République Gabonaise
Union - Travail - Justice
Ministère de l'Enseignement Supérieur
Ministère des Mines, du Pétrole
et de la Recherche Scientifique et des hydrocarbures
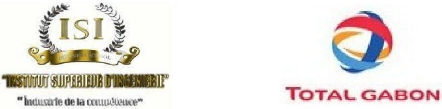
Année académique 2014 - 2015
MEMOIRE EN VUE DE L'OBTENTION
DU DIPLÔME DE LICENCE PROFESSIONNELLE EN EXPLOITATION
PÉTROLIÈRE
OPTIMISATION D'UN PROCÉDÉ DE
DÉSHYDRATATION DE GAZ NATUREL
Présenté par :
Nicolas SAULET LOMBE
II
INSTITUT SUPERIEUR D'INGENIERIE
Mémoire de fin de cycle sur le thème :
OPTIMISATION D'UN PROCÉDÉ DE
DÉSHYDRATATION DE GAZ NATUREL
Dans le cadre de la validation de la formation de :
Bachelor Production
Pétrolière
Cas du site de production pétrolière
: Torpille Marine - Total Gabon
Réalisé par :
Nicolas SAULET LOMBE
Le lundi 05 octobre 2015
III
IV
REMERCIEMENTS
" Cette formation a nécessité tout au long
de sa durée l'aide et le soutien de plusieurs personnes auxquelles il me
semble opportun de témoigner toute ma reconnaissance.
Je tiens, de ce fait, à remercier dans un premier
temps, toute l'équipe pédagogique de l'Institut Supérieur
d'Ingénierie (ISI), et les différents intervenants professionnels
de la formation - notamment Messieurs Honoré GNANGA, Neron NGANDZA,
Charles MISSO, Jean-Pierre MBOUMBA SANGHANY, David PONO RAFEMO, etc... - pour
avoir assurés la partie théorique de celle-ci. Messieurs, votre
disponibilité et vos conseils m'ont vraiment permis de progresser sans
cesse et d'orienter ma curiosité technique.
Je poursuivrai en remerciant également
l'encadrement administratif : Mesdames Vick MOUKETOU, Armelle MOUBAGHOU,
Lidvine DONGO, Messieurs Cyriaque ONDO ASSOUMOU, Béranger NZENGUE, qui
ont sus chacun à leur niveau, créer un cadre propice à mon
apprentissage.
D'autre part, je tiens à remercier tout
particulièrement l'entreprise Total Gabon, qui a su m'offrir un
environnement fonctionnel pour appliquer mes connaissances. Je citerai entre
autres Messieurs Alexis OYEMBO, Urphée LOUEMBET, Boris ANGUILE, Armand
BIDJOGO, Marc MBINGT MOCTAR, Paul NDONG EDOU, etc... Il m'est de ce fait
important d'exprimer toute ma gratitude à l'ensemble de leur personnel
pour leur accueil sympathique, leur coopération professionnelle; mais
surtout l'expérience enrichissante et pleine d'intérêt
qu'ils m'ont fait vivre durant ces mois. C'est grâce aux missions que
l'on m'a confiées que j'ai su orienté mon domaine de
connaissances et de compétences qui me sera, à n'en point douter,
utile dans ma vie professionnelle future.
Merci Mesdames et Messieurs pour m'avoir
intégré rapidement au sein de l'entreprise et m'avoir
accordé toute votre confiance et consacré tout ce temps tout au
long de cette période, sachant répondre à toutes mes
interrogations. Ainsi que tout ceux qui, même sans être
mentionnés ici, ont participé de près comme de loin
à l'accomplissement de cet ouvrage.
Je ne terminerai pas tout ceci sans adresser un regard
particulier à ma famille qui a su me témoigner tout le soutien
moral inconditionnel et la motivation nécessaires pour accomplir cet
ouvrage. "
Nicolas SAULET
V
« Je dédie ce modeste ouvrage à mon petit
ange XAVIER SAULET Léa Divine »
VI
AVANT - PROPOS
L'Institut Supérieur d'Ingénierie (ISI), dont le
pôle scientifique a été délocalisé à
Port-Gentil au Gabon, forme des ingénieurs dans différents
domaines techniques tels que l'exploration et la production
pétrolière.
L'institut est reconnu d'utilité publique sur le
territoire gabonais depuis novembre 2012 sous l'arrêté
n°00646/MENESTFPCJS relatif aux prestations de service d'enseignement de
formation et de recherche par établissement privé d'enseignement
supérieur.
Le présent document est un mémoire de fin de
cycle. Il est rédigé en vue de l'obtention du diplôme de
licence professionnelle dans la discipline d'ingénierie
pétrolière. Il est le fruit d'une étude de trois mois
effectuée au sein du site d'exploitation pétrolière
offshore de Torpille de l'entreprise Total Gabon. Il vise ainsi l'optimisation
du procédé de traitement de gaz naturel du site de Torpille
Marine de l'entreprise Total Gabon.
La méthodologie envisagée est basée sur
le modèle d'évaluation des procédés des bureaux
d'études. Une modélisation à partir de différents
modèles thermodynamiques d'un simulateur industriel sert de
référence au projet.
L'opérabilité et la sécurité de
l'unité constituent les principaux axes de réflexion retenus.
Cependant, de manière à rester succinct, la maintenabilité
du procédé - point crucial de toute amélioration de
procédés industriels - n'est pas abordée dans le
présent compte rendu.
Ce mémoire ne prétend pas traiter de
manière exhaustive tous les axes de réflexion, mais pourrait
servir de support à des études plus spécifiques.
VII
RÉSUMÉ
Le gaz naturel est un combustible fossile composé d'un
mélange d'hydrocarbures, présent naturellement dans des roches
poreuses, sous forme gazeuse. À sa sortie des puits, il n'est pas
directement utilisable avant qu'il ne soit traité et
débarrassé de ses constituants indésirables. Le traitement
du gaz naturel consiste à séparer au moins partiellement certains
des constituants présents à la sortie des puits tels que l'eau,
les gaz acides et les hydrocarbures lourds.
Les hydrates - cristaux solides qui se forment lorsque les
molécules de gaz se trouvent en présence d'eau dans les
conditions de pressions et de températures les plus usuelles en
production - constituent le problème majeur dans la production et le
transport du gaz naturel. Le rôle essentiel de l'unité de
déshydratation de gaz du site de Torpille est de séparer la
partie liquide (condensats + eau) de la partie gazeuse (gaz humide).
L'objectif principal de ce travail, est de fournir des
propositions d'optimisation du procédé existant de
déshydratation de gaz naturel du site de Torpille en se basant sur le
simulateur Invensys PRO/II®. Le but ici, étant de fiabiliser les
installations de traitement en renforçant leur sécurité et
leur opérabilité. La finalité du projet est de revoir la
compression de gaz HP du site, pour en faire le « hub » de la
compression de gaz offshore. Toutefois, dans un contexte de « cash-flow
» tendu pour l'entreprise Total Gabon, les travaux sont à
prévoir selon un objectif de CAPEX minimum.
Les simulateurs de procédés utilisés
classiquement dans l'industrie, peuvent être considérés
comme des modèles de connaissance. Ils sont basés sur la
résolution de bilans de masse et d'énergie, des équations
d'équilibres thermodynamiques, etc... ; Et sont à même de
fournir l'information de base pour la conception. Ils sont principalement
utilisés pour la conception de nouveaux procédés
(dimensionnement d'appareil, analyse du fonctionnement pour différentes
conditions opératoires, optimisation), pour l'optimisation de
procédés existants et l'évaluation de changements
effectués sur les conditions opératoires.
VIII
SIGLES & ABRÉVIATIONS
· AGM : Anguille
Marine
· BDM : Baudroie
Marine
· BDNM : Baudroie Nord
Marine
· BDV : Blow Down
Valve
· BSM : Baliste Marine
· BSW : Basic Sediment
Water
· CA : Colonne
d'Absorption
· DDM : Demande De
Modification
· DG / DI : Détection
Gaz / Détection
Incendie
· DS : Drum Strainer
· ESD / SD : Emergency
Shut Down / Shut
Down
· ESP : Electric
Submersible Pump
· FCW : Full Control
of Well
· GIM : Girelle Marine
· GRM : Grondin Marine
· GTI : Grands Travaux
d'Intégrité
· HP : Haute
Pression
· HYM : Hylia Marine
· LCV / LDCV : Level
Control Valve / Level
Differential Control
Valve
· MAP : Manque À
Produire
· PAM : Pageau Marine
· PC / PCI / PCS : Pouvoir
Calorifique / Pouvoir
Calorifique Inférieur /
Pouvoir Calorifique
Supérieur
· PCH : Pressure
Casing Head (pression en tête du
cuvelage du puits)
· PFC : Plate-Forme
Centrale
· PFD : Process
Flow Diagram
· PH : Potentiel
Hydrogène
· PID : Piping &
Instrumentation Diagram
· Qgl : Débit d'injection
gas-lift
· QHA : Débit de production d'huile
anhydre
· QHH : Débit de production d'huile
hydratée
· SERTERE :
Société d'Études et de
Réalisations Techniques pour
l'Exploitation des Ressources
Énergétiques
· SPAEF : Société des
Pétroles de l'Afrique
Équatoriale Française
· SNCC : Système
Numérique de Conduite
Centralisée
· TAG : Turbine À
Gaz
· TEG :
TriÉthylène-Glycol
· TNEM : Torpille
Nord-Est Marine
· TRM : Torpille
Marine
· TXT : Texsteam : pompe pneumatique
fabriquée par ladite société
· VNM : Vanneau Marine
IX
TABLE DES ILLUSTRATIONS
I - LISTE DES FIGURES
Figure 1.1 : Courbe de formation d'hydrates 13
Figure 1.2 : Domaine de fonctionnement de l'ouvrage 14
Figure 2.1 : Plan topographique du site de Torpille 19
Figure 2.2 : Hiérarchie organisationnelle du site TRM
23
Figure 2.3 : PFD colonne de déshydratation gaz ..
25
Figure 2.4 : Schéma de principe de la colonne de
déshydratation 26
Figure 2.5 : PFD flash tank glycol DS504 27
Figure 2.6 : Schéma de principe du flash tank DS 504
28
Figure 2.7 : PID unité SERTERE UB406 .... 30
Figure 2.8 : Logigramme de sécurité de
l'unité SERTERE 33
Figure 3.1 : Interface graphique du simulateur PRO/II®
35
Figure 3.2 : Procédure de simulation PRO/II®
39
Figure 3.3 : Flowsheet unité SERTERE 40
Figure 3.4 : Unités de mesure unité SERTERE
40
Figure 3.5 : Définition des unités de mesure
41
Figure 3.6 : Sélection des composants du flux
traité 41
Figure 3.7 : Complément des flux de simulation . 42
Figure 3.8 : Propriétés spécifiques du
TEG 42
Figure 3.9 : Modèle thermodynamique de simulation
43
Figure 3.10 : Exécution de la simulation 43
Figure 3.11 : Schéma d'optimisation unité
SERTERE 50
Figure 3.12 : Grafcet de démarrage unité SERTERE
. 51
Figure 3.13 : Épingle électrique BGHE 4301
53
II - LISTE DES PHOTOGRAPHIES
Photo 2.1 : Vue aérienne du complexe central du site
TRM 17
Photo 3.1 : Vue de profil unité SERTERE 52
III - LISTE DES TABLEAUX
Tableau 1.1 : Statut des champs du secteur Torpille 11
Tableau 2.1 : Plates-formes & puits du site TRM en 2015
18
Tableau 2.2 : Chiffres de production du site de TRM en 2005
21
Tableau 2.3 : Fonctionnement des organes de contrôle et
de régulation 31
Tableau 3.1 : Conditions opératoires actuelles
unité SERTERE 44
Tableau 3.2 : Résultats des tests effectués sur
l'unité de déshydratation .... 47
Tableau 3.3 : Composition des gaz associés TRM &
AGM 48
Tableau 3.4 : Upgrade de l'unité de
déshydratation : estimation des « manhours » .... 46
Tableau 3.5 : Upgrade de l'unité de
déshydratation : estimation des coûts ..... 46
X
SOMMAIRE
Introduction 1
Première partie : Introduction au traitement de
gaz naturel 4
Chapitre I : Le gaz naturel 5
Chapitre II : Hydrates de gaz 12
Deuxième partie : Description du
procédé de déshydratation de gaz 16
Chapitre I : Présentation du complexe de Torpille
Marine 17
Chapitre II : Présentation du procédé de
déshydratation 24
Troisième partie : Optimisation du
procédé de déshydratation de gaz naturel 34
Chapitre I : Simulation de l'unité SERTERE 35
Chapitre II : Optimisation du procédé 45
Conclusion 55
1

|
Optimisation d'un procédé de déshydratation
de gaz naturel
|
|
INTRODUCTION
Le gaz naturel représente aujourd'hui plus de 20% de la
consommation énergétique globale, contre 40% pour le
pétrole brut. C'est la troisième source d'énergie
consommée dans le monde, après le pétrole et le charbon.
Son rendement énergétique élevé et ses avantages
environnementaux, le rangent parmi les énergies dites « propres
».
Au Gabon, le gaz naturel prend une place de plus en plus
importante dans le secteur énergétique - les réserves
prouvées étant estimées à près de 32,59
milliards de mètres cubes en 2008. Le pays s'est, de fait,
récemment lancé dans une nouvelle forme de valorisation de ses
ressources, avec la transformation locale du gaz naturel.
Les contraintes techniques de production, de traitement et
surtout de transport du gaz naturel, restent toutefois élevés, et
représentent un handicap. En effet, le gaz naturel à sa sortie
des puits, n'est pas directement utilisable, avant qu'il ne soit traité
et débarrassé de ses constituants indésirables. Le
traitement du gaz naturel consiste alors à séparer au moins
partiellement certains des constituants présents à la sortie des
puits tels que l'eau, les gaz acides et les hydrocarbures lourds.
Les hydrates - cristaux solides qui se forment lorsque les
molécules de gaz se trouvent en présence d'eau dans les
conditions de pression et de température les plus usuelles en production
- constituent le problème majeur dans la production et le transport du
gaz naturel. En effet, la formation d'hydrates dans un ouvrage, conduit
très rapidement à l'obstruction totale des tuyauteries ou des
appareils, et à l'interruption pure et simple de la totalité de
la production. La remise en service des installations, ne peut intervenir
qu'après leur disparition ; disparition qui peut demander plusieurs
heures à plusieurs jours, et nécessiter des opérations
coûteuses de décompression et d'injection d'inhibiteurs
d'hydrates.
Pour pallier à ce problème, on doit
éviter que des condensations d'eau se produisent dans l'ouvrage,
c'est-à-dire, déshydrater le gaz en amont de l'installation, ou
faire prévaloir dans celle-ci, des conditions de pression et de
température telles que les hydrates ne puissent se former ou, enfin, si
la présence d'eau dans l'ouvrage ne peut être
évitée, inhiber celle-ci par un inhibiteur d'hydrates
(méthanol ou glycol par exemple).
Le rôle essentiel d'une unité de
déshydratation de gaz, est de séparer la partie liquide
(condensats + eau) de la partie gazeuse (gaz humide). Celles-ci doivent
être ainsi dissociées dans le but de faciliter le transport et le
stockage, d'une part, et la commercialisation de ces produits en tant que
produits finis ou semi-finis d'autre part.
2

|
Optimisation d'un procédé de déshydratation
de gaz naturel
|
|
La plate-forme de Torpille Marine (TRM), opérée
par TOTAL E&P GABON, est équipée d'une unité de
déshydratation de gaz naturel par triéthylène-glycol
(ci-après désigné TEG ou glycol). Cette unité,
fournie par la société SERTERE et mise en service en 1986, a
été le théâtre de plusieurs incidents de
sécurité à haut potentiel de risque. De plus, la
capacité de l'unité à accompagner le dégoulottage
de la chaîne gaz est incertaine.
La problématique de l'optimisation du traitement du gaz
offshore de Total Gabon est double :
? Manque de fiabilité de la compression
(approvisionnement) et du traitement actuels, d'où des Manques À
Produire (MAP) ;
? Programme en cours de réduction du brûlage de
gaz offshore du Gabon, d'où d'importantes quantités de gaz
à renvoyer à terre : environ 700 kSm3/j en 2017.
Pour satisfaire les objectifs du Groupe de réduction du
brûlage de gaz associé, Total Gabon s'est vu dans l'obligation de
contraindre sa production dès 2014, afin de limiter le gaz
excédentaire à l'entrée de la compression. Les
réserves associées au dégoulottage de la compression gaz,
viennent donc de la production supplémentaire autorisée par un
surcroît de la capacité de compression de gaz associé. Le
gaz comprimé, non utilisé pour le gas-lift, est envoyé
à terre en vue de sa commercialisation. De plus, le besoin total en
gas-lift offshore sera amené à croître dans le futur :
augmentation des besoins du Socle, redéveloppements envisagés des
champs d'Anguille et de Torpille.
Aussi, le travail d'optimisation du procédé de
déshydratation de gaz naturel, dont il est ici question, se divisera en
trois principales parties.
La première partie, sera essentiellement
théorique. Elle contiendra des généralités sur le
traitement du gaz naturel, avec notamment une vue succincte sur les
caractéristiques du gaz naturel, ses spécifications
technico-commerciales et les procédés de son traitement. Il
s'agira également ici de présenter la nature, les modes de
formation, et par là même de prévention des hydrates,
problème majeur des installations gazières.
La deuxième partie aura pour vocation de décrire
le procédé de déshydratation de gaz du site de Torpille.
L'occasion ici sera également donnée de présenter le champ
de Torpille. Dans la présentation du procédé de
déshydratation du site, nous verrons en détail les
mécanismes d'absorption d'eau par le glycol, et la
régénération de ce dernier. Nous n'oublierons pas de
détailler ses mécanismes de supervision et de
sécurisation.
3

|
Optimisation d'un procédé de déshydratation
de gaz naturel
|
|
Enfin, la troisième et dernière partie de ce
mémoire sera consacrée à l'optimisation du
procédé à proprement parler. Nous nous attèlerons
à modéliser et simuler le procédé existant
grâce au logiciel thermodynamique Invensys PRO/II®. L'optimisation
du procédé, se basera sur les résultats de sa simulation ;
ainsi que la nécessité d'automatiser les processus de
démarrage et de marche normale, pour les fiabiliser et les
sécuriser.
4

|
Optimisation d'un procédé de déshydratation
de gaz naturel
|
|
PREMIÈRE PARTIE
INTRODUCTION AU TRAITEMENT DE GAZ NATUREL
5

|
Optimisation d'un procédé de déshydratation
de gaz naturel
|
|
CHAPITRE I Le gaz naturel
Le gaz naturel est un combustible fossile composé d'un
mélange d'hydrocarbures, enfoui naturellement dans des roches poreuses,
sous forme gazeuse. Le gaz naturel et le pétrole brut sont souvent
associés et extraits simultanément des mêmes gisements, ou
encore des mêmes zones de production. L'exploration (recherche de
gisements) et l'extraction du gaz naturel utilisent des techniques à peu
près identiques à celles de l'industrie du pétrole. Une
grande partie des gisements de gaz connus à travers le monde a
d'ailleurs été découverte au cours de campagnes
d'exploration dont l'objectif était de trouver du pétrole.
Section 1 : Généralités sur le gaz
naturel
Les qualités du gaz naturel sont principalement
liées à son bon rendement énergétique et à
ses avantages environnementaux : sa combustion n'émet pas de
poussières, peu de dioxyde de soufre (SO 2), peu d'oxyde d'azote (NO 2)
et moins de dioxyde de carbone (CO 2) que d'autres énergies fossiles. De
plus, on peut réduire le volume qu'il occupe en le liquéfiant.
Essentiellement composé de méthane, il est incolore et inodore,
mais "odorisé" pour être détectable. L'apparition d'une
phase liquide dans le gaz naturel dépend des conditions de pression et
de température dans le réservoir, et aux conditions de surface.
Ce qui conduit à distinguer les différents types de gaz naturel
suivants :
? Gaz sec : ne forme pas de gaz liquide (condensats) dans les
conditions de production surface.
? Gaz humide : forme une phase liquide au cours de la production
dans les conditions de surface, sans qu'il n'y ait de condensation
rétrograde dans le gisement.
? Gaz a condensats : forme une phase liquide dans le
réservoir lors de la production par condensation rétrograde.
? Gaz associé : Coexistant dans le réservoir avec
une phase « huile ». Le gaz associé comprend le gaz de
couverture et le gaz dissous.
Section 2 : Spécifications technico-commerciales
2. 1 - Spécifications commerciales
6

|
Optimisation d'un procédé de déshydratation
de gaz naturel
|
|
Plus strictes que les spécifications liées
à son transport, les spécifications du gaz commercial sont :
2. 1. 1 - Teneur en H2S : En général de
1.5 à 4 ppm vol. maximum
Sa forte toxicité impose des traitements
spécifiques permettant de diminuer sa teneur en fonction des
spécifications de transports ou commerciales par le
procédé « d'adoucissement ».
Risques de toxicité, en plus du risque d'inflammation
lié au gaz naturel, lors de mise à l'atmosphère permanente
ou accidentelle.
2. 1. 2 - Soufre total et autres contaminants : Teneurs
maximales en
3
composés soufrés : de 50 à 150
mg/Smmaximum
Sont aussi considérés comme des
impuretés, les composés soufrés qui sont les plus
gênants mais aussi l'oxygène, l'azote et même des atomes
métalliques tels que le nickel et le vanadium. L'oxygène n'est
pas un contaminant naturel du gaz produit mais il apparaît souvent dans
les analyses. Son apparition est due aux entrées d'air dans les
installations à basse pression. Il peut être corrosif et dans
certaines proportions, former aussi un mélange explosif avec le gaz.
2. 1. 3 - Teneur en CO2 : De 2 à 3 % molaire
maximum
Le CO2 diminue le pouvoir calorifique du gaz naturel car il ne
fournit pas de chaleur de
combustion. Il est donc extrait, généralement
lorsqu'il est enlevé en même temps que l'H2S dans
différents procédés. Il doit être
éliminé quand le gaz doit être refroidi dans certains
domaines (essentiellement dans le cas de liquéfaction -GNL) de
température (cristallisation
bouchages).
2. 1. 4 - Point de rosée
Point de rosée eau : de l'ordre de -15°C à
70bar ;
Point de rosée hydrocarbure : de l'ordre de - 2 °C
à 70 bar.
7

|
Optimisation d'un procédé de déshydratation
de gaz naturel
|
|
2. 1. 5 - Pouvoir calorifique
Pouvoir calorifique inférieur : C'est
la quantité de chaleur, que dégage la combustion complète
à pression constante (de 1.01325 bar), de 1 kg de combustible liquide ou
de 1 m3 de gaz (conditions normales). Les produits de la combustion sont
ramenés à la température de 0°C et l'eau provenant de
la saturation en eau du combustible est supposée rester à
l'état vapeur à cette température.
Pouvoir calorifique supérieur :
Même définition que pour le PCI mais l'eau est
supposée totalement condensée à 0°C.
2. 2 - Spécifications pour le transport
2. 2. 1 - Point de rosée eau
Il s'exprime en °C pour une pression donnée (ex :
- 15°C à 70 bar a). Les problèmes de transport liés
à la présence d'eau dans le gaz sont les suivants :
- L'eau à l'état liquide est responsable de la
plupart des formes de corrosion lorsqu'elle est associée à des
gaz acides (H2S et CO2) ou à des sels (carbonates de calcium).
- Risques de formation d'hydrates. Le phénomène
de formation d'hydrates constitue le problème majeur dans la production
et le transport du gaz naturel. Il conduit à l'obstruction des conduites
et des équipements donc à des arrêts de production et des
risques de surpression pour les installations.
- Formation de bouchons d'eau. Les dépôts d'eau
par condensation dans les conduites ou les entraînements d'eau libre de
gisement peuvent engendrer de fortes pertes de charge avec des risques
d'érosion et de "coup de bélier" des bouchons liquides.
2. 2. 2 - Teneur en hydrocarbure liquide
3
La teneur en condensat s'exprime en g/Sm. Équivalent au
point de rosée hydrocarbures
en °C. Ce qui correspond à un point de rosée
hydrocarbure de 7 °C à 50 bar. Lorsque l'on est
8

|
Optimisation d'un procédé de déshydratation
de gaz naturel
|
|
en présence d'un gaz naturel à condensat, on
peut avoir des dépôts liquides de condensats dans les conduites.
Les « lourds » dans le gaz (C5+) peuvent condenser dans
les lignes de transport en provoquant une réduction de la section de
passage du gaz dans les lignes et par conséquence, une augmentation des
pertes de charge et des arrêts intempestifs de production. L'indice de
Wobbe est utilisé, dans les applications domestiques du gaz, pour
déterminer les pressions d'alimentation à appliquer à un
injecteur pour conserver la puissance pour des pressions variables.
Il se définit comme le rapport du pouvoir calorifique
supérieur (PcS) du gaz (kWh/m3) par la racine carrée de
la densité d dudit fluide.
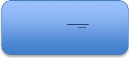
w=
PcS 1d
Section 3 : Bases théoriques du traitement du
gaz naturel
3. 1 - Teneur en eau
La teneur en eau peut être déterminée selon
deux méthodes et s'expriment généralement en :
? Unités anglo-saxonne: lbs / MMSCF ;
? Unités SI: kg / MMSm3 (15°C / 1 atm.) ou kg / MMNm3
(0°C /1 atm.).
3. 1. 1 - Détermination graphique
L'abaque de MACKETTA (voir annexe 1) est la méthode
pratique la plus simple pour une estimation relativement précise de la
teneur en eau d'un gaz. Ce diagramme s'applique pour des gaz naturels de
densité < 0.8. Un facteur de correction est appliqué pour les
gaz dont la teneur en gaz acide est > 2%.
|
Optimisation d'un procédé de déshydratation
de gaz naturel
|
|
3. 1. 2 - Détermination empirique
La détermination se fait soit à l'aide d'un
programme de simulation qui utilise des équations d'états tel que
Invensys PRO/II® (que nous utiliserons un peu plus loin dans ce document)
; soit en appliquant la corrélation de BUKACEK qui permet de
déterminer la teneur en vapeur d'eau d'une façon plus
précise & plus facile. La teneur en eau est calculée en
utilisant une contribution idéale et un facteur de déviation. En
terme d'équation, la corrélation est la suivante:
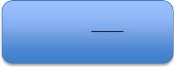
????????????????????????
????????????
???? = 47484 + ????
????????????????????????
Avec :
log???? =
459,6 + ???? (°????) + 6,69449
-3083,87
Où W représente la teneur en eau en lb/MMCF et t la
température en °F.
Cette corrélation n'est vérifiée que pour
des températures comprises entre 60 ° et 460 ° C et à
une pression de 15 à 10 000 psia. Encore une fois, elle est seulement
applicable aux gaz non corrosif. La paire d'équations dans cette
corrélation est simple en apparence. La complexité
supplémentaire qui manque est qu'il nécessite une estimation
précise de la pression de vapeur de l'eau pure.
9
10

|
Optimisation d'un procédé de déshydratation
de gaz naturel
|
|
3. 2 - Techniques de traitement du gaz naturel
Le traitement du gaz naturel consiste à séparer
au moins partiellement certains des constituants présents à la
sortie du puits tels que l'eau, les gaz acides, et les hydrocarbures lourds,
pour amener le gaz à des spécifications de transport, ou à
des spécifications commerciales déterminées. Les
procédés de traitement de gaz sont multiples de par le monde, et
le choix de l'un d'eux se base sur les critères suivants :
> La qualité de l'effluent brut ;
> Le taux de récupération des hydrocarbures
liquides visés ;
> Les spécifications des produits finis ; > Le
coût global des investissements.
Certains composants du gaz naturel doivent être
extraits, soit pour des raisons imposées par les étapes
ultérieures de traitement ou de transport, soit pour se conformer
à des spécifications commerciales ou réglementaires. Il
peut être ainsi nécessaire d'éliminer au moins
partiellement les composants suivants :
> L'hydrogène sulfuré H2S - toxique et corrosif
;
> Le dioxyde de carbone CO2 - corrosif ;
> Le mercure - corrosif pour les équipements
fabriqués en aluminium ; > L'eau - conduisant à la formation
des hydrates ;
> Les hydrocarbures lourds - condensant dans les
réseaux de transport.
Les spécifications à respecter pour le gaz
traité sont en général liées, soit aux conditions
et spécifications de transport, soit aux conditions d'utilisation (gaz
commercial).
Dans le cadre du transport par gazoduc, les
spécifications de transport visent à éviter la formation
d'une phase liquide, le bouchage des conduites par des hydrates et une
corrosion trop importante. On impose dans ce cas, une valeur maximale au point
de rosée eau des hydrocarbures, qui dépend des conditions de
transport, et peut être par exemple fixée à 0°C, pour
éviter tout risque de formation d'une phase liquide par condensation en
ligne.
Dans le cadre d'un gaz commercial, les spécifications
sont plus sévères et comprennent également une fourchette
dans laquelle doit se situer le pouvoir calorifique. Le gaz associé au
pétrole est un mélange (gaz + hydrocarbures liquides) contenant
une forte proportion d'eau de gisement, et concerne l'objet ici de notre
étude.
11

|
Optimisation d'un procédé de déshydratation
de gaz naturel
|
|
Le tableau 1 ci-dessous montre les principales données de
production des champs opérés, d'où est extrait le gaz
naturel associé, dont nous nous attèlerons à en optimiser
le traitement.
|
Secteur Torpille (principal)
|
Satellites Torpille
|
Champs
|
TRM
|
TNEM
|
MSSM
|
BDM-BDNM
|
BSM
|
GIM
|
PAM
|
Réservoirs
|
Anguille Inf. / Term.
|
Batanga (+ Mandorové, Anguille)
|
Qualité huile
|
34 API
|
34 API
|
34 API
|
31 API
|
28 API
|
31 API
|
20 API
|
STOIIP, Mb
|
713
|
62
|
68
|
250
|
79
|
95
|
14
|
Début prod°
|
1971
|
1984
|
1984
|
1982
|
1980
|
1975
|
1975
|
Potentiel, b/d
|
7541
|
1688
|
741
|
5536
|
920
|
780
|
123
|
BSW
|
25%
|
5%
|
0%
|
70%
|
72%
|
72%
|
90%
|
Statut Puits
|
16 OP GL
5 WI 2 GP 20 fermés
|
4 OP GL 1 fermé
|
3 OP GL
|
|
4 OP GL
10 fermés
|
1 OP GL 8 fermés
|
1 OP GL 6 fermés
|
NP, Mb
|
140
|
12
|
4.3
|
124
|
15
|
43
|
2
|
RF
|
24%
|
19%
|
6%
|
50%
|
19%
|
45%
|
14%
|
RR 2P, Mb
|
44
|
9
|
2.8
|
8
|
1.6
|
6.6
|
0.3
|
URF
|
26%
|
34%
|
10%
|
53%
|
21%
|
52%
|
16%
|
Tableau 1.1 : Statut des champs du secteur Torpille
(source : Audit unité SERTERE, Prosernat, 2014)
12

|
Optimisation d'un procédé de déshydratation
de gaz naturel
|
|
CHAPITRE II
Hydrates de gaz
Les hydrates sont des structures cristallines qui peuvent se
former lorsqu'on met des hydrocarbures et de l'eau en contact dans certaines
conditions de pression et de température. Ils se forment pratiquement
avec les hydrocarbures suivants : méthane, éthane, propane,
butane et également avec le gaz carbonique CO2 et
l'hydrogène sulfuré H2S.
Section 1 : Nature
Un certain nombre d'études ont été
consacrées à la détermination de la composition des
hydrates sans qu'un accord soit intervenu entre les différents auteurs.
Il est admis cependant que les hydrates seraient des inclusions de
molécules de gaz dans les espaces laissés libres dans un
empilement dodécaédrique de molécules d'eau sans liaisons
chimiques entre le gaz et l'eau. Ce sont des solides de couleur blanche qui
peuvent revêtir différents aspects (neige, givre, cristaux ou
arborescences).
La densité des hydrates est d'environ 0,98 de sorte que
leur première apparition se traduit par une fine pellicule à
l'interface eau-gaz permettant d'ailleurs d'effectuer les mesures
expérimentales de conditions de formation en cellule. La réaction
de formation est exothermique.
Dans le cas du bouchage d'une tuyauterie par des hydrates,
l'adhérence aux parois et la dureté du bloc d'hydrates est telle
qu'aucun moyen mécanique normal de débouchage ne peut être
mis en oeuvre.
Section 2 : Conditions de formation
Le phénomène de formation d'hydrates constitue
le problème majeur dans la production et le transport du gaz naturel. Il
y a formation d'hydrates lorsque les conditions suivantes sont
simultanément réalisées :
13

|
Optimisation d'un procédé de déshydratation
de gaz naturel
|
|
2. 1 - Présence d'eau liquide
Un gaz naturel saturé ou non en eau ne donne pas lieu
à la formation d'hydrates. Celle-ci ne peut intervenir qu'en
présence d'eau liquide par exemple libérée par le gaz au
cours d'un changement des conditions de pression ou de température.
2. 2 - Présence d'hydrocarbures légers
Seuls les quatre premiers hydrocarbures (méthane,
éthane, propane, butane) sont susceptibles de former des hydrates en
présence d'eau liquide. D'autres corps tels que le gaz carbonique ou
l'hydrogène sulfuré peuvent également former des hydrates
avec l'eau.
2. 3 - Réalisation de certaines conditions (P,
T)
En plus des conditions précédentes, pour que des
hydrates puissent se former, il faut, pour un gaz donné, que la pression
soit suffisamment élevée et la température suffisamment
basse. La formation des hydrates est favorisée par un certain nombre de
facteurs :
> Tourbillons ;
> Vitesse du gaz ;
> Coude, orifice, changement de diamètre ;
> Phénomène auto amplifié ;
> Haute pression ;
> Basse température.
Pour un gaz naturel donné, en présence d'eau
liquide, les hydrates se forment à une certaine température pour
une pression donnée.
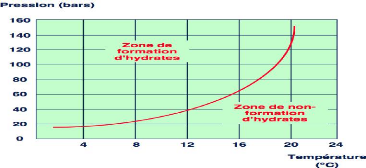
Figure 1.1 : Courbe de formation d'hydrates (source :
Les hydrates, IFP Training, 2007)
14

|
Optimisation d'un procédé de déshydratation
de gaz naturel
|
|
Une des méthodes pour tracer la courbe de formation
d'hydrates est l'utilisation des abaques de Katz. En effet, comme nous pouvons
le voir sur la figure 1.1 précédente, les conditions de formation
d'hydrates dans un domaine (P, T) sont définies par une courbe
séparant le plan en 2 zones. La zone à gauche de la courbe
où il y a formation d'hydrates (hautes pressions, basses
températures). La zone à droite de la courbe où il n'y a
pas de formation d'hydrates (basses pressions, hautes températures).
Notons que le début de formation d'un bouchon
d'hydrates augmente la perte de charge dans la conduite, donc
créé une détente supplémentaire du gaz, ce qui a
pour effet de le refroidir et donc d'entretenir et d'accélérer la
formation des hydrates.
Section 3 : Prévention contre les hydrates
Le domaine de fonctionnement est représenté par
un quadrilatère délimité par les pressions maxi et mini
(avec les températures qui leur sont associées) et les
températures mini et maxi (avec les pressions qui leur sont
associées) que l'on trouve dans l'ouvrage considéré sur la
figure 1.2 suivante :
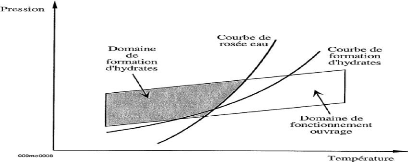
Figure 1.2 : Domaine de fonctionnement de l'ouvrage
(source : traitement de gaz, ENSPM, 2005)
À partir de ce diagramme, nous pouvons définir
les trois ensembles de solutions qui permettent de protéger le domaine
de fonctionnement de l'ouvrage des risques de formation d'hydrates :
- Déplacement du domaine de fonctionnement de l'ouvrage
hors de la zone d'hydrates : grâce à la mise en place de
réchauffeurs en amont et de calorifugeage de lignes ;
15

|
Optimisation d'un procédé de déshydratation
de gaz naturel
|
|
- Déplacement de la courbe de rosée eau du gaz :
en évitant des condensations d'eau. Ceci peut être obtenu en
déshydratant suffisamment, ce qui revient à déplacer la
courbe de rosée eau initiale du gaz vers la gauche ;
- Déplacement de la courbe de formation d'hydrates : en
injectant des inhibiteurs chimiques tels que les glycols ou le
méthanol.
Il existe des formules qui permettent de calculer la
concentration d'inhibiteur (méthanol ou autre) qu'il faut injecter pour
déplacer de x°C la courbe de formation d'hydrates. Les principales
formules sont basées sur le "Dew point depression" : c'est-à-dire
le nombre de degrés nécessaire pour déplacer la courbe de
formation d'hydrates en dehors de l'ouvrage pour supprimer tout risque de
formation. Plus cet écart est important, plus la quantité
d'inhibiteur à injecter sera grande. La formule la plus utilisée
est celle d'Hammerschmidt :
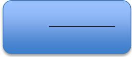
W =
100 . du . M K+ du . M
W : % en poids de la concentration d'inhibiteur // du :
dépression de température à réaliser °F
M : Masse molaire de l'inhibiteur utilisé // K :
Coefficient dépendant de l'inhibiteur
Cette formule se trouve généralement bien
vérifiée par l'expérience et permet de prévoir la
translation effective de la courbe de formation d'hydrates à #177;
3°C.
(Tous deux en livres/jour)

Débit d'eau à inhiber
X = Qi
q
= Débit de glycol concentré à
injecter
Dans le cas des inhibiteurs régénérables
tels que les glycols, on calcule la quantité X de glycol
concentré à injecter par livre d'eau à inhiber selon la
formule suivante :
16

|
Optimisation d'un procédé de déshydratation
de gaz naturel
|
|
DEUXIÈME PARTIE
DESCRIPTION DU PROCÉDÉ DE
DÉSHYDRATATION DE GAZ
17

|
Optimisation d'un procédé de déshydratation
de gaz naturel
|
|
CHAPITRE I
Présentation du complexe de Torpille Marine
Section 1 : Historique du champ
Le secteur de Torpille Marine (TRM en abrégé) -
dont nous pouvons voir le complexe central sur la photo 2.1 suivante - est
situé au large de l'île Mandji (l'île sur laquelle est
située la ville de Port-Gentil) à environ 60km des côtes.
La desserte de ce champ, se fait par bateau (surfer) à partir de la base
logistique de Total Gabon à Port-Gentil, ou par
hélicoptère à partir de l'aéroport de la ville.
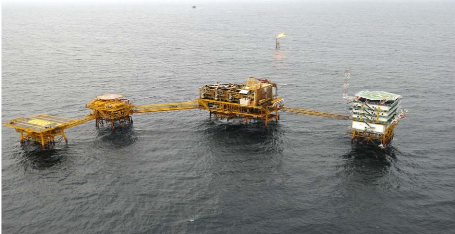
Photo 2.1 : Vue aérienne du complexe central
du site TRM
(source : ressources bibliographiques de l'entreprise, Total
Gabon, 2005)
En 1968, le puits de découverte TRM 1 puis le puits
d'appréciation TRM 2 sont forés. Au cours des années 1970
- 1971, les plates-formes : Torpille Marine 1 (TRM1), Torpille Marine 2 (TRM2),
Torpille Marine - Plate-forme Centrale (TRM PFC) du complexe Torpille ont
été installées. Suivent Girelle Marine (GIM), Pageau
Marine PAM PF1 et PAM PFC posées en 1974/1975, Baliste Marine (BSM) en
1980, Baudroie Nord Marine (BDNM) en 1982, Baudroie Marine (BDM) en 1983,
Torpille Nord-Est (TNEM), les plates-formes compression et habitation TRM PFK
et TRM PFQ en 1984. Les deux derniers champs développés ont
été ceux d'Hylia Marine (HYM PFC) et de Vanneau Marine (VNM) en
1993 - appartenant actuellement à la société Perenco Oil
& Gas.
18

|
Optimisation d'un procédé de déshydratation
de gaz naturel
|
|
Les 103 puits du complexe de TRM ont été
forés sur 07 gisements différents. En 2015, l'exploitation du
champ repose sur 51 puits producteurs d'huile, 05 puits injecteurs d'eau, 47
puits producteurs abandonnés, ainsi que le montre le tableau 2.1 suivant
:
PLATE- FORME
|
PUITS PRODUCTEURS
|
PUITS
ABANDONNÉS
|
RÉSERVOIR
|
|
Injecteurs : TRM001/009/012 Producteurs :
|
|
|
|
|
TRM003/03B/004/005/
|
|
TRM I
|
TRM003/006/007/011/024/029
|
|
Anguille, Clairette
|
|
|
05Z
|
|
|
/033/034
|
|
|
|
Injecteurs : TRM030/501
|
|
|
|
Producteurs :
|
|
|
TRM II
|
TRM013/014/015/016/017/018
|
TRM019/022/026
|
Anguille, Clairette
|
|
/020/021/023/027/028/031
|
|
|
|
TNEM001/002/003/005 &
|
|
|
TNEM
|
|
TNEM004
|
Anguille, Clairette
|
|
MSSM001/002/003
|
|
|
|
|
PAM001/002/003/004/
|
|
PAM
|
PAM007
|
|
Batanga
|
|
|
005/006
|
|
|
|
GIM/001/002/003/004/
|
Mandorove,
|
GIM
|
GIM005/GIM009
|
006/007/008
|
Batanga Supérieur,
|
|
|
|
Anguille Supérieur
|
|
BDNM002/006/008/010/011/0
|
BDNM001/003/004/00
|
|
BDNM
|
|
|
Anguille
|
|
12/014
|
5/05Z/007/010PH
|
|
|
|
BDNM001/02TL/003/0
|
|
BDM
|
BDM02TC/005/006
|
|
Anguille, Batanga
|
|
|
04/007
|
|
|
|
BSM001/002/003/005/0
|
|
|
|
06/007/008/08G/09B/0
|
Mandorove,
|
BSM
|
BSM004/010/012/013
|
|
Batanga
|
|
|
11/013G/013PH
|
|
HYM
|
HYM02B/003/004/005/007/00
|
HYM006
|
Anguille Supérieur,
|
|
8/009
|
|
Anguille Inférieur
|
Tableau 2.1 : Plates-formes & puits du site TRM
en 2015
19

|
Optimisation d'un procédé de déshydratation
de gaz naturel
|
|
Section 2 : Installations de production
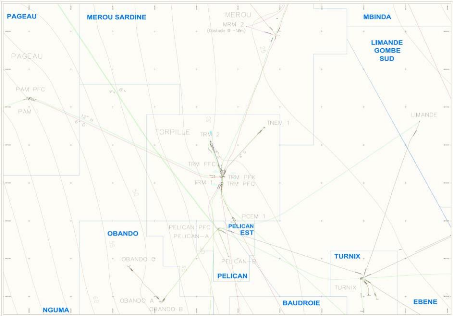
Figure 2.1 : Plan topographique du site de
Torpille
(source : ressources bibliographies de l'entreprise, Total
Gabon, 2005)
Les installations d'extraction et de traitement de
pétrole brut du site d'exploitation de Torpille Marine,
représentée sur le plan topographique de la figure 2.1 ci-dessus,
comprennent :
- Un complexe central TORPILLE constitué :
+ D'une plate-forme habitation TRM PFQ sur laquelle se trouve la
salle de contrôle du champ, les bureaux, logements et réfectoires
;
+ D'une plate-forme production TRM PFC sur laquelle se trouvent
:
> Des séparateurs de production ;
> Des pompes d'expédition d'huile vers le terminal de
Cap Lopez. - d'une plate-forme de compression TRM PFK sur laquelle se trouvent
:
> Quatre compresseurs de gas-lift, et le traitement gaz
associé ; > Une unité de traitement d'eau d'injection ;
20

|
Optimisation d'un procédé de déshydratation
de gaz naturel
|
|
> Une génération d'électricité
pour les besoins du complexe central et des plates-formes satellites ;
> Les utilités correspondantes (air comprimé,
purges, gasoil, etc...).
- D'une plate-forme puits TRM1 sur laquelle se trouvent des
puits producteurs d'huile et injecteurs d'eau.
- D'une deuxième plate-forme puits TRM2 reliée
par ligne sous-marine, sur laquelle se trouvent :
> Des puits producteurs d'huile et injecteurs d'eau.
- D'une troisième plate-forme puits TNEM reliée
par ligne sous-marine, sur laquelle se trouvent :
> Des puits producteurs d'huile ; > Un séparateur
test.
Un ensemble de plate-forme de traitement et plate-forme puits
PAGEAU (PAM PFC/PAM1). Cet ensemble est raccordé par passerelle. Le
traitement de séparation production effectué sur la plate-forme
traite la production GIM ET PAM.
La plate-forme GIRELLE (GIM) dispose de puits producteurs
d'huile et d'un puits à gaz (et un séparateur test).
La plate-forme BAUDROIE MARINE (BDM) dispose de :
> Puits producteurs d'huile ;
> Un séparateur test, deux séparateurs de
production et une pomperie d'expédition.
La plate-forme BAUDROIE NORD MARINE (BDNM) dispose de :
> Puits producteurs d'huile ;
> Un séparateur test, trois séparateurs de
production et sa pomperie d'expédition.
La plate-forme BALISTE (BSM) dispose de :
> Puits producteurs d'huile ;
> Un séparateur test, deux séparateurs de
production et sa pomperie d'expédition.
La plate-forme HYLIA (HYM PFC) dispose de :
> Puits producteurs d'huile ;
> Un séparateur test, deux séparateurs de
production, sa pomperie d'expédition ; > Un système de
compression gaz HP pour l'activation de ses puits.
21

|
Optimisation d'un procédé de déshydratation
de gaz naturel
|
|
Section 3 : Philosophie d'exploitation
3. 1 - Mode d'exploitation
3. 1. 1 - Champs
L'exploitation du champ de Torpille - champ mature - met en
oeuvre un mode principal d'assistance de puits : le gas-lift. Notons toutefois
qu'un essai d'activation via ESP (Electric Submersible Pump) fût
implémenté en 2014 sur le puits HYM 02B de la plate-forme HYM. On
y utilise de ce fait, la méthode de gas-lift continu direct : par
injection de gaz à haute pression (HP) au niveau des espaces annulaires
des puits, grâce à des vannes de gas-lift disposées le long
du tubing. Sur les champs de HYM et de BDM, BDNM, TRM2 et TRM1, un
système d'optimisation de l'activation gas-lift Full Control Well (FCW)
a été installé.
Les pressions gaz HP de gas-lift en tête de puits sont
les suivantes :
? Pression de démarrage du puits : P. réseau env.
70 bar. // PCH = 20 - 30 bar ; ? Pression de marche normale : P. réseau
70 bar. // PCH = 58 - 60 bar.
Les puits TRM007/016/034 - TNEM 005 - GIM005 sont
naturellement éruptifs. Du côté des puits
semi-éruptifs, nous pouvons citer en autres : TRM029 - BDNM011. Le
tableau 2.2 suivant résume les principaux chiffres de production par
plate-forme du site en 2005 :
Plate- forme
|
QHH
|
QHA
|
BSW
|
Qgl
|
Qgl/QHA
|
GOR
|
Qgaz puits
|
TRM I
|
454
|
321
|
29
|
43
|
133,95
|
299
|
96
|
TRM II
|
969
|
585
|
40
|
148
|
252,9
|
1 048
|
613
|
TNEM
|
262
|
241
|
17
|
50
|
207,46
|
170
|
41
|
PAM
|
212
|
57
|
73
|
23
|
403,5
|
85
|
5
|
GIM
|
863
|
328
|
62
|
11
|
33,53
|
250
|
110
|
BDNM
|
4 133
|
2 645
|
36
|
67
|
25,33
|
164
|
433
|
BDM
|
446
|
249
|
44
|
47
|
188,75
|
60
|
15
|
BSM
|
657
|
214
|
67
|
33
|
154,2
|
228
|
49
|
HYM
|
897
|
530
|
41
|
177
|
333,96
|
90
|
45
|
Tableau 2.2 : Chiffres de production du site de TRM
en 2005 (source : Manuel opératoire secteur Torpille, Total Gabon,
2005)
22

|
Optimisation d'un procédé de déshydratation
de gaz naturel
|
|
3. 1. 2 - Réseau gaz HP
Le gaz HP de gas-lift (voir annexe 2) produit par les
compresseurs de TRM PFK est distribué à quasiment l'ensemble des
plates-formes de production (à l'exception de GIM & HYM),
directement ou après transit par une autre plate-forme. Le gaz
associé venant des puits de HYM est utilisé par le module de
compression de la plate-forme : KX 501. Il est à noter que la
plate-forme AYOL du secteur Grondin reçoit le gaz HP de Torpille, tout
comme les secteurs d'Anguille et de N'Tchengué. Ce gaz est surtout
utilisé comme gaz d'appoint pour le fonctionnement du complexe GRM
PFC.
3. 1. 3 - Réseau huile
L'huile produite sur VNM est envoyée sur le complexe
HYM. L'ensemble de la production est traité et envoyé sur TRM PFC
pour export par une ligne sous-marine de 12". L'huile produite sur GIM est
expédiée vers le complexe PAM et y est aussi traitée.
L'ensemble de cette production est exporté vers TRM PFC par une ligne
sous-marine 12". L'huile produite et traitée sur BSM, BDM, et BDNM est
envoyée par une ligne sous-marine 8" connectée au pipe 12" export
de HYM, qui lui, se pique sur le pipe 20" en provenance du secteur Grondin vers
TRM PFC, N'Tchengué puis le terminal du Cap Lopez.
L'huile de TRM1 est envoyée vers TRM PFC via une
passerelle de 35m, celle de TRM2 via une ligne sous-marine de 12" (8" pour le
test), celle de TNEM via une ligne sous-marine de 12". La production de TRM PFC
est exportée via le pipe 20" de Grondin vers le Cap Lopez.
3. 2 - Mode de fonctionnement
Le contrôle et la supervision des plates-formes sont
assurés par un Système Numérique de Conduite
Centralisée (SNCC) et par télésurveillance, selon la
répartition suivante :
? Télésurveillance via GEFANUC : PAM - GIM - BSM -
TNEM ;
? Conduite à distance via SNCC : VNM - HYM - BDM - BDNM -
TRM1 - TRM2 - TRM PFK - TRM PFC.
Ces réseaux SNCC disposent de consoles
numériques situées d'une part en salle de contrôle de TRM
PFQ et d'autre part dans un local technique à Port-Gentil.
23

|
Optimisation d'un procédé de déshydratation
de gaz naturel
|
|
3. 2. 1 - Détection feu & gaz
Chaque plate-forme est dotée de boucles fusibles, d'un
système de détection feu & gaz ; fusible pouvant
déclencher un arrêt d'urgence. L'arrêt d'urgence peut
également, pour les plates-formes
télé-contrôlées, être déclenché
par les opérateurs en salle de contrôle.
3. 2. 2 - Réseau électrique
La génération électrique du complexe
central est assurée par la centrale électrique à terre du
site de PG2. L'électricité transformée est ensuite
distribuée à la plate-forme TRM2 par câble
électrique sous-marin et via les passerelles pour TRM1 et TRM PFQ. La
plate-forme TRM PFQ possède un groupe électrogène de
secours tandis que HYM, BDM et BDNM sont alimentés par AYOL (secteur
Grondin). Les plates-formes TNEM et BSM utilisent des panneaux solaires, PAM
PFC et GIM un groupe électrogène chacune.
3. 3 - Organisation du travail
Une présence permanente est assurée sur le champ
au niveau du complexe central de Torpille. La plate-forme TRM PFQ est
dotée d'une salle de contrôle, de bureaux, d'atelier et de
magasins de stockage. L'hébergement et les repas sont assurés sur
TRM PFQ. Le travail y est organisé selon la hiérarchisation de la
figure 2.2 suivante :
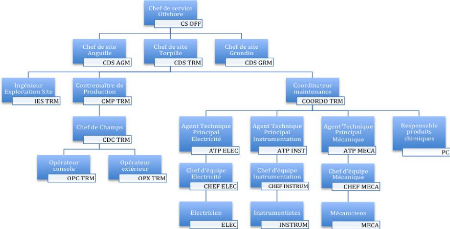
Figure 2.2 : Hiérarchie organisationnelle du
site TRM
24

|
Optimisation d'un procédé de déshydratation
de gaz naturel
|
|
CHAPITRE II
Description du procédé de
déshydratation de gaz
Certains produits chimiques liquides (les glycols en
particulier) ont la propriété d'absorber une grande
quantité d'eau si bien que, mise en présence d'un gaz naturel,
leur affinité pour l'eau étant plus grande que celle du gaz, la
vapeur d'eau sera transférée du gaz dans le liquide. Ce
phénomène chimique est appelé :
absorption.
L'objectif du système de déshydratation du gaz
de la plate-forme TRM PFK est de fournir du gaz sec à haute pression
pour :
? Permettre une récupération d'huile du champ de
Torpille assistée, par la technique du "gas-lift" ;
? Alimenter le poste à gaz combustible pour les besoins
des machines thermiques ; ? Fournir ce gaz aux autres champs de Torpille (TRM1,
TRM2 et TNEM), Pageau
(PAM), Baliste (BSM), Baudroie (BDM et BDNM) ; ainsi qu'aux
secteurs d'Anguille,
Grondin et N'Tchengué à terre (en cas de
nécessité).
La disponibilité du système est critique pour la
production du champ, les équipements le constituant n'étant ni
secourus, ni dupliqués.
Par ailleurs, l'alimentation du poste à gaz combustible
en gaz sec de bonne qualité est critique pour le bon fonctionnement des
machines thermiques de la plate-forme (turbine à gaz - TAG). Toutefois,
un fonctionnement en mode dégradé peut être effectué
en by-passant la colonne de déshydratation CA 503 et en réalisant
une inhibition d'hydrates par injection de méthanol.
Section 1 : Section de déshydratation par
absorption
Au refoulement, les compresseurs gaz sont reliés
à un collecteur 8" gaz HP humide à 75 bar, qui dirige le gaz vers
une colonne d'absorption CA 503 qui sèche le gaz par contact avec
du Triéthylène-Glycol. Cette unité a une
capacité de traitement de 48 450 Sm3/h pour un point de
rossée gaz sec. Le TEG riche (hydraté) est
régénéré par rebouillage à 204°C dans
le rebouilleur H 507. Le système de régénération
comprend en outre, un séparateur triphasique gaz/hydrocarbures/glycol DS
504, un stockage-économiseur DS 508, un refroidisseur EC 900
et des pompes de circulation GX 509A/B, de débit nominal :
3 m3/h.
Les utilités requises pour le fonctionnement de
l'unité de déshydratation sont notamment :
25

|
Optimisation d'un procédé de déshydratation
de gaz naturel
|
|
? De l'eau de mer pour refroidissement du glycol dans la
boucle de régénération ; ? De l'électricité
pour l'entraînement des pompes de circulation ;
? Du gaz BP pour brûlage, stripping et couverture dans
la régénération du glycol ; ? De l'air service pour les
pompes d'appoint de glycol ;
? De l'air instrument pour le fonctionnement de l'instrumentation
pneumatique.
Le gaz HP sec sortant de la colonne CA 503, est
distribué soit dans le réseau de gas-lift via une ligne 8" vers
TRM PFC, soit vers le poste à gaz combustible UB 701 via une ligne 2".
La pression de distribution est contrôlée par la vanne PCV 400 qui
recycle le gaz HP sec excédentaire vers le scrubber BP DS 401, ou par la
vanne PCV 105A/B qui évacue le gaz HP sec excédentaire vers la
torche. Le gaz peut aussi être recyclé vers le scrubber MP DS 402.
La figure 2.3 ci-dessous illustre le schéma de procédé de
ladite colonne :
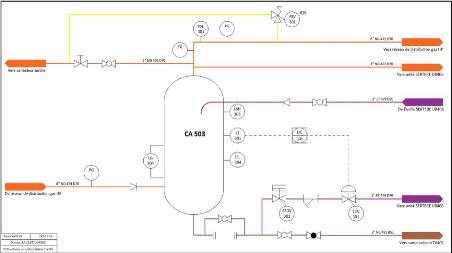
Figure 2.3 : PFD colonne de déshydratation
gaz
Le gaz HP humide provient des groupes de compression KB
410/420/430 (compresseurs alternatifs à piston) ou du compresseur
centrifuge KY 440. Il entre dans l'absorbeur via une ligne 8", à une
pression de l'ordre de 75 bar et une température de l'ordre de
60°C, en partie basse de la colonne de déshydratation CA 503, sous
les plateaux internes.
Le Triéthylène-Glycol, sortant de l'unité
de régénération, c'est-à-dire sec, poussé
par les pompes GX 509A/B, entre dans la colonne de déshydratation par
une ligne 2", au-dessus des plateaux internes.
26

|
Optimisation d'un procédé de déshydratation
de gaz naturel
|
|
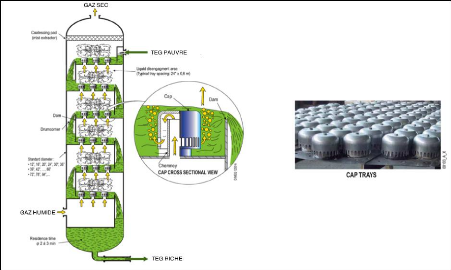
Figure 2.4 : Schéma de principe de la colonne
de déshydratation (source : traitement des gaz, ENSPM, 2005)
Les deux fluides sont mis en contact dans la série de
plateaux internes, le gaz se dirigeant vers le haut et le TEG s'écoulant
par cascades successives vers le bas, ainsi que représenté sur la
figure 2.4 ci-dessus. Au cours de ce contact sur les plateaux internes, le TEG
absorbe l'eau, et inversement le gaz se déshydrate. Le TEG humide, dit
riche, sort par une ligne 2" en fond de colonne, sous contrôle de niveau
de la partie basse située sous les plateaux internes, vers
l'unité de régénération (unité SERTERE). Le
gaz déshydraté sort par une ligne 8" en tête de colonne,
au-dessus des plateaux internes.
La colonne de déshydratation CA 503 peut être
entièrement by-passée. Elle est protégée par une
soupape évacuant le gaz (issu d'une surpression accidentelle) vers la
torche, mais ne possède pas de système automatique de
dépressurisation. Elle est également dotée d'un drain
fermé en point bas vers la cuve de purges.
Enfin, le gaz déshydraté est ensuite normalement
exporté soit dans le réseau gaz-lift, par une ligne 8", soit vers
le poste à gaz combustible, par une ligne 2". Le gaz excédentaire
est recyclé vers le scrubber BP DS 401 sous contrôle de pression
PCV 400 et via une ligne 8". Il peut aussi être recyclé
manuellement vers les scrubbers BP DS 401 ou MP DS 402 via une ligne 2".
27

|
Optimisation d'un procédé de déshydratation
de gaz naturel
|
|
Section 2 : Section de
régénération de TEG (unité SERTERE)
L'objectif de l'unité de
régénération du TEG (voir annexe 3) dans le module de
déshydratation de gaz est de traiter le TEG humide, dit riche,
récupéré au bas de la colonne de déshydratation CA
503, pour le rendre sec et réutilisable, et le réinjecter
à nouveau en haut de la colonne de déshydratation. La
disponibilité de l'unité de régénération du
TEG est essentielle pour la déshydratation du gaz. Les
équipements ne sont ni secourus ni dupliqués, à
l'exception des pompes de circulation de TEG.
Ainsi, le TEG sort de la colonne de déshydratation CA
503 sous forme humide, par une ligne 2" en fond de colonne, sous contrôle
de niveau de la partie basse située sous les plateaux internes. La
pression de sortie de la colonne est de l'ordre de 75 bar, à une
température d'environ de 60°C. Il est détendu à une
pression de 4 bar, essentiellement par la vanne de contrôle de niveau LCV
301, et réchauffé dans un serpentin-économiseur (servant
de condenseur de tête) récupérant une partie de la chaleur
de la tête de la colonne de distillation CA 506, jusqu'à une
température de l'ordre de 80°C. Le TEG humide, partiellement
détendu et réchauffé entre alors dans le ballon de
détente (flash tank) DS 504, maintenu sous pression positive avec une
couverture de gaz BP sous contrôle de pression.
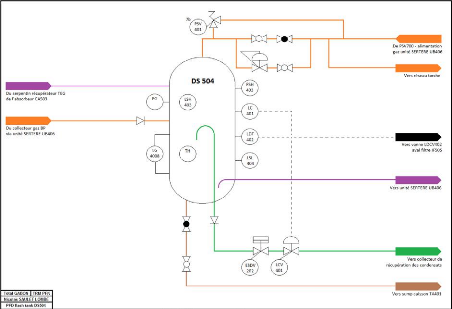
Figure 2.5 : PFD flash tank glycol DS504
Le ballon de détente DS 504 représenté sur
la figure 2.5 ci-dessus sépare trois phases :
28

|
Optimisation d'un procédé de déshydratation
de gaz naturel
|
|
? Le gaz résiduel, envoyé à la torche sous
contrôle de pression ;
? Les hydrocarbures liquides entrainés vers le
séparateur atmosphérique DS 202 sur TRM PFC sous contrôle
de niveau ;
? Le glycol humide, sous contrôle de niveau.
Le schéma de principe de la figure 2.6 suivante,
illustre les internes dudit ballon de détente et les différents
niveaux de fluide y présents, et de fait le principe de
régulation de niveau interface condensats - glycol.
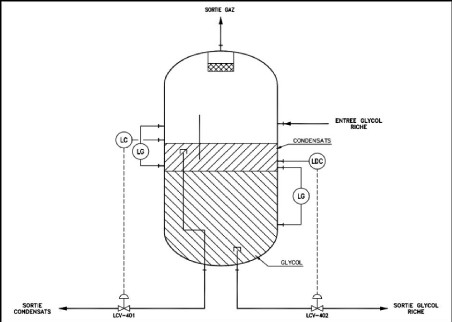
Figure 2.6 : Schéma de principe du flash tank
DS 504
(source : Traitement des gaz, ENSPM, 2005)
Le glycol humide, débarrassé du gaz et des
hydrocarbures liquides, est alors tout d'abord filtré par le filtre
à cartouche IF 505, détendu quasiment à la pression
atmosphérique, essentiellement par la vanne de contrôle de niveau
LDCV 402, puis réchauffé par un serpentin économiseur dans
le ballon tampon DS 508, jusqu'à une température de l'ordre de
90°C. Le glycol humide, filtré, détendu et
réchauffé passe ensuite dans la colonne de distillation CA506 et
s'écoule par gravité dans le rebouilleur H 507. Un foyer de
combustion de gaz combustible assure une température de
régénération de l'ordre de 204°C dans le rebouilleur
H 507.
29

|
Optimisation d'un procédé de déshydratation
de gaz naturel
|
|
En effet, à cette température, l'eau contenue dans
le glycol humide est transformée en vapeur et évacuée, via
une cheminée équipée d'un serpentin, à un
évent atmosphérique placé en zone
non dangereuse. Le brûleur BAS 701 est alimenté
en gaz BP prélevé sur le collecteur d'aspiration BP des
compresseurs, réchauffé par un serpentin dans le ballon tampon DS
508, et sous contrôle de pression.
Le glycol rebouilli s'écoule par débordement
dans un tube plongeur puis par gravité dans le ballon tampon DS 508
où il réside à une pression quasi-atmosphérique et
une température
légèrement inférieure à 200°C,
dépendant des conditions atmosphériques. Les appoints
périodiques en glycol, afin de compenser les pertes par
entraînement dans le gaz, sont réalisés dans le ballon
tampon DS 508 en utilisant une pompe pneumatique de type Texsteam (TXT). Du gaz
de stripping peut être introduit dans le ballon tampon DS 508 sous
contrôle de pression, mais n'est actuellement pas utilisé.
Le glycol régénéré s'écoule
par gravité vers l'aspiration des pompes de circulation GX 509A/B, en
étant refroidi par l'échangeur multitubulaire glycol-eau de mer
EC 900, jusqu'à une température régulée de l'ordre
de 65°C. Pour limiter les entraînements de glycol dans le gaz, la
température de glycol doit être de 5°C à 10°C
supérieure à celle du gaz.
Deux pompes de circulation GX 509A/B, disposées en
parallèle (une pompe en service et une en « back up »),
assurent le pompage jusqu'à la pression de l'ordre de 75 bar,
nécessaire pour l'injection du glycol
régénéré en haut de la colonne de
déshydratation CA 503.
Le glycol régénéré
pénètre par une ligne 2" dans la colonne CA 503, à
pression et température légèrement supérieures
à celle du gaz, ainsi que représenté sur le PID de la
figure 2.7 ci-après. Les lignes principales sont :
> Ligne 2" glycol humide "riche" en sortie de fond de colonne
CA 503 ;
> Ligne 2" sortie gaz DS 204 vers le réseau torche ;
> Ligne 2" sortie condensats vers le séparateur
atmosphérique DS 202 ;
> Ligne 1" gaz du collecteur d'aspiration BP des compresseurs
;
> Ligne 1" gaz de stripping de la colonne CA 503 ;
> Ligne 1" d'appoints de glycol dans le ballon tampon DS 508
;
> Ligne 2" de glycol régénéré vers
le haut de la colonne CA 503 ;
> Ligne liquide 2" vers la cuve de purge DA 201.
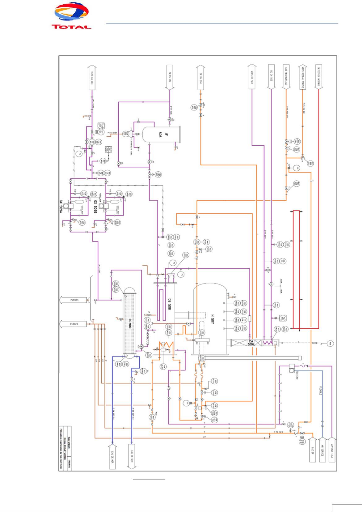
Optimisation d'un procédé de déshydratation
de gaz naturel
Figure 2.7 : PID unité SERTERE UB406
30
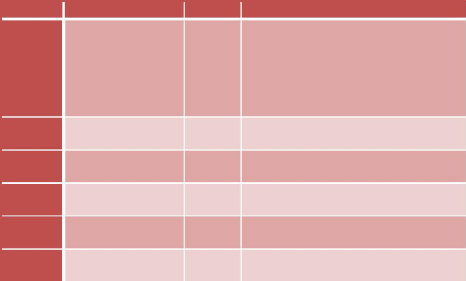
Section 3 : Contrôle & supervision du
procédé
Le niveau liquide dans la partie basse de la colonne CA 503
est contrôlé par le régulateur LC 301 qui agit sur la vanne
de régulation LCV 301 sur la sortie liquide. Le niveau hydrocarbures
liquides du ballon de détente DS 504, est contrôlé par le
régulateur LC 401 qui agit via la vanne de régulation LCV 401 sur
la sortie condensats vers le séparateur atmosphérique. Le niveau
interface glycol/hydrocarbures liquides du ballon de détente DS 504 est
contrôlé par le régulateur LDC 402 qui agit via la vanne de
régulation LDCV 402 sur la ligne glycol riche en aval du filtre IF
505.
La pression dans le ballon de détente DS 504 est
maintenue par une couverture de gaz BP, et contrôlée par le
détendeur PCV 402 qui évacue le gaz vers la torche. La pression
de gaz de couverture qui est envoyé vers le ballon de détente DS
504 est contrôlée par le détendeur PCV 400. La pression du
gaz de stripping expédié vers le ballon tampon DS 508 est
contrôlée par les détendeurs PCV 704 et PCV 702,
disposés en série.
La température du glycol dans le rebouilleur H 507 est
contrôlée par le détendeur PCV 703 et la vanne TCV 701 sur
la ligne de gaz combustible, permettant le contrôle de la flamme du
rebouilleur. La température de glycol en sortie de l'échangeur
glycol/eau EC 900 est contrôlée par la vanne trois voies TCV 900
contrôlant le débit de glycol by-passant l'échangeur.
Le tableau 4 suivant récapitule l'ensemble des
instruments et leurs actions sur l'unité de déshydratation :
Boucle Fonction Typique Remarque
FT503RG
FT503G
LIC301
LT301
TE503
TE507
Régulation liquide de l'absorbeur CA503
Débit gaz HP vers scrubbers DS401/402
Température glycol dans le rebouilleur
Niveau liquide du CA503
Débit gas-lift vers TRM-PFK
Température absorbeur CA503
CF-VTX
CF-GAS
PID
AI
AI
AI
Non représenté sur PID, mais existe
bien sur le SNCC
Correction en pression par PT1400 et en
température par TE503
- Mesure : LT301
- Contrôle : Opérateur seulement
- Mode : Auto / Manu
- Sens régulateur : Inverse
- Limite consigne : non
- Limite sortie : non
- Corrigé par Po et To, mesure
cumulée
---
---

|
Optimisation d'un procédé de déshydratation
de gaz naturel
|
|
31

LDIC402
Optimisation d'un procédé de déshydratation
de gaz naturel
PID
PID
H507
TIC507
Régulation température glycol dans le
rebouilleur H507
Régulation niveau liquide flash tank DS504
|
- Mesure : TE507
- Contrôle : Opérateur seulement
- Mode : Auto / Manu
- Sens régulateur : Inverse
- Forçage : non
- Limite consigne : oui
Limite sortie : non
- Mesure : LDT402
- Contrôle : Opérateur seulement
- Mode : Auto / Manu
- Sens régulateur : Inverse
- Forçage : non
- Limite consigne : non
- Limite sortie : non
LDT402
AI
AI
---
---
Niveau liquide DS504
TE900
Température glycol refoulement GX509A/B
PAL506
Pression basse entrée CA506
DI-ALM
GX509A
XA GX509A
MOT
DI
Pompe Glycol
Marche GX509A
- Commande locale.
---
XD GX509A
Défaut GX509A
DI-ALM
---
GX509B
XA GX509B
MOT
DI
Pompe Glycol
Marche GX509B
- Commande locale.
---
XD GX509B
DI-ALM
DI
DI-ALM
---
---
---
---
---
Défaut GX509B
UB406
XA
Marche UB406
UB406
XD
Défaut UB406
FAL509
DI-ALM
DI-ALM
Débit glycol bas
LAL508
Niveau alarme bas glycol dans DS508
---
32
Tableau 2.3 : Fonctionnement des organes de
contrôle et de régulation
(Source : Analyses fonctionnelles - process control &
safety TRM PFK, EVOLUTEC, rev 3.0, 2010)
|
Optimisation d'un procédé de déshydratation
de gaz naturel
|
|
Section 4 : Système de
sécurité
Un système de sécurité a les fonctions
suivantes :
> Sécurité du personnel ;
> Protection de l'environnement ;
> Protection des procédés.
Il détecte les événements à risques
et agit pour annuler ou réduire leurs effets :
> Fuite d'hydrocarbures ou de produits toxiques ;
> Incendie ;
> Explosion due à une surpression lors d'un
procédé.
Le système d'arrêt de sécurité
d'une installation, constitué d'un ensemble de boucles et de dispositifs
de sécurité, comporte différents sous-systèmes,
organisés en barrières complémentaires du contrôle
du traitement. Pour chaque installation, une logique ESD/SD sera définie
et représentée par un schéma logique ESD/SD. Cette logique
est basée sur la hiérarchie des niveaux ESD et SD, le niveau N
activant le niveau N+1. Le schéma logique ESD/SD illustre la
hiérarchie du haut vers le bas des niveaux ESD et SD, avec toutes leurs
causes et actions sous forme de schéma de principe de la logique. Chaque
niveau est subdivisé en plusieurs barres de sécurité
(jusqu'à une barre par équipement selon le cas). Le nombre de
barres de sécurité varie selon le type d'installation, le nombre
de zones de feu et leurs emplacements, le nombre d'unités
indépendantes dans chaque zone et d'autres caractéristiques de
conception - chaque cas étant spécifique.
L'ensemble des organes de sécurité de
l'unité SERTERE de Torpille est résumé dans le logigramme
de sécurité de la figure 2.8 suivante. Il est à noter que
chaque barre de sécurité est pourvue d'une logique « ou
» (représentée par les deux barres) qui permet à l'un
ou l'autre des défauts ou des niveaux de sécurité en
amont, de déclencher la barre avale en cas d'activation.
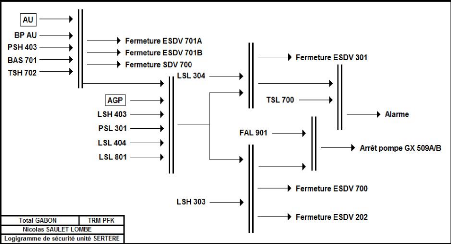
Figure 2.8 : Logigramme de sécurité de
l'unité SERTERE
33
34

|
Optimisation d'un procédé de déshydratation
de gaz naturel
|
|
TROISIÈME PARTIE
OPTIMISATION DU PROCÉDÉ DE
DÉSHYDRATATION DE GAZ NATUREL
|
Optimisation d'un procédé de déshydratation
de gaz naturel
|
|
CHAPITRE I
Simulation de l'unité SERTERE
La simulation est un outil utilisé dans
différents domaines de l'ingénierie et de la recherche en
général, permettant d'analyser le comportement d'un
système avant de l'implémenter et/ou d'en optimiser le
fonctionnement, en testant différentes solutions et différentes
conditions opératoires. Elle s'appuie sur l'élaboration d'un
modèle du système, et permet de réaliser des
scénarii et d'en déduire le comportement du système
physique analysé.
Section 1 : Présentation du simulateur
Pro/II®
Les simulateurs de procédés utilisés
classiquement dans l'industrie, peuvent être considérés
comme des modèles de connaissance. Ils sont basés sur la
résolution de bilans de masse et d'énergie, des équations
d'équilibres thermodynamiques, ... et sont à même de
fournir l'information de base pour la conception. Ils sont principalement
utilisés pour la conception de nouveaux procédés
(dimensionnement d'appareil, analyse du fonctionnement pour différentes
conditions opératoires, optimisation), pour l'optimisation de
procédés existants et l'évaluation de changements
effectués sur les conditions opératoires.
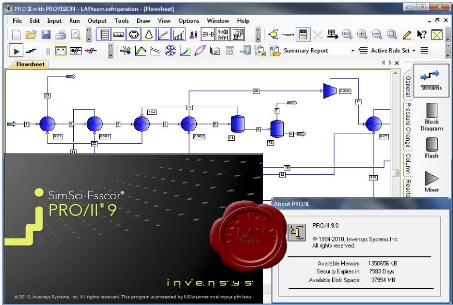
Figure 3.1 : Interface graphique du simulateur
Pro/II®
35
36

|
Optimisation d'un procédé de déshydratation
de gaz naturel
|
|
Le simulateur PRO/II® (dont l'interface graphique est
présentée sur la figure 3.1 précédente) est l'offre
phare dans la suite logicielle de processus des concepteurs SimSci-Esscor
Ingénierie Suite (PSE). Ce simulateur d'état stable effectue des
bilans massiques et énergétiques rigoureux pour un large
éventail de procédés. De la séparation de l'huile
et du gaz à la distillation réactive, PRO/II® combine les
ressources de données d'une grande bibliothèque de composants
chimiques, et des méthodes extensives de prédiction de
propriétés thermodynamiques, avec les techniques les plus
avancées et flexibles d'opérations unitaires. Les
ingénieurs de procédés bénéficient
d'équipements informatiques pour effectuer tous les calculs de bilan de
masse et d'énergie, nécessaires pour modéliser des
procédés pour la plupart à l'état stable dans les
industries chimiques, du pétrole, du gaz naturel, de la transformation
de matières solides, et des polymères.
Tout changement spécifié sur un
élément est répercuté dans tout le modèle.
C'est un logiciel de simulation interactif intégrant la gestion
d'événements (« Event driven ») : c'est-à-dire
qu'à tout moment, un accès instantané à
l'information est possible, de même que toute nouvelle information est
traitée sur demande, et que les calculs qui en découlent
s'effectuent de manière automatique. Deuxièmement, il allie le
concept d'opérations modulaires à celui de résolution
non-séquentielle. Non seulement toute nouvelle information est
traitée dès son arrivée, mais elle est propagée
tout au long du « Flowsheet ».
Avant même de parler de modèles
d'opération de transformation de la matière, il faut des
modèles pour prédire les propriétés physiques de la
matière. C'est pourquoi, ce simulateur dispose d'une base de
données thermodynamiques contenant les propriétés des
corps purs et des mélanges (masse molaire, température
d'ébullition sous conditions normales, paramètres des lois de
tension de vapeur, ...). Tout simulateur industriel de procédés
chimiques est organisé autour des modules suivants :
? Une base de données des corps purs et un ensemble de
méthodes pour estimer les propriétés des mélanges
appelés aussi modèles thermodynamiques ;
? Un schéma de procédé permettant de
décrire les liaisons entre les différentes opérations
unitaires constituant l'unité (PFD pour Process Flow Diagram)
;
? Des modules de calcul des différentes opérations
unitaires contenant les équations
relatives à leur fonctionnement : réacteur
chimique, colonne de distillation, colonne de séparation,
échangeurs de chaleur, pertes de charges, etc... ;
? Un ensemble de méthodes numériques de
résolution des équations des modèles.
37

|
Optimisation d'un procédé de déshydratation
de gaz naturel
|
|
Section 2 : Principes de fonctionnement du
simulateur
Il y a deux modes de fonctionnement dans un simulateur :
statique (ou stationnaire) et dynamique. Les simulateurs statiques
résolvent des équations statiques, qui traduisent le
fonctionnement en régime permanent (à l'équilibre), tandis
que les simulateurs dynamiques, permettent d'évaluer l'évolution
des variables dans le temps, à partir de la résolution de
systèmes d'équations différentielles. Les simulateurs
industriels sur la thermodynamique les plus connus mondialement sont :
· Statiques : ASPEN PLUS® (Aspen
Technologies), Design II® (WinSim), HYSYS®
(Hyprotech), PRO/II® (Simulation Sciences),
PROSIMPLUS® (Prosim) ;
· Dynamiques : HYSYS®
(Hyprotech), ASPEN DYNAMICS® (Aspen Technologies),
Design II® (WinSim), DYMSYM®
(Simulation Sciences Inc.).
Selon le « Chemical Information Bulletin »,
Volume 44, Number 01, Winter 1992 ; les simulateurs dynamiques sont en passe de
se substituer aux simulateurs en régime permanent. Néanmoins,
tout procédé ne peut être simulé à l'aide de
ces simulateurs industriels. En effet, dans le cas de la mise au point d'un
nouveau procédé, il est généralement
nécessaire de disposer de son propre simulateur. Le concept est le
même : sur la base des propriétés thermodynamiques des
corps purs impliqués dans l'opération, et des modèles
thermodynamiques, il y a résolution des équations de bilan de
matière et d'énergie, et des relations d'équilibre
constituant le modèle. La différence vient du fait que,
généralement, seules les propriétés des corps
présents dans le procédé chimique considéré
ne sont détaillées, et que l'environnement de
développement est moins convivial : on parlera alors de simulateur
dédié (spécifique à un procédé
donné). Il a l'avantage de pouvoir avoir une totale maîtrise sur
la façon d'écrire les équations du modèle, et de
les résoudre.
Voyons à présent dans ce qui suit, les
principaux concepts de base et vocabulaires associés, qui sont
utilisés pendant les étapes de construction d'un modèle
dans le simulateur :
- « Flowsheet » : c'est un ensemble
d'objets « Flowsheet Elements » (courants de matière,
d'énergie, d'opérations unitaires, de variables
opératoires) qui constituent tout ou une partie du procédé
simulé, et qui utilisent la même base de données
thermodynamique « Fluid Package ». Le simulateur PRO/II®
possède une Architecture Multi-Flowsheet : il n'y a pas de limite par
rapport au nombre de Flowsheets.
On peut préalablement construire des Flowsheets pour
les utiliser dans une autre simulation, ou organiser la description de
procédés complexes en le scindant en sous-Flowsheets, qui sont
des modèles plus concis (ceci permet de hiérarchiser un processus
très complexe).
38

|
Optimisation d'un procédé de déshydratation
de gaz naturel
|
|
- « Fluid Package » : il permet de
définir les composants chimiques présents dans le
procédé simulé, et leur affecte les
propriétés chimiques et physiques contenues dans la base de
données des corps purs. Il permet aussi de définir les
modèles thermodynamiques qui seront utilisés pour le calcul des
propriétés des mélanges, et de définir les
cinétiques des réactions chimiques mises en jeu dans le
procédé.
- « Process Flow Diagram » : ce
diagramme permet de visualiser les courants et les opérations unitaires,
représentées par des symboles dans le « Flowsheet » ;
ainsi que la connectivité entre les courants, les opérations
unitaires et les tableaux des propriétés des courants.
- « Workbook » : il permet d'avoir
accès à l'information sur les courants et les opérations
unitaires, sous forme de tableau de données.
- « Desktop » : c'est l'espace
principal de l'interface du simulateur PRO/II®, pour visualiser les
fenêtres lors de la conception.
- « Property view » : il contient
l'information décrivant un objet (opération ou courant)
- « Simulation Case » (fichier de
simulation) : c'est l'ensemble des « Fluid Packages »,
« Flowsheets » et « Flowsheet Elements » qui constituent le
modèle.
39

|
Optimisation d'un procédé de déshydratation
de gaz naturel
|
|
Section 3 : Simulation du procédé
3. 1 - Vue d'ensemble
La construction d'un modèle pour optimisation via le
simulateur PRO/II® suit la hiérarchie de la figure 3.2 suivante
:
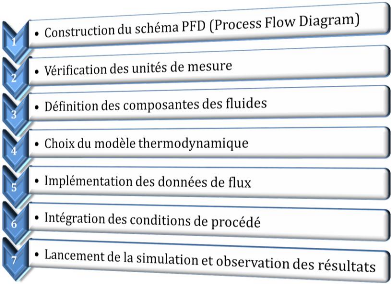
Figure 3.2 : Procédure de simulation
PRO/II®
Le logiciel offre une panoplie de modèles
thermodynamiques, pour le calcul des propriétés thermodynamiques,
tels que les constantes d'équilibres liquide-vapeur, les enthalpies et
les entropies, etc... ; et les propriétés physico-chimiques tels
que la masse volumique, la masse moléculaire, ...
Ces modèles utilisent des outils très divers tel
que :
? Les équations d'états de Peng-Robinson (PR),
Choe-Seader (CS), Soave-Ridliech-
Kwong (SRK).
? Les corrélations empiriques et semi empiriques de
Choe-Seader (CS) et Braun-
Grayon (BG).
? Les lois des états correspondants.
Comme nous nous disposons d'aucune information sur les
détails de calcul du cas design de l'unité SERTERE, nous avons
essayé deux modèle thermodynamiques : Peng-Robinson (PR) et
Soave-Ridliech-Kwong (SRk) qui sont les plus utilisés pour les
systèmes des hydrocarbures, et par défaut, le modèle
« Glycol ».
|
Optimisation d'un procédé de déshydratation
de gaz naturel
|
|
3. 2 - Construction du modèle d'optimisation
Premièrement, nous allons dessiner le schéma de
procédé (PFD) en sélectionnant le fonctionnement de
l'unité souhaitée dans la palette VFI et en faisant
glisser/déposer cette unité sur le schéma. Ensuite, nous
introduirons les flux d'alimentation et des produits pour chaque unité
ainsi que le montre la capture d'écran de la figure 3.3 suivante :
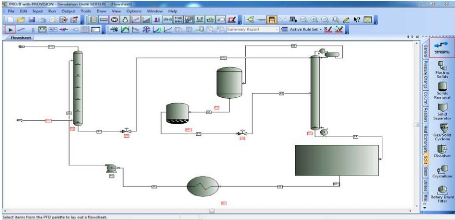
Figure 3.3 : Flowsheet unité SERTERE
Presque chaque quantité a une unité de mesure.
Initialement, le système d'unités par défaut est le
système anglo-saxon. Dans notre cas, nous allons modifier cette
série pour cette simulation, en choisissant le système
métrique, comme sur la figure 3.4 suivante :
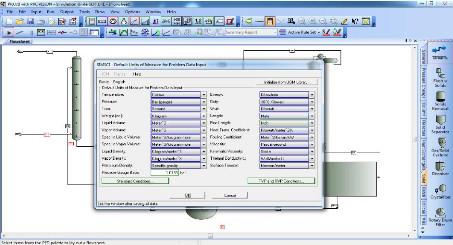
Figure 3.4 : Unités de mesure unité
SERTERE
40
|
Optimisation d'un procédé de déshydratation
de gaz naturel
|
|
Par défaut, le jeu standard anglo-saxon est la valeur
par défaut globale utilisée pour démarrer chaque
simulation. Nous allons modifier cette valeur globale par défaut, par
notre propre jeu de grandeurs, de sorte que chaque simulation
subséquente commence avec cet ensemble.
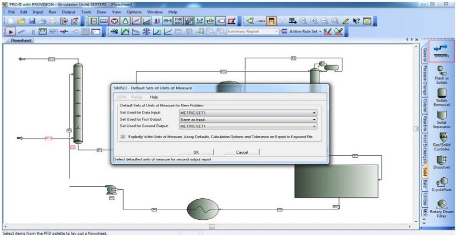
Figure 3.5 : Définition des unités de
mesure
Les composants peuvent être définis en tapant
leur nom dans la bibliothèque de composants, en notant de listes de
produits chimiques, ou en saisissant les composants définis par
l'utilisateur, des solides associés avec des distributions de taille de
particule, et des composants polymères, ainsi qu'illustré sur la
figure 3.6 suivante :
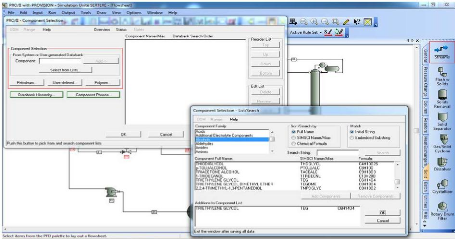
Figure 3.6 : Sélection des composants du flux
traité
41
|
Optimisation d'un procédé de déshydratation
de gaz naturel
|
|
Pour les flux d'alimentation, des conditions thermiques, de
débits, et des compositions doivent être fournis pour tous les
flux d'alimentation externe au schéma. Il est habituellement
souhaitable, mais pas nécessaire, pour fournir des données
estimées pour des courants de recyclage à la convergence de la
vitesse des calculs de recyclage.
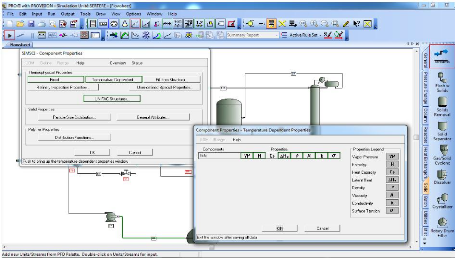
Figure 3.7 : Complément des
propriétés des flux de simulation
Les propriétés des composants purs que vous devez
exécuter une simulation peuvent dépendre de la méthode
thermodynamique sélectionnée, pour cela nous les
réajustons minutieusement.
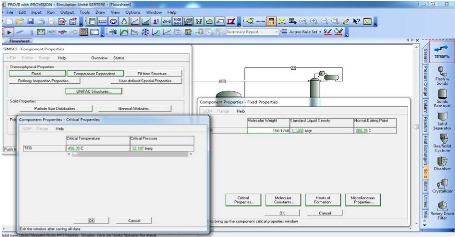
Figure 3.8 : Propriétés
spécifiques du TEG
42
|
Optimisation d'un procédé de déshydratation
de gaz naturel
|
|
La sélection des méthodes thermodynamiques
appropriées est une étape cruciale dans la résolution d'un
problème de simulation. Pour la plupart des problèmes, un
ensemble prédéfini de méthodes thermodynamiques pour le
calcul des valeurs K, enthalpies, entropies, et des densités peut
être utilisé. La figure 3.9 ci-dessous représente nos
modèles sélectionnés :
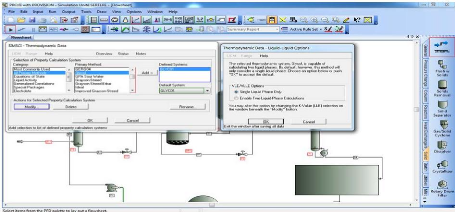
Figure 3.9 : Modèles thermodynamiques de
simulation
Avant d'exécuter la simulation, on vérifie qu'il
n'y a pas de champs bordés de rouge - supposant une insuffisance des
propriétés pour la simulation. Si toutes les frontières
sont en bleu, vert, ou noir sur les boutons de la barre, des étiquettes
de fonctionnement de l'unité, et des étiquettes de flux alors
suffisamment d'informations a été fourni pour exécuter le
schéma de traitement. La figure 3.10 représente le
résultat de la simulation.
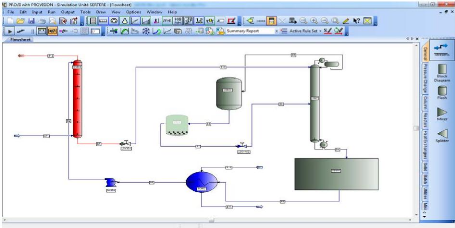
Figure 3.10 : Exécution de la
simulation
43
44

|
Optimisation d'un procédé de déshydratation
de gaz naturel
|
|
Section 4 : Résultats obtenus &
interprétations
L'unité a tout d'abord été
observée dans ses conditions opératoires normales,
c'est-à-dire celles données par le procédé au
moment du test. Le programme initial était donc de faire varier la
température du gaz de 40°C à 60°C en entrée CA
503 en jouant sur l'échangeur EC 443 en aval du compresseur KY 440 et
d'évaluer les performances en terme de régénération
du glycol. Ces différents cas opératoires sont
présentés dans le tableau 3.1 ci-dessous:
CAS
|
DEBIT GAZ (1) (MSm3/jour)
|
PRESSION (1) (Barg)
|
TEMPERATURE (°C)
|
DEBIT D'EAU A ENLEVER (kg/h)
|
1
|
1.05
|
78
|
40
|
33.5
|
2
|
1.05
|
78
|
43
|
40.2
|
3
|
1.05
|
78
|
45
|
45.1
|
4
|
1.05
|
78
|
50
|
59.3
|
5
|
1.05
|
78
|
55
|
77
|
6
|
1.05
|
78
|
60
|
98
|
Tableau 3.1 : Conditions opératoires actuelles
unité SERTERE
(1) Conditions opératoires constatées sur site
Le contacteur de glycol CA 503 traite entre 1.0 et 1.2
MSm3/J de gaz saturé en eau à 43 - 44°C et 76 -
78 bar. La température du rebouilleur est de 204°C et
l'unité est opérée sans gaz de stripping. La mesure du
point de rosée en sortie de la colonne CA 503 donne -16.6°C @ 78
bar (équivalent à -56.1°C @ ATM ou encore 17 ppm). Les
échantillons de glycol pauvre prélevés lors de ces
conditions opératoires donnent un glycol pauvre pur à 99.1% poids
et un glycol riche concentré à 98.7% poids. Les points de
rosée obtenus, bien que légèrement sous-estimés,
sont assez cohérents avec les puretés de glycol mesurées,
dans ces conditions opératoires. Ces résultats montrent que
l'unité de déshydratation et de régénération
atteint des performances tout à fait acceptables au regard de la
spécification demandée (point de rosée inférieur ou
égal à 11°C @ 78 bar), et dans les conditions
opératoires décrites précédemment. L'analyse des
relevés opératoires menés en parallèle, ne montre
pas d'anomalie particulière, et confirme que l'unité est
opérée de manière correcte et satisfait les
spécifications demandées. Cependant, toute augmentation de
capacité de l'unité glycol ne peut être envisagée
sans le remplacement des plateaux du contacteur comme le montre le
simulateur.
45

|
Optimisation d'un procédé de déshydratation
de gaz naturel
|
|
CHAPITRE II
Optimisation du procédé de
déshydratation de gaz naturel
Les machines thermodynamiques fonctionnent avec plusieurs
transformations successives et répétitives formant un cycle. Dans
la pratique, ces transformations ne sont pas réversibles. On remplace
alors ces processus irréversibles par des transformations
réversibles plus facilement calculables: d'où on obtient des
machines idéales qui donnent une première approche du
problème.
Dans les machines thermodynamiques, de la chaleur est
transformée en travail. Cette chaleur est fournie à partir de
combustibles fossiles ou nucléaires ou à partir d'énergie
solaire ou géothermique: elle est transférée au fluide de
travail (eau, air...) à la température la plus
élevée possible. Ces machines sont des systèmes
fermés où le fluide revient à son état initial
après diverses transformations successives.
Section 1 : Analyse d'évènements
L'étude de l'historique des différentes analyses
d'incidents relatifs à l'exploitation de l'unité de
déshydratation de gaz du complexe de Torpille a
révélé les principaux points - à haut potentiel de
risque - suivants :
- 21/07/2006 : Départ de feu localisé à
la sortie de la cheminée du rebouilleur H 507. L'arbre de causes
réalisé au sortir de cet incident a révélé
un défaut de procédure de démarrage de l'unité.
- 29/09/2006 : Incendie au démarrage de l'unité
SERTERE avec pour causes : une régulation flash tank DS504
défaillante associée à une absence de purges de
condensats, une insuffisance des moyens détection feu & gaz (DI/DG),
une absence de maintenance préventive poussée et un logigramme de
sécurité modifié et non suivi.
- 21/07/2008 : Incendie de la cheminée du rebouilleur.
L'arbre de causes réalisé a dévoilé : des
défaillances de la boucle fusible, du logigramme de
sécurité, une procédure de démarrage non
actualisée, et une inhibition locale des sécurités de
l'unité.
Aussi, au regard des différents incendies
répertoriés, il est apparu deux risques principaux
associés à l'unité SERTERE :
46

|
Optimisation d'un procédé de déshydratation
de gaz naturel
|
|
1. 1 - Démarrage du bruleur du rebouilleur de glycol
:
Le démarrage du brûleur est une phase sensible du
démarrage de l'unité glycol. La procédure de
démarrage actuellement en vigueur sur le site mentionne un allumage
manuel du brûleur principal avec vérification de présence
de flamme pilote par l'opérateur extérieur. Le risque principal
associé à cette procédure est le remplissage par du gaz,
de la chambre de combustion en cas de non/mauvaise vérification de la
présence de flamme pilote, et ensuite, une inflammation soudaine de
cette poche de gaz pouvant conduire à une détérioration du
tube à feu et une explosion potentielle. L'absence de séquence
automatique de purge de la chambre de combustion ne permet pas de se
prémunir contre ces risques.
Par ailleurs, selon le logigramme de sécurité de
l'unité, nous pouvons voir que sur non détection de flamme (BAS
701), les vannes de sécurité SDV 700, ESDV 701A/B sont
censées être fermées de manière automatique ; ce qui
ne rend théoriquement pas possible l'admission de gaz vers le bruleur en
l'absence de flamme pilote. Le fait que le problème mentionné
ci-dessus soit déjà arrivé plusieurs fois n'est pas
cohérent avec les organes de sécurité en place, et
impliquerait donc que les sécurités aient été
by-passées ou bien que le détecteur de flamme ne soit pas
fonctionnel.
1. 2 - Problème de pressurisation de la
régénération :
Les rapports d'incidents mis à disposition, exposent un
problème récurrent lors des phases de démarrage et qui
conduit à une pressurisation de la régénération de
glycol depuis le contacteur. Lors des phases d'arrêt de l'unité
SERTERE, le contacteur glycol CA 503 reste pressurisé et devient une
source de pressurisation de l'unité de
régénération. Deux scenarii sont à
considérer pour expliquer de tels incidents :
? Pressurisation depuis le refoulement des pompes glycol GX 509
A/B ;
? Pressurisation depuis la vanne de contrôle de niveau du
contacteur CA 503.
47

|
Optimisation d'un procédé de déshydratation
de gaz naturel
|
|
Section 2 - Performances du procédé
2. 1 - Spécifications techniques
Les performances de l'unité ont pu être
mesurées dans les conditions actuelles de fonctionnement. Les mesures
effectuées sont résumées dans le tableau 3.2 suivant :
|
|
Débit
|
Temp.
|
Temp.
|
Pureté
|
Pureté
|
Dew point
|
|
Condition
|
de
|
du
|
Rebouil
|
Glycol
|
Glycol
|
mesuré
|
Commentaires
|
|
gaz
|
Gaz
|
leur
|
pauvre
|
riche
|
(corrigé)
|
|
Unité
|
MSm 3/d
|
°C
|
°C
|
% mass
|
%mass
|
°C @ 78 barg
|
|
|
Entre
|
|
|
|
|
|
Mesure admise comme
|
Normales
|
1.0 et
1.2
|
44
|
204
|
99.1
|
97.3
|
-4.6
|
incohérente par Prosernat
|
|
|
|
|
|
|
|
(analyseur pas assez balayé)
|
|
Entre
|
|
|
|
|
|
Mesure fiable
|
|
1.0 et
|
43
|
186
|
98.7
|
97.2
|
-10
|
selon Prosernat
|
Modifiées
|
1.2
|
|
|
|
|
|
|
|
Entre
|
|
|
|
|
|
Mesure fiable
|
|
1.0 et
|
45
|
160
|
97.0
|
95.3
|
-8.6
|
selon Prosernat
|
1.2
Tableau 3.2 : Résultats des tests
effectués sur l'unité de déshydratation
Les spécifications recherchées sont un point de
rosée inférieur à 11° C à 78 bar.
D'après la simulation réalisée précédemment,
les performances de l'unité sont tout à fait acceptables,
même en conditions dégradées. Le maintien des performances
de l'unité, malgré une baisse de la température du
rebouilleur s'expliquerait par un effet de stripping, dû à la
vaporisation des condensats entrainés dans l'unité.
2. 2 - Potentiel Hydrogène du TEG
Le gaz à traiter contient environ 1,36% de CO2. Il y a
lieu de contrôler régulièrement le Potentiel
Hydrogène (PH) du TEG. La valeur du PH devra être maintenue entre
7,3 et 8,5 en additionnant au TEG (au niveau du ballon tampon DS 508) du borax,
de l'éthanolamine ou un produit équivalent. En aucun cas
l'unité ne devra fonctionner avec du TEG dont le PH sera
inférieur à 5. L'installation d'un analyseur de pH en ligne
permettra de suivre en temps réel le degré de pureté du
TEG et de réagir à des variations importantes de ces
paramètres.
48

|
Optimisation d'un procédé de déshydratation
de gaz naturel
|
|
2. 3 - Paramètres réglants de l'absorbeur
La composition du gaz à traiter est consignée
dans le tableau 3.3 suivant :
|
|
Sources
|
TRM
Retour TRM-TNEM-MSSM
|
AGM
Retour AGM
|
Point d'échantillonnage
|
Entrée du compresseur
|
Sortie d'AGMP
|
Composition (mol%)
|
N2
|
7.46
|
0.79
|
CO2
|
1.79
|
2.15
|
C1
|
73.53
|
75.50
|
|
7.31
|
7.08
|
C3
|
5.59
|
7.02
|
iC4
|
1.19
|
1.59
|
nC4
|
1.78
|
2.45
|
iC5
|
0.61
|
0.95
|
nC5
|
0.35
|
0.74
|
C6+
|
0.41
|
1.69
|
Poids Moléculaire (g/mol) Densité
relative
|
22.18
|
23.65
|
0.766
|
0.817
|
Tableau 3.3 : Composition des gaz associés TRM
& AGM (source : Audit SERTERE, Prosernat, 2014)
Bien qu'un grand nombre de paramètres soient
impliqués dans l'unité de déshydratation de gaz
présentée ici (nombre de plateaux dans l'absorbeur, débit
de circulation du glycol, conditions de saturation, etc.), la concentration du
glycol régénéré est la plus significative. On
retiendra donc en paramètres réglants :
? La concentration du glycol
régénéré : le degré de pureté du TEG
dépend de la température de bain du rebouilleur (la limite
fixée est de 204°C, le TEG se dégradant à 215°C)
et de la pression de fonctionnement de la colonne de distillation
(légère dépression) ;
? La température du gaz dans l'absorbeur : le point de
rosée en tête de l'absorbeur, dépend de la pression
partielle de l'eau en équilibre avec le glycol
régénéré à la température de
tête de l'absorbeur ;
? Le taux de circulation du glycol : quand le nombre de
plateaux de l'absorbeur et la concentration sont fixés, la
dépression du point de rosée eau du gaz est fonction du
débit de circulation de glycol - le débit minimum de circulation
de glycol pour assurer un bon contact glycol-gaz étant de 15 - 25 litres
par kg d'eau à enlever ;
? Les conditions de saturation du gaz : à pression
constante, une variation de 15°C sur la température du gaz modifie,
d'un facteur "2" sa teneur en eau.
49

|
Optimisation d'un procédé de déshydratation
de gaz naturel
|
|
Section 3 : Amélioration du
procédé
L'amélioration de l'opérabilité et de la
sécurité sur l'unité SERTERE, requiert une
numérisation plus importante du procédé (avec
l'installation de nombreuses jauges et transmetteurs et l'automatisation de la
séquence de démarrage), et selon les besoins à venir, le
remplacement du réchauffeur à gaz par un réchauffeur
électrique.
Outre ces opérations prioritaires, d'autres travaux aux
CAPEX très limités sont également importants :
? Le remplacement de la PSV manuelle de la colonne par une PSV
pilotée. En effet, la
pression de sortie de la compression (78 bar), laissera peu de
marge par rapport au « rating » des conduites (83 bar) ;
? L'installation de clapets individuels sur le refoulement des
pompes de circulation glycol GX 509A/B ;
? L'installation d'une BDV (Blow Down Valve) pour faire face
à un scénario de
dépressurisation d'urgence, dans la mesure où la
colonne peut être isolée et exposée au feu.
3. 1 - Automatisation du procédé
Un processus industriel est un ensemble d'équipements
qui permet, à partir d'énergie et de produits bruts ou non finis,
de fabriquer des produits finis ou des objets directement utilisables.
L'automatisation d'un processus revient à le placer sous la commande
d'un système qui le conduit vers un objectif donné en
dépit des perturbations qu'il subit.
L'étude de l'unité de déshydratation de
gaz du site de Torpille, permet d'affirmer qu'un certain nombre d'actions de
maintenance telle que le remplacement d'instruments manquants ou
défectueux seraient bénéfiques pour
l'opérabilité de l'unité et permettraient en outre de
faciliter les diagnostics en cas de problèmes opératoires.
L'ajout d'instruments et notamment de transmetteurs renvoyés en salle de
contrôle, et enregistrés dans le SNCC, faciliterait
également le suivi de la bonne marche de l'unité. Actuellement,
trop peu d'informations sont reportées et enregistrées dans le
SNCC. La figure 3.11 suivante expose la liste des instruments à
implémenter pour un « monitoring » efficace de l'unité
et le grafcet de démarrage de la figure 3.12 résoudra les
problèmes de sécurité au démarrage.
50

|
Optimisation d'un procédé de déshydratation
de gaz naturel
|
|
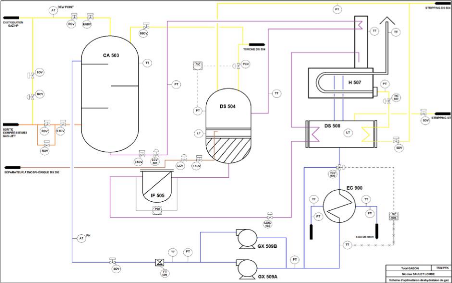
Figure 3.11 : Schéma d'optimisation
unité SERTERE
Ainsi, en considérant uniquement une optimisation du
procédé existant, les nouveaux instruments installés,
permettront entre autre de :
> Contrôler les températures d'entrée et
sortie de gaz et de TEG dans l'absorbeur et de
ce fait de s'assurer du respect de la différence de
température requise (entre 5°C et 10°C) ;
> Analyser le point de rosée eau en sortie de
l'absorbeur CA 503 et ainsi contrôler
l'efficacité du traitement effectué
(prévoir possibilité de comparaison manuelle des
résultats) ;
> S'assurer du degré de pureté du TEG en
décelant et en anticipant sur une dégradation éventuelle
par mesure du PH ;
> Permettre des dépressurations complètes de
l'unité en cas d'arrêt d'urgence ;
> Permettre le contrôle des températures en
ayant une vision globale des différentes étapes de
préchauffage et chauffage ;
> S'assurer de l'opérabilité continue de
l'unité selon les spécifications du constructeur ;
> Répondre aux besoins croissants de traitement par
ajustement contrôlé des paramètres. En complément de
ces modifications, une nécessité de revue et de consolidation de
la procédure actuelle de démarrage implique la mise en oeuvre de
l'automatisme de démarrage selon le grafcet présenté sur
la figure 3.12 suivante :
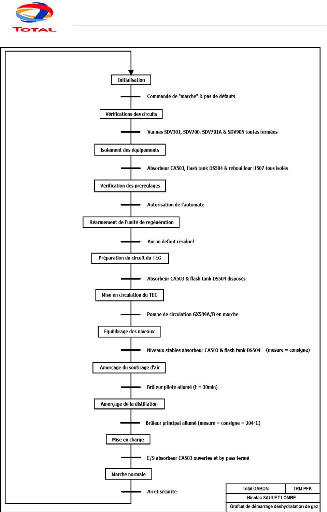
Optimisation d'un procédé de déshydratation
de gaz naturel
Figure 3.12 : Grafcet de démarrage
unité SERTERE
51
52

|
Optimisation d'un procédé de déshydratation
de gaz naturel
|
|
3. 2 - Installation du réchauffeur
électrique
Le remplacement du système de réchauffage
à flamme nue par un réchauffeur électrique permet de
résoudre la plupart des problèmes de sécurité de
l'unité, et est de ce fait prioritaire. Il a donc fait l'objet d'une
étude d'ingénierie par l'entreprise Sofresid en trois parties
:
+ Étude de l'installation des supports du faisceau
électrique (modifications des serpentins du rebouilleur,)
+ Philosophie électrique de protection et de
contrôle :
> Installation d'une salle technique pour les nouvelles
armoires électrique
> Etude du câblage > Bilan de puissance
+ Consultation des vendeurs de réchauffeurs : suite aux
résultats des deux études précédentes, les
spécifications portent sur trois éléments :
> Un réchauffeur électrique BGHE 4301 > Un
gradateur électrique BGIE 4301 > Un panneau de contrôle.
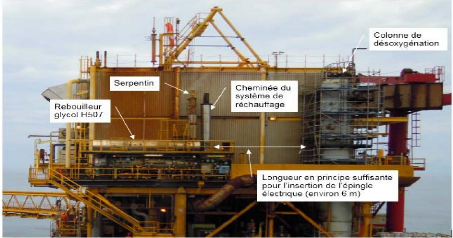
Photo 3.1 : Vue de profil unité
SERTERE
Son installation (sur les supports existants du rebouilleur)
nécessite un berceau guide (demi-tube) pour insertion dans le
réchauffeur sans heurter les supports internes. Un aperçu du
layout (voir photographie 3.1 ci-dessous) de TRM PFK indique qu'il y a
suffisamment d'espace entre le rebouilleur et la colonne de
désoxygénation située plus au Nord.
|
Optimisation d'un procédé de déshydratation
de gaz naturel
|
|
Les spécifications du réchauffeur
électrique (voir figure 3.13) s'appuient sur les calculs de Prosernat
:
- Puissance du rebouilleur électrique estimée: 400
kW
> Puissance requise : 331 kW + 20% marge, basé sur
le débit de gaz de 1.4 MSm3/d, soit 400 kW ;
> Le débit d'eau à évacuer est
estimé à 63 kg/h. Hypothèse : tous les condensats
accumulés sont entrainé dans l'unité et
doivent être vaporisés (calcul conservatif) ; > Pour un
débit gaz de 1.7 MSm3/j, la puissance estimée du
rebouilleur devrait être de
410 kW.
- Estimation de la taille du faisceau électrique
> Bride de 16"
> Longueur totale immergée : 3500mm > Flux de
chaleur : 2.2 W/cm2
> 0% d'épingles en plus non connectées
La société Vulcanic propose une épingle
électrique avec les caractéristiques suivantes :
> Longueur immergée : 4,10 m
> Longueur totale à installer : 5,075 m > Poids :
400 kg
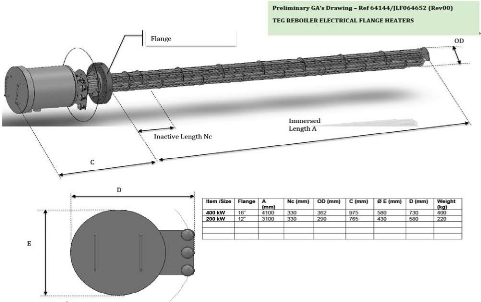
Figure 3.13 : Epingle électrique BGHE 4301
(source : Audit unité SERTERE, Prosernat, 2014)
53
|
Optimisation d'un procédé de déshydratation
de gaz naturel
|
|
Section 4 : Étude économique
L'estimation des « manhours » de ces travaux est
tirée de l'étude faite par la société Sofresid (cf.
tableau 3.4), et les coûts par EST (voir tableau 3.5). Les faibles
montants estimés sont en-dehors de l'intervalle d'étude EST. Il
en résulte une forte imprécision dans les résultats. Pour
ce type de travaux, une estimation par l'entreprise, plus au fait du contexte
local, est préférable. C'est aussi la raison pour laquelle la
demande de modification Instrumentation, et les installations de la BDV et des
clapets anti-retour sur les pompes n'ont pu être estimés.
Phase
Préfabrication
Unité TEG
150 h
SIMOPS
Shutdown
4600 h
900 h
Installation of BDV
New
instrumentati on system
Installation of glycol pump flaps
Tableau 3.4 : Upgrade de l'unité de
déshydratation : estimation des « manhours »
(source : Upgrading unité de déshydratation
de gaz, Sofreid, 2014)
Bulk mater ial
Construct ion
Contrac tor EMS
EP CI cost
Compa ny costs
Contingen cies
35%
CAP EX P50
Main équipem ent
No estimation, estimate should be considered by
TOTAL GABON
|

350 k$
568 k$
70 k$
58 k$
147 k$
171 3 k$
2775 k$
116 k$
343 k$
286 k$
104 k$
1208 k$
720 k$
266 2 k$
4313 k$
442 k$
532 k$
444 k$
156 k$
1621 k$
1118 k$
Installation of a piloted PSV
Replacement of internals+dem ister
Installation of an electrical heater
WU 4 TOTAL
52 k$
413 k$
100 k$
599 k$
120 k$
251 k$
970 k$
292 k$
34 k$
54
Tableau 3.5 : Upgrade de l'unité de
déshydratation : estimation des coûts (source : Upgrading
unité de déshydratation de gaz, EST, 2014)
55

|
Optimisation d'un procédé de déshydratation
de gaz naturel
|
|
CONCLUSION
L'évaluation de l'optimisation du procédé
de déshydratation du gaz naturel de la plateforme TRM-PFK du site de
Torpille a permis de cerner trois axes principaux :
L'étude de l'aspect « sécurité
» de l'unité a montré que des améliorations telles
que l'installation d'un réchauffeur électrique en lieu et place
du tube à feu existant permettrait de supprimer le facteur de risque
lié au démarrage du brûleur ; cet élément
étant le plus gros vecteur de risque de l'unité. D'autres
modifications mineures explicitées plus en détails dans ce
mémoire, permettraient également d'augmenter la
sécurité de l'unité, notamment en phase de
démarrage.
L'étude du fonctionnement de l'unité, permet
d'affirmer qu'un certain nombre d'actions de maintenance telle que le
remplacement d'instruments manquants ou défectueux, seraient
bénéfiques pour l'opérabilité du
procédé, et permettraient en outre de faciliter les diagnostics
en cas de problèmes opératoires. L'ajout d'instruments et
notamment de transmetteurs renvoyés en salle de contrôle, et
enregistrés dans le SNCC, faciliterait également le suivi de la
bonne marche du procédé de traitement. Actuellement, trop peu
d'informations sont reportées, enregistrées.
Enfin, les performances de l'unité ont pu être
mesurées et simulées dans les conditions actuelles de
fonctionnement. Il peut être affirmé que l'unité atteint
des performances tout à fait en ligne avec les spécifications
requises.
En revanche, il n'est pas actuellement possible de confirmer
les performances de l'unité de régénération dans
les conditions futures de fonctionnement les plus sévères. Les
calculs menés par Prosernat, montrent que la puissance de rebouillage
requise (410kW), est supérieure à la puissance installée
du tube à feu (350kW duty design). L'augmentation de la puissance
disponible au rebouilleur est indispensable à l'augmentation de la
capacité de traitement, dans les conditions énoncées dans
le rapport. Cette augmentation peut être accomplie par l'installation
d'un faisceau électrique de puissance adéquate - ce qui
permettrait également de supprimer les risques liés au
démarrage du bruleur existant.
Si les premières évaluations menées
permettent de supposer que l'installation d'un faisceau
56

|
Optimisation d'un procédé de déshydratation
de gaz naturel
|
|
électrique de diamètre 16" est réalisable
dans le rebouilleur existant, une étude complète est à
mener afin de confirmer la faisabilité d'un tel remplacement. En outre,
il semble important de notifier que l'augmentation de la capacité de
traitement de l'unité de déshydratation par absorption au glycol,
ne peut être envisagée sans le remplacement des plateaux de la
colonne de déshydratation.
XI
RÉFÉRENCES BIBLIOGRAPHIQUES
1. « Analyses d'évènements de Torpille
», Total Gabon, 2006-2015.
2. « Analyses fonctionnelles - Process control &
safety system TRM PFK », EVOLUTEC, Rev 3.0, 12/07/2010.
3. « Historique de Total Gabon »,
www.total.ga.
4. « Manuel d'Exploitation - secteur Torpille»,
Total Gabon, Rev 0, 30/05/2005.
5. « Notice de mise en service
régénération glycol de Torpille », SERTERE, Ref 137,
Rev A, 06/09/2001.
6. « PHILOSOPHIE ELECTRIQUE PROTECTION & CONTROLE
», SOFRESID Engineering, Contractor doc. No.:S47537, GA-TOR-04-SEN-030001
rev00, 25/06/2014.
7. « Préimplantation du réchauffeur dans
le rebouilleur », SOFRESID Engineering, Contractor doc. No.:S47537,
mark-up drawing, 10/06/2014.
8. « PRO/II academic manual - student edition »,
Invensys SIMSCI-ESSCOR, USA, 2007.
9. « Procédure de démarrage de
l'unité de déshydratation de gaz », Nicolas SAULET, Total
Gabon, 2014.
10. « Review of the existing Gas Dehydration Unit of
Torpille Installation (TRMPFK) - GABON », Kingsley EZEAGWULA / Aurelie
CHAMORET, DEV/ED/ECP, 284ECP13, 21/11/2013.
11. « Revue Qualité APP - Avant-projet "Torpille
compression gaz" - WU 2 et 4 », Guillaume POTTIER, DEV/ED/APP, 250APP14GP,
26/06/2014.
12. « SPECIFICATION FOR ELECTRICAL HEATER - BGHE 4301
», SOFRESID Engineering, Contractor doc. No.:S47537, GA-TOR-04-SEN-030004
rev00, 10/06/2014.
13. « TECHNICAL BID - TORPILLE - TRM DEGOULOTTAGE - TEG
Reboiler Electrical Heater and Thyristor Control Panel », Jean-Louis
FARIZZANO, VULCANIC, 66144/JLF064652 Rev 00, 16/06/2014.
14. « Torpille - Rapport d'audit et de test de
l'unité glycol de Torpille TRMPFK », PROSERNAT, n° 61320-001,
09/04/2014.
15. « TRMPFK - Electrical Consumer List and Load Balance
», SOFRESID Engineering, Contractor doc. No.:S47537, GA-TOR-04-SEN-030002
rev00, 12/06/2014.
ANNEXES
XII
Annexe I : Diagramme de McKETTA XIII
Annexe II : Synoptique SNCC « vue générale gaz
- TRM » XIV
Annexe III : Synoptique SNCC « unité SERTERE - TRM
» XV
|
|
H2O CONTENT OF MOISTURE SATURATED
GASES -- Chart of McKETTA --
|
|
|
enspm
F°rrr..n4~ IMI.IET N
I FF. . TRAPN IMta
|
|
-- Chart 1-
|
80000
60000
40000
20000
10000
8000
600D
4000
2022
1000
800
61X1
400
200
1pp1X1 1X1
60
40
20
10
8
5
4
2
2
II O Content of saturated wet gas
(IbVMMSCF)
80000
60000
40000
20000
10000 B000
6000
4000
2000
1000
800
690
400
200
100
80
60
40
20
10
8
5
4
2
1
.60 .20 4
XIII
20 40 60 BO 100 120 140 160 1B0 21X1 240 280
===--===UirimaiFi. ..
ai. ·rjrjr u ~ a
===--===~ m. ai. .9.
aailo.I~a.
=alalal==MFAMPA ME EN VAN ·
· alM.ErM I ·-----m-i41. Era M · U rJ/fiil
i
· -- ·--Ga-FAMP NNE !.5r4 !M
I
AVM Ain :
,MmmmmFaMraai ·ai5=mllo...ia
r- rrjra
!fr
~~mmailra.l ll.q.7
irllJ..6 ·
01MM''iM ~
i .il~.FJ.tiila'iLrJfi
Yii!Jiq_YI=. FI
U'AALrJiiRAi6.i
rail.!!!!i fqY REM ri
Rd MErd=17R
! ·!! il.ilRrli.a!alla'aa Paha= ia!
=!iMFJ===mllas A aJ7l
.iaa l WAi li.Jl RlLr....Olil...iiLI,..
i . ... lISiFF
pppY
lYig~~itiZârYaf~ryi
Y. 1.,==...i=, M! 1
i °A rJlFa WAN ILU
Ri ai Ra b*ripr Wisirni I
FM Wii = WA= Wi ·MIaerl~al
-5A-R-lNM Ma5RfilI --ER-w- ·PA gird
5111!
_a iw!
iml0lmm.4mm.C~raRfrJ
irA.A.AR r a r
irarnMR Iii iiMA= ari ram WEN
MMMEMEMIN
.Z,sâ
n ~i~r:~fJi~ilüSWLiA rar~ Fi J4
s... san. ...
r. .l.l HllCrJtgi Sii i1l. Rfi
. YY.Y.r!
Yi! i~Li.i WARM an mmmril
MFA r...{Il=Faa
K.FI i! Y! . !!.l..!
Y.N EiTi1 iOWE.A~. NN. .EN
YJm mm
.!!.l..
WAMINPRIMMWdrinliMOM · · ·
· · I
tiiM%91911/12i191L1d159E AIN E r ... ·
1
MISI WIiIGLIEPAN I
rff, mum mi

.
i
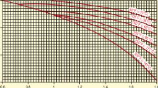
50
.{
EMI II INIMINE ·11110 Zr..1 ·1 II
Ia.
EMI II INEMENN ·I II II MI
EMI II MINIMS. .1MM I II ME
EMI II MINIMS. IFINEMEME II 1.1.1MININCREEME
Sp{eJIIQ 9rr.1ty morgue r
YYIYIYYY!
...
IY.Y.IY.YII----. ___._...
mi..
._a___ ME â i ·91 .-.--.
. N · AliIQii 1
n - DAME r
ml ai.. w mai10...!
i~ !!!!!i irA Y! al. =.i..q.
iliG! i. _____fl..
=Mrra= NA= =FA .. r1mma7!ii
ii iil il . lf.l R!!JI
i.d Yl . a. l ·A!M
!!!!!i ^.~!! FFY!f alil~~
Warning: dashed lints are meta-sta ble equilibrium.
Actual equilibrium is lower water cent nt. Angle isa function
ofoomposition.
9
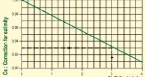
------
-m
.=
I F!
I
11 W
.. rEr
I iI.
. I -
wYYY!Y!Yl YIrJa.
!Y
IIIIIIIIIII _______I I~1 IIIIIIIIIII
IIIIIIIIIIIIIIIIIIIIIIIIIIIIIIIIIIIIIIIIIIIEMP.M51
·
lw w~!!!!~YlRi La lw
wYYYlYIYYi_J_ · a. lw
wYYlYIYIYIi.! ~. .....---mar_W i
M
n ~ --111_11__.
. mm. II-- mm aimn _i
--:III..IIIII.
a
mGi== --i1I mai. IIIII
a
. mm. II-- mm m~ mai m.1
I
n ENI
!i 1,0 iL!.iliii. I mR.u%Gi.
mi.i.ii
laaaR Oia'''&35Mlr
Mar/ r.=.riarmara. MN MU WM FM JliilOi
Wli4l FM MN `J=. LA mm.IIm!.'JR.91.I!1=7a6M
rard
.. __._..
Ri0P0 ·A4gi ·I1,077010FU0Ra1M=
m ..iiiii
MrA rue: ra loli.or.Inllc rl.Il II I. m .mai .
!w
...1..A1
fMYal.il.M
iHr.Lrll'i.M-......=i=_
_ __ ___
n iY
iiii
~..M â~~~ :
M..ar ~~ ii !i Position of th is line
Y.=M:=ii
.mm. mm.
F.mF.m!..1m~ai.9i..11
:I= E5 MS. 11M .m mm..
~~..! ii..~I./4FM Fol 15a
function
*iafgas · · m
· · · ·E!!!
=~ , i1~~ i i
li=Ai.Fiiiii:
Camp OS Ft ;On Ea a!EE!E!!Ii !ww An
Mald
il~L!l Can ri L!!!
!~Ylm.m!!.l..
lw tar .JlArtlaili YYYrYY.Y..
...faS FJi
·mai...
. ..r R WM mai..
.ararari .IPM
MMialalalalrna_.....MM..I EWA
PM.=OPMtI !' e
-----l ·- ·1
n rMIl--iIIMra ---- ·--I
ÎaSYi .} r.w wm~Iia.liE!!!
.Ma · mtS.O.I--mrar..
--7..191... .~ Fa ·miai~i~
rJ~.rFa ·Fl..
!w wYYIi.AFi.Jl Hl-
|
|
|
|
|
|
|
|
|
|
|
|
|
|
|
|
!!Y ___._..
mai..
mai....
mai.m
|
|
|
|
|
|
|
|
|
|
|
|
|
|
|
|
|
|
|
|
|
|
|
|
|
|
|
|
|
|
|
|
|
|
|
|
|
|
|
|
|
|
|
|
|
|
|
|
|
|
|
|
|
|
|
|
|
|
|
|
|
|
|
|
|
|
|
|
|
|
|
MMAM
|
|
|
|
|
|
|
|
|
|
|
|
|
|
|
|
|
|
|
|
|
|
|
|
|
|
|
|
|
|
|
|
|
|
|
|
|
|
|
|
|
|
|
-60 -40 -20 0 20 40 60 80 100 120 140 160 180 200 240
290
Temperature °F)
m3 4135
.11VMMSCF .16.9076 Ir N ' = 1E0187 m &m' - S$ Km
Y4lrme,
@ 21}09 - I F P Training
Annexe I : Diagramme de McKETTA (source :
Traitement des gaz, IFP Training, 2009)
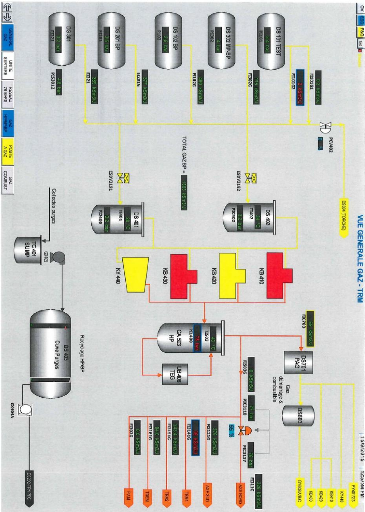
XIV
Annexe II : Synoptique SNCC « Vue
générale gaz - TRM » (Source : Interface
opérateur, DeltaV EMERSON, 2015)
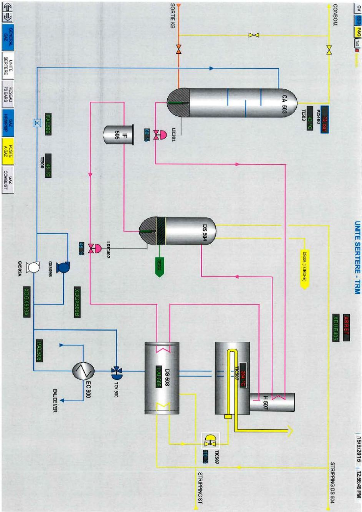
XV
Annexe III : Synoptique SNCC « unité
SERTERE - TRM » (Source : Interface opérateur, DeltaV
EMERSON, 2015)
XVI
TABLE DES MATIÈRES
Remerciements IV
Dédicace V
Avant-propos VI
Résumé VII
Sigles & abréviations VIII
Table des illustrations IX
Sommaire X
Introduction 1
Première partie : Introduction au traitement de
gaz naturel 3
Chapitre I : Le gaz naturel 4
Section 1 : Généralités sur le gaz naturel
5
Section 2 : Spécifications technico-commerciales 5
2. 1 - Spécifications commerciales 5
2. 1. 1 - Teneur en H2S 6
2. 1. 2 - Souffre total et autres contaminants 6
2. 1. 3 - Teneur en CO2 6
2. 1. 4 - Point de rosée 6
2. 1. 5 - Pouvoir calorifique 7
2. 2 - Spécifications pour le transport 7
2. 2. 1 - Point de rosée eau 7
2. 2. 2 - Teneur en hydrocarbure liquide 7
Section 3 : Bases théoriques du traitement de gaz naturel
8
3. 1 - Teneur en eau 8
3. 1. 1 - Détermination graphique 8
3. 1. 2 - Détermination empirique 9
3. 2 - Techniques de traitement du gaz naturel 10
Chapitre II : Hydrates de gaz 11
Section 1 : Nature 11
Section 2 : Conditions de formation 11
2. 1 - Présence d'eau liquide 13
2. 2 - Présence d'hydrocarbures légers 13
2. 3 - Réalisations de certaines conditions (P, T) 13
Section 3 : Prévention contre les hydrates 14
Deuxième partie : Description du
procédé de déshydratation 16
Chapitre I : Présentation du complexe de Torpille
Marine 17
Section 1 : Historique du champ de Torpille 17
Section 2 : Installations de production 19
Section 3 : Philosophie d'exploitation 21
3. 1 - Mode d'exploitation 21
XVII
3. 1. 1 - Champs 21
3. 1. 2 - Réseau gaz HP 22
3. 1. 3 - Réseau huile 22
3. 2 - Mode de fonctionnement 22
3. 2. 1 - Détection feu & gaz 23
3. 2. 2 - Réseau électrique 23
3. 3 - Organisation du travail 23
Chapitre II : Description du procédé de
déshydratation de gaz naturel 24
Section 1 : Section de déshydratation par absorption 24
Section 2 : Section de régénération du TEG
(Unité SERTERE) 27
Section 3 : Contrôle & supervision du
procédé 31
Section 4 : Système de sécurité 33
Troisième partie : Optimisation du
procédé de déshydratation de gaz 34
Chapitre I : Simulation de l'unité SERTERE
35
Section 1 : Présentation du simulateur Pro/II 35
Section 2 : Principes de fonctionnement du simulateur 37
Section 3 : Simulation du procédé 39
3. 1 - Vue d'ensemble 39
3. 2 - Construction du modèle d'optimisation 40
Section 4 : Résultats obtenus & Interprétations
44
Chapitre II : Optimisation du procédé
45
Section 1 : Analyse d'évènements 45
1. 1 - Démarrage du bruleur du rebouilleur de glycol 46
1. 2 - Problème de pressurisation de la
régénération 46
Section 2 : Performances du procédé 47
2. 1 - Spécifications techniques 47
2. 2 - Potentiel hydrogène du TEG 47
2. 3 - Paramètres réglants de l'absorbeur 48
Section 3 : Amélioration du procédé 49
3. 1 - Automatisation du procédé 49
3. 2 - Installation du réchauffeur électrique 52
Section 4 : Etude économique et environnementale 54
Conclusion générale 55
Références bibliographiques XI
Annexes XII
Table des matières XVI
L'objectif principal de ce travail, est de fournir des
propositions d'amélioration du procédé existant de
déshydratation de gaz naturel du site de Torpille de l'entreprise Total
Gabon. Cette unité a été le théâtre de
plusieurs incidents de sécurité à haut potentiel de risque
et sa capacité à accompagner le dégoulottage de la
chaîne gaz est incertaine. L'optimisation du procédé ici
décrite, se basera sur les résultats de sa simulation grâce
au logiciel thermodynamique Invensys PRO/II®; ainsi que sur la
nécessité d'automatiser les processus de démarrage et de
marche normale. En effet, l'étude du fonctionnement de l'unité,
permet d'affirmer qu'un certain nombre d'actions de maintenance telle que le
remplacement d'instruments manquants ou défectueux, seraient
bénéfiques pour l'opérabilité du
procédé, et permettraient en outre de faciliter les diagnostics
en cas de problèmes opératoires. L'installation d'un
réchauffeur électrique, en lieu et place du tube à feu
existant, permettrait de supprimer le facteur de risque lié au
démarrage du brûleur - cet élément étant le
plus gros vecteur de risque de l'unité.
Mots-clés : Gaz - Hydrates -
Déshydratation - Simulation - Optimisation - Sécurité.
The main objective of this work is to provide proposals for
improving the existing process natural gas dehydration of production site
Torpille of the company Total Gabon. This unit has been the scene of several
safety incidents with high risk potential and its ability to support the
debottlenecking of the gas chain is uncertain. The optimization of the process
described here, will be based on the results of its simulation software through
thermodynamic Invensys PRO / II®; and the need to automate startup and
normal operation process. Indeed, the study of the functioning of the unit, for
the proposition that a number of maintenance actions such as the replacement of
missing or defective instruments are beneficial for the operability of the
process and allow for further facilitate diagnostics in case of operating
problems. The installation of an electric heater, instead of in existing fire
tube would remove the risk factor linked to the burner start - this element
being the biggest risk of vector unit.
Keywords : Gas - hydrates -
dehydratation - simulation - optimization - safety.
|