DEDICACE
À TOUTE LA FAMILLE DJEUKEM
REMERCIEMENTS
Je remercie tout d'abord l'Eternel Dieu Tout-Puissant pour sa
grâce, sa bonté et sa bénédiction.
Je voudrais également exprimer ma reconnaissance et
gratitude à l'encontre de tous ceux qui d'une manière ou d'une
autre m'ont apporté leur aide multiforme. Je pense notamment
à :
· Prof NSO Emmanuel J., le Directeur de l'ENSAI et
tout le personnel enseignant de l'école pour les encadrements et les
enseignements reçus ;
· Mes encadreurs académiques, Pr. NDI KOUNGOU
Sylvere et Dr KOFA Guillaume, pour les améliorations apportées
à ce travail ;
· M. TEDOM Bonaventure, le P.C.A du Complexe Industriel
du Littoral pour m'avoir accepté en stage et pour les conditions de
stage favorables ;
· Mme TEDOM Diane, la Directrice Générale
pour son soutien et sa confiance ;
· M. OLAMA Seme, le Directeur Technique pour son accueil
chaleureux, son encadrement, sa disponibilité, son suivi, son appui et
ses divers conseils ;
· M. JIOTSA Martin, le Responsable de Maintenance
pour sa disponibilité, patience et rigueur ;
· M. KAPTUE Emmanuel, le Responsable de Production pour
son esprit d'ouverture, son hospitalité, sa constante présence
malgré ses multiples occupations, sa patience, sa confiance et pour la
transmission de son immense savoir-faire et de son savoir être ;
· Tout le personnel du laboratoire du Complexe Industriel
du Littoral pour leurs conseils, le partage de leurs savoir-faire, leurs
collaborations et l'ambiance conviviale pendant la période de stage ;
· Tout le personnel du Complexe Industriel du Littoral
;
· Mes très chers parents, M. et Mme DJEUKEM, pour
l'amour et le soutien qu'ils m'ont toujours porté ;
· Ma grand-mère KENGMO Antoinette à Paris,
M. et Mme DJIOGHO à N'Gaoundéré, M. et Mme TEKAPI
à Douala pour leurs soutiens financiers et morales pendant toute la
période du stage ;
· M. et Mme NGOUANA, pour leurs hospitalités
pendant toute la durée du stage ;
· Tous mes frères et soeurs pour l'assistance
morale lors de la rédaction de ce document ;
· Tous mes camarades de la 7ème
promotion de la filière Chimie Industrielle et Génie de
l'Environnement (CIGE), de la 21ème promotion de la
filière Industrie Agro-Alimentaire (IAA) et de la
15ème promotion de la filière Maintenance
Industrielle et Productique (MIP) ;
· Tous mes camarades du « University of
Ngaoundéré Anglophone Students Association »,
(UNASA) ;
· Tous ceux dont les noms ne figurent pas ici mais qui
ont d'une manière ou d'une autre, de près ou de loin
contribué à la réalisation de ce mémoire.
TABLE DES MATIERES
DEDICACE
Erreur ! Signet non
défini.
REMERCIEMENTS
ii
TABLE DES MATIERES
iv
LISTE DES ABBREVIATIONS
vii
LISTE DES TABLEAUX
viii
LISTE DES FIGURES
ix
LISTE DES ANNEXES
x
AVANT-PROPOS
xi
RESUME
xii
ABSTRACT
xiii
PRESENTATION DE L'ENTREPRISE
xiv
INTRODUCTION
1
CHAPITRE I : REVUE DE LA LITERATURE
2
I.1. Ressources en eau
2
I.2. Généralités sur les eaux
du forage
2
I.2.1. Caractéristiques de l'eau des nappes
souterraines (Eau du forage)
3
I.3. Généralités sur les eaux
de process
3
I.4. Quelques indicateurs de la qualité des
eaux
4
I.4.1. Dureté
4
I.4.2. Alcalinité
4
I.4.3. Salinité totale - Conductivité
et Résistivité
5
I.4.4. Teneur en fer
6
I.4.5. Teneur en chlorures
8
I.5. Généralités sur les
chaudières
9
I.5.1. Historique des chaudières
10
I.5.2. Présentation de la chaudière
du Complexe Industriel du Littoral
11
I.6. Généralités sur la
méthodologie appliquée
13
I.6.1. Méthode DMAIC ou Six Sigma
13
I.6.2. Principe de la méthode
15
CHAPITRE II : MATERIEL ET METHODES
16
II.1 MATERIEL
16
II.2. METHODES
17
II.2.1. Etat des lieux
18
II.2.2. Caractérisation physicochimique de
l'eau du forage
18
II.2.3. Brainstorming
20
II.2.4. Propositions des actions correctives
21
II.2.5. Evaluation des coûts
21
CHAPITRE III: RESULTATS ET DISCUSSION
22
III.1. ETAT DES LIEUX
22
III.1.1. Station de traitement
22
III.1.2. Procédé de traitement
24
III.1.3. Constats fait
27
III.2. QUALITE PHYSICOCHIMIQUE DE L'EAU DU
FORAGE
27
III.2.1. Produits du traitement existant de l'eau
du forage
28
III.3. CLASSIFICATION ET HIERARCHISATION DES CAUSES
DU TRAITEMENT INSUFFISANT DE L'EAU DU FORAGE (BRAINSTORMING)
29
III.3.1. Classification des causes du traitement
insuffisant de l'eau du forage
29
III.3.2. Hiérarchisation des causes du
traitement insuffisant de l'eau du forage
29
III.3.3. Identification des anomalies majeures dans
le mauvais traitement de l'eau
30
III.4. PROPOSITION DES ACTIONS CORRECTIVES
31
III.4.1. Déferrisation de l'eau du
forage
31
III.4.2. Dé-chloration de l'eau du
forage
35
III.5. EVALUATION DES COÛTS DES ACTIONS
CORRECTIVES
38
III.5.1. Evaluation des coûts du projet
38
III.5.2. Evaluation des charges annuelles
38
CONCLUSION
39
REFERENCES BIBLIOGRAPHIQUES
40
ANNEXES
42
LISTE DES ABBREVIATIONS
NTU : Nephelometric Turbidity Unit
pH : Potentiel d'Hydrogène
DMAIC :
Définir-Mesurer-Analyser-Innover-Contrôler
CIL : Complexe Industriel du Littoral
ISO : International Standard Organization
TH : Titre Hydrotimétrique
TA : Titre Alcalimétrique
TAC : Titre Alcalimétrique Complet
QQOQCP : Qui-Quoi-Où-Quand-Comment-Pourquoi
LISTE DES TABLEAUX
Tableau 1: Fiche
d'identification du Complexe Industriel du Littoral
iii
Tableau 2: Les ressources
en eau sur le globe terrestre (Eagleson, 1970)
2
Tableau 3: Qualité
des eaux du Complexe Industriel du Littoral
9
Tableau 4: Description du
problème avec l'outil QQOQCP
27
Tableau 5: Qualité
physicochimiques de l'eau du forage
28
Tableau 6: Valeurs
pondérés des causes liées au traitement insuffisant de
l'eau
30
Tableau 7 : valeurs
moyennes des ozoneurs
32
Tableau 8: Valeurs moyennes
des compresseurs d'air
34
Tableau 9 : Etude
comparative de la méthode de déferrisation avec l'ozone et avec
l'oxygène
35
Tableau 10:
Caractéristiques du filtre à cartouche de charbon actif
granulaire proposé
35
Tableau 11: Evaluation des
coûts du projet
38
Tableau 12: Charges
Annuelles
38
LISTE DES FIGURES
Figure 1: Organigramme du
Complexe Industriel du Littoral (source CIL, 2014)
iii
Figure 2: Vue de face de la
chaudière du Complexe Industriel du Littoral
11
Figure 3: Schéma
indiquant la circulation de l'eau dans la chaudière
13
Figure 4 : Schema de la
methodologie
15
Figure 5: Schéma
synoptique du travail effectué
17
Figure 6 : Vue
générale d'un diagramme d'ISHIKAWA
21
Figure 7:
Présentation de la station de traitement d'eau du forage
du Complexe Industriel du Littoral
24
Figure 8: Schéma
block du traitement existant de l'eau du forage du Complexe Industriel du
Littoral
25
Figure 9: classification
des Causes du traitement insuffisant de l'eau
29
Figure 10: Diagramme de
Pareto
30
Figure 11 :
Présentation de la station de traitement (Actions correctives) d'eau du
forage du Complexe Industriel du Littoral
36
Figure 12: Schéma
block du traitement de l'eau du forage (Actions correctives) du Complexe
Industriel du Littoral
37
LISTE DES ANNEXES
Annexe 1 :
Répartitions des votes pondérés suivant
les cotations
3
Annexe 2 :
Récapitulatif des fréquences du diagramme de Pareto
42
Annexe 3:
Présentation des eaux du Complexe Industriel du
Littoral
43
Annexe 4: Vue de face de la
station de traitement
43
Annexe 5:
Présentation des dispositifs de traitement d'eau
44
Annexe 6:
Présentation de la bâche
45
Annexe 7: Questionnaire
45
Annexe 8:
Caractéristiques des équipements utilisés pour le
traitement de l'eau
46
Annexe 9:
Procédé de fabrication du savon
47
Annexe 10: Plan de
localisation du Complexe Industriel du Littoral (CIL)
48
Annexe 11: Fiche du rapport
journalier contrôle qualité
49
AVANT-PROPOS
L'Ecole Nationale Supérieure des sciences
Agro-Industrielles, connue sous l'acronyme ENSAI, est une des écoles de
l'université de Ngaoundéré crée lors de la
réforme universitaire de Janvier 1993. Elle a pour mission :
· La formation des ingénieurs de conception
hautement qualifiés dans les spécialités que
sont :
1. Industrie Agro-Alimentaire (IAA) ;
2. Maintenance Industrielle et Productique
(MIP) ;
3. Chimie Industrielle et Génie de l'Environnement
(CIGE).
· La formation des masters professionnels en
Contrôle et Gestion de la Qualité (CGQ),
Nutrition Appliquée (NA), Maintenance et Gestion des
Equipements Frigorifiques et Thermiques (MAINGEFT).
· La formation des masters recherches et le cycle
doctoral en Chimie Appliquée ; Génie Electrique,
Energétique et Automatique ; Génie Mécanique ;
Génie des Procédés Industriels ; Mathématiques
Informatiques ; et Science Alimentaire et Nutrition (SAN).
Le cycle de formation des ingénieurs de conception
s'étale sur une période de 36 mois et est marqué par 03
stages académiques :
§ Un stage ouvrier de 1 à 2 mois à la fin
de la première année ;
§ Un stage agent de maitrise de 1 à 2 mois
à la fin de la deuxième année ;
§ Un stage fin d'études (Stage Ingénieur)
de 3 à 4 mois à la fin de la formation.
Les stages fins d'études sont sanctionnés par une
soutenance devant un jury. Durant cette période de stage, le futur
ingénieur doit résoudre un problème en particulier, de
nature industrielle, en proposant une solution innovante. C'est dans cette
optique que ce mémoire a été rédigé au terme
d'un stage fin d'étude ingénieur effectué au
Complexe Industriel du Littoral (CIL) à Douala, du 01
juillet au 15 septembre 2017.
RESUME
Dans le souci de veiller au bon fonctionnement de la
chaudière afin d'assurer sa longue durée, le Complexe
Industriel du Littoral (CIL), situé à Bonabéri
(Douala), s'engage à traiter davantage l'eau provenant de son forage
(profondeur environ 100 m). Il est question dans ce travail de réduire
la teneur en fer et chlorure que contient cette eau, car ils sont
néfastes pour la chaudière et ils entrainent la corrosion de
cette dernière et celles des tuyauteries. C'est ainsi que l'entreprise
CIL nous a assigné le thème «Etude Critique du
Système de Traitement de l'Eau de Chaudière du Complexe
Industriel du Littoral». Pour ce travail, la démarche
DMAIC qui s'articule en cinq (05) étapes a été
utilisée : Définir - Mesurer - Analyser - Innover et
Contrôler. La première étape a permis de faire un
état des lieux afin d'évaluer les problèmes. La
deuxième étape consistait à évaluer les
paramètres physico-chimiques de l'eau du forage. La troisième
étape nous a permis de rechercher les différentes causes des
problèmes à résoudre. Puis s'ensuivait la prescription des
actions correctives et enfin l'analyse des coûts des actions
proposés. Les doses hebdomadaires en produits utilisés par
l'entreprise pour le traitement existant de 18 m3 d'eau sont :
25 kg de sulfate d'alumine hydraté + 9 kg de soude pour l'étape
de coagulation, et 25 kg de soude pour hausser le pH de l'eau du forage
étant donner qu'elle est acide. Afin d'améliorer le traitement de
l'eau du forage, nous avons proposé l'usage d'un ozoneur ou un
compresseur d'air, pour la diffusion de l'ozone ou l'oxygène dans la
tour d'oxydation lors du captage de l'eau du forage. L'ozone ou
l'oxygène généré va entrainer la
précipitation du fer présent dans l'eau du forage par oxydation
forcée. Ensuite un système de dé-chloration, qui consiste
à intégrer un filtre à cartouche de charbons actifs
granulaires en aval du filtre sable-gravier et le préchauffage de la
bâche, ont également été proposé. Ces
solutions proposées ne sont pas néfastes pour la chaudière
et les tuyauteries. Les coûts de ce projet ont été
évalué à 28 970 000 FCFA (pour le cas de
l'ozoneur plus filtre charbon actif) et 7 985 000 FCFA (pour le cas
du compresseur d'air plus filtre charbon actif). Les charges annuelles ont
également été évaluées à 4 324
097,28 FCFA (dans le cas de l'ozoneur) et 2 427 680 FCFA (dans le cas du
compresseur d'air).
Mots-clés : Forage,
chaudière, DMAIC, traitement.
ABSTRACT
In order to look after the good functioning of the boiler so
as to assure its long lasting, the Littoral Industrial
Complex, situated in Bonaberi (Douala) engages itself in a further
treatment of water from its bore-hole (about 100 m deep). This work is all
about reducing the iron and chloride content present in water. This iron and
chloride are harmful to the boiler for they cause the corrosion of the latter
and that of the pipes. It is thus that the enterprise assigned to us the theme
«Critical Study of the Boiler Water Treatment System of the
Littoral Industrial Complex». For this work, we used the DMAIC
gait which articulates in five (05) stages: Define - Measure - Analyze -
Innovate - and Control. The first stage has permitted to make an inventory of
fixtures in order to evaluate the problems. The second stage consists in
evaluating the physico-chemical parameters of raw water. The third stage
allowed us to search the different causes of the problems to solve. Then
follows the prescription of corrective actions, and finally cost analysis of
these proposed actions. The weekly doses in products used by the enterprise for
the existing treatment of 18 m3 of water are: 25 kg of hydrated
aluminium sulfate + 9 kg of sodium hydroxide for the coagulation stage, and 25
kg of sodium hydroxide in order to increase the pH of the raw bore-hole water
given that it is acidic. In order to improve the treatment of water from the
bore-hole, we proposed the use of an ozone generator or an air compressor, for
the diffusion of ozone or oxygen in the oxidation tower during the collection
of water from the bore-hole. Ozone or oxygen will cause the precipitation of
iron present in the bore-hole water. Afterwards a de-chlorination system, which
consists of integrating a granular activated charcoal filter downstream the
sand-gravel filter and the pre-heating of the tarpaulin, have equally been
proposed. These solutions proposed are not dangerous for the boiler and the
pipes. The cost of the project were evaluated at 28 970 000 FCFA (in
the case of an ozone generator plus activated charcoal filter) and
7 985 000 FCFA (in the case of an air compressor plus activated
charcoal filter). The annual charges were also evaluated at 4 324 097.28
FCFA (case of an ozone generator) and 2 427 680 FCFA (case of an air
compressor).
Key-words: Bore-Hole, boiler, DMAIC,
treatment.
PRESENTATION DE
L'ENTREPRISE
EMERGENCE ET HISTORIQUE
Le projet du Complexe Industriel du Littoral
installé à Bonabéri dans la banlieue Ouest de la ville de
Douala au Cameroun a été initié par son promoteur qui fait
dans la distribution des produits alimentaires et autres produits de
consommation courante depuis plus d'une vingtaine d'années avec la
société SODIPALCAM SARL qui a des agences
à Douala, Yaoundé ainsi qu'à Bafoussam, couvrant ainsi les
trois principales villes du Cameroun.
Le Complexe Industriel du Littoral a été
constitué sous la forme d'une Société à
Responsabilité Limitée (SARL) au capital de 5 000 000
Francs CFA le 29 septembre 2004 réparti à l'origine entre cinq
associés à raison de 20%. L'essentiel des fonds
nécessaires a été cependant apporté par le
promoteur sous forme d'avance en compte courant pendant toute la durée
d'installation de 2004 à 2009. Il en assurait alors la gestion
quotidienne parallèlement à ses activités de Gérant
de la SODIPALCAM SARL. Ces fonds ont été complétés
par un emprunt contracté auprès d'une banque de la place. La
Société à Responsabilité Limitée (SARL) a
ainsi été transformée en Société Anonyme
(S.A) et le capital porté à 10 000 000 Francs CFA lors
de l'Assemblée Générale Extraordinaire (AGE) du 05
août 2008, avant même le démarrage de la production. Le
promoteur a alors été désigné Président du
Conseil d'Administration (PCA). La production a effectivement
démarré à la date du 24 novembre 2009. Ce capital a
été porté successivement par l'Assemblée
Générale Extraordinaire du 28 décembre 2010 à 702
000 000 Francs CFA et à 2 054 000 000 Francs CFA par
celle du 28 décembre 2014. Il est de nos jours détenu par quatre
personnes physiques à hauteur de 25% chacun. Malgré ce statut de
Société Anonyme avec quatre actionnaires tous membres du conseil
d'administration et la nomination d'un directeur général,
l'essentiel de la gestion est dans les mains du PCA.
L'usine tient sur un
terrain de 4 000 m² dont environ 2 500 m² bâtis,
propriété de l'entreprise. Un forage, un groupe
électrogène, des cuves de stockage des différentes
matières premières, une chaudière, un compresseur, un
groupe de refroidissement et une chaîne complète de production,
constituent ses principaux équipements. Un parc d'une quinzaine de
véhicules pour l'administration, le transfert entre les magasins et la
vente, est aussi à mentionner.
En effet, elle commence son activité de production et
de commercialisation du savon de ménage SANET tout en ayant pour
ambition de se faire une place de choix au sein des sociétés
concurrentes. C'est ainsi qu'elle réussi à se faire remarquer sur
le marché au bout de quelques mois seulement grâce à ses
nombreux circuits de distribution et sa main d'oeuvre appliquée
constituée de près de 100 employés. Ceci laissant voir son
chiffre d'affaire toujours grandissant.
ACTIVITES ET OBJECTIFS
L'activité du Complexe Industriel du Littoral porte
d'une part sur la production du savon de ménage, et d'autre part sur la
commercialisation du savon, du détergent et de la bougie. Tous ces
produits sont commercialisés sous le label
« SANET », excepté le détergent dont le label
est « SANET CLEANER ».
Le Complexe Industriel du Littoral a pour principal objectif
la production du savon de ménage baptisé SANET et sa distribution
sur le marché. La fabrication de ce produit nécessite un choix
minutieux des matières premières que sont l'huile de palme,
l'huile de palmiste, la stéarine, la soude caustique, le sel et
l'eau.
L'ORGANISATION
La bonne gestion d'une entreprise passe par la mise en place
des organes de direction et de gestion. Elle passe également par la
décentralisation des pouvoirs et des taches dans le but de
réaliser les objectifs qui lui sont assignés. C'est donc dans
cette voie que s'est engagé le Complexe Industriel du Littoral. Sa
structure se présente de la manière suivante :
· Le Président du Conseil d'Administration
· Le directeur Général ;
· Le Service Comptable ;
· Le Service Commercial ;
· Le Service Technique et Production ;
· La Secrétaire ;
· Les Services Externes.
RESSOURCES FINANCIERES
Société Anonyme de son état, le Complexe
Industriel du Littoral possède un capital social qui est passé de
10 000 000 de Francs CFA, à 702 000 000 de Francs
CFA, et aujourd'hui est à 2 054 000 000 de Francs CFA.
LA FICHE D'IDENTIFICATION
Cette fiche contient essentiellement les renseignements
primordiaux de l'entreprise et est illustré comme suit :
Tableau 1: Fiche
d'identification du Complexe Industriel du Littoral
Raison sociale
|
Complexe Industriel du Littoral (C.I.L)
|
Forme juridique
|
S.A
|
P.C.A
|
M. TEDOM BONAVENTURE
|
Date de création
|
29 Septembre 2004
|
Siège social
|
Mambanda, Bonabéri - Douala
|
Adresse
|
B.P. 12296 Douala - Cameroun
|
N° du contribuable
|
M090400022640A
|
Capital social
|
2 054 000 000 Francs CFA
|
Registre de commerce
|
RC/DLA/2004/B/033855
|
Activité principale
|
Fabrication des savons, détergents et produits
d'entretiens
|
Situation géographique
|
Mambanda - Bonabéri
|
Téléphone
|
+237 233 39 46 71
|
E - mail
|
cil_sanet@yahoo.fr
|
L'ORGANIGRAMME
Le Complexe Industriel du Littoral est divisé en
plusieurs organes décisionnels sous la direction du Président du
Conseil d'Administration, comme le montre l'organigramme ci-après :
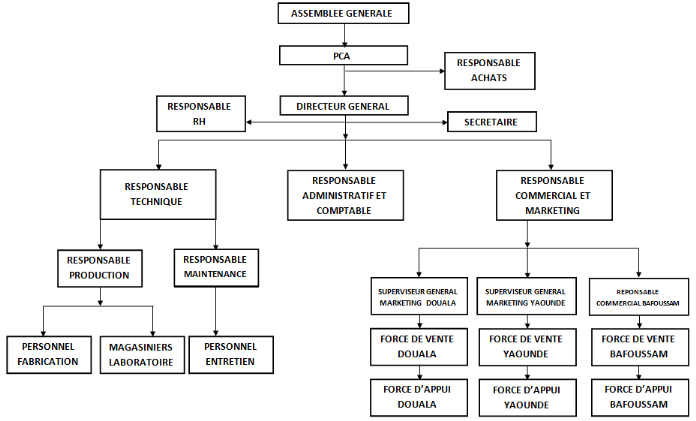
Figure 1:
Organigramme du Complexe Industriel du Littoral (source CIL, 2014)
INTRODUCTION
L'eau est le composé le plus abondant sur la surface du
globe (Eisenberg et al, 1969). Sans elle, la vie cesserait d'exister. L'eau est
donc indispensable pour nos besoins de consommation, ménagers, agricole,
industriels et bien d'autres.
Les industries utilisent souvent l'eau en tant que fluide
thermique dans les circuits de refroidissement, d'alimentation de
chaudière ou encore pour les dilutions de produits chimiques. Pour
qu'elles conviennent à leurs besoins, ces eaux doivent être
suffisamment traitées par différentes techniques souvent mises en
oeuvre successivement suivant l'eau de process voulue. Les industries
paramètrent l'eau recherchée par une ou plusieurs étapes
successives afin d'obtenir une eau traitée qui n'endommage pas leurs
installations lors de son passage. Ces traitements peuvent être
physiques, chimiques, physico-chimiques ou encore biologiques. L'eau de process
ainsi obtenue par ces traitements, sera utilisée pour des
systèmes tels que les eaux de refroidissement, les eaux de
nettoyage, les eaux de coupe, la composition de médicament, les bains de
graissage (www.ademe.fr).
Ceci nous amène à l'objectif principal de notre
travail qui consiste à faire une étude critique du système
de traitement de l'eau de chaudière du Complexe Industriel du Littoral.
À cet effet nous avions comme objectif spécifique :
· De faire un état des lieux ;
· D'effectuer un brainstorming sur les causes du
traitement insuffisant de l'eau de chaudière ;
· De proposer des actions correctives et ensuite
faire une analyse des coûts des actions proposées.
Afin d'atteindre ces objectifs nous avons
procédé de la manière suivante :
· Premièrement, nous avons fait une
présentation de l'entreprise d'accueil et une revue de la
littérature sur les types d'eaux, les chaudières et l'approche
adoptée pour la résolution du problème ;
· Deuxièmement, nous avons présenté
les matériels et méthode employés pour ce
travail ;
· Troisièmement, nous avons donné les
résultats et discussion ;
· Nous avons terminé par une conclusion de notre
travail, puis donné les recommandations et perspective.
CHAPITRE I : REVUE DE
LA LITERATURE
I.1. Ressources en eau
L'eau est essentielle à la survie et au bien-être
de l'homme et est indispensable au fonctionnement de nombreux secteurs de
l'économie. Les ressources en eau sont inégalement
réparties sur le globe terrestre comme illustré ci-dessous.
Tableau 2: Les
ressources en eau sur le globe terrestre (Eagleson, 1970)
Ressources
|
Millions de km3
|
% (Pourcentage)
|
Océans
|
1320
|
97,20
|
Neiges et glaces
|
30
|
2,15
|
Eaux souterraines à moins de 800 m
|
4
|
0,31
|
Eaux souterraines à plus de 800 m
|
4
|
0,31
|
Zone non saturée
|
0,07
|
0,005
|
Lacs en eau douce
|
0,12
|
0,009
|
Lacs en eau salée
|
0,10
|
0,008
|
Rivières
|
0,001
|
0,0001
|
Atmosphère
|
0,013
|
0,001
|
Il en ressort que le globe terrestre regorge 0,62% d'eau
souterraine.
I.2. Généralités sur les eaux du
forage
Un puits foré ou un forage est un ouvrage de captage
vertical permettant l'exploitation de l'eau d'une nappe souterraine contenue
dans les interstices ou dans les fissures d'une roche du sous-sol qu'on nomme
aquifère. L'eau du forage est remontée grâce à une
pompe motorisée. Un forage est caractérisé par sa
profondeur (jusqu'à 300 m de profondeur), son volume d'eau journalier
à collecter, son coût de réalisation et sa pureté
(justifiable ou non d'un traitement avant de pouvoir être
utilisée, et qu'il convient d'ailleurs de contrôler non seulement
à l'achèvement des ouvrages mais régulièrement)
(Desbordes, 2000).
Pour la construction d'un forage de bonne qualité, il
est essentiel de connaître :
- Si le sol forer est perméable ou imperméable.
Cet à dire, sa capacité à se laisser traverser par
l'eau ;
- La qualité de l'eau, cet à dire, ces
caractéristiques organoleptiques tels que la couleur, l'odeur ;
- Le débit du forage.
I.2.1. Caractéristiques
de l'eau des nappes souterraines (Eau du forage)
L'eau des nappes souterraines ou eau du forage est
généralement de meilleure qualité que l'eau de surface, en
raison du pouvoir épurateur des sols. Cette eau présente ainsi un
grand intérêt comme source d'approvisionnement en eau de
consommation, à usage ménager ou industriel.
L'eau du forage est caractérisée par :
(Gonthiez, 2009)
· Sa faible turbidité ;
· Sa faible salinité ;
· Sa faible teneur en minéraux tels que les nitrates,
nitrites... ;
· Une faible contamination en micro-organismes.
Toutefois bien que l'eau du forage se trouve sous la surface
du sol, elle reste vulnérable aux activités humaines. La
vulnérabilité se définit par la sensibilité de
l'aquifère à toute contamination provenant de la surface du
sol.
I.3.
Généralités sur les eaux de process
L'essor industriel est intimement lié à l'eau.
De tout temps, les usines se sont implantées pour de multiples raisons
à proximité de l'eau. De par ses propriétés
physico-chimiques, l'eau est impliquée dans de nombreux process
industriels. De plus, les cours d'eau représentent de réelles
opportunités de transport des matières premières ou encore
des produits finis.
L'eau de process industriel est l'eau utilisée dans les
installations industrielles pour le fonctionnement d'un procédé
ou la fabrication d'un produit. Elle est utilisée en majorité
pour approvisionner un process. Elle représente la plus grande
consommation d'eau sur les sites industriels. Elle est
généralement utilisée dans les chaudières, les
circuits de refroidissement, les dilutions des produits chimiques, le process
ou dans le produit lui-même.
La qualité et la quantité d'eau de process
industriel peuvent être variables d'une industrie à une autre, ce
choix se fait selon les exigences de l'entreprise (O'Dowd, 2000).
I.4. Quelques indicateurs de la
qualité des eaux
I.4.1. Dureté
§ Titre hydrotimétrique (TH)
L'expression `dureté de l'eau' est issue du langage
populaire et caractérise la difficulté rencontrée lors de
la lessive : les eaux nécessitant beaucoup de savon pour obtenir de
la mousse sont réputées dures. En fait, la dureté d'une
eau correspond à sa teneur en sel de calcium, magnésium et de
métaux qui forment avec le savon des composés insolubles dans
l'eau.
La dureté d'une eau est mesurée par son titre
hydrotimétrique (TH), et est exprimée en degré
français (°f).
I.4.2. Alcalinité
L'alcalinité d'une substance caractérise la
possibilité qu'a cette substance de libérer des ions hydroxydes
(OH-) et de rendre basique une solution.
Dans l'eau les substances alcalines sont au nombre de
trois :
- Les hydroxydes métalliques tels que
la soude (NaOH) (ou la potasse (KOH)), qui se dissocient dans l'eau en ions
Na+ (ou K+) et OH- ;
- Les carbonates (comme le carbonate de
sodium (Na2CO3)), qui se décomposent à
haute température en libérant des ions OH- :
Na2CO3(s) + H2O(l)
2NaOH(aq) + CO2(g)
Cette décomposition est totale à partir de 250
°C, ce qui correspond à la température de l'eau dans une
chaudière de 20 bars environ ;
- Les bicarbonates (ou
hydrogénocarbonates) comme le bicarbonate de sodium
(NaHCO3), qui se décompose à température
modérée (dès 100 °C la décomposition est
totale) en carbonate selon la réaction :
2NaHCO3(s)
Na2CO3(s) + CO2(g) +
H2O(l)
§ Titres alcalimétriques
La mesure de l'alcalinité des eaux s'effectue par
dosage par l'acide sulfurique des substances alcalines dissoutes dans l'eau.
On distingue deux (02) mesures de l'alcalinité de l'eau
selon la valeur du pH en fin d'addition d'acide :
- Titre Alcalimétrique Complet (TAC)
Le Titre Alcalimétrique Complet (TAC) est la grandeur
utilisée pour mesurer le taux d'hydroxydes, de carbonates et de
bicarbonates d'une eau,
son unité est le degré français (°f), en millimole de
CaCO3 par kg d'eau ou milligramme de CaCO3 par kg
d'eau.
Ainsi la quantité d'acide ajouté lors de
l'analyse a permis de neutraliser les hydroxydes, les carbonates, et les
bicarbonates, éventuellement présents.
Ces trois produits alcalins ne peuvent exister tous
simultanément. En effet les bicarbonates sont transformés en
carbonates par les hydroxydes. C'est le cas du bicarbonate de sodium en
présence de soude :
NaHCO3(s) + NaOH(aq)
Na2CO3(s) + H2O(l)
- Titre Alcalimétrique (TA)
Il permet de connaître les teneurs de l'eau en
carbonates et
bases fortes
présentes dans l'eau. Cette analyse se fait en présence de
phénolphtaléine
qui vire de l'incolore au rose-fuchsia à un
pH de 8,2.
Le Titre alcalimétrique s'exprime en degré français
(°f), en millimole de CaCO3 par kg d'eau ou milligramme de
CaCO3 par kg d'eau.
La quantité d'acide ajoutée permet de
neutraliser les hydroxydes et de transformer les carbonates en bicarbonates.
I.4.3. Salinité totale -
Conductivité et Résistivité
La salinité totale d'une solution peut être
évaluée par pesée de l'extrait sec après
ébullition totale de l'eau liquide. La méthode opératoire
étant délicate, le plus souvent cette salinité est
appréciée indirectement par la mesure de la conductivité
ou de la résistivité électrique de la solution, chacune de
ces mesures évoluant significativement chaque fois que la
salinité évolue.
La conductivité d'une solution est mesurée par
la conductance électrique d'une colonne d'eau de 1 cm de hauteur
comprise entre deux (02) électrodes de section de 1 cm². Elle
s'exprime le plus souvent en microsiemens par cm (uS/ cm).
La résistivité est l'inverse de la
conductivité. Les unités les plus souvent employées sont
le kilohm cm (kÙ.cm) ou le mégohm cm (MÙ.cm).
On passe facilement de la conductivité à la
résistivité par la relation :
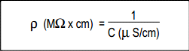
I.4.4. Teneur en fer
Le fer est le deuxième plus abondant métal de la
croute terrestre, d'une hauteur d'environ 5%. L'élément chimique
fer est présent sous forme ionique avec deux valences
principales que sont le fer ferreux (Fe2+) et le fer ferrique
(Fe3+). Le fer ferreux est présent dans les eaux
souterraines sous formes de soluble sulfatées (FeSO4) ou
carbonatées (FeCO3 ou Fe(HCO3)2). Il
(Fe2+) est instable et se précipite, par simple
aération dans l'eau, en hydroxyde de fer (III) (Fe(OH)3), qui
est peu soluble. Cette oxydation (optimal à pH = 7,2) est due à
une augmentation d'oxygène, de la température, et une diminution
de la pression de l'eau. Cependant la réaction est lente surtout si le
pH est faible, et que le milieu n'est pas saturé en oxygène
(Chibi C., 1991). Ceci est interprété par la réaction
suivante :
4Fe2+(aq) + O2(g) +
8OH-(aq) + 2H2O(l)
4Fe(OH)3(aq)
Généralement les eaux de surface et de la nappe
phréatique ont une teneur en fer ne dépassant pas 1 mg/l (Fe = 1
ppm). Toutefois des hautes teneurs en fer (Fe = 10 mg/l), dues au drainage
minier et/ou industriel, sont observées dans les eaux souterraines.
Une teneur élevée en fer dans l'eau de process,
entraine la corrosion des installations métalliques (surtout en aciers
ordinaires) d'une entreprise, notamment les chaudières et tuyauteries
(WEDECO, 2003).
I.4.4.1. Déferrisation de l'eau du
forage
La déferrisation est le fait d'enlever le fer,
spécialement de l'eau. Une teneur élevée en fer
présente des effets gênants sur les installations du Complexe
Industriel du Littoral que sont :
§ La corrosion dans les canalisations métalliques
avec libération du métal ;
§ Distribution d'eau de couleur rouille, au robinet qui
tâche les installations de plomberie ;
§ Inconvénients d'ordre
organoleptique
(trouble colloïdal, coloration jaune orangé) ;
§ Colmatage des ouvrages d'exploitation par
précipitation en présence d'oxygène, entrainant la
réduction progressive des débits de conduite (formation de
dépôts).
Il existe de nombreuses techniques de traitement pour
l'élimination du fer de l'eau. Ces techniques sont :
o Oxydation puis
filtration
La déferrisation par
oxydation (à l'air
ou autre oxydant suivant la concentration en Fer), suivie d'une filtration, est
généralement utilisée pour les eaux d'origine profonde.
C'est une technique simple mais qui nécessite souvent l'emploi de
réactif oxydant tels que le permanganate de potassium
(KMnO4),
l'oxygène,
l'hypochlorite de calcium ou sodium (eau de javel), et l'
ozone.
Le traitement par oxydation avec des composés
chlorés tels que l'eau de javel, et le permanganate de potassium
présente l'inconvénient d'avoir un pouvoir rémanent lors
du traitement. Cette rémanence porte préjudice à la
chaudière. Ces méthodes de traitement sont le plus
utilisées dans le cas de l'épuration de l'eau de consommation,
cependant l'eau que nous désirons traiter est une eau de
chaudière.
o Traitement
biologique
L'élimination du fer peut être aussi faite par
oxydation biologique (utilisation de ferrobactéries qui oxydent et
précipitent le fer dissous). Les ferrobactéries
catalysent par production d'enzymes spécifiques des réactions
exothermiques d'oxydation qui alimentent leur métabolisme grâce
à l'énergie libérée.
2FeO(s) + 1/2O2(g) +
3H2O(l)
2Fe(OH)3(s) + 1057 Joules
Cependant cette méthode de traitement est difficile et
demande en particulier des délais d'ensemencement, des
ferrobactéries, beaucoup plus longs (de l'ordre du mois).
o Traitement catalytique
Le procédé d'élimination
catalytique du fer repose
sur un phénomène d'
adsorption et d'
oxydation des formes
dissoutes du fer ferreux (Fe2+), à la surface d'un
matériau spécifique de filtration. Ces matériaux
catalytiques jouent à la fois le rôle d'adsorbant et
d'échangeur d'électrons. Les matériaux utilisables (tels
que la zéolite, le quartz, et la latérite) pour la filtration
catalytique sont des matériaux recouverts de façon naturelle ou
artificielle par le dioxyde de manganèse (MnO2). Le dioxyde
de manganèse joue le rôle d'échangeur d'électron
dans la catalyse). Au contact avec la surface de ces matériaux, le fer
ferreux est adsorbé et forme une sorte de filme gluant et aqueux autour
du matériau. Ce type de méthode n'est utilisable que pour des
eaux de forage ayant des faibles teneurs en fer.
2Fe2+(aq) + 2MnO2(s) +
H2O(l)
2Fe3+(aq) + Mn2O3(s) +
2OH-(aq)
I.4.5. Teneur en chlorures
Les chlorures inorganiques font parties des anions les plus
souvent rencontrés dans les eaux de forage. Elles sont localement
impliquées dans les
pluies acides et
phénomènes d'
acidification
d'eaux superficielles ou souterraines. En industrie, la concentration des
chlorures doit être surveillée car elle peut entrainer
l'entartrage et la corrosion des installations (Jolley et al, 1990).
Les filtres à cartouche de charbon actif sont
utilisés pour la dé-chloration de l'eau en industrie.
* Caractéristiques physicochimiques des eaux au
Complexe Industriel du Littoral
Les caractéristiques physicochimiques des eaux de
l'entreprise sont illustrées dans le tableau
ci-après. Les valeurs des consignes pour chaque paramètre sont
entre parenthèses (NORME NF EN ISO 32-020-1). Les
paramètres requis pour les eaux de chaudières sont
exprimées pour une pression de service, de la chaudière, de 20
bars (P = 20 bars). D'après le tableau, nous constatons que la teneur en
fer et en chlorures des eaux, ne respecte pas la norme. Tous ces
paramètres analysés ne varient pas beaucoup en
général.
Tableau 3:
Qualité des eaux du Complexe Industriel du Littoral
Paramètres Analysés
|
Eau du forage
|
Eau Adoucie
(ou D'appoint)
|
Eau de la Bâche
|
Eau de la Chaudière
|
Aspect
|
Trouble(Limpide)
|
Trouble(Limpide)
|
Trouble(Limpide)
|
Leger trouble (Limpide)
|
Turbidité (NTU)
|
7,2 (=5)
|
8,1 (=5)
|
8,4 (=5)
|
5,6 (=5)
|
Température (°C)
|
26,6 (=25)
|
26,2
|
26,3
|
95,5
|
pH
|
2,7 (7,5-8,5)
|
6,9 (6,5-7,5)
|
7,6 (7,5-9,5)
|
11,6 (10,5-12)
|
Salinité (mg/l)
|
290 (0,0)
|
290 (<25)
|
310 (<80)
|
1360 (<2500)
|
Conductivité (uS/ cm)
|
649,3 (<50)
|
190,7 (<50)
|
104,3 (<150)
|
2732,3 (<5000)
|
TH (°f)
|
16 (0,0)
|
12,8 (0,0)
|
4,8 (<10)
|
1,02 (<5)
|
TA (°f)
|
13,4 (10)
|
16,2 (10)
|
10,2 (<0,7*TAC)
|
10,4 (<0,7*TAC)
|
TAC (°f)
|
23,2 (15-50)
|
24,8 (<40)
|
20,8 (<40)
|
107,1 (80-120)
|
SiO2 (mg/l)
|
30 (<5)
|
29 (<5)
|
26 (<5)
|
24 (<200)
|
SO3 2- (mg/l)
|
15,3 (<10)
|
6,8 (<10)
|
6,8 (<10)
|
16 (10-50)
|
PO43- (mg/l)
|
0 (0,0)
|
0 (0,0)
|
11,7 (<15)
|
11,7 (25-50)
|
Fe2+ (mg/l)
|
2,7 (<0,05)
|
3 (<0 ,05)
|
3,5 (<1)
|
4,5 (<1)
|
Cl- (mg/l)
|
28,4 (<5)
|
28,4 (<5)
|
30,1 (<150)
|
274,8 (<800)
|
N.B : Valeurs des consignes entre
parenthèses (NORME NF EN ISO 32-020-1)
Les moyens disponibles pour maintenir la qualité de
l'eau dans les limites autorisées reposent sur :
- Le traitement externe de l'eau du forage et l'eau d'appoint
avant son admission à la chaudière pour réduire ou
éliminer les impuretés (sels dissous, oxygène), qu'elle
introduit en chaudière ;
- Le traitement interne de l'eau de chaudière par des
produits chimiques de conditionnement ;
- L'élimination des impuretés présentent
en chaudière par des purges de déconcentration.
I.5.
Généralités sur les chaudières
Dans son acception moderne, une chaudière
désigne un appareil (voire une installation industrielle, selon sa
puissance) permettant de transférer en continu de l'
énergie
thermique à un
fluide caloporteur
(le plus généralement de l'
eau). L'énergie thermique
transférée (source de chaleur) peut être soit la chaleur
dégagée par la
combustion (de
charbon, de
fioul, de
gaz, de
bois, de
déchets,
...), soit la chaleur contenue dans un autre fluide (chaudière de
récupération sur gaz de combustion ou gaz de
procédés chimiques, chaudière « nucléaire
» recevant la chaleur du circuit primaire, etc.), soit encore d'autres
sources de chaleur (chaudières
électriques,
par exemple). Les chaudières sont aussi bien des systèmes
industriels que domestiques. À l'intérieur de la
chaudière, ce fluide caloporteur peut être soit uniquement
chauffé (c'est-à-dire qu'il reste en phase liquide), soit
chauffé et vaporisé, soit chauffé, vaporisé puis
surchauffé (donc avec passage de phase liquide à phase
gazeuse).
On distingue les chaudières selon leurs combustibles
(chaudières à combustibles liquides ou gazeux et
chaudières à combustibles solides) et selon leurs constructions
(chaudières à tubes de fumées et chaudières
à tubes d'eaux).
La chaufferie est le bâtiment où sont
rassemblées les chaudières dans une entreprise. Il est
nécessaire qu'elle soit alimentée en eau, en combustible, en
électricité, bref tout ce qui est nécessaire à la
production de la vapeur. Elle est la chambre de chauffe d'une usine et est
chargée de produire et de canaliser la vapeur d'eau. Dans le cas d'une
savonnerie cette vapeur est utilisée surtout pour le nettoyage des
circuits (aquap.fr).
I.5.1. Historique des
chaudières
C'est au 1er siècle après J.C.
qu'apparut pour la première fois l'idée d'utiliser
l'énergie de la vapeur à des fins motrices, dans l'ouvrage
intitulé Pneumatica de l'inventeur et mathématicien grec
Héron d'Alexandrie. Il y décrivit un éolipyle, une turbine
à vapeur se composant d'une chaudière connectée par deux
tubes creux aux pôles d'une sphère creuse tournant librement. La
première amélioration importante apportée à la
chaudière fut la chaudière « Lancashire » à tube
de fumée brevetée en 1845 par l'ingénieur britannique sir
William Fairborn. Les chaudières à tubes de fumée avaient
cependant une capacité et une pression limitées et
présentaient parfois des risques d'explosion (www.wikipedia.org).
La première chaudière à tubes d'eau,
brevetée en 1867 par les inventeurs américains George Herman
Babcock et Stephen Wilcox, autorisa une pression supérieure à
celle de la chaudière à tube de fumée. Les
chaudières à tubes d'eau modernes peuvent fonctionner à de
très hautes pressions et produisent plus de quatre mille cinq cents
tonnes de vapeur par heure (
Technique
de chauffage : erdgas.lu).
I.5.2. Présentation de
la chaudière du Complexe Industriel du Littoral
La chaufferie de l'entreprise est constituée
principalement d'une chaudière, d'une tuyauterie de vapeur, d'une
tuyauterie d'alimentation d'eau, d'une pompe alimentaire en eau et d'une
bâche d'alimentation. La chaudière du Complexe Industriel du
Littoral est un élément incontournable dans la mesure où
la vapeur et l'eau chaude qu'elle va générer participe
directement au processus de fabrication du savon. C'est une chaudière
à fuel et à tube de fumées. La vapeur est utilisée
pour le blanchiment de l'huile de palme, à la saponification, au
nettoyage des circuits après chaque transfert, et au séchage du
savon dans la boudineuse.
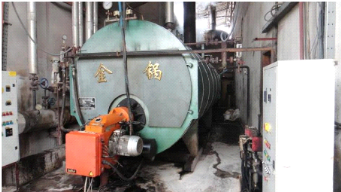
Figure 2: Vue de
face de la chaudière du Complexe Industriel du Littoral
Elle est la deuxième chaudière de l'entreprise
et la seule en activité, la première étant en panne ; et
se présente sous la forme d'un corps fermé et renferme les
éléments suivants :
- Un tube foyer, il est légèrement
excentré de l'axe de la chaudière (vers le bas) et constitue les
parcours des fumées ;
- Des tubes échangeurs disposés ;
- D'un brûleur à pulvérisation
mécanique par gicleur ;
- Des organes de régulation et de
sécurité ;
- D'une cheminée.
Les caractéristiques de la chaudière du Complexe
Industriel du Littoral sont présentées comme suit :
o Type : MBA-S-5000 ;
o N° de série : 5651 ;
o Timbre : 14 bars ;
o Température Maximale : 184 °C ;
o Surface de chauffe : 86 m2 ;
o Année de construction : 2003 ;
o Production de vapeur : 2920 kg/h ;
o Pression de service : 20 bars ;
o Marque du brûleur : Baltur ;
o Combustible : fuel 1500.
I.5.2.1. Principe de fonctionnement de la
chaudière
Le fuel contenu dans la bâche de stockage est
acheminé vers le réchauffeur pour réduire sa
viscosité et facilité l'allumage (75 °C - 110 °C) par
une pompe. Avant son entrée dans le réchauffeur, le fuel est
filtré pour éliminer les particules solides qui pourraient
obstruer les injecteurs, et ensuite filtré de nouveau par un filtre plus
fin à l'entrée du bruleur. La flamme est produite par un
mélange air/gaz qui est enflammé par une étincelle
produite par un allumeur. Une fois ce mélange enflammé, le
brûleur laisse passer le fuel déjà chaud, qui continu
à s'enflammé avec de l'air.
Cette combustion produit la chaleur nécessaire pour
transformer l'eau en vapeur. L'eau à vaporiser est à
l'extérieur des tubes, tandis que la fumée qui transporte la
chaleur (due à la combustion) est à l'intérieur des tubes.
Cette chaleur est dissipée par convection et conduction,
réchauffant ainsi l'eau dans laquelle les tubes sont plongés. Les
fumées sont expulsées à l'extérieure via la
cheminée et la vapeur produite est acheminée en utilisation via
les conduites.
I.5.2.2. Circulation de l'eau dans la
chaudière
La chaudière reçoit de l'eau provenant de la
bâche, qui est de l'eau adoucie, après avoir directement
été tirée du réseau d'eau de la
société.
Les impuretés contenues dans l'eau d'alimentation
peuvent par leur nature ou par leur concentration perturber son fonctionnement
et cela dû aux dépôts sur les tubes vaporisateurs ou la
mauvaise séparation de l'eau dans la vapeur. Ce disfonctionnement de la
chaudière implique le respect des consignes du constructeur ou à
défaut du respect des normes de traitement des eaux de
chaudières.
Ces impuretés contenues dans l'eau de la
chaudière proviennent des sels dissous (calcium, sodium, sulfates), des
gaz dissous (oxygène et dioxyde de carbone) contenus dans les eaux ainsi
que des matières en suspension (sable, boue, matière organique).
Par conséquent, pour respecter les limites imposées par le
constructeur ou les normes, les moyens suivants ont été mis en
place :
- Les purges de déconcentration ;
- Les purges d'extraction de fond ;
- Le détartrage général du
générateur.
Notons que seules les purges d'extraction de fond sont
réalisées régulièrement. Le cycle parcouru par
l'eau à travers sa transformation est schématisé comme
suit :
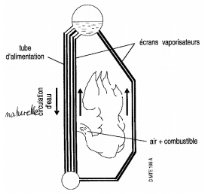
FIGURE 3:
SCHÉMA INDIQUANT LA CIRCULATION DE L'EAU DANS LA CHAUDIÈRE
I.6.
Généralités sur la méthodologie appliquée
I.6.1. Méthode DMAIC ou
Six Sigma
Les bases de cette approche DMAIC, ont été
posées par un ingénieur de Motorola, nommé Mikel Harry en
1986, mais la méthode devient célèbre dans les
années
1990 lorsque
General Electric
décide de l'appliquer et de l'améliorer. L'approche six sigma
repose sur la maîtrise statistique des procédés.
C'est une approche globale de l'amélioration continue de la
qualité du produit et des services rendus aux clients (Lopez, Redchuk,
Moguerza, 2011).
L'approche se décline de plusieurs façons. En
effet, six sigma c'est :
o Une philosophie de la qualité pour satisfaire
totalement le client ;
o Un indicateur de performance permettant de connaître
la situation de l'entreprise en matière de qualité ;
o Une méthode de résolution de problème
permettant de réduire la variabilité des produits ;
o Une organisation des compétences et des
responsabilités des hommes de l'entreprise ;
o Un mode de management de la qualité s'appuyant
fortement sur une gestion des projets.
Cette méthode utilise la norme ISO
9000:2000 comme référentiel. En effet l'ISO 9000:2000
est utilisé pour la réalisation des systèmes de
gestion de la qualité. Elle est orientée vers la
réalisation des objectifs de l'entreprise, y compris la satisfaction des
clients. D'où l'importance de l'amélioration continue pour
aller vers le management de la qualité totale.
I.6.2. Principe de la
méthode
La méthode suit le processus suivant : (Thomas Roth,
2011)
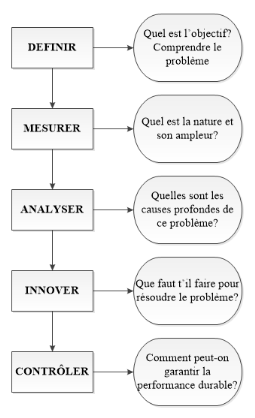
FIGURE 4 : SCHEMA DE LA
METHODOLOGIE
CHAPITRE II : MATERIEL
ET METHODES
II.1 MATERIEL
Afin de mener à bien ce travail les matériels
suivants ont été utilisés :
o Turbidimètre de marque HI88703, pour mesurer la
turbidité de l'eau ;
o Conductimètre de marque HI63041, pour mesurer la
conductivité de l'eau ;
o Kit d'analyse chimique du fer de marque HI3834, pour
déterminer la teneur en fer de l'eau ;
o Kit d'analyse chimique des chlorures de marque HI3815, pour
déterminer la teneur en chlorure de l'eau ;
o Thermomètre de marque ZOLUX, pour mesurer la
température de l'eau.
o Glacières de marque ICETIME, pour le transport des
échantillons ;
o Papier pH de marque DF UNIVERSAL, pour mesurer le pH de
l'eau ;
Les logiciels suivants ont également été
utilisés :
o ChemOffice 8.0 pour la réalisation des structures
chimiques ;
o Microsoft visio 2010 pour la réalisation des
schémas synoptiques ;
II.2. METHODES
La démarche DMAIC, qui est une démarche
structurée en cinq étapes a permis de faire une évaluation
des différents problèmes rencontrés lors de la prise en
charge et de la mise en service de la chaudière par l'entreprise, afin
de proposer des améliorations aux processus impliqués et de faire
une évaluation des coûts des améliorations
proposées. C'est ainsi que le schéma synoptique du travail
effectué s'articule comme suit :
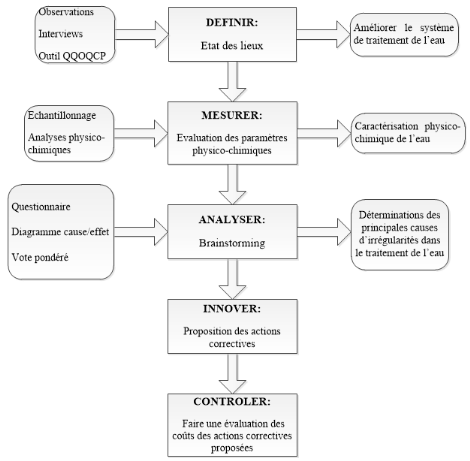
FIGURE 5:
SCHÉMA SYNOPTIQUE DU TRAVAIL EFFECTUÉ
II.2.1. Etat des lieux
Cette première étape a permis de définir
le problème afin de mieux le comprendre. Ceci s'est fait par le biais
d'un état des lieux qui avait pour but:
§ De présenter les installations de traitement de
l'eau et le traitement existant ;
§ D'identifier les problèmes
rencontrés lors du traitement existant ;
§ De décrire le problème principal à
l'aide de l'outil QQOQCP.
Cela consiste à répondre aux questions suivantes
:
- Qui : qui est concerné par le problème ?
- Quoi : quel est le problème ?
- Où : en quel lieu se pose-t-il ?
- Quand : à quel moment apparait-t-il ?
- Comment : comment a-t-il été
détecté ?
- Pourquoi : quelles sont les raisons qui poussent à
résoudre ce problème ?
Ces questions répondues, les prochaines étapes
étaient de prélever l'eau du forage, d'évaluer ces
paramètres physico-chimiques, proposer les actions correctives
appropriées et enfin évaluer les coûts.
II.2.2. Caractérisation
physicochimique de l'eau du forage
Ici, les paramètres physico-chimiques de l'eau du
forage prélevée ont été évalués.
II.2.2.1. Prélèvements des
eaux
Les prélèvements de l'eau du forage ont
été faits in situ, dans trois bouteilles PET d'un litre chacun
(Poly Téréphtalate d'Ethylène), tout en évitant la
pénétration de l'air. Avant son remplissage, la bouteille a
été plusieurs fois rincée avec l'eau à analyser
puis étiquetée.
Le transport des échantillons du point de
prélèvement jusqu'au laboratoire se fait dans une
glacière.
II.2.2.1.1. Paramètres
physico-chimiques
Les paramètres évalués sont : le pH,
la température, la turbidité, la teneur en fer, la teneur en
chlorure, et la conductivité. Les modes opératoires des
paramètres analysés sont présentés en annexe 13.
Le pH
Sa mesure repose sur l'activité chimique des ions
hydrogènes (H+) dans l'eau.
La température
Sa mesure repose sur la sensation de froid et de chaud,
provenant du
transfert
thermique entre l'eau et son environnement.
La turbidité
Sa mesure repose sur la capacité que l'eau a à
disperser et absorber la lumière. La dispersion de la lumière qui
passe à travers un liquide est principalement due aux matières
solides en suspension présentes. Plus il y a de matières en
suspension dans l'eau, plus la turbidité est élevée et
vice-versa.
La conductivité
Sa mesure repose sur l'aptitude qu'a l'eau à laisser
les
charges
électriques se déplacer librement, donc à permettre le
passage d'un
courant
électrique.
La teneur en fer
La mesure est basée sur une méthode
colorimétrique. Tout d'abord, les ions ferriques (Fe3+) sont
réduits par le sulfite de sodium (Na2SO3), en ions
ferreux (Fe2+). Ensuite les ions ferreux (Fe2+) forment
un complexe stable avec l'ortho-phénantroline, de couleur orange.
L'intensité de la couleur détermine la teneur en fer dans l'eau.
Ceci peut être interpréter par les équations
suivantes :
2Fe(OH)3(aq) + Na2SO3(s)
2Fe2+(aq) +
4OH-(aq) + Na2SO4(s) +
H2O(aq)
Fe2+(aq) + 3 (aq) 3 Fe2+(aq)
Ortho-phénantroline Complexe orange
La teneur en chlorure
La mesure de la teneur est basée sur le dosage par le
nitrate de mercure. Le pH du milieu est abaissé par ajout de l'acide
nitrique (HNO3). Les ions mercureux (Hg+)
réagissent avec les ions chlorures pour formés le chlorure de
mercure (II), dont la couleur est jaune. Lorsque les ions mercuriques sont
présents en excès, ils forment un complexe avec le
diphénylcarbazone, qui se traduit par une solution de couleur pourpre.
Cette couleur marque le point d'équivalence du dosage. Cela est
présenté par les réactions suivantes:
HgNO3(aq) + 2H+(aq) +
2Cl-(aq) HgCl2(aq) +
NO2(g) + H2O(l)
Hg2+(aq) + (aq) Hg2+(aq)
Diphénylcarbazone
Diphénylcarbazone mercure (II)
II.2.3. Brainstorming
Il est question ici d'identifié les causes
d'irrégularités dans le traitement de l'eau. L'identification des
causes s'est faite selon la procédure suivante :
i. Le questionnaire
Les causes qui engendrent le traitement insuffisant de l'eau
du forage ont été mises en évidence par la méthode
des 5M, obtenue par un questionnaire à sept questions à
réponses ouvertes (Voir annexe 7). La phase du questionnaire a
été faite en présence du directeur technique, le
responsable de maintenance, le responsable de production, le contre maitre, et
les chefs des équipes (de chaque quart) A, B, C.
ii. Classification et hiérarchisation des
causes
La classification des causes a été faite par la
méthode des 5M : Matière, Matériel, Méthodes,
Milieu, Main d'oeuvre. Les résultats ont été
représentés par le diagramme d'Ishikawa, encore appelé
diagramme causes-effet.
La construction de ce diagramme se fait en plusieurs
étapes :
· Etape 1: Qualifier l'effet : cela consiste
à définir clairement le problème que l'on cherche à
résoudre ;
· Etape 2: Dresser un inventaire des causes
possibles : lister celles qui ont une influence sur le
problème ;
· Etape 3: Classer les causes par familles ;
· Etape 4: Construire le diagramme ;
· Etape 5: Evaluer les branches qui ont le plus
d'impact.
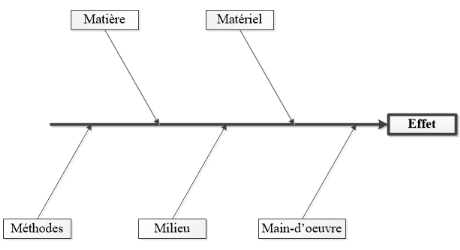
FIGURE 6 :
VUE GÉNÉRALE D'UN DIAGRAMME D'ISHIKAWA
À partir des causes identifiées du
questionnaire, un vote pondéré a été faite afin
d'identifier les causes majeures du problème. Ce vote a
été fait toujours en présence des mêmes personnes ou
individus que lors de la phase du questionnaire et les critères pour le
vote ont été :
§ 1 = pour la cause ayant peu
d'influence sur le traitement insuffisant de l'eau ;
§ 2 = pour la cause ayant une influence
sur le traitement insuffisant de l'eau ;
§ 3 = pour la cause ayant une
très grande influence sur le traitement insuffisant de l'eau.
Le vote terminé, les points attribués à
chaque cause par tous les membres ont été additionnés et
les résultats ont été présentés sous forme
de tableau en plaçant les causes par ordre d'influence
décroissante.
Par la suite, le diagramme de Pareto permet de mettre en
évidence, les éléments (effets et modes de
défaillance) les plus importants du problème sur lesquels devront
être concentrés en priorité les efforts
d'amélioration (actions correctives). Cette analyse est également
connue sous le nom de loi des 80/20 qui postule que, 80% des effets sont
imputables à seulement 20% de causes.
Après l'évaluation des principales causes
d'anomalies, on procède à une évaluation des actions
nécessaires pour remédier aux problèmes.
II.2.4. Propositions des
actions correctives
Il s'agit de présenter les actions correctives qui vont
aboutir à un traitement efficace de l'eau du forage. Un tableau
comparatif des solutions proposées est également
présenté.
II.2.5. Evaluation des
coûts
Il est question de faire une évaluation des coûts
des solutions proposées, cet à dire, les couts de mise en place
du projet et les charges annuelles.
CHAPITRE III: RESULTATS ET
DISCUSSION
III.1. ETAT DES LIEUX
III.1.1. Station de
traitement
La station de traitement d'eau du Complexe Industriel du
Littoral, est constituée de trois postes : un poste de captage,
deux postes de traitement, et un poste de relevage.
Ø Le poste de captage
L'eau utilisée par le Complexe Industriel du Littoral,
est captée dans un puits ayant une profondeur d'environ 100 m, par une
pompe centrifuge, pour un débit de 10 m3/h. L'eau
captée est introduite dans un bac ayant pour dimensions 4,5
m de longueur, 2 m de largueur et 2,5
m de hauteur. Le volume d'eau introduit est 18 m3.
Ø Les postes de traitements
· Poste de traitement 1
Les étapes de coagulation-floculation,
décantation et filtration sur sable, sont effectuées dans ce
poste.
Dans l'étape de coagulation-floculation, 25 kg de
sulfate d'alumine hydraté (coagulant) suivi de 9 kg de soude (36% de la
dose de sulfate d'alumine), sont introduits dans un mini-bac (diamètre =
75 cm et hauteur = 80 cm) contenant 310 L d'eau puis agiter par un agitateur
motoriser (de marque MILTON ROY), à une vitesse de 1340 tours/ min
pendant 40 minutes environ. En même temps 25 kg de soude sont introduite
dans un premier bac de décantation afin de hausser le pH de l'eau, vu
qu'elle est très basse (entre 2-3). Après la préparation
de la solution de coagulant, le robinet de ce mini-bac est ouvert pour laisser
la solution couler dans ce premier bac de décantation. Ceci afin de
permettre la formation des flocs qui vont éventuellement ce
décanté dans le bac. Il n'y a pas introduction du floculant lors
du traitement.
Le bac de décantation est relié à un
deuxième bac de récupération, ce qui va permettre à
l'eau de s'introduire dans ce dernier afin qu'une étape
supplémentaire de décantation puisse avoir lieu. Ce bac de
récupération est équipé d'un flotteur, qui à
son tour est connecté à une autre pompe. Lorsque l'eau a atteint
un certain niveau dans le bac, le flotteur enclenchera la pompe (débit =
8 m3/h) qui à son tour enverra l'eau dans un filtre,
composé de gravier et sables fins, pour la filtration de cet eau. Cette
filtration enclenchera une autre pompe, qui est connectée entre le
filtre et la cuve de stockage d'eau, qui conduira l'eau dans ce dernier.
· Poste de traitement 2
Ce poste est concerné par le fonctionnement des
résines échangeuses d'ions et le détartrant qui est
ajouté à la bâche.
L'eau qui est dans la cuve de stockage est envoyée dans
les résines échangeuses d'ions par ouverture de la vanne. Ces
résines échangeuses d'ions (qui sont au nombre de 2 à CIL)
ont pour rôle d'adoucir ou réduire la
dureté de
l'eau en réduisant la quantité de calcaire (carbonates
principalement de calcium et de magnésium) en suspension dans l'eau. Ces
résines échangeuses d'ions sont reliées à un bac de
saumure de 200 L, qui contient une solution saturée de sel (NaCl). Leurs
fonctionnements sont effectués grâce aux résines sur
lesquelles sont fixés des
ions
sodium (Na+). Les
ions
calcium (Ca2+) et
magnésium (Mg2+) de l'
eau dure sont
échangés lors de leur passage sur les résines par des ions
sodium (Na+). Lorsque tous les ions sodium (Na+) des
résines sont consommés, il faut régénérer
les échangeuses d'ions. On lui apporte alors une solution saturée
en sel (
chlorure de
sodium,
NaCl) riche en ions sodium
(Na+). De leur côté, les ions calcium (Ca2+)
et magnésium (Mg2+) sont évacués dans les
canalisations avec les eaux de rinçage. Ces échangeuses d'ions
sont munies d'un régulateur de dureté, qui va permettre le bon
rééquilibrage de la dureté.
Le détartrant (W588) est introduit dans la bâche,
contenant de l'eau, afin d'enlever le
tartre qui s'est
accumulé dans celle-ci. La quantité de détartrant
introduit est 1 kg. Le détartrant introduit, a également pour
rôle d'effectuer une diminution supplémentaire de la dureté
de l'eau, pour qu'elle ne soit pas nocive pour la chaudière.
Ø Poste de relevage
La cuve de stockage d'eau est équipée d'un
flotteur, afin de connaitre le niveau d'eau dans celle-ci. Lorsque l'eau
envoyée jusqu'aux résines échangeuses d'ions atteint un
certain niveau dans la cuve, la pompe de captage d'eau est actionner afin de
démarrer le cycle de traitement d'eau.
Il faut noter que le traitement de l'eau du forage est
effectué à peu près tous les samedis, afin d'utiliser
cette eau en semaine. Les caractéristiques des pompes, l'agitateur
motorisé et les résines échangeuses d'ions,
utilisés dans la station de traitement d'eau du forage, sont
présentées en annexe 8.
Le schéma présentant la station de traitement
d'eau du forage du Complexe Industriel du Littoral, est
présenté ci-dessous :
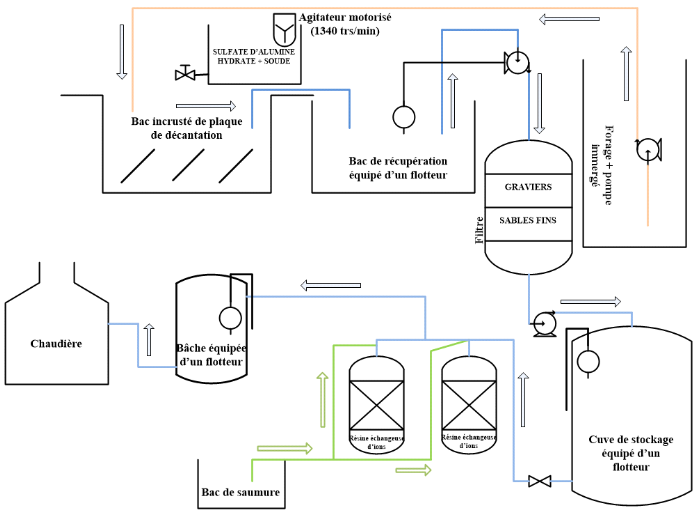
Figure 7:
Présentation de la station de traitement d'eau du forage du
Complexe Industriel du Littoral
III.1.2. Procédé
de traitement
Le schéma block du procédé de traitement
d'eau du forage du Complexe Industriel du Littoral, avec les différents
postes de la station, est présenté ci-dessous :
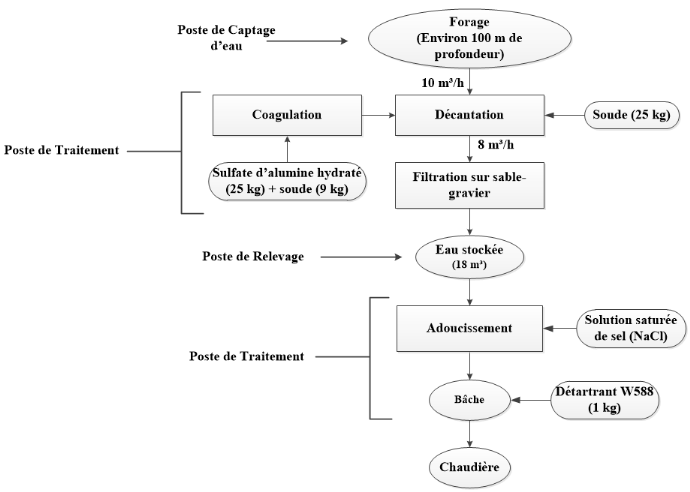
Figure 8:
Schéma block du traitement existant de l'eau du forage du
Complexe Industriel du Littoral
* Etude critique des opérations unitaires
impliquées dans le traitement de l'eau du forage
Coagulation : Il est question ici de
déterminé la concentration critique du coagulant (sulfate
d'alumine hydraté) utilisé dans l'étape de coagulation. 25
kg du coagulant sont introduits dans 310 L d'eau, puis agiter pendant 40
minutes. Puis la solution de coagulant est versée dans 18 m3
d'eau du forage captée. La concentration critique du coagulant (CCC)
nécessaire pour le traitement de l'eau du forage est,
Concentration Critique du Coagulant = 25000/
(18000 + 310) = 1,37 g/l
Décantation : Le bac de
décantation comporte des plaques (10 plaques) disposées
parallèlement, afin d'augmenter la surface de décantation. Les
plaques sont disposées de manière oblique de sorte à
permettre le glissement des matières colloïdales vers le fond du
bassin. Les matières colloïdales qui se déposent sur les
plaques, inclinées d'un angle de 60°, glissent le long de celles-ci
et sont évacuées en partie basse du bac. La distance entre les
plaques est 85 cm pour une longueur de plaque qui est 90 cm et largeur 75 cm.
Ce système reste le plus utilisé (Jean Pierre BECHAC et al,
1984). Le temps de décantation est 68 minutes et la distance de chute
est 174 cm. La vitesse de chute est donc,
Vitesse de chute = distance de chute/temps de
décantation = 174/68 = 2,56 cm/minute
La surface totale de projection (STP) est la projection
à la partie basse du bac de la surface de décantation. Elle est
calculée comme suit :
STP = Nplaque * Sp * Cos á
Où : Nplaque est le nombre de plaque,
Sp est la surface unitaire de chaque plaque et á est l'angle
de projection.
Surface Totale de Projection (STP) = 10 * 90 *
75 * Cos 60 = 33 750 cm²
Filtration : La filtration sur
sable-gravier a été choisie pour sa facilité de mise en
place afin de retenir les petites particules n'ayant pas pu être retenues
par la décantation. Le filtre adopté par l'entreprise a une forme
cylindrique de hauteur 210 m et diamètre 66 cm, donc une capacité
de 71,85 m3 (volume du cylindre = ð * (diamètre) ² *
hauteur/4). Dans le filtre, le gravier occupe un volume de 21,54 m3
et le sable fin occupe un volume de 44,32 m3.
Le temps de filtration des 18 m3 d'eau, contenue
dans le bac de récupération, est environ 141 minutes (soit 2,35
heures) et ceci à travers une section (circulaire), offerte à
l'écoulement de 0,76 m². Le débit (volumique)
d'écoulement d'eau à la sortie du filtre est donc,
Débit volumique = volume/temps =
18/2,35 = 7,66 m3/h
La vitesse de filtration est obtenue est également
calculée comme suit :
Vitesse de filtration = Débit
volumique/section d'écoulement = 7,66/0,76 = 10,08
m/h
Adoucissement : Cette étape
implique l'utilisation des résines échangeuses d'ions, car elle
repose sur un échange entre les ions sodium (Na+) de la
résine contre les ions calcium (Ca2+) et magnésium
(Mg2+) de l'eau à traiter. Lorsque la résine est
saturée, il faut la régénérer à l'aide d'une
solution saturée de chlorure de sodium (NaCl). La solution
saturée est obtenue en introduisant 35 kg de chlorure de sodium dans un
bac contenant 200 L d'eau. Ceci correspond à une concentration (NaCl)
de,
Concentration (NaCl) = 35000/200 = 175
g/l
III.1.3. Constats fait
Les constats qui ont été fait lors de notre
étude dans l'entreprise sont :
§ Economie dans l'utilisation des kits d'analyses
chimiques, car l'analyse des eaux est faite une fois tous les trois
jours ;
§ Le mauvais entretien des bacs de traitement.
Ø Description du problème avec l'outil
QQOQCP
Tableau 4:
Description du problème avec l'outil QQOQCP
Qui? Qui est concerné par le
problème?
|
Le Complexe Industriel du Littoral
|
Quoi? Quel est le problème?
|
Traitement insuffisant de l'eau, car il y a la présence
d'une forte teneur en fer et en chlorure dans l'eau de la chaudière
|
Où? Où survient le
problème?
|
L'eau du forage
|
Quand? À quel moment apparait t-il?
|
Lors de son utilisation
|
Comment? Comment a-t-il été
détecté?
|
Diagnostique des installations de traitement, interview,
observation basée sur la méthode des 5M (Matière,
Matériel, Méthodes, Milieu, Main d'oeuvre)
|
Pourquoi? Quels sont les raisons qui poussent
à résoudre le problème?
|
Assurer la durée de la chaudière en la
protégeant, empêcher la corrosion des tuyauteries
|
Après identification des principales anomalies sur la
station de traitement, l'eau du forage est prélevée et
caractériser.
III.2. QUALITE PHYSICOCHIMIQUE
DE L'EAU DU FORAGE
Les résultats des paramètres physicochimiques de
l'eau du forage du Complexe Industriel du Littoral (CIL), montrent qu'elle est
acide et trouble. Sa conductivité élevée ce qui
suggère une eau fortement chargée. La forte acidité de
cette eau est due à sa haute teneur en sulfites
(SO32-). Cependant son pH est élevé par
ajout de la soude, qui transformera les sulfites (SO32-)
en sulfates (SO42-), d'après la réaction
suivante :
2NaOH(aq) +
SO32-(aq) +
1/2O2(g)
Na2SO4(s) + 2OH-(aq)
Le sulfate de sodium (Na2SO4), est un
composé chimiquement très stable. Il est
généralement considéré comme étant
non-toxique, et à l'avantage de ne pas corroder les installations.
L'eau du forage détient également une forte
teneur en fer ferreux (Fe2+) et en chlorure (Cl-),
d'où l'objectif de notre travail, car ce sont les deux seules
paramètres qui ne sont pas contrôlés, jusqu'à
l'arrivée de l'eau à la chaudière.
Les résultats des paramètres physicochimiques de
l'eau du forage sont présentés ci-dessous :
Tableau 5:
Qualité physicochimiques de l'eau du forage
Paramètres Analysés
|
Eau du forage
|
Norme
NF EN ISO 32-020-1
|
Aspect
|
Trouble
|
Limpide
|
Turbidité (NTU)
|
7,2
|
=5
|
Température (°C)
|
26,8
|
=25
|
pH
|
2,7
|
7,5-8,5
|
Conductivité (uS/ cm)
|
649,3
|
<50
|
Fe2+ (mg/l)
|
2,7
|
<0,05
|
Cl- (mg/l)
|
28,4
|
<5
|
III.2.1. Produits du traitement
existant de l'eau du forage
Les produits du traitement existant de l'eau du forage du
Complexe Industriel du Littoral, cet-à-dire le sulfate d'alumine
hydraté (Al2(SO4)3 18H2O),
le détartrant W588, et la soude (NaOH), sont fournis par la
société ADER. Le sel (NaCl) est fourni par la
société SOCAPURSEL. Ces produits permettent de corriger le pH, la
turbidité, la dureté (TH), la teneur en sulfite et
l'alcalinité (TA et TAC) de l'eau du forage avant qu'elle n'arrive
à la chaudière.
Les doses des produits de traitement hebdomadaires sont :
25 kg de sulfate d'alumine hydraté + 9 kg de soude dans le mini bac, et
25 kg de soude dans le bac de décantation. Ces produits sont
utilisés pour traiter 18 m3 d'eau.
III.3. CLASSIFICATION ET
HIERARCHISATION DES CAUSES DU TRAITEMENT INSUFFISANT DE L'EAU DU FORAGE
(BRAINSTORMING)
III.3.1. Classification des
causes du traitement insuffisant de l'eau du forage
La recherche des causes du traitement insuffisant de l'eau du
forage s'est faite par un questionnaire et des observations sur le site. Ces
causes ont ainsi été regroupées par la méthode des
5M et représentées sur un diagramme causes-effet (figure 9).

FIGURE 9:
CLASSIFICATION DES CAUSES DU TRAITEMENT INSUFFISANT DE L'EAU
Il est important de noté que lorsque le compresseur
d'air était utiliser dans la station de traitement d'eau, la teneur en
fer dans l'eau après traitement de l'eau du forage était 0,03
mg/l. Cette valeur respecte la norme NF EN ISO 32-020-1 qui voudrait que la
teneur en fer dans l'eau du forage soit inférieure à 0,05 mg/l.
Les caractéristiques du compresseur d'air utilisé, avant qu'il ne
tombe en panne, sont présentées en annexe 8.
III.3.2. Hiérarchisation
des causes du traitement insuffisant de l'eau du forage
Après la séance de questionnaire, le vote de
chaque participant est effectué. Les résultats du vote sont
consignés dans le tableau donné en annexe 1. Les totaux de ces
résultats ont été par la suite regroupés dans le
tableau 6 suivant.
Tableau 6:
Valeurs pondérés des causes liées au traitement
insuffisant de l'eau
Causes
|
Note finale
|
Panne du compresseur à air auparavant utilisé
pour l'élimination du fer
|
21
|
Absence des réactifs ou kits d'analyses chimiques
|
21
|
Absence de quantification des produits de traitement
supplémentaire
|
20
|
Eau du forage acide avec forte teneur en fer et chlorure
|
18
|
Corrosion de la vanne rendant le prélèvement
difficile
|
16
|
Personnel peu qualifié
|
10
|
Total
|
106
|
III.3.3. Identification des
anomalies majeures dans le mauvais traitement de l'eau
Sur le diagramme de Pareto obtenu sur la figure 10 suivante,
la loi des 80/20 n'est pas respectée. En effet, 33,33% des effets sont
induits par 66,67% des causes (résultat du calcul des fréquences
en annexe 2). Les actions correctives seront donc proposées pour tous
les 66,67% défauts observés sur le site.
Les principales causes recensées sont donc : panne du
compresseur, l'absence (auparavant) de réactifs ou kits d'analyses du
fer et chlorure, absence de quantification des produits de traitement
supplémentaire, et la forte teneur en fer et chlorures contenus dans
l'eau du forage.
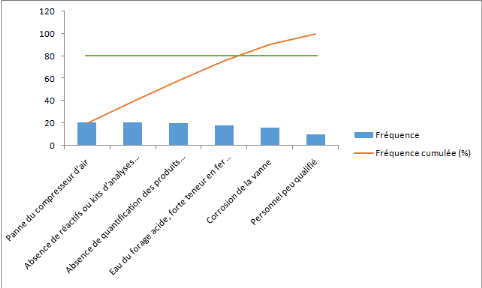
Figure 10:
Diagramme de Pareto
III.4. PROPOSITION DES ACTIONS
CORRECTIVES
Dans notre travail, il était question pour nous de
proposer un système de déferrisation et dé-chloration de
l'eau du forage.
III.4.1. Déferrisation
de l'eau du forage
Les méthodes de déferrisation de l'eau du forage
proposées à l'entreprise CIL sont l'oxydation par l'ozone (en
utilisant un ozoneur) ou par l'oxygène (en utilisant un compresseur
d'air).
Ø Déferrisation avec l'ozone
(O3) (Ozonation)
L'ozone peut être obtenu industriellement par
décharge électrique dans l'air très sec ou de
l'oxygène entre deux électrodes. C'est un oxydant très
puissant. Il se présente comme un gaz instable, qui doit donc être
produit sur place dans des ozoneurs industriels. L'ozone est produit
d'après la réaction suivante :
3O2(g) 2O3(g)
L'ozone précipite le fer via une réaction
présentée comme suit :
2Fe2+(aq) + O3(g) +
5H2O(l) 2Fe(OH)3(s) +
O2(g) + 4H+(aq)
L'ozone agi de façon très complexe et sont
utilisation présente les avantage suivant :
- C'est un composé instable (formation d'ozonide
instable par des réactions d'addition) : sa stabilité dans l'eau
est de l'ordre de 10 à 20 minutes avant de se décomposer en
oxygène sans laisser de produits dérivés dans l'eau,
même lorsqu'il est présent en excès dans l'eau ;
- Temps de réaction très court (2 à 6
minutes), et ceci quel que soit le pH de l'eau ;
- Ne présente pas d'action rémanente ;
- Produit sur place, il ne pose aucun problème de
transport de matière dangereuse ou de stockage de produit toxique et ne
fait appel à aucun consommable.
- Favorise également l'élimination des
bactéries, et virus.
Cependant sa production est grande consommatrice
d'énergie et les coûts d'investissement sont importants. (Lamb et
al, 1995)
Les caractéristiques des ozoneurs varient en fonction
des constructeurs. Les valeurs moyennes (www.agrochem.fr) sont
généralement de :
TABLEAU 7 :
VALEURS MOYENNES DES OZONEURS
Tension entre les électrodes
|
15 000 à 20 000 V
|
Fréquence du courant
|
50 à 60 Hz
|
Débit d'air
|
1 000 m3/h
|
Concentration du gaz obtenu
|
20 à 60 g d'O3 par m3 d'air
|
Production spécifique
|
15 à 20 g d'O3/h
|
Consommation d'énergie
|
24 à 72 kWh/g d'O3
|
Puissance appliquée
|
25 W/ l minute d'air sec
|
Pression de fonctionnement
|
0,5 à 0,6 bar (1 bar maxi)
|
L'ozone peut être généré dans des
concentrations comprises entre 20 et 60 g/m3, et la consommation
d'énergie étant généralement située entre 24
et 72 kWh/g d'ozone.
§ Estimation de la quantité
(théorique) d'ozone nécessaire
La quantité minimale théorique d'ozone
nécessaire pour la déferrisation de l'eau est 0,43 g d'O3
par g de Fe2+ (Lamb et al, 1995).
La quantité de Fe2+ contenu dans l'eau du
forage est 2,7 mg/l (1 mg/l = 1 g/m3). La quantité de
Fe2+ dans 18 m3 d'eau du forage est,
Quantité de Fe2+ dans l'eau
= 2,7 * 18 = 48,6 g de Fe2+
Ainsi pour 48,6 g de Fe2+, la quantité
d'ozone nécessaire pour la déferrisation est,
Quantité d'ozone nécessaire pour la
déferrisation = 48,6 * 0,43 = 20,898 g
d'ozone
Le débit d'ozone produit pour 18 m3 d'eau
est,
Débit nécessaire = 20,898/ 18 =
1,161 g d'ozone par m3 d'eau
Le temps nécessaire pour le remplissage du bac de
décantation est,
Temps = Volume/ débit
= 18/10 = 1,8 heures
La quantité d'ozone produite par heure pour 48,6 g de
Fe2+ est,
Quantité d'ozone par heure = 20,898/1,8
= 11,61 g d'ozone par heure
Ainsi pour 15 grammes par heure d'ozone
pulvérisé dans l'eau, la quantité d'ozone produit en
excès est,
Quantité en excès = (15-11,61)
* 1,8 = 6,102 g d'ozone en excès dans l'eau
Le pourcentage d'ozone utilisé pour le traitement de
l'eau est,
Pourcentage = (11,61/15) * 100 = 77,4
%
Ainsi pour la déferrisation de l'eau, il faut un
ozoneur produisant 15 grammes par heure d'ozone. Ceci correspond à une
consommation d'énergie de 24 kilowattheures par gramme d'ozone. Ainsi
l'énergie consommée pour la production de 20,898 g d'ozone
est,
Energie consommée = 24 * 20,898 =
501,552 kWh
Les calculs (théoriques) effectués ci-dessus
nous montrent effectivement que, pour la déferrisation de l'eau du
forage, le pourcentage d'ozone utilisé est 77,4 %, pour
une consommation d'énergie de 501,552 kWh.
Ø Déferrisation avec l'oxygène
(O2)
Cette méthode de traitement nécessite
l'utilisation d'un compresseur d'air. L'air est prélevé de
l'atmosphère puis comprimé. La compressibilité est
utilisée à l'aide d'un
système
pneumatique. L'air comprimé est maintenu sous une
pression supérieure
à celle de l'atmosphère. L'oxygène produit
précipite le fer via la réaction suivante :
4Fe2+(aq) + O2(g) +
10H2O(l) 4Fe(OH)3(s)
+ 8H+(aq)
L'hydroxyde de fer formé est éliminé par
décantation et/ou filtration. L'énergie nécessaire
à la compression de l'air est importante et s'accompagne d'une
production d'
énergie
thermique (chaleur) qui reste le plus souvent inexploitée. L'air
comprimé est donc un
vecteur
d'énergie relativement coûteux.
L'avantage de cette méthode est que l'oxygène
utilisé pour la déferrisation est prélevé de
l'atmosphère. La vitesse de déferrisation est plus grande si le
pH de l'eau est élevé. Cependant le temps de réaction pour
cette méthode est long (entre 45 et 90 minutes), dépendant du
débit d'air et la consommation d'énergie relativement couteuse.
(Lamb et al, 1995)
Les spécifications des compresseurs d'air varient d'un
concepteur à l'autre, cependant les valeurs moyennes (
www.agrochem.fr) disponibles sur le
marché sont présentées dans le tableau
ci-après :
Tableau 8:
Valeurs moyennes des compresseurs d'air
Exigences électriques
|
230 V (#177;10 %), 50 Hz - 60 Hz
|
Consommation de courant nominal
|
2,0 A
|
Niveau sonore
|
44 dB en moyenne
|
Niveau de concentration d'O2
|
0,05 à 5 litres/ min (Niveau de concentration obtenus
après une période de chauffe d'environ 30 minutes)
|
Pression de sortie maximale
|
34,5 kPa (#177; 3,45 kPa)
|
Gamme de débit
|
0,5 à 5 litres/ min (les débits inférieurs
à 0,5 litre/ min ne sont pas recommandés)
|
Consommation d'énergie
|
90 à 120 kW
|
§ Estimation de la quantité
(théorique) d'oxygène nécessaire
La quantité minimale théorique d'oxygène
nécessaire pour la déferrisation de l'eau est 0,14 g d'O2
par g de Fe2+ (ou 0,104 l d'O2 par g de
Fe2+ ou 0,5 l d'air par g de Fe2+). (Lamb et al, 1995)
La quantité de Fe2+ dans 18 m3
d'eau est 48,6 g (Voir le calcul ci-dessus). La quantité
d'oxygène nécessaire pour la déferrisation est donc,
Quantité d'oxygène nécessaire pour
la déferrisation = 48,6 * 0,14 = 6,804 g
d'O2
Cette quantité d'oxygène correspond à
5,0544 litres d'O2 ou 24,3 litres
d'air. Le temps nécessaire pour le remplissage du bac de
décantation est 1,8 heure ou 108 minutes.
La quantité d'oxygène par minute
nécessaire pour la déferrisation est,
Quantité d'oxygène par minute
= 6,804/108 = 0,063 g d'O2 par minute
La masse volumique de l'oxygène est 1,429
kg/m3, ce qui correspond à 1,429 g/l. Ainsi le nombre de
litres d'oxygène par minutes que le compresseur doit produire est,
Nombre de litres d'oxygène par minute =
0,063/1,429 = 0,0441 litre par minute d'O2
Cela correspond à un compresseur d'air ayant un
débit de 0,05 litre d'oxygène par minute. Ainsi il y aura donc
une grande partie de l'oxygène fourni qui précipitera le
Fe2+. La quantité d'oxygène en excès se
trouvant dans l'eau du forage est,
Quantité en excès = (0,05 -
0,0441) = 0,0059 litre par minute
Le pourcentage d'oxygène utilisé pour la
déferrisation est,
Pourcentage = (0,0441/0,05) * 100 =
88,2 %
La puissance correspondant à ce débit est 90 kW.
L'énergie consommée par le compresseur d'air est 90 * 1,8 =
162 kWh.
Les calculs (théoriques) ci-dessus ont permis de faire
une étude comparative de la méthode de déferrisation avec
l'ozone et avec l'oxygène.
TABLEAU 9 : ETUDE
COMPARATIVE DE LA MÉTHODE DE DÉFERRISATION AVEC L'OZONE ET AVEC
L'OXYGÈNE
Caractéristiques
|
Ozoneur
|
Compresseur d'air
|
Consommation d'énergie
|
Elevé
|
Faible
|
Temps de réaction
|
Très faible (2 à 6 minutes)
|
Elevé (45 à 90 minutes)
|
Pourcentage d'oxydant utilisé
|
Elevé
|
Très élevé
|
Les opérations de maintenance de ces équipements
(ozoneur ou compresseur d'air) doivent être effectuées par des
techniciens qualifiés. Les filtres et dessiccateurs dans les
systèmes de préparation de l'air doivent être
changés régulièrement en fonction de la qualité de
l'air utilisé et du nombre d'heures de fonctionnement. Les canalisations
et chambre de contact doivent être inspectées à
échéance régulière pour pallier à toute
corrosion et fuite.
III.4.2. Dé-chloration
de l'eau du forage
Etant donner que la teneur en chlorure de l'eau du forage est
élevée, un système de dé-chloration devient
nécessaire. Le système de dé-chloration proposé
dans notre méthode de traitement, consiste à installer une
cartouche de charbons actifs granulaires en aval du filtre sable-gravier. Le
charbon actif granulaire offre une grande surface de contact, entre 600 et 1500
m²/g, d'où la nécessité de l'utilisation pour la
dé-chloration (KNAPPE, MATSUI, SNOEYINK, 1998).
Tableau 10:
Caractéristiques du filtre à cartouche de charbon actif
granulaire proposé
Débit d'eau moyen (m3/ h)
|
8
|
Pression de service (bar)
|
10
|
Pression max d'utilisation (bar)
|
16
|
Température max (°C)
|
50
|
Surface spécifique (m2/
g)
|
600 à 1500
|
Diamètre des pores (mm)
|
0,55 à 1,05
|
Les actions correctives proposées ont été
présenté au moyen des figures ci-après (figure 11 et 12).
Il a été proposé que pour l'opération de
déferrisation, qu'un compresseur d'air ou ozoneur soit connecté
par simple branchement (à l'aide du tube de venturi, afin de maximiser
le contact entre l'eau et l'ozone (ou l'oxygène)) à la tour
d'oxydation existante. Ceci va permettre la déferrisation de l'eau,
lorsque la pompe de captage sera démarrée. L'air ou l'ozone sera
diffusés en continu dans la tour d'oxydation jusqu'à arrêt
de la pompe. Aussi, pour la dé-chloration, nous avons proposé
qu'une cartouche de charbons actifs granulaires soit incorporé en aval
du filtre sable-gravier, ceci afin d'éviter que la cartouche soit
chargé en particules colloïdales.
Il est aussi à noter que le préchauffage de la
bâche est important dans le deuxième poste de traitement pour un
dégazage de l'eau qui va à la chaudière. Cela permet
d'éliminer les gaz (oxygène et/ou dioxyde de carbone) dissous
présent dans l'eau, afin d'éviter une quelconque oxydation qui
pourrait se produire à la chaudière. Ces gaz dissous
(oxygène et/ou dioxyde de carbone) s'échappent du système
avec les vapeurs incondensables. La solubilité de ces gaz dissous dans
l'eau, diminue avec augmentation de la température.
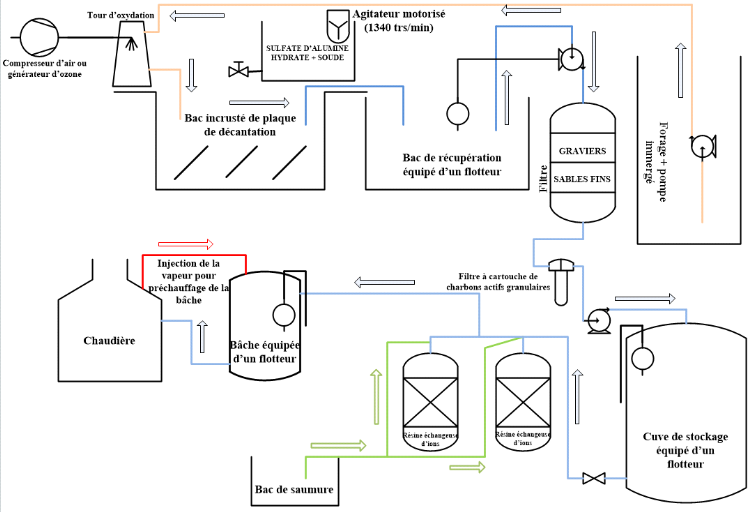
FIGURE 11 :
PRÉSENTATION DE LA STATION DE TRAITEMENT (ACTIONS CORRECTIVES) D'EAU DU
FORAGE DU COMPLEXE INDUSTRIEL DU LITTORAL
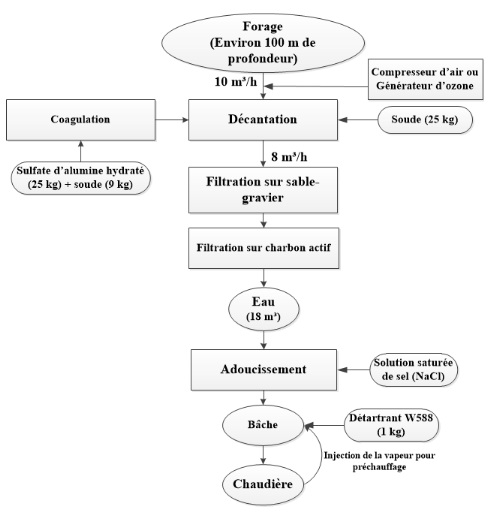
Figure 12:
Schéma block du traitement de l'eau du forage (Actions
correctives) du Complexe Industriel du Littoral
III.5. EVALUATION DES
COÛTS DES ACTIONS CORRECTIVES
III.5.1. Evaluation des
coûts du projet
L'évaluation des coûts du projet tient compte du
coût d'achat, coût d'installation et coût des pièces
de rechanges. Ces différents coûts sont regroupés dans le
tableau 10 ci-après :
TABLEAU 11:
EVALUATION DES COÛTS DU PROJET
Désignation
|
Ozoneur
|
Compresseur d'air
|
Coût d'achat
|
20 000 000 FCFA
|
3 500 000 FCFA
|
Coût d'installation
|
300 000 FCFA
|
65 000 FCFA
|
Coût des pièces de rechanges
|
5 000 000 FCFA
|
750 000 FCFA
|
Filtre à cartouche de charbon actif
|
350 000 FCFA
|
350 000 FCFA
|
Armoire électrique de commande et câbles
électrique
|
3 320 000 FCFA
|
3 320 000 FCFA
|
Total
|
28 970 000 FCFA
|
7 985 000 FCFA
|
III.5.2. Evaluation des charges
annuelles
Le prix unitaire du kilowattheure = 55 FCFA
Etant donné que l'eau du forage est traitée dans
l'entreprise un jour par semaine, le coût de consommation
énergétique mensuel et annuel dans le cas de l'ozoneur est,
Coût énergétique mensuel =
501,552 * 55 * 4 = 110 341,44 FCFA
Coût énergétique annuel =
110 341,44 * 12 = 1 324 097,28 FCFA
Le coût de consommation mensuel et annuel dans le cas du
compresseur d'air est,
Coût énergétique mensuel =
162 * 55 * 4 = 35 640 FCFA
Coût énergétique annuel =
35 640 * 12 = 427 680 FCFA
Les calculs des charges annuelles révèlent que
l'entreprise CIL bénéficiera plus sur l'utilisation d'un
compresseur d'air, pour l'amélioration du traitement de son eau du
forage. Les charges annuelles sont présentées dans le tableau
ci-dessous :
TABLEAU 12: CHARGES
ANNUELLES
Charges
|
Ozoneur
|
Compresseur d'air
|
Maintenance
|
3 000 000 FCFA
|
2 000 000 FCFA
|
Consommation d'énergie
|
1 324 097,28 FCFA
|
427 680 FCFA
|
Total
|
4 324 097,28 FCFA
|
2 427 680 FCFA
|
CONCLUSION
En somme, il était question dans ce travail de faire
une étude critique du système de traitement de l'eau de
chaudière du Complexe Industriel du Littoral. La démarche DMAIC a
été utilisée pour réaliser cet objectif. Les
principales causes d'insuffisance dans le traitement de l'eau du forage sont la
panne du compresseur d'air (qui n'a pas été réparé
depuis plus d'un an), l'absence de réactifs ou kits d'analyse chimique
du fer et chlorure, absence de quantification des produits de traitement
supplémentaire, et la forte teneur en fer et chlorure contenus dans
l'eau du forage. Pour la déferrisation de l'eau du forage, l'utilisation
d'un compresseur d'air ou ozoneur a été proposé, et pour
la dé-chloration, l'entreprise devrait incorporer un filtre à
cartouche de charbon actif granulaire en aval du filtre sable-gravier. Les
coûts de mise en place du projet ont été
évalué à 28 970 000 FCFA (pour le cas de
l'ozoneur plus filtre charbon actif) et 7 985 000 FCFA (pour le cas
du compresseur d'air plus filtre charbon actif). Les charges annuelles ont
également été évaluées à 4 324
097,28 FCFA (dans le cas de l'ozoneur) et 2 427 680 FCFA (dans le cas du
compresseur d'air).
RECOMMANDATIONS
Il a été recommandé à l'entreprise
CIL,
§ Le préchauffage de la bâche
d'alimentation, par les chefs d'équipe à la prise de chaque
quart, afin d'éliminer les gaz (oxygène et dioxyde de carbone)
dissous dans l'eau ;
§ La construction (en acier inoxydable de
préférence) des nouveaux bacs de décantation et
récupération. Ceux existants étant
sévèrement corrodés ;
§ De recruter un ingénieur (de conception)
spécialisé en traitement des eaux et en hygiène,
sécurité et environnement.
PERSPECTIVE
En guise de perspective,
§ L'entreprise devrait organiser les opérations de
maintenance (avec les techniciens) du compresseur d'air ou l'ozoneur, une fois
le projet adopté.
REFERENCES
BIBLIOGRAPHIQUES
Ø Eisenberg D., Kauzman W., (1969) Oxford
University Press, New York and London, p.10 ;
Ø Eagleson, 1970. « How can
we cope with the water resources situation by the year 2015? »,
Ambio : a Journal of the Human Environment, vol. 3,
no 3-4, p.107-109 ;
Ø Desbordes, 2000. Le Forage d'eau -
Réalisation, entretien, réhabilitation, p.40-42 ;
Ø Bertrand Gonthiez, 2009.
Réaliser et entretenir son puits, éd. Eyrolles,
p.26 ;
Ø D. O'Dowd, 2000. « Industrial
waters », ISBN 0-632-00683-8, p.86 ;
Ø Chibi, C. (1991). 'Design and
performance of a community-level iron-removal plant,' Waterlines. Vol.
10,No.2, pp.9-11 ;
Ø WEDECO, 2003. Amphoteric nature of
ferrous hydroxide: Chem. News, v. 138, p.354-356 ;
Ø Jolley et al, 1990. Trace elements
in drinking and groundwater samples in Southern Nigeria, Sci. Total Environ,
208, p.12-15 ;
Ø Emilio Lopez, Andres Redchuk, Javier
M.Moguerza, 2011.
«
SixSigma: Six Sigma Tools for Quality and Process Improvement »,
p.42-47 ;
Ø Thomas Roth, 2011.
«
qualityTools: Statistical Methods for Quality Science »,
p.53 ;
Ø P. Fleury, 1998. Héron
d'Alexandrie et Vitruve in Sciences et vie intellectuelle à Alexandrie
(Ier - IIIe siècle après J.-C.),
Publications de l'Université de St-Etienne, p.36 ;
Ø Duirk S.E., Gombert B., Croue J. P.,
Valentine R. L., Water Res. 39 (14) (2005) 3418,
p.22-24 ;
Ø Hureiki L., Croue J. P., Legube B.,
Water Res. 28 (1994) 2521, p.38-40 ;
Ø Cardot C., Ed. Ellipse. Paris,
(1999). France, ISBN 978-2-7298-5981-7, p.256 ;
Ø Dore M., Ed. Tech. et Doc. Lavoisier, Paris,
(1989). France. ISBN 2-85206-562-2, p.528-531 ;
Ø Harrat N., Achour S., Larhyss
Journal, 8 (2010), p.47-49 ;
Ø Liu S., Zhu Z., Qiu Y., Zhao J.,
Journal of Environmental Sciences. 23 (5) (2011),
p.765 ;
Ø PELEKANI C., SNOEYINK V.L.
(1999). Competitive adsorption in natural water: role of
activated carbon pore size, Water Research, 33 (5), pp.1209-1219 ;
Ø SIBILLE, 1997. «Iron (Fe) and
Manganese (Mn) Removal Trials at Barrie Ontario», p.315-319 ;
Ø KNAPPE D.R.U., MATSUI Y., SNOEYINK
V.L. (1998). Predicting the capacity of Powdered
Activated Carbon for trace organic compounds in natural waters, Environmental
science & technology, 32 (11), pp.1694-1698 ;
Ø Arden T.V., New World Water.
(1994), p.59 ;
Ø Lamb, A. B. and Elder, L. W., Jr.,
1995. The electromotive activation of oxygen: Am. Chem. Soc. Jour., v.
52, p.137-149 ;
Ø J-P BECHAC, Pierre BOUTIN, Bernard MERCIER,
Pierre NUER (1984): Traitement des eaux usées, EYROLLES, 61 Bd
Saint Germain - 75005 PARIS, p.281 ;
Ø Rapport de l'historique du Complexe Industriel du
Littoral (CIL), 2014 ;
SITES WEB
Ø
http://fr.wikipedia.org/wiki/Charbon_activ%C3%A9, consulté le
05-10-2017 à 20h45 minutes ;
Ø http://www.gwp.org/Global/GWP-Etude nationale sur le
financement du secteur de l'eau au Cameroun.pdf, consulté le 12-10-2017
à 20h45 minutes ;
Ø
www.carbochem.com/activatedcarbon101.html#Properties, consulté le
07-10-2017 à 10h05 minutes ;
Ø
www.activated-carbon.com/3-3.html, consulté le 07-10-2017 à
10h35 minutes ;
Ø
http://step.ipgp.fr/images/0/08/ADSORPTION_SUR_CHARBON_ACTIF.pdf,
consulté le 07-10-2017 à 10h45 minutes ;
Ø www. ademe.fr, consulté le 10-10-2017 à
05h20 minutes ;
Ø www.erdgas.lu, consulté le 10-10-2017 à
05h50 minutes ;
Ø www.agrochem.fr, consulté le 09-10-2017
à 13h15 minutes ;
Ø www.aquap.fr, consulté le 10-10-2017 à
07h10 minutes.
ANNEXES
ANNEXE 1 :
RÉPARTITIONS DES VOTES PONDÉRÉS SUIVANT LES COTATIONS
Causes
/ personnes
|
Panne du compresseur d'air
|
Absence de réactifs ou kits d'analyses
chimiques
|
Absence de quantification des produits de traitement
supplémentaire
|
Eau du forage acide
Forte teneur en fer et chlorures
|
Corrosion de la vanne
|
Personnel peu qualifié
|
Responsable Technique
|
3
|
3
|
2
|
2
|
1
|
1
|
Responsable de Maintenance
|
3
|
3
|
3
|
2
|
1
|
1
|
Responsable de Production
|
3
|
3
|
3
|
2
|
2
|
1
|
Contremaître
|
3
|
3
|
3
|
3
|
3
|
1
|
Chef équipe A
|
3
|
3
|
3
|
3
|
3
|
2
|
Chef équipe B
|
3
|
3
|
3
|
3
|
3
|
2
|
Chef équipe C
|
3
|
3
|
3
|
3
|
3
|
2
|
Total
|
21
|
21
|
20
|
18
|
16
|
10
|
Annexe 2 :
Récapitulatif des fréquences du diagramme de Pareto
Causes
|
Fréquence
|
% Fréquence
|
Fréquence cumulée (%)
|
80%
|
Panne du compresseur d'air
|
21
|
19,81
|
19,81
|
80%
|
Absence de réactifs ou kits d'analyses
chimiques
|
21
|
19,81
|
39,62
|
80%
|
Absence de quantification des produits de traitement
supplémentaire
|
20
|
18,87
|
58,49
|
80%
|
Eau du forage acide, forte teneur en fer et
chlorures
|
18
|
16,98
|
75,47
|
80%
|
Corrosion de la vanne
|
16
|
15,09
|
90,56
|
|
Personnel peu qualifié
|
10
|
9,44
|
100
|
|
Total
|
106
|
100
|
|
|
ANNEXE 3:
PRÉSENTATION DES EAUX DU COMPLEXE INDUSTRIEL DU LITTORAL
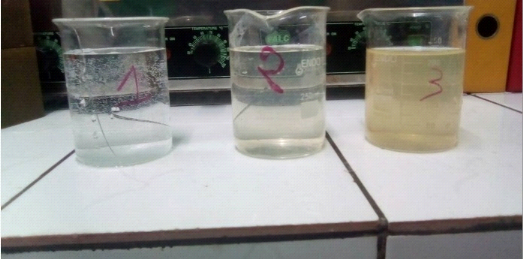
Eau de la bâche
Eau du forage
Eau filtrée
Annexe 4: Vue de
face de la station de traitement
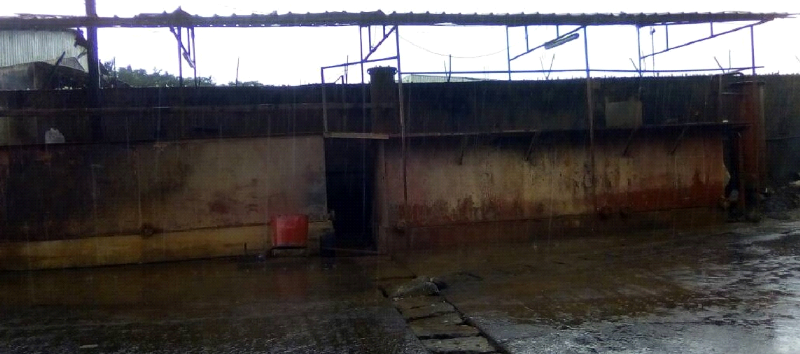
Annexe 5:
Présentation des dispositifs de traitement d'eau
Filtre sable-gravier
Tour d'oxydation
Bac de récupération
Bac de décantation
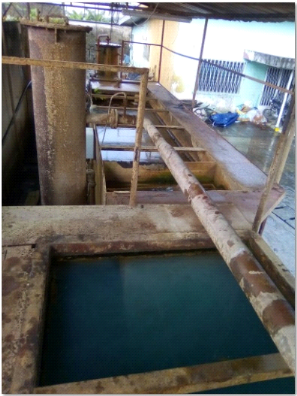
Résine échangeuse d'ions
Bac de saumure
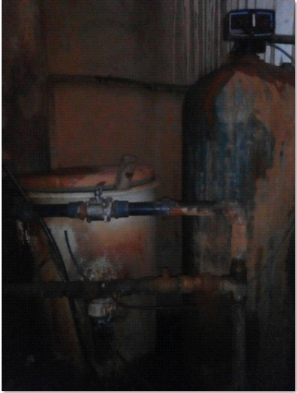
ANNEXE 6:
PRÉSENTATION DE LA BÂCHE
Bâche
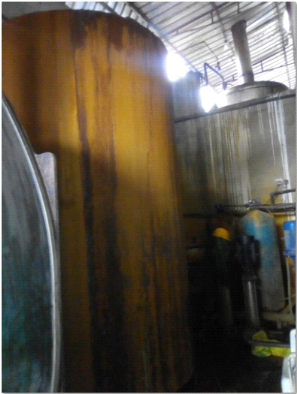
ANNEXE 7:
QUESTIONNAIRE
Questions
|
Réponses
|
1. Comment jugez-vous la qualité de l'eau du
forage ?
|
.........................................................
|
2. Avec quels réactifs traitez-vous l'eau du
forage?
|
.........................................................
|
3. Comment savez-vous que l'eau du forage est traitée
?
|
.........................................................
|
4. Comment entretenez vous la station de traitement
d'eau ?
|
.........................................................
|
5. Comment suivez-vous la qualité de l'eau
traitée ?
|
.........................................................
|
6. Comment jugez-vous le personnel ?
|
.........................................................
|
7. Qu'avez-vous fait après la panne du compresseur
d'air ?
|
.........................................................
|
Annexe 8:
Caractéristiques des équipements utilisés pour le
traitement de l'eau
Equipement
|
Caractéristiques
|
Pompe de forage
|
Marque : MILTON ROY
Hauteur de relevage : 125 m
Débit (max) : 15
m3/h
Diamètre de refoulement : 75
mm
N° de série : TC-X
1510302583
|
Pompe de surface
|
Marque : MILTON ROY
Hauteur de relevage : 55 m
Débit (max) : 10
m3/h
N° de série : EWN-A
8003462571
|
Pompe de relevage
|
Marque : MILTON ROY
Hauteur de relevage : 6 m
Débit (max) : 8
m3/h
Diamètre de refoulement : 25
mm
Section de passage : 8mm
N° de série : MD-F
3592650048
|
Agitateur Motorisé
|
Marque : MILTON ROY
Nombre de tour : 1340 tours/minutes
Courant : 2,2 A
Tension : 380 V
Puissance : 0,75 kW
Cos ö : 0,60
N° de série : RC-N
1409020032
|
Résine échangeuse d'ions
|
Marque : AMBERJETTM 1200
Na
Matrix : Copolymère
styrène di vinylbenzène
Capacité d'échange total :
= 2,00 eq/l (Forme Na+)
Capacité de rétention de
moisissure : 43 à 47% (Forme Na+)
Température de fonctionnement
(max) : 135 °C
Hauteur du lit (min) : 800 mm
Vitesse de service (max) : 60 m/h
Débit : 5 à 50 m3
de solution par m3 de résine
Regénérant : NaCl (10%),
HCl (4 à 10%), H2SO4 (1 à 8%)
Temps de contact (min) : 20
minutes
N° de série : AT 3414-2
|
Compresseur d'air utilisé (Avant sa panne)
|
Marque : MAXIMATOR
Tension : 230 V (60 Hz)
Courant : 2,5 A
Niveau sonore : 46 dB
Concentration
d'oxygène : 2 litres/minutes
Pression de sortie : 36 kPa
Débit d'air : 3 litres/minutes
Consommation d'énergie : 110
kW
N° de série : DLE 8503-1
|
Annexe 9:
Procédé de fabrication du savon
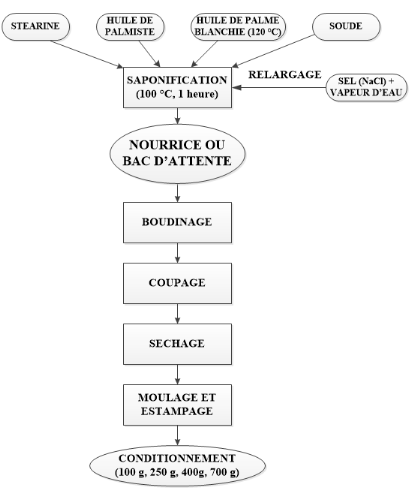
Annexe 10: Plan de
localisation du Complexe Industriel du Littoral (CIL)
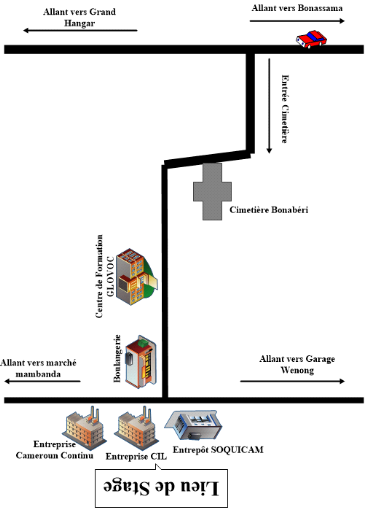
ANNEXE 11: FICHE
DU RAPPORT JOURNALIER CONTRÔLE QUALITÉ
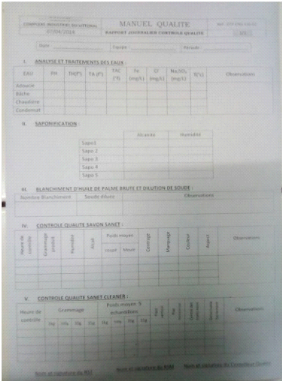
Annexe 12: Test Chimique de la
dureté, TH (Manuel d'instruction HANNA Instruments)
Matériel :
§ Un bécher en plastique (20 ml), avec couvercle
perforé ;
§ Un bécher en plastique (50 ml), avec
couvercle perforé ;
§ Une seringue calibrée (1ml).
Réactifs :
§ Solution tampon, avec compte-gouttes (30 ml) ;
§ Indicateur Calmagite, avec compte-gouttes (10
ml) ;
§ Solution EDTA (HI 3812-0), 120 ml.
Mode Opératoire :
- Retirer le couvercle du bécher en plastique (20 ml).
Puis rincer le bécher avec l'eau qu'il contiendra. Ensuite ajouter 5 ml
de cet eau (jusqu'au trait de jauge) et replacer le couvercle ;
- Ajouter 5 gouttes de la solution tampon, à travers le
couvercle du bécher, puis agiter minutieusement en formant des
cercles ;
- Ajouter également 1 goutte de l'indicateur calmagite,
ensuite agiter. La solution devient de couleur rouge-violette ;
- Prendre la seringue et le plonger dans la solution EDTA (HI
3812-0). Ensuite prélever la solution jusqu'à la marque
zéro de la seringue ;
- Placer la seringue à travers le couvercle du
bécher, et doser la solution goutte à goutte ;
- Continuer d'ajouter la solution d'EDTA jusqu'à
l'obtention d'une couleur pourpre, ensuite agiter pendant 15 secondes
après chaque nouvelle goutte jusqu'à ce que la solution devient
bleue ;
- Lire le nombre de millilitres d'EDTA utilisés sur
l'échelle de la seringue et multiplier la valeur obtenue par 300, afin
d'obtenir le nombre de mg/ l de calcaire (CaCO3).
Annexe 13: Test Chimique de
l'alcalimétrie, TA et TAC (Manuel d'instruction HANNA Instruments)
Matériels :
§ 2 béchers en plastiques calibrés avec
couvercles perforés (10 ml et 50 ml) ;
§ 1 seringue calibrée.
Réactifs :
§ Indicateur phénolphtaléine, avec
compte-gouttes (10 ml) ;
§ Indicateur bromophénol bleu, avec compte-gouttes
(10 ml) ;
§ Solution titrant HI 3811-0 (120ml).
Mode opératoire (TA) :
- Retirer le couvercle du bécher en plastique (20 ml).
Puis rincer le bécher avec l'eau qu'il contiendra. Ensuite ajouter 5 ml
de cet eau (jusqu'au trait de jauge) et replacer le couvercle ;
- Ajouter 1 goutte de l'indicateur
phénolphtaléine, à travers le couvercle du bécher,
puis agiter minutieusement en formant des cercles. Si la solution demeure
incolore, noter la valeur du TA comme zéro et procéder à
la mesure du TAC. Si la solution est rose ou rouge, procéder à la
prochaine étape ;
- Prendre la seringue et le plonger dans la solution HI
3811-0. Ensuite prélever la solution jusqu'à la marque
zéro de la seringue ;
- Placer la seringue à travers le couvercle du
bécher, et doser la solution goutte à goutte en agitant,
après chaque goutte. Continuer d'ajouter la solution HI 3811-0
jusqu'à l'obtention d'une in-coloration ;
- Lire le nombre de millilitres d'EDTA utilisés sur
l'échelle de la seringue et multiplier la valeur obtenue par 300, afin
d'obtenir le nombre de mg/ l de calcaire (CaCO3).
Mode opératoire (TAC) :
- Retirer le couvercle du bécher en plastique (20 ml).
Puis rincer le bécher avec l'eau qu'il contiendra. Ensuite ajouter 5 ml
de cet eau (jusqu'au trait de jauge) et replacer le couvercle ;
- Ajouter 1 goutte de l'indicateur bromophénol bleu,
à travers le couvercle du bécher, puis agiter minutieusement en
formant des cercles. Si la solution est verte ou bleue, procéder
à la prochaine étape ;
- Prendre la seringue et le plonger dans la solution HI
3811-0. Ensuite prélever la solution jusqu'à la marque
zéro de la seringue ;
- Placer la seringue à travers le couvercle du
bécher, et doser la solution goutte à goutte en agitant,
après chaque goutte. Continuer d'ajouter la solution HI 3811-0
jusqu'à l'obtention d'une couleur jaune ;
- Lire le nombre de millilitres d'EDTA utilisés sur
l'échelle de la seringue et multiplier la valeur obtenue par 300, afin
d'obtenir le nombre de mg/ l de calcaire (CaCO3).
Annexe 14: Test Chimique de sulfite
(Manuel d'instruction HANNA Instruments)
Matériels :
§ 2 béchers en plastiques calibrés avec
couvercles perforés (20 ml et 50 ml) ;
§ 1 seringue calibrée.
Réactifs :
§ Solution d'acide sulfamique, avec compte-gouttes (30
ml) ;
§ Solution EDTA, avec compte-gouttes (30 ml) ;
§ Solution d'acide sulfurique, avec compte-gouttes (15
ml) ;
§ Indicateur amidon, avec compte-gouttes (10
ml) ;
§ Solution titrant HI 3822-0 (120 ml).
Mode opératoire :
- Retirer le couvercle du bécher en plastique (20 ml).
Puis rincer le bécher avec l'eau qu'il contiendra. Ensuite ajouter 5 ml
de cet eau (jusqu'au trait de jauge) et replacer le couvercle ;
- Ajouter 4 gouttes chacune de la solution d'acide sulfamique
et l'EDTA, à travers le couvercle du bécher, puis agiter
minutieusement en formant des cercles ;
- Ensuite ajouter également 2 gouttes de l'acide
sulfurique et agiter ;
- Puis ajouter encore 1 goutte de l'indicateur amidon et
agiter ;
- Prendre la seringue et le plonger dans la solution HI
3822-0. Ensuite prélever la solution jusqu'à la marque
zéro de la seringue ;
- Placer la seringue à travers le couvercle du
bécher, et doser la solution goutte à goutte en agitant,
après chaque goutte. Continuer d'ajouter la solution HI 3822-0
jusqu'à l'obtention d'un mélange qui change d'incolore à
bleu ;
- Lire le nombre de millilitres d'EDTA utilisés sur
l'échelle de la seringue et multiplier la valeur obtenue par 200, afin
d'obtenir le nombre de mg/ l de sulfite de sodium
(Na2SO3).
Annexe 15: Mode opératoire des
paramètres physico-chimiques analysés de l'eau du forage
pH : Le pH de l'eau du forage a
été obtenu à l'aide du papier pH, par simple comparaison
de la couleur de ce dernier avec le comparateur. Ceci a été
effectué, après avoir trempé ce papier dans un
bécher contenant 50 ml de cette eau.
Température : La
température de l'eau du forage a été mesurée
à l'aide d'un thermomètre, par simple lecture de la valeur
affiché sur ce dernier. Ceci a été effectué,
après avoir immergé ce thermomètre dans un bécher
contenant 50 ml de cette eau. Elle est exprimée en degré Celsius
(°C).
Turbidité : La turbidité
de l'eau du forage a été mesurée à l'aide d'un
turbidimètre, par simple lecture de la valeur affiché sur
l'écran de ce dernier. Ceci a été effectué,
après avoir immergé la sonde dans un bécher contenant 50
ml de cette eau. Elle est exprimée en NTU (Nephelometric Turbidity
Unit).
Conductivité : La conductivité
de l'eau du forage a été mesurée à l'aide d'un
conductimètre, par simple lecture de la valeur affiché sur
l'écran de ce dernier. Ceci a été effectué,
après avoir immergé la sonde dans un bécher contenant 50
ml de cette eau. Elle est exprimée en micro Siemens par
centimètre (uS/ cm).
Teneur en fer : La teneur a
été déterminée en utilisant un kit d'analyse
chimique du fer (matériels et réactifs fourni par HANNA
Instruments). Dans un bécher de 20 ml, (préalablement
rincé avec l'eau qu'elle contiendra, après que son couvercle a
été enlevé) 10 ml d'eau du forage ont été
ajouté. Ensuite un sachet du réactif HI 3834-0 a
été ajouté. Puis le couvercle a été
replacé et son contenu agiter jusqu'à dissolution complète
des solides. Par la suite le couvercle est enlevé et le contenu du
bécher a été transvaser dans le cube du comparateur. La
solution est laissée pendant quatre minutes. La couleur de la solution
dans le cube, a été comparée avec ceux du comparateur afin
de déterminer la teneur qui correspond. Elle est exprimée en
milligramme par litre (mg/l).
Teneur en chlorure : La teneur a
été déterminée en utilisant un kit d'analyse
chimique des chlorures (matériels et réactifs fourni par HANNA
Instruments). Dans un bécher de 20 ml, (préalablement
rincé avec l'eau qu'elle contiendra, après que son couvercle a
été enlevé) 5 ml d'eau du forage ont été
ajouté et le couvercle replacé. Ensuite deux gouttes de
l'indicateur diphénylcarbazone ont été ajoutées
à travers le couvercle du bécher, et ce dernier a
été agité minutieusement en formant des cercles. Une
coloration rouge-violette a été observée. Pendant
l'agitation du bécher, la solution d'acide nitrique a été
ajoutée goutte à goutte jusqu'à ce que la solution est
devenue jaune. Une seringue a été prise et plonger dans la
solution de nitrate de mercure (la solution HI 3815-0), afin de prélever
celle-ci jusqu'à la marque zéro. La seringue a été
placée à travers le couvercle du bécher, et la solution
dosée goutte à goutte en agitant, après chaque goutte. La
solution HI 3815-0 est dosée jusqu'à l'obtention d'un
mélange qui change de jaune à violet. Le nombre de millilitres de
la solution HI 3815-0 ajoutée a été lu sur
l'échelle de la seringue, puis multiplié par mille (1000), afin
d'obtenir le nombre de milligramme par litre (mg/l) de chlorure.
 
|