CHAPITRE I. GENERALITES
I.1 Présentation de
l'entreprise
L'histoire de CONGELCAM débute en 1982, quand son
Directeur Général actuel, M. NGOUCHINGUE Sylvestre commence la
vente en détail de poissons congelés. Ses premiers
bénéfices sont réintroduits dans l'achat de
congélateurs, ce qui augmenta rapidement son chiffre d'affaire.
Les établissements CONGELCAM ne tarderont pas alors
à naître, avec la construction des premières chambres
froides. Le génie de M. NGOUCHINGUE pour les affaires étant
remarquable, ses activités ne cesseront de croître pour aboutir en
1994 à la création de la société CONGELCAM Sarl,
avec un capital de 2 milliards de francs CFA.
Aujourd'hui les activités de CONGELCAM consistent
essentiellement en l'importation, la distribution et la vente des produits de
la mer et de certaines viandes. Ainsi, l'entreprise dispose de plusieurs sites
d'entreposage de grande envergure à Douala, terminus des bateaux
d'importation. Des camions frigorifiques sont chargés d'acheminer les
produits ainsi stockés vers d'autres sites disséminés dans
les autres provinces (Centre, Ouest, Est, Sud, Nord-Ouest, Sud-Ouest). De
là, des camions plus légers pourront ravitailler les points de
vente. L'exceptionnelle capacité logistique actuelle de CONGELCAM permet
de réceptionner un bateau entier de produits pratiquement tous les 10
jours, faisant d'elle le leader national incontesté sur le marché
du poisson et de la volaille.
I.2 Les chambres froides I.2.1
Présentation
Une chambre froide est une enceinte destinée à
conserver des produits (agroalimentaires, pharmaceutiques, ...), à une
humidité relative et une température (généralement
inférieure à la température ambiante) fixées. Ses
façades, son plafond et son plancher sont thermiquement isolés.
La technologie d'isolation des façades et du plafond la plus
utilisée actuellement est celle des panneaux sandwiches, où une
couche compacte d'isolant (polyuréthane, polystyrène, ...) est
prise en sandwich entre deux plaques métalliques. Ces panneaux sont
préfabriqués, et permettent des constructions plus rapides, plus
efficaces et plus économiques que les technologies
précédentes (AUDIFFRET, 1984).
Les conditions climatiques internes requises sont
assurées par des installations frigorifiques, dont les
évaporateurs (organes de production de froid) sont situés dans
l'enceinte, et le reste de l'installation à l'extérieur. Pour les
plus grandes chambres, une ossature métallique vient renforcer
l'édifice en panneaux sandwiches. On parle alors souvent
d'entrepôt frigorifique.
I.2.2 Exploitation
I.2.2.1 L'installation frigorifique
Le circuit frigorifique est généralement celui
d'un cycle de réfrigération à compression mécanique
de vapeurs. Une configuration très souvent rencontrée sur les
entrepôts frigorifiques est la suivante :
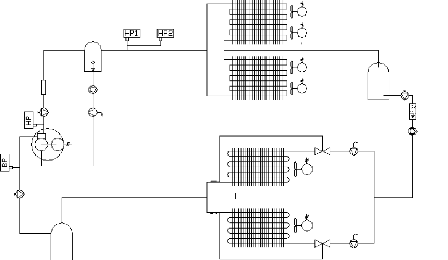
Electrovanne liquide
Bouteille d'aspiration
Pressostats de régulation
Condenseur
Séparateur d'huile
Bouteille liquide
Voyant d'huile
Electrovanne d'huile
Filtre déshydrateur Voyant liquide
Compresseur
Vanne 3 voies d'aspiration
Evaporateur
Détendeur thermostatique
Figure I.1 : Exemple de schéma fluidique
d'installation frigorifique I.2.2.2 Le calcul d'une chambre froide
Le dimensionnement des éléments d'une chambre
froide a pour base le calcul des puissances frigorifiques à fournir par
les évaporateurs. Ces puissances s'obtiennent par un bilan thermique sur
la chambre. Pour une chambre classique, les charges à calculer sont :
· Charges par transmission à travers les parois Qtp
: il s'agit des gains de chaleur par échange thermique avec
l'environnement extérieur et le sol ;
· Charges par renouvellement d'air Qra : dans de
nombreuses chambres froides, il est prévu de renouveler plus ou moins
l'air ambiant par de l'air extérieur. Ce sont les gains thermiques
apportés par cet air extérieur qui sont pris en compte dans cette
rubrique ;
· Charges par ouverture des portes Qop : ce sont les
charges dues aux échanges de matière entre l'intérieur et
l'extérieur, suite à l'ouverture des portes ;
· Charges dues aux appareillages divers Qad : il s'agit
des charges engendrées par le fonctionnement d'appareils tels que les
luminaires, les moteurs d'évaporateurs, les chariots
élévateurs, ... ;
· Charges dues au personnel travaillant Qpt : elles
sont dues à la chaleur dégagée par les corps en
activité ;
· Charges dues au dégivrage Qdg : en fonction de
la température de la chambre, il est possible d'avoir une formation de
givre sur les évaporateurs. Dans ce cas, il est alors prévu une
procédure de dégivrage, destinée à fondre ce givre.
C'est la chaleur dégagée au cours du dégivrage qui est
prise en compte dans cette rubrique ;
· Charges dues aux denrées Qdr : ces charges sont
dues au fait que les denrées sont généralement introduites
à une température supérieure à celle d'entreposage.
Il faut donc les porter à bonne température. Aussi, les produits
végétaux dégagent une chaleur de respiration qu'il faut
compenser.
La charge totale est alors donnée par :
Qtot = Qtp + Qra + Qop + Qad
+ Qpt + Qdg + Qdr (1).
Comme une installation est conçue pour fonctionner
tf ( tf = 24 ) heures par jour,
cette
charge sera multipliée par 24 pour avoir la puissance
nette à installer. Une valeur courante tf
de tf est 16 heures (BREIDERT, 1998).
I.2.2.3 La maintenance des installations frigorifiques
D'après la norme AFNOR NF X60 010 (ZWINGELSTEIN,
1995), la maintenance se définie comme : « Toutes les
activités destinées à maintenir ou à
rétablir un bien dans un état ou des conditions données de
sûreté de fonctionnement, pour accomplir une fonction requise. Ces
activités sont une combinaison d'activités techniques,
administratives et de management. ». Il faut noter ici que toute la
science de la maintenance consiste à atteindre ces objectifs de
sûreté de fonctionnement à moindre coût.
En ce qui concerne les installations frigorifiques de
chambres froides, il s'agira de garantir un niveau suffisant de
disponibilité des installations, car ici les arrêts
prolongés coûtent cher (dégradation des denrées
stockées). Cet objectif est atteint en assurant une bonne
fiabilité (maintenance préventive bien mise en oeuvre) et une
bonne maintenabilité (bonne gestion des stocks de pièces de
rechange et bonne réactivité du service maintenance face aux
défaillances). Précisons ici que ces installations sont
très souvent sujettes à des défaillances par
dégradation, et qu'un état de fonctionnement
dégradé ici est assimilable à un arrêt, car les
conséquences sur la conservation des denrées sont à long
terme identiques.
La maintenance préventive des installations
frigorifiques est principalement conditionnelle. Elle consistera donc au suivit
des pressions, températures, intensités absorbées,
degré de contamination en humidité du circuit, degré de
dégradation de l'huile, état sensitif des organes (toucher,
odorat, vue, ...), etc. Tout l'art ici étant alors de savoir bien
analyser les informations ainsi collectées, afin de décider des
actions à entreprendre.
Dans ce cadre, une bonne expérience est requise. Quand
cette expérience devient insuffisante pour expliquer des modes de
dégradations compliqués, alors un expert en la matière
s'impose, à moins d'avoir recours à un système d'expertise
informatique.
I.3 Principes de l'expertise
technique
I.3.1 Les principales étapes
Il n'existe pas de procédure type d'expertise
technique d'unités industrielles, car la démarche d'une expertise
dépend de la précision et de la profondeur recherchées.
Mais de façon générale, on retrouvera les étapes
suivantes (MONCHY, 2000) :
· Renseignements préliminaires : ici, une
enquête de terrain permettra de rassembler tous les
éléments de connaissance utiles : conditions de fonctionnement,
caractéristiques techniques, ... ;
· Observations et examens : il s'agit d'effectuer des
observations visuelles ou instrumentales des zones accessibles ;
· Diagnostic : il s'agit de retrouver les causes à
l'origine des disfonctionnements constatés dans les deux
premières étapes ;
· Propositions et remèdes : ici des mesures
correctives et préventives sont énoncées pour une remise
à niveau du dispositif expertisé.
Le rôle d'un système informatique d'expertise est
donc de mettre en oeuvre ces étapes de la manière la plus
automatique possible.
I.3.2 La phase de diagnostic
Dans la démarche précédente, c'est la
phase de diagnostic qui est la plus délicate à automatiser. Il
s'agira là d'inverser une relation de cause à effet. En d'autres
termes, connaissant les effets (symptômes observés sur
l'équipement), il faudra retrouver les causes qui les ont crées.
Pour y parvenir il existe actuellement deux grandes familles de techniques de
diagnostic automatique (ZWINGELSTEIN, 1995).
I.3.2.1 Les méthodes de diagnostic interne
Ces méthodes supposent l'existence d'un modèle
physique ou expérimental de simulation de l'équipement à
diagnostiquer. Ce modèle de calcul décrit donc de façon
plus explicite la relation de cause à effet sous la forme :
? ?
E = F C (2)
( )
?
E est le vecteur des effets (observations
effectuées sur l'équipement), et (paramètres internes, non
accessibles par l'observation).
|
?
C celui des causes
|
|
?
Ayant observé sur l'équipement un vecteur
d'effets Em , le problème revient alors à
?
retrouver le(s) meilleur(s) vecteur(s) cause Copt
à l'origine des effets, en d'autres termes qui
? ?
minimise(nt) la fonction objectif
Em - F(C)
, où · est une norme définie dans l'espace
des

effets. La fonction F n'est très souvent pas
connue sous forme explicite, mais plutôt sous forme algorithmique. Dans
ce cas, la minimisation de la fonction objectif ne peut être faite que
par des méthodes non déterministes. Parmi ces méthodes,
les plus utilisées actuellement pour résoudre ce type de
problème sont :
· Les méthodes de Monte Carlo : la fonction
objectif est évaluée en un grand nombre de points pris
aléatoirement dans l'espace de recherche, et les solutions choisies
parmi ces points ;
· Le recuit simulé : à chaque
itération, on effectue un déplacement aléatoire à
partir du point en cours. Si le déplacement mène à une
valeur plus petite de la fonction, il est accepté. Sinon, il est
accepté avec une probabilité dépendant d'une «
température » T diminuant au fil du temps (d'où le nom de
recuit simulé) ;
· les algorithmes génétiques : un point de
l'espace de recherche est assimilé à un individu. Le principe est
alors de simuler l'évolution d'une population d'individus divers
auxquels on applique différents opérateurs
génétiques et que l'on soumet à chaque
génération à une sélection. Ces algorithmes sont de
plus en plus utilisés dans l'industrie, car ils sont
particulièrement adaptés aux problèmes d'optimisation
comportant de nombreux paramètres. Nous y reviendrons dans la suite.
I.3.2.2 Les méthodes de diagnostic externe
Ces techniques n'exigent pas un modèle de calcul pour
l'équipement. Par contre elles nécessitent une expertise humaine
ou une solide banque de données de retour d'expérience. Dans
cette catégorie, on peut citer :
· Méthode par reconnaissance des formes : ici, y
a d'abord une phase d'analyse où les données de retour
d'expérience sont regroupées en classes expérimentalement
ou à l'aide d'une technique de classification automatique (nuées
dynamiques, réseaux de neurones à apprentissage non
supervisé, ...). Les classes (ou formes) ainsi constituées
représentent des modes de fonctionnement de l'équipement.
Ensuite, un système de détection automatique est mis en oeuvre
à l'aide d'une technique de reconnaissance de formes (classification
floue, discrimination bayésienne, réseaux de neurones, ...).
Partant de symptômes observés sur l'équipement, ce
système de détection permettra de retrouver le mode de
fonctionnement correspondant.
· Méthodes utilisant des systèmes à
base de règles : les systèmes experts classiques sont à la
base de ces méthodes. Là, à partir d'une base de faits
(faits observés sur l'équipement) et d'une base de connaissances
(règles de
diagnostic), un moteur d'inférence pourra
inférer de nouveau faits, permettant ainsi de remonter aux causes des
effets observés. Ces méthodes peuvent aussi être mis en
oeuvre avec des systèmes intelligents plus évolués tels
que les réseaux bayésiens, les systèmes experts flous, et
même les agents intelligents, derniers nés des laboratoires de
recherche en intelligence artificielle.
I.4 Quelques techniques d'intelligence artificielle
I.4.1 La logique floue
La logique classique (booléenne) a pour base la
théorie des ensembles classiques. Dans cette dernière, tout
ensemble A est caractérisé par une fonction
caractéristique définie par :
1 si x A
?
?( )
x = (3). 0 si x A
?
Cette formulation très idéalisée ne permet
d'aborder qu'un nombre très restreint d'objets ou de
phénomènes du monde réel, qui est par essence
imprécis et incertain.
Les logiques multivalentes (trivalente, pentavalente, ...),
en introduisant d'autres niveaux entre 0 et 1 constituent une
amélioration à cette formulation de base, mais restent toujours
insuffisantes face à la grande complexité de notre monde. Les
deux énoncés suivants illustrent bien cette complexité qui
met en défaut ces logiques classiques :
E1 : Si la température augmente plus ou
moins, alors ouvrez légèrement les volets ;
E2 : Il pleuvra probablement aujourd'hui.
C'est pour traiter de tels énoncés vagues et
imprécis que L.A. Zadeh (à l'époque professeur à
l'Université de Californie Berkeley) a introduit en 1965 la
théorie des ensembles flous. Dans cette théorie, la fonction
caractéristique d'un ensemble, appelée fonction d'appartenance
peut prendre toutes les valeurs de l'intervalle [0, 1]. La logique floue est
une logique construite à partir de cette théorie des ensembles
flous.
En logique floue, on introduit la notion de variable
linguistique, dont les valeurs ne sont pas numériques, mais plutôt
symboliques. Ces variables sont donc une extension des variables binaires
classiques prenant les valeurs « Vrai » et « Faux ». Pour
définir une variable linguistique, il faut :
· Un univers U : par exemple, l'intervalle [0, 100] ;
· Une désignation valable sur cet univers : par
exemple « Température » ;
· Un ensemble de termes relatifs à cette
désignation : par exemples « Elevée », « Faible
», « Normale », ... .
Chaque terme ainsi définit est caractérisé
par un ensemble flou, donc par une fonction d'appartenance
ì(x) bien définie. On peut par exemple
définir les températures
« Normales » par la fonction ci-après :

ì(x)
18 23 28 T (°C)
Figure I.2 : Exemple de fonction d'appartenance
du terme « Température Normale »
L'accentuation des termes peut être
caractérisée par des modificateurs linguistiques, qui viennent en
fait modifier leurs fonctions d'appartenance ì(x) en
ìM (x) , rendant compte de la modification
apportée. Les modificateurs de base introduits par Zadeh sont :
· « Très » : 2
ì M ( x ) = [ ì
( x )] (4) ;
·

« Plus ou moins » : ìM (
x ) = ì(x) (5) ;
· « Non » : ìM ( x
) = 1 - ì(x) (6) .
Ceci dit, les énoncés E1 et E2
précédentes deviennent parfaitement manipulables en logique
floue.
|