III.1 Introduction
Au titre du chapitre (III), nous verrons les principaux
résultats retrouvés durant nos travaux qui ont conduit à
la réalisation de notre capteur de gaz. A savoir les performances du
mini four, ainsi que l'élément sensible aux gaz formé par
l'oxyde de zinc non dopé et dopé à l'aluminium (1 et 3%)
et au cuivre (1%).
III.2 Dimension du capteur de gaz obtenu
Selon le motif proposé au départ, nous avons obtenu
un capteur de gaz possédant la dimension indiquée sur la figure
III.1.
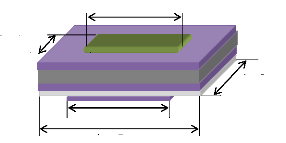
L" = 3 mm
l = 1 mm
l = 2 mm
L' = 3 mm
L = 5 mm
Figure III.1. Géométrie du capteur
de gaz réalisé en technologie des couches minces.
III.2.1 Mesures d'épaisseur et de résistance des
couches minces métalliques
A partir de la technique dite des quatre pointes aligné
(ou Wanner) décrites dans le chapitre précédent, et selon
le temps de dépôt, nous avons obtenus les résultats
suivants :
Tableau III.1. Mesure des épaisseurs
des couches minces métallique.
Echantillons
|
Temps de dépôt (min)
|
Epaisseur des plaques chauffantes (nm)
|
Résistance des mini fours (?)
|
S1
|
15 min (Ni) + 15min (W)
|
eNi 37 nm, eW 14 nm ~ 51 nm
|
R0 (Ni/W) = 72 ?
|
S2
|
30 min (Ni) + 30 min (W)
|
eNi 78 nm, eW 27 nm ~ 105 nm
|
R0 (Ni/W) = 7 ?
|
Remarque 1 :
Les valeurs des résistances ont été
mesurées par la méthode directe à partir du dispositif de
test du capteur décri dans le chapitre précédent.
III.2.2 mesure d'épaisseur des couches minces
d'oxyde de silicium formée par oxydation thermique
Le microscope électronique à balayage (MEB) nous
a permis d'estimé l'épaisseur de l'oxyde de silicium (SiO2)
formé par oxydation thermique. Comme l'indique la figure III.2 et dont
les valeurs sont indiquées dans le tableau III.2.
Tableau III.2. Mesure des épaisseurs de
l'oxyde de silicium.
Si poly + SiO2
|
Epaisseur
|
Substrat de Si poly pur
|
230
|
~ 240 um
|
Substrat de Si poly pur restant
|
|
160 um
|
SiO2 face du substrat
|
|
80 um
|
SiO2 dos du substrat
|
|
30 um
|
Si + SiO2
|
300 um
|
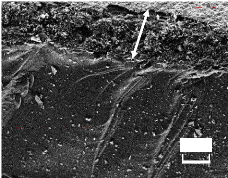
Si poly-cristallin
e = 80 um
16 um
ZnO
Figure III.2. Image MEB
de l'épaisseur de la couche de SiO2 coté face du substrat
de Si, IM x 300.
III.2.3 Mesure d'épaisseur des couches minces
d'oxyde de zinc non dopé et dopé
Le microscope électronique à balayage (MEB) nous
a permis aussi d'estimer l'épaisseur de l'oxyde de zinc (ZnO) non
dopé et dopé déposé par pulvérisation
cathodique rf. Comme l'indique les figure III.3, III.4, III.5, III.6 et dont
les valeurs sont indiquées dans le tableau III.3.
Tableau III.3. Mesure des épaisseurs de
l'oxyde de zinc.
Echantillon
|
Temps de dépôt
|
Epaisseur des couches minces
|
ZnO non dopé
|
3h
|
1.5 um
|
ZnO : 3%Al
|
3h
|
1 um
|
ZnO : 1%Al
|
3h
|
1.5 um
|
ZnO : 1%Cu
|
3h
|
1 um
|
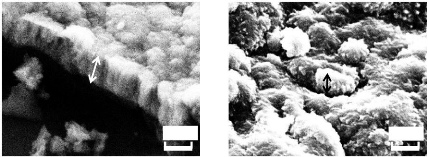
e = 1.5 Lm
1.5 Lm
e = 1 Lm
1.5 Lm
Figure III.3. Image MEB
de l'épaisseur de la couche de ZnO avec grossissement de 10k.
Figure III.4. Image MEB
de l'épaisseur de la couche de ZnO : 3% Al avec grossissement de
10k.
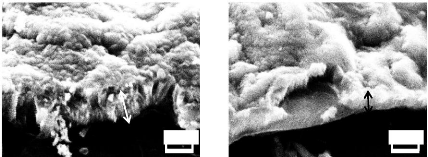
e = 1,5 Lm e = 1 Lm
1.5 Lm
1.5 Lm
Figure III.5. Image MEB
de l'épaisseur de la couche de ZnO : 1% Al avec grossissement de
10k.
Figure III.6. Image MEB
de l'épaisseur de la couche de ZnO : 1% Cu avec grossissement de
10k.
Nous observons d'après les figures III.3, III.4, III.5 et
III.6 que l'épaisseur des couches minces de ZnO non dopé et
dopé aluminium 1% sont plus importante que celles des couches minces de
ZnO dopé Al 3% et dopé cuivre 1%.
|