ANNEXES
ANNEXE 1 : Fiche technique Régulateur
GEFRAN 450.
Caractéristiques principales :
· Entrée universelle configurable par la face
avant
· Précision meilleure que 0,2% PE aux conditions
de référence
· Sortie régulation : relais ou logique avec
fonction chaud ou froid
· Une alarme à fonction configurable
· Autoréglage, auto-adaptation, rampe au
démarrage, fonction Auto/Manu
· Possibilité de configuration par liaison
numérique
Généralités :
Le régulateur de température série 450,
qui mesure 48x48mm (1/16 DIN), allie facilité d'utilisation et haute
qualité de régulation. L'entrée depuis les sondes de
température est « universelle » et configurable pour des
thermocouples des types J,K,R,S,T,B,E,N et des thermistances Pt100 à
trois fils. L'interface utilisateur se compose d'un double afficheur
très complet, comprenant des diodes vertes, 4 touches et deux diodes
rouges de signalisation des sorties actives.
Caractéristiques techniques:
· Entrées
Précision 0,2% f.s. +/- 1 digit
Acquisition de la mesure 120 ms
· TC - Thermocouples
J(Fe-CuNi) 0... 1000°C / 32 ... 1832°F
K(NiCr-Ni) 0...1300°C / 32...2372°F
R(Pt13Rh-Pt) 0...1750°C / 32...3182°F
S(Pt10Rh-Pt) 0...1750°C / 32...3182°F
T(Cu-CuNi) -200...400°C / -328...752°F
B(Pt30Rh-Pt6Rh) 44...1800°C / 111...3272°F
E(NiCr-CuNi) -100...750°C / -148...1382°F
N(NiCrSi-NiSi) 0...1300°C / 32...2372°F
· RTD 3 fils Pt100
-200...600°C / -328...1112°F
· Sorties
Sorties entièrement configurables pour la
régulation ou alarme
· Relais
Pouvoir de coupure : 5A/250Va.c., cos?=1
(Référence de commande R)
· Logique
12V (6V min 20mA) (Référence de commande D)
· Alimentation
-(Standard) 100...240 V a.c. +/- 10%
- (Optionnel) 11...27 V a.c./d.c. +/-10%
- 50/60Hz, max. 10VA
· Conditions Ambiantes
- Température de fonctionnement : 0...50°C
- Température de stockage : -20...70°C
- Humidité : 20...85% HR sans condensation
· Régulation
- On/Off, P, PD, PID pour chauffage ou refroidissement,
paramètres configurables depuis la face avant.
- Consigne « froid » asservie à la consigne
« chaud ».
- Reset manuel -999...999 digits
- reset puissance -100,0...100,0%
- Cycle 0...200sec
- Rampe au démarrage 0,0...500,0 min
· Alarme
- Une alarme avec seuil d'intervention programmable en valeur
absolue, relative ou relative symétrique par rapport au setpoint avec
fonction directe ou inverse.
- Alarme réglable sur toute l'étendue
d'échelle configurée.
- Alarme rupture de la boucle (LBA) -
Hystérésis d'alarme configurable
· Poids
- 210g pour la version complète
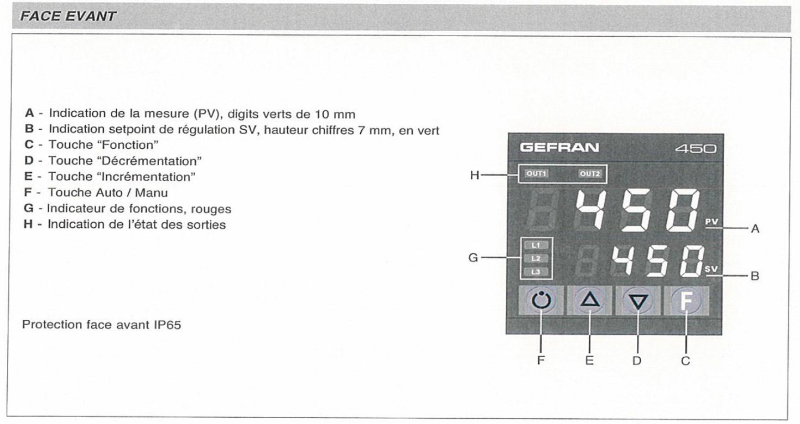
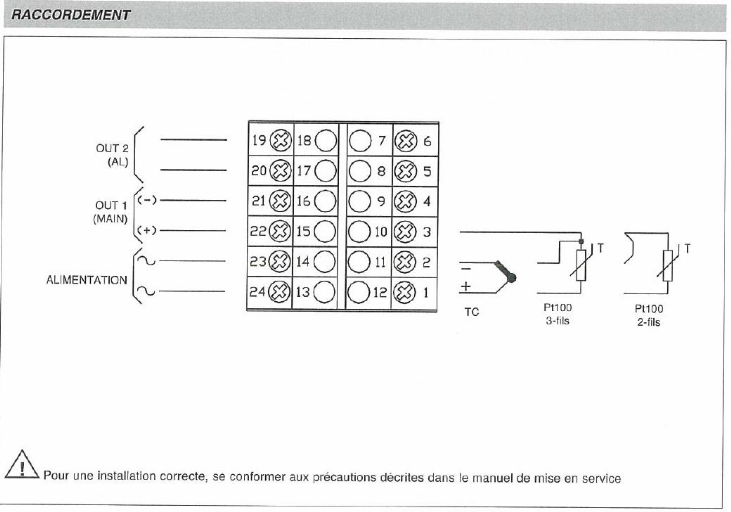
ANNEXE 2 : Fiche technique du Filtre Collecteur
de
Boue.
Caractéristiques techniques
- Pression de service = 5 bars maxi (à 60 °C).
- Captation magnétique par barreau magnétique
Alnico 600 positionné verticalement sur support facilement
démontable.
- Filtration 300 microns sur tamis inox (filtre vertical
entraînant la chute des boues).
- Réduction de vitesse 0,1 m/s dans le corps du
collecteur de boues mini-CDB.
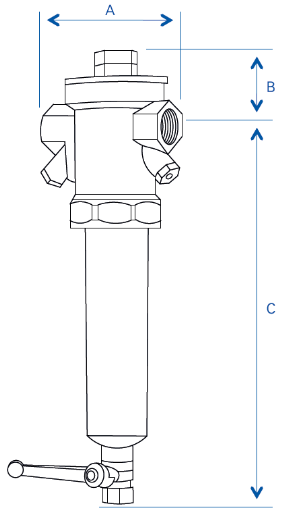
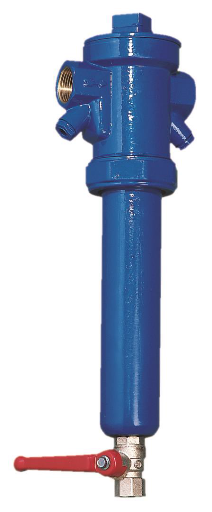
Matériau cuve
|
Température d'utilisation
|
Ø Entrée/ Sortie
|
Référence
|
A*
|
B*
|
C*
|
Plastique
|
5 à 60°C
|
3/4'
|
521006
|
96
|
65
|
190
|
1''
|
521008
|
123
|
93
|
190
|
1''1/4
|
521010
|
123
|
93
|
195
|
1'1/2
|
521012
|
145
|
110
|
230
|
2''
|
RI970047
|
145
|
110
|
230
|
Métallique
|
5 à 90°C
|
3/4'
|
521086
|
96
|
65
|
290
|
1''
|
521088
|
123
|
93
|
290
|
1''1/4
|
521090
|
123
|
93
|
295
|
1'1/2
|
521092
|
145
|
110
|
330
|
2''
|
RI970018
|
145
|
110
|
330
|
ANNEXE 3 :Fiche d'historique des pannes de
L'ILLIG
Date
|
Organe
|
Effet de la défaillance
|
Diagnostic
|
Travail à faire
|
activité
|
Temps mis
|
Matériaux utilisés
|
Priorité
|
Causes probables
|
|
Moule
|
La tige d'éjection est cassée
|
Tige cassée
|
Changer la tige
|
Démontage de l'esseuil ; Fixation de la tige ;
remontage
|
|
|
|
Accident imprévu
|
27-08-15
|
Vérin des poinçons
|
Le vérin des poinçons ne fonctionne pas
|
Fin de course défectueuse (30min)
|
Remplacer le fin de course
|
remplacement du fin de course ; réglage ;
essai
|
1h20min
|
Interrupteur de position
|
Très urgent
|
|
29-07-15
|
Valve
|
|
|
- - Remplacer les valves de commande des soufflettes
|
Remplacement des valves défectueuses : fixation du
support des valves par soudure
|
2h35min
|
valves simple effet ; écrou de diamètre
06
|
|
|
27-08-15
|
Circuit pneumatique
|
Impossible de produire (les pots ne se forment pas)
|
Disfonctionnement de l'interrupteur de position (30min)
|
Contrôler le circuit électrique et le circuit
pneumatique du soufflage des pots-
|
contrôle du circuit électrique (anormal) ;
Contrôle ; Circuit
Pneumatique
(anormal) ; fixation et Recâblage de
l'interrupteur de
position ; soufflage
essai et mise en service
|
2h
|
|
- Très urgent
|
Accident imprévu
|
24-08-15
|
Moule
|
Echange du produit
|
Changer le moule (30min)
|
Remplacer le moule 121-46 parle le moule 125-42
|
Démontage du moule 121-42 et ses accessoires
|
09h30min
|
|
- Très urgent
|
normal
|
04-08-15
|
Moteur
|
Trop de déchet (il faut tendre la chaine)
|
Chaine détendue (15min)
|
Tendre la chaine motrice
|
Chaine du moteur tendue ; serrage des vis de la
découpe pour remédier à la fuite d'eau sur le moule
|
1H15min
|
|
- Très urgent
|
Accident imprévu
|
30-07-15
|
Goulotte
|
La goulotte ne coulisse pas bien
|
Vis de fixation de bras cassée (15min)
|
Changer la vis et remonter le bras de commande de la
goulotte
|
Changement et montage du bras de commande de la goulotte ;
essai et mise en service
|
1h15min
|
Vis CHC, écrou, rondelle plate
|
Très urgent
|
fatigue
|
28-07-15
|
Ventilo
|
Présence de masse sur la machine
|
Ventilo broyeur illig à la masse (30min)
|
Rechercher la masse isolée ; sinon faire une mise
à la terre
|
Recherche de la masse, mise à la terre de la carcasse de
la machine ; essai et mise en service
|
45min
|
-
|
Très urgent
|
|
21-07-15
|
Ejecteur
|
Mauvaise injection des pots
|
Valve simple effet défectueuse (10min)
|
Réparation de la valve
|
Remplacement de la valve
|
1h
|
-
|
urgent
|
Usure
|
20-07-15
|
Moteur
|
Vibration du moteur
|
Vis de blocage cassée ; chaine principale
détendue (25min)
|
Remplacer les vis du moteur cassées ; tendre la
chaine principale
|
Remplacement des vis du moteur cassé ; tension de
la chaine du moteur principale
|
2h
|
- Vis CHC
- écrou
|
Très urgent
|
Mauvaise manipulation
|
16-07-15
|
Moule
|
Impossible de produire, présence d'eau sur les pots
|
Fuite d'eau sur le moule mobile (15min)
|
Corriger la fuite d'eau
|
Serrage des vis d'assemblage, essai et mise en service
|
45min
|
|
Très urgent
|
Accident imprévu
|
29-06-15
|
Graisseurs
|
|
|
Faire le graissage
|
Graissage des colonnes de guidage, des paliers de guidage, de
la canne, purger la graisse usée
|
30min
|
|
|
|
18-06-15
|
Moule
|
Mauvaise qualité des pots (l'eau entre dans le moule)
|
Fuite d'eau sur le raccord retour du moule mobile (15min)
|
Corriger les fuites d'eau
|
Correction des fuites d'eau ; essai et mise en service
|
45min
|
|
Très urgent
|
Accident imprévu
|
17-06-15
|
Moteur
|
Le moteur vibre
|
Vis de fixation cassée (30min)
|
Remplacer la vis de fixation cassée
|
Démontage de la chaine, démontage des trois vis
support moteur, remplacement des vis et fixation du moteur, remontage de la
chaine, essai et mise en service
|
2h30min
|
Vis CHC, écrou, rondelle
|
Très urgent
|
fatigue
|
15-06-15
|
Four bas
|
La zone 2 du bas ne chauffe pas
|
Alimentation contacteur zone 2 débranché
|
Fixer l'alimentation du contacteur
|
Alimentation fixée, essai et mise en service
|
15min
|
|
Très urgent
|
|
11-06-15
|
Chauffe
|
Le régulateur de température de la zone 1 ne
fonctionne pas bien
|
Régulateur de température grillé
(20min)
|
Remplacer le régulateur grillé
|
Remplacement régulateur, essai et mise en service
|
40min
|
Régulateur XMTE
|
Très urgent
|
|
22-05-15
|
Moteur
|
Difficulté de produire les pots
|
Vis de fixation du moteur principal coupée (10min)
|
Remplacer la vis coupée
|
Remplacement de la vis coupée
|
1h
|
Vis CHC ; écrou
|
Très urgent
|
|
29-04-15
|
Four bas
|
Le four ne chauffe pas
|
Résistance infrarouge cassées (10min)
|
Remplacer les résistances cassées
|
Démontage des résistances endommagées,
nettoyage du four, montage des nouvelles résistances, mise en chauffe et
observation
|
02h45min
|
Ecrou HC, émetteur infrarouge sans sonde 200W
|
Très urgent
|
Fatigue, matière qui se déverse sur les
résistances des
|
22-04-15
|
Circuit d'eau
|
Mauvais refroidissement des pots
|
Circuit d'eau bouché (30min)
|
Déboucher le circuit d'eau
|
Débouchage du circuit d'eau sur le moule
|
2h
|
|
Urgent
|
impureté
|
09-04-15
|
Moule
|
Mauvaise qualité des pots
|
Ressort de compression cassé, écrou de
réglage découpe défectueux (30min)
|
Remplacer le ressort cassé
|
Vis changée
|
08h30min
|
Vis épaulée, collier de serrage, ressort de
compression
|
Urgent
|
fatigue
|
26-03-15
|
Moule
|
Fuite d'eau sur le moule
|
Vis de serrage desserrée, tuyau percé (10min)
|
Serrer la vis de fixation du moule, remplacer le tuyau
percé
|
Serrage de la vis de fixation, remplacement du tuyau
percé, mise en service et essai
|
15min
|
Tuyau tressé tricolore
|
Très urgent
|
|
12-02-15
|
Goulotte
|
La goulotte ne fonctionne pas
|
Pas de vis du côté droit au bras de la goulotte
(15min)
|
Remplacer la vis cassée
|
Remplacement des vis cassées
|
15min
|
Vis HM, écrou HM, rondelle plate
|
Très urgent
|
Cassée
|
19-01-15
|
Circuit d'air
|
Impossible de produire
|
Filetage soufflette défectueux (10min)
|
Refaire le filetage de la soufflette
|
Filetage par Fillon, serrage de la vis support moteur
|
50min
|
Tube colle super glue
|
Très urgent
|
usure
|
17-02-15
|
Refroidissement
|
Fuite d'eau
|
Fissure de la conduite (15min)
|
Soudure de la fissure de la conduite
|
Soudure des fuites d'eau
|
40min
|
Baguette en cuivre
|
Urgent
|
|
17-02-15
|
Vanne d'air
|
Insuffisance d'air de soufflage des pots
|
Joints d'étanchéité défectueux dans
la vanne simple effet (30min)
|
Remplacer la vanne simple effet de commande
|
Adaptation d'un joint d'étanchéité, essai
et mise en service
|
1h
|
Super glue
|
Très urgent
|
fatigue
|
07-01-15
|
Soufflette
|
Impossible de produire
|
Soufflette cassée (5min)
|
Remplacer la soufflette cassée
|
Remplacement soufflette cassée, essai et mise en
service
|
10min
|
soufflette
|
Très urgent
|
|
ANNEXE 4 : Planning de maintenance
préventive
ILLIG RDM 37/10
|
Conducteur de la Machine
|
Equipe de Maintenance
|
Désignation de l'opération
|
Périodicité de l'intervention
|
20h
|
100h
|
200h
|
300h
|
500h
|
1500h
|
2500h
|
5000h
|
8760h
|
10200h
|
|
|
Vérification de l'état des émetteurs
infrarouge (Résistance chauffante)
|
|
|
|
|
|
|
|
|
|
|
|
|
Vérification des températures :
température affichée - température de consigne
(étalonnage)
|
|
|
|
|
|
|
|
|
|
|
|
|
Nettoyage des Capteurs
|
|
|
|
|
|
|
|
|
|
|
|
|
Vérification de l'état des tuyaux d'alimentation
en air du vérin des poinçons
|
|
|
|
|
|
|
|
|
|
|
|
|
Vérification de l'état du vérin des
poinçons
|
|
|
|
|
|
|
|
|
|
|
|
|
Vérification du circuit d'alimentation en air (circuit
pneumatique)
|
|
|
|
|
|
|
|
|
|
|
|
|
Vérification des lubrificateurs d'air
|
|
|
|
|
|
|
|
|
|
|
|
|
Vérification si la sonde de température est bien
fixée
|
|
|
|
|
|
|
|
|
|
|
|
|
Vérification de l'état des tuyaux d'alimentation
en eau pour le refroidissement dans le moule
|
|
|
|
|
|
|
|
|
|
|
|
|
Vérifier les colliers de serrages des tuyaux
d'alimentation en eau
|
|
|
|
|
|
|
|
|
|
|
|
|
Vérification de l'état et du serrage des vis de
différents organes (découpe, goulotte ; moteur)
|
|
|
|
|
|
|
|
|
|
|
|
|
Graissage des chaines picot
|
|
|
|
|
|
|
|
|
|
|
|
|
Vérifier si la chaine picot est tendue
|
|
|
|
|
|
|
|
|
|
|
|
|
Vérification du circuit d'éjection des pots
|
|
|
|
|
|
|
|
|
|
|
|
|
Vérification et serrage de la connectique dans l'armoire
électrique
|
|
|
|
|
|
|
|
|
|
|
|
|
Graissage des colonnes
|
|
|
|
|
|
|
|
|
|
|
|
|
Contrôle du degré d'usure des glissières
|
|
|
|
|
|
|
|
|
|
|
|
|
Serrage des cosses
|
|
|
|
|
|
|
|
|
|
|
|
|
Nettoyage du filtre à eau
|
|
|
|
|
|
|
|
|
|
|
|
|
Lubrification du vérin des poinçons
|
|
|
|
|
|
|
|
|
|
|
|
|
Changement des joints du vérin des poinçons
|
|
|
|
|
|
|
|
|
|
|
|
|
Contrôle des éléments roulant qui servent
au guidage des goulottes
|
|
|
|
|
|
|
|
|
|
|
|
|
Purger la graisse usée
|
|
|
|
|
|
|
|
|
|
|
|
|
Vérification de l'état des électrodes des
émetteurs infrarouge et des sondes de température
|
|
|
|
|
|
|
|
|
|
|
|
|
Nettoyage des émetteurs infrarouge
|
|
|
|
|
|
|
|
|
|
|
ANNEXE 5 : Fiche de suivi du recyclage
Centre : bonaberi Folio
n°1a
Atelier : Emballages Alimentaires
FICHE DE SUIVI DU RECYCLAGE DE MATIERE PS
Recyclage des feuilles et carottes
PROCESS
|
|
Production
|
Gros
Broyeur
|
Début broyage
|
|
|
Fin broyage
|
|
|
Temps réel de
broyage
|
|
|
Temps d'interruption
|
|
Heure
début
|
|
Heure
fin
|
|
Temps
mis
|
|
Motif de
L'arrêt
|
Date : _ _ _ _ _ Quart de : _ _ _ _ h
à _ _ _ _ h fiche n° : _ _ _ _
étiquette n° : _ _ _ _
observation
|
|
INTRANTS
|
|
Produits fabriqués
|
Article
|
unité
|
|
|
Bobine de feuille
|
Kg
|
|
|
Carotte de moule
|
Kg
|
|
|
Pots non conforme
|
Kg
|
|
|
Nombre de fois où la matière a été
rebroyé :
|
EXTRANT
|
|
Produits fabriqués
|
Article
|
unité
|
|
|
Matière rebroyé
|
Kg
|
|
|
Etat de recyclage actuel :
|
MAIN D'OEUVRE
|
|
Chef d'équipe
|
Producteur
|
|
Nom
|
|
|
Visa Kg
|
|
|
Observations : Nom et Visa du chef de quart
ANNEXE 6 :Table de niveau de contrôle II et
table de critère d'acceptation et de rejet
Effectif des lots
|
Lettre code
|
Effectif des échantillonnages
|
2 à 8
9 à 15
16 à 25
26 à 50
51 à 90
91 à 150
151 à 280
281 à 500
501 à 1200
1201 à 3200
3201 à 10000
10001 à 35000
35001 à 150000
150001 à 500000
Supérieur à 500001
|
A
B
C
D
E
F
G
H
J
K
L
M
N
P
Q
|
2
3
5
8
13
20
32
50
80
125
200
315
500
800
1250
|
Table de niveau de contrôle II
Lettre code
|
n
|
A = 0
R = 1
|
A = 1
R = 2
|
A = 2
R = 3
|
A = 3
R = 4
|
A = 5
R = 6
|
A = 7
R = 8
|
A = 10
R = 11
|
A = 14
R = 15
|
A = 21
R = 22
|
A
B
C
D
E
F
G
H
J
K
L
M
N
P
Q
|
2
3
5
8
13
20
32
50
80
125
200
315
500
800
1250
|
6,5
4
2,5
1,5
1
0,65
0,4
0,25
0,15
0,1
0,065
0,04
0,025
0,015
|
10
6,5
4
2,5
1,5
1
0,65
0,4
0,25
0,15
0,1
0,065
0,025
|
10
6,5
4
2,5
1,5
1
0,65
0,4
0,25
0,15
0,1
0,04
|
10
6,5
4
2,5
1,5
1
0,65
0,4
0,25
0,15
0,065
|
10
6,5
4
2,5
1,5
1
0,65
0,4
0,25
0,1
|
10
6,5
4
2,5
1,5
1
0,65
0,4
0,15
|
10
6,5
4
2,5
1,5
1
0,65
0,25
|
10
6,5
4
2,5
1,5
1
0,4
|
10
6,5
4
2,5
1,5
0,65
|
Table de critère d'acceptation et de rejet
Taille de l'échantillon : n
ANNEXE 7 :Plan de localisation de CAMLAIT S.A
département plastique
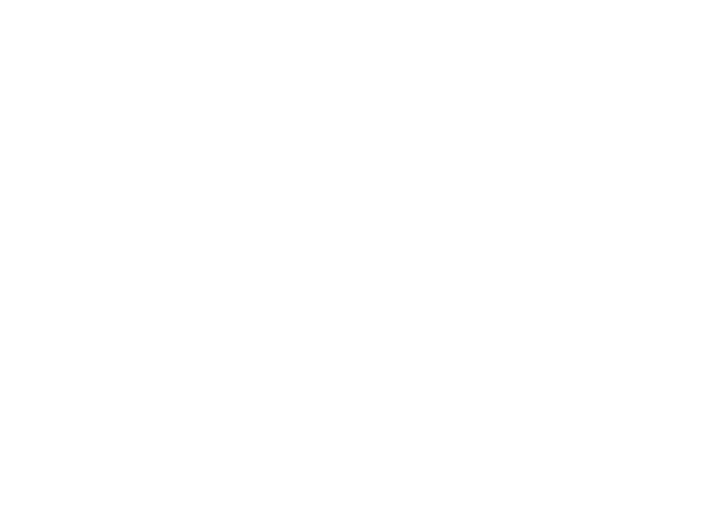
   
|
|