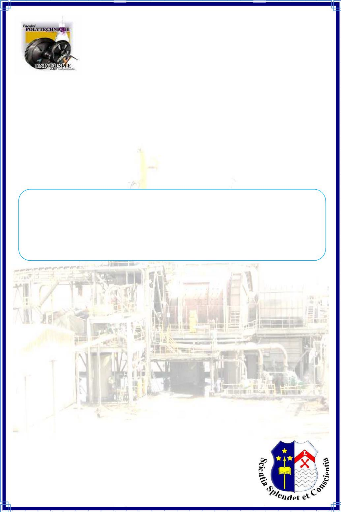
UNIVERSITE DE LUBUMBASHI FACULTE
POLYTECHNIQUE
DEPARTEMENT ELECTROMECANIQUE
DIMENSIONNEMENT D'UN SYSTEME AUTOMATIQUE DE
REFROIDISSEMENT PAR EAU DU CIRCUIT DE
LUBRIFICATION DES PALIERS DU SAG MILL
« Cas du SAG Mill de RUASHI MINING
»
Par MBUMBA NDAKA
Gradué en Sciences Appliquées
Mémoire présenté et
défendu en vue de l'obtention du grade d'ingénieur
civil en Electromécanique
Directeur: Prof. Dr. Ir. Arthur KANIKI Co
directeur : C.C Tristan MATANDA
Juillet 2012
I
DEDICACE
A toi l'éternel Dieu, pour ce privilège que tu
m'accorde de présenter ce travail de fin d'étude.
A mes parents ;
A mes frères et soeurs ; A la famille KIBWE.
A tous, je dédie ce travail
Yves NDAKA
A tous je dis merci et que Dieu vous bénisse !
II
AVANT PROPOS
Arrivée au terme de ce travail, je suis heureux de
pouvoir remercier toutes les personnes qui en ont permis ou facilité la
réalisation par leur appui scientifique, leur collaboration, leur aide
matérielle ou leur aide financière.
En premier lieu, j'ai beaucoup de gratitude à adresser
au Professeur Docteur ingénieur Arthur KANIKI qui a bien voulu assurer
de main de maitre la direction de ce travail.
Ma gratitude s'adresse à Monsieur Tristan MATANDA et
MAZOWA pour leurs conseils et disponibilité permanente, que leur
compétence dans le suivi de ce travail trouve ici l'assurance de ma
reconnaissance la plus sincère.
Le co-parrainage scientifique de ce mémoire revient
à Monsieur Rufus PIETERSE, Chef du service d'instrumentation de l'usine
hydro métallurgique Ruashi Mining et à Monsieur Samy KOSHI dont
les suggestions nous ont été d'un concours inestimable.
Mes remerciements s'adressent à tout le corps
professoral de la faculté polytechnique.
Je tiens à remercier MUKEPE Moise, ZEKA Léon et
KYONI Idriss pour leurs soutiens tout au long de mon parcours
académique, que ce travail soit le fruit de ma reconnaissance.
Je tiens également à exprimer mes remerciements
à mes amis pour leurs encouragements et suggestions durant
l'élaboration de ce travail
Une pensée spéciale à papa LWINDA
Jacques, pour son soutien tant moral que financier.
III
TABLE DES MATIERES
DEDICACE I
AVANT PROPOS II
TABLE DES MATIERES III
LISTE DES FIGURES V
TABLE DES TABLEAUX VI
LISTE DES SYMBOLES VII
GLOSSAIRE IX
INTRODUCTION GENERALE 1
CHAPITRE I. CONSIDERATIONS GENERALES 3
I.1. HUILES HYDRAULIQUES 3
I.1.1. Viscosité des lubrifiants 3
I.1.2. Indice de viscosité 4
I.1.3. Influence de la température et de la pression sur
la viscosité 5
I.2. LUBRIFICATION DES PALIERS LISSES 7
I.2.1. Principes qui régissent les paliers à
coussinets 7
I.2.2. Lubrification des paliers à coussinet 7
I.3. THEORIE SUR LES ECHANGEURS 10
I.3.1. Définitions de l'échangeur
élémentaire 10
I.3.2. Architecture générale de l'échangeur
13
I.3.3. Grandeurs classiques définissant l'échangeur
15
I.3.4. Types d'échangeurs 15
I.3.5.Echangeur à tubes et calandre 16
I.3.6. Dimensionnement d'un échangeur 18
I.3.7. Calcul de la tuyauterie 21
I.4. L'AUTOMATISATION 22
I.4.1. Structure d'un système automatisé [15,16]
22
I.4.2. Automate programmable industriel : API [16,17] 22
I.4.3.Capteurs 24
I.4.4. Les pré-actionneurs 25
I.4.5. Les actionneurs 25
CHAPITRE II. PRESENTATION DU CADRE D'ETUDE 26

II.1. PRESENTATION DE L'USINE 26
II.2. BROYEUR A BOULETS SEMI AUTOGENE : SAG MILL 28
II.2.1. Présentation du broyeur à boulets semi
autogène 28
II.2.2. Circuit de lubrification du SAG Mill 29
II.2.3. Commande du broyeur 32
II.3. IMPACT DES MONTEES DE LA TEMPERATURE D'HUILE SUR LES
PALIERS 35
II.4. DISCUSSION ET INTERPRETATION DES DONNEES 41
II.4.1. Températures de l'huile au niveau des paliers
41
II.4.2. Température de l'huile dans le réservoir
45
CHAPITRE III. DIMENSIONNEMENT DU SYSTEME DE REFROIDISSEMENT 48
III.1. PRESENTATION DU SYSTEME DE REFROIDISSEMENT 48
III.2. CALCUL DE L'ECHANGEUR 51
CHAPITRE IV. SYSTEME DE COMMANDE AUTOMATIQUE 59
IV.1. IDENTIFICATION DES COMPOSANTS 59
IV.2. DESCRIPTION FONCTIONNELLE 61
IV.3. Algorithme de programmation du système de commande
63
IV.3.1. Algorithme de démarrage automatique 63
IV.3.2. Algorithme de démarrage automatique de la pompe
01-PMP-02 63
IV.3.3. Algorithme d'arrêt automatique 64
IV.3.4. Algorithme de contrôle de vitesse 64
IV.3.5. Algorithme de contrôle de température 65
CONCLUSION GENERALE 66
BIBLIOGRAPHIE 67
ANNEXES 69
CODE DE PROGRAMMATION POUR LE CALCUL DE L'ECHANGEUR 80
V
LISTE DES FIGURES
Figure I.1. Champs de vitesse dans le film (Ecoulement de
COUETTE) 4
Figure I.2. Variation de la viscosité avec la
température pour une huile minérale 5
Figure I.3. Variation viscosité-température sur
abaque ASTM 6
Figure I.4. Dommages sur les coussinets 7
Figure I.5. Palier à coussinet 8
Figure I.6. Principe de fonctionnement d'un palier
hydrostatique 9
Figure I.7. Schéma du quadripôle 10
Figure I.8. Profil de température et de vitesse dans un
tube 12
Figure I.9. Différents profils qualitatifs de
température dans un échangeur 14
Figure I.10. Différents types d'échangeurs
tubulaires 16
Figure I.11. Échangeur à tubes et calandre 16
Figure I.12. Divers constituants d'un échangeur TEMA
type AEL 17
Figure I.13. Pas des tubes 18
Figure I.14. Logique de la phase de dimensionnement thermique
18
Figure I.15. Principe de calcul thermique d'un
échangeur 19
Figure I.16. Méthode de DTML 20
Figure I.17. Méthode de NUT 20
Figure I.18. Présentation d'un système
automatisé 22
Figure I.19. Architecture d'un API 23
Figure I.20. Principe de mesure d'un capteur 24
Figure II.1. Vue aérienne des gisements 26
Figure II.2. Bande transporteuse 27
Figure II.3. Vue du Cyclone et du SAG Mill 27
Figure II.4. Parties constitutives du SAG Mill 29
Figure II.5. Composants de la salle de lubrification des
paliers 31
Figure II.6. Schéma de puissance du SAG Mill 33
Figure II.7. Température de l'huile du 28/08/2008 au
30/10/2008 42
Figure II.8. Température de l'huile du 01/06/2009 au
01/12/2009 43
Figure II.9. Température de l'huile du 01/09/2009 au
08/12/2009 44
Figure II.10. Fuite de l'huile au niveau des joints 45
Figure II.11. Température de l'huile dans le
réservoir : Février 2012 46
Figure II.12. Température de l'huile dans le
réservoir : Mars 2012 46
Figure II.13. Température de l'huile dans le
réservoir : Avril 2012 47
Figure III.1. Système de lubrification muni de
l'échangeur 49
Figure III.2. Configuration du système de
refroidissement 50
Figure III.3. Schéma hydraulique de l'échangeur
57
Figure IV.1. Système de refroidissement 60
Figure IV.2. Circuit hydraulique du système de
refroidissement 61
Figure A.2.1. Circuit de commande du SAG Mill 72
VI
TABLE DES TABLEAUX
Tableau 2.1. Caractéristiques des moteurs des pompes de
lubrification et du SAG Mill 32
Tableau 2.2. Conditions de validation de démarrage du
moteur du SAG Mill 34
Tableau 2.3. Température de l'huile au niveau des
paliers du 28/08/2008 au 30/10/2008 36
Tableau 2.4. Température de l'huile au niveau des
paliers du 01/06/2009 au 31/08/2009 37
Tableau 2.5. Température de l'huile au niveau des
paliers du 01/09/2009 au 08/12/2009 38
Tableau 2.6.Température de l'huile dans le
réservoir de Février - Avril 39
Tableau 2.7. Données climatologiques de la ville de
Lubumbashi 40
Tableau 3.1. Composants électroniques du circuit de
lubrification et de refroidissement 48
Tableau 3.2. Dimensions échangeur et
propriétés thermo physiques des fluides 53
Tableau 3.3. Résultats de calcul de l'échangeur
56
Tableau 3.4. Caractéristiques du circuit de
l'échangeur 58
Tableau 4.1. Identification des zones fonctionnelles 59
Tableau 4.2. Description fonctionnelle du système de
refroidissement 62
Tableau A.1.1.Classification ISO des huiles industrielles
69
Tableau A.1.2. Désignation des échangeurs TEMA
70
Tableau A.1.3. Tableau du coefficient des pertes de charge
singulière 71
Tableau A.2.1. Fiche technique de l'huile ALPHA SP 320 73
Tableau A.3.1. Conductivité des différents
Matériaux 74
Tableau A.3.2. Caractéristiques de l'eau 75
Tableau A.3.3. Caractéristiques du cuivre 76
Tableau A.4.1. Dimensions des tubes pour échangeurs de
chaleur 77
Tableau A.4.2. Gamme d'échangeur produit par QVF
LTD® 78
Tableau A.4.3. Caractéristiques des pompes LT LEROY
SOMER® 79
VII
LISTE DES SYMBOLES
Symbole
|
Unité
|
Définition
|
C~
|
W/K
|
Débit de capacité thermique d'un fluide :
AñVq (débit calorifique) Ou débit massique
Ù= m~ c,
|
Hg
|
m
|
Hauteur géométrique
|
Hm
|
mm CE (ou Pa)
|
Hauteur manométrique
|
N~
|
Nombre
|
Nombre de tubes par passes
|
Pm
|
m
|
Périmètre mouillé, intersection de la paroi
et de la section droite A
|
~~~
|
m/s
|
Vecteur vitesse
|
Vq ou V
|
m/s
|
Vitesse moyenne de débit dans une section donnée
|
c,
|
J/(kg. K)
|
Capacité thermique massique à pression constante
|
m
|
kg/s
|
Débit - masse : m = AñVq
|
#~
|
Nombre
|
Rendement de la pompe
|
$~~
|
W/m2
|
Puissance thermique surfacique (vecteur dont l'orientation est en
général perpendiculaire à la surface, par simplification
ö )
|
?'
|
K
|
Différence de température de mélange des
deux fluides en une même section droite de l'échangeur
|
DTML
|
°C
|
Différence des températures de mélange
moyenne logarithmique (moyenne logarithmique de ?T de x = 0 à x = L)
?Te - ?T.
DTML K
= si = cte
|
?Te
ln
|
?T.
|
NUT
|
Nombre
|
Nombre d'unités de transfert
KS
NUT= C~1 C2~
|
Cl si <
|
A
|
m2
|
Section droite de passage d'un fluide
|
F
|
Nombre
|
Facteur de correction de la différence des
températures moyenne
logarithmique DTML
F = 1 pour une configuration à contre courant
|
H
|
J/kg
|
Enthalpie massique
|
J
|
mm CE (ou Pa)
|
Pertes de charge régulières ou reparties
|
K
|
W/(m2. K)
|
Coefficient d'échange convectif global (du fluide 1 au
fluide 2) ou coefficient de transmission thermique globale
|
L
|
m
|
Longueur (ou indicée, longueur du circuit d'un des
fluides).
|
P
|
Pa ou bar
|
Pression
|
Pu
|
W
|
Puissance utile (ou d'entrainement du moteur)
|
Q
|
J
|
Quantité d'énergie thermique
|
R
|
m
|
Rayon variable
|
S
|
m2
|
Surface d'échange entre deux fluides ; si indicée 1
ou 2, surface d'échange du fluide correspondant avec la paroi en
contact
|
VIII
T
|
K (ou en °C) Température locale ; par extension,
température de mélange dans une section
A donnée
|
Z
|
mm CE (ou Pertes de charge singulières ou
localisées
Pa)
|
b
|
mm Distance entre 2 chicanes
|
d( ou D)
|
mm Diamètre
|
e
|
m (ou Epaisseur (ou exponentielle)
nombre)
|
g
|
m/s2 Accélération gravitationnelle
locale
|
h
|
W/(m2. K) Coefficient d'échange convectif local
fluide/paroi
|
k
|
Nombre Coefficient de perte charge (régulière)
|
p
|
mm Pas
|
r
|
Nombre r = VW VX rapport des débits de capacité ( r
~ 1)
|
t
|
s Temps
|
x,y,z
|
m Coordonnées du repère orthonormé
|
^
|
m2. K/W Resistance thermique surfacique
|
_
|
W Puissance ou flux thermique
|
8
|
N. ma2 Contrainte de cisaillement
|
b
|
Nombre Efficacité d'un échangeur :
cdWaceW
C1 ~
å = avec <C2
|
cdWacdX
|
A
|
W/(m. K) Conductivité thermique
|
g
|
PI = Pa. s Viscosité dynamique
1PI = 10P
|
y
|
m2/s Viscosité cinématique (í =
ì )
ñ
|
j
|
Nombre Coefficient de perte de charge (singulière)
|
p
|
kg/ml Masse volumique
|
Indices
|
|
e
|
entrée, extérieur
|
I
|
Intérieur
|
p
|
Paroi
|
s
|
sortie
|
o
|
Linéique
|
1
|
fluide 1
|
2
|
fluide 2
|
IX
GLOSSAIRE
API (ou PLC): Automates Programmables Industriels (ou
Programmable Logic Controller)
ASTM: American Society Testing Materials
BP (LP): Basse pression (Low pressure)
BWG: Birming-ham Wire Gauge
CNTP : Condition Normale de Température et de
pression
DCS: Direct Control System: Système de contrôle
local.
E/S: Entrée/Sortie Interface
FSL: Flow Switch level
HP : Haute pression
INTERLOCK (verrouillage) : Système de protection des
équipements industriels qui pose des conditions avant que
l'équipement démarre en toute sécurité.
P.C : Partie commande
P.O: Partie opérative
PSL: Pressure Switch Level
RH: Resistance hydraulique
rpm : round per minute (ou tour par minute)
SAG Mill : Semi Autogenous Grinding Mill (ou Broyeur à
boulets semi autogène)
SCADA: Supervisor Controller and Data Acquisition: Système
de contrôle à distance supervisé par les moniteurs dans une
salle de contrôle
TEMA: Tabular Exchanger Manufacture Association TIT: Temperature
Indicating Transmitter VI: Viscosity Index (ou indice de viscosité) LSL:
Low switch level
Mis à part cette introduction et la conclusion, notre
travail comprend quatre chapitres. Le premier chapitre traite des
considérations générales dans lesquelles nous passons
1
INTRODUCTION GENERALE
La lubrification en générale et celle des
paliers à coussinet en particulier est un domaine qui intéresse
les industriels, les exploitants et les constructeurs car épargnant
l'équipement ou la machine des frottements excessifs en sa partie de
contact et en mouvement. Elle doit répondre cependant, à
certaines exigences telles que le refroidissement en vue de garantir la
disponibilité opératoire de l'équipement aussi bien
préserver le plus longtemps possible la qualité de l'huile
lubrifiante.
L'huile hydraulique utilisée pour la lubrification des
paliers à coussinets du SAG Mill de Ruashi Mining voit sa
température augmenter au fur et à mesure à cause des
frottements et cela au-delà de la plage de fonctionnement car ce circuit
est dépourvu d'un système adéquat de refroidissement.
De ce fait, notre étude en ce domaine est surtout
dirigée vers le contrôle de la température de l'huile de
lubrification des paliers du SAG Mill qui est un paramètre essentiel
dans le fonctionnement de ce dernier. Les montées excessives de la
température de cette huile influent négativement sur ses
propriétés lubrifiantes, l'état de surface des coussinets
et rend la lubrification difficile à cause des fuites au niveau des
joints. C'est pourquoi dans le souci d'optimiser et contourner les
difficultés liées aux montées récurrentes de la
température d'huile du circuit de lubrification, nous nous proposerons
dans ce travail de dimensionner l'échangeur avec le logiciel Matlab 7.0
à gérer par l'automate Siemens SIMATIC S7-300.
Le système de refroidissement (échangeur) est
à munir des modules électroniques tels que les capteurs de
température, de pression, de débit et de niveau. La logique de
programmation pour la partie commande est à faire à l'aide du
logiciel « step 7 ».
Cette étude compte apporter aux industriels de Ruashi
Mining et aux chercheurs un modèle de dimensionnement du système
de refroidissement du circuit de lubrification des paliers du SAG Mill (et de
tout autre circuit similaire) en vue de contrôler les grandeurs physiques
via les modules électroniques et permettre par cette occasion le bon
fonctionnement du SAG Mill afin d'atteindre les objectifs de production de la
pulpe avec plus d'efficacité.
2
en revue les huiles hydrauliques, les principes de
lubrification hydrostatique des paliers à coussinets, une brève
théorie sur les échangeurs ainsi que l'automatisation.
La présentation du lieu de travail tout en faisant
ressortir l'impact que les montées de températures de l'huile
jouent sur le circuit de lubrification des paliers, l'analyse ainsi que
l'interprétation des données de température font l'objet
du second chapitre. Tandis que le troisième chapitre quant à lui
concerne le dimensionnement de l'échangeur au regard des données
de l'évolution des températures dans le système.
Le quatrième chapitre est une de mise au point d'un
système de contrôle et de commande du système de
refroidissement par eau, il présente également l'algorithme de
programmation dudit système.
3
CHAPITRE I. CONSIDERATIONS GENERALES
Le fonctionnement du SAG Mill requiert l'existence d'un
circuit de lubrification qui doit être adapté au système
réalisé et répondre aux exigences du cahier de charge.
D'où la nécessité d'avoir une huile hydraulique
répondant aux normes quant à ce qui concerne ses
propriétés lubrifiantes, un système de refroidissement
muni des modules électroniques pour réguler les montées de
température due aux frottements des organes en mouvement.
I.1. HUILES HYDRAULIQUES [1,2]
Les systèmes hydrauliques utilisent des fluides qui ont
une influence notable sur leur conception, leurs conditions de fonctionnement,
leur durée de vie. Il est donc utile d'en rappeler les
caractéristiques essentielles.
Le fluide hydraulique a pour rôle de transmettre
l'énergie de la pompe hydraulique aux organes de travail tels que les
vérins et moteurs. Il doit également lubrifier et protéger
les différents organes du circuit. Pour assurer ces deux fonctions
correctement, il doit posséder un certain nombre de qualités
fondamentales:
- Viscosité appropriée;
- Variation de viscosité avec la température aussi
faible que possible;
- Pompabilité à la température minimale
d'utilisation;
- Propriétés lubrifiantes;
- Propriétés antirouille et anticorrosives.
I.1.1. Viscosité des lubrifiants [3]
De toutes les propriétés physiques et chimiques
à considérer en lubrification, la viscosité est l'une des
plus importante car permettant le bon fonctionnement d'un circuit et de ses
composants : Dans les paliers, les engrenages et les systèmes
hydrauliques, c'est la viscosité qui détermine les pertes par
frottement, la capacité de charge et l'épaisseur du film d'huile.
Cette viscosité doit être supérieure à une valeur
limite qui dépend du type d'organe, de la vitesse relative des faces en
présence.
Selon la norme N.F. T 60-100 de Novembre 1959 : « La
viscosité d'un liquide est la propriété de ce liquide,
résultant de la résistance qu'opposent ses molécules
à une force tendant à les déplacer par glissement dans son
sein ».
4
vw
u
r
Vitesse t
Plaque mobile (2)
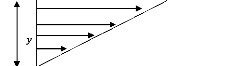
e
Fluide
Plaque mobile (1)
Figure I.1. Champs de vitesse dans le film (Ecoulement de
COUETTE)
Considérons deux plaques parallèles horizontales
distantes de e (figure. I.1), Un fluide sépare ces deux plaques.
L'épaisseur e est très faible par rapport aux dimensions des
plaques, donc on parle de film d'huile. On constate qu'il est nécessaire
d'exercer une force tangentielle vw parallèle à la
direction du filet pour déplacer tangentiellement la plaque (2) à
la vitesse V, par rapport à la plaque (1) supposée immobile.
Si l'écoulement est linéaire : le champ des
vitesses admet l'allure représentée sur la figure I.1, il y a
donc glissement des couches de fluide les unes par rapport aux autres, et
l'on
peut définir un gradient de vitesse : xy(z"
xz
La résistance au glissement est
caractérisée par une contrainte de cisaillement {(r". Le
modèle Newtonien suppose qu'il existe une relation de
proportionnalité entre la contrainte de cisaillement et le gradient de
vitesse comme suit :
dV(y"
ä~y" = u. (I. 1"
dy
Avec u coefficient de viscosité dynamique qui
caractérise la résistance au glissement fluide sur fluide.
Dans les applications industrielles, c'est la viscosité
cinématique qui est souvent utilisée. La relation qui lie la
viscosité cinématique à la viscosité dynamique est
donnée par l'expression ci-dessous :
I.1.2. Indice de viscosité [4]
L'importance de la variation de viscosité avec la
température est exprimée par un nombre conventionnel, obtenu
empiriquement à partir des mesures de viscosité à 100 et
210 °F, appelé indice de viscosité. Plus l'indice de
viscosité est élevé, moins la viscosité varie en
fonction de la température.
5
Pour définir la viscosité d'une huile, il est
évidemment nécessaire de choisir des températures de
référence. Une norme internationale ISO recommande d'utiliser les
températures de 40°C et 100 °C.
y' Si l'huile est trop visqueuse, l'écoulement se fait
mal, il y a risque de cavitation, de vibrations et chute de rendement ;
y' Si l'huile est trop fluide, les fuites internes augmentent,
les conditions de lubrification hydrodynamique sont défavorables, il y a
chute de rendement et risque d'incident
Les viscosités idéales dans les conditions de
fonctionnement se situent dans la plage 15 à 100cSt. La limite
inférieure de viscosité assurant une lubrification convenable est
de 10cSt; la limite supérieure de viscosité pour les
démarrages à froid, assurant la non cavitation est comprise entre
500 et 1000cSt.
Le tableau A.1.2 donne la classification des huiles
industrielles et leurs limites minimales et maximales de viscosité.
I.1.3. Influence de la température et de la pression
sur la viscosité [2]
La température et la pression sont les
paramètres les plus influents sur la viscosité d'un fluide. De ce
fait, la viscosité des huiles minérales croit avec la pression de
façon quasi exponentielle. Une viscosité d'huile peut atteindre
le double de sa valeur pour une pression croissant de 0 à 300 MPA. Il en
est de même pour les pompes à haute pression. Cependant, elle
décroît de façon quasi exponentielle avec la
température (figure. I.2).
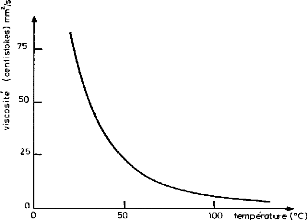
Figure I.2. Variation de la viscosité avec la
température pour une huile minérale
La viscosité est une grandeur dépendante de la
température ainsi que de l'agitation. Lorsque la température est
faible et que l'huile est donc froide, le frottement intérieur est
important et la viscosité élevée. Plus l'huile est chaude,
plus le frottement interne est réduit et la viscosité faible.
6
Pour une huile lubrifiante, on peut poser :
a(E c
u ~ u0e(I. 3)
Avec : E = a1 + a2T + a3T#177;2
Où /20 est la viscosité dynamique à une
température donnée, T la température absolue et où
a1 , a2, a3 sont à déterminer pour chaque lubrifiant.
La relation de Mac Coull et Walther nous permet
d'écrire:
Log10Log10(í + a) = -mLog10T + n (I.4)
a, m et n des constantes qui dépendent du lubrifiant,
et T la température absolue. La valeur de a dépend de
l'unité de viscosité ; si y est en centistokes a est compris
entre 0,6 et 0,75.
Cette représentation (Mac Coull et Walther) est
très pratique à exploiter ; en effet, il suffit de
connaître deux viscosités à deux températures
différentes (par exemple à 40 et à 100 °C,
généralement données dans les fiches techniques), de
tracer la droite ASTM pour déterminer les viscosités de l'huile
à d'autres températures par interpolation ou par extrapolation
(figure I.3).
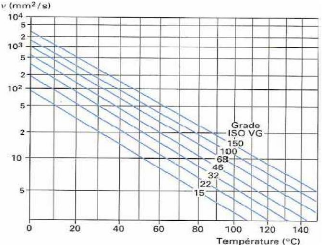
Figure I.3. Variation viscosité-température
sur abaque ASTM
D'autre part, la perte de charge subie par un fluide dans une
tuyauterie étant une fonction croissante de la viscosité, il
importe de limiter celle-ci afin d'éviter d'une part que la
dépression à l'entrée des pompes ne devienne trop grande,
conduisant ainsi à la cavitation et à la libération de
l'air en solution dans l'huile, et d'autre part que les pertes d'énergie
dans les
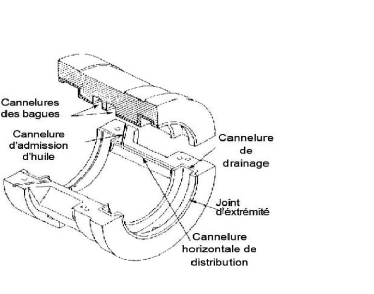
7
conduites de puissance ne deviennent trop grandes, ce qui
diminuerait fortement le rendement global de l'installation.
I.2. LUBRIFICATION DES PALIERS LISSES
I.2.1. Principes qui régissent les paliers à
coussinets
[5,6]
Les paliers à coussinet sont en apparence très
simples. Constitués d'un métal doux (alliage antifriction
composé principalement d'étain et de plomb), ils épousent
la forme de l'arbre et supportent ainsi la charge. L'arbre et les paliers se
trouvent lubrifiés de façon continue par un film d'huile, ce qui
diminue le frottement. Les corps étrangers qui s'infiltrent entre les
paliers et l'arbre deviennent emprisonnés dans le matériau
antifriction, protégeant ainsi la partie plus dure et plus
coûteuse de l'arbre.
Généralement, les frottements sont importants au
démarrage de la machine et le palier ne remplit pas
nécessairement son rôle s'il a à supporter de fortes
tensions pendant cette période. La figure I.4, nous montre les dommages
qui peuvent advenir lors du fonctionnement d'un palier à coussinet.
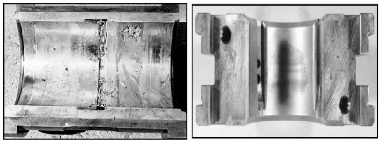
a. Bris par érosion b. Erosion au
démarrage
Figure I.4. Dommages sur les coussinets
La figure I.4a illustre l'érosion du palier lisse
montrant le métal antifriction resolidifié dans la cannelure de
lubrification centrale, tandis que la figure I.4b montre des
légères traces au fond d'un palier soumis à une charge
verticale.
I.2.2. Lubrification des paliers à coussinet [5, 7,
8,9]
Une lubrification adéquate permettant un minimum de
frottement est l'élément clé de la durée de vie
d'un palier à coussinet. Un débit continu d'huile est
assuré à l'aide de la pompe à engrenage (système
forcé). L'huile est acheminée par la partie supérieure de
l'arbre où une cannelure de distribution se remplit (Figure I.5).
L'huile est extraite de la cannelure de drainage à chacune des
extrémités pour être ensuite refroidie à l'aide d'un
échangeur ou lorsqu'elle se mélange à celle qui se trouve
déjà dans le réservoir.
8
Figure I.5. Palier à coussinet
En outre, la lubrification des paliers existe sous
différentes formes à savoir :
V' La lubrification hydrodynamique
V' La lubrification mixte
V' Et la lubrification hydrostatique qui fait l'objet de
notre travail.
En lubrification hydrostatique, la formation et le maintien
d'un film de fluide imposent l'existence d'une pression dans ce film afin
d'équilibrer la charge appliquée entre les deux surfaces du
mécanisme. Cette pression est engendrée par un système
extérieur au contact (pompe) et son calcul permet de déterminer
la charge que peut supporter le contact, le couple ou la force de frottement et
le débit de fluide dans le mécanisme.
Les deux principales méthodes utilisées pour
introduire le liquide à l'intérieur du palier sont l'alimentation
à débit constant et celle à pression constante (figure
I.6a).
Dans les systèmes à débit constant, une
pompe à débit constant est placée entre le
réservoir et l'alvéole ou cannelure. Ce système est peu
employé car, lorsque le mécanisme comporte plusieurs
alvéoles (ce qui est pratiquement toujours le cas), il faut soit
alimenter chacun d'entre eux par une pompe individuelle, soit utiliser des
régulateurs à débit constant. Cette solution, qui assure
une grande raideur, est complexe et coûteuse. On lui
préfère le système à pression constante.
Dans les mécanismes à pression constante, une
résistance hydraulique est placée immédiatement en amont
de l'alvéole. Le rôle de cette résistance est de
créer une perte de charge, c'est-à-dire d'asservir le
débit à la chute de pression. Ce système, simple à
mettre en oeuvre, permet d'alimenter plusieurs alvéoles avec une seule
pompe à condition, que le débit de celle-ci soit suffisant. Dans
la pratique, le système hydraulique est plus complexe. La figure I.6b
donne le schéma du circuit pour l'alimentation à pression
constante d'un palier à quatre alvéoles. Une pompe alimente le
palier à un débit supérieur d'environ 30 % à celui
nécessaire ; le surplus de liquide retourne au réservoir par
l'intermédiaire d'un régulateur de
9
pression. Un capteur de pression permet d'arrêter
l'entraînement du rotor si la pression atteint une valeur trop faible. Le
clapet anti-retour et l'accumulateur hydraulique assurent l'alimentation du
palier jusqu'à l'arrêt complet de l'arbre. L'écoulement est
ensuite dérivé vers chaque alvéole ; sur chaque portion de
circuit, on peut prévoir un clapet anti-retour en cas de surpression
dans un alvéole. La résistance hydraulique RH doit être
placée au plus près de l'alvéole afin d'éviter les
instabilités de type pneumatique dues à la compressibilité
du lubrifiant. Une pompe peut être nécessaire pour assurer le
retour du lubrifiant vers le réservoir. Une prise de température
T permet de contrôler la température du liquide à la sortie
du palier et déclencher l'arrêt si la température devient
trop importante. Enfin, un système de refroidissement assure une
température constante au niveau de l'alimentation.
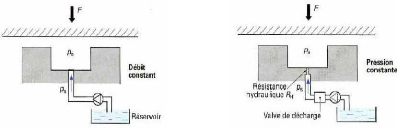
Figure I.6. Principe de fonctionnement d'un palier
hydrostatique
a. Schématisation de deux types d'alimentation
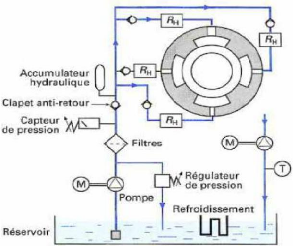
b. Cas réel
a
at = 0 (I.5)
10
I.3. THEORIE SUR LES ECHANGEURS
L'échangeur d'énergie thermique est un des
éléments essentiel dans le circuit de lubrification du broyeur,
que son but est de refroidir l'huile hydraulique. Il s'agit d'un système
qui permet de transférer un flux de chaleur d'un fluide chaud (huile)
à un fluide froid à travers une paroi sans contact direct entre
les deux fluides.
I.3.1. Définitions de l'échangeur
élémentaire [10]
I.3.1.1. Aspect extérieur : échangeur
comme quadripôle
Vu de l'extérieur, un échangeur se
présente comme une boîte noire pourvue de deux entrées et
de deux sorties auxquelles sont mesurées les caractéristiques
essentielles de fonctionnement à l'un de ces quatre pôles. Les
fluides 1 ou 2 ont des paramètres mesurables et mesurés à
l'entrée et à la sortie du quadripôle:
- l'état : liquide, gazeux ;
- le débit-masse, constant de l'entrée à la
sortie ;
- la température, variable dans l'échangeur ;
- la pression, peu variable.
Par ailleurs, les caractéristiques thermo physiques de
chacun des deux fluides peuvent être déterminées entre
autre: la capacité thermique massique (chaleur massique)cp,
la masse volumique p , la conductivité thermique A , la viscosité
4u ;
Le quadripôle est généralement muni de
deux pompes (ou ventilateurs) destinées à mettre en mouvement les
fluides 1 et 2 à l'intérieur de l'échangeur, en
générant pour chacun des fluides entre l'entrée et la
sortie une différence de pression égale à la perte de
pression visqueuse à l'intérieur de l'échangeur. Cette
perte de pression (perte de charge) dépend pour chacun des fluides de la
nature du fluide, de sa température, de son débit et de la
géométrie interne de l'échangeur.
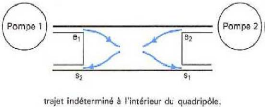
Figure I.7. Schéma du quadripôle
Hypothèses restrictives
1. Le régime est stationnaire ou permanent
c'est-à-dire que la température T est indépendante du
temps t
11
2. Les deux fluides sont physiquement séparés
l'un de l'autre par une paroi étanche au transfert de masse mais
perméable au transfert d'énergie thermique. En
conséquence, le débit-masse de chacun des fluides est constant
tout au long de son écoulement et en particulier :
D'où
|
(AñVq)ei = (AñVq)si (AñVq)ez =
(AñVq)sz
m 1 = (AñVq)ei = cte
m 2 = (AñVq)ez = cte
|
|
(I . 6)
|
3. L'enthalpie perdue par l'un est intégralement
cédée à l'autre ; c'est donc l'adiabatisme sans
stockage
#177;(He - H.)1 = (He - H.)2
Ce qui en monophasique conduit à :
#177;(AñcpVq)1(Te - T.)1 =
(AñcpVq)2(Te - T.)2 (I.7)
4. Le coefficient d'échange global K est admis comme
constant tout au long de l'échangeur si chacun des fluides reste
monophasique.
5. K constant tout au long de l'échangeur
I.3.1.2. Aspect interne : échange
élémentaire
Soit un élément de volume dT en évolution
thermique circulant en trois dimensions (x, y, z). cet élément
est repéré par son abscisse curviligne s grâce aux notions
de la température de mélange et de la vitesse de débit
(figure I.8) depuis l'entrée jusqu'à la sortie après un
trajet de longueur L. L'évolution de ce fluide est évidemment
couplée à celle du deuxième fluide et les deux calculs
doivent donc être concomitants.
En général la section droite de passage A d'un
fluide est constante de 0 à L en exceptant les zones de distribution ou
de collectage du fluide au voisinage de l'entrée ou de la sortie. Cette
section A, éventuellement somme des différentes sections droites
des canaux élémentaires si plusieurs de ceux-ci sont
montés en parallèle, est limitée par un
périmètre mouillé Pmdu canal ou de l'ensemble
des canaux.
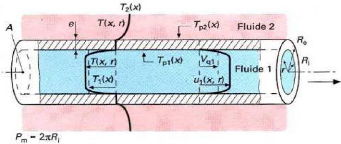
12
1 1
%o
%o
h9 h%
e 1
ë = ~I. 12"
K
° =
#177;2 : Résistance thermique de la paroi
séparatrice de 1 et de 2,
Figure I.8. Profil de température et de vitesse dans
un tube Le flux élémentaire perdu par le fluide 1
s'écrit alors :
|dÖ| = h9centsT9(x" - Tp9(x"£Pù9dx (I.8"
En admettant une condition à la limite exclusivement
convective définie par un coefficient h9 entre le fluide 1 et la paroi
p9. De même, pour le fluide 2 :
|dÖ| = h%centsT%(x" - Tp%(x"£Pù%dx (I.9"
Si Pù § Pù9 § Pù% :
séparation des deux fluides par plaques planes ou tubes peu épais
devant leur diamètre avec un échange monodimensionnel en x. Du
fait des hypothèses restrictives, ces flux élémentaires
sont égaux. Par ailleurs, ils sont transférés par
conduction dans l'épaisseur e de la paroi conductrice suivant
l'expression :
ë
|dÖ| = centsT~9~x" -
T~%~x"£Pùdx I. 10"
e
Avec Pù = ðD
Localement à la valeur de x choisie (I.10)
devient:
(T9 - T%"(x" = AT(x" =
dÖdx« (x" 1
1%o 1 %o e ë« ~I.11"
Pù h9 h%
x#172; x représente le
flux linéique et P
dx ()=tPZ~ ~ ~ q (Re
mtP
Il en résulte de toutes ces relations qu'en chaque point de
l'échangeur, la différence
de température de mélange des deux fluides
crée un flux surfacique d'échange proportionnel à cette
différence ÄT (x " et à l'inverse d'une résistance
thermique surfacique égale à :
13
I.3.2. Architecture générale de
l'échangeur
L'échangeur a deux aspects complémentaires :
l'aspect global, caractérisé par des mesures aux
entrées-sorties, et celui de l'échange au niveau de la surface
élémentaire, caractérisé par son flux. Ce dernier
est défini à partir des températures de mélange, de
la nature des matériaux et des dimensions géométriques et
mécaniques dont la vitesse.
L'un des fluides circule dans un canal à
géométrie fermée, qu'il s'agisse d'un tube circulaire ou
d'une section rectangulaire parfois très allongée
(échangeur à plaques). L'autre fluide circule à
l'extérieur de ce canal.
Trois géométries d'écoulement peuvent
être réalisées :
- Ecoulements des deux fluides parallèles et de
même sens : l'évolution qualitative des températures est
représentée sur la figure I.9a;
- Ecoulements parallèles mais de sens contraires ou
à contre-courant (figure I.9b);
- Ecoulements perpendiculaires l'un à l'autre : la
figure I.9c. est un peu plus complexe puisque l'un des fluides s'écoule
suivant oe, l'autre suivant r. La figure symbolique d'un radiateur d'automobile
y est donnée. n étant le nombre de plans perpendiculaires
à l'écoulement d'air et contenant des tubes d'eau (1 Y 3 Y 4 sur
le croquis).
Dans le cas des courants croisés on a :
(Añc'vq"· ?T = (Añc'vq",1 ?T
?y« ?z« (I. 13"
· ,1
14
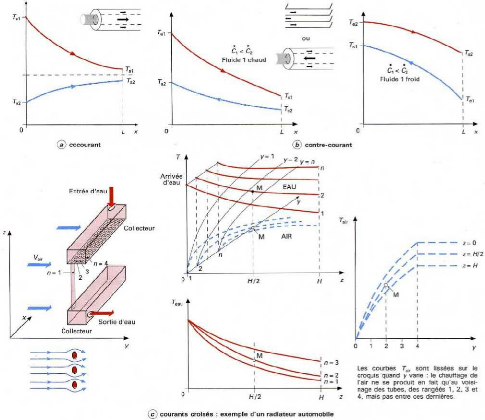
Figure I.9. Différents profils qualitatifs de
température dans un échangeur
Les trois écoulements : à concourant, à
contre-courant, à courants croisés sont rarement utilisés
dans toute leur simplicité. Par ailleurs, le concepteur a le choix entre
deux géométries élémentaires principales :
- Les tubes, ce qui fixe l'espace dévolu à l'un
des fluides mais non celui de l'autre fluide : il peut être soit
entièrement enfermé, soit non délimité (cas de
l'air pour le radiateur d'automobile) ;
si T.1 < T.2 : configuration contre courant
si T.1 > T.2 : configuration co-courant
si T.1 < Te2 : les deux configurations sont difficilement
réalisables
- Les plaques planes choisies pour un fluide imposent la
même géométrie pour l'autre.
15
Souvent le choix des combinaisons résulte de
contingences technologiques : des risques d'encrassement dans les tubes les
feront préférer rectilignes et parallèles, donc faciles
à ramoner plutôt que spiralés ou en U. Mais ce sont des
propriétés plus fondamentales, intrinsèques, qui serviront
préférentiellement de référence.
I.3.3. Grandeurs classiques définissant
l'échangeur La DTML est donnée par :
Ö
ÄT1/41/41/41/4
= I. 14"
KS
De ce fait : Ö = KS ÄT = KSFÄT1/23/4
F dépend de la configuration des écoulements ;
il est calculé ou déterminé à partir d'abaques,
toujours compris entre 0 et 1. Il est important de noter que le DTML doit
être calculé comme si l'échangeur était en
contre-courant.
Efficacité et NUT
L'efficacité est donnée par l'expression :
(T,9 - T.9"C~9
~
(T,9 - T,%"C~9
Ö
(I.15"
Öù
å ~
Ainsi on définit trois types d'efficacité :
- Efficacité partielle en température
coté 1 : s9 ~ cdWacdX cdWaceW
-
cdWacdX
Ö
- Efficacité de l'échangeur : s =
Efficacité partielle en température coté
2 : s% ~ ceXacdX
ÖÀÁÂ
L'efficacité de l'échangeur est alors
donnée par la plus grande valeur de 9 ou %
Si C9 = C% on a å9 » å% donc å =
å9
ÄÅ
NUT ~ V W pour C9 = C% (I. 16"
I.3.4. Types d'échangeurs [11]
Les échangeurs sont classés sur base de
plusieurs critères et ils peuvent être regroupés de la
manière suivante :
- Les échangeurs tubulaires et à plaques pour des
raisons technologiques (figure I.10) ;
- Les évaporateurs et condenseurs pour leurs applications
;
- Et autres types d'échangeurs en fonction de la nature
de la paroi.
16
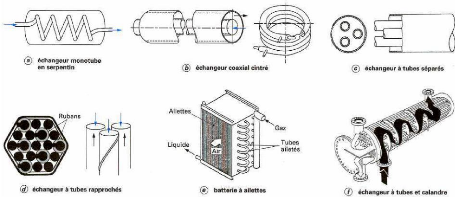
Figure I.10. Différents types d'échangeurs
tubulaires
En outre, le choix d'un échangeur de chaleur pour une
application donnée dépend de nombreux paramètres : les
propriétés physiques des fluides, leur agressivité, les
températures ainsi que les pressions de service. Les contraintes
d'encombrement et de maintenance doivent aussi être prises en compte,
ainsi que les considérations économiques.
I.3.5.Echangeur à tubes et calandre [11]
Les principales technologies d'échangeurs à
tubes et calandre sont représentées sur la figure I.11.La
désignation la plus couramment appliquée par ce type
d'échangeur est celle du standard américain TEMA, dans
lequel il existe trois classes : C, B et R, par ordre de
sévérité croissante.
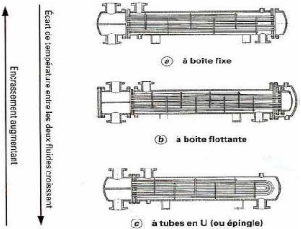
Figure I.11. Échangeur à tubes et
calandre
17
La classe C est réservée aux échangeurs
ne présentant aucun risque d'utilisation, la classe B est adoptée
pour la majorité des cas et la classe R est réservée aux
échangeurs fonctionnant dans des conditions très dures au point
de vue mécanique ou dans des conditions inhabituelles (gaz toxique par
exemple).
Un échangeur TEMA est désigné par trois
lettres représentant respectivement le type de boîte avant, de
calandre et de boîte arrière de l'échangeur. La figure I.12
donne les différents éléments constitutifs d'un
échangeur TEMA type AEL (Tableau A.1.2)
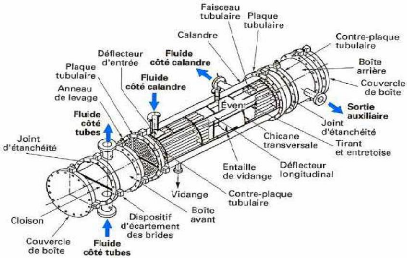
Figure I.12. Divers constituants d'un échangeur TEMA
type AEL
Les dimensions des tubes sont normalisées ; le
diamètre annoncé correspond exactement au diamètre
extérieur (Tableau A.4.1) et sont généralement de longueur
standard 2,44 ; 3,05 ; 3,66 ; 4,88 ou 6,10 m.
Le démontage du faisceau de tubes est de plus en plus
difficile au fur et à mesure que sa longueur s'accroît
(problème de rigidité du faisceau). Pour tous les
échangeurs démontables, il convient de laisser un espace libre
suffisant dans l'axe de l'échangeur pour permettre la sortie du faisceau
de tubes. Les matériaux utilisés dépendent des fluides
choisis ; les plus courants sont les aciers ordinaires, les aciers inoxydables,
le cuivre, le laiton, les cupronickels, le graphite, le verre ou les
matières plastiques.
Deux dispositions de tubes sont possibles : le pas
triangulaire et le pas carré (figure I.13). La disposition en pas
carré offre une plus grande facilité de nettoyage. La disposition
en pas triangulaire est plus compacte, donc plus économique. Les pas
standards les plus courants sont 0,024 ; 0,025 ; 0,030 ; 0,032 et 0,038 m
(15/16 ; 1 ; 19/16 ; 5/4 et 3/2 in). Le rapport du pas au diamètre
extérieur des tubes sera au minimum de 1,25 et sera pris
supérieur à 1,25 si l'on souhaite limiter les pertes de pression
côté fluide dans la calandre
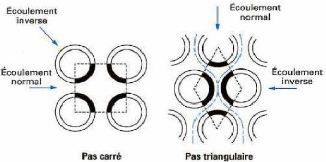
18
Figure I.13. Pas des tubes
I.3.6. Dimensionnement d'un échangeur [12, 13]
I.3.6.1. Logique de la phase de dimensionnement
Le dimensionnement thermique dans une installation
industrielle commence, tout d'abord, par la sélection du type
d'échangeur adapté au problème posé, puis vient la
phase de dimensionnement thermique proprement dite ; elle est destinée
à fixer par le calcul la surface d'échange nécessaire au
transfert de puissance sur les fluides considérés (figure
I.14).
Cette phase de calcul est le plus souvent itérative et
permet d'approcher par des essais successifs la solution qui semble la
meilleure, à la fois du point de vue thermique et du point de vue
hydraulique. L'aspect hydraulique concerne les pertes de pression (charge) sur
chaque circuit, et apparaît comme une contrainte au problème
d'optimisation thermique :
Sélection d'un type
d'échangeur
Choix d'un ensemble de
données
géométriques
Calcul thermique de
l'échangeur
Modification des
paramètres de
conception
Non
Puissance, pertes de
pression acceptables ?
Oui
Coût de l'échangeur
Calcul Numérique
Figure I.14. Logique de la phase de dimensionnement
thermique
19
I.3.6.2. Principe de calcul thermique d'un
échangeur
Le principe de calcul thermique de l'échangeur est
illustré sur la figure I.14 et peut être abordé de deux
façons algorithmiques très différentes :
Mode simulation :
Connaissant la géométrie complète de
l'appareil, ainsi que les deux fluides et leurs conditions d'entrée, on
désire connaître les conditions de sortie des fluides
(température, titre de vapeur), d'où la puissance thermique
échangée ;
Mode vérification :
Connaissant les deux fluides et la puissance thermique
à transférer entre eux, et ayant par expérience une
idée approximative de la géométrie de l'appareil, on
cherche à savoir si cet appareil est bien adapté ou non au
service demandé.
Données : Phase thermique Grandeurs
proprement dite : thermiques :
-


1) Calculs géométriques annexes
2) Calculs de transfert de chaleur

3) Calculs de pertes de pression

Puissance thermique (mode simulation) ou
Surface d'échange (mode vérification)
Pertes de pression
Débits, températures, encrassement
- Pressions, propriétés physiques des fluides
- Type d'appareil (tubes, plaques,...),
Type de configuration d'écoulement (co- courant,...)
Figure I.15. Principe de calcul thermique d'un
échangeur I.3.6. 3. Méthode du DTML
La valeur locale de la puissance élémentaire
dÖ échangée à travers un élément de
surface dS est donnée par l'équation :
dÖ = K (T1 - T2)dS (I. 17"
T1 et T2 températures des fluides F1 et F2 de part et
d'autre de la paroi, la surface d'échange totale s'obtient en
intégrant l'équation précédente (I.17):
S -- J
|
dÖ
(I. 18"
K(T1 -- T2)
|
|
L'intégration ne peut s'effectuer que pas à pas
si l'on connaît l'évolution du coefficient d'échange K en
fonction des températures T1 et T2, dont l'évolution suivant
l'écoulement doit elle-même être connue.
20
En se référant, à l'hypothèse
restrictive 5 (§ I.3.1.1, p.11), la surface s'obtient par la relation :
dÖ _ f dÖ
S = J KÄT12 -- J FKÄTML (I.19"
¼¼¼¼¼¼¼
Avec ÄT12 différence moyenne de
température entre les deux fluides sur tout l'échangeur. Le
déroulement du calcul peut être schématiquement le suivant
:
Détermination de la température
moyenne
caractéristique à partir des
températures
entrée/sortie
Calcul du ?TML
et du coefficient correctif F
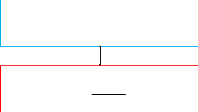
S =
FKÄTML
Calcul de la puissance échangée :
Ö = Ci(Tei - Ts1) = #177;C~2(Ts2 - Te2)
Recherche de la surface :
Ö
Figure I.16. Méthode de DTML
I.3.6.4. Méthode du NUT
Avec cette méthode, il est question de
déterminer les températures de sortie d'un échangeur
connaissant les températures d'entrée et la surface
d'échange. Ce problème est itératif, car on ne peut pas
trouver directement une température moyenne caractéristique des
fluides. Le déroulement du calcul peut être schématiquement
le suivant :
Estimation des températures de sortie
TS1 et Ts2
|
|
Coefficient d'échange global K
Détermination du NUT
et de l'efficacité E
Itération
Figure I.17. Méthode de NUT
21
I.3.7. Calcul de la tuyauterie [14]
Le calcul de la tuyauterie commence par l'évaluation
des pertes de charge dans les canalisations. Ces dernières tirent leurs
origines :
a. Des frottements entre les différentes couches de
liquide et des frottements entre le liquide et la paroi interne de la conduite
le long de l'écoulement : ces sont les pertes de charge
régulières.
k V2
J = d ñ 2 [Pa/mi (I.
20"
La détermination du coefficient de perte de charge
régulière k est complexe, on utilise cependant
les abaques fournies par les constructeur ou soit on fait appel à des
formules empiriques tel que si l'écoulement est:
- Laminaire ( Re < 2000) : loi de Poiseuille
:k = Re (I. 21"
- Turbulent lisse ( Re < 10Ï
): k = 0,316Re-1/4 = (100Re)-1/4 (I. 22"1
- Turbulent rugueux Re > 10Ï
: il ya d'autres lois tel que de Blench
b. De la résistance à l'écoulement
provoqués par les accidents de parcours (vannes, coudes, etc.,...) ; ce
sont les pertes de charges singulières ou localisés.
V2
Z = î ñ2 [Pa] (I.23"
Le tableau A.1.5 en annexe, nous donne les différentes
valeurs du coefficient î selon la nature de l'accident
de parcours.
Nous venons de nous rendre compte qu'il y a des pertes de
pression le long du parcours dans les tuyauteries. D'autre part, le fluide a
besoin de pression pour pouvoir circuler normalement dans le système
(échangeur). Cette pression sera donnée, soit par la
différence d'altitude ou soit par une pompe de circulation. Cette
pression motrice est donnée également en mm CE, on l'appelle
« hauteur manométrique de l'installation ». Ainsi, ces pertes
de pression doivent être compensées par la pression motrice, il
faut cependant que, pour chacun des circuits, la hauteur manométrique
Hm soit égale à la somme de la
hauteur géométrique, les pertes de charge linéaires et
localisées.
Hm=Hg+J+Z (I.24"
ù~ ÔÀ
D'où la puissance d'entrainement pour l'eau dans le CNTP
Pu =
[kW] (I. 25"
367xip
1 La loi de Blasius
çb : 0,6 - 0,7 pour les pompes
volumétriques (piston) çb : 0,4 - 0,8 pour les
pompes centrifuges
22
I.4. L'AUTOMATISATION
Au sein des industries modernes chimiques,
métallurgiques ou pétrolières du 21ème
siècle, les différents procédés régissant
leurs fonctionnements respectifs, sont contrôlés et
commandés au moyen des terminaux bien définis suivant des
programmes chargés au préalable dans des processeurs
appropriés qui sont dans la plupart des cas des automates programmables
industriels.
L'usage de ces unités automatisées a pour
avantage d'assurer une optimisation de la production à tous les niveaux
et de permettre ainsi une amélioration du rendement par la
régulation automatique de tous les processus industriels.
I.4.1. Structure d'un système automatisé
[15,16]
Tout système automatisé comporte :
- Une Partie Opérative (P.O.) procédant au
traitement et à l'exécution des ordres provenant de l'automate ou
la partie commande,
- Une partie commande (P.C.) qui élabore, coordonne
les ordres nécessaires à l'exécution du processus, en
fonction des rendus d'exécution qui lui sont fournis par la partie
opérative ; la partie commande assure le traitement logique des
informations et échange des informations avec l'extérieur du
système pilote, usager, surveillant dont elle reçoit les
consignes et à qui elle fournit des comptes rendu visuels ou sonores.
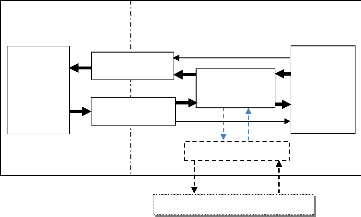
AUTRES PARTIES COMMANDES
PARTIE OPERATIVE PARTIE COMMANDE
COMMUNICATION
DIALOGUE
HOMME
MACHINE
MACHINE
UNITE DE
TRAITEMENT
CAPTEURS
PRE-
ACTIONNEURS
Figure I.18. Présentation d'un système
automatisé
I.4.2. Automate programmable industriel : API [16,17]
Un automate programmable est un dispositif
électronique programmable qui reçoit les informations relatives
à l'état du système (via les capteurs, contrôleurs)
et puis commande les pré-actionneurs (partie opérative) suivant
le programme inscrit dans sa mémoire.
La structure interne d'un API se représente comme suit
:
23
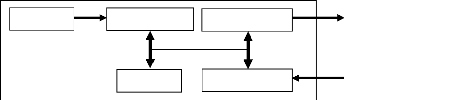
Commande
des pré-actionneurs
Dialogue Homme/Machine Etat du
système
Horloge
Microprocesseur
Mémoire
Bus
Interface de sortie
Interface d'entrée
Figure I.19. Architecture d'un API
Un API se compose donc de trois grandes parties :
- Le processeur ;
- La zone mémoire ;
- Les interfaces Entrées/Sorties
I.4.2.1. Le microprocesseur
Le microprocesseur réalise toutes les fonctions logiques
ET/OU, les fonctions de temporisation, de comptage, de calcul... à
partir d'un programme contenu dans sa mémoire. Il est connecté
aux autres éléments (mémoire et interface E/S) par des
liaisons parallèles appelées « BUS» qui
véhiculent les informations sous forme binaire.
I.4.2.2. La zone mémoire
La Zone mémoire va permettre :
- De recevoir les informations issues des capteurs
d'entrées ;
- De recevoir les informations générées par
le processeur et destinées à la commande des sorties (valeur des
compteurs, des temporisations, ...) - De recevoir et conserver le programme du
processus
I.4.2.3. Les interfaces d'entrées/sorties
Les entrées reçoivent l'information en
provenance des capteurs, traite le signal en le mettant en forme tout en
éliminant les parasites et en isolant électriquement
l'unité de commande de la partie opérative.
Les sorties commandent les pré-actionneurs (relais,
électrovannes ...) et éléments des signalisations du
système (voyants), adapte les niveaux de tensions de l'unité de
commande à celle de la partie opérative du système en
garantissant une isolation galvanique entre ces dernières.
Le réseau d'interfaces est constitué:
- Des interfaces de puissances qui délivrent aux
actionneurs au moment voulu, l'énergie nécessaire.
- Des capteurs transformant les grandeurs physiques
détectés sur la partie opérative (position, vitesse,
pression, etc.) en signaux adaptés au traitement de la partie
commande.
- Des boutons poussoir et clavier qui permettent à
l'opérateur de communiquer des informations à la partie
commande.
- Des voyants qui renseignent l'opérateur de l'état
du système.
Figure I.20. Principe de mesure d'un capteur
24
I.4.3.Capteurs [18 :22]
I.4.3.1. Présentation
Tout problème d'automatisme commence par celui de la
saisie d'information provenant du système à automatiser. Ainsi,
les capteurs se définissent comme étant des composants de la
chaîne d'acquisition qui prélèvent une information sur le
comportement de la partie opérative et la transforment en une
information exploitable par la partie commande.
Une information est une grandeur abstraite qui précise
un événement particulier parmi un ensemble
d'événements possibles. Pour pouvoir être traitée,
cette information sera portée par un support physique (énergie),
on parlera alors de signal. Les signaux sont généralement de
nature électrique ou pneumatique.
Dans les systèmes automatisés séquentiels
la partie commande traite des variables logiques ou numériques. Ainsi,
l'information délivrée par un capteur peut être :
- Logique (2 états) :
Il ne compte que deux valeurs possibles, c'est un signal tout
ou rien (TOR). (L'état logique 1 traduit la présence du signal,
et l'état logique 0 correspond à l'absence du signal). Notons
aussi que les capteurs logiques modernes possèdent toujours deux
contacts à savoir :
· Un contact normalement fermé (qui s'ouvre
lorsqu'il y a commutation en atteignant le seuil défini à
l'avance).
· Et un contact normalement ouvert (qui se ferme lors
d'une éventuelle commutation au seuil préalablement
défini).
- Numérique (valeur discrète),
- Analogique (prend une infinité des valeurs dans un
intervalle donné) dans ce cas il faudra adjoindre à la partie
commande un module de conversion analogique numérique.
|
Énergie
|
|
Grandeur physique
|
|
Signal électrique
|
- Température - Pression - Force - Etc.
|
CAPTEUR
|
- Signal logique (TOR) - Signal analogique - Signal
numérique
|
|
|
25
I.4.3.2. Types de capteurs
Les capteurs peuvent être classés en fonction:
- De la nature de la grandeur physique captée ou
mesurée ; on parle alors de capteur de position, de température,
de vitesse, de force, de pression, etc.
- Du type de la grandeur de sortie ou caractère de
l'information délivrée ; on parle alors de capteurs logiques
appelés aussi capteurs tout ou rien (TOR), de capteurs analogiques ou
numériques.
I.4.4. Les pré-actionneurs
Les pré-actionneurs reçoivent les informations
du système par l'intermédiaire des interfaces de sorites et
agissent à leurs tour sur les actionneurs, il s'agira par exemple
d'ouvrir une vanne, de commander le déplacement d'un chariot, de
déclencher l'ouverture d'une porte, etc. La plupart de ces actionneurs
seront dotés d'un moteur réalisant la manoeuvre
recherchée.
Le courant délivré par le processeur
n'étant pas suffisant pour actionner directement un moteur, faudra-t-il
donc disposer des contact-relais qui reçoivent une information binaire
(logique ou TOR) via le processeur. Dans d'autres cas l'actionneur peut
requérir différents niveaux de commande.
Comme la logique du processeur ne peut délivrer que
des nombres digitaux, on aura recours à un convertisseur
digital-analogique capable de convertir des nombres binaires (en
général de 8,10 ou 12 bits) en un courant proportionnel au nombre
binaire affiché à entrée.
Un convertisseur courant-tension est alors souvent
nécessaire avant l'interface de puissance. On fait appel pour cela
à un amplificateur opérationnel.
I.4.5. Les actionneurs
Dans une machine ou un système de commande à
distance, semi-automatique ou automatique, un actionneur est l'organe de la
partie opérative qui, recevant un ordre de la partie commande via un
éventuel pré-actionneur, convertit l'énergie qui lui est
fournie en un travail utile à l'exécution des tâches,
éventuellement programmées, d'un système
automatisé. Un actionneur peut être :
V' Un vérin pneumatique ou hydraulique :
L'énergie est fournie par un fluide comprimé par une pompe
(pneumatique ou hydraulique), via un distributeur considéré comme
son pré-actionneur.
V' Un moteur électrique ou une résistance
chauffante sont des actionneurs car ils fonctionnent grâce à une
alimentation électrique, via un relais et/ou un interrupteur.
V' Une électrovanne est un actionneur car elle
régule le débit d'écoulement des fluides en se servant de
l'énergie fournie par l'air comprimé via un distributeur ou un
positionneur selon que l'électrovanne utilisée est de type «
tout ou rien » ou modulante.
26
CHAPITRE II. PRESENTATION DU CADRE D'ETUDE
II.1. PRESENTATION DE L'USINE
L'entreprise Ruashi Mining SPRL est une entreprise
minière exploitant du Cuivre (3,69%) et du Cobalt (0,77%) au Katanga.
Elle est une filiale du groupe Metorex, puissant holding en matière
minière. Metorex est actionneur à 75% et la Gécamines
à 25%.
Elle possède un gisement constitué par trois
écailles dénommées gisement RUASHI 1, 2 et 3 (Figure II.1)
dont chacune de ces écailles constitue un projet exploité
à part, avec possibilité de la réunification des deux
premières déjà en exploitation à ciel ouvert par la
méthode des fasses emboitées. Le 3ème gisement
étant encore en projet.
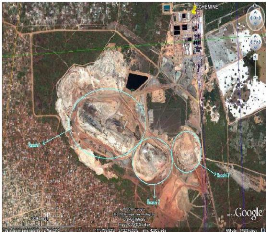
Figure II.1. Vue aérienne des gisements (source :
Google earth) L'usine comprend principalement trois grandes phases
à savoir :
Phase 1 : Concassage et pré lixiviation Phase 2 : Usine
Hydro métallurgique Phase 3: Usine acide (H2SO4)
La mission essentielle de Ruashi Mining consiste, partant des
minerais venant des carrières, et remblai fournir des cathodes de cuivre
de haute teneur (99.9% Cu) et le carbonate de cobalt. Ces opérations se
résument en différentes étapes :
· Concassage et Broyage humide ;
· Pré lixiviation ;
· Lixiviation et Décantation ;
· Séchoir cobalt ;
· Déferrage ;
· Magnésium ;
· Electrolyse ;
27
· Neutralisation.
C'est la section de concassage et broyage humide qui fait
partie de notre cadre d'étude. Cette section consiste à la
réduction du minerai selon la granulométrie voulue et la mise de
ce dernier en pulpe. Le concasseur primaire à mâchoire (Jaw
crusher) est fourni en minerais sulfureux à faible concentration (venant
par voie routière avec utilisation des chargeuses), le minerai est
réduit en dimension, ensuite passe dans le concasseur secondaire qui le
broie en dimension plus réduite. Ce dernier, est convoyé par
l'entremise des bandes transporteuses (figure II.2) jusqu'au broyeur à
boulets semi autogène (figure II.3).
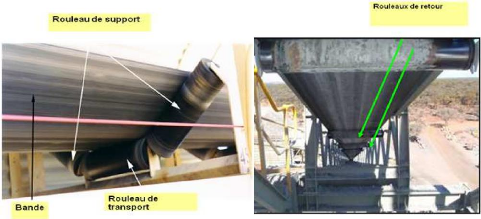
Figure II.2. Bande transporteuse
A l'intérieure du SAG MILL on y ajoute de l'eau pour
former une boue appelée pulpe, ainsi cette pulpe est acheminée
vers les cyclones (Figure II.3) par l'intermédiaire d'une pompe.
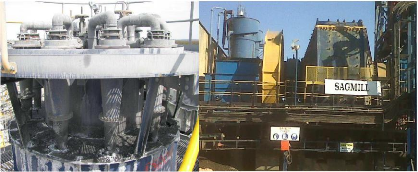
Figure II.3. Vue du Cyclone et du SAG Mill
28
Le traitement par voie humide des minerais est assuré
par le SAG Mill lequel est régit par des principes tant
mécanique, qu'électrique pour son fonctionnement. C'est dans ce
cadre partant de notre sujet d'étude, nous nous intéressons
à son circuit de lubrification lequel nécessite des
améliorations en vue d'en assurer l'optimisation la disponibilité
du broyeur.
II.2. BROYEUR A BOULETS SEMI AUTOGENE : SAG MILL
II.2.1. Présentation du broyeur à boulets
semi autogène
Le broyeur à boulets semi autogène est un
cylindre tournant autour de son axe horizontal et supporté par des
tourillons creux dans lesquels se trouvent mélangés la
matière et les corps broyant (les boulets d'acier). Le minerai est
introduit par une écope fixée au tourillon avant ; il sort par le
tourillon arrière sous forme de pulpe (mélange eau - minerai).
La rotation est assurée par une couronne dentée
circulaire qui est sur l'enveloppe externe du broyeur et qui est
entrainée par un pignon relié au réducteur de vitesse du
moteur (Figure II.3).
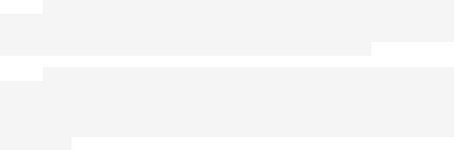
Ce broyeur fait usage d'une charge minimale des boulets de 6
à 15%. Il a un grand diamètre et une longueur courte. Il tourne,
culbute son contenu (mimerai) dans le but de réduire ses dimensions.
L'intérieure est revêtue d'acier dur et résistant et est
équipée des releveurs, qui contribuent à élever la
charge au moment où le broyeur tourne.
Le minerai sec, les boulets d'acier et de l'eau que
contiennent le SAG Mill occupent 30% du volume du broyeur. 8% de ce volume est
constitué des boulets. La goulotte du broyeur lave et écrase sans
cesse le minerai jusqu'à ce qu'il soit suffisamment petit pour passer
à travers les grilles de libération. Le débit
d'alimentation dépend de la puissance accessible et la coquille peut
supporter une charge qui est fonction de la résistance des paliers du
tourillon hydrostatique. Par suite de la rotation du tambour (cylindrique), le
corps broyant roulent, cascadent et retombent en chute libre, fragmentant ainsi
la matière entre eux et contre les parois.
- La lubrification haute pression avec une consigne de pression
de 2MPa - 2,5MPa : L'huile est introduite dans les paliers de bas vers le haut
pour soulever l'axe et vaincre
29
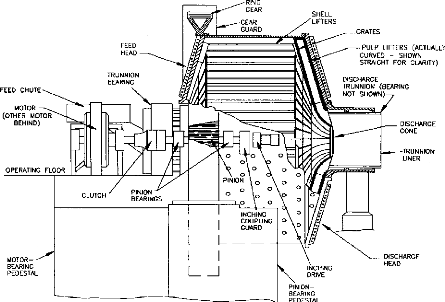
Figure II.4. Parties constitutives du SAG Mill
II.2.2. Circuit de lubrification du SAG Mill
La lubrification du SAG Mill concerne deux points à savoir
:
- Les paliers
- Et le réducteur (Gear box)
Notre étude concerne la lubrification des paliers
à coussinets qui doit être muni d'u système de
refroidissement pour maintenir la température de l'huile constante.
Les tourillons sont supportés par les deux paliers en
amont et en aval (de décharge) du SAG Mill, ces paliers ont pour
rôle de permettre un mouvement libre de l'axe.
Pour réduire les efforts des frottements, l'usure entre
les pièces en contact et en mouvement l'une par rapport à
l'autre, évacuer une partie de l'énergie thermique
engendrée par ces frottements, ainsi qu'éviter la corrosion entre
les pièces en contact qui sont les tourillons et les coussinets, deux
modes de lubrification sont pratiqués au niveau des paliers:
30
l'inertie du SAG Mill avant son démarrage, le tenir
horizontal, enfin d'éviter que la charge de ce dernier ne puisse se
sentir sur les paliers.
- La lubrification basse pression avec une consigne de
pression de 80kPa -150kPa : Qui se fait au niveau des chapeaux pour l'arrosage
complet de telle sorte que le SAG Mill tourne sur un film d'huile.
Les tourillons et les paliers sont des pièces
métalliques en contact et en mouvement ; il y a des
élévations des températures dans les paliers malgré
la lubrification. Ces températures deviennent néfastes au
delà de 40°C, d'où un contrôle minutieux de la
température est prépondérant. C'est ainsi, que dans la
salle de contrôle le seuil de température est fixé à
60°C et cela conformément à la fiche technique de l'huile
ALPHA SP 320 (Tableau A.2.1).
Le SAG Mill est commandé en DCS ou par les API à
distance via la salle de contrôle en mode SCADA et est actionné
par un moteur électrique triphasé dont les
caractéristiques sont reprises dans le tableau 2.1.
Le circuit de lubrification des paliers est constitué de :
- Pompes à engrenage pour la lubrification BP
o 02-LP-PMP-01A
o 02-LP-PMP-02A
- Pompe à pistons radiaux pour la lubrification HP
o 02-HP-PMP-01
o 02-HP-PMP-02
o 02-HP-PMP-03
- 02-HP-FSL-(01, 02,03) : capteur de débit HP
- 02-HP-PSL-(01, 02,03) : capteur de pression HP (ou
manostats)
- 02-LP-FSL-(01,02) : capteur de débit BP
- 02-LP-PSL-(01,02) : capteur de pression BP
- Des manomètres
- Des manodétendeurs
- Un réservoir d'huile d'une capacité de 1600
litres
31
Figure II.5. Composants de la salle de lubrification des
paliers
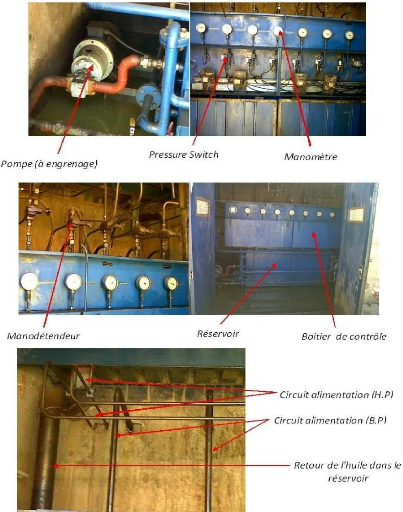
32
Tableau 2.1. Caractéristiques des moteurs des pompes de
lubrification et du SAG Mill
Basse Pression
|
Haute Pression
|
SAG MILL
|
ALSTROM ELECTRICAL
|
ALSTROM ELECTRICAL
|
ALSTROM ELECTRICAL
|
MACHINE
|
MACHINE
|
MACHINE
|
Type : LS 4130-4AB
|
Type: -
|
Type :-
|
Poids : 61 Kg
|
Poids: 68 Kg
|
Poids :-
|
Fréquence : 50Hz
|
Fréquence: 50Hz
|
Fréquence 50 Hz
|
rpm: 1440
|
rpm: 965-970
|
rpm : 386
|
Puissance: 5, 5 KW
|
Puissance: 7, 5 KW
|
Puissance : 1100KW
|
Tension: 525/910
|
Tension: 527
|
Courant :
|
IP 55
|
Courant : 117
|
- Stator : 344A
|
C.O: D/Y
|
Température : 40°C
|
- Rotor : 467A
|
|
Cosö= 0,83
|
Température : 80°C
|
|
IP 55
|
Altitude : 500m
|
|
|
Isolation : classe F
|
|
Source : Ruashi Mining
II.2.3. Commande du broyeur
La commande du broyeur est constituée de deux circuits
à savoir :
II.2.3.1. Circuit de puissance
Dans le circuit de puissance du moteur actionneur du broyeur
à boulets semi autogène nous retrouvons les
éléments suivants :
y' Le discontacteur :
Le discontacteur est un disjoncteur qui est muni des fusibles
à moyenne tension et qui est manipulé manuellement ou
automatiquement, à distance ou localement. Ces fusibles protègent
le moteur contre le défaut de court-circuit et des
surintensités.
En cas de court-circuit, les fusibles fondent et percutent
sur tringle mécanique qui agit sur le disjoncteur, ce dernier ouvre le
circuit d'alimentation du moteur en agissant sur un contact normalement
fermé NF (ou normalement ouvert NO) qui à son tour agit sur un
relais et qui fait déclencher le discontacteur électriquement
à partir de sa bobine d'enclenchement.
y' Le relais de protection moteur :
Le relais de protection du moteur est un relais
électronique, qui est équipé d'un microprocesseur
basé en unité de protection, spécifiquement destiné
pour être employé sur les moteurs dont la charge peut aller
jusqu'à 2000 A. le relais protège le moteur contre :
- Les surcharges
- Les déséquilibres de phases
- Les défauts de terre et de phases
- Les surtensions
33
y' Les appareils des mesures
Ces appareils nous donnent les valeurs de la tension,
l'intensité de chaque phase, la puissance apparente, la puissance
active, la puissance réactive, le facteur de puissance, la
fréquence.
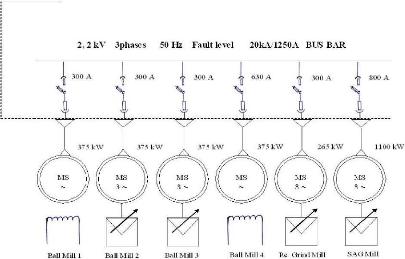
Figure II.6. Schéma de puissance du SAG
Mill
II.2.3.2.Circuit de commande
Le moteur qui entraine la couronne dentée du SAG Mill
démarre conformément aux conditions présentées dans
le tableau 2.2
Ce circuit est constitué de :
- Des manostats et capteur de pression
- Manodétendeurs
- Capteurs de température.
34
Tableau 2.2. Conditions de validation de démarrage du
moteur du SAG Mill
LUBRIFICATION HAUTE PRESSION
|
Discharge end bearing NDE (palier de décharge)
|
Discharge end bearing DE (palier amont)
|
02-HP-PMP-01 active
02-HP-FSL-01 : indique le débit d'huile F> 2l/min
02-HP-PSL-01 : indique la pression d'huile P> 10 bar
02-HP-FSL-02: indique le débit d'huile F> 2l/min
02-HP-PSL-02: indique la pression d'huile P> 10 bar
02-HP-FSL-03: indique le débit d'huile F> 2l/min
02-HP-PSL-03: indique la pression d'huile P> 10 bar
|
02-HP-PMP-03 active
02-HP-FSL-01A: indique le débit d'huile F> 2l/min
02-HP-PSL-01 A01 : indique la pression d'huile P> 10 bar
02-HP-FSL-02A: indique le débit d'huile F> 2l/min
02-HP-PSL-02 A: indique la pression d'huile P> 10 bar 02-HP-FSL-03A: indique
le débit d'huile F> 2l/min 02-HP-PSL-03A: indique la pression d'huile
P> 10 bar
|
02-HP-PMP-02 est en stand by, cette pompe démarre en
cas d'arrêt d'une des pompes de la haute pression.
L'alarme retentit et le moteur du SAG Mill s'arrête
quelques instants après si:
- F < 2l/min
- P < 10bar ou P > 30bar
Le débit nominal de l'huile est de 5l/min
|
LUBRIFICATION BASSE PRESSION
|
LP bearing Lub (lubrification de deux paliers par arrosage)
02-OL-PMP-01A active
02-LP-FSL-01 : indique le débit d'huile F> 35l/min
02-LP-PSL-01 : indique La pression d'huile P < 2,2 bar 02-LP-FSL-02: indique
le débit d'huile F > 35l/min 02-LP-PSL-02: indique La pression
d'huile P < 2,2 bar
|
02-OL-PMP-02A est en stand by, cette pompe démarre en
cas d'arrêt de 02-OL-PMP-01A. L'alarme retentit et le moteur du SAG Mill
s'arrête quelques instants après si:
- F < 35l/min
- P > 2,2 bar (et si l'huile n'est pas by passée du
filtre)
Le débit nominal de l'huile est de 50 l/min
|
CYCLONE
|
03-PMP-01 (ou 03-PMP-02 du cyclone) active
|
RESERVOIR D'HUILE
|
LSL indique le niveau d'huile >20% du volume total TSH
indique la température d'huile < 55°C
|
COURONNE DENTEE
|
Pompe de graissage active
|
|
Source : Ruashi Mining
En dessous du seuil de la pression tarée à la
BP tout comme à la HP, le moteur du SAG Mill ne démarre pas car
étant en interlock avec les contrôleurs ou capteur de pression.
Le démarrage se fait avec une temporisation (temps
d'avertissements) et prend plus ou moins 5 minutes avant de démarrer et
en cas de défaut électrique, une lampe s'allume pour le signaler
sur l'état du système (figure A.2.1, p.72)
35
II.3. IMPACT DES MONTEES DE LA TEMPERATURE D'HUILE SUR
LES PALIERS
Un lubrifiant se qualifie pour une application
déterminée par les propriétés (température,
viscosité, etc.) requises qui sont consignées dans une fiche
technique.
Le mouvement relatif ou de rotation entre deux surfaces est
freiné par une force résistante qui a pour effet de :
- Provoquer l'usure ;
- Consommer de l'énergie ;
- Engendrer des échauffements pouvant conduire à
des soudures entre les surfaces.
La chaleur dégagée est absorbée par le
lubrifiant utilisé d'où ce dernier voit sa température
augmentée dans le cas qui nous concerne au détriment de la
préservation de ses qualités lubrifiantes. Car à Ruashi
Mining ces températures vont au delà de la température de
consigne (Tableau 2.3 - 2.5).
Ainsi, le film d'huile devient de plus en plus mince car
l'augmentation de température rend l'huile très fluide avec une
perte accrue de viscosité (figure I.2, p.5) d'où le coussinet en
bronze voit sa surface s'user au fur et à mesure
En outre, le bronze étant normalement composé
de plus de 60 % de cuivre et d'une proportion variable, non seulement
d'étain, mais aussi d'aluminium, de plomb, de béryllium, de
manganèse et de tungstène, ainsi qu'accessoirement de silicium et
de phosphore, mais pas de zinc en quantité notable. Sa
caractéristique principale est une bonne résistance à
l'usure, une résistance moyenne à la corrosion. On les utilise
souvent comme matériau de frottement en face de l'acier. La corrosion
des pièces en bronze est une entrave à leur usage dans plusieurs
applications dont le fonctionnement du SAG Mill.
Le tableau A.2.1 reprend les caractéristiques de l'huile
ALPHA SP 320 utilisée à Ruashi Mining selon la norme ISO VG, BS
4231 DIN 51517 Part 3.
Sur terrain, les échauffements sont excessifs et
l'huile voit sa température toujours augmenter au fur et à mesure
que le SAG Mill est en service.
Dans la salle de contrôle le seuil de
température est fixé à 60°C selon la fiche technique
alors que dans son fonctionnement, le seuil est souvent dépassée
et cela surtout en période chaude tel que montré sur la figure
II.9 (p.44)
En outre, les montées de température ont un
impact sur la production, car lorsque celles ci deviennent excessives il y a
arrêt urgente du SAG Mill et cela pendant un temps qui est
déterminée par la diminution notable de la température de
l'huile dans le réservoir. Et cela cause un manque à gagner pour
l'entreprise puisqu'évoluant dans un système capitaliste
où le temps occupe une position privilégié dans la
rentabilité. L'alimentation du minerai brute à la section broyage
humide (SAG Mill) étant de 250 - 300 tonnes par heure.
36
Tableau 2.3. Température de l'huile au niveau des paliers
du 28/08/2008 au 30/10/2008
Date
|
01-TIT-15
|
01-TIT-16
|
28/08/2008
|
56,2
|
61,3
|
30/08/2008
|
57,1
|
64,3
|
01/09/2008
|
59,2
|
64,4
|
02/09/2008
|
47,7
|
51,1
|
03/09/2008
|
58,8
|
63,6
|
04/09/2008
|
58,3
|
63,4
|
05/09/2008
|
49,7
|
53,5
|
06/09/2008
|
55,9
|
61
|
08/09/2008
|
59,5
|
64,1
|
09/09/2008
|
60,4
|
65,8
|
10/09/2008
|
60,9
|
66,9
|
11/09/2008
|
59,2
|
64
|
12/09/2008
|
58,7
|
64,1
|
13/09/2008
|
53,2
|
57,5
|
15/09/2008
|
60,9
|
65,4
|
16/09/2008
|
61,3
|
66,7
|
17/09/2008
|
62,7
|
67,2
|
18/09/2008
|
63,9
|
68,6
|
19/09/2008
|
63,7
|
68,6
|
20/09/2008
|
65,3
|
70,6
|
22/09/2008
|
65,3
|
70,8
|
23/09/2008
|
66,9
|
66,9
|
24/09/2008
|
56,2
|
60,3
|
25/09/2008
|
69,3
|
74,6
|
26/09/2008
|
63,9
|
69,3
|
27/09/2008
|
63,3
|
68,4
|
29/09/2008
|
48,3
|
51,5
|
01/10/2008
|
72,2
|
77,4
|
|
Source : Ruashi Mining
02/10/2008
|
56
|
60
|
03/10/2008
|
64,4
|
69,5
|
04/10/2008
|
57,8
|
62,3
|
06/10/2008
|
57,6
|
61,1
|
07/10/2008
|
57,8
|
62,3
|
08/10/2008
|
60,1
|
65,2
|
09/10/2008
|
62,4
|
66,9
|
10/10/2008
|
47,6
|
51,3
|
14/10/2008
|
55,4
|
59,7
|
15/10/2008
|
58,2
|
63,1
|
16/10/2008
|
58
|
58,4
|
17/10/2008
|
61,7
|
66,6
|
18/10/2008
|
61,8
|
66,6
|
20/10/2008
|
59,9
|
64,7
|
21/10/2008
|
59,4
|
64,3
|
22/10/2008
|
58,1
|
63
|
23/10/2008
|
57,1
|
61,9
|
24/10/2008
|
55,9
|
60,1
|
25/10/2008
|
51,2
|
55,3
|
27/10/2008
|
58,6
|
67,8
|
28/10/2008
|
58,9
|
63,8
|
29/10/2008
|
64,7
|
69,9
|
30/10/2008
|
63,3
|
68,3
|
Moyenne (°C)
|
59,2921569
|
63,98
|
Max (°C)
|
72,2
|
77,4
|
Min (°C)
|
47,6
|
47,8
|
Intervalle
|
28/08/2008 - 30/10/2008
|
Heure
|
9 heures
|
|
Ce tableau présente l'évolution des
températures de l'huile lubrifiante au niveau des deux paliers avec une
moyenne de température respective de 59,3 et 63,98°C. Les
températures deviennent de plus en plus élevées à
partir du mois de Septembre avec une température maximale qui peut
atteindre respectivement une valeur pour les deux paliers de 72,2° et
77,4°C.
37
Tableau 2.4. Température de l'huile au niveau des paliers
du 01/06/2009 au 31/08/2009
Date
|
01-TIT-15
|
01-TIT-16
|
01/06/2009
|
48,2
|
52,7
|
02/06/2009
|
51,9
|
56,8
|
03/06/2009
|
39,8
|
43,8
|
05/06/2009
|
45,8
|
50,2
|
08/06/2009
|
57,8
|
58,8
|
09/06/2009
|
56,3
|
62,4
|
10/06/2009
|
45,1
|
49,2
|
12/06/2009
|
56,1
|
61,1
|
16/06/2009
|
54,1
|
59,3
|
17/06/2009
|
48,7
|
53,2
|
18/06/2009
|
56,2
|
61,6
|
19/06/2009
|
55
|
60
|
22/06/2009
|
47,3
|
51,7
|
23/06/2009
|
60,8
|
66,4
|
24/06/2009
|
64
|
69,4
|
25/06/2009
|
55,5
|
60,7
|
27/06/2009
|
49,7
|
54,5
|
29/06/2009
|
51,7
|
56,8
|
08/07/2009
|
53,7
|
58,6
|
10/07/2009
|
51,3
|
56,4
|
11/07/2009
|
53,7
|
58,7
|
13/07/2009
|
55,5
|
60,4
|
15/07/2009
|
59,4
|
64,7
|
16/07/2009
|
59
|
63,6
|
17/07/2009
|
56,1
|
61,7
|
18/07/2009
|
52,6
|
57,1
|
20/07/2009
|
52,6
|
56,9
|
|
Source : Ruashi Mining
21/07/2009
|
53,9
|
59,3
|
25/07/2009
|
55,6
|
60,8
|
27/07/2009
|
57,1
|
61,9
|
28/07/2009
|
51,3
|
56,2
|
03/08/2009
|
60
|
65,2
|
04/08/2009
|
59,1
|
64,8
|
10/08/2009
|
55,1
|
60,5
|
12/08/2009
|
65,2
|
70,6
|
13/08/2009
|
59,6
|
65,1
|
14/08/2009
|
53,1
|
58,3
|
15/08/2009
|
56,8
|
62,1
|
17/08/2009
|
55,9
|
61,9
|
18/08/2009
|
56,1
|
61,8
|
19/08/2009
|
53,4
|
58,3
|
20/08/2009
|
55,6
|
61,1
|
21/08/2009
|
57,1
|
62,3
|
22/08/2009
|
58,2
|
63,4
|
24/08/2009
|
56,5
|
61,8
|
25/08/2009
|
52,7
|
58
|
26/08/2009
|
54
|
59,1
|
28/08/2009
|
58,1
|
63
|
29/08/2009
|
56,1
|
61,4
|
31/08/2009
|
54,5
|
59,9
|
Moyenne (°C)
|
54,658
|
59,67
|
Max (°C)
|
65,2
|
70,6
|
Min (°C)
|
39,8
|
43,8
|
Intervalle
|
01/06/2009- 31/08/2009
|
Heure
|
9 heures
|
|
Il ressort de ce tableau la température de l'huile
lubrifiante au niveau des paliers du mois de juin jusqu'au mois d'août
avec une moyenne pour les deux paliers de 54,7 et 59,7°C. Les
températures évoluent toujours dans cette moyenne et peuvent
à limite atteindre des valeurs au dessus de 60°C, c'est le cas du
mois d'août.
38
Tableau 2.5. Température de l'huile au niveau des paliers
du 01/09/2009 au 08/12/2009
Date
|
01-TIT-15
|
01-TIT-16
|
01/09/2009
|
55,5
|
58,7
|
02/09/2009
|
54,1
|
59,3
|
04/09/2009
|
57,4
|
62,7
|
05/09/2009
|
55,8
|
60,7
|
07/09/2009
|
54,5
|
59,4
|
08/09/2009
|
59,7
|
65
|
09/09/2009
|
62,8
|
67,9
|
10/09/2009
|
62,1
|
67,4
|
11/09/2009
|
59,5
|
64,5
|
12/09/2009
|
63,3
|
68,6
|
14/09/2009
|
63,9
|
69,7
|
15/09/2009
|
61,3
|
66,8
|
16/09/2009
|
62,6
|
67,4
|
17/09/2009
|
63,2
|
67,1
|
19/09/2009
|
60,8
|
66,4
|
21/09/2009
|
62,6
|
67,7
|
22/09/2009
|
64,9
|
69,9
|
24/09/2009
|
62,6
|
68,4
|
25/09/2009
|
63,8
|
69,5
|
26/09/2009
|
59,7
|
64,1
|
02/10/2009
|
59,8
|
65,2
|
05/10/2009
|
61,8
|
67
|
06/10/2009
|
62,7
|
68,1
|
07/10/2009
|
66,6
|
71,9
|
08/10/2009
|
64
|
69,1
|
09/10/2009
|
60,8
|
66
|
10/10/2009
|
61,7
|
66,8
|
12/10/2009
|
62,5
|
67,7
|
|
Source : Ruashi Mining
19/10/2009
|
65,3
|
70,5
|
20/10/2009
|
58,9
|
63,9
|
21/10/2009
|
55,1
|
59,5
|
22/10/2009
|
65,6
|
71,1
|
23/10/2009
|
61,5
|
66,7
|
24/10/2009
|
60,1
|
65
|
26/10/2009
|
63,6
|
68,9
|
27/10/2009
|
68,6
|
74
|
28/10/2009
|
62
|
67,1
|
29/10/2009
|
68,6
|
74
|
30/10/2009
|
66,3
|
68,3
|
02/11/2009
|
60,6
|
65,6
|
03/11/2009
|
65,3
|
66
|
05/11/2009
|
54,5
|
59,5
|
06/11/2009
|
64,4
|
70,1
|
07/11/2009
|
58,4
|
63,5
|
08/11/2009
|
45,8
|
49,6
|
01/12/2009
|
59,7
|
65,3
|
02/12/2009
|
59,3
|
64,6
|
03/12/2009
|
60
|
65,2
|
04/12/2009
|
60,8
|
66
|
05/12/2009
|
62,3
|
67,4
|
07/12/2009
|
60,4
|
65,4
|
08/12/2009
|
84,8
|
91,1
|
Moyenne (°C)
|
61,575
|
66,5634615
|
Max (°C)
|
84,8
|
91,1
|
Min (°C)
|
45,8
|
49,6
|
Intervalle
|
01/09/2009 - 08/12/2009
|
Heure
|
9 heures
|
|
Ce tableau présente la variation des
températures de l'huile avec un accroissement au fur et à mesure
qu'on évolue en mois pour les deux paliers. La moyenne étant
respectivement de 61,6°C et 66,6°C, pour des valeurs maximales qui
peuvent atteindre 90°C surtout pour les mois les plus chauds.
Source : Ruashi Mining
39
Tableau 2.6.Température de l'huile dans le
réservoir de Février - Avril
Evolution de la température de l'huile dans le
réservoir
|
FEVRIER 2012
|
|
01/02/2012
|
02/02/2012
|
03/02/2012
|
06/02/2012
|
07/02/2012
|
08/02/2012
|
09/02/2012
|
10/02/2012
|
13/02/2012
|
14/02/2012
|
15/02/2012
|
16/02/2012
|
17/02/2012
|
18/02/2012
|
19/02/2012
|
20/02/2012
|
21/02/2012
|
22/02/2012
|
23/02/2012
|
24/02/2012
|
27/02/2012
|
28/02/2012
|
29/02/2012
|
Moyenne (°C)
|
Avant midi
|
62
|
63
|
65
|
63
|
64
|
68
|
66
|
69
|
62
|
63
|
64
|
66
|
67
|
68
|
60
|
65
|
63
|
65
|
68
|
69
|
62
|
68
|
67
|
65
|
Après midi
|
65
|
70
|
72
|
71
|
72
|
79
|
73
|
74
|
70
|
68
|
69
|
73
|
76
|
69
|
71
|
65
|
68
|
69
|
75
|
76
|
79
|
78
|
77
|
72
|
Moyenne (°C)
|
63,5
|
67
|
68,5
|
67
|
68
|
73,5
|
69,5
|
71,5
|
66
|
66
|
67
|
69,5
|
71,5
|
68,5
|
65
|
65
|
66
|
67
|
71,5
|
72,5
|
71
|
73
|
72
|
69
|
MARS 2012
|
|
01/03/2012
|
02/03/2012
|
05/03/2012
|
06/03/2012
|
07/03/2012
|
08/03/2012
|
09/03/2012
|
12/03/2012
|
13/03/2012
|
14/03/2012
|
15/03/2012
|
16/03/2012
|
19/03/2012
|
20/03/2012
|
21/03/2012
|
22/03/2012
|
23/03/2012
|
26/03/2012
|
27/03/2012
|
28/03/2012
|
29/03/2012
|
30/03/2012
|
31/03/2012
|
Moyenne (°C)
|
Avant midi
|
66
|
64
|
65
|
63
|
61
|
67
|
66
|
64
|
66
|
63
|
64
|
66
|
59
|
61
|
69
|
60
|
63
|
69
|
76
|
69
|
68
|
63
|
71
|
65
|
Après midi
|
69
|
70
|
72
|
71
|
62
|
73
|
70
|
73
|
71
|
68
|
69
|
72
|
63
|
64
|
71
|
64
|
68
|
75
|
80
|
76
|
76
|
78
|
79
|
71
|
Moyenne (°C)
|
67,5
|
67
|
68,5
|
67
|
61,5
|
70
|
68
|
68,5
|
69
|
66
|
67
|
69
|
61
|
62,5
|
70
|
62
|
66
|
72
|
78
|
72,5
|
72
|
71
|
75
|
68
|
AVRIL 2012
|
|
02/04/2012
|
03/04/2012
|
04/04/2012
|
05/04/2012
|
06/04/2012
|
09/04/2012
|
10/04/2012
|
11/04/2012
|
12/04/2012
|
13/04/2012
|
16/04/2012
|
17/04/2012
|
18/04/2012
|
19/04/2012
|
20/04/2012
|
23/04/2012
|
24/04/2012
|
25/04/2012
|
26/04/2012
|
27/04/2012
|
28/04/2012
|
29/04/2012
|
30/04/2012
|
Moyenne (°C)
|
Avant midi
|
70
|
67
|
69
|
68
|
64
|
62
|
66
|
62
|
62
|
65
|
64
|
66
|
57
|
58
|
60
|
60
|
63
|
65
|
68
|
69
|
62
|
67
|
69
|
64
|
Après midi
|
71
|
70
|
72
|
71
|
62
|
63
|
67
|
62
|
63
|
68
|
69
|
70
|
60
|
63
|
61
|
64
|
64
|
66
|
75
|
70
|
67
|
72
|
77
|
67
|
Moyenne (°C)
|
70,5
|
69
|
70,5
|
70
|
63
|
62,5
|
66,5
|
62
|
62
|
67
|
67
|
68
|
58,5
|
60,5
|
60
|
62
|
64
|
66
|
71,5
|
69,5
|
65
|
70
|
73
|
66
|
|
40
Il ressort du tableau 2.6, l'évolution de
température de l'huile dans le réservoir où la moyenne
varie autour de 68°C alors que le maximum peut atteindre des valeurs de
80°C.
Les avant midi accusent des températures moins
élevées par rapport à celles des après midi compte
tenu de la fraicheur matinale car ces températures sont
prélevées aux alentours de 7 heures, cependant elles restent
sujet de traitement car allant au delà de la température de
fonctionnement.
Tableau 2.7. Données climatologiques de la ville de
Lubumbashi
Mois
|
Moyennes maxi (°)
|
Moyennes mini (°)
|
Précipitations (mm)
|
Janvier
|
27
|
16
|
1220
|
Février
|
27
|
16
|
240
|
Mars
|
27
|
16
|
260
|
Avril
|
27
|
13
|
200
|
Mai
|
27
|
10
|
50
|
Juin
|
26
|
6
|
0
|
Juillet
|
26
|
6
|
0
|
Aout
|
28
|
7
|
0
|
Septembre
|
31
|
11
|
0
|
Octobre
|
32
|
14
|
0
|
Novembre
|
30
|
16
|
20
|
Décembre
|
27
|
16
|
160
|
Moyenne annuelle
|
28
|
12
|
250
|
|
Source: (c) 2001-2012, The Weather Channel, LLC
weather.com® Licence TRUSTe
41
II.4. DISCUSSION ET INTERPRETATION DES DONNEES
II.4.1. Températures de l'huile au niveau des
paliers
L'évolution de température de l'huile au niveau
des paliers évolue dans la plage de 40° à 90°C cela due
aux frottements générées par les pièces en
mouvement séparées par le film d'huile.
Il se crée une différence moyenne de
température de l'huile au niveau du palier amont (01-TIT-15 : Feed End
bearing NDE) et le palier de décharge (01-TIT-16 : Discharge End bearing
DE) d'environ 4°C due au fait que le palier 01-TIT-16 à part la
charge contenue dans le SAG Mill qu'il supporte, il supporte en plus la
couronne (roue dentée) d'entrainement du broyeur. Puisque les
montées de températures dans un palier dépendent aussi de
la charge lui appliquée.
L'évolution de température de l'huile ALPHA SP
320 telle que montrée sur les tableaux 2.4- 2.6 dépasse dans
plusieurs cas la consigne. Ainsi, constatons-nous que selon les données
climatologiques de la ville de Lubumbashi (Tableau 2.7) que les mois les plus
chaudes c'est-à-dire Septembre, Octobre, Novembre se prêtent
favorable aux montées des températures tandis que les mois les
moins chaudes gardent une température moyenne de 26°C.
Il ressort de ce constat que la température de
l'environnement dans lequel l'équipement est placé a un impact
non négligeable quant à ce qui concerne la variation de la
température de l'huile de lubrification des paliers du SAG Mill d'autant
plus que ces paliers sont à l'air libre.
Les figures II.7, II.8, II.9 illustre les variations des
températures de l'huile selon qu'il s'agit des mois chaud ou moins
chaud.
42
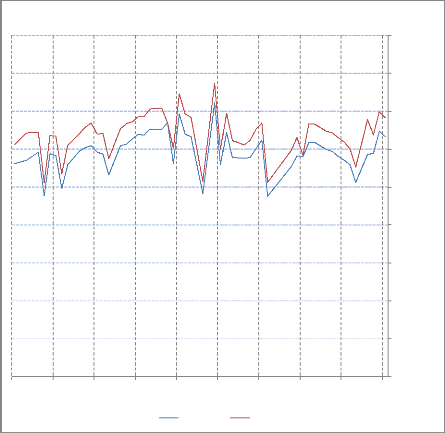
28/8 4/9 11/9 18/9 25/9 2/10 9/10 16/10 23/10 30/10
TEMPÉRATURE DE L'HUILE: DU 28/08/2008 AU 30/10/2008
01-TIT-15 01-TIT-16
t °C
40
90
80
0
70
60
50
30
20
10
Figure II.7. Température de l'huile du 28/08/2008 au
30/10/2008
43
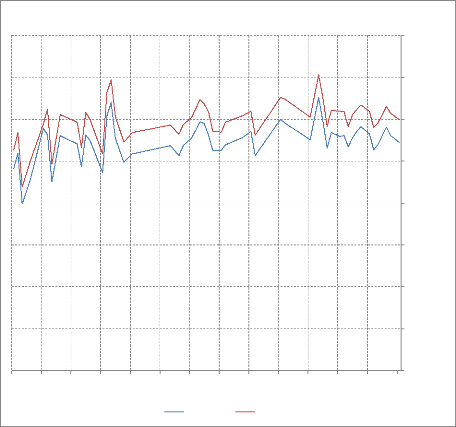
1/6 8/6 15/6 22/6 29/6 6/7 13/7 20/7 27/7 3/8 10/8 17/8 24/8
31/8
TEMPÉRATURE DE L'HUILE: DU 01/06/2009 AU 31/08/2009
t°C
01-TIT-15 01-TIT-16
40
80
0
70
60
50
30
20
10
Figure II.8. Température de l'huile du 01/06/2009 au
01/12/2009
44
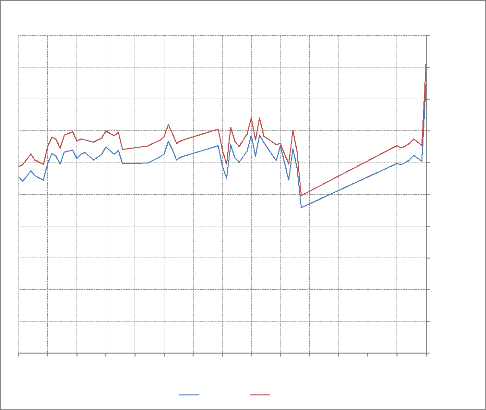
1/9 8/9 15/9 22/9 29/9 6/10 13/10 20/10 27/10 3/11 10/11 17/11
24/11 1/12 8/12
TEMPÉRATURE DE L'HUILE: DU 01/09/2009 AU 08/12/2009
01-TIT-15 01-TIT-16
t°C
40
90
80
0
70
60
50
30
20
100
10
Figure II.9. Température de l'huile du 01/09/2009
au 08/12/2009
45
II.4.2. Température de l'huile dans le
réservoir
La température de l'huile dans le réservoir
varie dans la plage de 60° à 80°C ; il s'agit presque de la
même température issue des conduites de retour de l'huile de
lubrification avec une légère augmentation compte tenu des pertes
de charge dans le circuit. Cette huile voit sa température toujours
croitre puisqu'elle n'est pas soumise à un refroidissement afin de la
garder toujours dans la plage de température de fonctionnement. C'est
ainsi que les pompes aspirent une huile chaude avec toutes les
conséquences qui peuvent en découler entre autre :
- Réduction du film d'huile, d'où les paliers
s'usent puisqu'il y a contact de l'arbre en mouvement et du coussinet (figure
I.4, p.7);
- L'huile devient très fluide ce qui entraine des
fuites au niveau des joints de raccordement et la lubrification devient
difficile. La figure II.10 montre les fuites d'huile dans la salle de
lubrification.
- Les composants internes des pompes se voient aussi
affectés.
Et par conséquent, cette huile est souvent
remplacée avant qu'elle n'atteigne sa durée de vie optimale.
Les figures II.11 ; II.12 ; II.13 montrent les
évolutions des températures de l'huile dans le réservoir
pendant le mois de février jusqu'au mois d'avril avec une
différence de température selon qu'on est dans les avants ou
après midi.
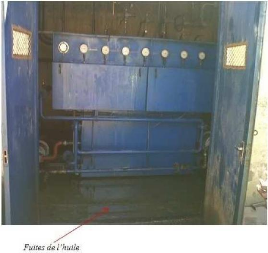
Figure II.10. Fuite de l'huile au niveau des
joints
46
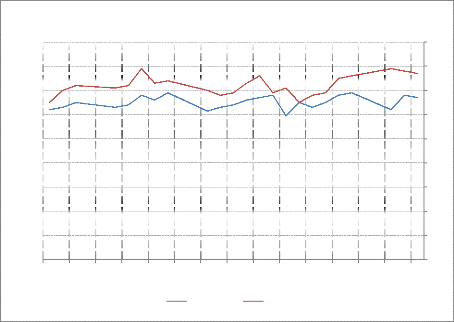
1/2 3/2 5/2 7/2 9/2 11/2 13/2 15/2 17/2 19/2 21/2 23/2 25/2 27/2
29/2
TEMPÉRATURE DE L'HUILE DANS LE RÉSERVOIR:
FÉVRIER 2012
Avant midi Après midi
t oC
40
0
90
80
70
60
50
30
20
10
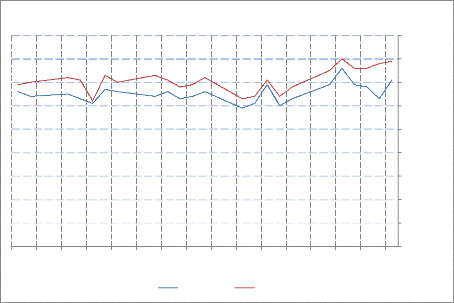
1/3 3/3 5/3 7/3 9/3 11/3 13/3 15/3 17/3 19/3 21/3 23/3 25/3 27/3
29/3 31/3
TEMPÉRATURE DE L'HUILE DANS LE RÉSERVOIR:
MARS 2012
Avant midi Après midi
toC
40
90
80
0
70
60
50
30
20
10
Figure II.12. Température de l'huile dans le
réservoir : Mars 2012
Figure II.11. Température de l'huile dans le
réservoir : Février 2012
47
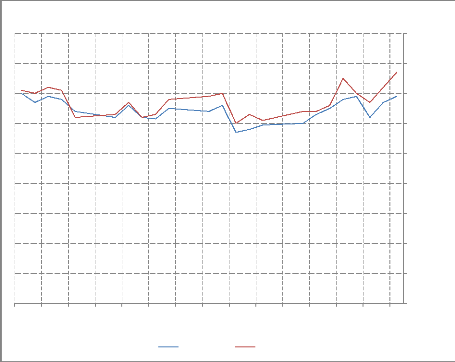
2/4 4/4 6/4 8/4 10/4 12/4 14/4 16/4 18/4 20/4 22/4 24/4 26/4
28/4 30/4
TEMPÉRATURE DE L'HUILE DANS LE
RÉSERVOIR:AVRIL 2012
Avant midi Après midi
40
90
80
0
toC
70
60
50
30
20
10
Le chapitre qui va suivre va nous permettre de dimensionner
l'échangeur sur base des données de température
présentées dans les tableaux 2.4 - 2.6.
Figure II.13. Température de l'huile dans le
réservoir : Avril 2012
En considération de ce qui précède, nous
constatons que la lubrification occupe une place de choix dans le
fonctionnement du SAG Mill, car cette dernière dispense les paliers de
toute forme d'usure due aux frottements et aux échauffements excessifs
pouvant conduire à des soudures entre les surfaces.
Cependant, pour que cette lubrification assure toutes les
fonctions requises, elle doit être soumise à un bon
refroidissement ; élément non négligeable dans le circuit
de lubrification des paliers.
En outre, le système que nous venons de
présenter souffre d'un système de refroidissement. D'où la
nécessité de mettre sur pieds un échangeur dont le but
sera de transférer le flux de chaleur de l'huile vers un autre fluide
(eau) afin de préserver la qualité de l'huile ainsi que les
paliers
Source : Ruashi Mining
48
CHAPITRE III. DIMENSIONNEMENT DU SYSTEME
DE
REFROIDISSEMENT
Dans les sociétés industrielles,
l'échangeur de chaleur est un élément essentiel dans la
chaine de production en matière de maîtrise de l'énergie.
Une grande part de l'énergie thermique utilisée dans les
procédés industriels transite au moins une fois par un
échangeur de chaleur, aussi bien dans les procédés
eux-mêmes que dans les systèmes de récupération de
l'énergie thermique de ces procédés. On les utilise
principalement dans les secteurs de l'industrie, du transport, mais aussi dans
le système de refroidissement.
Le choix d'un échangeur de chaleur, pour une
application donnée, dépend de nombreux paramètres :
domaine de température et de pression des fluides,
propriétés physiques et agressivité de ces fluides,
maintenance et encombrement.
III.1. PRESENTATION DU SYSTEME DE REFROIDISSEMENT
Il s'agit d'un échangeur à tubes et calandre
qui va assurer le refroidissement de l'huile ALPHA SP 320.
Deux pompes fonctionnant en redondance 02-PMP-OL-01 et
02-PMP-OL-02 sont placées en aval du réservoir afin d'amener
l'huile vers l'échangeur tel que montré sur la figure
III.1(p.49), il s'agit des pompes de recirculation et c'est dans ce circuit que
les pompes 02-HP-PMP-01 & 02-HP-PMP-03 de la haute pression aspirent de
l'huile.
La pompe 02-HP-PMP-02 est en stand-by au cas où une de
pompe de la haute pression ne serait pas en service dû à une
quelconque perturbation du circuit.
Le système de lubrification ainsi que celui de
refroidissement sont munis des capteurs électroniques qui assurent le
contrôle des paramètres d'entrée et de sortie. La commande
se faisant avec l'API Siemens SIMATIC S7-300.
Tableau 3.1. Composants électroniques du circuit de
lubrification et de refroidissement
Capteurs
|
Type
|
Grandeur mesurée
|
01-TIT-01
|
Température
|
Te1
|
01-TIT-02
|
Température
|
T.1
|
01-TIT-03
|
Température
|
Te2
|
01-TI-01
|
Température
|
T.2
|
01-FSL-01
|
Débit
|
m2
|
02-LP-FSL-03
|
Débit
|
m1
|
01-PSL-01
|
Pression
|
P2
|
02-HP-PSL-03
|
Pression
|
P1
|
02 - LP- FSL- 03 est incorporé dans la commande du SAG
Mill et ce dernier démarre si la pression P1 (BP) lue par PSL respecte
la consigne (cfr. Tableau 2.2, p.34)
01-TI-01 : nous donne une lecture simple de la
température de l'eau et n'intervient pas l'interlock (ou verrouillage)
du système de refroidissement.
01- PMP-01 & 01- PMP-02 : Pompes à pression d'eau,
qui fonctionnent en redondance.
|
|
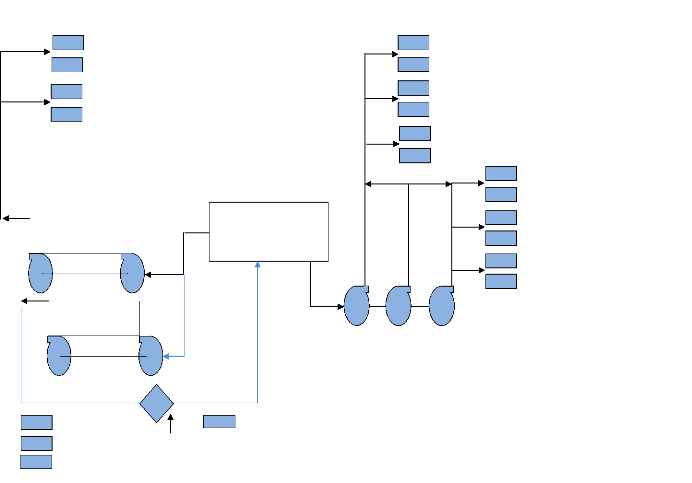
OFF- LINE CONDITIONING
Figure III.1. Système de lubrification muni de
l'échangeur
02-LP- PDSH-
01-TIT-02
FEED END BEARING - NDE
02-LP-FSL-01 02-LP-PSL-01
02-LP-FSL-02 02-LP-PSL-02
02-HP-FSL-01A 02-HP-PSL-01A 02-HP-FSL-02A 02-HP-PSL-02A
02-HP-FSL-03A 02-HP-PSL-03A
02-LP-FSL-03
02-HP-PSL-03
Water
01-TIT-01
02 -LP-PMP- 01A
02 -LP-PMP- 02A
02 - OL-PMP- 01
02 - OL-PMP- 02
RESERVOIR
D'HUILE
02-HP-FSL-01A 02-HP-PSL-01A 02-HP-FSL-02A 02-HP-PSL-02A
02-HP-FSL-03A 02-HP-PSL-03A
DISCHARGE END BEARING - DE
LP BEARING LUB
02-HP-PMP-01
02-HP-PMP-02 STD-BY 02-HP-PMP-03
HP JACKING SYSTEM
49
50
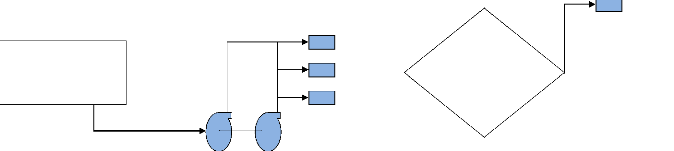
01-TI- 01
01-PSL-01
01-FSL-01 01-TIT-03
RESERVOIR D'EAU
ECHANGEUR
01-PMP-01
01-PMP-02 STD - BY
|
REFROIDISSEMENT PAR EAU
|
|
Figure III.2. Configuration du système de
refroidissement
51
III.2. CALCUL DE L'ECHANGEUR
- Type d'appareil : A tubes et calandre
- Configuration de l'écoulement : contre - courant
avec Ts1 < Ts2 (cfr § I.3.2)
- Méthode de calcul : DTML
- Type d'huile : APLHA SP 320 (Tableau A.2.1)
- Norme : ISO VG, BS 4231 DIN 51517 PART 3
- Les caractéristiques de l'eau sont reprises dans le
Tableau A.3.2
- Type de pompe à huile : à engrenage (Tableau
2.1) avec un débit nominal de 120l/min
- Caractéristiques de l'échangeur :
o Nombre de tubes N = 55
o Nombre de passe : 1
o Nombre de tubes par passe (s)= Nt =
|
Nombre de tubes nombre de passe
|
=
|
55
9
|
= 55
|
|
o Tube BWG 10 (voir Tableau A.4.1)
o Diamètre calandre [mm] D = 500
o Espace entre 2 chicanes [mm] b = 30
o Epaisseur chicane [mm] e = 5
o Pas [mm] p = 32 (ou 5/4 po cfr. § I.3.5)
o Paroi des tubes en Cuivre avec ë~ = ëcu =
401 kcal/ m K (Tableau A.3.3)
La hauteur laissée libre à chaque chicane est de 25
% du diamètre intérieur de la calandre.
- Les dimensions géométriques de l'échangeur
et les propriétés thermo physiques des
fluides sont donnée dans le Tableau 3.2:
- Tei = 85°C Selon les données de
température traitées au chapitre précédent. Il
s'agit de se placer dans les conditions les moins favorables.
- Ts1 cette température peut être
fixée dans la plage de fonctionnement, c'est une température qui
pourra varier entre 38°C et 50°C en vue de garantir un fonctionnement
optimum du SAG Mill. Ainsi, pour le cas d'espèce cette valeur peut
être fixée à 38°C.
- Te2 cette température varie entre 20 -
22°C : Te2 = 22°C
- Ts2 est la moyenne logarithmique de la
température d'entrée de l'huile et de l'eau
Ts2 =
|
Tei - Te2
|
85 - 22
=
|
= 46,6°C
|
|
ln Tei Te2
|
|
85 ln 22
|
52
- La température moyenne logarithmique de
l'échangeur sera donné par :
ATML = ln T.1 - Te2
Tei - T.2
(T.1 - Te2) - (Tei - T.2)
16
ln 35,07
16 - 35,07
=
= 25,6°C
- La section intérieure des tubes est donnée par :
A2 = ðxX X
Í = 4,9 X 10aÍ m2
- La section de passage de l'huile entre les chicanes s'obtient
par la relation ci-dessous :
A1 = (p - d1)(b - e) = (32 - 28,58) X (30 - 5) X 10-6
= 8,55 X 10a5m2
- Le diamètre intérieur équivalent de la
calandre vaut :
D2-NtdW X
De = = 0,130463196 m
ÛáxW
53
Tableau 3.2. Dimensions échangeur et
propriétés thermo physiques des fluides
CARACTERISTIQUES DE L'ECHANGEUR
|
ECHANGEUR
|
|
Valeur
|
|
Mm
|
m
|
Diamètre extérieur du tube
|
|
28,58
|
0,02858
|
Diamètre intérieur du tube
|
|
25,177
|
0,025177
|
Diamètre Calandre
|
|
500
|
0,5
|
Espace entre 2 Chicanes
|
|
30
|
0,03
|
Epaisseur de la chicane
|
|
5
|
0,005
|
Pas
|
|
32
|
0,032
|
Nombre de passes
|
|
1
|
Nombre des tubes
|
|
55
|
Nombre des tubes par passe (s)
|
|
55
|
diamètre équivalent
|
|
0,130463196
|
m
|
Section intérieure
|
|
0,000497597
|
m2
|
Section de passage entre chicanes
|
|
8,55×10-05
|
m2
|
Section extérieure
|
|
0,130463196
|
m2
|
FLUIDES
|
|
Propriétés thermo physiques
|
Huile
|
|
Eau
|
Unité
|
Masse volumique
|
|
895
|
1000
|
kg/m3
|
Chaleur massique
|
|
2100
|
4185,5
|
J/kg.K
|
Conductivité thermique
|
|
0,14
|
0,6
|
W/m.K
|
Viscosité dynamique
|
|
0,2864
|
0,001002
|
Pa.s
|
Viscosité cinématique
|
|
320
|
1,002E-12
|
Cst
|
Température entrée
|
|
85
|
22
|
°C
|
Température sortie
|
|
38
|
46,6111199
|
°C
|
ÄT sortie Huile et entrée eau
|
|
16
|
°C
|
ÄT entrée Huile et sortie eau
|
|
38,38888009
|
°C
|
ÄTML
|
|
25,58205483
|
°C
|
Conductivité paroi
|
|
401
|
W/m.K
|
Source : calcul précedent
54
- RESULTATS DES CALCULS
Le logiciel Matlab 7.0 nous permet de calculer
l'échangeur au regard des relations présentées au chapitre
premier. Le code de programmation est donné en annexe. Les
résultats sont présentés dans le tableau 3.3.
Le flux de chaleur échangée est calculé par
la relation de la figure I.16 :
Ö= m9~ cp9(T,9 - T.9"
D'où Ö = 197, 4 kW ou 47, 16 kcal/s
Ö
Et le débit massique se calcul à partir de (I.7) :
m% =
ߨX(ceXacdX"
9âÕÍÉÉ
~
= 1,9 l/s
Í9ãÏ,Ï(ÍÌ,âa%%"
VW ceXacdX ÍÌ,âa%%
Le rapport de débit est donné par r ~ VX~ ~ ~ ~
0,52
cdWaceW ãÏalã
Calcul du coefficient d'échange h de deux
fluides
La relation (I.6) nous permet de tirer la valeur de la vitesse de
l'eau dans le tube connaissant la section intérieure du tube A% (Tableau
3.2):
V% =
|
m%
|
1,9
|
= 0,407 m/s
|
=
ñ%NÚA%
|
|
1000 Ö 55 Ö 4,9 Ö 10aÍ
|
Le calcul du nombre de Reynolds pour l'eau donne :
R,% =
u%
1000 Ö 0,69 Ö 0,025
~
0,001002
ñ%V%d%
= 10239,43
V9 =
|
m9
ñ9NßA9
|
m9~ p
~ ñ9DA9
|
2 Ö 0,032
|
= 1,67 m/s
|
895 Ö 0,5 Ö 8,5 Ö 10aÏ
|
Avec D le diamètre calandre en [m] (Tableau 3.2)
En utilisant la corrélation de Colburn qui est une
relation semi empirique on a:
h% =
ë%
0,023Re% É,ãPr% 9/l ~ 1692,71
W/m%. K
d%
uc% 0,001002 Ö 4185,5
Pr% ~ ~ ~ 6,98
ë% 0,6
Connaissant la section de passage A9 de l'huile entre les
chicanes la relation (I.6) nous permet de trouver également la vitesse
de l'huile par :
55
Le nombre de Reynolds de l'huile est :
Re1 =
|
ñ1V1D
u1
|
895 X 1,67 X 0,5
=
0,2864
|
= 2613,61
|
h1 =
|
ë1Nu1
|
0,14 X 574,82
=
0,028
|
= 2172,06 W/m2.K
|
d1
|
Avec Nu1 = 0,36Re1 É,55Pr1 1/3 = 443,41
Ainsi le coefficient global d'échange sera donné
par (I.12) :
1 K
|
1
+
h1 d1
d2
|
1
+ h2
|
d2 ln 2ëc
|
d1
d2
|
K = 999,67 W/m2. K
La relation (I.14) nous permet de calculer la surface
d'échange connaissant K :
S =
|
Ö
= FKÄTML
|
197400
|
|
= 7,718 m2
|
1 X 999,67 X 25,6
|
Avec :
F=1 pour une configuration contre courant D'où la
longueur L du tube dans la calandre est donnée par:
L =
|
S
|
7,718
|
= 1,77 m
|
=
ðd2Nt
|
|
3,14 X 0,0251 X 55
|
Longueur tube
Et le nombre des chicanes est donnée par :
= 59,17
espace entre deux cä·can,.
Tei-Tsi 85-38
La relation I.15 nous permet de trouver l'efficacité : e =
= = 0,74
Tei-Tez 85-22
k
i = p
d2
|
V2 2
2
|
= 103,6 Pa/m
|
De plus, comme nous sommes dans un régime turbulent (Re
< 10e) la relation (I.22) nous permet de trouver k = 0,316 X Re2
a1/4 = 0,316 X 16690a9/Í = 0,03
56
Tableau 3.3. Résultats de calcul de l'échangeur
RESULTATS
|
Grandeurs
|
Huile
|
Eau
|
Unité
|
Vitesse
|
1,67271064
|
0,40751127
|
m/s
|
Débit massique
|
2
|
1,91632174
|
l/s
|
Nombre de Reynolds
|
2613,61038
|
10239,4323
|
|
Nombre de Prandtl
|
4296
|
6,989785
|
|
Nombre de Nusselt
|
443,410926
|
110,52033
|
|
Coefficient d'échange convectif
|
2172,06192
|
1692,71354
|
W/ (m2.K)
|
Coefficient global d'échange
|
999,6793456
|
W/ (m2.K)
|
Puissance thermique
|
197400 (ou 47 kcal/s)
|
W
|
Efficacité
|
0,746031746
|
%
|
Rapport de débit
|
0,523640849
|
|
Facteur de correction
|
1
|
|
Surface d'échange
|
7,718821604
|
m2
|
Longueur du tube
|
1,775230236
|
m
|
Nombre de chicanes
|
59,1743412
|
|
Source : Calcul précédent
Au regard des résultats trouvés ci haut nous
pouvons faire un choix sur l'échangeur RBW200/80/G1G produit par la
société QVF LTD®. (Tableau A.4.2) avec les tubes en cuivre
et la calandre en acier inoxydable. Tandis que le diamètre de la
calandre peut être ajusté au cas où elle ne
répondait pas aux attentes de bon fonctionnement tout en
contrôlant aussi la vitesse de l'huile qui est fonction du
diamètre de la calandre. (D\ = V1 7)
En effet, le catalogue QVF COMPOSANTS donne également
les caractéristiques de cet échangeur à savoir le
matériau constituant la calandre et les tubes, la pression de service,
nombre de tubes, nombre de passe, etc.
L'évaluation des pertes de charge vont nous permettre
de faire un choix sur la puissance de la pompe adaptée pour
véhiculer de l'eau dans le circuit de refroidissement.
Evaluation des pertes de charge linéaire
La relation I.20 nous permet d'évaluer les pertes de
charge linéaires dans le circuit de refroidissement :
57
L'échangeur aussi génère les pertes
régulières qui peuvent être évaluées à
:
k
Jéch = ñ
d2
|
V2 2
2
|
L = 183,9 Pa
|
Evaluation des pertes de charge singulière
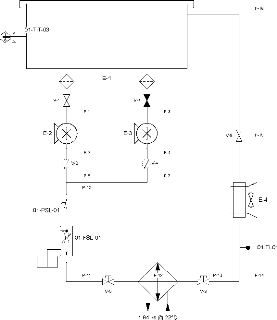
vannes
|
Description
|
V-1
|
vanne d'isolement
|
V-2
|
clapet anti retour
|
V-3
|
vanne d'isolement
|
V-4
|
clapet anti retour
|
V-5
|
vanne à fermeture étanche
|
V-6
|
vanne à fermeture étanche
|
Liste des équipements
|
|
|
Texte affiché
|
Description
|
|
|
|
E-1
|
réservoir
|
|
|
|
E-2
|
01-PMP-01
|
pompe à pression de l'eau
|
E-3
|
01-PMP-02
|
pompe à eau stand by
|
E-4
|
ventillateur
|
|
Z = 6808,673Pa
Figure III.3. Schéma hydraulique de
l'échangeur
Le circuit hydraulique (figure III.3) présente les
obstacles au niveau :
V' 5 vannes (~ = 7)
V' 1 clapet anti retour (~ = 40)
V' 1 échangeur (~ = 2,5)
V' Débitmètre ( = 0,5)
V' 4 coudes (~ = 1)
Les valeurs de sont données dans le tableau A.1.3
(p.71)
La somme de toutes ces pertes de charge singulières
donne en se référant à la relation (I.23) donne :
58
La relation (I.24) nous permet d'évaluer la hauteur
manométrique en supposant Hg négligeable puisque les pompes
fonctionnent en surface.
Hù ~ êëì Émm CEÊ
d'où Hù ~ 723,36 mm CE g
Connaissant le débit de l'eau qui est de 1,9163 l/s (ou
6,89 m3/h) pouvons-nous choisir la pompe LT 20 dans le catalogue des
pompes LEROY SOMER® (tableau A.4.3) dont voici les caractéristiques
:
Code produit : T 051 PC 03
Débit [m3/h]= 6
Puissance [kW]=0,55
Intensité Tri 230V/400V [A]= 2,35/1,35
Le tableau 3.4 illustre les caractéristiques du
système de refroidissement par rapport aux pertes de charges.
Tableau 3.4. Caractéristiques du circuit de
l'échangeur
EVALUATION DES PERTES DE CHARGE
|
Longueur du circuit
|
1
|
m
|
Coefficient de perte de charge
|
0,031413629
|
|
Pertes de charge régulières
|
103,6008646
|
Pa/m
|
Pertes de charge du circuit
|
103,6008646
|
Pa
|
Pertes de charge singulières
|
vannes (x5)
|
2906,145081
|
Pa
|
clapet anti retour (x1)
|
3321,308664
|
Pa
|
débitmètre (x1)
|
41,5163583
|
Pa
|
échangeur (x1)
|
207,5817915
|
Pa
|
coudes (x4)
|
332,1308664
|
Pa
|
Pertes régulières échangeur
|
183,9153873
|
Pa
|
Hauteur géométrique
|
0
|
mm
|
Hauteur manométrique
|
723,3638138
|
mm CE
|
Hm majorée de 50%
|
1085,045721
|
mm CE
|
Source : calcul précédent
59
CHAPITRE IV. SYSTEME DE COMMANDE AUTOMATIQUE
Le système de refroidissement est commandé par
les API (ou PLC) et supervisé par un moniteur en mode SCADA et comporte
les modules électroniques pour faciliter et permettre la gestion des
paramètres de fonctionnement et cela selon un programme pré
établit.
IV.1. IDENTIFICATION DES COMPOSANTS
Le système de refroidissement est constitué tel
que montré sur le figure VI.1 de :
- Echangeur à eau multitubulaire
- Des pompes 01-PMP-01 et 01-PMP-02 fonctionnant en
redondance.
- Des capteurs (température, pression, débit)
- Des vannes (isolement, d'alimentation et d'admission)
- D'un réservoir d'eau
- Et de la tuyauterie
Tableau 4.1. Identification des zones fonctionnelles
Zone fonctionnelle
|
Equipements associés
|
Zone 1 : Huile
|
02-0L-PMP-01 & 02-0L-PMP-02
02-LP-FSL-03
02-HP-PSL-03
01-TIT-01
Vanne d'alimentation
Vannes d'isolement
Clapets anti retour
Filtre à huile
|
Zone 2 : Eau
|
01-PMP-01 & 01-PMP-02 01-PSL-01 01-FSL-01 01-TIT-03 Vanne
d'alimentation Vannes d'isolement Clapet anti retour
|
Zone 3 : Sortie échangeur
|
01-TIT-02
01-TI-01
Vannes d'isolement
|
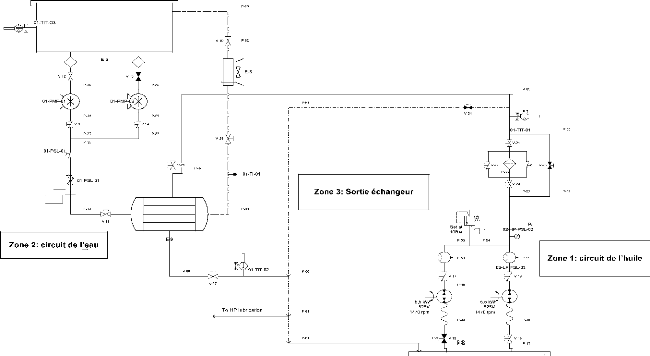
60
Figure IV.1. Système de refroidissement
Figure IV.2. Circuit hydraulique du système de
refroidissement
61
IV.2. DESCRIPTION FONCTIONNELLE
La commande du système est constituée des
pré-actionneurs (relais), des actionneurs ainsi que des capteurs pour
l'acquisition et le traitement des données suivant un programme
utilisateur.
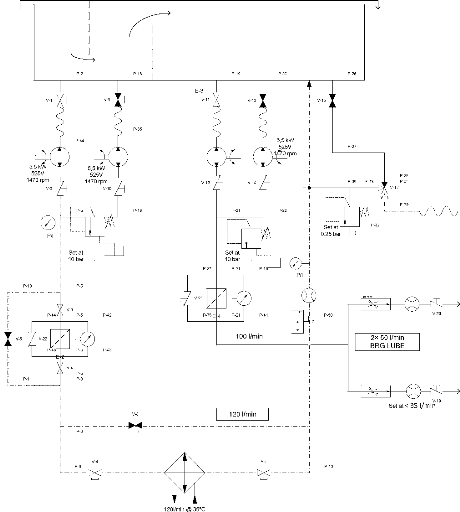
62
Tableau 4.2. Description fonctionnelle du système de
refroidissement
Zone 1 et 2 : 02-0L-PMP-01 et 01-PMP-01
|
02-0L-PMP-01
· débit : 2l/s
· puissance : 5,5 kW
· rpm : 1470
|
01-PMP-01
· débit : 1,9l/s
· puissance : 0,55 kW
· rpm : -
|
Le démarrage et l'arrêt des pompes sont
commandés à partir de la salle de contrôle.
Le nombre de démarrages est comptabilisé
à des fins de maintenance. Il est possible de remettre à
zéro le compteur et l'indicateur à l'aide d'un même
bouton-poussoir.
|
Les conditions de validation sont les suivantes :
Le capteur de débit (02-LP-FSL-03) signale le débit
d'huile (figure IV.1)
Si 01-TIT-01 indique Tei ~ 60°C
Si 01-PSL-01 indique une pression P2 > 10,64 kPa
(tableau 3.4)
La vanne d'admission d'huile s'ouvre vers le circuit de
refroidissement
La vanne d'alimentation du circuit de refroidissement est
ouverte
L'arrêt d'urgence n'est pas activé.
01-FSL-01 est munie d'une électrovanne modulante qui ouvre
en fonction de Tei et Te2 lue par 01-
TIT-01 et 01-TIT-02 en vue de faire passer un débit
optimal m2~
Ou sinon le système de refroidissement est by
passé. (figure IV.2)
|
Les conditions d'arrêt sont les suivantes :
Si 01-TIT-01 indique Tei = 40°C
Si 01-TIT-02 indique T.1 > 45°C
Le capteur de débit (01-FSL-01) ne signale pas de
débit 7 s après le déclenchement du moteur des
pompes.
Le capteur de débit (01-FSL-01) ne signale plus de
débit pendant le fonctionnement.
|
Zone 1 : Vanne d'admission et d'alimentation
|
La vanne d'admission de l'huile lubrifiante permet de by passer
ou d'amener l'huile dans le circuit de refroidissement, cette vanne est munie
d'un commutateur. (figure IV.2) La vanne laisse passer l'huile dans circuit de
refroidissement si Tei ~ 60°C. La vanne by passe
l'échangeur si Tei = 40°C
|
Les électrovannes et capteurs sont commandés par le
programme « step 7 »
|
La condition de validation est la suivante : 02-0L-PMP-01 est
activée.
|
Les conditions d'arrêt sont les suivantes : 02-LP-FSL-03
n'indique pas de débit
|
Echangeur
|
L'échangeur assure le maintien de la température de
l'huile
|
Le démarrage et l'arrêt de l'échangeur sont
commandés à partir d'un poste d'opération situé
dans la salle de contrôle et cela en mode SCADA. Le nombre de
démarrages est comptabilisé à des fins de maintenance. Il
est possible de remettre à zéro le compteur et l'indicateur
à l'aide d'un même bouton-poussoir.
|
Commutateur de mesure du niveau
|
Ce commutateur est placé dans le réservoir d'eau
et sert également au verrouillage de 01-PMP-01 et du moteur du SAG
Mill.
Si le niveau d'eau atteint 20%, une alarme retentit pour signaler
l'opérateur (figure III.3 & IV.1)
|
63
02-HP-PSL-03 est incorporé dans l'interlock ou le
verrouillage du SAG Mill et ce dernier démarre si la pression P1 (BP)
lue par ce capteur respecte la consigne (§ II.1.3)
01-TI-01 : nous donne une lecture simple de la
température de l'eau et n'intervient pas dans le verrouillage de
démarrage du système de refroidissement.
01- PMP-01 et 01- PMP-02 : Pompes à pression d'eau, qui
fonctionnent en redondance.
IV.3. Algorithme de programmation du système de
commande
Le programme de commande de l'automate va nous permettre de
contrôler toutes les grandeurs d'entrée et de sortie du
système de refroidissement entre autre :
y' Le débit d'eau
y' Les températures d'entrée et de sortie de l'eau
et de l'huile
Le programme assure le démarrage et l'arrêt
automatique du système (langage à contact), la conversion des
signaux analogiques en signaux numériques des capteurs
(langages des blocs fonctionnels) et il est exécuté
avec le logiciel step 7.
IV.3.1. Algorithme de démarrage automatique
Lire Te1 : température
Lire Ce : la commande
Lire Pe1 :01-PMP-01
Ue : urgence
Se : le système de commande
lecture de la température Tei ;
si commande automatique activée ;
si Tei ~ 60°C ;
alors activer marche / l'électrovanne du circuit
d'huile s'ouvre et la pompe 01-PMP-01 du système
démarre automatiquement ;
si urgence ;
alors appuyer manuellement sur arrêt
d'urgence/le système s'arrête
automatiquement ;
sinon si ;
sur le système il y a pas d'urgence ;
alors le système reste en
fonctionnement ;
sinon ;
procéder à un démarrage manuel du
système ;
fin.
IV.3.2. Algorithme de démarrage automatique de la
pompe 01-PMP-02
Lire Te1: température Lire Ce : la commande
Lire Po : position du commutateur
Lire Pe1 : 01-PMP-01
64
Lire Pe2 : 01-PMP-02
Ue : urgence
Se : le système de commande
lecture de la position du commutateur ;
si commande automatique activée ;
si la pompe 01-PMP-01 ne marche pas ;
alors la pompe 01-PMP-02 entre en marche ;
si urgence ;
alors appuyer manuellement sur arrêt
d'urgence/ le système s'arrête
automatiquement ;
sinon si ;
sur le système il n'y a pas d'urgence ;
alors le système reste en
fonctionnement ;
sinon ;
procéder à un démarrage manuel du
système ;
fin.
IV.3.3. Algorithme d'arrêt automatique
Lire Te1 : température
Lire Ce : la commande
Lire Pe1 : 01-PMP-01
Se : le système de commande
lecture de la température Tel;
si commande automatique activée ; si arrêt
automatique activé ;
si Tel = 40°C ;
sinon ;
procéder à un arrêt manuel du système
;
fin.
IV.3.4. Algorithme de contrôle de vitesse
Cet algorithme concerne le contrôle du débit
d'eau qui est fonction de sa vitesse. D'où son moteur sera muni d'un
variateur de vitesse.
Lire Te1 : température
Lire Ce : la commande
Lire Pe1 :01-PMP-01
Ue : urgence
De : le débit
Se : le système de commande
lecture de la température ;
si températureTel< valeur maximale ;
si température Te2< valeur maximale
alors diminution du débit de la pompe/ le débit
diminue en fonction de Tel et Te2 ;
sinon (Te2 = valeur maximale ou Te2= valeur
maximale) ;
65
la pompe refoule à son débit nominal/
l'électrovanne est ouverte à 100%
fin.
Les températures maximales de l'huile et de l'eau sont
fixées par l'opérateur, pour le cas qui nous concerne et en se
référant aux données de température
présentées au tableau 2.3-2.7 ces valeurs sont respectivement
fixées à 85°C et 22°C.
IV.3.5. Algorithme de contrôle de
température
Lire Te1 : température
Lire Ce : la commande
Lire Pe : 01-PMP-01
Se : le système de commande
lecture de la température :T.i ;
si commande automatique du système activée ; si
arrêt automatique activé ;
si T.1 < 38°C ;
alors arrêt automatique de la pompe 01-PMP-01 ;
sinon ;
procéder à un arrêt manuel su système
;
fin.
L'arrêt de la pompe 01-PMP-01 entraine automatiquement
l'arrêt du SAG Mill.
66
CONCLUSION GENERALE
Les montées de température de l'huile de
lubrification des paliers du SAG Mill ont un impact défavorable sur son
fonctionnement comme nous l'avions démontré dans ce travail.
Ce travail a porté sur la mise au point d'un
système automatique de refroidissement par eau du circuit de
lubrification des paliers à coussinets du SAG Mill, de l'entreprise
Ruashi Mining en vue de contourner les difficultés liées aux
montées des températures de l'huile ALPHA SP 320 dans ce
circuit.
Notre approche méthodologique de dimensionnement de
l'échangeur a été basée sur l'algorithme de DTML
(différence de température moyenne logarithmique) lequel nous a
permis de choisir à juste titre les caractéristiques
géométriques de l'échangeur à tubes et calandre car
nous avions à cet effet utilisé le logiciel Matlab 7.0 pour
parvenir à nos fins.
La commande du système étant assurée par
l'automate Siemens SIMATIC S7-300. Cependant, nous avions éprouvé
lors de l'élaboration de notre travail des difficultés
liées à la récolte des données et à
l'accès dans certaines installations telles que la salle de serveur pour
la programmation du système de commande par rapport à
l'algorithme présenté au quatrième chapitre.
L'intérêt de ce système automatique de
refroidissement repose sur le fait qu'à part la préservation des
paliers à coussinets du SAG Mill et le maintien des
propriétés lubrifiantes de l'huile ALPHA SP 320 du circuit. Ce
système peut s'appliquer à plusieurs autres systèmes
similaires à celui du SAG Mill et compte tenu du fait qu'il offre les
méthodes à la prise de contrôle de la température,
du débit et de la pression des fluides entrant dans l'échangeur
en vue de prédire son comportement selon un programme
prédéfinit par l'utilisateur et en rapport avec les conditions de
bon fonctionnement (consigne). Disons aussi par ailleurs que ce système
réalise les tâches répétitives de régulation
de débit lors de son fonctionnement tout en se soustrayant de
l'intervention manuelle.
Eu égard à ce qui précède, disons
qu'avant le début de ce travail, les mesures recherchées pour
contrôler la température de l'huile de lubrification des paliers
ont été menées entre autre la mise des chicanes dans le
réservoir quand bien même ne constituant pas la panacée car
soulevant encore d'éventuelles améliorations. C'est dans ce cadre
que nous avions voulu apporter une pierre à l'édifice avec notre
système.
Par ailleurs, plusieurs voies de recherche et de
développements techniques peuvent être envisagées pour
poursuivre cette étude. Disons enfin, à tous nos lecteurs que
leurs suggestions et critiques seront les biens venus pour la promotion de la
science.
67
BIBLIOGRAPHIE
[1] Frêne J., Nicolas D., DEGUEURCE B., Berthe
D. et GODET M., 1990, Lubrification hydrodynamique . paliers et
butées, éditons Eyrolles, Pp28 - 148.
[2] RICHARD J. et ROUX F, 1978,
.Lubrifiants, Techniques de l'ingénieur, B 590-591-592,
[3] GROFF J., 1961, ABC du
graissage, édition Technip, 74p.
[4] MC COULL N and WALTHER C., 1921,
Viscosity-Temperature chart, Lubrication.
[5] Electrical Apparatus Service Association, Inc.
Réparation des paliers à coussinet, Disponible sur :
http://www.easa.com (Avril 2012)
[6] LAROUSSE P., 1865, Grand
dictionnaire Universel du XIX siècle, Tome 12, p.63.
[7] P. GERARD, 1949, Le palier
fluide, Mémoire des Ingénieurs Civils de France
Pp.106-134.
[8] Daniel NICOLAS, 1978, Butées
et paliers hydrostatiques, Techniques de l'ingénieur, B5325,
25p.
[9] FRÊNE J., 1978, Butées
et paliers hydrodynamiques, Techniques de l'ingénieur, B5320,
48p.
[10] BONTEMPS A., GARRIGUE A., HUETZ J., MARVILLET
C., MERCIER P. et VIDIL R., 1978, Echangeurs de chaleur .
Définitions et architecture générale, Techniques de
l'ingénieur, B 2340, 24p.
[11] BONTEMPS A., GARRIGUE A., HUETZ J., MARVILLET
C., MERCIER P. et VIDIL R., 1978, Echangeurs de chaleur .
Description des échangeurs, Techniques de l'ingénieur, B
2341, 27p.
[12] BONTEMPS A., GARRIGUE A., HUETZ J., MARVILLET
C., MERCIER P. et VIDIL R., 1978, Echangeurs de chaleur .
Dimensionnement thermique, Techniques de l'ingénieur, B
2342,20p,
[13] LEONTIEV (A.), 1985, Théorie
des échanges de chaleur et de masse, éd. MIR, Moscou.
[14] DESSERS P., Pertes de charge dans
les tuyauteries . calculs et dimensionnements, Disponible sur:
http://www.courselec.free.fr
(Juin 2012).
[15] LE BRUN P., 1999, Automates
programmables industriels . Technologie, choix et mise en oeuvre,
Lycée Louis ARMAND, Pp.4-8.
[16] ROIZOT S., Etude des automates
programmables industriels, Disponible sur :
http://www.courselec.free.fr,
(Février 2012).
[17] LP DESCARTES 76400 FECAMP,
L'automate programmable industriel, Disponible sur:
http://www.courselec.free.fr
(Février 2012)
68
[18] MABILLEAU P. ing., 2001,
Capteurs, éd.,59p,
[19] BISSIERES C., Acquisition d'une
grandeur physique (capteurs), Disponible sur :
http://cbissprof.free.fr,
(Janvier 2012).
[20] ASCH G. & Collaborateurs, 1999,
Les capteurs en instrumentation industrielle, Dunod
5ème édition ISBN 2 10 004758 2.
[21] BENSOAM M., 2005, Cours : Capteurs et
Actionneurs Master SIS.1, Université Paul CEZANNE, 41p.
[22] WILLIAM C. Dunn, 2006, Introduction
to Instrumentation, Sensors, and Process Control, ARTECH HOUSE, INC.
323p.
[23] BERGER P., Capteurs,
Disponible sur :
http://philippe.berger2.free.fr/automatique/,
(Février 2011).
[24] PINSON G., Chaîne
d'acquisition et de traitement numérique, Disponible sur :
http://www.syscope.net/elec/,
(Janvier 2012).
69
ANNEXES
Tableau A.1.1.Classification ISO des huiles
industrielles
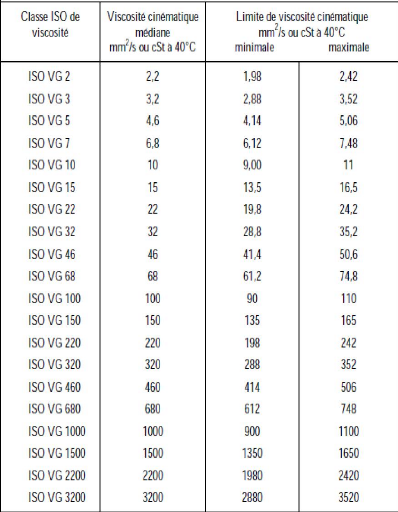
Source : Frêne J. et all, 1990, Lubrification
hydrodynamique : paliers et butées, p42.
70
Tableau A.1.2. Désignation des échangeurs
TEMA
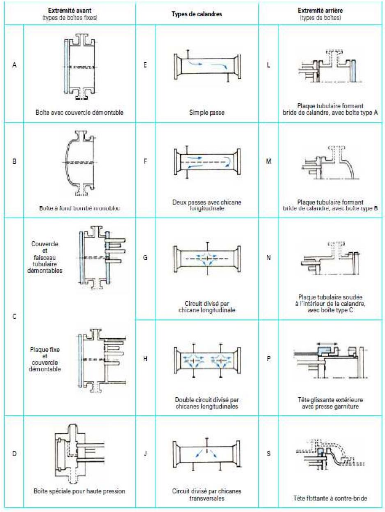
Source : André B.et all., Description des
échangeurs, Techniques de l'ingénieur, B 2341, p.8, 1978.
71
Source : DESSERS P., Pertes de charge dans
les tuyauteries : calculs et dimensionnements, p.16
Tableau A.1.3. Tableau du coefficient des pertes de
charge singulière
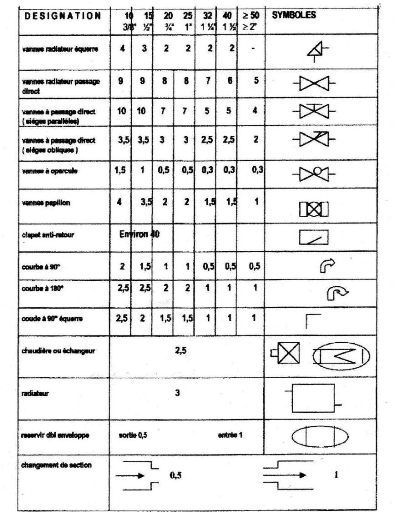
Figure A.2.1. Circuit de commande du SAG Mill (source :
Ruashi Mining/ Service électrique/Département de maintenance)
72
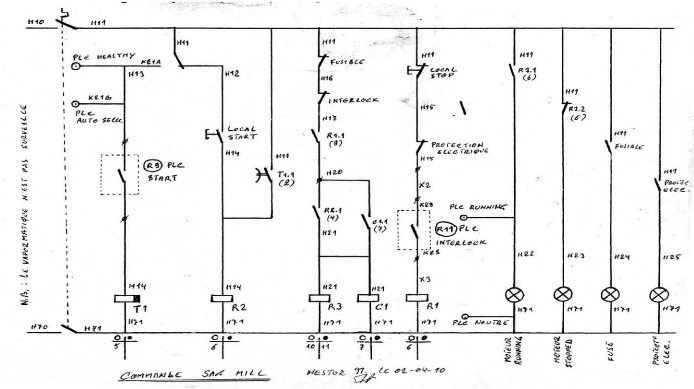
73
Tableau A.2.1. Fiche technique de l'huile ALPHA SP
320

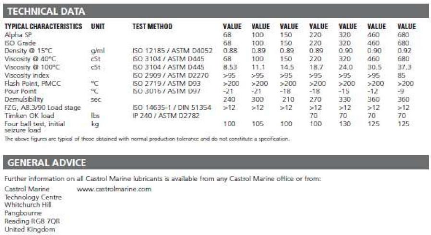
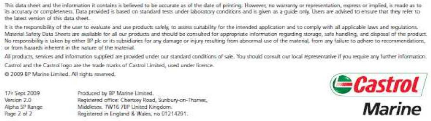
Source : BP Marine LTD®
74
Tableau A.3.1. Conductivité des
différents Matériaux
Matériau
|
Conductivité
[W·m-1·K-1]
|
Argent
|
430
|
Cuivre
|
348 à 390
|
Or
|
320
|
Aluminium
|
200 à 236
|
Platine
|
70
|
Fer
|
56
|
Acier
|
60
|
Acier doux
|
52
|
Quartz
|
8
|
Pierre naturelle non poreuse
|
3,5
|
Marbre
|
2,5
|
Béton ordinaire
|
1,6 à 2,1
|
Diamant
|
1000 à 2600
|
Verre
|
1 à 1,15
|
Terre sèche
|
0,17 à 0,58
|
Terre à 10% d'eau
|
0,50 à 2,10
|
Terre à 20% d'eau
|
0,80 à 2,60
|
Eau
|
0.58 à 0,6
|
Pierre naturelle poreuse
|
0,55
|
Maçonnerie en briques
|
0,30 à 0,96
|
Béton cellulaire
|
0,14 à 0,23
|
Bois
|
0,13 à 0,2
|
Sapin
|
0,12
|
Béton-chanvre
|
0,09 à 0,17
|
Linoléum naturel
|
0,081
|
Isolant fibreux
|
0,05
|
Laine
|
0,05
|
Perlite
|
0,045 à 0,05
|
Liège
|
0,04 à 0,05
|
Cellulose
|
0,04
|
Laine de verre
|
0,04
|
Mousse d'EPDM (élastomère)
|
0,04
|
Polystyrène
|
0,04
|
mousse de polyuréthane
|
0,025
|
Air
|
0,024
|
Huile Minérale
|
0,14
|
Source : Wickipedia®
75
Tableau A.3.2. Caractéristiques de l'eau
Général
|
Nom
|
Eau
|
Synonyme
|
Monoxyde de dihydrogène
|
Apparence
|
Liquide incolore, inodore et insipide
|
Propriétés chimiques
|
Formule brute
|
H2O (isomère)
|
Masse molaire
|
18,01530,0004 g. mol-1
H 11, 19%, 0 88,81% 18g. mol-1
|
Propriétés physiques
|
Température de fusion
|
0°C
|
Température d'ébullition
|
100°C, 100,02°C #177; 0,04
|
Masse volumique
|
1g. cm-3 à 4°C
|
Viscosité dynamique
|
1,002×10-3 Pa.s à 20°C
0,547×10-3 Pa.s à 50°C
0,2818×10-3 Pa.s à 100°C
|
Point critique
|
374,15°C 22,12 MPa
|
Point triple
|
0,01°C 611 Pa
|
Conductivité thermique
|
0,6Wm-1.K-1 à
20°C
|
Vitesse du son
|
1497 m.s-1 à 25°C
|
Thermochimie
|
Chaleur massique
|
4185,5 J. kg-1. K-1 à 15°C et
101,325 kPa
|
Propriétés optiques
|
Indice de réfraction
|
1,33
|
Constante de verdet
|
4,10 rad. T-1.m-1 à 480nm
|
Unités du SI & CNTP, sauf indication contraire.
|
Source : Wickipedia®
76
Tableau A.3.3. Caractéristiques du cuivre
Informations générales
|
Nom, symbole, Numéro
|
Cuivre, Cu, 29
|
Série chimique
|
Métaux de transition
|
Groupe, période, bloc
|
11, 4, d
|
Masse volumique
|
8,96 g. cma3
|
Dureté
|
3
|
Couleur
|
Orange cuivré, métallique
|
Propriétés physiques
|
Etat ordinaire
|
Solide
|
Point de Fusion
|
1084,62°C
|
Point d'ébullition
|
2562°C
|
Energie de fusion
|
1305kJ. mol(1
|
Energie de vaporisation
|
3003 kJ. mol(1
|
Volume molaire
|
711×10(6m3. mol(1
|
Pression de vapeur
|
0,0505 Pa à 1084,45°C
|
Vitesse du son
|
3570 m.s(1 à 20°C
|
Divers
|
Electronégativité
|
1,9
|
Chaleur massique
|
380 J. kg(1. K(1
|
Conductivité électrique
|
596×106 S. m(1
|
Conductivité thermique
|
401 W. m(1. K(1 sol dans HNO3
|
Unités du SI & CNTP, sauf indication contraire.
|
Source : Wickipedia®
77
Tableau A.4.1. Dimensions des tubes pour
échangeurs de chaleur
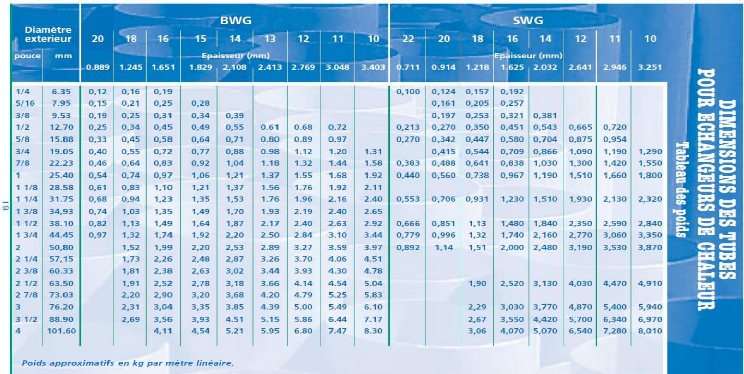
Source : charron inox
Source : Catalogue échangeur QVF LTD®, p.5.15
78
Tableau A.4.2. Gamme d'échangeur produit par QVF
LTD®
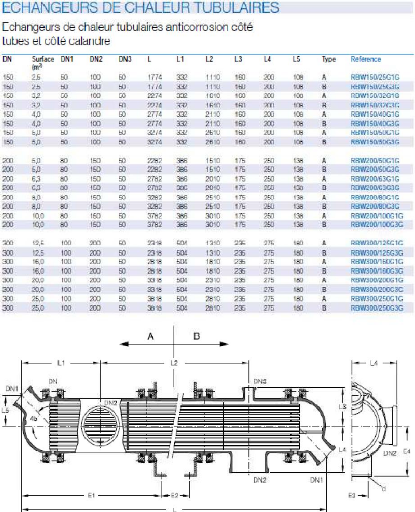
79
Tableau A.4.3. Caractéristiques des pompes LT
LEROY SOMER®
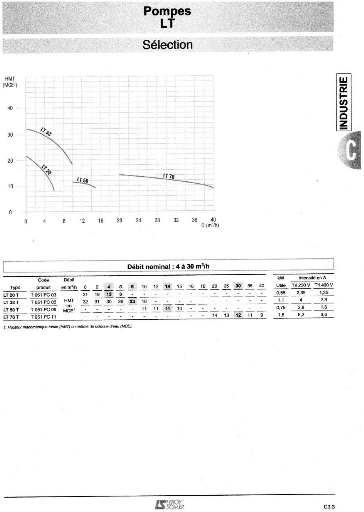
Source : Catalogue technique des pompes LEROY SOMER®
80
CODE DE PROGRAMMATION POUR LE CALCUL
DE
L'ECHANGEUR
%DIMENSIONNEMENT DE L'ECHANGEUR
% ce programme calcul l'échangeur au regard des relations
présentées au
% chapitre I du travail, il donne les caractéristiques
géométriques de
% l'échangeur en fonction des grandeurs d'entrée et
de sortie de deux
% fluides c'est à dire de l'huile et l'eau
d1=input('Introduisez le diamètre extérieur du tube
en [m]:'); d2=input('Introduisez le diamètre intérieur du tube en
[m]:'); D=input('Introduisez le diamètre intérieur calandre en
[m]:'); b=input('Introduisez l''espace entre deux chicanes en [m]:');
e=input('Introduisez l''epaisseur de la chicane en [m]:'); p=input('Introduisez
le pas en [m]:');
n=input('Introduisez le nombre de passes:');
N=input('Introduisez le nombre de tubes:');
Rho1=input('Introduisez la masse volumique de l''huile en
[kg/m3]:');
Rho2=input('Introduisez la masse volumique de l''eau en
[kg/m3]:'); Cp1=input('Introduisez la chaleur massique de l''huile en
[J/kg.K]:');
Cp2=input('Introduisez la chaleur massique de l''eau en
[J/kg.K]:'); Lambda=input('Introduisez la conductivité thermique de la
paroi en [W/m.K]:');
Lambda1=input('Introduisez la conductivité thermique de
l''huile en [W/m.K]:');
Lambda2=input('Introduisez la conductivité thermique de
l''eau en [W/m.K]:');
mu1=input('Introduisez la viscosité dynamique de l''huile
en [Pa.s]:');
mu2=input('Introduisez la viscosité dynamique de l''eau en
[Pa.s]:');
qmh=input('Introduisez le débit massique de l''huile en
[kg/s]:'); Te1=input('Introduisez la température d''entrée de
l''huile en [°C]:');
Ts1=input('Introduisez la température de sortie de
l''huile en [°C]:');%cette température est
déterminé à partir de la fiche technique de l'huile ALPHA
SP320, de tel sorte qu'elle soit dans la plage de fonctionnement
Te2=input('Introduisez la température d''entrée de
l''eau en [°C]:');
F=input('Introduisez le facteur de correction:');% cette valeur
est lue dans les abaques de kern, cependant elle vaut
généralement 1 pour une configuration contre courant
Nt=N/n
disp(['Le nombre de tubes par passe=' num2str(Nt)])
A2=(pi*d2^2)/4
disp(['La section intérieure du tube en [m2]='
num2str(A2)]) A1=(p-d1)*(b-e)
disp(['La section de passage entre deux chicanes en [m2]='
num2str(A1)])
Ts2=(Te1-Te2)/log(Te1/Te2)
81
disp(['La température de sortie de l''eau en
[°C]=' num2str(Ts2)])
DTLM=((Ts1-Te2)-(Te1-Ts2))/log((Ts1-Te2)/(Te1-Ts2))
disp(['La différence de température
logarithmique moyenne en [°C]='
num2str(DTLM)])
Pther=(qmh*Cp1)*(Te1-Ts1)
disp(['Le flux thermique échangé en [W]='
num2str(Pther)])
qme=Pther/[Cp2*(Ts2-Te2)]
disp(['Le débit massique de l''eau en [kg/s]='
num2str(qme)])
Vh=(qme*p)/(Rho1*D*A1)
disp(['La vitesse de l''huile en [m/s]=' num2str(Vh)])
Ve=qme/(Rho2*Nt*A1)
disp(['La vitesse de l''eau en [m/s]=' num2str(Ve)])
Re1=(Rho1*Vh*D)/mu1
disp(['Le nombre de Reynolds de l''huile=' num2str(Re1)])
Re2=(Rho2*Ve*d2)/mu2
disp(['Le nombre de Reynold de l''eau=' num2str(Re2)])
Pr1=(mu1*Cp1)/Lambda1
disp(['Le nombre de Prandtl de l''huile=' num2str(Pr1)])
Pr2=(mu2*Cp2)/Lambda2
disp(['Le nombre de Prandlt de l''eau =' num2str(Pr2)])
Nu=0.36*(Re1^0.55)*(Pr1^0.33)
disp(['Le nombre de Nusselt de l''huile=' num2str(Nu)])
h1=(Lambda1*Nu)/d1
disp(['Le coefficient d''échange convectif de l''huile
en [W/m2.K]
=' num2str(h1)])
h2=(0.023*Lambda2*(Re2^0.8)*(Pr2^0.33))/d2
disp(['Le coefficient d''échange de l''eau en
[W/m2.K]='
num2str(h2)])
K=1/((d2/(h1*d1))+(1/h2)+(d2*log(d1/d2))/(2*Lambda))
disp(['Le coefficient thermique global d''échange en
[W/m2.K]='
num2str(K)])
S=Pther/(F*K*DTLM)% la surface d'échange thermique
disp(['La surface d''échange thermique en [m2]='
num2str(S)])
L=S/(pi*d2*Nt)
disp(['La longueur du tube en [m]=' num2str(L)])
Nc=L/b
disp(['Le nombre de chicanes=' num2str(Nc)])
eff=(Te1-Ts1)/(Te1-Te2)
disp(['L''efficacité de l''echangeur='
num2str(eff)])