Année universitaire : 2020 / 2021

|
République Algérienne
Démocratique et Populaire Ministère de l'Enseignement
Supérieur et de la Recherche Scientifique Université des
Frères Mentouri Constantine Faculté des Sciences de la
Technologie Département d'Electronique
|
|
MEMOIRE DE FIN D'ETUDES
EN VUE DE L'OBTENTION DU DIPLOME
MASTER
EN
Filière : Automatique
Spécialité : Automatique et Informatique
Industrielle
Thème
Conception et Réalisation de la
commande
supervisée de gestion de
l'eau
Présenté par : Encadré par
:
Ziad Youcef Pr Mansouri Noura
& &
Kismoune Khaled Mr. Naidja Abderaouf
(Ingénieur EGSA/C)
Résumé :
Le présent travail porte sur l'automatisation et la
supervision d'un système de distribution d'eau au sein de
l'aéroport Mohamed Boudiaf de Constantine.
Durant notre projet, nous avons étudié
l'installation actuelle et assimiler son fonctionnement pour réaliser un
cahier de charges du projet en respectant cette installation, en
intégrant quatre automates programmable industriels avec une interface
de supervision.
Notre travail est divisé en plusieurs parties :
identification de matériel à utiliser, Elaboration d'un programme
d'API via le logiciel TIAPORTAL V16, conception d'une interface de supervision
et télégestion ihm via SIMATIC WINCC avec un système de
communication réseau et réalisation des schémas
électriques.
Abstract:
This work focuses on the automation and supervision of a water
distribution system at Moha med Boudiaf Airport in Constantine.
During our project, we studied the current installation and
assimilate its operation to achieve a project specification by respecting that
installation, integrating four industrials programmable automats with a
monitoring interface.
Our work is divided into several parts: identify hardware to use,
develop an API program thro ugh TIAPORTAL V16 software, design a monitoring
interface and remote management hmi via SIMATIC WINCC with a network
communication system and make electrical schematics
: jeiliall
|
|
.ÉäíØäÓÞ í
ÇíÖæÈ ÏãÍã
ÑÇØã í åíáÚ
ÇÑÔáÅÇæ
åÇíãáÇ
ÚíÒæÊ ãÇÙäá
íááÂÇ
áíÛÔÊáÇ ìáÚ
áãÚáÇ ÇÐå
񧄒
|
ÊáÇÂ
|
ÚÈÑ
|
ÌãÏæ ÇåÈ
ÏíÞÊáÇ ááÇÎ
äã ØæÑÔáÇ
ÑÊÏÞíÞÍÊá
ÇåáíÛÔÊ
ÇäÈÚæÊÓÇæ
ÉÏæÌæãáÇ
|
ÊÇäíæßÊáÇ
ÇäÓÑÏ
ÚæÑÔãáÇ
ááÇÎ
|
ÉåÌÇæ
|
ÌãÇäÑÈ
ÑíæØÊæ
ÇåãÇÏÎÊÓÇ
ÏÇÑãáÇ
ÉÒåÌáÇ
ÏíÏÍÊ :ÁÇÒÌ
ÉÏÚ ìáÅ
ÇäáãÚ ãÓÞäí
.ÏÕÑ
|
ÉåÌÇæ Úã
ÉÌãÑÈã
ÉíÚÇäÕ
|
|
|
IHMÏÚÈ äÚ
ÉÑÇÏÅæ
ÉÈÞÇÑã
ÉåÌÇæ
ãíãÕÊæ TIAPORTAL V16
ÌãÇäÑÈ
|
ááÇÎ äã (API)
ÊÇÞíÈØÊ
ÉÌãÑÈ
|
.ÉíÆÇÈÑåßáÇ
ÊÇØØÎãáÇ
ÚäÕæ ÉßÈÔáÇ
ÊáÇÇÕÊÇ
ãÇÙä Úã SIMATIC WINCC
ááÇÎ äã
Remerciements
Avant de commencer ce mémoire, nous tenons à
remercier et glorifier ALLAH le tout puissant et miséricordieux, de nous
avoir donné le courage et la volonté de mener à terme ce
présent travail.
Ces remerciements sont adresses chaleureusement aussi
à notre promotrice à l'université Mme.
MANSOURI Noura de nous avoir encadrés, sa disponibilité et la
confiance qu'elle nous a accordée et à notre
Co-promoteur Mr NAIDJA Abderraouf pour nous avoir permis d'user de
son précieux temps et de nous avoir guidé et
encouragé à réaliser ce travail Nous tenons aussi à
remercier également les membres du jury pour avoir eu
l'extrême gentillesse de bien vouloir évaluer ce
travail.
Enfin nous remercions vivement tous ceux qui ont
participés de près ou de loin, ont contribué d'une
manière ou d'une autre à la réalisation de ce
mémoire.
Grand Merci à tous
Dédicace
Je tiens c'est avec grande plaisir que je dédie ce
modeste travail :
À l'être le plus cher de ma vie, ma mère
HALIMI SALIHA, qui m'a
soutenu et encouragé durant ces années
d'études. Qu'elle trouve ici le
témoignage de ma profonde reconnaissance.
A mes Chers Frères, et ma seule Soeur.
À mon binôme Khaled.
À tous les membres de ma famille et toute personne qui
porte le nom
Ziad, je dédie ce travail à tous ceux qui ont
participé à ma réussite.
A mes chers Amis.
A tous ceux que j'aime.
Ziad Youcef
Kismoune Khaled
Dédicace
A l'aide de DIEU tout puissant, qui trace le chemin
de ma vie, j'ai pu
Arriver à réaliser ce modeste travail
que je dédie :
À ma chère mère BOURAHLI Karima à
mon cher père Ahmed qui je ne
serai pas là
où je suis, que je remercie
Pour leurs présences, leurs amours leurs soutient et
leurs encouragements.
A ceux qui sont la source de mon
inspiration et mon courage, à qui je dois
De
l'amour et de la reconnaissance :
Une spéciale dédicace à mes frères
Med Zakaria et Abderrahmane, et mes
Soeurs Wissem et Rayen.
À tous les professeurs qui m'ont
apporté leurs connaissances tout au long
de mon parcours
de l'école primaire à l'université
A mon binôme Youcef.
A toute ma famille.
A mes
chers Amis.
A tous mes ami(e)s.
Et à tous ceux qui me
sont chers.
Table des matières
Introduction Générale 1
Chapitre 1 : Présentation Générale
de la problématique
1.1 Introduction 3
1.2 Système de distribution de l'eau de l'aéroport
3
1.3 Description du système actuel 4
1.4 Solution proposée 8
Chapitre 2 : Étude Fonctionnelle du
Système de Gestion de l'Eau
|
2.1 Introduction
|
10
|
2.2 Cahier des charges fonctionnel
|
10
|
2.3 Description de la partie matérielle de la solution
proposée
|
15
|
2.3.1 Les capteurs
|
15
|
2.3.2 Les pré actionneurs
|
19
|
2.3.3 Les Actionneurs
|
21
|
2.3.4 L'automate programmable industriel (API)
|
23
|
2.3.5 Les autres équipements
|
..24
|
Chapitre 3 : Description de la plateforme de
développement
|
|
3.1 Introduction
|
28
|
3.2 L'automate programmable industriel (API) S7-1200
|
29
|
3.3 Les modules entrées/sorties
|
31
|
3.3.1 Le Château d'eau et la Bâche a eau
|
31
|
3.3.2 Système anti-incendie
|
34
|
3.3.3 Système d'irrigation
|
35
|
3.4 La partie communication
|
38
|
3.4.1 Le réseau industriel Ethernet
|
38
|
3.4.2 Le protocole de communication PROFINET
|
39
|
3.4.3 Leonton CET2-0800 Series
|
41
|
3.5 Les logiciels
|
42
|
3.5.1 SIMATIC TIAPORTAL V16
|
42
|
3.5.2 SIMATIC WinCC
|
..42
|
3.5.3 SIMATIC STEP7
|
44
|
3.5.4 EPLAN Electric P8
|
46
|
Chapitre 4 : Programmation et Supervision
4.1 Introduction 48
4.2 Les modes de fonctionnement 48
4.2.1 Organigramme générale du choix du mode de
commande 49
4.2.2 Mode Manuel 49
4.2.3 Mode Automatique 50
4.2.4 Mode hors communication 63
4.3 La programmation 63
4.3.1 Les Alarmes 64
4.3.2 L'Interface Graphique (HMI) 65
Conclusion Générale 72
Introduction Générale
1
Introduction Générale
Le volume du trafic aérien ne cesse d'augmenter et le
nombre de passagers devrait plus que doubler au cours des 20 prochaines
années. Les aéroports doivent donc adapter leurs infrastructures
d'accueil et leurs services dans tous les domaines, pour simplifier la vie des
passagers de plus en plus nombreux et exigeants.
Comme tous les aéroports du monde, les aéroports
algériens doivent investir dans les nouvelles technologies qui
garantissent de meilleures performances et contribuent au confort des
voyageurs. D'où le besoin d'automatiser la gestion des ressources de
l'aéroport telle que la gestion d'eau pour faire baisser les
coûts, améliorer l'utilisation et réduire les pertes.
L'automatisation permet d'assurer l'approvisionnement continu
en eau à partir du réseau SEACO, du château d'eau ou de la
bâche à eau selon les conditions et cela sans aucune intervention
humaine. On peut ainsi remédier aux éventuelles absences des
personnes en charge de l'ouverture et de la fermeture des vannes
d'alimentation, de suivre en temps réel le fonctionnement du
système de distribution d'eau, de localiser de manière proactive
les pannes éventuelles et d'intervenir rapidement grâce à
des données et des alertes instantanées. Elle permet
également de garantir une bonne gestion de la consommation et de la
distribution de l'eau tout en évitant les gaspillages et de là
réduire la facture d'eau.
Au vu des améliorations que l'automatisation peut
apporter dans le contrôle et le fonctionnement de tout processus auquel
elle est appliquée, L'EGSA/C (Établissement de Gestion de
Services Aéroportuaires) Constantine place l'automatisation des
systèmes parmi ses premières priorités. L'automatisation
partielle ou complète de tous les systèmes est un concept
attrayant. En effet, il est communément admis que les opérateurs
humains actuellement chargés de la gestion de l'aéroport ne
peuvent plus améliorer leur productivité sans l'aide d'outils
informatiques relatifs à la présentation d'information et la
participation à la prise de décision.
Le stage que nous avons effectué au sein de
l'unité technique d'EGSA de l'aéroport Mohamed BOUDIAF de
Constantine, nous a permis de nous faire une idée sur l'importance de
l'automatisation du système de distribution et de gestion de l'eau dans
cette structure et l'intérêt du contrôle et de la
surveillance de toutes les opérations à partir d'une salle de
supervision pour bien suivre l'état de fonctionnement du système
et permettre une intervention rapide et efficace en cas de défaut.
L'objectif de notre projet est la conception d'un système utilisant les
principes de l'automatisation dans le but d'apporter des améliorations
au système de gestion et de distribution de l'eau de l'installation
existante et répondre ainsi à la problématique
posée par l'EGSA/C. Pour cela, nous avons élaboré un
nouveau schéma d'automatisation puis élaboré les
2
Introduction Générale
programmes correspondants et conceptualisé une
interface de contrôle et de supervision du système.
Le travail réalisé, sera exposé dans ce
mémoire en quatre chapitres comme suit :
Dans le premier chapitre, nous avons donné une vue
générale de l'installation de distribution d'eau existante avec
une analyse fonctionnelle, ensuite nous avons posé la
problématique pour enfin énoncer la solution proposée.
Le deuxième chapitre est consacré à la
présentation fonctionnelle de l'installation proposée pour
comprendre l'amélioration apportée au cahier de charges que nous
avons défini et les instruments présentés dans ce
processus.
La description de la plateforme de développement et des
logiciels utilisés dans ce travail est faite dans le troisième
chapitre alors que le quatrième et dernier chapitre de ce mémoire
traite de la partie programmation et supervision de ce projet, les
organigrammes fonctionnels ainsi que les résultats.
Chapitre 1 : Présentation Générale
de
La problématique
3
Chapitre 1 : Présentation
Générale de la problématique
1.1. Introduction :
L'eau est un bien précieux qu'il est nécessaire
de préserver. C'est également une ressource épuisable et
son utilisation doit faire l'objet d'une attention particulière de la
part de tout gestionnaire. L'une des missions essentielles attribuées
à l'EGSA/C, est justement la gestion de l'alimentation en eau potable
dans les aéroports qui sont sous sa responsabilité.
Une gestion efficace des ressources est donc indispensable
pour réduire la consommation d'énergie et d'eau et
prévenir les pertes. Pour cela, l'EGSA/C a initié un plan de
modernisation qui permettrait de mieux surveiller le réseau de
distribution, connaitre les évolutions de la consommation d'eau et mieux
anticiper les besoins en maintenance, tout en offrant de meilleures conditions
de confort aux passagers et aux personnes travaillant sur le site. Cela
permettra également un partage et une utilisation plus efficaces des
ressources
L'automatisation et la modernisation des équipements
présente des atouts importants. On citera par exemple,
l'amélioration de la collecte des données offrant une vue
d'ensemble et en temps réel, de l'état de fonctionnement du
système d'alimentation en eau potable. Ce qui permet l'identification
instantanée des problèmes pouvant intervenir et leur
résolution dans des délais plus courts. La réduction
significative des temps d'arrêts contribue à réduire les
coûts et à permet une plus grande disponibilité de
l'eau.
Dans ce chapitre nous allons faire une description
générale du système de distribution d'eau actuel avec une
étude fonctionnelle du système installé, ensuite on
détaillera la problématique posée ainsi que les solutions
proposées.
1.2. Présentation du Système de
distribution de l'eau :
Comme dans toute autre infrastructure du même type, un
aéroport est un grand consommateur d'eau à des fins diverses.
Pour cela, le système de distribution de l'eau de l'aéroport
Mohamed Boudiaf comporte un château d'eau et une bâche à
eau. Ce système trouve ses sources d'eau dans le réseau SEACO qui
assure également l'alimentation continue en eau de l'aéroport. La
planification, le développement, la distribution et la gestion de
l'utilisation optimale des ressources en eau sont les missions assurées
par l'EGSA Constantine.
· Le château d'eau :
Le château d'eau sert à alimenter
l'aéroport en cas de coupure sur le réseau principal de SEACO. Il
est directement approvisionné par le réseau d'eau potable de
SEACO. Il a une hauteur suffisante pour obtenir une pression statique et une
capacité de 500m3 dont seuls une quantité de 300 m3
peut être utilisée pour l'alimentation en eau courante, le reste
de la capacité est réservé pour les cas d'urgence.
4
Chapitre 1 : Présentation
Générale de la problématique
· La bâche à eau :
Ce réservoir est aussi approvisionné par le
réseau d'eau potable de SEACO. Il sert également à
alimenter l'aéroport en cas de coupure sur le réseau principal.
Comme pour le château d'eau, seule une quantité de 300
m3 peut être utilisée pour la consommation et le reste
pour les cas d'urgence.
· Le système anti incendie :
Les réserves en eau du château d'eau et de la
bâche servent également à stocker une certaine
quantité appelée réserve d'incendie. Cette réserve
est destinée à être utilisée par les
sapeurs-pompiers en cas d'incendie. Une station de surpression permet d'assurer
une pression importante en cas d'incendie important.
· Le système d'irrigation :
Les espaces verts à irriguer représentent plus
de 13000 m2 divisés en plusieurs zones. Actuellement,
l'arrosage de ces espaces se fait manuellement et selon des périodes.
L'arrosage de certaines zones se trouvant à des endroits
éloignés nécessite en plus, l'utilisation de camion
citernes. Cet arrosage manuel est peu économique et peut entrainer soit
un gaspillage d'eau soit une insuffisance en eau pour certaines zones. De plus,
il nécessite beaucoup de temps et une présence humaine
permanente.
1.3 Description du système actuel :
Le système de distribution d'eau fonctionne selon un
procédé plus ou moins complexe. Toutes les opérations
relatives à la gestion de l'alimentation en eau au niveau de
l'aéroport, se fait sur intervention des opérateurs de l'EGSA
soit pour faire le remplissage des réserves soit pour faire la
distribution de l'eau lors de coupures sur le réseau de distribution
SEACO. Le démarrage des pompes et l'ouverture ou fermeture des vannes se
font manuellement. On peut également avoir des problèmes de
disfonctionnement de matériel dont la détection peut prendre
beaucoup de temps et parfois sans connaitre l'origine de problème.
La gestion manuelle des taches, génère une
perte de temps considérable et peut parfois être la cause de
perturbations voire même de coupure de l'alimentation en eau potable.
La compréhension du fonctionnement du système
d'alimentation en eau actuel, passe par la description des 4 constituants
essentiels cités précédemment et qui sont : le
château d'eau, la bâche à eau, le système
anti-incendie et le système d'irrigation. Nous allons donc
décrire dans ce qui suit, le fonctionnement de chacun de ces
éléments.
5
Chapitre 1 : Présentation
Générale de la problématique
1.3.1 Fonctionnement du château d'eau :
Le château dispose de 3 conduites d'eau principales :
· La première permet le remplissage de
château d'eau qui se fait à partir de la canalisation principale
reliée au réseau de distribution d'eau potable de la
société SEACO. Le remplissage se fait par l'ouverture des vannes
responsables du remplissage et le démarrage de la pompe d'eau. Si cette
dernière est en panne l'opérateur met en marche une
deuxième pompe.
· La deuxième conduite sert à la
distribution de l'eau vers l'aéroport en cas de coupure sur le
réseau SEACO ou pour toute autre utilisation spécifique comme le
remplissage de camions-citernes. Tout le processus est contrôlé
par la manipulation de vannes manuelles.
· La troisième conduite est
réservée pour le réseau anti-incendie et le vidange.
Le château d'eau est équipé d'un flotteur
qui indique le niveau de l'eau : niveau très bas, bas, haut, très
haut, cela permet de gérer son remplissage et l'alimentation de
l'aéroport en eau.
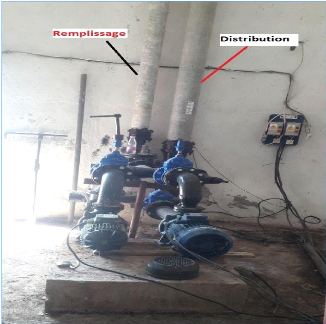
Figure 1.1 : Canalisations du château
d'eau
6
Chapitre 1 : Présentation
Générale de la problématique
1.3.2 Fonctionnement de la Bâche à eau :
Comme le château d'eau le remplissage de bâche
à eau se fait à partir de la canalisation principale
reliée au réseau SEACO. Cette dernière est
également équipée d'un flotteur de niveau pour gère
le remplissage et la distribution d'eau
S'il n'y a pas d'eau dans le château d'eau ou qu'il y a une
coupure sur le réseau de la SEACO, la bâche à eau devient
la source d'alimentation en eau grâce à 2 pompes
électriques centrifugeuses et des vannes manuelles.
Une partie de l'eau contenue dans la bache à eau, est
réservée pour le réseau anti-incendie en cas
d'extrême urgence.
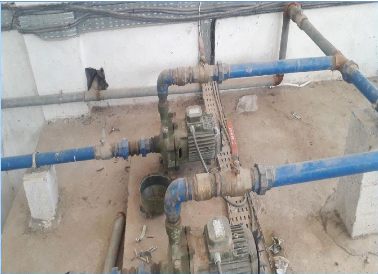
Figure 1.2 : Canalisation de distribution de
la bâche à eau
1.3.3 Station de surpression eau incendie :
Comme indiqué précédemment, une station
de surpression composée de 2 suppresseurs et 2 pompes électriques
permet d'atteindre une pression supérieure ou égale à 7
bars. Elle dispose également de 2 vannes qui alimentent le site en eau
incendie et est gérée grâce à un détecteur de
débit et d'un autre de pression et à partir de réseau
SEACO, le château d'eau et la bâche à eau. Cette station est
installée de manière à satisfaire les besoins
nécessaires en eau, même en cas de coupure sur le réseau
SEACO et son état de fonctionnement doit être
régulièrement vérifié. Ce qui nécessite le
déplacement des opérateurs à l'endroit où elle est
installée pour faire la vérification.
7
Chapitre 1 : Présentation
Générale de la problématique
La station de surpression est reliée à un
réseau constitué de plusieurs postes installés à
différents endroits de l'aéroport.
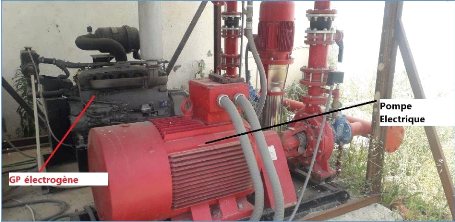
Figure 1.3 : Station de surpression eau
incendie
1.3.4 Le système d'irrigation :
L'arrosage des espaces verts se fait de manière
totalement manuelle et seulement à partir de la canalisation principale
du réseau de distribution d'eau potable de la société
SEACO et en plein soleil, ce qui provoque un gaspillage d'eau car
jusqu'à 75 % de l'eau s'évapore plutôt que d'atteindre la
plante.
Cet arrosage manuel de la totalité des espaces verts
est très chronophage et nécessite des gros efforts de la part de
l'opérateur en charge de cette mission pour arroser toutes les zones.
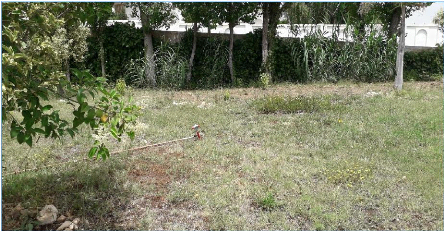
Figure 1.4 : système d'arrosage
actuel
8
Chapitre 1 : Présentation
Générale de la problématique
1.4 Solution proposée :
Après étude du fonctionnement de l'installation
actuelle et l'assimilation de son fonctionnement, nous avons relevé
plusieurs points sur lesquels il est utile d'intervenir en vue
d'améliorer le fonctionnement du système de distribution tout en
assurant une disponibilité continue de l'eau.
La solution proposée intègre un fonctionnement
basé sur la programmation autour de quatre automates de type SIEMENS
S7-1200, cette programmation des automates via le logiciel TIAPORTAL V16 a deux
modes de fonctionnement : Le mode manuel et le mode automatique, et une
interface de supervision qui permet de superviser et télé
gérer en temps réel l'installation automatisée.
Cette automatisation intégrée par des API permet
d'assurer le contrôle et la surveillance à distance de tous les
équipements et les installations du système de distribution en
évitant d'éviter les problèmes liés à une
conduite manuelle du système et aussi remédier aux
problèmes récurrents des arrêts de fonctionnement de
l'alimentation en eau. Cette automatisation permettra également
l'affichage des paramètres de fonctionnement et le déclenchement
d'alarmes d'avertissements en cas de dysfonctionnement pour permettre un
diagnostic pertinent sur les défaillances pouvant apparaitre au niveau
des divers matériels : pompes, électrovannes et câblages et
permettre une intervention rapide et efficace.
Chapitre 2 : Analyse fonctionnelle du
Système de Gestion d'eau
10
Chapitre 2 : Étude Fonctionnelle du
Système de Gestion de l'Eau
2.1 Introduction :
Dans ce chapitre nous allons présenter l'étude
fonctionnelle du système de distribution d'eau puis définir les
règles d'automatisation essentielles à suivre et identifier les
équipements nécessaires pour réaliser la solution
automatisée. On détaillera en particulier le fonctionnement des 4
parties à savoir : le château d'eau, la bâche à eau,
le système anti-incendie et le système d'irrigation.
On abordera également le cas de l'élaboration d'une
solution programmable dans le cas où la gestion demande
l'interdépendance des systèmes et la synchronisation entre
eux.
2.2. Cahier des charges fonctionnel :
Nous avons divisé le système en quatre parties
essentielles chaque une est géré par un automate siemens de type
S7-1200, programmé pour faire le contrôle à distance et en
temps réel à partir d'une station de supervision situé
à la salle de contrôle.
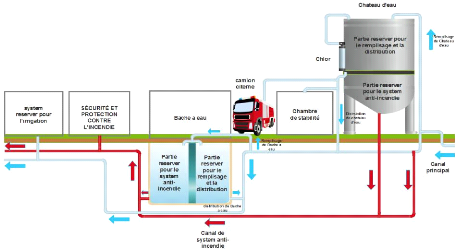
Figure 2.1: Schéma synoptique global
après l'automatisation
2.2.1 Le Remplissage du château d'eau et la
Distribution :
Afin d'éviter les débordements et le manque
d'eau récurrents constatés sur le château d'eau et
éliminer toute intervention humaine sur le fonctionnement des groupes de
pompage, l'exploitant du site a exprimé le besoin d'automatiser le
château d'eau ainsi que la télégestion de ce dernier via la
supervision de secteur avec le SIMATIC WINCC.
Chapitre 2 : Étude Fonctionnelle du
Système de Gestion de l'Eau
Gérer par un automate indépendant du type siemens
S7-1200, l'automatisation du remplissage et de la distribution de l'eau
à partir du château d'eau est réalisé en tenant
compte des paramètres suivants :
Ø Contrôle du niveau de chlore.
Ø Commandes des électrovannes canalisations
principales et de distribution.
Ø Commande des pompes de remplissage avec synchronisation
entre elles.
Ø Contrôle du niveau d'eau réservé
à l'utilisation quotidienne et du réseau anti-incendie.
Ø Détection de la présence d'eau dans la
canalisation SEACO et contrôle du débit.
Ø Déclenchement d'alarmes en cas des
défauts au niveau des pompes et/ou des électrovannes ou d'une
surabondance ou absence d'eau.
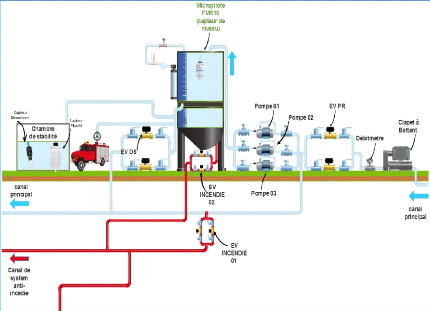
11
Figure 2.2: Schéma synoptique du
château d'eau après l'automatisation
12
Chapitre 2 : Étude Fonctionnelle du
Système de Gestion de l'Eau
2.2.2 Le remplissage de la bâche à eau
et la distribution :
La bâche à eau aussi est gérée par un
automate de même type et de mêmes caractéristiques que celui
utilisé pour l'automatisation du fonctionnement du château
d'eau.
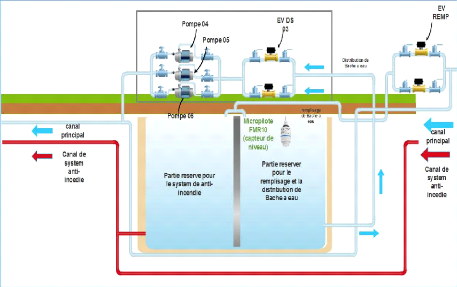
Figure 2.3: Schéma synoptique de la
Bâche à eau après l'automatisation
L'automatisation du remplissage et de la distribution de
l'eau à partir de la bâche à eau est réalisée
en tenant compte des paramètres suivants :
Ø Commande des électrovannes (ouverture/
fermeture) de remplissage et distribution.
Ø Commande des pompes de distribution avec
synchronisation entre elles.
Ø Contrôle du niveau d'eau réservé
à l'utilisation quotidienne et du réseau anti-incendie.
Ø Déclenchement d'alarmes dans le cas de :
défauts ou pannes au niveau des pompes, des électrovannes ou en
cas de débordement ou manque d'eau.
Ø Surveillance et contrôle à distance en
temps réel de toutes les opérations.
2.2.3 Système anti-incendie :
Pour contrôler et surveiller à distance et en
temps réel la station de surpression, on a choisi d'utiliser un automate
spécifique pour gérer et surveiller le fonctionnement de ce
système.
13
Chapitre 2 : Étude Fonctionnelle du
Système de Gestion de l'Eau
Ce dernier va remplacer la carte électronique existant sur
le système actuel et dont le cout est très élevé et
qui n'est ni contrôlable ni observable à distance.
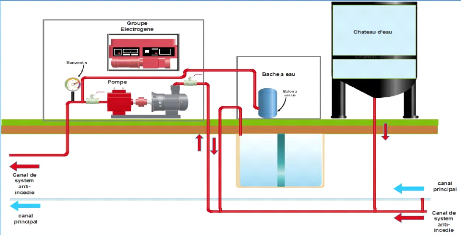
Figure 2.4: Schéma synoptique de la
station de surpression après l'automatisation
2.2.4 Système d'irrigation :
Pour assurer l'indépendance de ce système et
éliminer les inconvénients du système actuel, on a choisi
de consacrer au système d'arrosage, son propre automate. Ce dernier aura
à gérer l'arrosage de l'ensemble des espaces verts
répartis en 6 zones, grâce à une commande
automatisée périodique et à distance.
Le système est composé de tuyaux
équipés d'arroseurs, électrovannes et des pompes
directement branchés à la source principale de SEACO. L'ensemble
est ensuite relié à son propre API de type Siemens
S7-1200 permettant d'effectuer les différents réglages.
Cette option permet de planifier l'heure de l'arrosage et être
piloté à distance.
Cet arrosage automatique a pour objectif de réduire la
consommation d'eau par un arrosage optimal, diminuer les charges de personnel
et de maintenance, choisir les périodes d'arrosage sans contraintes,
limiter le ruissellement des eaux et l'érosion des sols.
14
Chapitre 2 : Étude Fonctionnelle du
Système de Gestion de l'Eau
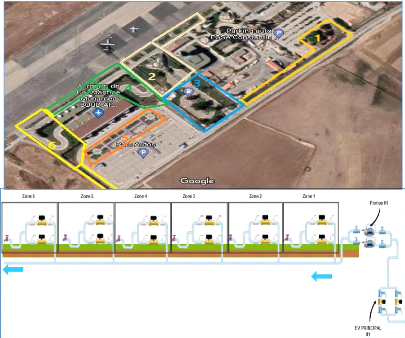
Figure 2.5 : Les zones d'irrigation
proposées
Remarques :
Le système global est basé sur la redondance
entre les équipements utilisés, dans le but d'augmenter les
performances en termes de fiabilité, disponibilité et
maintenabilité. Donc on a utilisé :
· Pour le château d'eau trois pompes de
remplissage. Dans le but de ne pas épuiser ces dernières on
procédera par combinaison lors de l'alimentation du château d'eau.
Ces combinaisons sont effectuées par rapport au niveau de château
d'eau.
· Pour les trois pompes de distribution de la
bâche à eau, la permutation entre eux se fait aussi par rapport au
niveau de réservoir.
· Les deux électrovannes placées en
parallèle aux différents points de système global ont un
fonctionnement alternatif. Elles remplissant les mêmes fonctions ou
missions, une seule suffit pour le fonctionnement normal, la deuxième
sert en cas de défaillance de la première ou dans le cas d'une
surcharge du système.
Chapitre 2 : Étude Fonctionnelle du
Système de Gestion de l'Eau
2.3. Description de la partie matérielle de la
solution proposée :
La mise en oeuvre d'un système automatisé revient
à mettre en interaction un ensemble d'éléments
organisés sous la forme d'un schéma identifiant trois parties :
partie opérative (PO), partie commande (PC) et partie pupitre ou
utilisateur (PP) du système
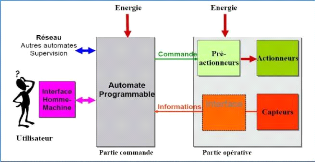
Figure 2.6 : Structure d'un système
automatisé
La partie opérative représente le sous-ensemble
qui effectue les actions physiques, mesure des grandeurs physiques et rend
compte à la partie commande. Elle comporte :
· Des capteurs qui communiquent à la partie
commande des informations sur l'état du système
· Des pré-actionneurs qui reçoivent des
ordres de la partie commande ;
· Des actionneurs (vérins, moteurs, vannes) qui
ont pour rôle d'exécuter ces ordres. 2.3.1. Les
capteurs :
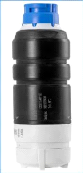
Dans notre projet, nous utilisons un certain nombre de
capteurs, que nous détaillons dans ce qui suit.
a/. Capteur de chlore (CCS51D) :
Le Memo sens CCS51D est une sonde de chlore libre robuste qui
nécessite peu d'entretien. Elle délivre des valeurs
mesurées très précises avec une stabilité à
long terme dans l'eau et assure une surveillance constante de la
désinfection, même dans de faibles volumes d'eau. La sonde de
chlore libre se caractérise par des temps de réponse
extrêmement rapides, ce qui garantit un contrôle efficace du
process. Grâce à la technologie numérique Memo sens, la
CCS51D combine intégrité maximale du process et des
données, avec un fonctionnement simple. [7]
15
Figure 2.7 : Memo sens CCS51D
Chapitre 2 : Étude Fonctionnelle du
Système de Gestion de l'Eau
b/. Capteur de niveau Radar à émission
libre (Micro pilot FMR10) :
Le radar de niveau Micro pilot FMR10 offre une mesure de
niveau continue sans contact et est idéal pour un grand nombre
d'applications dans le domaine de l'eau, des eaux usées et des
utilités industrielles. Le FMR10 fait partie des premiers radars sans
contact à technologie Bluetooth® pour une configuration et un
diagnostic d'une rare simplicité. Les courbes de signaux se visualisent
sur une application disponible pour tous les smartphones ou tablettes
Bluetooth® (iOS, Android). Grâce à un composant
électronique RF unique, le radar est très compact et s'installe
facilement dans les espaces réduits. [7]
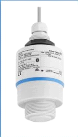
Figure 2.8 : Radar à émission
libre
c/. Capteur de pression (Cerabar PMC11) :
Le Cerabar PMC11 est un transmetteur de pression compact avec
un excellent rapport qualité/prix. Il est doté d'une cellule
capacitive céramique sans huile et permet de mesurer la pression
relative de 400 mbar à 40 bars. Le PMC11 est destiné aux
applications standards dans l'industrie et peut résister aux conditions
de process grâce à l'utilisation de matériaux de
qualité comme l'acier 316L et 99,9% Al2O3. [7]
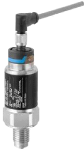
16
Figure 2.9 : Cerabar PMC11
17
Chapitre 2 : Étude Fonctionnelle du
Système de Gestion de l'Eau
d/. Débitmètres
électromagnétiques- Proline Promag W 400 :
Avec ses agréments internationaux pour les transactions
commerciales et l'eau potable, le Promag W peut être utilisé dans
les applications les plus diverses. Il est disponible en version compacte ou
séparée. Le Promag W 400 permet d'économiser du temps et
de l'argent grâce aux fonctionnalités étendues de son
transmetteur optimisé pour l'eau et les eaux usées. De plus, la
technologie Heartbeat garantit une mesure fiable et une vérification
conforme. C'est un Capteur avec protection anticorrosion EN ISO 12944 et
transmetteur de pointe pour l'eau et les eaux usées.
[7]
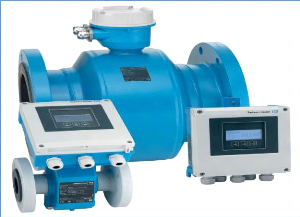
Figure 2.10 : Débitmètres
électromagnétiques
e/. Clapets à battant AVK :
Le clapet à battant est composé d'un disque qui
pivote sur une charnière ou un axe. Le disque se soulève du
siège pour permettre l'écoulement dans un sens. Lorsque la
pression diminue, le disque revient dans sa position initiale en se rabattant
sur le siège et bloque ainsi le fluide. Le poids du disque et le
débit ont un impact sur la fermeture du clapet.
Souvent un levier et un contrepoids ou un levier et un ressort
sont montés pour améliorer les performances. Les clapets
anti-retours avec levier et contrepoids conviennent aux installations
présentant un risque élevé de coup de bélier en
conditions d'écoulement normales. Les clapets anti-retours avec levier
et ressort de rappel conviennent pour les pressions élevées, les
contre-pressions insuffisantes et les vitesses d'écoulement
élevées. [8]
Chapitre 2 : Étude Fonctionnelle du
Système de Gestion de l'Eau
Nous choisissons ce clapet car il a 2 avantages principaux :
1. Le capotage est disponible avec des interrupteurs de fin de
course pour la surveillance à distance.
2. Anti-retour d'eau.
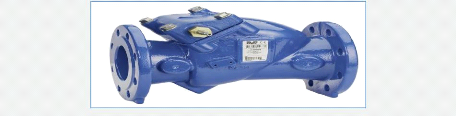
Figure 2.11: Clapet à battant AVK
f/. Capteur de niveau à flotteur Liquifloat
FTS20 :
Il s'agit d'un capteur TOR, c'est un dispositif suspendu
au-dessus d'un plan d'eau au moyen d'un câble électrique.
Lorsque le niveau de l'eau augmente jusqu'à immerger le
dispositif, sa capacité de flotter et sa forme de poire l'oblige
à se retourner mettant ainsi deux fils en contact électrique.
[7]
Les poires nécessaires pour nos projets sont au nombre de
6 :
· 2 poires de niveau (niveau bas, niveau haut) dans le
château d'eau.
· 2 poires de niveau (niveau bas, niveau haut) dans le
réservoir de 300m3 de la bâche a eau.
· 2 poires de niveau (niveau bas, niveau haut) dans le
réservoir de 200m3 de la bâche a eau.
18
Figure 2.12: Liquifloat FTS20
Chapitre 2 : Étude Fonctionnelle du
Système de Gestion de l'Eau
g/.manomètre émetteur pmp71 :
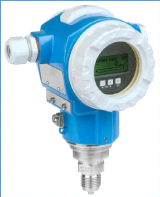
Le capteur - transmetteur de pression Cerabar PMP71 avec
membrane métallique est utilisé dans les industries de process
pour mesurer la pression, le niveau, le volume ou la masse dans les liquides ou
les gaz. Le PMP71 est conçu pour les applications haute pression
jusqu'à 700 bars. Menu Quick Setup avec gamme de mesure librement
réglable sans indication de pression. Conçu selon IEC 61508 pour
l'utilisation dans des systèmes de sécurité SIL2/3 et
disponible avec certificat MID pour les applications de transactions
commerciales. [7]
19
Figure 2.13: manomètre pmp71
h/. Capteur d'humidité du sol :
Pour minimiser le gaspillage d'eau surtout en hiver, nous
avons ajouté un capteur d'humidité du sol au réseau
d'arrosage avec une communication RS485 standard MODBUS Protocol qui facilite
la connexion avec l'API.
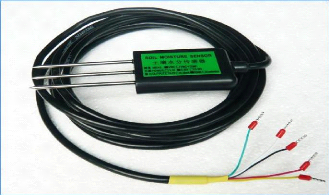
Figure 2.14: Capteur d'humidité du sol
(MODBUS Protocol)
2.3.2. Les pré actionneurs : a/. Contacteurs
:
Le contacteur est un appareil mécanique de connexion
ayant une seule position de repos et une seule position de travail. II est
capable d'établir, de supporter et d'interrompre des courants dans les
conditions normales du circuit, y compris les conditions de surcharges en
service.
20
Chapitre 2 : Étude Fonctionnelle du
Système de Gestion de l'Eau
L'intérêt du contacteur est de pouvoir être
actionnés manuellement ou automatiquement et à distance au moyen
de contacts peu encombrants et sensibles. [4] [5]
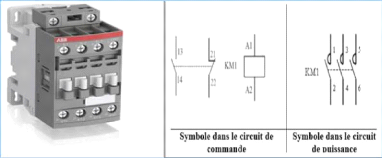
Figure 2.15 : Un contacteur
b/ Relais électromagnétique Ac/Dc 24v
(KONTRON ) :
Un relais électromagnétique, dans son principe
de commutation, s'apparente à un interrupteur mécanique dont la
manoeuvre serait non pas effectuée manuellement, mais en faisant
circuler un courant dans le circuit d'excitation du relais. Ce circuit est
constitué par une bobine appelée bobine d'excitation ou bobine de
commande.
La mise en action du relais par sa bobine de commande demande
une puissance électrique faible. Elle provoque l'ouverture ou la
fermeture d'un circuit dans lequel circule un courant élevé, et
par là même elle peut commander une puissance beaucoup plus grande
que la puissance d'excitation. [3]
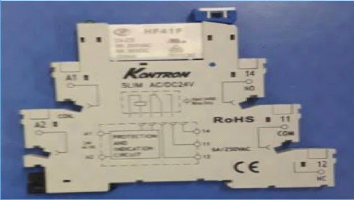
Figure 2.16 : Relais
électromagnétique KONTRON
21
Chapitre 2 : Étude Fonctionnelle du
Système de Gestion de l'Eau
c/ Disjoncteurs:
Le disjoncteur constitue l'appareil de protection par
excellence. C'est un interrupteur capable de s'ouvrir automatiquement en cas de
défaut pour couper les courants de court-circuit.
Il permet d'assurer une protection contre tous les
défauts. [4] [5]
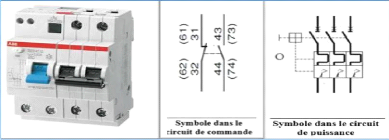
Figure 2.17 : disjoncteur :
représentation et symbole
2.3.3. Les actionneurs :
Dans un système automatisé, un actionneur est
un organe de la partie opérative qui a un ordre de la partie commande
via le pré-actionneur, convertit l'énergie qui lui est fournie
sous une forme utile pour les taches de programme dans un système
automatisé.
a/. Les pompes :
Une pompe est une machine hydraulique qui aspire et refoule
un liquide (eau, huile, Essence...) d'un point à un endroit voulu. Une
pompe est destinée à élever la charge de liquide
pompé. Pour remplir notre château d'eau et la Bâche à
eau on utilise le même type de pompe déjà existé qui
est la pompe centrifugeuse. Elles agissent sur l'énergie
cinétique et le mouvement du liquide résulte de l'augmentation
d'énergie qui est communiquée par la force centrifuge.
Une pompe centrifuge est constituée essentiellement de
:
· Une roue à aubes tournant autour de son axe,
· Un distributeur dans l'axe de la roue
· Un collecteur de section croissant, en forme de spirale
appelé volute.
Tous ces composants sont enveloppés dans un corps qui
est accouplé avec un moteur asynchrone qui fournit l'énergie
cinétique nécessaire pour la rotation de la roue à aubes
de la pompe. [6]
22
Chapitre 2 : Étude Fonctionnelle du
Système de Gestion de l'Eau
Pour ce projet, on utilise trois pompes de 3.5kw pour le
remplissage du château d'eau, trois autres de 3.5kw pour la distribution
de la bâche a eau, deux de 5.5kw pour le réseau d'irrigation et
les deux déjà existantes pour le réseau anti-incendie.
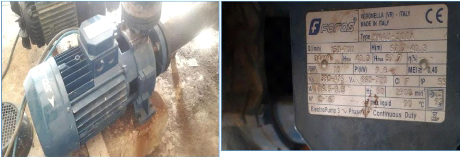
Figure 2.18 : Pompe centrifuge
b/. Les Vannes :
Une vanne est un dispositif destiné à
contrôler le débit de l'eau dans une canalisation. Elle est
utilisée pour arrêter ou pour faire circuler l'eau dans les
conduites. On distingue 2 types de vannes : les vannes électriques et
les vannes manuelles.
? Vannes électriques :
Comme vanne électrique, on peut citer la vanne
motorisée. La commande de cette vanne se fait par un API. Elle est
constituée d'un corps de vanne, d'un volant de commande manuelle et d'un
moteur réducteur alimenté en 380V comportant un limiteur d'effort
d'ouverture et de fermeture. L'ouverture ou la fermeture de la vanne est
effectuée grâce à l'entrainement de la tige de l'opercule
ou papillon par le moteur électrique (asynchrone triphasé
démarrage direct 2 sens de rotation).
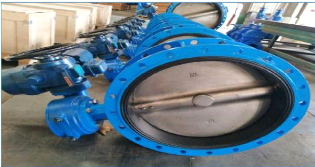
Figure 2.19 : Exemple de Vannes
électriques
Chapitre 2 : Étude Fonctionnelle du
Système de Gestion de l'Eau
? Vannes manuelles :
On les désigne comme vannes manuelles car leur commande
s'effectue manuellement. On distingue deux types : les vannes avec bras et les
vannes avec robinet. [6]
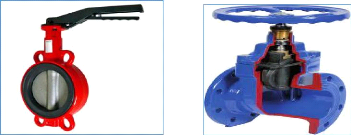
23
Figure 2.20 : Vannes avec bras Figure
2.21 : Vannes avec robinet.
2.3.4. L'automate programmable industriel (API):
Un automate programmable industriel, ou API, est un
dispositif électronique programmable destiné à la commande
de processus industriels. Il envoie les ordres vers les prés actionneurs
à partir de données d'entrées (partie commande ou PC
côté capteur), de consignes et d'un programme informatique.
[09]
Un API peut être compacte ou modulaire :
· L'API compacte ou monobloc possède un nombre
d'entrées et de sorties restreint et son jeu d'instructions ne peut
être augmenté. Ce type a pour fonction de résoudre des
automatismes simples avec la logique séquentielle et utilisant des
informations TOR.
· L'API modulaire est adaptable à toutes
situations. Selon le besoin, des modules d'E/S analogiques sont disponibles en
plus de modules spécialisés. La modularité permet un
dépannage rapide et une plus grande flexibilité.
D'après le cahier de charge qui nous a
été établi, le choix de l'automate doit se faire en tenant
compte des critères suivants :
Ø Les nombres et la nature d'entrées/sorties.
Ø Le type du processeur et sa capacité de
traitement.
Ø La nature de traitement souhaité (temporisation,
comptage régulation...etc).
Ø La communication avec d'autres automates.
Ø Le dialogue (la console programmation, pupitre,
écran de supervision).
Ø La fiabilité et la durée de la
garantie.
Ø Le coût de l'automate.
Ø La qualité du service après-vente.
24
Chapitre 2 : Étude Fonctionnelle du
Système de Gestion de l'Eau
Pour notre projet, l'automate le mieux adapté à
notre problématique et qui représente le meilleur choix c'est
l'automate modulaire de la famille S7-1200.
2.3.5 Les autres équipements
a/ Alimentation de type Schneider (ABL8REM24050) :
C'est une alimentation en mode commutation
régulé c'est-à-dire une alimentation électrique
dont la régulation est assurée par des composants
électroniques de puissance utilisés en commutation.
L'influence de la température ambiante joue un
rôle déterminant dans la limitation de la puissance qu'une
alimentation électronique peut délivrer en permanence. Si les
composants électroniques sont dans un environnement où la
température ambiante est trop élevée, leur durée de
vie sera considérablement réduite.
La gamme Optimum des alimentations Phaseo est
conçue pour fonctionner à une température ambiante
nominale de 50 °C. Au-delà, il est nécessaire de recourir
à une réduction de charge jusqu'à une température
maximale de 60 °C.
La réduction de charge doit être prise en compte
dans des conditions de fonctionnement extrêmes, telles que :
· Fonctionnement intensif (courant de sortie proche en
permanence du courant nominal, avec une température ambiante
élevée)
· Tension de sortie définie comme
supérieure à 24 VCC (pour compenser les chutes de tension en
ligne, par exemple)
· Raccordement parallèle pour augmenter la
puissance totale. [2]
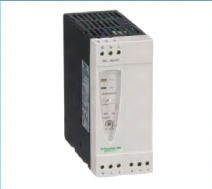
Figure 2.22: Power Supply Schneider
25
Chapitre 2 : Étude Fonctionnelle du
Système de Gestion de l'Eau
b/ Réservoir à vessie :
Le réservoir à vessie permet d'accumuler l'eau
sous pression. Il est idéalement utilisé pour réduire le
nombre de démarrages d'une pompe, ce qui augmente la durée de vie
de celle-ci. Pour notre projet, on a utilisé :
· Deux réservoirs à vessie pour la Station de
surpression eau incendie.
· Un réservoir à vessie pour les deux pompes
d'arrosage.
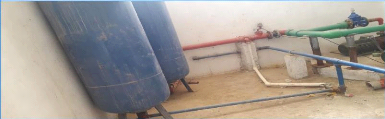
Figure 2.23 : Réservoir à
vessie
c/. Afficheur RIA15 :
L'afficheur de process est disponible en 4 à 20 mA ou
protocole HART®. La version HART® permet de visualiser en alternance
jusqu'à 4 valeurs mesurées d'un capteur sur le terrain ou en
façade d'armoire.
Pour cela, l'afficheur peut être réglé
comme maître HART® primaire ou secondaire et interroge activement
les valeurs du capteur. La faible chute de tension de < 1 V (< 1,9 V avec
HART®) est un avantage considérable, notamment dans les
applications Ex dans lesquelles seule une faible tension est disponible dans la
plupart des cas. [7]
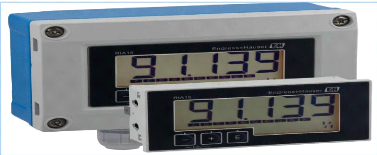
Figure 2.24: Afficheur RIA15
26
Chapitre 2 : Étude Fonctionnelle du
Système de Gestion de l'Eau
d/ Groupe électrogène :
Un groupe électrogène est un dispositif autonome
capable de produire de l'électricité en cas de coupure de
l'alimentation du réseau électrique. Il ne nécessite qu'un
approvisionnement en carburant. L'électricité est toujours
produite par une génératrice (dynamo qui produit un courant
continu, ou alternateur qui produit un courant alternatif). Cette
génératrice doit recevoir un mouvement rotatif produit par un
moteur thermique essence, GPL ou diesel, équipé d'un
régulateur mécanique modulant sa vitesse de rotation en fonction
de la charge. [6]
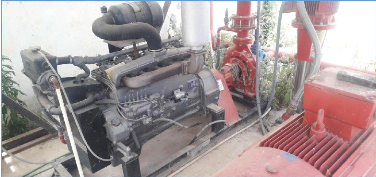
Figure 2.25: Groupe Electrogène
e/ Clapet anti-retour:
Un clapet anti-retour est un dispositif (une vanne) permettant
de contrôler le sens d'un fluide dans une tuyauterie. Il instaure donc un
sens unique de circulation pour un liquide ou un gaz : ils peuvent
s'écouler vers l'aval, mais le clapet évite les remontées
en amont.[1] On va utiliser juste un clapet donne le canal
d'anti-incendie de bâche a eau.
Chapitre 3 :
Description de la plateforme de
développement
28
Chapitre 3 : Description de la plateforme de
développement
3.1 Introduction :
Dans ce chapitre nous allons détailler la partie
commande et les outils nécessaires pour la réalisation de ce
travail. En premier lieu nous présenterons l'automate et ses outils,
ensuite on abordera la partie télégestion et ses outils et en
dernier on abordera les outils de communication. On utilise un automate
programmable pour la gestion automatique du système. On l'associe
à un système SCADA pour contrôler le processus en prenant
en charge les fonctions d'acquisition et d'archivage de données,
l'interface homme-machine, la surveillance et la gestion des alarmes.
SCADA est l'acronyme désignant Supervisory
Control And Data Acquisition ou Système de Contrôle et
d'Acquisition de Données. En réalité, il fait
référence à une catégorie de logiciels
dédiés au contrôle des processus industriels et à la
collecte de données en temps réel dans des sites distants.
Il est généralement fourni sous forme de
logiciel combiné à des éléments matériels,
tels que des émetteurs, une unité de télégestion
(Remote Terminal Unit-RTU), de protocoles de communication permettant la
communication entre les serveurs et les émetteurs RTU, de serveur de
données destiné à l'archivage des données et
à alimenter les interfaces homme-machines (IHM).
La Figure suivante représente le schéma
synoptique d'un système automatisé SCADA
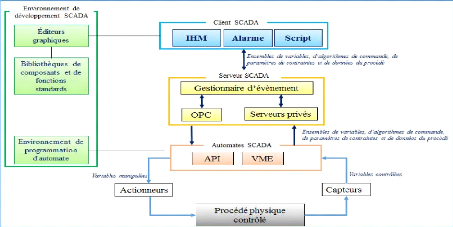
Figure 3.1 : Structure d'un système
automatisé SCADA
29
Chapitre 3 : Description de la plateforme de
développement
3.2 L'Automate S7-1200 :
L'automate SIMATIC S7-1200 est un mini-contrôleur
modulaire. Il existe un éventail complet de modules pour une adaptation
optimisée à la tâche d'automatisation. Le contrôleur
S7 est composé d'une CPU équipée d'entrées et de
sorties de signaux numériques et analogiques. Des modules additionnels
d'entrées/sorties (modules IO) peuvent être installés si
les entrées et sorties intégrées ne sont pas suffisantes.
Si besoin est, des modules de communication RS232 ou RS485 peuvent
également être ajoutés. Une interface TCP/IP
intégrée est obligatoire pour toutes les CPU. Avec le programme
S7, l'API surveille et contrôle une machine ou un process. Les modules IO
sont interrogés dans le programme S7 au moyen d'adresses
d'entrées (%I) et référencés au moyen d'adresses de
sorties (%Q). [11]
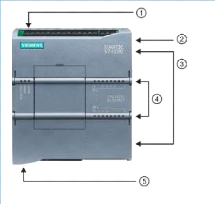
Figure 3.2: Automate S7-1212c (DC/DC/DC).
1. Prise d'alimentation.
2. Logement pour carte mémoire sous le volet
supérieur.
3. Connecteurs amovibles pour le câblage utilisateur
(derrière les volets).
4. DEL d'état pour les E/S intégrées.
5. Connecteur PROFINET (sur la face inférieure de la
CPU).
Des modules supplémentaires peuvent être
utilisés pour communiquer par le biais de réseaux et de
protocoles tels que : PROFIBUS, GPRS, WAN, RS485, RS232, USS, MODBUS.
Dans notre cas, nous avons utilisé 4 automates siemens
S7-1212C DC/DC/DC avec les Caractéristiques reportées dans le
tableau suivant :
30
Chapitre 3 : Description de la plateforme de
développement
·
·
|
CPU
Version du firmware
|
S7 1212 C DC/DC/DC. V 4.4
|
·
|
Pack de programmation
|
À partir de STEP 7 V16
|
·
|
Valeur nominale (CC)
|
24 V
|
·
|
Mémoire
|
|
|
Mémoire de travail
|
75 k byte
|
·
|
Temps de traitement CPU
|
|
|
Pour opérations sur bits
|
0,08 us
|
|
Pour opérations sur mots
|
1,7 us
|
·
|
Entrées TOR
|
|
|
Nombre d'entrées TOR
|
8
|
·
|
Sorties TOR
|
|
|
Nombre de sorties TOR
|
6
|
·
|
Entrées analogiques
|
|
|
Nombre d'entrées ANALOGIQUE
|
2
|
·
|
Sorties analogiques
|
|
|
Nombre de sorties ANALOGIQUE
|
0
|
·
|
Capteurs
|
|
|
Détecteur 2 fils
|
oui
|
·
|
Interface
|
|
|
Type d'interface
|
PROFINET
|
·
|
Réalisation physique de l'interface
|
|
|
RJ 45(Ethernet)
|
Oui
|
|
Nombre de ports
|
1
|
|
Commutateur intégré
|
Non
|
·
|
Protocoles (ETHERNET)
|
|
|
Supporte le protocole pour PROFINET IO
|
Oui
|
|
PROFIBUS
|
1242-5
|
|
AS-Interface
|
Oui
|
31
Chapitre 3 : Description de la plateforme de
développement
3.3 Les modules entrées/sorties :
Dans notre projet nous avons utilisé plusieurs types de
modules d'entrées sorties. Le tableau suivant résume
l'affectation des modules E/S pour 3 des 4 automates utilisés.
L'affectation pour l'automate utilisé pour le système
d'irrigation sera détaillé dans la suite.
Système
|
Modules
|
Le Château d'eau
|
DI 16/DQ 16x24VDC_1 AI 4x13BIT 1
|
Bâche a eau
|
DI 16/DQ 16x24VDC_1 AI 4x13BIT 1
|
Système Anti Incendie
|
DQ 8x24VDC _1
|
3.3.1 Le Château d'eau et la Bâche a eau :
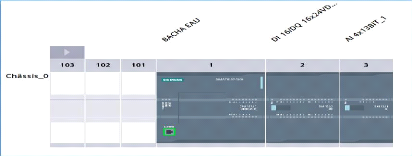
Figure 3.3: Automate S7-1212c et le module
utilisé pour le système de bâche a eau.
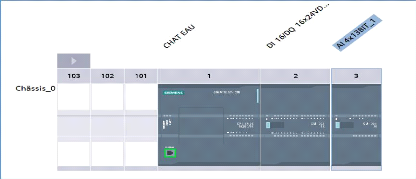
Figure 3.4: Automate S7-1212c et le module
utilisé pour le système de château d'eau.
32
Chapitre 3 : Description de la plateforme de
développement
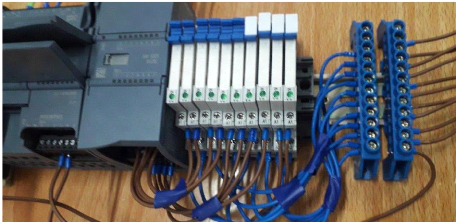
Figure 3.5: Automate S7-1212c et le module
utilisé pour la réalisation du système de château
d'eau.
A/ Module DI 16/DQ 16x24VDC1 : (Module d'entrées
TOR)
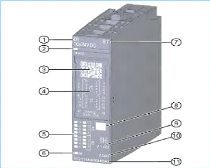
Figure 3.6: Module DI 16/DQ 16x24VDC_1
1) Type et désignation du module.
2) LED pour le diagnostic.
3) Code de matrice 2D.
4) Raccordement.
5) LED pour l'état de la voie.
6) LED pour la tension d'alimentation.
7) Classe de fonction.
8) Repérage couleur type de module.
9) Version des fonctions et du firmware.
10) Code couleur permettant de sélectionner les
étiquettes de repérage couleur.
33
Chapitre 3 : Description de la plateforme de
développement
11) Numéro d'article. [13]
Caractéristiques du module :
l Module d'entrées TOR à 16 entrées
l Sink Input, (PNP, type P)
l Tension d'alimentation L+
l Retard à l'entrée paramétrable 0,05 ms
à 20 ms (par voie)
l Diagnostic paramétrable (par module)
l Convient au raccordement de commutateurs et de capteurs 2 fils
selon CEI 61131, type 3 Le module prend en charge les fonctions suivantes :
l Mise à jour du firmware
l Données d'identification I&M
l Re paramétrage en RUN B/ Module AI 4x13BIT1
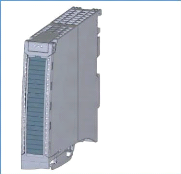
Figure 3.7: Module AI 4x13BIT_1
Le module possède les caractéristiques techniques
suivantes :
l 4 entrées analogiques.
l Résolution 16 bits signe compris.
l Type de mesure tension réglable pour chaque voie.
l Type de mesure courant réglable pour chaque voie.
l Type de mesure Résistance réglable pour les
voies 0 et 2.
l Type de mesure Thermomètre à résistance
(RTD) réglable pour les voies 0 et 2.
l Type de mesure thermocouple (TC) réglable pour chaque
voie.
l Diagnostic paramétrable (par voie).
34
Chapitre 3 : Description de la plateforme de
développement
l Alarme de processus en cas de dépassement de la valeur
limite réglable pour chaque voie (deux limites supérieures et
deux limites inférieures pour chacune d'elles). [14]
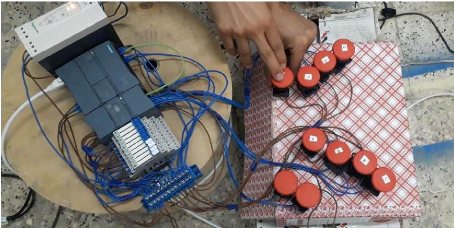
Figure 3.8: Automate S7-1212c et le module
utilisé pour la réalisation du système de château
d'eau.
3.3.2 Système anti incendie :
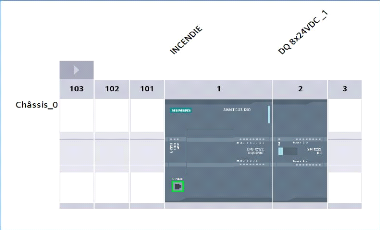
Figure 3.9: Automate S7-1212c et le module
utilisé pour le système Anti-incendie
35
Chapitre 3 : Description de la plateforme de
développement
A/ Module DO 8x24VDC :
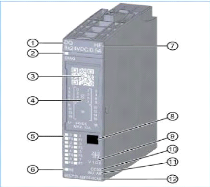
Figure 3.10: Module DQ 8x24VDC
1) Type et désignation du module.
2) LED pour le diagnostic.
3) Code de matrice 2D.
4) Raccordement.
5) LED pour l'état de la voie.
6) LED pour la tension d'alimentation.
7) Classe de fonction.
8) Repérage couleur type de module.
9) Version des fonctions et du firmware.
10) Code couleur permettant de sélectionner les
étiquettes de repérage couleur.
11) Type de BU.
12) Numéro d'article. [15]
3.3.3 Le Système d'irrigation :
La notion d'arrosage automatique désigne les
systèmes permettant de fournir de l'eau à
des plantes durant un certain temps sans intervention humaine.
Les étapes que nous avons suivies pour réaliser ce
projet :
- Etude de l'espace concerné par l'arrosage.
- Définition du matériel.
- Analyse du type d'automate qui convient le mieux.
- Architecturer de notre projet.
- Architecturer de programme.
36
Chapitre 3 : Description de la plateforme de
développement
Pour bien faire ce projet et le réaliser correctement,
on a demandé l'aide d'un ouvrier ayant de l'ancienneté dans le
domaine de l'irrigation au niveau de l'aéroport. Ce dernier nous a
donné toutes les informations et éclaircissements concernant les
plantes et les espaces verts devant être arrosés. Dans la solution
que nous avons retenue, les espaces devant être irrigués sont
divisés en six zones comme indiqué sur la figure suivante.
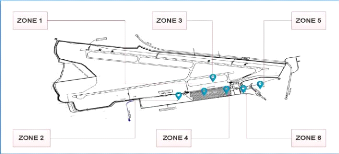
Figure 3.11 : les zones concernées par
l'arrosage
Pour la réalisation du système de commande de cette
partie, on a utilisé le matériel suivant :
1. Un disjoncteur différentiel (pour la protection des
biens).
2. Une alimentation Schneider.
3. Un automate S7 1212c DC/DC/DC.
4. Un module d'entrée/sortie 8DO 8DI.
5. Des relais (comme sortie).
6. Des fils électriques (bleu pour le neutre, marron pour
la phase, vert pour la terre).
7. Des boutons poussoirs NO (comme des entrées d'un
pupitre).
8. Un câble RJ45 (pour la communication).
9. Un répartiteur.
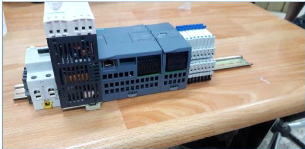
Figure 3.12: le matériel utilisé
pour le système d'irrigation
37
Chapitre 3 : Description de la plateforme de
développement
L'automate S7 1212c DC/DC/DC offre des caractéristiques
suffisantes pour la gestion des taches relatives à ce système
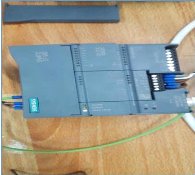
Figure 3.13: Automate S7 1212c
Module 223-1BH32-0XB0
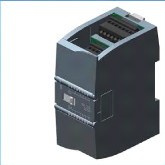
Figure 3.14: Module
d'entrées/sorties
- Tension d'alimentation : Valeur nominale (CC) 24 V. -
Entrées TOR : Nombre d'entrées TOR 8.
- Tension d'entrée : Type de tension d'entrée
CC.
l Valeur nominale (CC) 24 V.
- Sorties TOR : Nombre de sorties TOR 8.
- Alarmes : Alarme de diagnostic Oui.
La figure suivante représente la réalisation du
système après le câblage :
38
Chapitre 3 : Description de la plateforme de
développement
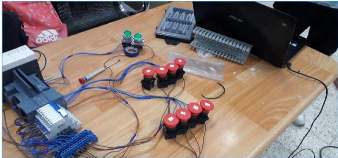
Figure 3.15: le système
réalisé
3.4 Partie communication :
Un protocole de communication est une spécification de
plusieurs règles pour un type de communication particulier.
Initialement, on nommait protocole, ce qui est utilisé pour communiquer
sur une même couche d'abstraction entre deux équipements
différents. Par extension de langage, on utilise parfois ce mot, pour
désigner les règles de communication entre deux couches sur un
même équipement.
Pour notre projet, il a fallu tenir compte du problème
de la distance entre les armoires des différentes parties et la salle de
contrôle. Nous avons alors choisi d'utiliser :
Ø Un réseau industriel ETHERNET.
Ø Un Protocole de communication PROFINET.
Ø Un switch CET2-0800 Series (utilisable
pour la technologie fibre optique). 3.4.1 Le réseau
industriel Ethernet :
Ethernet est basé sur le principe d'accès au
media régit par un mécanisme de détection de collision.
Chaque station est identifiée par une clé globalement unique,
appelée adresse MAC, afin de s'assurer que tous les postes sur un
réseau Ethernet aient des adresses distinctes. Cette technologie connue
sous le nom de (Carrier Sense Multiple Access with Collision Detection)
Détection de porteuse avec accès multiples et détection de
collision ou CSMA/CD garantit qu'une seule station à la fois transmet un
message sur le media. Les évolutions successives d'Ethernet ont
donné naissance au standard IEEE 802.3, Il définit seulement les
caractéristiques des couches physiques, la façon dont les
informations accèdent au réseau (ainsi que la trame de
donnée doivent être définies par des couches
complémentaires).
L'Ethernet industriel dispose également de
sérieux atouts en comparaison avec les autres technologies de
réseau industriel :
39
Chapitre 3 : Description de la plateforme de
développement
? 1) L'Ethernet industriel se base sur des vitesses allant de
100Mb/s jusqu'à 10Gb/s. Un atout pour les applications exigeantes en
temps de réponse.
? 2) Avec Ethernet, le média n'est pas partagé,
une anomalie n'affectera que la station concernée par le lien. Les
technologies comme RSTP, HSP/PRP, ou comme le TURBO RING de MOXA ou le
X-RING d'Advantech permettent d'assurer le fonctionnement même
après la coupure d'une connexion.
? 3) Ethernet s'avère plus robuste qu'un bus de
terrain par rapport aux perturbations électromagnétiques, et
répondent entièrement à ces problématiques.
? 4) Grâce à Ethernet, il est possible de
connecter sur un même réseau par exemple des stations PROFINET et
MODBUS-TCP.
? 5) La technologie Ethernet permet d'accéder beaucoup
plus facilement à l'appareil même à distance, que s'il se
trouvait sur un bus série. [16]
3.4.2 Le protocole de communication PROFINET :
PROFINET (Process Field Network) est une norme de
communication basée sur Ethernet industriel offrant une vaste gamme
d'applications. Le bus de terrain qui utilise le protocole TCP/IP et les normes
de technologie de l'information, permet un traitement en temps réel et
l'intégration de systèmes de bus de terrain. PROFINET a
été développé par Siemens et les entreprises
membres de l'organisation d'utilisateurs de PROFIBUS (PNO) et est
utilisé en association avec les systèmes de commande Siemens.
Il permet une automatisation en temps réel ainsi qu'une
intégration informatique avec un seul système. L'architecture
ouverte de PROFINET permet en outre une intégration simple et fluide des
solutions de bus de terrain établies, par exemple en utilisant des
proxys ou des passerelles. De plus, PROFINET offre des concepts de diagnostic
intelligents pour les appareils de terrain et les réseaux.
Grâce à la structure modulaire, les utilisateurs
peuvent sélectionner de manière parfaitement individuelle un pack
PROFINET (profil d'application) adapté et l'implémenter dans leur
installation.
Pour l'échange de données entre les participants
du réseau, PROFINET prend en charge le principe du Provider
(émetteur) et du Consumer (destinataire). Cela signifie qu'aussi bien le
contrôleur que l'appareil de terrain (IO-Device) transmettent
automatiquement les données cycliques par eux-mêmes dès
qu'ils doivent le faire en raison d'un défaut ou d'une requête. Il
existe en outre la possibilité d'une requête programmée,
c'est-à-dire que les données soient envoyées
automatiquement. Afin de respecter les exigences élevées en temps
réel, la
40
Chapitre 3 : Description de la plateforme de
développement
communication avec PROFINET est évolutive grâce
à trois niveaux de performance dont chacun est basé sur le
précédent :
? La transmission de données d'ingénierie et non
sensibles à la latence s'effectue via TCP/IP. Cette communication
standard est possible entre tous les automates.
? Pour la transmission de données de process, le canal
temps réel (RT) est disponible. ? Pour les applications
synchronisées telles que la commande de mouvement (Motion
Control), on utilise la communication temps réel
isochrone (IRT) qui permet une
meilleure précision.
Enfin, PROFINET offre une topologie de réseau flexible
afin d'apporter une réponse optimale aux exigences en matière
d'étendue géographique et de disponibilité et s'adapte
ainsi aisément aux spécificités des installations.
À cet effet, le protocole prend en charge :
? La topologie en ligne ou en bus qui relie principalement les
équipements terminaux aux commutateurs intégrés sur le
terrain
? La topologie en étoile avec un commutateur central,
principalement installée en armoire ? La topologie en anneau,
principalement pour la réalisation de la redondance des médias ?
La topologie en arbre mélangeant les topologies ci-dessus.
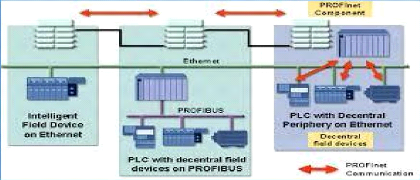
Figure 3.16: Structure représentative
du Protocole PROFINET
L'interconnexion d'appareils PROFINET dans des installations
industrielles est possible par manières différentes.
? Sur fil : via un conducteur électrique ou via un
câble à fibres optiques
? Sans fil via l'interface sans fil par ondes
électromagnétiques
Pour une connexion électrique, une longueur maximale de
100 m entre deux appareils est admissible par contre lorsque la distance entre
l'automate et ses équipements est supérieure à cette
distance une connexion optique est recommandée. [16]
41
Chapitre 3 : Description de la plateforme de
développement
Pour recréer les signaux reçus et les distribuer
on utilise un commutateur. Il apprend l'adresse Ethernet d'un appareil PROFINET
connecté ou d'un autre commutateur et transmet les signaux qui sont
destinés à l'appareil PROFINET ou au commutateur. Il existe un
switch qui s'appelle `CET2-0800 Series' qui ne coûte pas
cher et qui est très utile pour les industries.
3.4.3 Leonton CET2-0800 Series :
Commutateur Ethernet industriel à 8 ports avec les
caractéristiques suivantes :
? Ethernet rapide 10/100Base-T(X) à 8 ports.
? Conception d'entrée d'alimentation redondante,
12-48VDC
? Conception de boîtier métallique robuste IP30
? Plage de température de fonctionnement, STD : -10°C
~ 65°C, EOT : -40°C ~ 75°C
? Normes Ethernet : IEEE 802.3 10Base-T
l IEEE 802.3u 100Base-TX Fast Ethernet.
? Type de traitement : Store and Forward.
? Protocole : CSMA/CD.
? Mémoire Tampon : 448Kbits.
? RJ45 Ports : 8*10/100 Base-T(X).
? Contact relais : 24 VDC, 1A résistif.
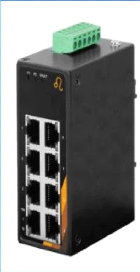
Figure 3.17: Leonton CET2-0800
42
Chapitre 3 : Description de la plateforme de
développement
3.5 Les logiciels :
3.5.1 SIMATIC TIAPORTAL V16 :
TIAPORTAL est l'un des logiciels de programmation
évolués qui permet de programmer des automates Siemens. Cette
plate-forme regroupe différents dispositifs de programmation : SIMATIC
STEP 7, SIMATIC WinCC, SINAMICS Startdrive, SIMOCODE ES.
Outre les fonctionnalités de travail collaboratif, TIA
Portal V16 intègre une nouvelle interface de contrôle pour les
systèmes de contrôle de version externes tels que GIT, SVN
et TFS.
Une autre innovation est la fonctionnalité
dénommée TIA Portal Test Suite. Celle-ci permet la
création et la vérification automatisées du respect des
instructions de programmation, appelées Styleguide Check.
Il est également possible de générer et de
réaliser des tests de programme avec le contrôleur virtuel
S7-PLCSIM Advanced. Cela permet ainsi de réduire les temps
d'ingénierie et de mise en service tout en améliorant la
qualité du programme.
Avec TIAPortal V16, tous les automates Simatic S7-1200 sont
équipés des fonctionnalités du serveur OPC UA.
Les communications entre contrôleurs Siemens sont
désormais facilitées grâce au standard OPC UA, et il est
possible de créer une interface de serveur OPC UA. Aussi la
remontée de variables issues des données de production est
désormais plus fluide. [17]
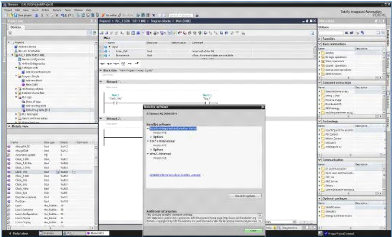
Figure 3.18: Tia Portal V16.
3.5.2 SIMATIC WinCC:
SIMATIC WinCC est un logiciel de contrôle et
d'acquisition de données (SCADA) ainsi qu'une interface homme-machine
développé par Siemens. Les SCADA sont particulièrement
utilisés dans la surveillance des processus industriels et des
infrastructures.
43
Chapitre 3 : Description de la plateforme de
développement
SIMATIC WinCC flexible est le fruit d'un perfectionnement
systématique des logiciels d'interface homme-machine.
Le WinCC offre, pour les applications au niveau machine (couvert
jusqu'à présent par la famille ProTool), un considérable
gain d'efficacité dans la configuration ainsi que des concepts
d'automatisation innovateurs. Il permet entre autres de :
? Réaliser des concepts d'HMI et d'automatisation
innovants dans le cadre de réseaux TCP/IP et Web.
? Accroître la disponibilité des machines et
installations par de nouveaux concepts de maintenance.
? Accéder facilement, en toute sécurité aux
données de process à partir de n'importe quel endroit.
Caractéristiques techniques :
? Intégration dans les automates programmables.
? Editeurs de tableau.
? Gestion de données orientée objet avec
possibilités d'édition et de recherche
? Bibliothèques d'objets de configuration
prédéfinis ou confectionnés par l'utilisateur.
? Prise en charge linguistique.
? Visual Basic Script Support.
? Runtime.
? Test et assistance à la mise en service.
? Communication ouverte entre systèmes HMI et
systèmes de niveau supérieur.
Avantages :
? La cohérence du logiciel de configuration assure une
réduction des coûts de formation,
de maintenance et d'entretien tout en étant une garantie
d'évolutivité du produit
? Minimisation des coûts d'ingénierie
? Outils intelligents pour une configuration simple et
efficace.
? Prise en charge exhaustive de configurations multilingues pour
une mise en oeuvre
globale
? Rapport performances/prix optimisé
? Fonctionnalité de runtime flexible grâce à
des scripts Visual Basic
? Des concepts de maintenance innovateurs avec commande à
distance, le diagnostic,
l'administration via intranet/Internet et la communication par
courrier électronique
améliorent la disponibilité
44
Chapitre 3 : Description de la plateforme de
développement
? Prise en charge de solutions d'automatisation
distribuées simples sur la base de réseaux TCP/IP au niveau
machine [18]
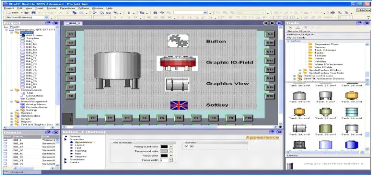
Figure 3.19: Exemple de réalisation
d'une HMI
WinCC (TIA Portal) est un logiciel d'ingénierie pour la
configuration de SIMATIC Panels, de PC industriels SIMATIC et de PC standard
avec le logiciel de visualisation WinCC Runtime Advanced ou avec le
système SCADA WinCC Runtime Professional. WinCC est disponible en quatre
versions, selon les systèmes de conduite configurables :
Ø WinCC Basic.
Ø WinCC Comfort
Ø WinCC Advanced
Ø WinCC Professional
Pour notre projet et pour la surveillance et la supervision de
notre système, nous avons utilisé un système basé
sur PC standard avec le logiciel de visualisation WinCC Runtime Advanced.
3.5.3 SIMATIC STEP 7
A) Fonctionnalités :
STEP 7 Professional fédère toutes les fonctions
requises pour concevoir, configurer, programmer, tester, mettre en service et
maintenir les systèmes d'automatisation. Il permet de concrétiser
tous les atouts du concept "Totally Integrated Automation" :
? Interface utilisateur orientée objet,
commune à tous les outils logiciels SIMATIC Industriel Software
? Base de données unique des projets
garantissant la cohérence des applications même complexes
? Cohérence des réseaux de
communication entre les composants d'une application
45
Chapitre 3 : Description de la plateforme de
développement
STEP 7 Professional intègre en particulier les outils
suivants :
? Interface utilisateur SIMATIC Manager commune à tous les
outils logiciels intégrés et
optionnels
? Tous les langages de programmation pour automates programmables
définis dans le
standard CEI 61131-3 : schémas contact, logigrammes,
listes d'instructions, graphes
séquentiels (S7-GRAPH) et langages structuré
(S7-SCL)
? Le logiciel de simulation automate S7-PLCSIM pour la mise au
point de programmes
sans disposer d'automates cible
? Outil configuration graphique des composants matériels
et des réseaux de
communication
STEP 7 Professional comporte de nombreuses fonctions
évoluées comme par exemple :
? Programmation structurée, avec des blocs fonctions
paramétrables et instanciables
? Vérification globale de la cohérence d'un
programme
? Gestion multilingue de projet
? Interfaces d'import/export de code source des programmes, de la
liste des noms
symboliques de variables, de configurations matérielles
? Modèle objet STEP 7 pour réalisation de scripts
destinés à "automatiser le travail de
l'automaticien» [18].
B) Avantages :
STEP 7 Professional permet d'obtenir des gains de
productivité importants de l'ingénierie
durant toutes les phases d'un projet d'automatisation :
? Configuration plus rapide des systèmes grâce
à des outils de configuration graphiques
des composants et des réseaux
? Programmation plus efficace grâce à la
possibilité de combiner dans des projets
structurés, orientés objet, tous les langages de
programmation standard selon CEI 61131-
3
? Phases de test plus courtes grâce aux outils de
simulation et de mise au point intégrés
? Temps d'arrêts fortement réduits grâce
à des moyens puissants de diagnostic de pannes
et de maintenance à distance
46
Chapitre 3 : Description de la plateforme de
développement
3.5.4 EPLAN Electric P8 :
EPLAN Electric P8 est un système d'ingénierie
intégré et rapide qui permet de planifier et de concevoir des
plans d'ingénierie électrique pour les machines et les
installations. Le logiciel prend en charge une grande variété de
méthodes d'ingénierie ; de la création manuelle aux
approches standardisées et basées sur des modèles.
Les données du projet, une fois entrées dans le
schéma, deviennent la base de l'achèvement automatisé de
la documentation des machines et des systèmes d'installation.
[19]
Chapitre 4 :
Programmation et Supervision
48
Chapitre 4 : Programmation et Supervision
4.1 Introduction :
Dans ce chapitre, nous allons détailler les
différentes étapes de la réalisation de l'aspect logiciel
de la solution proposée dans le chapitre 2. Pour cela, on
présentera les parties programmation et supervision
résumées aux points suivants :
1. L'élaboration des organigrammes de fonctionnement pour
les différents systèmes présentés dans ce
mémoire.
2. La configuration de logicielle TIA PORTAL de l'automate
S7-1200.
3. La programmation.
4. La réalisation d'un système de supervision
basé sur une IHM de contrôle et de commande. 4.2 Les
modes de fonctionnement :
On a défini deux modes de fonctionnement possible pour le
système :
V' Le mode manuel.
V' Le mode automatique.
Pour le changement entre les deux modes de fonctionnement on a
ajouté un commutateur
(Auto/Man) dans l'interface homme machine (HMI).
Pour le choix de la commande, il se fait par un commutateur
(Remote/ Local) c'est-à-dire que
la commande se fait soit à partir de l'armoire ou à
distance.
La figure suivante représente un organigramme simple pour
le choix du mode du
fonctionnement :
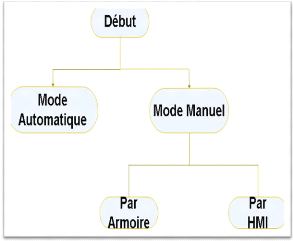
Figure 4.1: Organigramme pour le choix du mode
de fonctionnement
49
Chapitre 4 : Programmation et Supervision
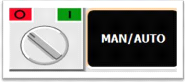
Figure 4.2: Commutateur de sélection du
mode de fonctionnement
4.2.1 Organigramme général du choix du
mode de commande :
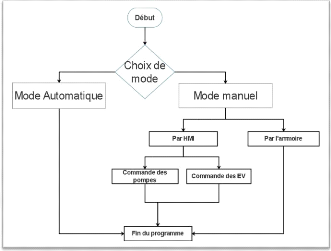
Figure 4.3 : Organigramme général
du mode de commande
4.2.2 Le mode manuel :
Ce mode est sélectionné lorsque les commutateurs
Manu / Auto est sur la position Manuel, puis on choisit entre le type de
contrôle choisi : soit à distance HMI (Remote) ou bien en local
à partir de l'armoire de commande.
Dans le mode manuel, tout le système est sous le
contrôle de l'opérateur qui peut commander le démarrage,
l'arrêt ou l'effacement des défauts de n'importe quelle pompe ou
électrovanne et cela depuis les armoires de commande. Ce mode n'est
choisi que pour :
· Des opérations de maintenance.
· Des réglages internes.
· Des tests.
· Ou en cas de défaillance sur l'automate de
télégestion.
50
Chapitre 4 : Programmation et Supervision
Dans ce mode, aucune tâche n'est assurée par
l'automate de télégestion, tous les événements de
fonctionnement y compris les défauts et les alarmes seront
détectés par l'automate de télégestion, enregistres
dans sa mémoire et envoyés vers le poste de supervision.
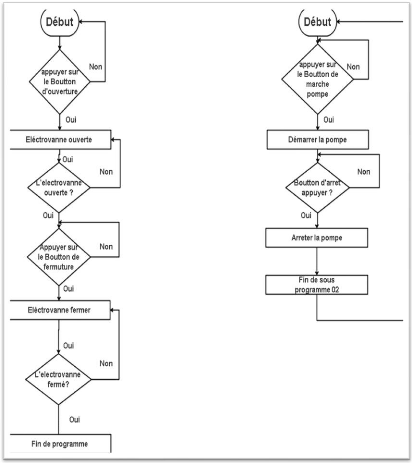
Figure 4.4 : Organigramme de commande
manuelle pour les électrovannes et les pompes
4.2.3 Mode automatique :
Ce mode est sélectionné lorsque les commutateurs
Manu / Auto sont sur la position Auto en mode Automatique, aucune intervention
sur site n'est nécessaire. Le système est sous le contrôle
de l'automate de télégestion ou les opérateurs du centre
de télégestion.
Chapitre 4 : Programmation et Supervision
Toutes les séquences sont exécutées par
l'automate de télégestion qui surveille en permanence les
états des équipements, les archives ainsi que les défauts
et les alarmes qui seront transmis vers les supervisions de WINCC. Le mode
automatique est composé en deux modes :
· Mode automatique.
· Mode télégestion.
Il est a préciser qu'en situation normale,
c'est-à-dire lorsque l'approvisionnement en eau est assuré par la
Société de distribution d'eau (SEACO), la distribution aux
différentes zones de l'aéroport et le remplissage du
château d'eau et de la bâche a eau sont assurés directement
à partir du réseau d'alimentation en eau. En revanche, en cas de
coupure d'eau, le château d'eau s'occupe de la distribution de l'eau
à bâche a eau et à toutes les parties de l'aéroport.
Une fois que la quantité d'eau dans le château d'eau atteint un
certain niveau minimum, le réservoir d'eau prend le relais pour assurer
la distribution de l'eau à l'aéroport.
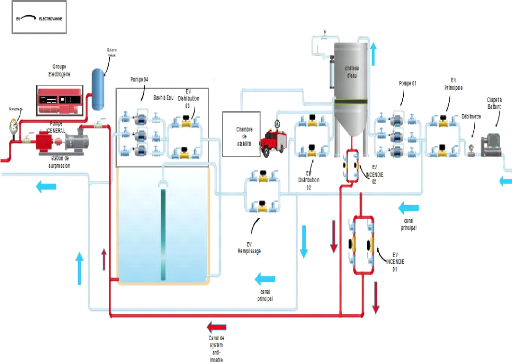
51
Figure 4.5 : schéma global de
l'installation après l'automatisation
52
Chapitre 4 : Programmation et Supervision
A) Les organigrammes du château d'eau :
1)Remplissage :
Partie une
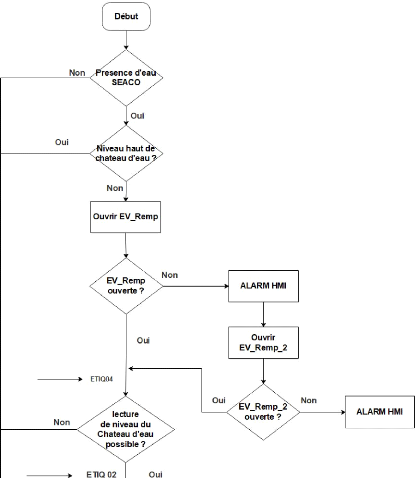

Figure 4.6.1 : Organigramme de remplissage de
château d'eau (partie une)
53
Chapitre 4 : Programmation et Supervision
Partie deux
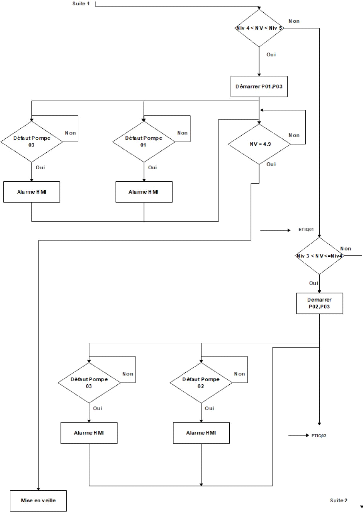
Figure 4.6.2 : Organigramme de remplissage de
château d'eau (partie deux)
54
Chapitre 4 : Programmation et Supervision
Partie trois
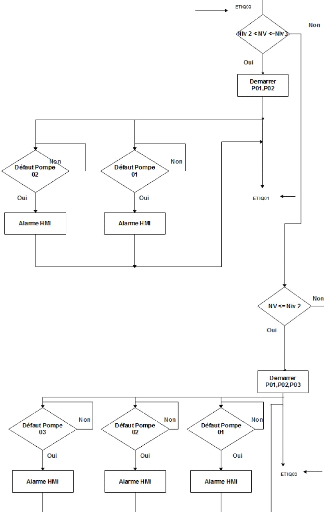
Figure 4.6.3 : Organigramme de remplissage de
château d'eau (partie trois)
Chapitre 4 : Programmation et Supervision
2)Distribution :
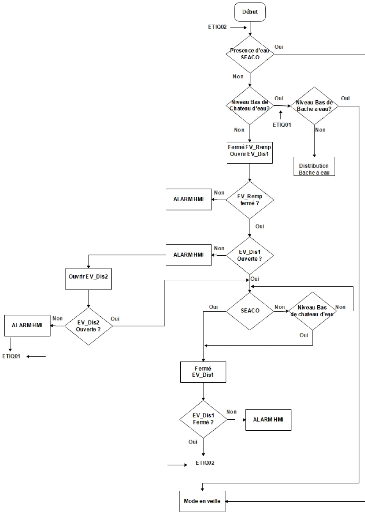
55
Figure 4.7 : Organigramme de distribution
d'eau à partir du château d'eau
56
Chapitre 4 : Programmation et Supervision
B) Les organigrammes de bâche à eau :
1)Remplissage :
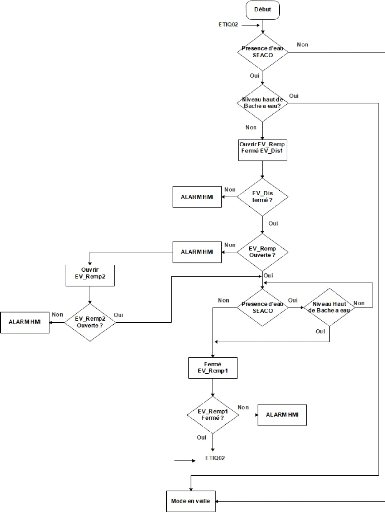
Figure 4.8 : Organigramme de remplissage de
Bâche a eau
Chapitre 4 : Programmation et Supervision
2)Distribution : Partie une


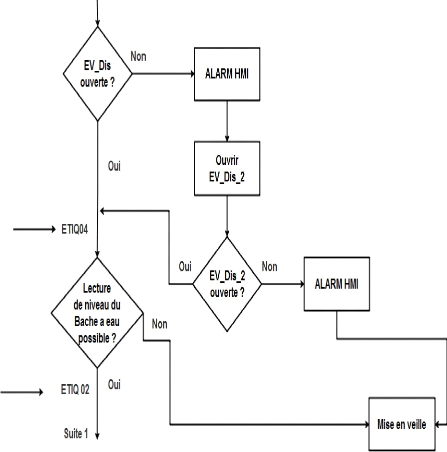
57
Figure 4.9.1 : Organigramme de distribution de
Bâche a eau (partie une)
Chapitre 4 : Programmation et Supervision
Partie deux
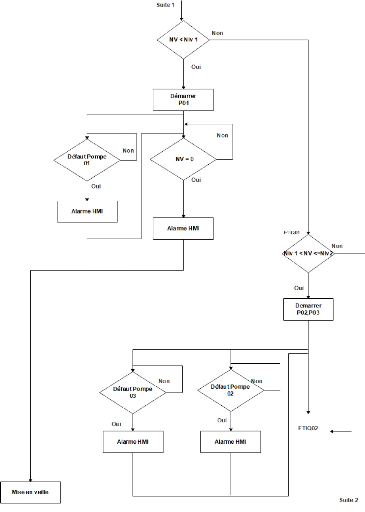
58
Figure 4.9.2 : Organigramme de distribution de
Bâche a eau (partie deux)
59
Chapitre 4 : Programmation et Supervision
Partie trois
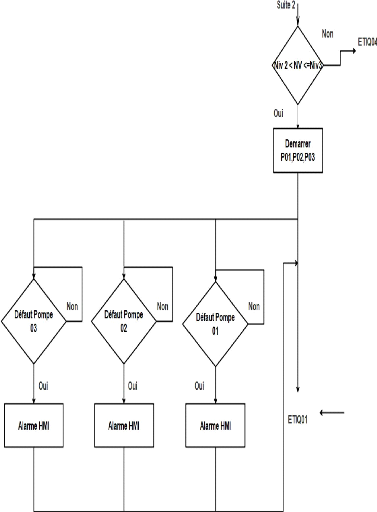
Figure 4.9.3 : Organigramme de distribution de
Bâche a eau (partie trois)
Chapitre 4 : Programmation et Supervision
C) Organigramme de système de l'irrigation :
Partie une
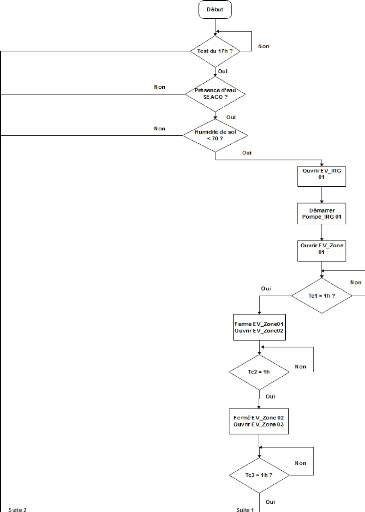
60
Figure 4.10.1 : Organigramme de système
d'irrigation (partie une)
Chapitre 4 : Programmation et Supervision
Partie deux

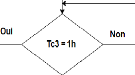
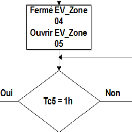
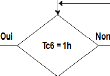

61
Figure 4.10.2 : Organigramme de système
d'irrigation (partie deux)
62
Chapitre 4 : Programmation et Supervision
D) Organigramme de système anti-incendie :
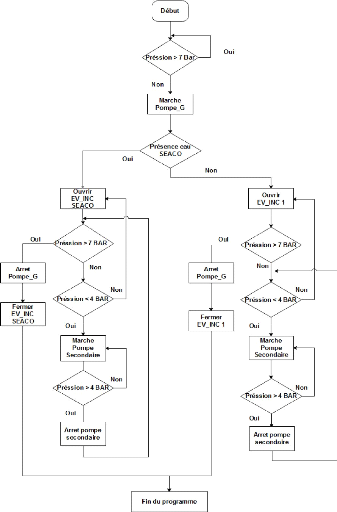
Figure 4.11 : Organigramme de système
de protection contre l'incendie
63
Chapitre 4 : Programmation et Supervision
4.2.4 Mode hors communication :
Dans le cas où il n'y aura pas de communication entre
l'automate du château d'eau, celui de la bâche a eau, du
système anti-incendie ainsi et l'automate réservé à
l'irrigation, le système ne reçoit aucune information à
propos du niveau d'eau donc on ne peut pas gérer la gestion d'eau dans
le mode automatique, c'est pour cela qu'on a créé ce mode (Mode
hors communication) pour gérer la situation afin que l'eau soit toujours
disponible dans le château d'eau et le bâche a eau.
Voici un organigramme qui explique lorsque la connexion entre
HMI et l'automate est coupée le mode local est activé
automatiquement lorsqu'on est en mode manuel.
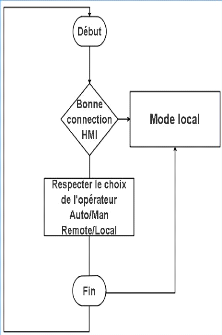
Figure 4.12 : Organigramme du mode hors
communication
4.3 La programmation :
Le programme utilisé comprend toutes les constructions et
déclaration ainsi que les données nécessaires au
traitement des signaux de commande d'une installation ou d'un processus. Pour
notre projet on a utilisé le langage graphique Ladder.
64
Chapitre 4 : Programmation et Supervision
4.3.1 Les Alarmes :
Une alarme apparait dès qu'un défaut quelconque
apparait sur le système. Cette alarme va réapparaitre tant que le
superviseur ne l'a pas acquittée. Un acquittement signifie que
l'opérateur a pris en charge le défaut et va le corriger.
Les alarmes sont nécessaires quel que soit le
système donc on a programmé tous les messages d'erreurs qui
permettent de signaler les défauts et les pannes des équipements
:
Ø Déclenchement d'une alarme de défaut
si on a un problème avec la pompe (elle s'affiche en rouge dans
l'écran HMI avec un message d'erreur).
Ø Si le niveau d'eau dans le château d'eau ou la
bâche à eau atteint le niveau minimum (dans le cas de la
distribution) déclenchement d'une alarme avec un message d'erreur.
Ø Si le niveau d'eau dans le château d'eau ou la
bâche à eau atteint le niveau max (dans le cas du remplissage)
déclenchement d'une alarme avec un message d'erreur.
Ø En cas où il y'à n'importe quel
disfonctionnement (problème, arrêt...etc.) Une alarme
déclenchera automatiquement (électrovannes ou bien les pompes :
elle s'affiche en rouge dans l'écran IHM avec un message d'erreur).
Ø Si la terre des zones concernées par
l'arrosage est humide, le système d'irrigation s'arrête
automatiquement avec une alarme et un message d'erreur.
Ø En cas d'alarme incendie on aura une alarme sonore
dans toutes les vues.
4.3.2 L'Interface Graphique (HMI) :
L'interface graphique du système se compose de quinze vues
:
A. Page d'accueil.
B. Présentation du système.
C. Schéma global de fonctionnement.
D. Château d'eau.
E. Bâche à eau.
F. Château d'eau et bâche à eau.
G. Anti-incendie.
H. Vue globale de système d'irrigation (toutes les
zones).
I. Une vue avec Autocade pour connaitre les zones
d'irrigation
J. Vue Zone 1.
K. Vue Zone 2.
L. Vue Zone 3.
Chapitre 4 : Programmation et Supervision
M. Vue Zone 4.
N. Vue Zone 5.
O. Vue Zone 6.
P. Gestion de vue (vue globale pour du diagnostic et les
alarmes).
A/ Page d'accueil :
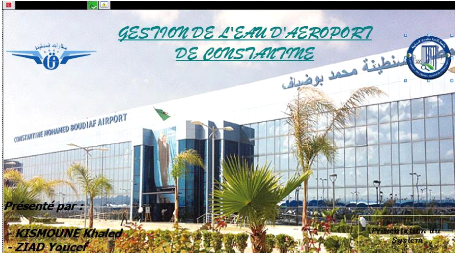
Figure 4.13 : Page d'accueil
B/ Présentation du système :
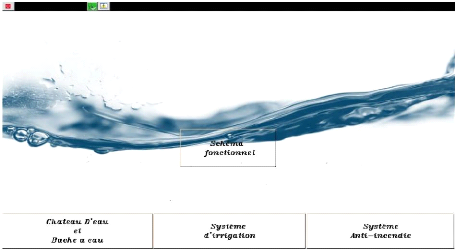
Figure 4.14 : Présentation du
système
65
66
Chapitre 4 : Programmation et Supervision
C/ Schéma fonctionnel : À
partir de cette vue :
· On peut connaitre l'état du système.
· Le niveau de remplissage du château d'eau.
· Le niveau de remplissage de la Bâche à
eau.
· On peut accéder pour chaque sous-système,
juste en cliquant sur la partie graphique le représentant.
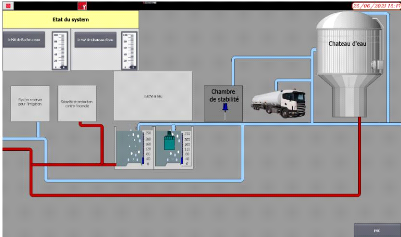
Figure 4.15 : Schéma globale du
fonctionnement
D/ Château d'eau :
À partir de cette vue, on peut :
· Choisir le mode de fonctionnement (auto/man) avec le
commutateur.
· Visualiser le niveau d'eau dans le château
d'eau.
· Commander l'ouverture et la fermeture des
électrovannes (par un clic sur électrovannes).
· Commander le démarrage et l'arrêt des pompes
(par un clic sur la pompe)
· Connaitre le niveau de chlore dans l'eau.
· Connaitre le débit de l'eau.
67
Chapitre 4 : Programmation et Supervision
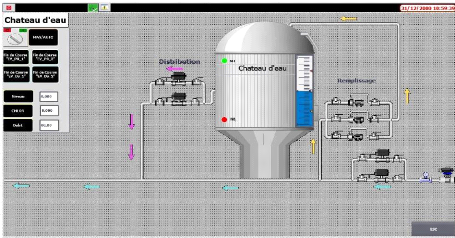
Figure 4.16 : Vue de l'état du
Château d'eau
E/ Bâche a eau :
À partir de cette vue, on peut :
· Choisir le mode de fonctionnement (auto/man) avec le
commutateur.
· Visualiser le niveau d'eau dans le Bâche a eau.
· Commander l'ouverture et la fermeture des
électrovannes (par un clic sur électrovannes)
· Commander le démarrage et l'arrêt des pompes
(par un clic sur la pompe)
· Connaitre le niveau de chlore dans l'eau.
· Connaitre le débit de l'eau.
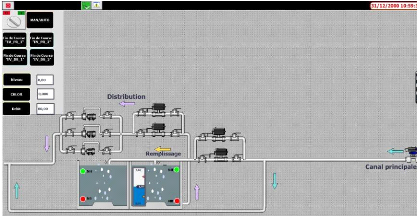
Figure 4.17 : Vue de l'état de la
Bâche a eau
68
Chapitre 4 : Programmation et Supervision
F/ Château d'eau et bâche à eau :
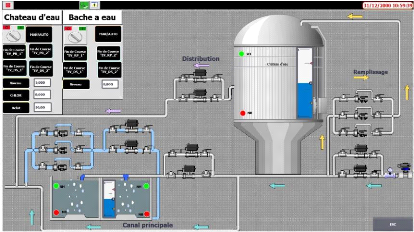
Figure 4.18: vue de l'état du
Château d'eau et de la Bâche a eau
G/ Système anti-incendie :
À partir de cette vue :
v Contrôler les électrovannes et les deux pompes de
ce système.
v Afficher l'état des pompes et des
électrovannes.
v Le déclenchement automatique de ce système est
lié aux pressions des RIA situé au niveau de
l'aéroport.
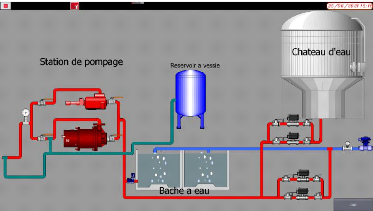
Figure 4.19 : Vue de l'état du
système de protection contre l'incendie
Chapitre 4 : Programmation et Supervision
H/ Système d'irrigation :
À partir de cette vue :
· On peut connaitre la présence de l'eau dans le
canal principale (SEACO).
· On peut visualiser l'état de chaque
électrovanne du système d'irrigation.
· On peut sélectionner la pompe qui va être
utilisée.
· On peut aussi sélectionner les
électrovannes qui vont être utilisées.
· On peut préciser la durée pour chaque pompe
ou électrovanne sélectionnée.
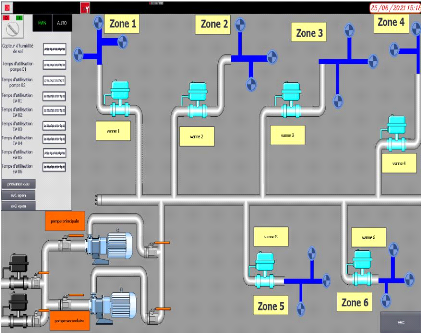
69
Figure 4.20 : Vue de l'état du
Système d'irrigation
Chapitre 4 : Programmation et Supervision
P/ Diagnostic et alarmes
Cette Interface est divisée en deux parties :
· La première partie (à droite) concerne
la partie diagnostic. Elle permet de connaitre les problèmes du
matériel, réseaux et l'automate en indiquant l'emplacement, le
numéro de référence et l'état du
problème.
· La deuxième partie (à gauche) concerne
l'activation de l'alarme. Elle permet d'afficher, enregistrer tous les messages
d'alarmes avec identification de lieu, la date et la nature de problème
(erreurs, avertissements) tels que les défauts des pompes, les erreurs
et les dépassements des valeurs limites de niveau et de pression...
Etc.
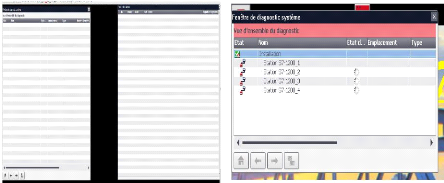
70
Figure 4.21 : Vue de diagnostic et alarme
Figure 4.22 : Vue de diagnostic
Conclusion Générale
72
Conclusion Générale
Le travail présenté que nous avons
effectué au sein de la société EGSA/C a pour but
d'améliorer l'environnement de travail et d'optimiser les performances
du système actuel de gestion de l'eau, en vue d'assurer une gestion
optimale de cette dernière, sans aucune intervention des
opérateurs sur site. L'automatisation du système actuel permet de
remédier à un certain nombre d'insuffisances, comme :
+ L'absence d'un système d'irrigation automatique
(Cette dernière se fait manuellement et de manière
aléatoire par un ouvrier)
+ L'impossibilité de connaître les quantités
d'eau dans le château d'eau et la Bâche à eau. + La
difficulté de contrôler le remplissage et la distribution de ces
derniers.
+ L'absence d'un système qui permet d'analyser l'eau
stockée (chlore, moisissures) + Une perte de temps énorme
à cause de l'intervention d'un opérateur pour ouvrir ou
fermer les vannes, faire démarrer ou arrêter les
pompes ou chercher la cause d'un
problème en cas de défaut ou
dysfonctionnement.
+ L'absence d'un système de communication réseau et
d'un système de supervision.
Par notre projet nous avons apporté des
améliorations en intégrant quatre automates programmables qui
communiquent entre eux grâce à la nouvelle technologie de fibre
optique et de programmer une interface Homme-Machine pour faciliter la
surveillance et la gestion du processus en temps réel.
Notre principale tâche a été de programmer
l'automate et l'interface de supervision et ensuite les relier en software et
en hardware, prévoir aussi les défaillances que peut
présenter le système, de les afficher en tant qu'alarme sur
l'écran de supervision et permettre la gestion à distance de la
station en temps réel.
Enfin, nous tenons à mentionner que ce travail nous a
été très bénéfique. Le contact direct avec
les spécialistes dans le domaine sur le terrain, nous a permis
d'enrichir nos connaissances théoriques et pratiques acquises durant nos
études, surtout en ce qui concerne la compréhension du processus
global du fonctionnement d'un système complexe comme celui de la gestion
de l'eau.
Bibliographie
[1] :
https://www.mesdepanneurs.fr/blog/clapet-anti-retour
[2] : https://www.se.com/
[3] :
http://gilles.berthome.free.fr/02-Syntheses/F_Transmision_info/Synthese_relais.pdf
[4] : RAISEMCHE. A : « Conception et programmation d'une
armoire de commande assistée par ordinateur » Mémoire
Magister En Electrotechnique, Université De Sétif Disponible en
ligne :
http://dspace.univsetif.dz:8888/jspui/bitstream/123456789/1949/1/M%C3%A9moire%20magi
ster%20Raisemche%20Aziz.PDF
[5] : Sghaier.N & Mbarek.M. "Chapitre 2 : Structure des
circuits de commande et de puissance". Page 11-13 .2014
[6] : SAIDOUN. A, ZABOT. T « Automatisation et supervision
d'une station de pompage et distribution d'eau à la S.N.V.I»
Mémoire de Fin d'Etude de MASTER PROFESSIONNEL Université Mouloud
Mammeri De Tizi-Ouzou 1 juillet 2018, Chapitre 2 Page 17-18.
[7] : https://www.endress.com/
[8] : https://www.avk.fr/
[09]
http://www.geea.org/IMG/pdf/LES_AUTOMATES_PROGRAMMABLES_INDUSTRIE
LS_pour_GEEA.pdf
[10] : Supervision Industrielle_ Chapitre 1_Dr.
ZIANI Salim, Cours Université Constantine1
[11]: s7-1200_system_manual_fr-FR_fr-FR.
https://suport.indusry.siemens.com
[12]:
https://mall.industry.siemens.com/mall/en/ru/Catalog/Product/6MF1013-0CB15-0AA0
[13]:ModuleDI16/DQ16x24VDC_1
https://cache.industry.siemens.com/dl/files/523/83501523
/att 897447/v1/s71500 di 16x24vdc dq16x24vdc 0.5a ba manual en-US
en-US.pdf
[14]: ModuleAI4x13BIT_1
https://cache.industry.siemens.com/dl/files/624/59753624/att
75682/v1/et200sp ai 4xu i 2 wire st manual fr-FR fr-FR.pdf
[15]: ModuleDQ8x24VDC
https://cache.industry.siemens.com/dl/files/588/59753588/att
90147/v1/et200sp dq 8x24vdc 0 5a st manual fr-FR fr-FR.pdf
[16] : Simatic profinet description du système manuel
système
https://suport.indusry.siemens.com
[17] :
https://support.industry.siemens.com/cs/document/109772803/simatic-step-7-incl-safety-and-wincc-v16-trial-download?dti=0&lc=en-WW
[18] : Documentation du logiciel « Tia Portal »
https://support.industry.siemens.com/cs/document/65601780/tia-portal-an-overview-of-the-most-important-documents-and-links-controller?dti=0&lc=en-WW
[19] :
https://www.eplan.fr/solutions/plateforme-eplan/eplan-electric-p8/