Année universitaire 2015 / 2016
N° d'ordre : . / Faculté / UMBB / 2016
REPUBLIQUE ALGERIENNE DEMOCRATIQUE ET POPULAIRE MINISTERE DE
L'ENSEIGNEMENT SUPERIEUR ET DE LA RECHERCHE SCIENTIFIQUE UNIVERSITE
M'HAMED BOUGARA BOUMERDES

Faculté des Hydrocarbures et de la
Chimie Mémoire de fin d'études
En vue de l'obtention du diplôme :
MASTER
Présenté par :
BENBOUDIAF MERWAN
Filière : Hydrocarbures
Option : Forage des puits
Thème
STABILITE DE LA PRESSION DE FOND ET MAINTIEN
DE L'ETAT D'UNDERBALANCE DES PUITS EN UBD APPLICATION AU PUITS ONIZ-40 A
HASSI MESSAOUD
Devant le jury :
|
|
|
|
MELLAK Abderrahmane
|
Professeur
|
UMBB
|
Président
|
HADJADJ Ahmed
|
MC (A)
|
UMBB
|
Encadreur
|
BENTRIOU Abdelhak
|
MC (A)
|
UMBB
|
Examinateur
|
BENYOUNES Khaled
|
MC (A)
|
UMBB
|
Examinateur
|
BOUMAZA Nadia
|
MA (A)
|
UMBB
|
Examinatrice
|
AZRIL Nadjet
|
MA(A)
|
UMBB
|
Examinatrice
|
Remerciements
Je tiens tout d'abord à remercier ALLAH tout
miséricordieux, qui m'a facilité la voie à chaque
carrefour de ma vie, et qui a fait que je suis là maintenant.
Je tiens également à remercier mon encadreur, Dr.
Hadjadj pour sa patience, ses conseils avisés et sa disponibilité
tout au long de la réalisation de ce travail.
Ma gratitude va également vers tout le personnel de
Weatherford que j'ai rencontré sur le chantier ENF#47, en particulier
Luis Rodriguez, ingénieur UBD, qui m'a orienté vers
l'étude présente, je tiens à lui exprimer mes
sincères remerciements pour tout ce qu'il a fait pour moi.
En dernier lieu, je remercie toute personne ayant
contribué de près ou de loin, à la réalisation de
ce travail.
Dédicaces
Je dédie ce travail en premier lieu à mes parents,
qui m'ont toujours soutenus, qui ont toujours crus en moi et m'ont toujours
encouragés tout au long de mes études.
A toute ma grande famille.
A mes amis les plus chers, Tahar, Raouf et Choayab
A Mon frère Moh
A ceux qui n'ont eu de cesse de me soutenir pendant tout ce
temps
Merci infiniment.
Une dédicace spéciale pour mes petits foreurs que
je laisse derrière moi et qui soutiendront prochainement InchaALLAH. A
Zaki, Sam et Nassim, j'attends beaucoup de vous pour la suite.
« Dans la nature, tout a toujours une raison, si on
comprend cette raison, il n'y a plus besoin de l'expérience
»
Leonard de Vinci (1452-1519)
Résumé
Le forage en underbalance est un moyen efficace pour
améliorer les performances de forage et maximiser la production en
réduisant l'endommagement de la formation. Les avantages de l'UBD sont
directement dépendants de la capacité à maintenir cet
état d'underbalance durant toute l'opération de forage. Le
maintien de cet état est compliqué car il est sujet à des
fluctuations permanentes, ou plutôt à un régime
transitoire. Une meilleure compréhension de cet état transitoire
va aider les ingénieurs à mieux prendre leurs décisions en
fonction des phénomènes rencontrés. Ce mémoire
traite du problème d'oscillation de la pression de fond, dû
à une discontinuité dans l'injection de gaz, ceci est connu sous
le nom d'«effet d'accumulateur », il est également
illustré comment une simulation de la pression en régime
transitoire peut aider l'ingénieur dans la compréhension et la
prévention de ce phénomène, en mettant en évidence
les facteurs influents sur son comportement, d'où est tiré
plusieurs propositions pour palier au problème. Le logiciel de
simulation Drillbench, et précisément le module Dynaflodrill est
utilisé pour étudier cet effet et pour optimiser les
paramètres de forage afin de minimiser les oscillations. L'étude
a été faite dans le cas de l'injection par tubage concentrique
qui est la moins connue et donc la moins maitrisée des techniques
d'injection de gaz dans le puits.
Mots clés : underbalance,
accumulateur, transitoire, fluctuations, stabilité.
Abstract
Underbalanced Drilling has the potential to add value by
enhancing Drilling performances and maximizing productivity by reducing
formation damage. The benefits of UBD are directly dependent on the ability to
maintain underbalanced conditions throughout the entire Drilling time.
Maintaining this state is complicated because there are subject to permanent
fluctuations, or a transient flow behaviour. Impoved understanding of the
transient flow behaviour will help the engineer to take better decisions
regarding the different phenomenas encountered. This thesis studies the BHP
oscillation problem, du to a discontinuity in gas injection flow rate, this is
well known as the « accumulator bottle effect », it's also
illustrated how a transient simulation can help the engineer understanding and
mitigating the problem, illustrating the factors influencing its behaviour,
from where some solutions are proposed as recommandations. The Dynaflodrill
transient simulator was used to optimize Drilling parameters to minimize
pressure fluctuations. We chosed to make the study in the case of concentric
casing injection method du to less experience available and thus less less
options known to control pressure instability.
Keywords : underbalance, accumulator,
transient, fluctuations, stability.
Sommaire
Résumé
Nomenclature Liste des figures Liste des tableaux
Introduction 1
Chapitre-1 Underbalanced Drilling, Theorie et Principes 3
1.1 Généralités 3
1.1.1 Introduction 3
1.1.2 Définition 3
1.1.3 Définition, classification IADC 4
1.1.4 Avantages du forage UBD, Challenges et defis 6
1.1.5 Equipements spécifiques à l'UBD 8
1.2 Techniques et Operations Communes à l'UBD
10
1.2.1 Well Control 10
1.2.2 Stripping 14
1.2.3 Pipe light 17
1.3 Flow Drilling, Forage avec fluide monophasique 17
1.3.1 Introduction 17
1.3.2 Historique 17
1.3.3 Avantages 18
1.3.4 Limites et défis de la technique 18
1.4 Forage avec fluide Biphasique 19
1.4.1 Historique 19
1.4.2 Definitions 19
1.4.3 Avantages 21
1.4.4 Méthode de réduction de la pression de
fond 22
1.4.5 Défis de la technique 23
1.4.6 Méthodes d'injection du gaz dans le puits
24
1.5 Séléction des puits candidats à l'UBD
26
Chapitre-2 UBD dans la région de Hassi Messaoud 29
2.1 Descriptif du champ 29
2.2 Historique de l'UBD à Hassi Messaoud 30
2.3 Planning et développement des opérations
31
2.4 Paramètres opérationnels et problèmes
31
2.5 Resultats de puits forés 32
2.6 Conclusion 34
Chapitre-3 Propiétés des mélanges
liquide/gaz, Modélisation et Simulation des
écoulements Multiphasiques 36
3.1 Facteur de volume 36
3.2 Densité 38
3.3 Débit standard, Débit actuel 40
3.4 Rapports de volume 41
3.5 Vélocités et effet de glissement
41
3.6 Viscosité 42
3.7 Rappel sur la modélisation d'un
écoulement monophasique incompressible 44
3.8 Simulation des écoulements Diphasiques 44
3.9 Planification et modélisation des
opérations en underbalance 47
3.10 Dynaflodrill 48
Chapitre-4 Initiation à la geomécanique en
forage 53
4.1 Introduction, description du problème 53
4.2 Etat des contraintes dans le puits 53
4.3 Analyse de stabilité des parois pour puits
verticaux 55
4.4 Analyse de stabilité des parois pour puits
déviés 57
4.5 Estimation des contraintes in-situ 58
Chapitre-5 Effet d'accumulateur : définition et
expliquation 60
5.1 Description du phénomène, Illustration du
phénomène de Slugging 60
5.2 Vélocité critique du gaz 63
Chapitre-6 Facteurs influençants la stabilité de
la pression de fond 68
6.1 Volume du concentrique 68
6.2 Débit de gaz 68
6.3 Débit de liquide 69
6.4 Surface d'injection TFA 70
6.5 Pression à la Duse 72
6.6 Influence de production 73
6.7 Viscosité de la phase liquide 74
Chapitre-7 Etude de cas ONIZ-40 76
7.1 Présentation du puits 76
7.2 Paramètres opérationnels 78
7.3 Modélisation statique de la pression de fond 78
7.4 Modélisation Dynamique : illustration du
problème 80
Chapitre-8 Propositions et solutions 83
8.1 Manipulation de la pression à la duse 83
8.2 Mise en place d'un clapet anti-retour 84
8.3 Injection duale 86
8.4 Injection par parasite string 89
8.5 Injection par Drill Pipe 90
Conclusion 97
Références ANNEXES
Nomenclature
B9 Facteur de volume pour le gaz [scf/stb]
B0 Facteur de volume pour l'huile [stb/stb]
c0 compressibilité de l'huile [R/psi]
E~ Energie cinétique
[lbf-ft/ft3]
f Fraction volumique
g constante gravitationnelle [32.2 ft/s2]
Gp Gradient de pression Hydrostatique [atm/ft]
H Holdup
h hauteur [feet]
k ratio des chaleurs spécifiques
lpm litre par minutes = l/min
P Pression [Psi|bars]
Patm Pression [atm]
1pore pression de formation [bars]
P Pression de fond [bars]
'wf Pression de fracturation [bars]
MD hauteur mesurée [ft]
n Fraction de gaz dans la boue [%]
q débit [ft3/s]
r rayon [ft]
Rs Ratio gaz/huile dans la solution [scf/stb]
SP pression de surface [psi]
T Température [Rankine]
TVD hauteur réelle [ft]
V Volume [m3]
v9 vitesse superficielle du gaz [ft/s]
v1 vitesse superficielle du liquide [ft/s]
y9 vitesse actuelle du gaz [ft/s]
vl vitesse actuelle du liquide
[ft/s]
vs vitesse de glissement
[ft/s]
WC water cut [%]
Wds Poids de la garniture [lbf]
Z Facteur de compressibilité
a azimuth
yo densité de
l'huile
yg densité du
gaz
p masse volumique
[lbm/ft3]
A Holdup sans glissement
o, contrainte verticale [bars]
aH contrainte horizontale maximale
[bars]
ah contrainte horizontale minimale
[bars]
To cohésion de la roche
[bars]
0 angle de friction interne de la
roche
V inclinaison du puits
Abréviations
BHP BottomHole Pressure
BOP Blowout Preventer
DDV Downhole deployment
Valve
ECD Equivalent Circulating
Density
FV Facteur de volume
IADC International Association of
Drilling Contractors
MPD Managed Pressure Drilling
MD Measured Depth
MWD Measurments While Drilling
NPT Non-Productive Time
NRV Non-Return Valve
PDM Positive Displacement
Motor
RCD Rotating Control Device
ROP Rate Of Penetration
TFA Total Flow Area
TVD True Vertical Depth
UBD Underbalanced Drilling
UBO Underbalanced Operations
WOB Weight On Bit
Liste des figures
Figure 1.1 : Illustration des profils de pression et
UB zone. (ECK-OLSEN, 2003) 3
Figure 1.2 : Evolution du ROP en fonction de la
densité du fluide de forage pour différentes formations.
(Bourgoyne
and Young, 1991) 6
Figure 1.3 : Schéma équipements de
surface pour UBO 8
Figure 1.4 : Model RCD utilisé en
Algérie (a) et illustration du domaine d'opération (b).
9
Figure 1.5 : ESD valve 9
Figure 1.6 : Schéma NRV deux types.
10
Figure 1.7 : Effet du gas cut sur la pression au fond
du puits. (Rehm, 2012) 11
Figure 1.8 : Changement de la pression au fond est
inférieur à celui en tête. 13
Figure 1.9 : Matrice de décision, cas invasion
liquide. (Valeurs pour Weatherford) 13
Figure 1.10 : Matrice de décision, cas invasion
gaz. (Valeurs pour Weatherford) 14
Figure 1.11 : Principe du Mud Cap 16
Figure 1.12 : DDV, principe de fonctionnement.
16
Figure 1.13 : Illustration DDV dans le puits.
17
Figure 1.14 : Séparation gaz/liquide. (Rehm,
2012) 19
Figure 1.15 : Illustration de l'évolution de la
qualité du gaz. (Rehm, 2012) 20
Figure 1.16 : Principe Jet sub. 20
Figure 1.17 : Constant circulating sub. (Rehm, 2012 et
CANRIG) 21
Figure 1.18 : Régimes de pression en fonction
du débit de gaz injecté. (Rehm, 2012) 22
Figure 1.19 : Evolution des frictions dans l'annulaire
en fonction du débit d'injection de gaz pour differents débits
de
liquide 23
Figure 1.20 : Injection par Drill Pipe ou stand pipe.
(Blade) 25
Figure 1.21 : Injection par parasite. (Blade)
25
Figure 1.22 : Injection par concentrique. (Blade)
26
Figure 1.23 : Séléction candidat pour
UBD. (Aadnoy, 2009) 27
Figure 2.1 : Localisation Hassi Messaoud (Moore, 2004)
29
Figure 2.2 : Les zones à Hassi Messaoud avec
localisation de puits forés en UBD. (Moore, 2004) 30
Figure 2.3 : Comparaison ROPs des puits forés
en underbalance. (Moore, 2004) 33
Figure 2.4 : Comparaison temps pour forer la partie
latérale des puits UBD. (Moore, 2004) 33
Figure 2.5 : Débit de production selon la
moyenne du secteur pour les puits en UBD (Moore, 2004) 35
Figure 3.1 : Evolution du facteur de volume pour le
gaz naturel en fonction de le temperature. 36
Figure 3.2 : Evolution du facteur de volume pour le
gaz naturel en fonction de la pression. 37
Figure 3.3 : Evolution du facteur de volume de l'huile
en fonction de la pression. 38
Figure 3.4 : Abaque de conversion en degré API
(
Petroleum.co.uk,
2014) 39
Figure 3.5 : Viscosités pour plusieurs gaz
à pression 200 psi. (Leirkaer, 2014) 43
Figure 3.6 : Viscosité de l'huile morte en
fonction de sn degré API. (Leikaer, 2014) 43
Figure 3.7 : Régimes d'écoulement en
conduite verticale. (Rehm, 2012) 45
Figure 3.8 : Régimes d'écoulement en
conduite horizontale. (Rehm, 2012) 46
Figure 3.9 : Modèle de régime de
Mandhane. (Rehm, 2012) 47
Figure 3.10 : Influence du débit de gaz sur la
BHP et enveloppe UBD 48
Figure 3.11 : Injection par parasite : données
experimentales Vs. Données simulées à l'aide du
Dynaflodrill
(Rommetveit, 2001) 51
Figure 3.12 : Interface de travail Dynaflodrill
52
Figure 3.13 : Interface de simulation Dynaflodrill.
52
Figure 4.1 : Etat des contraintes dans le puits.
(Mitchell, 2011) 54
Figure 4.2 : Contraintes agissant sur le puits.
(Mitchell, 2011) 54
Figure 4.3 : Modes de collapse du trou. (Mitchell,
2011) 55
Figure 4.4 : Illustration des contraintes pour le
modèle de Mohr-Coulomb (Mitchell, 2011) 56
Figure 4.5 : Orientation des contraintes
déviées. (Mitchell, 2011) 57
Figure 5.1 : Débit de gaz sortant, illustration
du phénomène de slugging. 60
Figure 5.2 : Evolution de la pression de fond pendant
le phénomène de slugging 61
Figure 5.3 : Evolution du débit d'injection de
gaz pendant le phénomène de slugging. 61
Figure 5.4 : Evolution du niveau des bacs de pendant
le phénomène de slugging. 62
Figure 5.5 : Régimes d'écoulement du gaz
à travers un orifice et effet de blocage (Ryhming, 2009). 63
Figure 5.6 : Evolution du débit sortant de gaz,
régime critique. 65
Figure 5.7 : Evolution de la pression de fond,
régime critique. 65
Figure 5.8 : Evolution du débit d'injection de
gaz, régime critique. 65
Figure 5.9 : Evolution du débit sortant de gaz,
régime sur-critique. 66
Figure 5.10 : Evolution pression de fond,
régime sur-critique. 66
Figure 5.11 : Evolution du débit d'injection de
gaz, régime sur-critique. 66
Figure 5.12 : Evolution du débit de gaz
sortant, régime idéal. 67
Figure 5.13 : Evolution de la pression de fond,
régime idéal. 67
Figure 5.14 : Evolution débit d'injection de
gaz, régime idéal. 67
Figure 6.1 : Variation de la BHP en fonction du temps
pour différents points d'injection. 68
Figure 6.2 : Variation de la BHP en fonction du temps
pour différents débits de gaz (m3/min) 69
Figure 6.3 : Variation de la BHP en fonction du temps
pour différents débits de liquide. 69
Figure 6.4 : Relation entre le débit de liquide
et le temps de stabilisation de la BHP. 70
Figure 6.5 : Illustration d'un point d'injection de
gaz. (Rehm, 2012) 71
Figure 6.6 : Illustration section du concentrique.
72
Figure 6.7 : Evolution de la BHP en fonction du temps
pour différents pourcentages de fermeture de la Duse. 73
Figure 6.8 : Relation entre l'ouverture de la Duse et
la durée de stabilisation de la BHP. 73
Figure 6.9 : Variation de la BHP en fonction du temps
dans le cas avec production et sans. 74
Figure 6.10 : Variation de la BHP en fonction du temps
pour différentes viscosités. 75
Figure 6.11 : Evolution des pertes de charge
annulaires en fonction de la viscosité de la phase liquide.
75
Figure 6.12 : Influence de la viscosité du
liquide sur la durée de stabilisation de la BHP. 75
Figure 7.1 : Localisation ONIZ-40. (Sonatrach)
76
Figure 7.2 : Survey et illustration profil du puits
ONIZ-40. (Bleu : Tubage et Rouge : Openhole) 76
Figure 7.3 : Architecture du puits ONIZ-40
77
Figure 7.4 : Modélisation de la pression de
fond en fonction du débit de gaz injecté. 79
Figure 7.5 : Evolution BHP cas ONIZ-40 81
Figure 7.7 : Débit sortant en sortant de
l'annulaire en surface. 82
Figure 7.8 : Ouverture de la duse pendant la phase
d'injection du gaz, ONIZ-40. 82
Figure 8.1 : Evolution de la BHP pour une pression de
duse contrôlée. 83
Figure 8.2 : Evolution du pourcentage d'ouverture de
la duse. 83
Figure 8.3 : Evolution des débits d'injection
de gaz pour pression de duse contrôlée. 84
Figure 8.4 : Evolution BHP ONIZ-40 avec incorporations
d'une check valve 85
Figure 8.5 : Evolution BHP ONIZ-40 avec check valve.
85
Figure 8.6 : Evolution du débit de gaz au
séparateur, check valve avec manipulation de la duse. 85
Figure 8.7 : Ouverture de la duse, check valve.
86
Figure 8.8 : Principe injection duale. 87
Figure 8.9 : Evolution BHP ONIZ-40 avec injection
double. 88
Figure 8.10 : Evolution débit de gaz au
séparateur, injection double. 88
Figure 8.11 : Ouverture de la duse, injection double.
89
Figure 8.12 : modélisation statique de la BHP,
cas injection par parasite. 89
Figure 8.13 : Evolution BHP, cas injection par parasite.
90
Figure 8.14 : Modélisation statique de la BHP
et illustration des pressions de collapse et de formation. 92
Figure 8.15 : Diagramme opérationnel.
93
Figure 8.16 : BHP en fonction du temps pour injection
par tiges. 93
Figure 8.17 : Différents régimes
d'écoulement pour conduites horizontales (Falcone, 2009) 94
Figure 8.18 : Diagrammes d'écoulement pour
conduites horizontales (Falcone, 2009) 94
Figure 8.19 : Evolution du Holdup pour le liquide avec
650 et 700 l/min de débit. 95
Figure 8.20 : Abaque de Standing Katz pour la
détermination du facteur de
compressibilité pour le gaz (Tarek, 2012)
96
Liste des tableaux
Tableau 1 : Classification IADC du niveau de
risque pour les UBO (Aadnoy, 2012) 5
Tableau 2 : Classification IADC de la
catégorie d'application en Underbalance (Aadnoy, 2012)
5
Tableau 3 : Classification IADC des types de
fluide pour puits en underbalance (Aadnoy, 2012)
5
Tableau 4 : Avantages et inconvénients
du forage en underbalance. 7
Tableau 5 : Limites de stripping
recommandées (Sonatrach) 15
Tableau 6 : Types de réservoirs
candidats et non candidats. 28
Tableau 7 : Paramètres dans les
équations de conservation 50
Tableau 8 : Données du puits
utilisé pour la simulation 64
Tableau 9 : Récapitulatif informations
sur le puits ONIZ-40 78
Tableau 10 : Paramètres relatifs au
puits ONIZ-40 nécessaires à la simulation. 79
Tableau 11 : Etapes de réduction de la
BHP pour 650 l/min 80
1
Introduction
Le forage en underbalance a connu un grand essor durant les
dernières années. Et ce, à cause de la nature
deplétée des réservoirs à forer. Par
deplété on entend les réservoirs à faible pression
ou bien alors ceux ayant atteint une certaine maturité après
avoir été exploités pendant une longue période. La
seconde raison est liée aux exigences et défis du forage
d'aujourd'hui ; minimiser l'endommagement de la formation, les pertes de
circulations, et également les risques de coincement de la garniture. Le
forage en underbalance offre également de meilleures performances de
forage ; augmentation de la vitesse d'avancement et maximisation de la vie de
l'outil.
Pour la bonne tenue d'une opération en underbalance, le
contrôle des pressions dans le puits est crucial. La pression de fond
doit être contrôlée en permanence pour être sûr
d'avoir les conditions d'underbalance maintenues à tout moment des
opérations. Le contrôle des pressions depuis la surface
nécessite des équipements et des procédures de mise en
oeuvre bien précises.
Ce mémoire traite du problème de maintien de
l'état d'underbalance dans le cas d'un système d'injection par
tubage concentrique. C'est un problème bien connu des ingénieurs
mais mal étudié. En effet, il s'agit de l'effet d'accumulateur,
qui entraine une discontinuité dans l'injection de gaz dans le puits et
donc une oscillation dans la valeur de la pression de fond, causant un bon
nombre de problèmes :
· Une perte périodique de l'état
d'underbalance, et donc un endommagement de la formation productrice par le
fluide de forage.
· Risque de fracturation et donc des pertes de
circulation, ou alors d'éboulement de la formation.
· Difficultés à contrôler les
effluents en surface.
Ce travail se divise en 8 chapitres, chacune d'elles ayant un
but précis dans la compréhension du problème.
? Le chapitre 1 donne une introduction générale
sur le forage en underbalance, les principes et la théorie essentielle
pour comprendre la suite du mémoire, il sera particulièrement
axé sur le forage avec liquide biphasique.
? Le chapitre 2 décrit un historique du forage en
underbalance dans la région de Hassi Messaoud, il sera discuté
des résultats des premiers puits d'essai qui ont été
forés, une comparaison des résultats et un descriptif des
problèmes rencontrés en fait également l'objet.
? Le chapitre 3 traite d'abord des propriétés
essentielles des mélanges liquides/gaz nécessaires à la
simulation des écoulements diphasiques, et qui seront importantes pour
l'étude de simulation. Il est ensuite question des fondements de la
théorie des écoulements diphasiques et la modélisation des
opérations en underbalance, avec un petit rappel sur la
modélisation des écoulements monophasiques incompressibles. Pour
finir, une présentation du logiciel de simulation Dynaflodrill
utilisé dans ce mémoire pour mettre en évidence le
problème.
2
- Le chapitre 4 présente une introduction à la
géomecanique en forage et à l'étude de stabilité
des parois dans le cas des puits verticaux et puits déviés. En
plus de la présentation d'un algorithme pour la détermination des
contraintes liées à la roche. Ce chapitre est un
complément au sujet étudié, il décrit
l'étude de stabilité des parois qui représente une part
essentielle dans le design d'une opération en underbalance. Les
équations présentées joueront une part essentielle dans le
chapitre 7.
- Le chapitre 5 est une introduction à l'effet
d'accumulateur, en illustrant les différents régimes
d'écoulements du gaz au point d'injection dans le puits, une simulation
de chaque cas a été faite avec le software Dynaflodrill.
- Le chapitre 6 traite des différents facteurs
influençant la stabilité de la pression avec une simulation de
l'influence de l'évolution de chaque paramètre sur la tendance
oscillatoire de la pression du fond.
- Le chapitre 7 va vers l'étude de cas du puits ONIZ-40
dans la région de Hassi Messaoud. Premièrement une
présentation du puits et des paramètres opérationnels
relatifs. Est entreprise ensuite une simulation en régime permanent de
la pression de fond en fonction du débit de gaz, et ce dans le but de
connaitre les valeurs de débit d'injection de liquide et de gaz
correspondants à une pression voulue. Enfin, une simulation de la
pression de fond en régime transitoire et une illustration du
problème rencontré pendant le forage du puits en question est
présenté.
- Le chapitre 8 étudie certaines propositions pour
remédier au problème d'accumulateur, avec à la fin une
étude détaillée sur l'éventualité de
l'injection par l'intérieur des tiges en prenant en compte l'analyse de
stabilité des parois vue au chapitre 4. Le calcul des contraintes
in-situ et de la pression d'effondrement des parois a été fait
avec les données du puits ONIZ-40, cependant le processus de calcul
étant trop fastidieux, il a été
préféré de ne pas le mettre par soucis de rester dans le
thème du mémoire.
- Enfin une conclusion de l'étude menée, suivie
de quelque recommandations particulières sur d'autres problèmes
apparus au cours du forage du puits ONIZ-40 qui sont
présentés.
3
Chapitre1-Underbalanced Drilling : Theorie et Principes
Chapitre-1 Underbalanced Drilling : Theorie et
Principes
1.1 Généralités
Ce qui suit informe sur les bases du forage underbalance,
incluant les principes généraux en plus des différents
équipements utilisés, et pour terminer le rôle et la
contribution de l'UBD dans l'industrie du forage.
1.1.1 Introduction
Les réservoirs à faible
perméabilité ou deplétés sont un défi pour
l'ingénieur forage d'aujourd'hui, avec un certain nombre de
problèmes récurrents tels que les pertes de circulation, les
coincements et l'endommagement du réservoir par le fluide de forage.
Dans le but de limiter ces problèmes le forage en Underbalance est
devenu un principe essentiel depuis la fin du XXème siècle.
1.1.2 Définition
Le forage en underbalance est une technique dans laquelle la
pression de fond exercée par le système de fluide de forage est
maintenue à une certaine valeur inférieure à celle du
réservoir, la Figure 1.1 donne une illustration de la fenêtre
Underbalance.
Pformation > PBHP = PHydrostatique + Pfriction
+ PDuse (1.1)
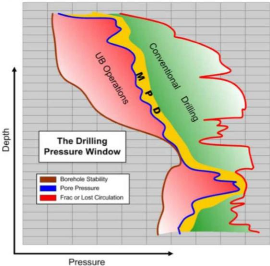
Figure 1.1 : Illustration des profils de pression et
UB zone. (ECK-OLSEN, 2003)
4
Chapitre1-Underbalanced Drilling : Theorie et Principes
A la différence du forage conventionnel, le fluide de
forage n'agit plus comme la première barrière de
sécurité. Les équipements de surface pour les UBO comme le
RCD (Rotating Control Diverter) et le manifold de duses jouent ce rôle.
La deuxième barrière de sécurité reste toujours
l'ensemble BOP. Et à l'instar du forage en overbalance, le
contrôle du puits doit être maintenu à chaque instant,
à la seule différence que l'UBD est prévu pour laisser les
fluides de réservoir affluer dans le puits.
Cette condition pouvant être
générée naturellement, via des fluides de faible
densité (Brute, Gasoil, Eau) dans certains cas où il y a une
grande pression de formation. Cette pratique est dite Flow Drilling. Mais dans
beaucoup de situations, la condition d'underbalance est
générée artificiellement par l'injection simultanée
d'un gaz non condensable dans le système de circulation dans le but de
réduire la pression hydrostatique effective de la colonne de fluide. Le
gaz le plus utilisé est le Nitrogène pour sa disponibilité
et sa facilité de transport, mais l'utilisation de l'air appauvri en
oxygène (par l'utilisation de membrane semi-perméable), ou du gaz
naturel se fait également, dépendant des cas d'application.
1.1.3 Définition, classification IADC
La définition du forage Underbalanced selon l'IADC
: « Drilling with the hydrostatic head of the drilling fluid
intentionally designed to be lower than the pressure of the formations being
drilled. The hydrostatic head of the fluid may naturally be less than the
formation pressure, or it can be induced. The induced state may be created by
adding natural gas, nitrogen, or air to the liquid phase of the drilling fluid.
Whether the underbalanced status is induced or natural, the result may be an
influx of formation fluids which must be circulated from the well and
controlled at the surface » (Aadnoy,2009)
« C'est le forage avec une pression
hydrostatique de fluid intentionnellement choisie pour être plus faible
que la pression de formation forée. La pression hydrostatique du fluide
peut être naturellement en dessous de celle de la formation, ou peut
être induite. L'état induit peut être crée par ajour
de gaz naturel, azote, ou air à la phase liquide du fluide de forage.
Que l'état underbalanced soit induit ou naturel, le résultat peut
être un afflux de la formation qui devra être circulé et
controlé à la surface. »
Les mots « intentionnellement choisie » clarifient
le fait que l'état underbalance est une part primordiale du design du
puits.
Une deuxième définition « A
drilling activity employing appropriate equipment and controls where the
pressure exerted in the wellbore is intentionally less than the pore pressure
in any part of the exposed formations with the intention of bringing formation
fluids to the surface.» (Leirkjaer, 2014)
« C'est une activité de forage employant des
équipements et controles appropriés où la pression
exercée sur les parois du puits est intentionnellement inférieur
à la pression de pore en toutes parts de de la formation avec
l'intention de laisser les fluides de formation filtrer et monter en surface
»
Un système de classification a été
développé par l'IADC pour établir les risques
associés, la catégorie d'application et le système de
fluide utilisé en UBO et en MPD.
Les puits sont classifiés selon :
· Le niveau de risque (0 à 5)
5
Chapitre1-Underbalanced Drilling : Theorie et Principes
· Catégorie d'application (A, B ou C)
· Système de fluide (1 à 5)
Cette classification procure une base pour le design des
équipements de surface, et des procédures de
sécurité.
Tableau 1 : Classification IADC du niveau de
risque pour les UBO (Aadnoy, 2012)
|
Level 0
|
Amélioration des performances de forage. Pas de zone
contenant des hydrocarbures
|
Level 1
|
Puits intrinsèquement stable, risque faible du point de
vue Well Control
|
Level 2
|
Possiblité que le fluide de formation arrive en surface,
mais les methodes standards pour tuer le puits sont suffisantes,
conséquences faibles en cas de panne du materiel en surface
|
Level 3
|
Production en surface non hydrocarbures, la pression maximale de
fermeture est inferieure à la pression opérationnelle des
équipements en surface. Panne des équipements de surface entraine
des conséquences immédiates
|
Level 4
|
Production d'hydrocarbures, la pression maximale de fermeture
est inferieure à la pression opérationnelle des
équipements en surface. Panne des équipements de surface entraine
des conséquences immédiates
|
Level 5
|
Les pressions maximales prévues sont au-dessus de la
pression des équipements de surface, mais en dessous de la pression de
service du BOP. Panne des équipements de surface entraine des
conséquences immédiates et serieuses.
|
|
Tableau 2
|
: Classification IADC de la catégorie
d'application en Underbalance (Aadnoy, 2012)
|
Catégorie A
|
|
Managed Pressure Drilling - MPD Forage avec retours en surface
du fluide opérant avec une densité équivalente de boue
égale ou légerement superieure à la pression en
openhole.
|
Catégorie B
|
|
Underbalanced Operations - UBD Forage avec retour en surface du
fluide maintenant une densité équivalente de boue en-dessous de
la pression en openhole.
|
Catégorie C
|
|
Mud-Cap Drilling
Forage sans retour en surface, avec une colonne de fluide en
annulaire qui est maintenue au-dessus d'une formation qui prend le fluide
injecté et les cuttings.
|
|
Tableau 3 : Classification IADC des types de
fluide pour puits en underbalance (Aadnoy, 2012)
|
Gas
|
1
|
Brouillard (mist)
|
2
|
Mousse (foam)
|
3
|
Liquide gazeifié
|
4
|
Liquide
|
5
|
|
6
Chapitre1-Underbalanced Drilling : Theorie et Principes
1.1.4 Avantages du forage en underbalance, Challenges et
defis
Le but essentiel du forage en underbalance est de minimiser
les problèmes de forage. Mais à mesure que la technologie MPD
s'est développée, l'UBD est plus souvent remplacé par
l'MPD dans cette mesure. Aujourd'hui l'UBD est globalement utilisé pour
réduire l'endommagement de la formation. (Rehm, 2012)
L'UBD est devenu est une methode très interessante
pour l'évaluation du réservoir en cours de forage et pour
améliorer la performance des puits forés. (Rehm, 2012)
Minimisation des problèmes dus à la
pression. La plupart des problèmes de forages
relatés à la pression peuvent être minimisés avec
l'UBD. Ceci fait de cette technologie un outil idéal pour le forage des
réservoirs deplétés.
Collage par pression différentielle.
L'absence de pression overbalance sur la formation, combinée avec
l'absence de mud cake, prévient le collage par pression
différentielle.
Pertes de circulation. En général, la
réduction de la pression hydrostatique dans l'annulaire réduit
les pertes dans la formation sujette. En UBD, la pression hydrostatique est
réduite au niveau où les pertes ne peuvent arriver. Ceci est
important dans la protection des microfractures contre l'endommagement.
Augmentation de la vitesse d'avancement. La
réduction de la pression hydrostatique a un effet significatif sur la
vitesse d'avancements (Figure-1.2). Ce qui a également un effet positif
sur la vie de l'outil. La vitesse d'avancement ou taux de
pénétration (ROP) est fonction du type de formation, de la
porosité, de la résistance à l'écrasement de la
roche, en plus de la combinaison du WOB et de la vitesse de rotation. C'est
difficile de dire que le ROP va augmenter seulement si on fore en UBD, parfois
son augmentation est due à d'autres facteurs.
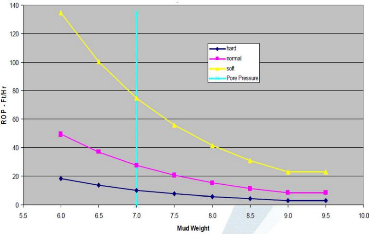
Figure 1.2 : Evolution du ROP en fonction de la
densité du fluide de forage pour différentes
formations. (Bourgoyne and Young, 1991)
7
Chapitre1-Underbalanced Drilling : Theorie et Principes
Maximiser la récupération.
Même si ce n'est pas la raison primaire pour la
sélection des puits en underbalance, les résultats de puits UBD
montrent une augmentation significative de la production en comparaison avec
ceux foré conventionnellement. Ceci peut s'expliquer par le fait qu'il
n'y aucune invasion de solides ou de filtrat de boue dans la formation. Ce qui
peut également accroitre la durée de vie d'un puits. Une
meilleure productivité implique également un drawdown plus
faible, ce qui diminue le water coning.
Même si la production initiale des puits forés
en underbalance n'est pas très indicative d'une augmentation de la
production, les profils de production à long terme montrent un
déclin moins important pour les puits UBD. Ce phénomène
est attribué à la production à partir de zones moins
perméable du réservoir qui n'ont pas soufferts de
l'endommagement. (Rehm, 2012)
Caractérisation du réservoir.
La possibilité d'identifier les zones productive en cours
de forage, résulte dans une meilleure prise de décision quant
à la suite des opérations. En plus de ça le forage en
underbalance permet de révéler des zones productives à
faible perméabilité qu'on croyait non productive.
Toutefois cette technique présente certains
défis et complications dus à la pression appliquée sur les
parois.
Contrôle des fluides de formation en
surface. Problématique dans le cas où l'on ne peut
pas en disposer en toute sécurité. Surtout dans le cas de
présence de H2S.
Instabilité des parois.
C'est l'un des problèmes qui limitent l'usage de l'UBD.
L'instabilité peut prendre plusieurs formes :
· Zones où les contraintes in-situ sont très
importantes dû une activité tectonique.
· Zones fracturées naturellement.
· Sédiments jeunes où les pressions de
pore, de fracturation et la pression d'intégrité des parois
tendent à converger.
· Zones à haut pourcentage d'argiles.
· Zones salifères, de nature plastique qui vont
tendre à affluer dans le puits.
Un récapitulatif des avantages et inconvénients de
l'UBD est présenté dans le tableau suivant :
Tableau 4 : Avantages et inconvénients du forage
en underbalance.
|
Avantages
|
Inconvénients
|
Augmentation du ROP
Réduction de l'endommagement de la formation
Elimination du risque de collage Réduction des risques de
pertes Augmentation de la durée de vie de l'outil Forage des zones
deplétées
Caractérisation du réservoir et Well testing while
drilling
|
Possibles problèmes d'instabilité des parois
Coût des opérations élevé
Non compatible avec les systèmes MWD conventionnels
Compléxité de mise en oeuvre
Augmentation du torque et des frottements en cours de forage
|
|
8
Chapitre1-Underbalanced Drilling : Theorie et Principes
1.1.5 Equipements spécifiques à l'UBD
La figure 1.3 donne une configuration standard des
équipements en UBD, et donne une idée des équipements
nécessaires en surface.
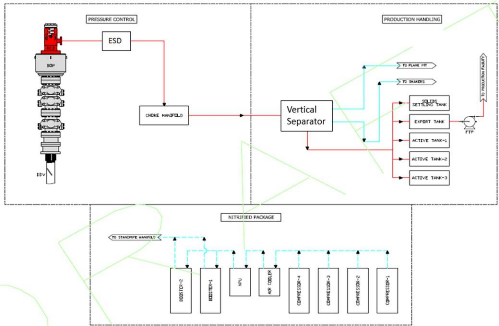
Figure 2.3 : schéma équipements de
surface pour UBO
Description du circuit d'injection.
L'ensemble des compresseurs aspirent l'air à la pression
atmosphérique et le refoule à pression de 300 psi et à
temperature 110-120°C, l'air passe ensuite dans le refroidisseur où
il est amené à 80°C et entre également à
travers un filtre à charbon pour le débarrasser de
l'humidité et des impuretés. Avec les pertes de charges
occasionnées, la pression à la sortie du refroidisseur est de
l'ordre de 200-220 psi. Il rentre ensuite dans le NPU (Nitrogen Production
Unit) pour en retirer l'azote, la pureté atteinte peut aller
jusqu'à 95% d'azote. A la sortie du NPU l'azote passe par le Booster-1
et le Booster-2 (respectivement medium et high booster). A la sortie du high
booster la pression peut atteindre 3000 psi, l'azote est ensuite directement
injecté dans le puits.
Equipements de contrôle du
puits.
· BOP conventionnel
· BOP rotatif, ou RCD (Rotating Control Device). Dit
ainsi car l'élément d'étanchéité tourne en
même temps que les tiges de forage (Figure 1.4). C'est la première
barrière de sécurité en UBD contrairement au forage
conventionnel où la première barrière est la pression
hydrostatique exercée par le fluide de forage. Caractérisé
par deux « Rubbers » inferieur et superieur qui sont concentriques
à la garniture. Le rubber inferieur est dit polyrubber car il est fait
de matière synthétique et il est fixe.
9
Chapitre1-Underbalanced Drilling : Theorie et Principes
Le rubber superieur est dit natural rubber car il est de
caoutchouc naturel, et il tourne avec les tiges de forage. La partie tournante
est racordée à la partie fixe par un roulement à
billes.
Caractéristiques : pression statique 2000 psi
Pression dynamique 1500 psi
L'élément d'étanchéité se
compose de deux pièces (Rubbers)
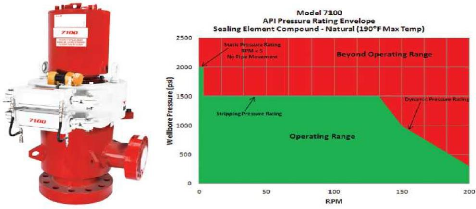
(a) (b)
Figure 1.4 : Model RCD utilisé en Algérie
(a) et illustration du domaine d'opération (b).
· Vanne ESD (Emergency ShutDown). Vanne hydraulique,
située à la sortie de la Hard line (Figure 1.5). Utilisée
dans le cas de certains problèmes.
Fuite au niveau des équipements de retour
Détection d'un gaz toxique H2S
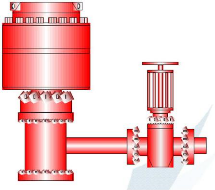
Figure 1.5 : ESD valve (Blade)
· Choke Manifold. Dans un chantier UBD, il y toujours
deux manifolds de duses, le premier est celui du Rig qui vient avec le BOP. Le
second se trouve à la sortie du puits connecté à la flow
line. Souvent on prévoit un cross-over entre le manifold du Rig et
Chapitre1-Underbalanced Drilling : Theorie et Principes
celui de l'UBD, cela offre plus de flexibilité et de
réactivité au système. Le but de la duse est de
contrôler la pression dans le puits, par ouverture et fermeture de
celle-ci il s'en suit une manipulation de la pression dans l'annulaire et donc
de la pression de fond.
· Clapet anti-retour incorporés dans la
garniture. NRV (non-return valve) pour éviter l'intrusion des fluides de
formation dans la garniture. En général on place 3 NRV dans la
garniture. (figure 1.6)
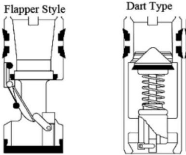
~~~~ (1.2)
Z2T2
Ply1 ~ Z1T1
10
Figure 1.6 : schéma NRV deux types.
· Système de séparateur. Il existe un
système avec séparateur horizontal (4 phases) et vertical (2
phases). Dans le cas du séparateur vertical on dissocie le gaz de la
phase liquide (fluide de forage + cuttings), le fluide de forage étant
ensuite traité dans un bac de décantation pour enlever les
cuttings en suspension
1.2 Techniques et Operations Communes à
l'UBD
1.2.1 Well Control
Les principes de base du contrôle des éruptions
et les différentes procédures associées sont une part
permanente des UBO. Tant que l'UBD tend à laisser les fluides de
formation remonter en surface en même temps qu'il y une pression
exercée sur l'annulaire, il est important de comprendre comment
contrôler les influes venant de la formation. Avant d'aborder les
procédures de Well control, il est important de revoir certaines
bases.
Loi générale des gaz.
Il est important de comprendre l'effet d'une bulle de gaz dans un
puits. Dans un puits présentant un « gas cutting », le gas cut
peut ne pas changer la pression de fond significativement. Quand un bulle de
gaz sous pression se déplace dans le puits (parfois cela arrive pendant
les connections), la relation pression/volume prend place dans l'effet de
réduction de la pression au-dessus de la bulle en question. La loi
générale des gaz s'exprime comme suit :
11
Chapitre1-Underbalanced Drilling : Theorie et Principes
Effet du gas cut sur la pression de fond.
Les études montrent qu'une invasion du fluide de forage
par le gaz ne réduit pas significativement la pression de fond
jusqu'à 50% de gaz dans la colonne. L'équation de Strong-White
simplifiée permet de calculer la réduction en statique de la
pression de fond due à l'effet du gaz. (Rehm, 2012)
hGp -- Patm = ~
ioo--n Ln(Patm + 1) (1.3)
Goins et O'Brien (1962) ont publiés un abaque
illustrant la réduction de la pression de fond en fonction du
pourcentage de gaz dans la colonne. (Figure 1.7)
La figure montre bien qu'avec un gas cut de moins de 25%, la
réduction de la pression de fond est presque négligeable.
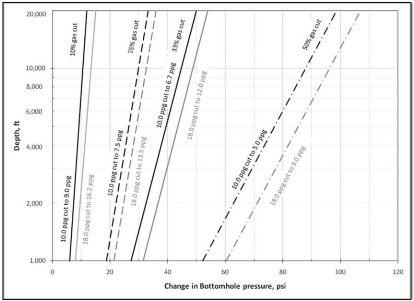
Figure 1.7 : Effet du gas cut sur la pression au fond
du puits. (Rehm, 2012)
Well control en UBD. Quasiment
toutes les opérations en UBD marchent selon le principe de circuler le
puits dans un système fermé avec un débit des pompes
constant et un control de la pression à la duse. Ce principe est le
même que celui de la première circulation de la Driller's
method.
12
Chapitre1-Underbalanced Drilling : Theorie et Principes
La pression de fond peut être contrôlée en
maintenant un débit constant des pompes et en contrôlant la
pression en tête de tiges avec la duse. Le changement de la pression de
fond en réponse à un changement de la production du
réservoir peut se faire de différentes manières.
· Augmenter ou diminuer la pression de la duse. Ceci
donne une réponse immédiate à une augmentation de la
production.
· Changement de la densité du la phase liquide
dans le cas du flow drilling.
· Changement du ratio liquide/gaz dans le cas dans le
cas du forage avec liquide gazeifié.
· Changement du débit des pompes
Dans le cas d'un fluide de forage monophasique, les
règles de base du Well Control peuvent être appliquées.
Débit constant et changement de la pression au fond par manipulation de
la pression en tête de tiges.
Dans le cas d'un fluide de forage biphasique, le changement
de la pression en surface n'est pas directement suivi par celui de la pression
de fond, et ce dû à la compression du gaz.
Temps de retard (Lag-Time). Ou.
C'est le temps pour que le changement de la pression à la duse montre
une réponse en tête de tige. Il est en général
estimé à 1minute/1000 feet de distance totale dans le cas
où on a 100% de liquide dans le puits.
Si on a une grande quantité de gaz dans le puits
(comme pour un liquide gazeifié), le Lag-time dépend de la somme
des vélocités dans un système mixte sous
différentes pression, plus le temps de compression et
décompression du gaz. Ce qui prend plus longtemps. Pour les liquides
gazefiés, il faut en moyenne prendre 5 à 8 minutes de plus.
La propagation de pression dans les fluides est analogue
à la vitesse du son dans ce milieu. Le temps, pour qu'une onde de
pression voyage de la duse vers un point défini est dit « pressure
transient lag-time ». Donc le fait d'appliquer une pression avec la duse
ne pressurise pas le puits instantanément, c'est un principe très
important à prendre en compte lors des opérations.
Changement de la BHP. Dans le cas
d'un fluide monophasique (Flow Drilling) le changement de pression au niveau de
la pression en tête de tiges est égal au changement au fond du
puits.
S'il n'y pas de gaz dans la garniture (injection concentrique
casing ou parasite) le changement de pression d'injection va affecter la
pression au point d'injection du gaz en premier lieu, et la pression de fond
suivra ensuite le changement (#177;).
S'il y a du gaz dans la garniture (injection par
l'intérieur des tiges), le changement de la pression en tête va
être moins important que celui de la BHP. Et ceci parce que le gaz
à l'intérieur des tiges est toujours comprimé au contraire
dans l'annulaire on le trouve détendu. La différence est lue en
pression en tête d'annulaire. (Figure 1.8)
Chapitre1-Underbalanced Drilling : Theorie et Principes
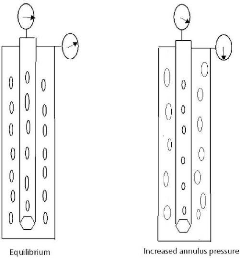
13
Figure 1.8 : Changement de la pression au fond est
inférieur à celui en tête.
Matrice de décision Well
Control. Même si, en UBD on laisse les fluides de formation
circuler dans l'annulaire jusqu'en surface. Le débit en surface est
prudemment controlé, et le contrôle du puits est maintenu en
faisant en sorte que les pressions en surface et la production soient aussi
faibles que possible. Une matrice de décision est toujours
élaborée montrant les pressions en tête et les volumes de
retour et les décisions à prendre dans chaque cas. (Figures 1.9
et 1.10)
Si, pendant les opérations, le puits doit être
tué pour raison de sécurité, cela pourrait être pour
l'une de ces raisons :
· Panne ou fuite d'un équipement de control de
pression en surface.
· Rupture de la garniture
· Remontée d'H2S inattendue
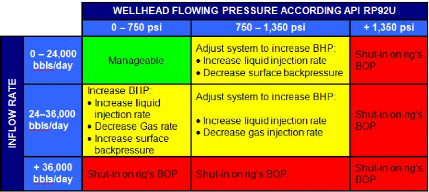
Figure 1.9 : matrice de décision, cas invasion
liquide. (Valeurs pour Weatherford)
14
Chapitre1-Underbalanced Drilling : Theorie et Principes
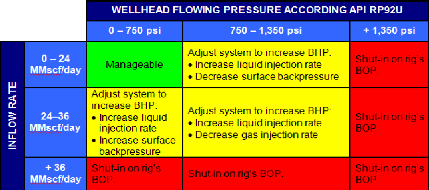
Figure 1.10 : matrice de décision, cas invasion
gaz. (Valeurs pour Weatherford)
La matrice de décision dispose les paramètres
comme suit :
· Les pressions de surface sur l'axe des x :
i. Vert : 50% ou moins de la pression dynamique du RCD
ii. Jaune : de 50% à 90% de la pression dynamique du
RCD
iii. Rouge : au-dessus de 90%, nous avons une situation de Well
control.
· Les débits de retour sur l'axe des y :
i. Vert : jusqu'à 60% de la capacité du
système de séparation
ii. Jaune : de 60% à 90% de la capacité du
système de séparation
iii. Rouge : au-dessus de 90% nous avons une situation de Well
control.
1.2.2 Stripping
Le mot stripping désigne le fait de mouvoir les tiges
de forage avec le puits fermé par le RCD, le BOP annulaire, ou alors le
pipe rams, avec une pression limitée ou nulle en tête d'annulaire.
C'est une technique commune aux UBOs quand il y a un risque de venue importante
de gaz pendant les manoeuvres de la garniture. Les opérations en
général sont faites avec une pression de fermeture très
faible ou carrément nulle.
Usure sur les éléments
d'étanchéité du RCD. Le stripping cause une
usure des éléments d'étanchéité. La
sévérité de l'usure dépend essentiellement du type
de tige de forage, de l'épaulement du tool joint, de la vitesse de
manoeuvre, et également de la force appliquée sur ces
éléments d'étanchéité par la clamp (voir
figure 1.4-a). En général les fabricants livrent avec le RCD un
tableau de la limite d'utilisation des Rubbers, si cette limite est
dépassée, ils doivent être changés. Les valeurs pour
le model illustré dans la Figure-1.4 sont définies dans le
Tableau-5
15
Chapitre1-Underbalanced Drilling : Theorie et Principes
Tableau 5 : limites de stripping
recommandées (Sonatrach)
|
|
WHP<10% de la pression dynamique du RCD
|
WHP entre 10% et 40%de la pression dynamique du RCD
|
WHP entre 40% et 70%de la pression dynamique du RCD
|
WHP>70% de la pression dynamique du RCD
|
Maximum longueur permis avant remplacement (mètres)
|
3655
|
2435
|
1525
|
610
|
Maximum temps opérationnel (heures)
|
600
|
500
|
200
|
150
|
Déplacement par la boue.
C'est une pratique qui se fait souvent lors des remontées
de garniture, pour « tuer » le puits. On remonte l'outil jusqu'au
sabot, et on déplace le fluide de forage par une boue plus lourde de
façon à ce que la pression hydrostatique résultante des
deux colonnes soit suffisante pour contrebalancer la pression du
réservoir (Figure 1.11). La colonne supérieure est dite Mud Cap.
La boue lourde doit avoir des caractéristiques bien définies.
Viscosité. Pour minimiser l'effet de
mélange avec le fluide de forage, la viscosité doit être
élevée. Mais ne doit pas être plus grande de plus de 10
secondes sur le viscosimètre Marsh. De grandes viscosités
entraineraient un effet de pistonnage (swabbing) et des problèmes lors
de la recirculation avec le fluide de forage.
Densité. En pratique la densité de la
boue lourde ne dépasse jamais celle du fluide de forage de plus de 40
points.
Cette technique est évidemment très couteuse en
temps, la durée d'un déplacement peut aller jusqu'à 7 ou 8
heures. Certaines compagnies préfèrent utiliser une DDV (downhole
deployment valve) pour empêcher les fluides de formation de remonter en
surface. Cette dernière agit comme une barrière de
sécurité, empêchant les fluides de formation de remonter
dans le puits. Elle actionnée hydrauliquement par des manches qui
ouvrent et ferment le clapet (Figures 1.121.13).
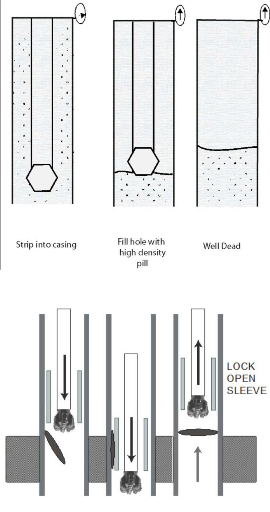
Figure 1.11 : principe du Mud Cap (Rehm,
2012)
Figure 1.12 : DDV, principe de fonctionnement (Rehm,
2012)
16
Chapitre1-Underbalanced Drilling : Theorie et Principes
17
Chapitre1-Underbalanced Drilling : Theorie et Principes

Figure 1.13 : Illustration DDV dans le puits
(Weatherford)
1.2.3 Pipe light
« Pipe light » ou tiges légères est un
terme pour la condition où la force appliquée sur le fond de la
garniture est égale ou presque égale au poids de celle-ci. Ce
phénomène est observé partiellement pendant les strippings
ou alors pendant les opérations de snubbing quand il y a une pression
venant de la formation qui tend à pousser la garniture hors du trou.
Le point « pipe light » doit toujours être
calculé dans ces cas et le Driller doit être informé de ce
risque. Il est donné suivant la formule :
WdS -- (nr2P) --* 0 (4) et donc P
=
(1.4)
Wds
71:12
P étant pression en tête d'annulaire et r le rayon
du plus large composant de la garniture. Wds : poids de la garniture.
1.3 Flow Drilling, Forage avec fluide monophasique
1.3.1 Introduction
C'est un système qui utilise un liquide monophasique comme
fluide de forage. Ce liquide peut être de l'eau, du brut, ou même
parfois une boue. Ce chapitre discute des raisons et des limitations
d'utilisation d'un système monophasique.
1.3.2 Historique1
L'utilisation délibérée d'un liquide seul
comme fluide de forage en UBD n'est pas une nouvelle approche, car on trouve
des cas datant des années 50'. La plus grande partie de la
littérature à ce sujet décrit l'utilisation de l'eau
salée par la Gulf Oil Company au Texas.
Dans les années 50', ils ont dû faire face à
un réservoir formé de siltstones très fins. Ces formations
ont une très faible perméabilité et une grande
porosité. Pour limiter les venues de gaz pendant les connections et les
remontées, ils ont tout d'abord utilisés une boue à 1.92
kg/l, ce qui a limité le ROP à 1m/h au maximum.
1 Référence Rehm, 2012.
18
Chapitre1-Underbalanced Drilling : Theorie et Principes
L'opérateur a trouvé qui s'il forait la formation
avec une boue salée à 1.17kg/l, la vitesse d'avancement s'en
retrouvait multipliée par 10 (10m/h), et que le gaz pouvait être
controlé avec un séparateur. Ce qui a prodigué un gain de
temps incroyable.
1.3.3 Avantages
Système simple. L'utilisation
d'un fluide de forage monophasique simplifie tout le processus.
Nécessite moins d'équipements en surface. En plus les changements
d'ECD dus au mouvement des tiges dans puits ou au changement du débit
des pompes sont faciles à prédire.
Réduction des coûts. Des
équipements de surface pour l'injection de gaz, ou du personnel
supplémentaire.
Les systèmes MWD conventionnels peuvent
être utilisés. Pas besoin de MWD-EM
(électromagnétique), car le signal de la
télémétrie par pression passe normalement (sans
interférences).
Indice de production en cours de forage.
Puisqu'on fore avec un fluide monophasique, les premiers indices
de gaz dans le séparateur sont ceux d'une production de la formation, et
donc de l'entrée dans une zone à gaz, et pour le cas d'une zone
à huile, l'indice de production se voit directement à
l'augmentation du niveau des bacs.
1.3.4 Limites et défis de la technique
Non appropriés pour les réservoirs
très deplétés. Le degré
d'underbalance ne peut être descendu en-dessous d'un certain point sans
toucher à d'autres nécessités comme le bon nettoyage des
parois. Donc le Flow Drilling n'est pas désigné pour les
réservoirs ayant une pression très faible, il y aura
nécessité d'injection de gaz pour alléger la colonne et
atteindre un drawdown désiré.
Contrôle de la pression. Il peut
être risqué de forer avec un fluide qui est créé une
situation d'underbalance même en circulation. En cas de problème
la remise en overbalance prendrait un temps considérable. Il serait
préférable d'utiliser une phase liquide qui seule, engendrerait
un overbalance et de l'alléger avec un gaz.
1.4 Forage avec fluide Biphasique
Cette section discute de la théorie et utilisation des
systèmes gazéifiés, des critères de
sélection des fluides de forage et essentiellement de l'utilisation du
tubage concentrique comme moyen d'injection du gaz.
Les fluides gazéifiés sont une mixture liquide/gaz
sans ajout d'un émulsifiant ou stabilisant quelconque. Ils sont faciles
à manipuler et mettre en oeuvre. La phase liquide pouvant être de
l'eau ou du brut, le gaz peut être de l'air, du gaz naturel, de l'azote
ou du CO2.
Le problème majeur avec ce système est le
phènomène de séparation du gaz avec le liquide, ce qui
crée des bouchons difficiles à contrôler en surface.
(Figure 1.14)
19
Chapitre1-Underbalanced Drilling : Theorie et Principes
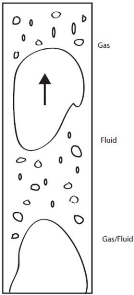
Figure 1.14 : Séparation gaz/liquide. (Rehm,
2012)
1.4.1 Historique2
Les premières applications des « mélanges
gaz-liquide » en forage se sont faites très tôt,
essentiellement pour résoudre des problèmes de perte de
circulation. Le premier cas connu fut aux USA en 1866, on utilisait une boue
bentonitique en plus de gaz naturel injecté dans le puits.
Dans les années 1960s, les système de liquide
aéré furent utilisés dans les Rocky Mountains dans le but
d'augmenter la vitesse d'avancement et réduite les risques de perte. La
technologie s'est vraiment développée au début des
années 1990s avec les premières applications de l'UBD en
offshore.
1.4.2 Definitions
Drawdown. Exprimé en
pourcentage, il représente la déplétion
créée entre celle appliquée par le fluide de forage et la
pression du réservoir. (Exemple : un drawdown de 10% sur un
réservoir de pression 200 bars équivaut à appliquer une
pression dynamique de 190 bars sur les parois en cours de forage)
Ratio des volumes en surface. Varie
entre 1:1 jusqu'à 100:1. C'est le ratio du volume injecté de gaz
sur celui du liquide. C'est un outil essentiel pour la mesure des volumes
nécessaires de gaz.
2 Référence Rehm, 2012
20
Chapitre1-Underbalanced Drilling : Theorie et Principes
Qualité. C'est la mesure du
volume du gaz sur celui du liquide à n'importe quel point du puits.
Reporté en général en pourcentage. (Figure 1.15)
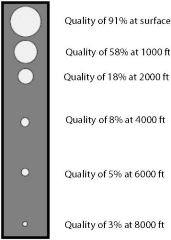
Figure 1.15 : Illustration de l'évolution de la
qualité du gaz. (Rehm, 2012)
Jet sub. C'est un outil
incorporé dans la garniture qui facilite le passage du gaz de
l'intérieur de celle-ci vers l'annulaire, il est
généralement placé entre 1000 m et 1200 m de profondeur,
avec des duses ressemblant à celles de l'outil, il laisse
échapper le gaz vers l'annulaire. Très intéressant pendant
les connections car il laisse échapper du gaz dans l'annulaire pendant
l'arrêt de circulation, ce qui permet de maintenir un drawdown. (Figure
1.16)
Parasite. Methode d'injection du gaz
à la base du tubage de surface.
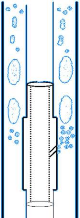
Figure 1.16 : Principe Jet sub.
21
Chapitre1-Underbalanced Drilling : Theorie et Principes
Tubage concentrique. Ou garniture de
tubage dual, c'est une methode d'injection du gaz dans le puits, le
concentrique est défini comme étant le volume entre les deux
tubages.
Constant Circulating Sub. Prodigue une
méthode pour circuler en continue même pendant les connections.
(Le plus connu ne Non-Stop Driller, Figure 1.17)

Figure 1.17 : Constant circulating sub. (Rehm, 2012 et
CANRIG)
Effet de dune. En puits horizontaux,
les cuttings ont tendance à se déposer sur la partie horizontale
du puits et à former des dunes. (Phénomène très
courant en Algérie, car la phase liquide utilisée est du brut
avec une Yield Value=0)
Zone des 60°. Quand le puits est
incliné de 50° à 70°, il y a des revers
d'écoulement qui causent le dépôt des cuttings dans cette
zone. Menant parfois à des coincements lors des remontées
Remarque : l'effet de dune et le
dépôt des cuttings dans la partie inclinée peuvent
être évités par le pompage d'un bouchon HighVis (liquide
très visqueux) qui va nettoyer le puits, en général ce
bouchon est pompé chaque 50m forés.
1.4.3 Avantages
Flexibilité. La
possibilité de contrôler la pression de fond et aller vers des
drawdowns plus élevés. C'est un outil idéal pour le forage
des zones déplétées ou à faible
perméabilité.
Réduire l'endommagement du
réservoir.
Eliminer les pertes de circulation.
Eliminer les risques de collage par pression
différentielle. Augmentation de la vitesse d'avancement et de la vie de
l'outil. Evaluation du réservoir.
22
Chapitre1-Underbalanced Drilling : Theorie et Principes
1.4.4 Methode de réduction de la pression de
fond
La pression hydrostatique exercée sur les parois du
puits est réduite par l'injection du gaz dans ce dernier. L'addition du
gaz diminue donc la pression hydrostatique de la colonne dans l'annulaire par
le déplacement du liquide hors du trou. (Réduction
hydrostatique)
Dans le régime hydrostatique, avec les
débits d'injection de gaz faibles, la pression au fond est très
réceptive au changement de ratio d'injection. Et tend à
être instable.
Avec l'augmentation du débit injecté, la
vélocité du liquide dans l'annulaire croit également, ce
qui induit une augmentation des pertes de charges dans l'annulaire. Le
système rentre dans le régime de friction. Où une
augmentation du ratio des volumes en surface conduit à une augmentation
des pertes de charge dans l'annulaire ce qui va entrainer une augmentation de
la pression au fond, c'est ce qui arrive dans les sections de petit
diamètre (41/2), mais en général il se produit
un équilibre entre deux phénomènes, qui va stabiliser la
pression de fond. La pression de fond sera plus réactive au changement
de la pression en surface qu'à celui de la quantité de gaz
injectée. (Figures 1.18 et 1.19)
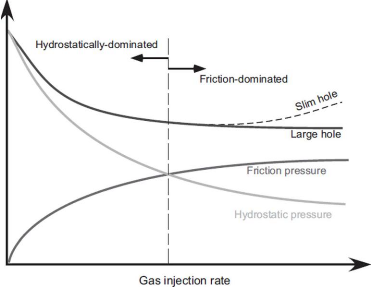
Figure 1.18 : Régimes de pression en fonction du
débit de gaz injecté. (Rehm, 2012)
23
Chapitre1-Underbalanced Drilling : Theorie et Principes
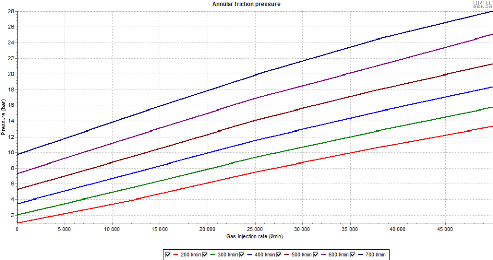
Figure 1.19 : Evolution des frictions dans l'annulaire
en fonction du débit d'injection de gaz pour différents
débits de liquide.
1.4.5 Défis de la technique
Le coût. Le prix d'un
système de fluide gazéifié est évidemment plus
élevé que pour un système monophasique. Il présente
plus d'exigences ; matériel de surface en plus (compresseurs,
boosters...), système d'injection du gaz (Tubage concentrique,
parasite...), personnel en plus.
Les montées de pression. Les
systèmes gazéifiés sont instables, le gaz se sépare
du liquide par gravité et forme des bouchons qui arrivent en surface
périodiquement, ce qui génère des à-coups de
pression à la duse. Après passage au séparateur, la
colonne dans l'annulaire est désormais plus lourde ce qui augmente la
pression au fond, et à mesure qu'un bouchon de gaz se forme et remonte
avec expansion ce qui réduit à nouveau la pression au fond. Le
cycle se répète ainsi, la durée d'un cycle peut varier de
10 minutes à une heure en général.
C'est un problème dangereux qui peut
générer des problèmes d'instabilité des parois, et
qui peut endommager la formation si au cours du cycle le puits se retrouve
momentanément en overbalance.
Imbibition. Les forces capillaires
dans le réservoir peuvent causer ce phénomène, ce qui peut
endommager le réservoir et également donner une impression de
perte partielle. Pour éviter ce phénomène, la pression en
annulaire doit être inférieure à une certaine valeur pour
contrebalancer les forces capillaires.
Tuer le puits périodiquement.
Peut créer des situations d'overbalance et endommager le
réservoir. Problème peut être réglé par
l'installation d'un DDV (downhole deployment valve) (voir Figures 1.12 et
1.13).
24
Chapitre1-Underbalanced Drilling : Theorie et Principes
Corrosion. Les fluides diphasiques
peuvent causer un phènomène de corrosion des tubulaires, par la
présence d'oxygène à une température
élevée dans le puits.
Risque d'incendie. Présence
de gaz en permanence, surtout dans le cas de l'utilisation du gaz naturel comme
gaz injecté.
Frottements et torque. Le facteur de
friction est plus élevé dans le cas d'un fluide biphasique, ce
qui cause des frottements en plus du « whirling effect » qui va
entrainer des torques élevés.
Mesures en cours de forage MWD. Les
systèmes conventionnels de MWD (mudpulse telemetry) ne fonctionnent pas
avec les fluides diphasiques, car le signal arrive avec trop de bruit pour
être interprété correctement.
C'est pour ça qu'on utilise les systèmes EM MWD
(electromagnetic MWD) qui transmet les mesures sous forme d'un signal
électromagnétique.
Quoiqu'à Hassi Messaoud, la couche LD2 (LIAS)
composée essentiellement d'anhydrite saturée en eau salée,
brouille le signal de l'EM MWD, le rendant impossible à intercepter en
surface. Une solution ingénieuse consiste à brancher une barre
métallique en plomb dite Sinker bar sur l'outil de transmission du MWD,
reliée par un câble de wireline à l'intérieur des
tiges jusqu'à une antenne plus haut qui va être placée de
façon à pouvoir transmettre le signal jusqu'en surface.
1.4.6 Méthodes d'injection du gaz dans le puits
Injection par Drill Pipe. La
technique conventionnelle utilisée en UBD est d'envoyer le liquide et le
gaz en même temps à l'intérieur de la garniture de forage.
Cette methode ne requiert pas de grandes modifications par rapport à un
puits conventionnel. (Figure 1.20)
Dans ce cas, la présence de gaz dans l'intérieur
des tiges va brouiller le signal du MWD conventionnel et le rendre illisible,
et ce pour des ratios de surface au-dessus de 20%.
L'utilisation de l'injection par tiges signifie que le gaz va
passer à travers la BHA, ce qui va influer grandement sur la performance
des moteurs de fond.
L'un des problèmes majeurs de cette methodes est le
contrôle de la pression de fond pendant les connections. Ceci est
pourtant possible par l'incopporation d'un constant circulating sub, ou bien
alors d'un jet sub.
Chapitre1-Underbalanced Drilling : Theorie et Principes
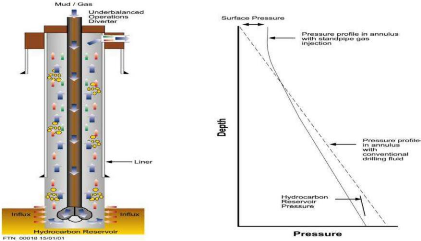
Figure 1.20 : Injection par Drill Pipe ou stand pipe.
(Blade)
Injection par parasite. Cette
méthode utilise un tubing parasite de petit diamètre
(11/2 ou 23/8) comme conduite pour l'injection du gaz, ce
dernier est descendu avec le tubage, le point d'injection se trouve donc dans
la partie tubée du trou. (Figure 1.21)
Cette technique présente nombre d'avantages comme le
fait de pouvoir continuer l'injection de gaz pendant les connections, ou encore
l'élimination des problèmes de performance du moteur de fond, et
surtout la possibilité de contrôler l'afflux de la formation en
manipulant le débit de gaz seulement. Mais il présente toutefois
certains inconvénients, comme le besoin d'apporter des modifications
à la tête de puits pour laisser passer le parasite, ou encore le
risque d'endommagement du parasite pendant sa descente.
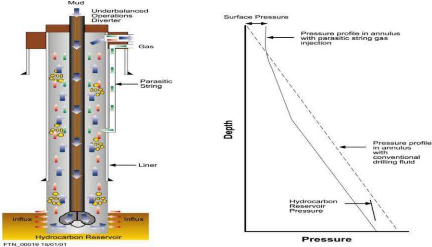
25
Figure 1.21 : Injection par parasite.
(Blade)
Chapitre1-Underbalanced Drilling : Theorie et Principes
Injection par tubage concentrique.
C'est la technique la plus utilisée au monde, l'injection
de gaz se fait dans l'espace annulaire entre deux tubages, elle a
été mise au point pour remédier aux problèmes
relatifs à l'utilisation du parasite et de l'injection par tiges de
forage. (Figure 1.22)
Il présente un seul inconvénient majeur,
à cause du volume important de l'espace annulaire, il se produit un
phènomène dit effet d'accumulateur, qui va induire une
fluctuation de pression au fond causant beaucoup de problème. Ce point
sera discuté plus en détail dans le chapitre 5. (Voir aussi les
travaux de Myktiw, 2003)
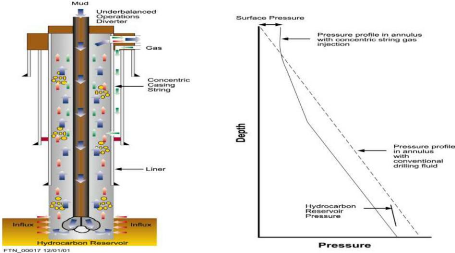
26
Figure 1.22 : injection par concentrique.
(Blade)
1.5 Sélection des puits candidats à
l'UBD
Une évaluation détaillée des
propriétés du réservoir et une étude poussée
sur les fluides en place en plus des propriétés des roches
réservoirs est recommandée avant d'entamer le design d'un puits
UBD.
La sélection des puits candidats à l'UBD s'est
considérablement développée durant les dernières
années, et il existe désormais des softwares capables d'assister
l'ingénieur dans ses études. L'un des algorithmes les plus
utilisés est présenté dans la Figure- 1.23. Il y plusieurs
aspects à prendre en compte.
Type de puits. Le réservoir est
l'objectif de la technologie UBD, et tant que les aspects positifs sur celui-ci
ont été définis, le type de puits peut être revu
pour être plus rentable et plus profitable techniquement.
L'underbalanced drilling peut être appliqué à
un nouveau puits foré, mais également à un ancien puits
qui aura été repris en Re-entry. Il peut être
implémenté en offshore tout comme en onshore et des puits
multilatéraux peuvent être forés en underbalance.
27
Chapitre1-Underbalanced Drilling : Theorie et Principes
Considérations du réservoir.
Le forage en underbalance d'un réservoir proprement
sélectionné va résulter en une meilleure production car
cette technique élimine le risque d'endommagement du réservoir
par la boue de forage.
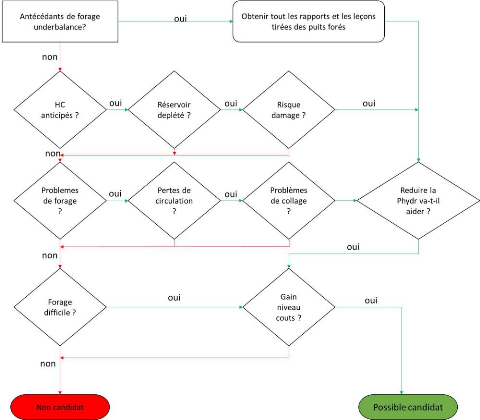
Figure 1.23 : Séléction candidat pour UBD.
(Aadnoy, 2009)
Mécanismes d'endommagement.
L'endommagement du réservoir peut résulter de
diverses actions. Mais les causes les plus communes sont le forage, la
complétion et l'endommagement induit par la production. Le forage et la
complétion causent en général des dommages
résultants de l'intrusion de fluides et de particules solides dans la
formation productrice.
La production cause également un endommagement du
réservoir, et ce dû à une incompatibilité de fluides
ou à des altérations de la pression du réservoir.
28
Chapitre1-Underbalanced Drilling : Theorie et Principes
En général, quel que soit l'origine de
l'endommagement, il se présente sous les formes suivantes :
· Changement dans la perméabilité absolue de
la roche.
· Changement dans la perméabilité relative
aux Hydrocarbures.
· Changement dans la viscosité des fluides de
formation.
L'endommagement peut être induit par voie
mécanique, chimique, biologique ou thermique.
Mécanique. Causé par la migration des
particules fines des puits en cours de production, ou alors l'intrusion de
particules solides de la boue qui vont boucher les pores et les microfractures
de la roche.
Chimique. Résultat d'une
incompatibilité entre fluides, qui peut causer la précipitation
de sels ou bien alors la formation d'émulsions.
Biologique. Causée par l'intrusion de
bactéries dans le réservoir suite à un traitement
chimique.
Thermique. Ce phenomène arrive souvent
lorsqu'on fore en underbalance avec un fluide biphasique. Il se produit un
phénomène appelé « glazing effect », le gaz
utilisé pour le forage se mélange avec les cuttings, et sous
haute température il se forme un émail imperméable
très difficile à enlever.
Tableau 6 : Types de réservoirs candidats et non
candidats.
|
Candidats
|
Non candidats
|
Formation qui présente un potentiel d'endommagement
élevé, avec des skins de 5 ou plus dans les puits
conventionnels
|
Puits dans des zones où le coût du forage
conventionnel est très bas
|
Formations qui ont tendances à faire des collages par
pression différentielle
|
Zones où le ROP est très élevé
(>15m/h)
|
Formations présentant des risques de pertes
sévères
|
Réservoir à très haute
perméabilité
|
Formations naturellement fracturées
|
Réservoirs à très faible
perméabilité ou médiocre
|
Réservoir de faible à moyenne
perméabilité
|
Formations peu consolidées
|
Réservoirs très hétérogènes
avec des zones de différentes perméabilités,
porosités.
|
Zones avec des problèmes d'instabilité des
parois
|
Zones à faible ROP avec le forage conventionnel
|
Réservoirs avec des lits d'argiles, de charbon
intercalés.
|
|
29
Chapitre2-UBD dans la région de Hassi Messaoud
Chapitre-2 UBD dans la région de Hassi
Messaoud1
2.1 Descriptif du champ
Le champ de Hassi Messaoud est un anticlinal applati
situé dans le bassin de Berkine en Algérie, à 800 km au
sud-est d'Alger, dans la partie nord du désert du Sahara (Figure 2.1).
Découvert en 1956, la zone productive se trouve dans le Cambrien, des
grés quartzitiques d'une épaisseur de 60-150 m, le champ est
divisé géographiquement en 25 zones, qui sont
séparées par des perméabilités faibles ou alors des
failles, où il n'existe pas une isolation complete. (Figure 2.2), 4
horizons productives ont été identifiées : le Ra qui est
le plus important, le R2, Ri et R3. Le Ra est lui-même divisé en 4
drains qui varient selon la productivité et qui sont classifiés
selon le pourcentage de grés perméables contre celui des
discontinuités créées par des lits d'argiles. Les
grés sont naturellement fracturés avec une
perméabilité primaire de l'ordre de 10 milliDarcy et peut
atteindre jusqu'à 1000 milliDarcy dans certains cas. Les reserves
initales estimées s'élevent à 12.6 milliards de barils qui
le place dans la catégorie des gisements géants. L'huile produite
est légère avec une densité de l'ordre de 45°API avec
un GOR moyen de 200m3/ m3. La temperature de la formation
est de 120°C en moyenne. La pression initale du réservoir
était 473 bars et maintenant de l'ordre de 140 à 250 bars. Le
point de bulle varie entre 142 et 196 bars.
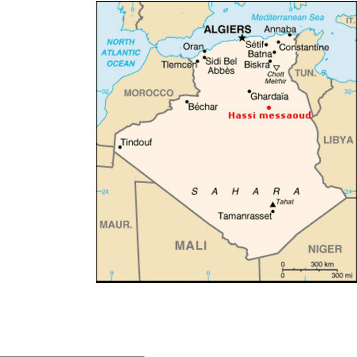
Figure 2.1 : Localisation Hassi Messaoud (Moore,
2004)
1 Moore, 2004
30
Chapitre2-UBD dans la région de Hassi Messaoud
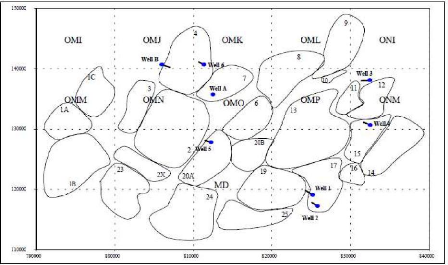
Figure 2.2 : les zones à Hassi Messaoud avec
localisation de puits forés en UBD. (Moore, 2004)
2.2 Historique de l'UBD à Hassi Messaoud
Le design de puits standard à Hassi Messaoud est comme
suit : tubage 185/8 à 500m, 133/8 à 2500m
et 95/8 à 3200 m TVD. Et un liner 7» vers 3300-3500m, la
zone productrice est forée en horizontale et complétée en
openhole. Si un problème de stabilité des parois est
envisageable, un liner perforé est descendu. Le Cambrien est
composés de grés très abrasifs, en conséquence la
vitesse de pénétration dans la phase réservoir a toujours
été très lente (de l'ordre de 0.5-1 m/h). Le forage en
underbalance à initialement reçu un certain intérêt
dans le but d'augmenter ce dernier. Des expériences
précédentes montraient que plus la pression hydrostatique de la
boue dans le puits approchait de celle du réservoir, plus on avait des
ROPs intéressants. Spécialement en utilisant des outils
tricônes.
La décision fut prise de forer un puits test en
underbalance, un puits vertical (puits A), décidé pour
éliminer la besoin de MWD. En octobre 2001, le puits a été
foré avec injection d'azote dans la colonne. Dû à la faible
perméabilité du réservoir, aucune production n'a
été reportée pendant le forage, et donc la condition
d'underbalance n'a pas été confirmée. 91 mètres ont
été forés avec un ROP 3.5 fois superieur au ROP moyen dans
cette zone. Basé sur les résultats de ce puits, d'autres puits
underbalance ont été planifiés afin d'évaluer la
faisabilité de la technologie.
Le premier puits horizontal en UBD en Algérie fut
foré en mars 2002, le drawdown a été limité
à très proche de la balance afin d'éviter tout risque
d'instabilité des parois.
31
Chapitre2-UBD dans la région de Hassi Messaoud
2.3 Planning et développement des
opérations
Dès lors qu'il a été
décidé de continuer le projet, plusieurs décisions ont
dû être prises. La première ayant été de
comment achever un underbalance et le maintenir en cours de forage, les puits
précédent ayant été forés avec une boue
à l'huile de densité 0.9, la solution logique a été
de forer avec du brut, étant le fluide qui cause le moins de dommage
à la formation et avec une densité de 0.83 en moyenne. En plus de
sa disponibilité, il élimine les problèmes de corrosion du
matériel tubulaire.
La deuxième décision majeur concernait la
méthode la méthode d'injection de l'azote dans le puits, la
methode conventionnelle était l'injection par Drill pipe, alors que le
technique présente nombre d'avantages, il a été
décidé d'utiliser l'injection par tubage concentrique pour palier
à tout soucis pendant les opérations. Pour rendre
l'opération possible, le liner 7» doit être raccordé
à un Tie-back et l'injection se fait entre le tubage 95/8 et
le Tie-back 7».
2.4 Paramètres opérationnels et
problèmes
Avec le choix du tubage concentrique comme moyen d'injection,
la fenêtre opérationnelle est très petite. Les moteurs de
fond requiert un débit de liquide de 700-900 lpm, et le point
d'injection de Nitrogène ne peut pas être plus bas que le point
d'ancrage du liner 7» (vers 3000 m TVD), et le débit de gaz maximum
fourni en surface ne peut dépasser 65 m3/min. les simulations
montrent que pour obtenir un drawdown de 10%, il serait nécessaire de
jouer sur d'autres paramètres. La manière la plus simple serait
de diminuer le débit d'injection du liquide, mais ceci entraine une
baisse de performance du moteur, en plus d'influencer sur les performances de
nettoyage du drain horizontal. Les principaux problèmes posés
sont décrit ci-dessous :
Stabilité des parois.
Initialement les études de stabilité ont
indiqués que la pression de fond pouvait être descendue à
10-15% en dessous de celle du réservoir sans rencontrer de risque de
collapse du trou dans le Cambrien.
Outil et moteurs. Au début
le Cambrien a été foré avec des outils
imprégnés avec une turbine ou bien alors un PDM high speed. Mais
l'expérience a montré que ces outils qui transmettent leur torque
au moteur ne convenaient pas pour une formation hautement abrasive comme le
Cambrien. Leur utilisation entraine une usure très rapide du moteur ce
qui conduit bien sûr à le remonter pour le changer. Il a alors
été décidé d'utiliser des outils tricônes
à pastilles de Tungstène.
Effet d'accumulateur.
Phénomène très souvent rencontré dans
l'utilisation du tubage concentrique comme moyen d'injection. Au fur et
à mesure de l'injection, l'annulaire Tubage/Tubage se charge de gaz un
peu comme une bouteille de gaz et la pression à l'intérieur
augmente petit à petit jusqu'à atteindre la pression dans
l'annulaire Tubage/Tiges à cette profondeur, il se libère alors
une bulle de gaz qui va alléger la colonne et réduire la pression
au fond. La pression dans l'annuaire Tubage/Tubage chute également, et
du liquide entre dans celui-ci, temps qu'il se charge à nouveau pour
expulsera une autre bulle la première a déjà
commencée son ascension. Donc il n'y a pas de stabilité de la
BHP.
32
Chapitre2-UBD dans la région de Hassi Messaoud
Etude sur le NPT. Des études
sur le temps non productif (NPT) ont été menées sur le
puits B, les résultats ont été très positifs avec
une réduction de moitié des temps non productifs.
2.5 Resultats des puits forés
Puits 1. Après plusieurs
problèmes liés aux équipements de surface, le puits a
été foré en underbalance sur une longueur de 1117m avec un
ROP moyen de 6.08m/h, 87% mieux que la moyenne dans le secteur. Après
conduite d'un flow test à la fin du forage, la production était 2
fois plus élevée qu'attendue. Ce qui a encouragé sur les
bénéfices de l'UBD en termes de productivité du
réservoir.
Puits 2. Dans ce cas-ci, la
production a été multipliée par 3.4 avec un ROP moyen de
5.5m/h, moins élevé qu'attendu.
Puits 3. Ce puits a
présenté un ROP moyen de 7.04m/h, 117% plus élevé
que pour les puits en overbalance. 909m ont été forés en
tout avec un début de production après 533m. La production
été la même que pour la moyenne de zone en question.
Puits 4. Des problèmes
d'instabilité des parois furent rencontrés, et le puits s'est
éboulé après 174m dorés dans réservoir. La
décision de faire un sidetrack fut prise pour éviter la zone
à problèmes, le sidetrack a été forés
alternativement en underbalance et en overbalance sur 431m. Un ROP moyen de
6.96m/h fut recordé pour les sections UBD, et un gain de production de
1.7 fois la moyenne du réservoir fut notée.
Puits 5. 815m de drain en UBD avec
un ROP moyen de 13.99m/h, 330% plus rapide que la moyenne de la région.
La production était 3.9 fois superieur à la moyenne de la
région.
Puits 6. 768m forés avec un
ROP moyen de 8.32m/h, mais des problèmes d'instabilité furent
rencontrés, un liner perforé a donc été descendu
durant la complétion.
Chapitre2-UBD dans la région de Hassi Messaoud
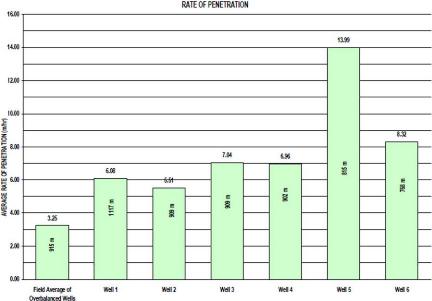
Figure 2.3 : Comparaison ROPs des puits forés
en underbalance. (Moore, 2004)
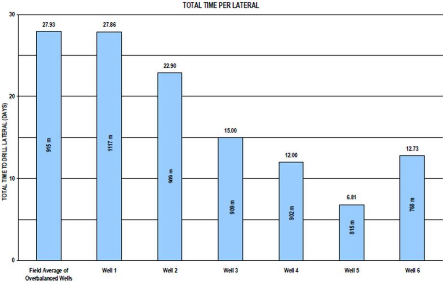
33
Figure 2.4 : Comparaison temps pour forer la partie
latérale des puits UBD. (Moore, 2004)
34
Chapitre2-UBD dans la région de Hassi Messaoud
La Figure 2.3 montre bien l'amélioration de la vitesse
d'avancement dans le cas de l'underbalance. La Figure 2.4 quant à elle
illustre l'avantage de l'UBD pour minimiser le temps de forage, qui est
réduit de moitié en moyenne.
2.6 Conclusion
Beaucoup de considérations doivent être prises en
compte dans le design d'un puits en underbalance :
· Propriétés des roches
· Pression du réservoir
· Stabilité des parois
· Type de fluide de forage
· Methode d'injection du gaz dans le puits
· Effet des fluides compressible sur le MWD
· Exigence du moteur de fond
· Type d'outil de forage
· Corrosion
· Programme de complétion
Un planning détaillé et un travail consciencieux,
est essentiel pour la bonne conduite d'un projet de puits en UBD.
Pour une meilleure efficacité, une bonne
coopération entre l'opérateur et le personnel de service est
primordiale.
L'UBD a montré son intérêt dans
l'amélioration de la vitesse d'avancement de manière
significative à Hassi Messaoud.
Une grande amélioration de la productivité des
puits a été enregistrée, ce qui présente un second
point positif pour l'UBD. (Figure 2.5)
L'enregistrement de la production en cours de forage aide
à mieux comprendre le réservoir pour une meilleure prise de
décision de la suite des opérations.
Chapitre2-UBD dans la région de Hassi Messaoud
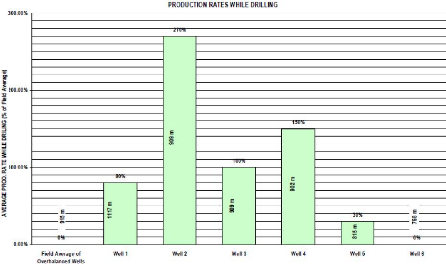
35
Figure 2.5 : Débit de production selon la
moyenne du secteur pour les puits en UBD (Moore, 2004)
36
Chapitre3-Modélisation des écoulements
bi-phasiques
Chapitre-3 Propiétés des mélanges
liquide/gaz, Modélisation et Simulation des écoulments
Multiphasiques
3.1 Facteur de volume
C'est un facteur qui montre comment un volume, sous des
conditions spécifiques de pression et de volume (in-situ), change en
fonction des conditions de surface (standards), son expression
générale est définie comme suit :
vi(P,T)
Facteur de volumes _ (3.1)
vi,sc
Il est très important pour convertir les volumes depuis
les conditions du réservoir jusqu'aux conditions de surface.
Facteur de volume du gaz. Le facteur
de volume du gaz exprimé en [scf/stb] est donné par :
_ Psc T z _ 14.7 T +459.67 z
B(3.2)
g P Tsc P 519.67
Avec l'augmentation de la pression, le facteur de volume du
gaz approche de zéro et l'effet de la temperature sur ce dernier devient
moins significatif.
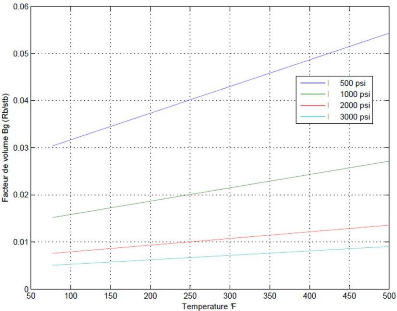
Figure 3.1 : Evolution du facteur de volume pour le
gaz naturel en fonction de le temperature.
Chapitre3-Modélisation des écoulements
bi-phasiques
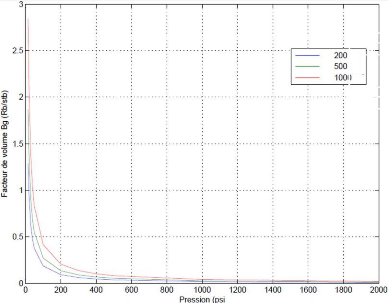
°F
°F
°F
Figure 3.2 : Evolution du facteur de volume pour le gaz
naturel en fonction de la pression.
Facteur de volume de l'huile. C'est le
rapport du volume d'huile dans les conditions in-situ sur celles de surface. En
dessous du point de bulle il est estimé comme suit : (Figure 3.3)
Bo = 0.972 + 0.000147F1.17s (3.3)
o.s
Avec : F = RS (Y g) + 1.25T (3.4)
Yo
Au-dessus du point de bulle l'expression suivante est valide
:
Bo6 = Boexp (Co(Pb
-- P)) (3.5)
Avec la compressibilité de l'huile, co
exprimée comme suit :
--27321+33.78RS+238.81T
(3.6)
Co =
106P
37
Le facteur de volume de l'huile est influencé par la
présence du gaz dans la solution (ratio et densité).
Chapitre3-Modélisation des écoulements
bi-phasiques
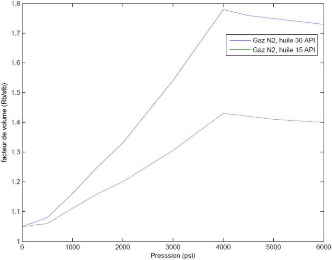
Figure 3.3 : Evolution du facteur de volume de l'huile
en fonction de la pression, point de bulle à 4000 psi.
3.2 Densité
La densité d'une phase influence à la fois son
énergie cinétique et potentielle, qui est utilisé pour
trouver le changement global d'énergie d'un système correspondant
à une chute de pression. Il peut être très complexe de
déterminer la densité d'un mélange biphasique dû
à la séparation par gravité et à l'effet de
glissement entre le liquide et le gaz.
La densité d'une phase dépend de la pression et de
la température de celle-ci. Pour chaque phase elle peut être
calculée en divisant la densité dans les conditions standards par
le facteur de volume aux conditions in-situ.
L'équation générale s'exprime comme suit
:
(P)
yi
}' i,ref
(3.7)
Pi =
Bi
38
Masse volumique du gaz. Peut facilement
être déterminée de l'expression générale si
sa densité est connue. Avec une densité de l'air de l'ordre de
0.0764 lbm/ft3, l'expression devient :
Avec : Yg =
|
Mg
(3.9)
28.97
|
|
Mg etant la masse moléculaire du gaz en question.
39
Chapitre3-Modélisation des écoulements
bi-phasiques
Masse volumique du liquide. Elle est
souvent présentée en degré API, qui est la mesure de
l'inverse de la densité dans les conditions standards. La Figure 3.4
illustre l'évolution du degré API et les domaines d'huile
légère, moyenne ou lourde.
Yo =
|
141.5
(3.10)
°A~I 131.!
|
|

Figure 3.4 : Abaque de conversion en degré API
(Leirkjaer, 2014)
La masse volumique de l'huile est calculée suivant la
formule suivante, mais nécessite un réajustement en cas de
présence de gaz en grande quantité.
Po =
0.0764Rs+62.4yo
5.615 (3.11)
Bo
Il est intéressant de noter que la masse volumique de
l'huile va augmenter légerement au-dessus du point de bulle car le gaz
est plus comprimé et on aura une baisse de Bo.
Masse volumique d'une mixture. La
densité du liquide utilisée dans la modélisation des
écoulements multiphasiques est la somme des densités de l'huile
et de l'eau multipliées par leur fraction volumique. Cette
densité ne prend pas en compte l'effet de glissement entre l'huile et
l'eau, il est considéré négligeable :
Pt = Pof$ + Pwfw (3.12)
Pour calculer la densité d'un mélange liquide/gaz,
il faut prendre en compte l'effet de glissement de ce dernier.
Chapitre3-Modélisation des écoulements
bi-phasiques
La densité avec glissement (slip density) est une
densité moyenne pondérée avec les fractions holdup, c'est
la plus utilisée en simulation des écoulements multiphasiques
:
Ps = P1H1 + PgHg
(3.13)
La densité sans glissement est une moyenne
pondérée avec les fractions volumiques qui élimine les
effets de glissement, donné par la formule :
Pn = P1A1 + PgAg
(3.14)
Une troisième densité est utilisée pour le
calcul des facteurs du facteur de friction et du Reynolds dans certaines
corrélations :
]l_l2
]0_02
Pk = + (3.15)
Hl Hg
3.3 Débit standard, Débit actuel
Le débit standard représente le volume vrai que
chaque phase va occuper dans les conditions standards quand elle débite
à travers une section pendant une certaine période de temps.
Alors que le débit actuel est ajusté pour les variations de
pression et de température.
Débit de gaz. Le GLR (gas
liquid ratio) est une mesure du débit volumétrique de gaz
relativement au débit volumétrique de liquide dans les conditions
standards. Si le GLR est en [scf/stb], le débit standard pour le gaz en
[scf/day] :
gg,sc = qh,scGLR (3.16)
Le débit actuel de gaz dans un segment est calculé
comme suit :
qg = qo,sc(GOR - Rs)Bg (3.17)
Débit d'huile. Le débit
standard d'huile est calculé simplement par l'expression suivante en
[bbl/day]:
qo,sc = qh,sc(1 - WC)
Le débit actuel est alors :
qo = qo,scBo
|
(3.18)
(3.19)
|
Débit du mélange.
Calculé comme suit :
|
|
qh = qo + qw
|
(3.20)
|
qt = qh + qg
|
(3.21)
|
|
40
|
|
41
Chapitre3-Modélisation des écoulements
bi-phasiques
3.4 Rapports de volume
Water Oil Ratio. Paramètre
adimensionnel qui décrit le volume fractionnaire de l'eau comparé
au volume d'huile.
gf, = jk,sc (3.22)
j1,sc
Gas Oil Ratio. C'est une mesure de
combien le volume de gaz est présent dans les conditions standards
comparé au volume d'huile. Peut être exprimé en plusieurs
unités en [m3/m3] ou en [scf/stb] :
df, = j0,sc (3.23)
j1,sc
Holdup (pas de glissement). C'est la
fraction de volume dans une conduite occupée par la phase liquide dans
le cas où il n'y a pas d'effet de glissement. Dans le cas où les
deux phases ont la même vélocité et la valeur du holdup est
donnée par la fraction du débit de liquide sur le débit
total. Le holdup pour le gaz est au pourcentage restant dans la conduite.
[V = j^ (3.24)
jl
[g = 1 - [V (3.25)
Holdup (avec glissement). C'est une
valeur très importante utilisée en modélisation des
écoulements diphasiques pour déterminer certaines
propriétés comme la densité des mixtures, leur
viscosité. Il est défini comme étant la fraction de volume
de conduite occupée par la phase liquide. Pour une section totalement
pleine de gaz le liquid holdup est nul et le gas holdup est 1.
V^jmntoH opqs ^H sH0rHql
YV = (3.26) VsH0rHql
Le gas holdup est défini comme suit : Y9 = 1 -
YV (3.27)
Fractions liquides.
Représentent les fractions volumiques de l'huile et de
l'eau, peuvent être estimées à partir des débits
actuels :
W$ = j1 (3.28)
j^
WX = 1 - W$ (3.29)
Les fractions sont aussi dites WLR (water liquid ratio) et OLR
(oil liquid ratio).
3.5 Vélocités et effet de glissement
Le glissement est utilisé pour décrire les
conditions d'écoulement quand les deux phases ont des vitesses
différentes. Les vitesses sont nécessaires au calcul du facteur
de friction qui est proportionnel aux pertes de charge qui sont utilisés
pour calculer la pression en chaque point du système.
Chapitre3-Modélisation des écoulements
bi-phasiques
Vitesse superficielle. La vitesse
superficielle d'une phase est celle qu'elle pourrait avoir s'il n'y avait
qu'une seule phase en écoulement dans la conduite. Il est calculé
en divisant le débit actuel par la section d'écoulement. Les
vitesses superficielles pour le liquide et le gaz sont données comme
suit :
j^
v-V = (3.30) N
Vitesse actuelle. C'est un terme de
vitesse qui a été ajusté pour le holdup et donne une
représentation plus réelle de la vitesse de chaque phase dans le
segment. Plus le holdup sera petit plus il y aura de grandes vitesses.
ss^ (3.32)
V =
a^
ss0 (3.33)
~~ =
a0
42
Effet de glissement. C'est une mesure
de comment les bulles de gaz dans une mixture peuvent surpasser la phase
liquide. C'est un facteur qui dépend de la densité, des vitesses
et de la section d'écoulement. Peut être exprimé de
différentes manières, l'une d'elle est la vitesse de glissement
qui représente la différence entre les vitesses actuelles des
deux phases. C'est également celle qui est le plus utilisées dans
les corrélations.
~- = ~ - V (3.34)
Ou alors le ratio de glissement, ou slip ratio.
s0
t = (3.35)
s^
3.6 Viscosité
Elle représente la résistance d'un fluide à
son écoulement. C'est un paramètre très important qu'il
faut connaitre. C'est un avantage de pouvoir la mesurer au laboratoire, mais il
existe beaucoup de corrélations qui pallient cette
nécessité.
Viscosité du gaz. Augmente avec
la température au contraire des liquides, à cause de
l'augmentation de la densité des collisions intermoléculaires,
phénomène négligeable pour les liquide mais non pour les
gaz. (Figure 3.5)
43
Chapitre3-Modélisation des écoulements
bi-phasiques
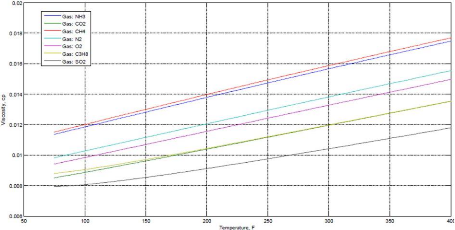
Figure 3.5 : Viscosités pour plusieurs gaz
à pression 200 psi. (Leirkaer, 2014)
Viscosité de l'huile. Pour le
brut, la viscosité est proportionnelle à sa densité, ou
inversement proportionnelle à son degré API (Figure 3.6).
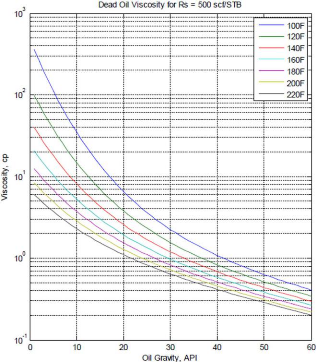
Figure 3.6 : Viscosité de l'huile morte en
fonction de sn degré API. (Leikaer, 2014)
44
Chapitre3-Modélisation des écoulements
bi-phasiques
3.7 Rappel sur la modélisation d'un
écoulement monophasique incompressible
Le but de modéliser l'écoulement dans le puits est
de pouvoir calculer la pression en chaque point. Depuis l'équation de
conservation d'énergie avec un volume de contrôle entre le fond du
puits et la surface (l'annulaire). En négligeant la
compressibilité du fluide, le transfert de chaleur et les
phénomènes d'accélération. La pression de fond
(BHP) est relatée à la pression de surface (SP) par la formule
suivante : (Blade)
SP = BY: - ?:vwic-?:gwxs (3.36)
?:gwxs Représente la perte de pression par
gravité. Dans le cas d'un fluide incompressible, elle est égale
à la pression hydrostatique du fluide en question.
?:vwic Illustre les pertes de charge par effet de friction.
Dépend de plusieurs paramètres ; le diamètre de la section
d'écoulement, la densité du fluide, le débit, la hauteur
mesurée du puits et le facteur de friction. Ce dernier est plus
difficile à évaluer, il est en général
calculé à partir du nombre de Reynolds et de la rugosité
des parois du puits.
Extension aux fluides non-Newtoniens.
Sont d'un grand intérêt dans les applications en
engineering. Un fluide non-Newtonien est caractérisé par une
relation non linéaire entre la contrainte et le taux de cisaillement.
Plusieurs modèles ont été proposés pour
décrire leur comportement (Bingham, Hershel-Bulkley). La
différence avec les fluides Newtoniens dans la description de
l'évolution de la pression dans le puits est qu'il faut rajouter un
terme d'accélération.
t: = BY: - ?:vwic-?:gwxs - ?:xcc (3.37)
3.8 Simulation des écoulements Bi-phasiques
Beaucoup d'approches pour la détermination du profile
de pression dans le cas d'un fluide biphasique étaient des
corrélations empiriques, les premières ont été
développées pour des puits verticaux comme celle de Poettman et
Carpenter ou Hagedorn et Brown. Dans les années 1960' le forage
directionnel a immergé, rendant les corrélations
précédentes obsolètes. En 1973 Beggs et Brill ont
développés le premier modèle d'écoulement
multiphasique pour les puits inclinés.
Modèles d'écoulement.
Quand deux phases ont présentes dans un même
système, le modèle d'écoulement dépend des vitesses
superficielles du gaz et du liquide. Le mécanisme de transfert
d'énergie et de quantité de mouvement diffère d'un
modèle à l'autre. Il est donc très important d'identifier
ces derniers pour connaitre l'évolution de l'écoulement dans le
puits.
45
Chapitre3-Modélisation des écoulements
bi-phasiques
Modèles pour puits vertical.
Les régimes d'écoulement observés dans une
conduite verticale sont illustrés dans la Figure-3.7, les modèles
observés sont :
? Bulle dispersées. Se passe dans le cas de
faible débit de gaz. La phase liquide est continue et on a un
écoulement en spirale depuis le centre de la conduite.
? Ecoulement Slug. Une augmentation du débit
de gaz entraine la coalescence des bulles et génère de grandes
bulles dans la conduite. La bulle est dite de Taylor, ces dernières
n'ont pas assez de pression pour supporter la phase liquide. En
conséquence, le liquide glisse sous la bulle et se rassemble en
attendant la prochaine bulle de Taylor. Le débit minimum de gaz pour
soulever la phase liquide est donné par la corrélation de Turner
(1968).
? Ecoulement Churn. C'est un Slug flow chaotique, se
passe dans des domaines de débit supérieurs à ceux du Slug
flow. La bulle de Taylor est déformée et les bulles ont une forme
aléatoire.
? Ecoulement Annulaire. Dans des hauts débits
de gaz, il s'écoule en phase continue au milieu de la conduite.
? Ecoulement Mist. A des débits de gaz
très élevés, le gaz brise la tension liquide/conduite et
enlève le film liquide sur la conduite, le gaz est une phase continue et
le liquide sous forme de gouttelettes dispersées.
Les modèles d'écoulement observés dans
l'annulaire sont les mêmes que dans une conduite. Mais la
géométrie de l'annulaire, parfois excentrique, et la
présence de lits de cuttings influe énormément sur le
régime d'écoulement. La pression appliquée en surface
affecte aussi grandement les changements de régime.
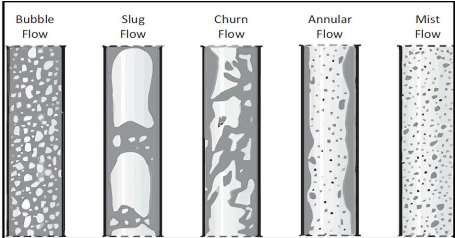
Figure 3.7 : Régimes d'écoulement en
conduite verticale. (Rehm, 2012)
46
Chapitre3-Modélisation des écoulements
bi-phasiques
Modèles pour puits horizontal.
Les classifications des régimes d'écoulement
varient selon la littérature (Figure 3.8), les modèles
présentés ci-dessous sont ceux reconnus dans le design des puits
en UBD :
? Ecoulement en bulles dispersées. A des
débits de gaz très faibles, le gaz se déplace dans la
conduite sous forme de bulles dispersées. Les bulles de gaz n'ont pas la
même taille, et elles tendent à aller dans la section superieur de
la conduite par effet de gravité.
? Ecoulement stratifié lisse (smooth) le gaz
et le liquide se séparent, le gaz se déplace au-dessus et le
liquide en dessous. Avec une interface non courbée entre eux.
? Ecoulement stratifié ondulatoire (wavy) une
augmentation du débit de gaz fait que l'interface devient
ondulée.
? Ecoulement Slug. Quand l'effet ondulé de
l'interface liquide/gaz prend de l'ampleur, le gaz de scinde en poches
séparés par des Slugs de liquide.
Le premier pas dans la modélisation d'un
écoulement biphasique, est de connaitre le régime
d'écoulement in-situ, des abaques sont disponibles basés sur les
vélocités superficielles du liquide et du gaz, pour
différentes inclinaison, la Figure-3.9 montre le modèle de
Mandhane pour les conduite horizontales.
La prochaine étape concerne l'utilisation d'un
modèle ou une corrélation pour l'estimation de la pression aux
différents points du puits. La présentation des différents
modèles ne fait pas l'objet de ce mémoire, le lecteur est
redirigé vers des ouvrages plus spécialisés pour plus de
détail. (Voir modèle de Beggs and Brill, et modèle de
Guo)
Le travail de simulation a été fait avec le
logiciel Drillbench, propriété du groupe SPT, qui contient deux
modules de simulation multiphasiques spécifiés pour l'UBD. Le
Steadyflodrill simule les paramètres de forage en régime
permanent (en fonction du débit d'injection de gaz), et le Dynaflodrill
donne l'évolution des paramètres dans le temps (transitoire)
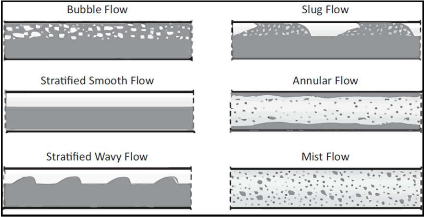
Figure 3.8 : Régimes d'écoulement en
conduite horizontale. (Rehm, 2012)
47
Chapitre3-Modélisation des écoulements
bi-phasiques
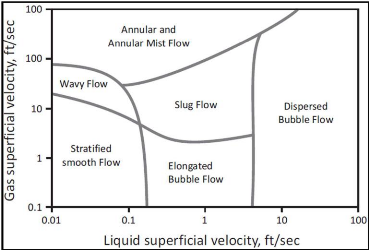
Figure 3.9 : Modèle de régime de
Mandhane. (Rehm, 2012)
3.9 Planification et modélisation des
opérations en underbalance
Pression de fond. La pression de
fond doit être contrôlée à tout moment des
opérations. Pour ce faire, une planification des actions rigoureuse doit
être entreprise. En définissant tout d'abord la fenêtre de
drawdown (exemple 7%-9%). En faisant cela, il y beaucoup de paramètres
à prendre en jeu : la pression hydrostatique nécessaire pour
avoir un underbalance suffisant, mais également le nettoyage du trou, la
stabilité des parois, capacité d'injection de gaz en surface.
Différence de pression. Il
faut considérer la pression nécessaire pour avoir un underbalance
suffisant, et ainsi contrer les forces capillaires qui agissent entre le fluide
de forage et la roche et qui causent le phénomène d'imbibition.
Et en même temps ne pas avoir un drawdown trop élevé qui
pourrait causer des problèmes de stabilité des parois ou bien
alors un afflux trop important de la formation qui serait difficile à
maitriser en surface.
Zone opérationnelle. Pour
trouver les débits de liquide et de gaz qui conviennent il est
nécessaire de construire un graphe comme celui de la Figure-3.10, qui
montre l'évolution de la BHP en fonction du débit d'injection de
gaz pour plusieurs débits d'injection de liquide. Et montrant
également la fenêtre de drawdown désirée en plus de
la courbe de limite de nettoyage des parois, au-dessus de cette courbe toute
combinaison de paramètres donne un bon nettoyage, en dessous de cette
dernière, on n'aura pas un écoulement turbulent dans l'annulaire
ce qui peut entrainer un effet de dune dans le cas d'un forage horizontal.
48
Chapitre3-Modélisation des écoulements
bi-phasiques

Figure 3.10 : influence du débit de gaz sur la
BHP et enveloppe UBD.
Cette figure a été développée avec
le simulateur Steadyflodrill qui est un simulateur en régime permanent,
une simulation en régime transitoire peut être faite avec le
Dynaflodrill pour une meilleure compréhension des
phénomènes.
Remarque : l'effet d'accumulateur (Chapitre 5) dont traite ce
mémoire n'est pas décelable avec une simulation en régime
permanent, il est nécessaire d'utiliser le Dynaflodrill pour mettre en
évidence ce problème. Ceci illustre l'importance des simulations
en régime transitoire dans la détection des fluctuations de
pression leur prévention.
3.10 Dynaflodrill
Dans ce mémoire, l'utilisation du logiciel Drillbench, et
en particulier du module Dynaflodrill a joué une part primordiale dans
la mise en évidence du problème posé et dans la simulation
des solutions à ce problème. Le paramètre le plus
étudié est l'évolution de la pression de fond (BHP) en
fonction du temps.
Présentation du système physique.
Dans un système en underbalance typique, le fluide de
forage est pompé à travers la garniture où il passe par un
moteur de fond, et ressort par les duses de l'outil et remonte par l'annulaire.
Le fluide de forage peut être un liquide, un liquide gazeifié ou
un mousse dans ce cas-ci. Dans l'annulaire, le fluide de forage va être
mélangé avec les cuttings et les fluides de formation, en plus du
gaz injecté par concentrique ou par parasite.1
1 La source d'information dans ce
paragraphe est issue d'un papier SPE écrit par (Rommetveit et Lage,
2001)
Chapitre3-Modélisation des écoulements
bi-phasiques
En surface, l'annulaire est fermé par un système
de BOP rotatif et les fluides venants du puits sont dirigés vers un
système de duse régulée qui applique une certaine pression
de surface est appliquée pour maintenir les conditions de fond
désirées et réguler le flux sortant.
Pendant le forage, la profondeur du puits augmente en fonction
du ROP. Les manoeuvres seront nécessaires également, ces deux
procédures vont entrainer le changement de la géométrie de
l'écoulement dans le puits.
Tous les phénomènes physiques relatés aux
opérations citées sont modélisés.
Représentation mathématique.
Le coeur du simulateur est basé sur les équations
de conservation de masse et de quantité de mouvement qui
décrivent le comportement des composants du fluide le puits dans une
situation de forage.
Les équations suivantes sont la base du code source du
simulateur : Conservation de masse du gaz produit :
a [A as
agnpgn] = -- a [A
at agng}Dg}~ - {rim g} + {bvg} (3.38) Conservation
de masse du gaz injecté :
yi z{|gVDgV~ = - y
y y- z{|~V~VD~V~ - {m yV + {bgV
(3.39) Conservation de masse de la phase liquide de forage :
yi {(1 - |)DV = - yy- {(1 - |)VDV + {my (3.41)
y
Conservation de masse du gaz dissous :
yi z{(1 - |)É~DV~ = - y
y y- z{(1 - |)É~VDV~ + {~€ ~ + {b~
(3.42)

y
yyi z{(1 - |)ÉvXDV~ = - y- z{(1 - |)ÉvXVDV~ +
{bvX (3.44)
Conservation de masse des cuttings :
y
yi {(1 - |)ÉcDV = - yy- {(1 - |)ÉccDV +
{bc (3.45)
Pour la conservation de la quantité de mouvement,
l'équation générale n'est pas employée, on utilise
une version simplifiée qui décrit l'équilibre des
pressions :
yy- ... = -Wi - W> + z(1 - |)DV +
|Dg~co (3.46)
Conservation de masse de l'huile de formation :
yi z{(1 - |)Év$DV~ = - y
y y- z{(1 - |)Év$VDV~ + {bv$ (3.43)
Conservation de masse de l'eau de formation :
49
50
Chapitre3-Modélisation des écoulements
bi-phasiques
Tableau 7 : Paramètres dans les
équations de conservation
|
A
|
Section de l'annulaire
|
p
|
Pression
|
f1
|
Terme de perte de charge par frictions
|
s
|
Distance
|
f2
|
Terme de pertes de pression localisées
|
v
|
Vitesse
|
~€
|
Débit de dissolution du gaz
|
x
|
Fraction massique
|
~g€
|
Débit total de dissolution du gaz
|
c
|
Cuttings
|
q
|
Influx massique
|
a
|
Fraction de gaz
|
qg1
|
Influx massique pour le gaz injecté
|
p
|
Densité
|
qfgp
|
Influx massique pour le gaz produit non dissolu
|
8
|
Inclinaison du puits
|
|
fo
|
Huile de formation
|
gl
|
Gaz injecté
|
fw
|
Eau de formation
|
gp
|
Gaz produit
|
g
|
Gaz
|
l
|
Liquide
|
gd
|
Gaz dissous
|
|
|
Pour pouvoir résoudre ces équations, des
informations supplémentaires doivent être acquises. Des
sous-modèles intégrés dans le logiciel décrivent
d'autres processus dans le fluide mathématiquement.
Sous-modèles. Les
sous-modèles les plus importants sont décrits ci-dessous :
· Densité de la phase liquide, incluant l'effet du
gaz dissous, des cuttings et des fluides de réservoir.
· Densités du gaz injecté, incluant le gaz
injecté l'annulaire et celui par l'intérieur des tiges
séparément.
· Densité du gaz produit.
· Transport du gaz dans le puits, la vitesse de
déplacement du gaz dépend des propriétés du
système au point où se trouve le gaz.
· Débit d'injection du gaz, varie selon les
conditions du trou et son emplacement.
· Rhéologie de la phase liquide.
· Pertes de charge dans l'annulaire : plusieurs
modèles mathématiques sont disponibles, qui prennent en compte la
rugosité des parois.
· Pertes de pression localisées.
Précision du logiciel de simullation.
Des expériences ont été effectuées
sur un puits vertical de hauteur 1300m avec injection par parasite, avec une
garniture de 31/2 de diamètre. L'expérience a
été faite dans les mêmes conditions d'un forage normal. On
a effectués des variations du débit d'injection d'azote, et on a
mesurés les variations de la pression au fond avec un capteur
installé é cet effet. Une simulation des mêmes
manipulations fut entreprise avec le Dynaflodrill, les résultats sont
représentés dans la Figure-3.11. (Rommetveit, 2001)
51
Chapitre3-Modélisation des écoulements
bi-phasiques
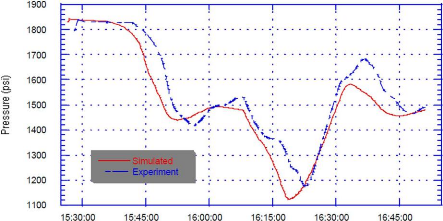
Figure 3.11 : Injection par parasite : données
experimentales Vs. Données simulées à l'aide
du Dynaflodrill (Rommetveit, 2001)
On remarque que le simulateur donne d'assez bons
résultats et qu'il suit les mêmes variations de pression que pour
les cas réels.
Remarque : le graphe ci-dessus a été
réalisé avec une version ancienne du logiciel, qui a
été amélioré au fil du temps et donne une bien
meilleure précision avec la nouvelle version (6.1) utilisée dans
ce travail.
Utilisation du logiciel de simulation.
Une illustration de l'interface est présentée dans
la Figure-3.12.
Le simulateur nécessite un certain nombre de
données, sur le profil du puits (Survey), la géometrie du puits,
les spécifications de la garniture de forage, le fluide de forage, sur
les équipements de surface, sur le système d'injection, en plus
des détails sur le réservoir (Perméabilité,
porosité, GOR...).
Une fois entré tous les paramètres
nécessaires demandés, on peut passer à l'interface de
simulation (Figure-3.13), il est demandé d'entrer les paramètres
opérationnels, tels que le débit des pompes, le débit
d'injection, le ROP.... En commençant la simulation il est possible
d'obtenir l'évolution des paramètres en fonction du temps.
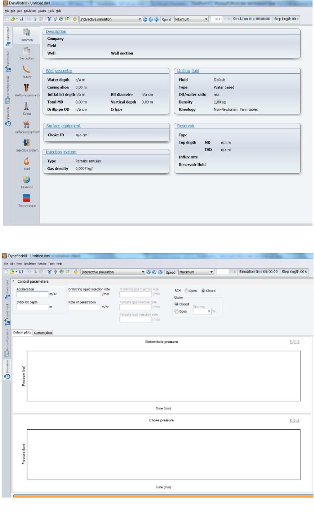
Figure 3.12 : Interface de travail
Dynaflodrill
Figure 3.13 : Interface de simulation
Dynaflodrill.
52
Chapitre3-Modélisation des écoulements
bi-phasiques
53
Chapitre4-Initiation à la geomécanique en
Forage
Chapitre-4 Initiation à la geomécanique
en forage
Ce chapitre offre une introduction à l'étude de
stabilité des parois en cours de forage, c'est un pas essentiel dans le
design des puits en underbalance, et ce dans le but de fixer les limites de
dépression (drawdown) et éviter les problèmes de collapse
du puits. Il sera d'abord présenté une explication de
l'état des contraintes dans le puits, suivi des principes de l'analyse
de stabilité des parois pour puits verticaux et horizontaux
respectivement. Pour terminer une méthode de calcul des contraintes
in-situ. Ce chapitre sera essentiel dans le suivi de ce travail qui a pour
sujet principal le design des puits en UBD. Ce chapitre est tiré de
Fundamentals of Drilling Engineering, Mitchell (2011), le lecteur y
est redirigé pour plus de clarté dans les principes et fondements
exposés.
4.1 Introduction, description du problème
L'étude de stabilité des parois est devenue une
discipline reconnue au début des années 1980 avec
l'avènement des forages déviés. Bradley (1979) est
considéré comme le premier à avoir introduit les calculs
de mécanique des roches dans le domaine du forage pétrolier.
La majorité des problèmes rencontrés en
cours de forage sont reliés directement à la stabilité
mécanique des parois.
? Collapse mécanique du puits, se produit avec des
pressions de fond insuffisantes, liés à une densité de
boue trop faible.
? Particulièrement avec les argiles, des
phénomènes chimiques peuvent induire un élargissement du
trou ou un collapse, surtout avec les boues à base d'eau, les argiles
réagissent avec le filtrat
(Les problèmes liés des pressions de boue trop
fortes ne seront pas abordés, sortant du sujet du mémoire)
4.2 Etat des contraintes dans le puits
Les roches sont soumises à des contraintes à toute
profondeur, ils sont définis comme suit :
? Une contrainte verticale principale, liée au poids des
minéraux sus-jacents. Il est
obtenu par intégration de la densité des
minéraux par la profondeur. Noté o,.
o = ? J' ~~~ d
Zt+l
~ (4.1) ~~
? Deux contraintes horizontales principales, la
première dite contrainte maximum et la seconde minimum notées
respectivement aH et ah (Figure-4.1)
On définit également les notions suivantes :
? Dans les milieux de dépôts (bassins
sédimentaires) les contraintes horizontales sont moins
élevées que la contrainte verticale, ce qui nous donne une faille
dite normale. ? Du aux mouvements tectoniques, nous pouvons avoir les deux cas
suivants :
· ah < a < aH ; on appel cet état
faille de décrochement.
· a < ah < aH ; cet état
est dit faille inverse.
54
Chapitre4-Initiation à la geomécanique en
Forage
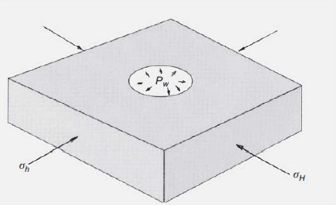
Figure 4.1 : Etat des contraintes dans le puits.
(Mitchell, 2011)
Contrainte effective. Il faut également
considérer les propriétés du milieu poreux. Terzaghi
(1943) a défini le principe de contrainte effective. La contrainte
totale subie est la somme de la contrainte effective plus la pression de
pore.
atot = a' + Ppore (4.2)
Ce principe est essentiel dans l'étude de la destruction
de la roche, car on calcul la contrainte effective, à appliquer à
la roche elle-même.
On peut également voir les contraintes agissant sur le
puits en coordonnées cylindriques comme suit, on prend le cas où
aH = ah, ce qui est le plus souvent le cas :
(Figure-4.2)
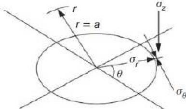
Figure 4.2 : Contraintes agissant sur le puits.
(Mitchell, 2011)
· Contrainte radiale ar, qui est la
pression appliquée par le fluide de forage Pw.
· Contrainte tangentiellea9, avec a9 = 2ah --
Pw
· Contrainte axiale, ou verticale, a qui est la
même que avpour un puits vertical.
Dans le cas où aH * ah, la contrainte
tangentielle dépend de l'angle 8
Chapitre4-Initiation à la geomécanique en
Forage
4.3 Analyse de stabilité des parois pour puits
verticaux
Collapse. Prend place habituellement
dans les cas de pression de fond faibles, le contraste élevé
entre la contrainte tangentielle et la pression appliquée au fond par le
fluide de forage va engendrer une contrainte de cisaillement. En
conséquence, le collapse est définit comme étant une
rupture par cisaillement.
Parfois au lieu d'une rupture on a un resserrement des parois,
phénomène dit « Tight hole », ce
phénomène nécessite plusieurs passes de reforage.
La Figure 4.3 illustre des ruptures par cisaillement typiques,
les plans de cisaillement sont courbés du fait de la
géométrie circulaire du trou, la première illustration
montre le cas où les plans de cisaillement se connectent,
résultant une fragmentation des roches qui vont tomber dans le trou.
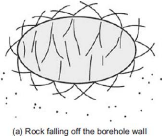
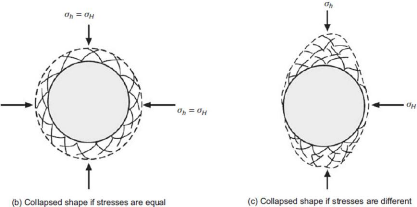
55
Figure 4.3 : Modes de collapse du trou. (Mitchell,
2011)
Analyse de la rupture par collapse. Le
mécanisme de la rupture a été définit comme
étant une rupture par cisaillement, les résistances de la roche
sont estimées à partir des essais sur carottes avec une pression
de confinement constante. La discussion sur les tests sur échantillons
ne fait pas l'objet de ce mémoire, le lecteur est dirigé vers un
cours sur l'essai triaxial pour plus de détails.
Chapitre4-Initiation à la geomécanique en
Forage
Plusieurs modèles de ruptures ont été
élaborés pour décrire les mécanismes de rupture de
la roche, il est cité les plus utilisés : Critère de Von
Mises, Critère de Mogi-Coulomb et aussi Critère de Lade
modifié. Cependant la description classique du modèle de
Mohr-Coulomb donne de très bons résultats dans l'estimation de la
pression de collapse.
Modèle de Mohr-Coulomb. En 2 dimensions, les
contraintes peuvent être estimées par le biais du cercle de Mohr.
Ceci est fait par la construction d'un cercle dont le diamètre est
égal à la différence entre la contrainte maximale et
minimale à la rupture. (Figure-4.4)
Le modèle de rupture de Mohr-Coulomb est cette ligne de
rupture, est décrite mathématiquement comme suit :
# = #$ + a't&'( (4.3)
Où ( est définit comme étant l'angle de
friction interne de la roche.
La courbe est obtenue avec des données de laboratoire,
pour appliquer ce modèle au puits, il faut dériver les
expressions pour les contraintes agissant sur le trou.
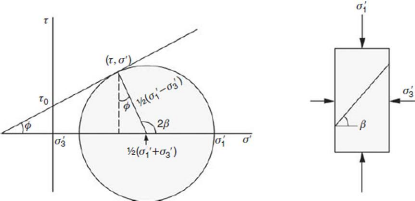
56
Figure 4.4 : Illustration des contraintes pour le
modèle de Mohr-Coulomb (Mitchell, 2011)
Avec ) = * + + 45° (4.4)
Les coordonnées à la rupture sont définies
comme suit :
# =
|
+ 0a'/ - a'12345(
/ (4.5)
|
|
I = + / 0,/ 12 ~ + /
0/ --a'1256'( (4.6)
La pression de collapse est directement tirée de
l'expression de l'équation (4.3) égal (4.5), en y insérant
l'équation (4.6), on cherche Pw pour que l'égalité soit
correcte.
La contrainte a'/ étant égale
à la contrainte tangentielle effective, et a1 à la
contrainte radiale effective.
57
Chapitre4-Initiation à la geomécanique en
Forage
4.4 Analyse de stabilité des parois pour puits
déviés
Contraintes déviées.
Avant d'entamer l'étude de stabilité des parois
pour les puits déviés, on doit tout d'abord définir la
notion de contrainte déviée. Ces dernières sont le produit
de la transformation par matrice de passage des contraintes déjà
connus (2 horizontales et une verticale) à des contraintes
équivalentes dans un autre système de coordonnées.
(Figure-4.5)
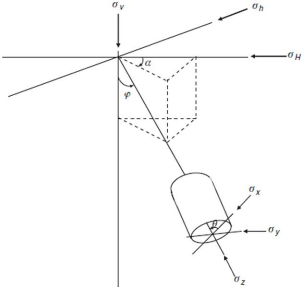
Figure 4.5 : Orientation des contraintes
déviées. (Mitchell, 2011)
On définit les contraintes orientées :
|
|
6x = (6Hcos2a +
6hsin2a)cos2a + 6sin2Cp
|
(4.7)
|
6y = (6Hsin2a +
6hcos2a)
|
(4.8)
|
6z = (6Hcos2a +
6hsin2a)sin2a + 6cos2Cp
|
(4.9)
|
|
En plus des contraintes de cisaillement :
|
|
ixy = 0.5(6h -- 6H)sin2a cosCp (59)
|
(4.10)
|
iyz = 0.5(6h -- 6H)sin2a sinCp (60)
|
(4.11)
|
ixz = 0.5(6Hcos2a +
6hsin2a -- 6)sin2Cp (61)
|
(4.12)
|
|
58
Chapitre4-Initiation à la geomécanique en Forage
On définit les contraintes agissant sur le puits :
Contrainte radial 6r = Pw
(4.13)
Contrainte tangentielle 6 = 6x + 6y --
Pw -- 2(6x -- 6y)cos28 -
4Txysin28 (4.14)
Contrainte axiale az = 6z --
2v(6x -- 6y)cos28 - 4VTxysin28 (4.15)
Contrainte de cisaillement iez = 2(TyzcosG --
TxzsinG) (4.16)
avec les contraintes sur les autres plans
considérées nulles.
Analyse pour le Collapse. Les
contraintes dans le cas d'un puits dévié deviennent :
6i = 0.5(a9 + az) + 0.5/(69 -
az)2 + 41-9z (4.17)
63 = Pw (4.18)
Le résultat du calcul de la pression de collapse pour le
cas d'étude est présenté dans le chapitre 8, le principe
de calcul est le même que pour un puits vertical. Les étapes de
calcul étant trop fastidieuses et n'entrant pas dans le but de ce
mémoire il a été préféré les
négliger.
4.5 Estimation des contraintes in-situ1
Le but de cette partie est d'estimer les contraintes
horizontales pour un puits quelconque, pour cela l'algorithme suivant est
proposé :
Si cy < ax
Pwf+Ppore
|
|
+ sin2(p = (3sin2a - cos2a
cos2(p) QH
Qv
|
+ (3cos2a - sin2a
cos2(p)Qh
Qv
(4.19)
|
|
Qv
|
|
|
|
|
|
Pwf+Ppore
|
|
3sin2(p = (3cos2a cos2(p -
sin2a )QH
Qv
|
+ (3sin2a cos2(p - cos2a )Qh
Qv
|
|
Qv
|
|
|
|
|
|
|
(4.20)
|
|
|
|
|
|
|
Dans les deux cas elle peut s'écrire sous la forme :
P' = a QH
Qv
P', a et b étant des termes adimensionnels.
|
+ b Qh (4.21)
Qv
|
|
En insérant les données d'un puits comme sont
azimuth, inclinaison, on obtient les matrices suivantes :
1 Aiyeru, 2014.
59
Chapitre4-Initiation à la geomécanique en Forage
~~/&/ O/ ~~ ~~
~~+ &+ O+ U
P S = P S T ?? ~~ ~~ V (4.22)
? U
P R &R OR
Qui peut s'exprimer comme suit :
WP'X = WYXWQX (4.23)
Cette équation peut se résoudre avec autant de
données que ce soit, avec un minimum de 2. Cependant un grand nombre de
données risque d'entrainer des erreurs de calcul, et donc pour cela il
faut minimiser l'erreur e :
WeX = WYXWaX - WP'X (4.24)
On utilise la méthode des moindres carrés et on
minimise le carré de l'erreur :
e+ = WeXZWeX (4.25)
Pour le minimiser, on le dérive par rapport à
WaX et on prend la dérivée égale à 0 pour chercher
un extrema.
[ e2 [WJX
= 0 (4.26)
En substituant l'équation (4.24) dans (4.26) on obtient
:
W0X = \WYXZWYX]^/WYXZWP'X
(4.27)
Le résultat donne toujours deux valeurs, on prend la plus
grande comme étant aH et la plus petite ah.
Chapitre5-Effet d'Accumulateur : définition et
expliquation
Chapitre-5 Effet d'accumulateur : définition et
explication
5.1 Description du phénomène,
Illustration du phénomène de Slugging
La méthode d'injection par tubage concentrique
présente nombre d'avantages, mais un contrôle inapproprié
du débit de gaz peut générer des fluctuations de la
pression d'injection qui va influencer la quantité de gaz qui entre dans
le puits. Un flux irrégulier qui va entrainer des problèmes en
surface et des variations de la BHP, ce qui affecte grandement le bon
déroulement des opérations.
Avec l'utilisation du tubage concentrique, les compagnies de
services se heurtent parfois à des oscillations énormes de
pression dues à l'effet d'accumulateur. En injectant un fluide
incompressible dans l'annulaire crée par les deux tubages concentriques,
le gaz commence à s'accumuler, on observe alors une augmentation de la
pression dans l'annulaire jusqu'à ce que celle-ci soit supérieur
à la pression du puits au point d'injection. A ce moment-là le
gaz commence à rentrer dans l'annulaire Tubage/Tiges avec un
débit qui est supérieur au débit d'injection en
surface.
Le débit d'injection au fond va augmenter avec
l'allègement de la colonne de fluide dans le puits donc la diminution de
la pression au point d'injection. Ceci continue jusqu'à ce que la
pression du concentrique soit en dessous de celle du puits et que l'afflux
s'arrête. Le concentrique se recharge à nouveau, et le cycle se
répète, ce phénomène est connue sous le nom de
« Accumulator Bottle Effect ». Le comportement de la pression est
oscillatoire et le débit de gaz est intermittent. Ce dernier arrive en
surface sous forme de bouchons dits « slugs » (voir Figure 5.1), ce
qui induit qu'à un moment donné, entre deux bouchons, il n'y a
pas de gaz dans le puits pour alléger la colonne hydrostatique. On a
alors une fluctuation de la BHP ce qui entraine la remontée en
Overbalance temporaire. (Figure 5.2)
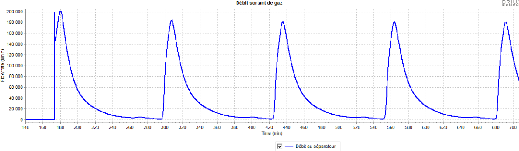
60
Figure 5.1 : Débit de gaz sortant, illustration
du phénomène de slugging.
Chapitre5-Effet d'Accumulateur : définition et
expliquation
A chaque remontée de pression, le liquide rentre et
remonte dans le concentrique, donnant les signes d'une perte de circulation
(Figure 5.4), au fur et à mesure de l'injection du gaz, ce dernier
chasse le liquide hors du concentrique, le phénomène se
répète à chaque fois. Les variations du niveau de liquide
donnent l'impression d'un ressort, ce phénomène est dit «
Spring effect ».
La figure 5.3 illustre les variations de débits
d'injection de gaz, on remarque que malgré que le débit sortant
des boosters soit constant, le débit rentrant dans l'annulaire fluctue,
les pics correspondants à la sortie d'une grande quantité de gaz,
et les zones plates aux phases de recharge du concentrique où la
pression de fond au point d'injection sera supérieur à la
pression à l'intérieur de l'annulaire Tubage/Tubage.
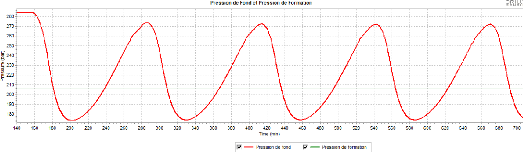
Figure 5.2 : Evolution de la pression de fond pendant
le phénomène de slugging.
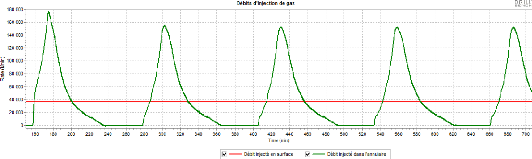
61
Figure 5.3 : Evolution du débit d'injection de
gaz pendant le phénomène de slugging.
62
Chapitre5-Effet d'Accumulateur : définition et
expliquation
Ce phénomène est non souhaité mais
parfois prévu, il engendre un certain nombre de problèmes et de
risques.
Risques de pertes de circulation.
Le retour momentané dans les conditions d'overbalance peut
entrainer des pertes surtout dans les réservoirs fracturés
où la fenêtre opérationnelle est très mince. A ne
pas confondre avec le « Spring effect » qui peut feindre les
mêmes signes.
Instabilité des parois. La
libération d'une grande quantité de gaz en un coup provoque une
dépression qui diminue la BHP plus que prévu, ce qui peut causer
un éboulement (collapse) du trou. D'un autre côté, le
retour brusque en overbalance dans une zone qui ne doit pas subir une grande
pression de la part du fluide de forage peut causer une fracturation. Ceci peut
arriver dans les grés non consolidés où le gradient de
fracturation et d'intégrité des parois sont très
proches.
Contamination du réservoir.
Le passage même momentané en overbalance suffit
à perdre l'avantage de non altération de la formation et permet
au filtrat de boue, en plus de particules solides de pénétrer
dans la formation productrice. Ce problème est souvent résolu par
l'utilisation du brut comme phase liquide de forage, étant le liquide le
moins contaminant pour un réservoir pétrolier, à condition
qu'il y ai compatibilité entre le brut utilisé et le fluide de
formation, et ce, pour éviter la formation d'émulsions et la
réduction de la perméabilité autour du puits.
Contrôle des retours en surface.
Le contrôle de bouchons de gaz en surface pose un vrai
défi aux opérateurs de service. Qui doivent gérer
alternativement les bouchons de gaz et les afflux de liquide qui
excèdent parfois la capacité du séparateur en surface.
(Voir Figure 5.1 et 5.4)
Nettoyage du trou. Pour les puits
horizontaux, la dépression engendrée par le gaz dans la partie
tubée du puits (en général verticale) va créer un
effet de succion dans la partie horizontale qui va tendre à aspirer les
déblais de cette partie. Toutefois, le phénomène
d'oscillation va faire que les cuttings sont aspirés
périodiquement, en finalité ils se déposent à des
zones différentes créant un effet de Dune. Ce
phénomène entraine des problèmes lors des remontées
de la garniture, et les cuttings déposés vont boucher les pores
et microfractures, causant une baisse de productivité.
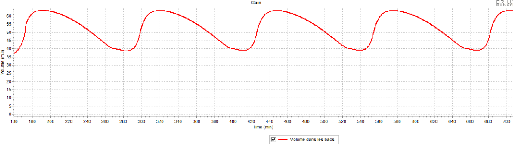
Figure 5.4 : Evolution du niveau des bacs de pendant
le phénomène de slugging.
63
Chapitre5-Effet d'Accumulateur : définition et
expliquation
5.2 Vélocité critique du gaz
Pour la définir simplement elle serait le débit
minimal de gaz à la sortie du point d'injection pour garantir un flux
ininterrompu dans le puits. Ceci implique que le volume de gaz sortant des
points d'injection ne dépend pas des variations de la pression de puits
au même point mais seulement des conditions régnants dans le
concentrique. Pour un fluide compressible (gaz), cela veut dire qu'il faut
atteindre un écoulement dit sonique, pour une vitesse du gaz
au-dessus de la vitesse du son (supersonique), on observe une stabilisation
rapide de la pression de fond ; pour un débit d'injection donné,
le débit de gaz sortant est constant, ceci est connu comme l'effet de
blocage d'un écoulement compressible (Ryhming, 2009)
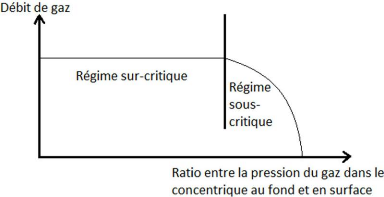
Figure 5.5 : Régimes d'écoulement du gaz
à travers un orifice et effet de blocage (Ryhming, 2009).
On verra par la suite que le ratio critique pour l'azote est
égal à 0.528.
Les figures 5.1 à 5.4 ont été obtenues
avec les données d'un puits foré à Hassi-Messaoud
(ONIZ-40) avec un réajustement des paramètres pour des raisons de
temps de simulation. Une simulation réelle du cas d'ONIZ-40 est
présentée dans le chapitre 7.
Détermination de la vélocité
critique. Dans le but de déterminer le débit
critique d'injection du gaz, une simulation en régime transitoire
s'impose, les données du puits simulé sont illustrées dans
le tableau ci-contre, on a utilisés un débit d'injection de
liquide de 550 l/min et une variation d'injection de gaz entre 36.5 et 50
m3/min.
Chapitre5-Effet d'Accumulateur : définition et
expliquation
Tableau 8 : données du puits
utilisé pour la simulation
|
Profondeur
|
|
Profondeur verticale
|
3434.2 m
|
Profondeur mesurée
|
3572 m
|
Inclinaison max
|
89.5°
|
Openhole mesuré
|
60 m
|
Géométrie du puits
|
|
Tubage de production
|
95/8
|
Tie Back
|
7»
|
Tiges de forage
|
31/2
|
Point d'injection
|
|
Profondeur verticale
|
2439 m
|
Profondeur mesurée
|
2440 m
|
Inclinaison
|
0.8°
|
Fluide d'injection
|
|
Liquide injecté
|
Brut
|
Densité
|
0.83
|
Viscosité plastique
|
4 cp
|
Gaz injecté
|
Nitrogène
|
Densité
|
0.003 sg
|
Temperature injection
|
70° Celsius
|
Fluide de réservoir
|
|
GOR
|
183 m3/ m3
|
Temperature
|
115° Celsius
|
Pression
|
206.8 bars
|
Viscosité
|
4 cp
|
Densité
|
0.85 sg
|
Equipement surface
|
|
Diamètre Duse
|
3»
|
Variation des paramètres
|
|
Injection de liquide
|
550-750 lpm
|
Injection de gaz
|
36.5-55 m3/min
|
|
-- Régime sous-critique (36,5 m3/min).
(Figures 5.1 à 5.4) comme illustré dans la Figure-6.1,
l'intermittence est inévitable et va continuer infiniment sans
intervention de l'opérateur. La réponse de la pression du
concentrique montre qu'il se charge cycliquement. Il est aussi
intéressant de constater que la première bulle de gaz qui sort
est injectée met environ 16 minutes à arriver en surface alors
que le temps de recharge du concentrique est de l'ordre de 38 minutes, ce qui
veut dire que pendant un période, il n'y a pas de gaz dans le puits.
-- Régime critique (38 m3/min).
(Figures 5.6 à 5.8) comme illustré avant, 36.5m3/min
est en dessous de la vélocité critique nécessaire pour
assurer un écoulement continue du gaz à travers les orifices
d'injection. Des simulations en plus ont été faites, et on
observe qu'avec un débit de 38 m3/min, il y a début de
stabilisation, la BHP converge lentement et il y a continuité de gaz
malgré une oscillation importante au début, cet état est
le point où le temps de chargement du concentrique est égal ou
légerement superieure au temps que met la bulle de gaz pour arriver en
surface. Toutefois il n'y a toujours pas stabilisation de la condition
d'underbalance après 8 heures d'injection. Il est donc nécessaire
d'aller plus loin pour trouver un débit qui stabilise la pression dans
des temps raisonnables.
-- Régime sur-critique (41 m3/min).
(Figures 5.9 à 5.11) on remarque que la réponse de la
pression est plus applati et que le débit de gaz sortant tend à
être constant. Le débit d'injection de l'azote par l'annulaire
oscille autour de la valeur du débit d'injection en surface. Toutefois,
la pression de fond ne se stabilise pas totalement malgré que la
64
condition d'underbalance puisse être maintenue
après 6 heures d'injection, ce qui n'est pas toujours le cas. Il est
donc nécessaire d'aller plus loin dans la simulation pour trouver un
débit qui stabilise la pression dans un temps raisonnable
-- Régime idéal (47 m3/min).
(Figures 5.12 à 5.14) avec ce débit la BHP se stabilise en
une seule oscillation. Avec une période de stabilisation d'à
peine deux heures après la première bulle de gaz sortie. Le
débit d'injection du concentrique converge rapidement vers le
débit entrant dans ce dernier en surface.
65
Chapitre5-Effet d'Accumulateur : définition et
expliquation
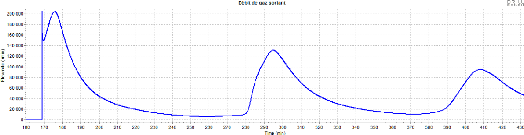
Figure 5.6 : Evolution du débit sortant de gaz,
régime critique.
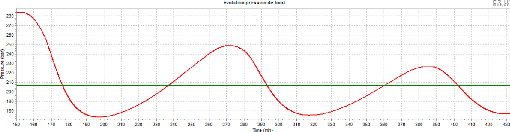
Figure 5.7 : Evolution de la pression de fond,
régime critique.
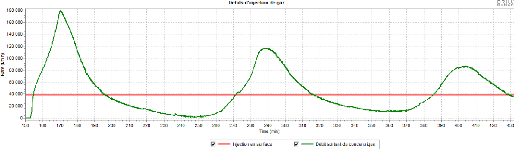
Figure 5.8 : Evolution du débit d'injection de
gaz, régime critique.
Chapitre5-Effet d'Accumulateur : définition et
expliquation
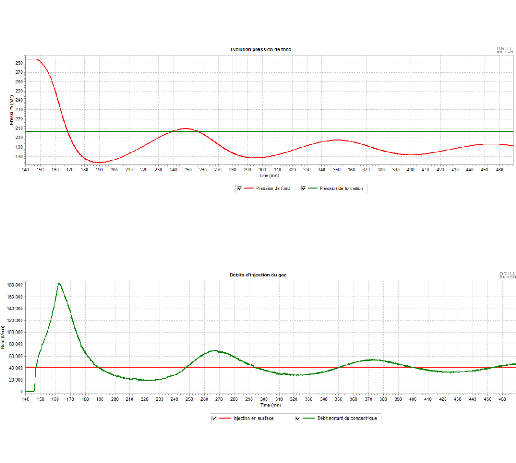
Figure 5.9 : Evolution du débit sortant de gaz,
régime sur-critique.
Figure 5.10 : Evolution pression de fond,
régime sur-critique.
Figure 5.11 : Evolution du débit d'injection de
gaz, régime sur-critique.
66

67
Chapitre5-Effet d'Accumulateur : définition et
expliquation

Figure 5.12 : Evolution du débit de gaz
sortant, régime idéal.
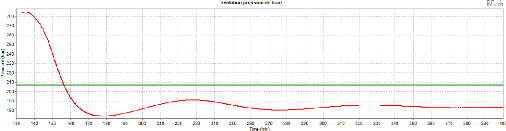
Figure 5.13 : Evolution de la pression de fond,
régime idéal.
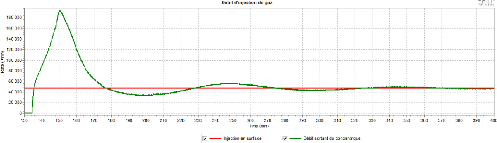
Figure 5.14 : Evolution débit d'injection de
gaz, régime idéal.
68
Chapitre6-Facteurs Influençants la stabilité de la
BHP
Chapitre-6 Facteurs influençants la
stabilité de la pression de fond
6.1 Volume du concentrique
Dû au phénomène d'accumulation, le volume
du concentrique est directement proportionnel à la tendance de
fluctuation de la BHP. Plus grand est le volume du concentrique, plus grande
sera la durée de stabilisation. Ceci est illustré dans la
Figure-6.1, ce paramètre est varié simplement par variation de la
profondeur du point d'injection, qui a été placé à
2440m comme dans l'exemple Tableau-7 ensuite à 2000m de profondeur, une
comparaison de l'évolution de la BHP a été faite.
(Simulation faite avec débit de gaz 53m3/min et débit
de liquide 650 l/min)
Remarque : le point d'injection peut être mis plus haut
avec l'incorporation d'un packer avec le Tie-Back 7» durant sa descente et
mise en place de la circulating sub au-dessus de ce dernier. (Figure 6.5).
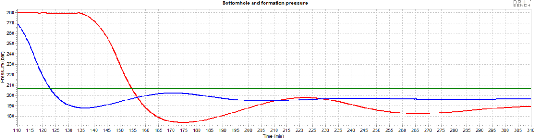
Figure 6.1 : Variation de la BHP en fonction du temps
pour différents points d'injection.
Le volume du concentrique au point d'injection 2440m est de
35.58m3, alors que si on met le point à 2000m, on aura une
diminution de 6.4m3 de volume à remplir, la Figure ci-dessus
illustre l'effet significatif du volume sur la stabilisation de la pression.
Cependant, mettre le point d'injection plus haut signifie que la
colonne à alléger est moins importante, et donc la pression de
fond stable sera plus élevée, il sera donc nécessaire
d'augmenter le débit d'injection de gaz ou bien de diminuer le
débit de liquide.
Un autre moyen pour diminuer le volume du concentrique de
façon significative serait de descendre un tubage 75/8 au
lieu d'un tubage 7», dans le puits exemple il diminuerait le volume
à remplir de 11.3m3 ce qui engendrerais une meilleure
stabilisation de la BHP.
6.2 Débit de gaz
Il est évidemment inversement proportionnel à la
tendance de fluctuation de la BHP. Un débit élevé augmente
la poussée du gaz, et donc sa vitesse au point d'injection. Et donc de
meilleures chances d'atteindre le régime critique. (Simulation faite
avec un débit de liquide 550 l/min et une pression de surface de 5
bars)
69
Chapitre6-Facteurs Influençants la stabilité de la
BHP
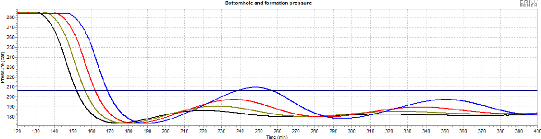
Figure 6.2 : Variation de la BHP en fonction du temps
pour différents débits de gaz (m3/min)
On remarque dans la Figure 6.2 que pour un débit
d'injection de 47m3/min, la pression de fond gagne une certaine
stabilité au bout de 4 heures, alors que pour 41m3/min, on
n'atteint vraiment un underbalance qu'après 5 heures d'injection, et la
pression ne se stabilise pas au bout de 7 heures.
6.3 Débit de liquide
Le débit des pompes a une influence directe sur la
pression de fond, et sur la pression du puits appliquée au point
d'injection du gaz, et donc est directement proportionnel au
phénomène de fluctuation de la BHP. (Simulation faite avec un
débit de gaz 50m3/min et une pression de surface de 5 bars)
(Figure 6.3)
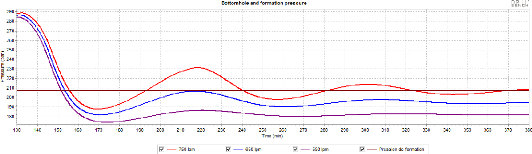
Figure 6.3 : Variation de la BHP en fonction du temps
pour différents débits de liquide.
En plus, un débit important aux pompes entraine une
augmentation de la BHP, et donc le risque perdre définitivement la
condition d'underbalance. Le Figure 6.4 montre la variation du temps de
stabilisation en fonction de la variation du débit de liquide pour
différents débits de gaz, la stabilisation étant prise
comme l'état où les fluctuations de pression ne dépassent
pas un bar d'amplitude. On remarque une pente linéaire ascendante. Le
fait qu'il y a une relation directe entre ces deux paramètres facilite
grandement la compréhension de l'influence d'un sur l'autre et ouvre la
voie pour l'établissement de corrélations qui pourront aider les
ingénieurs sur chantier à mieux contrôler le
phénomène.
70
Chapitre6-Facteurs Influençants la stabilité de la
BHP
DUREE DE STABILISATION (MINUTES)
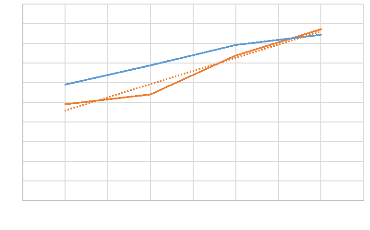
450
400
500
350
300
250
200
150
100
50
0
400 450 500 550 600 650 700 750 800
DEBIT DE LIQUIDE EN LITRE PAR MINUTE
53000 m3/min 50000 m3/min Linéaire (53000 m3/min)
Figure 6.4 : Relation entre le débit de liquide
et le temps de stabilisation de la BHP.
6.4 Surface d'injection TFA (Total Flow Area)
Pour minimiser les fluctuations de pression, il est
nécessaire de garantir un flux constant de gaz à travers les
orifices d'injection. D'après les équations d'écoulement
de gaz à travers un orifice (Buse de Laval, Ryhming, 2009), le
débit critique est directement proportionnel à la section
d'écoulement. Une methode déjà utilisée au
Moyen-Orient est d'installer une Duse de fond, ou restriction sur les ports
d'injection, ce qui provoque des pertes de charge et réduit la
quantité de gaz qui sort à chaque pic, régulant ainsi le
débit sortant dans le puits.
Le calcul de la TFA de par le diamètre des orifices,
nécessite en premier de connaitre la pression en amont de ces derniers
(P1). Connaissant la pression en aval qui est égale à la pression
dynamique exercée par la colonne de fluide de forage en circulation (P2)
(Figure-6.5). Pour cela, on utilise le concept du ratio critique du gaz
(Ryhming, 2009) qui donc le rapport entre la pression en aval et en amont d'un
orifice pour une onde de choc. Au point critique, ce ratio s'écrit :
k
Yc = p2 = 1 2
k+1p1
|
k-1 (6.1)
|
|
Où k : ratio des chaleurs spécifiques pour le gaz
en question, est égal à 1.4 pour l'azote (gaz diatomique)
Le ratio critique est donc toujours égal à
0.528 pour un gaz diatomique.
Chapitre6-Facteurs Influençants la stabilité de
la BHP
Pour l'exemple simulé en chapitre 5, la pression
dynamique au point d'injection est égale à 2886 psi, ce qui nous
donne une pression en amont égale à :
P
1 = = 5465 psi Ce
qui dépasse la capacité du matériel en surface. Donc le
point
0.528
critique peut être difficilement atteint dans les
conditions de ce puits.
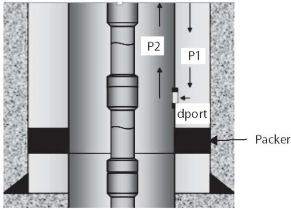
Figure 6.5 : llustration d'un point d'injection de
gaz. (Rehm, 2012)
Pour calculer le diamètre du point d'injection on
applique la formule suivante : (Rehm, 2012)
71
= Qsc*JYgTi%i
DPI I k 2 k+1
(6.2) 844P14 (k+1)(Yck-Yc k )
Avec :
Qsc : débit condition standards (Mscf/day)
|
2288 (équivalent à 45m3/min)
|
yg : masse spécifique du liquide
|
0.83
|
T1 : temperature en amont (Rankine)
|
699
|
Z1 : facteur de compressibilité du gaz
|
0.76
|
|
L'application numérique donne DPI=0.229in. Ce qui nous
donne une TFA=0.04in2. Donc si 4 ports sont installés, le
diamètre de chaque port devra être égal à 0.1145in
(environ 3mm).
Une autre méthode de calcul basée sur
l'expérience stipule que le problème de Slugging peut être
évité totalement avec une TFA=1% de la section du concentrique.
Comme illustré dans la
8.532-7t
Figure-6.6, la surface de la section est égale à :
if = 18.66 nt.
&
Ce qui nous donne une TFA de 0.1866in2. Donc un
diamètre de 0.48in, pour 4 ports installés on a un
diamètre de 0.24in (6.1 mm).
72
Chapitre6-Facteurs Influençants la stabilité de la
BHP
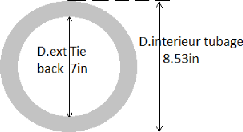
Figure 6.6 : Illustration section du
concentrique.
On remarque bien que les diamètres des orifices sont
assez petits, ce qui augmente les chances de bouchage par les cuttings ou par
des particules solides de la boue. Les compagnies de services
préfèrent de loin avoir une fluctuation de pression qu'un
bouchage des points d'injection, car c'est un problème très
délicat qui peut entrainer des complications sévères
(jusqu'à l'abandon de l'injection de gaz).
Pour éviter le risque de bouchage des orifices, une TFA
de 40% de la section du concentrique est recommandée, soit un
diamètre pour 4 orifices de 1.54in (soit 3.9 cm). Mais un
diamètre pareil amplifie le phénomène de Slugging, en plus
de provoquer une intrusion de fluides dans le concentrique (voir 6.1 «
Spring effect »). Pour remédier à ce
phénomène, il peut être nécessaire d'installer une
valve anti-retour à chaque orifice (voir 8.2)
6.5 Pression à la Duse
La Figure-6.7 montre l'évolution de la pression de fond
en fonction du temps pour différents pourcentages de fermeture de la
Duse. On rappelant que plus on ferme la Duse plus la pression appliquée
en surface est élevée. (Simulation faite avec 650 l/min de
liquide et 53m3/min de gaz)
Il est observé que plus le pourcentage d'ouverture de la
duse diminue, plus la pression se stabilise rapidement. Toutefois puisque la
pression de fond dépend de la pression appliquée en surface,
celle-ci se stabilise à chaque fois à une pression superieur.
Ceci s'explique par le fait que plus on ferme la Duse, plus on limite
l'évacuation rapide du gaz du puits. Et donc la colonne hydrostatique
reste plus longtemps allégée avec du gaz.
Une ouverture de 40% par exemple du puits dans ce cas-ci donne
une stabilisation idéale pour la BHP, mais toutefois elle se stabilise
au-dessus de la pression de formation, créant ainsi une situation
d'overbalance.
73
Chapitre6-Facteurs Influençants la stabilité de la
BHP
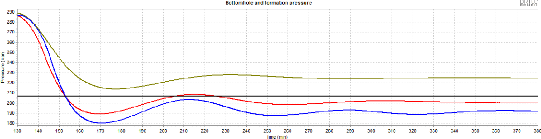
Figure 6.7 : Evolution de la BHP en fonction du temps
pour différents pourcentages de fermeture de la
Duse.
0
20 30 40 50 60 70 80 90 100
Ouverture de la Duse %
550 lpm 650 lpm Linéaire (650 lpm)
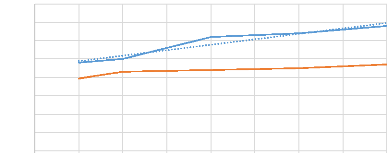
Durée de stabilisation (min)
450
400
350
300
250
200
150
100
50
Figure 6.8 : Relation entre l'ouverture de la Duse et
la durée de stabilisation de la BHP.
6.6 Influence de la production
La production à vraisemblablement un effet sur la
stabilité de la pression de fond. D'un côté si le fluide de
formation est à fort GOR, le gaz échappé va alléger
encore plus la colonne de liquide et « aider » l'azote, une
réduction de la BHP conduit à une meilleure stabilité et
une atténuation des fluctuations.
D'un autre côté, un afflux non
contrôlé peut entrainer une baisse trop grande de la pression de
fond entrainant une augmentation des fluctuations. Et donc avoir un effet
inverse.
Cependant dans la région de Hassi Messaoud, avec un GOR
faible (< 150m3/m3), l'influence de la production
n'est pas très élevée. (Figure 6.9)
74
Chapitre6-Facteurs Influençants la stabilité de la
BHP
Toutefois, dans le cas où il a possibilité de
rencontrer des zones à gaz, il faut prendre en considération leur
influence, un moyen rapide de détecter l'intrusion d'une grande
quantité de gaz dans le puits est par l'incorporation d'un capteur de
pression de fond avec le MWD. Qui donne instantanément les variations de
la BHP.
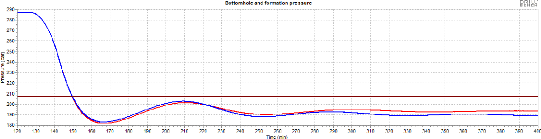
Figure 6.9 : Variation de la BHP en fonction du temps
dans le cas avec production et sans.
6.7 Viscosité de la phase liquide
Durant la phase de forage en underbalance, le fluide de
réservoir qui va affluer dans le puits va se combiner avec le fluide de
forage et modifier la viscosité du fluide sortant. Il est donc
nécessaire d'étudier l'effet de la fluctuation de la
viscosité sur la stabilisation de la BHP.
D'après les travaux de Myktiw (2003), il est clair que la
viscosité de la phase liquide a un impact direct sur la stabilité
de la BHP. Plus la viscosité croit plus on a une meilleure
stabilité de la BHP, ceci est dû au fait que la viscosité a
tendance à générer une résistance à la
montée des bulles de gaz et donc à diminuer leur vitesse de
migration dans le puits, et donc la BHP s'en trouve diminuée pour une
plus longue durée, augmentant la possibilité de passer d'un
régime sous-critique à un régime critique. D'un autre
point de vue, une grande viscosité provoque de plus grandes pertes de
charge à la sortie des points d'injection, la vitesse du gaz s'en trouve
diminuée, l'écoulement est régulé. Les bulles de
gaz sortantes tendent à se rassembler, ce qui en résulte un
écoulement continu.
Cependant, une forte viscosité a tendance à
augmenter les pertes de charge dues aux effets de friction dans l'annulaire,
augmentant ainsi la BHP, et donc contribue à l'effet de slugging.
(Figure 6.11)
Pour les fortes valeurs de viscosités, l'augmentation des
pertes par friction contre les parois va finir par vaincre la tendance «
stabilisante » de la viscosité. Il est donc nécessaire de
faire des simulations pour déterminer l'influence du changement de la
viscosité sur la BHP. (Figure-6.10)
Les simulations pour l'influence de la viscosité ont
été faites pour un débit de liquide de 650 l/min et un
débit de gaz de 45m3/min.
On remarque sur la Figure-6.12 qu'il y a un optimum autour de
50cp, au-delà de cette valeur, l'action d'amplification des forces de
frottements l'emporte sur l'effet stabilisant de la viscosité.
75
Chapitre6-Facteurs Influençants la stabilité de la
BHP
Conclusion. L'étude de
l'influence de chaque paramètre est très intéressante car
il permet à l'ingénieur spécialiste en UBD d'optimiser la
conception du puits pour de meilleures performances et un gain de temps.
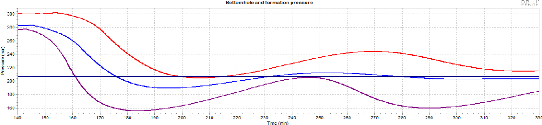
Figure 6.10 : Variation de la BHP en fonction du temps
pour différentes viscosités.
0 50 100 150 200
Viscosité (cp)
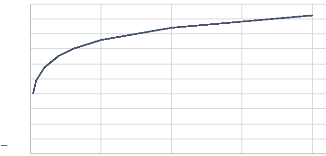
Pertes de charge annulaires (bar)
45
40
50
35
30
25
20
15
10
5
0
Figure 6.11 : Evolution des pertes de charge annulaires
en fonction de la viscosité de la phase liquide.
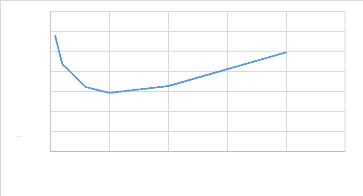
0 50 100 150 200 250
Viscosité (cp)
Durée de stabilisation (min)
400
700
600
500
300
200
100
0
Figure 6.12 : Influence de la viscosité du
liquide sur la durée de stabilisation de la BHP.
Chapitre7-Etude de cas ONIZ-40
Chapitre-7 Etude de cas ONIZ-40
7.1 Présentation du puits
ONIZ-40 est un puits de développement horizontal
foré dans la subdivision ONI du champ de Hassi Messaoud. Le puits a
été foré à une profondeur totale de 3439m/4070m
TVD/MD, l'objectif principal était de forer un drain de 900m en
underbalance à travers le réservoir Cambrien RaD2. Le puits est
situé dans une zone très compartimentée entre les puits
ONIZ402, ONMZ572, ONIZ411 et ONIZ301 (Sonatrach).
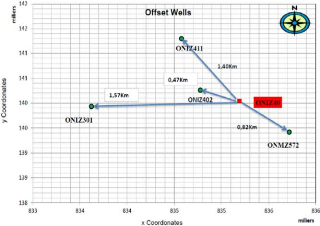
Figure 7.1 : Localisation ONIZ-40.
(Sonatrach)
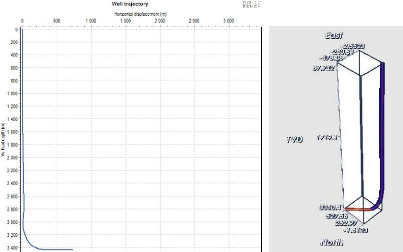
76
Figure 7.2 : Survey et illustration profil du puits
ONIZ-40. (Bleu : Tubage et Rouge : Openhole)
77
Chapitre7-Etude de cas ONIZ-40
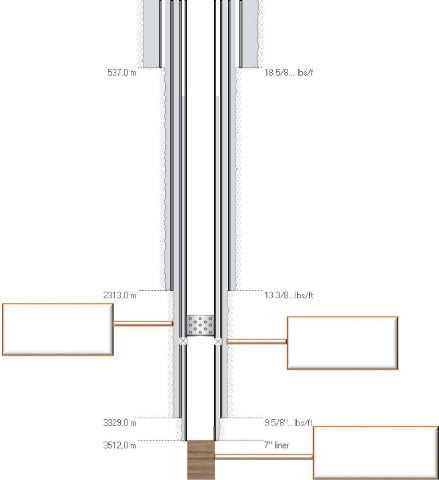
Ports d'injection du concentrique 2440m MD/TVD
Top Liner 7» 2457 m MD/TVD
Openhole 6» jusqu'à 4020 m MD/3437m TVD Inc
89°
Figure 7.3 : Architecture du puits ONIZ-40
Les objectifs de Sonatrach pour ce puits sont :
· Forer 900 m en 6» après pose du Liner 7»
à travers le Drain RaD2 dans des conditions d'underbalance.
· Minimiser l'endommagement de la formation productrice.
· Caractérisation du réservoir en cours de
forage en effectuant un flow test suivi d'un test Build up après
obtention des premiers signes de production.
· Augmentation de la vitesse d'avancement.
78
Chapitre7-Etude de cas ONIZ-40
Cependant il n'a été foré que 693 m sous
le sabot, la production ayant atteint 8m3/heure, il a
été jugé qu'il n'était pas nécessaire de
continuer plus loin.
L'objectif de minimisation de l'endommagement n'a pas
été totalement respecté car il a été
nécessaire de tuer le puits plusieurs fois avec une boue lourde avant de
remonter la garniture (Mud cap)
Tableau 9 : Récapitulatif informations
sur le puits ONIZ-40
|
Champ
|
Hassi Messaoud
|
|
|
Développement
|
Opérateur
|
Sonatrach
|
Contracteur de forage
|
ENAFOR
|
Appareil
|
ENF#47
|
Localisation
|
Latitude
|
N 31° 48' 18.3111»
|
|
E 06° 14' 20.57»
|
|
X=806673.976 m
|
|
Elévation
|
Niveau du sol
|
161.393m au-dessus du niveau de la mer
|
|
9.14m au-dessus du sol
|
|
170.53m au-dessus du niveau de la mer
|
Profondeur puits
|
TVD/MD
|
3439/4070 m
|
|
7.2 Paramètres opérationnels
Les considérations suivantes doivent être prises en
compte pour la simulation :
· Système biphasique, le brut comme phase liquide et
le gaz N2 comme phase gazeuse.
· Une vitesse annulaire d'au minimum 50m/min dans la partie
horizontale pour assurer une bonne remontée des cuttings et un bon
nettoyage des parois (environ 650 l/min) (Weatherford)
· Densité des cuttings 2.71 sg, avec un
diamètre moyen de 0.12 cm.
· La fenêtre drawdown est comprise entre 7% et 9%
Les paramètres relatifs au puits sont décrits dans
le Tableau-10.
7.3 Modélisation statique de la pression de
fond
Une simulation de la pression de fond en fonction du
débit de gaz injecté a été faite en utilisant le
logiciel Drillbench, les résultats sont illustrés dans la
Figure-7.4.
La simulation est faite après 60 mètres
forés sous le sabot, à l'entrée du drain.
L'opération d'injection de gaz a commencée.
Dans le cas ONIZ-40, un débit de liquide de 650 l/min a
été choisi pour pallier aux risques de mauvais nettoyage du trou.
Avec un débit initial de gaz de 41m3/min ce qui correspond au
drawdown minimal exigé de 7%.
79
Chapitre7-Etude de cas ONIZ-40
Tableau 10 : Paramètres relatifs au puits
ONIZ-40 nécessaires à la simulation.
|
Profondeur Top réservoir (MD)
|
Pression réservoir
|
Production d'huile estimée
|
GOR
|
WOR
|
3561 m
|
196 bars
|
8m3/min
|
183
|
0
|
IPR
|
0.00153 bbl/jour/psi/ft
|
Profil de température dans le tubage
|
43°C à 0m - 117°C à 3420 TVD
|
Ports d'injection
|
2440 MD/TVD
|
Densité du brut utilisé pour le forage
|
0.83
|
Propriétés du Nitrogène
|
96% N2 + 4% O2
|
Pertes de charge à travers le MWD
|
200 psi
|
Pertes de charge à travers le moteur de
fond
|
400 psi
|
Duses de l'outil ( /32 in)
|
13, 13, 13
|
Pression à la tête de puits
|
14.6 psi
|
|
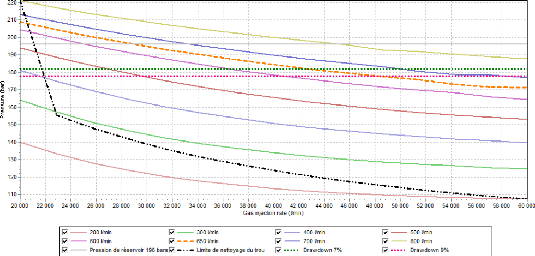
Figure 7.4 : Modélisation de la pression de
fond en fonction du débit de gaz injecté.
80
Chapitre7-Etude de cas ONIZ-40
Tableau 11 : Etapes de réduction de la
BHP pour 650 l/min
|
Débit de gaz
|
Pression de fond
|
Drawdown
|
Drawdown2
|
m3/min
|
psi
|
%
|
psi
|
30000
|
194,87
|
0,57
|
1,13
|
32142,85612
|
192,36
|
1,86
|
3,64
|
34285,71582
|
190,00
|
3,06
|
6,00
|
36428,57194
|
187,76
|
4,20
|
8,24
|
38571,42806
|
185,66
|
5,27
|
10,34
|
40714,28418
|
183,70
|
6,28
|
12,30
|
42857,14388
|
181,88
|
7,20
|
14,12
|
45000
|
180,20
|
8,06
|
15,80
|
47142,85612
|
178,63
|
8,86
|
17,37
|
49285,71582
|
177,18
|
9,60
|
18,82
|
51428,57194
|
175,83
|
10,29
|
20,17
|
53571,42806
|
174,58
|
10,93
|
21,42
|
55714,28418
|
172,42
|
12,03
|
23,58
|
57857,14388
|
171,36
|
12,57
|
24,64
|
60000
|
171,33
|
12,58
|
24,67
|
|
7.4 Modélisation Dynamique : illustration du
problème
Après avoir foré 60m MD sous le sabot, on a
commencé l'injection de gaz dans le but de passer en underbalance avant
de débuter la phase de forage de la zone productrice. Avec un
débit initial de gaz à 41 m3/
min. au bout de deux heures on observait des
bouchons de gaz qui atteignaient 100 m3/min, la duse a
été fermée à plusieurs reprises pour réguler
le flux de gaz en surface. (Figure 7.7 et 7.8)
La Figure 7.5 montre les fluctuations de pression qui se sont
produites et qui ont été simulées avec le module
Dynaflodrill. Après 7 heures, la décision d'augmenter le
débit de gaz à 47 m3/min par palier de 0.5
m3/min.
On observe sur le graphe d'injection de gaz (Figure 7.6) une
oscillation du débit autour de la valeur du débit d'injection en
surface après passage à 47 m3/min, on entre dans une
situation d'underbalance permanente après 7h 30min d'injection.
Cependant la BHP fluctue toujours après 12 heures d'injection et n'est
pas encore entrée dans la fenêtre exigée de 7-9%.
Les principaux problèmes rencontrés :
- Difficultés dans le contrôle des effluents en
surface ; une alternance rapide entre gaz et liquide au séparateur.
- Dû à l'augmentation de la BHP pendant
l'état de fermeture de la duse1, un grand volume de liquide
est rentré dans le concentrique quand il s'est déchargé du
premier bouchon de gaz, donnant les signes d'une perte de circulation.
1 La pression de fond ayant atteint plus de 320 bars
après 4 heures d'injection, la fermeture de la duse pour endiguer
l'afflux vers le séparateur a causé un pic de pression.
81
Chapitre7-Etude de cas ONIZ-40
? Impossibilité de forer dans ces conditions,
l'état d'underbalance n'étant pas assuré lors du
forage, la décision d'attendre la stabilisation de la
pression fut prise2. Ce qui implique un temps non productif.
? Pendant le forage, les fluctuations de pression ont
occasionnées un effet de dune, ce qui a eu pour conséquence des
tirages excessifs lors des remontées de la garniture.3
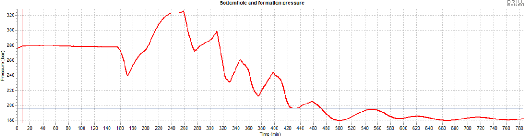
Figure 7.5 : Evolution BHP cas ONIZ-40
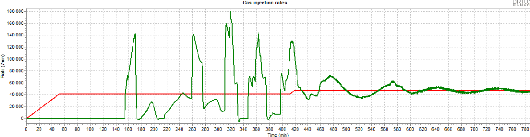
Figure 7.6 : Débit d'injection de gaz
ONIZ-40
2 Le temps d'attente total fut environ 24 heures.
3 Le gaz, même injecté dans le tubage,
va créer une dépression dans la partie openhole qui va aider au
nettoyage des parois, une fluctuation de l'injection de ce dernier va entrainer
la retombée des cuttings dans la zone des 60° car la
dépression nécessaire pour transporter les cuttings dans cette
zone disparait momentanément.
82
Chapitre7-Etude de cas ONIZ-40
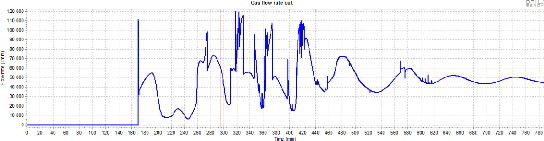
Figure 7.7 : Débit sortant en sortant de
l'annulaire en surface.
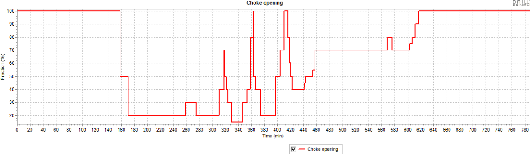
Figure 7.8 : Ouverture de la duse pendant la phase
d'injection du gaz, ONIZ-40.
Chapitre8- Solutions et Propositions
Chapitre-8 Solutions et Propositions
8.1 Manipulation de la pression de la duse
L'un des moyens les plus habiles pour contrôler la
pression de fond est par l'application d'une pression en surface (Back
Pressure) avec la duse. Si la TFA est trop grande pour garantir la
stabilité, un bon moyen pour contrôler la pression du puits est
par la manipulation de la duse en surface. En prenant en compte le temps de
retard de la réponse de pression.
Un contrôle dynamique de la pression à la duse
permet donc d'atténuer au fur et à mesure les fluctuations de
pression, la pression de surface peut être augmentée en fermant la
duse avant le pic de pression pendant le déchargement du concentrique,
et inversement pendant son chargement.
Une simulation avec les mêmes paramètres
d'injection que le problème vue au chapitre 7 a été faite,
avec un contrôle précis de l'ouverture de la duse, et une
anticipation des variations de pression et de débit à la sortie
des puits d'injection. En prenant en compte un temps de retard de la
réponse de 20 minutes en moyenne. Cette manipulation est
basée sur le fait d'anticiper l'évolution du débit de gaz
au point d'injection et non en surface.
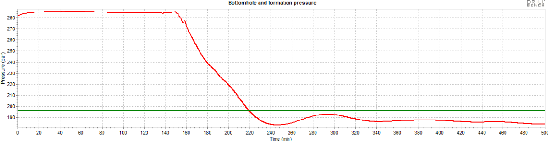
Figure 8.1 : Evolution de la BHP pour une pression de
duse contrôlée.
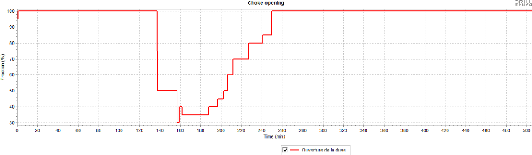
Figure 8.2 : Evolution du pourcentage d'ouverture de
la duse.
83
84
Chapitre8- Solutions et Propositions
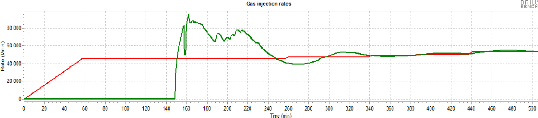
Figure 8.3 : Evolution des débits d'injection
de gaz pour pression de duse contrôlée.
De par la Figure-8.1, une manipulation précise du
degré d'ouverture de la duse suffit à contrôler les
variations de pression. Au moment de la sortie de la première bulle de
gaz, une pression de surface appliquée sert à endiguer
l'entrée de gaz dans le puits. Le gaz qui est relâché
ensuite avec une ouverture progressive de la duse en prenant en compte le fait
qu'un débit de gaz de plus de 120m3/min serait au-dessus de
la capacité du séparateur en surface, et donc il faut essayer de
ne pas laisser le gaz entrant dépasser 100m3/min (marge de
sécurité).
Après stabilisation de la pression le débit de
gaz ajusté à 47m3/min pour avoir une BHP dans la
fenêtre exigée de drawdown entre 7% et 9%. On constate avec cette
méthode qu'on entre dans la fenêtre après 7 heures
d'injection de gaz ce représente une évolution significative par
rapport au présenté dans le chapitre 7.
Cependant cette methode nécessite une manipulation
précise et une bonne communication entre l'opérateur de duse et
l'ingénieur UBD. Il serait également indispensable d'incorporer
une duse dite semi-automatique utilisée en général pour
les opérations MPD où il faut garder une pression de surface
constante et contrôler avec précision le pourcentage d'ouverture
de la duse avec un panel numérique.
8.2 Mise en place d'un clapet anti-retour
L'installation d'une vanne anti-retour ou « check valve
» permettrait d'empêcher le liquide d'entrer dans le concentrique,
minimisant ainsi le « Spring effect ». Et donc le flux de gaz s'en
trouve régulé, car il n'y a plus de communication de pression
entre le puits en le concentrique du moment que la pression de ce dernier est
inférieure à celle de la colonne hydrostatique dans le puits au
point d'injection.
Ce qui implique un temps de rechargement plus rapide pour le
gaz et donc une meilleure stabilité de la BHP. La Figure 8.4 montre une
comparaison de ce que serait l'évolution de la BHP dans le puits ONIZ-40
avec et sans incorporation d'un clapet anti-retour, sans aucune manipulation de
la duse et avec un débit de gaz de 45m3/min. On remarque une
grande différence entre les profils de pression, avec une vanne
anti-retour on a des oscillations avec une amplitude plus faible que pour le
deuxième cas.
85
Chapitre8- Solutions et Propositions
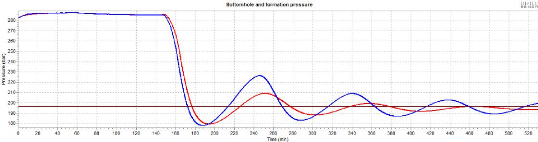
Figure 8.4 : Evolution BHP ONIZ-40 avec incorporations
d'une check valve sans manipulation de la duse.
Mais ce cas est évidemment impossible à avoir en
réalité, car en réalité il faut prendre en compte
la quantité de gaz qui arrive en surface et qui est
contrôlée par fermeture de la duse et donc application d'une
pression en surface, ce qui a un effet stabilisant sur la pression.
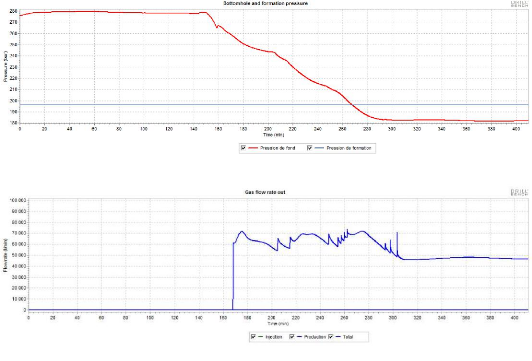
Figure 8.5 : Evolution BHP ONIZ-40 avec check valve, cas
avec manipulation de la duse.
Figure 8.6 : Evolution du débit de gaz au
séparateur, check valve avec manipulation de la duse.
Les Figures suivantes montrent les résultats de la
simulation en prenant en compte un débit de gaz maximum admissible en
surface de 100m3/min et un débit d'injection initial de
41m3/min.
86
Chapitre8- Solutions et Propositions
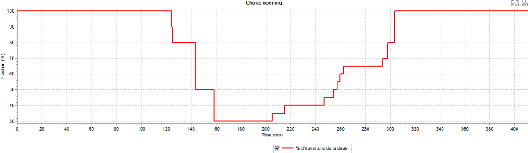
Figure 8.7 : Ouverture de la duse, check
valve.
On observe une stabilisation de la pression au bout de 5h 30min,
ce qui donne un résultat significatif par rapport au cas ONIZ-40.
Au contraire du premier cas où il était
proposé de contrôler la pression de la duse, cette manipulation
n'exige pas une grande expertise, elle n'est pas basée sur
l'anticipation des fluctuations de pression au point d'injection mais
simplement sur la maitrise des effluents en surface (Figure 8.6 débit de
gaz en surface).
Cette solution présente nombre d'avantages :
? Simple d'utilisation, n'exige pas des calculs
avancés.
? Un temps de stabilisation très réduit, 6 heures
dans le cas étudié.
? Pas de « Spring effect », donc pas d'intrusion de
liquide dans le concentrique qui pourrait simuler une perte.
Cette technique exige l'installation de clapets anti-retour sur
les ports d'injection avant descente de la Circulating sub. Cependant elle
présente un risque d'usure rapide des clapets dû au
phénomène d'érosion.
8.3 Injection duale
L'un des facteurs qui influent sur le phénomène
de slugging est la pression qui est appliqué sur les ports d'injection
par le fluide présent dans le puits qui est directement proportionnelle
à la BHP. On a bien vu que plus la BHP est élevée, plus le
débit entrant de gaz présente des instabilités. Ceci est
dû au fait que le fluide « pousse » le gaz dans le
concentrique, ne le laissant pas entrer dans le puits (ce problème peut
être résolu avec un clapet anti-retour). Une solution donc serait
de diminuer la BHP d'une façon à ce que le gaz rencontre une
pression moins faible à sa sortie dans le puits.
87
Chapitre8- Solutions et Propositions
Une méthode habile serait de faire une injection
double, l'une par l'intérieur de la garniture, la deuxième par
concentrique. On commence avec l'injection par tiges, dont le but est de faire
descendre rapidement la BHP1, et pour ne pas perdre de temps on
commence au même moment à charger le concentrique et à
chasser le liquide à l'intérieur avec le gaz.
Avant que le concentrique ne commence à
débiter, il faut arrêter l'injection de gaz par tiges, et par la
suite augmenter le débit dans le concentrique. (Initialement à
32.5m3/min ensuite à 47m3/min).
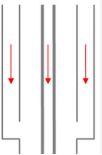
Figure 8.8 : Principe injection duale.
La simulation a été faite en prenant en
considération la capacité maximale du séparateur en
surface à 100m3/min, et le contrôle des débits
en surface s'est fait par manipulation de la duse.
Cette technique ne présente pas de contraintes
pratiques, car les compresseurs sont divisés en deux blocs, chacun avec
son refroidisseur et son générateur de Nitrogène. Chaque
bloc refoule dans une ligne d'injection, et les deux lignes se rencontrent pour
être connectés au concentrique.2
Une ligne auxiliaire est toujours installée qui est
raccordée à la colonne montante au cas où il faudrait
injecter par tiges. Donc il est possible de raccorder un bloc au concentrique
et le deuxième à la colonne montante.
La procédure suivie est de commencer par injecter
20m3/min de gaz par l'intérieur des tiges, ce qui va diminuer
la pression de fond, tout en injectant dans le concentrique un débit de
32.5m3/min afin de le charger. Avant que la première bulle de
gaz ne commence à sortir du concentrique, il faut diminuer le
débit d'injection par tiges graduellement de façon à ce
que au moment où commence l'injection par concentrique, l'injection de
gaz par tiges devient nulle.
A ce moment il faut connecter la deuxième ligne
d'injection au concentrique pour monter le débit à
47m3/min.
1 Car l'injection par tige n'entraine pas de
phénomène de slugging quel que soit le débit d'injection
du gaz, ceci dû au faible volume interieur des tiges.
2 Chaque bloc de compresseurs possède une
capacité maximum de refoulement de 32.5m3/min, ceci a
été pris en compte lors de la simulation.
88
Chapitre8- Solutions et Propositions
On observe une stabilisation à l'intérieur de
la fenêtre de drawdown (7%-9%) au bout de 5h 30min. ce qui est
équivalent au cas avec clapet anti-retour.
L'avantage de cette methode c'est qu'elle peut être
réalisée avec les moyens présents déjà sur
chantier, et qu'elle procure une stabilisation rapide de la BHP. En revanche,
elle implique une bonne coordination des opérations en surface pour que
le BHP ne remonte pas avant le début de l'injection par concentrique, et
également pour ne pas avoir un trop grand débit de gaz dans le
puits qui pourrait entrainer un drawdown trop élevé et des
difficultés à contrôler les effluents en surface.
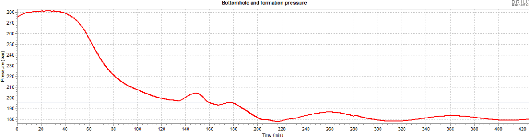
Figure 8.9 : Evolution BHP ONIZ-40 avec injection
double.
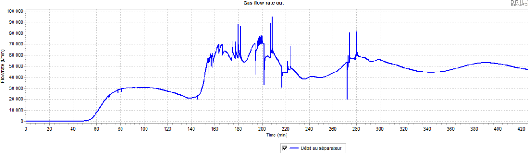
Figure 8.10 : Evolution débit de gaz au
séparateur, injection double.
89
Chapitre8- Solutions et Propositions
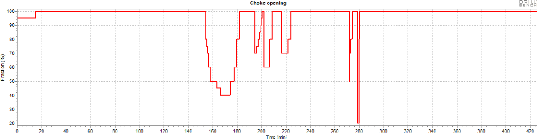
Figure 8.11 : Ouverture de la duse, injection
double.
8.4 Injection par parasite string
La proposition ici est de changer totalement la méthode
d'injection d'azote, on opte plutôt pour l'injection via parasite, qui un
tubing de petit diamètre (2» dans le cas simulé) descendu
avec le tubage, le point d'injection se trouve dans la partie tubée du
trou.
La simulation de l'évolution de la BHP en fonction du
débit de gaz injecté est présentée dans
Figure-8.12
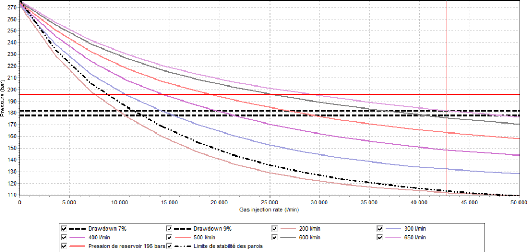
Figure 8.12 : modélisation statique de la BHP,
cas injection par parasite.
90
Chapitre8- Solutions et Propositions
Avec cette technique on réduit le volume à remplir
de 15m3 par rapport à celui du concentrique.
L'évolution de la BHP est présentée dans la
Figure-8.13.
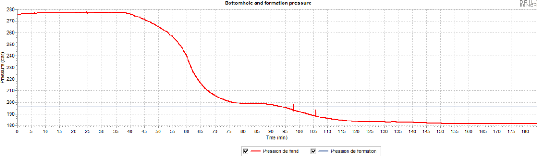
Figure 8.13 : Evolution BHP, cas injection par
parasite.
On constate un underbalance permanent au bout de 1h 30min et une
stabilisation au bout de 2h 30min dans la zone exigée (7%-9%).
Cette technique présente un avantage certain en termes
de temps gagné, mais quelques difficultés liées à
son installation.
- Précaution à suivre pendant la descente du
tubage raccordé au parasite, risques d'endommagement de ce dernier
pendant les connections.
- Besoins d'une tête de tubage spéciale pour
prendre en compte l'extension du parasite sur le tubage.
8.5 Injection par Drill Pipe
C'est une solution très intéressante, elle
présente de nombreux avantages :
- Ne nécessite pas de grandes modifications par rapport
aux puits conventionnels. - Moins d'équipements et personnel
nécessaire sur chantier.
- La quantité de gaz à envoyer pour
alléger la colonne est moindre car puisque le point d'injection se
trouve plus bas, et donc l'expansion du gaz à travers la colonne va
faire qu'elle s'allège plus.
Cependant elle présente un certain nombre de
problèmes :
- La pression de fond ne peut pas être
contrôlée avec précision en cours de forage, il est
donc nécessaire d'appliquer les paramètres
optimaux dès le début de la phase en underbalance.
- En puits horizontal, le gaz a tendance à se
séparer du liquide et à gagner la partie superieur du trou, ce
qui crée un drawdown plus élevé à la partie
superieur du trou, qui peut entrainer un effondrement du trou.
91
Chapitre8- Solutions et Propositions
Fenêtre opérationnelle.
Dans le but de choisir les paramètres d'injection
adéquats débit de gaz et débit de liquide), il est
nécessaire de construire une certaine limite qui impose un ratio entre
ces deux débits, et ce dans but d'éviter certains
problèmes. Les différents problèmes rencontrés sont
:
· Problème d'instabilité des parois
(Collapse).
· Maintien de la condition d'underbalance.
· Problème de nettoyage.
· Problème de cavage (washout) dû à
l'érosion des parois.
La zone à l'intérieur de ce diagramme
représente l'ensemble des combinaisons de débit de gaz et de
liquide qui évite ces 4 problèmes. La construction du diagramme
se fait comme suit :
Limite droite. Représente le
problème d'instabilité des parois, dans le cas de l'UBD on parle
plutôt de collapse. L'estimation de la pression de collapse dans le cas
du puits passe d'abord par la détermination des contraintes horizontales
et verticale (chapitre 4)
La contrainte verticale est déterminée par
l'équation (4.1), par intégration d'un log de densité d'un
puits voisin sur la hauteur TVD du puits ONIZ-40.
On trouve a = 876.09 bars au TD (3437m), soit 0.255
bar/m.
~~
o -v
Et par application de l'algorithme section-4.5 au puits ONIZ-40,
on trouve :
= 0.7148 et ° = 0.7035 Soit
crH = 626.43 bars et ah =
616.32 bars
o -v
La valeur de ah = 616.32 bars = 8936.77 psi donne une
très bonne approximation par rapport aux valeurs proposées par
(Koceir, 2000) qui était de 8450 psi résultat d'une étude
sur l'influence des contraintes sur la fracturation hydraulique (voir
références), elle nous donne une erreur de 5.76%. On admet donc
que les valeurs trouvée sont correctes.
Le calcul de la pression de collapse s'est fait en utilisant
le modèle de Mohr-Coulomb (équation 4.5 et 4.6) et les
équations (4.17) et (4.18), on trouve
1c ttapse = 160.011 bars ce qui correspond à
un drawdown de 18.36% par rapport à la pression de réservoir.
L'étape suivante est de faire une simulation avec
Drillbench et de prendre pour chaque débit de liquide le débit de
gaz qui correspond à cette pression. (Figure 8.14)
Limite gauche. Cette limite peut
être définie de deux manières, c'est soir l'ensemble des
débits de liquide et de gaz qui sont capables de maintenir un
underbalance, soit on impose un drawdown précis, par exemple 7%.
L'ensemble est déterminé directement par simulation avec
Drillbench pour différents débits. (Figure-8.14)
92
Chapitre8- Solutions et Propositions
Limite inférieure. C'est la
limite de nettoyage des parois, une élaboration plus précise de
cette courbe pourrai faire l'objet d'une étude très
interessante.
Elle définit comme la capacité à remonter
les cuttings du fluide de forage, elle est calculée suivant
l'énergie cinétique du fluide.
E = 0.5Ym
g
Vm étant la vitesse du mélange
liquide/gaz et Ym la masse volumique du mélange.
Des études montrent (Guo, 2002) qu'une énergie
cinétique minimum de 3 lbf-ft/ft3 suffi à transporter
les cuttings jusqu'en surface dans des conditions de puits normales.
Et pour aller dans le cas le plus défavorable, on prendre
en compte seulement la phase liquide, car la phase gazeuse crée une
turbulence qui va aider à remonter les cuttings.
Et donc par calcul simple, avec un diamètre du trou de
6» et un diamètre extérieur des tiges de 31/2,
cette énergie cinétique correspond à un débit de
liquide de 423 l/min.
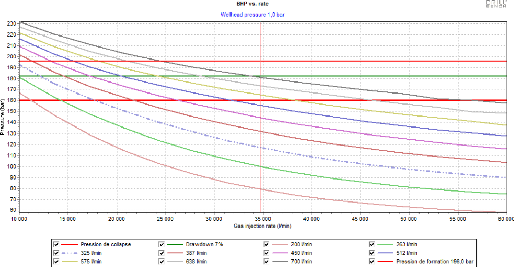
Figure 8.14 : Modélisation statique de la BHP et
illustration des pressions de collapse et de formation.
Limite supérieure. C'est la
limite de cavage par érosion des parois, il n'existe pas de
modèle pour modéliser le phénomène, les limites de
« washout » sont surtout basées sur l'expérience locale
de forage. Dans le cas du réservoir RaD2, qui est essentiellement
formé de quartzites, on considère que cette limite n'est pas
nécessaire à déterminer, les risques d'érosion
étant très faible.
93
Chapitre8- Solutions et Propositions
Construction du diagramme. Le diagramme
en prenant en compte les 4 limites présentées est illustré
dans la Figure 8.15, les deux lignes de balance et de 7% drawdown y sont
plotées.
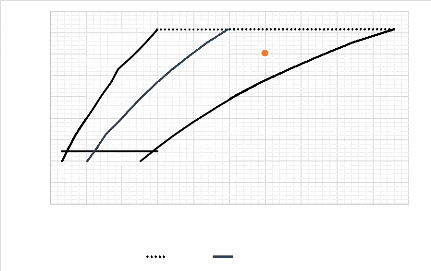
Débit de liquide l/min
450
400
750
700
650
600
550
500
350
300
10000 15000 20000 25000 30000 35000 40000 45000 50000 55000
60000
Washout 7% Drawdown
Débit de gaz l/min
Figure 8.15 : Diagramme
opérationnel.
Le point indiqué sur le diagramme correspond à
(650,40000) est un point opérationnel, la simulation en dynamique est
présentée sur la figure 8.16.
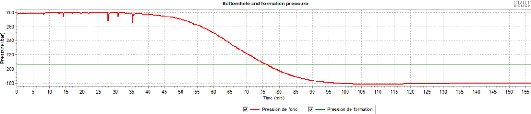
Figure 8.16 : BHP en fonction du temps pour injection
par tiges.
La pression se stabilise à 180.1 bar, ce qui correspond
à un drawdown de 8.11% ce qui est acceptable.
Cependant en puits horizontal, le gaz a tendance à
adopter un écoulement stratifié, dans ce cas il faut
également examiner le régime d'écoulement, le plus
appréciable étant le régime à bulle
dispersées ou régime Slug, il faut à tout prix
éviter le régime stratifié (SS et SW). Il
présenté sur les Figures 8.17 et 8.18 un rappel sur les
différents régimes d'écoulement et les diagrammes pour
puits horizontaux et presque horizontaux, ce dernier point est essentiel car en
forage on ne peut pas avoir une horizontalité parfaite.
94
Chapitre8- Solutions et Propositions
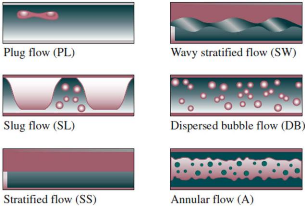
Figure 8.17 : Différents régimes
d'écoulement pour conduites horizontales (Falcone, 2009)
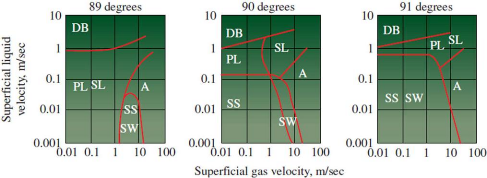
Figure 8.18 : Diagrammes d'écoulement pour
conduites horizontales (Falcone, 2009)
Vérification du régime
d'écoulement. On va vérifier le régime
d'écoulement pour le cas (650,40000), d'abord il faut calculer le
débit de gaz dans les conditions de fond, à cause de la
compression, ce dernier voit son débit diminuer en quelque sorte. Pour
cela on applique la loi des gaz réels (équation 1.2), l'indice 1
représente les conditions en surface et 2 représente les
conditions au fond.
On prend P1 = 200 psi bar et P2 =2886 psi, T1=158°F et
T2=242.6°F,
Le facteur de compressibilité est déterminé
en utilisant l'abaque de Standing et Katz (Tarek, 2010) Figure-9.20, on trouve
Z1=1 et Z2=1.05. (Données pour l'azote : Température critique 227
R, pression critique 493.1 psi, Tarek, 2010)
On trouve un débit de gaz de 4.43m3/min.
95
Chapitre8- Solutions et Propositions
On applique les équations (3.30) et (3.31) pour trouver
les vitesses superficielles du liquide et du gaz. En prenant une section
annulaire de 0.015322m2 et un diamètre de 6», le
diamètre hydraulique est de 0.128m et donc on a une section de
0.0128m2.
On trouve
*$! = 0.85./s et *$) = 5.76./s,
et ce sans prendre en compte le Holdup.
L'estimation du Holdup pour le cas présent est
présentée dans la Figure 8.19. On trouve un Holdup pour le
liquide de 53.53%.
En appliquant les équations (3.32) et (3.33), il en
résulte *! = 1.60./s et *) =
12.5./s
En mettant ces valeurs dans les diagrammes Figure 8.18, on
remarque qu'on est dans le régime Slug pour une inclinaison de 89°
et 90° et dans le régime en bouchons pour 91°.
Ces valeurs ne sont donc pas acceptables car elles occasionnent
une séparation entre le liquide et le gaz.
Il faut donc changer de paramètres. On prend un
deuxième point sur le diagramme 8.15 : (750,45000) et on refait les
calculs dans ce cas. Le Holdup dans ce cas est présenté dans la
Figure 9.19. Le Holdup est égal à 53.07% pour le liquide.
On trouve *! = 3.92./s et *) =
10.7./s.
Dans ce cas-ci, on entre dans le régime de bulles
dispersées pour 89° d'inclinaison. Et dans le régime Slug
pour 90° et 91°. Ce qui est acceptable.
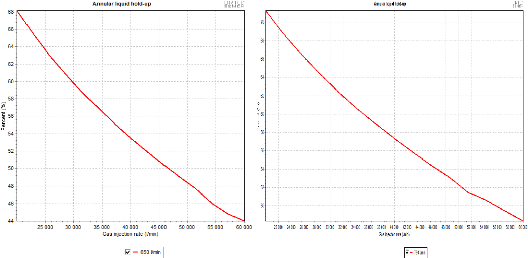
Figure 9.19 : Evolution du Holdup pour le liquide avec
650 et 700 l/min de débit.
96
Chapitre8- Solutions et Propositions
Conclusion. Une élaboration d'un
diagramme de référence pour le choix des paramètres
d'injection avec injection par tiges, en plus d'une vérification du
point choisi pour atteindre un régime de bulles dispersées,
pourrai se montrer comme un outil très intéressant pour
l'ingénieur spécialiste en UBD dans la conception et le suivi des
opérations.
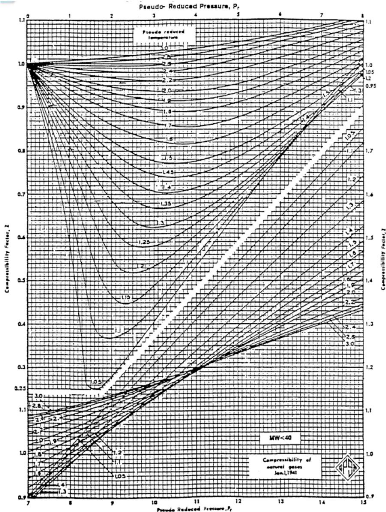
Figure 8.20 : Abaque de Standing Katz pour la
determination du facteur de compréssiblité pour le
gaz
(Tarek, 2012)
97
Conclusion
Le but premier de ce mémoire fut de mettre en
évidence l'effet d'accumulateur, qui est un problème
récurrent en Algérie, et d'exposer les phénomènes
physiques le régissant. Tout en proposant plusieurs solutions pour
limiter les oscillations de la pression de fond et mieux contrôler cette
dernière en UBD.
Toutefois, les solutions proposées présentent
une certaine lacune ; ils ne traitent que d'un point de vue pratique sans
prendre en compte le côté économique du problème. Ce
dernier point n'ayant pas été abordé par manque de
donnés en la matière.
Ce travail montre également l'importance d'une
simulation dynamique dans la planification des opérations en
underbalance. En comparaison avec la simulation en régime permanent qui
n'illustre pas les fluctuations des différents paramètres et donc
la réalité de la chose.
Afin d'entreprendre convenablement de remédier au
problème de l'effet d'accumulateur, il peut être
nécessaire, soit de jouer sur les paramètres influençants
l'écoulement de gaz à travers les orifices, ou bien alors adopter
une des solutions proposées au chapitre 8. On propose ce qui suit :
? Utilisation d'une phase liquide plus visqueuse. Les
opérations en underbalance n'empêchent pas l'ajout d'un produit
viscosifiant au brut pour atteindre une viscosité d'environ 30 à
50 cp. (la viscosité initale du brut étant de 2 cp)
? Mettre les points d'injection plus haut dans le Tie back, en
plus de l'incorporation d'un packer sous le niveau des point d'injection, ce
qui va limiter le volume du concentrique, et donc permettre un meilleur
contrôle de la BHP.
? L'incorporation d'une duse semi-automatique permettrait un
contrôle plus précis de la pression appliquée en surface et
donc la possibilité de manipuler depuis la surface le débit qui
sort des points d'injections au fond.
? L'installation d'un clapet anti-retour à la sortie
des points d'injection, ce qui limite le temps de rechargement du concentrique
et donc le temps entre deux bulles relâchées. Cependant, cette
option présente le risque de bouchage des clapets par les particules
solides de la boue. En plus du fait qu'une usure au niveau des clapets rend
cette option nettement moins interessante d'un côté pratique
quoique théoriquement elle semble la plus adaptée et la moins
contraignante.
98
? L'injection par parasite est un moyen efficace et radical de
mettre fin au problème, mais il faudrait s'interrogPer sur la
disponibilité de la technologie, en plus des contraintes liées
à son utilisation :
· Risque d'endommagement du parasite pendant sa descente
avec le tubage.
· Besoin d'une tête de tubage (casing hanger)
spéciale qui prend en compte la forme du parasite.
? Envisager l'injection duale comme solution au
problème, car la procédure ne demande pas des équipements
supplémentaires à ceux déjà présents sur
chantier. Elle requiert surtout une bonne coordination de l'équipe en
place et peut vraiment se présenter comme une solution rapide au
problème rencontré.
? Pour ce qui est de la dernière proposition, qui est
l'injection par l'intérieur des tiges, la fenêtre
opérationnelle est un outil très intéressant pour la
conception des paramètres d'injection. Cependant, la fenêtre
modélisée dans ce mémoire n'est pas complete, il reste
à ajouter les limites de performance du moteur de fond. En y ajoutant
également les considérations liées aux vibrations au
niveau de l'outil induites par l'intermittence de l'écoulement.
? Installation d'une DDV dans le puits, permet de minimiser
l'endommagement de la formation par rapport au Mud Cap. En plus cela
représente un gain de temps dans les manoeuvres, car on élimine
le temps de déplacer le brut par une boue lourde.
? Dans le cas d'un long drain horizontal, les performances de
nettoyage du trou sont réduites, il est alors nécessaire de
pomper un bouchon dit HighVis, très visqueux, qui va nettoyer le trou et
éviter les problèmes lors de la remonté de la
garniture.
96
Références
1. Aadnoy, B., Cooper, I., Miska, S., Mitchell, R., Payne, M.
(2009). «Advanced Drilling and Well Technology». SPE,
Richardson, Texas, USA.
2. Abdullah, H., Singh, S (2010). `'Laboratory evaluation of
five quartzites''. Présenté à l'Indian Geotechnical
Conference, IIT Bombay
3. Aiyeru, S. G (2014).''Inversion Method to determine in-situ
stresses''. Université de Stavanger, Norvège.
4. Bennion, B., Thomas, B., Bietz, R., Bennion, D
(1996).''Underbalanced Drilling, Praises and Perils''. SPE 35242,
présenté à la conférence sur la
récupération dans le bassin permien, Midland, Texas, USA.
5. BLADE, `'A Course in Advanced Underbalanced Drilling''
Version 1.0
6. Brill, J. P., Beggs, H. D (1991). `'Two phase flow in
pipes'', Université de Tulsa, USA
7. Eck-Olsen, J. (2003). `'Underbalanced Drilling
Orientation.''. IADC RIGPASS pour Statoil.
8. Falcone, G., Hewitt, G. F., Alimonti, C (2009).''Multiphase
Flow Metering''. Editions Elsevier
9. Guo, B., Ghalambor, A (2002).''An innovation in designing
Underbalanced Drilling Flow rates : A Gas-liquid rate window approach''. SPE
77237, présenté à l'IADC/SPE Asia Pacific Drilling
Technology, Jakarta, Indonésie
10. Koceir, M., Tiab, U (2000).''Influence of Stress and
Lithology on Hydraulic Fracturing in Hassi Messaoud Reservoir, Algeria''. SPE
62608, présenté à la SPE/AAPG conférence
régionale ouest, Long Beach, Californie, USA
11. Leirkjaer, R. S (2014). `'Simulating Underbalanced
Drilling''. Université de Stavanger, Norvège
12. Mitchell, R., Miska, S (2011).''Fundamentals of Drilling
Engineering''. SPE, USA
13. Moore, D. D., Bencheikh, A., Chopty, J. R
(2004).''Drilling Underbalanced in Hassi Messaoud''. SPE 91519,
présenté à la conférence IADC/SPE sur les
technologies en UBD, Houston, Texas, USA
14. Myktiw, C. G., Davidson, I. A., Frink, P. J
(2003).»Design and operational considerations to maintain underbalanced
conditions with concentric casing injection». SPE 81631,
présenté à l'IADC/SPE conférence sur le forage
Underbalance, Houston, Texas, USA
15. Raen, J (2012). `'Managing Pressure during underbalanced
drilling». Université de Stavanger, Norvège
16. Rommetveit, R., et al. (1999). `'Dynamic Underbalanced
Effects are predicted by Design Model`'. SPE 56920, présenté
à la conférence européenne sur l'Offshore, Aberdeen,
Ecosse.
17. Rehm, B., Haghshenas, A., Paknejad, A., Al-Yami, A., Hughes,
J., Schubert, J (2012).»Underbalanced Drilling : Limits and Extrems».
IADC, Houston, Texas, USA
18. Rhyming, I (2009). `'Dynamique des fluides». Presse
polytechnique et universitaire Romande, université de Lausanne,
Suisse
19. Tarek, A (2012). `'Reservoir engineering handbook».
4ème éditiion, Editions Elsevier, Oxford,
Angleterre.
97
20. Weatherford. `'Downhole Isolation Valve».
Annexes
Données de Survey du puits ONIZ-40
MD (m)
|
Inclinaison
(°)
|
Azimuth
(°)
|
TVD (m)
|
Offset Nord
(m)
|
Offset sud (m)
|
Section verticale
(m)
|
2770
|
0,58
|
133,67
|
2769,87
|
-15,95
|
10,05
|
-18,52
|
2780
|
0,43
|
143,26
|
2779,87
|
-16,01
|
10,11
|
-18,6
|
2781,43
|
0,41
|
145,2
|
2781,3
|
-16,02
|
10,12
|
-18,61
|
2790
|
0,25
|
279,29
|
2789,87
|
-16,05
|
10,12
|
-18,63
|
2793,56
|
0,49
|
293,75
|
2793,43
|
-16,04
|
10,1
|
-18,61
|
2800
|
0,96
|
297,73
|
2799,87
|
-16
|
10,02
|
-18,53
|
2808,39
|
1,57
|
299,35
|
2808,25
|
-15,91
|
9,86
|
-18,36
|
2810
|
1,7
|
300,1
|
2809,86
|
-15,89
|
9,82
|
-18,31
|
2820
|
2,53
|
303
|
2819,86
|
-15,7
|
9,51
|
-17,96
|
2827,07
|
3,11
|
304,12
|
2826,92
|
-15,5
|
9,22
|
-17,62
|
2830
|
3,32
|
304,67
|
2829,84
|
-15,41
|
9,08
|
-17,46
|
2838,35
|
3,93
|
305,91
|
2838,18
|
-15,1
|
8,65
|
-16,94
|
2840
|
4,03
|
305,99
|
2839,82
|
-15,04
|
8,56
|
-16,83
|
2850
|
4,65
|
306,38
|
2849,79
|
-14,59
|
7,95
|
-16,09
|
2853,4
|
4,86
|
306,49
|
2853,18
|
-14,42
|
7,72
|
-15,81
|
2860
|
5,03
|
309,55
|
2859,76
|
-14,07
|
7,27
|
-15,25
|
2867,47
|
5,23
|
312,76
|
2867,2
|
-13,63
|
6,77
|
-14,58
|
2870
|
5,23
|
313,05
|
2869,72
|
-13,48
|
6,6
|
-14,35
|
2879,2
|
5,25
|
314,09
|
2878,88
|
-12,9
|
5,99
|
-13,51
|
2880
|
5,22
|
314,36
|
2879,67
|
-12,85
|
5,94
|
-13,44
|
2890
|
4,88
|
317,98
|
2889,64
|
-12,21
|
5,33
|
-12,56
|
2895,28
|
4,71
|
320,1
|
2894,9
|
-11,88
|
5,04
|
-12,12
|
2900
|
4,46
|
320,14
|
2899,6
|
-11,59
|
4,8
|
-11,74
|
2910
|
3,93
|
320,23
|
2909,58
|
-11,03
|
4,33
|
-11,01
|
2910,5
|
3,9
|
320,24
|
2910,07
|
-11
|
4,31
|
-10,98
|
2920
|
3,68
|
321,02
|
2919,55
|
-10,52
|
3,91
|
-10,35
|
2924,49
|
3,58
|
321,42
|
2924,03
|
-10,29
|
3,73
|
-10,07
|
2930
|
3,36
|
320,43
|
2929,53
|
-10,04
|
3,52
|
-9,74
|
2939,1
|
2,99
|
318,47
|
2938,62
|
-9,65
|
3,2
|
-9,23
|
2940
|
2,99
|
318,53
|
2939,52
|
-9,62
|
3,17
|
-9,19
|
2950
|
2,95
|
319,19
|
2949,51
|
-9,23
|
2,82
|
-8,67
|
2953,63
|
2,94
|
319,44
|
2953,13
|
-9,09
|
2,7
|
-8,48
|
2960
|
3
|
319,83
|
2959,49
|
-8,83
|
2,49
|
-8,15
|
2966,32
|
3,06
|
320,2
|
2965,8
|
-8,58
|
2,27
|
-7,82
|
2970
|
3,15
|
319,14
|
2969,48
|
-8,43
|
2,15
|
-7,62
|
2978,36
|
3,36
|
316,95
|
2977,82
|
-8,07
|
1,83
|
-7,14
|
2980
|
3,38
|
317
|
2979,46
|
-8
|
1,76
|
-7,05
|
2990
|
3,47
|
317,32
|
2989,44
|
-7,57
|
1,36
|
-6,45
|
2995,47
|
3,52
|
317,49
|
2994,9
|
-7,32
|
1,13
|
-6,12
|
3000
|
3,82
|
317,88
|
2999,42
|
-7,11
|
0,94
|
-5,83
|
3010
|
4,49
|
318,55
|
3009,4
|
-6,56
|
0,45
|
-5,1
|
3010,42
|
4,52
|
318,57
|
3009,82
|
-6,54
|
0,43
|
-5,07
|
3020
|
5,17
|
318,78
|
3019,36
|
-5,93
|
-0,1
|
-4,26
|
3023,48
|
5,4
|
318,84
|
3022,83
|
-5,69
|
-0,31
|
-3,94
|
3030
|
5,86
|
318,7
|
3029,32
|
-5,21
|
-0,74
|
-3,3
|
3039,61
|
6,55
|
318,54
|
3038,87
|
-4,43
|
-1,42
|
-2,26
|
3040
|
6,58
|
318,59
|
3039,26
|
-4,4
|
-1,45
|
-2,22
|
3050
|
7,23
|
319,82
|
3049,19
|
-3,49
|
-2,24
|
-1,02
|
3053,47
|
7,46
|
320,2
|
3052,63
|
-3,15
|
-2,52
|
-0,57
|
3060
|
7,81
|
320,83
|
3059,1
|
-2,48
|
-3,07
|
0,29
|
3067,48
|
8,22
|
321,48
|
3066,51
|
-1,66
|
-3,73
|
1,33
|
3070
|
8,39
|
321,2
|
3069
|
-1,38
|
-3,96
|
1,69
|
3080
|
9,05
|
320,21
|
3078,88
|
-0,21
|
-4,92
|
3,21
|
3082,01
|
9,18
|
320,03
|
3080,87
|
0,04
|
-5,12
|
3,52
|
3090
|
9,78
|
319,87
|
3088,75
|
1,04
|
-5,97
|
4,84
|
3097,05
|
10,31
|
319,75
|
3095,69
|
1,98
|
-6,76
|
6,07
|
3100
|
10,46
|
320,03
|
3098,59
|
2,39
|
-7,1
|
6,6
|
3110
|
10,99
|
320,93
|
3108,42
|
3,83
|
-8,29
|
8,46
|
3111,55
|
11,07
|
321,06
|
3109,94
|
4,06
|
-8,47
|
8,75
|
3120
|
11,84
|
319,64
|
3118,22
|
5,35
|
-9,54
|
10,43
|
3125,42
|
12,33
|
318,82
|
3123,52
|
6,21
|
-10,29
|
11,56
|
3130
|
12,72
|
318,53
|
3127,99
|
6,95
|
-10,94
|
12,55
|
3138,61
|
13,46
|
318,02
|
3136,38
|
8,41
|
-12,24
|
14,5
|
3140
|
13,59
|
318
|
3137,73
|
8,65
|
-12,46
|
14,83
|
3150
|
14,55
|
317,85
|
3147,43
|
10,45
|
-14,09
|
17,26
|
3154,51
|
14,98
|
317,79
|
3151,79
|
11,31
|
-14,86
|
18,41
|
3160
|
15,52
|
317,64
|
3157,09
|
12,37
|
-15,83
|
19,85
|
3168,39
|
16,35
|
317,44
|
3165,15
|
14,07
|
-17,38
|
22,15
|
3170
|
16,49
|
317,41
|
3166,7
|
14,41
|
-17,69
|
22,61
|
3180
|
17,4
|
317,23
|
3176,26
|
16,55
|
-19,67
|
25,52
|
3182,72
|
17,64
|
317,19
|
3178,86
|
17,15
|
-20,22
|
26,34
|
3190
|
18,04
|
317,44
|
3185,79
|
18,79
|
-21,74
|
28,57
|
3196,49
|
18,4
|
317,65
|
3191,95
|
20,29
|
-23,11
|
30,6
|
3200
|
18,59
|
317,79
|
3195,28
|
21,11
|
-23,86
|
31,72
|
3210
|
19,12
|
318,19
|
3204,74
|
23,51
|
-26,02
|
34,95
|
3211,61
|
19,21
|
318,25
|
3206,27
|
23,91
|
-26,37
|
35,47
|
3220
|
19,82
|
317,99
|
3214,17
|
26
|
-28,24
|
38,28
|
3225,13
|
20,19
|
317,84
|
3218,99
|
27,3
|
-29,42
|
40,03
|
3230
|
20,55
|
317,94
|
3223,56
|
28,56
|
-30,55
|
41,73
|
3240
|
21,3
|
318,15
|
3232,9
|
31,21
|
-32,94
|
45,3
|
3240,65
|
21,35
|
318,16
|
3233,51
|
31,39
|
-33,1
|
45,53
|
3250
|
22,27
|
318,03
|
3242,19
|
33,97
|
-35,42
|
49,01
|
3256,09
|
22,87
|
317,95
|
3247,81
|
35,71
|
-36,98
|
51,34
|
3260
|
23,24
|
317,98
|
3251,41
|
36,85
|
-38,01
|
52,87
|
3269,68
|
24,14
|
318,05
|
3260,27
|
39,74
|
-40,61
|
56,76
|
3270
|
24,16
|
318,05
|
3260,56
|
39,84
|
-40,7
|
56,89
|
3280
|
24,64
|
318,02
|
3269,67
|
42,91
|
-43,46
|
61,02
|
3283,81
|
24,83
|
318,01
|
3273,13
|
44,09
|
-44,53
|
62,62
|
3290
|
25,69
|
318,03
|
3278,73
|
46,06
|
-46,29
|
65,26
|
3297,45
|
26,73
|
318,06
|
3285,41
|
48,5
|
-48,49
|
68,55
|
3300
|
27,07
|
318,12
|
3287,69
|
49,36
|
-49,26
|
69,7
|
3310
|
28,42
|
318,36
|
3296,54
|
52,83
|
-52,36
|
74,36
|
3311,35
|
28,6
|
318,39
|
3297,72
|
53,32
|
-52,79
|
75
|
3320
|
29,54
|
318,59
|
3305,28
|
56,46
|
-55,58
|
79,2
|
3330
|
30,63
|
318,82
|
3313,94
|
60,23
|
-58,89
|
84,21
|
3331,63
|
30,81
|
318,85
|
3315,34
|
60,86
|
-59,43
|
85,05
|
3340
|
33,23
|
318,62
|
3322,43
|
64,19
|
-62,36
|
89,48
|
3349,76
|
36,05
|
318,38
|
3330,46
|
68,35
|
-66,04
|
95,03
|
3350
|
36,11
|
318,35
|
3330,66
|
68,45
|
-66,13
|
95,17
|
3360
|
38,73
|
317,24
|
3338,6
|
72,95
|
-70,21
|
101,24
|
3364,75
|
39,97
|
316,75
|
3342,27
|
75,15
|
-72,27
|
104,25
|
3370
|
41,35
|
317,19
|
3346,25
|
77,65
|
-74,6
|
107,67
|
3380
|
43,97
|
317,96
|
3353,61
|
82,66
|
-79,17
|
114,45
|
3384,29
|
45,1
|
318,27
|
3356,66
|
84,9
|
-81,18
|
117,46
|
3390
|
46,69
|
318,7
|
3360,64
|
87,97
|
-83,9
|
121,56
|
3395,48
|
48,21
|
319,09
|
3364,34
|
91,01
|
-86,55
|
125,59
|
3400
|
49,38
|
319,07
|
3367,32
|
93,58
|
-88,78
|
128,99
|
3409,79
|
51,91
|
319,02
|
3373,53
|
99,29
|
-93,74
|
136,55
|
3410
|
51,94
|
319,01
|
3373,66
|
99,42
|
-93,85
|
136,72
|
3420
|
53,14
|
318,75
|
3379,74
|
105,4
|
-99,07
|
144,65
|
3423,02
|
53,51
|
318,67
|
3381,55
|
107,22
|
-100,67
|
147,07
|
3430
|
55,1
|
318,01
|
3385,62
|
111,45
|
-104,44
|
152,74
|
3437,97
|
56,93
|
317,29
|
3390,07
|
116,34
|
-108,89
|
159,35
|
3440
|
57,25
|
317,25
|
3391,17
|
117,59
|
-110,05
|
161,05
|
3450
|
58,83
|
317,07
|
3396,47
|
123,81
|
-115,81
|
169,53
|
3451,3
|
59,03
|
317,05
|
3397,14
|
124,62
|
-116,57
|
170,65
|
3460
|
59,96
|
317,1
|
3401,56
|
130,11
|
-121,68
|
178,14
|
3466,53
|
60,66
|
317,13
|
3404,79
|
134,27
|
-125,54
|
183,82
|
3470
|
60,7
|
317,09
|
3406,49
|
136,49
|
-127,6
|
186,84
|
3480
|
60,83
|
316,99
|
3411,37
|
142,87
|
-133,54
|
195,57
|
3481,82
|
60,85
|
316,97
|
3412,26
|
144,03
|
-134,63
|
197,16
|
3490
|
62,66
|
316,61
|
3416,13
|
149,29
|
-139,56
|
204,36
|
3497,76
|
64,38
|
316,27
|
3419,59
|
154,32
|
-144,35
|
211,31
|
3500
|
64,52
|
316,46
|
3420,56
|
155,78
|
-145,74
|
213,33
|
3510
|
65,17
|
317,3
|
3424,81
|
162,39
|
-151,93
|
222,38
|
3512
|
65,3
|
317,47
|
3425,64
|
163,73
|
-153,16
|
224,2
|
3520
|
70,32
|
317,76
|
3428,67
|
169,2
|
-158,15
|
231,6
|
3530
|
76,59
|
318,11
|
3431,51
|
176,31
|
-164,57
|
241,18
|
3540
|
82,86
|
318,43
|
3433,3
|
183,65
|
-171,11
|
251,01
|
3550
|
89,13
|
318,75
|
3433,99
|
191,13
|
-177,71
|
260,98
|
3550,59
|
89,5
|
318,77
|
3434
|
191,57
|
-178,1
|
261,56
|
3560
|
89,5
|
318,75
|
3434,08
|
198,65
|
-184,3
|
270,97
|
3570
|
89,5
|
318,72
|
3434,17
|
206,16
|
-190,9
|
280,97
|
3580
|
89,5
|
318,7
|
3434,26
|
213,68
|
-197,49
|
290,96
|
3590
|
89,51
|
318,68
|
3434,34
|
221,19
|
-204,1
|
300,96
|
3600
|
89,51
|
318,65
|
3434,43
|
228,7
|
-210,7
|
310,95
|
3610
|
89,51
|
318,63
|
3434,51
|
236,2
|
-217,31
|
320,95
|
3620
|
89,51
|
318,6
|
3434,6
|
243,7
|
-223,92
|
330,94
|
3630
|
89,51
|
318,58
|
3434,68
|
251,2
|
-230,53
|
340,94
|
3640
|
89,51
|
318,56
|
3434,77
|
258,7
|
-237,15
|
350,93
|
3650
|
89,52
|
318,53
|
3434,85
|
266,2
|
-243,77
|
360,93
|
3660
|
89,52
|
318,51
|
3434,94
|
273,69
|
-250,39
|
370,92
|
3670
|
89,52
|
318,48
|
3435,02
|
281,18
|
-257,02
|
380,92
|
3680
|
89,52
|
318,46
|
3435,11
|
288,66
|
-263,65
|
390,92
|
3690
|
89,52
|
318,44
|
3435,19
|
296,14
|
-270,28
|
400,91
|
3700
|
89,52
|
318,41
|
3435,27
|
303,63
|
-276,92
|
410,91
|
3710
|
89,53
|
318,39
|
3435,36
|
311,1
|
-283,56
|
420,9
|
3720
|
89,53
|
318,36
|
3435,44
|
318,58
|
-290,2
|
430,9
|
3730
|
89,53
|
318,34
|
3435,52
|
326,05
|
-296,85
|
440,9
|
3740
|
89,53
|
318,32
|
3435,6
|
333,52
|
-303,49
|
450,89
|
3750
|
89,53
|
318,29
|
3435,68
|
340,99
|
-310,15
|
460,89
|
3760
|
89,53
|
318,27
|
3435,77
|
348,45
|
-316,8
|
470,89
|
3770
|
89,54
|
318,24
|
3435,85
|
355,91
|
-323,46
|
480,88
|
3780
|
89,54
|
318,22
|
3435,93
|
363,37
|
-330,12
|
490,88
|
3790
|
89,54
|
318,2
|
3436,01
|
370,82
|
-336,78
|
500,88
|
3800
|
89,54
|
318,17
|
3436,09
|
378,28
|
-343,45
|
510,88
|
3810
|
89,54
|
318,15
|
3436,17
|
385,73
|
-350,12
|
520,87
|
3820
|
89,54
|
318,12
|
3436,25
|
393,17
|
-356,79
|
530,87
|
3830
|
89,55
|
318,1
|
3436,33
|
400,62
|
-363,47
|
540,87
|
3840
|
89,55
|
318,08
|
3436,41
|
408,06
|
-370,15
|
550,87
|
3850
|
89,55
|
318,05
|
3436,49
|
415,5
|
-376,83
|
560,86
|
3860
|
89,55
|
318,03
|
3436,56
|
422,93
|
-383,52
|
570,86
|
3870
|
89,55
|
318
|
3436,64
|
430,37
|
-390,21
|
580,86
|
3880
|
89,55
|
317,98
|
3436,72
|
437,8
|
-396,9
|
590,86
|
3890
|
89,56
|
317,95
|
3436,8
|
445,22
|
-403,6
|
600,85
|
3900
|
89,56
|
317,93
|
3436,88
|
452,65
|
-410,3
|
610,85
|
3910
|
89,56
|
317,91
|
3436,95
|
460,07
|
-417
|
620,85
|
3920
|
89,56
|
317,88
|
3437,03
|
467,49
|
-423,7
|
630,85
|
3930
|
89,56
|
317,86
|
3437,11
|
474,9
|
-430,41
|
640,85
|
3940
|
89,56
|
317,83
|
3437,18
|
482,32
|
-437,12
|
650,85
|
3950
|
89,56
|
317,81
|
3437,26
|
489,73
|
-443,83
|
660,84
|
3960
|
89,57
|
317,79
|
3437,34
|
497,14
|
-450,55
|
670,84
|
3970
|
89,57
|
317,76
|
3437,41
|
504,54
|
-457,27
|
680,84
|
3980
|
89,57
|
317,74
|
3437,49
|
511,94
|
-464
|
690,84
|
3990
|
89,57
|
317,71
|
3437,56
|
519,34
|
-470,72
|
700,84
|
4000
|
89,57
|
317,69
|
3437,64
|
526,74
|
-477,45
|
710,84
|
4010
|
89,57
|
317,67
|
3437,71
|
534,13
|
-484,18
|
720,84
|
4020
|
89,58
|
317,64
|
3437,78
|
541,52
|
-490,92
|
730,83
|
|
|