I.4.4. Interface renfort / matrice
L'interface est définie comme une zone
particulière d'épaisseur quasiment nulle formée par une
frontière commune entre le renfort et la matrice, elle assure la liaison
entre ces entités pour le transfert de charge et constitue une zone
clé pour l'optimisation des propriétés mécaniques
des matériaux composites, cette zone est considérée comme
un constituant du composite car elle possède des
propriétés physiques, chimiques et mécaniques
différentes de celles de la fibre et de la matrice.
Ces propriétés sont difficilement accessibles
expérimentalement et la plupart des données sont obtenues
à partir des modélisations sur la réponse mécanique
des composites, Par contre, à l'échelle réelle,
l'épaisseur de cette interphase peut être mise en évidence
de plusieurs manières à l'aide d'analyse viscoélastique et
fluage thermo stimulé. Dans une matrice composée des charges de
verre ensimées en résine époxy l'épaisseur de
l'interphase est de 1,4 à 1,75 um.[13]
Il est possible d'identifier trois couches avec une
stabilité hydrolytique différente : une couche
physisorbée, une couche tridimensionnelle et une couche interfaciale.
v Le schéma d'interphase renfort/ matrice est
représenté dans la Figure I.9 suivante :
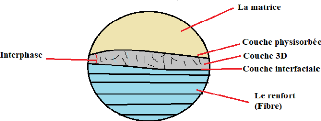
CHAPITRE I Matériaux composites pour
l'aéronautique
11 | P a g e
Figure I.9 : l'interphase entre
la matrice et le renfort
Le rôle des fibres est de supporter la grande partie de
la contrainte, par contre, celui de la matrice est la redistribution et le
transfert des charges d'une fibre à l'autre via l'interface. Le
rôle de la zone interfaciale est primordial pour améliorer les
performances finales du composite. La quantification de l'adhérence est
généralement évaluée par des tests
micromécaniques consistant à étudier une fibre unique
enrobée de résine.
Une interphase très cohésive permettra aux
fissures de se propager perpendiculairement à l'axe des fibres et
entraînera une rupture de l'échantillon. Une interphase moins
résistante, permettra de dévier la fissure vers l'interphase et
de limiter son impact à quelques fibres uniquement[6].
· Les interfaces fibres/matrices sont supposées
parfaites et ne sont pas considérées dans les calculs de cette
étude.
I.4.5. Les différentes structures des
matériaux composites
Ils peuvent être classées en trois types liés
un par rapport aux autres :
1. Les monocouches
Représentent l'élément de base de la
structure composite stratifié et sont constitué d'un seul pli de
renfort, est souvent appelée une strate.[6]
2. Les stratifiés
Sont constitués par plusieurs monocouches successives
(2 ou plus) de même ou de différentes orientations des renforts.
(Voir le schéma de la Figure I.10)
Les stratifiés sont utilisés comme des
matériaux structuraux, où on a, la nécessité
d'excellentes performances mécaniques en termes de résistance,
rigidité, comportement à la fissuration, et l'exigence de limite
en poids.

CHAPITRE I Matériaux composites pour
l'aéronautique
12 | P a g e
Figure I.10 : Monocouches
constituant le stratifié.
3. Les composites sandwiches
Sont constitués d'un nid d'abeille (une matière
résineuse, mousse ou en aluminium) entre deux surfaces des composites
stratifiés (Figure I.11) pour faire face à
l'effort tranchant.
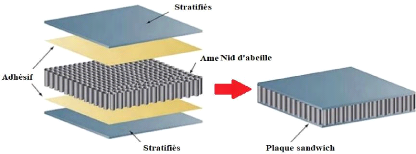
Figure I.11 : Schéma d'un
composite sandwich
I.5. Aspect physico-mécanique des structures
composites
Dans le domaine de l'espace et de l'aviation (Hautes
performances), on cherche des matériaux les plus performants possible en
mesure de sécurité, un module élevé avec une masse
volumique faible. Ça nous conduira automatiquement à des
composites.
|