ANNEXE
1. FIBRES DE VERRE
Les fibres de verre sont peu coûteuses en production, et
constituent le renfort le plus utilisé actuellement. Leur fabrication se
fait en général par étirage décrit par la figure
ci-dessous. Les oxydes minéraux constituant la matière
première (silice, alumine, etc.) sont mélangés en
proportion voulue suivant le type de fibres de verre désiré (voir
tableau II.1.). Ce mélange est ensuite porté
à très haute température (Environ 1250°C). A cette
température, la viscosité du verre permet un écoulement
par gravitation à travers la filière sous forme des fibres de
quelques dixièmes de millimètres. A la sortie de la
filière le verre en phase plastique est simultanément
étiré à grande vitesse (de l'ordre 250 m/s) et refroidi,
les conditions des refroidissements et de vitesse d'étirage permettent
d'obtenir des fibres sous forme de filaments de diamètres
calibrés[1] . Ces filaments isotropes sont ensimés
pour optimiser l'adhésion de la matrice, puis assemblés pour
former les fils, eux-mêmes stockés sous forme de bobine
appelée gâteau. Le gâteau est alors étuvé,
pour éliminer l'eau résiduelle et pour stabiliser l'ensimage. Les
fibres de verre ainsi obtenues sont amorphes, ce qui leur confère des
caractéristiques mécaniques parfaitement
isotropes.[2]
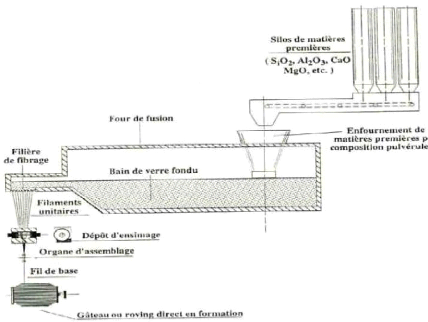
Figure.1. Procédé de fabrication des
fibres de verre

II | P a g e
2. FIBRES DE CARBONE
Les fibres de carbone ont de très fortes
propriétés mécaniques et sont largement utilisées
dans les composites HP, élaborées à partir de l'un des
trois précurseurs suivants : la rayonne, le brai de pétrole, et
le poly acrylonitrile [(CH2-CH-CH) n] noté (PAN). Les fibres de carbone
utilisées comme des renforts sont produites à partir de brai de
mésophase ou de PAN, en commençant tout d'abord par le traitement
thermique de brai isotope afin d'orienter les molécules poly
aromatiques. Ensuite, le filage et l'étirage de cette mésophase
sont réalisés pour l'obtention des fibres ; ces dernières
sont composées de 90 à 70 % de carbone, moins de 10 % d'azote,
environ, 1% d'oxygène et moins de 1% d'hydrogène. La fabrication
des fibres de carbone à partir de PAN passe par quatre étapes :
Oxydation, carbonatations, graphitisation et traitement de surface [3]
a. Oxydation
Les fibres acryliques étant fusibles, la phase
d'oxydation a pour but de supprimer artificiellement le point de fusion ; cette
opération est effectuée en chauffant les fibres à environ
200 à 300 c° en atmosphère oxygéné pendant 0.5
à 3h. Il se produit alors une oxydation conduisant à une
réticulation des chaines moléculaires et à la
création d'un réseau tridimensionnel.
b. Carbonatation
Consiste à chauffer progressivement les
réticulées de 300 °C à 1100 °C environ, en
atmosphère inerte. Il y a alors élimination de l'eau et de
l'acide cyanhydrique, seuls les carbones étant conservés dans la
chaîne. Les fibres obtenues après cette phase ont de bonnes
caractéristiques mécaniques et peuvent être
utilisées après traitement des surfaces. Ces fibres sont alors
dénommées fibres HR (haut résistance) ou fibres HT (haut
ténacité).
c. Graphitisation
Cette phase est utilisée lorsqu'on souhaite obtenir des
fibres à module de Young élevé ; cette phase consiste
à effectuer, à la suite de la carbonatation, une pyrolyse des
fibres en atmosphère inerte jusqu'à 2600°C ou à des
températures supérieures ; la graphitisation provoque une
réorientation des réseaux hexagonaux de carbone suivant l'axe des
fibres, ce qui aboutit à une augmentation du module de Young. Toutefois,
simultanément à cette réorientation, des défauts se
créent dans la structure, entraînant une diminution de la
contrainte à la rupture. Suivant le taux de graphitisation, on distingue
deux types de fibres : fibres à haute résistance (HR) pour une
combustion à 1500 °C, et fibres haut module (HM) pour une
température de combustion de 1800 à 2000 °C [4]
III | P a g e
d. Traitement de surface
Il consiste en un traitement de surface par oxydation
ménagée en milieu acide (nitrique ou sulfurique). Cette phase a
pour objet d'accroitre la rugosité des filaments. Un traitement final
par ensimage effectué à l'aide d'une dispersion aqueuse
spécifique comportant un agent antistatique, permet d'assurer
différents rôles telle que la compatibilité de la liaison
fibre - matrice et la protection contre l'abrasion générée
par la mise en oeuvre (frottement contre pièces métalliques).
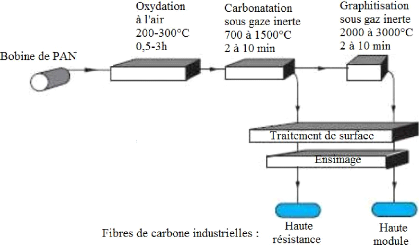
Figure.2. Procédé de fabrication des
fibres de carbone à partir de (PAN).
3.
LES UNITES UTILISES EN ABAQUS
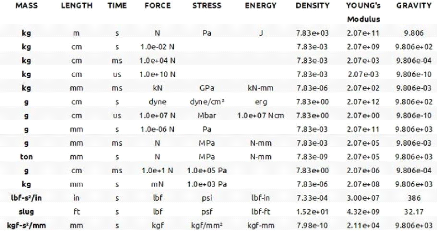

Figure.3. Les unités utilisées en
Abaqus
4. MESURE DES PARAMETRES ELASTIQUE PAR
ULTRASON
2_ E(1-u)2= E
On a VL -- p(1+u)(1-2u) VT 2p(1+u)
Trouvons E
2 3E(1-u)
3VL - 4 V= p(1+u)(1-2u)
|
4E
|
2p(1+u)
|
=
=
=
IV | P a g e
3E(1-u)-2E(1-2u)
p(1+u)(1-2u) 3E-3Eu-2E+4Eu
p (1+u)(1-2u) E+Eu
p(1+u)(1-2u)
= ??(1+u)
??(1+u)(1-2u)
3VL 2- 4 VT2 = ??
??(1-2u)
|
??(1-u)
VL 2- VT2=
??(1+u)(1-2u)
|
??
|
2??(1+u)
|
2??(1-u)-??(1-2u) ??
(1+u)(1-2u)
2??-2??u-E+2??u
??(1+u)(1-2u) (simplification)
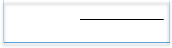
??
VL 2- VT2=
2??(1+u)(1-2u)
Calculons le rapport 3VL2 4?? 22 = E . 2??
(1+u)(1-2u)
???? --VT ??(1-2u) ??
= 2(1 + u)
??
?????? 2 3???? 2-4????2
?? 2
??2-????2 = ?? ??(1-2u) (2(1 + u)) = E
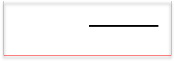
2-4????2
?? = ?????? 2 3???? ????2-????2
Finalement
Trouvons u
VL 2- 2VT2= ??(1-u)
??(1+u)(1-2u)
|
2??
|
2??(1+u)
|
V | P a g e
??(1-u)-??(1-2u) ??
(1+u)(1-2u)
??(1-u)-??(1-2u) ??
(1+u)(1-2u)
??-??u-??+2??u
?? (1+u)(1-2u)
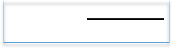
VL 2- 2VT2 =
??u
??(1+u)(1-2u)
?? =
|
1
|
???? 2-2????2
|
2????
2-????2
|
1 ???? 2-2????2
2???? 2-????2
Finalement
1 ??u
2??(1+u)(1-2u) ·
2??(1+u)(1-2u) =
u
??
VI | P a g e
Références annexe
1. Guillon, D., Fibres de verre de renforcement.
Techniques de l'ingénieur. Plastiques et composites,
1995(A2110): p. A2110. 1-A2110. 15.
2. Aribi, C., Étude comparative du comportement
des différents matériaux composites (différentes
matrices), 2012, Université de Boumerdès-M'hamed Bougara.
3. Wang, P., Étude numérique et
expérimentale de procédé d'élaboration
des matériaux composites par infusion de résine, 2010,
Saint-Etienne, EMSE.
4. Davim, J.P., Book Review: Machining of Polymer
Composites by Jamal Y. Sheikh- Ahmad. International Journal of
Machining and Machinability of Materials, 2009. 6(3-4): p.
322-323.
|