|
|
Université de Yaoundé I University of
Yaoundé I
|
DÉPARTEMENT DE PHYSIQUE LABORATOIRE DE
SCIENCE DES MATÉRIAUX
THÈME :
L'ANALYSE DE SENSIBILITÉ DES
PARAMÈTRES SUSCEPTIBLES D'INFLUENCER L'ÉTAT DE SURFACE DES
PIÈCES OBTENUES EN FABRICATION ADDITIVE POUR DES APPLICATIONS
AÉRONAUTIQUES
Mémoire réalisé en partenariat
international présenté et soutenu en vue de l'obtention du
Master of Science en Physiques
Spécialité : Sciences
Matériaux
Par : KOND NGUE PIERRE GÉRARD
DAREL Matricule : 15S2382 Licencié
en Physique
Co-Encadreur : Encadreur :
Pr YETNA N'JOCK Michel Pr NDJAKA Jean-Marie
Bienvenu
Institut Polytechnique des Sciences Avancées
de Paris Université de Yaoundé I
Année 2021
KOND NGUE PIERRE GÉRARD DAREL
(c)2021
DÉDICACE
DÉDICACE
À mes parents :
Monsieur NGUEKOND Fridolin Félix
Médard et Madame NGUE Chantal ;
Monsieur BENGA Severin et Madame
BENGA Marie De-liz
À mes frères et soeurs...
À mes deux nièces préférées :
Gabriella et
Perline
MASTER II- LABORATOIRE SCIENCES DES
MATÉRIAUX
KOND NGUE PIERRE GÉRARD DAREL
(c)2021
REMERCIEMENTS
REMERCIEMENTS
Celui qui lira cette page risquera de croire que celle-ci
a été écrite en premier, ce qui n'est évidemment
pas le cas car, dit-on souvent, le meilleur se garde pour la fin. Il est
difficile pour moi d'exprimer par écrit la reconnaissance et la
gratitude qui reviennent aux personnes m'ayant aidé, encouragé et
soutenu pendant cette période chevaleresque de ma vie. J'espère
que vous tous et toutes sentirez la sincérité rattachée
à mes remerciements. Je tiens alors à rappeler que, si ce qui
suivra a été écrit avec la tête, cette page elle est
écrite avec le coeur.
Tout d'abord, je tiens à exprimer ici toute ma
reconnaissance à Dieu de qui sont venus tous les moyens
nécessaires pour l'aboutissement d'un tel travail, mes mots ne suffiront
pas pour Lui exprimer ma gratitude.
J'exprime mes vifs remerciements au Professeurs NDJAKA
Jean Marie Bienvenu et YETNA Michel, mes directeurs de mémoire qui ont
accepté de m'encadrer tout au long de ce travail. Merci de m'avoir fait
confiance, en respectant mes choix. Non seulement vous m'avez
imprégné des bases de la méthode et de la rigueur
scientifique, mais aussi vous m'avez appris des valeurs humaines et
d'intégrité. Trouvez ici toute ma reconnaissance et ma
gratitude.
Un merci particulier au Professeur YETNA Michel. Merci
pour sa disponibilité, ses conseils et sa promptitude à
répondre à mes différentes questions. Malgré la
distance et vos multiples occupations, vous avez toujours trouvé du
temps pour me tenir la main.
Je remercie particulièrement tous les enseignants
qui, malgré leurs multiples occupations, ont accepté de
participer à mon jury de soutenance.
J'ai naturellement une pensée forte pout tous mes
enseignants du Département de Physique de la Faculté des Sciences
de l'Université de Yaoundé I, sans qui je ne serais pas
arrivé à ce niveau. Un merci particulier aux enseignants du
laboratoire Sciences des Matériaux : Professeur NDJAKA Jean Marie
Bienvenu, Professeur ZEKENG Serge, Professeur NDOP Joseph, Professeur Annie
WAKATA, Dr TCHOFO Fidèle, Dr FEUDJIO David, Dr EDONGUE Hervais, Dr OTTOU
ABE Matin Thierry, Dr ETINDELE Anne Justine, Dr TEYOU NGOUPO Ariel.
Sans le soutien inconditionnel de ma famille, il m'aurait
été impossible de rédiger ce mémoire et surtout, de
poursuivre mes études jusque-là.
Je tiens à remercier ici mes parents : Monsieur
NGUEKOND Fridolin et Madame NGUE Chantal née NGO NEMI, Monsieur BENGA
Severin et Madame BENGA Marie De-liz née NGO KOMOL, Monsieur BILLONG Job
Salomon et Madame BILLONG Clotilde, Maman
II
MASTER II- LABORATOIRE SCIENCES DES
MATÉRIAUX
KOND NGUE PIERRE GÉRARD DAREL
(c)2021
REMERCIEMENTS
Micheline NGO KOMOL, le couple MOUKOURI merci d'avoir
toujours été là pour moi, puisse ce travail vous honorer.
Sachez que pour chaque goutte de sueur que j'ai versée pour ce travail,
vous en avez versé cent pour me soutenir.
Un merci spécial à mes soeurs KOMOL
Angeline, NGO KOMOL Orly, NGO KOMOL Micheline Perrette, OUM Kutcher, BENGA
Ghislaine, BENGA Tatiana, à mes frères KOMOL NGUE KOND Emmanuel,
KOMOL AMOS Stéphane, HOS MBOUI Otto Claude, KOND BILLONG DONALD pour
m'avoir soutenu tout ce temps et surtout d'avoir toujours supporté
toutes mes intrigues.
Mention spéciale à toi DOUNGUIA Carelle
Épse KOMOL pour tes conseils et ta promptitude à toujours vouloir
me venir en aide.
J'ai une pensée particulière pour vous qui
n'aviez jamais cessé de me soutenir tant spirituellement que moralement.
C'est aussi en pensant à vous que je suis allé au bout de mes
efforts. Vous êtes : NGUEKOND Fridolin, NGO NEMI Chantal, NGO KOMOL Marie
De-liz, KOMOL Angeline, KOMOL Micheline, Simon MANGUELE (et tout le peuple de
la MISCREV de Ngousso), DOUNGUIA Carelle.
Je serais impardonnable si je manquais d'adresser ici mes
sincères remerciement à mes camarades de promo ANEFO Patricia,
ASSANGA Lopez, BISSI Ferdinand, BOMBA Richard, KAMGA Arauld, KAMGANG Aubin,
KOWA Ibrahim, MOULIOM PAGNA, NDANG Kevin, NGOUME NDEMA Cédric, NOUDJI
Vincent, NZEBENG Dilane, OSSE Benjamin, OWONO MEBA Djames, Samuel TAGUIEKE, SOP
Leonel, TAMOKOUE Linda, TANKEU YANKAM, YONTA Julio et ZEBAZE Ginette. J'y suis
parvenu grâce à l'ambiance conviviale qu'on a toujours su
entretenir.
Au couple ABESSOLO, ESSAMA Aurélien, ainsi
qu'à tous les membres du Club Physique de l'Université de
Yaoundé I, votre indéfectible amitié et la grande
complicité qui anime notre relation ont été pour moi un
atout. Merci encore d'être là pour moi.
À toi Euphraisie, ton soutien et tes encouragements
ont été pour moi un véritable pilier. Grand merci à
toi.
Je tiens également à remercier toute la
communauté d'Otaku du groupe Otaku RPG Univers et en particulier
à son administrateur Guilaine dite « Tsunade ».
À tous ceux qui de près ou de loin ont
contribué d'une manière ou d'une autre à l'aboutissement
de ce travail, ainsi qu'à tous ceux qui estiment que leur nom devrait
figurer ici.
III
MASTER II- LABORATOIRE SCIENCES DES
MATÉRIAUX
KOND NGUE PIERRE GÉRARD DAREL
(c)2021
TABLE DES MATIÈRES
TABLE DES MATIÈRES
DÉDICACE I
REMERCIEMENTS II
TABLE DES MATIÈRES IV
LISTE DES TABLEAUX VII
LISTE DES FIGURES XI
LISTE DES ABRÉVIATIONS XIV
RESUME XII
ABSTRACT 1
INTRODUCTION GÉNÉRALE
2
CHAPITRE 1-ÉLÉMENTS DE BIBLIOGRAPHIE
4
1.1. Introduction 4
1.2 Généralités Sur La
Fabrication Additive 5
1.2.1 Principe De La Fabrication Additive
5
1.2.2 Contexte Actuel 6
1.2.3 Avantages 7
1.2.4 Les Limites 8
1.2.5 Comparaison Par Rapport Aux Méthodes
Soustractive Et Formative 10
1.2.6 Applications De La Fabrication Additive
15
1.3 Les Technologies De La Fabrication Additive
18
1.3.1 La Photopolymérisation En Cuve
19
1.3.2 Projection De Matière
21
1.3.3 Extrusion De Matière 22
1.3.4 Stratification De Couches 22
1.3.5 Projection De Liant 23
1.3.6 Fusion Sur Lit De Poudre 25
IV
MASTER II- LABORATOIRE SCIENCES DES
MATÉRIAUX
KOND NGUE PIERRE GÉRARD DAREL
(c)2021
TABLE DES MATIÈRES
1.3.7 Dépôt De Matière Sous
Énergie Concentrée 26
1.3.8 Comparaison Entre Les Différentes
Technologies 27
1.4 Fusion Sur Lit De Poudre : Procédé
SLM (Selective Laser Melting) 28
1.4.1 Principe Et Description 28
1.4.2 Paramètres Du Procédé SLM
30
1.4.3 Simulation Et Modélisation Du
Procédé SLM 31
1.4.3.1. Généralités
31
1.4.3.2. Rôles De La Simulation
32
1.4.3.3. La Modélisation Multi-Échelle
(Micro, Méso, Macro) 32
1.4.3.4 Modélisation Numérique Du
Procédé SLM 34
1.5 Conclusion 35
CHAPITRE 2-MÉTHODE EXPÉRIMENTALE ET
MODÈLE NUMÉRIQUE 37
2.1 Introduction 37
2. 2 Configuration Expérimentale
37
2. 2. 1 Préparation Des Échantillons
37
2. 2. 2 Mesures In Situ De La Température Du
Bain De Fusion 39
2. 3 Configuration Numérique
40
2. 3. 1 Modèle Phénoménologique
40
2. 3. 2 Modèle Numérique
43
2.4 Conclusion 47
CHAPITRE 3-RÉSULTATS, ANALYSES ET DISCUSSIONS
48
3.1 Investigations Des Résultats
Expérimentaux Et Numériques 48
3.1.1 Effet des paramètres
procédés sur la morphologie de surface du cordon
48
3.1.2 Effet de la Densité d'Énergie
Volumique sur le régime de fusion 50
3.1.3 Seuil des régimes de fusion
53
3.1.4 Simulation numérique du bain de fusion
56
3.2 Étude De Sensibilité
60
3.2.1 Introduction 60
V
MASTER II- LABORATOIRE SCIENCES DES
MATÉRIAUX
KOND NGUE PIERRE GÉRARD DAREL
(c)2021
TABLE DES MATIÈRES
3.2.2 Étude De Sensibilité Du Module
Melting 60
3.3 Conclusion 65
CONCLUSION GÉNÉRALE ET PERSPECTIVES
66
RÉFÉRENCES 70
VI
MASTER II- LABORATOIRE SCIENCES DES
MATÉRIAUX
LISTE DES TABLEAUX
LISTE DES TABLEAUX
Tableau 1-1: liste des procédés de
la fabrication soustractive 10
Tableau 1-2: liste des éléments
comparatifs entre la fabrication additive et la fabrication
soustractive 12
Tableau 1-3: liste des procédés de
la fabrication formative 13
Tableau 1-4: éléments comparatifs
entre la fabrication additive et la fabrication formative
14 Tableau 1-5: Liste des
procédés de Fabrication Additive de la norme NF ISO 17296-2
[39].
19
Tableau 1-6 : Comparaison des différents
procédés 28
Tableau 2-1: Conception de l'expérience
(DOE) pour les pistes à balayage unique 38
Tableau 2-2: Propriétés
thermo-physiques utilisées pour les simulations 46
Tableau 3-1: Données d'entrée
considérée comme valeur de référence
61
KOND NGUE PIERRE GERARD DAREL
(c)2021
VII
MASTER II- LABORATOIRE SCIENCES DES
MATÉRIAUX
KOND NGUE PIERRE GÉRARD DAREL
(c)2021
LISTE DES FIGURES
LISTE DES FIGURES
Figure 1-1: Principe de la fabrication additive en
5 étapes, d'après P. Muller 6
Figure 1-2 : (a)* Évolution de la part (en
million d'euro) du marché mondial de l'impression
3D (b)* Répartition des projets par type
d'application (Rapport PIPAME, 2017). 7 Figure 1-3 : Éléments
aérospatiaux fabriqués par la technologie FA : (a) Pale de
turbine, et
(b) Pale intégrée [32]. 16 Figure
1-4 : Éléments automobiles fabriqués par la technologie FA
: (a) Boîtier de pompe à huile produit par fusion par faisceau
d'électrons (EBM), (b) boite de vitesse d'une voiture
de
course produite par EBM, et (c) collecteur
d'échappement produit par SLM [31] 16 Figure 1-5 : Pièces
biomédicales fabriquées par les technologies FA : (a)
Prothèse dentaire construite à l'aide de SLM, (b) Tiges de hanche
fabriquées à l'aide de EBM, et (c) Pont
dentaire à 3 éléments produit
à l'aide de SLM [31]. 17 Figure I-6 : Un circuit opérationnel
construit par la méthode de dépôt par fusion
(FDM)
[35]. 17
Figure I-7 : Produits artistiques construits par
les technologies FA [37] 18
Figure 1-8 : Principaux domaines d'application de
la fabrication additive de pièces [38] 18
Figure 1-9 : Schéma de fonctionnement de la
photopolymérisation en cuve [42] 20
Figure 1-10 : exemple de réalisation de
pièces par polymérisation laser, source ressource
«
Moulage à cire perdue : du modèle
à la pièce » [44] 20
Figure I-11 : Schéma de fonctionnement de
la projection de matière [42]. 21
Figure 1-12 : Exemples de réalisation de
pièces par projection de gouttes [47]. 21
Figure 1-13 : Schéma de fonctionnement du
dépôt de fusion au travers d'une buse
chauffante (Extrusion de Matière) [42].
22 Figure 1-14 : Exemples de réalisation par fusion au travers d'une
buse chauffante [50]. . 22
XI
MASTER II- LABORATOIRE SCIENCES DES
MATÉRIAUX
KOND NGUE PIERRE GÉRARD DAREL
(c)2021
LISTE DES FIGURES
Figure 1-15 : Schéma de fonctionnement de
l'assemblage de couches (Stratification De
Couches) [42]. 23
Figure 1-16 : Exemple de réalisation par
stratification de couches [47]. 23
Figure 1-17: Schéma de fonctionnement de la
projection de liant sur un substrat de poudre
[42]. 24
Figure 1-18 : Exemple de réalisation de
pièce par projection de liant [50]. 24
Figure 1-19 : Principe de fusion sur lit de poudre
[42]. 25
Figure 1-20 : Exemples de réalisation de
pièces par fusion sur lit de poudre [51]. 26
Figure I-21 : Schéma du principe de
dépôt de matière sous énergie concentrée
[42]. 26
Figure 1-22 : exemple de réalisation par le
procédé de dépôt de matière sous
énergie
concentrée [47]. 27 Figure 1-23 :
Schéma du procédé de Fusion Sélective Par Laser
(SLM), d'après Popular 3D
Printers 29
Figure 1-24 : Structure de soutien couramment
utilisées [49]. 30
Figure 1-25 : Paramètres du
procédé SLM, d'après L. Van Belle [60].
31
Figure 2-1: Vue schématique du processus de
fusion laser sur lit de poudre équipé d'un
système de caméra infrarouge haute
vitesse [72] 37 Figure 2-2 : Caractéristiques morphologiques
intrinsèques d'une trace de fusion mesurables
[72]. 39
Figure 2-3 : Vue d'ensemble schématique de
la configuration numérique 44
Figure 2-4 : Reference de l'épandage sur
lit de poudre. 45
Figure 3-1: Topologie de surface des cordons
obtenus sur un substrat en Ti6Al4V 49
Figure 3-2: Micrographie de cordons
déposés avec la DEV (21 J/mm3) pour
différentes
valeurs de puissance et de vitesse de balayage.
50
XII
MASTER II- LABORATOIRE SCIENCES DES
MATÉRIAUX
KOND NGUE PIERRE GÉRARD DAREL
(c)2021
LISTE DES FIGURES
Figure 3-3: Coupes transversales du bain de fusion
sous différentes puissances et vitesses de
balayage pour (a) le substrat et (b) le cas du lit
de poudre. 52 Figure 3-4: Variation des dimensions du bain en fonction de la
densité d'énergie volumique
(DEV) pour un (a) substrat en Ti6Al4V et (b)
substrat avec poudre du même matériau 54 Figure 3-5: Variation
de l'aspect rapport profondeur/largeur du bain en fonction de la densité
d'énergie volumique (DEV) pour un (a) substrat en Ti6Al4V et (b)
substrat avec
poudre du même matériau. 55 Figure
3-6: Prédiction de la forme d'un simple cordon obtenu à partir
des paramètres
d'impression S16 et T16 56 Figure 3-7: Section
transversale prédite d'une piste unique et résultats
numériques (ligne noire) comparés aux observations
expérimentales pour (a) le substrat S16 et (b) le lit
de
poudre T16. 57 Figure 3-8: Profondeur et
largeur du bain de fusion mesurées et prédites sous
différentes
puissances de faisceau laser et vitesses de
balayage pour le cas du substrat. 58 Figure 3-9: Coefficient d'absorption en
fonction de la température pour l'alliage Ti6Al4V
étudié. 59 Figure 3-10:
Comparaison entre les résultats numériques et
expérimentaux après calibration
du coefficient d'absorption pour la piste S16.
59 Figure 3-11: Cas P = 200 W, V = 1000 mm/s - interface métal / gaz
- contours de température
(K) 62
Figure 3-12: Indice de sensibilité sur la
profondeur du bain de fusion 62
Figure 3-13: Indice de sensibilité de la
largeur du bain de fusion. 63
Figure 3-14: Analyse de sensibilité des
réponses du modèle. 64
XIII
MASTER II- LABORATOIRE SCIENCES DES
MATÉRIAUX
KOND NGUE PIERRE GÉRARD DAREL
(c)2021
LISTE DES ABRÉVIATIONS
LISTE DES ABRÉVIATIONS
> ABS : Acrylonitrile Butadiène Styrène
> ALE: Arbitrary Lagrangien Euleran
> AM: Additive Manufacturing
> ASTM: American Society for Testing and Materials
> AZ : Zone Apparente
> CAD : Computer Aided Design
> CAM : Content-Adresable Memory
> CAO : Conception Assistée par Ordinateur
> CFD : Computational Fluids Dynamics (Dynamique des Fluides
Computationnelle)
> CNC: Computer Numerical Control
> DED: Directed Energy Deposition
> DEM : Discret Element Method (Méthode des
Eléments Discrets)
> DMLS : Direct-Metal Laser Sintering > DEV :
Densité d'Energie Volumique
> DOE : Conception Factorielle de l'Expérience
> EBM: Electron Bram Melting
> FA: Fabrication Additive (Additive Manufacturing)
> FAO : Fabrication Assistée par Ordinateur
> FVM : Méthode des Volumes Finis
> ISO: International Organization for Standardization
> LASER: Light Amplification by Stimulated Emission of
Radiation
> Nd:YAG: Neodymium - Doped Yttrium Aluminium Garnet
> RFID: Dispositif d'Identification par
Radiofréquence
> RZ: Zone Refondue
> SLA: Stéréolithographie
> SLM: Selective Layer Melting
> SLS: Selective Layer Sintering
> UV: Ultra-Violet
> ZAT: Zone Affectée Thermiquement
XIV
MASTER II- LABORATOIRE SCIENCES DES
MATÉRIAUX
RESUME
RESUME
Le procédé de fusion sélective par
laser (SLM) d'un lit de poudre métallique est un procédé
de fabrication additive qui permet de fabriquer des pièces de forme
complexe directement à partir d'un fichier CAO en passant par la fusion
totale de couches de poudre déposées successivement. De nombreux
problèmes techniques doivent encore être surmontés pour
faire du SLM un procédé de fabrication viable. C'est le cas de
l'état de surface des pièces obtenues à partir de ce
procédé qui est intimement lié à l'influence des
paramètres procédés. Dans ce contexte, les travaux
menés auront pour objectifs : 1) d'étudier l'influence de
certains paramètres procédés tels que la puissance du
faisceau laser, la vitesse de balayage et la densité d'énergie
volumique (DEV) au cours du procédé de fabrication et 2) de faire
une analyse de sensibilité desdits paramètres. Dans un premier
temps en considérant des géométries simples (largeur et
profondeur du bain de fusion) en alliage de Titane Ti6Al4V, on étudiera
l'influence de la puissance laser, de la vitesse de balayage et de la
densité d'énergie volumique sur la morphologie en surface et en
profondeur des cordons obtenus par SLM au cours de l'interaction faisceau
laser-lit de poudre/bain de fusion. Une analyse numérique sera faite
afin de corroborer ou non les résultats expérimentaux. Par la
suite grâce au module de simulation melting (module de simulation du bain
de fusion) développé par ESI Group, une analyse de
sensibilité sera effectuée afin de visualiser au mieux les
entrées susceptibles d'influencer les plus les sorties simulées :
la largeur et la profondeur du bain de fusion.
Mots clés : Fabrication Additive,
procédé de fusion sélective par laser (SLM),
modélisation numérique, alliage Ti6Al4V, keyhole.
KOND NGUE PIERRE GERARD DAREL
(c)2021
XII
MASTER II- LABORATOIRE SCIENCES DES
MATÉRIAUX
KOND NGUE PIERRE GÉRARD DAREL
(c)2021
ABSTRACT
ABSTRACT
Selective Laser Melting (SLM) of a metal powder bed is an
additive manufacturing process that allows the manufacture of complex shaped
parts directly from a CAD file through the total melting of successively
deposited powder layers. Many technical issues still need to be overcome to
make SLM a viable manufacturing process. This is the case of the surface finish
of the parts obtained from this process which is intimately linked to the
influence of the process parameters. In this context, the objectives of the
work carried out will be: 1) to study the influence of some process parameters
such as laser beam power, scanning speed and volume energy density (VED) during
the manufacturing process and 2) to perform a sensitivity analysis of these
parameters. First, considering simple geometries (width and depth of the melt)
in Ti6Al4V Titanium alloy, we will study the influence of the laser power, the
scanning speed and the volume energy density on the surface and depth
morphology of the beads obtained by SLM during the laser beam-powder bed/melt
bath interaction. A numerical analysis will be done to corroborate or not the
experimental results. Then, thanks to the melting simulation module developed
by ESI Group, a sensitivity analysis will be performed in order to visualize at
best the inputs likely to influence the most the simulated outputs: the width
and the depth of the melt bath.
Key words: Additive
Manufacturing, selective laser melting (SLM) process, numerical modeling,
Ti6Al4V alloy, keyhole.
1
MASTER II- LABORATOIRE SCIENCES DES
MATÉRIAUX
KOND NGUE PIERRE GÉRARD DAREL
(c)2021
INTRODUCTION GÉNÉRALE
INTRODUCTION GÉNÉRALE
La fabrication additive est un ensemble
procédé innovant en plein essor depuis quelques années.
Elle s'oppose aux procédés de fabrication soustractive (l'usinage
par exemple) ou par déformation (le forgeage par exemple) en permettant
de fabriquer des pièces couche par couche à partir d'un fichier
3D. Des designs difficilement fabricables, voire impossible à fabriquer
par des procédés conventionnels et la personnalisation en masse
d'objets simples peuvent ainsi être réalisés.
La fusion sur lit de poudre est un de ces
procédés. Il permet de fabriquer des pièces
métalliques à partir de poudre. Les pièces
fabriquées ont une bonne précision géométrique et
il est l'un des procédés laissant la plus grande liberté
de design. C'est pour ces raisons qu'il est utilisé dans le domaine
aéronautique et spatial pour fabriquer des pièces
métalliques, malgré une vitesse de fabrication plus lente et une
taille de pièces fabricable plus restreinte par rapport à
d'autres technologies. Parmi ces procédés on trouve celui de
fusion sélective par laser d'une poudre métallique (SLM). Ce
procédé permet de fabriquer des pièces par une fusion
totale et successive de couches de poudre métallique, sur la base d'un
modèle 3D établi en conception assistée par ordinateur
(CAO).
Au cours du procédé SLM, de nombreux
phénomènes physiques tels que la fusion, l'évaporation du
métal, la projection des particules, la solidification...et d'importants
cycles thermiques s'y produisent suite à l'apport d'énergie du
laser. Ces phénomènes dépendent des paramètres
procédés utilisés et certains peuvent nuire à la
qualité des pièces obtenues.
Avant d'utiliser ces pièces de façon
industrielle dans les équipements, une maitrise du procédé
SLM est nécessaire. La maitrise de ce procédé passe en
général par une lourde phase expérimentale. La
modélisation numérique représente une alternative et
permet de prédire l'influence des paramètres
procédés. Dans la littérature, les chercheurs traitent
principalement de l'effet des paramètres liés au laser tels que
la variation de la puissance et la vitesse de balayage où de ceux qui
sont liés à la matière comme la composition du
matériau et l'épaisseur du lit de poudre.
Ces travaux ont permis de développer de nombreux
modules de simulation numérique à toutes les échelles de
simulation (micro, méso et macro). Afin de valider la
reproductibilité de ces modules et d'améliorer leur
qualité, il est nécessaire d'étudier l'effet respectif des
entrées de ces modules sur leur sortie simulée : c'est l'analyse
de sensibilité.
2
MASTER II- LABORATOIRE SCIENCES DES
MATÉRIAUX
KOND NGUE PIERRE GÉRARD DAREL
(c)2021
INTRODUCTION GÉNÉRALE
L'objectif de ces travaux s'articule autour de l'analyse
de sensibilité des paramètres susceptibles d'influencer la
performance des pièces obtenues par fusion sélective par laser
aux fins de répertorier au mieux les paramètres
procédés les plus influents.
Ce sujet a été abordé tout d'abord
expérimentalement puis numériquement tout en s'appuyant sur des
travaux empiriques qui ont permis de vérifier les hypothèses
spécifiques considérées en modélisation, soit
d'éclairer en profondeur certains phénomènes intervenant
au cours du procédé SLM ou encore de valider les
prédictions expérimentales.
Le modèle numérique développé
permet ainsi l'analyse de sensibilité du modèle de simulations
des procédés de fabrication additive sur lit de poudre
métallique.
Dans ce cadre, le mémoire de cette étude a
été divisé en trois chapitres :
Dans le chapitre I, le contexte de l'étude sera
présenté. Le principe de la fabrication additive, ses avantages
et ses limites seront rappelés. Un état d'art sur une
étude comparative des méthodes formative et soustractive par
rapport à la fabrication additive sera fait. Les principales
technologies de la fabrication additive seront rapidement décrites en
accentuant sur la fusion sur lit de poudre.
Dans le chapitre II, les matériaux et les
méthodes utilisés seront décrit.
Dans le chapitre III, d'une part seront
présentés les résultats expérimentaux et
numériques obtenus et d'autre part une étude de
sensibilité du procédé SLM à l'échelle
microscopique sera également présentée.
3
MASTER II- LABORATOIRE SCIENCES DES
MATÉRIAUX
KOND NGUE PIERRE GÉRARD DAREL
(c)2021
CHAPITRE 1-ÉLÉMENTS DE BIBLIOGRAPHIE
CHAPITRE 1-ÉLÉMENTS DE
BIBLIOGRAPHIE
Nous nous proposons dans ce chapitre de présenter
la notion de Fabrication Additive (FA). Pour se faire, ce dernier sera
articulé autour de trois axes. Le premier portera sur les
généralités de la fabrication additive. Dans cette
section, il sera question de mettre en relief le principe de la FA, ses
avantages et ses limites ainsi que ses différents domaines
d'applications. Par la suite un focus portera sur les différentes
technologies de la FA. Une attention particulière sera accordée
à la technologie de Fusion Sur Lit De Poudre plus
précisément au procédé SLM (Selective Layer
Melting). Enfin nous parlerons sans toutefois entrer dans les profondeurs
(rôles et modélisation multi échelles) de la simulation et
de la modélisation en FA.
1.1. Introduction
La fabrication additive en abrégée FA (en
anglais : Additive Manufacturing) [1] est connue du grand public par la
terminologie « Impression 3D » [2]. Elle désigne l'ensemble
des procédés utilisés pour la création de
pièces physiques par ajout séquentiel de matière à
partir d'un model numérique (CAO) selon la norme ISO/ASTM 52900 :2015,
sans recourir à un outillage spécifique [1]. Elle s'oppose aux
procédés de production conventionnel où la matière
est soit soustraite (usinage, découpage), soit déformée
(forge, laminage) ou moulée (fonderie). Dans un premier temps, cette
méthode de fabrication était utilisée principalement par
les industries pour le prototypage rapide [3]. Les pièces obtenues sont
utilisées en tant que maquettes dans les bureaux d'étude pour
valider la forme définitive d'un produit donné. Avec le temps,
les progrès réalisés sur cette technologie et la
sensibilisation des industriels ont ouvert la porte à la production des
pièces fonctionnelles en petites séries [2].
Contrairement à ce que l'on pourrait penser, la
fabrication additive n'est pas une invention récente. En effet, le
premier brevet a été déposé dans les années
1971 par l'inventeur français Pierre Ciraud [4]. Il présente une
technologie de consolidation sélective de poudre métallique par
un laser. En suite au milieu des années 80, on trouve la
Stéréolithographie (photo polymérisation d'une
résine) qui a été développée dans les
laboratoires de l'École Nationale de Nancy en France par l'équipe
du professeur Jean-Claude André et breveté en 1984 [5]. Peu de
temps après, un brevet similaire sera déposé aux USA par
l'américain Chuck Hull. Il débutera son exploitation commerciale
avec la création de sa propre entreprise, 3D System [6].
4
MASTER II-LABORATOIRE SCIENCES DES
MATÉRIAUX
KOND NGUE PIERRE GÉRARD DAREL
(c)2021
CHAPITRE 1-ÉLÉMENTS DE BIBLIOGRAPHIE
Aujourd'hui, la fabrication additive est devenue une technique
de fabrication complémentaire à celles déjà
existantes, permettant ainsi le développement de nouvelles
compétences innovantes [7] et la réalisation de nouveaux types de
pièces [2]. Ces progrès et leur efficacité ont fait de la
FA une méthode de fabrication incontournable voir même
indispensable dans de nombreux domaines tels que l'aéronautique civile
et spatiale [8], [9], [10], l'automobile, le sport [11], le biomédical
[12], [13], [14], pour ne citer que ces derniers. Par exemple,
l'aéronautique et l'aérospatial qui voient là un moyen
d'accroitre la performance de leurs structures en pouvant augmenter de
façon optimale le ratio « performances mécaniques/masse
». Ainsi, la FA permet de réduire de façon
considérable le nombre de pièces d'un assemblage, et donc de
diminuer les étapes de construction et la masse additionnelle
liée aux assemblages.
Les procédés de fabrication additive permettent
la mise en oeuvre d'une grande variété de matériaux. En
2015, on estime à 88% la part des activités de la FA concernant
les polymères, 10% pour les matériaux métalliques. Les 2%
restant sont attribués à la mise en oeuvre des matériaux
céramiques, de composites et autres matériaux tels les
biomatériaux. Dans un souci de compréhension et
d'appréhension, ce chapitre marquera l'accent sur deux grandes sessions
: l'une qui portera sur une présentation globale de la FA et l'autre sur
les technologies liées à cette dernière.
1.2 Généralités Sur La Fabrication
Additive
Cette session présente brièvement la
technologie de fabrication additive (FA) à travers son principe, ses
avantages et ses limites afin de dresser une étude comparative avec
d'autres méthodes de fabrication telles que la fabrication soustractive
et formative, d'identifier ces applications et de mettre en lumière le
contexte actuel de la fabrication additive.
1.2.1 Principe De La Fabrication Additive
La fabrication additive est un groupe de procédé
consistant à assembler des matériaux pour fabriquer des
pièces à partir des données de modèle en 3D selon
la norme ISO/ASTM 52900-2015[15]. À ce titre, elle regroupe plusieurs
technologies ou méthodes de fabrication moderne en son sein basé
sur l'utilisation d'un modèle numérique. Le principe
général des procédés de fabrication additive se
divise plus ou moins (selon les littératures) en 5 étapes :
- La conception d'un objet numérique par
l'intermédiaire d'un logiciel de Conception Assisté par
Ordinateur (CAO) qui définit les contraintes morphologiques de la
pièce à réaliser ;
5
MASTER II-LABORATOIRE SCIENCES DES
MATÉRIAUX
KOND NGUE PIERRE GÉRARD DAREL
(c)2021
CHAPITRE 1-ÉLÉMENTS DE BIBLIOGRAPHIE
- L'exportation de l'objet sous forme d'un fichier informatique,
généralement au format «. Stl » ou
«. Amf » ;
- L'importation du fichier dans un logiciel permettant de
définir la stratégie d'élaboration de l'objet, ainsi que
les paramètres du procédé ;
- La transmission des instructions à la machine de
fabrication additive ;
- La production de l'objet sous forme physique par impression
3D.
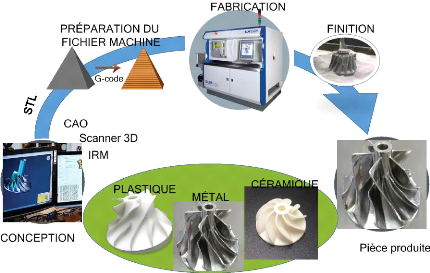
Figure 1-1: Principe de la fabrication additive en
5 étapes, d'après P. Muller
Si elle correspondait à un phénomène
d'ampleur limitée il y a quelques années, elle connaît
actuellement un engouement exceptionnel. Il est donc important de replacer la
fabrication additive dans son contexte actuel.
1.2.2 Contexte Actuel
D'après le rapport Wohlers (2015), l'utilisation de la
fabrication additive directe comme outil de production continue à
croitre, et représente 42,6 % du total des revenus des produits et
services de fabrication additive. De nombreux secteurs industriels
(aérospatial, médical, industrie automobile) se penchent sur les
nouvelles technologies, représentant plus de 60 % du
6
MASTER II-LABORATOIRE SCIENCES DES
MATÉRIAUX
KOND NGUE PIERRE GÉRARD DAREL
(c)2021
CHAPITRE 1-ÉLÉMENTS DE BIBLIOGRAPHIE
marché de la fabrication additive, avec des taux de
croissance de 15 à 25 % pour les cinq prochaines années.
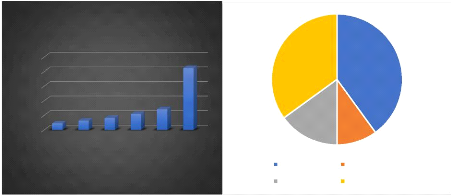
10000
4000 900 1288 1657 2200 2860
8000
6000
2000
0
2008 2011 2012 2013 2014 2020
8500
Prototypage communication
Outilage Pièces Finales
35%
15%
10%
40%
Figure 1-2 : (a)* Évolution de la part (en
million d'euro) du marché mondial de l'impression 3D (b)*
Répartition des projets par type d'application (Rapport PIPAME,
2017).
1.2.3 Avantages
L'usage de la fabrication additive ou impression 3D
présente de nombreux intérêts aussi bien pour les
particuliers comme pour les professionnels. Les principaux avantages
liés à cette technologie sont ;
- Liberté de design : Les
pièces en fabrication additive étant construites couche par
couche, le procédé offre une grande liberté de design. Il
est possible d'ajouter des fonctionnalités aux pièces
(principalement des canaux) [16] ou de diminuer leur masse, la
disparition des contraintes induites par l'outillage ou par le matériau
brut initial. L'optimisation topologique, notamment, permet d'optimiser le
design des pièces en insérant uniquement la quantité de
matière qu'il faut à l'endroit où il faut pour supporter
les différentes contraintes (mécaniques, thermiques,
géométriques...) [17]. Ces pièces sont optimisées
dans la plupart des cas pour diminuer la masse, mais elles peuvent aussi
l'être pour améliorer les performances thermiques ou autres. Des
pièces très complexes sont désormais réalisables
par fabrication additive [18] [19]. Dans le but de toujours
améliorer la qualité des pièces, d'optimiser la
matière ou d'éviter les supports, des guides de conceptions ont
été créé [20].
7
MASTER II-LABORATOIRE SCIENCES DES
MATÉRIAUX
KOND NGUE PIERRE GÉRARD DAREL
(c)2021
CHAPITRE 1-ÉLÉMENTS DE BIBLIOGRAPHIE
- Pas d'outillage : Contrairement aux
procédés conventionnels où un outil de coupe ou un moule,
peuvent être nécessaires, le procédé de fabrication
additive ne nécessite aucun outillage. La matière est
créée et mise en forme en même temps [21].
- Réduction du nombre
d'assemblages : Afin d'éviter les défauts pouvant
apparaitre lors de certains procédés d'assemblage (brasage...) et
de gagner du temps de fabrication, certains assemblages peuvent être
supprimés pour fabriquer une pièce en une seule entité. Il
est par exemple possible de passer d'un assemblage de plusieurs pièces
vissées à une pièce unique [22].
- Procédé
écologique : Le procédé est
considéré comme écologique car peu de matière est
perdue. En effet, il n'y a de la matière qu'aux endroits où elle
est nécessaire. Cela implique la réduction du ratio «
buy to fly » (rapport de la quantité de
matière nécessaire à la fabrication d'une pièce par
la quantité de matière effective de la pièce) [21]. De
plus, dans le cas de certains procédés, la matière qui
n'est pas utilisée peut parfois être
récupérée, traitée et réutilisée
[23].
1.2.4 Les Limites
Les avantages de la fabrication additive sont bien connus. Les
limitations sont également assez importantes et peuvent compromettre la
croissance future de l'industrie. Actuellement, la fabrication additive permet
et facilite la production en quantités diverses de produits qui peuvent
être personnalisés individuellement, tout en réduisant la
consommation d'énergie, le coût et l'empreinte carbone de
l'opération ou encore en raccourcissant les chaînes
d'approvisionnement. La technologie présente cependant un certain nombre
de limites liées aux caractéristiques des technologies existantes
et à l'état actuel de son développement. Celles-ci peuvent
être liées aux caractéristiques mêmes des
technologies de fabrication additive, qui ne peuvent être résolues
que par un développement et une augmentation de leurs capacités
actuelles, ou aux limitations non technologiques, manque d'adaptation ou
d'expérience des technologies qui empêchent la pleine exploitation
des capacités.
1.2.4.1 Limites technologiques
Les principales limites technologiques sont les suivantes :
- État de surface :
L'état de surface des pièces en sortie de machine est davantage
rugueux en comparaison avec les procédés conventionnels. Des
post-traitements plus ou moins importants suivant l'application sont
nécessaires [24], comme le sablage qui peut être utilisé
sur les surfaces externes des pièces.
8
MASTER II-LABORATOIRE SCIENCES DES
MATÉRIAUX
KOND NGUE PIERRE GÉRARD DAREL
(c)2021
CHAPITRE 1-ÉLÉMENTS DE BIBLIOGRAPHIE
- Logiciel : Il n'existe pas pour le
moment de logiciel de CAO permettant de concevoir et analyser les pièces
destinées à la fabrication additive (analyse des
géométries, besoin de supports, structures en treillis,
multi-matériaux) [18]. Cependant, de nombreux logiciels sont en
développement et permettront de compléter et améliorer les
outils de conception existants.
- Supports : Certaines
géométries de la pièce nécessitent des supports
permettant de conduire la chaleur, et surtout, de maintenir la pièce
lors de sa fabrication. Ils sont nécessaires dans les cas de fabrication
de parois horizontales ou fortement inclinées [25]. Ces supports peuvent
être compliqués à retirer et entrainer de mauvais
états de surface.
- Les capacités des
machines, qu'il s'agisse du volume de fabrication, de la
vitesse d'impression, des résolutions, des contrôles des processus
ou encore de la taille des pièces.
- Le déploiement de la
technologie entraînant des besoins en
sécurité, en formation spécialisée et en
infrastructures.
1.2.4.2 Les limites non technologiques
Les principales limites non technologiques ne sont pas
seulement liées au manque de compétences en conception et en
ingénierie ainsi qu'à l'absence d'opérateurs techniques,
mais plus particulièrement aux problèmes de normalisation, de
qualification et de certification. Les limites en termes de normalisation sont
les suivantes :
- L'absence des directives de
conception : Plusieurs technologies de fabrication additive ont
des caractéristiques différentes qui nécessitent des
directives de conception spécifiques, tandis que les produits logiciels
actuels n'ont pas encore le potentiel ou les capacités
nécessaires pour aider l'ensemble des applications de conception.
- L'absence d'équipements
standards : De nombreuses technologies fonctionnent sur
différentes machines, chacune avec des spécifications de
matériaux différentes, de volumes de fabrication, de
précisions, d'épaisseurs de couche, etc. Il est difficile pour
les utilisateurs potentiels d'avoir un planning de normalisation clair en ce
qui concerne, par exemple, le post-traitement des pièces
fabriquées.
- L'absence de norme pour la production
: Les applications en fabrication additive connaissent une forte
croissance mais nécessitent la normalisation de l'ensemble de la
chaîne de valeur industrielle.
9
MASTER II-LABORATOIRE SCIENCES DES
MATÉRIAUX
KOND NGUE PIERRE GÉRARD DAREL
(c)2021
CHAPITRE 1-ÉLÉMENTS DE BIBLIOGRAPHIE
1.2.5 Comparaison Par Rapport Aux Méthodes
Soustractive Et Formative 1.2.5.1 Focus Sur La Méthode Soustractive Et
Additive
? Méthode Soustractive
La fabrication soustractive est le terme
générique désignant divers processus d'usinage et
d'enlèvement de matière contrôlés qui commencent par
des blocs solides, des barres, des tiges de plastiques, de métal ou
d'autres matériaux qui sont façonnés par enlèvement
de matière par découpe, alésage, perçage et meulage
[26]. Ces processus sont soit exécutés manuellement, soit plus
communément pilotés par commande numérique par ordinateur
(CNC).
En CNC, un modèle virtuel conçu dans un logiciel
de CAO sert d'entrée pour l'outil de fabrication. La simulation
logicielle est associée à une entrée utilisateur pour
générer des parcours d'outil qui guident l'outil de coupe
à travers la géométrie de la pièce. Ces
instructions indiquent à la machine comment effectuer les coupes, les
canaux, les trous et toute autre caractéristique qui nécessitent
un enlèvement de matière, en tenant compte de la vitesse de
l'outil de coupe et de la vitesse d'avance du matériau. Les outils CNC
fabriquent des pièces sur la base de ces données de fabrication
assistée par ordinateur (FAO), avec peu ou pas d'assistance ou
d'interaction humaine.
Les processus de fabrication soustractive sont
généralement utilisés pour créer des pièces
en plastique ou en métal pour le prototypage, la fabrication d'outillage
et les pièces finales. Ils sont idéaux pour les applications qui
nécessitent des tolérances serrées et des
géométries difficiles à mouler, couler ou produire avec
d'autres méthodes de fabrication traditionnelle.
Comme toute méthode de fabrication, la fabrication
soustractive regroupe en son sein plusieurs processus de fabrication
consignés dans le tableau suivant [27] :
Processus
|
Matériaux
|
Usinage CNC (tournage, perçage,
alésage, fraisage)
|
Thermoplastique durs, plastiques thermodurcissable,
métaux mous, métaux durs (machines industrielles)
|
Usinage par décharge électrique (EDM)
|
Métaux durs
|
Découpe au laser
|
Thermoplastiques, bois, acrylique, tissus, métaux
(machines industrielles)
|
Découpe au jet d'eau
|
Plastiques, métaux durs et mous
|
Tableau 1-1: liste des procédés de la
fabrication soustractive
10
MASTER II-LABORATOIRE SCIENCES DES
MATÉRIAUX
KOND NGUE PIERRE GÉRARD DAREL
(c)2021
CHAPITRE 1-ÉLÉMENTS DE BIBLIOGRAPHIE
? Méthode Additive
Dans ce paragraphe, nous allons ajouter à ce qui a
déjà été énoncé plus haut certains
éléments afin de faire une étude comparative entre les
deux méthodes de fabrication.
Contrairement au processus soustractif d'élimination de
matériau d'une pièce plus grande, les processus de fabrication
additive ou impression 3D construisent des objets en ajoutant du
matériel une couche à la fois, chaque couche successive se liant
à la couche précédente jusqu'à ce que la
pièce soit complète [1].
Tout comme les outils CNC soustractifs, les technologies de
fabrication additive créent des pièces à partir des
modèles CAO. La préparation d'impression ou de tranchage est
principalement automatisée, ce qui rend la configuration du travail
beaucoup plus facile et plus rapide qu'avec les outils CNC. En fonction de la
technologie, l'imprimante 3D dépose le matériau, fond et fusionne
de manière sélective la poudre ou polymérise des
matériaux photopolymères liquides pour créer des
pièces basées sur les données CAM. Les pièces
imprimées en 3D nécessitent souvent une certaine forme de
nettoyage et de finition pour atteindre leurs propriétés finales
et leur apparence avant d'être prêtes à être
utilisées [26].
La fabrication additive est idéale pour une gamme
d'applications d'ingénierie et de fabrication, y compris le prototypage,
l'outillage de fabrication et les modèles de moulage, ainsi que la
production à court terme, la production de ponts et la fabrication sur
mesure de pièces finales. Les imprimantes 3D offrent un très haut
degré de conception et peuvent produire des conceptions complexes qu'il
serait impossible ou excessivement couteux de créer avec toute autre
méthode de fabrication. Les matériaux les plus couramment
utilisés dans cette méthode
sont les plastiques et les métaux. Les imprimantes 3D
de bureau et de paillasse offrent une solution abordable pour créer
des pièces en plastique, tandis que les métaux sont actuellement
limités aux systèmes industriels.
1.2.5.2 Étude Comparative Entre La Méthode
Soustractive Et La Méthode Additive
Les procédés soustractifs sont les
méthodes de fabrication les plus utilisées. La fabrication
additive a ouvert la porte à de nouvelles applications dans plusieurs
domaines manufacturiers. Dans le tableau suivant ces deux méthodes sont
comparées à l'aide de quelques critères pertinents aux
applications industrielles aujourd'hui [26] :
11
MASTER II-LABORATOIRE SCIENCES DES
MATÉRIAUX
KOND NGUE PIERRE GÉRARD DAREL
(c)2021
CHAPITRE 1-ÉLÉMENTS DE BIBLIOGRAPHIE
Critères
|
Fabrication additive
|
Fabrication soustractive
|
Formation
|
Aussitôt que le CAD est fait par le designer ;
Procédé automatisé ;
|
Opérateur requis : code CNC ou opération manuelle
;
|
Taux de production
|
Procédé lent mais qualité et
propriétés supérieures
|
Production en masse, rapide ;
|
Variété de matériaux
|
Température de fusion assez basse ;
Augmente avec le progrès de la technologie
|
Non relié à la température de fusion ;
Assez variés
|
Perte
|
Moins de gaspillage de matériel-
principalement les supports ;
|
Plus de gaspillage-en copeaux, ferrailles, etc
|
Finition
|
Nettoyage et finition requise (pour la plupart des cas) ;
|
Les finitions se font durant la fabrication de la pièce
|
Maintenance
|
Nettoyage régulier
|
Nettoyage régulier ;
Changement d'outils usés (contact, friction,
chaleur,
|
Conception
|
Un degré plus élevé de liberté
dans le design ;
Pièces plus complexes ;
Flexibilité en terme densité de pièce ;
Pièces fusionnées, moins de pièces à assembler avec
des boulons, écrous et vis ;
|
Limité aux restrictions de
mouvements et outils utilisés ;
Complexités de pièces est limitée ;
Densité fixe ;
Quantité supérieure de pièces
|
Délai d'exécution
|
Peut-être incroyablement rapide (<24 heures)
|
Les délais sont rapides,
généralement sous 5 jours les
pièces demandées sont disponibles
|
Coût
|
Idéal pour une production ponctuelle ou à faible
volume, ou pour la production de géométries complexes ;
Les couts de mise en place après conception sont
faibles
|
Meilleure option pour la
production de pièce à faible et moyen volume (10
à 100) ;
Les investissements initiaux dans la configuration de la
machine ne sont pas bon marché, mais des pièces individuelles
peuvent alors être produites à un prix unitaire assez bas
|
Tableau 1-2: liste des éléments
comparatifs entre la fabrication additive et la fabrication
soustractive
Bien que les procédés additifs et soustractifs
présentent des différences apparentes, ils prennent souvent des
rôles complémentaires dans le cycle de vie d'un produit en
industrie. L'arrivée des procédés additifs a
révolutionné le prototypage. Malgré les nombreux avantages
qu'apporte la fabrication additive, la fabrication soustractive est toujours
considérée comme la méthode traditionnelle et fiable pour
les compagnies de production en masse. Notamment avec l'exploration de
nouvelles technologies comme la découpe par laser et l'EDM, cette
technologie ne risque pas de disparaitre [27].
12
MASTER II-LABORATOIRE SCIENCES DES
MATÉRIAUX
KOND NGUE PIERRE GÉRARD DAREL
(c)2021
CHAPITRE 1-ÉLÉMENTS DE BIBLIOGRAPHIE
1.2.5.3 Focus Sur La Fabrication Formative
Elle peut se définir comme étant l'ensemble des
procédés de formage utilisant des contraintes telles que la
compression, la tension, le cisaillement ou une certaine combinaison pour
provoquer la déformation plastique d'un matériau en une forme
souhaitée. Ce processus de fabrication concerne
généralement les plastiques et les métaux peuvent
être complétés en utilisant une grande
variété de matériaux. Il permet également aux
fabricants de fabriquer un seul produit à partir de différents
matériaux en même temps. Au cours de ce processus de fabrication,
aucun matériau n'est ajouté ou soustrait. La pièce
à usiner est seulement déformée ou déplacée.
Les matériaux linéaires tels que le tube, le tuyau ou la tige en
acier et les matériaux en feuille tels que la plaque d'acier ou le
thermoplastique peuvent être pliés, courbés,
tranchés, gaufrés ou déformés en forme par
l'application d'une pression externe et/ou la chaleur. Une telle transformation
nécessite des outils qui peuvent se plier et/ou se déformer
à l'aide de moules, poinçons, de matrices d'estampage ou d'outils
de pliage. La consommation de matière est plus importante dans ce
processus lorsque des moules sont utilisés. Cette méthode de
fabrication présente plusieurs procédés de fabrication
donnés dans le tableau suivant [28] :
Procédés
|
Caractéristiques
|
Moulage par injection
|
Le matériau fondu est injecté dans un moule
intérieur. Lorsque le matériau refroidit et durcit, il prend la
configuration formelle de la cavité.
|
Roto moulage ou moulage par rotation
|
Procédé dans lequel la matière
première (généralement sous forme de poudre) est
injectée dans un moule creux chauffé. Le moule tourne lentement
sur un ou plusieurs axes
|
Formation unique point (SPF)
|
Processus dans lequel le matériau en feuille est
incrémenté en une forme tridimensionnelle souhaitée,
généralement par un outil à pointe ronde. C'est
l'équivalent CNC
|
Ancien Vide
|
Le formage sous vide est une méthode de
thermoformage. Le matériau en feuille
(généralement en plastique) est placé dans le cade dans le
formateur sous vide chauffé jusqu'à ce qu'il soit
malléable.
|
Plieuse de tubes CNC (cintreuse de tubes
CNC)
|
Machine contrôlée par ordinateur qui peut
créer une série de coudes courbes complexes dans un
matériau de tuyau
|
Rouleau CNC
|
Machine contrôlée par ordinateur qui peut
créer des plis spécifiques dans la feuille et le matériau
de base
|
Presse à poinçonner CNC
|
Ici la machine utilise des matrices préformées
pour poinçonner des formes spécifiques à partir d'un
matériau en feuille (généralement de la tôle)
|
Presse plieuse CNC
|
On utilise une machine commandée par ordinateur pour
effectuer des opérations de pliage sur les matériaux en feuille
(généralement de la tôle)
|
Tableau 1-3: liste des procédés de la
fabrication formative
13
MASTER II-LABORATOIRE SCIENCES DES
MATÉRIAUX
KOND NGUE PIERRE GÉRARD DAREL
(c)2021
CHAPITRE 1-ÉLÉMENTS DE BIBLIOGRAPHIE
1.2.5.4 Étude Comparative
Dans le tableau suivant méthodes additive et formative
seront comparées à l'aide de quelques critères pertinents
aux applications industrielles aujourd'hui :
Critères
|
Méthode additive
|
Méthode formative
|
Processus
|
Construction additive d'une
pièce une couche à la fois
|
Le matériau est formé dans la forme
souhaitée par la chaleur et la pression, par exemple le moulage par
injection ;
|
Cout
|
Idéal pour une production
ponctuelle ou à faible volume,
ou pour la production de géométries complexes
;
Les couts de mise en place après conception sont
faibles
|
Un cout inégalé pour la
production à grand volume de pièces identiques ;
L'investissement initial en outillage est couteux
|
Délai
|
Peut-être incroyablement
rapide (<24 heures)
|
L'outillage en acier pour les volumes de production massifs
est complexe et prend du temps, ce qui augmente les délais à
plusieurs semaines
|
Propriétés du matériau
|
Il n'est pas possible de produire des pièces avec des
propriétés matérielles équivalentes à celle
de la technique formative
|
Capable de produire des pièces relativement complexes
avec des tolérances élevées et une large gamme de
propretés du matériau ;
Idéal pour des pièces fonctionnelles
|
Contraintes de conception
|
Les pièces peuvent être
produites avec presque toutes les géométries
|
La conception est limitée par le besoin de
fonctionnalités de moule telles que des éperons, des
glissières et une épaisseur de paroi uniforme
|
Taux de production
|
Procédé lent mais qualité et
propriétés supérieures
|
Élevé mais production lente
|
Variété des matériaux
|
Température de fusion assez basse ;
Augmente avec le progrès de la technologie
|
Relié à la température de
fusion ;
Principalement du plastique et des métaux
|
Perte
|
Moins de gaspillage de
matériel-principalement les supports
|
Consommation en matière
première élevée ; Pas de perte
|
Maintenance
|
Nettoyage régulier
|
Nettoyage régulier
|
Tableau 1-4: éléments comparatifs entre
la fabrication additive et la fabrication formative
14
MASTER II-LABORATOIRE SCIENCES DES
MATÉRIAUX
KOND NGUE PIERRE GÉRARD DAREL
(c)2021
CHAPITRE 1-ÉLÉMENTS DE BIBLIOGRAPHIE
Si la fabrication additive et soustraction semble jouirent
d'une certaine complémentarité, la fabrication formative semble
ne pas jouir de cette affinité avec la méthode additive. La
fabrication formative, en particulier le moulage par injection, se prête
également à une flexibilité créative et
financière. En fait, de nombreux fabricants peuvent produire des
pièces de haute qualité de n'importe quelle couleur à des
coûts par pièce très bas. Mais l'outillage peut avoir un
prix élevé, à la fois coût et fonctionnalité,
l'outillage est non seulement coûteux, mais nécessite
également des délais plus longs, ce qui n'est pas idéal
[29].
1.2.6 Applications De La Fabrication Additive
La fabrication additive est aujourd'hui compétitive
pour la fabrication de pièces complexes en petites séries ou pour
des pièces non fabricables avec d'autres procédés. Elle
permet également les concepts de « mass personalization »
(personnaliser les objets pour tout le monde) et de « mass customization
» (accès à tous pour concevoir et fabriquer des
pièces) [30]. Si le monde amateur s'intéresse beaucoup à
la technologie avec des machines qui deviennent abordables, permettant de
réaliser des petits objets du quotidien en plastique, les industriels de
certains secteurs sont eux aussi particulièrement
intéressés pour les raisons citées ci-dessus. Le
paragraphe suivant porte sur les applications de la FA dans différents
domaines (les principaux) tels que l'aérospatiale, l'automobile, le
biomédical, l'électricité et d'autres domaines
énergétiques.
- Industrie aérospatiale : Les
composants aérospatiaux présentent généralement
des
géométries complexes et sont fabriqués
à partir de matériaux avancés, tels que les superalliages
de nickel, les alliages de titane, les aciers spéciaux ou les
céramiques à ultra-haute température, qui sont
coûteux, longs et difficiles à fabriquer. La plupart des
applications industrielles se situent dans la production de moteurs à
réaction, de composants structurels de nervures, de boîtiers de
turbines, de pales de moteurs, d'aubes, etc. [31].
15
MASTER II-LABORATOIRE SCIENCES DES
MATÉRIAUX
KOND NGUE PIERRE GÉRARD DAREL
(c)2021
CHAPITRE 1-ÉLÉMENTS DE BIBLIOGRAPHIE
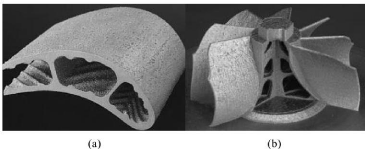
Figure 1-3 : Éléments
aérospatiaux fabriqués par la technologie FA : (a) Pale de
turbine, et (b) Pale intégrée [32].
- Industrie automobile : Le
développement de nouveaux produits est essentiel pour l'industrie
automobile et le développement de nouveaux produits est souvent un
processus très coûteux et long. L'industrie automobile utilise la
technologie FA comme un outil essentiel dans la conception et le
développement de composants automobiles et de pièces
structurelles et fonctionnelles, tels que les arbres de transmission, les
composants de boîtes de vitesses, les échappements de moteurs, les
pistons, les roues et les arbres de transmission pour les véhicules
[31].
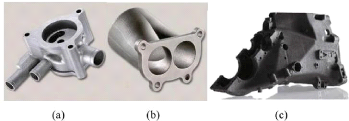
Figure 1-4 : Éléments automobiles
fabriqués par la technologie FA : (a) Boîtier de pompe à
huile produit par fusion par faisceau d'électrons (EBM), (b) boite de
vitesse d'une voiture de course produite par EBM, et (c) collecteur
d'échappement produit par SLM [31]
- Application biomédicale : La
FA est un procédé qui permet de sauver des vies dans le secteur
médical. Les développements récents dans le domaine des
biomatériaux, de la biomédecine et des sciences biologiques ont
élargi l'application des techniques de FA dans le domaine
biomédical à des produits tels que les implants
orthopédiques, les applications dentaires, les organes artificiels, les
échafaudages tissulaires, les dispositifs
16
MASTER II-LABORATOIRE SCIENCES DES
MATÉRIAUX
KOND NGUE PIERRE GÉRARD DAREL
(c)2021
CHAPITRE 1-ÉLÉMENTS DE BIBLIOGRAPHIE
médicaux, les vessies artificielles, la bio-impression,
les organes peints, les réseaux de microvasculature et les puces
biologiques [33].
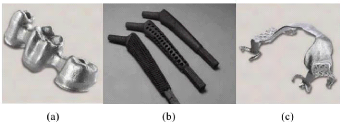
Figure 1-5 : Pièces biomédicales
fabriquées par les technologies FA : (a) Prothèse dentaire
construite à l'aide de SLM, (b) Tiges de hanche fabriquées
à l'aide de EBM, et (c) Pont dentaire à 3 éléments
produit à l'aide de SLM [31].
- Industrie électronique :
L'industrie électronique couvre des applications allant des
téléphones mobiles et des ordinateurs aux voitures. Les produits
électroniques sont souvent de petite taille et nécessitent des
outils de haute précision pour le processus de fabrication. La
production d'électronique embarquée représente un autre
champ d'application. En outre, l'AM est déjà utilisé pour
des produits tels que l'intégration de dispositifs d'identification par
radiofréquence (RFID) à l'intérieur d'objets
métalliques, la fabrication d'objets en 3D à base de
polymères, etc. Les systèmes micro
électromécaniques, les circuits micro-ondes et toutes sortes de
pinces [34].
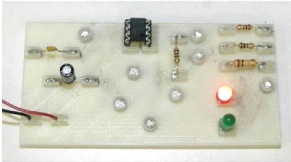
Figure I-6 : Un circuit opérationnel construit
par la méthode de dépôt par fusion (FDM)
[35].
- Industrie de l'art : Les
technologies FA sont un outil très puissant pour l'artiste dans la mode,
et le mobilier a donné la possibilité de produire virtuellement
la forme la plus
17
MASTER II-LABORATOIRE SCIENCES DES
MATÉRIAUX
KOND NGUE PIERRE GÉRARD DAREL
(c)2021
CHAPITRE 1-ÉLÉMENTS DE BIBLIOGRAPHIE
complexe imaginable. Certaines entreprises peuvent construire des
compléments d'ameublement et des accessoires, y compris des
vêtements, en utilisant la FA [36].
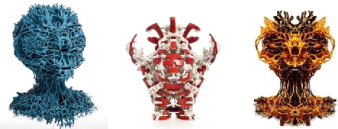
Figure I-7 : Produits artistiques construits par
les technologies FA [37]
En plus des principaux secteurs cités
précédemment, nous avons aussi des applications dans les domaines
tels que la mode, le cinéma, l'architecture, etc.
En dehors des applications citées plus haut, d'autres
domaines d'applications ont adopté cette nouvelle technologie qui semble
ne pas connaitre de frontières en termes de secteurs d'applications.
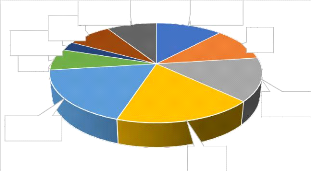
Aéronautique
18%
Architectu Autres
3%
7%
Militair
8%
Académique
9%
Industrie
18%
Electronique
12%
Santé
11%
Automobile
14%
Figure 1-8 : Principaux domaines d'application de la
fabrication additive de pièces [38]
1.3 Les Technologies De La Fabrication Additive
Les différentes catégories de procèdes de
fabrication additive sont listées dans la norme NF ISO 17296-2 [39]. Ces
catégories peuvent être classées en fonction de
l'état de la matière avant la fabrication. Il peut être
sous forme liquide, solide ou sous forme de poudre (Tableau I.2.1).
18
MASTER II-LABORATOIRE SCIENCES DES
MATÉRIAUX
KOND NGUE PIERRE GÉRARD DAREL
(c)2021
CHAPITRE 1-ÉLÉMENTS DE BIBLIOGRAPHIE
Les principes et les catégories décrites dans la
norme NF ISO 17296-2 se réfèrent aux technologies disponibles
dans le commerce qui se sont avérées utiles dans la pratique et
viables sur le marché depuis plusieurs années [39].
État
matière première
|
Catégorie
|
Exemples de technologies
|
Source d'activation
|
Type de matériau
|
LIQUIDE
|
Photo polymérisation en cuve
|
SLA : stéréolithographie
DLP : Digital Light Processing
|
UV, LED
|
Plastique
|
Projection de matière
|
MJM : Multi-Jet Modeling
|
UV
|
Plastique, Cire
|
SOLIDE
|
Extrusion de matière
|
FDM : Fused-Deposition Modeling
|
Chaleur
|
Plastique
|
Stratification de couches
|
UAM: Ultrasonic Additive
Manufacturing
LOM: Laminated Object Manufacturing
|
Chaleur
|
Plastique, métal, papier
|
POUDRE
|
Projection de liant
|
3DP : 3D Printing
|
Chimique
|
Plastique, Céramique, métal,
plâtre,
|
Fusion sur lit de poudre
|
SLM/SLS: Selective Laser Melting/Sintering
DMLS: Direct-Metal Laser Sintering EBM:
Electron Bram Melting
SMS: Selective Mask Sintering
|
Chaleur
|
Plastique, Céramique, métal
|
Dépôt de matière sous
énergie concentrée
|
CLAD: Construction Laser Additive Direct
LMD: Laser Metal Deposition
BPLAM: Blown Powder Laser Additive
Manufacturing
|
Chaleur
|
Metal
|
Tableau 1-5: Liste des procédés de
Fabrication Additive de la norme NF ISO 17296-2 [39].
1.3.1 La Photopolymérisation En Cuve
La photopolymérisation est le procédé de
fabrication additive le plus ancien. Deux brevets ont été
déposés en 1986 à une date très proche. L'un par
des français Jean-Claude André, Alain de Mehauté et
Olivier de Witte [40] et l'autre de l'américain Charles Hull,
co-fondateur de l'entreprise 3D System [41].
19
MASTER II-LABORATOIRE SCIENCES DES
MATÉRIAUX
CHAPITRE 1-ÉLÉMENTS DE BIBLIOGRAPHIE
Une résine photopolymère liquide contenue dans
une cuve est photo polymérisée sélectivement couche par
couche. La pièce peut être fabriquée à l'endroit ou
à l'envers suivant la technologie utilisée et la
polymérisation de la résine est activée par une source
lumineuse (UV ou LED).
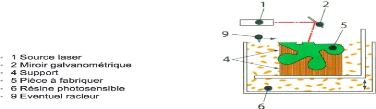
KOND NGUE PIERRE GÉRARD DAREL
(c)2021
Figure 1-9 : Schéma de fonctionnement de la
photopolymérisation en cuve [42]
La technologie de stéréolithographie est la plus
courante. Un laser UV est utilisé pour photopolymériser la
résine. La technologie DLP utilise une source étendue et un
masque. La pièce est fabriquée à l'envers et la source
lumineuse traverse une plaque transparente sous la cuve.
Seuls des matériaux plastiques polymérisables de
types polycarbonates, ABS et acryliques peuvent être mise en forme par
cette technologie [43].
Ce type de technologie a l'avantage d'être très
rapide car la couche est fabriquée d'un seul coup. L'état de
surface est bon ainsi que les qualités dimensionnelles. Il est
principalement utilisé en prototypage rapide ou pour faire des
modèles pour des pièces de fonderie car la tenue mécanique
des matériaux est limitée.
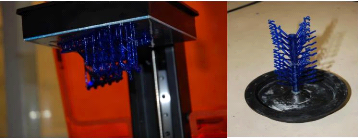
Figure 1-10 : exemple de réalisation de
pièces par polymérisation laser, source ressource « Moulage
à cire perdue : du modèle à la pièce »
[44]
20
MASTER II-LABORATOIRE SCIENCES DES
MATÉRIAUX
CHAPITRE 1-ÉLÉMENTS DE BIBLIOGRAPHIE
1.3.2 Projection De Matière
Le principe de fonctionnement est le même que les
imprimantes jet d'encre, une tête d'impression dépose de
manière sélective des gouttes de matériaux et fabrique
couche par couche le modèle par abaissement du plateau de fabrication.
Pour la solidification il y'a deux méthodes : le refroidissement ou la
photo polymérisation [45]. Dans le cas de la photo
polymérisation, une source lumineuse solidifie les gouttelettes
projetées directement sur la couche précédente, de la
même manière qu'en photo polymérisation en cuve. Dans le
cas de la solidification, les gouttelettes sont directement solidifiées
sur la couche précédente [43] [46].
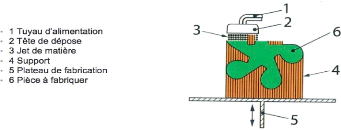
KOND NGUE PIERRE GÉRARD DAREL
(c)2021
Figure I-11 : Schéma de fonctionnement de la
projection de matière [42].
Comme matériaux utilisés dans cette technologie,
on retrouve des matériaux plastiques photopolymérisables, cires
synthétiques, thermoplastiques à bas point de fusion [39].
Avec ce procédé on obtient de très bonnes
qualités dimensionnelles et un bon état de surface
(détails, belles finitions). Cependant les caractéristiques
mécaniques sont limitées, de part les spécificités
des matériaux utilisés.
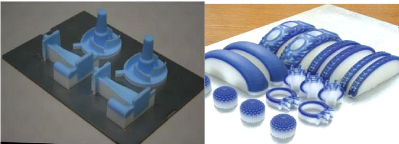
Figure 1-12 : Exemples de réalisation de
pièces par projection de gouttes [47].
21
MASTER II-LABORATOIRE SCIENCES DES
MATÉRIAUX
CHAPITRE 1-ÉLÉMENTS DE BIBLIOGRAPHIE
1.3.3 Extrusion De Matière
Le procédé d'extrusion de matière est le
plus connu en fabrication additive. Il a été inventé en
1992 par l'américain Scott Crump co-fondateur de l'entreprise Startasys
[48].
Une buse dépose un fil de façon sélective
couche après couche. Le matériau de départ est un fil
fondu qui est fondu avant d'être extrudé par la buse. Le fil
adhère sur les couches précédentes pour fabriquer les
pièces finales (Figure I.13).
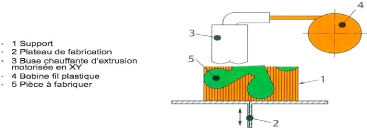
KOND NGUE PIERRE GÉRARD DAREL
(c)2021
Figure 1-13 : Schéma de fonctionnement du
dépôt de fusion au travers d'une buse chauffante (Extrusion de
Matière) [42].
Les matériaux utilisés sont des thermoplastiques :
ABS, polycarbonate, cire synthétique, Acide polylactique (PLA) [39].
Il s'agit d'un procédé assez lent, encore plus s'il
s'agit d'une pièce massive. Les caractéristiques
mécaniques sont limitées au matériau utilisé. La
finition et la précision sont des points à améliorer. Il
s'agit du procédé le plus connu et le plus mature
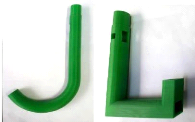
Figure 1-14 : Exemples de réalisation par
fusion au travers d'une buse chauffante [50].
1.3.4 Stratification De Couches
Le procédé de stratification de couches consiste
à fabriquer des couches puis les assembler. La matière initiale
est sous forme de rouleau laminé continu ou de plaque laminée
22
MASTER II-LABORATOIRE SCIENCES DES
MATÉRIAUX
KOND NGUE PIERRE GÉRARD DAREL
(c)2021
CHAPITRE 1-ÉLÉMENTS DE BIBLIOGRAPHIE
discontinue. Le découpage se fait au laser ou en
utilisant une machine CN (commande numérique) [43].
Un grand nombre de matériaux est disponible avec ce
procédé. Les plus utilisés sont des rouleaux ou des
plaques de papier, il peut aussi y avoir des polymères et de
l'aluminium. L'assemblage final se fait grâce à un rouleau
chauffant ou par soudage aux ultrasons dans le cas métal [39].
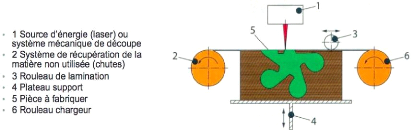
Figure 1-15 : Schéma de fonctionnement de
l'assemblage de couches (Stratification De
Couches) [42].
Ces procédés sont robustes et performants
surtout pour obtenir des modèles. Il faut cependant concevoir en ayant
en tête le retrait des parties intérieures.
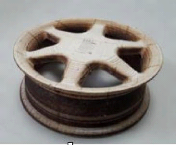
Figure 1-16 : Exemple de réalisation par
stratification de couches [47].
1.3.5 Projection De Liant
Le procédé de projection de liant est similaire
au procédé de projection de matière mis à part que
le liquide projeté permet de lier sélectivement un lit de poudre.
La solidification est activée thermiquement ou par réaction
chimique. Un certain nombre de post-procédés sont
nécessaires après la fabrication pour enlever la poudre non
liée et pour finaliser la liaison.
23
MASTER II-LABORATOIRE SCIENCES DES
MATÉRIAUX
CHAPITRE 1-ÉLÉMENTS DE BIBLIOGRAPHIE
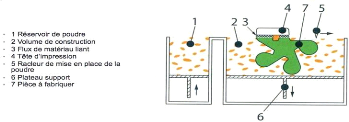
KOND NGUE PIERRE GÉRARD DAREL
(c)2021
Figure 1-17: Schéma de fonctionnement de la
projection de liant sur un substrat de poudre
[42].
La technologie d'impression 3D (non habituellement
utilisée abusivement pour désigner la fabrication additive)
utilise ce procédé. D'autres technologies ont été
développées et permettent de fabriquer des pièces dans une
grande variété de matériaux comme le plastique, le
métal, mais aussi le plâtre ou la céramique.
Dans le cas du métal, le liant est activé
thermiquement. Un post-procédé est nécessaire pour
finaliser la liaison dans un four, puis un autre pour enlever la poudre non
liée. Dans certaines technologies, du métal supplémentaire
est infiltré dans la pièce pour la densifier. Les principaux
métaux fabriqués sont des aciers inoxydables et des Inconels,
mais il est également possible de fabriquer des pièces en bronze,
chrome-cobalt ou tungstène [43].
Ce procédé est plus rapide (*5) mais on obtient
moins de détails et des finitions moins bonnes. Par contre, il est
possible d'imprimer directement en couleur. Il est possible d'utiliser des
matériaux écologiques et inoffensifs. Cependant, les
caractéristiques mécaniques sont limitées et on peut
obtenir un aspect granuleux.
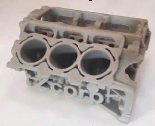
Figure 1-18 : Exemple de réalisation de
pièce par projection de liant [50].
24
MASTER II-LABORATOIRE SCIENCES DES
MATÉRIAUX
KOND NGUE PIERRE GÉRARD DAREL
(c)2021
CHAPITRE 1-ÉLÉMENTS DE BIBLIOGRAPHIE
1.3.6 Fusion Sur Lit De Poudre
Le procédé de fusion sur lit de poudre consiste
à fritter ou fusionner sélectivement un lit de poudre. La fusion
est activée thermiquement par l'intermédiaire d'un laser ou d'un
faisceau d'électrons. Des post-procédés sont
nécessaires pour enlever la poudre qui n'est pas fusionnée.
Ils existent d'autres technologies mais elles reposent toutes
sur le même principe. Les différences majeures proviennent de la
source d'énergie. Les technologies utilisant un laser sont les
technologies SLM, SLS, DMLS... La technologie utilisant un faisceau
d'électrons est l'EBM [43] [49].
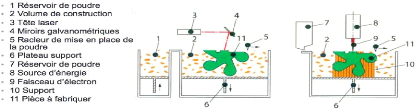
Figure 1-19 : Principe de fusion sur lit de poudre
[42].
Les pièces mises en forme sont en plastique,
métal ou céramique. Un très grand nombre de
matériaux sont disponibles avec plus ou moins de maturité. Les
principaux métaux utilisés sont des alliages de Titane (en
particulier le Ti-6Al-4V), les Inconels (625 et 718), les Aciers (aciers
inoxydables, aciers marasing) et les Aluminiums (aluminium de fonderie
uniquement). D'autres poudres métalliques existent mais sont moins
rependus (bronze, or, tantale) [43].
Les caractéristiques mécaniques sont bonnes,
puisque proche du matériau de base. Dans le cas d'une technologie
à haute température, on obtient des caractéristiques
similaires à des pièces obtenues en fonderie. Par contre, le
retrait de la pièce sur le support est une opération à
prévoir et très délicate à réaliser.
25
MASTER II-LABORATOIRE SCIENCES DES
MATÉRIAUX
CHAPITRE 1-ÉLÉMENTS DE BIBLIOGRAPHIE
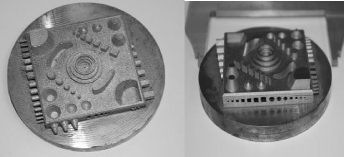
Figure 1-20 : Exemples de réalisation de
pièces par fusion sur lit de poudre [51].
1.3.7 Dépôt De Matière Sous
Énergie Concentrée
Le dépôt de matière sous énergie
concentrée consiste à projeter de la poudre métallique qui
est fusionnée sur la pièce grâce à une source
d'énergie thermique (laser, faisceau d'électrons ou plasma) de la
même façon que pour le lit de poudre [43]. La machine est souvent
composée de 4 ou 5 axes qui permettent de faire des couches qui ne sont
pas nécessairement planes. Il est aussi possible de réparer des
pièces en ajoutant de la matière ou de rajouter un
élément à une pièce existante [52]. Ce
procédé permet également de fabriquer des pièces
multi-matériaux en projetant des poudres différentes [53].

KOND NGUE PIERRE GÉRARD DAREL
(c)2021
Figure I-21 : Schéma du principe de
dépôt de matière sous énergie concentrée
[42].
Là encore, il existe plusieurs technologies utilisant
des sources ou des méthodes de projection de poudre différente.
Une autre technologie légèrement différente existe
également et est hybride entre l'extrusion de matière et le
dépôt de matière sous énergie concentrée.
Cette technologie consiste à déposer un fil métallique,
qui est fondu, pour créer les différentes couches [43]
[54].
26
MASTER II-LABORATOIRE SCIENCES DES
MATÉRIAUX
KOND NGUE PIERRE GÉRARD DAREL
(c)2021
KOND NGUE PIERRE GÉRARD DAREL
(c)2021
CHAPITRE 1-ÉLÉMENTS DE BIBLIOGRAPHIE
Seuls des matériaux métalliques peuvent
être fabriqués par ce procédé. Les matériaux
utilisés sont presque semblables à ceux utilisés en fusion
sur lit de poudre, sauf l'Aluminium qui pose certains soucis
supplémentaires pour le dépôt de poudre
(évaporation, dangerosité des poudres...). En dépôt
de fil métallique, la fabrication de certains alliages d'aluminium est
possible [39].
Ce procédé permet de fabriquer des pièces
de grandes dimensions, limité par l'enceinte de la machine. Les vitesses
de fabrication sont élevées : 10 à 200 cm3/h
selon la qualité désirée. Les caractéristiques
matériaux sont bons, proches du matériau de base. Il y a un large
choix de matériau. De plus, on peut ajouter de nouvelles parties
à une pièce. Il existe des machines de fraisage/tournage avec une
buse à poudre.
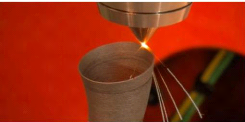
Figure 1-22 : exemple de réalisation par le
procédé de dépôt de matière sous
énergie
concentrée [47].
1.3.8 Comparaison Entre Les Différentes
Technologies
Pour contrôler les pièces, il existe des moyens
classiques comme la machine à mesurer tridimensionnelle et le scanner
3D, mais également la tomographie qui permet [55] de reconstruire
couche par couche la pièce pour constater les défauts et
connaitre la porosité. L'étude comparative menée entre les
différentes technologies sera basée sur des critères tels
que la qualité de finition, le nombre de matériau, l'outillage et
la taille des pièces. Elle sera consignée sous forme de tableau
:
27
MASTER II-LABORATOIRE SCIENCES DES
MATÉRIAUX
CHAPITRE 1-ÉLÉMENTS DE BIBLIOGRAPHIE
Type de procédé
|
Qualité de finition
|
Nombre de matériau
|
Outillages
|
Taille des pièces
|
Photo
polymérisation en cuve
|
Bonne
|
Limité
|
Moyen
|
Petites et moyennes
|
Projection de matière
|
Correcte
|
Limité
|
Moyen
|
Petites et moyennes
|
Extrusion de matière
|
Moyenne
|
Limité
|
Moyen
|
Petites et moyennes
|
Stratification de couches
|
Bonne
|
Important
|
Bon
|
Moyennes et grandes
|
Projection de liant
|
Moyenne
|
Limité
|
Moyen
|
Petites et moyennes
|
Fusion sur lit de poudre
|
Bonne
|
Correcte
|
Correcte
|
Petites et moyennes
|
Dépôt de matière sous
énergie concentrée
|
Correcte
|
Limité
|
Moyen
|
Petites et moyennes
|
Tableau 1-6 : Comparaison des différents
procédés
1.4 Fusion Sur Lit De Poudre : Procédé SLM
(Selective Laser Melting)
1.4.1 Principe Et Description
La fusion sélective par laser ou procédé
SLM est l'une des techniques de fabrication additive (FA) qui a vu le jour
à la fin des années 1980 et dans les années 1990 et qui ne
cesse de se développer grâce à des recherches intenses et
universitaires vigoureuses [56]. Ce procédé commence par le
découpage des données du fichier CAO 3D, au format Stl, en couche
et la création d'une image 2D de chaque couche. Ce fichier de
données tranché est ensuite envoyé à un logiciel de
préparation. Ce logiciel attribue des paramètres, des valeurs et
des supports physiques et permet au fichier d'être construit par
différents types de machines de fabrication additive [57].
28
MASTER II-LABORATOIRE SCIENCES DES
MATÉRIAUX
KOND NGUE PIERRE GÉRARD DAREL
(c)2021
CHAPITRE 1-ÉLÉMENTS DE BIBLIOGRAPHIE
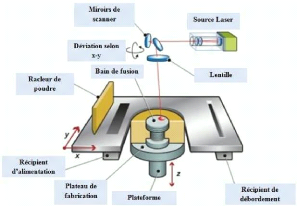
Figure 1-23 : Schéma du procédé
de Fusion Sélective Par Laser (SLM), d'après
Popular
3D Printers
Dans le procédé SLM, la pièce est
générée dans le cylindre de construction, au-dessus d'une
plaque de base ou d'un substrat. À côté du cylindre de
construction, il y a un récipient d'alimentation (également
appelé déposeur de poudre). À l'aide de ce dernier, une
fine couche de poudre (appelée épaisseur de couche) est
déposée uniformément au-dessus de la plaque de substrat
métallique, en abaissant le cylindre de construction et en relevant le
récipient d'alimentation. Après dépôt d'une couche,
une section transversale du composant à construire est balayé
avec le laser tel que le laser à fibre Nd :YAG et Ytterbium, qui produit
des centaines de watts de puissance. Ces sections transversales sont
calculées à partir d'un logiciel de préparation du
modelé CAO dont il a été question plus haut. En balayant
la surface de la couche de poudre, la chaleur s'ajoute au matériau en
absorbant la puissance. Elle fait fondre la couche de poudre, et le bain de
fusion se solidifie rapidement. Le matériau consolidé commence
à construire le produit. Après balayage d'une couche, la
plate-forme de construction est abaissée d'une quantité
correspondante à l'épaisseur de la couche et une nouvelle couche
est déposée sur la couche précédente à
l'aide du déposeur de couche. Le processus se répète
couche après couche jusqu'à ce que la pièce soit
complète, comme le montre la Figure 1-23. L'ensemble du processus
d'impression se déroule à l'intérieure d'une chambre qui
contient une atmosphère de gaz inerte, l'azote ou l'argon,
étroitement contrôlée. Dans certains cas, le lit de la
chambre est préchauffé.
La température à l'intérieur de la
chambre est uniformément répartie. Les structures de supports
sont également construites dans le cas du produit, ce qui implique
beaucoup de
29
MASTER II-LABORATOIRE SCIENCES DES
MATÉRIAUX
KOND NGUE PIERRE GÉRARD DAREL
(c)2021
CHAPITRE 1-ÉLÉMENTS DE BIBLIOGRAPHIE
complexité. Les structures de support couramment
utilisées sont illustrées à la Figure. Une fois le
processus SLM terminé, le substrat est retiré de la chambre de
fabrication, puis les supports et les pièces sont retirés. Les
supports doivent être conçus avec soin car ils peuvent être
difficiles à retirer, étant donné qu'ils sont
constitués du même matériau métallique dense que la
pièce [48], [49].
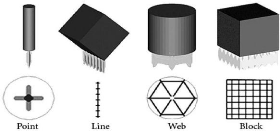
Figure 1-24 : Structure de soutien couramment
utilisées [49f.
Les différents matériaux pouvant être
traités sont l'acier allié, l'acier à outils, le bronze,
l'acier inoxydable, le titane-aluminium, le cobalt-chrome. Tous doivent exister
sous forme de poudre fine et présenter certaines caractéristiques
d'écoulement pour pouvoir être traités. Un certain nombre
de paramètres de processus affectant le processus SLM.
1.4.2 Paramètres Du Procédé SLM
Dans la technologie de fabrication additive, de nombreux
paramètres influence l'exactitude du procédé SLM (Figure
I-25). En analysant correctement ces paramètres, on peut comprendre les
mécanismes qui se produisent de manière appropriée pour
concevoir le procédé. Le procédé SLM est
très complexe car un grand nombre de paramètres peuvent
influencer la qualité de la pièce finale. Dans le cas
présent, les principaux paramètres du procédé SLM
sont la puissance du laser, le diamètre du faisceau laser/la taille du
point, la vitesse de balayage, le schéma de balayage, l'espacement des
hachures, les propriétés de la poudre, l'épaisseur de la
couche et la température à l'intérieur de la chambre
[32] [55], [58], [59].
30
MASTER II-LABORATOIRE SCIENCES DES
MATÉRIAUX
KOND NGUE PIERRE GÉRARD DAREL
(c)2021
CHAPITRE 1-ÉLÉMENTS DE BIBLIOGRAPHIE
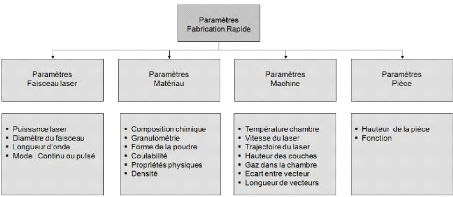
Figure 1-25 : Paramètres du
procédé SLM, d'après L. Van Belle [60f.
1.4.3 Simulation Et Modélisation Du
Procédé SLM 1.4.3.1. Généralités
Les technologies de FA suscitent un intérêt
considérable dans tous les secteurs industriels, car elles permettent de
concevoir et de fabriquer rapidement des prototypes et des produits. Toutefois
l'utilisation de ces technologies pose des problèmes, tels que la
défaillance des composants due à des problèmes de
dépôt de couches. Il existe de nombreux points au cours du
processus de fabrication où le composant fabriqué peut tomber en
panne pour cette raison. Des défaillances post-production de
pièces apparemment complètes peuvent également se
produire. L'identification de la forme devant être fabriquée
(forme compensée), pour obtenir la forme souhaitée, peut
être réalisée expérimentalement. En l'absence
d'expérience, cette étape peut s'avérer très
couteuse en temps et en matière première. De plus, elle est
envisageable uniquement pour les faces externes de la pièce [61].
Plusieurs facteurs influencent le processus de fabrication
tels que :
- Les méthodes de fabrication,
- Les caractéristiques des machines,
- Les propriétés des poudres utilisées,
- La trajectoire du laser,
- Les propriétés et le nombre des supports,
- L'orientation des pièces, etc.
Un grand nombre de paramètres (parfois plusieurs
dizaines), peuvent influencer la qualité des pièces et contribuer
à l'apparition de défauts, de fissures et de distorsions. Dans
ce
31
MASTER II-LABORATOIRE SCIENCES DES
MATÉRIAUX
KOND NGUE PIERRE GÉRARD DAREL
(c)2021
CHAPITRE 1-ÉLÉMENTS DE BIBLIOGRAPHIE
contexte, la simulation numérique s'impose comme un
outil indispensable pour la mise au point des processus de fabrication
additive, en permettant aux spécialistes d'anticiper les
déformations des pièces pendant leur fabrication.
1.4.3.2. Rôles De La Simulation
La simulation permet de répondre à
différentes problématiques industrielles, et permet de
[62] :
- Réduire les pertes de fabrication grâce
à la caractérisation des contraintes résiduelles dans la
pièce et de l'optimisation des zones finales à usiner pour les
réduire ;
- Optimiser les séquences de dépôts et les
conditions de bridage tout au long du processus de fabrication grâce
à l'anticipation des distorsions et contraintes ;
- Réduire le temps de fabrication en quantifiant
l'influence du préchauffage/refroidissement éventuel des
supports, et en déterminant les temps optimaux entre deux phases ;
- Améliorer et optimiser les processus post-fabrication
en qualifiant l'influence sur les contraintes et déformations de
traitements thermiques de dimensionnement.
Les avantages apportés par la modélisation
permettent aux industries une réelle maitrise de toute la chaine de
production sans avoir à effectuer de longs et couteux plans
d'expérience expérimentaux.
L'utilisation d'un model prédictif sera un outil
décisif pour guider les ingénieurs dans l'identification des
paramètres des processus de fabrication, et des géométries
« compensées » permettant d'obtenir les pièces
souhaitées dans les meilleurs délais et à un coût
maitrisé.
1.4.3.3. La Modélisation Multi-Échelle
(Micro, Méso, Macro)
L'objectif de la modélisation numérique
multi-échelle est de comprendre l'impact de l'interaction entre les
différents phénomènes physiques mis en jeu durant la
fusion et la solidification sur le comportement mécanique finale de la
pièce fabriquée. Elle permet aussi de réduire le recours
à l'expérimentation ce qui amorti considérablement le
temps et le coût de l'investigation [63].
? La modélisation à l'échelle
micro (échelle de la poudre)
Dans la modélisation à l'échelle micro,
on s'intéresse à l'interaction laser-matière et en
particulier à la réflectivité et l'absorption du rayon
laser pour estimer la quantité d'énergie thermique
absorbée. La modélisation de la distribution spatiale des
particules sur le lit de poudre joue un rôle important dans la zone
affectée thermiquement (ZAT). C'est en effet dans cette
32
MASTER II-LABORATOIRE SCIENCES DES
MATÉRIAUX
KOND NGUE PIERRE GÉRARD DAREL
(c)2021
CHAPITRE 1-ÉLÉMENTS DE BIBLIOGRAPHIE
zone que l'on définit les propriétés
thermo-physiques du processus de transfert thermique durant la fabrication. La
modélisation du bain de fusion permet de caractériser sa
dynamique, l'effet des phénomènes physiques durant la fusion
(tension de surface, effet Marangoni, pression de recul) sur sa forme
géométrique et sur les mécanismes de formation des
défauts (porosités, keyholes, ...). Dans cette catégorie,
on retrouve :
- La modélisation de la mise en couche
: au cours de la fabrication SLM, chaque nouvelle couche
nécessite une nouvelle distribution de particules de poudre sur le socle
de fabrication (spreding). Les propriétés physiques du bain de
fusion, le mécanisme de formation des porosités et la
qualité finale de la pièce dépendent étroitement de
l'uniformité du lit de poudre et de sa densité relative. En effet
la présence des porosités durant la mise en couche peut
influencer le bain de fusion et augmenter la probabilité de
piéger des gaz dans le matériau solidifié, d'où la
formation des défauts notamment des porosités et des keyholes.
Parmi les approches phares utilisées dans la modélisation de la
mise en couche, on peut signaler l'approche DEM (Discrete Element Method).
Cette méthode est basée sur l'assemblage d'éléments
distincts, déformables ou non, et reliés entre eux par des lois
très simples qui permettent de représenter le comportement du
matériau. Elle est très rependue pour les matériaux
granulaires, car elle représente naturellement la cinématique de
ces matériaux et leur comportement discontinu.
- Modélisation de l'apport thermique :
Durant le lasage, le lit de poudre est bombardé de rayon laser puissant
et de très courte durée. L'énergie photonique est alors
transformée en énergie thermique par absorption. La poudre permet
une pénétration en profondeur du rayon laser grâce à
multiples réflexions à la surface des particules.
L'énergie thermique absorbée dépend de la densité
relative et des propriétés réflectives du lit de poudre.
Les paramètres fonctionnels qui influencent l'intensité du
faisceau laser sont la puissance, la vitesse de déplacement,
l'espacement entre passes (hatch distance) et la longueur du scan.
- Modélisation du bain de fusion :
Elle a pour but de comprendre l'interaction entre les différentes
physiques du procédé lors de la phase de fusion et de
solidification. En effet, la géométrie du bain de fusion impacte
considérablement la microstructure qui dépend étroitement
de la vitesse et de la puissance du laser. Durant la fusion, les très
forts gradients de température provoquent un mouvement de convection qui
dirige le métal fondu vers les parois du bain de fusion. C'est ainsi que
se forment les keyholes ou capillaires. À la fin des bulles de gaz
peuvent être piégées et peuvent ne plus s'échapper
du fait d'un temps de solidification très court qui provoque la
formation de porosités.
33
MASTER II-LABORATOIRE SCIENCES DES
MATÉRIAUX
KOND NGUE PIERRE GÉRARD DAREL
(c)2021
CHAPITRE 1-ÉLÉMENTS DE BIBLIOGRAPHIE
? La modélisation à l'échelle
méso
Cette modélisation s'intéresse à
l'échelle de la couche ; elle porte sur la formation du cordon du bain
de fusion et l'apparition des défauts et des
irrégularités. À ce stade, la simulation va aider à
comprendre l'évolution de la microstructure issue du
procédé SLM. Elle permet aussi d'estimer l'histoire thermique et
les contraintes résiduelles locales au voisinage de la zone fondue,
point de départ pour modéliser les contraintes résiduelles
à l'échelle macro.
Plusieurs approches numériques se sont
développées pour la modélisation du bain et du cordon de
fusion, telle que l'approche ALE (Arbitrary Lagrangien Euleran), une approche
hybride très flexible qui peut être utilisée pour la
modélisation de la zone fondue à l'échelle micro et pour
la modélisation du cordon à l'échelle méso.
L'approche level-set est utilisée, quant à elle s'une part pour
suivre l'évolution à l'échelle microscopique de la surface
du bain de fusion et d'autre part à l'échelle mésoscopique
pour modéliser l'évolution du cordon en prenant en compte
certaines hypothèses sur le milieu. Ces deux méthodes sont
basées sur la méthode des éléments finis.
? La modélisation à l'échelle
macro
Elle prend en compte les contraintes résiduelles et la
déformation finale à l'échelle de la pièce.
L'approche macro n'envisage pas de prédire la forme du bain de fusion et
les défauts qui en résultent dans certaines approches, mais
essentiellement les transferts thermiques macroscopique et leurs
conséquences sur la ténue de la pièce et sa durée
de vie. On s'intéresse ici à la modélisation de l'apport
en énergie, thermomécanique et la modélisation
géométrique de la pièce finale. La plupart des
modèles macro sont basés sur la méthode des
éléments finis.
1.4.3.4 Modélisation Numérique Du
Procédé SLM
Les paramètres accessibles qui intéressent la
plupart des études antérieures sont la puissance du laser, le
diamètre du faisceau, la vitesse de balayage, l'épaisseur de la
couche de poudre te la granulométrie.
Gusarov et al. [64], [65], [66] ont
modélisés la pénétration de la chaleur et des
rayonnements dans un lit de poudre en prenant en compte des réflexions
multiples. Ils ont calculé numériquement la distribution de la
température dans la région d'interaction laser-poudre et ont
étudié l'influence de l'épaisseur de la couche de poudre
et de la puissance du laser sur la forme du bain de fusion. Ils ont
également étudié les effets de la vitesse de balayage.
Verhaeghe et al. [67] ont présenté un
modèle permettant de déterminer l'effet de l'évaporation
de la matière. Ils ont constaté l'évaporation devient un
phénomène très significatif
34
MASTER II-LABORATOIRE SCIENCES DES
MATÉRIAUX
KOND NGUE PIERRE GÉRARD DAREL
(c)2021
CHAPITRE 1-ÉLÉMENTS DE BIBLIOGRAPHIE
à des densités d'énergie importantes. Ils
ont aussi étudié les gradients thermiques et la dynamique des
fluides dans le bain de fusion.
Dai et Gu [68] ont développé une
simulation numérique qui concerne l'influence de la densité
d'énergie du faisceau sur la dynamique du bain de fusion et les
mécanismes de densification.
Khairallah et Anderson [69] ont développé
un modèle mésoscopique 3D de simulation. Ils ont
étudié la fusion par faisceau laser des particules d'un lit de
poudre aléatoire en acier inoxydable 316L disposé sur un substrat
solide et la solidification de la masse fondue en cordon, qui peut être
soit continu ou discontinu en raison de l'instabilité de
Rayleigh-Plateau.
Antony et al. [70] ont effectué une étude
numérique pour comprendre l'effet de certains paramètres du
procédé SLM lors de la fusion d'une poudre d'acier inoxydable
316L déposée sur un substrat constitué du même
matériau dans le cas d'un laser pulsé Nd :YAG. Ils ont
considéré l'effet de certains paramètres
procédés tels que la puissance du laser, la vitesse de balayage
et la taille du faisceau sur les caractéristiques dimensionnelles de la
zone de fusion à partir de la distribution des champs de
température. Les résultats confirment l'effet important de la
vitesse et de la puissance du laser sur les caractéristiques du bain
fondu.
Zhang et al. [71] ont étudié des
pièces en Ti pur fabriquées avec le procédé SLM
sous vide et ils ont montré que la surface devient plus lisse avec une
rugosité Ra de 5 um en évitant le phénomène de
balling. La masse volumique des échantillons obtenus à des
vitesses de balayages faibles était la même que la valeur
théorique de la densité du Ti. Ils ont aussi analysé
l'influence de la nature du gaz de protection sur la fabrication des
pièces en acier inoxydable 316L. Ils ont également
étudié l'effet de différents types de mélanges de
gaz protecteurs sur la densité d'échantillons en 316L. On observe
que les échantillons fabriqués sous Ar, N2 et leurs
mélanges avec H2 présentent des densités
supérieures à 99%. Toutefois une diminution de la pression dans
la chambre de fabrication a également entrainé une
réduction de la section des cordons résultant probablement d'une
augmentation du niveau de vaporisation.
1.5 Conclusion
Cette étude bibliographique a permis de
présenter des généralités sur la fabrication
additive notamment son principe, ses avantages et ses limites, ses
différents domaines d'applications en passant par la présentation
des différents procédés de fabrication qu'elle regroupe en
son sein et plus spécifiquement le procédé de fusion
sélective par laser (Selective Layer Melting : SLM).
35
MASTER II-LABORATOIRE SCIENCES DES
MATÉRIAUX
KOND NGUE PIERRE GÉRARD DAREL
(c)2021
CHAPITRE 1-ÉLÉMENTS DE BIBLIOGRAPHIE
Le procédé SLM permet de produire des
pièces de forme géométrique complexe grâce à
un laser faisant fondre le métal dans les zones souhaitées.
Toutefois, une meilleure compréhension des phénomènes
physiques intervenant lors du procédé et des effets de certains
paramètres procédés est encore nécessaire pour
améliorer son application industrielle.
De nombreuses études expérimentales portant sur
les paramètres opératoires du procédé SLM dans le
cadre de l'influences de ces derniers sur l'état de surface des
pièces obtenue par fabrication additive ont déjà
été menées. Toutefois les travaux expérimentaux
sont très couteux, leur mise en place est longue et les résultats
obtenus ne sont pas toujours suffisant pour comprendre les
phénomènes physiques intervenant lors du procédé.
C'est pourquoi de nombreux travaux ont cherché à
développer des modèles numériques simulant ces
phénomènes dans le but d'appréhender les
différentes influences des paramètres opératoires
lié du procédé.
36
MASTER II-LABORATOIRE SCIENCES DES
MATÉRIAUX
KOND NGUE PIERRE GÉRARD DAREL
(c)2021
CHAPITRE 2-MÉTHODE EXPÉRIMENTALE ET
MODÈLE NUMÉRIQUE
CHAPITRE 2-MÉTHODE EXPÉRIMENTALE ET
MODÈLE NUMÉRIQUE
2.1 Introduction
Dans ce chapitre on présente les travaux
expérimentaux effectués qui visent à étudier
principalement l'influence des caractéristiques du processus telles que
la puissance du laser, la vitesse de balayage, le diamètre du laser, la
distribution de la température et la compacité du lit de poudre
sur le bain de fusion. Une description du modèle utilisé dans le
cadre des simulations multi-échelles sera également
faite.
2. 2 Configuration
Expérimentale
2. 2. 1 Préparation Des
Échantillons
Les échantillons ont été
réalisés dans une machine de fusion à lit de poudre
Concept Laser M2 Dual Laser sous atmosphère d'argon. Le Concept Laser M2
est équipé d'un laser à fibre à onde continue Yb:
YAG (1070 nm) avec une puissance nominale maximale de 400 W et caméra
infrarouge SWIR haute vitesse (Fig. 2.1).
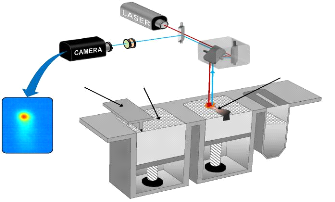
Scanning system
Filters
High speed
melt-pool
monitoring
piston
Semi-reflective blade
Part being fabricated
Recoater
Powder
Powder delivery
piston
Fabrication
Figure 2-1: Vue schématique du processus de
fusion laser sur lit de poudre équipé d'un système de
caméra infrarouge haute vitesse [72]
37
MASTER II-LABORATOIRE SCIENCES DES
MATÉRIAUX
CHAPITRE 2-MÉTHODE EXPÉRIMENTALE ET
MODÈLE NUMÉRIQUE
L'intensité du faisceau laser à fibre
présente une distribution gaussienne typique. Les stratégies de
balayage laser impliquent une seule direction et un balayage ponctuel. Les
paramètres de traitement expérimental sont
énumérés ci-dessous dans le Tableau 2.1.
Puissance (W)
|
200
|
250
|
300
|
350
|
Vitesse de balayage
|
Vs (mm.s-1)
|
Cordon
|
Vs (mm.s-1)
|
Cordon
|
Vs (mm.s-1)
|
Cordon
|
Vs (mm.s-1)
|
Cordon
|
200
|
S1/T1
|
250
|
S7/T7
|
300
|
S13/T13
|
350
|
S19/T19
|
400
|
S2/T2
|
500
|
S8/T8
|
600
|
S14/T14
|
700
|
S20/T20
|
500
|
S3/T3
|
625
|
S9/T9
|
750
|
S15/T15
|
875
|
S21/T21
|
667
|
S4/T4
|
833
|
S10/T10
|
1000
|
S16/T16
|
1167
|
S22/T22
|
1000
|
S5/T5
|
1250
|
S11/T11
|
1500
|
S17/T17
|
1750
|
S23/T23
|
2000
|
S6/T6
|
2500
|
S12/T12
|
3000
|
S18/T18
|
3500
|
S24/T24
|
Tableau 2-1: Conception de l'expérience
(DOE) pour les pistes à balayage unique
Des balayages simples ont été effectués
pour former des cordons uniques sur un substrat de plaque de base nu (sans
poudre) et une plaque de base avec une couche mince de 30 pm de poudre de
Ti-6Al-4V. Selon la conception factorielle de l'expérience (DOE)
où la taille du faisceau laser est Ö1 = 110 um, un total de
vingt-quatre pistes a été réalisé sur un substrat
nu (S1-20) et sur une couche de poudre (T1-20). Les particules de poudre
présentent une distribution de taille comprise entre 2 um (Ö10) et
36 um (90) avec un diamètre volumique moyen d'environ 13 um (Ö30).
Pour corréler les changements possibles des régimes de fusion
avec un paramètre énergétique fiable, une densité
d'énergie volumique (DEV) est calculée pour chaque condition
expérimentale comme suit :
4 P
DEV= (1) 1101 2 vs
Avec la vitesse de balayage (vs), la
puissance incidente (P) et le diamètre du faisceau (Öl). Certaines
conditions de procédé présentées dans le tableau 1
ont été choisies de manière à obtenir des plages de
DEV similaires. Afin d'étudier la morphologie du bain de fusion, chaque
piste a été sectionnée à trois endroits
(début, milieu et fin) pour une profondeur et une largeur moyenne. Les
coupes transversales ont ensuite été montées dans une
résine thermodurcissable, broyées jusqu'à 1200 à
l'aide de papiers abrasifs métallographiques, polies et finalement
gravées à l'aide d'une solution de Kroll entre 10 et 15 secondes
pour l'imagerie par microscopie optique et l'analyse d'image des Fidji (Image
J).
Comme le montre la Figure 2.2, trois dimensions principales
peuvent être mesurées à partir de la section transversale
des voies : (i) la hauteur de la zone apparente Happ, (ii) la
profondeur de la zone refondue HRZ et (iii) la largeur de la
perle eapp. La zone apparente (AZ) définit la zone
au-dessus de la surface de la plaque de construction ou de la couche
précédente dans le cas d'une fabrication couche par couche tandis
que la zone refondue (RZ) est la zone où
38
MASTER II-LABORATOIRE SCIENCES DES
MATÉRIAUX
KOND NGUE PIERRE GÉRARD DAREL
(c)2021
KOND NGUE PIERRE GÉRARD DAREL
(c)2021
CHAPITRE 2-MÉTHODE EXPÉRIMENTALE ET
MODÈLE NUMÉRIQUE
le métal a été refondu. Ces
paramètres de bain de fusion ont été mesurés
à l'aide du logiciel Image J.
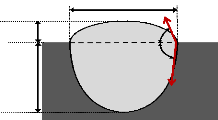
eapp
Happ
è
á
HZR
RZ
Substrate
Figure 2-2 : Caractéristiques morphologiques
intrinsèques d'une trace de fusion mesurables [72f.
Remelted zone
2. 2. 2 Mesures In Situ De La Température
Du Bain De Fusion
Afin d'obtenir des informations sur le bain de fusion, sa
dynamique et sa stabilité, des mesures in situ des champs de
température du bain de fusion spatiale et temporelle ont
été réalisées. Comme le montre la Figure 2.1, le
système développé par B. Fosse [72] de Mines Paris
Tech est équipé d'une caméra infrarouge SWIR haute vitesse
alignée coaxialement pour surveiller en temps réel le bain de
fusion en visualisant l'évolution de la température de surface et
les phénomènes d'interaction se produisant lors de la fusion du
matériau. La caméra atteint une fréquence d'images
maximale de 5000 images/s avec une taille de fenêtre de 160 pixels
horizontaux par 112 pixels verticaux. La taille des pixels est de 10,2 um et la
fenêtre équivaut à 1,632x1,142 mm. Une fois ces cadres
obtenus, ils sont analysés en seuillant (limitant) leur surface avec une
isotherme correspondant à la température de fusion (1928K) du
matériau Ti-6Al-4V étudié. Lorsque le seuil du bain de
fusion est effectué, les informations suivantes sont extraites :
température, température de pointe, inertie du bain de fusion
pour obtenir le profil de température le long de l'axe d'inertie, aire
du bain de fusion à l'isotherme de température de fusion,
gradients de température et largeur et longueur du bain de fusion.
Ces mesures qui fournissent des signatures de processus utiles
pour la qualité et le contrôle de processus nécessitent un
étalonnage de la température. La mesure étalonnée
de la température en un seul endroit du bain de fusion a
été réalisée grâce à l'application
d'une routine et d'un système d'étalonnage mis au point par B.
Fosse [72]. Ce dernier permet aux informations acquises et extraites du bain de
fusion d'être en température réelle.
39
MASTER II-LABORATOIRE SCIENCES DES
MATÉRIAUX
CHAPITRE 2-MÉTHODE EXPÉRIMENTALE ET
MODÈLE NUMÉRIQUE
2. 3 Configuration Numérique
2. 3. 1 Modèle Phénoménologique
Dans le cadre de cette étude, le module Melting de la
fabrication additive ESI a été utilisé et
développé afin de simuler avec précision le processus SLM.
Le module de fusion est un modèle mésoscopique multi-physique
utilisé pour étudier l'influence des caractéristiques du
processus telles que la puissance du laser, la vitesse de balayage, le
diamètre du laser, la distribution de la température et la
compacité du lit de poudre sur le bain de fusion et pour
améliorer la compréhension du processus LBM. Le modèle
comprend l'écoulement de fluide, le transfert de chaleur, la transition
de phase pendant la fusion, la solidification et l'évaporation du
métal avec la chaleur latente associée, le transport de masse et
les forces de tension superficielle dépendant de la température
conduisant aux forces de Marangoni.
Comme mentionné, l'approche numérique est
basée sur des méthodes de dynamique des fluides computationnelle
(CFD) pour résoudre toutes les équations physiques fondamentales
(équations de Navier-Stockes) [73], [74], [75], [76] qui
régissent les phénomènes mentionnés ci-dessus. Ces
équations physiques clés sont présentées ci-dessous
:
> Conservation de masse
Cette équation est considérée afin
d'assurer la continuité du matériau. Elle est donnée
par :
ap
+ V · p??? = 0 (2)
at
Où ñ est la densité du mélange de
fluides, t est le temps et v est le vecteur de vitesse moyenne en masse.
> Conservation du moment
La conservation de la quantité de mouvement est
modélisée par l'équation ci-dessous qui est étendue
à l'aide de termes source pour tenir compte des forces corporelles
gravitationnelles, de la pression de recul et de la tension superficielle.
C(1 - fL)2 ?
V
fL3 + CK
+ [o ·k??? + ??o ·
???? (V?? - n(n · VT))]
·n+pR ·n+pg (3)
+ V · pw= Vp+ V · T
at
api;
KOND NGUE PIERRE GÉRARD DAREL
(c)2021
40
MASTER II-LABORATOIRE SCIENCES DES
MATÉRIAUX
KOND NGUE PIERRE GÉRARD DAREL
(c)2021
CHAPITRE 2-MÉTHODE EXPÉRIMENTALE ET
MODÈLE NUMÉRIQUE
Où p est la pression hydrodynamique,
ô est le tenseur de contrainte de cisaillement
déviatorique calculé en utilisant la viscosité dynamique
effective du mélange, fL est la fraction liquide,
ó la tension superficielle, k la
courbure superficielle, ??? la normale superficielle, T la
température, ???? est la pression de recul et ??? le vecteur de
gravité. Le troisième terme appelé terme de Darcy sur le
côté droit décrit le terme d'amortissement dans la zone
pâteuse où C et CK sont
respectivement le coefficient de perméabilité et une petite
constante. Le quatrième terme représente les forces de tension
superficielle à la surface du matériau fondu et les effets
Marangoni résultant des valeurs de tension superficielle
dépendant de la température. Lorsque la variation de la tension
superficielle avec la concentration des espèces est
négligée, la tension superficielle est approximée pour
varier linéairement avec la température selon :
????
??(??) = ?????? + ???? (?? - ??????) (??)
Où ólt est la tension
superficielle à la température de liquidus Tls
et la dérivée de température ?ó/?T est
considérée comme constante
? Conservation d'énergie
L'équation énergétique qui tient compte
de la conduction (terme de diffusion) et de la convection est
complétée par des termes sources représentant la chaleur
latente requise ou libérée pendant la fusion / solidification et
l'évaporation / condensation ainsi que le rayonnement.
?????????? ???????????? ????(?? - ????)????
+ ?? · ????? ?? = ?? · (?????? + ? ?????? ?? ) + ????
+ ??: ????? - ???? - ??(????? ????????) - + ???? · ??? (??)
???? ???? ??
Où h est l'enthalpie totale et
ë est la conductivité thermique du mélange,
hi est l'enthalpie spécifique de l'espèce i, ??
?? est le flux massique d'espèce, Lf et Lv
sont la chaleur latente de fusion et d'évaporation,
respectivement. FL et fV sont respectivement
la fraction liquide et vapeur. D'autres termes sources représentant le
rayonnement sont nécessaires pour l'équation d'énergie.
Les équations ci-dessus sont complétées
par une équation scalaire pour suivre la surface libre du métal
fondu. Le scalaire est généralement choisi comme une fraction
volumique fluide de l'un des états du matériau, tel que celui de
l'état liquide (volume de fluide - VOF) :
41
MASTER II-LABORATOIRE SCIENCES DES
MATÉRIAUX
KOND NGUE PIERRE GÉRARD DAREL
(c)2021
CHAPITRE 2-MÉTHODE EXPÉRIMENTALE ET
MODÈLE NUMÉRIQUE
?????? ????
+ ?? · ??????? =
????
????
|
???? (??)
????
|
Où áL est la fraction volumique
du liquide et mL, mV sont les sources de
masse liquide et vapeur dues respectivement au changement de phase.
? Source de chaleur gaussienne
La modélisation de la source de chaleur est un point
fondamental dans la simulation de processus SLM. Dans cette étude, la
source de chaleur avec une distribution gaussienne est appliquée :
?????? ??(??, ??) = (??)
??????(??) ?????? [- ??????
????(??)] ??(??)
Où q (r, z) représente le flux
à la distance radiale r de l'axe laser et la profondeur
z du haut du lit de poudre, P est la
puissance laser telle que l'intégrale de surface de eq. (6) sur
r doit être égal à la puissance totale du
faisceau, R est le rayon laser effectif qui définit le
profil d'intensité gaussienne du laser à la profondeur
z. Dans ce cas, R est supposé
constant. Le paramètre â est un facteur
géométrique qui complète la définition du profil
gaussien.
? Modèle d'évaporation
L'évaporation du métal de la surface du liquide
enlève une chaleur significative du bain de fusion et produit la
pression de recul qui peut être calculée à partir de la
théorie cinétique. On trouve une relation entre la pression de
recul et la pression de vapeur saturée, PV, comme suit
:
???? ? ??. ????????(??) (??)
Sur la base de l'équation de Clausuis-Clapeyron, Leitz
et al. [77] ont calculé la pression de vapeur à partir de
la température connue ci-dessous :
???? = ???????? ?? [????? ???( ?? - ?? ??)] (??)
????
Où PV est la pression
d'évaporation, Pb est la pression d'ébullition,
Lv est la chaleur latente d'évaporation, M (kg
/ mol) est la masse molaire, R (J / mol K) est la
constante de gaz idéale et T (K) est la
température. Sous certaines hypothèses, Moscicki et al.
[78] ont calculé
42
MASTER II-LABORATOIRE SCIENCES DES
MATÉRIAUX
KOND NGUE PIERRE GÉRARD DAREL
(c)2021
CHAPITRE 2-MÉTHODE EXPÉRIMENTALE ET
MODÈLE NUMÉRIQUE
le taux de perte de masse (m ?) (kg /
(m2s)) sur la base de l'équation de Hertz Knudsen et
de Clausius-Clapeyron comme suit :
llxn= (1- c) * Pb* 2rrMRT * ex I3 [LvM(1R Tb T1 )]
(10)
Où c est la fraction de phase vapeur qui
revient.
Toutes les équations mentionnées ci-dessus ont
été discrétisées puis résolues à
l'aide d'une méthode des volumes finis (FVM) dans le module de fusion de
la solution de fabrication additive ESI qui est basée sur le logiciel
CFD-ACE + de Computational Fluid Dynamics (CFD) d'ESI Group.
2. 3. 2 Modèle Numérique
Un modèle de volume fini tridimensionnel a
été construit pour simuler la réponse de la fusion laser
de l'alliage de titane Ti-6Al-4V à l'aide du module de fusion de la
solution de fabrication additive ESI du fournisseur de logiciel commercial ESI
Group. Pour la validation du modèle, un domaine de substrat Ti-6Al-4V a
d'abord été modélisé comme un bloc tridimensionnel
de 750 x 500 x 660 um3 (Figure 2.3). Les propriétés
thermophysiques utilisées dans la simulation sont rapportées dans
le Tableau II.1. Un total de 1.140.000 cellules hexaédriques pour le
modèle de calcul est généré et les équations
sont résolues en utilisant un pas de temps de 2 x 10-7s
(Figure 2.3). Une taille de cellule de 3 um × 3 um × 3 um est
utilisée pour simuler avec précision le processus. Les
propriétés thermophysiques du Ti-6Al-4V et de l'argon sont
attribuées respectivement aux régions du substrat et du gaz. Une
source de chaleur laser est appliquée à partir du haut du
substrat pour parcourir 0,4 mm à une vitesse v dans la direction y. Le
temps de calcul pour une simulation d'un cordon nécessite environ 24
heures de temps de l'unité centrale (CPU) à 32 coeurs.
43
MASTER II-LABORATOIRE SCIENCES DES
MATÉRIAUX
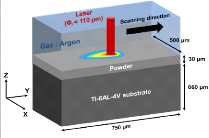
KOND NGUE PIERRE GÉRARD DAREL
(c)2021
CHAPITRE 2-MÉTHODE EXPÉRIMENTALE ET
MODÈLE NUMÉRIQUE
Figure 2-3 : Vue d'ensemble schématique de
la configuration numérique
Après la simulation de la fusion laser sélective
sur un substrat, un solveur DEM (DEM = Discrete Element Method) a
été utilisé pour simuler le processus d'étalement
d'une poudre Ti-6Al-4V de distribution de taille de grain allant de 2 à
36 um pour étudier l'effet de poudre sur le comportement du bain de
fusion. Cette distribution de taille expérimentale a été
utilisée comme paramètre d'entrée pour
générer le nuage de poudre. Un total d'environ 260 550
particules de poudre a été initialisé. Comme les
solveurs DEM nécessitent d'initialiser toutes les particules sans
contact, il est obligatoire de spécifier une case dans la région
dite source juste en face du bras de recouvrement comme indiqué sur la
Figure 2.4. Sous l'effet de la gravité, les particules de poudre sont
installées devant le racleur (Figure 2.4). Une fois les particules
déposées, le racleur est mis en mouvement pour répartir
les particules sur la table de traitement. La hauteur de la boite et du racleur
est automatiquement calculée par l'angle de repos supposé
de ? = 30 °. Une vue schématique des
entités géométriques utilisées dans la simulation
d'étalement est représentée sur la Figure 2.4 indiquant
également leurs dimensions. Les structures géométriques
(boîte, racleur, table de déplacement) sont
spécifiées par trois fichiers STL. Le racleur a une vitesse de
déplacement constante de translation de 0,1 m/s comme
dans l'expérience.
44
MASTER II-LABORATOIRE SCIENCES DES
MATÉRIAUX
KOND NGUE PIERRE GÉRARD DAREL
(c)2021
CHAPITRE 2-MÉTHODE EXPÉRIMENTALE ET
MODÈLE NUMÉRIQUE
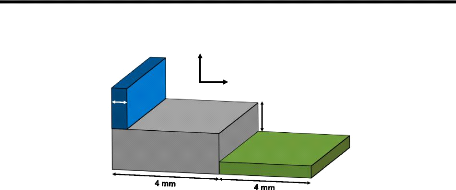
60 um
100 um
Box
Building
Spreader/
recoater
Spreading
Table
Figure 2-4 : Reference de l'épandage sur lit
de poudre.
Table displacement
À partir du solveur DEM, le lit de poudre simulé
sur la table de déplacement est utilisé comme entrée pour
la simulation de fusion. Par conséquent, toutes les particules d'une
région dédiée à l'intérieur du lit de poudre
sont utilisées pour initialiser le lit de poudre pour la simulation de
fusion. Cela se fait en utilisant les coordonnées des particules et
leurs diamètres spécifiques.
Dans la simulation de fusion, considérant que le
substrat est plus petit que dans le processus réel, un coefficient de
transfert thermique limite de ht = 5000 W.m-2 K-1
et une émissivité de å = 0,6 ont
été considérés comme prenant en tenant compte des
pertes de chaleur par convection et rayonnement à la limite
inférieure du domaine de la solution. Toutes les autres limites de mur
sont supposées être adiabatiques. La conception des
expériences (DOE) mentionnée ci-dessus a été
réalisée pour la simulation de la réponse du bain de
fusion. Les simulations ont été réalisées avec les
paramètres d'entrée mentionnés dans le Tableau II. 2.
45
MASTER II-LABORATOIRE SCIENCES DES
MATÉRIAUX
KOND NGUE PIERRE GÉRARD DAREL
(c)2021
CHAPITRE 2-MÉTHODE EXPÉRIMENTALE ET
MODÈLE NUMÉRIQUE
Propriétés du Ti-6Al-4V
|
Symboles
|
Propriétés
|
Valeurs
|
Références
|
Tb (K)
|
Température du point d'ébullition
|
3315
|
[79]
|
|
???? (Kg.m-3)
|
Densité du liquide au point d'ébullition
|
3780
|
[80],[81],[82]
|
|
TL (K)
|
Température de Liquidus
|
1928
|
[83]
|
|
TS (K)
|
Température de Solidus
|
1878
|
[83]
|
|
????(W.m-1.K-1)
|
Conductivité thermique du solide
|
21
|
[84]
|
|
????(J. Kg-1. K-1)
|
Chaleur spécifique du liquide au point
d'ébullition
|
730
|
[85]
|
???? (W.m-1. K-1)
|
Conductivité thermique du liquide au
point d'ébullition
|
29
|
[86]
|
|
|
???? (W.m-1. K-1)
|
Conductivité thermique du liquide
|
29
|
[87], [88]
|
|
???? (J. Kg-1. K-1)
|
Chaleur spécifique du solide
|
670
|
[89]
|
|
???? (J. Kg-1. K-1)
|
Chaleur spécifique du liquide
|
730
|
[89]
|
|
???? (Kg.m-3)
|
Densité du solide
|
4420
|
[90]
|
|
|
???? (Kg.m-3)
|
Densité du liquide
|
3920
|
[90]
|
|
??
|
Coefficient d'absorption laser
|
0.5
|
[90]
|
|
???? (J.K-1)
|
Chaleur latente de fusion
|
3×105
|
[90]
|
|
???? (J.K-1)
|
Chaleur latente d'évaporation
|
9.8×106
|
[90]
|
|
???? (N.m-1. s-1)
|
Tension superficielle
|
1.47
|
[90]
|
|
???? (N.m-1. s-1)
|
Tension superficielle au point d'ébullition
|
0.01
|
/
|
???? (Pa. s)
|
Viscosité dynamique
|
6x10-3
|
[89]
|
|
Propriétés thermo-physiques de
l'argon
|
???? (Kg.m-3)
|
Densité de gaz
|
1.67
|
/
|
???? (Pa. s)
|
Viscosité dynamique
|
2.1×105
|
[83]
|
|
???? (J. Kg-1. K-1)
|
Chaleur spécifique
|
520
|
/
|
?? ?? (W.m-1. K1)
|
Conductivité thermique
|
0.0163
|
/
|
Tableau 2-2: Propriétés
thermo-physiques utilisées pour les simulations
46
MASTER II-LABORATOIRE SCIENCES DES
MATÉRIAUX
KOND NGUE PIERRE GÉRARD DAREL
(c)2021
CHAPITRE 2-MÉTHODE EXPÉRIMENTALE ET
MODÈLE NUMÉRIQUE
2.4 Conclusion
Le chapitre 2 a été consacré aux
différents travaux expérimentaux et numériques
menés dans le cadre de cette étude.
Les travaux expérimentaux ont consisté
grâce à une machine de fusion sur lit de poudre Concept Laser M2
Dual à fabriquer des cordons unitaires sous différents
paramètres de puissance laser et de vitesse de balayage comme
décrit par le tableau 2.1 dans le but d'étudier l'influence des
paramètres considéré sur la topologie des pièces
obtenues en SLM. Ces paramètres ont été choisi de
manière à obtenir des plages similaires en terme de
densité d'énergie volumique du laser (Équation 1). Au
cours de ces travaux, deux cas ont été envisagé : celui du
substrat sans lit de poudre et celui du substrat avec lit de poudre fait
à partir de l'alliage de Ti6Al4V. Ainsi pour chacun de ces cas, un total
de 24 cordons unitaires a été réalisé.
Les travaux numériques ont porté sur la
simulation du procédé SLM avec pour objectif de prédire la
morphologie et la microstructure finale d'ne pièces d'une part et
d'autres part d'étudier l'influence des caractéristiques du
processus telles que la puissance laser, la vitesse de balayage et la
densité d'énergie volumique afin d'améliorer la
compréhension de ce procédé de fabrication. Pour ces
études de simulation, le module melting (module de fusion) de
fabrication additive ESI du fournisseur de logiciel commercial ESI Group a
été utilisé.
47
MASTER II-LABORATOIRE SCIENCES DES
MATÉRIAUX
KOND NGUE PIERRE GÉRARD DAREL
(c)2021
CHAPITRE 3-RÉSULTATS, ANALYSES ET
DISCUSSIONS
CHAPITRE 3-RÉSULTATS, ANALYSES ET
DISCUSSIONS
Le modèle numérique décrit dans le
Chapitre II a été développé avec pour objectif
principal d'analyser l'influence de la puissance laser, la vitesse de balayage
et de la densité d'énergie volumique (DEV) sur le
procédé de fusion sur lit de poudre par faisceau laser.
Dans ce Chapitre, une première partie sera
consacrée à l'analyse de l'influence de ces paramètres
procédés sur la morphologie des cordons, les régimes de
fusion du bain et les dimensions du bain de fusion respectivement. Ensuite dans
une seconde partie on traitera le sujet principal de cette étude qui
consiste en l'analyse de sensibilité des paramètres susceptibles
d'influencer l'état de santé des pièces obtenues par
fabrication additive.
3.1 Investigations Des Résultats
Expérimentaux Et Numériques
3.1.1 Effet des paramètres procédés
sur la morphologie de surface du cordon
Pendant le procédé SLM, les paramètres
procédés peuvent affecter la morphologie en surface et en
profondeur de chaque cordon entrainant par la même occasion des
modifications sur la pièce finale imprimée. La figure 3.1
montre la morphologie de surface des cordons obtenus à partir de la
paramètrie mentionnée au Chapitre II (Tableau 2.1).
L'observation des cordons déposés avec les
puissances laser de 200 W (Figure 3.1) montre qu'à des vitesses
de balayage de 200, 400, 500, 667 et 1000 mm/s avec des valeurs de
Densité d'Énergie Volumique (DEV) correspondantes de 105, 52.6,
42, 31.5 et 21 J/mm3 respectivement, on obtient une fusion
complète ainsi que la formation de cordons continus. Pour une puissance
laser de 250 W, la fusion est complète lorsqu'on applique des vitesses
de balayage de 250, 500, 625 et 833 mm/s correspondant aux DEV de 105, 52.6, 42
et 31.5 J/ mm3. Lorsqu'on utilise une puissance laser de 300 W, on
obtient la fusion complète et continue pour les mêmes DEV que 250
W avec des vitesses de balayage de 300, 600, 750 et 1000 mm/s. Dans le cas
d'une puissance laser de 350 W, la fusion est complète et continue
uniquement pour des vitesses de balayage de 350 et 700 mm/s avec des DEV de 105
et 52.6 J/mm3.
48
MASTER II-LABORATOIRE SCIENCES DES
MATÉRIAUX
KOND NGUE PIERRE GÉRARD DAREL
(c)2021
CHAPITRE 3-RÉSULTATS, ANALYSES ET
DISCUSSIONS
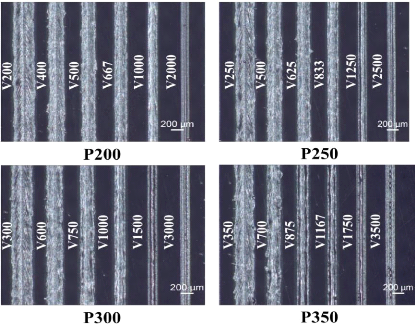
Figure 3-1: Topologie de surface des cordons
obtenus sur un substrat en Ti6Al4V
Il est évident que pour toutes les puissances
données, la largeur des cordons diminue avec l'augmentation de la
vitesse de balayage suscitant ainsi l'apparition d'une morphologie de surface
non désirable. En effet, l'augmentation de la vitesse de balayage va
causer une diminution de la densité d'énergie volumique fournie
et donc de la température nécessaire à la fusion du
matériau. Ce qui explique pourquoi à de faible densité
d'énergie volumique (vitesse de balayage élevée) on a un
faible volume de matière fondue qui résulte par une morphologie
de surface indésirable : c'est le régime instable. Ce
régime se produit lorsqu'une certaine vitesse de balayage de 1000 mm/s
(DEV = 21 J/mm3) est dépassée, la forme du cordon
passe d'un régime stable à un régime instable. Lorsqu'on
augmente la puissance, une tendance similaire à celle du cas de 200 W
est observée, à la seule différence que le régime
instable (surface irrégulière et discontinue) apparait pour des
valeurs de DEV plus élevées. Cette apparition de la morphologie
de surface irrégulière à des valeurs de DEV plus
élevées conduit à une augmentation du régime
d'instabilité et donc à un rétrécissement du plan
d'expérience de la conception optimal du cordon. Ce comportement peut
être observé sur la Figure 3.2, qui montre quatre cordons
obtenus à la même valeur de DEV = 21 J/mm3.
49
MASTER II-LABORATOIRE SCIENCES DES
MATÉRIAUX
KOND NGUE PIERRE GÉRARD DAREL
(c)2021
CHAPITRE 3-RÉSULTATS, ANALYSES ET
DISCUSSIONS
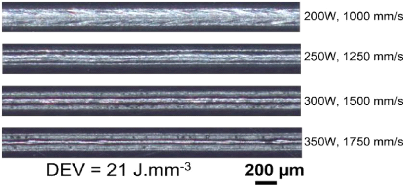
Figure 3-2: Micrographie de cordons
déposés avec la DEV (21 J/mm3) pour différentes valeurs
de puissance et de vitesse de balayage.
Dans toutes les expériences présentées
ici, la formation d'instabilités appelées « Humping »
est due à la fois à la force gravitationnelle et la force
capillaire, mieux connue sous le nom d'instabilité de Rayleigh. Cette
instabilité qui décrit la rupture d'un cylindre liquide par
l'action de la surface et de la force de gravité a été
systématiquement liée à la pression de recul et à
la déformation verticale du bain de fusion. En effet, les forces
capillaires rendent le liquide instable lorsque sa longueur L, dépasse
sa circonférence (K.C. Mills, 2002). En conclusion, la densité
d'énergie volumique nécessaire pour obtenir une morphologie de
surface uniforme et continue doit être supérieure à
21 J/mm3 pour une puissance de 200 W, 31.5
J/mm3 pour les puissances de 250 et 300 W, et 52.5
J/mm3 pour une puissance laser de 350 W respectivement.
La morphologie de surface du bain dépend aussi de la
puissance et de la vitesse de balayage. On constate que le régime
d'instabilité est atteint lorsque des puissances de balayage sont
à 1000 mm/s pour des puissances laser comprises entre 200 et 300 W quel
que soit la DEV utilisée. Ainsi, la densité d'énergie
volumique ne suffit pas pour la caractérisation de la morphologie de
surface d'un cordon.
3.1.2 Effet de la Densité d'Énergie Volumique
sur le régime de fusion
Pendant le processus SLM, les paramètres de
dépôt affectent sévèrement la morphologie de chaque
cordon qui est importante pour le produit final. La figure 3.3 montre la
morphologie des coupes transversales des cordons individuels obtenus sur un
substrat de base Ti6Al4V sans
50
MASTER II-LABORATOIRE SCIENCES DES
MATÉRIAUX
KOND NGUE PIERRE GÉRARD DAREL
(c)2021
CHAPITRE 3-RÉSULTATS, ANALYSES ET
DISCUSSIONS
poudre et avec poudre du même matériau, sous
différentes puissances et vitesses de balayage listées dans le
tableau II.1 avec un diamètre de faisceau focal Ö1=110 um. La
différence de microstructure met en évidence deux zones où
l'on peur clairement observer la zone refondue du bain de fusion. La figure
III.3 montre un total de i pistes nommées Si et Ti pour le substrat et
le cas avec poudre respectivement où i varie de 1 à 20.
À partir de ces deux zones, on peut clairement
identifier une différence de morphologie qui correspond à des
régimes de fusion. Ainsi, on distingue de la figure 3.3 quatre
morphologies qui correspondent aux différents régimes de fusion
:
? Le régime instable appelé « humping
» est caractérisé par un allongement du bain de fusion qui
tend à préférer les instabilités du tableau de
Rayleigh. Ce défaut est causé par les tensions de surface qui
poussent et rétrécissent la masse fondue. On l'observe chez les
cordons S15, S20, T5, T10, T15, T19 et T20.
? Le régime de conduction où la coupe
transversale ressemble à un demi-cercle. Dans ce cas, l'apport
d'énergie est inférieur à une certaine valeur seuil, ce
qui va rendre le régime de conduction prédominant pour le
mécanisme de transfert de chaleur. On observe ce régime chez les
cordons S5, S10, T4.
? Le régime indésirable appelé «
keyhole » où la section transversale est profonde avec une
région supérieure en forme de sablier, tandis que sa partie
inférieure est étroite et ressemble à la forme d'un trou
de serrure. Ce régime est également caractérisé par
la présence de défauts tels que la porosité du trou de
serrure. Il est marqué au niveau des cordons S1/T1, S6/T6, S11/T11 et
S16/T16.
? Le régime de transition qui opère entre le
régime de conduction et le régime keyhole. Dans ce cas,
l'hydrodynamique du bain de fusion est stable, générant une
pénétration de bain plus profonde que le régime de
conduction et aucune porosité de trou de serrure n'est
trouvée.
51
MASTER II-LABORATOIRE SCIENCES DES
MATÉRIAUX
KOND NGUE PIERRE GÉRARD DAREL
(c)2021
CHAPITRE 3-RÉSULTATS, ANALYSES ET
DISCUSSIONS
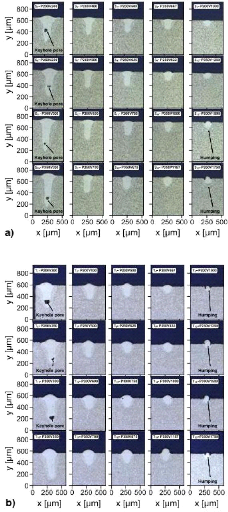
Figure 3-3: Coupes transversales du bain de fusion
sous différentes puissances et vitesses de balayage pour (a) le
substrat et (b) le cas du lit de poudre.
52
MASTER II-LABORATOIRE SCIENCES DES
MATÉRIAUX
KOND NGUE PIERRE GÉRARD DAREL
(c)2021
KOND NGUE PIERRE GÉRARD DAREL
(c)2021
CHAPITRE 3-RÉSULTATS, ANALYSES ET
DISCUSSIONS
La figure 3.3 montre que le régime keyhole apparait
lorsque que la densité d'énergie volumique est supérieure
à 52.5 J/mm3, tandis que le régime de conduction et
humping apparaissent pour des DEV inférieures à 42
J/mm3. Ce résultat n'est pas en accord avec les tendances
observées dans le cas de l'analyse de la morphologie de surface. On
constate que toutes les morphologies de surface en régime humping ne
sont pas identifiées par les coupes transversales. Ce qui signifie que
l'observation d'une coupe transversale seule ne suffit pas pour identifier les
défauts de surface d'un cordon. Donc les analyses micrographiques en
surface permettent d'optimiser la continuité et l'uniformité des
cordons tandis que les analyses de coupes transversales permettent plutôt
d'optimiser la densité du cordon. Ainsi, il est nécessaire
d'utiliser les deux formes d'approches pour optimiser le plan
d'expérience d'un procédé de fabrication SLM.
D'après l'analyse des différentes micrographies ci-dessus (Figure
3.2 et 3.3), on peut dire que pour obtenir des cordons de Ti6Al4V continus,
uniformes et denses, il convient d'utiliser les densités
d'énergie volumique comprises entre 52.6 et 42 J/mm3 pour les
puissances laser inférieures à 300 W et 52.5 J/mm3
pour une puissance de 350 W. Les valeurs 52.6 et 42 J/mm3 sembles
donc être des valeurs seuils permettant de passer d'un régime de
fusion à un autre dans le cas du procédé SLM d'un alliage
de Ti6Al4V.
3.1.3 Seuil des régimes de fusion
Pour identifier avec précision le seuil entre les
régimes de fusion humping, conduction, transition et keyhole,
l'influence de la densité d'énergie, DEV sur les dimensions du
bain de fusion (largeur eapp et profondeur HRZ) a été
évaluée pour le cas du substrat (fig.4a) et le cas du lit de
poudre (fig.4b).
53
MASTER II-LABORATOIRE SCIENCES DES
MATÉRIAUX
KOND NGUE PIERRE GÉRARD DAREL
(c)2021
CHAPITRE 3-RÉSULTATS, ANALYSES ET
DISCUSSIONS
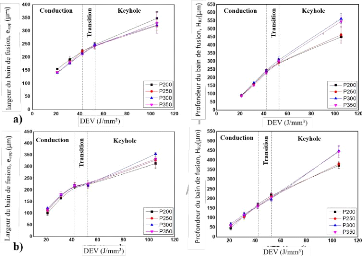
Figure 3-4: Variation des dimensions du bain en
fonction de la densité d'énergie volumique (DEV) pour un (a)
substrat en Ti6Al4V et (b) substrat avec poudre du même
matériau
Il est observé que la largeur et la profondeur
augmentent avec la densité d'énergie pour les deux cas substrat
et lit de poudre, respectivement. En combinant les analyses micrographiques
précédentes avec les points d'inflexions observés dans la
Figure 3.4, il est possible d'identifier les différents régimes
de fusion. Dans le cas du modèle de substrat (Fig.3.4a), le premier
point d'inflexion est la valeur seuille localisée à la
densité d'énergie, DEV de 42 J/mm3. En dessous de
cette valeur, le régime humping et conduction sont prédominants.
Lorsque la DEV est supérieure au second point d'inflexion de 52.2
J/mm3, c'est plutôt le régime de fusion keyhole qui est
prédominant. Le régime de transition mentionné
précédemment se trouve entre les deux points d'inflexions. Ce
résultat confirme bien que les valeurs 42 et 52.2 J/mm3 sont
bien des valeurs seuilles qui permettent de passer du régime conduction
au régime transition et du régime transition au régime
keyhole.
L'aspect de rapport (AR) profondeur/largeur du bain de fusion
a été montré comme un paramètre susceptible
d'être corrélé avec les différents régimes de
fusion. Par exemple, pour le cas de poudre Qi et al. ont
trouvé que lorsque AR < 0.5 on est en régime de conduction, en
régime transition lorsque AR est compris 0.5 et 1.1 et en régime
de keyhole lorsqu'on a 1.1<AR, respectivement. Tenbrock et al.
ont défini pour les aciers inoxydables, qu'il y'a régime
keyhole
54
MASTER II-LABORATOIRE SCIENCES DES
MATÉRIAUX
CHAPITRE 3-RÉSULTATS, ANALYSES ET
DISCUSSIONS
lorsque aspect de rapport est supérieure à 0.8
tandis que la fusion en régime conduction si cet aspect de rapport est
inférieur à 0.8.
D'après la figure 3.5, on observe les mêmes
seuils d'énergie de transition entre les différents
régimes de fusion. Dans le cas du modèle sans poudre, on trouve
que la fusion est en régime keyhole lorsque AR est supérieur
à 1.3, en régime conduction si AR est inférieur à
1.05 et en régime transition lorsqu'il est compris entre 1.05 et 1.3.
Pour le cas avec poudre on trouve que le régime keyhole
est prédominant si AR est supérieur à 1.05, tandis que le
régime conduction prédomine si AR est inférieur à
0.7 et le régime transitoire lorsque AR est compris entre 0.7 et 1.05.
En conclusion, ces valeurs peuvent être utilisées comme
critères permettant d'identifier le régime de fusion en SLM des
alliages de Ti6Al4V. Ces critères permettront de s'affranchir des
analyses métallurgiques qui sont parfois très couteuses.
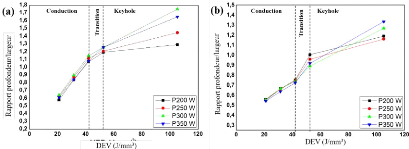
Figure 3-5: Variation de l'aspect rapport
profondeur/largeur du bain en fonction de la densité d'énergie
volumique (DEV) pour un (a) substrat en Ti6Al4V et (b) substrat avec poudre
du même matériau.
Pour discuter de la précision des résultats obtenus
précédemment nous avons réalisé des simulations du
procédé de fabrication avec les modèles numériques
développés au sein de l'entreprise ESI Group à Rungis en
France.
55
MASTER II-LABORATOIRE SCIENCES DES
MATÉRIAUX
KOND NGUE PIERRE GÉRARD DAREL
(c)2021
CHAPITRE 3-RÉSULTATS, ANALYSES ET
DISCUSSIONS
3.1.4 Simulation numérique du bain de fusion
La figure 3.6 montre les résultats de simulation pour
les cordons S16 et T16 où une puissance de faisceau de 350 W et une
vitesse de balayage de 350 mm.s-1 sont appliquées dans le cas
du modèle de substrat et de poudre.
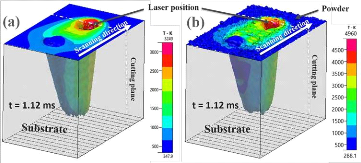
Figure 3-6: Prédiction de la forme d'un
simple cordon obtenu à partir des paramètres d'impression S16
et T16
Dans cette section, notons qu'initialement les calculs
numériques sont effectués avec un coefficient d'absorption
constant de 0.42, issu de la littérature. Dans le cas du modèle
avec poudre, l'état initial du lit de poudre est tiré d'un
modèle DEM (Discret Element Method) et étalé sur le
substrat en vrac, puis les mêmes paramètres laser sont
utilisés pour la simulation de la fusion. Comme on le voit, on observe
une bonne stabilité des pistes. La profondeur du bain de fusion augmente
jusqu'à atteindre un état quasi-stationnaire. La
température maximale localisée varie de 288.1 à 4960 K en
comparaison avec le modèle de substrat qui varie de 347.9 à 3249
K. Comme prévu, le modèle avec poudre nécessite plus
d'énergie que le modèle de substrat car l'énergie de
radiation est moins réfléchie et absorbée par le lit de
poudre de 0.35mm.
Les sections transversales obtenues à partir du plan de
coupe des résultats numériques sont comparées aux
observations expérimentales sur la figure 3.7. Les simulations montrent
qu'une dépression de vapeur (interface métal gaz/liquide) est
créée dans le matériau pendant la fusion laser pour
différentes conditions de traitement. Il est observé qu'une
dépression de vapeur élevée (interface gaz/métal
liquide) conduit à un bain de fusion profond pour former le mode trou de
serrure. Cela confirme que la formation du trou de serrure est principalement
due à une dépression de vapeur qui pénètre dans la
masse de la pièce pendant le processus SLM, comme
56
MASTER II-LABORATOIRE SCIENCES DES
MATÉRIAUX
KOND NGUE PIERRE GÉRARD DAREL
(c)2021
CHAPITRE 3-RÉSULTATS, ANALYSES ET
DISCUSSIONS
prévu. Cependant, une différence est
observée à l'avant du bain de fusion, en particulier pour le mode
prédominant du trou de serrure (Fig. 3.7).
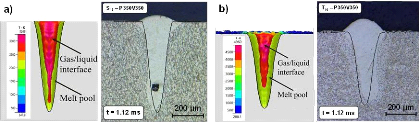
Figure 3-7: Section transversale prédite
d'une piste unique et résultats numériques (ligne noire)
comparés aux observations expérimentales pour (a) le substrat S16
et (b) le lit de
poudre T16.
Concernant les dimensions associées, les largeurs
prédites du bain de fusion sont de 180 (Fig. 3.7a) et 195 um (Fig. 3.7b)
pour les deux pistes S16 et T16 respectivement. Ces résultats sont 45 %
et 30 % inférieurs aux largeurs moyennes du pool de fusion
mesurées expérimentalement de 330 #177; 39 et 280 #177; 10
ìm (Fig. 3.8b). La profondeur prédite du pool de fusion de 533
ìm (Fig. 3.7a) est bien corrélée avec la profondeur
moyenne mesurée expérimentalement de 546 #177; 34 ìm pour
la piste S16 (Fig. 3.7a) tandis que nous pouvons trouver une profondeur
prédite du pool de fusion de 450 ìm (Fig. 3.7b) qui concorde avec
la profondeur moyenne mesurée expérimentalement de 426,75 #177; 8
ìm pour la piste T16. Enfin, on constate que toutes les tailles du pool
de fusion sont bien corrélées avec les résultats
expérimentaux, sauf pour la largeur lorsque la DEV est supérieure
à 45 J.mm-3 dans le cas du modèle de substrat. Dans ce
cas, on peut trouver une différence entre la largeur du bain de fusion
prédite et mesurée. Ces caractéristiques peuvent
être observées à titre d'exemple dans la Fig. 3.8 où
la profondeur et la largeur du bain de fusion mesurées et
prédites sous différentes puissances de faisceau laser et
vitesses de balayage pour le cas du substrat sont comparées.
57
MASTER II-LABORATOIRE SCIENCES DES
MATÉRIAUX
KOND NGUE PIERRE GÉRARD DAREL
(c)2021
CHAPITRE 3-RÉSULTATS, ANALYSES ET
DISCUSSIONS
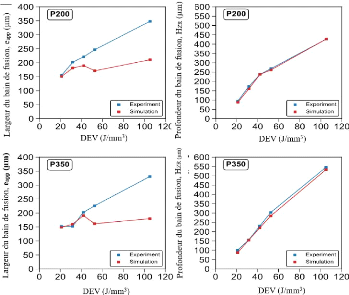
Figure 3-8: Profondeur et largeur du bain de fusion
mesurées et prédites sous différentes puissances de
faisceau laser et vitesses de balayage pour le cas du
substrat.
Pour conclure, sur la base de la comparaison de la forme et
des dimensions du bain de fusion mentionnée précédemment,
il apparaît que toutes les simulations concordent bien avec
l'expérience en ce qui concerne la morphologie et les dimensions pour
les modes de fusion par conduction et par transition. Cependant, pour le mode
de fusion prédominant par trou de serrure, seules la forme et la
profondeur prédites du bassin de fusion correspondent bien à
l'expérience, tandis qu'une différence significative est
observée dans la largeur du bain de fusion. Ces résultats peuvent
être expliqués par le fait que dans le mode de fusion en trou de
serrure, une énergie élevée est engagée,
entraînant un chauffage excessif et localisé du métal qui
provoque la vaporisation des éléments d'alliage et l'apparition
d'une très grande cavité de vapeur ainsi que la présence
d'un plasma dans le liquide [91]. Cette vaporisation intensive du
matériau applique une pression de recul au bain liquide, créant
ainsi une zone de dépression. Avec la formation de cette
dernière, le faisceau laser interagit directement sur le mélange
liquide-vapeur à l'intérieur du bain où se trouve le
capillaire gazeux. Cette interaction complexe liquide-vapeur augmente le
coefficient d'absorption, ce qui entraîne une augmentation de la largeur
du bain de fusion, qui variera davantage que la profondeur, car à une
certaine profondeur, le rayonnement est piégé et devient constant
(proche du corps noir) [92]. Par conséquent, pour corréler la
largeur
58
MASTER II-LABORATOIRE SCIENCES DES
MATÉRIAUX
KOND NGUE PIERRE GÉRARD DAREL
(c)2021
CHAPITRE 3-RÉSULTATS, ANALYSES ET
DISCUSSIONS
prédite du bassin de fusion avec les valeurs
mesurées, une amélioration de la façon dont
l'énergie est distribuée dans le bain de fusion en augmentant le
coefficient d'absorptivité est nécessaire.
Dans cette étude, une estimation du coefficient
d'absorptivité a été proposée numériquement
pour comparer efficacement les mesures expérimentales et la simulation
numérique. Comme le montre la figure 3.9, cette approche permet
d'augmenter le coefficient d'absorption de 0,42 à 0,7.
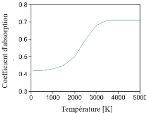
Figure 3-9: Coefficient d'absorption en fonction de
la température pour l'alliage Ti6Al4V
étudié.
La comparaison entre la forme prédite du bain de fusion
en utilisant les nouvelles valeurs calibrées pour l'absorptivité
et l'observation expérimentale est présentée dans la
Figure 3.10
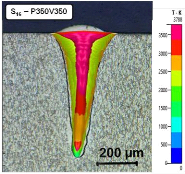
Figure 3-10: Comparaison entre les résultats
numériques et expérimentaux après calibration du
coefficient d'absorption pour la piste S16.
Cette comparaison est obtenue pour le cas du substrat avec la
piste S16. Comme le montre la figure 3.10, un bon accord est obtenu entre le
profil numérique basé sur la variation
59
MASTER II-LABORATOIRE SCIENCES DES
MATÉRIAUX
KOND NGUE PIERRE GÉRARD DAREL
(c)2021
CHAPITRE 3-RÉSULTATS, ANALYSES ET
DISCUSSIONS
de température et le résultat
expérimental (ligne noire) dans le cas du mode de fusion en trou de
serrure. Ce résultat démontre l'importance de prendre en compte
la variation du coefficient d'absorption avec la température pour le
mode de fusion en trou de serrure prédominant afin d'obtenir un bon
accord avec le résultat expérimental. Par conséquent, la
calibration de l'absorptivité est répétée pour les
cas simulés afin d'améliorer tous les résultats.
3.2 Étude De Sensibilité 3.2.1
Introduction
Au cours du procédé de fabrication SLM, un
grand nombre de paramètres gouvernent l'intégrité finale
de la pièce à fabriquer. Les investigations expérimentales
et numériques effectuées précédemment ont permis
d'analyser l'effet de certains paramètres procédés tels
que la puissance laser, la vitesse de balayage et la densité
d'énergie volumique durant le processus de fabrication. Ces analyses ont
permis de définir la paramètrie optimale nécessaire
à l'obtention de cordons stables, continus, uniformes et denses. Par
contre on constate que ces analyses ne considèrent qu'un nombre
très limité de paramètres parmi ceux que compte le
procédé et ne renseignent aucunement sur l'influence de ces
paramètres vis-à-vis du procédé et vis-à-vis
des paramètres considérés. Or la compréhension de
la relation entre ces paramètres et leurs effets sur le processus de
fabrication est crucial la qualité géométrique et physique
des pièces produites.
Grace aux modules Spreading et Melting
développés pour des simulations à l'échelle
microscopique par ESI Group, il est possible d'analyser des indices de
sensibilité qui quantifient l'influences des entrées de ces
modules sur leur sortie simulée : c'est l'analyse ou l'étude de
sensibilité. Elle permettra de mieux comprendre les relations entre
l'entrée et la sortie des variables du modèle
étudié, d'identifier les paramètres qui nécessitent
une meilleure estimation afin de réduire les incertitudes du
modèle, l'identification des phénomènes
prédominants dans le système physique étudié et la
simplification du modèle en fixant les entrées qui n'ont pas
d'effet sur la sortie simulée.
Dans cette section, on présentera l'analyse de
sensibilité du modèle de simulations des procédés
de fabrication additive sur lit de poudre du module melting.
3.2.2 Étude De Sensibilité Du Module
Melting
Nous cherchons à étudier la sensibilité
des paramètres de sortie (taille du bain de fusion) à une
perturbation de chaque paramètre d'entrée. En étudiant
comment la réponse du modèle réagit aux variations de ses
variables d'entrée, l'analyse de sensibilité nous permet de
répondre
60
MASTER II-LABORATOIRE SCIENCES DES
MATÉRIAUX
CHAPITRE 3-RÉSULTATS, ANALYSES ET
DISCUSSIONS
à un certain nombre de questions : le modèle
est-il bien fidèle au phénomène modélisé ?
en effet, si l'analyse exhibe une forte influence d'une variable
d'entrée, habituellement connue comme non influente, il sera
nécessaire de remettre en cause la qualité du modèle ou/et
la véracité de nos connaissances sur l'impact réel de ces
variables d'entrée. C'est l'analyse de sensibilité locale
appelée One-Factor-AT-A-Time qui a été utilisée
dans cette étude. Elle nous renseigne sur l'effet d'une faible
perturbation autour d'une variable d'entrée sur une variable de sortie
simulée. Dans le cas présent la perturbation correspond à
diminuer chaque valeur d'entrée de 10% de sa valeur de
référence initiale. L'analyse de sensibilité est obtenue
à partir du calcul d'un indice de sensibilité simple :
?????? = (??(????) - ??(????????) ) × ( ????????
) (11)
???????? ???? - ????????
Xi représente une variable d'entrée
perturbée c'est-à-dire diminuée de 10% de sa
variable de référence, Xref. Les variables
d'entrée de référence sont indiquées dans le
tableau III.1.
N°
|
Paramètres d'entrée
|
Valeurs
|
N°
|
Paramètres d'entrée
|
Valeurs
|
1
|
Température solide/ liquide [K]
|
1868/1923
|
15
|
Tension de surface [L/m2]
|
2.026
|
2
|
Densité solide [kg/m3]
|
4200
|
16
|
Densité du gaz [kg/m3]
|
0.6
|
3
|
Densité liquide [kg/m3]
|
3900
|
17
|
Viscosité du gaz [mPa.s]
|
2e-5
|
4
|
Conductivité thermique solide [W/m.K]
|
18
|
18
|
Chaleur spécifique du gaz [J/mol.K]
|
1007
|
5
|
Conductivité thermique liquide [W/m.K]
|
34.5
|
19
|
Conductivité thermique gaz [W/m.K]
|
1.7e-2
|
6
|
Chaleur spécifique solide [J/kg.K]
|
650
|
20
|
Power [W]
|
200
|
7
|
Chaleur spécifique liquide [J/kg.K]
|
830
|
21
|
Diamètre du laser [um]
|
60
|
8
|
Chaleur latente de fusion [J/kg.K]
|
32e4
|
22
|
Speed [m/s]
|
1
|
9
|
Chaleur latente solide [J/kg]
|
28.6e4
|
23
|
Épaisseur de couche [m]
|
0.12e-3
|
10
|
Chaleur latente liquide [J/kg.K]
|
97e5
|
|
|
|
11
|
Émissivité liquide
|
0.4
|
|
|
|
12
|
Émissivité solide
|
0.6
|
|
|
|
13
|
Coefficient absorption solide
|
0.2
|
|
|
|
14
|
Coefficient d'absorption liquide
|
0.2
|
|
|
|
Tableau 3-1: Données d'entrée
considérée comme valeur de
référence
Après simulation, on obtient une variable de sortie de
référence Y(Xref) correspondant
aux variables d'entrée de référence. Dans
notre cas les variables de sortie de référence sont la largeur et
la profondeur du bain de fusion puisque la longueur du bain présente une
instabilité
61
MASTER II-LABORATOIRE SCIENCES DES
MATÉRIAUX
KOND NGUE PIERRE GÉRARD DAREL
(c)2021
KOND NGUE PIERRE GÉRARD DAREL
(c)2021
CHAPITRE 3-RÉSULTATS, ANALYSES ET
DISCUSSIONS
importante. La figure 3.12 montre l'effet de la perturbation
d'une variable d'entrée sur la profondeur du bain de fusion à
l'instant t=0.0003s (Figure 3.11).
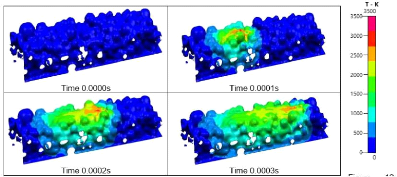
Figure 3-11: Cas P = 200 W, V = 1000 mm/s -
interface métal / gaz - contours de
température (K)
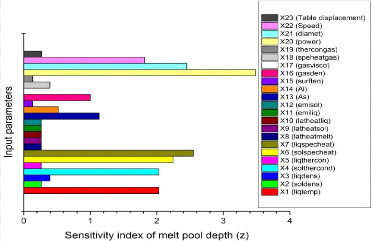
Figure 3-12: Indice de sensibilité sur la
profondeur du bain de fusion
La température du liquidus ou solidus (X1), la
conductivité thermique solide (X4), la chaleur spécifique solide
(X6) et liquide (X7), la puissance, la vitesse et le diamètre du laser
sont des variables qui contribuent le plus à la variabilité de la
profondeur du bain de fusion. Ainsi la variabilité de la profondeur du
bain de fusion pourra être diminuée en concentrant les efforts sur
la réduction de la variabilité de ces entrées les plus
influentes. Il doit être précisé que
62
MASTER II-LABORATOIRE SCIENCES DES
MATÉRIAUX
KOND NGUE PIERRE GÉRARD DAREL
(c)2021
CHAPITRE 3-RÉSULTATS, ANALYSES ET
DISCUSSIONS
cela n'est pas toujours possible, notamment lorsque la
variabilité d'une variable d'entrée est intrinsèque
à la nature de la variable et non due à un manque d'information
ou à des imprécisions de mesures. Certaines variables
d'entrée semblent au contraire moins influentes. On pourrait supprimer
les variables qui n'ont aucune influence tel que la viscosité du gaz
(X17), et obtenir ainsi un modèle plus léger avec moins de
variables d'entrée qui n'ont aucune influence. L'analyse étant
locale, il n'est pratiquement pas possible de connaitre quelles variables, ou
quels groupes de variables, interagissent entre eux.
Pour le cas de la largeur du bain de fusion, les
paramètres d'entrée ayant un indice de sensibilité plus
important sont la température du liquidus ou solidus (X1), la
conductivité thermique solide (X4), la chaleur spécifique solide
(X6) et liquide (X7), la puissance, la vitesse et la hauteur de poudre
(Figure 3.13). Ainsi la variabilité de la largeur du
bain de fusion pourra être diminuée en réduisant la
variabilité de ces entrées les plus influentes. Comme dans le cas
précédent, afin d'obtenir un modèle plus léger avec
moins de variables d'entrée, on pourrait supprimer les variables qui
n'ont aucune influence sur cette réponse du modèle tel que les
tensions de surface (X15), la densité du gaz (X16), la viscosité
du gaz (X17) et la chaleur spécifique du gaz (X18).
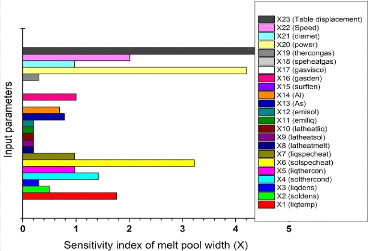
Figure 3-13: Indice de sensibilité de la
largeur du bain de fusion.
Il est possible que la modification d'une variable
d'entrée la plus influente pour diminuer les incertitudes n'influe pas
seulement sur une variable de sortie mais plutôt sur
63
MASTER II-LABORATOIRE SCIENCES DES
MATÉRIAUX
KOND NGUE PIERRE GÉRARD DAREL
(c)2021
CHAPITRE 3-RÉSULTATS, ANALYSES ET
DISCUSSIONS
plusieurs variables de sortie. Dans ce cas il n'est pas
recommandé de s'aventurer à l'analyse de sensibilité
présentée précédemment. Dans une telle situation,
on pourrait effectuer une analyse de sensibilité spatiale. La
Figure 3.14 illustre l'analyse de sensibilité spatiale dans le
cas de notre modèle.
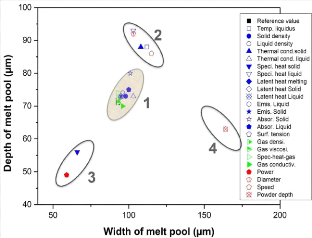
Figure 3-14: Analyse de sensibilité des
réponses du modèle.
Les données d'entrée sont
différenciées par couleur : bleue pour les
propriétés du matériau, verte pour les
propriétés du gaz et rouge les paramètres du
procédé. Le domaine 1 ou zone 1 est constitué des
variables qui entrainent une faible variabilité des réponses du
modèle. On constate que les propriétés du gaz et quelques
propriétés matériau influent moins les réponses du
modèle. Les zones 2, 3 et 4 représentent les variabilités
importantes du modèle. On peut noter que les paramètres
procédés (hauteur de poudre, vitesse, puissance et
diamètre du laser) sont des variables d'entrée qui contribuent le
plus à la variabilité du couple profondeur-largeur du bain de
fusion. Ce résultat est en accord avec les travaux publiés dans
la littérature. On observe que la variabilité de la profondeur du
bain est plus importante pour les données d'entrée de la zone 2
tandis que celles de la zone 4 influent plus la largeur du bain de fusion. La
variabilité de la hauteur et la largeur du bain de fusion est
plutôt décroissante pour les données d'entrée de la
zone 3.
64
MASTER II-LABORATOIRE SCIENCES DES
MATÉRIAUX
KOND NGUE PIERRE GÉRARD DAREL
(c)2021
CHAPITRE 3-RÉSULTATS, ANALYSES ET
DISCUSSIONS
3.3 Conclusion
Ce chapitre a mis en évidence expérimentalement
et numériquement l'influence des certains paramètres
procédés tels que la puissance laser, la vitesse de balayage et
la densité d'énergie volumique sur la morphologie en surface et
en profondeur de cordons au cours du procédé SLM. Les analyses
effectuées ont permis de définir la paramètrie
nécessaire à l'obtention de cordons continus, uniformes, stables
et denses.
Par la suite, une étude de sensibilité sur le
module des paramètres de sortie (taille du bain) à une
perturbation de chaque paramètre d'entrée a été
effectuée sur le module melting développé par ESI Group.
Il en découle que les paramètres procédés sont ceux
qui ont le plus d'influence sur la variabilité des réponses du
modèle.
65
MASTER II-LABORATOIRE SCIENCES DES
MATÉRIAUX
KOND NGUE PIERRE GÉRARD DAREL
(c)2021
CONCLUSION GÉNÉRALE ET PERSPECTIVES
CONCLUSION GÉNÉRALE ET PERSPECTIVES
Le procédé de fusion laser sélective,
appartenant à la famille de la fabrication additive, présente de
nombreux avantages (flexibilité géométrique,...) mais
aussi quelques inconvénients, comme l'état de surface des
pièces construites, qui doit être amélioré. Une
bonne maîtrise et compréhension du procédé est
importante afin d'augmenter la qualité des pièces construites.
Puisque le procédé SLM est gouverné par
un grand nombre de paramètres dits paramètres
procédés et qu'une pièce obtenue par ce
procédé représente plusieurs centaines de mètres de
cordons, les objectifs de cette étude étaient d'analyser et de
simuler l'influence de certains paramètres procédés tels
que la puissance laser, la vitesse de balayage et la densité
d'énergie volumique lors de la fusion du lit de poudre afin de mieux les
quantifier, avant de faire une analyse de sensibilité. Pour cette
étude, le principal matériau utilisé est l'alliage de
Titane Ti6Al4V.
L'étude de bibliographie dont le premier chapitre fait
l'objet a mis en évidence certaines notions essentielles de la
fabrication additive telles son principe, ses avantages, ses limites, ses
domaines d'applications. Un état d'art a également
été consacré à une étude comparative entre
la fabrication additive et les méthodes de fabrication conventionnelles
telles que les méthodes soustractive et formative avant de
présenter les différents procédés appartenant
à la famille de fabrication additive et plus spécifiquement le
procédé de fusion sélective par laser ou SLM (Selective
Layer Melting).
Le chapitre 2 a porté sur la présentation des
différents travaux numériques et expérimentaux
menés au cours de cette étude.
? Les travaux expérimentaux
ont consisté grâce à une machine de fusion sur lit de
poudre Concept Laser M2 Dual à fabriquer des cordons
unitaires sous différents paramètres de puissance laser et de
vitesse de balayage comme décrit par le tableau 2.1 dans le but
d'étudier l'influence des paramètres considéré sur
la morphologie en surface des pièces obtenues en SLM. Ces
paramètres ont été choisi de manière à
obtenir des plages similaires en terme de densité d'énergie
volumique du laser (Équation 1). Au cours de ces travaux, deux cas ont
été envisagé : celui du substrat sans lit de poudre et
celui du substrat avec lit de
66
MASTER II-LABORATOIRE SCIENCES DES
MATÉRIAUX
KOND NGUE PIERRE GÉRARD DAREL
(c)2021
CONCLUSION GÉNÉRALE ET PERSPECTIVES
poudre fait à partir de l'alliage de Ti6Al4V. Ainsi
pour chacun de ces cas, un total de 24 cordons unitaires a été
réalisé.
V' Les travaux numériques ont porté sur la
simulation du procédé SLM avec pour objectif principal
d'étudier l'influence des caractéristiques du processus telles
que la puissance laser, la vitesse de balayage et la densité
d'énergie volumique afin d'améliorer la compréhension de
ce procédé de fabrication. Pour ces études de simulation,
le module melting (module de fusion) de fabrication additive EST du fournisseur
de logiciel commercial EST Group a été utilisé. L'approche
numérique s'est basée sur la méthode de la dynamique des
fluides computationnelle (DFC) pour résoudre les différentes
équations fondamentales qui régissent les différents
phénomènes physiques qui ont lieu au cours de la fusion du lit de
poudre. Par la suite un solveur DEM (Discret Element Method) a
été utilisé pour simuler le processus d'étalement
d'une poudre Ti6Al4V sur une table de déplacement qui sera
utilisé comme entrée pour la simulation de fusion.
Dans le chapitre III, consacré d'une part aux
investigations expérimentales et numériques de l'interaction
laser-poudre-zone fondue en SLM, nous avons pu caractériser et
quantifier : (1) l'effet des paramètres procédés sur la
morphologie de surface d'un cordon, (2) l'effet des paramètres
procédés sur le régime de fusion, et (3) le seuil des
régimes de fusion. Pour chacune de ces analyses, il en est ressorti les
observations suivantes :
V' Pour toutes les puissances données, la largeur des
cordons diminue avec l'augmentation de la vitesse de balayage ceci pouvant
s'expliquer par le fait que l'augmentation de la vitesse de balayage va causer
une diminution de la densité d'énergie volumique fournie et donc
de la température nécessaire à la fusion du
matériau. Cette augmentation de la vitesse de balayage sera à
l'origine de morphologie non désirable marqué par des
instabilités appelées « Humping » (Figure 3.1). Un
faisceau laser balayant à faible vitesse la surface d'un matériau
produit un bain liquide de forme approximativement hémisphérique,
qui prend une forme plus allongée à haute vitesse.
V' La densité d'énergie volumique à elle
seule ne suffit pas à la caractérisation de la morphologie de
surface d'un cordon. Elle dépend aussi bien de la puissance laser et de
la vitesse de balayage (Figure 3.2).
V' Les coupes transversales (Figure 3.3) montrent qu'au cours
du procédé SLM, quatre régimes de fusion sont
observés : le régime instable appelé « Humping
»,
67
MASTER II-LABORATOIRE SCIENCES DES
MATÉRIAUX
KOND NGUE PIERRE GÉRARD DAREL
(c)2021
CONCLUSION GÉNÉRALE ET PERSPECTIVES
le régime de conduction, le régime
indésirable appelé « Keyhole » et le régime
transitoire.
V' L'aspect de rapport (AR)
profondeur/largeur du bain de fusion a été montré comme un
paramètre susceptible d'être corrélé avec les
différents régimes de fusion (Figure 3.4).
Fort de ce qui précède, il en découle que
les analyses micrographiques en surface permettent d'optimiser la
continuité et l'uniformité des cordons tandis que les analyses de
coupe transversales permettent plutôt d'optimiser la densité du
cordon. Ainsi, il est nécessaire d'utiliser les deux formes d'approches
pour optimiser le plan d'expérience d'un procédé de
fabrication SLM. Largeur et profondeur de pénétration du bain de
fusion sont les caractéristiques géométriques les plus
importantes pour obtenir des pièces denses car leurs dimensions doivent
être suffisantes pour permettre le chevauchement des cordons et la
liaison des couches successives entre elles. En comparant les résultats
numériques et expérimentaux, une corrélation plutôt
satisfaisante est observée. Les valeurs numériques de la largeur
et de la profondeur du bain de fusion se trouvent bien dans la gamme des
valeurs du domaine expérimental correspondant. La méthode
d'analyse numérique proposée semble donc adaptée pour
fournir une bonne prédiction des dimensions du bain de fusion. La
profondeur du bain de fusion et sa largeur sont inversement proportionnelles
à la vitesse de balayage effective du laser. Les dimensions du bain de
fusion diminuent avec l'augmentation de la vitesse de balayage
(c'est-à-dire la diminution de la durée d'exposition). Le temps
d'exposition du faisceau laser affecte la quantité d'énergie
transférée au matériau. Ce paramètre est donc un
facteur important pour obtenir une fusion complète du matériau.
Les observations faites dans notre cas (alliage de Titane Ti6Al4V)
correspondent aux conclusions tirées par Antony et al. [70] lors
de la fusion d'une poudre d'acier inoxydable 316L.
D'autre part, le chapitre III a également
été consacré à l'analyse de sensibilité des
paramètres procédés grâce au module melting
développé par ESI Group. Elle consiste en une analyse des indices
de sensibilité qui quantifient l'influence des entrées du module
sur leur sortie simulée. Cette analyse considèrera comme indice
de sensibilité la profondeur et la largeur du bain de fusion pour le cas
d'espèce présent. Il en découle les conclusions suivantes
:
V' La température du liquidus
ou solidus (X1), la conductivité thermique solide (X4), la chaleur
spécifique solide (X6) et liquide (X7), la puissance, la vitesse et le
diamètre du laser sont des variables qui contribuent le plus à la
variabilité de la profondeur du bain de fusion (Figure 3.12).
68
MASTER II-LABORATOIRE SCIENCES DES
MATÉRIAUX
KOND NGUE PIERRE GÉRARD DAREL
(c)2021
CONCLUSION GÉNÉRALE ET PERSPECTIVES
? Pour le cas de la largeur du bain de fusion, les
paramètres d'entrée ayant un indice de sensibilité plus
important sont la température du liquidus ou solidus (X1), la
conductivité thermique solide (X4), la chaleur spécifique solide
(X6) et liquide (X7), la puissance, la vitesse et la hauteur de poudre
(Figure 3.13).
De cette étude il est clair que les paramètres
procédés sont ceux qui ont le plus d'influence sur la
variabilité des réponses du module melting (Figure 3.14). Ainsi
une connaissance des données d'entrées importantes ou
négligeable permettrons d'améliorer le module de fusion.
Ce travail constitue donc une étape dans l'étude
et la modélisation des phénomènes physiques intervenant
lors de l'interaction d'un faisceau laser avec la matière en SLM en
considérant le rôle des paramètres procédés.
Il a permis de fournir des éléments de réponse sur
l'influence de la vitesse de balayage, la puissance laser et la densité
d'énergie volumique sur la caractérisation dimensionnelle
(largeur et profondeur du bain de fusion) des cordons obtenus par SLM. Une
amélioration du modèle et la mise en place d'autres
caractérisations expérimentales peuvent être entrevues
à travers une étude plus approfondie de l'aspect rapport
profondeur/largeur du bain de fusion qui permettra peut-être de trouver
une valeur optimale de ce paramètre pour un objectif principal et commun
à toutes les recherches autour du procédé SLM, celui de
l'amélioration de la qualité des pièces fabriquées
avec ce procédé.
69
MASTER II-LABORATOIRE SCIENCES DES
MATÉRIAUX
KOND NGUE PIERRE GÉRARD DAREL
(c)2021
RÉFÉRENCES
RÉFÉRENCES
[1] AFNOR. Fabrication additive-Vocabulaire, NF E
67-001,2011.
[2] A.F. Obaton, A. Bernard, G. Taillandier et J.M.
Moschetta, "fabrication additive : état de l'art et besoins
métrologiques engendrés", Revue française de
métrologie, pp. 21-36,2015.
[3] P. Dubois, A. Aoussat et R. Duchamp,
"Généralités, Techniques de l'Ingénieur", BM7017,
10/04/2000.
[4] P. Alfred, P. Ciraud. "Verfahren und Vorrichtung zur
Herstellung beliebiger Gegenstände aus beliebigem schmelzbarem Material".
German patent application, DE 2263777, July 5th 1973.
[5] J.C. André, A. Le Méhauté, O. De
Witte, "Dispositif pour réaliser un modèle de pièce
industrielle", Brevet français 2567668, Juillet 1984.
[6] C.W. Hull, «Apparatus for production of
three-dimensional objects by stereolithography», US Patent 4575330, Mars
1986.
[7] T. Wohlers and T. Gornet, «History of additive
manufacturing», pp. 12-21, In Wohlers Report 2012, 2012.
[8] L. Sexton, S. Lavin, G. Byrne, A. Kennedy,
«Laser cladding of aerospace materials», Journal of Materials
Processing Technology, pp. 63-68, Vol. 122, 2002.
[9] M. Kerschbaumer, G. Ernst, P. O'Leary, «Tool
path generation for 5-Axis laser cladding, in Proceedings of the Fourth Laser
Assisted Net Shape Engineering», Vol. 2, pp. 831-842, September
2004.
[10] M. Tomlin, J. Meyer, «Topology optimization of
an additive layer manufactured (ALM) Aerospace Part», the 7th Altair CAE
Technology conference, 2011.
[11] J.M. Williams, A.A. dewunmi, R.M. Schek, C.L.
Flanagan, P.H. Krebsbach, S.E. Feinberg, S.J. Hollister, S. Das, «Bone
tissue engineering using polycaprolactone scaffolds fabricated via selective
laser sintering, Biomaterials», Vol. 26, pp. 4817- 4827,2005.
[12] P. Bartolo, J.P. Kruth, J. Silva, G. Levy, A.
Malshe, K. Rajurkar, M. Mitsuishi, J. Ciurana, M. Leu, «Biomedical
production of implants by additive electro-chemical and physical
processes», CIRP Annals - Manufacturing Technology, Vol. 61, pp.
635-655,2012.
[13] J. Parthasarathy, B. Starly, S. Raman, «A
design for the additive manufacture of functionally graded porous structures
with tailored mechanical properties for
70
MASTER II-LABORATOIRE SCIENCES DES
MATÉRIAUX
KOND NGUE PIERRE GÉRARD DAREL
(c)2021
RÉFÉRENCES
biomedical applications», Journal of Manufacturing
Processes. Vol.13. pp.160-170. August 2011.
[14] V. Manoharan, S.M. Chou, S. Forrester, G.B. Chai,
P.W. Kong, «Application of additive manufacturing techniques in sports
footwear, Virtual and Physical Prototyping», pp. 249-252, April
2013.
[15] AFNOR, NF ISO / ASTM 52900 "Fabrication additive --
Principes généraux -- Terminologie", 2016.
[16] L.E. Rännar, A. Glad, and G.C. Gustafson,
«Efficient cooling with tool inserts manufactured by electron beam
melting,» Rapid Prototyp. J., vol. 13, no. 3, pp. 128-135, 2007.
[17] R. Rezaie, M. Badrossamay, A. Ghaie, and H. Moosavi,
«Topology Optimization for Fused Deposition Modeling Process,»
Procedia CIRP, vol. 6, pp. 521-526, Jan. 2013.
[18] B. Vayre, F. Vignat, and F. Villeneuve,
«Designing for Additive Manufacturing,» Procedia CIRP, vol. 3, pp.
632-637, Jan. 2012.
[19] M. Tomlin and J. Meyer, «Topology Optimization
of an Additive Layer Manufactured (ALM) Aerospace Part,» in The 7th Altair
CAE Technology Conference, Gaydon, UK, 10th May, 2011.
[20] G.A.O. Adam and D. Zimmer, «Design for Additive
Manufacturing--Element transitions and aggregated structures,» CIRP J.
Manuf. Sci. Technol., vol. 7, no. 1, pp. 20-28, Jan. 2014.
[21] P. Reeves, «Additive Manufacturing - A supply
chain wide response to economic uncertainty and environmental
sustainability,» Econolyst Limited, Silversmiths, Crown Yard, Wirksworth,
Derbyshire, DE4 4ET, UK, 2009.
[22] R. Becker, A. Grzesiak, and A. Henning,
«Rethink assembly design,» Assem. Autom., vol. 25, no. 4, pp.
262-266, 2005.
[23] H. Galarraga, D.A. Lados, R.R. Dehoff, M.M. Kirka,
and P. Nandwana, «Effects of the microstructure and porosity on properties
of Ti-6Al-4V ELI alloy fabricated by electron beam melting (EBM),» Addit.
Manuf., vol. 10, pp. 47-57, 2016.
[24] L. Löber, C. Flache, R. Petters, U. Kühn,
and J. Eckert, «Comparison of different post processing technologies for
SLM generated 316l steel parts,» Rapid Prototype. J., vol. 19, no. 3, pp.
173-179, 2013.
[25] B. Vayre, F. Vignat, and F. Villeneuve,
«Identification on Some Design Key Parameters for Additive Manufacturing:
Application on Electron Beam Melting,» Procedia CIRP, vol. 7, pp. 264-269,
Jan. 2013.
[26] Fabrication Additive VS Fabrication Soustractive:
https://www.3dz.fr/fabrication-additive-ou-soustractive.
71
MASTER II-LABORATOIRE SCIENCES DES
MATÉRIAUX
KOND NGUE PIERRE GÉRARD DAREL
(c)2021
RÉFÉRENCES
[27] Fabrication Additive VS Fabrication Soustractive:
https://techso.ca/la-fabrication-additive-et-soustractive.
[28] Formative Manufacturing:
https://meltcollective.com/project/tool-library/formative-fabbrication.
[29] Fabrication Formative:
https://fr.slideshare.net/MonarchMetal/how-common-manfacturing-methode-compare.
[30] B.P. Conner, G.P. Manogharan, A.N. Martof, L.M.
Rodomsky, C.M. Rodomsky, D.C. Jordan, and J.W. Limperos, «Making sense of
3-D printing: Creating a map of additive manufacturing products and
services,» Addit. Manuf., vol. 1-4, pp. 64-76, 2014.
[31] N. Guo & M.C. Leu «Additive manufacturing:
Technology, applications and research needs». Frontiers of Mechanical
Engineering Front. Mech. Eng., 8(3), 215-243, 2013.
[32] A. Stwora & G. Skrabalak, «Influence of
selected parameters of Selective Laser Sintering process on properties of
sintered materials». Journal of Achievements in Materials and
Manufacturing Engineering, 61(2), 375-380, 2013.
[33] 3D Printing Electronics Laser Additive Manufacturing
Systems. (n.d.). Retrieved May 19, 2016, from
http://www.optomec.com
[34] J. Gausemeier, N. Echterhoff, M. Kokoschka & M.
Wall,» Thinking ahead the Future of Additive Manufacturing - Analysis of
Promising Industries». DMRC study, Paderborn, 2011.
[35] J.P. Swensen, L.U. Odhner, B. Araki & A.M. Dollar,
«Printing Three-Dimensional Electrical Traces in Additive Manufactured
Parts for Injection of Low Melting Temperature Metals». Journal of
Mechanisms and Robotics, 7(2), 021004, 2015.
[36] J.M. Chua, «Are 3D-Printed Fabrics the Future of
Sustainable Textiles». Ecouter re, 2010.
[37] L. Ingham. (2014, November 20). In Pictures: 3D printed
art showcases incredible possibilities of additive manufacturing - Factor.
Retrieved May 19, 2016, from
http://factor-tech.com/3d-printing/9685-in-pictures-3d-printed-art-showcases-incredible-possibilities-of-additive-manufacturing/.
[38] Wohlers report 2017
[39] NF ISO, «NF ISO 17296-2 Fabrication additive -
Principes généraux - Partie 2 : Vue d'ensemble des
catégories de procédés et des matériaux de
base.» 2015.
[40] J.C. André, A. Le Méhauté & O.
de Witte, «Dispositif pour réaliser un modèle de
pièce industrielle,» 25676681984.
[41] C.W. Hull, «Apparatus for production of
three-dimensional ojects by stereolithography,» US Patent
4,575,330,1986.
72
MASTER II-LABORATOIRE SCIENCES DES
MATÉRIAUX
KOND NGUE PIERRE GÉRARD DAREL
(c)2021
RÉFÉRENCES
[42] F. Laverne, F. Segonds & P. Dubois, "Fabrication
additive : Principes généraux", Techniques de L'ingénieur,
1-15, 2016.
[43] T.T. Wohlers, «Wohlers Report 2013: Additive
Manufacturing and 3D Printing State of the Industry: Annual Worldwide Progress
Report,» Fort Cllins, CO: Wohlers Associates, Inc, 2011.
[44] Moulage à cire perdue : du modèle
à la pièce, B. Anglade, H. Horsin Molinaro, F. Ventura, ressource
Culture Sciences de l'Ingénieur,
http://eduscol.education.fr/sti/si-ens-paris-saclay/ressources_pedagogiques/moulage-cire-perdue-du-modele-ala-piece.
[45]
http://www.maxisciences.com/imprimante-3d/un-robot-va-imprimer-en-3d-un-pont-en-acier-au-dessus-d-un-canal-d-amsterdam
art35128.html.
[46] Stratasys, «Stratasys Design Series.»
[Online]. Available:
http://www.stratasys.com/3dprinters/design-series/connex-systems.
[47] Du prototypage rapide à la fabrication additive
- Cours de Bruce Anglade, ENS Paris-Saclay.
[48] S.S Crump, «Apparatus and method for creating
three-dimensional objects,»US Patent 5,121,329, 1992.
[49] K.P. Karunakaran, A. Bernard, S. Suryakumar, L.
Dembinski, and G. Taillandier, «Rapid manufacturing of metallic
objects,» Rapid Prototyp. J., vol. 18, no. 4, pp. 264-280, 2012.
[50] Impression 3D : procédé de fusion sur lit
de poudre, D. Comberton, N. Muller, ressource
Culture Sciences de l'Ingénieur,
http://eduscol.education.fr/sti/si-ens-paris- saclay/ressources_pedagogiques/impression-3d-procede-de-fusion-sur-lit-de-poudre
[51] Moulage à cire perdue : du modèle
à la pièce, B. Anglade, H. Horsin Molinaro, F. Ventura, ressource
Culture Sciences de l'Ingénieur,
http://eduscol.education.fr/sti/si-ens-paris-saclay/ressources_pedagogiques/moulage-cire-perdue-du-modele-ala-piece
[52] J. Fréchard and E. Laubriat, «CLAD Process
to build and repair aeronautic parts,» in AEFA, 2015.
[53] P. Muller, «Fabrication Additive de pièces
multimatériaux,» 2013.
[54] K. M. Taminger and R. A. Hafley, «Electron Beam
Freeform Fabrication (EBF3) for Cost Effective Near-Net Shape
Manufacturing,» 2006.
[55] F. Hild, H.H. Molinaro, S. Roux "La tomographie en
sciences et mécanique des matériaux : voyage au centre de la
matière", ressource Culture Sciences de l'Ingénieur,
http://eduscol.education.fr/sti/si-ens-cachan/ressources_pedagogiques/la-tomographie-en-sciences-et-mecanique-des-materiaux
73
MASTER II-LABORATOIRE SCIENCES DES
MATÉRIAUX
KOND NGUE PIERRE GÉRARD DAREL
(c)2021
RÉFÉRENCES
[56] Introduction of SLM process. (n.d.). Retrieved
from
http://www.birmingham.ac.uk/Documents/college
-eps/irc/amp-lab/SLM.pdf
[57] G. Dongdong, «Laser Additive Manufacturing of
High -Performance Materials», Springer-Verlag Berlin Heidelberg
2015.
[58] N.T. Aboulkhair, N.M. Everitt, I. Ashcroft & C.
Tuck, "Reducing porosity in AlSi10Mg parts processed by selective laser
melting». Additive Manufacturing, 1-4, 77-86, 2014.
[59] T. Kurzynowski, E. Chlebus, B. Ku·nicka &
J. Reiner, «Parameters in selective laser melting for processing metallic
powders». High Power Laser Materials Processing: Lasers, Beam Delivery,
Diagnostics, and Applications 8239, 317-322, 2012.
[60] L.V. Belle, "Analyse, modélisation et
simulation de l'apparition de contraintes en fusion laser métallique",
Mechanics of the solides, INSA de Lyon, France, 2013.
[61]
https://accsimia-software.com/fabrication-additive
[62] Modélisation des procédés de
fabrication additive,
https://www.ec2-modelisation.fr
[63] S. Jedid, «La simulation numérique au
service de la fabrication additive SLM», ressource Metalblog,
https://metalblog.ctif.com/2018/06/25/la-simulation-de-la-fabrication-additve-slm/,
2018
[64] A.V. Gusarov, I. Smurov, «Two-dimensional
numerical modelling of radiation transfer in powder beds at selective laser
melting», Applied Surface Science 255, 5595-5599, 2009.
[65] A.V. Gusarov, I. Smurov, «Modelling the
interaction of laser radiation with powder bed at selective laser
melting», Physics Procedia, pp. 381-394, 2010.
[66] A.V. Gusarov, I. Yadroitsev, Ph. Bertrand, I.
Smurov, «Model of Radiation and Heat Transfer in Laser-Powder Interaction
Zone at Selective Laser Melting», Journal of Heat Transfer, Vol. 131, no
7, 2009.
[67] F. Verhaeghe, T. Craeghs, J. Heulens, L. Pandelaers,
«A pragmatic model for selective laser melting with evaporation»,
Acta Materialia, Vol. 57, no 20 6006 6012,2009.
[68] D. Dai, D. Gu, «Thermal behavior and
densification mechanism during selective laser melting of copper matrix
composites: Simulation and experiments», Materials & Design, pp.
482-491, Vol. 55, 2014.
[69] S.A. Khairallah, A. Anderson, «Mesoscopic
simulation model of selective laser melting of stainless steel powder»,
Journal of Materials Processing Technology, Vol. 214, no11, 2627 36.
2014.
74
MASTER II-LABORATOIRE SCIENCES DES
MATÉRIAUX
KOND NGUE PIERRE GÉRARD DAREL
(c)2021
KOND NGUE PIERRE GÉRARD DAREL
(c)2021
RÉFÉRENCES
[70] K. Antony, N. Arivazhagan, K. Senthilkumaran,
«Numerical and experimental investigations on laser melting of stainless
steel 316L metal powders», Journal of Manufacturing Processes 16,no 3,345
55, 2014.
[71] B. Zhang, H. Liao, C. Coddet, «Microstructure
evolution and density behavior of CP Ti parts elaborated by Self-developed
vacuum selective laser melting system», Applied Surface Science
279,310-316, 2013.
[72] C. Tix, G. Simon, «A transport theoretical
model of the keyhole plasma in penetration laser welding» J. Phys. D:
Appl. Phys. 26, 2066-2074, 1993.
[73] R.B. Bird, W.E. Stewart, E.N. Lightfoot,
«Transport phenomena», New York: John Wiley & Sons. p 780,
1960.
[74] R. Ansorge, T. Sonar, «Mathematical models of
fluid dynamics: modeling, theory, basic numerical fact-an introduction»,
John Wiley & Sons, 2009
[75] P.W. Fuerschbach, J.T. Norris, X. He, T. DebRoy,
«Understanding metal vaporization from laser welding», Sandia
National Laboratories Report No.: SAND2003-3490, 2003.
[76] D. Bäuerle, «Laser processing and
chemistry», Springer Verlag, 2011.
[77] J. Trapp, A.M. Rubenchik, G. Guss, et al., «In
situ absorptivity measurements of metallic powders during laser powder-bed
fusion additive manufacturing», Appl. Mater.Today 9, 341-349,
2017.
[78] C. Tang, J.L. Tan, C.H. Wong, «A numerical
investigation on the physical mechanisms of single-track defects in selective
laser melting», Int. J. Heat Mass Transf.126 ,957-968, 2018.
[79] P.A. Hooper, «Melt pool temperature and cooling
rates in laser powder bed fusion». Additive Manufacturing, 22, 548-559,
2018.
[80] S.A. Khairallah, A.T. Anderson, A. Rubenchik, W.E.
King,» Laser powder-bed fusion additive manufacturing: Physics of complex
melt flow and formation mechanisms of pores, spatter, and denudation
zones», Acta Mater., 108, 36-45, 2016.
[81] M.J. Matthews, G. Guss, S.A. Khairallah, A.M.
Rubenchik, P.J. Depond, W.E. King, "Denudation of metal powder layers in laser
powder bed fusion processes» Acta Mater., 114 (Supplement C), 33-42,
2016.
[82] K.H. Leitz, P. Singer, A. Plankensteiner, B.
Tabernig, H. Kestler, L.S. Sigl, «Thermo-Fluiddynamical Modelling of Laser
Beam-Matter Interaction in Selective Laser Melting». Proceedings of the
2016 COMSOL Conference in Munich.
[83] T. Moscicki, J. Hoffman, Z. Szymanski,
«Modelling of plasma formation during nanosecond laser ablation».
Arch. Mech., 63 (2), 99-116, 2011.
75
MASTER II-LABORATOIRE SCIENCES DES
MATÉRIAUX
RÉFÉRENCES
[84] S. Schiller, U. Heisig and S. Panzer, «Electron
Beam Technology» John Wiley & Sons, 1982.
[85] E.A. Brandes. «Keyhole modeling during laser
welding». Journal of applied physics and Brook G B (ed) 1992 Smithells
Metals Reference Book 7th edn (Boston, MA: Butterworth- Heinemann)
[86] E.T. Turkdogan «Physical Chemistry of High
Temperature Technology» New York: Academic, 1980.
[87] C.Y. Ho, P.E. Liley and R.W. Power, «Thermal
Conductivity of Selected Materials Part 2» National Bureau of Standards
National Standard Reference Data Series: No 16, 1968.
[88] D.R Lide «CRC Book of Chemistry and
Physics» 81st edn (Boca Raton, FL: CRC Press) 2000.
[89] X. He, J.W. Elmer, T. DebRoy, «Heat transfer
and fluid flow in additive manufacturing». J. Appl. Phys. 97 (2005)
84909
[90] C.L. Yaws," Handbook of Thermal Conductivity».
Houston, TX: Gulf (1997)
[91] U.S. Bertoli, A.J. Wolfer, M.J. Matthews, et al,
«On the limitations of volumetric energy density as a design parameter for
selective laser melting»,Mater.Des. 113, 331-340, 2017.
[92] X. He, J. Elmer, T. DebRoy, «Heat transfer and
fluid flow in additive manufacturing». J. Appl. Phys. 97, 84909,
2005.
76
MASTER II-LABORATOIRE SCIENCES DES
MATÉRIAUX
|