2.2. Le Sable
Le sable est le constituant du squelette granulaire qui a le
plus d'impact sur les qualités du béton et du mortier.
Il joue un rôle primordial en réduisant les
variations volumiques, les chaleurs dégagées et le prix de
revient des bétons. Il doit être propre et ne pas contenir
d'éléments nocifs. Il convient de se méfier de la
présence de sables granitiques, de micas en paillettes, d'argiles, de
sulfates...et dans le cas de sable concassé: des poussières, des
plaquettes, des aiguilles.
Dans notre étude expérimentale, nous avons
utilisé un sable normalisé (SABBIA NORMALE STANDARD SAND)
certifié CEN, EN 196-1 conforme ISO 679 :2009
Un sable normalisé, est un sable naturel, siliceux
notamment dans ses fractions les plus fines. Il est propre, les grains sont de
forme généralement isométrique et arrondie. Il est
séché, criblé et préparé dans un atelier
moderne offrant toutes garanties de qualité et de
régularité dans le laboratoire d'essais des matériaux de
la ville de paris contrôlé par le L.E.M.V.P.
Le sable est conditionné en sachets de
polyéthylène contenant chacun 1 350 #177; 5 g.
2.3. La pouzzolane naturelle
La pouzzolane utilisée est une pouzzolane naturelle de
provenance du gisement de Bouhamidi (Béni-Saf), extraite à la
côte 210 km et fournie par la cimenterie de zahana en quantité
suffisante pour nos besoins d'élaboration sur le plan
expérimental. Cette pouzzolane est fournie sous forme de roches
concassées de type pierre ponce et scorie de diamètres variant de
5 à 10 mm. Pour pouvoir la substituer au ciment CPA de Zahana, nous
avons d'abord procédé à son étuvage à 105
°C afin d'éliminer toute éventuelle humidité et
faciliter son broyage. Nous l'avons ensuite complètement broyé
puis passé au tamisage.
L'ensemble du tamisât du tamis de dimension 0.063 mm est
récupéré et utilisé en substitution au ciment
à différentes propositions
7. Préparation des matières
premières
ü Concassage du clinker.
ü Ajout du gypse et pouzzolane.
ü Broyage du ciment préparé.
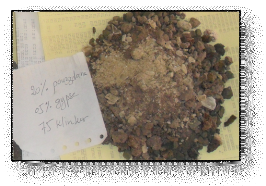
Figure 3 : Préparation
mélange (clinker +pouzzolane + gypse)
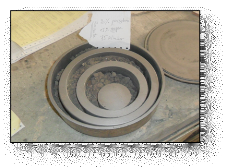
Figure 4 : Broyage de mélange
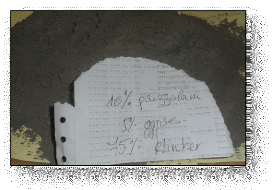
Figure 5 : Produit finale après
broyage
Le ciment préparé est conditionné en
sachets de polyéthylène contenant chacun 1 500 #177; 5 g.
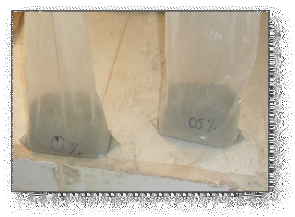
Figure 6 : Ciment conservé dans
sachets de polyéthylène
Nous utiliserons des mortiers normaux, selon la norme
NFP 15-403 dont la composition est la suivante :
ü 450g de liant, les ajouts étant toujours
introduits en substitution du ciment.
ü 1350g de sable normalisé.
Ceci correspond donc à un rapport sable/ciment
égal à 3.
-Le taux de l'eau de gâchage à été
maintenu constant pour l'ensemble des gâchées : E/C = 0.5
- Le mortier normal est réalisé à l'aide
d'un malaxeur HOBART dans une cuve de cinq litres répandant aux
caractéristiques de la norme NF P 15-411.
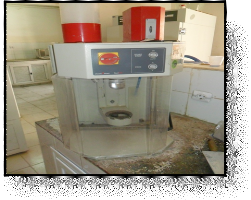
Figure 7 :
malaxeur normalisé pour pâte et mortier
La procédure de malaxage est celle
préconisée dans la norme NF P 15
ü Le liant +la vitesse de 140 tours/min pendant une
minute.
ü Le sable est ensuite ajouté.
ü Un malaxage de 3 minutes à la vitesse de 280
tours /min est réalisé.
ü Après l'arrêt du malaxage, on effectue un
raclage manuel des pa
ü Enfin, le cycle se termine par un malaxage de trois
minutes à 280 tours/min.
Nous avons élaboré les séries
d'éprouvettes suivantes :
Des moules normalisé permettant de réaliser 3
éprouvettes prismatiques de section carrée 4cm×4cm et de
longueur 16cm (40×40×160mm)
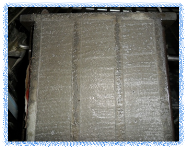 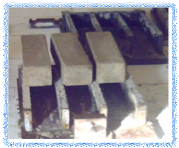
Figure 8 : Moules pour éprouvettes
de mortier
Un appareil de chocs permettant d'appliquer 60 chocs aux
moules en les faisant chuter d'une hauteur de 15 mm #177; 0.3 à la
fréquence d'une chute par seconde pendant 60s.
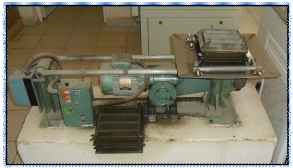
Figure 9 : Appareil à chocs
ü Une chambre ou une armoire humide Maintenue à
une température de 20 °C #177; 1 °C et à une
humidité relative supérieure à 90 %
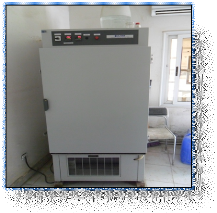
Figure 10 : Armoire humide
ü Les éprouvettes sont conservées dans
l'eau dans armoire humide comme suivant :
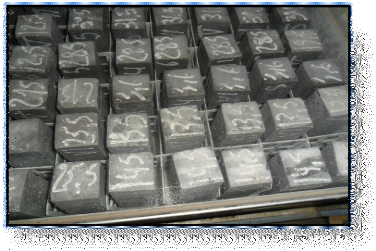
|