Introduction
générale
Gabès est parmi les grands villes de la Tunisie, il
compte d'environ 150.000 habitants, également plusieurs activités
économiques diversifiées sont abrites à cette ville. Comme
il était un pôle d'industrie pétrochimique très
important dans le pays, beaucoup des problèmes sont apparus, des taux
intolérables des polluants chimiques et organiques ont
été déversés dans le milieu naturel à cause
des problèmes d'hygiène et de la maladie chronique telle que le
cancer et les différents types d'allergies.
Pour trouver une solution pour la pollution d'air au sein de
la société dans la quelle on va effectuer notre stage de PFE
(Projet Fin d'Etude), il est donc nécessaire dans un premier temps
d'identifier la situation actuelle de séquenceur numérique
utilisé qui est câblé par un filtre de poussière. Et
dans un deuxième temps on va remplacer la solution existante par un
automate programmable, ceci essentiellement pour automatiser le fonctionnement
de la solution existant.
Durant les dix dernières années le monde
industriel a reconnu une évolution rapide et ce
grâce à l'utilisation des nouvelles technologies d'automatisation,
en plus des nombreuses études ont été consacrées
à l'automatisation des applications industrielle. Dans nos jours
l'automatisation devient une tâche nécessaire qui apporte
plusieurs avantages, elle permet de remédier plusieurs problèmes
tel que la minimisation des coûts, l'optimisation des méthodes de
production, la réduction des pertes, en plus la sécurité
du matériel et la protection des personnes. Dans le thème de
l'automatisation de système industrielle, s'inscrite le sujet de notre
PFE.
Ce rapport se décompose en quatre parties.
Une première partie présente le lieu au sien de
la quelle on a effectué notre stage de projet de fin d'études,
Industriel Chimique du Fluor de Gabés (ICF)
La deuxième partie est consacrée, aprés
une brève présentation de la solution existante et les
problèmes associées, à la proposition d'une nouvelle
solution plus automatisée. Également nos motivations, les
objectifs et les contraintes attendus sont traités.
Dans la troisième partie nous allons aborder les outils
et les logiciels utilisés
La quatrième partie est consacrée à
décrire la phase de programmation, de câblage et de la mise en
ouvre de l'automate programmable industrielle.
Chapitre n°1:
Présentation de la société
I. Introduction
Ce chapitre débute par un bref aperçu de
société Industriel Chimique du Fluor de Gabés, au sein de
la quelle on a effectué notre stage de PFE. Également, au cours
de ce chapitre on donne en bref une présentation générale
de la société et le cycle de la production. Enfin, on termine par
une présentation de l'organigramme de l'ICF.
II. Présentation de l'ICF
La société Industrielle Chimique du Fluor de
Gabés (ICF) est une société anonyme crée le 11 juin
1974 par le gouvernement tunisienne, elle est située dans la zone
industrielle de Ghannouch à Gabés. Deux ans âpres, l'ICF
fait l'entrée en production. La mission principale de l'ICF consiste
à effectuer toutes les opérations industrielles commerciales et
financière, également elle se rattachée à la
fabrication et à la commercialisation du fluor d'aluminium (ALF3). En
effet, elle fait l'exportation de la matière pré final pour la
production d'aluminium à travers le monde tel que la France,
brésil. Il faut noter que la fabrication de l'ALF3 nécessite
l'importation du Spath Fluor et l'Alumine principalement de la Chine, l'Italie,
Maroc. Afin de mieux satisfaire les besoins et les exigences de ces clients et
améliorer l'environnement de travail, la société a
procédé à une réhabilitation des ses installations
en améliorant la qualité de ces produits, en traitant les rejets
gazeux fluores tout en augmentation.
Le Chiffre d'affaire de la société en
DT est égale à 45000000, la valeur de l'exportation est
égale à 45000000D, et de l'importation est égale
20000000D. L'ICF est dirigée par M RLAKHDAR Tlili, elle embauche 180
agents hiérarchisés comme suit, 30 cadres supérieurs, 101
agents de maitrise et 51 agents d'exécution.
III. Cycle de
production
L'ICF est constituée principalement par deux
unités, l'unité de séchage et l'unité de
production. Ils sont utilisées essentiellement pour la production de
spath de fluore et spath d'alumine. Dans la suite, on va présenter en
détails ces deux unités dans le cycle de production (voir figure
n°1).
L'état des matières primaires importées,
Alumine et spath fluor, sont humides ce qui nécessite donc une
opération de séchage avant de procéder les
différentes étapes de fabrication. Ces étapes sont
identiques pour l'unité de séchage Alumine et l'unité de
séchage spath, et qui nécessite une alimentation en gaz.
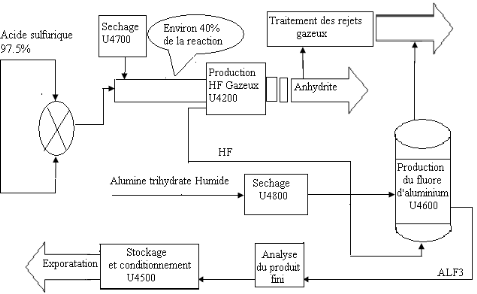
Figure n° 1 : Cycle de la
production
III.1 Unité de
séchage de spath fluor
III.1.1 Fonctionnement de
différents blocs de l'unité de séchage de spath
fluor
L'unité de séchage de spath fluor est
subdivisée selon son fonctionnement en plusieurs blocs, chacun assure
une fonction bien définie dans le cycle de la production. Une structure
de l'unité de séchage de spath fluor est présentée
dans la figure n°2.
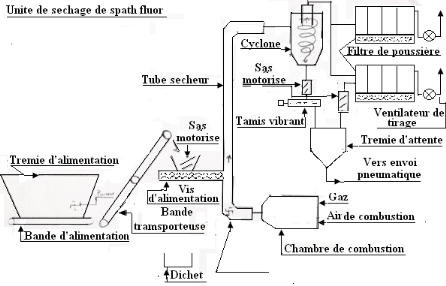
Figure n°
2 : Unité de séchage de spath fluor
ü Le premier bloc rassemble la trémie
d'alimentation et la Bande d'alimentation, ce bloc assure l'alimentation de
l'unité de séchage de spath de fluor.
ü Le deuxième bloc est constitué par le sas
motorisé, la bande transporteuse, et le vis d'alimentation. il sert
à véhiculer la matière à sécher.
ü Le troisième bloc assure le séchage de
spath de fluor, cette fonction est faite par différents
éléments comme la chambre de combustion, le tube sécheur
et le désintégrateur.
ü Le quatrième bloc récupère le
spath sec en assurant l'étanchéité de système, ce
qui est assurée par le cyclone, le tamis vibrant, le piocheur et la
trémie d'attente.
ü Le cinquième bloc comporte le filtre de
poussière, le ventilateur de tirage et le sas motorisé. Il sert
à filtrer les poussières.
III.1.2 Fonctionnement des
principaux éléments de l'unité de séchage
La trémie d'alimentation est alimentée par le
spath fluor humide (avec une humidité de 8 jusqu'au 10%),
également par l'intermédiaire d'une bande d'alimentation à
vitesse variable. Le piocheur fragmente la matière afin de faciliter
régulièrement son passage sur une bande transporteuse qu'elle va
le transmettre vers le sas motorisé, c'est qui assure
l'étanchéité du vide dans le circuit par l'ouverture
alternée de ses clapets. L'injection de spath dans une double vis qui
le conduit à son tour vers le tube sécheur.
III.1.2.1 Vis d'alimentation
La vis d'alimentation facilite l'entrée de spath fluor
dans le tube sécheur, son type de construction est une double vis porte
à faux. Il travaille de façon continue afin de produire le spath
de fluor(CAF2) d'un masse volumique varie entre 1700 et 1800 en Kg/m.Elle
est caractérisée par l'abrasion en utilisant une capacité
normale est égale 10900kg/h par rapport au maximal est égal 12000
kg/h. De même, elle est caractérisée par une vitesse
maximale constante 50tr/min et une puissance installée égale
à 3×380/50Hz. La variation de tension est de +/- 15% et la
tension de contrôle installée varie entre (220, 50) et une
puissance de moteur est égale à 7,5 kw et le niveau sonore est
égale 80db. À cause de ses caractéristiques, sa
construction est robuste pour un usage industriel.
III.1.2.2 Filtre de poussière
Il récupère les poussières pour diminuer
le maximum de perte du spath sec. Un système d'envoi pneumatique permet
l'envoi du produit sec vers le silo de stockage. Le principe de fonctionnement
du transport commence par l'ouverture de double Caplet qui actionne l'ouverture
de la vanne pneumatique, dite aussi vanne à casque. Par la suite, le
produit commence à chuter de la trémie d'attente vers le
centenaire, lorsque le produit atteint le détecteur de niveau, ce
dernier actionne la fermeture de la vanne à casque et double Caplet.
Ensuite, la vanne d'admission d'air s'ouvre et l'envoi se déclenche avec
une pression d'envoi égal à 1, 8 bar. Lorsque le centenaire se
vide de produit la pression chute à 0,4 bar et la vanne d'admission
d'air se ferme et cycle se recommence. La figure n°3 présente le
filtre de poussière.
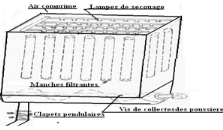
Figure n°3: Filtre de poussière
III.1.2.3 Ventilateur de tirage
Le ventilateur fait nettoyer le circuit, il fonctionne de
façon continue pour produire le gaz de dilution et une poussière
approximative de 50 mg/m. Il est manipulé par une puissance
installée égale à 3 ×380V/50Hz et une tension de
contrôle égal à 220V/50Hz. Il utilise une pression de
système est égale à -65mbar et un débit de
ventilateur égal à 7500kg/h. Il est caractérisé par
une température de service varie entre 100 °C jusqu'a 140°C,
une densité égale à 0.88 kg/m à 110°C et une
pression d'aspiration varie entre-55 mbar et -60 mbar et le niveau sonore
égal à 80 dB.
III.1.3 Unité de séchage d'Alumine
L'unité de séchage alumine est similaire
à l'unité de séchage spath fluor à l'exception de
quelques éléments tel qui un vis de brassage à
l'unité de séchage d'alumine au lieu d'un sas motorisé
à l'unité de spath et un seul vis d'introduction de
matière dans le tube sécheur d'alumine au lieu d'une double vis
à l'unité de spath. Le principe de commande et de fonctionnement
des deux unités est le même, également le résultat
de séchage est le même (produit sec d'alumine atteint d'environ
0,05% d'humidité). L'alumine est importé aussi tri
hydratée de l'étranger (Italie, Australie...) à une
humidité de 4 jusqu' à 6 %. La figure ci-dessous présente
la structure de l'unité de séchage d'alumine.
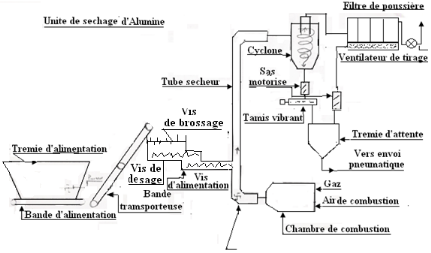
Figure n°4 : Unité de séchage
d'alumine
III.2 La production de
l'ALF3
La production de l'ALF3 se déroulé en les
étapes. D'abord, on mélange l'acide sulfurique à 97% par
l'oléum à 10,4% pour avoir le gaz HF <<gaz
Fluorhydrique>>.
Ensuite on réagit le gaz Fluorhydrique
<<HF>> avec l'alumine séchée pour produire le fluor
d'aluminium(ALF3). La production se fait par différentes matières
primaires tels que le spath fluor, l'alumine, l'acide sulfurique et
l'oléum, qui sont destinés à la commercialisation.
IV. Organigramme de la
société l'ICF
L'ICF est repartie en deux sites une au Tunis et l'autre en
Gabés. La figure n°5 présente une hiérarchie de
l'ICF, elle comporte 5 directions à Tunis et 4 directions à
Gabés.
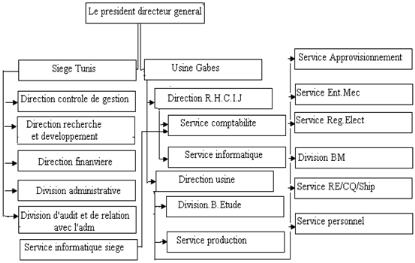
Figure n°5: L'organigramme de
l'ICF
Le local de Gabès est
divisé en 4 services qui sont : service d'approvisionnement,
service d'entretien mécanique, service informatique et service
régulation électrique. Les deux dernières services sont le
plus importants et dans le quelle c'est localisée notre projet.
IV.1 Service informatique
Il s'intéresse
à faire l'optimisation de l'expédition de moyennes
informations, puis la préparation des nouveaux plans informatiques,
ensuite, le développement et la maintenance des applications
informatiques.
IV.2 Service régulation électrique
Il se charge de la consignation,
la de consignation des moteurs, la surveillance de bruleurs, ainsi que la
réparation, la programmation et la maintenance des équipements de
distribution d'énergie et du gaz naturel.
V. Conclusion
Dans ce premier chapitre, nous
avons présentés d'une façon générale l'ICF
(industriel chimique de fluor de Gabes). Ainsi nous avons illustrés les
différents unités qui les constitue ceci nous a permis de
comprendre le système de production, les conditions et les
mécanismes de travail. Tous ça nous a permis de mieux comprendre
le contexte du travail de notre sujet de PFE, ce qui constitue l'objectif du
deuxième chapitre.
Chapitre n°2:
Présentation du contexte de travail
I. Introduction
Ce stage est effectué à la société
Industriel Chimique de Fluor de Gabés au sien du département
régulation électrique. L'un des objectifs
visés consiste à identifier le séquenceur
numérique également le filtre de poussière. Ce
séquenceur conduit à assurer une fonction bien définie
pour la commande de filtre de poussière. Bien que le séquenceur
apporte certains avantages, il présente comme même quelques
inconvénients, pour cela une solution doit être proposée
afin de remédier ces problèmes. La solution proposée
consiste à remplacer la solution existante par un automate programmable,
également les justifications de choix de l'API sont illustrées.
Dans ce chapitre, après avoir préciser les
motivations et restituer le contexte, la problématique et l'objectif de
stage sont décrits.
II. Motivation
Pour mettre en oeuvre une solution automatisée qui
assure les mêmes fonctionnements que celle existante, on va identifier
dans la première partie la situation existante de séquenceur
numérique. Ce dernier se caractérise par son coût
très élevé, une difficulté de variation de tension
d'alimentation des sortie d'électrovannes (24V, 220V) et une
sensibilité aux parasites, en plus la possibilité
de bugs dans le microcode et la lenteur de la machine. Grâce
à ces inconvénients, dans une deuxième partie, on propose
de remplacer la solution existante par une autre à base d'une automate
programmable. Les principaux caractéristiques de la solution
proposée est la suppression de certaines tâches pénibles,
les répétitives ou les nocives pour l'homme, de même la
souplesse d'adaptation pour le développement des systèmes, la
simplicité d'utilisation, le diagnostic des pannes, la rapidité
et la fiabilité de système.
Il existe des circuits électroniques optimisés
pour s'interfacer avec les entrées et les sorties physiques du
système, l'envoi et la réception des signaux est faite de
façon très rapide avec l'environnement. En plus, avec une
exécution séquentielle cyclique sans modification de
mémoire, ils permettent d'assurer un temps d'exécution maximal,
respectant un déterminisme temporel et logique, garantissant un temps
réel effectif.
III. Description détaille
de sujet
III.1 Avis
général
Le sujet de notre PFE sert à identifier le
fonctionnement d'un séquenceur qui organise les tâches de
filtrage de poussière, en utilisant en parallèle un appareil de
mesure de pression différentielle ou relative avec un séquenceur
qui permet la commande et le contrôle de la gamme de poussière.
L'organigramme suivant (figure n°6) est une représentation
schématique fonctionnelle, organisationnelle et hiérarchique d'un
organisme ou de programme de notre sujet, c'est pour cela en ajoutant le
schéma illustré au dessous pour décrire le fonctionnement
de séquenceur en utilisant un organigramme qui explique son
fonctionnement.
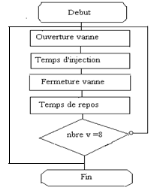
Figure n°6 : Organigramme de fonctionnement
de filtre
Au départ le séquenceur permet la mise en marche
des vannes, il actionne de façon cyclique une vanne après
l'autre. Les vannes sont commandés par trois paramètres, le
premier est un temporisateur de temps d'injection, la deuxième est un
temporisateur de temps du repos et le dernier pour le variateur de nombre de
vanne qui dépend de plusieurs conditions tel que l' humidité de
produit primaire, la disponibilité de vanne et la pression d'air. Le
schéma présenté ci- dessous (figure n°7)
décrit le fonctionnement de séquenceur en utilisant un Grafcet
qui décrit le fonctionnement du séquenceur.
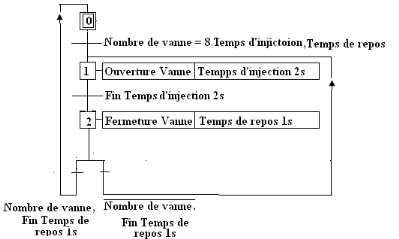
Figure n°7 : Grafcet décrit de
fonctionnement de filtre
Chaque vanne est constituée par des manches qui
absorbent et ramassent les poussières. Ainsi pour que les manches ne
soient pas colmater, il ya un système de pression d'air qui assure le
nettoyage des manches de la poussière. Le schéma
présenté ci-dessous (figure n°8) décrit le
fonctionnement de séquenceur en utilisant un chronogramme
détaillé de cycle de système.
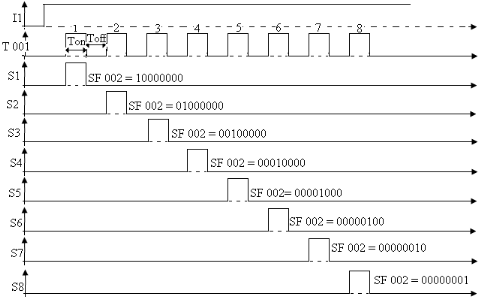
Figure n°8: Chronogramme descriptif de
fonctionnement de filtre
III.2
Problématiques de la solution existante
L'ancien séquenceur numérique est de type
AUXITROL ESD 900, il est utilisé pour assure le nettoyage de filtre.
Dans la suite, nous allons illustrer les inconvénients de
séquenceur :
- Limite le nombre de vannes à filtrer.
- L'inexistante des composants.
- Difficultés de dépannage, complexité et
ambigüité.
- Coût des composants très chers.
Pour
remédier aux problèmes et aux inconvénients
déjà annoncées de séquenceur numérique
utilisé, les personnels de l'unité ont choisi de remplacer la
solution câblée à base de séquenceur de type
`AUXITROL ESD 900' par une autre solution câblée à base
d'un automate programmable pour plusieurs raisons. La nouvelle solution
présente plusieurs avantages, on va le citer en détails par la
suite.
III.3 Présentation de la
solution existante: Séquenceur Numérique Câblé
III.3.1 Présentation de
séquenceur
III.3.1.1
Généralité sur le séquenceur
Le séquenceur est commandé à partir de la
perte de charge du filtre par un capteur de pression différentielle
DE20. Il peut être considéré comme une machine
d'état, ses entrées sont les conditions issues du chemin des
données et ses sorties sont les commandes pour le chemin de
données.
Le séquenceur Maitre/Esclave est la partie intelligente
de système, il permet de lire le Äp et de contrôler la
séquence des vannes à membranes dans le filtre de
poussière, aussi il utilise la technologie microprocesseur. Toutes les
caractéristiques techniques ont été homologuées par
un laboratoire agrée, son fonctionnement est facile par un menu clair et
des consignes précise par exemple il identifie les anomalies
éventuelles au niveau des vannes à membranes. Par la suite, il
localise et identifie les problèmes de câblage où des
courts-circuits au niveau de vanne à membrane.
III.3.1.2 Guide d'utilisation de séquenceur
ü Capteur de pression différentielle
Start/Stop
Il est possible de commander le séquenceur à
partir de la perte de charge des filtres, dans ce cas on utilise un capteur de
pression différentielle. La vanne qui a été
décolmaté pour la dernière fois est enregistrée et
le décolmatage commence après « Restart»
avec la vanne suivante.
ü Ajustement de temps pour les compartiments de
filtre
Tous les séquenceurs sont
préréglés, le temps d'impulsion est réglé
à 50 ms, cette temps peut être modifie seulement par des
directives de fournisseur.
ü Démarrage/Arrêt -
Entrée
Cette entrée permet de contrôler le
nettoyage du filtre qui dépend de la pression différentielle. Par
l'entrée Démarrage/Arrêt les appareils principaux en
addition, les auxiliaires peuvent être mis en marche où
arrêté le séquenceur de base. Pour cela un interrupteur de
pression différentielle est nécessaire comme appareil
additionnel. Le raccordement s'effectue aux bornes de D1 et D2 du
séquenceur de base. L'appareil principal enregistre qu'elle vanne a
été épurée la dernière et par la suite il
commence après un démarrage de nouveau avec la vanne suivante.
III.3.1.3 Fonctionnement de
séquenceur numérique
Le séquenceur a pour fonction de commander les
processus de nettoyage des filtres JET. Le filtre est composé d'une
commande des électrovannes pour fixer de temps de l'ouverture des vannes
(temps d'impulsion) et d'une commande de temps d'arrêt et de fixation de
l'ordre de la mise en fonction des électrovannes. L'indication de bon
fonctionnement par des diodes lumineuses (LED) du réseau, de
l'alarme, de la sortie du vanne, de la durée de cycle, de l'indicateur
de défaut sur le relais d'alarme, la surveillance de tension de
réseau et le démarrage-arrêt pour la commande
dépendant de la pression différentielle.
II.3.2
Présentation de Filtre de poussière
II.3.2.1 Description de fonctionnement de
filtre
Tout d'abord, on va décrire le
fonctionnement de filtre FT-S qui a pour fonction d'éliminer les
particules liquides, les impuretés solides de l'air comprimé
et d'introduire l'air avec le plus grand degré de
pureté possible dans le consommateur. Initialement, l'air chargé
de poussière est aspiré latéralement dans le caisson
central, un déflecteur assure sa répartition interne tout en
préservant le corps filtrant de l'abrasion. Deuxièmement, les
poussières lourdes sont entrainées par leur propre poids vers le
bas et les poussières plus légères se déposent
à faible vitesse sur le media filtrant. Troisièmement, l'air
propre est aspirée dans le caisson supérieure par un ventilateur
d'extraction de puissance appropriée à la perte de charge de
réseau Finalement, le séquenceur commande l'intervalle et la
durée d'ouverture des vannes de décolmatage des manches par
injection de l'air comprimée, les poussières sont
évacuées vers la partie inférieure.
III.3.2.2 Caractéristiques technique de
filtre
Le filtre de poussière est caractérisé
par un faible niveau d'émission de poussières à
l'environnement et une durée de vie prolongée du système
de filtration. Également le nettoyage des filtres est assuré par
un système d'injection d'air comprimé à contre courant, un
système électronique adapte la fréquence de nettoyage
selon les besoins de l'installation.
III.3.2.3 Applications de filtre
Le filtrage des poussières où
pulvérulents secs se fait par plusieurs opérations tel que le
pesage, le broyage, le malaxage, le mélange, le polissage, le meulage,
le tamisage, le affûtage. La fabrication de comprimés
pharmaceutiques par filtre aspire les poussières et nettoyé les
manches qui aspirent les poussières. Les poussières peuvent
être lourdes où légère, fine où
grossière, collante où volatile, sèche où humide,
chargée d'électricité statique. Il est donc très
important de choisir le bon type de filtre de poussière et le bon type
des matériaux filtrants lorsqu'on conçoit un système pour
filtrer les poussières. Nous proposons une grande variété
de matériaux filtrants qui s'intègrent et s'adaptent à
l'ensemble de notre gamme de filtres. Cela signifie que ces filtres peuvent
être utilisés pour traiter efficacement les pluparts types des
poussières.
III.3.2.4
Avantages du filtre de poussière
La gamme de filtre de poussière (voir annexe A)
proposé peut être utilisée pour traiter efficacement la
plupart types de poussières. Les avantages de filtre de
poussière sont nombreux :
- L'air ambiant est plus propre au poste de travail.
- L'efficacité des machines et des appareils est
augmenté.
- L'usure des machines ainsi que les arrêts de
production diminuent.
- Le personnel se sent mieux, et la productivité est
améliorée.
- Les marchandises restent propres et plus attractives sur le
plan visuel.
III.4 Présentation de la
solution proposées: Automate programmable
III.4.1 Historique de l'API
Les automates programmables sont apparus aux USA vers les
années 1969, à l'époque ils étaient
destinés essentiellement à automatiser les chaînes de
montages automobiles. Ils sont apparus en France en 1971, ils sont de plus en
plus employés dans l'industrie.
Un Automate Programmable Industrielle (API) est distingue d'un
calculateur par le fait qu'il s'agit d'un système électrique
programmable, spécialement adapte pour les non-informaticiens. Il est
général destine à être mis entre les mains d'un
personnel dont la formation a été surtout orientée vers
l'électromécanique. L'API s'est substitue aux armoires à
délais en raison de sa souplesse, mais aussi parce que dans les
automatisations de commande complexe, les coûts de câblage et de
mise au point devenaient trop élevés.
III.4.2 Définition de l'API
Un API est une machine électronique programmable par un
personnel non informaticien, il est destiné à piloter en
ambiance industrielle et en temps réel des procédés
appelés encore partie opérative. On programme l'API pour
effectuer des opérations cycliques qui reçoit des données
par ces entrées, ensuite ces derniers sont traitées par un
programme définis et les résultats obtenu sont
délivrées par ses sorties pour commander le système.
III.4.3 Avantages de
l'API
L'utilisation de l'automate programmable dans le domaine
industrielle présenté plusieurs avantages, dans la suite on va
illustrer les plus importantes.
ü Moins de
constituants
La substitution des relais à un gain en volume, on
encombrement et à la simplicité de l'emploi,
particulièrement apprécies sur les
machines simples.
ü Moins de câblage
Les connections se réduisent au raccordement des
capteurs aux entrées et des prés actionneurs aux sorties.
L'accès aux différents organes de l'automatisme, lots des
modifications et des réglages, se trouve ainsi facile.
ü Plus de
confort
Le programme qui se substitue au câblage et
l'ensemble des graphiques on peut le saisir, le modifier et l'archiver
facilement grâce au terminal de programmation et de réglage. Ce
programme peut être duplique pour les machines construites ainsi une
diminution des coûts.
ü Plus de
fonctionnalités
Pour les machines spéciales où leur
installations sont compliquées, l'automate programmable offre des
fonctions d'automatisme spécifiquement intégrées.
ü Plus d'information
La maintenance et la mise en place d'un automatisme est
facile par la visualisation permanente de l'état des
entrées/sorties, qui sont signalés par des voyants lumineux. Le
dialogue entre l'homme et la machine est assuré par un terminal de
programmation ainsi de réglage grâce à son mode
conversationnel et les messages affichés sur l'écran.
III.4.4 Architecture de
l'API
L'automate programmable se constitue en trois parties, le
premier partie c'est le processeur, le deuxième c'est la mémoire
programme et le troisième c'est l'interface des entrées et des
sorties. Une structure qui simplifie l'interaction entre les composants de
l'automate est schématisée dans la figure n°9.
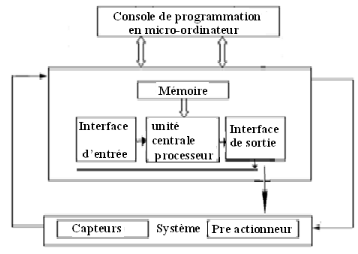
Figure n°9 : Architecture de
l'automate programmable
III.4.5 Constitution de l'API
La partie intelligente de l'automate réside dans
l'unité centrale (CPU), elle est décomposé par plusieurs
éléments qui sont:
ü Le microprocesseur
D'abord, le microprocesseur est utilisé essentiellement
pour le traitement des informations, il réalise les fonctions logiques
telles que l'addition binaire, le comptage, le décomptage et d'autres
fonctions intégrées telles que la temporisation, le calcul etc.
puis, il est connecté aux autres éléments comme le
mémoire et l'interface d'E/S à travers des liaisons
parallèles appelées bus pour véhiculer les informations
sous forme binaire. Ensuite, il possède des liaisons avec
l'extérieur pour la communication avec l'outil de programmation, de
même pour le raccordement avec le terminal où sur réseau
inter automates. La zone mémoire contient toutes les données
nécessaires pour assurer fonctionnement de l'automate ainsi une liste
du jeu d'instruction qui constitue le programme.
ü Les entrées
Les entrées sont utilisées pour la
réception des données externes, plus précisément
ils reçoivent les informations à travers des capteurs où
des boutons poussoirs du système. Puis, elles sont transmissent par un
organe d'isolation galvanique vers le microprocesseur (ex :
opto-coupleur). Ensuite, elles scrutées autant de fois qu'il est
nécessaire, au moins une fois par cycle.
ü Les sorties
Sont utilisées pour l'émission des
données vers l'extérieur, en outre pour faire le relais entre
l'écran et l'imprimante. Pour plus de détails, ces sorties
reçoivent les informations dictées par le microprocesseur et les
stockés en mémoire, elles sont rafraichies au fur et à
mesure du déroulement du programme. De même, ces
sorties détectent les changements d'état des signaux
d'entrée, ils combinent ces informations suivant une séquence
préenregistrée et fournissent les signaux des sorties
adéquates.
ü Les mémoires
Les mémoires sont classifiées de la
façon suivante :
RAM (Random Acces Memory): C'est la mémoire
vivante dans laquelle on peut lire ou écrire, de sa part aussi elle est
divisée en plusieurs parties: la premiére partie est le
programme utilisateur (code binaire, assembleur), la deuxième partie
représente les données utiles au programme et la troisième
partie sont les données utiles au programmeur (programme de base,
registres, drapeaux, constantes).
ROM (Read Only Memory): C'est la mémoire morte dans
laquelle on peut lire seulement, il serve à stoker le continue de
système d'exploitation. L'EEPROM est une mémoire morte
reprogrammable avec un effacement électrique, l'EPROM et
l'UVPROM sont deux mémoires morte reprogrammable avec effacement
aux U V.
III.4.6 Fonctionnement de l'API
L'automate programmable reçoit les informations
relatives au système. Il traite ces informations en fonction du jeu
d'instruction et modifie l'état de ses informations pour commander les
prés actionneur.
- Réception : nécessaire
pour l'information d'entrées.
- Traitement : notion de programme et de
microprocesseur.
- Jeu d'instructions : notion de
stockage et de mémoire.
- Commander : notion de sortie pour
donner des ordres.
III.4.7 Critères de choix
de l'API
L'ICF a opté par un automate programmable LOGO
essentiellement pour des raisons de standardisation. Vu que ce type d'automate
a été utilisé sur le site, en plus elle a
déjà donnée une bonne satisfaction. Également, les
gents y sont formes et ont acquit une expérience. Le choix d'utilisation
d'un automate programmable industriel Logo(voir annexe B) principalement
grâce à son extensibilité qui lui offre un outil de
programmation évolué et sans oublier sa capacité
importante pour traiter un grand nombre d'E/S. L'automate LOGO fait le
même travail de séquenceur, il est moins coûteux,
automatise le travail à faire et offre un bon gain de temps.
III. Objectifs et
Contraintes
Parmi les principaux objectifs de l'utilisation de l'automate
programmable industriel LOGO est l'automatisation de la solution existant
« séquenceur numérique câble», aussi
pour minimiser la pollution de l'air et pour éliminer les effets
négatifs sur la santé des opérateurs.
Dans les deux unités, unité de séchage de
spath de fluor et unité de séchage d'alumine, il existe un
filtre de poussière câblé par un séquenceur que fait
organiser les procédures de filtrage de poussière et pour
exploiter le maximum de produit. L'API a pour rôle d'assurer la
même fonction de séquenceur numérique câblé
mais avec les contraintes attendus.
IV. Conclusion
Au cours de ce chapitre, nous avons présentés
dans un première temps nos motivations, de même nous avons
décrit en détails le sujet de notre PFE et la
problématique a été posé. Dans un deuxième
temps nous avons identifiées la solution existante (séquenceur
numérique câblé par filtre de poussière). Ainsi,
leurs avantages et leurs inconvénients sont présentés.
Pour remédier les problèmes provoqués par la solution
existante, nous avons proposées une nouvelle solution qui est
basée sur l'utilisation d'un automate programmable industrielle.
Chapitre n°3: Logiciels et outils utilisés
I. Introduction
Ce chapitre se consacré à présenter les
logiciels et les outils utilisées pour effectuer notre application. Tous
d'abord on va définir le logiciel siemens LOGO, il est utilisé
essentiellement pour réaliser notre application qui est basée sur
l'API. Ensuite la prise en main de logiciel est donnée aussi. Enfin, on
va parler du langage de programmation LADDER ainsi les étapes de
programmation.
II.
Présentation de Logiciel utilisé
II.1 Définition de
Logiciel siemens LOGO
LOGO nous permet d'exécuter des tâches dans la
technique domestique et d'installation (notamment
l'éclairage des cages d'escalier, l'éclairage extérieur,
les stores, les volets roulants, l'éclairage des devantures et bien
d'autres choses). Dans la construction des armoires de commande, des machines
et des appareils (par exemple, les commandes des portes, les installations de
ventilation, les pompes d'eau industrielle et bien d'autres choses).
II.2
Fonctionnalités de LOGO
Depuis des années, LOGO est le premier module logique
qui résout les tâches simples d'automatisme dans les domaines
tertiaire, résidentiel et l'industrielle. Sa modularité permet
de s'adapter à toutes les applications, et son logiciel LOGO Soft
Comfort facile à utiliser avec un choix de 36 fonctions
intégrées. Le contrôle et la commande s'effectuent
grâce à un écran intégré
rétro-éclairé.
II.3
Caractéristiques techniques de LOGO
Les modules de base existent avec ou sans écran pour 8
entrées et 4 sorties. Les modules d'extension permettent des
configurations jusqu'à 24 entrées, 16 sorties et 8 entrées
analogiques. La mise en réseau peut se faire sur AS-i, Eib et LON. Le
logiciel permet l'utilisation de 8 fonctions de base et 26 fonctions
spéciales. La cartouche mémoire permet de sauvegarder les
programmes.
II.4 Avantage de LOGO
LOGO permet d'économiser 50% des coûts de
réalisation en remplaçant les appareils traditionnels, en
utilisant des coffrets plus petits et en diminuant les frais de maintenance.
Aussi il nous fait économiser 70% de votre temps en réduisant le
câblage, en proposant des programmes type gratuits, en évitant les
interventions avec le passage automatiques des heures
été/hivers.
III. I. Prise en main de
LOGO
III.1 Les étapes de programmation
Siemens LOGO est un outil permet d'optimiser les performances
de système et d'économiser le temps de développement
de projet.
III.1.1 Description de l'interface de logiciel
Le logiciel de programmation Siemens LOGO est compatible avec
l'automate LOGO. Le programme avec Siemens LOGO ce fait avec la version
confort V 6.0, d'abord on va présenter le logiciel (voir figure
n°10).
Figure n°10 : L'interface de logiciel Siemens
LOGO
Barre des menus 1: Il nous propose
différentes instructions de commande pour éditer et gérer
nos programmes de commande, cela inclut les paramétrages par
défaut et les fonctions de transfert du programme de commande et vers
LOGO.

Barre d'outils "Standard"2: Cette barre (voir
figure n°11) nous permet d'accéder directement aux principales
fonctions de LOGO Soft Comfort.
Figure n°11 : Les icones de barre d'outils
"Standard"
Interface de programmation 3 : c'est le
champ de l'application à faire.
Fenêtre d'infos 4: Les
informations et des remarques seront affichées dans la fenêtre
d'infos. Les modules LOGO qui nous avons proposées via la fonction comme
modules éventuels pour notre programme de commande, sont
également mentionnes dans la fenêtre d'infos.

Barre d'état (voir figure
n°12): Elle fournit les indications sur l'outil actif,
l'état de programme, le facteur de zoom, la page du schéma de
raccordement et le module LOGO.
Figure n°12 : Les icones de
barre d'état
6 : La présente les constantes et
bornes de connexion, en plus les fonctions de base (uniquement éditeur
LOG) et des fonctions spéciales.
Barre d'outils "Outil"7 (figure n°13):
Ces icônes nous permettent de passer entre les différents modes
d'édition afin de créer où d'éditer facilement et
rapidement un programme de commande.

Figure n°13 : Les icones de
barre d'outils "Outil"
Barre d'outils "Simulation" 8: Lorsque on
appelle la commande simulation, une barre d'outils s'affiche, il contient:
ü Des icônes (p. ex. commutateurs) de commande d'
entrées.
ü Une icône de simulation d'une
panne
de réseau, permettant de tester la rémanence du circuit en
cas de défaillance de la tension du réseau,
ü Des icônes (p. ex. voyants) de supervision de
sorties.
ü Des icônes de commande de la simulation.
ü Des icônes de commande des temporisations.

Figure n°14 :L'icone de commande
"Simulation"
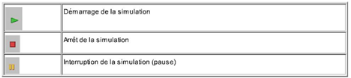
Tableau n°1 : Les icones de commande
simulation
III.1.2 Les étapes de création d'une
programmation sur logiciel
ü Etape n°1
Lorsque nous démarrons LOGO Soft Comfort V6.0,
l'interface utilisateur de LOGO Soft Comfort s'affiche. Crée sur nouveau
projet on accédant le menu fichier, ensuite on choisi l'éditeur
de programmation de CONT (Voir Figure
n°15).
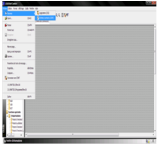 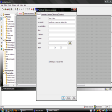
Figure n°15 : création d'un
nouveau programme
ü Etape n°2
On passe à la barre d'outils
« outil » puis on choisit l'icône de constantes et
bornes pour placer
les blocs d'entrées sorties dans l'interface de programmation.
ü Etape n°3
On passe à la barre d'outils puis on
choisit l'icône de fonction spéciale pour placer les blocs
d'E\S comme le bloc de bornes constante , le bloc de
temporisation comme bloc d'un générateur d'impulsions
asynchrone , bloc
compteur\ décompteur le bloc texte de message et le registre de
décalage dans
l'interface de programmation (voir figure
n°16).
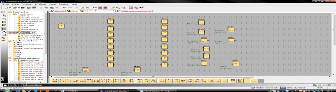
Figure n°16 : Liste de composants
nécessaires
ü Etape n°4
On passe à la barre d'outils puis on choisit
l'icône d'un connecteur pour faire la liaison
entre les blocs dans l'interface de programmation comme il est monté
dans la figure n°17.
Figure n°17: Liaison entre les blocs
ü Etape n°5
On passe à la barre d'outils
« Standard » puis on choisit l'icône organisation
automatiquement
pour organiser les blocs dans l'interface de programmation.
ü Etape n°6
Pour convertir vers l'autre éditeur différent de
l'existant quelque soit de LOGO où CONT on passe à la barre des
menus puis on choisit dans la liste « convert vers
LOG......».
ü Etape n°7
On passe à la barre d'outils et on choisit
l'icône de simulation pour simuler le programme et l'affichage des messages dans l'interface
de programmation (figure n°18).
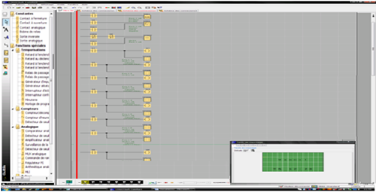
Figure n°18: la simulation du
programme
ü Etape n°8
On passe à la barre d'outils
« Standard » et on choisit l'icône de
l'enregistrement
pour enregistrer le programme (figure n°19).
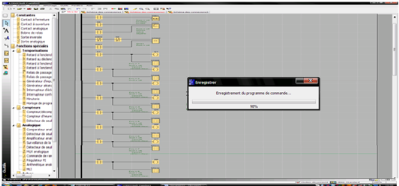
Figure n°19: Message
d'enregistrement
ü Etape n°9
On passe à la barre d'outils et on choisit
l'icône de test pour tester le programme. La figure n°20 présente un
exemple d'une application du programme.
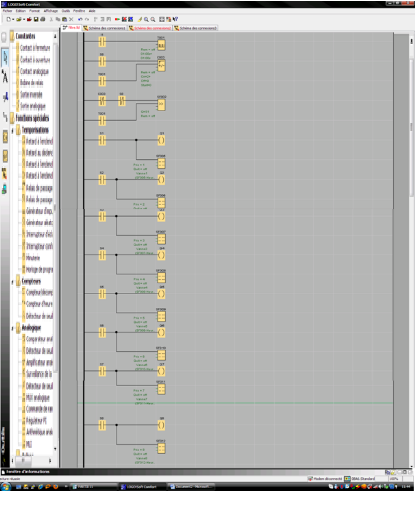
Figure n°20 : Programme d'une
application en LADDER
IV. Le langage de programmation
LADDER
IV.1 Définition de LADDER
Ladder Diagramme (LD) où Langage Ladder où
schéma à contacts est une langage graphique très populaire
auprès des automaticiens pour programmer les automates programmables
industriels. Il ressemble un peu aux schémas électriques, en plus
il est facilement compréhensible. Ladder est le mot anglais pour
échelle, figure n°21 présente un exemple de programme avec
le langage Ladder.
Figure 21: Langage de Ladder
IV.2 Origine de LADDER
L'idée initiale du Ladder est la représentation
de fonction logique sous forme de schémas électriques. Cette
représentation est originalement matérielle, quand l'automate
programmable industriel n'existait pas, les fonctions sont
réalisées par des câblages. Par exemple pour
réaliser un ET logique avec des interrupteurs, il suffit de les mettre
en série et pour réaliser un OU logique avec des interrupteurs,
il faut les mettre en parallèle. Partant de ce principe Ladder a
été créé et normalisé dans la norme CEI
61131-3. Il est très utilisé dans la programmation des Automates
Programmables Industriels.
IV.3 Principe de LADDER
Un
programme Ladder se lit de haut en bas et l'évaluation des valeurs se
fait de gauche vers la droite. Les valeurs correspondent en fait, si on le
compare à un schéma électrique, à la
présence ou non d'un potentiel électrique à chaque noeud
de connexion. En effet, Ladder est basé sur le principe d'une
alimentation en tension représentée par deux traits verticaux
reliée horizontalement par des bobines, des contacts et des blocs
fonctionnels, d'où le nom `Ladder'.
IV.4 Les composants du langage LADDER
Il existe trois types d'élément de langage
ü Les entrées (contact) permettent de lire la valeur
d'une variable booléenne.
ü Les sorties (bobines) permettent d'écrire la
valeur d'une variable booléenne.
ü Les blocs fonctionnels qui permettent de
réaliser des fonctions avancées.
IV.4.1 Les entrées (ou
contacts)
X
--| |--
Il existe deux types de contact :
ü Contact normalement ouvert (NO Normally Open)
X
--|/|--
Ce contact est fermé lorsque la variable
booléenne associée (X ici) est vraie, sinon, il est ouvert.
ü Contact normalement fermé (NC Normally Closed)
Ce contact est ouvert lorsque la variable booléenne
associée (X ici) est vraie, sinon il est fermé.
IV.4.2 Les sorties (ou bobines)
X
--( )--
Il existe de même deux types de bobines
ü Bobine normalement ouverte (NO Normally Open)
X
--(/)--
Si cette bobine est soumise à un potentiel,
c'est-à-dire qu'il existe un circuit fermé reliant cette bobine
des deux côtés du potentiel, alors la variable booléenne
associée (X ici) est mémorisée à 'vraie', sinon
elle est mémorisée à 'fausse'.
ü Bobine normalement fermée (NC Normally
Closed)
Si cette bobine est soumise à un
potentiel, c'est-à-dire qu'il existe un circuit fermé reliant
cette bobine des deux côtés du potentiel, alors la variable
booléenne associée (X ici) est mémorisée à
'fausse', sinon elle est mémorisée
à 'vraie'.
IV.5 Réalisation de
fonction logique
Comme dit précédemment, les fonctions logiques
sont dérivées de leurs réalisations électriques.
Donc chaque fonction logique (
AND,
OR,
XOR,
NAND,
NOR,
NOT) à une
représentation qui correspond à son équivalent
électrique.
Équivaut à X
AND Y
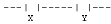
Équivaut à
NOT(X)
AND Y
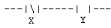
Équivaut à X
OR Y
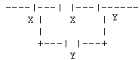
Équivaut à S = X. (Y+Z): (exemple plus
compliqué)
V. Intérêt d'utilisation du LOGO et
LADDER
Le projet consiste à commander le circuit de
poussière par l'automate programmable industriel LOGO à
l'aidé de logiciel siemens LOGO. Nous avons configurés les
étapes nécessaires de ce circuit, après certaines
modifications du schéma LADDER qui a pour rôle de visualiser le
déroulement de système et d'éliminer tous les
défauts également de gagner beaucoup des intérêts
comme simplicité d'installation, le câblage minimum, une
programmation facile.
La logique Ladder est largement utilisée pour la
programmation des l'API, avec lesquels le contrôle séquentiel des
processus de fabrication est requis. Il est utile pour les systèmes de
contrôle simples mais critiques et pour reprendre l'ancien circuit
à relais câblés, de même il a été
utilisé avec succès dans des systèmes d'automatisation
très complexes.
Le langage diagramme Ladder est rapidement implanté
pour devenir une norme en programmation d'automates industriels. Au fil de
temps, le diagramme Ladder s'est habillé de fonctions puissantes et
mieux adaptées aux progrès technologiques. Aujourd'hui, des
instructions spécialisées permettent d'effectuer des
opérations qui auraient été impossibles en logique
câblée. Bien que diagramme Ladder demeure l'un des langages les
plus adaptés pour le contrôle industriel, force est d'admettre
que certaines opérations restent difficiles à implémenter.
VI. Conclusion
L'importance de ce chapitre
réside dans la mise en évidence du rôle des
différents outils utilisés pour implanter et simuler le programme
de l'automate. En effet, ces outils nous as permis de simplifier le travail
demandé à faire, ainsi a amener à automatiser
l'application et faciliter son utilisation par les personnels de l'ICF. Donc il
nous reste à implanter l'application, ensuite le câblage et la
mise en oeuvre de l'automate programmable industrielle.
Chapitre n°4 : Automate
Programmable Industrielle Programmation Câblage et Mise en oeuvre
I. Introduction
Dans un monde plein d'évaluation technologique
où la compétitivité est l'objectif essentiel,
l'automatisation devenue une nécessité dans le monde industriel.
Dans nos travaux, l'utilisation de l'automate programmable industrielle
à pour but principale d'automatiser les systèmes industrielle que
se soit pour améliore le rendement de la production où pour
faciliter l'usage des matériels utilisés et pour remédier
les problèmes provoqués par l'ancienne technique utilisée.
Au cours de ce chapitre, on va attaquer dans un premier temps la partie
programmation en langage LADDER, que ce soit par un schéma de diagramme
CONT où un schéma de diagramme LOG. Enfin on termine nos travaux
par le câblage de l'automate programmable avec son environnement et sa
mise en oeuvre est abordée aussi.
II.
Justifications de choix de l'Automate Programmables LOGO
L'Automate Programmable LOGO est un produit de l'entreprise
Siemens, elle est prévue pour des petites applications. Elle
possède 6 entrées et 4 sorties, nous trouvons actuellement des
LOGO qui ont plus d'entrées et des sorties (par exemple 12
entrées, 8 sorties). Le tableau suivant compare les différentes
versions de l'API.
Type de LOGO
|
Alimentation et Contacts
|
Sorties
|
Version de l'automate LOGO
|
LOGO 24
|
alimentation et contacts 24 V
|
sorties transistorisées
|
version 6 entrées et 4 sorties
|
LOGO 24R
|
Alimentation et contacts 24V
|
sorties à relais
|
version 6 entrées et 4 sorties
|
LOGO 24 L
|
alimentation et contacts 24V
|
sorties transistorisées
|
version 12 entrées et 8 sorties
|
LOGO 24RC
|
alimentation et contacts 24V
|
Sortie à relais+ horloge
|
version 6 entrées et 4 sorties
|
LOGO 24RL
|
alimentation et contacts 24V
|
sorties transistorisées
|
version 12 entrées et 8 sorties
|
Tableau n°2: versions de l'automate
LOGO
Avec des sorties à relais chaque contact supporte 2 A,
l'alimentation des entrées se fait avec la même tension que celle
d'alimentation de l'automate. Le LOGO peut se programmer avec un PC, toute fois
le mode de programmation est le même, on actionne les touches du LOGO
dessiné à l'écran. Le seul avantage est de pouvoir
visualiser le programme dans son ensemble c'est pour cela on va utiliser ce
logiciel pour avoir un affichage qui permet de visualiser les états
logiques des sorties et des entrées et d'autres bloc, etc...
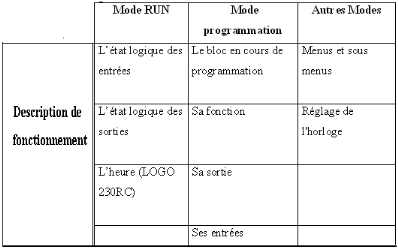
Tableau n°3: Les modes de programmation de
l'automate LOGO
On va utiliser l'automate LOGO 24L car il possède 12
entrées et 8 sorties car pour notre application on aura besoin d'une
entrée et 8 sorties pour le fonctionnement de 8 vannes. Il résout
les tâches d'automatisme dans tous les domaines, aussi sa
modularité permet de s'adapter à toutes les applications.
ü LOGO : Encore plus
puissant
Le nouveau LOGO bénéficie d'une mémoire
de programme accrue de 50 %, passant ainsi à 200 blocs fonctionnels.
ü LOGO : Plus de clarté, nouvelles
possibilités
Le nouveau LOGO garantit une transparence maximale dans la
pratique jusqu'à 50 messages sur quatre lignes avec un maximum de 32
caractères par ligne permettent une représentation clairement
structurée de tous les paramètres machines importants.
ü LOGO: Un afficheur
supplémentaire
Nous pouvons désormais raccorder au nouveau LOGO un
afficheur supplémentaire, parfaitement adapté aux exigences d'un
module logique. La liaison ne nécessite pas de module de communication,
en plus la configuration s'effectue avec le même bloc fonctionnel que
celui de l'afficheur interne.
III. Programmation
III.1 Programmation de LOGO
La programmation en logigramme est une représentation
en portes logiques et des éléments fonctionnels tels que
compteurs, horloges, relais temporisés et relais pas à pas. Elle
peut s'effectuer de trois manières différentes comme sur l'A.P.I,
à l'aide de touches où une console de programmation reliée
par un câble spécifique à l'A.P.I où bien avec un PC
et un logiciel approprié.
III.2
Langages utilisés pour la programmation
ü LADDER
Le langage LADDER utilise des symboles électriques qui
sont assemblés pour former le programme. Ce type de programmation
à l'avantage de pouvoir être utilisé par du personnel
électricien où des personnes ayant une connaissance au domaine de
schématique électrique sans pour autant apprendre un langage
spécifique. La plupart types des automates programmables industrielles
utilisent ce type de langage de programmation.
ü Diagramme (CONT) et Diagramme de blocs
fonctionnels (LOG)
LOGO Soft Conforts permet de créer des programmes de
commande de deux manières différents soit sous forme de
schéma à contacts (diagramme CONT) où sous forme de
diagramme fonctionnel (diagramme de blocs fonctionnels, LOG).
Au niveau des choix d'utilisation entre ce deux types de
diagrammes les utilisateurs sont habitués à manipuler les
schémas des connexions ont emploient le diagramme de CONT. Ainsi, ils
sont habitués à manipuler les zones logiques de l'algèbre
booléenne ont emploient le diagramme de blocs fonctionnels LOG.
ü Différence entre diagramme CONT et
diagramme LOG
Pour comprendre les différences entre l'éditeur
LOG et l'éditeur CONT il y a des règles à appliquer
pour la conversion de LOG vers CONT et inversement :
- Un bloc AND est converti en contacts en série.
- Un bloc OR est converti en contacts en parallèle.
- Les commentaires des fonctions de base ne sont pas repris
dans CONT car une fonction de base est convertie en plusieurs contacts.
- L'attribution invoque d'un commentaire n'est alors plus
possible.
- Les commentaires des entrées sont affectés
dans CONT à tous les contacts de cette entrée.
- Les commentaires libres ne sont pas repris car leur position
dans le schéma des connexions ne peut pas être
déterminée à l'aide des blocs.
- Les blocs XOR doivent être convertis en structures
CONT composées de contacts et contacts inverses.
La figure n°22 présente ci-dessous
permet de convertir le schéma des connexions de LOG en CONT

Figure n°22: Symbole de conversion du CONT vers
LOG
Un exemple de programme de notre application par les
deux diagrammes est expliqué dans la figure suivante :
Editeur CONT
Editeur LOGO
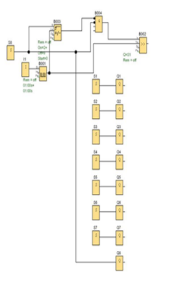
Figure n°23 : Exemple
d'application
III.3 Blocs
utilisés
Pour la réalisation de notre application, nous avons
utilisé le langage à contact (LADDER), c'est type de langage
peut être considéré comme une transcription directe du
schéma électrique à contacts vers un langage de
programmation. Le langage LADDER à contact utilise des symboles
représentant des contacts ouverts et fermés assemblés en
série. Par la suite, le programme sera exécuté ligne par
ligne en commençant par la ligne supérieure, chaque ligne se lit
de la gauche vers la droite et on terminant par le symbole d'affectation
où en parallèle de manière à représenter
les conditions de fonctionnement.
III.3.1 Contact à fermeture
Comme les contacts à ouverture et les contacts
analogiques, les contacts à fermeture (voir figure n°24)
eux-mêmes représentent les bornes des entrées de module
LOGO. Lorsque nous plaçons le symbole de contact dans notre
schéma des connexions, une fenêtre s'affiche qui nous permettons
de définir dans cette boite de dialogue de quelle entrée
s'agit-il. En fonction de bloc dans le schéma une fenêtre
s'affiche nous permettant d'effectuer des modifications. LOGO nous permet de
sélectionner un niveau fixe pour l'entrée, la modification de
l'entrée du schéma des connexions CONT se fait par double-clic
sur, par la suite une fenêtre s'affiche qui nous permes d'y effectuer
les modifications.
Figure n°24 : symbole d'un contact à fermeture
III.3.2 Contact à ouverture
Comme les contacts à fermeture et les contacts
analogiques, les contacts à ouverture (voir figure n°25)
eux-mêmes représentent les bornes d'entrée de module LOGO.
Lorsque nous plaçons le symbole de contact dans notre schéma des
connections, une fenêtre s'affiche qui nous permettons de définir
dans cette boite de dialogue de quelle entrée s'agit-il. En fonction de
notre LOGO nous pouvons sélectionner un niveau fixe pour
l'entrée. La modification de l'entrée d'un schéma des
connexions CONT, se fait par double-clic sur le bloc dans le schéma,
donc une fenêtre s'affiche qui nous permettant d'y effectuer les
modifications.
Figure n°25 : symbole d'un contact à
ouverture
III.3.3 Bobine à relais
Comme les sorties inversées et les sorties
analogiques, les bobines à relais (voir figure n°28)
eux-mêmes représentent les bornes de sortie de module LOGO. La
modification de la sortie du schéma des connexions CONT, se fait par un
double-cliquez sur le bloc dans le schéma, une fenêtre s'affiche
qui nous permettent d'affecter les différentes fonctions à la
sortie.
Figure
n°26 : symbole d'une bobine à relais
III.3.4 Générateur d'impulsions
asynchrone
Le type d'impulsion de la sortie peut être
modifié par le rapport du paramétrable impulsion/Pause.
Figure n°27 : Symbole d'un générateur
d'impulsions asynchrone
III.3.5 Compteur \décompteur
En fonction du paramétrage, une impulsion
d'entrée incrémente ou décrémente par une valeur de
comptage interne. La sortie est mise à 1 où 0 lorsque les
valeurs de seuil paramétrées sont atteintes. Une entrée
Dir permet d'inverser le sens de comptage.
Figure n°28: symbole d'un Compteur
\décompteur
III.3.6 Registre de décalage
Le registre de décalage, son symbole est
montré dans la figure n°29, en nous permise de lire la valeur d'une
entrée et le décaler par un bit. La valeur de la sortie
correspond à celle du bit du registre de décalage ayant
été paramétré. Le sens de décalage peut
être modifié grâce à une entrée
spécifique.
Figure n°29: symbole d'un registre à
décalage
III.4 Implantation de programme de notre application
Le filtre de poussière utilisé contient 8
vannes à manches, il est manipulé par un séquenceur
numérique qui contient deux temporisateurs un pour le temps d'injection
et l'autre pour le temps de repos. Il est alimenté par 220V, en plus il
possède 8 sorties pour les vannes et une sortie commune pour minimiser
l'encombrement de câblage. Ce séquenceur est asservi par un
ventilateur de tirage qui lui permet la mise en marche c'est-à-dire que
cet appareil essaie de remplir la chambre d'air bouchonnée par une
membrane qui contient un petit trou sert à détecter l'existence
de l'air nécessaire pour laisser son passage aux vannes un par un. Ceci
pour faire l'opération de secouage de poussière pour nettoyer les
manches, assurer le bon fonctionnement de système et essayer
d'éliminer toutes possibilités de colmatage de manches par une
grande quantité de poussier.
Initialement le filtre poussière est commandé
par un séquenceur numérique mais à cause l'importance de
l'automate et ces nombreux avantages, on a remplacé cette
séquenceur par un automate programmable industrielle. L'automate assure
la même travaille faite par le séquenceur mais il est moins
coûteux aussi il automatise le programme à faire, il offre un gain
de temps pour le temps de manipulation. Ainsi il fait adapter la tension
convenable au besoin de filtre.
La figure ci-contre présente un exemple de programme en
LADDER de notre application, vous trouvez en détaille dans l'Annexe C
tous les exemples faites, le commande de 8 vannes.
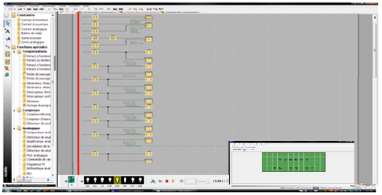
Figure n°30 : Commande de vanne numéro
5
IV. Câblage de l'automate
programmable
IV.1 Description
Les modems et le port COM de l'ordinateur utilisés
sont configurés conformément à la description.
Après l'établissement de la liaison Télé
service, on peut utiliser les fonctions habituelles, par exemple
transférer le programme utilisateur, changer le mode de fonctionnement
de la CPU où exécuter des tests en ligne.
IV.2
Validité
Avec la série LOGO 0BA6, une liaison modem
analogique entre un PC et le Module LOGO de base 0BA6 est
supportée. La connexion de modem ne peut être configurée
qu'avec le logiciel LOGO Soft Comfort à partir de V6.1, pour
actualiser la version de V6.0 en V6.1 il faut utiliser un centre de mise
à jour dans le menu d'aide du LOGO Soft Comfort.
IV.3 Connexion des composants
Hardware Pour Connecter LOGO et le PC par un
modem 56k sur un réseau téléphonique analogique il faut
se connecter à un modem analogique local et à modem analogique
décentralisée en utilisant un réseau
téléphonique public (PTSN), nous trouverons dans la figure
ci-dessous les informations nécessaire sur la connexion des composants.
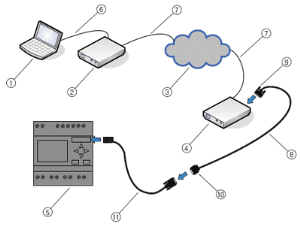
Figure n°31 : Schéma de câblage
de l'automate programmable industrielle
ü (1) PC (Desktop ou Laptop)
ü (2) Modem analogique local (recommandé
: modem INSYS)
ü (3) PSTN (réseau
téléphonique public)
ü (4) Modem analogique
décentralisé (recommandé : modem INSYS)
ü (5) Module de base LOGO
ü (6) Câble RS232 (9-points)
ü (7) Connexion téléphonique
RJ11
ü (8) Câble modem LOGO (Longueur: 0,5
m)
ü (9) et (10) Connecteur avec le texte
visible "MODEM" et "PC CABLE"
ü (11) Câble PC LOGO
IV.4 Informations
complémentaires Les modems analogiques doivent
remplir les conditions suivantes :
ü Communication par 11 bits (8 bits de
données, 1 bit Stop, 1 bit de parité paire).
ü Capacité de traitement des commandes AT standard
ou commandes de fonction AT standard.
ü Le modem connecté au LOGO doit fournir un
courant au moins de 5 mA par l'intermédiaire du borne 1 de l'interface
RS232 (modem INSYS).
IV.5 Adaptation du port COM
ü Par la commande « Démarrer =>
Paramètres => Panneau de configuration =>
Système », allons dans le menu
« Propriétés système »
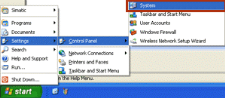
ü Dans la boite de dialogue
« Propriétés système », cliquons sur
l'onglet « Matériel » puis le bouton
« Gestionnaire de périphériques ».
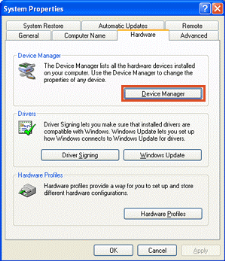
Dans l'arborescence « Gestionnaire de
périphériques », nous allons jusqu'à la ligne
« Ports (COM et LPT) », avec un clic droit de souris, le
menu contextuel du port COM utilisé (COM1) puis sélectionnons la
commande « Propriétés ».
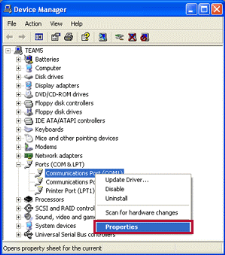
ü Dans la boîte de dialogue «
propriétés du port COM » choisi, nous adaptons les
paramètres dans l'onglet « Paramètres du
port ».
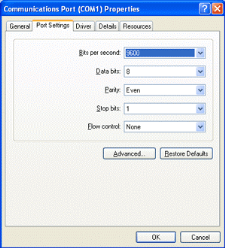
ü Validons par OK pour prendre en compte l'adaptation et
les modifications des paramètres.
IV.5.1 Configuration et établissement de la
liaison Télé service
Pour la création d'une liaison Télé
service analogique entre le PC et un module de base LOGO, veuillons
procéder la manière suivante.
ü Informations modem
· Sélectionnons dans la barre de menu du
logiciel LOGO Soft Comfort l'icone « Outils » puis
choisissons la commande « Etablissement de la connexion
modem »
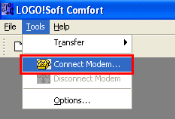
· L'assistant de connexion de modem est
démarré et il vous guide étape par étape. Pour
commencer cliquons sur le bouton « Suivant ».
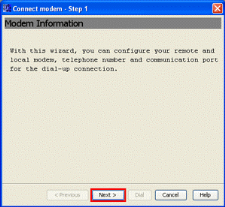
Cette description présente une première de
configuration nécessaire pour les modems et la liaison
téléphonique. D'autres informations sur ce thème se
trouvent dans l'aide « Outils => Connecter
modem ».
ü Sélection du modem
· Activons l'icone «Modem distant » pour
la configuration du modem décentralisé, puis cliquons sur le
bouton « Suivant ».
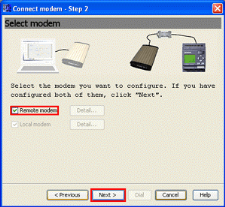
· Le dialogue de configuration de modem local est
appelé automatiquement par l'assistant de liaison modem lors d'une
première configuration.
· D'autres informations sur ce thème se trouvent
dans l'aide « Outils => Connecter modem » puis
« Sélectionner modem »
ü Sélection de la configuration
décentralisée
· Pour créer une nouvelle configuration pour notre
modem distant, sélectionnons l'option « Créer une
nouvelle configuration », ensuite cliquons sur
« Suivant ».
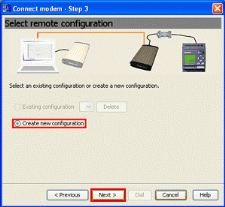
· Si aucune configuration n'est disponible (par exemple lors
d'une première utilisation de l'assistant de modem), la seule option
disponible est « Créer une nouvelle configuration ».
· D'autres informations sur ce thème se trouvent dans
l'aide « Outils =>
Connecter modem » puis Sélectionnons
« configuration décentralisée ».
IV.5.2 configuration des commandes pour le modem
distant
Dans l'espace « Nom de
modem », indiquons un nom pour la configuration du modem distant
(ici:"INSYS Remote"). La configuration pourra être assignée
ultérieurement aux modems respectifs. Activons l'option
« Standard » pour reprendre les réglages par
défaut afin de commander de modem. Enfin n'oublions pas d'enregistrer
nos réglages en cliquant sur le bouton « Sauvegarder la
configuration » sous le nom donné au modem, puis cliquons sur
le bouton « Suivant » pour passer à
l'étape suivante.
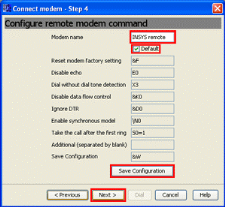
D'autres informations sur ce thème se trouvent dans
l'aide sous « Outils => Connecter modem » puis
Sélectionnons la commande « configuration
décentralisée ».
IV.5.3 Configuration du modem distant
Pour configure le modem distant, il faut le connecter par un
câble RS232 au port COM de votre PC. Pour cela positionnons la case
à cocher « Terminé » et sélectionnons
l'interface de connexion (port COM) utilisée et transférons la
configuration dans le modem distant par le bouton « Configurer le
modem distant ».
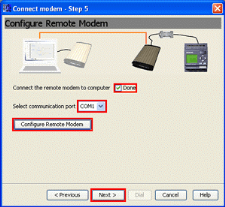
Relions notre LOGO au réseau
téléphonique, comme décrit sous Connexion des composants
Hardware. Faisons attention aux repères des connecteurs du câble
modem LOGO. La configuration enregistrée dans le modem est
conservée aussi après une coupure de tension. Pour d'autres
informations sur ce thème se trouvent dans l'aide sous
« Outils => Connecter modem => Configurer modem
décentralisé ». Pour créer
une nouvelle configuration pour notre modem local, sélectionnons
l'option « Créer une nouvelle configuration »,
ensuite cliquons sur le bouton « Suivant ».
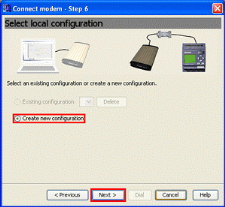
Si aucune configuration n'est disponible (par exemple lors
d'une première utilisation de l'assistant de modem), la seule option
disponible est l'option "Créer une nouvelle configuration". De
même, d'autres informations sur ce thème se trouvent dans l'aide
sous « Outils =>Connecter modem » puis
Sélectionner l'option « configuration locale ».
IV.5.4 Configuration des commandes pour modem local
Dans la zone « Nom de modem », indiquons
un nom pour la configuration du modem local (ici: "INSYS local"), la
configuration aussi pourra être assignée
ultérieurement aux modems respectifs. Pour reprendre les
réglages standards de la commande du modem il faut activer l'option
« Standard », n'oublions pas d'enregistrer nos
réglages en cliquant sur le bouton « Sauvegarder la
configuration » sous le nom donné au modem. Pour passer
à l'étape suivante cliquons sur le bouton
« Suivant ».
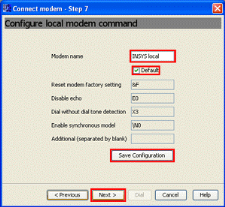
Les utilisateurs expérimentés peuvent s'adapter
individuellement pour commander le modem distant. De même, d'autres
informations sur ce thème se trouvent dans l'aide sous
« Outils => Connecter modem => Configurer commande pour
modem local ».
ü Configuration du numéro de
téléphone
Accédons au tableau le numéro de
téléphone du modem décentralisé avec la commande
« Ajouter ». Pour une attribution univoque, donnons un nom
et une description pour cette connexion. Nous pouvons enregistrer plusieurs
numéros de téléphone parmi lesquels nous choisirons le
numéro souhaité.
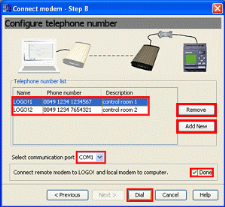
Pour entrer des données dans le tableau,
utilisons la commande « Ajouter » puis cliquons dans le
champ respectif et confirmons notre saisie avec la touche
« Entrée ». Ainsi, nous pouvons effacer des lignes
du tableau en les sélectionnant, puis en utilisant le bouton
« Supprimer ». Nous trouverons des informations sur ce
point dans l'aide sous « Outils => Connecter modem =>
Configurer le numéro de téléphone».
ü Établissement de la liaison
Télé service
Connectons le modem local par un câble RS232 au port
COM de votre PC et sur une ligne téléphonique analogique par un
câble de liaison téléphonique RJ11, ensuite positionnons la
case à cocher « Terminé » et
sélectionnons l'interface de connexion (port COM) utilisé, le
bouton « Composer » doit être actif.
Sélectionnons l'enregistrement de la liste des numéros de
téléphone et établissons par la commande
« Composer » une connexion de Télé
service avec le LOGO Souhaité.
ü Coupure de la liaison Télé
service
Le déconnection de la liaison Télé
service se fait par la commande « Déconnecter
modem » trouve la l'icone « Outils ».
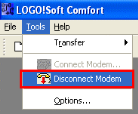
Nous trouverons des informations supplémentaires sur ce
point dans la zone « Outils => Déconnecter modem ». Le
logiciel LOGO Soft Comfort met à notre disposition un outil d'aide des
informations complémentaires sur chaque étape. Nous trouverons
l'aide dans la barre de menu sous « Aide => Sommaire ».
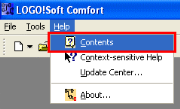
Sélectionnons le menu « Sommaire »
et naviguons dans l'arborescence par « Interface utilisateur
=> Barre de menus => Menu Outils » vers le point
« Outils => Connecter modem => ... (puis chacun des
sous-menus)".
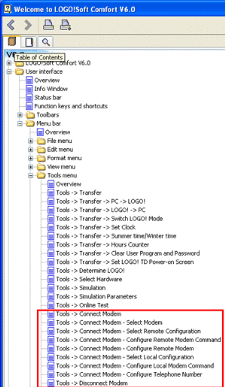
La Possibilités d'accès au LOGO par une liaison
Télé service après avoir établi une liaison vers
le LOGO via le réseau téléphonique se fait par
l'utilisation comme d'habitude des fonctions du logiciel LOGO Soft
Comfort. Nous pouvons également transférer le programme
utilisateur, change le mode de fonctionnement de la CPU ou exécuter des
tests en ligne.
IV.5.5 câblage de LOGO (RS232) à un PC
Pour connecter 'un câble LOGO à un ordinateur,
celui-ci doit normalement disposer d'une interface série (RS232).
Certains récents PC sont munis seulement de ports USB (USB = universel
serial bus) dans ce cas il faut un convertisseur pour établir la liaison
entre le câble LOGO et l'interface USB du PC. Donc il faut
décrire les différentes étapes nécessaires à
l'utilisation d'un convertisseur USB-RS232. Le convertisseur est fourni avec un
CD ou une disquette contenant le logiciel à installer sur le PC.
Après avoir enfiché le convertisseur USB sur l'interface USB de
notre PC, nous pouvons installer le pilote, pour cela, insérons le CD ou
la disquette dans le lecteur adéquat. Enfin suivons les instructions
fournies par l'assistant d'installation. Prenons garde à indiquer la
bonne version de notre système d'exploitation Windows.
IV.5.6 Raccordement d'un LOGO avec un PC
Lors du raccordement de module logique LOGO à un
PC/PG, il faut éviter de nombreux problèmes, pour cela il fait
suivre les informations données ci-dessous
ü Raccordement le LOGO à l'interface
série de votre PC avec un câble PC
Si la liaison est effectuée via l'USB, il faut utiliser
donc un convertisseur USB RS232C en plus un Câble PC. Si une erreur
apparaît avec ce convertisseur ou avec ce pilote, voulons-nous
référer à notre fournisseur de ces composants.
ü Mettre votre LOGO en mode de fonctionnement
- LOGO Basic jusqu'à la référence
0BA2
Basculons notre LOGO en mode de transfert au moment du
démarrage avec le câble PC connecté dessus à la mise
sous tension, aussi nous pouvons basculer en mode transfert sans avoir besoin
de couper l'alimentation pour cela mettre notre LOGO de RUN en mode
STOP en appuyant simultanément les touches ?, ? et OK. De
même, laissons-nous guider avec le menu qui s'affiche et utiliser les
touches du pupitre comme le montre l'image ci contre : 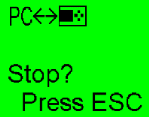
- LOGO Basic jusqu'à la référence
...-0BA3
Mettons notre LOGO en mode transfert en appuyant sur la touche
ESC de votre appareil se trouvant en mode RUN, ensuite laissons nous guider par
le menu qui s'affiche et utiliser les touches du pupitre.
- LOGO Basic à partir de la
référence ...-0BA4
Le transfert des données est possible si le LOGO est en
mode STOP et ne se trouve pas dans le menu dialogue, nous pouvons le faire
à partir du menu d'affichage. Nous pouvons arriver à ce
menu, par exemple en appuyant sur le bouton ESC de notre LOGO qui se
trouve dans l'état RUN, ensuite laissons nous guider par le menu qui
s'affiche et utiliser les touches du pupitre pour le passer en mode STOP. Si le
transfert des données est initialisé sur le PC
équipé du logiciel LOGO Soft Comfort, le LOGO passera
automatiquement en mode transfert et l'afficheur nous le montrera comme nous
pouvons le voir sur l'image ci-dessous. 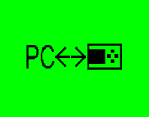
- LOGO Pure jusqu'à la référence
0BA3
Basculons notre LOGO en mode transfert au moment du
démarrage avec le câble PC connecté dessus à la mise
sous tension. Après le démarrage, si le câble PC n'est pas
raccordé sur le LOGO, le mode RUN bascule automatiquement si un
programme valide est présent dans l'appareil.
- LOGO Pure à partir de la référence
0BA4
Si un câble PC est raccordé sur l'appareil, le
logiciel LOGO Soft Comfort peut initialiser le transfert entre le LOGO et le
PC. Si le module logique est en RUN, le logiciel LOGO Soft Comfort
demandera si nous souhaitons le basculer en mode STOP. Après le
démarrage sans câble PC connecté au LOGO, celui ci
bascule automatiquement en mode RUN si un programme valide y est
présent. Assurons nous que l'interface COM sélectionnée
n'est pas utilisée par une autre application .Si c'est le cas, nous
obtiendrons le message d'erreur ci-dessous.

Dans cette fenêtre d'information du logiciel LOGO! Soft
Comfort vous êtes informé du non disponibilité de
l'interface. Et donc veuillons fermer l'autre application et assure que
l'interface COM que nous avons définie dans le logiciel LOGO Soft
Comfort est celle que nous avons connectée au module logique en
utilisant le câble PC. Si nous avons définie la mauvaise
interface, nous obtiendrons cette fenêtre d'erreur :

Dans le menu « Outils => Choix du
matériel», dans le champ « Choix du
matériel » tous les types et versions de LOGO qui ne
supportent pas les fonctions programmées où le
paramétrage, apparaissent en grisés et par
conséquent ne peuvent pas être utilisés pour notre
application souhaitée. Modifier notre programme applicatif ou utiliser
un module logique adéquat. Dans le champ
« Ressources » de la fenêtre « Choix du
matériel » dans la partie du haut nous trouverons
affiché la contradiction entre la programmation, le paramétrage
et le module logique choisi si nous choisissons un module en grisé.
V. Identification de notre application: Câblage
de l'automate avec le filtre
Les éléments constituant l'automate programmable
industriel LOGO sont particulièrement robustes par l'absence de
mécanique tournante pour le refroidissement et le stockage des
données. Également ils permettent de fonctionner dans des
environnements particulièrement hostiles (poussière, vibrations
des supports, variations de température, ...). Ils possèdent des
circuits électroniques optimisés pour s'interfacer avec les
entrées et les sorties physiques du système, les envois et les
réceptions de signaux se font très rapidement avec son
environnement. Avec plus d'exécution séquentielle cyclique sans
modification de mémoire, ils permettent d'assurer un temps
d'exécution maximal, respectant un déterminisme temporel
et logique, également ils garantissent un temps réel effectif
(le système réagit par un délai fixé). En
contrepartie, ils sont beaucoup plus chers que des solutions informatiques
classiques mais restent à l'heure actuelle les seules plateformes
d'exécution considérées comme fiables au milieu
industriel.
Après le transfert de programme de PC vers l'automate
LOGO par un câble USB (RS 233) et la validation d'existence de programme
dans cette automate, on va câbler l'automate avec l'alimentation et le
filtre de poussière.
Dans le schéma ci-dessous on va présenter notre
automate LOGO, au même temps on essaye de montrer son câblage avec
la tension d'alimentation pour l'entrée I1 qui est égale
à 24 V et pour les 8 sorties qui est égale à 220V qu'ils
sont reliés par les vannes. En remarquant qu'il y a une sortie commune
pour la deuxième phase de sorties qui assure la diminution
d'encombrement de câblage.
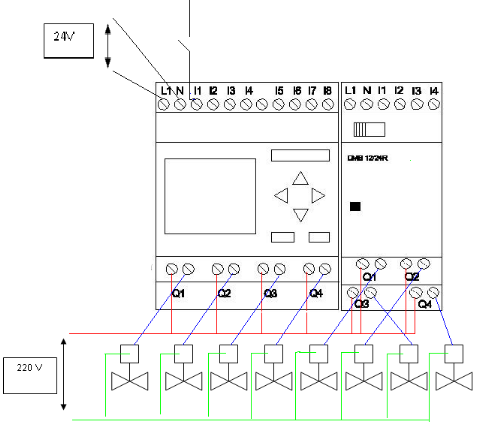
Figure n°34 : Schéma de câblage
de l'automate LOGO par le filtre
NB : on a fait le câblage de l'automate avec
l'autokad (voir l'annexe D)
I.
Conclusion
Premièrement la réalisation de programme de
notre application avec le langage de programmation avec LADDER a
été décrite dans le but de développer un algorithme
d'automatisation, que ce soit par un schéma de diagramme CONT où
un schéma de diagramme LOG. En effet cet automate programmable
présente une solution adéquate, vue son extensibilité pour
commander notre système qui possède un nombre des entrées
et des sorties très important. Ensuite le câblage et la mise en
oeuvre cet automate avec le filtre de poussière sont achevés
aussi.
Conclusion et perspective
Les objectifs des travaux réalisés consistaient
à identifier la solution existante, séquenceur numérique
câblé par un filtre de poussière, qui a pour rôle de
commande le fonctionnent de filtre de poussière, puis de remplacer cette
solution par une autre plus efficace et surtout plus automatisée
basé sur l'utilisation d'un automate programmable industrielle LOGO.
Actuellement le filtre de poussière est commandé
par un séquenceur numérique AUXITROL type ESD 900, ce
séquenceur provoque certains problèmes liés aux
difficultés de manipulation et l'absence des modules de communication
permettant à ce séquenceur de se connecter à une
supervision.
Les travaux déjà faite au cours de stage
consiste tous d'abord à la description et l'identification de
séquenceur numérique câblé par un filtre de
poussière. Par la suite une solution plus automatisée et plus
performante a été proposée dans le but de remédier
les inconvénients de l'ancien technique, également les
justifications des choix de l'automate programmable parmi plusieurs sont aussi
décris. Enfin nous avons fini nos travaux par la partie programmation de
l'application, de même le câblage de l'automate programmable.
Un point n'a pas été traité, mais il ne
cause pas de grand problème pour la validation de nos travaux, cette
point est la mise en ouvre de l'automate programmable, c'est grâce au non
disponibilité de l'automate programmable dans la société
au sien de la quelle nous avons effectuée notre stage de PFE.
Sommaire
Introduction générale
Erreur ! Signet non
défini.
Chapitre n°1: Présentation de
la société
2
I. Introduction
2
II. Présentation de l'ICF
2
III. Cycle de production
2
IV. Organigramme de la société
l'ICF
6
IV.1 Service informatique
7
IV.2 Service régulation
électrique
7
V. Conclusion
7
Chapitre n°2: Présentation du
contexte de travail
8
I. Introduction
8
II. Motivation
8
III. Description détaille de
sujet
9
III.1 Avis général
9
III.2 Problématiques de la solution
existante
10
III.3 Présentation de la solution existante:
Séquenceur Numérique Câblé
11
III.3.1.1
Généralité sur le séquenceur
11
III.3.1.2 Guide d'utilisation de
séquenceur
11
III.3.2.2 Caractéristiques technique de
filtre
12
III.3.2.3 Applications de filtre
12
III.3.2.4 Avantages du filtre de
poussière
13
III.4 Présentation de la solution
proposées: Automate programmable
13
III.4.1 Historique de l'API
13
III.4.2 Définition de l'API
14
III.4.3 Avantages de l'API
14
III.4.4 Architecture de l'API
15
III.4.5 Constitution de l'API
15
III.4.6 Fonctionnement de l'API
16
III.4.7 Critères de choix de l'API
16
IV. Objectifs et Contraintes
17
V. Conclusion
17
Chapitre n°3: Logiciels et outils
utilisés
18
I. Introduction
18
II. Présentation de Logiciel
utilisé
18
II.1 Définition de Logiciel siemens
LOGO
18
II.2 Fonctionnalités de LOGO
18
II.3 Caractéristiques techniques de
LOGO
18
III. Prise en main de LOGO
19
III.1 Les étapes de programmation
19
III.1.1 Description de l'interface de logiciel
19
III.1.2 Les étapes de création
d'une programmation sur logiciel
21
IV. Le langage de programmation LADDER
23
IV.1 Définition de LADDER
23
IV.2 Origine de LADDER
23
IV.4 Les composants du langage LADDER
24
IV.4.1 Les entrées (ou contacts)
24
IV.4.2 Les sorties (ou bobines)
24
IV.5 Réalisation de fonction logique
25
VI. Conclusion
26
Chapitre n°4 : Automate
Programmable Industrielle Programmation Câblage et Mise en
oeuvre
27
I. Introduction
27
II. Justifications de choix de l'Automate
Programmables LOGO
27
III.1 Programmation de LOGO
29
III.2 Langages utilisés pour la
programmation
29
III.3 Blocs utilisés
30
III.3.1 Contact à fermeture
31
III.3.2 Contact à ouverture
31
III.3.3 Bobine à relais
31
III.3.4 Générateur d'impulsions
asynchrone
32
III.3.5 Compteur \décompteur
32
III.3.6 Registre de décalage
32
III.4 Implantation de programme de notre
application
32
IV. Câblage de l'automate
programmable
33
IV.1 Description
33
IV.2 Validité
33
VI. Conclusion
44
Conclusion et perspective
45
|