Dédicace

Oidimome
Je rends grace a L'Eternel créateur du ciel et
de la terre
pour ses bienfaits dans ma vie, lui qui a permis
la
réalisation de ce mémoire et qui m'a donné
la grace
d'être la aujourd' hui.



A mon pere, M. TCHIEGANG Francois qui m'a toujours montre
le droit chemin
A ma mere Mme TCHIEGANG née NGO EONE NGO NGUE
Christine, elle qui s'est sacrifice afin que je ne puisse manquer de rien
durant mes etudes
A ma sceur et mes freres
Rédigé par TCHIEGANG MBITCHA Alain Bertrand
|
1
|
Remerciements

oemerciements
Mes remerciements s'adressent en particulier :

Au Pr. Thomas TAMO TATIETSE pour l'honneur qu'il me fait de
présider ce jury.
Au Dr. DANWE RAIDANDI, mon encadreur académique pour sa
patience, sa disponibilité. A Ing. FOTSO Serge, mon encadreur
professionnel, pour ses conseils, et son attention à mon
égard.
Messieurs les membres du jury qui ont examiné ce
mémoire de fin d'études :
Pr. Thomas TAMO TATIETSE, Dr. DANWE RAIDANDI, Dr. Lucien MEVA'A,
Ing. VOUFO
Au Dr. Benoit NDZANA qui a mis à ma disposition des
documents et a consacré une partie de son temps à
l'élaboration de ce mémoire.
A tout le personnel enseignant de l'Ecole Nationale
Supérieure Polytechnique de Yaoundé.
A tout le personnel de la SCTB particulièrement du Service
Maintenance, Achat et Magasin, je pense notamment à M. Tahafo, Mlle
Ngueya, à Narcisse, à Sébastien.
A mes camarades de Promotion et spécialement mes camarades
de la classe de 5 GIND 2008 A ma famille et tous mes amis pour leurs
encouragements
A mes amis depuis le lycée Stéphane et Gabriel
A tous ceux qui m'ont encouragé et qui ont prié
pour moi, à ceux qui m'ont aidé dans les corrections.
A tous ceux qui ont contribué indirectement à
l'élaboration de ce document.
Que tout soit pour le Seigneur Jesus-Christ
Rédigé par TCHIEGANG MBITCHA Alain Bertrand
|
2
|
Glossaire

qtoss~ire
AC : Alternative Current
ADEPA : Agence nationale pour le DEveloppement
de la Production Automatisée
AFCET : Association Française pour la
Cybernétique Economique et Technique
API: Automate Programmable Industriel
AU : Arrêt d'Urgence
Bcp : Bouton coup de poing Bp :
Bouton poussoir
DC : Direct Current
EEPROM : Electrically Erasable Programmable Read
Only Memory
E/S : Entrée/Sortie
F: Fusible
FAO : Fabrication Assistée par
Ordinateur
Fc : Fin de course
FDB: Function Block Diagram (schema par
blocs)
GRAFCET: GRAphe Fonctionnel de Commande Etapes
Transitions
In : Intensité nominale
ISO: International Organization for
Standardization (Organisation internationale de normalisation)
KM : Contacteur Moteur Lc :
Levier de commande LD: Ladder Diagram (schéma
à relais)
M : Moteur
NO: Normally Open (normallement ouvert)
NC: Normally Close (normallement
fermé)
PC: Partie Commande
Ph : Photoélectrique
PO: Partie Opérative
PROM : Programmable Read Only Memory
RAM : Random Access Memory ROM :
Read Only Memory
SAP: Système Automatisé de
Production
SCTB : Société Camerounaise De
Transformation Du Bois
SFC: Sequential Function Char
ST: Structured Text (texte structuré)
TOR : Tout Ou Rien
TRH : TRancheuse Horizontale TRV :
TRancheuse Verticale VCC : Volt courant continu
VCA : Volt courant alternatif
Resume

oesume
Les objectifs de l'automatisation des systèmes sont
d'accroître la productivité, améliorer la
flexibilité ainsi que la qualité du produit et ce pour un
coût le plus faible possible en ayant recours le moins possible à
l'homme. La SCTB produit du placage tranché qui est utilisé pour
le revêtement des meubles à l'aide d'une machine spéciale
appelée `'trancheuse verticale». Ce produit est destiné au
marché extérieur. Cet outil de production vieux de part son
utilisation est soumis quotidiennement à des défaillances
accidentelles entraînant des arrêts de production et engendrant des
coûts. Soucieuse de rester compétitive dans le domaine du placage
tranché, la SCTB se doit de trouver des solutions à ce
problème. Ce document expose une solution apportée en vue de la
résolution du problème.
En effet les défaillances sont de nature
électrique et localisées dans l'armoire électrique. La
partie commande de ladite machine a été réalisée en
logique câblée. Il est question de reconcevoir la partie commande
en migrant vers la logique programmée ce qui permettra d'accroître
les performances de celle-ci et faciliter sa maintenance. Pour atteindre ces
objectifs nous avons analysé le système automatisé
existant, ensuite nous avons ressorti ses différentes
fonctionnalités ce qui a permis sa modélisation sous la base d'un
nouveau formalisme : le GRAFCET. Nous avons programmé les
séquences de fonctionnement après avoir effectué un choix
judicieux de l'automate programmable. Une simulation de l'automatisme a aussi
été effectuée. Pour la mise en service de l'automate nous
avons réalisé les schémas de câblage, et choisi
l'appareillage électrique. Le projet a été validé
est estimé à 12.577.360 FCFA.
Mots des : Automatisation, placage tranche, partie
commande, logique cablee, logique programmee.
Abstract

4:Abstract
The aim of system automation is to increase productivity,
ameliorate flexibility and the quality of the final product with the least
possible costs and human effort. SCTB produces sliced veneer, which is used in
decorating furniture, using a special machine called «trencher
vertical». This product is destined for export. This production tool due
to age and wear is subject to daily failures, causing a halt in production and
additional production costs. In a bid to stay competitive in this domain, SCTB
has to find solutions to this problem. This work proposes a solution to this
problem.
In fact, the failures are electric in nature and are localized
in the electrical command box. This command unit was cable-programmed. Hence, a
new command unit is to be designed. This system would be programmable logic
controller which would permit and increase in efficiency and facilitate
maintenance. In order to achieve this, the current automatic system was
analyzed and the different functional requirements noted. This permitted the
modeling of the control in a new manner: GRAFCET. The sequential functioning of
the controller was programmed after the programmable logic controller had been
carefully chosen. A simulation of the automatic system was also done. For the
installation of this controller, the cabling was designed and the electrical
appliance chosen. The project was validated and would cost an estimated
9.456.662 FCFA.
Keywords: Automation, sliced veneer, command unit,
cable-programmed, logic programmed.
Liste des tableaux

4,,f,iste des
tableaux
Tableau 1: Parties du Grafcet 31
Tableau 2: Boutons poussoirs 42
Tableau 3: Commandes mecaniques 43
Tableau 4: Capteurs et securites 44
Tableau 5: Verins 44
Tableau 6: Moteurs a courant continu 45
Tableau 7: Moteurs a courant alternatif 46
Tableau 8: Voyants 47
Tableau 9: Notation preactionneurs 55
Tableau 10 : Comparaison TSX 60
Tableau 11: Bilan de consommation 63
Tableau 12: TSX Premium 63
Tableau 13: Codage des entrees / sorties automate
64
Tableau 14: Bits systeme 68
Tableau 15 : Entrees API 68
Tableau 16 : Sorties API 69
Tableau 17 : References contacteurs 91
Tableau 18 : Autres references 92
Tableau 19 : References fusibles 93
Tableau 20 : Devis estimatif 93
Liste des figures

`Liste des
figures
Figure 1: Flow-sheet de fabrication placages tranches
15
Figure 2: Placage tranche 17
Figure 3: Structure dAun systeme automatise
22
Figure 4: Demarrage etoile-triangle 23
Figure 7: Grafcet 30
Figure 8:Trancheuse verticale TRV03 34
Figure 9: Bdti en fonte 35
Figure 10: Circuit hydraulique 36
Figure 11: Synoptique moteur trancheur 37
Figure 14: Chariot porte couteau 38
Figure 15: Conditionnement d'air 38
Figure 16: Synoptique du bloc de variation de vitesse du
moteur trancheur 41
Figure 17: Capteurs de contact 43
Figure 18: Grafcet principal point de vue systeme
53
Figure 19: Grafcet 1 chariot 54
Figure 20: Grafcet 1 grandes griffes 54
Figure 21: Grafcet 1 table elevatrice 55
Figure 22: Grafcet principal point de vue partie commande
56
Figure 23: Grafcet 2 chariot 57
Figure 24: Grafcet 2 grandes griffes 57
Figure 25: Grafcet 2 table elevatrice 58
Figure 26: Navigateur d'application 65
Figure 27: Configuration materielle 65
Figure 28:Configuration logicielle 66
Figure 29: Gracet principal point de vue API
70
Figure 30: Grafcet 3 chariot 71
Figure 31: Grafcet 3 grandes griffes 71
Figure 32 : Grafcet 3 table elevatrice 72
Figure 33 : Traitement sur coupure et reprise secteur
72
Figure 34: Alimentation automate 73
Figure 35: Entrees connecteur A 74
Figure 36: Entrees connecteur B 74
Figure 37: Sorties connecteur A 75
Figure 38 : Alimentation bobines contacteurs et voyants
75

Figure 39: Alimentation bobines distributeurs
...........................................................................................................................
76 Figure 40: Configuration automate du laboratoire
.....................................................................................................................
78 Figure 41: Initialisation grafcet principal
......................................................................................................................................
79 Figure 42: Initialisation grafcet grandes griffes
...........................................................................................................................
80 Figure 43: Table d'animation entree
...............................................................................................................................................
80 Figure44: Etape X4 validee
.............................................................................................................................................................
81 Figure 45: validation de la condition
.............................................................................................................................................
81 Figure46: Activation de l'etape X5
................................................................................................................................................
81 Figure47: Table d'animation sortie
................................................................................................................................................
82 Figure48: Sortie active
......................................................................................................................................................................
82 Figure49: Activation de X31
............................................................................................................................................................
83 Figure50 : Sortie %Q5.13
..................................................................................................................................................................
83 Figure51: Ecran
d'accueil..................................................................................................................................................................
85 Figure 52: Ecran principal en mode stop
......................................................................................................................................
85 Figure53: Ecran principal a l'etape X5
..........................................................................................................................................
86 Figure54: Etat des capteurs
.............................................................................................................................................................
87

$omm~ire
Dédicace
|
.1
|
Remerciements
|
..2
|
Glossaire
|
.3
|
Résumé
|
4
|
Abstract
|
..5
|
Liste des tableaux
|
..6
|
Liste des figures
|
.7
|
Sommaire
|
9
|
Introduction
|
11
|
Chapitre 1 : Contexte et Problématique
|
12
|
I. Contexte
|
13
|
1. Présentation sommaire de la SCTB Sarl
|
13
|
2. Les produits
|
13
|
3. Placages tranchés
|
14
|
|
II. Problématique
|
17
|
Chapitre 2 : Généralités sur
l'automatique
|
..19
|
I. Définitions
|
20
|
II. Différents types de systèmes automatisés
|
20
|
III. Etude logique et l'étude dynamique des
systèmes
|
21
|
IV. Système automatisé de production (S.A.P)
|
21
|
V. Partie Opérative
|
22
|
VI. Les automates programmables industriels
|
24
|
Chapitre 3 : Démarche de résolution du
problème
|
.27
|
I. Partie commande 28
II. Modélisation des systèmes séquentiels
29
III. Une méthode d'étude des systèmes
séquentiels : le GRAFCET 30
VI. Méthodologie 32
Chapitre 4 : Analyse du système automatisé
existant .33
I. Etat des lieux 34
II. Description 34
III. Constitution 35
IV. Procédures avant le tranchage 39
V. Systèmes de variation de vitesse du moteur trancheur
et de freinage 40
VI. Organes de commandes et capteurs 42
VII. Actionneurs 44
VIII. Problème rencontré au niveau de la centrale
hydraulique 47
Chapitre 5 : Modélisation 49
I. Analyse des différentes fonctionnalités de la
machine 50
II. Grafcet point de vue système 52
III. Grafcet Partie commande 55
Chapitre 6 : Programmation des séquences de
fonctionnement et câblage entrées / sorties 59
I. Etude architecturale 60
1. Choix de l'automate 60
2. Présentation 61
3. Configuration matérielle 62
4. Codage des entrées sorties de l'automate 64
5. Configuration logicielle 64

6. Programmation sous PL7 Pro
|
66
|
7. Notion de cycle de scrutation
|
66
|
8. Les objets adressages
|
67
|
II. Mise en oeuvre des séquences du système
automatisé
|
68
|
1. Entrées API
|
68
|
2. Sorties API
|
69
|
3. Grafcet point de vue API
|
69
|
III. Câblage des entrées / sorties
|
73
|
1. Alimentation de l'automate
|
73
|
2. Alimentation des entrées de l'automate
|
74
|
3. Alimentation des sorties de l'automate :
|
75
|
Chapitre 7 : Simulation
|
..77
|
I. Test du programme : simulation
|
78
|
II. Ecrans d'exploitation
|
84
|
|
Chapitre 8 : Analyse financière
|
.88
|
I. Choix des appareillages électriques
|
89
|
II. Devis estimatif
|
91
|
|
Conclusion
|
94
|
Références bibliographiques
|
..95
|
Annexes
|
97
|
Introduction

jntroduetion
Les arrêts de production dues aux défaillances
partielles ou complètes de l'outil de production ont pour
conséquences l'indisponibilité machine, la perte de rendement et
engendrent des coûts :
~ de mesures palliatives
~ de pénalités contractuelles
~ de perte de production, manque à gagner ~ de stocks
intermédiaires
Conscient de cela, le Service Maintenance de la SCTB s'est
lancé dans une politique de réhabilitation de ses outils de
production visant ainsi à améliorer leurs performances. Cette
réhabilitation avait déjà concernée certaines
machines (massicots, séchoirs). L'objectif cette fois est de refaire la
partie commande des trancheuses verticales : migrer vers la logique
programmée.
C'est dans cette optique que se situe le travail qui nous a
été confié et ayant pour thème :
»Amélioration Des Performances De La Trancheuse verticale TRV 03 de
la SCTB Sarl ».
Le présent document résume le travail
effectué, il s'articule en huit chapitres. Le contexte et la
problématique figurent dans le premier chapitre où nous
présentons la SCTB et les principales étapes de
réalisation du placage tranché. Le chapitre deux porte sur les
généralités sur l'automatique. Le chapitre trois est celui
de la démarche adoptée pour la résolution du
problème. Dans les chapitres quatre à sept, nous analysons le
système automatisé existant, le modélisons, programmons
les séquences de fonctionnement et simulons l'automatisme. Enfin le
dernier chapitre est réservé à une analyse
financière du projet.
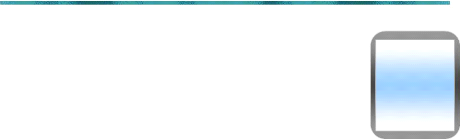
Chapitre
1
CHAPITRE 1 :
Contexte et problimatique

I. Contexte
1. Presentation sommaire de la SCTB Sarl
Située à NSAM à l'entrée de la
ville de Yaoundé venant de Douala, la Société Camerounaise
De Transformation Du Bois en abrégé SCTB est une filiale du
Groupe FOKOU. Elle est à l'heure actuelle l'une des plus grandes
structures dans la transformation du bois au CAMEROUN et dans la sous
région AFRIQUE CENTRALE vu la diversité de ses produits (Grumes,
Placage déroulé, placage tranché, Contreplaqué,
Bois débité) et sa capacité de production annuelle
d'environ 100 000 m3.
Ses produits sont destinés à l'Europe, l'Asie,
l'Amérique, l'Afrique et leur demande sans cesse croissante montrent
qu'au niveau de la qualité, la SCTB Sarl reste compétitive sur le
marché du bois dans le monde entier et entend aller plus loin à
travers la certification de ses activités aux normes ISO dans un avenir
très proche.
2. Les produits Les produits de la
SCTB Sarl sont destinés à diverses
utilisations :
· LES GRUMES
Elles sont principalement utilisées comme
matière première dans les unités de
transformation de bois et à partir d'elles on peut obtenir : des
débités ; du placage tranché ; du placage
déroulé ; du copeau de bois ; de la pâte à
papier.
· LE PLACAGE TRANCHE
Le placage tranché est utilisé pour le
revêtement des meubles, la décoration murale et
la fabrication des tableaux en mosaïque. Il est beaucoup plus
prisé à cause de ses motifs décorateurs que forment les
fils du bois. Le choix des différents types de motifs se fait au
départ lors de la production des quater lots.
· LE PLACAGE DEROULE
Le placage déroulé quant à lui est
utilisé principalement pour le revêtement des meubles, des murs et
la fabrication des contreplaqués à âmes.
· LE CONTRE PLAQUE
En construction, celui-ci est le plus souvent utilisé pour
les faux-plafonds, le coffrage des murs pour les grandes
constructions, les constructions des cases provisoires... En
ameublement, les contreplaqués

servent à faire des maquettes pour certaines
pièces à produire avec des formes irrégulières ;
à fabriquer des meubles (caisses ; classeurs) pour ce dernier
cas, ils sont très souvent habillés de feuilles de placage
tranchées ou de formicas.
· LE BOIS DEBITE
Principalement utilisé pour l'ameublement, le bois
débité sert, en menuiserie et ébénisterie pour la
fabrication des meubles, pour les décorations
intérieures (faux-plafond en lambris ; lambris de hauteurs ; lambris
muraux ; sol en parquets ...) et extérieures (maisons en bois ...)
; en construction, il est utilisé pour les moulures, les charpentes
en bois et les solivages.
Mais tout part de l'exploitation forestière, la SCTB
Sarl dispose de plusieurs forets riches en essences les plus sollicitées
sur le marché des bois tropicaux pour pouvoir satisfaire le
ravitaillement de toutes ses unités de production en matière
première bois et la satisfaction de ses clients acheteurs de grumes.
3. Pla cages tranches
Que signifie le mot placage ?
Le placage est une feuille de bois destinée à la
marqueterie. Les épaisseurs varient de 3/10e de mm à
9/10e pour un placage tranché ou déroulé, et de
12/10e à 50/10e de mm pour du placage
scié.
Que signifie le terme tranchage ?
Après un étuvage consistant à tremper la
bille de bois, dans un bain d'eau bouillante afin de la faire ramollir, on la
découpera en fines feuilles sur toute sa longueur, à l'aide d'une
machine appelée trancheuse.
4.1. Flow-sheet de fabrication pla cages
tranches
La figure ci-après nous montre le processus de fabrication
du placage tranché.


















Figure 1: Flow-sheet de fabrication placages tranchés
4.2. Principales etapes de fabrication
Le Sapelli, l'Aniegre, le Lati sont les essences de bois
utilisés pour le placage tranché. Les grumes ou billes de bois
qui proviennent de la forêt sont réceptionnées au Parc
à Grume. Ce dernier assure :

- Le contrôle des données (volume de la grume)
- L'attribution des numéros et fiche technique à
chaque bille
- Le traitement du bois
1. LE TRONÇONNAGE (PARC)
Le tronçonnage peut être exécuté,
parfois, sur le lieu d'abattage. Mais la SCTB comme beaucoup de scierie
reçoit des bois aussi longs que possible et les longueurs de
découpe sont déterminées en se basant sur les longueurs
demandées par la clientèle. Il se fait à la
tronçonneuse à chaîne et doit être parfaitement
perpendiculaire à l'axe de la bille.
2. PREPARATION/SCIAGE
Les billons sont sciés en dosses ou quartiers dans le but
de faciliter le tranchage et obtenir un rendement élevé.
3. ETUVAGE
Des bois verts ou des bois très tendres peuvent
être travaillés sans étuvage préalable. Mais c'est
un cas relativement rare. Les étuves sont des bacs en ciment où
l'on envoie de la vapeur détendue pour ramollir les fibres avant le
tranchage. Les bois restent en général 48 heures dans les
étuves de façon à laisser pénétrer la vapeur
jusqu'au coeur, mais les bois plus dur doivent être « bouillis
» à l'eau chaude.
4. NETOYAGE/ECORSAGE
Il est fait généralement à la hache. On
veille avec un soin tout particulier à l'élimination de la terre,
de l'écorce et des petits cailloux retenus par les souches (de noyer par
exemple). Il est essentiel afin d'éviter des affûtages ou des
détériorations des outillages.
5. TRANCHAGE
La dosse nettoyée est découpée en fines
feuilles sur toute sa longueur, à l'aide d'une machine appelée
trancheuse.
6. SECHAGE
Il s'agit de ramener l'humidité des placages qui, en
sortant des machines, contiennent 40 à 60 % d'eau, à un taux de
10 à 15 %.
7. PAQUETAGE ET COLISAGE Les tranches sont
rangées en paquet et disposées sur des palettes traitées
suivant la norme de la FAO.
8. MASSICOTAGE
|
9.
|
|
|
Rédigé par TCHIEGANG MBITCHA Alain Bertrand
|
16
|

Les déchets et les défectuosités sont
éliminés par des massicots et des dresseuses. Ce sont des
couteaux à guillotine de 3 à 4 m de long, destinés
à dresser les paquets de placage en long et en travers. Elles
fonctionnent en marche continue ou coup par coup.
9. EMBALLAGE ET STOCAKGE
Les produits finis sont emballés avec de la polyamine et
stockés.
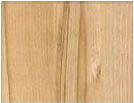
Figure 2: Placage tranché
II. Problematique
Les machines nécessaires à une industrie de
tranchage sont coûteuses et nécessitent des investissements
importants. Un équipement complet comprend au moins deux trancheuses,
une scie verticale, plusieurs guillotines, des étuves ou bouillottes,
une chaudière, des séchoirs, de vastes magasins pour entreposer
des placages. Au Cameroun nombreuses sont les entreprises qui achètent
de l'étranger des machines industrielles de seconde main. Ces machines
vieilles par leur utilisation et la technologie utilisée ne disposent le
plus souvent des documents techniques nécessaires pour assurer une
maintenance corrective en cas de défaillance. La SCTB Sarl pour produire
une quantité importante de placage tranché (en
moyenne 4,64 m3 par mois), possède 3
trancheuses (2 trancheuses verticale, 1 trancheuse horizontale).
Actuellement une seule trancheuse (trancheuse verticale N°3)
est en état de marche. C'est elle qui assure la production des placages
tranchés.
D'après le service maintenance, elle tombe
régulièrement en panne (au lendemain d'un jour de production,
elle ne démarre plus) et le temps de recherche de la défaillance
ainsi que le temps de diagnostic sont élevés entraînant des
retards en production et des coûts (coût de stockage,
pénalités contractuelles...).
Le prix moyen de vente d'un mètre carré de
placage tranché est de 492 FCFA et la production moyenne
journalière est de 464 m2. Le temps moyen de
réparation étant de trois jours en un mois, nous avons une
immobilisation financière de 684.864 FCFA.

Par ailleurs cette machine a un fonctionnement complexe difficile
à maîtriser par les maintenanciers présents à
l'usine (défavorable pour une intervention rapide en cas de panne).
Les défaillances ont été
localisées dans la partie commande qui toutefois a été
réalisée en logique câblée avec des composants
électriques (en grand nombre dans l'armoire électrique) qui
aujourd'hui dépassés n'existent plus sur le marché. Ces
composants (contacteurs, bobines à relais) ont plus de chance
aujourd'hui d'être défaillants. De plus il n'existe pas une
documentation technique (schémas électriques) et un
repérage des fils électriques n'a été
effectué dans ladite armoire.
Pour pallier à ces problèmes, il nous a
été confié ce travail visant le passage à la
logique programmée et ayant le cahier de charge suivant :
- Avantages et inconvénients de la logique
câblée et la logique programmée
- Analyse et amélioration du système
automatisé existant
- Modélisation du système
- Programmation des séquences de fonctionnement du
système
- Câblage des entrées / sorties de l'automate
- Simulation et analyse financière
Nous commencerons ce travail par un chapitre, essentiel pour la
compréhension de ce qui sera fait par la suite et portant sur
l'automatique, l'automatisme et les automates programmables industriels.
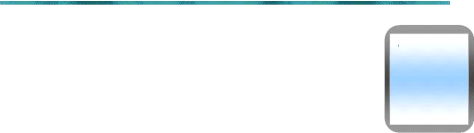
Chapitre
2
CHAPITRE 2 :
goneralites sur l~automatique

I. Definitions
L'automatique est à la fois une science et une technique
qui étudie les méthodes scientifiques et les moyens techniques
pour la conception et la réalisation des systèmes
automatisés.
L'automatisation est l'exécution automatique de
tâches domestiques, industrielles, administratives ou scientifiques sans
intervention humaine. [5]
Des systèmes automatisés permettent :
· De réaliser des opérations trop complexes
ou dangereuses et ne pouvant être confiées à l'homme
(alunissage d'un engin spatial, maintenance et contrôle dans les
centrales nucléaires)
· De substituer l'homme dans les opérations
répétitives ou pénibles (électroménager,
boîte de vitesses automatique, embrayage piloté)
· D'accroître la précision (applications
militaires, gestion électronique de moteur thermique, pilote
automatique)
· D'accroître la rentabilité et la
productivité par la diminution de la main-d'oeuvre (chaîne de
montage, atelier automatisé) [5]
II. Differents types de systemes automatises
· Systèmes linéaires, continus et
invariants
Les grandeurs d'entrée et de sortie évoluent de
manière continue en fonction du temps.
· Systèmes combinatoires
Les grandeurs d'entrée et de sortie sont des grandeurs
binaires. La commande est appelée TOR (Tout Ou Rien). Les grandeurs de
sortie s'expriment comme une combinaison des grandeurs d'entrée.
· Systèmes séquentiels
Les grandeurs d'entrée et de sortie sont des grandeurs
binaires. Les grandeurs de sortie ne peuvent pas s'exprimer comme une
combinaison des grandeurs d'entrée. En effet pour un même
état des entrées, on n'a pas forcément les même
sorties. Une notion d'état du système, de mémoire, se
rajoute. [5]
Les systèmes logiques sont des
systèmes pour lesquels toutes les variables
d'état (entrées ou sorties) peuvent être
représentées par des variables du type logique (signal
binaire).

III. Etude logique et l'etude dynamique des
systemes
L'étude logique est
complémentaire de l'étude dynamique des
systèmes linéaires ou asservis. Un système
automatisé est constitué de plusieurs chaînes
d'actions. [16]
1. L'etude dynamique
L'étude dynamique des asservissements
consiste à étudier une seule chaîne
d'action afin d'optimiser les différents éléments
de cette chaîne pour qu'elle réponde au cahier de charges.
Exemple d'un asservissement en vitesse d'un moteur
électrique :
Il s'agit d'étudier l'état transitoire entre
l'arrêt et le régime permanent
2. L'etude logique
L'étude logique consiste à
étudier et décrire l'évolution de l'état du
système dans sa globalité, il s'agit de tenir compte de
l'état de toutes les chaînes d'actions en
même temps. [16]
Dans ce cas on considère que l'état du
système ne sera décrit que par des variables binaires :
C'est cette étude (étude logique) que nous
mènerons tout au long de ce rapport.
Exemple : pour un moteur électrique,
On ne tiendra pas compte du régime transitoire du moteur.
On considèrera que le `'problème» a été
réglé par l'étude de la commande.
IV. Systeme automatise de production (S.A.P)
Un système automatisé est un ensemble
d'éléments en interaction, et organisés dans un but
précis : agir sur une matière d'oeuvre afin de
lui donner une valeur ajoutée. [5]
1. Structure d'un systeme automatise :
Tout système automatisé peut se décomposer
selon le schéma ci-après :
Rédigé par TCHIEGANG MBITCHA Alain Bertrand
|
21
|
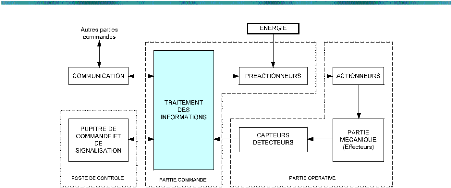
Figure 3: Structure d'un système automatisé
[5]
o Partie opérative : Elle agit sur la
matière d'oeuvre afin de lui donner sa valeur ajoutée.
o Partie commande : Coordonnant la succession
des actions sur la partie opérative avec la finalité d'obtenir
cette valeur ajoutée.
o Poste de contrôle : Composé des
pupitres de commande et de signalisation, il permet à
l'opérateur de commander le système (marche, arrêt,
départ cycle ...). Il permet également de visualiser les
différents états du système à l'aide de voyants.
V. Partie Operative
Le déplacement d'un élément de machine
outil, de mécanisme ou d'appareillage, actionné
électriquement, est du à l'un des organes moteurs suivants :
moteur électrique, vérin électro-hydraulique ou
électro-pneumatique. [2]
1. Machines electriques (Moteurs)
Une machine électrique est un
dispositif électromécanique permettant la conversion
d'énergie électrique en énergie
mécanique. Les machines électriques produisant une
énergie électrique à partir d'une énergie
mécanique sont appelées dynamos,
alternateurs ou générateurs
suivant la technologie utilisée. Les machines électriques
produisant une énergie mécanique à partir d'une
énergie électrique sont appelées des
moteurs. [6]
Les machines tournantes
Les machines tournantes sont constituées de deux parties
principales. Le stator est la partie fixe du système.
Il entoure la partie tournante, appelée rotor. On
distingue :

Les machines à courant continu
La machine à courant continu est une machine
électrique tournante qui fonctionne, comme son nom l'indique, à
partir de tensions et de courants continus.
Machines à courant alternatif
Ces moteurs alternatifs se déclinent en deux types :
· Les moteurs asynchrones
· Les moteurs synchrones : souvent utilisé comme
génératrice. Comme le nom l'indique, la vitesse
de rotation de ces machines est toujours proportionnelle à
la fréquence des courants qui les traversent. [6]
Demarrage des moteurs asyn chrones
Lors de la mise sous tension d'un moteur asynchrone, celui-ci
provoque un fort appel de courant qui peut provoquer des chutes de tension
importantes dans une installation électrique. Pour ces raisons en
autres, il faut parfois effectuer un démarrage différent du
démarrage direct. Il est donc logique de limiter le courant pendant le
démarrage à une valeur acceptable. [5]
Outre le démarrage direct, nous pouvons citer le
démarrage étoile- triangle
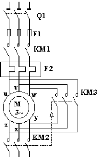
Figure 4: Démarrage
étoile-triangle
2. Les Verins
Ils transforment l'énergie d'un fluide sous pression en
énergie mécanique (mouvement avec effort). Ils peuvent soulever,
pousser, tirer, serrer, tourner, bloquer, percuter, ...
Leur classification tient compte de la nature du
fluide, pneumatique ou hydraulique, et du
mode d'action de la tige : simple effet (air comprimé
admis sur une seule face du piston), double effet (air
comprimé admis sur les deux faces du piston)... [5]

Figure 6:Vérin simple effet classique rappel par
ressort
|
Figure 5:Vérin double effet
|
VI. Les automates programmables industriels
1. Definition
L'Automate Programmable Industriel (API) est un appareil
électronique programmable, adapté à l'environnement
industriel, qui réalise des fonctions d'automatisme pour assurer la
commande de préactionneurs à partir d'informations logiques,
analogiques ou numériques. [5]
Les API sont spécialement conçus pour traiter,
par un programme, des problèmes de logique séquentielle (ou
combinatoire) afin de remplacer les commandes d'automatismes en logique
câblée réalisée avec des circuits logiques ou des
relais.
2. Avantages
- emploi facile par des personnes non qualifiés en
informatique, grâce à des langages de programmation de type
langage à relais, équations booléennes ou GRAFCET.
- Conçus pour fonctionner en milieu industriel, afin de
remplacer les armoires à relais.
3. Nature des informations traitees par l'automate
:
Les informations peuvent être de type :
- Tout ou rien (T.O.R.) : l'information ne peut
prendre que deux états (vrai/faux, 0 ou 1 ...).
- Analogique : l'information est continue et
peut prendre une valeur comprise dans une plage bien
déterminée.
- Numérique : l'information est contenue
dans des mots codés sous forme binaire ou bien hexadécimale.
4. Architecture des automates Aspect exterieur
:
Les automates peuvent être de type compact
ou modulaire.
De type compact, Il intègre le processeur,
l'alimentation, les entrées et les sorties. Ces automates, de
fonctionnement simple, sont généralement destinés à
la commande de petits automatismes.
Généralités sur
l'automatique

De type modulaire, le processeur, l'alimentation et les
interfaces d'entrées / sorties résident dans des unités
séparées (modules) et sont fixées sur un
ou plusieurs racks contenant le "fond de panier" (bus plus
connecteurs).
Ces automates sont intégrés dans les automatismes
complexes où puissance, capacité de traitement et
flexibilité sont nécessaires.
Structure interne :
Module d'alimentation : il assure la
distribution d'énergie aux différents modules.
Unité centrale : à base de
microprocesseur, elle réalise toutes les fonctions logiques,
arithmétiques et de traitement numérique (transfert, comptage,
temporisation ...).
Le bus interne : il permet la communication de
l'ensemble des blocs de l'automate et des éventuelles extensions.
Mémoires : Elles permettent de stocker le
système d'exploitation (ROM ou PROM), le programme (EEPROM) et les
données système lors du fonctionnement (RAM).
Interfaces d'entrées / sorties :
· Interface d'entrée : elle permet
de recevoir les informations du S.A.P. ou du pupitre et de mettre en forme
(filtrage, ...) ce signal tout en l'isolant électriquement
(optocouplage).
· Interface de sortie : elle permet de
commander les divers préactionneurs et éléments de
signalisation du S.A.P. tout en assurant l'isolement électrique [5]
5. Criteres de choix d'un automate
Un automate utilisant des langages de programmation de type
Grafcet est préférable pour assurer les mises au point et
dépannages dans les meilleures conditions.
La possession d'un logiciel de programmation (PL7 Junior/Pro...)
est aussi source d'économies (achat du logiciel et formation du
personnel). Des outils permettant une simulation des programmes sont
également souhaitables. [5]
Ensuite les besoins doivent être quantifiés.
m Nombre d'entrées/sorties : le nombre
de cartes peut avoir une incidence sur le nombre de racks dès que le
nombre d'entrées/sorties nécessaires devient
élevé.
m Type de processeur : la taille
mémoire, la vitesse de traitement et les fonctions spéciales
offertes par le processeur permettront le choix dans la gamme souvent
très étendue.

0 Fonctions ou modules spéciaux :
certaines cartes (commandes d'axe, pesage...) permettront de
`'soulager» le processeur et devront offrir les
caractéristiques souhaitées (résolution,...)
0 Fonctions de communication : l'automate doit
pouvoir communiquer avec les autres systèmes
de commande (API, supervision...) et offrir des
possibilités de communication avec des standards
normalisés (Profibus...)
6. Langages de programmation pour API
La norme IEC 1131-3 définit entre autres choses, cinq
langages qui peuvent être utilisés pour la programmation
d'applications d'automatisme. [10]
Les cinq langages sont :




SFC (« sequential function char ») :
issu du langage GRAFCET, ce langage, de haut niveau, permet la programmation
aisée de tous les procédés séquentiels ;
FBD (« function block diagram », ou
schéma par blocs) : ce langage permet de programmer graphiquement
à l'aide de blocs, représentant des variables, des
opérateurs ou des fonctions. Il permet de manipuler tous les types de
variables ;
LD (« ladder diagram », ou
schéma à relais) : ce langage graphique est essentiellement
dédié à la programmation d'équations
booléennes (true/false) ;
ST (« structured text » ou texte
structuré) : ce langage est un langage textuel de haut niveau,
particulièrement adapté à la programmation de fonctions
arithmétiques complexes, manipulations de tableaux, gestion de
messages...
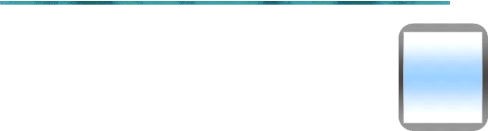
Chapitre
3
CHAPITRE 3 :
.2)emarche de resolution du problem~
Introduction :
Le but de ce chapitre est de presenter la methode adoptee
pour la resolution du probleme, mais avant cela il semble interessant de
presenter :
o les avantages et inconvenients qu'offrent la logique
cablee et la logique programmee o une methode d'etude des
systemes sequentiels.

La logique programmée est à définir par
opposition à la logique câblée, qu'elle soit combinatoire
ou séquentielle.
I. Partie commande
1. La logique cablee
L'automatisme est obtenu en reliant entre eux les
différents constituants de base ou fonctions logiques par câblage.
La logique câblée correspond à un traitement
parallèle de l'information. Plusieurs constituants peuvent être
sollicités simultanément. [8]
Elle est étudiée et réalisée une
fois pour toutes sur un schéma donné : Les fonctions sont
réalisées par voie matérielle. Elle exige un
grand nombre de composants et rend les montages encombrants et chers. Enfin,
elle n'offre guerre de souplesse : la durée des études pour
réaliser un montage donné (et donc pour le modifier le cas
échéant) est longue.
- les applications nouvelles
Le gain : le micropresseur est d'une
grande souplesse, car les fonctions sont réalisées par
voie logicielle, et sont modifiables à
tout moment en un temps réduit. De
plus, le nombre de composants est réduit à sa plus simple
expression.
Les limites :
- Limite inférieure : si la fonction
à réaliser est trop simple, il est plus économique de
conserver une logique câblée.
- Limite supérieure : si le nombre
d'unités à réaliser est très important, il est plus
économique de la fabriquer en circuits intégrés à
la demande ou en logique câblée pour des fonctions simples.
2. Logique programmee
Elle correspond à une démarche séquentielle,
seule une opération élémentaire est exécutée
à la fois, c'est un traitement série. Le schéma
électrique est transcrit en une suite d'instruction qui constitue le
programme. En cas de modification des équations avec les mêmes
accessoires, l'installation ne comporte aucune modification de câblage
seul le jeu d'instructions est modifié. [8]
Si un circuit est réalisé en logique
programmée, il utilisera moins de composants puisque ceux-ci
réalisent directement les fonctions logiques désirées. Un
circuit ayant moins de composants sera habituellement moins coûteux
à concevoir, réaliser et distribuer. La réduction du
nombre de composants électroniques tend aussi à augmenter la
fiabilité des circuits et à réduire la consommation
énergétique.

L'automate simplifie grandement le schéma de la logique
câblée prenant en compte tout ce qui est extérieur à
la programmation, comme les voyants. Il sert pour se substituer à une
partir commande complexe qu'on programmera dans un automate.
Automatiser avec les automates pour :
- réduire les coûts d'ingénierie
- réduire les coûts de maintenance
Le choix du type d'une logique pour résoudre un
problème, dépend de plusieurs critères :
Complexité ; coût ; évolutivité ;
rapidité.
3. Logique cablee v.s programmee
Logique câblée
n Inconvénients
o Volume du contrôleur proportionnel à la
complexité du problème
o Des modifications de la commande impliquent des modifications
de câblage
n Avantages
o Vitesse car fonctionnement simultané des
opérateurs [7]
Logique programmée
n Avantages
o Banalisation du matériel : même matériel
quel que soit la fonction logique à réaliser
o Facilité de modification de la loi de contrôle :
il suffit de modifier le programme. Simplification de la maintenance !
o Faible liaison entre le volume matériel et la
complexité du problème (effet simplement
sur les entrées/sorties et taille mémoire)
n Inconvénients
o Vitesse inversement proportionnelle à la
complexité du problème.
Ceci peut être une limitation pour les processus
électromécaniques rapides [7]
II. Mod~lisation des systemes sequentiels
La modélisation d'un système
séquentiel est la traduction de son cahier de charge (suite de phrase
décrivant le fonctionnement désiré du système) en
un formalisme qui ne permet aucune erreur d'interprétation. [9]
Comme modèle nous pouvons citer : le chronogramme
(diagramme des temps), le graphe de fluence, les tableaux d'état, le
graphe d'état, le graphe d'événement, le GRAFCET, les
Réseaux de Pétri.

Nous nous intéresserons plus particulièrement au
Grafcet car il permet de représenter le fonctionnement de la partie
commande des systèmes automatisés de production.
III. Une méthode d'étude des systemes
séquentiels : le GRAFC ET
L'AFCET (Association
Française pour la Cybernétique
Economique et Technique) et l'ADEPA
(Agence nationale pour le DEveloppement de la
Production Automatisée) ont mis au
point et développé une représentation graphique qui
traduit, sans ambiguïté, l'évolution du cycle d'un
automatisme séquentiel.
Ce diagramme fonctionnel: le GRAFCET (Graphe
Fonctionnel de Commande,
Etapes Transitions) permet de décrire
les comportements attendus de l'automatisme en imposant une démarche
rigoureuse, évitant ainsi les incohérences dans le
fonctionnement. [5]
1. De'initions
Le Grafcet est défini par un ensemble constitué
:
- d'éléments graphiques de base
comprenant : les étapes, les transitions, les liaisons
orientées.
- d'une interprétation traduisant le
comportement de la partie commande vis-à-vis de ses entrées et de
ses sorties, et caractérisée par les réceptivités
associées aux transitions et les actions associées aux
étapes.
- de 5 règles d'évolution
définissant formellement le comportement dynamique de la partie
commande. (voir annexe 1)
- d'hypothèses sur les durées
relatives aux évolutions.
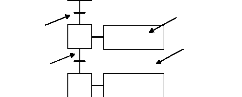
Transition
Liaison
2
1
Fin de perçage
Déplacer
Percer
Action
Récéptivité
associée à la transistion
Figure 7: Grafcet
Rédigé par TCHIEGANG MBITCHA Alain Bertrand
|
30
|

Tableau 1: Parties du Grafcet [5]
Etape:
|
une étape représente une situation stable de la
PC
Une étape est soit active soit inactive. On peut associer
à chaque étape i une variable Xi image de son activité.
ex: Etape 2 active 4 X2 = 1 Etape 2 inactive
4 X2 = 0
|
Etape initiale:
|
étape active au début du fonctionnement.
Elle se représente par un double carré.
|
Liaisons orientées:
|
Elles relient les étapes aux transitions et les
transitions aux étapes. Le sens général d'évolution
est du haut vers le bas. Dans le cas contraire, des flèches doivent
être employées
|
Transitions :
|
une transition indique une possibilité d'évolution
d'activité entre deux ou plusieurs étapes. Cette évolution
s'accomplit par le franchissement de la transition.
|
Réceptivité :
|
La réceptivité associée à une
transition est une fonction logique : - des entrées (capteurs, commande
opérateur)
- des activités des étapes (Ex : X1 pour
étape 1 active.)
- des variables auxiliaires (Ex : [C1=10] pour un test sur
compteur C1)
|
Action:
|
L'action indique, dans un rectangle, comment agir sur la variable
de sortie, soit par assignation (action continue), soit par affectation (action
mémorisée)
|
2. Construction des grafcets
La construction des grafcets peut se faire avec ou sans
méthode. [13]
1. Sans méthode = « A l'intuition
»
Envisageable pour des automatismes simples, à faible taux
de parallélisme.
2. Avec méthode = approche basée sur les
fonctions
Il exprime les fonctions à assurer auxquelles sont
associées des contraintes.
Avec méthode = approche basée sur une
analyse fonctionnelle
> Conception mécanique
· La décomposition fonctionnelle conduit à
choisir des constituants physiques (un vérin, un capteur inductif, une
butée, un convoyeur ...)
· Les constituants sont « localisés » dans
l'espace
> Automatisation
· La décomposition fonctionnelle conduit à
définir des actions (actionner un vérin, mise en route d'un
moteur, déclenchement d'une alarme ...)
· Les actions sont « synchronisées » dans
le temps (=> grafcet)

3. Les differents points de vue du GRAFCET
Il existe 3 représentations du fonctionnement d'un
système par le GRAFCET :
- le GRAFCET point de vue système qui représente
le fonctionnement du système tel que le voit quelqu'un
d'extérieur à celui-ci.
- le GRAFCET point de vue Partie Opérative qui
représente le fonctionnement du système tel que le voit quelqu'un
connaissant la PO de celui-ci.
- le GRAFCET point de vue Partie Commande qui représente
le fonctionnement du système tel que le voit quelqu'un connaissant tout
le système.
VI. Methodologie
La méthode adoptée pour la résolution du
problème est la suivante :
=> Une analyse du système automatisé existant
=> Une analyse de ces différentes
fonctionnalités qui sera suivie de la modélisation du
système
=> La programmation des séquences de fonctionnement
qui s'articulera comme suit :
o Le choix de l'automate
o Sa configuration matérielle et logicielle
o La mise en oeuvre des séquences de fonctionnement
o Le câblage des entrées / sorties
=> Une simulation
=> Le choix des appareillages électriques
=> Une analyse financière du projet
Conclusion :
La logique programmée a de nombreux avantages par rapport
à la logique câblée. Toutefois le choix du type d'une
logique pour la résolution d'un problème dépend de
plusieurs critères.
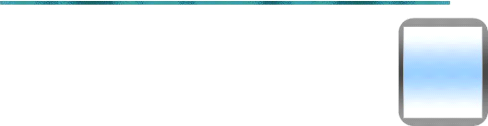
Chapitre
4
CHAPITRE 4 :
cAnalyse du systeme
automatise existant
Introduction :
Le traitement des donnees au niveau de la trancheuse
verticale est effectue par des contacteurs auxiliaires et des relais
d'automatisme.
Le fonctionnement des equipements en logique cablee est
defini par le schema de cablage qui n'existe pas pour cette machine. Nous nous
proposons dans ce chapitre de faire une analyse du systeme
automatise.

I. Etat des lieux
Type : Machine américaine type «
capital »
De seconde main et de plus de 50 ans [17]
1ère mise en service à la SCTB :
1er juillet 2002
Prix d'achat : 120 000 000 FCFA
Alimentation générale :
réseau triphasé 380 V
Caractéristiques du disjoncteur : de
type Merlin Gerin, Compact
NS 250 N
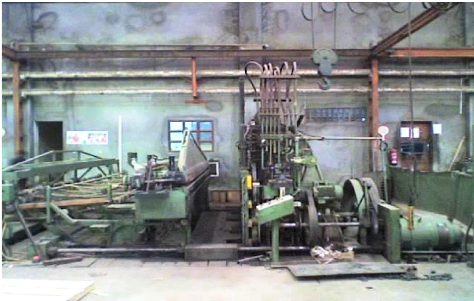
Figure 8:Trancheuse verticale TRV03
II. Description
C'est une machine américaine type « Capital »
qui produit des placages par déplacement de la grume (dosse) devant le
couteau. La grume est fixée sur un bâti en fonte
à l'aide des griffes (petites et grandes griffes) et
elle se déplace verticalement, tandis que le couteau de
3 à 4 m de longueur est fixé sur un chariot
mobile. La cadence peut aller jusqu'à 30 coups minute. C'est
une machine adaptée pour trancher les placages de bois tropicaux
à fil droit. Elle fonctionne à poussée par bielle.
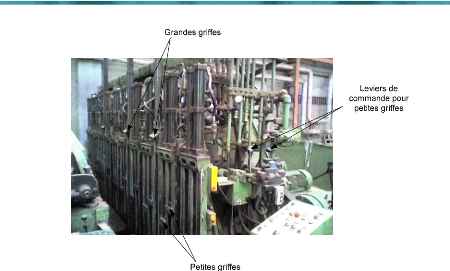
Figure 9: Bâti en fonte
III. Constitution
Comme toutes les autres trancheuses, elle est constituée
d'un bâti en fonte et d'un couteau. En plus de ces éléments
on retrouve : une centrale hydraulique, une centrale de lubrification, le
moteur trancheur (moteur principal), un chariot mobile, une table
élévatrice, un circuit pneumatique.
1. La centrale hydraulique
Elle permet aux vérins hydrauliques (où en bout de
tige sont montées des griffes : petites et grandes griffes) d'assurer
leur fonctionnalité qui est de maintenir solidaire la grume (dosse) sur
le bâti en fonte. La pression exercée sur le fluide (huile 40) est
transmise à travers le système par ce dernier.
Elle comporte quatre composants mécaniques :
réservoir (50 litres), filtre, pompe, valves de commande. Le fluide
hydraulique (huile 40) qu'elle contient remplit quatre fonctions simples :
· transmission d'énergie
· lubrification des composants - pompe, valves et joints
· protection du système, par élimination des
contaminants
o humidité
o souillures
o chaleur
o air
· étanchéité entre les composants
internes
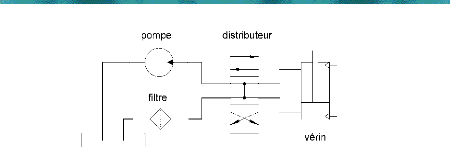

Figure 10: Circuit hydraulique
2. Centrale de lubrifi cation
Nous avons dit précédemment que la grume se
déplace verticalement. En effet elle est fixée sur le bâti
en fonte ou « bâti porte grume ». Ce dernier monté sur
des glissières effectue un mouvement rectiligne sinusoïdal
(bas-haut). La lubrification de ces glissières est assurée par
cette centrale.
3. Moteur tran cheur
C'est le moteur principal de la trancheuse. C'est un moteur
à courant continu. Il dispose :
- D'une plage de vitesse étendue
permettant d'optimiser la vitesse de coupe
- D'un couple élevé à base
vitesse, pour pouvoir soulever la grume
Son mouvement de rotation est transmis à un arbre (arbre
de transmission) sur lequel est monté un pignon par un
système poulie-courroie. Le pignon engraine sur deux
grandes roues dentées qui par un système bielle-
manivelle transmet leur mouvement de rotation au « bâti
porte grume ».
Pour son fonctionnement une génératrice produit le
courant continu (In = 240 A) dont il a besoin et un ventilateur assure son
refroidissement.
Sa vitesse de rotation est variable :
N = 0/ 1 25 / 75 0
Max : 2250tr /min
Pour cela un dispositif permet de faire varier le courant de
l'inducteur.
|
|
|
|
Rédigé par TCHIEGANG MBITCHA Alain Bertrand
|
36
|
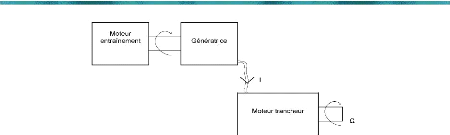
Figure 11: Synoptique moteur trancheur
|
|
Figure 12: Moteur trancheur
|
Figure 13: Génératrice
|
4. Chariot porte couteau
Le chariot est monté sur une vis sans fin et porte le
couteau qui attaque la grume (production des tranches).
Pour une production continue (épaisseur des tranches fixe)
le mouvement d'avance du chariot est synchronisé avec le
déplacement du « bâti porte grume ».
En effet un arbre est lié à l'une des grandes roues
dentées et il transmet son mouvement de rotation à l'arbre du
chariot grâce à un système d'embrayage.
Cet arbre transmet son mouvement de rotation à la vis sans fin (par
pignon conique) sur laquelle est monté le chariot.
Pour avance/recule rapide du chariot un moteur transmet son
mouvement à l'arbre du chariot à l'aide d'un
système poulie-courroie.
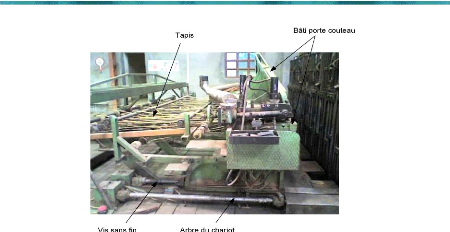
Figure 14: Chariot porte couteau
5. Table elevatrice
C'est à ce niveau qu'est réceptionnée la
tranche. La tranche est transportée par un tapis roulant monté
sur le chariot jusqu'à la table élévatrice.
6. Circuit pneumatique
Il assure le conditionnement de l'air et alimente les
vérins pneumatiques. Ensemble de conditionnement d'air
:
Lors du passage de l'air du compresseur à son lieu
d'utilisation, l'air "s'enrichit" en eau due à la condensation de l'eau
dans la cuve du compresseur, et en poussière, rouille des tuyaux des
canalisations. Il est donc nécessaire de le filtrer pour retirer ces
éléments nuisibles au bon fonctionnement des composants, de le
lubrifier pour faciliter le déplacement des organes mobiles des
composants pneumatiques et d'en contrôler la pression. A cet effet une
succession de composants est utilisé : un filtre, un détendeur de
pression et un graisseur à goutte.
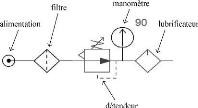
Figure 15: Conditionnement d'air
Rédigé par TCHIEGANG MBITCHA Alain Bertrand
|
38
|

IV. Procedures avant le tranchage
Nous avons identifié quatre systèmes qui
fonctionnement indépendamment les uns des autres, à savoir :
- Le bloc de tranchage
· La centrale hydraulique
· La génératrice
· La centrale de lubrification
· Le moteur trancheur
· Embrayage
· Le tapis
- Le chariot mobile
- Les grandes griffes
- La table élévatrice Mais avant de commencer le
tranchage proprement dit (production du placage tranché) des
réglages
doivent être effectués :
- Serrage de la grume par les petites et grandes griffes
- Positionnement du chariot
- Positionnement de la table élévatrice
1. Procedure de grillage (serrage de la
grume)
Après l'étuvage et le nettoyage, la dosse est
apportée au niveau des petites griffes de la trancheuse au moyen d'un
palan 5 tonnes.
Les opérations suivantes sont alors effectuées :
1) Actionner l'ouverture des petites griffes
2) Bien positionner la dosse
3) Actionner la fermeture des petites griffes
4) Enlever doucement le palan tout en vérifiant que la
dosse a été bien retenue par les petites griffes
5) Actionner la fermeture des grandes griffes afin de bien
saisir la dosse.
6) Démarrer le moteur trancheur
7) Passer à une vitesse assez élevée afin
de vérifier que la dosse a été bien fixée sinon
reprendre depuis le début (saisie de la grume à l'aide du
palan)

2. Procedure du positionnement chariot
Après avoir maintenu solidairement fixe la grume du
`'bâti porte grume», le chariot mobile doit être bien
positionné, c'est-à-dire : le couteau fixé sur le chariot
doit être à quelques centimètres de la grume avant de
commencer le tranchage, ceci pour des raisons simples : éviter
l'affûtage du couteau, éviter les chocs au moment où le
couteau attaque la grume.
3. Positionnement de la table elevatrice Afin
d'éviter que les tranches ne finissement au sol, la table
élévatrice doit être bien positionnée.
V. Systemes de variation de vitesse du moteur trancheur
et de freinage
1. Variation de vitesse du moteur tran cheur
Rappels :
Notons :
U, I : la tension et le
courant dans l'induit
Ue, Ie : la tension et le
courant dans l'inducteur
E : la fem (force électromotrice)
induite
Cem : le moment du couple
électromagnétique souvent appelé, par abus de langage
`'couple électromagnétique»
Pe : la puissance électrique fournie
: la vitesse de rotation
K : une constante qui dépend des
paramètres de constitution de la machine (construction,
géométrie, matériaux...)
R : la résistance de l'induit
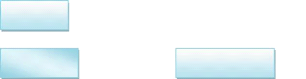
E = K ÖÙ
Cem = KÖI (2)
Pe = U.I +Ue.Ie (3)
(1)

Ù
U = KÖÙ + RI (4)
U - RI (5)
K Ö
Pour un moteur à excitation séparée, U = E +
RI soit :

Pour faire varier la vitesse d'un moteur à courant
continu, on peut soit agir sur :
· la tension U aux bornes de l'induit :
La tension d'induit est directement proportionnelle à la
vitesse de rotation (voir équation 5).
La puissance varie mais le couple reste
constant (voir équations 2 et 3). On dit alors que l'on
fait de la variation de vitesse à couple constant.
· le flux produit par l'inducteur (1) :
Lorsque le flux d'excitation (produit par l'inducteur) diminue
(équation 5), le moteur accélère mais le couple diminue
(équation 2). On dit alors que l'on fait de la variation de vitesse
à puissance constante.
Le moteur trancheur est à excitation
séparée, pour faire varier sa vitesse il faut agir sur
le flux produit par l'inducteur.
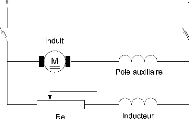
Figure 16: Synoptique du bloc de variation de vitesse
du moteur trancheur
Au démarrage, l'inducteur (circuit d'excitation) est
traversé par le courant maximum (rhéostat d'excitation Re au
minimum de résistance).
Pour varier la position du curseur du rhéostat, un moteur
triphasé à deux sens de marche transmet son mouvement à
l'arbre de rotation du curseur par pignons.
Ce moteur fonctionne comme suit :
- sens d'accélération moteur trancheuse : sens
n° 1
- sens décélération moteur trancheuse :
sens n° 2
2. Systeme de freinage
Nous avons dit précédemment que la grume maintenue
fixe par les griffes sur un bâti se déplace verticalement (bas en
haut). Imaginez un instant qu'elle soit entrain de monter et que survient une
coupure d'alimentation. Elle retombera aussitôt sous l'action de son
poids et peu ainsi causer sans doute des dégâts importants au
niveau de la machine.
Pour pallier à ce problème un système de
freinage a été prévu (voir figure : moteur trancheur). Il
est situé au niveau de l'arbre de transmission (le moteur trancheur
transmet son mouvement de rotation à

cet arbre qui permet à la grume de se déplacer) et
est constitué de garnitures montées sur un tambour sur lequel est
fixé un vérin pneumatique simple effet.
- Lorsque le moteur trancheur est mis en marche, le distributeur
commandant le vérin pneumatique est alimenté et le frein se
libère (rentrée de la tige du vérin)
- A l'action sur le bouton d'arrêt du moteur trancheur ou
sur l'une de ses sécurités d'arrêt, ou lorsque survient une
coupure d'alimentation électrique, ce distributeur n'est plus
alimenté (commande monostable) et le frein est activé.
VI. Organes de commandes et capteurs
1. Boutons poussoirs
Lorsque nous analysons les rôles des différents
boutons poussoirs sur les pupitres de commande (voir tableau ci-dessous), il en
ressort que :
Tableau 2: Boutons poussoirs
DESIGNATION
|
TYPE
|
FONCTIONS
|
bp1
|
NO
|
Mise en marche centrale hydraulique
|
bp2
|
NO
|
Mise en marche génératrice
|
bp3
|
NC
|
Arrêt centrale hydraulique
|
bp4
|
NO
|
Mise en marche moteur trancheur
|
bp5
|
NO
|
Embrayage chariot et mise en marche Tapis
|
bp6
|
NC
|
Débrayage chariot
|
bp7
|
NC
|
Arrêt moteur trancheur et tapis avec temporisation (pour
le tapis)
|
bp8
|
NO
|
Accélération moteur trancheur
|
bp9
|
NO
|
Décélération moteur trancheur
|
bp10
|
NO
|
Mise en marche avance chariot
|
bp11
|
NO
|
Mise en marche recule chariot
|
bp12
|
NC
|
Arrêt moteur chariot
|
bp13
|
NO
|
Mise en marche griffage (grande griffe)
|
bp14
|
NO
|
Mise en marche dégriffage (grande griffe)
|
bp15
|
NO
|
Mise en marche montée table élévatrice
|
bp16
|
NO
|
Mise en marche descente table élévatrice
|
|

2. Leviers de commande mecanique
La machine dispose de deux rangées de petites griffes
commandées par des leviers mécaniques. Nous tenons à
signaler que le couteau se fixe sur le bâti du chariot à l'aide
des vérins hydrauliques alimentés par des distributeurs à
commande mécanique.
Tableau 3: Commandes mécaniques
DESIGNATION
|
FONCTIONS
|
lc1
|
Mise en marche 1ère rangée de griffe
(petites griffes)
|
lc2
|
Mise en marche 2ème rangée de griffe
(petites griffes)
|
lc3
|
Mise en marche 1ère fixation du couteau
|
lc4
|
Mise en marche 2ème fixation du couteau
|
|
3. Capteurs et securites
La machine dispose de plusieurs organes de
sécurité pour la protection de la machine ou de
l'opérateur au cours de son fonctionnement. Nous avons :
- Un détecteur photoélectrique
(ph) qui signale la présence d'une personne entre le bâti
et le chariot au moyen d'un faisceau lumineux et arrête
immédiatement le moteur trancheur. Ses deux constituants de base sont un
émetteur et un récepteur.
Actuellement il est endommagé (problème de sécurité
humaine).
- Trois capteurs de fin de course ou capteurs
de contact ou interrupteurs de position électromécanique qui
permettent de localiser la position du chariot.
· Le premier (fc1) lorsqu'il n'est pas actionné
verrouille le maintien du moteur trancheur
· Le second (fc2) arrête le moteur trancheur et le
mouvement avant du chariot
· Le troisième (fc3) arrête le mouvement
arrière du chariot
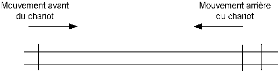
fc3 fc1 fc2
Figure 17: Capteurs de contact
- Un capteur (nv) de contrôle de niveau
d'huile dans la centrale de lubrification, utilisé pour commander le
démarrage et l'arrêt.

- Un pressostat pour le contrôle de la
présence d'air surpression : qui ne permet le démarrage de la
machine qu'en cas de présence d'air au dessus de 5 bars.
Tableau 4: Capteurs et
sécurités
DESIGNATION
|
FONCTIONS
|
AU1
|
Arrêt d'urgence moteur trancheur
|
AU2
|
Arrêt d'urgence moteur trancheur et
génératrice
|
ph (détecteur
photoélectrique)
|
Arrête le moteur trancheur
|
fc1
|
Fin de course verrouillage du maintien du moteur trancheur
|
fc2
|
Fin de course arrêt du moteur trancheur
|
fc3
|
Fin de course arrêt recule chariot
|
Nv
|
Détection du niveau d'huile dans la centrale de
lubrification
|
Pa
|
Détection de la présence d'air surpression
(supérieur à Pmin = 5 bar)
|
bcp (bouton coup de point)
|
Coupure alimentation générale de la machine
|
4. Commutateur
C : blocage et déblocage de
l'accélération moteur trancheur
VII. Actionneurs
Dans sa constitution, la machine dispose d'un ensemble de
vérins (simple effet et double effet) à la fois hydraulique, et
des vérins simples effets pneumatiques.
1. Verins Les types de vérins
utilisés sont les suivants :
Tableau 5: Vérins
DESIGNATION
|
FONCTIONS
|
1V
|
vérin hydraulique à double effet commande grandes
griffes
|
2V
|
vérin pneumatique d'embrayage simple effet
|
3V
|
vérin pneumatique de freinage simple effet
|
4V
|
vérin hydraulique simple effet table
élévatrice
|
|
2. Moteurs La machine dispose des moteurs
asynchrones et à courant continu :
Rédigé par TCHIEGANG MBITCHA Alain Bertrand
|
44
|

Tableau 6: Machines à courant
continu
MACHINES A COURANT CONTINU
|
Désignation
|
Moteur
|
Rôle
|
Puissance (KW)
|
Vitesse de rotation (tr/min)
|
Induit
|
Inducteur
|
U (V)
|
I (A)
|
U (V)
|
I (A)
|
M1
|
Génératrice
|
Transforme l'énergie mécanique reçue
en énergie électrique
|
55
|
1445
|
230
|
239
|
220
|
2,1
|
M2
|
Moteur trancheur
|
Permet le déplacement de la grume devant le
couteau
|
45
|
0/125/750 Max : 2250
|
220
|
240
|
220
|
7,7
|
Rédigé par TCHIEGANG MBITCHA Alain Bertrand
|
45
|

Tableau 7: Moteurs à courant
alternatif
MOTEURS ASYNCHRONES
|
Désignation
|
Moteur
|
Rôle
|
Puissance (kW)
|
Vitesse de rotation (tr/min)
|
Facteur de puissance
|
Intensité I (A)
|
Tension (triangle) U (V)
|
Tension (étoile) U (V)
|
M0
|
Moteur d'entraînement génératrice
|
Fournie l'énergie mécanique à
la génératrice
|
55
|
1445
|
0,87
|
107
|
380
|
-
|
M3
|
Moteur centrale lubrification
|
Moteur pompe pour la lubrification
des glissières
|
0,09
|
1350
|
0,65
|
0,21
|
380
|
220
|
M4
|
Moteur centrale hydraulique
|
Moteur pompe pour le circuit hydraulique
des vérins (grandes griffes)
|
7,5
|
1455
|
0,80
|
16,5
|
380
|
-
|
M5
|
Moteur accélération/décélération chariot
porte couteau
|
Moteur avance/recule rapide chariot porte couteau
|
9
|
1455
|
0,9
|
15,5
|
380
|
-
|
M6
|
Moteur tapis
|
Moteur d'entraînement du tapis
|
5,5
|
956
|
0,79
|
12
|
380
|
-
|
M7
|
Moteur ventilation moteur trancheur
|
Assure le refroidissement du moteur trancheur
|
0,18
|
4320
|
0,75
|
0,36
|
380
|
220
|
M8
|
Moteur table élévatrice
|
Moteur pompe pour la table élévatrice
|
2,5
|
-
|
-
|
-
|
380
|
-
|
M9
|
Moteur rhéostat
|
Moteur pour la variation de la position du curseur du
rhéostat
|
0,5
|
-
|
-
|
-
|
380
|
-
|
Rédigé par TCHIEGANG MBITCHA Alain Bertrand
|
46
|

3. Voyants
Tableau 8: Voyants
Designation
|
Fonctions
|
V1
|
Signalisation présence tension
|
V2
|
Signalisation marche moteur trancheur
|
V3
|
Signalisation mise en marche embrayage
|
V4
|
Signalisation fonctionnement centrale hydraulique
|
V5
|
Signalisation fonctionnement génératrice
(allumé au passage en triangle)
|
V6
|
Signalisation présence d'huile dans la centrale de
lubrification (absent sur le pupitre de commande)
|
V7
|
Montée table
|
V8
|
Avance chariot
|
VIII. Probleme rencontre au niveau de la centrale
hydraulique
Il peut arriver que la pompe de la centrale hydraulique tourne
mais ne débite pas, ou alors la pression du fluide n'a pas atteint une
valeur seuil pour permettre un fonctionnement acceptable de la machine. Le
technicien pilotant la machine ne prend pas en compte ces informations
capitales, permettant de s'assurer que l'énergie est disponible au
niveau des griffes.
1. Solution proposee
Nous proposons d'insérer dans le circuit hydraulique
à la sortie de la centrale hydraulique, un pressostat
électro-hydraulique.
C'est un capteur destiné à contrôler la
pression dans les circuits pneumatiques ou hydrauliques. Lorsque la pression
atteint la valeur de réglage, le contact NO/NC à action brusque
change d'état. Dès que la valeur de la pression diminue, compte
tenu de l'écart réglable sur certains modèles, les
contacts reviennent à leur position initiale.
Ce pressostat sera utilisé pour :
- commander la mise en marche de la
génératrice,
- s'assurer de la circulation de l'huile dans le circuit
hydraulique.
Nos critères de choix sont les suivant :
- Type de fonctionnement : surveillance d'un
seuil

- Nature du fluide : huile hydraulique
- Valeur de la pression à contrôler
: P = 25 bars
- Environnement : poussière,
humidité
- Nature du circuit électrique : circuit
de commande
La pression nominale de la pompe est : 70
bars
Le pressostat choisi appartient à la gamme de
détection de pression Nautilus. Type : XML - A à
écart fixe sans affichage
Plage de réglage (bar) : 5...70
Gamme de température (° C) : -25
à 70
Dimension (mm) H (hauteur) * l (largeur) * L
(longueur) : 113*35*73 Référence : XML -
A070D2S11
Conclusion :
Cette analyse nous a permis de comprendre d'une maniere globale
la constitution de cette machine, son utilité, de déceler un
probleme majeur rencontré au niveau de la centrale hydraulique et
proposer ainsi une solution.
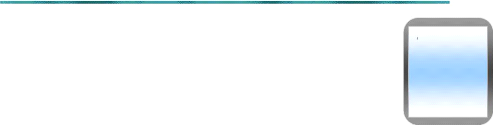
Chapitre
5
CHAPITRE 5 :
411jodelisation
Introduction :
Ce chapitre est réservé a la modélisation du
système. Tout d'abord, nous analyserons ses différentes
fonctionnalités et par la suite apres avoir présenté le
cahier de charge, nous le traduirons en un formalisme qui ne permet aucune
erreur d'interprétation.

I. Analyse des differentes fonctionnalites de la
machine
Une étude rigoureuse de la trancheuse verticale, nous
emmène à recenser ses différentes fonctionnalités
à savoir :
1. Déplacement vertical du bâti porte grume (qui
peut être accéléré)
2. Déplacement horizontal du chariot porte couteau (qui
peut être accéléré)
3. Griffage / dégriffage de la grume
4. Montée / descente de la table
élévatrice
1. Fonctionnalite no 1 : deplacement vertical du bati
porte grume
Après avoir déverrouillé le bouton coup de
poing (bcp) et fermer le sectionneur, les opérations
suivantes sont à effectuées :
Mise en marche
- Démarrage de la centrale hydraulique (moteur
M4) par l'action sur le bouton bp1
- Démarrage de la génératrice
(M1) après confirmation du démarrage de la
centrale hydraulique (action sur bp2)
- Après passage en triangle de la
génératrice, libération du frein (rentrée du
vérin 3V), démarrage de la centrale de
lubrification (M3), démarrage du moteur trancheur
(M2) et du moteur ventilation (M7)
(après action sur bp4)
- Après démarrage du moteur trancheur, trois
options sont possibles :
o Accélération du moteur trancheur (action sur
bp8)
o Décélération du moteur trancheur (action
sur bp9)
o Maintenir la vitesse initiale
- Mise en marche de l'embrayage (vérin 2V) par l'action
sur bp5 et le tapis est automatiquement mis en marche
(M6)
Nous rappelons que l'embrayage permet de synchroniser le
mouvement d'avance du chariot avec le déplacement vertical de la grume
sur le bâti.
m le chariot avance et lâche la 1ère fin
de course fc1. cette fin de course verrouille le maintien du
moteur trancheur. A ce stade, la grume est presque qu'entièrement
tranchée.
m Entre fc1 et fc2 le moteur
trancheur fonctionne par à coup
Mise à l'arrêt
- l'action sur le bouton bp3 arrête
toutes les fonctionnalités du système

- l'action sur le bouton bp7 arrête le
moteur trancheur et le tapis (après une temporisation de 5 secondes)
2. Fonctionnalite n° 2 : deplacement du
chariot
- l'action sur le bouton bp10 met en marche le
moteur (M5) sans maintien, la fin de course
fc2 verrouille le mouvement avant du chariot.
- l'action sur le bouton bp11 met en marche le
mouvement arrière avec maintien, le bouton poussoir
bp12 ainsi que la fin de course fc3 met en
arrêt le mouvement arrière.
3. Fonctionnalite n° 3 : grandes
griffes
- L'action sur bp3 actionne la fermeture des
griffes (distributeur bistable 1D à la position N°1)
NB : la pression de l'huile doit être supérieure
à 25 bars dans les vérins.
- L'action sur bp14 actionne l'ouverture des
griffes (distributeur 1D à la position N°2)
4. Fonctionnalite n° 4 : table
elevatrice
- l'action sur bp15 met en marche le moteur
pompe M8 pour la montée (et sans maintien)
- l'action sur bp16 actionne le distributeur
4D pour le retour d'huile et donc la descente de la table
(moteur M8 en arrêt) et sans maintien électrique.
5. Verrouillage
- L'arrêt de la centrale hydraulique verrouille la
génératrice
- L'arrêt de la génératrice verrouille le
moteur trancheur
- L'arrêt du moteur trancheur verrouille l'embrayage et le
tapis
6. Choix du modele
Il ressort de ces fonctionnalités que le système
est séquentiel. La suite de phrases décrivant le fonctionnement
de ce système constitue pour nous le cahier des charges.
Afin d'analyser et de valider ce cahier de charges, il doit
être traduit en un formalisme qui ne permet aucune erreur
d'interprétation. On parle de modélisation.
Le modèle choisi est le GRAFCET : outil
d'analyse de la commande séquentielle d'un processus. Dans la suite il
sera présenté les grafcets :
Rédigé par TCHIEGANG MBITCHA Alain Bertrand
|
51
|
|

- point de vue système qui
décrit littérairement avec plus ou moins de précision les
fonctions principales assurées par le système automatisé.
Il fait abstraction des technologies qui seront utilisées sur la partie
opérative.
- point de vue partie commande qui exprime avec
précision les spécifications fonctionnelles qui permettront de
concevoir la partie commande.
II. Grafcet point de vue systeme
1.
Grafcet principal
Rédigé par TCHIEGANG MBITCHA Alain Bertrand
|
52
|
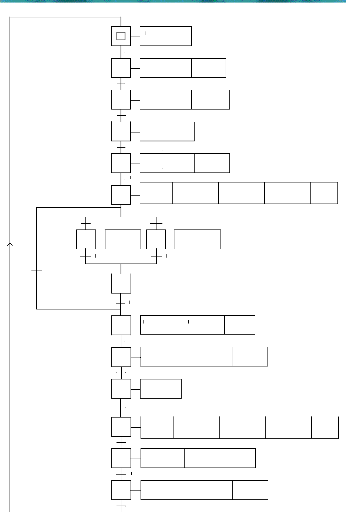
Bouton 5
6
Bouton 8 relâché
Bouton 8
Accélération
10
11
13
14
12
4
0
2
3
5
8
9
1
Fin de course n°1 relâchée
Contacteur triangle ouvert
Bouton 5
Bouton 4 et fin de course n°1 relâchée
Bouton 4
Bouton 4 et bouton 5
Fin de course n°2 relâchée
Bouton 1
Bouton 2
Fin temporisation
Fin temporisation
Fin temporisation
Libération du frein
|
Mise en marche centrale de
|
Mise en marche
trancheur
moteur
|
Mise en marche ventilation moteur
|
voyant
|
|
lubrification
|
|
trancheur
|
|
Libération
|
Mise en marche
de
centrale
|
Mise en marche
|
Mise en marche ventilation moteur
|
|
du frein
|
lubrification
|
moteur trancheur
|
trancheur
|
voyant
|
Mise en marche de l'embrayage
|
Mise en marche du tapis
|
voyant
|
Mise en marche de
l'embrayage
Mise à l'arrêt de tous
les dispositifs
Mise en marche
centrale hydraulique
Passage en triangle
de la génératrice
Arrêt du tapis
Contacteur de ligne
Activation du frein, arrêt de la centrale
de
lubrification, du moteur trancheur,
du moteur ventilation
Démarrage étoile
de la
génératrice
Activation du frein, arrêt de la centrale
de
lubrification, du moteur trancheur,
du moteur ventilation
7
Bouton 9
Bouton 9 relâché
Décélération
Mise en marche
du tapis
Temporisation
voyant
voyant
voyant
Temporisation
Temporisation
Figure 18: Grafcet principal point de vue
système
Rédigé par TCHIEGANG MBITCHA Alain Bertrand
|
53
|

2. Grafcet Chariot
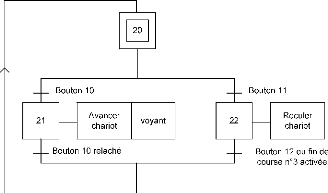
Figure 19: Grafcet 1 chariot
3. Grafcet grandes griffes
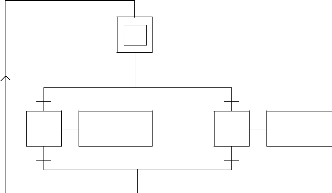
31
Bouton 13 relâché
Bouton 13
Serrer la grume
30
32
Bouton 14
Bouton 14 relâché
Desserrer
la grume
Figure 20: Grafcet 1 grandes griffes
4. Grafcet table elevatrice
Rédigé par TCHIEGANG MBITCHA Alain Bertrand
|
54
|
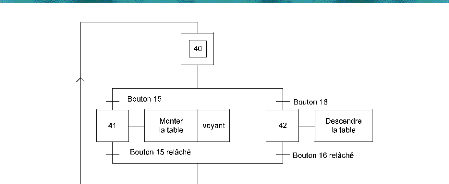
Figure 21: Grafcet 1 table
élévatrice
III. Grafcet Partie commande
Pour une bonne lisibilité des différents Grafcet,
nous adoptons les notations suivantes :
Tableau 9: Notation préactionneurs
Preactionneurs et voyants
|
KM1 L
|
Contacteur de ligne du moteur n°1
|
KM1 Y
|
Contacteur étoile du moteur n°1
|
KM 1Ä
|
Contacteur triangle du moteur n°1
|
KM 5 d · (
KM 9 d)
|
Contacteur « marche avant » moteur
n°5 (idem moteur n°9)
|
KM 5 g · ( KM
9 g )
|
Contacteur « marche arrière » moteur
n°5 (idem moteur n°9)
|
KMi
|
Contacteur « moteur n°i »
|
iD
|
Distributeur « vérin n°i »
|
Vi
|
Voyant n°i
|
Notation Preactionneurs et voyants
|
KMi +
|
Mise en marche « moteur n°i »
|
KM-i-
|
Mise à l'arrêt « moteur n°i
»
|
iD +
|
Mise en marche « distributeur n°i
»
|
iD-
|
Mise à l'arrêt « distributeur
n°i »
|
Vi +
|
Mise sous tension « voyant n°i »
|
Vi-
|
Mise hors tension « voyant n°i »
|
1. Grafcet principal
Rédigé par TCHIEGANG MBITCHA Alain Bertrand
|
55
|
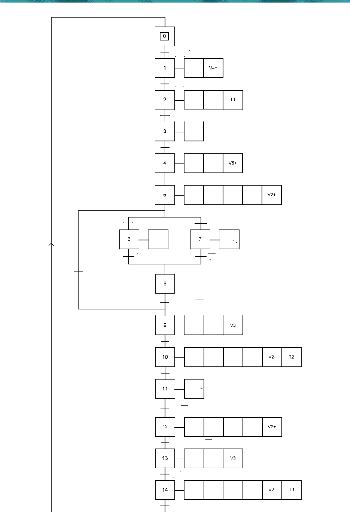
bp 5 . KM 2 . bp 6
bp
bp8
8
KM 9
d
bp 4. fc 1. fc 2
bp 1 . bp 3
1 0 s / X 2
bp 4 . KM 1 Ä . fc 1 .
fc 2 . nv . pa . bp 7
bp 5 . KM 2 . bp
bp5
.KM2.bp4.fc1.fc2
bp 2 . pr
KM1 Y
fc2
fc1
5 s / X 10
5 s / X 14
KM1
|
KM1
|
|
L
|
Y
|
|
KM1
|
|
|
L
|
KM 1Ä
|
|
KM 2 +
|
KM 3 +
|
KM 7 +
|
3D +
|
|
|
|
|
|
|
2D
|
|
|
2D
|
KM 6 +
|
|
|
|
|
|
KM
3
|
KM
7
|
|
|
|
|
|
|
3D
|
|
|
KM 2 -
|
-
KM 3
|
-
|
3D -
|
|
|
|
|
KM 7
|
|
|
|
KM 2 +
|
KM 3 +
|
KM 7 +
|
3D +
|
|
|
|
|
|
|
KM 4 +
KM1 L
KM 2
KM 6
6
bp9
KM 6 +
bp
9
KM9
g
Figure 22: Grafcet principal point de vue partie
commande

2. Grafcet chariot
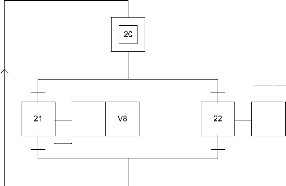
KM5 g
bp1 0 .fc2
KM5d
bp1 0
bp1 1 .bp1 2.fc3
bp 12 + fc3
Figure 23: Grafcet 2 chariot
3. Grafcet grandes griffes
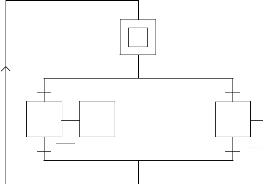
30
bp 1 3.pr
bp1 4
31
1D +
32
bp1 3
bp1 4
1D -
Figure 24: Grafcet 2 grandes griffes
Rédigé par TCHIEGANG MBITCHA Alain Bertrand
|
57
|
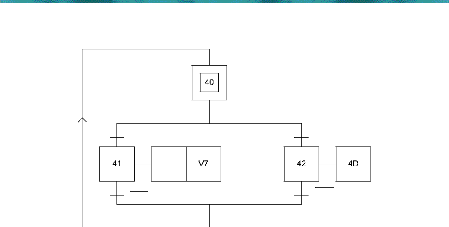
4. Grafcet table elevatrice
bp1 5
bp1 5
KM8
bp1 6
bp1 6
Figure 25: Grafcet 2 table
élévatrice
Conclusion :
Nous avons modélisé le système et
réalisé les différents grafcets (point de vue
système et partie commande). Ces grafcets doivent être traduits en
un langage compréhensible par l'automate : c'est l'objectif du prochain
chapitre.
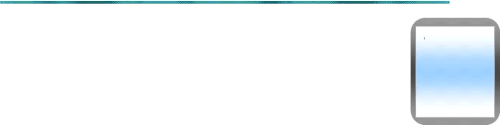
Chapitre
6
CHAPITRE 6 :
programmation des séquences de
fonctionnement et coblage entrées /
sorties
Introduction :
Dans ce chapitre, il sera abordé en premier lieu la
programmation des séquences de fonctionnement qui regroupe une
étude architecturale de l'automate choisi et la mise en oeuvre des
séquences de fonctionnement. En second lieu nous présenterons les
schémas de cablage des entrées / sorties de l'automate.
Rédigé par TCHIEGANG MBITCHA Alain Bertrand
|
59
|

I. ETUDE ARCHITECTURAL
1. Choix de l'automate
Nous allons utiliser dans ce projet un automate de marque
Télémécanique et ceci pour les raisons suivantes :
· Il est le plus utilisé dans les industries
camerounaises
· Nous possédons son logiciel de programmation
· Nous ne trouvons pas d'inconvénient pouvant nuire
à notre projet
Panorama de l'offre de Schneider Electric : TSX Nano, TSX Micro,
TSX Premium, TSX Quantum donc les caractéristiques principales
s'articulent comme suit :
Tableau 10 : Comparaison TSX [3]
|
TSX Nano
|
TSX Micro
|
TSX Premium
|
TSX Quantum
|
Particularites et caracteristiques
|
0 compact
0 rapide
0 convient pour les petits
automatismes
0 E/S TOR = 24
|
0 compact
0 modulaire
0 jusqu'à 248 E/S TOR `'in rack»
0 programmation : langage Grafcet
|
0 architecture distribuée
0 modulaire
0 jusqu'à 2048 E/S `'in rack»
0 langage Grafcet
|
0 architecture modulaire et évolutive
0 sur châssis unique 448 E/S
|
besavantages
|
Langage :
0 Ladder
0 List
(inadapté au langage Grafcet)
|
7 lignes maximum pour un réseau de contacts
|
0
|
0
|
Nous choisissons la gamme TSX Premium et ceci
pour des raisons suivantes :
- Le nombre d'entrées / sorties élevé (25
entrées et 17 sorties)
- Il utilise le langage de programmation de type Grafcet qui
nous permettra d'assurer les dépannages dans les meilleures
conditions
- Nous disposons au sein du laboratoire d'automatique et
de productique de l'Ecole Nationale Supérieure
Polytechnique d'un TSX premium pour des essais et simulation.

2. Presentation
Les automates TSX Premium sont entièrement modulaires. Une
station automate est construite à partir des éléments de
base suivants : [3]
o Racks (standard ou extensibles),
Les racks TSX RKY... constituent
l'élément de base des automates TSX Premium. Deux familles de
racks sont proposées en 3 modularités (6,8 et 12 positions).
n Modules alimentation,
Les alimentations se présentent sous la forme de modules
et sont choisies en fonction du réseau distribué (continu ou
alternatif) et de la puissance nécessaire :
Le module alimentation TSX PSY .... est
destiné à l'alimentation de chaque rack TSX
RKY... et des modules.
n Modules processeur,
Chaque station automate est pourvue d'un processeur, choisi en
fonction de la puissance de traitement nécessaire. Un module processeur
TSX P57.. s'implante sur un rack TSX RKY ...
en position 00 ou 01 selon que le rack est
équipé d'un module alimentation de type standard ou double
format.
NB : le rack sur lequel est implanté le
processeur a toujours l'adresse 0.
o Entrées/sorties TOR,
Les modules E/S TOR du TSX Premium sont au format standard (1
position). Ils se positionnent indifféremment sur le rack standard ou
sur un rack extensible.
Une large gamme d'entrées et de sorties tout ou rien (TOR)
permet de répondre aux besoins rencontrés au niveau :
· Fonctionnel : entrées/sorties continus ou
alternatives, logique positive ou négative,
· Raccordement par borniers à vis ou connecteurs
HE10,
· Modularité : 8, 16, 32, 64 voies/module
o Entrées/sorties analogiques,
Les modules d'entrées/sorties analogiques de l'offre TSX
57 sont des modules au format standard (qui occupent une seule position),
équipés soit d'un connecteur SubD 25 points (TSX AEY 800), soit
de deux connecteurs SubD 25 points (TSX AEY 1600), soit d'un bornier à
vis (TSX AEY 414 et TSX ASY 410).
Ils peuvent être implantés dans toutes les positions
des racks TSX RKY.., à l'exception de la première position
réservée à l'alimentation du rack.

o Modules métiers (comptage, commande
d'axes, commande pas à pas, communication, pesage, ventilation).
3. Configuration materielle
Notre station automate sera constituée :
· 1 rack standard 6 positions : TSX RKY
6
· 1 processeur : TSX P57 352M
Capacité de traitement:
- 1024 E/S TOR
- 128 E/S analogiques
- 32 voies metier
Capacité mémoire
- intégrée processeur : 80 K mots
- extension PCMCIA : 256 K mots maximum
· 1 module d'entrées `'Tout ou Rien»
- Type du module : entrées à connecteurs -
Modularité : 32 entrées
- Tension : 24 VCC
- Logique positive
- Raccordement : connecteurs HE 10 Référence :
TSX DEY 32D2K
· 1 module de sorties `'Tout ou Rien»
- Type du module : soties statiques à connecteurs
- Modularité : 32 sorties
- Tension : 24 VCC
- Courant puissance : 0,1 A
- Logique positive
- Raccordement : connecteurs HE 10 Référence :
TSX DSY 32T2K
· 1 module d'alimentation
La puissance nécessaire à l'alimentation de chaque
rack TSX RKY est fonction du type et du nombre de modules implantés dans
celui-ci. De ce fait, il est nécessaire d'établir un bilan de
consommation rack par rack afin de définir le module d'alimentation TSX
PSY adapté à chaque rack.

Tableau 11: Bilan de consommation
Référence
|
Consommation en mA
|
puissance (W)
|
|
tension continue 24 V
|
|
TSX P57 352M
|
500
|
-
|
2,5
|
Entrées "Tout ou Rien"
|
TSX DEY 32D2K
|
135
|
160
|
4,515
|
Sorties "Tout ou Rien"
|
TSX DSY 32T2K
|
140
|
-
|
0,7
|
Total 7,715
|
|
D'après ce tableau, la puissance nécessaire est de
7,72 W.
Nous choisissons de préférence un module
alimenté à partir d'un réseau à courant alternatif
et possédant une alimentation capteur 24 VCC.
Référence : TSX PSY 2600M
Alimentation : 100...240 VCA
Puissance utile totale : 26 W
Accessoires
Une pile de sauvegarde mémoire RAM interne
Référence : TSX PLP 01
NB : Tension continue 5 V destinée
à l'alimentation des modules TSX Premium Tension
continue 24 V destinée à l'alimentation des capteurs
d'entrées
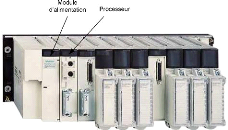
Tableau 12: TSX Premium

4. Codage des entrees sorties de l'automate
L'adressage des voies est géographique ;
c'est-à-dire qu'il dépend :
· De l'adresse du rack,
· De la position physique du module dans le rack,
La syntaxe de l'adresse d'une entrées / sortie TOR est la
suivante :
Tableau 13: Codage des entrées / sorties automate
[3]
%
|
|
I ou Q
|
|
adresse rack x
|
|
position module y
|
|
.
|
|
numéro de voie i
|
Symbole
|
|
I = entrée Q = sortie
|
|
x = 0 à 7
|
|
y = 00 à 10
|
|
Point
|
|
i = 0 à 63
|
Exemples :
(1) %Q7.3 signifie : sortie 3 du module placé en position
07 dans rack 0
(2) %I102.5 signifie : entrée 5 du module placé en
position 02 dans rack adresse 1 Application
Le module d'entrées sera en
position 01 et le module de sorties en
position 02.
5. Configuration logi cielle
Comme plusieurs automates disponibles sur le marché,
l'automate TSX Premium de la société
Télémécanique possède son propre logiciel de
programmation.
Le logiciel de programmation utilisé ici est le
PL7 Pro V3.1
Apres le démarrage du logiciel, nous créons une
nouvelle application de nom `'TRANCHEUSE»
Rédigé par TCHIEGANG MBITCHA Alain Bertrand
|
64
|
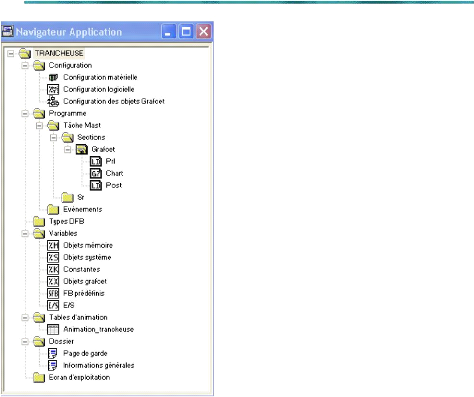
Figure 26: Navigateur d'application
Une configuration matérielle est nécessaire car
elle assure l'interface et la cohérence entre l'environnement externe et
l'application logicielle.
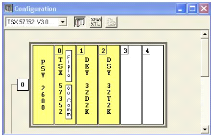
Figure 27: Configuration matérielle
La configuration logicielle permet d'ajuster les
éléments logiciels tels que temporisateur, compteur ... aux
besoins de l'application. En effet il n'est pas nécessaire que le
processeur scrute des éléments qui ne sont pas utilisés
par le programme, gain de temps d'exécution.
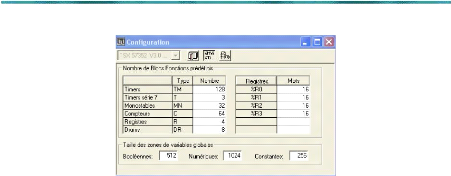
Figure 28:Configuration logicielle
6. Programmation sous PL7 Pro
6.1 Procedure pour une programmation sous PL7
Pro
1) La première étape, consiste à
transformer le GRAFCET de manière à ce qu'il soit
compréhensible par l'automate. En langage automate on appelle cette
étape « CHART ».
2) La deuxième étape consiste à traiter les
transitions. On appelle cette partie PRELIMINAIRES.
3) La troisième consiste à affecter les sorties
correspondantes aux étapes de notre GRAFCET. Cette partie est
appelée POSTERIEUR.
4) La quatrième et dernière étape consiste
à faire « dérouler » le GRAFCET. En effet, il faut
indiquer à l'automate quand passer d'une étape à
l'autre.
6.2 Table d'animation
Afin de suivre l'évolution des variables et de valider
le bon fonctionnement, il nous faut définir la table d'animation. Elle
est indispensable pour diagnostiquer les disfonctionnements durant la phase de
mise au point du programme.
6.3 E crans d'exploitation
La plate forme logicielle PL7 Pro propose aussi un outil de
conception d'écran d'exploitation du système automatisé.
Ces pages écrans constituent l'équivalent d'un terminal de
dialogue interactif.
7. Notion de cycle de s crutation
On appelle scrutation l'ensemble des
quatre opérations réalisées par l'automate et le
temps de scrutation est le temps mis par l'automate
pour traiter la même partie de programme.

1) Traitement interne
- surveillance de l'automate
- Détection RUN / STOP
- Echange avec le terminal de programmation
2) Acquisition des entrées
- écriture en mémoire de l'état des
informations présentes sur les entrées des modules TOR
3) Traitement du programme
- Traitement séquentiel des opérations logiques du
programme en utilisant l'état des entrées disponibles en
mémoire
4) Mise à jour des sorties
- affectation sur les sorties présentes sur les modules
TOR
8. Les objets adressables
Les objets booléens dits bits peuvent se résumer
comme suit :
· Bits d'entrée/sortie : %I, %Q
sont les images des bornes d'entrées et de sorties.
· Bits internes %M : permettent de
mémoriser les états intermédiaires durant
l'exécution du programme.
· Bits système %S : qui indiquent
les états de l'automate ou permettent d'agir sur le fonctionnement de
celui-ci.
· Bits de blocs fonctions :
temporisateurs, compteurs, monostables, registres à décalages,
séquenceurs.
· Bits d'état des étapes Grafcet :
%X qui mémorisent l'état des étapes actives ou
inactives.
Récapitulatif des bits système
Rédigé par TCHIEGANG MBITCHA Alain Bertrand
|
67
|
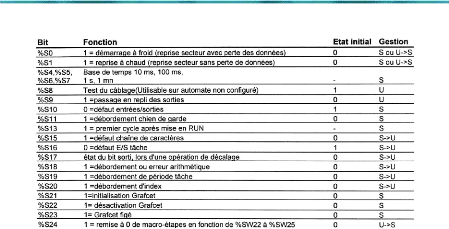
Tableau 14: Bits système
U : géré par l'utilisateur
S : géré par le système
U->S : mise à 1 par U, mise à zéro par
S
S->U : mise à 1 par S, mise à zéro par U
II. Mise en oeuvre des sequences du systeme automatise 1.
Entrees API
Tableau 15 : Entrées API
Mnetnoniques
|
Affectation API
|
bp1
|
I1.0
|
bp2
|
I1.1
|
bp3
|
I1.2
|
bp4
|
I1.3
|
bp5
|
I1.4
|
bp6
|
I1.5
|
bp7
|
I1.6
|
bp8
|
I1.7
|
bp9
|
I1.8
|
bp10
|
I1.9
|
bp11
|
I1.10
|
bp12
|
I1.11
|
bp13
|
I1.12
|
bp14
|
I1.13
|
bp15
|
I1.14
|
bp16
|
I1.15
|
ph
|
I1.16
|
pr
|
I1.17
|
fc1
|
I1.18
|
fc2
|
I1.19
|
fc3
|
I1.20
|

Mnemoniques
|
Affectation API
|
nv
|
I1.21
|
Pa
|
I1.22
|
Kmly
|
I1.23
|
AUl
|
I1.24
|
NB :
Pr : pressostat
2. Sorties API
Tableau 16 : Sorties API
Mnemoniques
|
Affectation API
|
Km4 - v4
|
Q2.0
|
Kml2
|
Q2.1
|
KmlY
|
Q2.2
|
Kmla - v5
|
Q2.3
|
Km2 - Km7 - v2
|
Q2.4
|
Km3
|
Q2.5
|
Km9d
|
Q2.6
|
Km99
|
Q2.7
|
Km5d - v8
|
Q2.8
|
Km59
|
Q2.9
|
Km6
|
Q2.10
|
Km8 - v7
|
Q2.11
|
3b
|
Q2.12
|
lb+
|
Q2.13
|
lb-
|
Q2.14
|
2b - v3
|
Q2.15
|
4b
|
Q2.16
|
3. Grafcet point de vue API 3.1 Grafcet
principal
Rédigé par TCHIEGANG MBITCHA Alain Bertrand
|
69
|
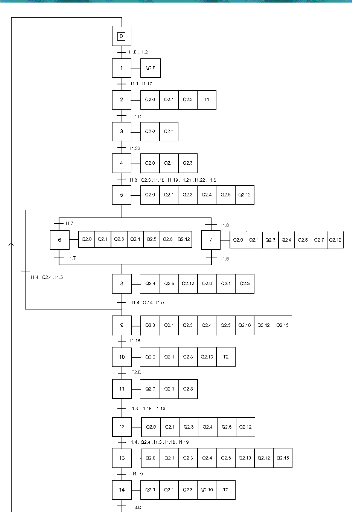
Figure 29: Gracet principal point de vue API
Rédigé par TCHIEGANG MBITCHA Alain Bertrand
|
70
|

3.2 Grafcet chariot
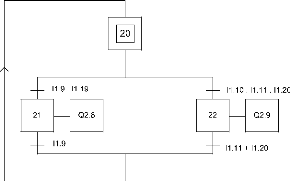
Figure 30: Grafcet 3 chariot
3.3 Grafcet grandes griffes
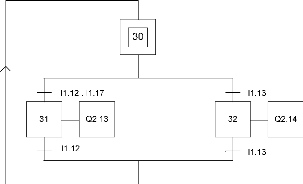
Figure 31: Grafcet 3 grandes griffes
3.4 Grafcet table elevatrice
Rédigé par TCHIEGANG MBITCHA Alain Bertrand
|
71
|
Programmation des sequences de fonctionnement et cablage
entrees / sorties

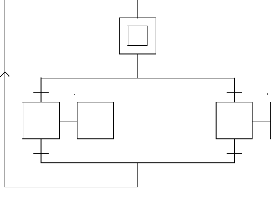
40
I1.14
I1.15
41
Q2.11
42
I1.14
Figure 32 : Grafcet 3 table
élévatrice
I1.15
Q2.16
3.5 Programmation des sequences sous PL7 Pro
Voir annexe pour la programmation des séquences de
fonctionnement sous PL7 Pro. 3.6 Traitement sur Coupure et Reprise Se
cteur
Lors d'une coupure du secteur, le bit %S1 se positionne à
1.
Pour réinitialiser toutes les variables lors du retour du
secteur, le bit %S1 doit positionner à 1 par programme le bit %S0.
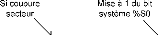
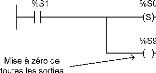
Figure 33 : Traitement sur coupure et reprise
secteur
%S1 et %S0 sont remis à zéro automatiquement
après une scrutation complète du programme.
Programmation des sequences de fonctionnement et cablage
entrees / sorties

III. Cablage des entrees / sorties
1. Alimentation de l'automate
L'automate sera alimenté par le réseau
monophasé 230V ; 50 Hz. La protection sera de type
magnéto-thermique.
Il est souhaitable d'asservir l'alimentation de l'automate par un
circuit de commande spécifique (contacteur KM0).
De même, les sorties seront asservies au circuit de
commande et alimentées après validation du chien de garde
(vérification du temps de scrutation à chaque cycle automate).
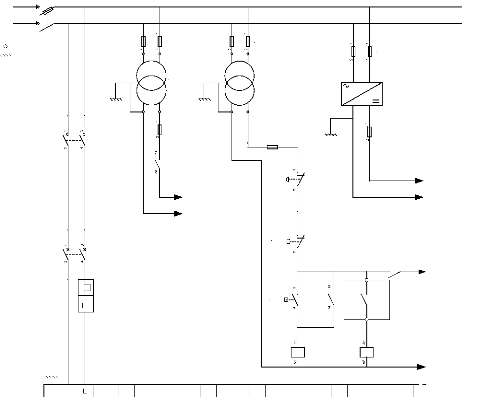
PE
L1
N
1
3
PE
4
2
1
2
3
7 F3
7 2 x F2
7 KA1
230 / 110 V
4
7 T1
e
Alimentation
commande
f
5
6
7
8
7 2 x F4
9
230 / 24 V
1 2
7 F5
7 T2
7 KM0
7 S2
7 Bcp
10
7 S1
11
12
7 KM0
13
7 KA1
14
15
Chien de
garde
16
7 2 x F6
7 F7
13 14
17
7 KA1
AL
18
24 VDC
d
Vers sorties
automate
Alimentation
commande
7 Q1
7 KM0
7 Q2
N
I >
a
b
c
Alimentation de l'automate Sorties automate
Alimentation de l'automate
Sorties automate
AUTOMATE
Alimentation des capteurs
0 V 24 V
1
2
3
4
5
6
7
8
9
10
11
12
13
14
15
16
17
18
Entrées automate


Figure 34: Alimentation automate
|
|
|
|
Rédigé par TCHIEGANG MBITCHA Alain Bertrand
|
73
|

2. Alimentation des entrees de l'automate
Le module TSX DEY 32D2K comporte des entrées
alimentées en 24 VCC et est équipé de 2 connecteurs HE10
male : [3]
Connecteurs A et B associés au raccordement des
entrées :
A (0 à 15)
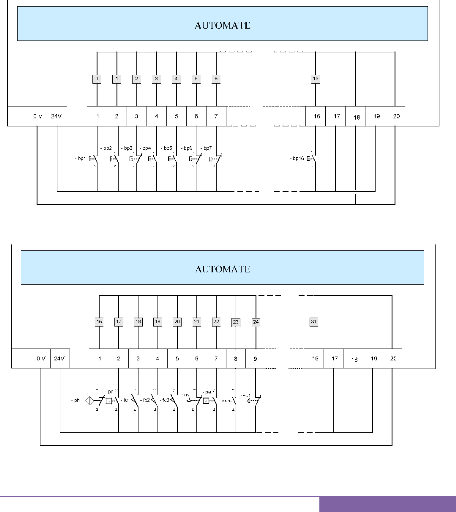
74
Rédigé par TCHIEGANG MBITCHA Alain Bertrand
Figure 35: Entrées connecteur A
Figure 36: Entrées connecteur B
B (16 à 31)
Programmation des sequences de fonctionnement et
cablage entrees / sorties

3. Alimentation des sorties de l'automate :
Le module TSX DSY 32T2K comporte des sorties statiques de type
source logique positive et équipé
de connecteurs HE10 male : [3]
connecteur A pour les sorties 0 à 15
connecteur B pour les sorties 16 à 31 Nous avons que
représenté le connecteur A
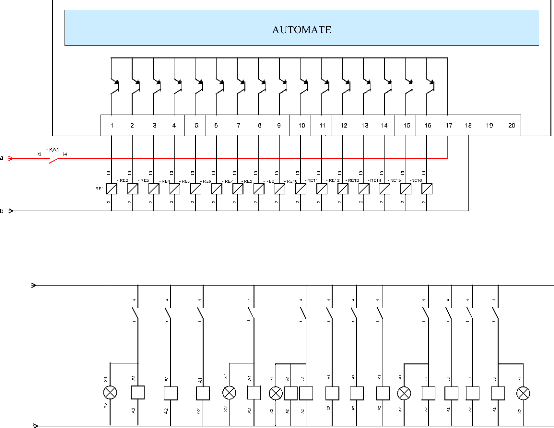
Figure 37: Sorties connecteur A
7 RE1 7 RE2 7 RE3 7 RE4 7 RE5 7 RE6 7 RE7 7 RE8 7 RE9 7 RE10 7
RE11 7 RE12
7 KM4
7 KM1L
7 H4
7 KM1Y
7 H5
7 KM1.
7 H2
7 KM7 7 KM2
7 KM3
7 KM9D
7 KM9G
7 H8
7 KM5D
7 KM5G
7 KM6
7 KM8
7 H7
d
c
Figure 38 : Alimentation bobines contacteurs et
voyants
Rédigé par TCHIEGANG MBITCHA Alain Bertrand
|
75
|
Programmation des sequences de fonctionnement et cablage
entrees / sorties
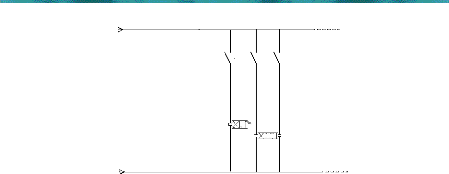
7 RE13
1 4
7 RE14 7 RE15
1 4
f
e
4
Figure 39: Alimentation bobines distributeurs
Conclusion :
Au terme de ce chapitre, nous avons choisi l'automate
programmable qui remplacera la partie commande de notre système. La
programmation des séquences de fonctionnement a été faite
avec le logiciel PL7 Pro. Par ailleurs nous avons réalisé les
schémas pour l'alimentation de l'automate, ses entrées et ses
sorties. Le prochain chapitre porte sur la simulation de l'automatisme
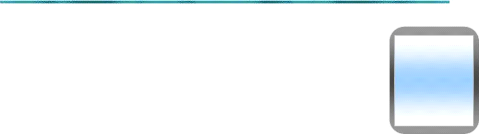
Chapitre
7
CHAPITRE 7 :
Simulation
Introduction :
Ce chapitre presente les resultats des tests effectues au sein du
Laboratoire d'Automatique et de Productique de l'Ecole Nationale Superieure
Polytechnique.

Il existe deux façons de tester le fonctionnement d'un
automatisme [9] :
· En simulation (sans partie opérative)
Le fonctionnement est vérifié en simulant le
comportement de la Partie Opérative, c'est à dire l'état
des capteurs et des actionneurs, en validant uniquement les entrées.
· En condition réelle (avec Partie Opérative)
Le fonctionnement est vérifié en suivant le comportement de la
Partie Opérative
La simulation a été effectuée sans partie
opérative dans le laboratoire d'automatique et de
productique de l'Ecole Nationale Supérieure
Polytechnique qui dispose de deux automates TSX Premium.
La configuration matérielle de ces automates est
différente de celle utilisée dans notre projet (position des
modules E/S sur le rack), une adaptation a été nécessaire
afin de pouvoir tester notre programme. Ce qui fait qu'au lieu de
%I1.x nous aurons %I4.x, de même
%Q2.x sera remplacé par %Q5.x
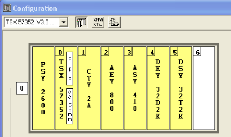
Figure 40: Configuration automate du
laboratoire
I. Test du programme : simulation 1.
Principe
Les tests des programmes passent nécessairement par le
transfert du programme vers l'automate. Pour ce faire nous allons passer par le
lien série qui relie l'ordinateur au module processeur. La seule
condition pour pouvoir transférer le programme en cours est qu'il soit
entièrement validé, c'est-à-dire qu'il ne contienne pas de
partie non validée (en rouge). Lorsque c'est le cas :
· Sélectionner le menu AP
· Dans le menu déroulant, sélectionner
Transférer programme
- Choisir le sens du transfert PC -->
Automate

- Valider par OK (le transfert s'opère
sans surprise si le câble de liaison PC - automate est en place)
NB : pour que le transfert se déroule il
faut au préalable préciser le driver de communication
utilisé et l'adresse de l'automate.
Lorsque le transfert est terminé, il nous faut
établir explicitement la connexion à partir du menu
AP et choisir l'action Connecter, un petit
rectangle bleu se déplace de gauche à droite signifiant que la
scrutation est en cours. A partir de ce moment, si nous entrons dans une
fenêtre de programmation, nous verrons plusieurs cases. Cette couleur
indique la validité de la condition en question.
Le programme transférer et nous sommes connecté,
il s'agit maintenant de lancer l'exécution du programme dans l'A.P.I
· Sélectionner dans le menu AP
l'action Init... cette action force toutes les étapes
initiales à la valeur 1. c'est l'initialisation de tous les grafcets.
· Sélectionner dans le menu AP
l'action Run... cette action active toutes les sorties.
2. Application
Le driver utilisé est : UNTLW01
disponible sur le net [14] Et l'adresse automate :
SYS
Après l'action sur Init... nos
différents grafcets sont initialisés.
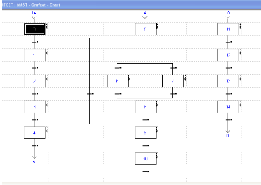

Figure 41: Initialisation grafcet
principal

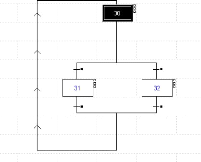
Figure 42: Initialisation grafcet grandes
griffes
Maintenant vient la phase de test de notre programme. Nous
devons respecter scrupuleusement les changements d'états des variables
du système, conformément à l'évolution de la partie
opérative. Pour cela nous nous servons de la table d'animation, les
variables d'entrées sont forcés à
l'état 1 et nous contrôlons l'état des
variables de sorties.
Nous vous présentons ci-dessous les résultats
obtenus à l'étape 5 du grafcet principal.
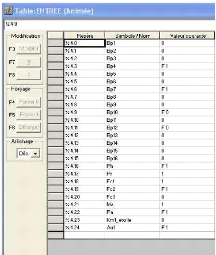
Figure 43: Table d'animation entrée
Nous forçons à 1 les variables d'entrées
intervenant dans la transition X4 ? X5 à savoir :
%I4.3, %I4.19, %I4.22, %I4.16, %I4.6 (%I4.18 et %I4.21 sont par défaut
à l'état 1) (voir figure ci-dessus)

L'étape X4 étant déjà active
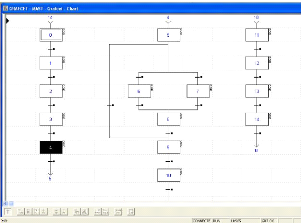
Figure 44: Etape X4 validée
et la transition X4 ? X5 venant d'être
validée, l'étape X5 s'active et l'étape X4 se
désactive.

Figure 45: validation de la condition
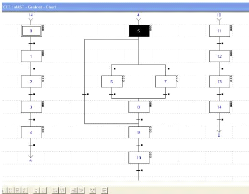
Figure 46: Activation de l'étape X5
L'étape X5 s'active on constate sur le tableau ci-dessous
que les actions associées sont actives à savoir : la centrale
hydraulique a démarré (%Q5.0 = 1), le contacteur de ligne est
fermé (%Q5.1 = 1),

de même le contacteur triangle (%Q5.3 = 1), le frein s'est
libéré (%Q5.12 = 1), la centrale de lubrification a
démarré (%Q5.5 = 1) et le moteur trancheur et son moteur
ventilation sont lancés (%Q5.4 = 1).
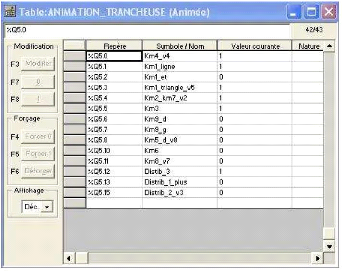
Figure 47: Table d'animation sortie
La figure ci-dessus montre bien qu'à l'étape X5,
la sortie %Q5.0 est active. Cette sortie est celle de la centrale
hydraulique.
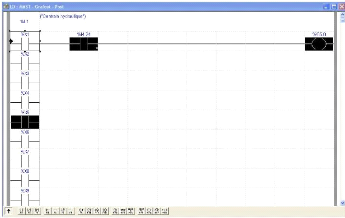
Figure 48: Sortie active
Rédigé par TCHIEGANG MBITCHA Alain Bertrand
|
82
|
|

En ce qui concerne les grandes griffes, à l'activation de
l'étape X31 (figure ci-dessus)
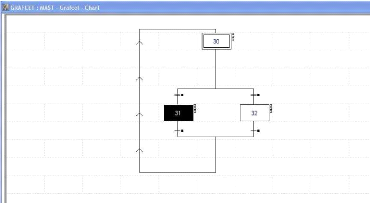
Figure 49: Activation de X31
La figure ci-dessous montre bien que la sortie %Q5.13 actionnant
le serrage est active.
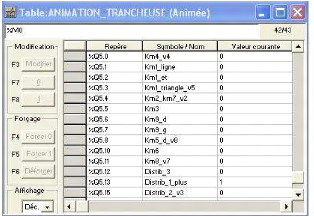
Figure 50 : Sortie %Q5.13
En somme, plusieurs tests et ceci pour tous les grafcets ont
été effectués, afin de valider notre programme.
Rédigé par TCHIEGANG MBITCHA Alain Bertrand
|
83
|
|

II. Ecrans d'exploitation
Les écrans d'exploitation vont nous permettre de
faciliter l'exploitation du processus automatisé (comprendre facilement
l'état du procédé et d'intervenir rapidement en cas de
problème).
1. Principe
Le principe des objets est qu'ils sont disposés les uns
par dessus les autres. Le premier sera affiché lorsque la variable
associée sera à 0 et le second lorsqu'elle sera à 1.
Nous indiquons ci-dessous sommairement la procédure de
création d'un écran, pour plus d'explications voir
référence [15].
· Double cliquez sur « écrans d'exploitation
» dans le navigateur.
· Cliquez avec le bouton droit sur écran et
choisissez créer.
· Cliquez sur « nouvel_ecran_0 »
· Placez un objet `'voyant» par exemple en
sélectionnant l'onglet « objet ». Cliquez sur la page
`'voyant» dans « Afficheur » et faites un copier
coller d'un voyant vers votre écran.
Le voyant est composé des 2 objets animés par la
variable %MW0:X0, il va falloir remplacer cette adresse par celle
appropriée.
Nous avons réalisé quatre écrans
d'exploitation :
- L'écran d'accueil
- L'écran pour l'exploitation des grandes griffes,
chariot et table élévatrice
- L'écran pour l'exploitation du grafcet principal
- L'écran pour visualiser l'état des
différents capteurs
2. Application Ecran d'accueil
Rédigé par TCHIEGANG MBITCHA Alain Bertrand
|
84
|
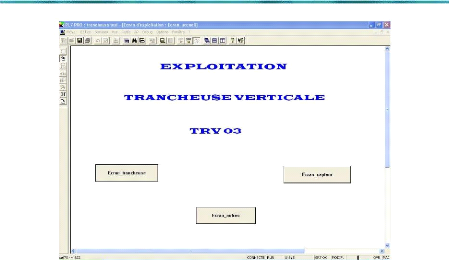
Figure 51: Ecran d'accueil
Ecran principal
Cet écran est obtenu après l'initialisation des
grafcets.
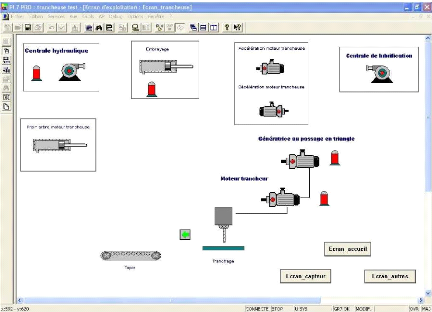
Figure 52: Ecran principal en mode stop
Rédigé par TCHIEGANG MBITCHA Alain Bertrand
|
85
|

Lorsqu'un objet représentant soit un moteur, une pompe ou
un voyant est n'est pas actif, une couleur rouge apparaît sur une partie
de l'objet. Et une couleur verte dans le cas contraire.
Il est présenté ci-dessous, l'écran
principal à l'étape X5. Nous rappelons qu'à ce niveau les
sorties suivantes sont actives :
· Centrale hydraulique
· Démarrage étoile-triangle
effectué
· Centrale de lubrification
· Frein libéré
· Moteur trancheur
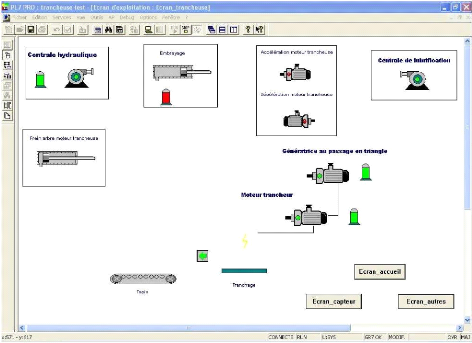
Figure 53: Ecran principal à l'étape
X5
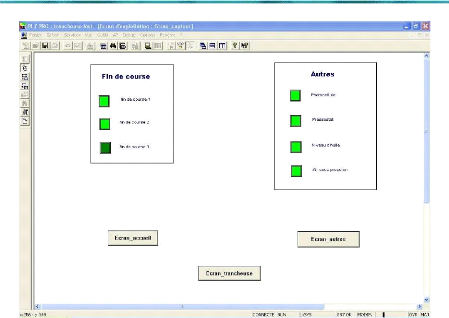
Figure 54: Etat des capteurs
NB : Capteurs actifs en vert clair et inactifs
en vert foncé.
Conclusion :
Cette simulation nous a permis de déceler des erreurs de
programmation qui ont été toutefois corrigées. Notre
programme est testé et entièrement validé, il ne reste
plus qu'à éditer le dossier de l'application qui sera disponible
en annexe 2.
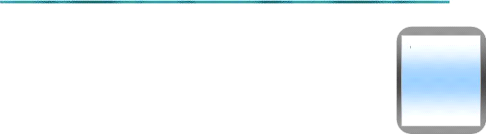
Chapitre
8
CHAPITRE 8 :
cAnalyse
financiire
Introduction :
L'objectif de ce chapitre est d'effectuer une analyse financiere
par l'estimation des différents couts du projet. Par ailleurs il serait
judicieux de faire une présentation sur le choix des appareillages
électriques.

NB : les références ci-dessous
sont tirées du catalogue 1999/2000 de Schneider Electric, sauf
indication contraire.
I. Choix des appareillages electriques
1. Conta cteurs
Le contacteur est un appareil de commutation, de connexion qui
permet à partir de la commande en tout ou rien d'un
électro-aimant d'établir ou d'interrompre par
l'intermédiaire de contacts le circuit entre le réseau
d'alimentation et le récepteur.
Les contacteurs utilisés pour ce projet ont
été choisis en général en fonction :
- De la nature de la tension du réseau : 380 v
- Des caractéristiques de la charge (puissance et courant
d'emploi)
- De la catégorie d'emploi du contacteur (AC3, DC5)
2. Transformateurs
Le transformateur d'alimentation à ce niveau assure la
transformation de la tension du secteur, en diminuant sa valeur de façon
à obtenir les tensions d'alimentation des différents circuits.
o Choix du transformateur T1 (sortie : 110 VCA/
2A)
Puissance nominale : 110 × 2 = 220 VA
Référence : ABL - 6TD25G
Fusible du primaire F2 : 2 A aM
Fusible du secondaire F3 : 10 A gG
o Choix du transformateur T2 (sortie 24 VAC /
2A)
Puissance nominale : 24 × 2 = 48 VA
Référence : ABL - 6TD06B
Fusible du primaire F4 : 0,5 A aM
Fusible du secondaire F5 : 2A Gg
3. Alimentation redressee, monophasee
L'alimentation redressée nous permet d'obtenir à
partir de la tension du secteur, une tension diminuée et continue.
Nous avons besoin pour alimenter les sorties de l'automate d'une
tension continue de 24 V et d'une puissance de 24 W.
L'alimentation choisie à pour
caractéristiques :

Tension nominale de sortie : 24VDC
Référence : ABL - 6RF2401
Fusible en amont F6 : 2A aM
Fusible en aval F7 : 2A gG
4. Relais electroniques
Les relais utilisés permettent de commuter la puissance
pour les bobines des contacteurs.
Référence : KA4474-1
Bobine : 24 VDC
Contact : 7,5 A 120 VCA / 5A 28 VDC
3.P.D.T 11 pins
|
|
|
Figure 52 : Relais 11 pins
|
5. Disjon cteur magneto-thermique unipolaire +
neutre
Il assure une protection contre les surcharges et les
courts-circuits d'un récepteur électrique.
Pour choisir le calibre du disjoncteur on prend en compte les
trois caractéristiques suivantes du module d'alimentation TSX PSY 2600
:
- Le courant nominal d'entrée : Ieff = 0,3 A
- Le courant d'appel : I = 75 A
- Le It = 0,067 As
Le choix du calibre minimum du disjoncteur se fait de la
façon suivante :
- Calibre disjoncteur IN > Ieff alimentation,
- I max. disjoncteur > I appel alimentation,
- It disjoncteur au point A de la courbe (des
caractéristiques fournies par le constructeur de disjoncteurs) > It
alimentation.
Référence : GB2 - CD12
Calibre : 6A
6. Fusible Fl de l'interrupteur se ctionneur
Le calibre du fusible F1 doit être supérieur ou
égal à la somme des calibres des fusibles et disjoncteur aval.
Calibre F1 > = 0,5 + 2 + 2 + 6 = 10,5

Soit : F1 = 12 A aM
7. Interrupteur se ctionneur
Calibre : 12 A
Référence : VCDN 12
Eléments additifs
Référence : VZN 11 et VZN 14
II. Devis estimatif
· Equipements
Tableau 17 : Références
contacteurs
Contacteurs
|
Références [4]
|
Caractéristiques électriques
|
Quantité
|
Prix unitaire €
|
Référence prix
|
1
|
LC1-D6511B5
|
440V 65 A - bobine 24 V CA
|
2
|
288,21
|
Internet Catalogue en ligne de
Schneider Electric [11]
|
2
|
LC1-D4011B5
|
440V 40 A - bobine 24 V CA
|
1
|
169,80
|
3
|
LC1-F265B7
|
440V 265 A - bobine 24 V CA
|
2
|
856,38
|
4
|
LC1-K0610B7
|
440V 6 A - bobine 24 V CA
|
5
|
23,51
|
5
|
LC1-D1810B5
|
440V 18 A - bobine 24 V CA
|
1
|
73,95
|
6
|
LC1-D2500B5
|
440V 25 A - bobine 24 V CA
|
2
|
91,40
|
7
|
LC1-K1210B7
|
440V 12 A - bobine 24 V CA
|
1
|
28,02
|
8
|
LC1-K0910B7
|
440V 9 A - bobine 24 V CA
|
1
|
24,67
|
Total 1 2885,97
|
|

Tableau 18 : Autres références
Autres
|
Référence [4]
|
Caractéristiques électriques
|
Quantité
|
Prix unitaire €
|
Référence prix
|
KA1
|
CA2-DN31B5
|
3 F + 1 O - instantané - 10 A - 24 V CA
|
1
|
41,56
|
Internet Catalogue en
ligne de
Schneider Electric [11]
|
Transformateur Ti
|
ABL - 6TD25G
|
230..400 V - 2 x 115 V - 250 VA
|
1
|
101,32
|
Transformateur T2
|
ABL - 6TD06B
|
230..400 V - 2 x 24 V - 63 VA
|
1
|
68,60
|
Alimentation redressee
|
ABL - 6RF2401
|
230-400-24V 1A
|
1
|
119,00
|
bisjoncteur magneto-thermique
|
GB2 - CD12
|
6 A 1P plus N 1d
|
1
|
21,58
|
Voyant lumineux vert
|
XB4 - BVB3
|
DEL intégrée 24 V bornes
|
3
|
11,80
|
Voyant lumineux rouge
|
XB4 - BVB4
|
DEL intégrée 24 V bornes
|
3
|
11,80
|
Voyant lumineux bleu
|
XB4 - BVB6
|
DEL intégrée 24 V bornes
|
2
|
11,80
|
Relais
|
KA4474 - 1
|
Bobine : 24 VDC
|
17
|
3,99
|
Sectionneur
|
VCDN 12
|
690 V 12 A
|
1
|
17,76
|
pressostat
|
XML - A070D2S11
|
70 bar écart fixe
|
1
|
101,52
|
bisjoncteur moteur
MO
|
GV7 - RS150
|
90 à 150 A
|
1
|
726,23
|
M3
|
GV2 - M03
|
0,25 à 0,4 A
|
1
|
48,66
|
M4
|
GV2 - M20
|
13 à 18 A
|
1
|
61,40
|
M5
|
GV2 - M21
|
17 à 23 A
|
1
|
69,38
|
M6
|
GV2 - M16
|
9 à 14 A
|
1
|
56,66
|
M7
|
GV2 - M04
|
0,4 à 0,63 A
|
1
|
48,66
|
M8
|
GV2 - M10
|
4 à 6,3 A
|
1
|
48,66
|
M9
|
GV2 - M06
|
1 à 1,6 A
|
1
|
48,66
|
Rack standard 6 positions
|
TSX RK 6
|
-
|
1
|
129,61
|
Internet [12]
|
processeur avec carte
extension memoire
|
TSX P57 352M
|
-
|
1
|
2782,90
|
Module d'entries A'TOR''
|
TSX DEY 32D2K
|
-
|
1
|
363,00
|
Module d'entries A'TOR''
|
TSX DEY 32D2K
|
-
|
1
|
363,00
|
Module d'alimentation
|
TSX PSY 2600 M
|
-
|
1
|
337,05
|
Pile de sauve garde memoire
|
TSX PLP 01
|
-
|
1
|
13,60
|
Total 2 5731,04
|
|
Rédigé par TCHIEGANG MBITCHA Alain Bertrand
|
92
|

Tableau 19 : Références
fusibles
Fusibles
|
Calibre (A)
|
Type
|
Quantité
|
Prix unitaire
FCFA
|
Référence prix
|
0,5
|
aM
|
1
|
400
|
FOKOU - MOKOLO
|
2
|
aM
|
2
|
300
|
2
|
gG
|
2
|
300
|
6
|
gG
|
1
|
600
|
12
|
aM
|
1
|
725
|
Total 3 2925
|
|
NB : les taxes à la SCTB représentent 33%
du prix de l'équipement (logistique exclue) Ainsi donc, le prix
de l'ensemble des équipements est estimé à 7.521.566,33
Fcfa
Et le prix du logiciel PL7 est de 2.552.709,14 Fcfa
· Câblage
Dans un processus automatisé, les câblages prennent
du temps et coûtent cher (30 % de l'équipement au minimum). [1]
Tableau 20 : Devis estimatif
Articles
|
Prix (Fcfa)
|
Equipements
|
7.521.566,3
|
Logiciel PL7 Pr0
|
2.552.709,1
|
Cablages (30% des Equipements)
|
2.256.469,9
|
Imprevus (2% du total)
|
246.614,9
|
TOTAL
|
12.577.360,3
|
Conclusion :
Il faudra donc investir la somme de 12.577.360 (douze millions
cinq cent soixante dix-sept mille trois cent soixante) francs pour ce projet.
Sachant que l'immobilisation financiere due aux défaillances au niveau
de la trancheuse verticale en une année est de 8.218.368 francs (684.864
francs/mois), le temps de retour sur investissement est de 18 mois.
Conclusion

2onctUsion
Le travail qui s'achève portait sur l'amélioration
des performances de la trancheuse verticale TRV 03 de la SCTB Sarl. Il
s'agissait principalement d'une reconception de la partie commande de cette
machine en migrant vers la logique programmée. Pour y parvenir, cette
machine ne disposant pas d'une documentation technique complète, nous
avons en premier lieu décri et analysé le système
automatisé existant, ressorti ses différentes
fonctionnalités, et le modéliser sous la base du GRAFCET.
L'automate programmable choisi est un TSX Premium, il remplace la partie
commande. Les séquences de fonctionnement ont été
programmées, testées et validées.
Par ailleurs, ce travail qui avait aussi pour objectif de
faciliter la maintenance corrective de cette machine permettra ainsi au service
maintenance, en cas de panne accidentelle, une meilleure aide au diagnostic.
Pour ce faire il n'aura qu'à repérer sur l'écran de
contrôle le niveau d'évolution du grafcet ou se servir des
écrans d'exploitation que nous avons développé.
La SCTB dispose à présent de toutes les
informations techniques et financières lui permettant de mettre en
oeuvre ce projet qui a été estimé à 12.577.360
(douze millions cinq cent soixante dix-sept mille trois cent soixante)
En perspectives nous proposons :


Un suivi de la maintenance pour cette machine.
Après acquisition par la SCTB de l'automate programmable
et des différents appareillages électriques, une autre simulation
: cette fois avec la partie opérative et en se servant du logiciel PL7
Pro, une vérification du raccordement des capteurs aux entrées de
l'automate.
Que ce travail effectué pour la trancheuse verticale TRV
03 soit étendu aux autres trancheuses TRH 01 et TRV 02.

ooforences bibliographiques
References Bibliographiques
[1] Jean - Claude Humblot. 1993. Automates
programmables industriels.- Ed Hermes : Paris ;
139p
[2] Maurice Milsant. 1976. Automatismes d
sequences.- Ed Eyrolles : Paris ; pp 35
[3] GROUPE SCHNEIDER. Modicom Telemecanique : TSX
Premium, Automates TSX 57 Manuel demise en ceuvre
[4] Schneider Electric : Controle
industriel, Catalogue 1999/2000
Documents Electroniques
[5] Genie electrique electrotechnique automatisme [en
ligne]. Disponible sur Internet :
http://www.geea.org/IMG/pdf/
[6] Wikipedia. Machine
electrique [en ligne]. Disponible sur internet :
http://fr.wikipedia.org/wiki/Machine_/0C3/0A9lectrique
[7] Pierre Duysinx, Henri Lecocq. Structure
des Automates Programmables. [en ligne]. [Universite de Liege]
15p. Disponible sur Internet :
http://www.ingveh.ulg.ac.be/fr/cours/Notes_de_cours_Syst_0015/Chapitre/0202.pdf
[8] Automate programmable industriel [en ligne]. 10 p.
Disponible sur Internet :
http://michel.all.free.fr/Fichierstexte/Automate/020(APO1.pdf
[9] Introduction a la logique sequentielle [en ligne].
41 p. Disponible sur Internet :
http://auto.polytech.univ-tours.fr/automatique/AUS/ressources/Poly1.pdf
[10] Nicolas Jouvray. Langages de
programmation pour systemes automatises [en ligne]. Disponible sur
Internet :
http://www.techniquesingenieur.fr/dossier/langages_de_programmation_pour_api_norme_iec_1131_3/S8030?Jsessionid=
D45C616F089551FDA EB6BD952AA047E6gresourceName=true
[11] e-Catalogue Schneider Electric France [en ligne].
Disponible sur Internet :
http://www.e-catalogue.schneider-electric.fr/
Rédigé par TCHIEGANG MBITCHA Alain Bertrand
|
95
|

[12] Automatismes Industriel [en ligne]. Disponible sur
internet :
http://sylvain.marsol.free.fr/index_fichiers/premium.htm
[13] Automates programmables Programmation
du Grafcet [en ligne]. [Universite catholique de Louvain] 43 p.
Disponible sur Internet :
http://www.prm.ucl.ac.be/cours/meca2755/05-
06/Automate2forweb.pdf
[14] Telechargement Drivers UNITELWAY SCHNEIDER [en
ligne]. Disponible sur Internet :
http://www.irai.com/ta7_fichiers/page0002.html
[15] A. THIERRY. Doc ecrans
d'exploitation [en ligne]. P.S. :2006 . 6 p. Disponible sur
Internet :
http://wwwphp.ac-orleans-tours.fr/lyc-augustin-thierryblois/bts_mai/doc/doc_ecran_exploitation.pdf
[16] Logique appliquee aux Systemes Automatises [en
ligne] . 4 p. Disponible sur Internet :
http://lyc-francois1-lehavre.ac-
rouen.fr/public/si/telecharger/cours/logique°/020appliqu°/0
E9e°/020au°/020syst°/0 E8mes.pdf
[17] About Capital [en ligne]. disponible sur Internet :
http://www.capitalmachineco.com/about.asp
Rédigé par TCHIEGANG MBITCHA Alain Bertrand
|
96
|