
Faculté des Sciences, Université M'hamed Bougara
de Boumerdès

Mémoire
Pour obtenir le diplôme de :
MASTER EN PHYSIQUE
Spécialité : PHYSIQUE DES MATERIAUX
Présenté par :
Asma BESSAAD
Intitulé :
Etude du comportement mécanique des
matériaux composites destinés à
l'aéronautique
Soutenu le 29/09/2022, devant le jury composé de :
MAZOUZ H.M Ahmed (MCA UMBB) Président
SERSOUR Zakia (MAA UMBB) Examinatrice
ARIBI Chouaib (MCA UMBB) Encadrant
TOUBANE Mahdia (MCA UMBB) Co-Encadrante
Département de Physique, Faculté des Sciences,
Université de Boumerdès, Avenue de l'indépendance 35000
Boumerdès Tel : +213 (0) 24 81 62 49 / Fax : +213 (0) 24 81 62
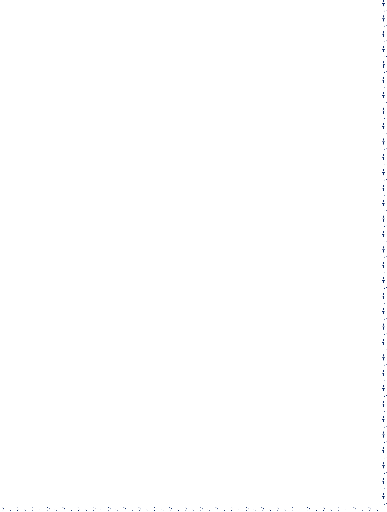
Remerciement
Nous remercions tout d'abord, le bon Dieu de nous
avoir donné la santé, la volonté, le courage et la foi
pour pouvoir atteindre nos objectifs et surmonter les moments difficiles
pour réaliser ce mémoire.
Je remercie ma chère Mme TOUBANE ma
Co-encadrante en premier pour son encouragement, sa disponibilité et
ses qualités d'enseignement exceptionnelles, depuis
que j'étais en licence, t'es une enseignante exemplaire et que j'aime
trop, merci pour tout. J'exprime ma gratitude et ma reconnaissance à
mon promoteur Mr ARIBI Chouaib pour sa patience et son soutien qu'il m'avais
donné pour réaliser ce mémoire. Je tiens a
remercié également monsieur le président de jury Mr MAZOUZ
Ahmed Hadj Moulay et l'examinatrice Mme SERSOUR Zakia d'avoir
acceptés d'examiner ce travail. Je remercier mes chers enseignants de
département de physique spécialement Mme LAMRANI, Mme
BOUKHERROUB et Mr MAZOUZ encore une fois, Vous êtes les meilleurs
à nous. Sans oublier tous mes enseignants au
département. Aussi je désire à adresser mes
sincère remerciements au doyen de la faculté des sciences
Mr RIBA Omar pour ses sages décisions et ses bonnes qualités
personnelles et professionnelles. Merci aussi à mon oncle Mr BASAID
Djamel pour le guide qui m'avais donné pour choisir cette
spécialité merveilleuse et ce
thème. Dernièrement je remercie toutes les équipes qui
m'ont aidé dans la compagnie Air Algérie, CNERIB, CRTI et
l'unité de recherche UR-MPE. J'adresse aussi mes remerciements
à tous les personnages qui m'ont aidées : Dr Zara,
Dr Nour.

Asma BESSAAD
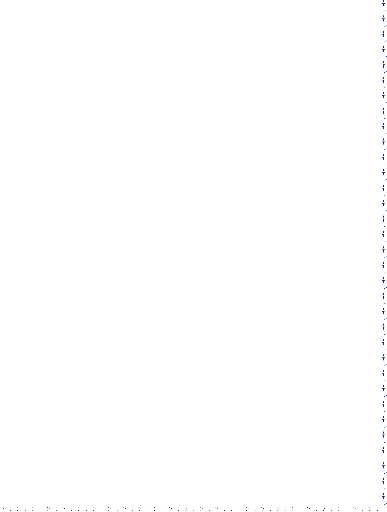
II
Dédicace
Je dédie ce modeste travail tout d'abord
à ma chère mère Djamila et mon père Ahmed pour
leur tendresse et leur énorme soutien tout au long de mon cursus
d'étude,
Et à mes chères soeurs (Hassina,
Hanane et Imane) et mes frères (Mohamed, Yacine, Karim, Nassim et
Islam sans oublier leurs femmes) et à toute la famille.
Aux enfants de ma famille que j'aime le plus :
Marwa, Samy, Ritadj, Siradj, Saraa, Israa, Malak, Ahmed et
Safa.
Je le dédie également à mes
chères amies Anissa, Meriem, Amel, Feriel et tous
mes collègues de toutes mes 17 années d'études
...
Aux membres de mon club scientifique (BIOBEST) avec
lequel j'ai passé mes plus beaux moments et mes plus belles
expériences à l'université.
Que ce travail soit l'accomplissement de vos voeux
tant allégués, et le fruit de votre soutien
infaillible.
III
Table des matières
Remerciement i
Dédicace ii
Table des matières iii
Liste des figures vii
Liste des tableaux x
Liste des abréviations xi
Résumé . xii
Introduction Générale
1
CHAPITRE I Matériaux composites pour
l'aéronautique
I.1. Introduction 4
I.2. Classification des matériaux
4
I.3. Propriétés mécaniques
5
I.3.1. Les essais mécaniques
6
a) Compression 6
b) Flexion 6
c) Traction 6
d) Fatigue 7
I.3.2. Le contrôle non destructif (CND)
7
I.4. Les matériaux composites
8
I.4.1. Définition 8
I.4.2. Les deux types de composites
8
I.4.2.1. Les composites GD
8
I.4.2.2. Composites HP 8
I.4.3. Classification des matériaux composites
9
I.4.3.1. Suivant la forme des renforts
9
I.4.3.2. Suivant la nature des matrices
9
I.4.4. Interface renfort / matrice
10
I.4.5. Les différentes structures des
matériaux composites 11
1. Les monocouches 11
2. Les stratifiés
11
3. Les composites sandwiches
12
I.5. Aspect physico-mécanique des structures
composites 12
I.5.1. Densité 12
I.5.2. Fractions volumiques et massiques
13
iv
I.5.2.1. Fraction massique 13
I.5.2.2. Fraction volumique 13
I.5.3. L'isotropie des matériaux composites
14
I.6. La fabrication des matériaux composites
14
I.6.1. Moulage au contact 15
I.6.2. Moulage sous vide 15
I.6.3. Moulage par compression 16
I.7. Intégration des matériaux
composites dans l'aéronautique 16
I.7.1. Les avantages des matériaux composites
pour utilisation aéronautique 18
I.7.2. Les inconvénients des matériaux
composites destinés à l'aéronautique 18
I.8. Les exigences des matériaux composites
stratifiés en aéronautique 18
I.9. Conclusion 19
Références de chapitre I
20
CHAPITRE II Procédés d'élaboration
et caractérisation des matériaux composites
II.1. Introduction 22
II.2. Matériaux d'étude
22
II.2.1. Le matériel utilisé
22
II.2.2. Les renforts 23
II.2.2.1. Caractéristiques des fibres de
carbone et de verre 24
II.2.2.1.a. Fibre de verre 24
II.2.2.1.b. Fibre de carbone 25
II.2.2.2. Préparations des renforts
27
II.2.3. La matrice 27
II.2.3.1. Caractéristiques de la
résine 28
II.2.3.2. Préparation de la matrice
28
II.2.4. Tissu d'arrachage 30
II.2.5. Feutre de drainage 30
II.3. Procédure de fabrication
30
II.3.1. L'étape de mise sous vide :
32
II.4. Représentation des pièces pour
les essais mécaniques 34
II.4.1. Eprouvettes de traction de la matrice
résineuse 34
II.4.2. Eprouvettes de traction des
stratifiés composites 34
II.4.3. Eprouvette de l'essai de flexion
35
II.5. Les machines utilisées pour les essais
mécaniques 35
II.6. Caractérisation des stratifiés
composites élaborés 35
V
II.6.1. Caractérisation physique
35
III.6.1.1. Analyse thermique (ATD, ATG)
35
II.6.1.2. Détermination de la masse volumique
36
II.6.1.3. Taux massique et volumique du renfort
37
II.6.1.4. Contrôle non destructive par
ultrasons 37
II.7. Conclusion 39
Références chapitre II
40
CHAPITRE III Résultats et
discussion
III.1. Introduction 41
III.2. Caractérisation de la matrice
41
III.2.1. Caractérisation physique
41
III.2.1.1. Analyse thermique (ATD, ATG)
41
III.2.2. Caractérisation mécanique
42
III.2.2.1. Essai de traction
42
III.3. Caractérisation du matériau
composite stratifié 43
III.3.1. Caractérisation physique
43
III.3.1.1. Mesure de densité
43
III.3.1.2. Mesure de taux des fibres
44
III.3.2. Caractérisation mécanique du
stratifié 44
III.3.2.1. Essai de traction
44
III.3.2.2. Essai de flexion (trois points)
47
III.3.2.3. Essai de fatigue
48
III.3.2.3.1. Fatigue d'éprouvette en composite
à fibre de verre 49
III.3.2.3.1. Fatigue d'éprouvette en composite
à fibre de carbone 50
III.3.3. Caractérisation par ultrasons
51
III.4. Validation des résultats
expérimentaux par simulation 53
III.4.1. Définition
53
III.4.2. Organisation de l'interface ABAQUS/CAE
54
III.4.2.1. Modules 54
1. Module " PART " 54
2. Module "PROPERTY " 55
3. Module "ASSEMBLY " 55
4. Module "STEP " 56
5. Module " INTERACTION " 57
6. Module "LOAD " 57
7.
vi
Module "MESH " 58
8. Module "JOB " 59
9. Module " VISUALIZATION " 59
10. Module "SKETCH " 60
III.4.3. Modélisation numérique (MFE)
60
III.4.4. Comparaison entre les résultats
expérimentaux et numériques. 62
III.5. Conclusion 62
Références Chapitre III
64
CONCLUSION GENERALE ET PERSPECTIFS
Conclusion générale 65
Perspectifs 66
ANNEXE
1. FIBRES DE VERRE I
2. FIBRES DE CARBONE II
3. LES UNITES UTILISES EN ABAQUS
IV
4. MESURE DES PARAMETRES ELASTIQUE PAR ULTRASON
IV
Références annexe.
VI
VII
Liste des figures
FIGURE I.1 : FAMILLES DES MATERIAUX
DE GRANDES CLASSES 4
FIGURE I.2 : DIAGRAMME DE LA
CONTRAINTE EN FONCTION DE LA
DEFORMATION 5
FIGURE I.3 : SOLLICITATION EN
COMPRESSION 6
FIGURE I.4 : SOLLICITATION EN
FLEXION 6
FIGURE I.5 : SOLLICITATION EN
TRACTION 6
FIGURE I.6 : LES CONSTITUTIFS D'UN
MATERIAU COMPOSITE 8
FIGURE I.7 : LES DIFFERENTS
RENFORTS POUR LE MATERIAU COMPOSITE 9
FIGURE I.8 : DIFFERENTES BASES POUR
CLASSIFICATION DES COMPOSITES .. 10
FIGURE I.9 : L'INTERPHASE ENTRE LA
MATRICE ET LE RENFORT 11
FIGURE I.10 : MONOCOUCHES
CONSTITUANT LE STRATIFIE. 12
FIGURE I.11 : SCHEMA D'UN COMPOSITE
SANDWICH 12
FIGURE I.12 : SCHEMA DE MOULAGE AU
CONTACT. 15
FIGURE I.13 : MOULAGE SOUS VIDE
15
FIGURE I.14 : MOULAGE PAR
COMPRESSION 16
FIGURE I.15 : TAUX DES MATERIAUX
COMPOSITES DANS LA STRUCTURE DE
BOING787 17 FIGURE I.16 : EVOLUTION
D'INTEGRATION DES MATERIAU COMPOSITE DANS
AERONEFS 17
FIGURE I.17 : STRATIFIE A PLIS DE
CONSTRUCTION [0/90/0/0/90/0°] 19
FIGURE II.1 : OUTILS POUR
FABRICATION DES PLAQUES COMPOSITES (AIR
ALGERIE) 23 FIGURE II.2 : ROULEAUX DE
FIBRES DE CARBONE ET DE VERRE
BIDIRECTIONNEL 24
FIGURE II.3 : DESSIN D'ARMURE
TAFFETAS (0/90°) [1] 24
FIGURE II.4 : STRUCTURE CRISTALLINE
DU GRAPHITE. 26
FIGURE II.5 : PREPARATION DES
RENFORTS (ETAPE DE DECOUPAGE) 27
FIGURE II.6 : TISSUS DES FIBRES DE
CARBONE ET DE VERRE (TAFFETAS) 27
FIGURE II.7 : A. RESINE EPOCAST
50-A1. B. DURCISSEUR (HARDENER 946) 28
FIGURE II.8 : ETAPES DE PREPARATION
DE LA MATRICE EPOCAST 50-A1 29
VIII
FIGURE II.9 : TISSU D'ARRACHAGE
30
FIGURE II.10 : FEUTRE DE DRAINAGE
30
FIGURE II.11 : IMPREGNATION DE
RESINE SUR LES 1ERES COUCHES DE FIBRES
31
FIGURE II.12 : IMPREGNATION DE
RESINE DE 8 COUCHES SUCCESSIVES 31
FIGURE II.13 : DEPOT DU TISSU
D'ARRACHAGE 31
FIGURE II.14 : DEPOT DE TISSU DE
DRAINAGE 32
FIGURE II.15 : DEPOT DE FILM
PLASTIQUE POUR FERMETURE DU SYSTEME 32
FIGURE II.16 : SYSTEME
D'ELABORATION DES PLAQUES COMPOSITES SOUS
VIDE 33 FIGURE II.17 : PLAQUE COMPOSITE ,
A. FIBRE DE VERRE , B. FIBRE DE
CARBONE 33
FIGURE II.18 : DECOUPAGE SELON LES
NORMES 34
FIGURE II.19 : EPROUVETTES SOUS
FORME HALTERE 34
FIGURE II.20 : DIMENSIONS DES
EPROUVETTES DE TRACTION. 34
FIGURE II.21 : DIMENSIONS DES
EPROUVETTES DE FLEXION 35
FIGURE II.22 : A. MACHINES DE
TRACTION ET B. MACHINE DE FLEXION 3
POINTS 35
FIGURE II.23 : APPAREIL DE DSC
36
FIGURE II.24 : BANC DE PESAGE.
36
FIGURE II.25 : FOUR ELECTRIQUE.
37
FIGURE II.26 : BANC DE CONTROLE PAR
IMMERSION 39
FIGURE II.27 : OSCILLOSCOPE ET
GENERATEUR 39
FIGURE III.1 : DIAGRAMME DE L'ATD
ET L'ATG DE LA RESINE EPOCAST 41
FIGURE III.2 : RUPTURE EN TRACTION
DE RESINE 42
FIGURE III.3 : COURBE D'ESSAI DE
TRACTION DE RESINE 42
FIGURE III.4 : DISPOSITIF D'ESSAI
DE TRACTION 45
FIGURE III.5 : COURBES DE TRACTION
DES EPROUVETTES CARBONE-
VERRE/EPOXY. 45 FIGURE III.6 : COURBES DE
FLEXION DES D'EPROUVETTES CARBONE-
VERRE/EPOXY. 47
ix
FIGURE III.7 : COURBE DE FATIGUE
D'EPROUVETTE EN COMPOSITE A FIBRE
DE VERRE 49 FIGURE III.8 : COMPORTEMENT
EN TRACTION AVANT ET APRES FATIGUE-
VERRE 49 FIGURE III.9 : COURBE DE FATIGUE
D'EPROUVETTE EN COMPOSITE A FIBRE
DE CARBONE 50 FIGURE III.10 :
COMPORTEMENT EN TRACTION AVANT ET APRES FATIGUE-
CARBONE 50 FIGURE III.11 : SIGNAUX
LONGITUDINALES - A. COMPOSITE A FIBRE DE
CARBONE B. COMPOSITE A FIBRES DE VERRE
51 FIGURE III.12 : SIGNAUX TRANSVERSALES - A.
COMPOSITE A FIBRE DE
CARBONE B. COMPOSITE A FIBRES DE VERRE
52
FIGURE III.13 : COMPOSANTS DE
L'INTERFACE DU LOGICIEL ABAQUS 54
FIGURE III.14 : MODULE DE CREATION
DE LA GEOMETRIE 55
FIGURE III.15 : MODULE
D'INTRODUCTION DES PARAMETRES DE MATERIAUX
55
FIGURE III.16 : MODULE D'ASSEMBLAGE
GEOMETRIQUE 56
FIGURE III.17 : PHASE DE CREATION
DES SOLLICITATIONS 56
FIGURE III.18 : MODULE
D'INTERACTION 57
FIGURE III.19 : PHASE DES
CONDITIONS LIMITE ET CHARGEMENT 58
FIGURE III.20 : PHASE DE MAILLAGE
58
FIGURE III.21 : PHASE DE LANCEMENT
DE SIMULATION 59
FIGURE III.22 : PHASE CONSULTATION
DES RESULTATS 59
FIGURE III.23 : MODULE DE CREATION
BIDIMENSIONNELLE 60
FIGURE III.24 : DIMENSIONS DU
MODELE NUMERIQUE. 61
FIGURE III.25 : MODÈLE
ÉLÉMENTS FINIS 61
FIGURE III.26 : COMPARAISON ENTRE
LES RESULTATS EXPERIMENTALE ET
NUMERIQUE 62
X
Liste des tableaux
TABLEAU II.1 : DIFFERENTS TYPES
DE FIBRES DE VERRE FILABLES 25
TABLEAU II.2 : CARACTERISTIQUES
DU TISSU DE CARBONE ET DE VERRE 26
TABLEAU II.3 : CARACTERISTIQUES
DES EPOCAST 50-A1/946 28
TABLEAU II.4 : CARACTERISTIQUES
DU FEUTRE DE DRAINAGE 30
TABLEAU III.1 : PROPRIETES
MECANIQUES DE LA MATRICE EPOCAST. 43
TABLEAU III.2 : RESULTATS DES
MASSES VOLUMIQUES OBTENUS 44
TABLEAU III.3 : TAUX MASSIQUE DE
RENFORT PAR ESSAI DE CALCINATION 44
TABLEAU III.4 : L PROPRIETES DE
TRACTION DES STRATIFIES COMPOSITES 46
TABLEAU III.5 : PROPRIETES DE
FLEXION DES COMPOSITES. 48
TABLEAU III.6 : PARAMETRES
ELASTIQUES DETERMINES PAR ULTRASON 53
TABLEAU III.7 :
PARAMÈTRES GÉOMÉTRIQUES ET
MÉCANIQUES UTILISÉS 61
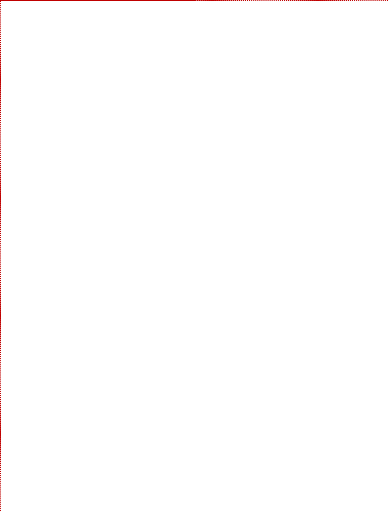
Liste des abréviations
CRTI : Centre de Recherche
en Technologies Industrielles
CNERIB : Centre National
d'Etudes et de Recherches
Intégrées du Bâtiment
UR-MPE : Unité de
Recherche Matériaux,
Procédés et Environnement
ASTM : American Society
for Testing and Materials
ATD : Analyse Thermique
Différentielle
ATG : Analyse
Thermo-Gravimétrique
E : Module de Young.
Ep : Matrice Epocast
G : Module de cisaillement.
GPa : Giga Pascal
P : Pression
S : Surface
T : Température
Tg : Température de transition
vitreuse
UD : Uni-Directionnelle
ó : Contrainte.
p : Masse volumique.
i : Tenseur de déformation.
y : Coefficient de poisson.
xi
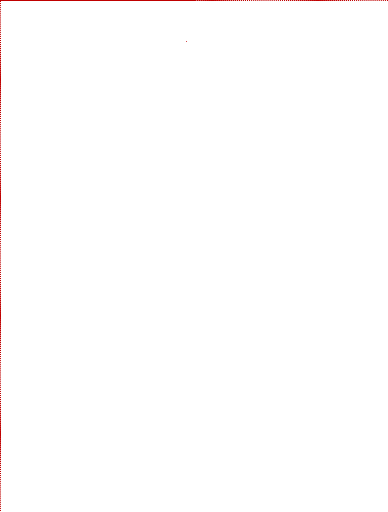
ÕÎáã
ÚæäáÇ äã
äÇíÑØáÇ
áÇãÌ í ÉãÏÎÊ
ÓáãÇ
ÓíßæÈíÇáÇ
ÊÇÌäÊÇÑæ
ÉíÌÇÌÒáÇ
ÇíááÇæ
äæÈÑßáÇ Çíá
áìÚ ÉÆãÇÞáÇ
ÉÈßÑáãÇ
ÆÍÇÔÑáÇ
ÉÓÇÑÏ
æå áãÚáÇ
Ç
Ðå äã ÏåáÇ
Epocast 50-A
.ËÑß ÉÞãÚã
ÉÓÇÑÏ áÌÇ äã
ÉíÆíÇíÒáÇ
ÊÇÑÇÈÊÎÇáÇ
ÇÖíæ ÉÏãÇáá
ÏÇÌåÅáÇ
ÊÇÑÇÈÊÎÇæ
ÉíßíÊÇÊ
ÓÇáÇ
ÊÇÑÇÈÊÎÇáÇ
ÁÇÑÌÅá ÇÈå
áæãÚáãÇ
íÑíÇÚáãÇ
ÞÑØ Þæ
ÊÇäíÚáÇ
íÑÖÊÍ Êãí
ÉÑÆÇØáÇ í
ÏÇÌåÅáÇ
ÉÏíÏÔ
ÁÇÒÌáÇ í
ÇãåÇÏÎÊ ÓÇ
ÓÑ í Çã æåæ
ÈÚÊáÇ
ÉãæÇÞã ËíÍ
äã äæÈÑßáÇ
Çíá ÊÇÈßÑáã
áíÇÚáÇ
ÁÇÏáÇ ÇíåáÚ
ÑæËÚáÇ Êã
ÊíáÇ
ÆÌÇÊäáÇ
ÊÑåÙ
. ÇÈå
ÉÕÇáÎÇ
ÊãÇáÚáãÇ
íÑíÛÊ
ááÇÎ äã
ÉäæÑáãÇ
áÇãÌ í
ÊÇÈßÑáãÇ
åÐå ßæáÓÈ
ÄÈäÊáÇ
ÉíäßÇãÅÇ
Abaqus
ÌãäÇÑÈ
ÉØÓÇæÈ
ÉßÇÇáãÍÇ
ÊÇÑÇÈÊÎÇ
ÊÖÍæ ÏÞæ
Abaqus
:
ÉíÍÇÊã
ÊãÇßá
ÉíÊæÕáÇ
Þæ ÊÇÌæáãÇ
ÉíÌÇÌÒ Çíá
äæÈÑßáÇ Çíá
ÓíßæÈíÇáÇ
ÌãäÇÑÈ
Résumé
L'objectif de ce travail est consacré à
étudier les stratifiés composites à base de fibre de
carbone, fibre de verre et résine époxy de type Epocast 50-A,
utilisés dans le domaine aéronautique. Les éprouvettes
sont préparés selon les modalités des normes en vigueurs
pour réaliser les essais mécaniques statiques et les essais de
fatigue.
Les résultats trouvés montrent la haute performance
des composites à base de fibre de carbone en termes de résistance
à la fatigue, ce qui explique leurs utilisations dans la partie
hautement sollicitée dans l'avion.
Des tests de simulation par logiciel Abaqus ont clarifiés
la possibilité de prévision de comportement de ces composites
dans leur domaine élastiques à travers de leurs propres
paramètres.
Mot clés : Epoxy, fibre de verre, fibre
de carbone, Ultrasons, Abaqus.
Abstract
The objective of this work is devoted to studying composite
laminates based on carbon fibers, fiberglass and epoxy resin of the Epocast
50-A type, used in the aeronautical field.
The specimens are prepared according to the methods of the
standards in force to carry out the static tests and the fatigue tests.
The results found show the high performance of carbon fiber
composites in terms of fatigue resistance, which explains their use in highly
stressed parts in the aircraft.
Simulation tests by Abaqus software clarified the possibility
of behavior prediction of these composites in its elastic domain through its
own parameters.
Keywords : Epoxy, fiberglass, carbon fibers,
Ultrasound, Abaqus.
xii
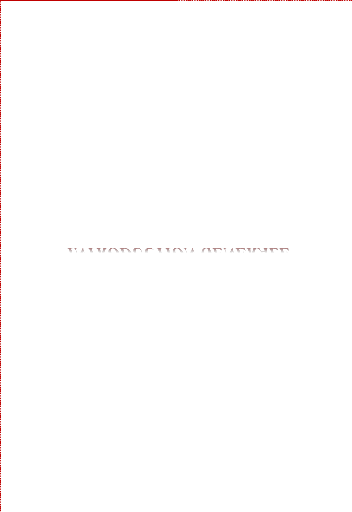
INTRODUCTION GENERALE
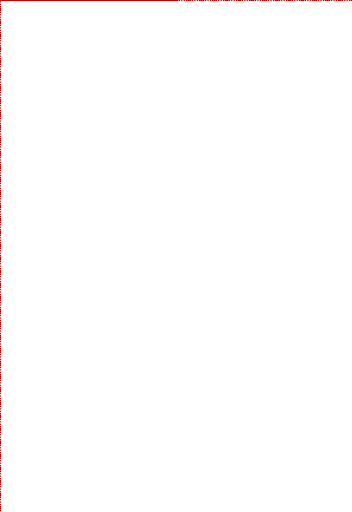
Introduction Générale
La physique des matériaux repose sur l'étude de
comportement des matériaux et leurs propriétés à
différentes échelles notamment les propriétés
électriques, physiques, optiques, magnétiques, chimiques,
thermiques et mécaniques. Cela peut dépendre de variables
externes (T, P).
Le domaine industriel de l'aéronautique exige des
matériaux avec des propriétés de haute performance
mécanique, bien conçus et sévèrement
contrôlés, pour cela les concepteurs façonnent des
matériaux composites à base de fibres continus, en les
développant chaque année dans diverses réalisations de
haute technologie.[1]
Dès le début des années 1960, les
matériaux composites (fibres/matrice) sont apparus dans le domaine
aérospatial, comme dans de nombreux autres domaines, pour remplacer les
alliages métalliques en raison de leur légèreté et
leur résistance spécifique élevée
(résistance dépendant de la densité, d'une meilleure
résistance à la corrosion et la résistance à la
fatigue)[2] . Aussi les matériaux du transport
aérien doivent respecter différents critères
d'élasticité, réduisant ainsi les coûts de
production. Les composites à matrice polymère (ou PMC) ont
d'abord été introduits dans les structures aéronautiques.
D'abord avec des composites renforcés en fibres de verre puis avec des
composites renforcés en fibres de carbone à partir du
début des années 1970.[3]
Dans ce travail, nous nous sommes en premier lieu
concentrés sur l'élaboration de deux types de matériaux
composites (carbone/époxy) et (verre/époxy), par la
méthode de moulage sous vide. Par la suite, étudier les
propriétés physiques et mécaniques des éprouvettes
à travers des essais mécaniques : traction, flexion et fatigue.
Ensuite faire une étude de contrôle de nos échantillons par
la méthode non destructive d'ultrasons. Nous terminons notre travail par
une étude du comportement mécanique par traction de composite
à l'aide d'un logiciel de simulation Abaqus pour une validation des
résultats expérimentaux.
Ce mémoire s'articule en trois chapitres. Dans le
1er chapitre nous donnerons en premier quelques notions
fondamentales sur les matériaux et leurs propriétés
mécaniques, et deuxièmement, étudier l'aspect physico
mécanique de composite spécifiquement, avec une description des
techniques les plus importantes de fabrication des matériaux composites,
et leurs intégrations et exigences en aéronautique
dernièrement.
Le 2ème chapitre inclut l'étape
d'élaboration des échantillons et les différents tests
réalisés pour la caractérisation, durant un stage pratique
au sein de la base de maintenance
1 | P age
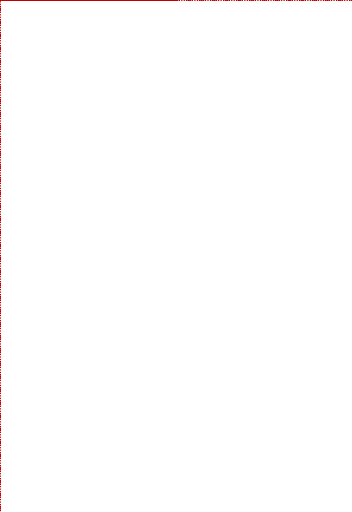
d'Air Algérie (Atelier plastiques et composites), ainsi
pour les procédés de caractérisations par les essais
mécaniques qui sont réalisés au Centre National d'Etudes
et de Recherches Intégrées du Bâtiment à Souidania
(CNERIB) et au sein d'unité de recherche (URMPE) à
l'université de Boumerdès pour les tests physiques. Ensuite nous
étudierons l'inspection de nos composites par la méthode CND des
ondes ultrasons au centre de recherche à Cheraga (CRTI).
Dans le 3ème chapitre nous discuterons les
résultats obtenus dans l'étude expérimentale ainsi que la
simulation pour ensuite faire une comparaison de comportement mécanique
de nos deux composites verre/époxy et carbone/époxy.
Nous terminons ce manuscrit par une conclusion
générale et des perspectives et d'une annexe sur la fabrication
des tissus de verre et de carbone avec les références
bibliographiques utilisées.
2 | P age
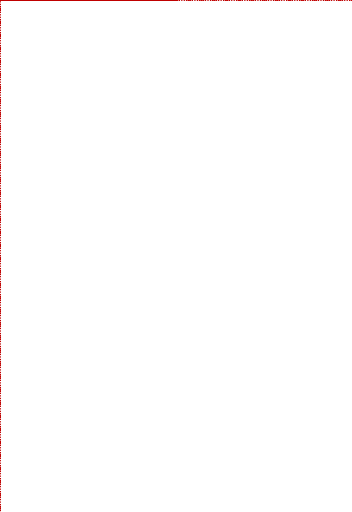
Références d'introduction
générale
1. Berthelot, J.-M., Matériaux composites.
Comportement mécanique et analyse des structures, 1999.
4.
2. Chapuis, D., V. Aerts, and R. Bonneville, Chapitre 4: Les
nouveaux matériaux composites pour l'aéronautique par Vincent
Aerts, in Chimie, aéronautique et espace. 2021, EDP Sciences. p.
75-84.
3. Cinquin, J., Les composites en aérospatiale. 2002:
Ed. Techniques Ingénieur.
3 | P a g e
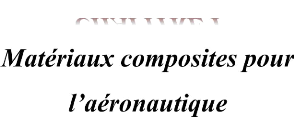
CHAPITRE I
I.1. CHAPITRE I Matériaux composites pour
l'aéronautique
4 | P a g e
Introduction
Les cinquante dernières années ont vu une
avancée significative dans le développement de matériau
composite renforcé de fibres artificielles pour applications
structurelles, notamment des fibres continues de verre ou de carbone à
des fractions volumiques de fibres élevées[1].
Spécifiquement dans le domaine d'aéronautique qu'il
nécessite un matériau le plus léger possible avec les
bonnes propriétés mécaniques pour la structure de fuselage
d'avion, d'où l'enjeu des chercheurs est d'introduire des composites
d'haute performance qui remplacent les matériaux métalliques dans
la confection de la structure d'aéronef[2].
Dans ce chapitre on a défini les matériaux
composites et l'importance de leur intégration dans
l'aéronautique et les exigences pour la confection de structure en
fuselage, en passant par décrire les essais mécaniques statique
qui nous renseigne sur leurs comportements, et les méthodes de
fabrication de ces composites stratifiés.
I.2. Classification des
matériaux
Dans le monde entier on trouve différents types de
matériaux selon le domaine d'utilisation (industriel ou aussi dans la
nature). On peut les distinguer d'après le tableau périodique des
éléments (le tableau de Mendeleïev).
Le choix d'un matériau n'est pas simple, il
dépend de besoins et des propriétés voulues.
Il existe quatre principales familles des matériaux
classées selon la nature des liaisons entre les atomes, qui sont : les
métaux (liaisons métalliques), les polymères ou les
matériaux organique (liaisons covalentes + van der Waals), les
céramiques ou les minéraux (ont des liaisons ioniques) et les
composites qui sont une combinaison entre deux de ces trois principales
familles (Figure I.1).[3]
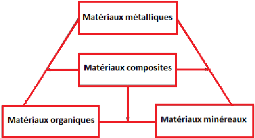
Figure I.1 : Familles des
matériaux de grandes classes [3]
· Le dernier type qui nous intéresse dans ce qui
suit de ce manuscrit.
CHAPITRE I Matériaux composites pour
l'aéronautique
5 | P a g e
I.3. Propriétés mécaniques
La connaissance des propriétés mécaniques
est essentielle à la conception des matériaux techniques afin de
mettre ces derniers en fonction, il est nécessaire de choisir le
matériau adéquat pour qu'il résiste aux contraintes
mécaniques appliquées [4].
On a résumé les différentes
propriétés mécaniques en quelques définitions
suivantes : Ductilité : Capacité d'un
matériau ou d'un composant à continuer à supporter
après avoir atteint un état de dommage jusqu'à ce qu'il
atteigne sa capacité de charge ultime. C'est la capacité de
maintenir la déformation à une certaine capacité de charge
sans se rompre. Dureté : Capacité d'un
matériau à résister à une déformation
plastique locale ou à résister aux rayures, aux coupures,
à l'abrasion, à l'indentation ou à la
pénétration.
Fragilité : La propriété
selon laquelle un matériau se brise sous l'action d'une force externe
(telle la traction) avec une seule petite déformation.
Malléabilité : Capacité
d'aplatir et de se courber sans rompre et conserver la nouvelle forme
Rigidité : La capacité d'un matériau ou
d'un composant à résister à la déformation sous
contrainte, ce qui est une représentation de la difficulté de la
déformation élastique et également de la force requise
pour provoquer un déplacement unitaire.
Résilience : Valeur caractérisant
la résistance aux chocs.
Elasticité : La
propriété selon laquelle un objet peut récupérer sa
taille et sa forme d'origine après déformation, qui est
exprimée par les constantes élastiques (E, V, G)
v Module de Young (module
d'élasticité) E
Est une constante qui relie la déformation ? et la
contrainte ó d'un corps élastique. Elle est mesurée par
plusieurs technique d'où l'essai de traction le plus monotone) en
traçant la courbe de contrainte en fonction de la déformation et
mesurant la pente de la droite de la zone élastique. Avec :
ó = E. ? (loi de Hooke)
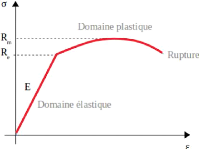
Figure I.2 : Diagramme de la
contrainte en fonction de la déformation
v CHAPITRE I Matériaux composites pour
l'aéronautique
Coefficient de poisson V
Est une constante élastique compris
généralement dans l'intervalle (0 et 0.5), et représente
la valeur de contraction d'un matériau placé perpendiculairement
à la direction de force appliquée.[5]
v Module de cisaillement G
Le module d'élasticité de glissement du
matériau ou module de Coulomb exprimé en pascal (Pa). Est la
mesure de la nature rigide du matériau.
Dans le cas des matériaux isotropes il existe une relation
qui relie le module de Young et le
coefficient de poisson et le module de cisaillement qu'elle est :
E = 2G (1+ V)
I.3.1. Les essais mécaniques
Peuvent être considérées comme des mesures
destructives, une contrainte est appliquée au matériau
jusqu'à ce qu'il se casse ou jusqu'à ce qu'il ait suffisamment de
déformation. Ces tests nous permettent de calculer les paramètres
d'élasticité et spécifier les protocoles pour d'autres
types de tests, tels que les tests dynamiques.[6]

Les essais mécaniques monotones les plus classiques sont
ceux de :
a) Compression
C'est le test qui permet la détermination du
comportement mécanique de matériau (déformation relative
au point de rupture) quand il est soumis à une contrainte de
compression.
Figure I.3 : Sollicitation en
compression
b) Flexion
Ce test permet la mesure de module d'Young, la
résistance en flexion et la force à la rupture. Sachant qu'elle
est une combinaison de traction et compression, il existe la flexion dite de
trois points (Figure I.4) et la flexion dite de quatre
points.[7]
|
|
Figure I.4 : Sollicitation en
flexion
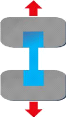
c) Traction
Figure I.5 : Sollicitation en
traction
Ce test permet la détermination du comportement des
matériaux lorsqu'ils sont soumis à une contrainte de traction. En
utilisant des capteurs de forces, il nous renseigne sur la rigidité du
matériau par le calcul du module de Young, la déformation et la
résistance à la rupture s'affichent, en utilisant des logiciels
intégrés au machines d'essais.
6 | P a g e
CHAPITRE I Matériaux composites pour
l'aéronautique
7 | P a g e
d) Fatigue
Est un essai mécanique (de traction, torsion ou de
flexion), le matériau est soumis à des cycles
répétés d'efforts[8], il subit des
modifications de microstructure c'est-à-dire une apparition des
défauts et des fissurations regroupées sous le terme
général d'endommagement par fatigue. Elle se développe
progressivement sous l'action de la répétition des sollicitations
au cours du temps.
L'endommagement par fatigue du matériau fait
référence au phénomène de rupture sous une
contrainte bien inférieure à la limite de résistance ou
même à la limite d'élasticité du matériau.
I.3.2. Le contrôle non destructif (CND)
Est un ensemble des méthodes qui permettent de
caractériser l'état d'intégrité d'une structure ou
d'un matériau, qui ne se dégradera ni en production, ni en
utilisation, ni dans le cadre de la maintenance. Également connu sous le
nom de test non destructif (NDT).
Les méthodes d'essais non destructives ont
été largement utilisées dans le monde industriel. Ils font
désormais partie d'un outil universel qui contribue à augmenter
la productivité, garantissant que les produits répondent aux
exigences de qualité strictes des clients, contribuant ainsi à
leur satisfaction ultime. Parallèlement à ce
développement, le contrôle non destructif a élargi son
champ d'application, passant du domaine de la détection locale stricte
de défauts, de l'identification et de la mesure dimensionnelle au
domaine de l'évaluation des propriétés intrinsèques
des matériaux, En conséquence, il devient un rôle
clé dans l'évaluation de la qualité des produits et les
matériaux.[9]
Basé sur les principes physiques qui sous-tendent les
principales méthodes CND telles que la radiographie, les techniques
électromagnétiques par courants de Foucault, la
perméabilité incrémentale, les techniques d'inspection de
surface pour les processus de flux de fuite, le ressuage, l'inspection optique
et les ondes ultrasonique.
Dans notre étude on a choisi la méthode non
destructive par ultrasons pour le contrôle de notre matériau
étudié. (Plus de détails dans les chapitre II et chapitre
III)
CHAPITRE I Matériaux composites pour
l'aéronautique
8 | P a g e
I.4. Les matériaux composites
Les matériaux composites ne sont pas nouveaux, ils ont
été utilisés par l'homme depuis la nuit des temps, comme
le bois, le béton et le béton armé.
I.4.1. Définition
Les composites représentent un assemblage de deux
matières ou plus d'une nature différente ce qui donne naissance
à un nouveau matériau hétérogène avec des
propriétés spécifiques [10]. Il est
composé d'une matrice et un renfort.
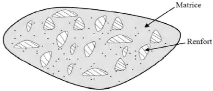
La matrice est une matière qui relie les renforts de
différents types comme il est montré sur la Figure I.6
:
Figure I.6 : Les constitutifs
d'un matériau composite [7] Ainsi, pour décrire
un matériau composite, il sera nécessaire de spécifier
:
Ø La nature des constituants (matrice) et leurs
propriétés.
Ø La géométrie du renfort avec sa
distribution.
Ø La nature de l'interface matrice/renfort.[10]
I.4.2. Les deux types de composites
I.4.2.1. Les composites GD
Les composites de grandes diffusions représentent 95%
des composites utilisés. Ce sont généralement des
plastiques renforcés. Dans 90% des cas, le taux de renforcement est
d'environ 30%. L'anisotropie est absente ou non maîtrisée car les
renforts sont des fibres courtes. Les principaux composants de base sont la
résine polyester (95 % de résine thermodurcissable) et la fibre
de verre (plus de 99 % de renfort utilisé).
I.4.2.2. Composites HP
Les composites de hautes performances dérivés de
matériaux fibrés sont utilisés en grand nombre pour des
applications nécessitant une reprise à des niveaux de
sollicitations au moins identiques à ceux rencontrés dans les
structures métalliques. Le secteur des transports, principalement
utilisé pour l'aviation, est coûteux. Les renforts sont des fibres
assez longues. Le taux de renfort est élevé, ce sont les renforts
qui impactent le coût. Les propriétés mécaniques
(résistance mécanique et rigidité) sont largement
supérieures à celles des métaux.[6]
CHAPITRE I Matériaux composites pour
l'aéronautique
9 | P a g e
I.4.3. Classification des matériaux composites
I.4.3.1. Suivant la forme des renforts
Les matériaux composites sont classés suivant la
forme des renforts utilisés, à savoir un renfort à fibres
courtes et continues ou à particules comme elle montre la Figure
I.7 ci-dessous :
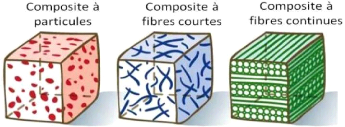
Figure I.7 : Les
différents renforts pour le matériau composite [11]
· La valeur des composites à fibres
justifié une étude exhaustive de leurs comportements
mécaniques excellents[10]. En conséquence, ce
mémoire sera essentiellement consacré par la suite à
l'étude de ce type de matériaux dans le domaine de
l'aéronautique.
I.4.3.2. Suivant la nature des matrices
Cependant, les renforts ou les fibres ne peuvent pas
être utilisés directement pour des applications mécaniques.
D'où l'idée de les incorporer dans une matrice pour former des
composites fibreux.
La matrice a alors différentes fonctions : lier les
fibres entre elles, transférer les charges mécaniques aux fibres,
protéger les fibres du milieu extérieur, etc.
Les composites sont classés en composites à
base d'une matrice organique (dans notre cas est la résine), à
base d'une matrice métallique ou à matrice minérale.
Les matériaux composites à matrice organique se
trouvent dans le domaine des températures ne dépassant pas 300
°C, alors que celles à matrices métallique et
minérale sont utilisées jusqu'à 600 °C pour une
matrice métallique et jusqu'à 1000 °C pour une matrice
céramique[10].
· La Figure I.8 détaille les
différents natures de renforts et des matrices utilisées pour
constituer un matériau composite.
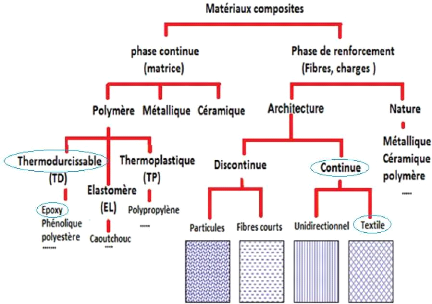
CHAPITRE I Matériaux composites pour
l'aéronautique
10 | P a g e
Figure I.8 : Différentes
bases pour classification des composites[12]
I.4.4. Interface renfort / matrice
L'interface est définie comme une zone
particulière d'épaisseur quasiment nulle formée par une
frontière commune entre le renfort et la matrice, elle assure la liaison
entre ces entités pour le transfert de charge et constitue une zone
clé pour l'optimisation des propriétés mécaniques
des matériaux composites, cette zone est considérée comme
un constituant du composite car elle possède des
propriétés physiques, chimiques et mécaniques
différentes de celles de la fibre et de la matrice.
Ces propriétés sont difficilement accessibles
expérimentalement et la plupart des données sont obtenues
à partir des modélisations sur la réponse mécanique
des composites, Par contre, à l'échelle réelle,
l'épaisseur de cette interphase peut être mise en évidence
de plusieurs manières à l'aide d'analyse viscoélastique et
fluage thermo stimulé. Dans une matrice composée des charges de
verre ensimées en résine époxy l'épaisseur de
l'interphase est de 1,4 à 1,75 um.[13]
Il est possible d'identifier trois couches avec une
stabilité hydrolytique différente : une couche
physisorbée, une couche tridimensionnelle et une couche interfaciale.
v Le schéma d'interphase renfort/ matrice est
représenté dans la Figure I.9 suivante :
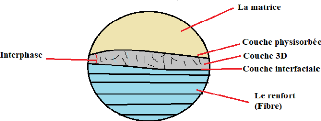
CHAPITRE I Matériaux composites pour
l'aéronautique
11 | P a g e
Figure I.9 : l'interphase entre
la matrice et le renfort
Le rôle des fibres est de supporter la grande partie de
la contrainte, par contre, celui de la matrice est la redistribution et le
transfert des charges d'une fibre à l'autre via l'interface. Le
rôle de la zone interfaciale est primordial pour améliorer les
performances finales du composite. La quantification de l'adhérence est
généralement évaluée par des tests
micromécaniques consistant à étudier une fibre unique
enrobée de résine.
Une interphase très cohésive permettra aux
fissures de se propager perpendiculairement à l'axe des fibres et
entraînera une rupture de l'échantillon. Une interphase moins
résistante, permettra de dévier la fissure vers l'interphase et
de limiter son impact à quelques fibres uniquement[6].
· Les interfaces fibres/matrices sont supposées
parfaites et ne sont pas considérées dans les calculs de cette
étude.
I.4.5. Les différentes structures des
matériaux composites
Ils peuvent être classées en trois types liés
un par rapport aux autres :
1. Les monocouches
Représentent l'élément de base de la
structure composite stratifié et sont constitué d'un seul pli de
renfort, est souvent appelée une strate.[6]
2. Les stratifiés
Sont constitués par plusieurs monocouches successives
(2 ou plus) de même ou de différentes orientations des renforts.
(Voir le schéma de la Figure I.10)
Les stratifiés sont utilisés comme des
matériaux structuraux, où on a, la nécessité
d'excellentes performances mécaniques en termes de résistance,
rigidité, comportement à la fissuration, et l'exigence de limite
en poids.

CHAPITRE I Matériaux composites pour
l'aéronautique
12 | P a g e
Figure I.10 : Monocouches
constituant le stratifié.
3. Les composites sandwiches
Sont constitués d'un nid d'abeille (une matière
résineuse, mousse ou en aluminium) entre deux surfaces des composites
stratifiés (Figure I.11) pour faire face à
l'effort tranchant.
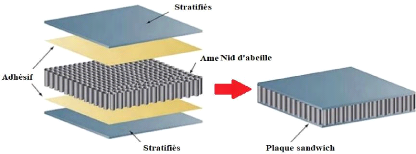
Figure I.11 : Schéma d'un
composite sandwich
I.5. Aspect physico-mécanique des structures
composites
Dans le domaine de l'espace et de l'aviation (Hautes
performances), on cherche des matériaux les plus performants possible en
mesure de sécurité, un module élevé avec une masse
volumique faible. Ça nous conduira automatiquement à des
composites.
I.5.1. Densité
La densité ou la masse volumique est la grandeur physique
qui caractérise la masse des substances par leur unité de volume
et déterminée par la méthode de balance hydrostatique et
calculé numériquement par la formule suivante :
ñr = ñe * mr /mr - (mf
- mp) (1)
CHAPITRE I Matériaux composites pour
l'aéronautique
13 | P a g e
Avec :
ñr densité d'échantillon.
(g/cm3)
ñe densité de liquide d'immersion.
(g/cm3)
mr masse d'échantillon en air. (g)
mf la masse du support de tube à essai et de l'ensemble
tube à essai dans le liquide
d'immersion à la fin du temps de séjour. (g)
mp la masse du porte-échantillon dans le liquide
d'immersion. (g)
I.5.2. Fractions volumiques et massiques
I.5.2.1. Fraction massique
Les fractions massiques Pf et Pm
sont définies à partir des masses pc, pf,
pm respectives de matériau composite, de fibres et de
matrice par l'essai de calcination (essai dit de perte au feu).
Avec pf + pm = pc (2)
D'où : ???? = ???????? (3)
???? = ???? (4)
????
I.5.2.2. Fraction volumique
Considérons un composite de volume Alc,
composé de fibres de volume ??f et d'une matrice de volume
??m.
Avec íc = íf + ím
(5)
La fraction volumique de fibres Vf et de matrice
Vm est donnée respectivement par :
???? ???? = ???? (6)
???? = ???? (7)
????
· La relation entre les fractions volumiques et
massiques fait intervenir les masses volumiques. Les masses volumiques
ñc, ñf, ñm respectives du
matériau composite, des fibres et de la matrice sont liés par les
relations suivantes[10]
On a: ???? = ???? ???? (8)
???? = ???? ????, (9)
???? = ???? ???? (10)
CHAPITRE I Matériaux composites pour
l'aéronautique
14 | P a g e
Et la fraction volumique des fibres Vf (taux de fibres)
est déterminée par la formule suivante :
????
???? = ???? * ????-???? .(????-????) 100% (11)
????= Masse volumique de fibres ????= Masse volumique de la
résine P??= Fraction massique de fibres
Avec la fraction V de la matrice : ???? = 100 - ????
(12)
I.5.3. L'isotropie des matériaux composites
Un matériau isotrope signifie que les
propriétés de ce matériau sont supposées identiques
dans toutes les directions de l'espace. Elle dépend essentiellement pour
le composite de l'orientation de renfort d'une manière :
Ø Lorsque l'orientation est aléatoire, le
comportement des composites est à peu près isotrope.
Ø Lorsque l'orientation suit une ou plusieurs
directions préférentielles comme dans le cas des fibres, le
comportement est anisotrope.[14]
I.6. La fabrication des matériaux
composites
La mise en oeuvre des composites se fait selon
différentes méthodes de moulage et ça selon
l'imprégnation du renfort par le système résineux et la
mise en forme à la géométrie de la pièce, Ces
méthodes sont généralement faciles à
exécuter et demandent un coût d'investissement faible en
matériels.
On va décrire le principe de quelques techniques
importantes pour les procédés d'élaboration des composites
dans cette partie qui sont en totale :
1. Moulage par contact.
2. Moulage sous vide.
3. Moulage par compression.
4. Moulage par centrifugation.
5. Moulage en continu.
6. Moulage par pultrusion.
7. Moulage par projection simultanée.[10]
CHAPITRE I Matériaux composites pour
l'aéronautique
I.6.1. Moulage au contact
C'est la méthode la plus simple qui ne demande pas
beaucoup d'équipements. On utilise des moules sur lesquels on
dépose successivement : un agent de démoulage, une couche de
surface et des couches successives des renforts imprégnés au
rouleau d'une résine polymérisée à la
température ambiante.
· Les moules sont de différentes matière soit
en plâtre, résine, bois ou en métal [7]
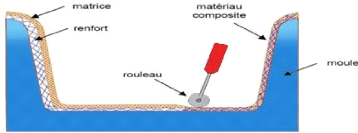
Figure I.12 : Schéma de
moulage au contact.
I.6.2. Moulage sous vide
Cette méthode dite du sac permet l'obtention de
plaques avec un taux minimum de résine [6], Elle implique
l'utilisation à la fois du vide et de la pression
atmosphérique.
Après le revêtement de moule avec un agent de
démoulage et une fine couche de résine sur la surface, le renfort
est placé sur un moule rigide et la matrice est coulée. Cette
Contre-moule, recouvert d'un film (feuille de nylon) pour assurer
l'étanchéité. [7]
La pompe à vide crée un vide qui permet
à la résine de se diffuser dans les renforts fibreux et
cavités. Cette méthode pourrait être combinée avec
un système de chauffage qui servirait à polymériser la
résine plus rapidement.[15]
Est un procédé de meilleure qualité que
le moulage par contact car il permet d'obtenir des plaques sans défaut
de produits composites aux formes complexes.
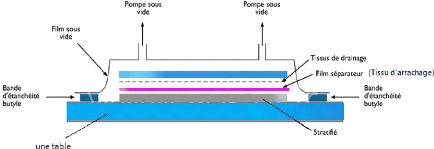
Figure I.13 : Moulage sous
vide
15 | P a g e
CHAPITRE I Matériaux composites pour
l'aéronautique
16 | P a g e
I.6.3. Moulage par compression
Le moulage par compression est l'un des
procédés les plus économiques pour la production de
grandes séries de pièces de petites et de moyennes
dimensions.[15]
La mise en forme par compression consiste à disposer
dans un moule les composants prés imprégnés. Sous l'action
du coulisseau de la pression, le contre-moule applique une pression sur le
volume de matière qui se trouve à l'intérieur du moule.
Le renfort et la matrice se déplacent afin de remplir
la cavité de l'outillage. Souvent, la pression exercée est de
l'ordre de 20 à 40 bars. Une polymérisation partielle est
effectuée à l'intérieur du moule et la pièce est
ensuite retirée afin que la polymérisation puisse continuer
à l'extérieur du moule. Ceci permet à l'outillage
d'accueillir plus rapidement une nouvelle pièce à
fabriquer[16]
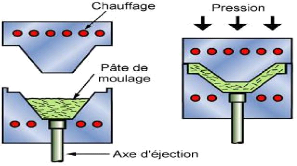
Figure I.14 : Moulage par
compression [15]
I.7. Intégration des matériaux
composites dans l'aéronautique
Les matériaux composites ont une bonne
résistance aux chocs et au feu, et assurent une meilleure isolation
thermique, acoustique et électrique. De manière
générale, les solutions composites sont toujours un saut
technologique pour les industriels car les composites offrent des
possibilités de réaliser des produits spécifiquement
adaptés aux propriétés recherchées.[17]
La direction privilège de chaque couche qui compose le
stratifié de composite permet une conception spécifique pour
chaque situation en charge et donc un poids réduit par rapport à
la conception d'un matériau métallique dont les
propriétés sont les mêmes dans toutes les directions. Cette
orientation est obtenue en alignant des fibres bidirectionnelles très
dur, en carbone ou en verre, dans une matrice plus souple (une
résine).[18]
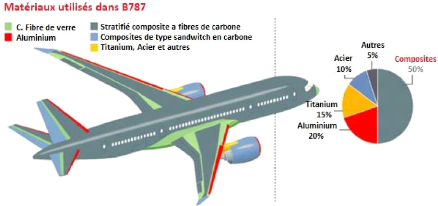
CHAPITRE I Matériaux composites pour
l'aéronautique
17 | P a g e
Figure I.15 : Taux des
matériaux composites dans la structure de Boing787 [18]
Dans la Figure I.15 ci-dessus un dessin qui
décrit la distribution de différentes natures des
matériaux dans la structure d'un aéronef (B787) ou le composite
représente 50%.
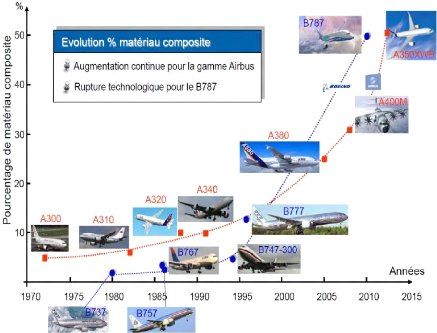
Figure I.16 : Evolution
d'intégration des matériau composite dans aéronefs
[17]
CHAPITRE I Matériaux composites pour
l'aéronautique
18 | P a g e
L'utilisation des matériaux composites depuis les
années 1970 dans la fabrication des avions ne cesse
d'augmenter[17] , D'après la Figure I.16, on
constate qu'en 40 ans, on est passé de moins de 9% en composite à
plus de 50% de la masse totale des matériaux. L'A380 est près de
25% au poids, et l'A350XWB est supérieur à 50% en poids dans
l'année 2015. Le Boing777 présente une valeur de 12% du composite
dans l'année 1995 tandis que le Boing787 présente un saut
technologique avec 50% de composite en 2010.
A savoir aussi que tous les avions de la nouvelle
génération sont constitués d'un pourcentage
élevé de matériau composite non seulement en fuselage mais
aussi pour l'équipement intérieur de l'avion.
I.7.1. Les avantages des matériaux composites pour
utilisation aéronautique y' Ils sont associés à de
nombreuses possibilités de conception ce qui permet de
construire des avions de plus en plus légers,
réduisant ainsi les dépenses de carburant
et économisant ainsi combustibles fossiles et bien
sûr la réduction de la pollution. y' Une grande résistance
à la fatigue entraîne donc une maintenance réduite.
y' Insensibles aux produits chimiques "mécaniques "
comme les graisses, huiles, peintures, solvants et le pétrole.
y' Faible vieillissement sous l'action d'humidité, de
la chaleur et de la corrosion (sauf en cas de contact entre l'aluminium et les
fibres de carbone).[7,19]
I.7.2. Les inconvénients des matériaux
composites destinés à l'aéronautique
· Le vieillissement sous l'action d'eau et de la
température (la température est basse lorsque l'avion est en vol
mais élevée dans le hangar des avions par exemple au
désert ou la température peut dépasser 50 °C).
· Tenue à l'impact moyenne par rapport aux
métaux.
· Emission de fumées parfois toxiques pour
certaines matrices en cas de feu[2].
I.8. Les exigences des matériaux composites
stratifiés en aéronautique
Les composites renforcés de fibres à base de
résines thermodurcissables permettent d'atteindre d'excellentes
performances mécaniques sont très appropriées pour
l'aéronautique et les voitures premium de course[20]. A ce
critère est venue s'ajouter depuis plusieurs années et d'une
manière cruciale, une exigence de dimensionnement à la fatigue.
La raison en est que les matériaux composites ne sont plus
confinés à des parties dites secondaires, c'est-à-
CHAPITRE I Matériaux composites pour
l'aéronautique
19 | P a g e
dire ne reprenant que peu d'efforts, mais à des
structures primaires largement sollicitées, pour lesquelles une
sécurité accrue est exigée.[21]
Pour de nombreux stratifiés aérospatiaux, chaque
pli a une épaisseur comprise entre 0,1 et 0,25 mm et contient des fibres
noyées dans une fine couche de matrice polymère.
Dans un stratifié, l'orientation des fibres par rapport
à la direction de chargement principale peut varier d'un à
l'autre. L'ordre dans lequel les strates avec différentes orientations
de fibres sont empilées est appelé la séquence
d'empilement et est conçu pour obtenir la rigidité et la
résistance souhaitée pour le stratifié.
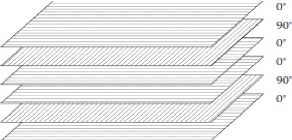
Figure I.17 : Stratifié
à plis de construction [0/90/0/0/90/0°] [22]
Les couches à 90° aident à réduire
la fissuration entre les fibres dans les couches à 0°, ce qui est
souvent un problème si la structure ne contient que des fibres à
0°.
I.9. Conclusion
Les principales raisons d'utiliser des matériaux
composites dans la structure d'aviation en première classe consiste
à réduire la masse tout en maintenant l'excellence du
comportement mécanique.
Le changement d'orientation entre les couches de renforts dans
le stratifié aident à réduire la fissuration entre les
fibres donc améliorer les propriétés mécaniques de
ces composites.
CHAPITRE I Matériaux composites pour
l'aéronautique
20 | P a g e
Références du chapitre
I
1. Summerscales, J.,
Microstructural characterisation of fibre-reinforced composites. 1998: CRC
Press.
2. Costa, J.P.M.r., Caractérisation et
modélisation des interfaces dans les composites organiques
stratifiés à haute température: Application à la
tenue au feu des structures aéronautiques, 2021, ISAE-ENSMA Ecole
Nationale Supérieure de Mécanique et
d'Aérotechique-Poitiers.
3. Pommier, S., Science des Matériaux (LA
314).
4. Jean Pierre Mercier, Gérald Zambelli, Wilfried
Kurz, Introduction à la science des matériaux, PPUR,
1999
5. Charmet, J.-C., Mécanique du solide et des
matériaux
Elasticité-Plasticité-Rupture. ESPCI-Laboratoire
d'Hydrodynamique et Mécanique Physique, 2005: p. 113-144.
6. Aribi, C., Étude comparative du comportement
des différents matériaux composites (différentes
matrices), 2012, Université de Boumerdès-M'hamed Bougara.
7. Basaid, Djamel. <i>Simulation Numérique
Du Comportement Macroscopique Des Matériaux
Hétérogènes À Matrice Élastique Et Inclusion
Élastoplastique Pour L'utilisation En Construction
Aéronautique</i>. 2019. Université M'hamed Bougara -
Boumerdes, Thèse de Doctorat.
8. Hertz-Clemens, S., Etude d'un composite
aéronautique à matrice métallique sous chargements de
fatigue: sollicitation mécano-thermique et propagation de fissures,
2002, École Nationale Supérieure des Mines de Paris.
9. Dumont-Fillon, J., Contrôle non destructif
(CND). 1996: Ed. Techniques Ingénieur.
10. Berthelot, J.-M., Matériaux composites.
Comportement mécanique et analyse des structures, 1999.
4.
11. Latifa, M.B.H., Elaboration de matériaux
composites biodégradables issus de ressources renouvelables, 2016,
Université de Mostaganem.
12. Friedrich, K., L. Chang, and F. Haupert, Current and
future applications of polymer composites in the field of tribology, in
Composite materials. 2011, Springer. p. 129167.
13. Ledru, Y., Etude de la porosité dans les
matériaux composites stratifiés aéronautiques,
2009.
14. Vannucci, P., Matériaux composites
structuraux, 2007, Université de Versailles
et Saint-Quentin-en-Yvelines.
21 | P a g e
CHAPITRE I Matériaux composites pour
l'aéronautique
15. Nguyen, A.V., Matériaux composites à
renfort végétal pour l'amélioration des performances de
systèmes robotiques, 2015, Université Blaise
Pascal-Clermont-Ferrand II.
16. Tossou, E., Développement de nouveaux
composites hybrides renforcés par des fibres de carbone et de lin:
mise en oeuvre et caractérisation mécanique, 2019, Normandie
Université.
17. Fendzi, C., Contrôle Santé des
Structures Composites: application à la Surveillance des Nacelles
Aéronautiques, 2015, Paris, ENSAM.
18. Kerfriden, P., Stratégie de
décomposition de domaine à trois échelles pour
la simulation du délaminage dans les stratifiés, 2008,
École normale supérieure de Cachan-ENS Cachan.
19. Chapuis, D., V. Aerts, and R. Bonneville, Chapitre 4:
Les nouveaux matériaux composites pour l'aéronautique par
Vincent Aerts, in Chimie, aéronautique et espace. 2021, EDP Sciences. p.
75-84.
20. Monti, M., et al., Design, manufacturing and FEA
prediction of the mechanical behavior of a hybrid-molded
polycarbonate/continuous carbon fiber reinforced composite component.
Composites Part B: Engineering, 2022. 238: p. 109891.
21. Renard, J., Fatigue des matériaux composites
renforcés de fibres continues. 2010: Ed. Techniques
Ingénieur.
22. P.K.Malick. « Processing of Polymer Matrix
Composites ».CRC press Broken Sound Parkway NW (2018).
CHAPITRE II
Procédés d'élaboration
et
caractérisation des
matériaux
composites
II.1. CHAPITRE II Procédés
d'élaboration et caractérisation des matériaux
composites
22 | P a g e
CHAPITRE II Procédés
d'élaboration et caractérisation des matériaux
composites
23 | P a g e
Introduction
Dans ce chapitre, nous abordons l'étude
expérimentale en commençant par présenter la
procédure d'élaboration des éprouvettes composites, qui a
été réalisée au sein d'atelier plastique et
composite de la base de maintenance d'air Algérie. Il
s'agit du procédé de moulage sous vide, qui consiste à
fabriquer des plaques en composite de (40/40cm) après on les
découpes en éprouvettes de dimensions suivant les normes en
vigueur.
Suite à cette réalisation expérimentale
et en tenant compte des différentes recommandations tout au long de la
fabrication, nous concluons la partie par la mise en place d'un organigramme de
plan pour une élaboration fiable des stratifiés composite
aéronautique.
Dans notre étude nous avons utilisé des renforts
en fibres continues de verre et de carbone imprégnés dans une
matrice résineuse de type Epocast. Le choix du type de matrice et du
renfort est fait selon les exigences de la règlementation
aéronautique internationale et de la faisabilité
expérimentale de ce type de matériau.
Premièrement, on entame l'étude
expérimentale de nos matériaux obtenus en effectuant des
caractérisations physiques par des méthodes d'ATD/ATG, mesure de
densité, taux de fibres, et la caractérisation par la
méthode non destructive des ultrasons.
Par la suite, nous effectuons bien sûr des essais
mécaniques tels que la traction, flexion et la fatigue,
détaillés avec les résultats dans le chapitre suivant.
II.2. Matériaux
d'étude
Avant la fabrication d'une pièce en matériaux
composites, il faut préparer tous les outils nécessaires
concernant l'étude et l'élaboration de cette pièce et bien
sûr tous les matériaux de base.
II.2.1. Le matériel utilisé
La figure II.1, présente tous les outils
nécessaires :
· Une table de travail et une table pour les plaques des
stratifiés
· Renforts (fibres de carbone/verre), matrice
(résine Epocast et durcisseur).
· Pompe à vide, scotch double faces (mastic
d'étanchéité).
· Un nylon, un tissu de drainage et un tissu
d'arrachage.
· Les gants, les raclettes et les gobelets.
· Ciseaux, une règle et un scotch.
· Diluant (pour le nettoyage).
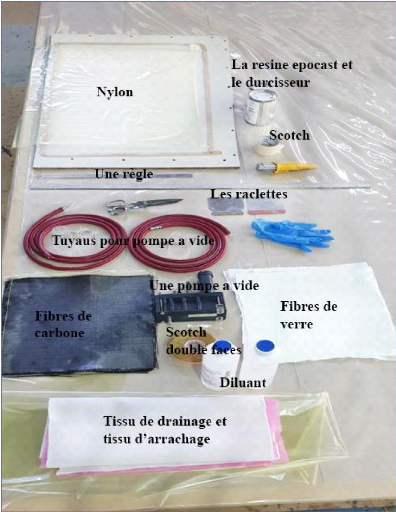
Figure II.1 : Outils pour
fabrication des plaques composites (air algérie)
II.2.2. Les renforts
Les renforts utilisés pour la réalisation des
éprouvettes sont des tissus de carbone, et de verre sous formes des
fibres continus bidirectionnels.
Voir les rouleaux dans la Figure II.2.
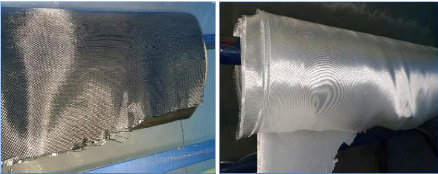
CHAPITRE II Procédés
d'élaboration et caractérisation des matériaux
composites
24 | P a g e
Figure II.2 : Rouleaux de fibres
de carbone et de verre bidirectionnel
Ces tissus de renfort sont constituée de deux couches
unidirectionnelles, l'une orientée à 0° et l'autre à
90° dite de type taffetas[1] voir dans la Figure
II.3.
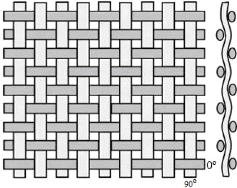
Figure II.3 : Dessin d'armure
taffetas (0/90°) [1J II.2.2.1. Caractéristiques des
fibres de carbone et de verre
II.2.2.1.a. Fibre de verre
Contrairement à l'état massif ou le verre est
très fragile du fait de sa forte sensibilité aux microfissures,
la conception de ce type de matériau se forme des fibres de faible
diamètre pour qu'il possède de bonnes performances
mécaniques est dû de la diminution des microfissures donc la
fragilité diminue. La matière première pour la fabrication
de ces fibres est composé de silice, alumine, magnésie,
etc.[1]
Il existe différents types de verre filable qui sont
résumés dans le Tableau II.1 :
CHAPITRE II Procédés
d'élaboration et caractérisation des matériaux
composites
25 | P a g e
Tableau II.1 : Différents
types de fibres de verre filables
Type des fibres de verre
|
Caractéristiques
générales
|
A
|
Haute teneur en alcali
|
C
|
Bonne résistance chimique
|
D
|
Haute propriétés
diélectrique
|
E
|
Bonne propriétés électrique
|
R, S
|
Haute résistance mécanique
|
Dans notre travail nous avons utilisé des fibres de
verre type D élaborées par une méthode de fibrage de verre
fondu (voir plus dans l'annexe).
II.2.2.1.b. Fibre de carbone
Les fibres de carbone appartiennent à la famille des
graphites, qui ont une structure hexagonale en atomes de carbone dispose en
plans cristallographique parallèle et décalé un par
rapport à l'autre.
La liaison entre les atomes de même plan est chimique
(un mélange des liaisons covalentes et métalliques). La liaison
covalente, qui résulte de l'hybridation sp2 de chaque atome
de carbone, est responsable du module et de la résistance
élevés dans le plan des couches de carbone. La liaison
métallique, qui est due aux électrons pz
délocalisés, est responsable de la conductivité
électrique élevée et de la conductivité thermique
élevée dans le plan des couches de carbone. Perpendiculaire aux
couches de carbone, la liaison implique des forces de van der Waals (liaison
secondaire).
En raison de la faible liaison inter couche, les couches de
carbone peuvent facilement glisser les unes par rapport aux autres. Dans les
fibres de carbone, les couches hexagonales sont disposées dans une
structure beaucoup plus amorphe, étant enroulées, pliées
et froissées les unes avec les autres. Cette structure amorphe ne permet
pas de déchirer les feuilles hexagonales et confère à la
fibre de carbone ses propriétés de matériau uniques avec
une résistance à la traction élevée et une
rigidité élevée.[2]
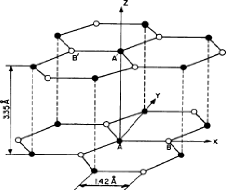
CHAPITRE II Procédés
d'élaboration et caractérisation des matériaux
composites
26 | P a g e
Figure II.4 : Structure
cristalline du graphite.
Les atomes A (cercles pleins) constituent une couche de
carbone, tandis que les atomes B (cercles vides) constituent la couche de
carbone adjacente[3] .
Elles sont obtenues par carbonisation de la fibre PAN (Poly
acrylonitrile).[1]
v Les caractéristiques de nos fibres utilisées
dans ce travail sont mentionnées dans le tableau
II.2.
Tableau II.2 : Caractéristiques du
tissu de carbone et de verre
Fibres continues de carbone
|
Fibres continues de verre
|
Caractéristiques
|
Valeurs
|
Caractéristiques
|
Valeurs
|
Architecture
|
TAFTAS
|
Type
|
D (diélectrique)
|
Géométrie des fibres
|
Rectangulaire
|
Géométrie des fibres
|
Cylindrique
|
Epaisseur (mm)
|
0.2
|
Epaisseur (mm)
|
0.1
|
Résistance à la
traction (N/mm2)
|
330
|
Résistance à la
traction (N/mm2)
|
140.29
|
Élongation (%)
|
1.9
|
Nombre de filament Par fibre
|
75
|
Poids spécifique (g/m2)
|
193
|
Poids
spécifique (g/m2)
|
106
|
CHAPITRE II Procédés
d'élaboration et caractérisation des matériaux
composites
27 | P a g e
II.2.2.2. Préparations des renforts
D'après les rouleaux des tissus de fibres de verre et
de carbone (Figure II.2) on coupe deux surfaces larges pour
l'extraction des plis de nos stratifiés, ensuite :
(1) On mesure avec une règle 40/40 cm du tissu de fibre
de verre et celle de carbone.
(2) On découpe 8 couches des deux fibres (Carbone/Verre)
en utilisant un ciseau.
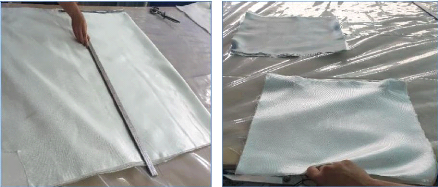
1 2
Figure II.5 : Préparation
des renforts (Etape de découpage)
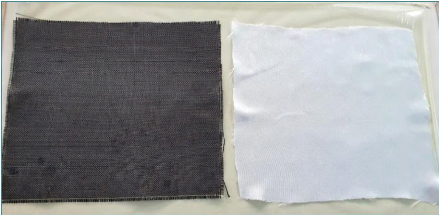
Figure II.6 : Tissus des Fibres
de carbone et de verre (taffetas)
II.2.3. La matrice
Les matériaux composites à matrice
polymère sont de plus en plus utilisés en aéronautique
à cause de leur faible masse. C'est un mélange homogène de
résine (EPOCAST 50-A1) et de durcisseur (HARDENER 946 US) qui se
présente comme un agent de
CHAPITRE II Procédés
d'élaboration et caractérisation des matériaux
composites
28 | P a g e
réticulation[4]. Ces ratios sont
basés sur les normes spécifiées par le fabricant, qui
nécessite un mélange de 100 grammes de résine pour 15
grammes de durcisseur. Figure II.7.
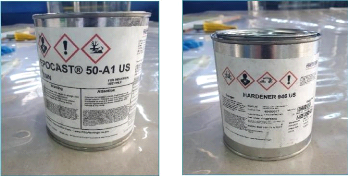
A B
Figure II.7 : A. Résine
EPOCAST 50-A1. B. Durcisseur (HARDENER 946)
II.2.3.1. Caractéristiques de la résine
Est une résine thermodurcissable utilisé pour la
stratification à cause de sa facilité à être
manipulée. Et peut être utilisé dans la fabrication ou la
réparation de structures composites aéronautiques. Les produits
sont conformes à la norme BMS 8-201.
Des détails supplémentaires sur cette
résine sont mentionnés dans la fiche technique fournie par le
fournisseur (Tableau II.3)
Tableau II.3 :
Caractéristiques des Epocast 50-A1/946
Caractéristiques
|
Valeurs
|
Densité g/cm3
|
2
|
Coefficient de dilatation thermique 10k
|
35
|
Résistance en compression MP
|
140
|
Module d'élasticité en compression
MP
|
11000-11500
|
Résistance en flexion MP
|
110
|
II.2.3.2. Préparation de la matrice
La quantité de résine nécessaire par
mètre carré de tissu a été calculée à
partir des normes imposées par le constructeur (Airbus) qui impose
375g de résine pour 1 m2 de
tissu (pour une seule couche).
· CHAPITRE II Procédés
d'élaboration et caractérisation des matériaux
composites
Calcule de la masse de résine et durcisseur de nos
plaques composites : La surface d'une couche de fibre (Sf) est de :
Sf=400mm*400mm=160000mm2 On a un stratifié de 8 couches donc
la surface totale St est de : St=8*160000=1280000mm2 La
quantité de résine plus durcisseur a appliqué M sera :

1m2 375g
1.28m2 M
M= 480g
29 | P a g e
Donc la masse totale pour imprégner 8 couches de
40/40cm est 480grammes (en epocast + durcisseur) donc par un petit calcul on
trouve la masse de durcisseur et d'Epocast qu'on doit mélanger.
480 X 15
100
= 72 g en durcisseur
480 - 72 = 408 g d'epocast
· Dans notre cas on a deux plaques
élaborées donc on a consommé le double de cette
résine.
Finalement on suivra les étapes suivantes pour
l'utilisation de la résine.
1. On pèsera la bonne quantité de la résine
Epocast (408 grammes)
2. On ajoute la quantité nécessaire du durcisseur
72 g
3. Après un mélange à peu près de
3 min on voit que la couleur de notre résine est homogène, Donc
notre matrice est prête à utiliser.
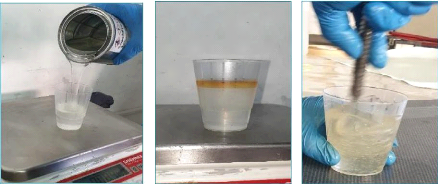
1
2
3
Figure II.8 : Etapes de
préparation de la matrice Epocast 50-A1
CHAPITRE II Procédés
d'élaboration et caractérisation des matériaux
composites
30 | P a g e
II.2.4. Tissu d'arrachage
Sont des tissus antiadhésifs présentent
plusieurs avantages lorsqu'ils sont utilisés sous vide. Ce tissu est
connu pour la finition de surface qu'il confère aux pièces des
composites, il permet aussi d'absorber la quantité de résine
surplus et il évite également l'adhésion de
l'échantillon à tous les tissus lors de la dissociation (lors du
démoulage).
II.2.5. Feutre de drainage
Son rôle est d'absorber la quantité de
résine supplémentaire aussi et de la piéger pour qu'il n'y
ait pas de débordement, et aussi il assure la bonne répartition
de l'aspiration de l'air dans le système sous vide. Il est connu aussi
sous le nom (de la ouate).
|
|
Figure II.9 : Tissu
d'arrachage
|
|
|
Figure II.10 : Feutre de
drainage
|
Tableau II.4 :
Caractéristiques du feutre de drainage
Caractéristiques
|
Valeurs
|
Matière
|
Fibres 100% polyester
|
Couleur
|
Blanc
|
Epaisseur (mm2)
|
4
|
Poids nominal (g/m2)
|
150
|
Température d'utilisation (?)
|
205
|
Température de fusion (?)
|
250
|
II.3. Procédure de
fabrication
La réalisation des éprouvettes stratifiés
carbone/époxy, verre/époxy de huit plis est faite par un moulage
sous vide en ajoutant la résine sur la surface des fibres et
l'étaler en utilisant la raclette comme vous montre en détails
dans les étapes et les figures jointes suivantes :
CHAPITRE II Procédés
d'élaboration et caractérisation des matériaux
composites
En premier lieu, après le malaxage de la
résine et le durcisseur en respectant le taux de pourcentage 100/15, en
étale une couche d'imprégnation sur le film inférieur
utilisé pour l'étanchéité et sur la
1ère couche des renforts.
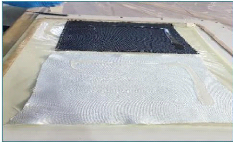
Figure II.11 :
Imprégnation de résine sur les 1ères couches de
fibres
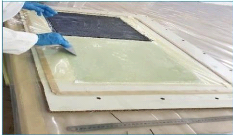
En deuxième étape on dépose les
couches des tissus sur la 1ère couche de renfort, de la
même façon que la première on étale une autre couche
de résine sur ces plis et en pose un autre pli, cette opération
est répétée jusqu'au huitième couches, ce sont tous
de même orientation (0.90°)
Figure II.12 : Imprégnation
de résine de 8 couches successives
Troisièmement, on pose directement le tissu
d'arrachage qu'est découpé selon les mêmes dimensions de
nos renforts. Et faire rentrer les deux tuyaux de la pompe sur les
côtés pour effectuer par la suite l'opération d'aspiration
de l'air.
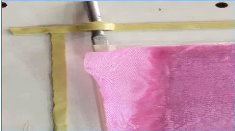
Figure II.13 : Dépôt
du tissu d'arrachage
31 | P a g e
CHAPITRE II Procédés
d'élaboration et caractérisation des matériaux
composites
32 | P a g e
Ensuite, on pose le tissu d'absorption (de drainage)
qu'est découpé de même dimensions qui couvre toute surface
du moule limité par le mastic d'étanchéité, en le
plaçant ainsi sur les tuyaux de la pompe à vide avant la
fermeture de notre système.
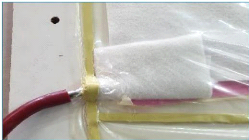
Figure II.14 : Dépôt
de tissu de drainage
Finalement on utilise un film plastique pour la
fermeture, d'où le but de son utilisation est
l'étanchéité l'ensemble de système et
réaliser la dépression par le système de création
de vide utilisé et coller ses extrémités avec le mastic
d'étanchéité pour éviter tout risque de fuite.
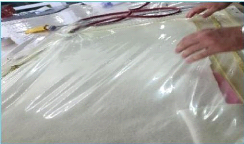
Figure II.15 : Dépôt
de film plastique pour fermeture du système
II.3.1. L'étape de mise sous vide :
Cette étape consiste à laisser le système
sous vide pendant 6 à 8 heures comme vous montre dans la Figure
II.16, afin de réaliser la polymérisation
complète à température ambiante (25°C) pour
éviter les contraintes résiduelles.
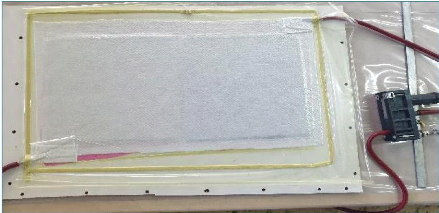
CHAPITRE II Procédés
d'élaboration et caractérisation des matériaux
composites
Figure II.16 : Système
d'élaboration des plaques composites sous vide
v Les étapes de la mise en forme par ordre chronologique
sont décrites dans ce plan suivant :


Découper les tissus de renforts et les tissus
d'arrachage et de drainage
Préparer le mélange de la résine
epocast avec 15% du durcisseur
Enduire la résine sur les 8 couches des fibres de
carbone et de verre


Enlever les tissus d'arrachage et de drainage de
nos plaques composite.
Fermer le système et laisser les
stratifiés sous vide pendant 6h à Ta
33 | P a g e
Ensuite le système est démoulé et on
obtient deux plaques stratifiées de dimensions 40x40cm et
d'épaisseur 2.1mm, (Figure II.17).
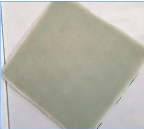
A

B
Figure II.17 : A. Plaque
composite fibre de verre. B. Plaque composite fibre de
carbone
CHAPITRE II Procédés
d'élaboration et caractérisation des matériaux
composites
· La fabrication des éprouvettes pour les tests
mécaniques nécessite un découpage préalable des
plaques, en respectant la forme et les dimensions relatives aux normes en
vigueur. En plaçant ainsi les talons en aluminium pour s'assurer que le
matériau testé est sous traction pure et ne subit pas les
contraintes et déformations imposées par les mors de
|
|
machine.
|
Figure II.18 : Découpage
selon les normes
|
II.4. Représentation des pièces pour
les essais mécaniques
La connaissance du comportement mécanique de composite
et sa structure permettant de comprendre et prédire son comportement en
service. Afin de faire la caractérisation nous avons recours à un
certain nombre d'essais mécaniques telle la traction et la flexion qui
nécessite des éprouvettes découpés selon les normes
internationales.
II.4.1. Eprouvettes de traction de la matrice
résineuse
Les dimensions des éprouvettes de la résine
Epocast préparer dans des moules, pour l'essai de traction sont aux
normes telles que définies dans la figure ci-dessous
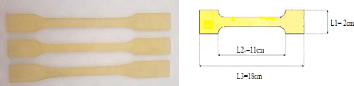
Figure II.19 : Eprouvettes sous
forme haltère
II.4.2. Eprouvettes de traction des stratifiés
composites
Les dimensions de l'éprouvette d'essai de traction sont
aux normes ASTM D3039 telles que définies dans la Figure II.20
ci-dessous :
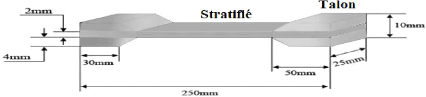
Figure II.20 : Dimensions des
éprouvettes de traction.
34 | P a g e
CHAPITRE II Procédés
d'élaboration et caractérisation des matériaux
composites
35 | P a g e
II.4.3. Eprouvette de l'essai de flexion
Les éprouvettes d'essai de flexion sont
préparées en forme rectangulaire plane dont la longueur est de 80
mm et la largeur est de 10 mm. Selon la norme ASTM D7264 comme définies
dans la Figure II.21 suivante :
b = 10mm (Largeur ) h = 2.1mm
(Epaisseur) l = 80mm (Longueur)
|
|
Figure II.21 : Dimensions des
éprouvettes de flexion
II.5. Les machines utilisées pour les essais
mécaniques
Les essais mécaniques sont réalisés
à l'aide des machines en traction et de flexion situés au centre
de recherche (CNERIB) pour la machine de traction de type MTS, et à
l'unité de recherche (UR-MPE) pour la machine de flexion trois points de
type Zwick.
(Voir Figure II.22).
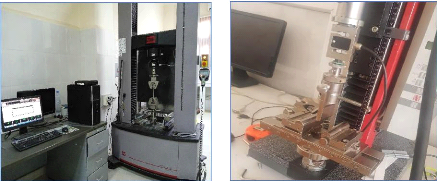
a
b
Figure II.22 : a. Machines de
traction et b. machine de flexion 3 points
II.6. Caractérisation des stratifiés
composites élaborés II.6.1. Caractérisation
physique
III.6.1.1. Analyse thermique (ATD, ATG)
Les analyses thermiques ATD et ATG sont effectuées au
niveau de l'UR- MPE à l'aide de l'appareil de type STA NETZSCH
(Simulaneous Themal Analysis) 409. Ce dernier est basé, d'une part, sur
la mesure différentielle de l'effet thermique à l'aide de deux
piles thermoélectriques et, d'autre part, sur la mesure de la chute de
masse sous l'effet de la
CHAPITRE II Procédés
d'élaboration et caractérisation des matériaux
composites
36 | P a g e
température. Cette technique fait partie de la norme
NF-EN31357-2 (plastique. Analyse calorimétrique
différentielle).
La Figure II.23. Présente l'appareil
STA 409 constitué de deux cellules identiques (échantillon et
référence) scellées dans un bloc hermétique
programmé en température et équipé d'une balance
pour l'analyse thermogravimétrique.
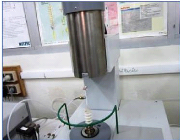
Figure II.23 : Appareil de
DSC
II.6.1.2. Détermination de la masse volumique
La masse volumique réelle (pour les matériaux
à l'état compact, comme le cas des composites stratifiés)
est déterminée suivant la méthode (par immersion à
la balance hydrostatique), cette méthode, basée sur le principe
d'Archimède, est plus précise qu'un simple rapport masse sur
volume.
Les masses volumiques sont déterminées sur une
moyenne de trois échantillons, par double pesée à
23°C. Les échantillons sont plongés dans un liquide ayant un
bon pouvoir mouillant et une densité connue, comme l'eau
(ñe= 0,998 g/cm3 à 23°C et 1 atm).
La balance analytique est équipée d'un
dispositif de mesure et d'un logiciel qui permet de donner directement la masse
volumique de l'échantillon, en introduisant les valeurs massiques
à l'air libre et sous l'eau.
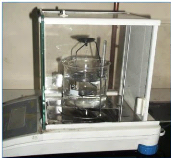
Figure II.24 : Banc de
pesage.
CHAPITRE II Procédés
d'élaboration et caractérisation des matériaux
composites
37 | P a g e
II.6.1.3. Taux massique et volumique du renfort
Le taux massique est déterminé par la
méthode de la perte au feu, applicable aux fils et stratifiés.
L'échantillon est de forme carrée, cette dernière est
pesée la première fois à la température ambiante
(Ma). Puis, elle est placée dans un four à 700 °C
pendant 1 heure afin de brûler la résine. Le renfort restant est
alors pesé (Mf). Le taux massique de renfort Tm est
déterminé par la formule suivante :
???? = (???? / ????) (1)
Le taux volumique Tv peut être déterminé par
la relation suivante :
???? = (????/ ????) ???? (2)
Voici dans la Figure II.25 une image de four
électrique utilisé pour la mesure de taux de renforts pour des
échantillons de dimensions 2/2 cm.
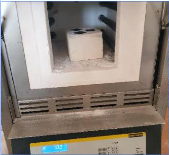
Figure II.25 : Four
électrique.
II.6.1.4. Contrôle non destructif par ultrasons
· Mesure des caractéristiques
mécaniques de matériau composite
Les ultrasons sont des vibrations mécaniques à
très haute fréquence avec des fréquences allant de 16 kHz
à 150 MHz. Le CND est une méthode d'étude de l'absence de
matière (défauts ou fissures) dans un
matériau[5].
Elle consiste à observer les échos dus au manque
de matière lors de la propagation de vibrations de très haute
fréquence et de très courte durée dans un matériau
contrôlé. Les vibrations sont transmises et reçues par le
même capteur, qui est connu pour convertir les signaux électriques
en vibrations mécaniques et vice versa. L'impulsion sonore émise
se propagera à travers le matériau et sera
réfléchie par tout obstacle sur son chemin.
CHAPITRE II Procédés
d'élaboration et caractérisation des matériaux
composites
38 | P a g e
Pour contrôler une pièce, le transducteur est
déplacé sur toute sa surface lors du déplacement et les
échos produits par les réflecteurs présents dans le trajet
des ondes sont observés sur l'écran de l'appareil à
ultrasons.[6]
On distingue les échos normaux sur la
géométrie de la pièce, des échos dus à un
éventuel défaut en prenant en compte le temps d'arrivée
des échos et la position de transducteur. Les principales applications
des ultrasons sont :
- La détection et caractérisation des
défauts.
- Analyse des propriétés mécaniques
- Mesure des contraintes appliquées et
résiduelles
- Détermination de la matrice de rigidité
La méthode de contrôle non destructif sur les
plaques composites stratifiés par ultrasons sert à évaluer
leurs propriétés mécaniques. Pour ce faire sur des
stratifiés [0°/90°] en résine époxy
renforcés par des fibres de verre et de carbone. Le mode de
contrôle par immersion en utilisant deux transducteurs nous a conduits
à des signaux qui permettent de mesurer le temps de vol dans un
échantillon et connaissant la distance entre les transducteurs, on en
déduit facilement les vitesses de propagation longitudinale et
transversale de l'onde de notre matériau d'après la relation
suivante :
(3)
2e
V = ?t
D'où les propriétés mécaniques sont
en relation avec la vitesse et la densité comme suit :
VL = v ??(1-o)
??(1+o)(1-2o) (4)
V?? = v ??
2??(1+o) (5)
Avec
e : L'épaisseur d'échantillon
?t : Le temps entre deux échos successifs sur
l'oscilloscope
VL : Vitesse de propagation de l'onde longitudinale
VT : Vitesse de propagation de l'onde transversale
?? : La masse volumique
E : Le module d'Young
o : Le coefficient de poisson
CHAPITRE II Procédés
d'élaboration et caractérisation des matériaux
composites
39 | P a g e
La méthode utilisée est dite de
contrôle par immersion :
Le contrôle par ultrason est réalisé au
niveau de centre de soudage et contrôle CRTI d'Alger, le dispositif
étant plongé dans l'eau afin de permettre une meilleure
propagation des ondes ultrasonores (voir Figure II.26). Le
transducteur, piézoélectrique est de marque Panametrics V326 de
fréquence de 5 MHZ, diamètre de 9.5 mm et d'une bande passante
à 3 dB varie entre 3.05 et 6.65 MHZ. Il peut être plus ou moins
éloignés de la pièce.
En utilisant un Oscilloscope pour afficher les courbes des
tensions détectées et un générateur d'impulsion
conventionnel de type OLYMPUS comme indique la Figure II.27
ci-après.
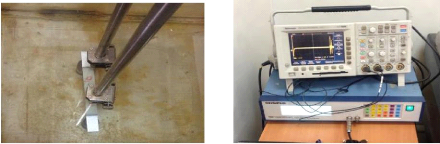
Figure II.26 : Banc de
contrôle par Figure II.27 : Oscilloscope et
immersion générateur
II.7. Conclusion
Dans ce chapitre on a montré les matériaux, les
outils et la procédure utilisée pour élaborer et
préparer les éprouvettes. Nous avons tenu à respecter dans
nos réalisations les normes en vigueur dans le domaine
aéronautique afin de mettre en évidence les conditions de
fabrication des composites considérés sur la réponse
mécanique des efforts de différentes natures.
On a obtenu des éprouvettes pour traction de 250 x 25
mm et pour flexion de 80 x 10 mm selon les normes exigées, et qui ont
été utilisées pour la caractérisation
mécanique expliquée dans le chapitre suivant.
Ainsi en décrivant toutes les méthodes
expérimentales utilisées pour les caractérisations.
CHAPITRE II Procédés
d'élaboration et caractérisation des matériaux
composites
40 | P a g e
Références de chapitre
II
1. Berthelot, J.-M., Matériaux composites.
Comportement mécanique et analyse des structures, 1999.
4.
2. Boris-Mahlting.Yordan kyosev. « Inorganic and
composite fibers: production, proprites and applications ».Edition
Woodhead, USA(2018)
3. Deborah D.L Chung. « Composite materials, second
edition ».Springer London Dordrecht Heidelberg, NewYork (2010)
4. Aribi, C., Étude comparative du comportement des
différents matériaux composites (différentes matrices),
2012, Université de Boumerdès-M'hamed Bougara.
5. Chevalier, Y., Essais dynamiques sur composites:
Caractérisation aux hautes fréquences. Techniques de
l'ingénieur. Plastiques et composites, 2003(AM5401): p. AM5401.
1-AM5401. 19.
6. Laroche, N., Méthodes d'imagerie ultrasonore
avancées et rapides pour le contrôle non destructif de
matériaux atténuants et diffusants, 2021, École centrale
de Nantes.
CHAPITRE III
Résultats et discussion
CHAPITRE III Résultats et
discussion
41 | P a g e
III.1. Introduction
Nous allons présenter dans ce chapitre les
résultats obtenus lors de notre expérimentation, pour but de
caractériser les stratifiés des deux types des composites
élaborés. Nous commençons d'abord par la
caractérisation de la matrice seule, puis par la suite trois essais
mécaniques de traction, de flexion et de la fatigue ont
été réalisés sur les composites, et faisant aussi
une caractérisation par la méthode des ultrasons. Finalement on a
validé nos résultats expérimentaux à l'aide du
logiciel de simulation Abaqus.
III.2. Caractérisation de la matrice
III.2.1. Caractérisation physique
III.2.1.1. Analyse thermique (ATD, ATG)
40 60 80 100 120 140 160 180 200
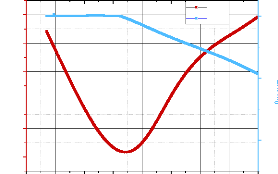
ATD
ATG
100
98
96
-0.20
-0.25
-0.30
-0.35
-0.40
-0.45
Figure III.1 : Diagramme de l'ATD
et l'ATG de la résine Epocast
Température(°C)
Interprétation :
D'après l'allure des courbes d'ATD/ATG (Figure
III.1), on remarque que la résine d'Epocast est stable pendant
le chauffage dans la température ambiante jusqu'à une valeur de
110 ° C ou le point de la transition vitreuse, et la décomposition
rapide se produit après cette valeur critique.
Donc la température d'utilisation ou de service doit
être inférieur à 110 °C.
Résine thermodurcissable : qualifie un
matériau qui durcit de façon irréversible au-dessus d'une
certaine température.[1]
CHAPITRE III Résultats et
discussion
III.2.2. Caractérisation mécanique
III.2.2.1. Essai de traction
On s'intéresse aux propriétés
mécaniques de la matrice. Pour cela, nous avons élaboré
des éprouvettes de traction sous forme haltère (Figure
II.19). Nous avons utilisé trois éprouvettes pour les
essais qui sont effectués sur une machine universelle MTS au sein du
laboratoire a (CNERIB), pilotée par un logiciel qui mesure la
déformation en variant la charge de la contrainte appliquée
jusqu'à rupture de l'éprouvette (Figure III.2)
en précisant la vitesse de déplacement à une valeur de 2
mm/min.
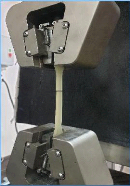
70 60 50 40
30 20 10
0.0 0.5 1.0 1.5 2.0
42 | P a g e
Déformation (%)
Figure III.2 : Rupture en traction
de
résine
0
|
Figure III.3 : Courbe d'essai de
traction de résine
|
Les courbes d'essais de traction des 3 éprouvettes de
la résine présentes des valeurs proches ce qui signifie
l'homogénéité de notre matrice préparée. La
valeur de la contrainte max c'est-à-dire au point de rupture est
donné par un calcul de moyenne des trois essais (60.31
MPa) et pour E= 3.47 GPa, avec une déformation
moyenne de 1.81%.
Les résistances en traction, et le module d'Young sont
très bonnes pour une matière polymère. [5]
CHAPITRE III Résultats et
discussion
43 | P a g e
Tableau III.1 :
Propriétés mécaniques par l'essai de traction de la
matrice Epocast.
Paramètre
|
Module de Young GPa
|
Contrainte max MPa
|
Déformation pour ómax (%)
|
Matrice Epocast 50 - A1
|
Essai 01
|
3.49
|
63.69
|
1.97
|
Essai 02
|
3.44
|
58.95
|
1.75
|
Essai 03
|
3.47
|
58.30
|
1.72
|
Moyenne
|
3.47
|
60.31
|
1.81
|
· Pour la suite de nos essais, nous avons choisi la
résine époxy comme matrice associée aux fibres pour
être en adéquation avec la règlementation
aéronautique internationale car c'est l'unique qui est autorisée
par l'organisation de l'aviation civile internationale [2].
III.3. Caractérisation du matériau composite
stratifié
Les renforts utilisés pour la réalisation des
éprouvettes sont des tissus de carbone et de verre bidirectionnel (voir
Figure II.2), imprégnés dans une matrice en
résine epocast, leurs caractéristiques sont mentionnées
dans les tableaux II.2 et II.3
respectivement.
On cherche à faire la caractérisation physique
et mécanique des matériaux stratifiés fabriqués par
la mesure de densité et en mesurant le taux de fibres, les
résultats sont résumés dans les tableaux ci-dessous. Et
faisant des caractérisations non destructives par ultrason et
destructives par des essais mécaniques de traction, de flexion et de la
fatigue.
III.3.1. Caractérisation physique
III.3.1.1. Mesure de densité
S'appelle aussi la méthode de double pesée,
elle permet de savoir si un matériau est dense ou pas. En utilisant une
balance hydrostatique sensible avec une exactitude de #177; 0.001 g. On mesure
de la masse volumique des 3 échantillons de chaque type de
stratifiés, les résultats sont mentionnés dans le tableau
ci-dessous (Tableau III.2).
CHAPITRE III Résultats et
discussion
44 | P a g e
Tableau III.2 : Résultats
des masses volumiques obtenus
Stratifié
|
Mesure 1
|
Mesure 2
|
Mesure 3
|
Moyenne
|
Carbone/ Ep
|
1.5198
|
1.5203
|
1.5235
|
1.521 g/cm3
|
Verre/ Ep
|
1.7193
|
1.7202
|
1.7271
|
1.722 g/cm3
|
|
III.3.1.2. Mesure de taux des fibres
Les fractions volumiques des fibres ont été
calculées par procédé de calcination en utilisant un four
et une balance, et ça pour assurer la cohérence et la
qualité de chaque composite avant d'entamer les essais
mécaniques.
Tableau III.3 : Taux massique
de renfort par essai de calcination
Matériaux
|
Fraction volumique des fibres
|
Carbone/ Epocast
|
53.37
|
%
|
Verre/ Epocast
|
47.97
|
%
|
|
Interprétation :
Les résultats obtenus de la mesure des fractions
volumiques des fibres et de la matrice montrent que les fractions volumiques en
fibres de verre (47.97 %) sont inférieures à
celles en fibres de carbone (53.37 %). Ces résultats
sont logiques et dûs à la masse volumique élevée des
fibres de verre 1.7 g/cm3 par rapport à
1.5 g/cm3 pour les fibres de carbone (le
matériau le plus léger occupe plus d'espace en volume), Ces
résultats sont confirmés par l'étude de Dr Belgacem et Dr
Basaid [2,3]. Dépend aussi de l'aspect
géométrique différents pour les deux types de fibres et
à l'architecture des tissus qui comprennent un taux de noeuds et vides
différents pour chaque type de fibres.
III.3.2. Caractérisation mécanique du
stratifié
III.3.2.1. Essai de traction
Les tests ont été effectué à la
température ambiante à l'aide d'une machine universelle «
Zwick/Z100 », qui a un capteur de force de capacité de 100 kN.
Cette machine est liée à un ordinateur pour
mesurer les forces et les déplacements en utilisant un logiciel
testXpert version 12.0, dotée d'un extensomètre de haute
résolution de type macro, positionné sur la zone utile de
longueur initiale de 50 mm pour mesurer la déformation ou l'allongement
de l'éprouvette en précision comme montré dans la
Figure III.4. Une vitesse de 2 mm/min est utilisée dans
le test.
CHAPITRE III Résultats et
discussion
45 | P a g e
Les propriétés de traction (Résistance
à la traction, allongement à la rupture et le module du Young)
ont été mesurées conformément à la norme
ASTM D3039. Trois éprouvettes ont été testées pour
chaque type de stratifié en exerçant des contraintes
jusqu'à la rupture éventuelle.
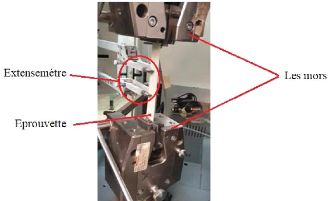
Figure III.4 : Dispositif
d'essai de traction
Les courbes des contraintes en fonction de la
déformation des trois essais de traction pour chaque composite sont
présentées dans (Figure III.5). Nous avons donc
estimé le module d'élasticité et la contrainte à la
rupture, ces résultats sont résumés dans le
(Tableau III.4).
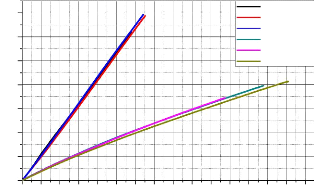
Carbone 1 Carbone 2 Carbone 3
Verre 1 Verre 2 Verre 3
400
300
200
100
0
0.0 0.2 0.4 0.6 0.8 1.0 1.2 1.4 1.6 1.8 2.0 2.2 2.4 2.6 2.8
3.0
700
600
500
Déformation %
Figure III.5 : Courbes de
traction des éprouvettes carbone-verre/époxy.
CHAPITRE III Résultats et
discussion
46 | P a g e
Interprétation :
Remarquant d'après la Figure III.5
que la valeur de contrainte max associé au composite à
fibre de carbone est élevée par rapport à celle du
composite a fibre de verre. Contrairement à la valeur de la
déformation qu'est supérieure pour l'échantillon de fibre
de verre à celle de fibre de carbone.
Le module du Young est calculé par le rapport de la
contrainte sur la déformation (mesure de la pente dans le domaine
élastique) dans une plage d'allongement de 0.1%, 0.2 %, jusqu'à
0,3 %. Il est bien évident que la valeur correspondante au composite
à fibre de carbone est supérieure pour une valeur de
(51.5 GPa en moyenne des trois essais) bien que le module
correspondant au composite à fibre de verre ait une valeur de
(19.16 GPa en moyenne des 3 essais), Les valeurs comparatives
sont résumées dans le tableau ci-dessous.
L'avantage bascule de composite à fibre de
carbone/résine Epocast en termes de résistance à la
traction peut être expliquer par les interactions et l'adhérence
entre la résine et le renfort. Les résines combinées avec
la fibre de carbone améliorent les performances en résistance
à la traction.
Comme l'avion en général en mouvement, est
soumis à des sollicitations de tous types donc l'utilisation de
composites à fibres de carbone est plus performante aux régions
qui sont soumise à des contraintes de traction.
Tableau III.4 : Les valeurs
comparatives des propriétés de traction des stratifiés
composites
Types des éprouvettes
|
Contrainte de rupture (MPa)
|
Déformation A la rupture %
|
Module de Young (GPa)
|
Composite a fibre de carbone
|
1
|
694.50
|
1.28
|
51.8
|
|
689.19
|
1.30
|
51.5
|
|
629.17
|
1.15
|
51.3
|
|
668.23
|
1.25
|
51.5
|
Composite a fibre de verre
|
1
|
395.32
|
2.55
|
19.5
|
|
343.34
|
2.13
|
19.5
|
|
413.86
|
2.81
|
18.5
|
|
384.17
|
2.5
|
19.16
|
|
CHAPITRE III Résultats et
discussion
47 | P a g e
III.3.2.2. Essai de flexion (trois points)
Les allures des courbes de force en fonction de
déplacement pour trois essais de flexion pour chaque type de composite
Epoxy/Tissu de carbone/tissu de verre sont présentés dans la
Figure III.6.
Les valeurs calculées des propriétés de
flexion comparatives entre les deux types d'échantillons sont
résumées dans le Tableau III.5.
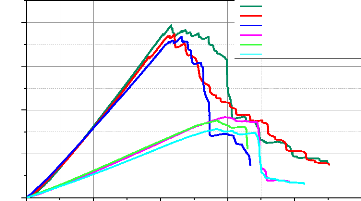
400
800
600
200
0
Fibres de carbone (1) Fibres de carbone
(2) Fibres de carbone (3) Fibres de verre (1)
Fibres de verre (2) Fibres de verre (3)
0 1 2 3 4 5
Déplacement (mm)
Figure III.6 : Courbes de
flexion des d'éprouvettes carbone-verre/époxy.
Interprétation :
On remarque un comportement linéaire élastique
pour les composites avec une rupture brusque lorsque la contrainte maximale est
atteinte ce qui montre la fragilité des stratifiés. Cette rupture
peut être due à la rupture totale des fibres ou à la
rupture de la matrice.
On remarque que les courbes obtenues pour chaque trois essais
sont presque identiques dans les zones élastiques et plastiques ce qui
explique l'homogénéité de ces composites stratifiés
élaborés.
Le composite à base de fibres de carbone
résiste à moyenne de 757.37 N avec un
déplacement moyen de 2.23 mm. Par contre il est plus
rigide que celui de fibre de Verre, qui résiste à une moyenne de
344.64 N avec une valeur de déplacement moyen de
2.88 mm.
CHAPITRE III Résultats et
discussion
48 | P a g e
Ce qui explique l'utilisation de la fibre de verre dans les
ailes d'avion qui sont soumis à des contraintes de flexion. Mais des
recherches sont entrepris par les constructeurs d'avion pour améliorer
ces caractéristiques.
Cette rigidité des composites en fibres de carbone se
distingue clairement sur les courbes, et voir aussi les valeurs comparatives
dans le Tableau III.5 ci-dessous
Tableau III.5 : Les valeurs
comparatives des propriétés de flexion des composites.
Types d'échantillons
|
Force appliquée (N)
|
Déplacement (mm)
|
Carbone/Epocast
|
1
|
787.45
|
2.16
|
|
746.42
|
2.21
|
|
735.24
|
2.31
|
|
756.37
|
2.23
|
Verre/Epocast
|
1
|
368.27
|
2.95
|
|
352.79
|
2.84
|
|
312.85
|
2.83
|
|
344.63
|
2.87
|
|
· La contrainte à la rupture a est relie
à la force appliquée par la formule suivante où S est la
section de l'éprouvette :
F
a = s
(1 Mpa = 1 N/mm2)
III.3.2.3. Essai de fatigue
La machine d'essai de fatigue est une machine standard, celle
qu'on a utilisée pour
p )
l'essai de traction type ZWICK/ROELL Z100, Lorsque on soumet
le matériau à des cycles répétés d'efforts,
il subit des modifications en microstructure (apparition d'une fissuration)
1 N/mm2)
regroupées sous le terme d'endommagement par fatigue.
Les mêmes dimensions d'éprouvettes utilisées pour la
traction sont utilisées dans ces tests.
Protocole pour fatigue :
Appliquant une contrainte de valeur constante de 100 MPa (ou
N/mm2) pendant 200 cycles pour les composites verre-époxy, et
une valeur répétitive de 350 MPa pendant 200 cycle pour les
stratifiés carbone-époxy. Puis, un essai de traction a
été réalisé pour observer la variété
de contrainte a rupture après la fatigue des composites. Aussi pour
objectif de voir l'évolution de la déformation au cours de ce
test.
CHAPITRE III Résultats et
discussion
49 | P a g e
III.3.2.3.1. Fatigue d'éprouvette en composite
à fibre de verre
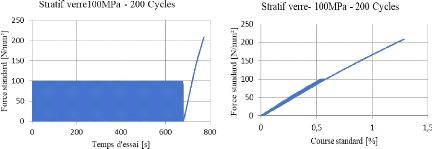
Figure III.7 : Courbe de fatigue
d'éprouvette en composite à fibre de verre
Interprétation :
L'application d'une charge de fatigue provoque une
réduction progressive au point de rupture pour le stratifié
à fibres de verre. Comme il est montré dans la Figure
III.8, une chute de résistance à la traction, pour une
valeur de 210 N/mm2 lorsque on réalise
l'essai de traction après 200 cycles de sollicitations
répétées, en comparant avec la valeur de cet essai sur une
éprouvette non endommagé qu'est résiste à
384 N/mm2. C'est dû à l'apparition
d'une fissuration en appliquant des cycles répétitifs d'efforts
de 100 N/mm2 (27% de contrainte max).
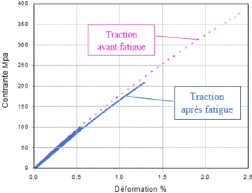
Figure III.8 : Comportement en
traction avant et après fatigue-verre
CHAPITRE III Résultats et
discussion
50 | P a g e
III.3.2.3.1. Fatigue d'éprouvette en composite
à fibre de carbone
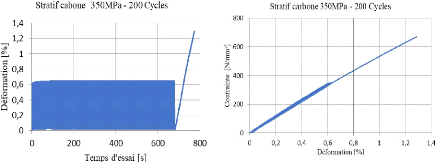
Figure III.9 : Courbe de fatigue
d'éprouvette en composite à fibre de carbone
Interprétation :
La Figure III.9 présente le
déroulement de fatigue Oligo cyclique (à faible nombre de cycles)
sur un stratifié à base de fibre de carbone, de contrainte de
répétition de plus de 50% de contrainte max de rupture
(350Mpa), à la fin de test, l'essai de traction
jusqu'à la rupture est appliqué. En comparaison avec le
comportement en traction avant fatigue, comme il est montré dans la
Figure III.10, nous constatons que les
propriétés mécaniques ne sont pas affectées, ni en
termes de déformation, ni en termes de résistance, ce qui preuve
la performance élevée de stratifié en fibre de carbone par
rapport au stratifié à base de fibre de verre. D'ailleurs les
parties fortement sollicitées dans l'aéronefs sont
élaborés par les composites à base de fibre de carbone.
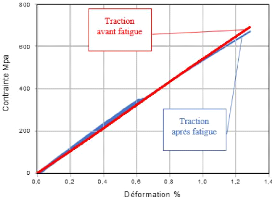
Figure III.10 : Comportement en
traction avant et après fatigue-carbone
CHAPITRE III Résultats et
discussion
51 | P a g e
III.3.3. Caractérisation par ultrasons
L'objectif de ce travail basé sur le contrôle
non destructif par ultrason des éprouvettes à base de fibre de
verre et à base de fibre de carbone et comparer les résultats
trouvés avec valeurs calculés par essai de traction.
s Mesure longitudinale
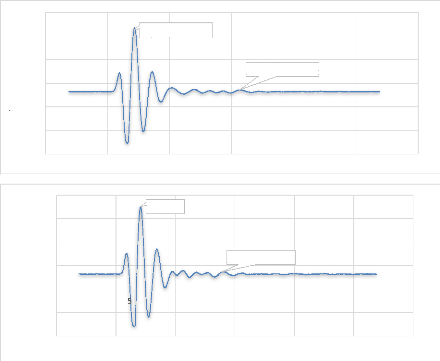
amplitude(mV)
amplitude(mV)
-1000
-2000
4000
3000
2000
1000
-1000
-2000
3.60E-05 3.68
4000
3000
2000
1000
0
3.60E-05 3.68
0
E-05
E-0
3.71E-05, 3260.31
3.71E-05
3.76E-05 3.84
3.76E-05 3.84
temps(s)
temps (s)
3.82E-05; 728.75
E-05 3.92E-05 4.00
E-05 3.92E-05 4.00
3.85E-05, 718.281
E-05 4.08E-05
E-05 4.08E-05
b
a
Figure III.11 : Signaux
longitudinales - a. composite à fibre de
carbone b. composite à
fibres de verre
Les résultats des vitesses longitudinales sont
indiqués dans le Tableau III.6, Après
l'utilisation de la formule mathématique (II.3) suivante :
2e
v= At ... ... ... ... ... (3)
Ou les deux points représentent le temps de parcours
aller-retour des ondes ultrasonores à travers l'éprouvette.
Calcul numérique : Atv= 3.82
10-5 - 3.71 10-5 = 1.1 ts VLv= 3818.18 m/s
Atc= 3.85 10-5 - 3.71 10-5 =
1.4 ts VLc= 3142 m/s
·
CHAPITRE III Résultats et
discussion
52 | P a g e
Mesure transversale
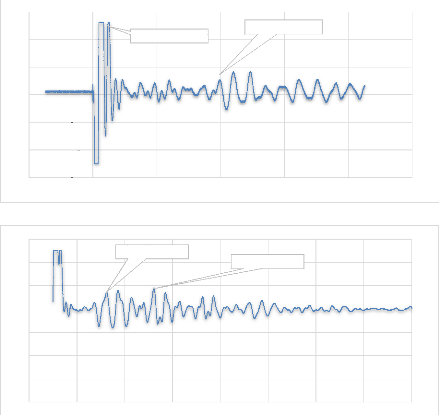
1.5
a
3.52E-06, 0.129102
1.01E-06, 0.126445
amplitude (v)
1
0.5
0
E-06 1.00E-05
0.5
1
1.5
temps (s)
- 2.00E-06 0.00E+00
2.00E-06 4.00E-06 6.00E-06 8.00
b
3.5
2.24E-06, 1.22055
4.20E-06, 1.37016
2.5
1.5
0.5
- 1.00E 0.506 1.00
E-06 9.00E-06 1.10
E-05 1.30E-05 1.50
E-05
1.5
- 2.5
- 3.5
E 06 3.00E 06 5.00E-06 7.00
Figure III.12 : Signaux
transversales - a. composite à fibre de
carbone b. composite à fibre de verre
v De la même façon que la mesure longitudinale on
mesure les vitesses transversales. A partir des formules
(II.4) (II.5), on déduit les
paramètres d'élasticité comme suit :
??= ??????2
|
3????2 - 4????2
????2 - ????2
|
??=
|
1
2
|
????2
|
-
|
2????2
|
???? 2
|
-
|
????2
|
CHAPITRE III Résultats et
discussion
53 | P a g e
Tableau III.6 : Paramètres
élastiques déterminés par ultrason
Paramètre
|
Stratifié Carbone/époxy
|
Stratifié Verre/époxy
|
Epaisseurs (mm)
|
2.1
|
2.1
|
Masse volumique p (kg/m3)
|
1520
|
1720
|
Vitesse longitudinale (m/s)
|
3142
|
3818
|
Vitesse transversale (m/s)
|
1673
|
2142
|
Module e Young E (GPa)
|
11.56
|
20.05
|
Module de poisson ?
|
0.3
|
0.27
|
Interprétation :
Les résultats trouvés par ultrason sont proches
à celle calculés par essai de traction pour le cas de
stratifié à base fibre de verre. Par contre, les valeurs
trouvées par ultrason sont très lion de valeurs
expérimentaux trouvés par l'essai de traction dans le cas des
fibres de carbone, ce qui montre les limites de cette technique pour les
matériaux composites à haute performance comme le cas des fibres
de carbone, car ces matériaux sont très légers d'une part,
ce qui donne des valeurs limitées de vitesse ultrasonores, et, d'autre
part, présente des performances mécaniques incontournables pour
utilisation aéronautiques.
III.4. Validation des résultats expérimentaux
par simulation
L'analyse est faite par un modèle de simulation avec un
outil de recherche nommé Abaqus qui aide à : la
modélisation, la simulation des différents
phénomènes physiques (mécanique, transfert thermique, MDF
...) et l'exploitation de leurs résultats.
Le composite choisi pour la simulation est le composite
Epoxy/Tissu de carbone car le tissu a une architecture plus simple que celle du
verre. Dans cette partie de simulation on va expliquer les
déférentes étapes de modélisation et simulation
pour l'analyse mécanique (essai de traction) et présenter les
résultats trouvés.
III.4.1. Définition
L'Abaqus est une suite de puissants programmes de simulation
d'ingénierie, basées sur la méthode des
éléments finis, qui peuvent résoudre des problèmes
allant d'analyses linéaires relativement simples aux simulations non
linéaires les plus difficiles. Abaqus contient une vaste
bibliothèque d'éléments qui peuvent modéliser
pratiquement n'importe quelle géométrie. Il dispose d'une liste
tout aussi étendue de modèles de matériaux qui permettent
de simuler le comportement de la plupart des matériaux
d'ingénierie les plus
CHAPITRE III Résultats et
discussion
54 | P a g e
courants, y compris les métaux, le caoutchouc, les
polymères, les composites, le béton armé, ainsi que les
matériaux géotechniques tels que les sols et les roches.
Conçu comme un outil de simulation, Abaqus peut être
utilisé pour étudier plus que les problèmes structurels
(contraintes/déplacements). Il peut simuler des problèmes dans
des domaines aussi divers que le transfert de chaleur, la diffusion de masse,
la gestion thermique des composants électriques etc[4]. Vous
trouvez dans la figure ci-après un aperçu détaillé
des composants de l'interface du logiciel ABAQUS et des principaux
contrôles.
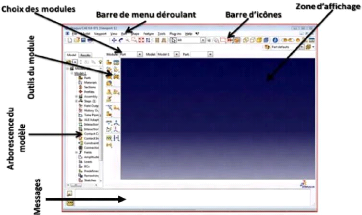
Figure III.13 : Composants de
l'interface du logiciel ABAQUS
III.4.2. Organisation de l'interface ABAQUS/CAE
III.4.2.1. Modules
ABAQUS/CAE est divisé en unités fonctionnelles
appelées modules, chaque module contient les outils qui sont propres
à une partie de la tâche de modélisation. La
réalisation complète d'un jeu de données s'effectue
après un passage successif dans les modules, qui sont par ordre :
1. Module " PART "
Le module Part permet de créer tous les objets
géométriques nécessaires à notre problème,
soit en les dessinant dans ABAQUS CAE, soit en les importants d'un logiciel de
dessin tiers (SolidWorks par exemple).
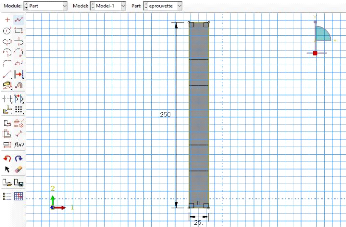
CHAPITRE III Résultats et
discussion
55 | P a g e
Figure III.14 : Module de
création de la géométrie
2. Module "PROPERTY "
Le module Property permet, comme son nom l'indique, de
définir toutes les propriétés d'un objet
géométrique ou d'une partie de ces objets. (Nombre de couches,
densité, E, ).
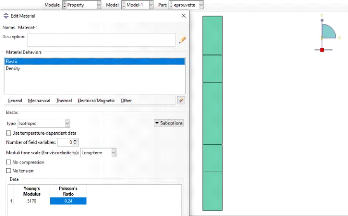
Figure III.15 : Module
d'introduction des paramètres de matériaux
3. Module "ASSEMBLY "
Ce module permet d'assembler les différents objets
géométriques créés dans un même repère
de coordonnées global.
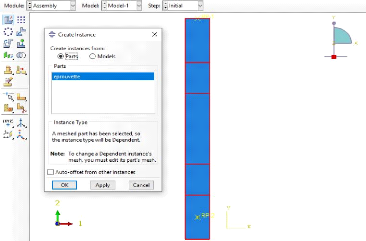
CHAPITRE III Résultats et
discussion
Figure III.16 : Module
d'assemblage géométrique
4. Module "STEP "
Ce module permet de définir toutes les étapes et
les requêtes pour le post traitement, c'est à dire le moment
(temps) à partir duquel une force est appliquée et jusqu'à
quand, il est aussi possible de créer des forces ou des conditions
limites qui s'activent à des moments donnés.
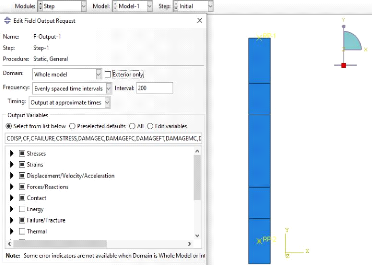
Figure III.17 : Phase de
création des sollicitations
56 | P a g e
5. CHAPITRE III Résultats et
discussion
57 | P a g e
Module " INTERACTION "
Grâce à ce module, il est possible de
spécifier toutes les interactions entre les différentes parties
et régions du modèle, qu'elles soient mécaniques,
thermiques ou autres. Il faut savoir qu'ABAQUS ne prend en compte que les
interactions explicitement définies, la proximité
géométrique n'étant pas suffisante.
On a choisi un point de référence pour concentrer
les forces en lui par l'outil Coupling.
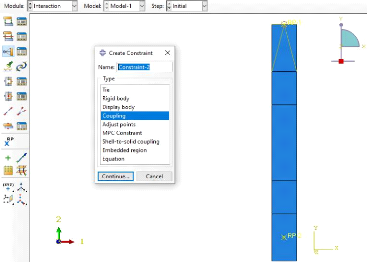
Figure III.18 : Module
d'interaction
6. Module "LOAD "
Le module Load permet de spécifier tous les chargements,
conditions limites et champs. Il faut savoir que les chargements et les
conditions limites sont dépendants des steps, par exemple une force est
appliquée au step 1 mais inactive au step 2.
Dans cette étape on fixe les talons de
l'éprouvette, (Encastrer en bas et le déplacement en haut est
suivant Y)
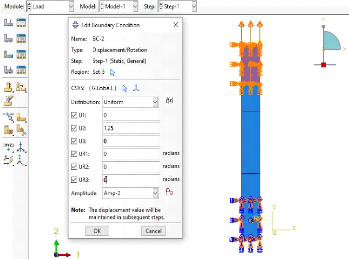
CHAPITRE III Résultats et
discussion
Figure III.19 : Phase des
conditions limite et chargement
7. Module "MESH "
Ce module contient tous les outils nécessaires pour
générer un maillage par la méthode des
éléments finis sur un assemblage.
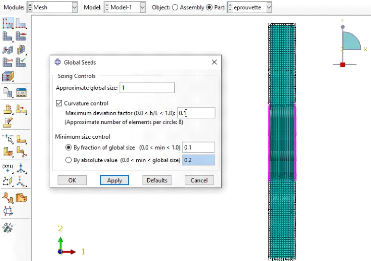
Figure III.20 : Phase de
maillage
58 | P a g e
8. CHAPITRE III Résultats et
discussion
Module "JOB "
Une fois que toutes les tâches de définition du
modèle ont été réalisées, il faut utiliser
le module Job pour analyser ce modèle. ABAQUS va alors réaliser
tous les calculs nécessaires et en tirer des résultats.
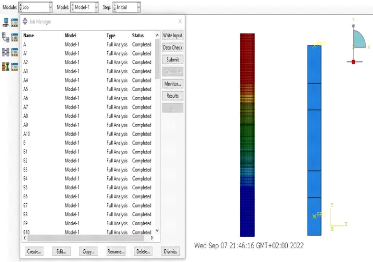
Figure III.21 : Phase de lancement
de simulation
9. Module " VISUALIZATION "
Ce module permet de visualiser le modèle et les
résultats, les courbes de charges, les déformations... etc
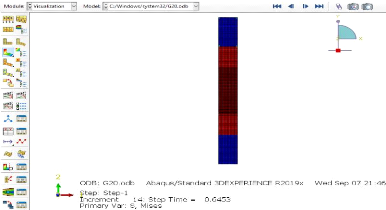
Figure III.22 : Phase
consultation des résultats
59 | P a g e
CHAPITRE III Résultats et
discussion
60 | P a g e
10. Module "SKETCH "
Ce module permet de créer des formes bidimensionnelles
qui ne sont pas associés à un objet. Il peut être
utilisé pour des extrusions par exemple (Nous ne l'avons pas
utilisé).
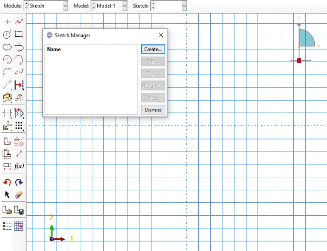
Figure III.23 : Module de
création bidimensionnelle
III.4.3. Modélisation numérique (MEF)
Afin de modéliser numériquement l'essai de
traction du matériau étudié, un modèle
numérique basé sur la méthode des éléments
finis (MEF), a été réalisé à l'aide du
logiciel commercial ABAQUS 2019, dans le but de valider les résultats
expérimentaux. La géométrie et les conditions aux limites
ont été choisies en fonction des conditions expérimentales
(ASTM), la partie inférieure du modèle est fixe dans tous les
degrés de liberté, tandis que la partie supérieure a une
liberté dans la direction des fibres. Comme le montre la Figure
III.25, qui indique également le type de maillage et nombre des
couches choisie.
La taille de l'élément dans la partie
médiane (zone de dommages attendus) est de (1 mm x 1 mm), et le reste de
l'échantillon de (2 mm x 2 mm). Le maillage a été
créé à l'aide d'une double courbe mince ou épaisse
(S4R) à 4 noeuds, affinant jusqu'à 2368 éléments et
2448 noeuds, afin d'obtenir une bonne précision du calcul
numérique qui est lié à la qualité du maillage.
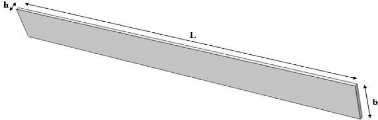
CHAPITRE III Résultats et
discussion
Figure III.24 : Dimensions du
modèle numérique.
Tableau III.7 : Paramètres
géométriques et mécaniques utilisés
Longueur L [mm]
|
Largeur b [mm]
|
Épaisseur h [mm]
|
Young's modulus E [GPa]
|
Density
p [ ]
|
Coefficient de Poisson
|
250
|
25
|
2.1
|
51.5
|
1.521
|
0.24
|
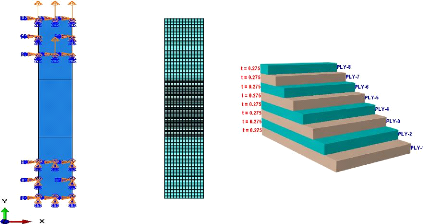
61 | P a g e
(a) (b) (c)
Figure III.25 : Modèle
éléments finis
(a) conditions aux
limites, (b) maillage utilisé et (c)
nombre de couches.
v L'objectif de la simulation ABAQUS du composite
stratifié (carbone/époxy) est de prédire la réponse
de l'essai de traction, puis de les comparer et de les vérifier avec les
résultats expérimentaux.
CHAPITRE III Résultats et
discussion
62 | P a g e
III.4.4. Comparaison entre les résultats
expérimentaux et numériques.
Les résultats obtenus par la méthode des
éléments finis ont été comparés aux
résultats expérimentaux pour valider la précision du
modèle numérique comme le montre la figure suivante

Figure III.26 : Comparaison entre
les résultats expérimentale et numérique.
Sur la base de cette comparaison, on observe que les graphes
ont presque la même pente, ce qu'implique que les valeurs obtenues
à partir des tests expérimentales et numériques sont
très similaires, avec un faible pourcentage d'erreur.
Après la validation réussie de modèle par
simulation, on peut jouer sur les paramètres géométrique
et mécaniques qu'on veut changer sans refaire l'expérimentale
à chaque fois, en changeant par exemple l'orientation des fibres et le
nombre des couches de notre composite et voir leur influence sur les
propriétés mécaniques. Cette méthode nous permet de
gagner de temps et d'économiser les outils pour les tests
expérimentales.
III.5. Conclusion
D'après la caractérisation physique et
mécanique sur la matrice seule, on déduit sa température
de service par la méthode ATD/ATG. Et en faisant l'essai de traction, on
trouve que la résistance en traction, et le module d'Young sont
très bonnes pour une matière polymère, c'est pour
ça la résine époxy est choisie comme matrice
associée aux fibres pour être en adéquation avec la
règlementation aéronautique internationale.
La légèreté des composites
aéronautique est dû à leur faible densité ainsi en
conservant leur excellente propriété mécanique à
cause de taux de fibres élevés.
CHAPITRE III Résultats et
discussion
63 | P a g e
On déduit d'après les essais mécaniques
sur les éprouvettes, que la résistance des composites à
fibres de carbone en traction et à la fatigue est meilleure que celle
qui est à fibre de verre, mais vu que le paramètre
diélectrique est important dans la sécurité des vols,
sachant que l'avion est soumis à des risques causés par les
courants électriques, on explique l'utilisation majoritaire sur fuselage
et aile d'avion de la fibre de verre comparativement à la fibre de
carbone qui sont utilisables dans les parties hautement solliciter dans
l'avion.
Les résultats trouvés par ultrason sont proches
à celle calculée par essai de traction pour le cas de composite
à fibres de verre en comparant la valeur de module de Young par ultrason
Eultrason=20.05 GPa avec Etraction=19.16 GPa,
ce qui permet d'utiliser cette technique comme un moyen de calculer les
paramètres élastiques sans détruire le matériau
mais seulement pour les matériaux denses et ce n'est pas le cas pour le
composite à fibres de carbone.
Comparant les deux graphes (Simulation/expérimental) on
trouve presque la même pente, avec des valeurs très similaires.
CHAPITRE III Résultats et
discussion
64 | P a g e
Références du chapitre
III
1. Chapuis, D., V. Aerts, and R. Bonneville, Chapitre 4: Les
nouveaux matériaux composites pour l'aéronautique par Vincent
Aerts, in Chimie, aéronautique et espace. 2021, EDP Sciences. p.
75-84.
2. Basaid, Djamel. Simulation Numérique Du
Comportement Macroscopique Des Matériaux
Hétérogènes À Matrice Élastique Et Inclusion
Élastoplastique Pour L'utilisation En Construction Aéronautique.
2019. Université M'hamed Bougara - Boumerdes, Thèse de
Doctorat.
3. Belgacem, L., et al., Experimental investigation of
notch effect and ply number on mechanical behavior of interply hybrid
laminates (glass/carbon/epoxy).
Composites Part B: Engineering, 2018. 145:
p. 189-196.
4. Systèmes, D., 'Getting Started with Abaqus
Interactive Edition version 6.8'. Dassault Systèmes Simulia Corp,
2008.
5. Aribi, C., Étude comparative du comportement des
différents matériaux composites (différentes matrices),
2012, Université de Boumerdès-M'hamed Bougara.
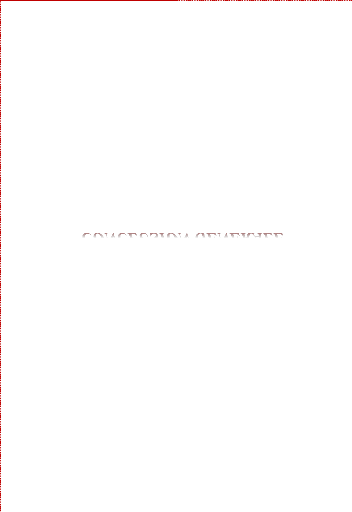
CONCLUSION GENERALE
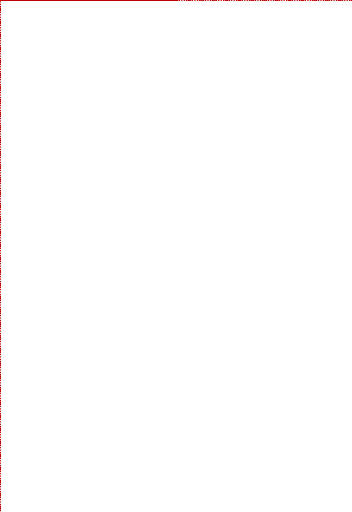
CONCLUSION GENERALE
Ce travail est réalisé au niveau de
différentes institutions, à savoir : Air Algérie pour
l'élaboration des composites, CRTI, CNERIB et UR-MPE
pour le contrôle et pour la caractérisation des matériaux
élaborés. L'objectif de base est de clarifier le comportement de
ces composites destinés à l'aéronautique d'une part, et de
classer les techniques d'analyse et de caractérisations adéquates
d'une autre.
Notre étude nous a permis de tirer les conclusions
suivantes :
+ D'après la caractérisation physique sur la
matrice seule, on déduit son domaine de service par la méthode
ATD/ATG, ce domaine ne doit pas dépasser la température de
transition vitreuse, en plus, cette matrice doit être stable en termes de
déformation pour les températures inférieures à
Tg.
+ En faisant l'essai de traction, on trouve que la
résistance en traction, et le module d'Young sont très bons pour
une matière polymère, le domaine élastique est très
important, c'est pour ça que cette résine époxy est
choisie comme matrice associée aux fibres pour être en
adéquation avec la règlementation aéronautique
internationale.
+ Les sollicitations mécaniques sont supportées
par le renfort, tandis que la matrice époxy assure la forme et la
transmission des contraintes vers les renforts.
+ Les composites à fibres de verre sont moins
performants d'où leurs modules de Young est inférieur à
celle que ceux renforcés par des fibres en carbone. Mais sont utilisable
dans le fuselage d'avion à cause de leur caractère
diélectrique et leur résistance à la
déformation.
+ Les composites à base de fibre de carbone
présentes des résistances mécaniques très
élevés, et une endurance dépasse 50% de la contrainte
ultime dans le cas des sollicitations par fatigue, par contre les
stratifiés à base de fibre de verre sont limité en termes
d'endurance. Une prudence obligatoire doit être considérés
dans les parties à base de ce renfort dans l'aéronef, le
contrôle périodique est obligatoire.
+ La légèreté des composites
aéronautiques est dûe à leur faible densité ainsi en
conservant leurs excellentes propriétés mécaniques, ce qui
limite les techniques de caractérisation par ultrason qui est
très souvent utilisé dans l'aéronautique, car cette
technique est basée essentiellement sur les matériaux les plus
denses tel que les métaux.
65 | P a g e
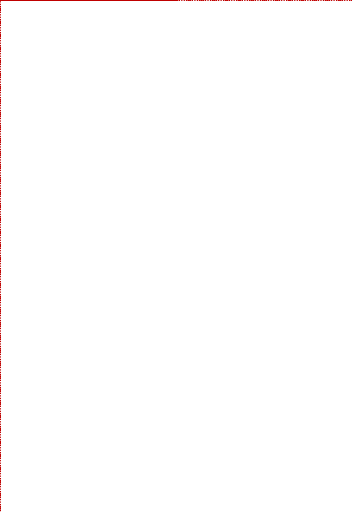
v La simulation est une technique satisfaisante car elle
donne des résultats très proches de la réalité, ce
qui permet d'exploiter cette technique pour étudier et formuler les
meilleures architectures des structures composites sans aller vers
l'élaboration et le tâtonnement, ce qui permet d'être
efficace et économique.
Les matériaux composites sont actuellement en cours de
développement pratique dans divers domaines, et sont la source de toutes
sortes de défis des réalisations high-tech. D'où dans le
domaine de l'aéronautique spécialement ou le pourcentage de ce
type de matériau dépasse 50% pour les avions de la nouvelle
génération.
Résume bien le rôle clé de la physique des
matériaux dans l'étude et le développement des
matériaux composites. D'un côté nous avons l'aspect virtuel
(la simulation par ordinateur), et de l'autre côté l'aspect
expérimental.
Perspectives
L'industrie aéronautique est un environnement où
la recherche et l'utilisation de nouveaux matériaux jouent un rôle
clé. Beaucoup de travail reste à faire pour optimiser leur
utilisation, notamment en ce qui concerne l'introduction des
nanomatériaux dans la construction aéronautique. Ainsi pour la
recherche, il s'agit de continuer à développer des résines
pour augmenter la performance des composites destinés
aéronautique.
66 | P a g e
ANNEXE
1. FIBRES DE VERRE
Les fibres de verre sont peu coûteuses en production, et
constituent le renfort le plus utilisé actuellement. Leur fabrication se
fait en général par étirage décrit par la figure
ci-dessous. Les oxydes minéraux constituant la matière
première (silice, alumine, etc.) sont mélangés en
proportion voulue suivant le type de fibres de verre désiré (voir
tableau II.1.). Ce mélange est ensuite porté
à très haute température (Environ 1250°C). A cette
température, la viscosité du verre permet un écoulement
par gravitation à travers la filière sous forme des fibres de
quelques dixièmes de millimètres. A la sortie de la
filière le verre en phase plastique est simultanément
étiré à grande vitesse (de l'ordre 250 m/s) et refroidi,
les conditions des refroidissements et de vitesse d'étirage permettent
d'obtenir des fibres sous forme de filaments de diamètres
calibrés[1] . Ces filaments isotropes sont ensimés
pour optimiser l'adhésion de la matrice, puis assemblés pour
former les fils, eux-mêmes stockés sous forme de bobine
appelée gâteau. Le gâteau est alors étuvé,
pour éliminer l'eau résiduelle et pour stabiliser l'ensimage. Les
fibres de verre ainsi obtenues sont amorphes, ce qui leur confère des
caractéristiques mécaniques parfaitement
isotropes.[2]
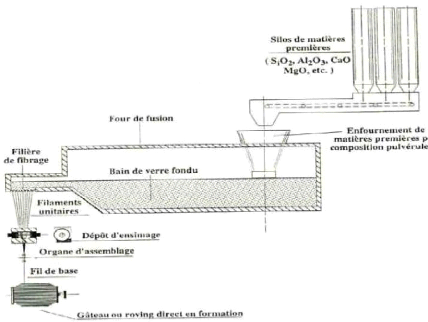
Figure.1. Procédé de fabrication des
fibres de verre

II | P a g e
2. FIBRES DE CARBONE
Les fibres de carbone ont de très fortes
propriétés mécaniques et sont largement utilisées
dans les composites HP, élaborées à partir de l'un des
trois précurseurs suivants : la rayonne, le brai de pétrole, et
le poly acrylonitrile [(CH2-CH-CH) n] noté (PAN). Les fibres de carbone
utilisées comme des renforts sont produites à partir de brai de
mésophase ou de PAN, en commençant tout d'abord par le traitement
thermique de brai isotope afin d'orienter les molécules poly
aromatiques. Ensuite, le filage et l'étirage de cette mésophase
sont réalisés pour l'obtention des fibres ; ces dernières
sont composées de 90 à 70 % de carbone, moins de 10 % d'azote,
environ, 1% d'oxygène et moins de 1% d'hydrogène. La fabrication
des fibres de carbone à partir de PAN passe par quatre étapes :
Oxydation, carbonatations, graphitisation et traitement de surface [3]
a. Oxydation
Les fibres acryliques étant fusibles, la phase
d'oxydation a pour but de supprimer artificiellement le point de fusion ; cette
opération est effectuée en chauffant les fibres à environ
200 à 300 c° en atmosphère oxygéné pendant 0.5
à 3h. Il se produit alors une oxydation conduisant à une
réticulation des chaines moléculaires et à la
création d'un réseau tridimensionnel.
b. Carbonatation
Consiste à chauffer progressivement les
réticulées de 300 °C à 1100 °C environ, en
atmosphère inerte. Il y a alors élimination de l'eau et de
l'acide cyanhydrique, seuls les carbones étant conservés dans la
chaîne. Les fibres obtenues après cette phase ont de bonnes
caractéristiques mécaniques et peuvent être
utilisées après traitement des surfaces. Ces fibres sont alors
dénommées fibres HR (haut résistance) ou fibres HT (haut
ténacité).
c. Graphitisation
Cette phase est utilisée lorsqu'on souhaite obtenir des
fibres à module de Young élevé ; cette phase consiste
à effectuer, à la suite de la carbonatation, une pyrolyse des
fibres en atmosphère inerte jusqu'à 2600°C ou à des
températures supérieures ; la graphitisation provoque une
réorientation des réseaux hexagonaux de carbone suivant l'axe des
fibres, ce qui aboutit à une augmentation du module de Young. Toutefois,
simultanément à cette réorientation, des défauts se
créent dans la structure, entraînant une diminution de la
contrainte à la rupture. Suivant le taux de graphitisation, on distingue
deux types de fibres : fibres à haute résistance (HR) pour une
combustion à 1500 °C, et fibres haut module (HM) pour une
température de combustion de 1800 à 2000 °C [4]
III | P a g e
d. Traitement de surface
Il consiste en un traitement de surface par oxydation
ménagée en milieu acide (nitrique ou sulfurique). Cette phase a
pour objet d'accroitre la rugosité des filaments. Un traitement final
par ensimage effectué à l'aide d'une dispersion aqueuse
spécifique comportant un agent antistatique, permet d'assurer
différents rôles telle que la compatibilité de la liaison
fibre - matrice et la protection contre l'abrasion générée
par la mise en oeuvre (frottement contre pièces métalliques).
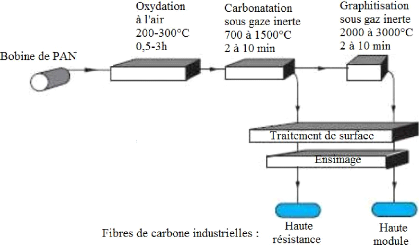
Figure.2. Procédé de fabrication des
fibres de carbone à partir de (PAN).
3.
LES UNITES UTILISES EN ABAQUS
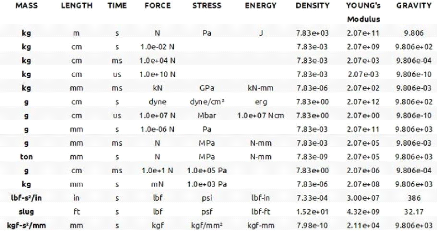

Figure.3. Les unités utilisées en
Abaqus
4. MESURE DES PARAMETRES ELASTIQUE PAR
ULTRASON
2_ E(1-u)2= E
On a VL -- p(1+u)(1-2u) VT 2p(1+u)
Trouvons E
2 3E(1-u)
3VL - 4 V= p(1+u)(1-2u)
|
4E
|
2p(1+u)
|
=
=
=
IV | P a g e
3E(1-u)-2E(1-2u)
p(1+u)(1-2u) 3E-3Eu-2E+4Eu
p (1+u)(1-2u) E+Eu
p(1+u)(1-2u)
= ??(1+u)
??(1+u)(1-2u)
3VL 2- 4 VT2 = ??
??(1-2u)
|
??(1-u)
VL 2- VT2=
??(1+u)(1-2u)
|
??
|
2??(1+u)
|
2??(1-u)-??(1-2u) ??
(1+u)(1-2u)
2??-2??u-E+2??u
??(1+u)(1-2u) (simplification)
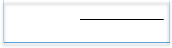
??
VL 2- VT2=
2??(1+u)(1-2u)
Calculons le rapport 3VL2 4?? 22 = E . 2??
(1+u)(1-2u)
???? --VT ??(1-2u) ??
= 2(1 + u)
??
?????? 2 3???? 2-4????2
?? 2
??2-????2 = ?? ??(1-2u) (2(1 + u)) = E
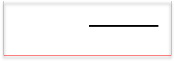
2-4????2
?? = ?????? 2 3???? ????2-????2
Finalement
Trouvons u
VL 2- 2VT2= ??(1-u)
??(1+u)(1-2u)
|
2??
|
2??(1+u)
|
V | P a g e
??(1-u)-??(1-2u) ??
(1+u)(1-2u)
??(1-u)-??(1-2u) ??
(1+u)(1-2u)
??-??u-??+2??u
?? (1+u)(1-2u)
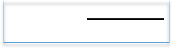
VL 2- 2VT2 =
??u
??(1+u)(1-2u)
?? =
|
1
|
???? 2-2????2
|
2????
2-????2
|
1 ???? 2-2????2
2???? 2-????2
Finalement
1 ??u
2??(1+u)(1-2u) ·
2??(1+u)(1-2u) =
u
??
VI | P a g e
Références annexe
1. Guillon, D., Fibres de verre de renforcement.
Techniques de l'ingénieur. Plastiques et composites,
1995(A2110): p. A2110. 1-A2110. 15.
2. Aribi, C., Étude comparative du comportement
des différents matériaux composites (différentes
matrices), 2012, Université de Boumerdès-M'hamed Bougara.
3. Wang, P., Étude numérique et
expérimentale de procédé d'élaboration
des matériaux composites par infusion de résine, 2010,
Saint-Etienne, EMSE.
4. Davim, J.P., Book Review: Machining of Polymer
Composites by Jamal Y. Sheikh- Ahmad. International Journal of
Machining and Machinability of Materials, 2009. 6(3-4): p.
322-323.
|