette activité peut s'exercer
au moyen de rondes;
? La vérification de conformité avec des
données préétablies, suivie d'un jugement. Elle peut
comporter une activité d'information, inclure une décision
(acceptation, rejet, ajournement) et déboucher sur les actions
correctives;
? La visite (de maintenance) consistant en un examen
détaillé et prédéterminé de tout (visite
générale) ou d'une partie (visite limitée) des
différents éléments de la machine et pouvant impliquer des
opérations de maintenance de premier niveau. Certaines opérations
de maintenance corrective peuvent être effectuées suite à
des anomalies constatées lors de cette visite;
La maintenance préventive s'adresse aux
éléments provoquant une perte de production ou des coûts
d'arrêts imprévisibles jugés importants pour l'entreprise.
L'analyse de ces coûts met en évidence un gain important dû
aux arrêts qu'elle permet d'éviter. La figure 19 présente
la réduction de l'accroissement du taux de panne de l'équipement
par l'application d'une «bonne» maintenance préventive.
Cependant, cet accroissement n'est pas réduit suffisamment par
l'application d'une «mauvaise» maintenance
préventive.
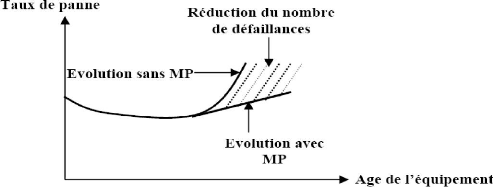
Figure 19 état de taux de panne avec ou sans
MP
68
69
On peut distinguer quatre types de maintenance
préventive : Maintenance Préventive Systématique,
Maintenance Préventive Conditionnelle, Maintenance Prévisionnelle
et Maintenance Proactive. Ces deux dernières représentent les
nouvelles formes de MP.
III.3.2.1 Maintenance préventive
systématique
« La maintenance préventive
systématique comprend l'ensemble des actions destinées
à restaurer, en totalité ou partiellement, la marge de
résistance des matériels non défaillants, lorsque ces
tâches sont décidées en fonction du temps ou de la
production, sans considération de l'état des matériels
à cet instant» [NFX60-010].
Cette méthode nécessite de
connaître : le comportement des équipements, les usures et les
modes de dégradation. Elle intervient à intervalles fixés
sur la base du minimum de vie des composants donnés par
l'expérience ou par le constructeur. C'est pourquoi ce type de
maintenance est aussi appelé maintenance préventive basée
sur la durée de fonctionnement [BOU , 88].
La maintenance préventive systématique se
traduit donc par deux types d'actions :
Des interventions planifiées qui consistent
à nettoyer, réparer ou remplacer certains matériels tels
que des composants ou sous-ensembles d'équipements ;
Des inspections périodiques qui consistent
à contrôler ces mêmes composants et sous-ensembles,
d'effectuer des révisions, mineures ou majeures, d'équipements,
voire d'ateliers entiers lors d'arrêts
généraux.
III.3.2.2 Maintenance préventive conditionnelle
C'est une maintenance préventive
subordonnée à un type d'événements
prédéterminé (autodiagnostic, information donnée
par un capteur, mesure d'une usure, etc.) révélateur de
l'état de dégradation d'un bien [BOU88]. C'est donc une
maintenance qui dépendant de l'expérience et fait intervenir des
informations recueillies en temps réel [BOT , 90]. La pratique de la
maintenance conditionnelle consiste à ne changer l'élément
que lorsque celui-ci présente des signes de vieillissement ou d'usure
mettant en cause, à brève échéance, ses
performances.
III.3.2.3 Les Nouvelles formes de maintenance
préventive
La maintenance préventive conditionnelle a
évolué vers la maintenance prévisionnelle
(prédictive). Celle-ci est définie par la norme NF X 60-010 comme
étant une «maintenance préventive subordonnée
à l'analyse de l'évolution surveillée de paramètres
significatifs de la dégradation d'un bien, permettant de retarder et de
planifier les interventions».
70
D'autre part, un nouveau type de maintenance a vu le
jour aux Etats-Unis, il repose sur une démarche proactive. La
maintenance proactive est une «forme avancée de
maintenance prévisionnelle consistant à déterminer
les causes initiales de défaillances à partir de l'état de
défaillance potentielle ».
III.4 Le système de maintenance
Après avoir présenté quelques
définitions de la maintenance et de ses différents types, nous
situons dans ce qui suit la maintenance par rapport au processus de production.
Ainsi, nous présentons les actions de maintenance, puis les fonctions et
les tâches associées à la maintenance.
III.4.1 Les actions de maintenance
La maintenance est définie comme un ensemble
d'actions techniques et de gestion. Elles sont destinées à
maintenir ou à remettre un équipement en état de
fonctionnement. Seules, elles peuvent maintenir ou rétablir
l'équipement dans des conditions normales d'opération. Il nous a
paru utile de définir quelques actions techniques essentielles qui vont
être décrites ci-après, et que l'on retrouve aussi bien en
maintenance corrective (C) qu'en maintenance préventive (P) [SAS , 98
& ZWI , 96].
V' Le diagnostic (C)
C'est l'identification de la cause probable de la
défaillance, qui se base sur un raisonnement logique fondé sur
les informations issues du système.
V' Le dépannage (C)
Le dépannage est une opération de
maintenance corrective donnant des résultats provisoires, et qui n'a pas
de condition d'applications particulières.
V' La réparation (C)
C'est une intervention définitive et
limitée de maintenance corrective après panne ou
défaillance. L'équipement réparé doit assurer les
performances pour lesquelles il a été conçu. Elle peut
être appliquée sur tous les équipements.
V' Le contrôle (C)
Après avoir exécuté les
opérations de maintenance corrective, il consiste à
vérifier le bon fonctionnement du matériel.
V' L'inspection (P)
Elle consiste à relever périodiquement
des anomalies et exécuter des réglages simples ne
nécessitant pas d'outillage spécifique, ni d'arrêt de
l'outil de production, ou des équipements.
V' La visite (P)
Ces interventions correspondent à une liste
d'opérations définies au préalable qui s'opèrent
selon une périodicité déterminée.
V' Le contrôle (P)
En maintenance préventive, le contrôle
consiste à faire des vérifications de conformité par
rapport à des données fournies à l'avance et suivies d'un
jugement. Le contrôle peut déboucher, comme la visite, sur des
opérations de maintenance corrective.
V' La révision (P)
C'est l'ensemble des actions d'examens, de
contrôle et des interventions effectuées en vue d'assurer le bien
contre toute défaillance majeure ou critique pendant un temps ou pour un
nombre d'usage donné [NFX60-011].
V' Historique (P et C)
Il consiste à structurer en mémoire toutes
les actions réalisées au cours des interventions.
D'autres activités complètent les
opérations de maintenance et participent à l'optimisation des
coûts d'exploitation. Même si ces activités sortent du cadre
direct de la maintenance, certains industriels trouvent des possibilités
d'amélioration par l'intermédiaire de ces formes de maintenance.
Ces activités sont : la rénovation, la modernisation, la
reconstruction et la sécurité.
III.4.2 Les fonctions et les tâches associées
à la maintenance
Nous identifions trois fonctions associées
à la gestion de la maintenance (Figure 20) : la fonction Etudes et
méthodes, la fonction Exécution - mise en et la fonction
documentation.
Les tâches associées à chacune de
ces fonctions, bien que différentes dans leurs descriptions, sont
complémentaires dans leurs finalités [KAF , 01].
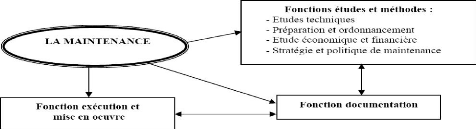
71
Figure 20 fonction et taches de la
maintenance
72
V' Etudes et méthodes
Elle consiste à optimiser toutes les
tâches en fonction des critères retenus dans le cadre de la
formulation de la politique de maintenance. Cette partie regroupe quatre
tâches principales : l'étude technique, la préparation et
l'ordonnancement et l'étude économique et
financière.
V' Exécution et mise en
oeuvre
Pour la fonction exécution - mise en oeuvre,
une expérience considérable sur le matériel des
entreprises modernes et une connaissance approfondie des différentes
technologies sont nécessaires. Les principales tâches pour remplir
cette fonction sont les suivantes :
· installer les machines et le matériel
(réception, contrôle, etc.);
· informer le personnel sur la façon
d'utiliser les équipements et faire la mise à niveau;
· appliquer les consignes d'hygiène, de
sécurité et des conditions de travail ;
· gérer l'ordonnancement et
l'intervention de la maintenance et établir le diagnostic de
défaillance du matériel;
· coordonner les interventions de la maintenance
et remettre en marche le matériel après intervention;
· gérer les ressources matérielles
(les pièces de rechange, l'outillage, etc.).
V' Documentation
Le troisième type de fonction, à savoir la
documentation, est complémentaire aux deux autres.
Ses principales tâches consistent à
:
· établir et mettre à jour
l'inventaire du matériel et des installations ;
· constituer et compléter les dossiers
techniques, historiques et économiques ainsi que le dossier des
fournisseurs;
· constituer et compléter une documentation
générale (technique, scientifique, d'hygiène et de
sécurité).
III.4.3 Les niveaux de maintenance
Une autre condition pour réussir un
système de maintenance est de spécifier les niveaux de
maintenance dans l'entreprise. Monchy [MONC , 96] et Lyonnais [LYON , 92]
présentent cinq niveaux de maintenance. Dans ce qui suit, nous
présentons les tâches associées à chaque
niveau.
73
III.4.3.1 Niveau I
Réglages simples prévus par le constructeur
au moyen d'organes accessibles sans aucun démontage
d'équipement ou d'échange
d'éléments accessibles en toute
sécurité.
III.4.3.2 Niveau II
Dépannage par échange standard
d'éléments prévus à cet effet ou
d'opérations mineures de maintenance préventive.
III.4.3.3 Niveau III
Identification et diagnostic de pannes,
réparation par échange de composants fonctionnels,
réparations mécanique mineures.
III.4.3.4 Niveau IV
Travaux importants de maintenance corrective ou
préventive.
III.4.3.5 Niveau V
Travaux de rénovation, de reconstruction ou de
réparations importantes confiées à un atelier
central.
Ces niveaux de maintenance font
référence à la complexité des tâches à
effectuer et aux ressources humaines et matérielles nécessaires
à la réalisation de chacune des tâches
III.5 La Gestion de la Maintenance Assistée par
Ordinateur
Depuis quelques années, les entreprises sont
confrontées à des variations de marchés très
rapides. La concurrence est très vive. Pour résister, la
qualité des produits fabriqués doit être sans reproche et
au meilleur prix. A cet effet l'organisation de l'entreprise a
été optimisée, les effectifs ont été
réduits, et l'automatisation a gagné la fonction maintenance pour
donner naissance au concept de la Gestion de la Maintenance Assistée par
Ordinateur (G.M.A.O.).
La G.M.A.O. est une étape que les entreprises
franchissent pour progresser vers plus d'efficacité, de
rentabilité et de productivité. Une G.M.A.O. se doit de prendre
en charge, d'une part, l'ensemble des données et des méthodes
liées à une organisation de maintenance, puis d'en tirer les
indicateurs stratégiques nécessaires à la prise des bonnes
décisions.
D'autre part, elle se doit de répondre aux
besoins quotidiens des hommes de la maintenance, c'est à dire permettre
de réaliser des interventions sur des équipements avec le maximum
d'efficacité. Pour cela, la G.M.A.O. va représenter la
mémoire et le savoir faire du service de maintenance.
Traditionnellement, cette mémoire et ce savoir-faire représentent
une base de travail commune entre les techniciens et les ingénieurs, ce
qui engendre de grosses difficultés pendant leurs absences. Bien
sûr, dans beaucoup de cas,
74
un historique papier des interventions est
néanmoins enregistré dans un rapport journalier, mais
l'information est longue à retrouver et le plus souvent ces rapports
manquent de précision. La G.M.A.O., avec l'avantage de l'informatique, a
permis de gérer la masse importante d'informations, de faciliter la
recherche d'informations, de calculer des coûts et des ratios, et de
proposer aux gestionnaires un planning de maintenance.
Une G.M.A.O. est constituée de différents
modules dont les plus important sont [GIR , 00] :
( Le module « Gestion des équipements
» qui permet la codification et la description des équipements,
machines et installations. Ces derniers seront décomposés en
plusieurs niveaux d'ensembles et de sous-ensembles. Un dossier technique par
équipement doit être établi. Ces dossiers techniques
doivent comprendre les plans de l'équipement, l'historique des
réparations ainsi que les procédures et gammes de maintenance de
ce dernier;
( Le module « Demande d'intervention »
permet de saisir et de référencer les demandes d'intervention
provenant des utilisateurs de matériel extérieurs à la
maintenance ou déclenchées par l'occurrence d'un
événement planifié dans un module de maintenance
préventive (date de visite, relevé de compteur, incident
capté par un superviseur).
( Le module « Gestion des travaux » qui a
pour fonction de traiter les demandes d'intervention qui arrivent dans un
portefeuille de travaux à préparer. Il s'agit de réserver
les pièces de rechange, les divers matériels et l'outillage, de
coordonner et de planifier, d'affecter les personnels selon les
compétences requises et d'adapter les plannings aux charges. Ce module
permet l'édition d'Ordres de Travail (OT) ou de Bons de Travaux (BT).
Ces modules ont la possibilité d'accéder à des outils de
gestion de projet pour aider la planification des gros travaux.
( Le module « Gestion de la maintenance
préventive » permet d'établir un planning de maintenance
préventive par ligne de production et par équipement, dont le
déclenchement se fera sur la base d'un mode de déclenchement
particulier.
( Le module « Retour d'expérience »
permet d'alimenter les historiques par la liste des causes et des modes de
défaillances.
( Le module « Gestion des stocks et achats »
permet de gérer les entrées/sorties du magasin. Le module doit
être capable de faire le lien entre un OT, les pièces de rechange
nécessaire et leur disponibilité. Il permet également le
réapprovisionnement et les commandes de matériel ainsi que les
commandes de service (sous-traitance).
( Le module « Contrôle des budgets et des
coûts » permet d'établir des prévisions à
partir des dépenses prévues pour les équipements ainsi que
de connaître les coûts et suivre leur évolution par rapport
au budget prévu.
75
76
En général, les raisons suivantes
reviennent le plus souvent pour justifier la mise en place d'une
G.M.A.O:
? Mettre en place une informatisation de la Gestion de
la Maintenance est structurant car cela impose une organisation minimale
;
? Le potentiel d'informations à gérer
par un service maintenance est considérable et doit être
accessible par de multiples clés d'accès. Or, l'informatique
répond parfaitement à ce double besoin de stockage important et
de gestion d'accès multiples ;
? Non seulement le volume d'informations est
important, mais il est souvent dispersé physiquement dans l'entreprise
et n'est pas toujours accessible au bon moment. Or l'informatique permet de
mettre aisément à disposition toutes les informations
souhaitées (historique, dossiers techniques, disponibilité des
pièces de rechange, etc.) et ce par l'intermédiaire d'un ou
plusieurs postes de travail fixes ou mobiles ;
? Enfin, la masse d'informations est brute : il est
nécessaire d'en dégager quelques indicateurs permettant une prise
de décision sous forme de compromis entre les pôles humain,
économique et technique.
Notre travail est axé sur la résolution
des conflits entre la production et la maintenance. La mise en place d'une
G.M.A.O ne pourrait, en aucun cas, répondre à nos attentes.
Malheureusement, quel que soit le planning proposé et le mode de
déclenchement choisi, le planning de production n'est pas pris en compte
vu qu'il n'y a aucune concertation entre les gestionnaires respectifs des deux
services de production et de maintenance.
III.6 Les nouvelles approches de maintenance
Les nouvelles approches de maintenance ont vu le jour
pour aider la personne intervenante à réaliser le processus
auquel elle est affectée. Ces méthodes, comme la
télémaintenance, la maintenance productive totale ou la
maintenance centrée sur la fiabilité sont
présentées dans ce qui suit.
III.6.1 La télémaintenance
La télémaintenance est une forme
évoluée de maintenance [KOL , 93 & LAU , 96]. Elle est
basée sur le principe suivant : les capteurs, mesurant des grandeurs
intimement liées à l'état de la machine, sont
reliés à une centrale de surveillance qui enregistre toutes les
alarmes et les mesures [MON , 96 & LAV , 96 & LYO , 92]. Des tableaux
synoptiques visualisent la localisation de l'information. Cette technique
permet d'une part, le suivi et l'enregistrement des données sur chaque
machine pour des fins de comparaison et d'autre part, la détection
d'aléas de fonctionnement. L'agent de surveillance qui constate une
évolution d'une dégradation ou l'apparition d'un défaut, a
la responsabilité de mettre hors service, de consigner la partie
lésée de l'installation et d'alerter les agents
d'intervention
[MAL , 93]. Cette technique voit son application dans
les chaînes de production automatisées ou auto-programmables. Avec
l'évolution fulgurante de la technologie lors de la dernière
décennie, la télémaintenance prend une place de plus en
plus grande dans les entreprises manufacturières. Cette technologie
permet de faire le contrôle et le suivi de l'évolution de
l'état des machines de production à l'interne ou à
l'externe.
III.6.2 La maintenance productive totale
Nakajima [NAK, 87 & NAK , 89] définit la
Maintenance Productive Totale (en anglais Total Productive
Maintenance : TPM) comme une approche où tous les
employés participent à la maintenance préventive par des
activités d'équipe. C'est la définition qui est
adoptée d'emblée dans la littérature sur la TPM Il ajoute
que le terme «Total» de TPM a trois significations : le rendement
global des installations, un système global de réalisation et une
participation de tout le personnel. La TPM vise à modifier la
manière de penser des employés vis-à-vis de la maintenance
et à améliorer leur niveau de connaissance.
Elle est définie en cinq points clés
:
1. le fonctionnement optimal des
installations;
2. un système exhaustif de maintenance
préventive, incluant la maintenance autonome et la détection des
micro-dégradations par un programme de propreté;
3. une approche multidisciplinaire (conception +
production + maintenance);
4. l'implication de tous les employés et
à tous les niveaux;
5. la réalisation des activités de
maintenance préventive par petits groupes autonomes.
L'implantation du concept de la TPM doit s'effectuer
progressivement, tel qu'exposé par Nakajima [NAKA , 87]. Il propose une
période de deux à trois ans aux membres de l'usine (incluant
travailleurs et administrateurs) pour adopter cette philosophie. Il conseille
d'essayer ce programme dans le cadre d'un projet-pilote avant de
généraliser l'expérience. L'aspect principal à
considérer, lors de l'implantation de la TPM, est le facteur humain. Peu
de problèmes sont à prévoir du côté
technique. Il est donc crucial de bien planifier et gérer le facteur
humain pour garantir la réussite d'un tel changement. Les
pré-requis à la TPM semblent être plus du côté
culture d'entreprise et du potentiel d'apprentissage des employés, que
du côté technique de la maintenance. Les méthodes
d'implantation proposées sont semblables mais non
génériques.
77
III.6.3 La maintenance basée sur la
fiabilité
La Maintenance Basée sur la Fiabilité
(MBF) (en anglais Reliability Centred Maintenance :
RCM) a vu le jour dans l'industrie aéronautique au cours
des années 60 [WHE , 96]. À la fin des années 50, le
coût des activités de maintenance dans cette industrie
était devenu exorbitant et a justifié une recherche
spéciale sur l'efficacité de ces activités. En
conséquence, un groupe de travail des forces armées
américaines a pris en charge l'étude de nouvelles alternatives de
l'entretien préventif. Ce groupe de travail a développé
une série de directives pour les compagnies aériennes. Le premier
ensemble a été émis en 1967 et a servi de base, entre
autres, au programme d'entretien pour le Boeing 747. D'autres directives ont
donné naissance à la maintenance basée sur la
fiabilité (RCM), définie par Moubray [MOUB , 97], comme un
processus qui détermine les besoins en maintenance du composant dans son
contexte opérationnel. Par la suite, la RCM2 a été
présentée par Moubray [MOUB , 97]. Elle ne présente pas
une variation significative des principes initiaux de la RCM à un niveau
théorique bien qu'il ait découvert quelques petites lacunes dans
la logique (notamment le manque des principes initiaux de la RCM dans la
considération explicite de l'impact potentiel d'une panne sur
l'environnement, et la logique concernant le traitement pertinent des pannes
cachées). La contribution de Moubray se situe dans les points suivants
:
1. les questions de RCM ont été
raffinées pour améliorer la clarté et la
convivialité. Ceci permet d'appliquer plus facilement les principes de
la RCM;
2. le processus intègre une approche de
gestion du changement pour le développement et la mise en place de
nouvelles stratégies d'entretien du matériel;
3. enfin il est bien davantage qu'un ensemble de
principes d'ingénierie; il est conçu pour renforcer et mettre en
valeur les qualifications des hommes de maintenance et des opérateurs.
Le processus contient une partie formation et une partie mise en
place.
III.7 Conclusion
Au cours de ce chapitre, nous avons défini la
maintenance et leurs types. Il est important de connaître les grandeurs
et les mécanismes qui en résultent pour pouvoir implanter un
système de maintenance efficace et rentable. Puis, nous avons
défini le système de gestion de la maintenance avec ses
différents aspects préventifs et correctifs. Nous avons
dressé la typologie de ce dernier et nous l'avons positionné par
rapport au système de production.
78
Dans le prochain chapitre, nous aborderons une
méthode méta heuristique inspiré des méthodes
probabiliste qui est les algorithmes génétiques, en
détaillant la mise en place des AG dans notre
problématique.
79
CHAPITRE IV
Les algorithmes
génétiques
80
IV. Introduction
Dans la littérature, les méthodes
d'optimisation se répartissent généralement en deux
grandes catégories : déterministes et
non-déterministes.
Les méthodes déterministes se basent sur
la valeur de la fonction objective et des contraintes, ainsi que sur la valeur
de leurs dérivées premières et parfois leurs
dérivées secondes. Ce sont des méthodes itératives
convergeant vers un minimum local. La convergence vers un optimum global n'est
pas toujours assurée. Les méthodes déterministes sont
généralement efficaces quand l'évaluation de la fonction
objective est très rapide, ou quand sa forme est connue a priori. Dans
la plupart des problèmes d'optimisation rencontrés par les
ingénieurs, on ne possède pas suffisamment d'information sur la
fonction objectif ni sur ses dérivées.
Les cas d'optimisation complexes impliquant des temps
de calcul importants, de nombreux optima locaux ou des fonctions
non-dérivables, seront souvent traités plus efficacement par des
méthodes non-déterministes. Ces méthodes font appel
à des tirages de nombres aléatoires qui permettent d'explorer
l'espace de recherche plus efficacement. Elles sont faciles à implanter
pour le traitement des problèmes d'optimisation discrète, quand
l'espace de recherche devient non-convexe ou lorsque les gradients sont
discontinus.
IV.? Enoncé de l'exemple
Cet exemple sera illustré dans tout le
processus de l'algorithme génétique.
Je montrerai comment appliquer un algorithme
génétique au problème bien connu de "l'informaticien en
vacances", [web 8] inspiré du problème du voyageur de commerce.
L'informaticien en vacances doit visiter plusieurs villes durant ses vacances :
{ A,B,C,D,E,F,G,H,I,J }. Il cherche donc le chemin le plus court pour passer
par chacune d'elles. Il souhaite également assister à un maximum
de festivals musicaux (ayant lieu dans les villes A,B et C). Il s'agit donc
d'un problème bi-critères (la distance entre les villes à
minimiser et le nombre de festivals auxquels il pourra assisté à
maximiser). Chaque festival a lieu à une date donnée. Nous
connaissons aussi les distances entre toutes les villes.
IV.3 Algorithmes génétiques
Les techniques de recherche et d'optimisation sont en
général classées en trois catégories
[Coel & al. 02] :
énumératives, déterministes et stochastiques. Les AG font
partie de la troisième catégorie et quatre
caractéristiques les distinguent des autres techniques d'optimisation
[Gold, 89, 94] :
81
? ils utilisent un codage des paramètres et non
les paramètres eux-mêmes;
? ils travaillent sur une population d'individus (ou de
solutions);
? ils n'utilisent que les valeurs de la fonction à
optimiser, pas sa dérivée, ou une autre
connaissance auxiliaire;
? ils utilisent des règles de transition
probabilistes et non déterministes.
IV.? Principe de base d'un AG standard
Un AG standard nécessite en premier le codage
de l'ensemble des paramètres du problème d'optimisation en une
chaîne de longueur finie. Le principe d'un AG est simple, il s'agit de
simuler l'évolution d'une population d'individus jusqu'à un
critère d'arrêt. On commence par générer une
population initiale d'individus (solutions) de façon aléatoire.
Puis, à chaque génération, des individus sont
sélectionnés, cette sélection est effectuée
à partir d'une fonction objectif appelée fonction d'adaptation.
Puis, les opérateurs de croisement et de mutation sont appliqués
et une nouvelle population est créée. Ce processus est
itéré jusqu'à un critère d'arrêt. Le
critère le plus couramment utilisé est le nombre maximal de
générations que l'on désire effectuer. La Figure 22
présente le principe de l'AG standard.
L'AG débute par la génération
d'une population initiale et l'évaluation de la fonction d'adaptation de
tous les individus qui composent cette première population. Puis, des
individus sont sélectionnés aléatoirement pour la
reproduction selon le principe de la survie du plus adapté. Ensuite, des
individus « enfants » (ou les descendants) sont
générés en appliquant les deux opérateurs
génétiques suivants : le croisement et la mutation. Ces enfants
sont placés dans une nouvelle population P(t) et vont se substituer, en
tout ou en partie, à la population de la génération
précédente. De nouvelles populations d'individus vont ensuite se
succéder, d'une génération (t) à la
génération (t+1), chaque génération
représentant une itération jusqu'à l'atteinte du
critère d'arrêt. L'AG présenté ci-dessus est dit
générationnel car tous les individus enfants
générés sont placés dans une population et vont
remplacer entièrement la population des individus parents.
On représente le principe fondamental de
fonctionnement d'un algorithme génétique dans la Figure 21 [web
8].
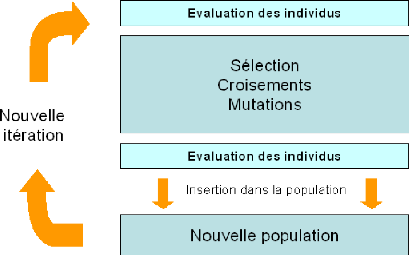
82
Figure 21 Schéma général d'un
algorithme génétique
Début
Population initiale de la génération t=0
Meilleur résultat
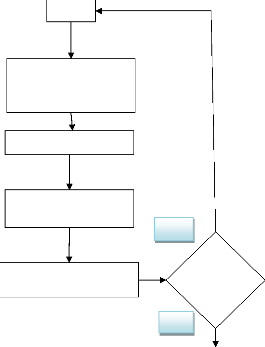
Création de la population
P(t)
Sélection des individus
Operateur de croisement et de mutation
Evaluation de la fonction d'adaptation de
chaque individu
t=t+1
Non
Oui
Critère d'arrêt respect
83
Fin
Figure 22 Organigramme d'un AG standard
84
IV.5 processus d'un algorithme génétique
IV.5.1 Création de la population initiale :
Pour démarrer un algorithme
génétique, il faut lui fournir une population à faire
évoluer. La manière dont le programmeur va créer chacun
des individus de cette population est entièrement libre. Il suffit que
tous les individus créés soient de la forme d'une solution
potentielle, et il n'est nullement besoin de songer à créer des
bons individus. Ils doivent juste fournir une réponse, même
mauvaise, au problème posé.
Par exemple, si vous cherchez un chemin entre 2
points, les individus créés devront simplement posséder le
bon point de départ et le bon point d'arrivée, peu importe par
où ils passent. De même si vous cherchez des solutions pour un jeu
d'échecs, il suffira que les individus créés
possèdent des mouvements autorisés sur des pièces
existantes. Même si les individus créés n'ont aucune chance
d'être des solutions acceptables pour le problème posé, ils
peuvent en avoir la forme. Il n'y a donc aucune objection à les mettre
dans la population initiale.
IV.5.1.1 Construction de la population initiale
Il est tout à fait possible de créer les
individus de manière aléatoire [web 8]. Et cette méthode
amène un concept très utile dans les algorithmes
génétiques : la diversité. Plus les individus de la
population de départ seront différents les uns des autres, plus
nous aurons de chance d'y trouver, non pas la solution parfaite, mais de quoi
fabriquer les meilleures solutions possibles.
Problème de l'informaticien en
vacances
Nous n'allons pas parcourir tous les chemins
possibles, il y en aurait trop. Nous créons une population d'individus
au hasard : par exemple {A,B,C,D,E,F,G,H,I,J}, {D,A,F,J,C,E,G,H,B,I},
{J,A,H,F,D,C,I,G,E,B} ou encore {J,F,A,C,B,E,I,H,G,D}.
Une population intéressante pourrait être
de taille 100, l'essentiel étant que les individus contiennent toutes
les villes une et une seule fois, et qu'ils soient relativement
différents les uns des autres.
IV.5.1.2 La taille de la population à manipuler
La taille de la population initiale est
également laissée à l'appréciation du programmeur.
Il n'est souvent pas nécessaire d'utiliser des populations
démesurées. Une taille de 100 ou 150 individus
85
s'avèrera souvent amplement suffisante, tant
pour la qualité des solutions trouvées que pour le temps
d'exécution de notre algorithme. Evidemment, ce n'est qu'un ordre de
grandeur. Ensuite, libre à vous de modifier la taille de la population
initiale en fonction du problème à résoudre si les
solutions trouvées ne vous conviennent pas
IV.5.2 L'évaluation des individus
Une fois que la population initiale a été
créée, nous allons en sortir les individus les plus
prometteurs, ceux qui vont participer à
l'amélioration de notre population. Nous allons donc attribuer une
'note' ou un indice de qualité à chacun de nos individus. La
méthode d'évaluation des individus est laissée au
programmeur en fonction du problème qu'il a à optimiser ou
à résoudre.
Cette étape intermédiaire
d'évaluation peut même devenir une étape importante du
processus d'amélioration de notre population. En effet, les
différents individus ne sont pas toujours comparables, il n'est pas
toujours possible de dire qu'un individu est meilleur ou moins bon qu'un autre.
C'est le cas des problèmes multicritères, lorsqu'une solution
dépend de plusieurs paramètres. Vous pourrez toujours dire qu'un
nombre est supérieur ou non à un autre, mais vous ne pourrez pas
dire si un vecteur est supérieur ou non à un autre. La notion de
supériorité pour les vecteurs n'existe pas. Vous pouvez comparer
leur norme, mais pas les vecteurs eux-mêmes.
IV.5.3 La création de nouveaux individus
IV.5.3.1 Sélection
La sélection a pour objectif d'identifier les
individus qui doivent se reproduire. Cet opérateur ne
crée pas de nouveaux individus mais identifie
les individus sur la base de leur fonction d'adaptation, les individus les
mieux adaptés sont sélectionnés alors que les moins bien
adaptés sont écartés [Deb, 00]. La sélection doit
favoriser les meilleurs éléments selon le critère à
optimiser (minimiser ou maximiser). Ceci permet de donner aux individus dont la
valeur est plus grande une probabilité plus élevée de
contribuer à la génération suivante.
Il existe plusieurs méthodes de
sélection, les plus connues étant la « roue de la fortune
» et la « sélection par tournoi » :
IV.5.3.1.1 La roulette
La sélection des individus par le système
de la roulette s'inspire des roues de loterie. A chacun
des individus de la population est associé un
secteur d'une roue. L'angle du secteur étant
86
proportionnel à la qualité de l'individu
qu'il représente. Vous tournez la roue et vous obtenez un individu. Les
tirages des individus sont ainsi pondérés par leur
qualité. Et presque logiquement, les meilleurs individus ont plus de
chance d'être croisés et de participer à
l'amélioration de notre population.
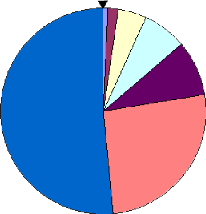
Figure 23 Schéma d'une roulette
IV.5.3.1.2 La sélection par rang
La sélection par rang est une variante du
système de roulette. Il s'agit également
d'implémenter
une roulette, mais cette fois ci les secteurs de la
roue ne sont plus proportionnels à la qualité des individus, mais
à leur rang dans la population triée en fonction de la
qualité des individus.
D'une manière plus parlante, il faut trier la
population en fonction de la qualité des individus puis leur attribuer
à chacun un rang. Les individus de moins bonne qualité obtiennent
un rang faible (à partir de 1). Et ainsi en itérant sur chaque
individu on finit par attribuer le rang N au meilleur individu (où N est
la taille de la population). La suite de la méthode consiste uniquement
en l'implémentation d'une roulette basée sur les rangs des
individus. L'angle de chaque secteur de la roue sera proportionnel au rang de
l'individu qu'il représente.
87
IV.5.3.1.3 La sélection par tournoi
Le principe de la sélection par tournoi augmente
les chances pour les individus de piètre qualité
de participer à l'amélioration de la
population. Le principe est très rapide à implémenter. Un
tournoi consiste en une rencontre entre plusieurs individus pris au hasard dans
la population. Le vainqueur du tournoi est l'individu de meilleure
qualité. Vous pouvez choisir de ne conserver que le vainqueur comme vous
pouvez choisir de conserver les 2 meilleurs individus ou les 3 meilleurs. A
vous de voir, selon que vous souhaitez créer beaucoup de tournois, ou
bien créer des tournois avec beaucoup de participants ou bien mettre en
avant ceux qui gagnent les tournois haut la main. Vous pouvez faire participer
un même individu à plusieurs tournois. Une fois de plus, vous
êtes totalement libre quant à la manière
d'implémenter cette technique de sélection.
IV.5.3.1.4 L'élitisme
Cette méthode de sélection permet de mettre
en avant les meilleurs individus de la population. Ce
sont donc les individus les plus prometteurs qui vont
participer à l'amélioration de notre population. Cette
méthode a l'avantage de permettre une convergence (plus) rapide des
solutions, mais au détriment de la diversité des individus. On
prend en effet le risque d'écarter des individus de piètre
qualité, mais qui auraient pu apporter de quoi créer de
très bonnes solutions dans les générations suivantes.
Cette méthode est extrêmement sensible à la présence
d'optimas locaux, c'est à dire à la présence de solutions
paraissant optimales tant que l'on ne s'en éloigne pas trop - le
véritable optimum pouvant alors être situé dans une toute
autre partie du domaine de recherche.
Une autre possibilité relevant aussi du domaine
de l'élitisme, pour s'assurer que les meilleurs individus feront
effectivement partie de la prochaine génération, est tout
simplement de les sauvegarder pour pouvoir les rajouter à coup sûr
dans la population suivante .
Le nombre d'individus que vous allez
sélectionner en vue d'un croisement ou d'une mutation est encore une
fois laissé à l'appréciation du programmeur. Pensez juste
qu'il n'est pas nécessaire (et pas recommandé non plus) de
modifier tous les individus d'une population.
Les méthodes de sélection permettent de
déterminer quels individus nous allons croiser. Reste maintenant
à définir comment nous allons les croiser.
IV.5.3.2 Croisement
On distingue deux types de croisements : croisement mono
point et multi points
IV.5.3.2.1 croisement mono point
Le croisement mono point permet de créer de
nouvelles chaînes en échangeant de l'information entre deux
chaînes (Figure 24). Le croisement s'effectue en deux étapes.
D'abord les nouveaux éléments produits par la reproduction sont
appariés, ensuite chaque paire de chaînes subit un croisement
comme suit : un entier k représentant une
position sur la chaîne est choisi aléatoirement entre 1 et la
longueur de chaîne moins un . Deux nouvelles chaînes sont
créées en échangeant tous les caractères compris
entre les positions k +1 et inclusivement. L'exemple
suivant (Figure 24) montre deux chaînes (A1 et A2) de longueur 5
appartenant à la population initiale. Les deux nouvelles chaînes
(A3 et A4) appartenant à la nouvelle population sont obtenues par
croisement à la position k = 4 :

88
Figure 24 exemple de croisement mono point.
IV.5.3.2.2 Croisements multi-points
Il faut découper en N morceaux (2 ou 3 peuvent
suffire) chacun des individus choisis, puis il faut prendre un gène de
chaque individu pour créer un nouvel individu.
Notez qu'il est possible de créer ainsi plusieurs
individus : si un gène d'un individu ne pas à la création
d'un individu, il peut servir à la création d'un
autre.
Donc en prenant X individus à croiser, vous
pouvez potentiellement obtenir X nouveaux individus. Mais rien ne vous
empêche d'utiliser plusieurs fois certains gènes, pour obtenir
plus de X nouveaux individus.
Il n'est pas nécessaire et surtout pas
recommandé de croiser tous les individus d'une population, car rien ne
nous dit si le résultat d'un croisement sera meilleur ou moins bon que
les individus parents.
89
Individus parents
|
Gène1
|
Gène2
|
Gène3
|
Gène4
|
Gène1
|
Gène2
|
Gène3
|
Gène4
|
Gène1
|
Gène2
|
Gène3
|
Gène4
|
|
Individus enfants
|
Gène1
|
Gène2
|
Gène3
|
Gène4
|
Gène1
|
Gène2
|
Gène3
|
Gène4
|
Gène1
|
Gène2
|
Gène3
|
Gène4
|
Figure 25 : croisement multi-point
Exemple
Dans notre exemple, nous ne pouvons pas juste prendre
des morceaux des individus parents pour créer les individus enfants. Il
faut que les nouveaux individus créés conservent la forme d'une
solution potentielle.
Ils doivent donc posséder chacune des villes une
seule fois.
La méthode de croisement que je propose pour ce
problème est la suivante : on commence à faire un croisement
"simple" entre deux individus, puis on corrige les individus
créés pour qu'ils aient la forme d'une solution.
Par exemple, si nous souhaitons croiser
{A,B,C,D,E,F,G,H,I,J} avec {D,A,F,J,C,E,G,H,B,I}, nous pouvons décider
que la première moitié du premier parent deviendra la
première moitié du premier enfant, et que la seconde
moitié du premier parent deviendra la seconde moitié du
deuxième enfant , Et inversement pour le second parent.
Nous obtiendrions ainsi les enfants {A,B,C,D,E,E,G,H,B,I}
et {D,A,F,J,C,F,G,H,I,J}.
On s'aperçoit tout de suite du problème
posé, certaines villes sont visitées 2 fois et d'autres ne le
sont pas. Je propose donc de supprimer les doublons et de les remplacer par les
villes non visitées.
Ainsi le premier enfant {A,B,C,D,E,E,G,H,B,I} serait
remplacé par {A,B,C,D,E,F,G,H,J,I} ou par {A,B,C,D,E,J,G,H,F,I} De
même le deuxième enfant passerait de {D,A,F,J,C,F,G,H,I,J}
à {D,A,F,J,C,B,G,H,I,E} ou à {D,A,F,J,C,E,G,H,I,B}
90
IV.5.3.3 Mutation
La mutation est exécutée seulement sur une
seule chaîne. Elle représente la modification
aléatoire
et occasionnelle de faible probabilité de la
valeur d'un caractère de la chaîne, pour un codage binaire cela
revient à changer un 1 en 0 et vice versa (Figure 26). Cet
opérateur introduit de la diversité dans le processus de
recherche des solutions et peut aider l'AG à ne pas stagner dans un
optimum local.

Figure 26 Représentation d'une mutation de bits
dans une chaîne
Une autre solution que le croisement pour créer
de nouveaux individus est de modifier ceux déjà existants. Une
fois de plus, le hasard va nous être d'une grande utilité. Il peut
s'avérer efficace de modifier aléatoirement quelques individus de
notre population en modifiant un gène ou un autre. Rien ne nous dit que
l'individu muté sera meilleur ou moins bon, mais il apportera des
possibilités supplémentaires qui pourraient bien être
utiles pour la création de bonnes solutions. De même que pour les
croisements, il n'est pas recommandé de faire muter tous les individus.
Il est possible de faire muter un individu de la manière qu'il vous
plaira. Une seule contrainte : l'individu muté doit être de la
forme d'une solution potentielle.
Généralement, on ne modifie qu'un
gène pour passer d'une solution à une autre solution de forme
similaire mais qui peut avoir une évaluation totalement
différente.
Problème de l'informaticien en
vacances
La méthode de mutation que je vous propose
consiste en une permutation de deux villes. Nous sommes certains que les
individus mutés auront toujours la forme d'une solution potentielle car
nous ne changeons que l'ordre des villes.
Par exemple, {A,B,C,D,E,F,G,H,I,J} pourra être
muté en {A,B,H,D,E,F,G,C,I,J}
91
IV.5.4 L'insertion des nouveaux individus dans la
population
Une fois que nous avons créé de nouveaux
individus que ce soit par croisement ou par mutation,
il nous faut sélectionner ceux qui vont
continuer à participer à l'amélioration de notre
population. Une fois encore, libre au programmeur de choisir ceux qu'il
souhaite conserver. Il est possible de refaire une étape
d'évaluation des individus nouvellement créés. De
même qu'il est possible de conserver tous les nouveaux individus en plus
de notre population.
Il n'est toutefois pas recommandé de ne
conserver que les nouveaux individus et d'oublier la population de travail. En
effet, rien ne nous dit que les nouveaux individus sont meilleurs que les
individus de départ.
Une méthode relativement efficace consiste
à insérer les nouveaux individus dans la population, à
trier cette population selon l'évaluation de ses membres, et à ne
conserver que les N meilleurs individus.
IV.?.?.? choix de nombre d'individus à
manipuler
Le nombre d'individus N à conserver est
à choisir avec soin. En prenant un N trop faible, la prochaine
itération de l'algorithme se fera avec une population plus petite et
elle deviendra de plus en plus petite au fil des générations,
elle pourrait même disparaître. En prenant un N de plus en plus
grand, nous prenons le risque de voir exploser le temps de traitement puisque
la population de chaque génération sera plus grande.
Une méthode efficace est de toujours garder la
même taille de population d'une génération à
l'autre, ainsi il est possible de dérouler l'algorithme sur un grand
nombre de générations.
IV.5.4.2 la génération suivante
Une fois la nouvelle population obtenue, vous pouvez
recommencer le processus d'amélioration
des individus pour obtenir une nouvelle population et
ainsi de suite ...
IV.? Paramètres d'un AG
Pour appliquer un AG à un problème
réel, on doit posséder les éléments suivants
:
? un codage des éléments appartenant
à la population, le codage des solutions du problème à
résoudre doit être choisi avec soin;
? une fonction d'évaluation ou
d'adéquation ou d'adaptation de l'individu qui mesure la qualité
de l'individu;
? un processus d'évolution des
générations;
92
? des opérateurs pour modifier les individus
d'une population de la génération (t) à la
génération (t+1) comme le croisement et la mutation;
? des paramètres de l'AG : les
opérateurs précédents dépendent de plusieurs
paramètres qui sont fixés à l'avance et dont dépend
fortement la convergence de l'algorithme :
1. taille de la population : c'est-à-dire le
nombre d'individus dans la population. Si la taille est trop petite, l'AG peut
ne pas converger, par contre si elle est trop grande, l'évaluation des
individus peut être très longue;
2. probabilité de croisement et de mutation.
Les valeurs de ces probabilités peuvent varier d'une application
à l'autre. Par exemple, dans l'étude des Algorithme
Génétiques pour l'optimisation de cinq fonctions
mathématiques, [De Jong 75] a suggéré de choisir une
probabilité de croisement élevée, une probabilité
de mutation faible (inversement proportionnelle à la taille de la
population), et une population de taille modérée [Gold, 90] . La
probabilité de mutation est en général très faible,
inférieure à 0,1, une probabilité trop grande, peut
modifier les meilleurs individus;
3. critère d'arrêt : c'est-à-dire
le nombre maximal de générations à effectuer.
IV.? Processus d'évolution des
générations : générationnel, stationnaire et
élitiste
Traditionnellement, les AG sont
générationnels. Les individus de chaque génération
sont testés et une nouvelle population en entier est
générée, le nombre de descendants produits est donc
égal au nombre d'individus parents.
Les deux populations ne se chevauchent pas [Lang, 98].
La nouvelle population d'individus enfants est formée à chaque
génération. Cependant, certains individus enfants peuvent
être une copie conforme des parents qui n'ont pas été
perturbés ni par un croisement ni par une mutation. La stratégie
de remplacement stationnaire (steady-state)
diffère de l'AG générationnel. Dans cette
approche, il y a seulement un ou deux individus qui sont
générés à la fois [Ryan, 00]. Il peut y avoir
différentes façons de sélectionner « l'individu
victime » à supprimer de la population. Par exemple, on peut
sélectionner un individu aléatoirement ou sélectionner
celui qui a la plus petite fonction d'adaptation. Dans ce type d'AG, les
nouveaux individus générés sont ajoutés à la
population et peuvent immédiatement être
sélectionnés comme parents de nouveaux individus [Lang,
98].
93
Approche élitiste (elitist
model) Les opérateurs de croisement et de mutation peuvent
affecter le meilleur individu d'une génération. Le modèle
élitiste a pour avantage d'écarter la possibilité de
perdre cet individu. Ce modèle copie le meilleur individu de chaque
génération dans la population de la génération
suivante. Ce modèle peut accélérer la vitesse de
domination exercée par ce super individu sur la population [Cerrolaza ,
Annicchiarico, 99].
IV.6.1 AG en îlots (ou avec demes)
Au lieu d'utiliser une seule population, on peut
trouver des AG qui utilisent des ensembles de petites sous-populations
(appelées des demes) qui évoluent
séparément. Ce modèle est appelé modèle en
îlots. Grâce à cette isolation, chaque îlot peut
évoluer avec ses propres paramètres, dans des directions
différentes, c'est-à-dire vers des solutions différentes.
Dans ce type d'AG, on peut faire migrer un certain nombre d'individus d'une
sous-population ( j ) à une sous population
voisine ( j +1). L'îlot qui évolue vers
un optimum local ou qui a convergé prématurément peut
être aidé par l'arrivée d'un ou de plusieurs individus
migrants.
La Figure 27 présente un exemple d'une
population avec cinq demes, dans laquelle deux
individus sont choisis aléatoirement pour migrer du deme (
j ) au deme ( j +1). Les
individus sélectionnés pour la migration peuvent rester dans leur
îlot et seulement une copie est envoyée dans l'îlot voisin,
ou bien ces individus sont envoyés directement dans l'îlot
voisin.
D'après Ryan (1995), la sélection des
individus migrants peut se faire de deux façons. La première est
aléatoire, l'avantage de cette méthode est la plus grande
variété des individus qui peut en résulter. La seconde
méthode consiste à sélectionner les individus en fonction
de leurs fonctions d'adaptation et choisir les plus performants de chaque
îlot pour les copier dans les autres îlots, ce qui peut engendrer
une évolution plus directe que la première
méthode.
[ Cantù-Paz ,00] a testé plusieurs
autres configurations, par exemple : les meilleurs migrants remplacent les
moins bons, les migrants sélectionnés aléatoirement
remplacent les moins bons, les meilleurs migrants remplacent des migrants
sélectionnés aléatoirement. Le choix des individus
migrants d'un deme à l'autre et des individus remplacés dans
chaque deme peut influencer la pression de sélection. Les configurations
qui sélectionnent les individus migrants ou remplacés en fonction
de leur fonction d'adaptation ont tendance à accélérer la
convergence.
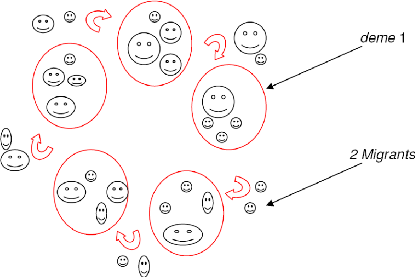
94
Figure 27 Représentation d'un AG en
îlots
L'avantage du modèle en îlots est que la
recherche de la meilleure solution se fait en parallèle, dans
différents espaces de recherche, ce qui permet d'avoir plusieurs
solutions qui peuvent être très utiles surtout dans le cas des
fonctions multimodales. Le second avantage est que, lorsque l'on envoie des
individus d'un îlot à l'autre, on peut éviter une
convergence prématurée de l'AG dans chaque îlot et le fait
de copier des individus d'un îlot à l'autre plutôt que de
les envoyer à l'îlot voisin ne cause aucune perte dans la
qualité des individus, même lorsque ces individus devront
s'apparier avec d'autres individus moins bons.
L'AG en îlots nécessite de
préciser, en plus des paramètres de l'AG standard cités
précédemment , les paramètres suivants : la taille des
sous-populations (ou nombre de demes), la fréquence de migration des
individus (exprimée en nombre de générations) et le nombre
d'individus qui migrent à chaque fois (peut être exprimé en
% de la taille du deme).
L'algorithme pour le modèle en îlots est
schématisé à la Figure 28. Dans chaque deme
(sous-population), un AG est exécuté séquentiellement. Les
demes peuvent s'échanger de l'information de temps à autre en
permettant à certains individus de migrer d'une sous-population à
l'autre selon certaines topologies.
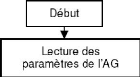
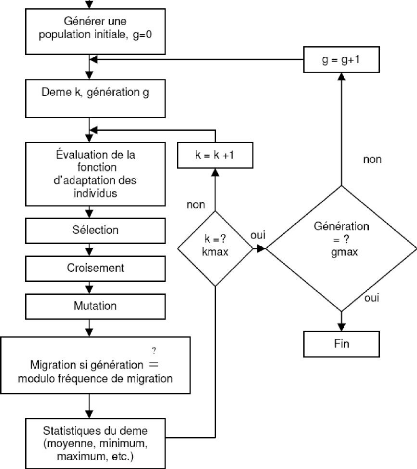
95
Figure 28 Processus d'évolution dans un
modèle d'AG en îlots, générationnel
96
IV.7 Conclusion
Un algorithme génétique vous donne une
grande liberté dans le paramétrage et dans
l'implémentation des différents
traitements. Libre à vous ensuite de modifier tel ou tel
paramètre si les solutions obtenues ne vous conviennent pas.
Les algorithmes génétiques ont
l'énorme avantage de pouvoir être appliqués dans un grand
nombre de domaines de recherche de solution, lorsqu'il n'est pas
nécessaire d'avoir la solution optimale, qui prendrait par exemple trop
de temps et de ressources pour être calculée (ou tout simplement
si personne n'est capable de la trouver de manière
théorique).
Les algorithmes génétiques sont aussi
particulièrement adaptés à l'évaluation de
problèmes multicritères et à la réalisation de
recherches de valeurs optimales selon plusieurs objectifs
simultanés.
97
CHAPITRE V
Conception
98
V.1 Introduction
Ce chapitre est consacré à la conception
d'un système de planification de la maintenance dans une raffinerie
pétrolière, et pour cela nous avons choisis le formalisme de
modélisation UML afin de schématiser tous les scénarios
inclus dans notre application. pour ce faire on va proposer trois diagrammes
UML qui sont le diagramme de cas utilisation, diagramme de classe, et le
diagramme de séquence et dans chacun des diagrammes citées
auparavant on identifie les détaille en raison d'utilisation de certain
classes d'où la dynamique de l'application.
V.2 conception UML
V.2.1 Le diagramme de cas utilisation V.2.1.1
définition
Les use cases permettent de structurer les besoins des
utilisateurs et les objectifs correspondants d'un système. Ils centrent
l'expression des exigences du système sur ses utilisateurs : ils partent
du principe que les objectifs du système sont tous motivés.
[web9] La détermination et la compréhension des besoins sont
souvent difficiles car les intervenants sont noyés sous de trop grandes
quantités d'informations : il faut clarifier et organiser les besoins
des clients (les modéliser). Pour cela, les cas d'utilisation
identifient les utilisateurs du système (acteurs) et leurs interactions
avec le système. Ils permettent de classer les acteurs et structurer les
objectifs du système. Une fois identifiés et structurés,
ces besoins :
? définissent le contour du système
à modéliser (ils précisent le but à
atteindre),
? permettent d'identifier les fonctionnalités
principales (critiques) du système.
Les use cases ne doivent donc en aucun cas décrire
des solutions d'implémentation.
V.2.1.2 Conception
Le but de notre application est de créer un
système d'aide a la décision ainsi de placer les taches de
maintenance dan un atelier de production et pour cela nous avons trois cas
d'utilisations peuvent être distingués dans notre système
:
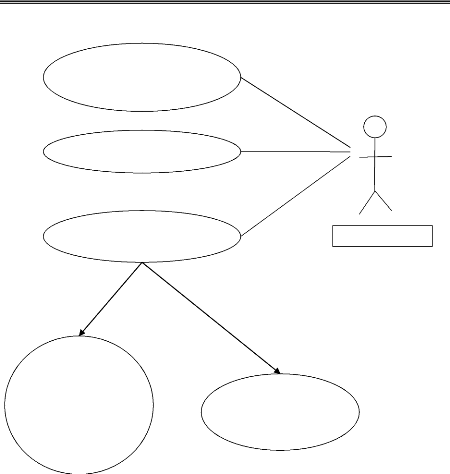
Utilisateur
Analyser les résultats
générés par le système
Saisir les données
Et chargement des
Exécuter le programme
Effectué l'Analyse du plan initiale
de production en présence de la maintenance et du
Diagnostic entre la fonction objective initiale
et finale
99
Figure 29 diagramme de cas utilisation
100
V.2.2 diagramme de classe V.2.2.1 définition
Le diagramme de classes exprime la structure statique du
système en termes de classes et de
relations entre ces classes.
L'intérêt du diagramme de classe est de
modéliser les entités du système
d'information.
Le diagramme de classe permet de représenter
l'ensemble des informations finalisées qui sont
gérées par le domaine. Ces informations
sont structurées, c'est-à-dire qu'elles ont
regroupées
dans des classes. Le diagramme met en évidence
d'éventuelles relations entre ces classes.
Le diagramme de classes comporte 6 concepts :
y' classe
y' attribut
y' identifiant
y' relation
y' opération
y' généralisation /
spécialisation
V.2.2.2 conception
La conception de notre système par le formalisme
de classe est donnée ainsi :
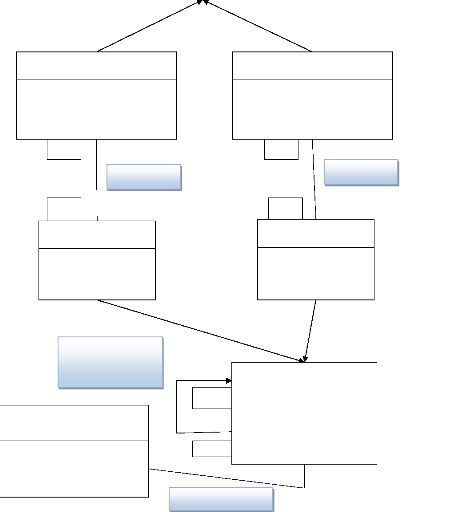
Plan de maintenance conjoint production
optimisé
Code tache Date début Date fin
Code de tache production
Propriété
Date de début
Date de fin
Code
Date de début Date de fin
1..*
1..*
Tache de production
Plan de production
Permuter et calculer les nouvelles dates de débuts
et de fin
Contient 2
Néme permutation
101
1..*
1..*
Plan contenant la
Maintenance et la production
Code de tache de production Code de tache de maintenance
Date de début
Date de fin
Code de tache maintenance
Propriété
Date de début
Date de fin
Tache de maintenance
Code
Date de début Date de fin
Plan de maintenance
1..*
1..*
Figure 30 Diagramme de classe
Contient 1
Plan de production en présence de la
maintenance
Code tache production Code tache maintenance
Propriété
Ressource tank Ressource pompe
Priorité
|
102
V.2.2.1 Clarification de diagramme de classe
Dans le diagramme ci-dessus on a utilisé sept
classes, la première désigne un plan de production en
présence de la maintenance dont nous avons une
généralisation de deux classes nommées respectivement plan
de production et plan de maintenance et cela porte que ses deux classe
appartiennent a la classe père nommée plan de production en
présence de la maintenance et en fusionnant les classes nommées
tache de production et tache de maintenance on aura un plan de production et a
travers d'un nombres de permutation on résulte un plan
optimisé
V.2.3 diagramme de séquence V.2.3.1
Définition
Les diagrammes de séquence possèdent une
dimension temporelle mais ne représente pas explicitement les liens
entre les objets.
Ils privilégient ainsi la représentation
temporelle à la représentation spatiale et sont plus aptes
à modéliser les aspects dynamiques du système.
En revanche, ils ne rendent pas compte du contexte des
objets de manière explicite, comme les diagrammes de
collaboration.
Le diagramme de séquence permet de visualiser
les messages par une lecture de haut en bas. L'axe vertical représente
le temps, l'axe horizontal les objets qui collaborent. Une ligne verticale en
pointillé est attachée à chaque objet et représente
sa durée de vie.
Les messages sont représentés comme dans le
diagramme de collaboration.
103
V.2.3.2 conception
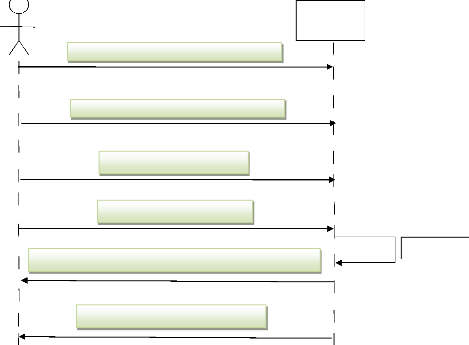
Programme
Entrer le nombre de tache de production
Entrer le nombre de tache de maintenance
Entrer le plan de production
Entrer le plan de maintenance
Traitement
Fournir un plan de production en présence de
maintenance
Minimisation de la fonction objective
Figure 31 diagramme de séquence
V.2.3.3 détail du diagramme
En entrée du programme nous avons le nombre de
tache de maintenance, le nombre de tache de production, le plan de production
ainsi le plan de maintenance et après traitement du programme on aura un
plan de production en présence de maintenance avec une fonction
objective optimisée.
V.? Stratégie utilisé dans le
problème de l'ordonnancement des activités de production et de
maintenance
On recense dans la littérature plusieurs
stratégies d'ordonnancement conjoint qui vont être décrites
ci-dessous et qui vise à résoudre les conflits structurels, qui
existent entre ces deux
104
activités, le plus efficacement possible. Trois
stratégies d'ordonnancement ont été recensées,
l'ordonnancement séparé, le séquentiel et
l'intégré [LEE , 00].
V.3.? l'ordonnancement séparé
Actuellement, la maintenance et la production sont le
plus souvent traitées de manière
indépendante au sein de l'entreprise [BEM ,
02]. Les ordonnancements correspondants à ces deux activités sont
donc réalisés de manière séparée et
interfèrent bien souvent l'un avec l'autre entraînant des retards
dans la production ou dans la maintenance. Cette méthode implique la
mise en place d'une communication accrue entre les services de maintenance et
de production pour limiter les conflits dans l'immobilisation des ressources
aussi bien humaines que matérielles.
V.3.? l'ordonnancement séquentiel
Cette politique consiste à planifier l'une des
deux activités, maintenance ou production, et à
utiliser cet ordonnancement comme une contrainte
supplémentaire d'indisponibilité des ressources dans la
résolution du problème d'ordonnancement de l'ensemble des deux
types de tâches (Figure 32). De manière générale, la
maintenance est planifiée en premier, par la suite l'ordonnancement de
la production est réalisé en prenant les opérations de
maintenance comme des contraintes fortes d'indisponibilité des
ressources [AGG , 02].
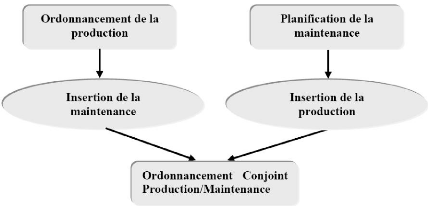
Figure 32 ordonnancement séquentiel
105
106
V.3.3 l'ordonnancement intégré
Cette politique consiste à créer un
ordonnancement conjoint et simultané des tâches de maintenance et
de production [BRA , 96] (Figure 33). Une telle politique de planification
limite les risques d'interférence entre la production et la maintenance
et permet ainsi d'optimiser la qualité des ordonnancements. Cependant,
cette politique n'est actuellement qu'au stade de recherche et de test, vu la
différence de caractérisation des tâches de maintenance et
de production. Néanmoins, elle offre un bon espoir de voir un jour
disparaître les conflits d'utilisation des ressources, mais elle implique
la fusion des deux services production et maintenance, ou au moins la
création d'un lien très fort entre les deux. De plus, un nombre
non négligeable de problèmes est posé par la
différence de caractérisation entre les tâches de
maintenance et de production. Les premières possèdent bien
souvent une date de début au plus tard en fonction des risques
admissibles et ne possèdent pas de durée opératoire connue
avec précision mais juste une durée moyenne (MTTR). Les secondes,
quant à elles, sont caractérisées par une date de
début au plus tôt, une date échue et une durée
opératoire déterminée. Voilà autant d'obstacles
à une planification commune aisée de ces deux types
d'activités.
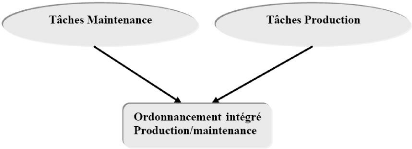
Figure 33 : ordonnancement
intégré
V.? algorithme génétique mis en place dans
l'application
Les algorithmes génétiques sont
considérés par plusieurs chercheurs une méthode bien
adaptée au
problème d'insertion des taches de maintenance
dans un plan de production, même si elle ne peut pas arriver à
l'optimum dans certains cas difficiles
Notre application porte uniquement sur l'algorithme
génétique standard, c-à-dire, la version de base de la
méthode. des versions plus évoluées et plus
sophistiquées ne sont pas appliquées.
Cependant, a la place des opérateurs binaires
classiques, nous avons utilisé des codages et des operateurs
améliorés, basés sur des connaissances spécifiques
du problème. L'algorithme implémenté est
détaillé par l'organigramme de la Figure 34.
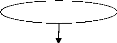
Début
Générer n chromosome s comme solution
initiale (population initiale) ; Construire l'ordonnancement actif à
partir de chaque chromosome ; Calculer le Cmax de chaque chromosome
Sélectionner 50% des chromosomes
Effectuer le croisement entre chaque deux chromosomes
pour produire deux enfants E1 et E2
Construire l'ordonnancement de E1 et E2 ; Calculer Cmax
de E1 et E2 ;
Tirer de chromosomes au hasard x1 et x2 .
Effectuer la mutation entre x1 et x2.
Construire l'ordonnancement de la nouvelle
population
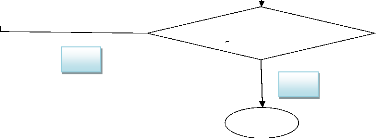
Non
Oui
Fin
Nombre itération
107
Figure 34 Organigramme générale de
l'algorithme génétique implémenté
108
V.4.1 codage de solution
Le codage est le déterminant important de
l'efficacité de la méthode .
Il signifie la transcription d'un ordonnancement
réel en représentation adéquate permettant la
réalisation des différents opérateurs
génétiques .
V.?.1.1 Codage d'un chromosome
Au sein de notre travail, on a codé les
chromosomes de la façon suivante :
Code de la tache
|
Date de début de la tache
|
Date de fin de la tache
|
Durée de la tache
|
Figure 35 représentations d'un
chromosome
V.5 Conclusion
Nous avons présenté dans ce chapitre une
mise en oeuvre d'un système de planification de la
maintenance dans une raffinerie
pétrolière.
Une description des différents composants du
système a été présentée a l'aide du
formalisme de
modélisation UML.
Le système développe permet :
y' Charger des fichiers textes dans le programme pour le
traitement
y' Insérer les taches de maintenance dans un
atelier de production
y' Optimiser le plan de production en présence de
la maintenance
109
CHAPITRE VI
Réalisation &
Expérimentation
110
VI.1 Introduction
Dans le but de résoudre le problème
complexe d'ordonnancement et d'insertion des tâches de
maintenance
dans un plan de production par la metaheuristique , les
algorithmes génétiques , nous présentons dans ce chapitre
, de manière synthétique l'implantation et la justification des
différents choix adoptés pour notre application qui concerne
l'insertion des tâches de maintenances dans un plan de production
.
Ce chapitre est subdivisé en deux sections. Nous
consacrons la première a l'implémentation des algorithmes
génétiques, nous présentons respectivement la
résolution du problème ainsi nous discutons les différents
paramètres utilisés dans notre logiciel.
VI.? présentation de l'application
Dans cette phase, on va données un
déroulement complet de notre application qui porte sur la planification
de tâche de maintenance dans un plan de production, et pour cela on va
illustrer les trois étapes fondamentale de notre
application.
VI.2.? première étape page d'accueil
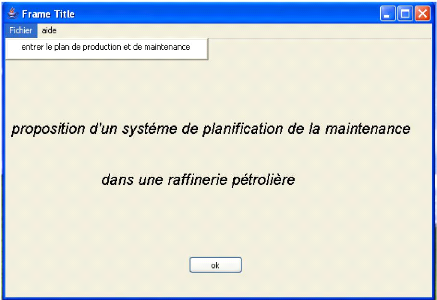
Figure 36 page d'accueil de notre logiciel
111
Cette page contient le nom de notre logiciel et
contient un menu intitulé « entrer le plan de production et de
maintenance »
VI.2.2 deuxième étape saisie des
données
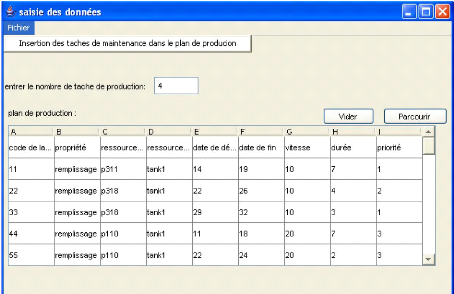
Figure 37 saisie et chargement des données du
plan de production
Cette étape permet à l'utilisateur
d'entrer le nombre de tâche de production et de charger le plan de
production (code de la tâches, propriété, ressource tank,
ressource pompe, date de début, date de fin, vitesse, durée,
priorité), ce chargement est effectué avec un fichier texte comme
le montre la figure suivante :
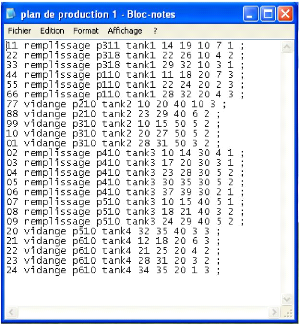
112
Figure 38 fichier texte qui se charge dans la matrice
du plan de production
Ce fichier contient 9 paramètres dont le
premier paramètre représente le code de la tâche de
production et le deuxième représente la propriété
de la tâche (remplissage ou vidange) , le troisième
paramètre est le code de la pompe utilisé , le quatrième
paramètre est le code de la tank, le cinquième paramètre
est la date de début de la tâche de production , le sixième
paramètre représente la date de fin de la tâche, le
septième paramètre est la vitesse de la pompe concerné et
le huitième paramètre est pour désigné la
durée de la tâche , et le dernier paramètre est pour
représenté la priorité de la tâche, si la
priorité est 1 alors c'est une tâche prioritaire par rapport a la
tâche qui a la priorité 2 ou 3 .
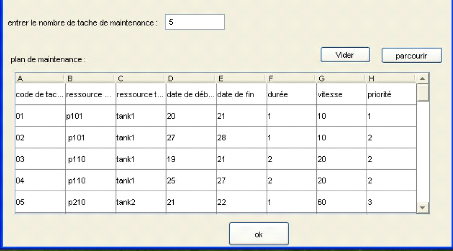
113
Figure 39 saisie et chargement des données du
plan de maintenance
En ce qui concerne le plan de maintenance, on
introduit le nombre de tâche de maintenance ensuite on charge un fichier
texte dans la matrice du plan de maintenance, exemple du fichier texte
:
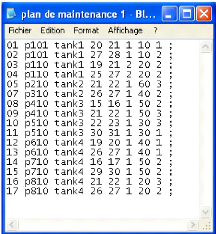
Figure 40 fichier texte qui se charge dans la matrice
du plan de maintenance
114
Ce fichier contient huit paramètres dont le
premier concerne le code de la tache de maintenance et le deuxième
représente le code de la pompe et le troisième représente
le code de la tank , le quatrième paramètre est la date de
début de la tâche de maintenance , le cinquième
paramètre concerne le date de fin de la tâche de maintenance , le
sixième paramètre représente la durée de la
tâche de maintenance et le septième paramètre concerne la
vitesse de la pompe , le dernier paramètre concerne la priorité
de la tâche de maintenance.
VI.2.3 troisième étapes affichage des
résultats et analyse
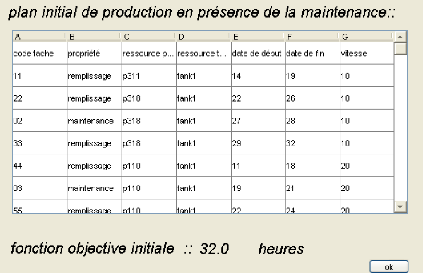
Figure 41 insertion des tâches de maintenance
dans le plan de production
Dans cette étape nous avons
inséré les tâches de maintenance dans le plan de production
en respectant les dates de début et de fin de chaque tâche ,et on
a affiché la fonction objective initiale et après insertion on a
eu le tableau décrit dans la figure 41 dont la tâche de
maintenance 02 est inséré dans l'emplacement 3 et la tâche
de maintenance 03 est inséré dans l'emplacement 6.
115
VI.2.3.1 Analyse de résultats
Le nombre de tâche de maintenance a
inséré dans cette exemple est 2 avec 5 tâches de
productions, puisque nous sommes dans le cas d'insertion des tâches de
maintenance sur plusieurs machine alors on effectue l'insertion en utilisant un
décalage à gauche s'il ya lieu pour pouvoir optimisé le
plan de production conjoint maintenance, dans cette exemple l'insertion des 2
tâches de maintenance a été sans difficulté car
l'intégration ne provoque pas un conflit production \ maintenance , en
effet la figure 41 représente un plan de production \ maintenance
initiale , sur le quel on va appliquer l'algorithme génétique
afin de donner un plan final de production \ maintenance.
On a appliqué l'algorithme
génétique sur le tableau illustré dans la figure 41 afin
d'optimiser la fonction objective et comme première étape de
l'algorithme génétique c'est la construction de la population
initiale dont chaque chromosome on fait un décalage à gauche s'il
ya lieu pour pouvoir optimiser la fonction objective ainsi la population est
représenté comme suit :
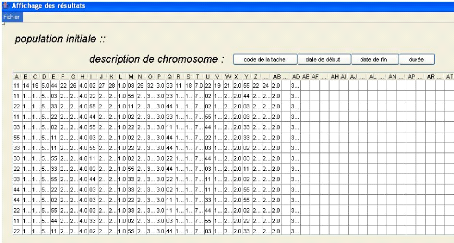
Figure 42 population initiale de l'algorithme
génétique
Le résultat obtenu dans la Figure 42 est une
population initiale dont nous avons sept chromosomes par ligne dont chaque
chromosome est structuré comme suit :
116
Code de la tâche de production
ou de maintenance
|
Date de début de la tache
|
Date de fin de la tache
|
Durée de la tache
|
Figure 43 structure d'un chromosome
Et le dernier paramètre indiqué dans le
tableau de la Figure 42 est la fonction objective
Après avoir construire la population initiale on
applique les opérateurs de sélection & croisement &
mutation sur la population initiale comme suit :
1. étape de sélection
Dans cette étape on a utilisé la
sélection par rang et on a fixé un pourcentage de 50% de chaque
population calculé.
2.étape de croisement
Durent cette étape on a croisé chaque deux
individus pour donner un autre individu enfant.
3.étape de mutation
L'opérateur de mutation a été fait
entre deux individus qui se suit afin de donner d'autre individus pour enrichir
notre population initiale.
Notre système traite environ de cinq populations
afin de donner une solution bien optimisé.
117
VI.2.3.2 résultat de notre application
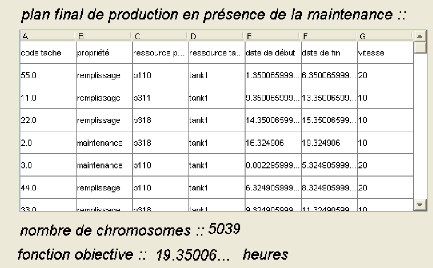
Figure 44 plan final des taches de production en
présence de la maintenance
Notre objectif est d'optimiser le plan de la Figure 41 et
d'optimiser aussi la fonction objective ou le Cmax
avec le principe de GANTT qui est basé sur des
décalages à gauche, et avec cette méthode on a obtenu le
tableau de la Figure 44.
VI.2.3.3 explication
La résolution du problème d'insertion
des tâches de maintenance dans un plan de production est donnée
dans la Figure 44, pour les machines « p110 » & « p311
» , nous n'avons pas de tâche de maintenance par contre pour les
machines « p318 » & « p110 » , nous avons une
tâche de maintenance pour chacune .
Pour la machines « p110 » on a trois taches,
55.0 et 3.0 et 44.0 dont la tâche 55.0 et 44.0 sont des tâches de
production de type « remplissage » et nous avons une seule
tâche de maintenance (3.0).
Pour la machines « p311 » nous avons une
seule tâche (11.0) et la machine « 318 » comporte trois
tâches (la tache 22.0 et 2.0 et 33.0) dont la tâche 2.0 est une
tache maintenance.
118
VI.2.3.4 but de l'application
Nous avons proposé un système de
planification de la maintenance dans un plan de production qui est capable de
faire les fonctions suivantes :
V' Chargement des fichiers textes dans le programme pour
le traitement V' Insertion des tâches de maintenance
dans un atelier de production V' Optimisation du plan de
production en présence de la maintenance
VI.3 conclusion
Dans ce chapitre, nous avons étudié le
problème de l'ordonnancement conjoint de la production et de la
maintenance préventive systématique.
Le but est d'optimiser une fonction objective qui
prend en compte les critères d'optimisation de la production et ceux de
la maintenance. Pour le résoudre, nous nous sommes
intéressés à l'algorithme génétique qui a
prouvé leur aptitude de résolution en ordonnancement de
production. De plus, nous avons abordé ce problème selon les deux
stratégies d'ordonnancement conjoint les plus intéressantes : la
stratégie intégrée et la stratégie
séquentielle. Et avec la stratégie intégré on a
réaliser une application qui répond au besoin de la raffinerie
dans le domaine de la planification des taches de maintenance dans un plan de
production.
119
Conclusion générale
120
Conclusion générale
Dans cette thèse, nous nous sommes
intéressés à l'aspect maintenance industrielle qui joue
aujourd'hui un rôle déterminant dans la conduite de la production
industrielle. Elle a acquis dans l'entreprise manufacturière une
position clef. Tandis que la main d'oeuvre de fabrication a perdu de son
importance, les coûts de maintenance des équipements industriels
se sont accrus considérablement, ce qui se reflète dans les
budgets.
Que ce soit dans le domaine de la gestion de
production ou dans celui du pilotage d'un atelier de production,
l'ordonnancement est un problème difficile qui recouvre souvent des
enjeux économiques de première importance. Cette importance
devient cruciale lorsqu'il touche deux fonctions aussi importantes
qu'antagonistes au sein de l'entreprise que le sont la production et la
maintenance.
Notre contribution touche deux aspects. D'une part
l'adaptation des heuristiques pour l'ordonnancement de production au
problème de l'ordonnancement conjoint de la production et de la
maintenance préventive systématique. Le but est d'optimiser une
« fonction objectif compromis » entre les
critères d'optimisation de la production et ceux de la maintenance. Ce
problème étant NP-complet, pour le résoudre, nous nous
sommes intéressés à l'heuristique des approches
constructive, itérative et évolutive, nommé les
algorithmes génétiques, qui ont prouvé leurs aptitudes de
résolution pour un nombre important de problèmes d'optimisation.
Nous avons abordé ce problème selon les deux stratégies
d'ordonnancement conjoint les plus intéressantes : la stratégie
intégrée et la stratégie séquentielle.
Pour les Algorithme Génétique, comme
nous manipulons une séquence conjointe de tâches de production et
de maintenance, le croisement et la mutation peuvent se faire aussi bien sur la
production que sur la maintenance. Les opérateurs de croisement et de
mutation sur la production et la maintenance restent les opérateurs
classiques de la méthode.
121
Références
Bibliographiques
122
Site web
> [web 1]
http://www.techno-science.net
> [web 2]
http://www.laas.fr/~lopez/
> [web 3] http://fr.wikipedia.org/
> [web 4] http://www.poleia.lip6.fr/
> [web 5]
http://www.enset-media.ac.ma/cpa/techniques_ordonnancement_taches.htm
> [web 6]
hal.inria.fr/inria-00001259/fr/
> [web 7] www.Afnor.fr
> [web 8]
www.developpez.com
> [web 9]
http://uml.fr
e.fr
Référence
[Boul &Cher , 081
Boulebiar Mohamed Mehdi, Cherifi Mohammed El Ghaouti, Thèse
d'ingéniorat 2007/2008 : Ordonnancement d'un atelier de production de
bien et de services de type Job Shop Flexible avec Contraintes.
[Bapt , 981 Philippe Baptiste, une
étude théorique et expérimentale de la propagation des
contraintes de ressource , thèse de doctorat, université de
technologie de compiégne ,1998.
[Bapt , 991 Philippe Baptiste, Claude Le Pape
et Wim Nuijten. Satisfiability Tests and Time-Bound Adjustments for Cumulative
Scheduling Problems. Annals of Operations Research 92(1999)305-333.
[Boit &Haza,871 BOITEL D et HAZARD C, guide
de la maintenance, Edition NATHAN ,1987. [Benb ,051 Fatima
BENBOUZID SITYEB thèse de fin d'étude pour l'obtention de
diplôme doctorat :Contribution a l'étude de la performance et de
la robustesse de ordonnancements conjoint production / maintenance- cas de
flow-shop
[Benm, 061 BENMBAREK Naima automatisation du
système de la maintenanc préventive [Blaz ,96]
J. Blazewicz, K.H. Ecker, E. Pesch, G. Schmidt & J.
Weglarz. Sche-duling in computer and manufacturing processes. Springer
Verlag,1996
123
[BOUL,88] Boulenger A., Vers le zéro panne avec la
maintenance conditionnelle, Guides de l'utilisateur, AFNOR, Paris,
??88.
[Coel, Carl, 00]. Coello et carlos "An updated survey of
GA-based multi Objective optimization techniques". ACM Computing
Surveys, ACM press, Vol. 32,No 2, pp.109-143. [Cant., 2000].
Cantù-Paz E Efficient and accurate parallel genetic
algorithms. Kluwer Academic Publishers, Boston, 162 p.
[Cerr Anni , 99]. "Genetic algorithms in shape
optimization : finite and boundary element applications", pp.283-3?3. Dans :
"Evolutionary algorithms in engineering and computer science: recent advances
in genetic algorithms, evolution strategies, evolutionary programming, genetic
programming and industrial applications" 500 p
[DebK, Prat 02]. Deb K., Pratap A "A Fast
and Elitist Multiobjective Genetic Algorithm: NSGA-II." IEEE
Transactions on Evolutionary Computation, Vol. 6, No 2, pp.182-197. [Fran&
Jean,03] FRANCASTEL et JEAN-CLAUDE, ingénierie de la
maintenance.2003.494 P. [ BAVI ] G BAVIER Technique
d'ordonnancement
[Goth , 93] Gotha , Modèles et algorithmes en
ordonnancement
[Giar , 88] Giard V gestion de la production ,
2éme edition , economuca paris, 1988
[GIRA,00] Girard B., Guide pratique du responsable de
maintenance, T1. Edition WEKA, 2000
[Gold, 1994]. Goldberg D.E , Algorithmes
génétiques : exploration, optimisation apprentissage automatique.
Traduction de l'anglais (américain) par Vincent Corruble.
Éditions Addison-Wesley France, 417 p.
[Gold, 1989] Goldberg D.E., Genetic
Algorithms in Search, Optimization and Machine Learning.
Addison Wesley Longman, 412 p.
[KOLS,93] Kolski C. & Millot P., "Problems in
telemaintenance decision aid criteria for telemaintenance system design",
International Journal of Industrial Ergonomics, VOL.11 (2), pp. 99-106,
1993.
[Kebe , 08] kebebla mebarak ,Thèse pour
l'obtention du diplôme magistère 2 juillet 2008 , utilisation des
stratégies metaheuristique pour l'ordonnancement des ateliers de type
job shop.
124
[KAFF,01] Kaffel H., La maintenance
distribuée : Concepts, Evaluation et Mise en oeuvre. Thèse PhD,
département de génie mécanique, Faculté des
sciences et de génie, Université de Laval, Québec, Canada,
2001.
[LAUG , 96] Laugier A., Allahwerdi N., Baudin
J., Gaffney P., Grimson W., Groth T. & Schilders L., "Remote instrument
telemaintenance", Computer Methods and Programs in Biomedicine, VOL. 50 (2) pp.
187-194, Elsevier Science Ireland Ltd Shannon Ireland, 1996. [LAVI ,
96] Lavina Y. & Loubère J. M., Maintenance et Travaux
Neufs, Les règles de la maintenance.
[lope & Esqu 99] Esquirol
P., Lopez P., L'ordonnancement, Edition Economica ,1999. [Leto , 01]
letouzey A Ordonnancement interactif basé sur les indicateurs :
application a la gestion des commandes incertaines et l'affectation des
operateurs, thése de doctorat, institut national polytechnique de
Toulouse, 2001
[LYON ,92] Lyonnais P., Maintenance
mathématique et méthode. Troisième édition,
[LAVI , 96] Lavina Y. & Loubère J. M., Maintenance
et Travaux Neufs, Les règles de la sous-traitance. Les Éditions
D'organisation, Paris France, 1996. Lavina Y., La maintenance:
fiabilité, maintenabilité, sécurité. Edition
Masson, 1998
[Lang , 1998] Langdon W.B " Genetic programming
and data structures: genetic ,278 p. [Monc&Fran 93]
MONCHAY FRANCOIS, maintenance : méthode et organisation 2003
513p [MONC,94] MONCHAY F, fonction maintenance : formation
à la gestion de la maintenance industrielle, deuxième ED, Masson,
Paris, 1994.
[MONC,96] Monchy F., La fonction maintenance.
Edition Masson, 1996.
[MCAL, 65] McCALL J.J., "Maintenance policies
for stochastically fail equipment: a survey", Management Science, VOL. 11(5),
pp.493-524, 1965.
[MOUB ,97] Moubray J., Reliability Centred
Maintenance. International Press1997.
[MALC , 93] Malcolm M., "Plant Maintenance. A
New Direction", Process and Control engineering, PACE, VOL. 46 (9), pp. 20-22,
September 1993.
[NAKA , 89] Nakajima S., La maintenance
productive Totale : Mise en oeuvre. AFNOR, 1989.
[NAKA , 87] Nakajima S., La maintenance
productive totale (TPM), nouvelle vague de la production industrielle. Afnor
Gestion, 1987.
[Pins 88] Pinson , Le Problème de Job
Shop, Thèse de Doctorat de Univ. Paris VI,1988.
125
[PIER , 76] Pierskalla W. & Voelker J., "A survey
of maintenance models: the control and surveillance of deteriorating systems",
Naval Research Logistics Quarterly, VOL. 23, pp.353-388, 1976.
[PIER,76] Pierskalla W. & Voelker J., "A survey of
maintenance models: the control and surveillance of deteriorating systems",
Naval Research Logistics Quarterly page .353-388, 1976.
[Roy , 71] Roy B, Sussmann B. «Les
problèmes d'ordonnancement avec contraintes disjonctives ». Note DS
NO 9 Bis, SEMA, Montrouge, 1964..*
[Ryan C. 2000]. Ryan C, 2000 Automatic
Re-Engineering of Software using Geneti Programming. Kluwer
Academic Publishers,140 p.
[SASS,98] Sassine C., Intégration des politiques
de maintenance dans les systèmes de production manufacturiers.
Thèse de doctorat soutenue à l')NP de Grenoble ?France?, ?99?.
[Sade , 91] Sadeh, Lookahead Techniques for Micro-Opportunistic Job Shop
Scheduling , 1991.
[Slow82] Slowinski 82 , Advances in project scheduling
(Eds) Elsevier
[T' kin & Bila ,06] T'kindt V & bilaut J . -C
multicritaria scheduling theory , mdel and algorithms translated from French
bay H scott , second edition , springer-verlague berlin 2006
[VERD,88] Verdol P., Térotechnologie :
interprétation économique d'un nouveau mode d'organisation
intégrée de la disponibilité des équipements
industriels, thèse de doctorat soutenue à l'université
Lumière Lyon II (France), 1988.
[WHEA ,96] Wheaton, R., "Reliability-Based Maintenance
Requires Mill Culture Change", Pulp and Paper, pp. 53-61, July
1996.
[ZWIN,96] Zwingelstein G., La maintenance basée
sur la fiabilité, Guide pratique d'application de la RCM. Série
Diagnostic et Maintenance, AFNOR, 1996.
|